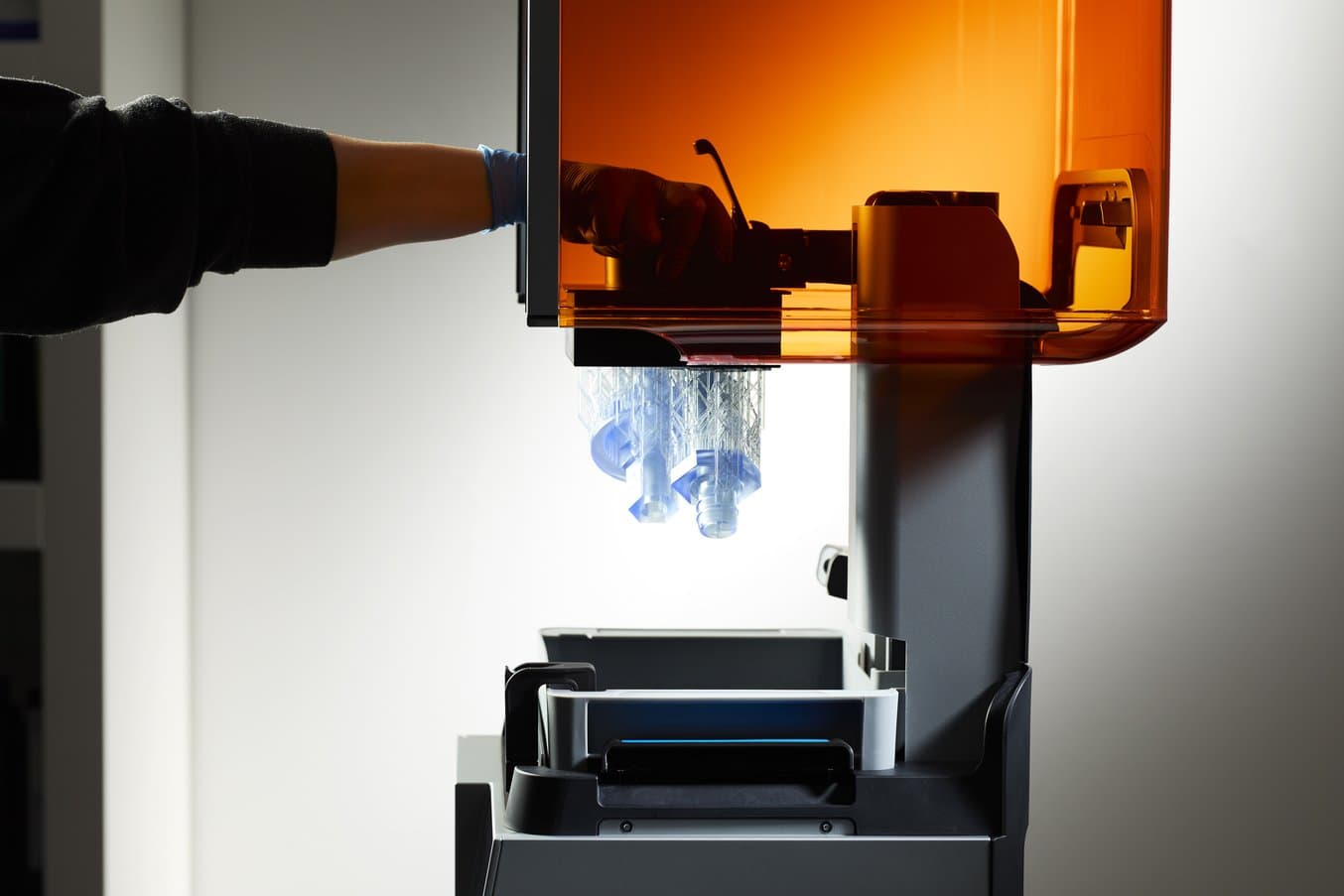
Additive manufacturing (AM), also known as 3D printing, is a powerful, popular tool to accelerate product development and manufacturing across many industries. Reliability is critical for any tool designed to create parts, and 3D printing is no exception. While 3D printing has made huge leaps over the past decade, many printers are still held back by poor reliability. In a 2024 survey by 3D Printing Industry, leaders in additive manufacturing listed “Machine and Process Reliability” as the number one barrier to achieving broader adoption in 3D printing.
Unfortunately, to date, there hasn’t been any reliable quantitative information available to customers to make purchasing decisions from. To help address this, we had a series of comprehensive performance tests conducted by an independent global leader in product testing. These tests were performed on select stereolithography (SLA) 3D printers including Form 4, Form 3+, and two comparatively low-cost resin 3D printers. This testing was to evaluate the print success rate and repeatability of parts printed on the respective printers.
Formlabs Form 4 was measured to have a 98.7% print success rate, while the benchmark printers tested have 10x-20x the failure rate of Form 4.
To read the complete description of the test methodology and to see the results, download the white paper.
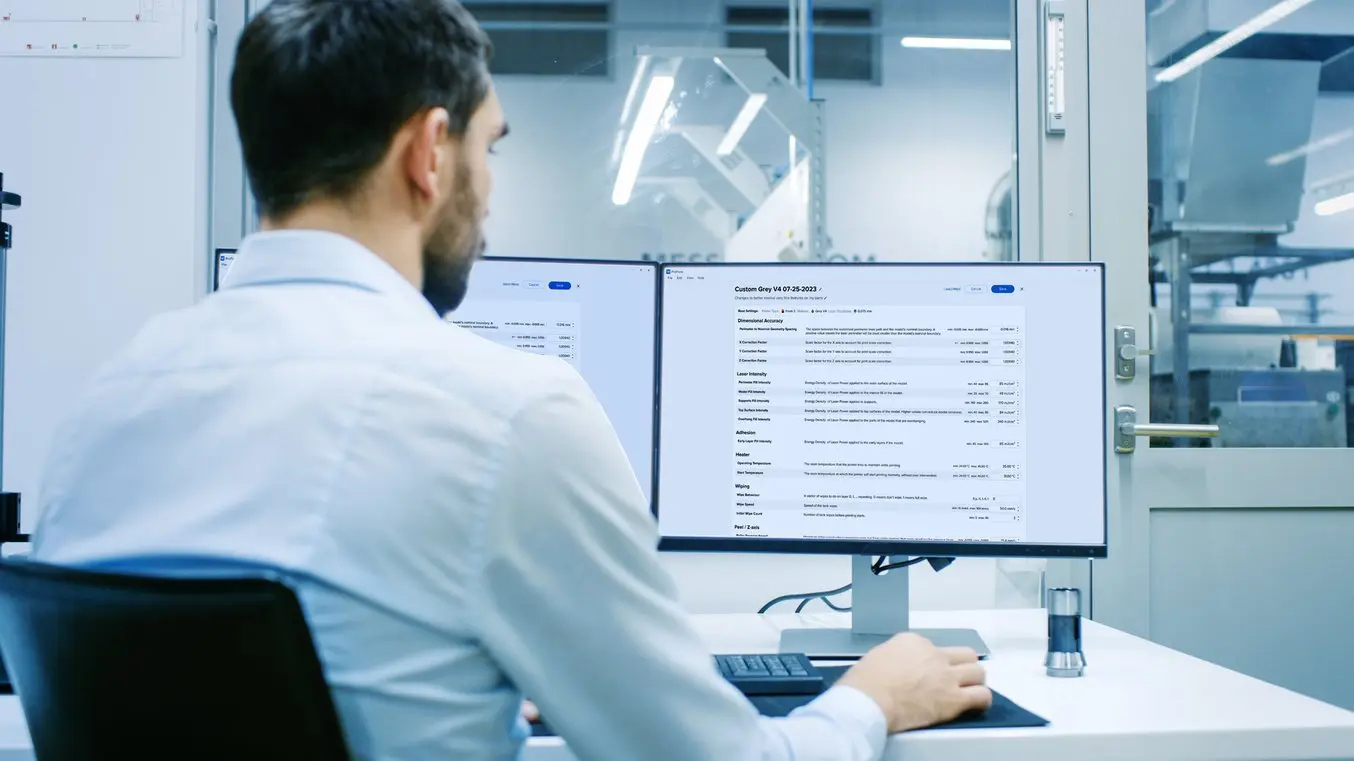
Talk to Our Sales Team
Whether you need to prototype at speed, or are producing end-use parts, we’re here to help. The Formlabs Sales team is composed of dedicated specialists who know exactly how to support you and your company's needs.
While testing was done by an independent third party at their labs, Formlabs defined the tests and procedures that were used during testing, with the goal of standardizing this testing across all printers. This standard operating procedure (SOP) largely consists of printing models from a standard setup and maintaining equivalent processing, with quality checks at each step of the process to eliminate the risk of user error changing results.
Following the SOP, 15 models were each printed three times on five different factory-condition printers from each manufacturer, resulting in 225 prints for each brand of printer, with the success or failure of the prints recorded.
Printers and Materials
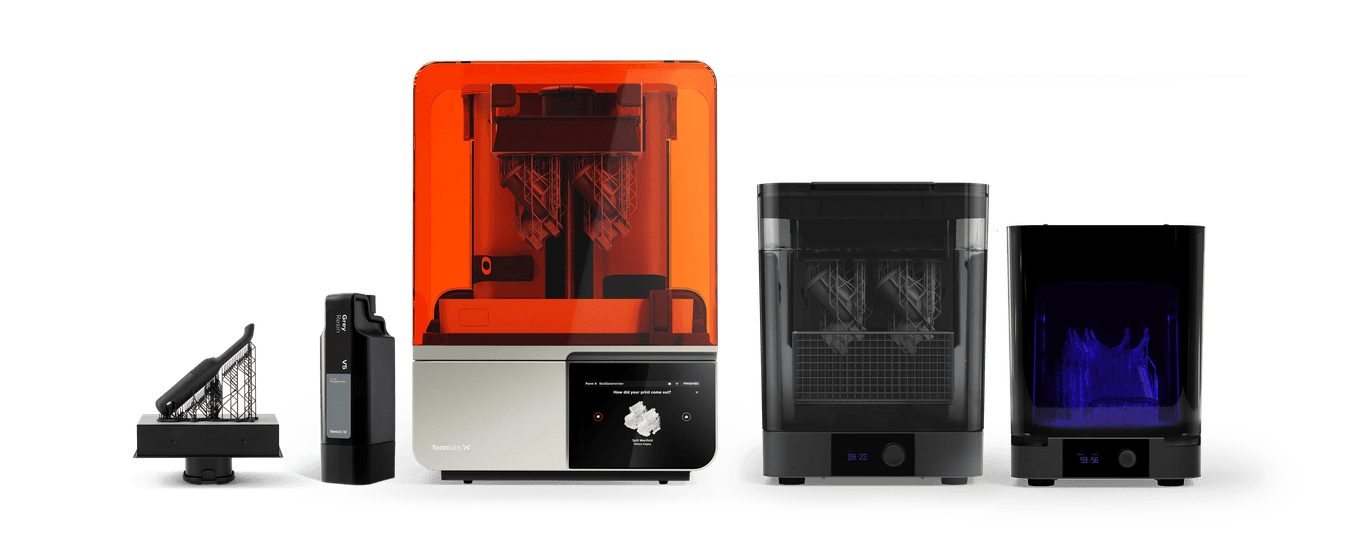
Form 4 ecosystem including Form Wash and Form Cure, as well as the build plate and auto-dispensing resin cartridge. For testing Form 4, Grey Resin V4 was used.
In order to fully understand the different available options, four different types of SLA or resin 3D printers were selected for this testing, all of which function based on vat photopolymerization.
- Formlabs Form 4
- Formlabs Form 3+
- Benchmark A
- Benchmark B
Each printer was used with only the most up-to-date hardware (including resin tank and build platform) and the resin selected for each printer was identified as the standard grey resin produced by the respective brands and advertised for that printer.
3D Models and Slicing
15 different 3D models were selected from a wide range of applications, sizes, and form factors, including engineering and manufacturing applications, biomedical applications, and dental applications. Most models required supports and could not be printed directly to the build plate.
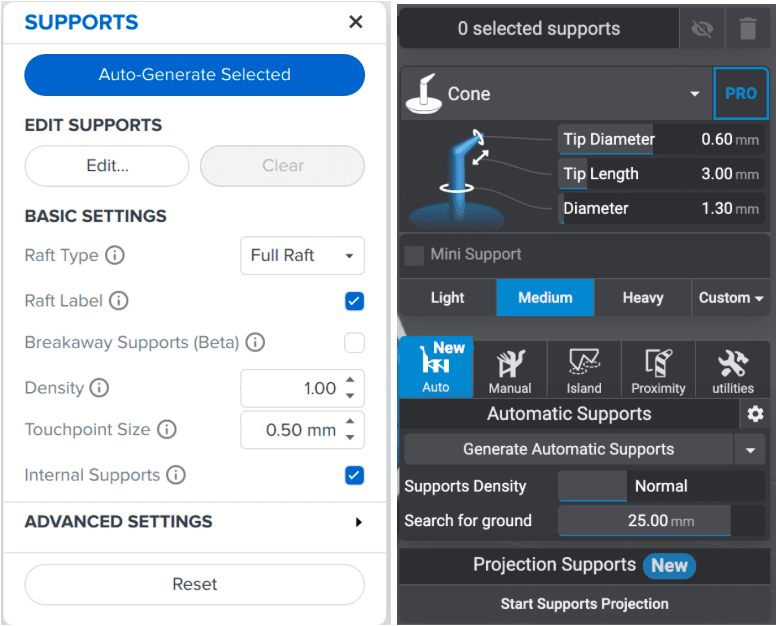
PreForm (left) and Lychee (right) automatic support generation tools on standard settings.
The following was done for print setup:
- Models were oriented via PreForm’s Auto-Orient tool for all printers.
- Support generation and final slicing was done in PreForm for Formlabs printers and Lychee Slicer for both benchmark printers.
- Supports were generated with the auto-generator tool in both slicers.
- Manufacturer-recommended settings were used for each material.
- A layer height of 100 μm was used.
The complete settings for each printer can be found in the appendix of the white paper.
Standard Operating Procedure
An SOP was followed for all four printers, with only small modifications necessary between each type. This includes:
- Weekly inspection of dedicated printer build platform and resin tank .
- For printers without automatic resin dispensing, the resin tank was prefilled with resin to just below the recommended maximum fill height prior to each print .
- Consumables and accessories were checked prior to selecting the print from the queue and starting the print.
- Prints were then allowed to run with no interference unless they output an error.
- Error codes were noted down and then the operators followed the onscreen prompts to either reset and resume the print or fail the print and stop printing as required.
- If prints failed, the tanks were checked for debris and cleaned prior to the next print if necessary.
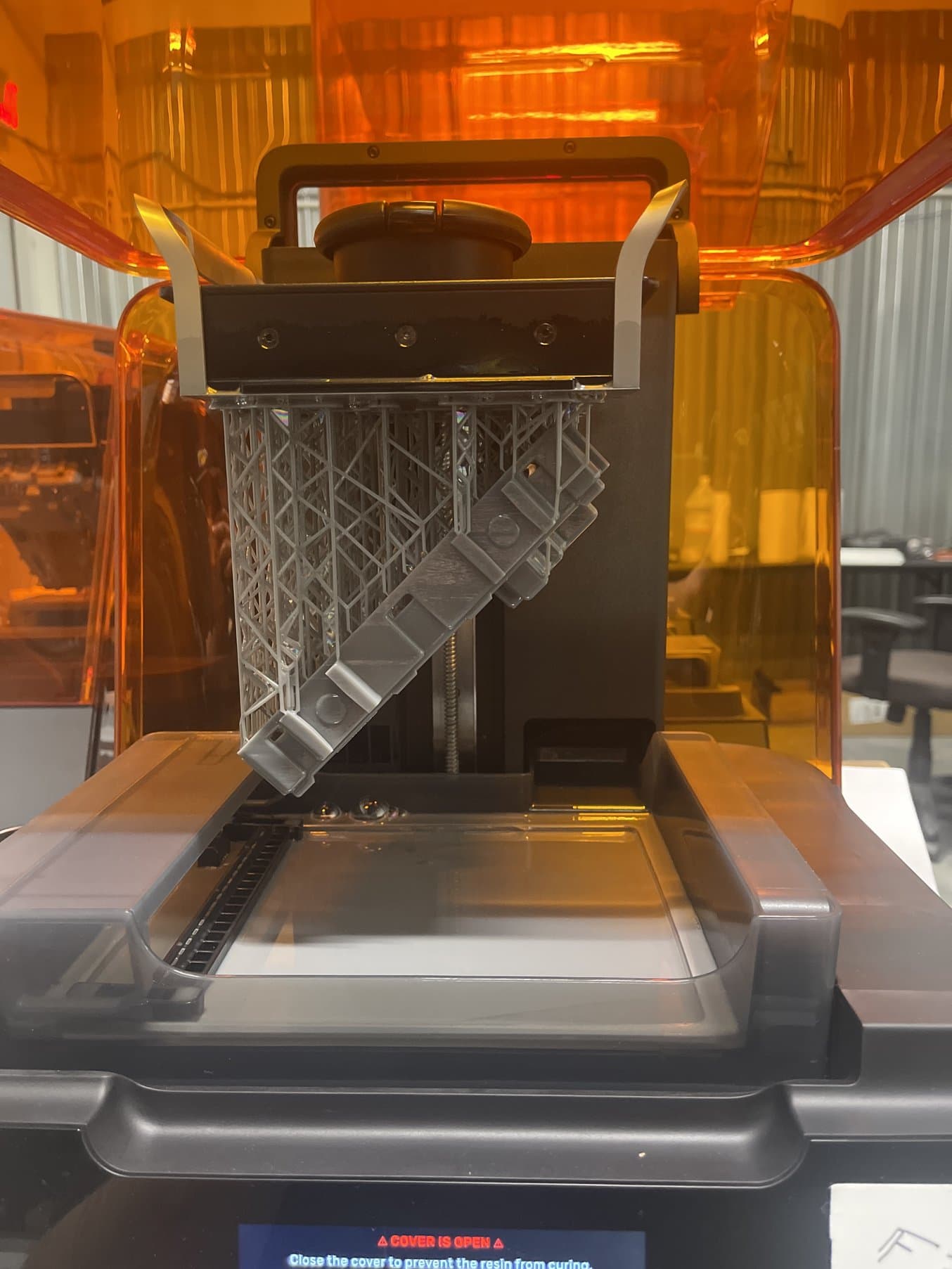
Test part printed on Form 3+ immediately after printing and still on printer.
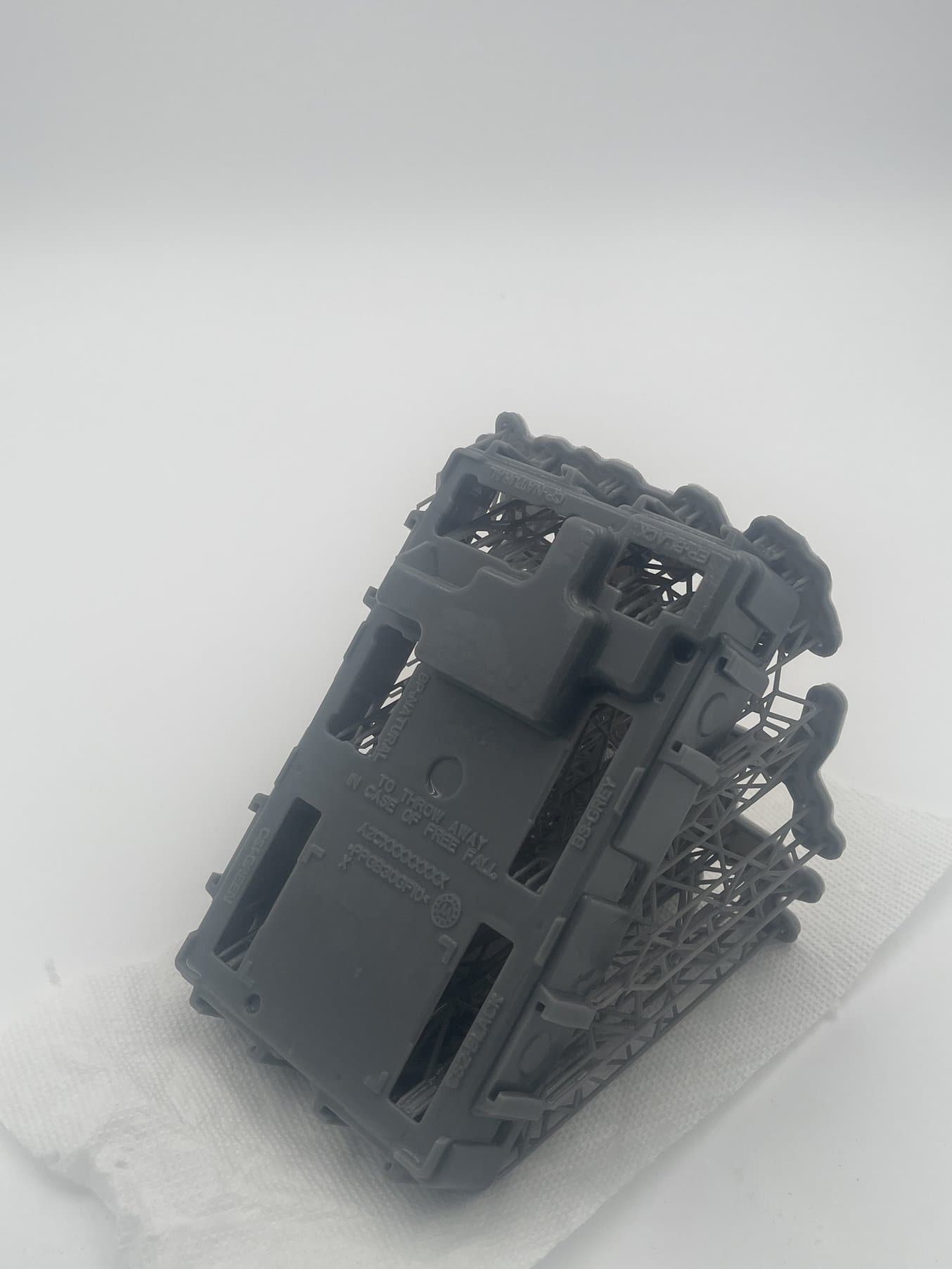
Test part printed on Form 3+ after the first wash with supports still on.
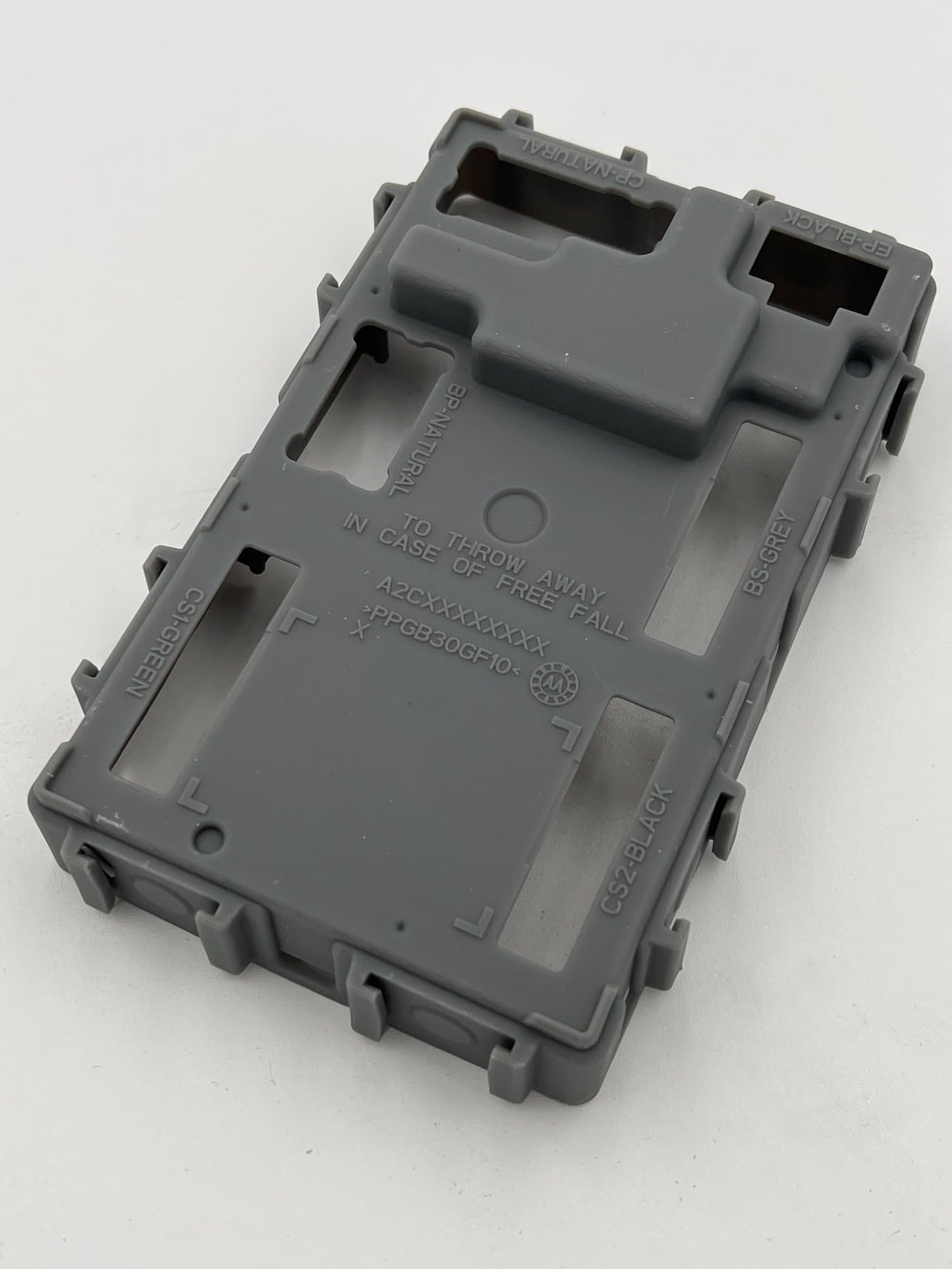
Test part printed on Form 3+ after support removal and cure.
Upon completion of the print, the following actions were taken:
- All prints were immediately photographed on the printer.
- Prints were removed from the build platform, using a scraper as necessary.
- Parts were washed in a Form Wash full of isopropyl alcohol (IPA) for 5 minutes.*
- Parts were photographed with the supports still attached.
- Supports were removed.
- Parts placed in a second IPA wash for 10 minutes.*
- Parts cured in Form Cure according to the manufacturer's instructions.
- A final set of images was taken of the part.
*Two washes were used for each type of printer and washes were cycled with new IPA every 100 washes to prevent the IPA from becoming saturated with resin and losing its efficacy.
After each print, the success/failure of the print was determined, being marked failed if there was a significant issue with printing that would obviously render the part non-functional. Examples of failure include non-adherence to the build platform, delamination, excessive warping, and undeveloped features. Minor blemishes, such as pinstriping or heavy support residue, were considered successful prints.
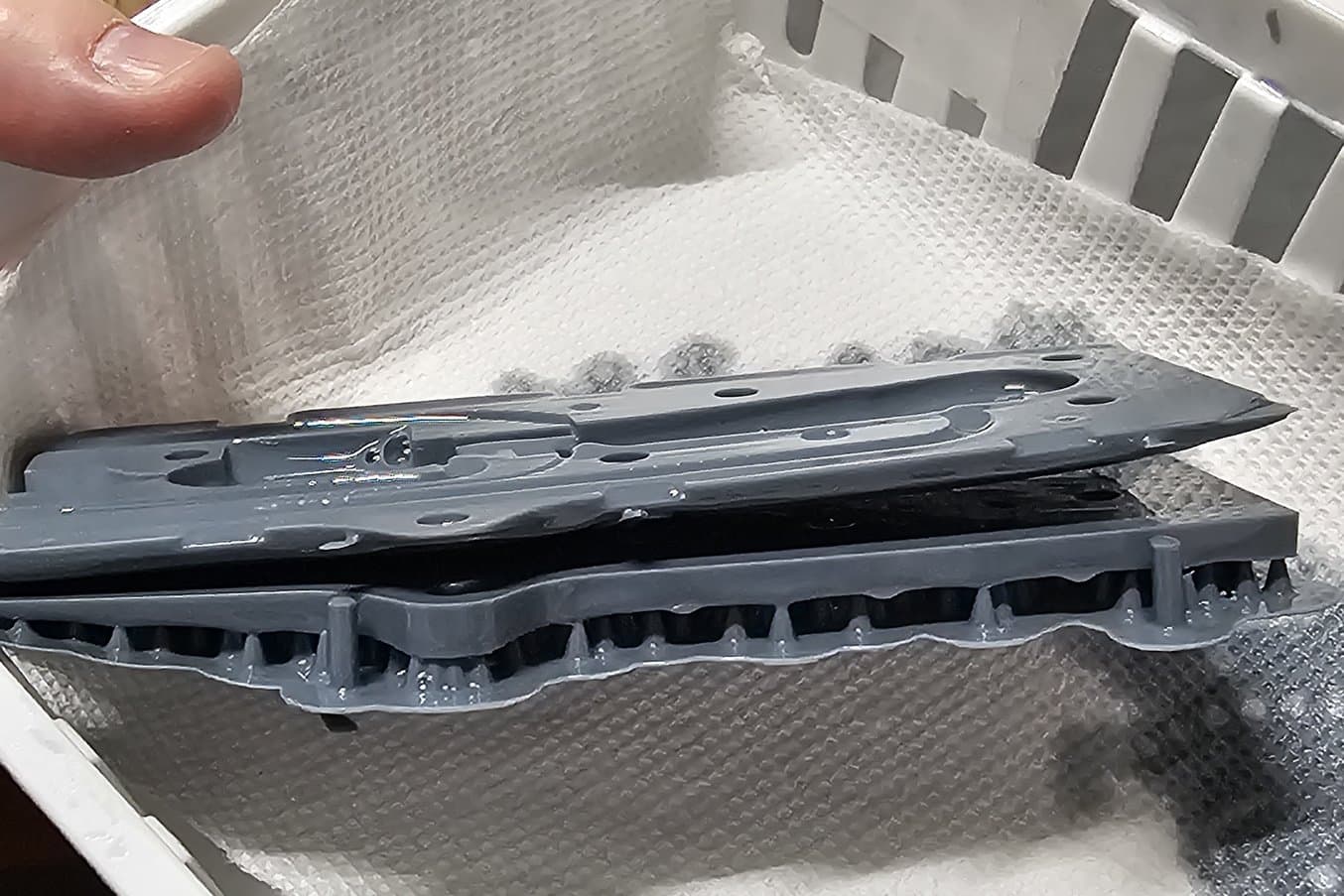
An example of a failed print due to warping.
Reliability Test Results
Print Successes and Failures
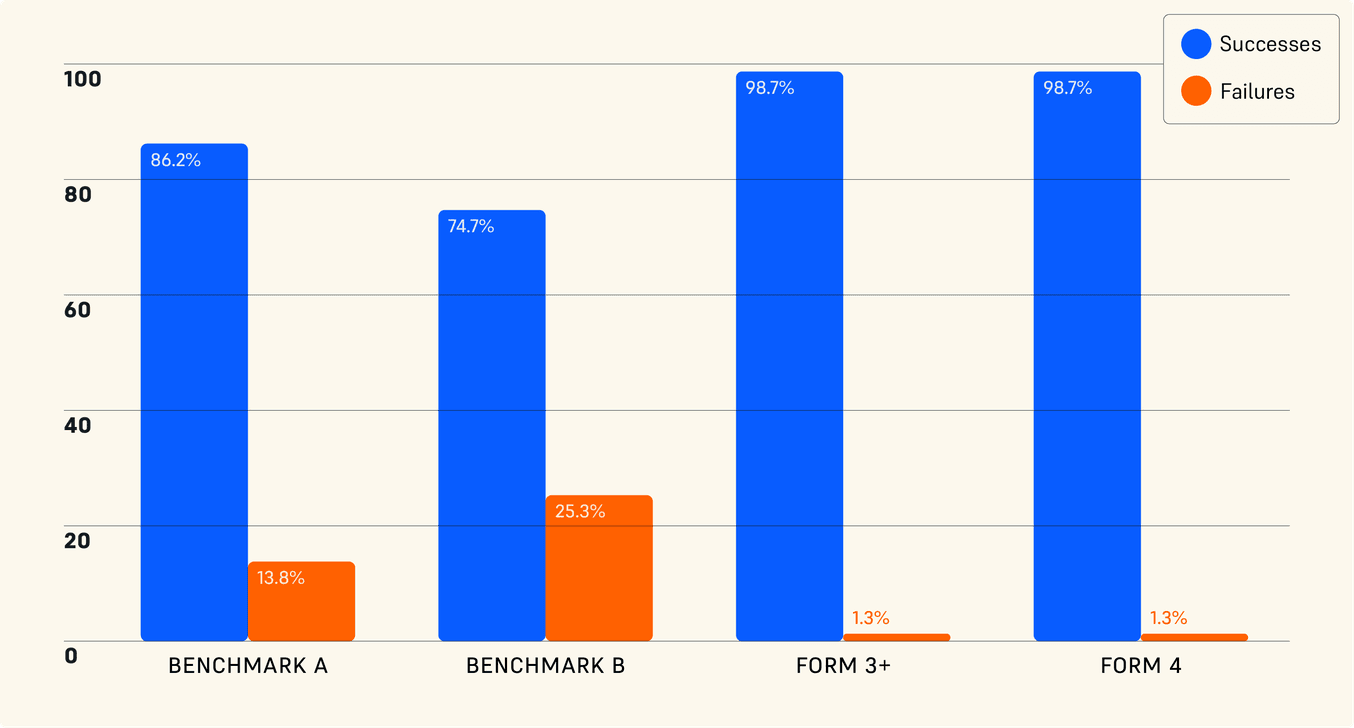
Formlabs’ Form 4 and Form 3+ each had failure rates of 1.3%, while Benchmark A had a failure rate of 13.8%, and Benchmark B performed the worst at a failure rate of 25.3%. These failure rates often directly factor into part cost, failure mode and effects analysis (FMEA), and many other important criteria. A model-by-model breakdown of failures can be found in the white paper.
Print Failure Rates
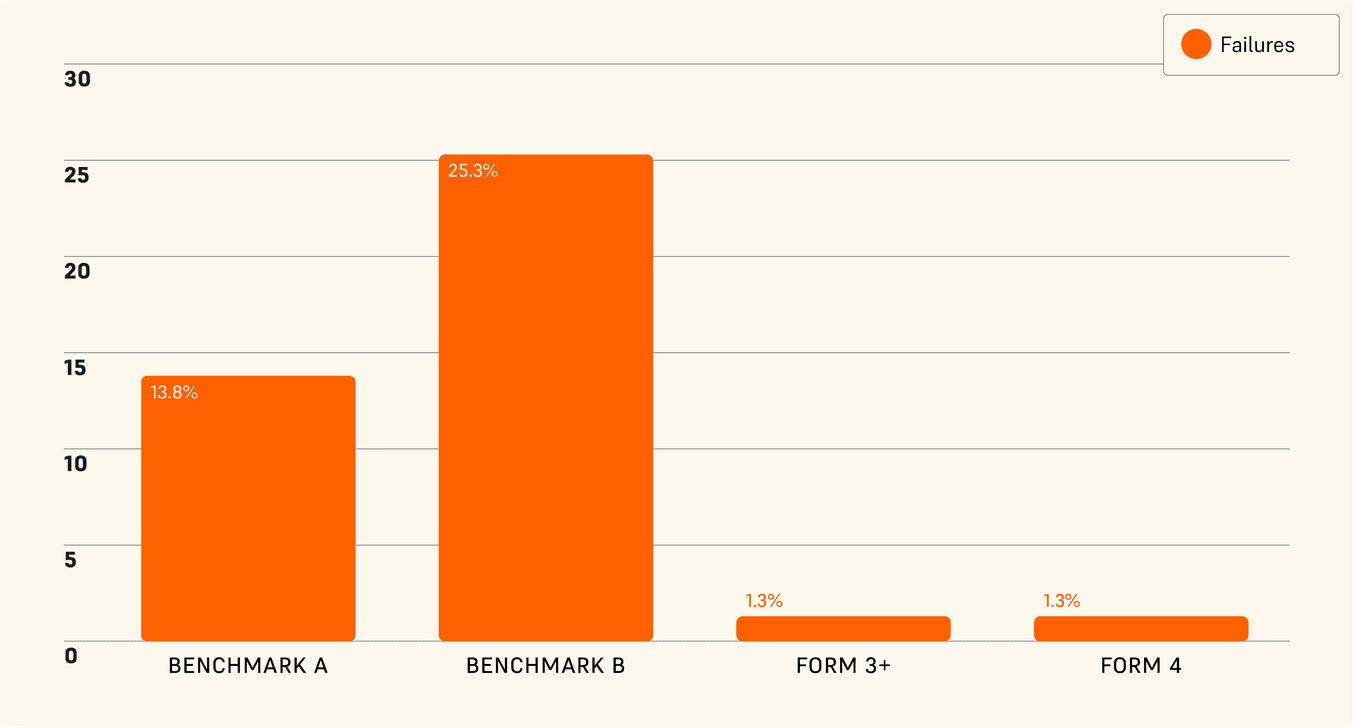
Form 4 was measured to have a 98.7% print success rate, which is equal to that of Form 3+, a printer that has been continuously optimized for five years to improve its performance in the field. The benchmark printers, A and B, measure 86.2% and 74.7% print success rates respectively, or equivalently 13.8% and 25.3% failure rates (versus 1.3% for Form 4). This shows that the benchmark printers have 10x-20x the failure rate of Form 4, with benchmark B failing one out of every four prints.
These results were all obtained in a laboratory with optimal conditions, and with prints that had been validated to print successfully on all four of the tested printers. It's important to note that conditions outside of the lab with user-generated models will typically be lower across the board. For example, the field print success rate of Form 4 at the time of writing (measured by Formlabs) was 94%.
These results exclude the fact that two of the printers from benchmark B arrived dead and had to be replaced in order to commence testing. In business settings this would result in losing several working days plus hours of labor troubleshooting problems, cleaning failed prints, and resetting the printer to reattempt the print.
There are many factors that contribute to the reliability of a printer. At Formlabs, this includes:
- Hardware: engineered for lower peel forces, consistent environment, temperature, automated diagnostics and monitoring
- Materials: high-performance materials, validated print settings
- Software: optimized print setup with automatic alerts
- Validation and testing on each new printer prototype
Printer | Form 4 | Form 3+ | Benchmark A | Benchmark B |
---|---|---|---|---|
Dead on Arrival | 0 | 0 | 0 | 2 |
Target Number of Prints | 225 | 225 | 225 | 225 |
Completed Prints | 225 | 225 | 225 | 216 |
Failed Prints | 3 | 3 | 31 | 55 |
Failure Rate | 1.3% | 1.3% | 13.8% | 25.3% |
Launch Year | 2024 | 2019 | 2023 | 2022 |
Build Volume | 7.9 x 4.9 x 8.3 in | 5.7 x 5.7 x 7.6 in | 7.8 x 4.7 x 8.6 in | 8.6 x 4.8 x 9.3 in |
Cost at Time of Testing | $4,500 | $2,500 | $450 | $650 |
Technology | MSLA | Laser SLA | MSLA | MSLA |
Failure Modes | Missing chunks (x2) Print stopped (x1) | Missing chunks (x2) Warping (x1) | Non-adherence (x13) Delamination (x7) Missing chunks (x6) Cracking (x5) | Non-adherence (x31) Cracking (x10) Missing chunks (x6) Delamination (x5) LCD failure (x3) |
Non-Print Issues | Outdated firmware (x1) | None | Required film replacement (x5) | Homing failure (x7) LED module failure (x1) LCD failure (x2) |
Lost Hours Printing Due to Failures | 9 | 17 | >100 | >250 |
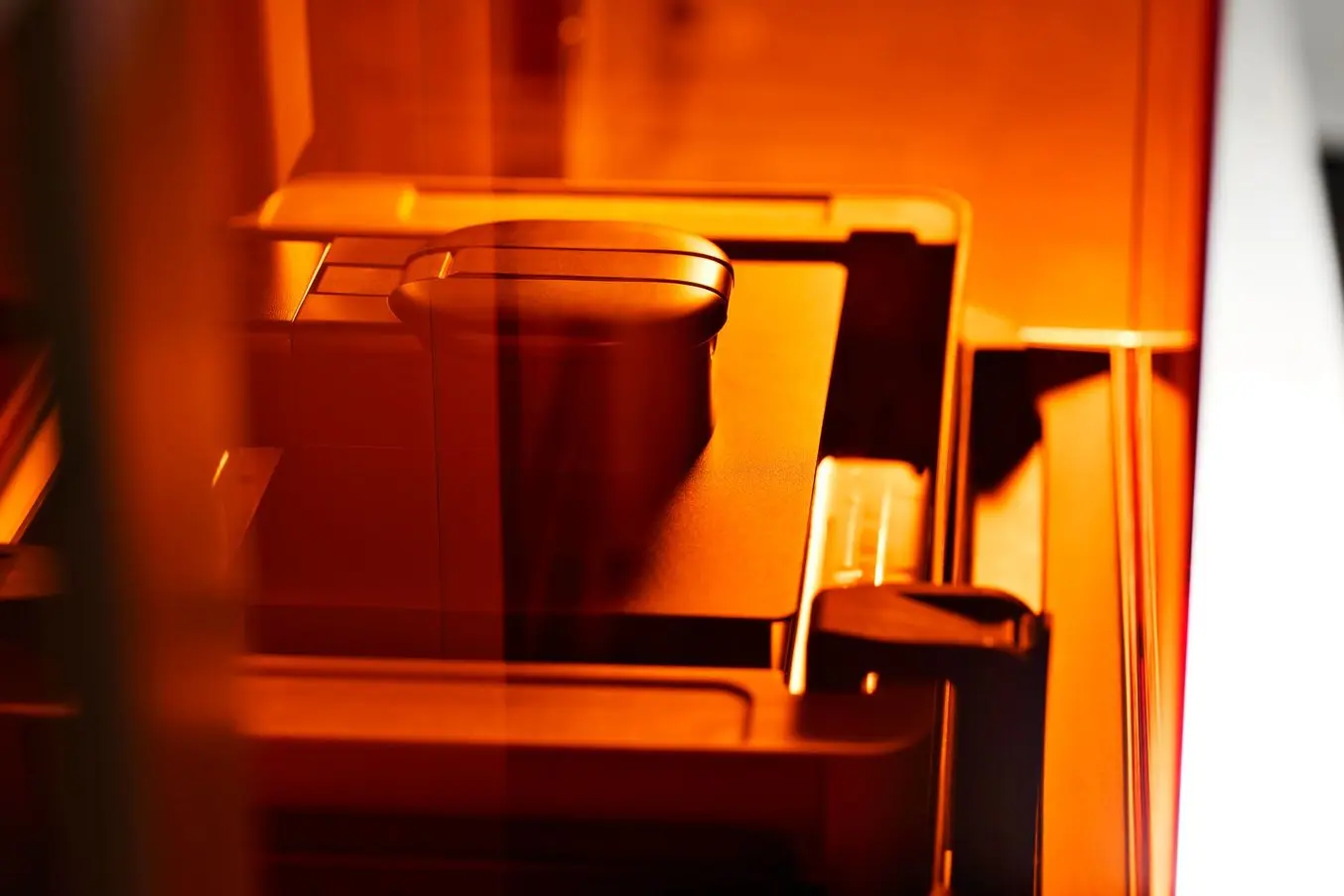
Product Demo: Form 4
See how Form 4 can enable new levels of productivity and innovation through its unmatched speed, accuracy, and reliability.
Print Reliably With Formlabs Form 4
Over the last decade, 3D printing has become a go-to tool for many professionals, meaning the need for reliable printers is higher than ever, as is the need for performance data from unbiased third parties so that professionals have the information needed to make informed business decisions.
For hobbyist and non-demanding applications, low-cost resin 3D printers may be a cost-effective choice. But for professionals who require parts to be printed reliably, accurately, and without manual labor overhead, reliability matters, and Form 4 can save in resin and consumables, time, and labor, as well as headaches and missed deadlines.
Download the white paper to read the complete testing parameters and results. Explore Form 4 to start printing or contact sales to learn more.