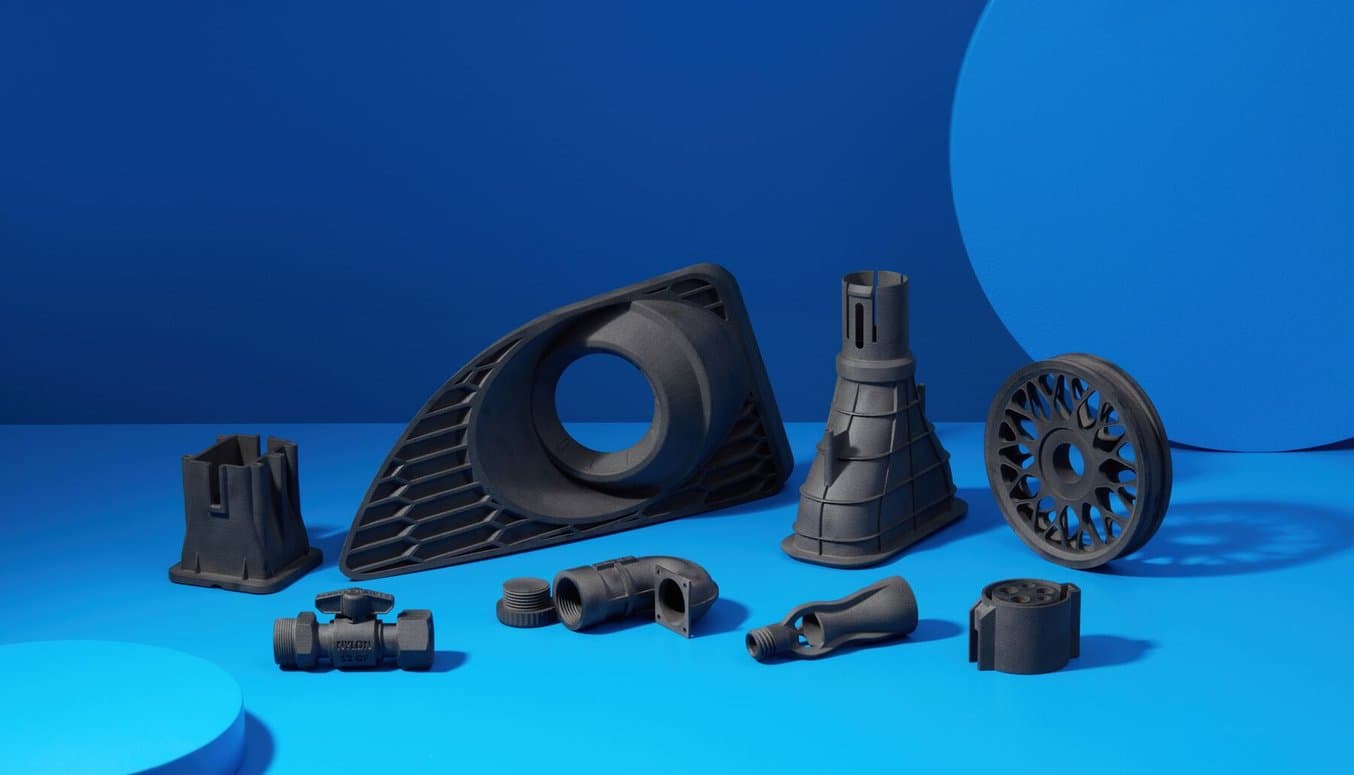
The Fuse 1 materials library is expanding, enabling engineers and manufacturers to create new, industrial grade products. Formlabs is introducing Nylon 12 GF Powder, a glass-reinforced plastic powder ideal for producing stiff, thermally stable parts on the Fuse 1 SLS printer.
Nylon 12 GF Powder is the third material designed specifically for the Fuse 1 ecosystem, providing Formlabs customers with options to scale in-house production affordably. The new material joins Nylon 12 Powder and Nylon 11 Powder in the Formlabs SLS materials library, enabling customers to diversify their operations and scale production with varied material properties.
This new material combines the utility of Nylon 12 with the rigidity and heat resistance of glass filler, making it the go-to material of choice for any application requiring sustained load-bearing ability and elevated thermal resistance. Fuse 1 users can now add Nylon 12 GF Powder to their catalog if they need stiff, functional prototypes, robust jigs and fixtures, replacement parts, and parts with threads or sockets.
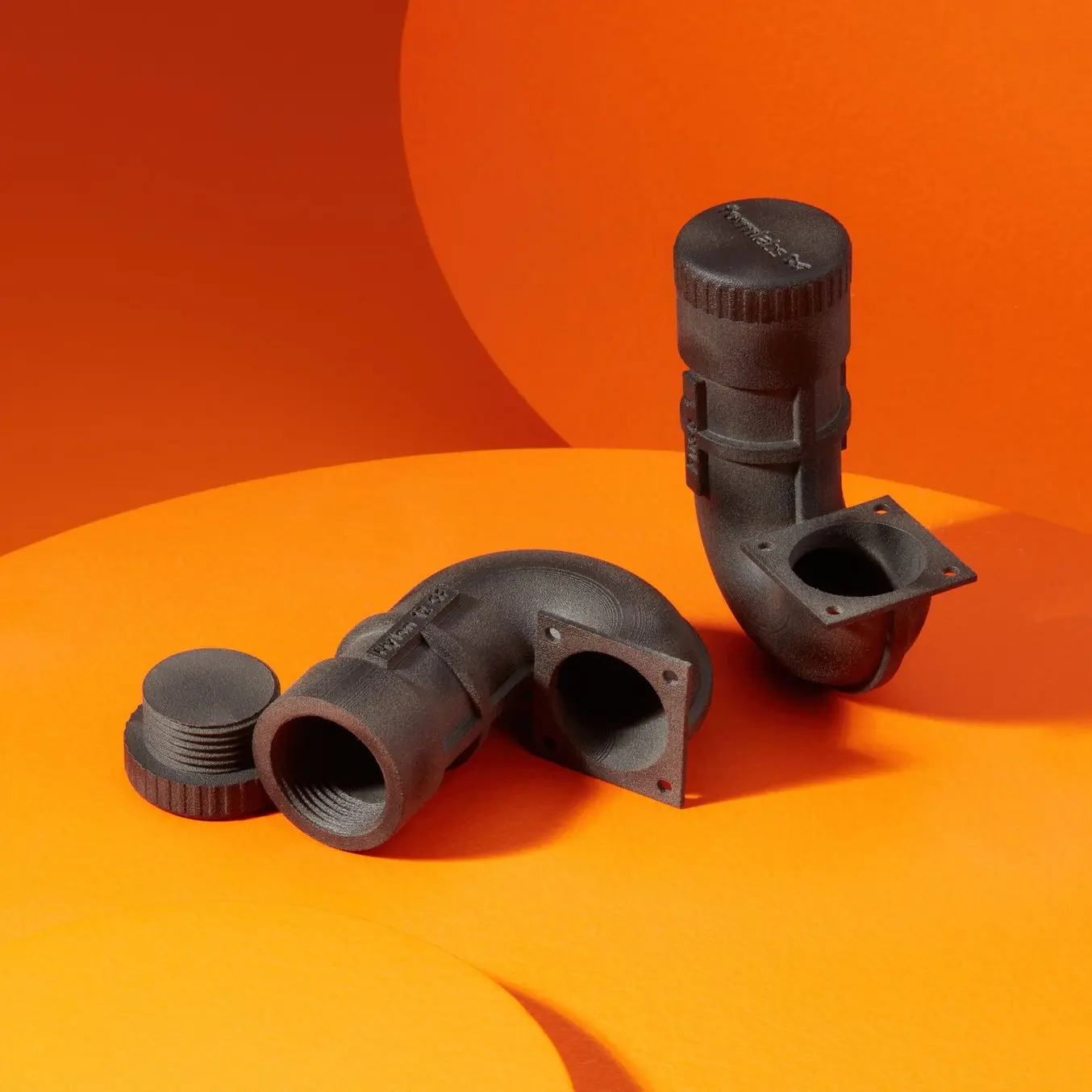
Introducing Nylon 12 GF Powder
Learn how to produce stiff and thermally stable functional parts in-house with our new glass-filled nylon SLS powder.
Glass-Filled Nylon 12 Applications
In the automotive industry, brackets are made to hold heavy car body models at an angle while they’re painted or additional components are affixed to them. If the type of model of car changes, the brackets often need to be switched out, meaning that low volume, custom sized brackets are always in demand, but expensive and slow to make. Because so many automotive parts are metal, a great deal of welding happens during the assembly process, and all manufacturing aids are subjected to high heat environments. Printing end-use brackets in Nylon 12 GF Powder is the low-cost, quick, and low-waste solution.
The tensile modulus of Nylon 12 GF Powder also makes it a good option for electronics casings and housings that need to be stiff and mountable. For a company like KUHMUTE, who designs and manufactures charging stations for electronic transport vehicles (scooters, mopeds, and e-skateboards), being able to produce directly mountable battery charging enclosures enables further design freedom. Because Nylon 12 GF Powder can be used for mountable parts, they can create in the entire enclosure in one material, without worrying about adding a mounting bracket in a different material or geometry.
Manufacturing parts, especially in design and jewelry, can require special tooling and fixtures to hold them in place while working on them, often in high-temperature environments. Those fixtures are often machined out of wood or metal and are expensive and time-consuming to create. Custom pieces or one-offs, therefore, are incredibly costly to the manufacturer. Producing thermally stable custom fixtures in-house allows manufacturers and designers to streamline their processes, improve efficiency and part quality.
Industry | Application | Part Type | ||
---|---|---|---|---|
Automotive and Aerospace | Parts under load in high temperature environments | Vents, valves, carburetors | ||
Manufacturing | Stiff, load-bearing jigs and fixtures | Brackets for holding products stable while on assembly line | ||
Healthcare | Strong, stiff, stable medical devices and replacement parts | Customizable end-user medical device components |
High-Performance Versatile Materials
Each material made for the Fuse 1 system is designed to help engineers and product designers solve specific problems. Let’s compare Nylon 12 GF Powder to the other materials in the Fuse 1 ecosystem.
Nylon 12 GF Powder has the highest modulus and heat deflection temperature of our nylon powders, making it the most suitable for long term stable parts that will have to withstand sustained load at elevated temperatures.
Nylon 12 GF Powder’s tensile modulus is more than 50% higher than that of Nylon 12 Powder, and almost 75% higher than Nylon 11 Powder. Customers should choose Nylon 12 GF Powder when printing parts that need to bear heavy loads for a long time without any bending or elongation. Stiff, static jigs and fixtures, brackets, mounts, and casings are all product types that would benefit from the strong, rigid mechanical properties of this new powder.
Nylon 12 GF Powder also withstands elevated temperatures, with a heat deflection temperature (HDT @ 1.8 MPa) of 113 °C. Many materials can deform when exposed to high heat, and lose their dimensional accuracy, especially when the heat is combined with a load-bearing application. Nylon 12 GF Powder has the necessary thermal stability to withstand many applications where other SLS powders would show signs of elongation and deformation.
Economical Refresh Rate and Simplified Material Changeover
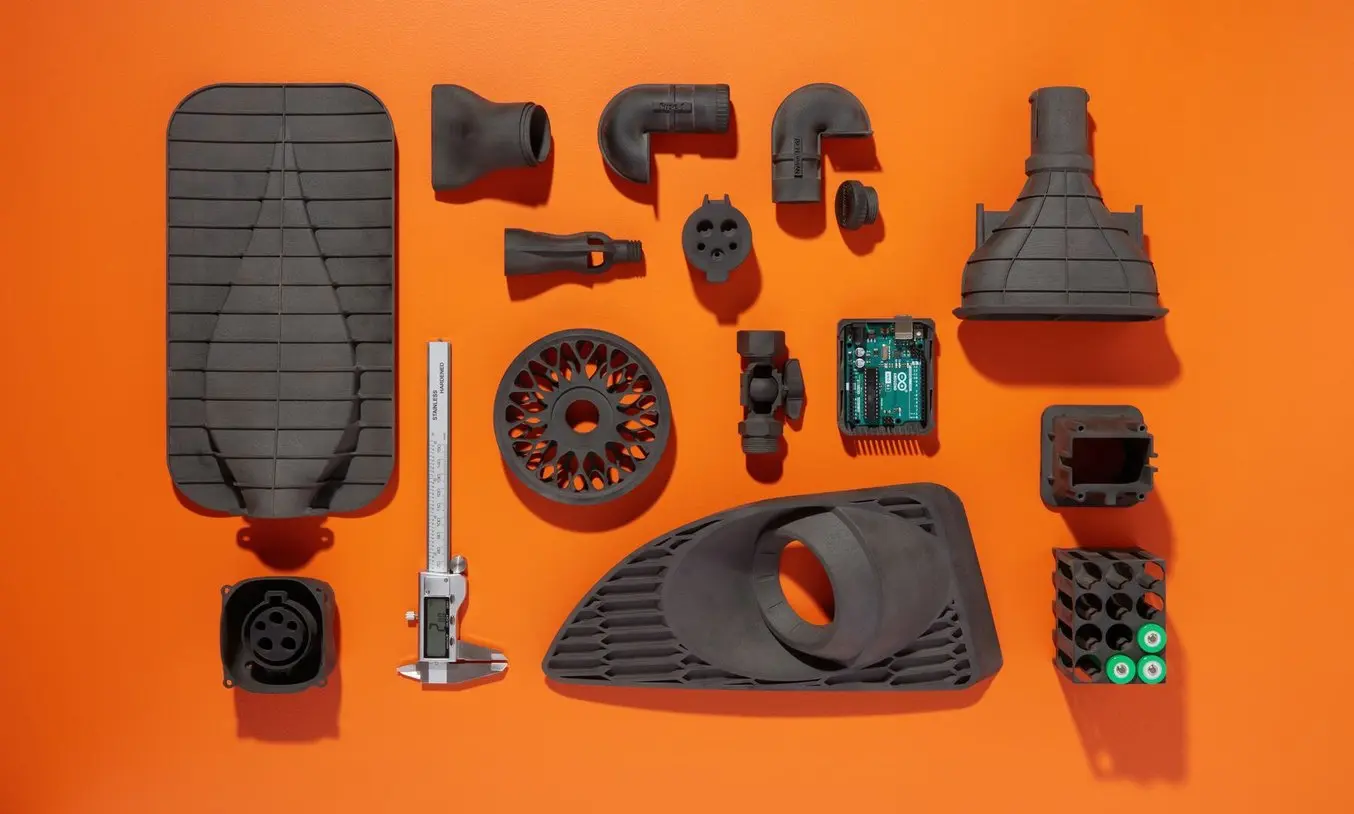
Refresh rate is the recommended percentage of fresh powder used when mixing a new powder cartridge. The minimum refresh rate of Nylon 12 GF Powder ranges from 30% to 50% and can be adjusted to minimize material waste, optimize cost per part, or improve part finish. The actual post-processing, dosing, and mixing of new cartridges are managed by the Fuse Sift. Users can manually adjust the refresh rate if necessary on the Fuse Sift touchscreen, making the post-processing and powder reclamation easy for any member of the team.
When switching between Nylon 12 GF Powder and Nylon 12 Powder, cleaning time for Fuse 1 and Fuse Sift is dramatically reduced, and requires only two hours of preparation and cleaning to start a new print. Compared to the full-day process required by most industrial SLS systems, the simplified material changeover process reduces downtime and enables more in-house, multi-material production with a single printer unit.
The Fuse 1 uses Formlabs’ patented Surface Armor Technology, which creates a semi-sintered shell around the part that enhances surface quality and ensures a smooth surface finish. When using Nylon 12 GF Powder, this semi-sintered shell requires de-powdering in the Fuse Sift and a post-processing media blasting step. Desktop or benchtop media blasters can be bought for prices as low as $200, and are a valuable addition to any SLS material workflow.
Increase Production Flexibility With Nylon 12 GF Powder
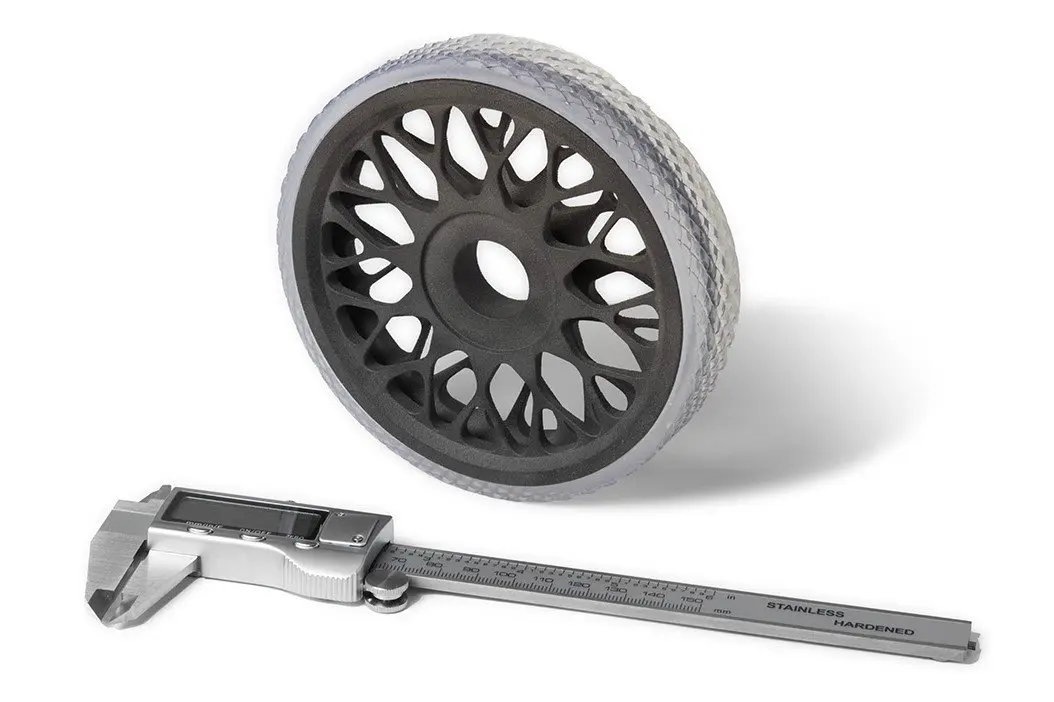
Historically, high-performance 3D printing materials like glass-filled powders have been out of reach of most small and medium manufacturers. Truly industrial quality composite parts have only been available on machines that cost in the hundreds of thousands of dollars. With the Fuse 1 and the expanded SLS materials library, it’s easier than ever to design, iterate, and manufacture any product.
With the addition of Nylon 12 GF, the Formlabs SLS materials library empowers users to take more control over their production, and extend the reach of their manufacturing abilities. With the highest tensile modulus and heat deflection temperature of the new glass-filled material, even more industrial applications are now accessible for Fuse 1 users.
Evaluate the material yourself to see how you can expand production. Order a free sample part or contact our SLS sales experts for more information.