Form 4 is fast, but your workflow can be even faster — introducing Form Cure (2nd Generation), offering blazing fast curing and nearly instant heat up time. Save 2x-8.6x in cure time over Form Cure (1st Generation) in a bigger cure that can fit any part printed on Form 4.
“The new cure unit has been a game changer for us, the overall team is really happy with it — it really cuts down on the curing time.”
Yash Khambayat, Mechanical Engineer, Cirkul
In addition to the release of Form Cure (2nd Generation) comes an update to Tough 1500 Resin. Tough 1500 Resin V2 has improved fracture toughness and thin wall impact resistance so that its performance now rivals the properties of extruded polypropylene. Other updates to Dashboard and PreForm software make your workflows faster and more efficient — explore those updates here.
Blazing Fast Curing With Form Cure (2nd Generation)
“We need to cure 600 parts per day. If we do this with our old Cure, we need more Cures to cure all those parts, meaning more time for us and more hours we need to pay, so the Cure (2nd Generation) process is better for us — cheaper and more efficient.”
Matthias Krabel, Managing Director, MAKRA PRO
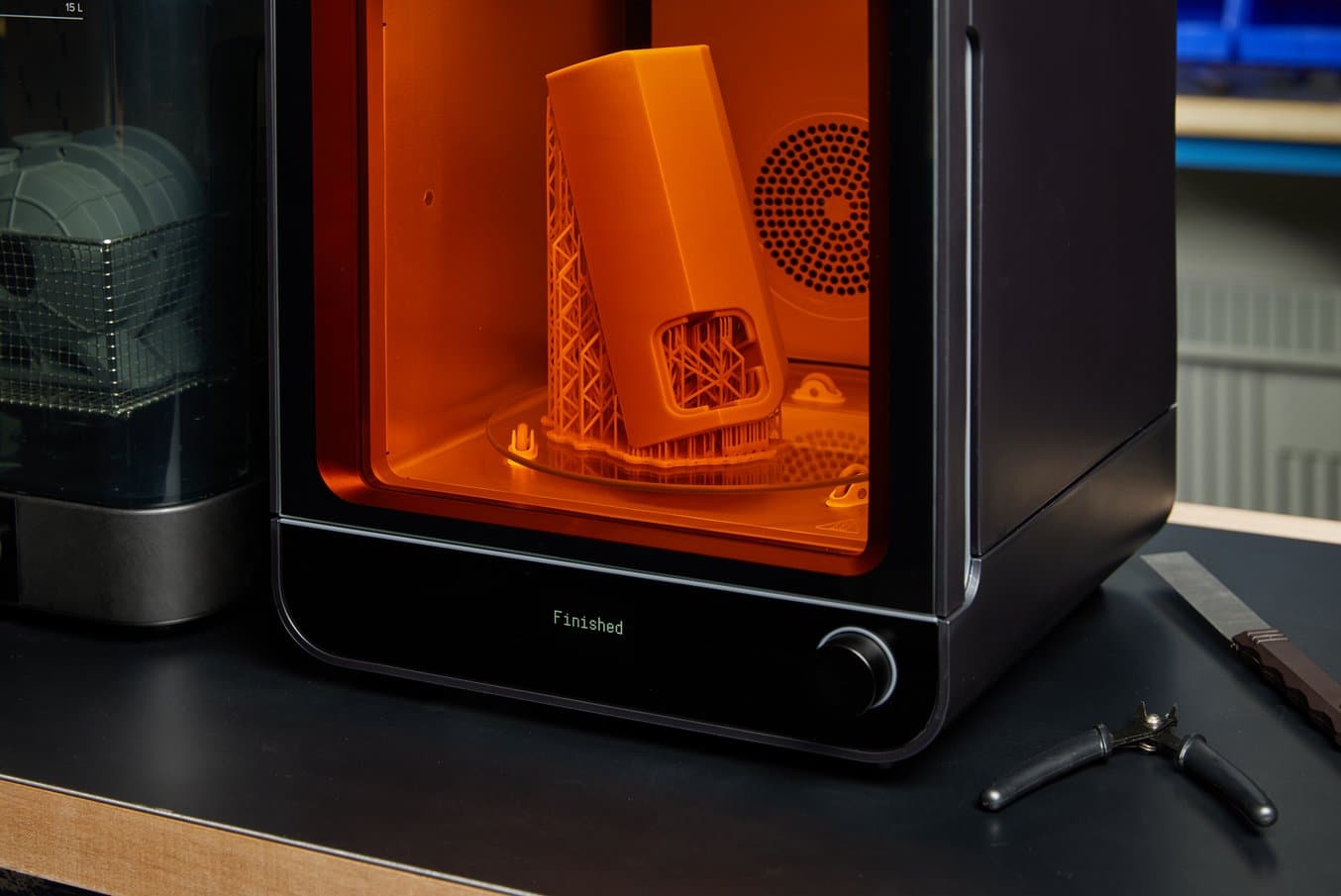
Form Cure (2nd Generation) appears orange when it is not actively curing.
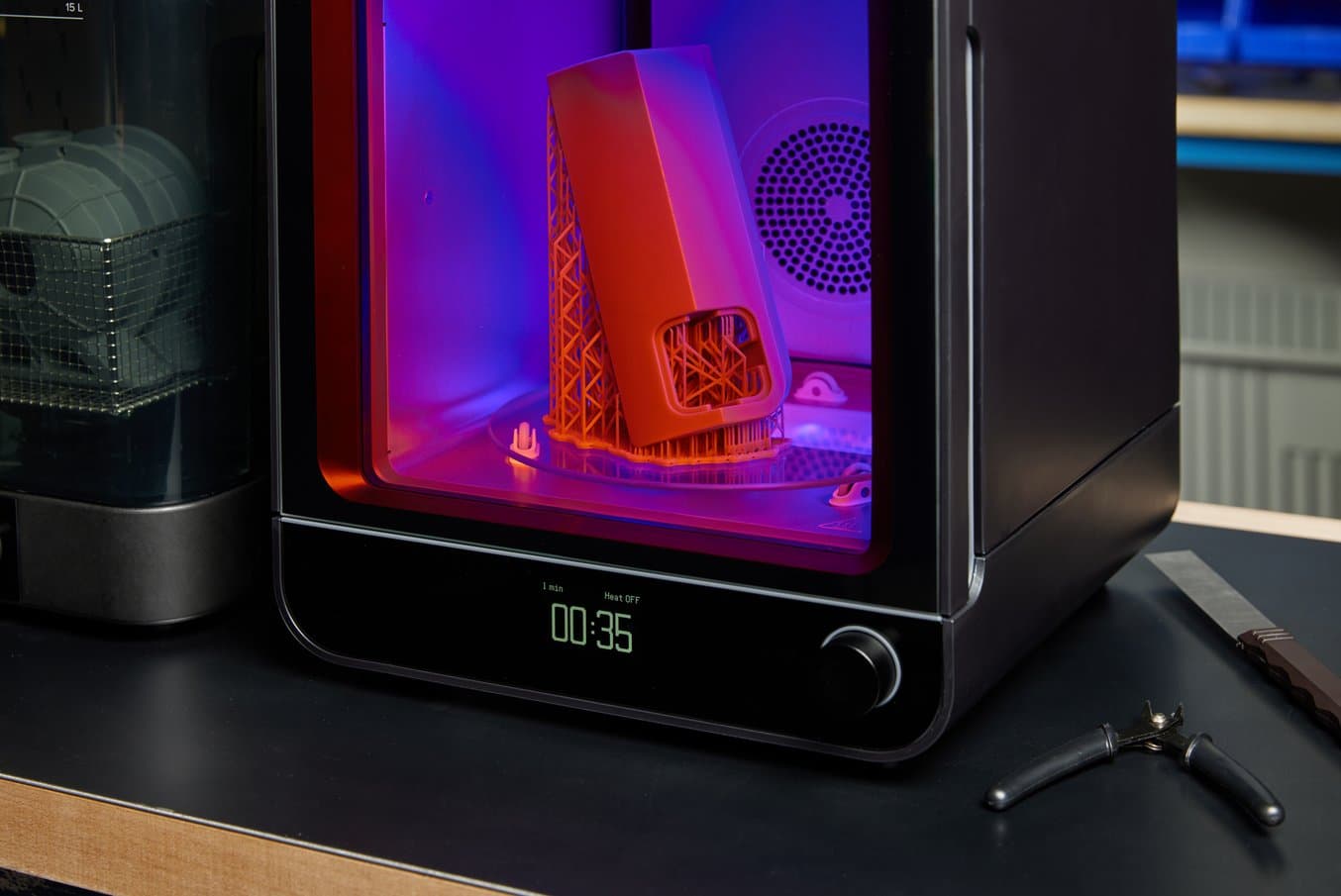
When Form Cure (2nd Generation) is in use, the window appears purple, so you can see, at a glance, that it’s curing.
Form Cure (2nd Generation) offers blazing fast curing — general purpose resins in just 60 seconds or engineering resins in less than 15 minutes — saving 2x-8.6x the time versus curing with Form Cure (1st Generation). Plus, Form Cure (2nd Generation) heats to 60 °C in just 60 seconds*, saving valuable workflow time.
*Based on the 230 V version. The 120 V version will heat to 60 °C in 80 seconds.
Form Cure (1st Generation) | Form Cure (2nd Generation) | Times faster | |
---|---|---|---|
Grey Resin V5 | 5 min | 1 min | 5x |
BioMed Amber Resin | 30 min | 5 min | 6x |
Tough 2000 Resin | 60 min | 7 min | 8.6x |
High Temp Resin | 120 min | 15 min | 8x |
Form Cure (2nd Generation) delivers consistent results for Formlabs resins with pre-programmed and validated cure settings. Simply select the resin and start the cycle. For curing third-party materials printed with Open Material Mode (OMM), it’s possible to save custom profiles for the resins you regularly print, or set the time via the dial.
The new Form Cure (2nd Generation) design features a 48-LED array and convective heating system to ensure uniform UV and heat exposure, delivering 14.5 mW/cm² irradiance and a maximum temperature of 100 °C. The larger size is designed to fit any part printed on Form 4, while a side-hinged door allows easy access within a compact footprint. The 235 mm turntable inside is glass, for easy cleaning.
Form Cure (1st Generation) | Form Cure (2nd Generation) | |
---|---|---|
Maximum Part Height | 185 mm | 245 mm |
Turntable Diameter | 193 mm (7.6 in) | 235 mm (9.25 in) |
Maximum Cure Chamber Temperature | 80 °C | 100 °C |
“Pairing the new cure with Form 4, we can do so much more with fewer units. The speed that we can do things now changes the way that we are handling projects."
Robert Mackowiak, Associate Rapid Prototyping Engineer, Hasbro
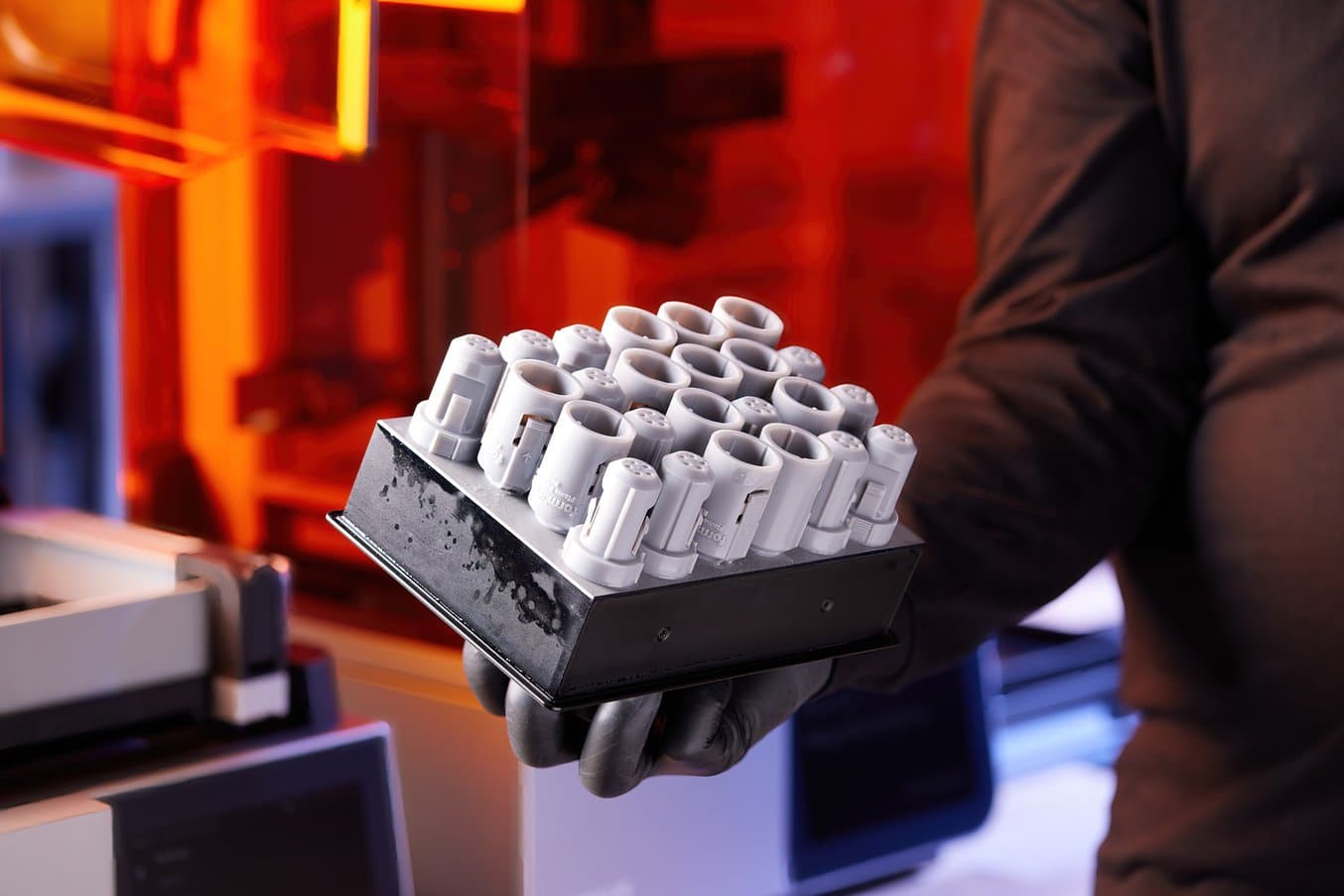
Producing these electrical connectors in Flame Retardant Resin takes almost a sixth of the time using Form 4 and Form Cure (2nd Generation) versus Form 3+ and Form Cure (1st Generation). Compared to Form 4 and Form Cure (1st Generation), upgrading to Form Cure (2nd Generation) cuts the time to part by close to 50%.
Time to manufacture electrical connectors at 100 μm layer height
Print time | Wash time | Post-curing time | Total | |
---|---|---|---|---|
Form 4 & Form Cure (2nd Generation) | 1 h 28 min | 10 min | 15 min | 1 h 53 min |
Form 4 & Form Cure (1st Generation) | 1 h 28 min | 10 min | 2 h | 3 h 38 min |
Form 3+ & Form Cure (2nd Generation) | 9 h 43 min | 10 min | 15 min | 10 h 8 min |
Form 3+ & Form Cure (1st Generation) | 9 h 43 min | 10 min | 2 h | 11 h 53 min |
Additional settings are available for tough and durable resins. These resins are more susceptible to warping during post-curing, particularly for certain geometries. The optional “low warp” setting for Tough 1500 Resin V1.1 and Tough 2000 Resin cures without heat, reducing the chance of warping. However, curing without heat will lower the mechanical properties that can be achieved. To compare the mechanical properties of each cure setting, refer to the technical data sheet (TDS) for each material.
Form Cure (2nd Generation) is compatible with Form 4/B, Form 3/B/+, and Form 2 and replaces both Form Cure and Fast Cure in our ecosystem.
Now Even Tougher: Tough 1500 Resin V2 Rivals Polypropylene
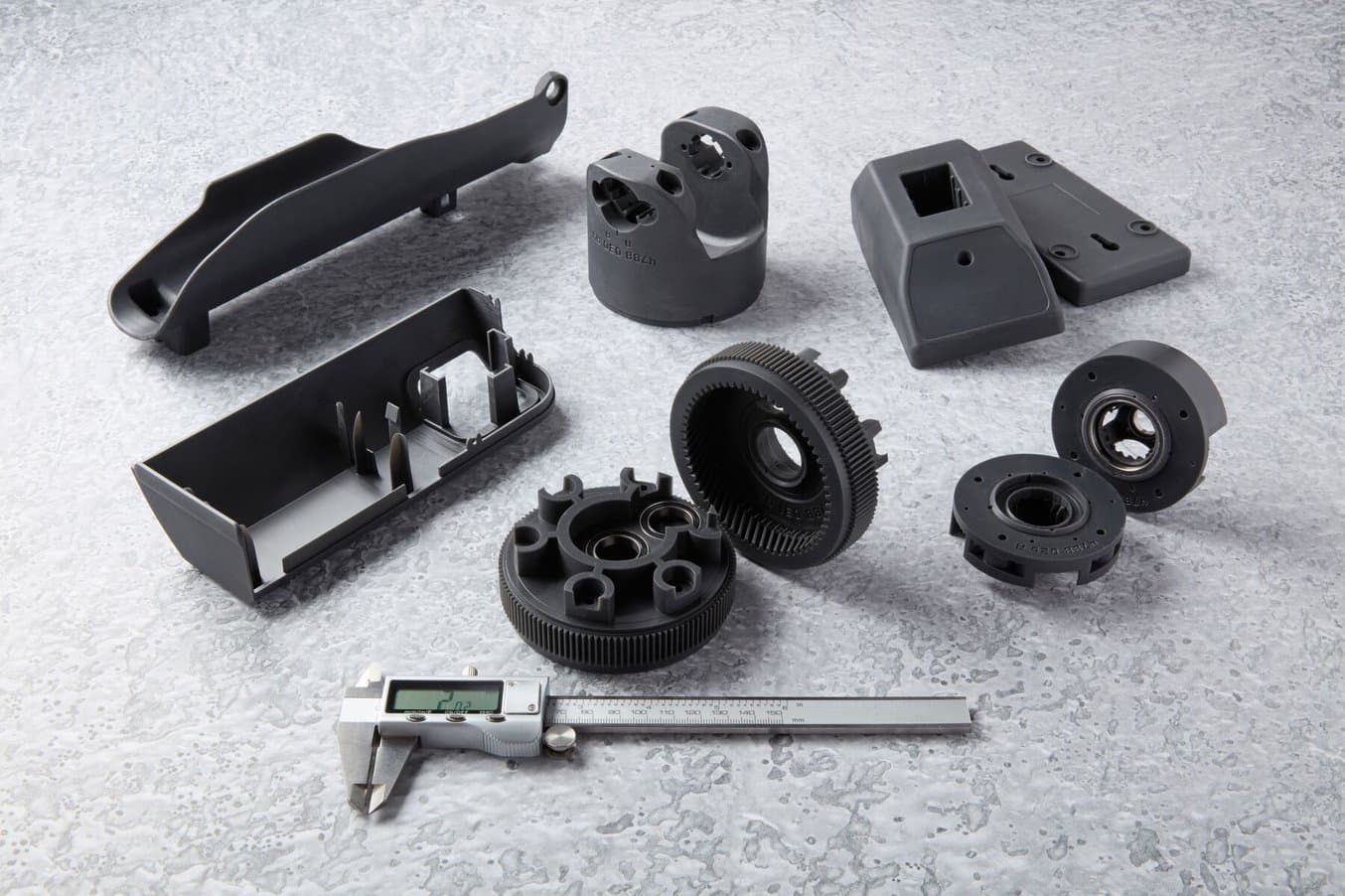
Tough 1500 Resin V2 has improved fracture toughness and thin wall impact resistance so that its performance now rivals the properties of extruded polypropylene.
Mechanical properties matter — whether you're prototyping or printing end-use parts, they need to meet your exacting standards. With Tough 1500 Resin V2, our materials engineers have improved fracture toughness and thin wall impact performance so that Tough 1500 Resin V2 now rivals the mechanical properties of polypropylene.
"This material reminds me of polypropylene; it just feels more like real plastic. I bent it about 30 degrees and it went right back to flat. And it printed very, very accurately, much better than the prior version."
John Nolte, Owner, Nolte Research and Design
Tough 1500 Resin is a resilient material for stiff but pliable parts that bend and spring back quickly, prototypes that repeatedly bend and quickly return to shape, jigs and fixtures requiring repeated deflection, and consumer goods.
The new material has a 10x higher work of fracture, so parts hold up to drilling, tapping, or cracking, and a 3x higher Gardner impact strength for thin walls that don’t shatter. Additionally, extremely high elongation at break and Ross flex fatigue means you can make ductile and resilient long-lasting compliant parts with features like snap fits and living hinges.
Material Property | Description | Tough 1500 Resin V2 | Tough 1500 Resin V1.1 | Loctite IND405 Resin | Polypropylene (extrusion grade) |
---|---|---|---|---|---|
Tensile Modulus | Stiffness | 1460 MPa | 1560 MPa | 1292 MPa | 1600 MPa |
Ultimate Tensile Strength | Strength | 34 MPa | 33.6 MPa | 38.3 MPa | 29.2 MPa |
Elongation at Break | Ductility | 155% | 63% | 119% | 125% |
Notched Izod | Toughness in impact on thick parts | 42 J/m | 62 J/m | 42 J/m | 36 J/m |
Work of Fracture (Wf) | Toughness to crack propagation at lower strain rates | 1011 J/m | 102 J/m | 407 J/m | ~2000 J/m |
Gardner at 1/32” | Toughness in impact on thin sheets | 5.9 J | 2.5 J | 3.4 J | 2.7 J |
Heat Deflection Temperature @ 0.45 MPa | Heat resistance | 66 °C | 49 °C | 53 °C | 85-100 °C |
Heat Deflection Temperature @ 1.8 MPa | Heat resistance | 53 °C | 42 °C | 44 °C | N/A |
Extensive testing was done on Tough 1500 Resin V2. Results include the highest temperature and UV resistance of any high-compliance stereolithography (SLA) material. To explore all the information needed to pursue demanding applications with confidence, explore the complete results in the Tough 1500 Resin V2 technical data sheet (TDS) or request a free sample part to evaluate the material for yourself.
Improving Speed, Throughput, and Part Performance
From print setup through post-curing, hardware to materials, we’re constantly optimizing workflow efficiency, ease of use, and increasing time-savings so you can focus on what you do best.
Form Cure (2nd Generation) saves valuable time and enables increased throughput with a larger capacity while additions and updates to the Formlabs material library make it easier for you to build high-performance prototypes and end-use parts.
Speed up your curing with Form Cure (2nd Generation), start printing stiff but pliable parts with Tough 1500 Resin V2, or contact sales to discuss your unique business goals.