Die Zukunft von Requisite und Make-up-Effekten: Großformatige 3D-gedruckte Requisiten und Formen aus dem Form 3L für die 2. Staffel „Raised by Wolves“
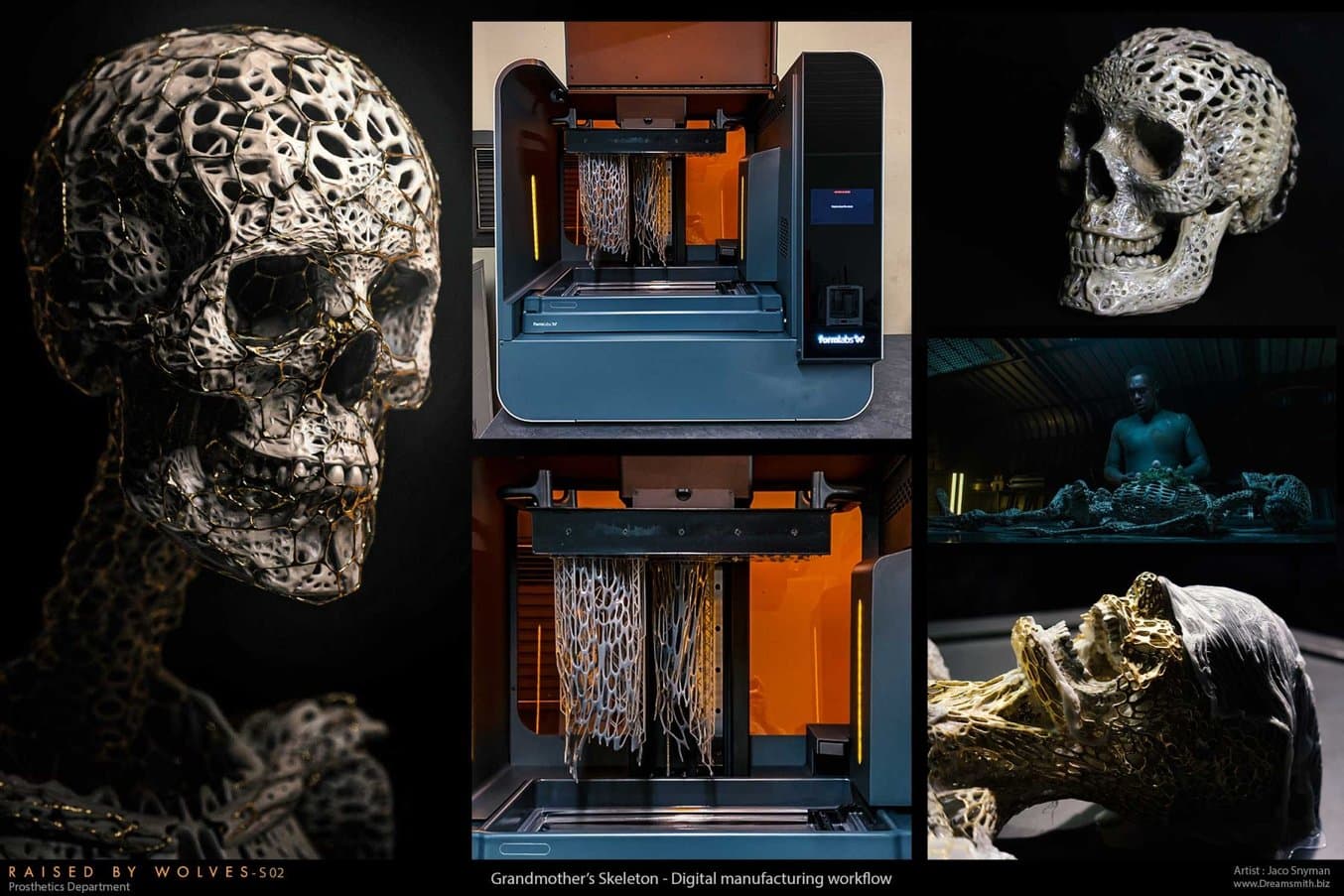
2020 unterhielten wir uns mit Jaco Snyman, dem Gründer des preisgekrönten Dreamsmith Studios für prothetische Make-Up-Effekte und Requisitenherstellung und leitenden Prothetikdesigner der SciFi-Serie „Raised by Wolves“. Snyman berichtete uns damals von seinem Prozess zur Herstellung 3D-gedruckter Formen und Modelle für die Endverwendung, die in der ersten Staffel der Serie zu sehen waren.
Die von Aaron Guzikowski kreierte und von Ridley Scott produzierte HBO-Max-Serie handelt von zwei Androiden, Vater und Mutter, deren Mission es ist, menschliche Kinder großzuziehen. Im Februar 2022 wurde die Serie um eine zweite Staffel ergänzt, in der noch mehr 3D-gedruckte Requisiten und Prothesen auftauchen – diesmal wurden sie auf einer ganzen Flotte großformatiger Stereolithografie-Drucker (SLA) des Typs Form 3L gedruckt.
“Raised By Wolves” Season 2 Teaser
Im folgenden Artikel erläutern Snyman und sein Team, wie Dreamsmith mithilfe des Form 3L großformatige Formen und Modelle druckte, um Aliens, Androide und andere Requisiten der apokalyptischen Welt von „Raised by Wolves“ zum Leben zu erwecken.
Requisiten und Make-up-Effekte der neuen Art: Fünf Fallstudien aus der zweiten Staffel „Raised by Wolves“
Der 3D-Druck ist dabei, die schnelllebige und von Fristen getriebene Welt der Filmindustrie komplett umzukrempeln. Er bringt nicht nur alle Vorteile eines digitalen Arbeitsablaufs mit sich und reproduziert digitale Modelle zuverlässig und genau als physische Objekte, sondern entlastet auch Arbeitskräfte, sodass sie sich kreativeren Aufgaben zuwenden können. Das ist eine geradezu revolutionäre Leistung, weshalb wir den 3D-Druck unbedingt in unsere Arbeit integrieren wollten. Wie bei allen neu aufkommenden Technologien gab es leider einige Startschwierigkeiten.
Damit uns der 3D-Druck nützen konnte, musste er drei bestimmte Kriterien erfüllen. Erstens musste er den gleichen Detailgrad erreichen, den uns traditionelle Techniken bieten. Außerdem mussten diese Details in einem ausreichend großen Maßstab reproduzierbar sein – wir brauchten also ein Fertigungsvolumen, das groß genug war, um zum Beispiel einen menschlichen Kopf ganz zu umfassen. Und schließlich musste der Drucker zuverlässig, genau und einfach zu handhaben sein. Aufgrund unserer knappen Fristen und Budgetvorgaben durften nur minimale fehlgeschlagene Drucke oder Ausfälle auftreten.
Einen Drucker zu finden, der all diesen Anforderungen gerecht wurde und trotzdem nicht unbezahlbar teuer war, stellte sich als extrem schwierig heraus. Die verfügbaren Drucker, die das alles zu einem erschwinglichen Preis erreichten, arbeiteten nicht verlässlich genug, während zuverlässigere Modelle nicht die erforderliche Detailtreue und Größe boten. Nach einigen Jahren des Testens begannen wir uns damit abzufinden, dass der 3D-Druck für uns vorerst nur ein Werkzeug von vielen bleiben würde, statt der völligen Revolution, die wir uns erhofft hatten. Dann kam der Form 3L auf den Markt.
Der Form 3L erfüllte alle Kriterien. Sein Fertigungsvolumen ist mit 33,5 x 20,0 x 30 cm riesengroß, und das bei einer Auflösung von 25 Mikrometern. Das alles wird unterstützt von der Software PreForm, die den ganzen Vorgang überaus zuverlässig und benutzerfreundlich macht. Zusammen mit der beeindruckenden Palette von Kunstharzen machen diese Vorteile den Form 3L zu einem unglaublich leistungsstarken Werkzeug, das unseren Arbeitsablauf in nur zwei Jahren vollständig revolutioniert hat.
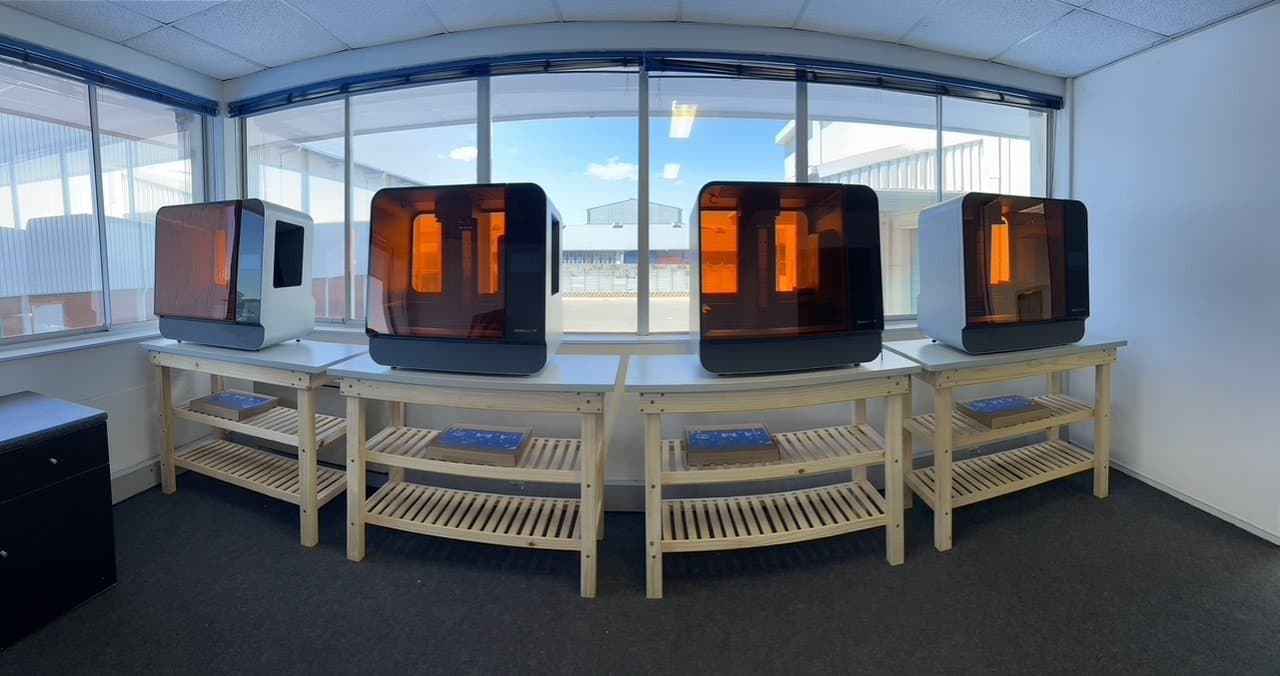
3D-Drucker des Typs Form 3L in Dreamsmiths Werkstatt in Kapstadt, Südafrika.
Es ist schwer zu beschreiben, wie sehr der Form 3L unsere Arbeit umgekrempelt hat, ohne zu erläutern, wie er unsere Herangehensweise an kreative Probleme verändert hat. In den folgenden Beispielen erklären wir unseren genauen Arbeitsprozess, um zu veranschaulichen, warum wir diesen Drucker in unserer Branche für so bahnbrechend halten.
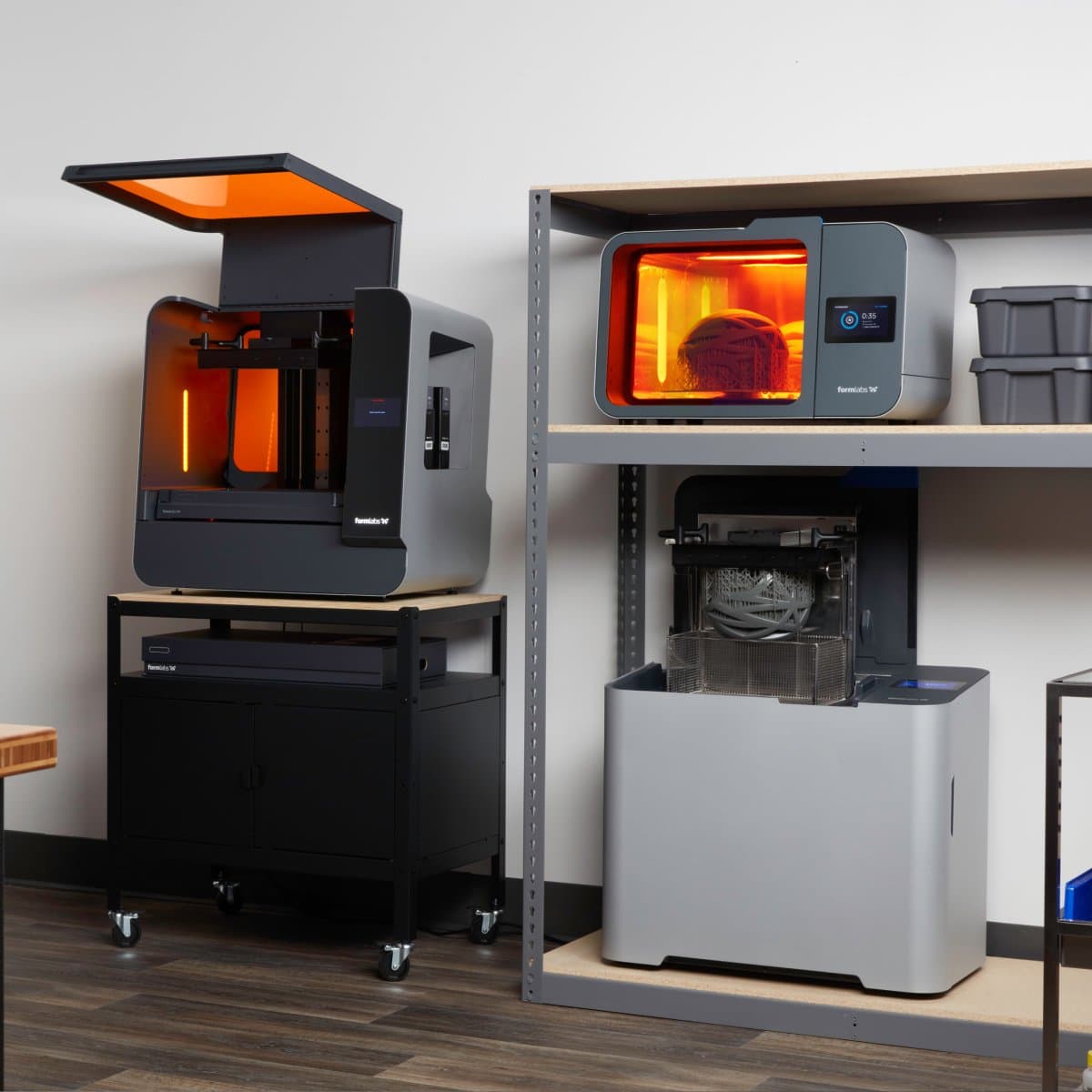
Live-Demo des Großformat-3D-Druckers Form 3L
In diesem kostenlosen Online-Webinar gibt Jakob Dobberow, Pro Services Trainer bei Formlabs, einen umfassenden Überblick zur betriebsinternen Herstellung und Nachbearbeitung von Teilen mittels SLA-3D-Druck im Großformat.
Erhalten Sie Tipps und Tricks unseres Experten bei einer exklusiven Live-Demonstration sowie einen Einblick in Anwendungsbereiche die Ihre größten Ideen mühelos zum Leben erwecken.
#1: Ein Ersatz für Abdrücke – Dummy-Nachbildung einer Schauspielerin
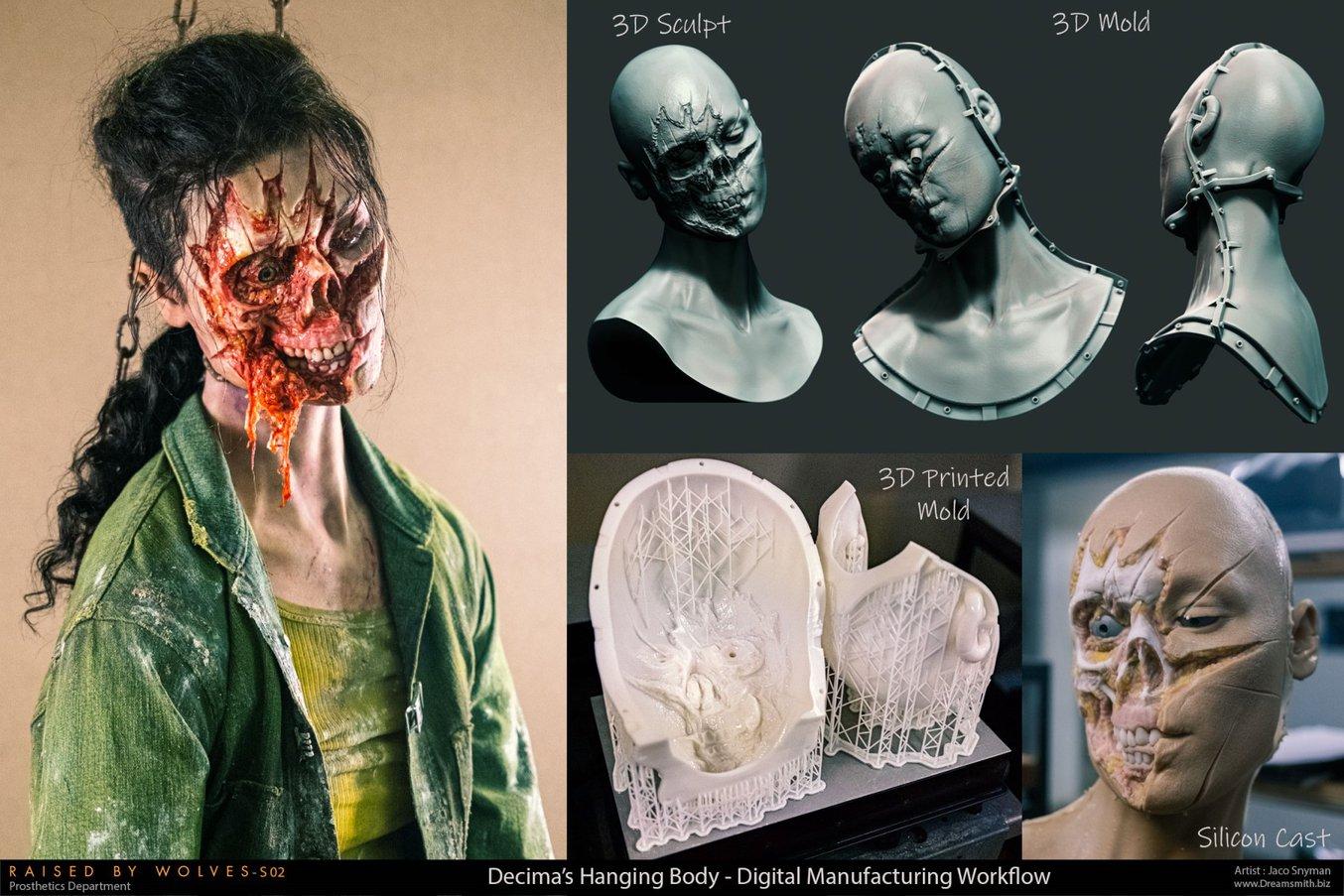
Die Herstellung einer hyperrealistischen Silikon-Nachbildung des Gesichts einer Schauspielerin, mit digital entworfenen und auf dem Form 3L aus Rigid 10K Resin 3D-gedruckten Formen.
In diesem Beispiel hatten wir die Aufgabe, eine hyperrealistische Silikon-Nachbildung des Körpers einer Schauspielerin zu erstellen. Der Haken an der Sache war aber, dass sie am Hals aufgehängt sein sollte, mit einem halb abgerissenen Gesicht.
Früher hätten wir einen Silikon-Abdruck von der Schauspielerin genommen und dafür ihr Gesicht mit Silikon und Gipsbinden bedeckt, um ein einzelnes Modell des Gesichts zu erhalten. Aus diesem Lebendabdruck würden wir dann einen Tonguss erstellen, auf dem wir die zusätzlichen für die Szene erforderlichen Details per Hand modellieren. In diesem Fall hätte das die Verlängerung des Halses und das Entfernen von Teilen des Gesichts bedeutet.
Von dieser Tonskulptur müsste dann mithilfe von Epoxidharz und Glasfasern eine neue Form erstellt werden. Schließlich hätten wir aus dieser endgültigen Form die fertige Silikon-Nachbildung des Kopfes erstellt. Dieser Prozess hätte drei Wochen und mindestens drei erfahrene Künstler und Techniker in Anspruch genommen – für eine Nachbildung aus rohem Silikon, die noch lackiert werden muss und in welche in aufwendiger Kleinarbeit Haare eingefädelt werden müssen, um den geforderten Hyperrealismus zu erreichen. Von Anfang bis Ende hätte der Prozess insgesamt ungefähr einen Monat gedauert.
„Der Form 3L ist in der Lage, die endgültige Form des Kopfes in einem Stück zu drucken, und zwar detailreich genug, dass sie nicht von traditionell hergestellten Formen zu unterscheiden ist. Dadurch war es uns möglich auf einen digitalen Ablauf umzusteigen, auf Grundlage eines hochpräzisen 3D-Scans der Schauspielerin. Das invasive Verfahren des Abdrucknehmens wurde somit überflüssig, was den ganzen Prozess für die Schauspielerin weitaus angenehmer machte.“
Jaco Snyman, Gründer von Dreamsmith Studio
Mithilfe von ZBrush konnten wir dann die zusätzlich benötigten Details hinzufügen. Der gesamte Vorgang ist nicht invasiv und lässt sich wiederholen. Außerdem bleibt er vollkommen flexibel, sodass wir größere kreative Veränderungen auf Grundlage des Feedbacks des Regisseurs mit Leichtigkeit implementieren können.
Im Anschluss entwarfen wir die digitale Form, die wir dank des großen Fertigungsvolumens des Form 3L in größere Einzelteile aufteilen konnten. Dadurch weist das endgültige Teil weniger Nahtlinien auf. Die Form wurde über Nacht gedruckt, und nach leichter Reinigung war sie schon am nächsten Tag bereit für die Verwendung.
Das Verfahren Schritt für Schritt
Der gesamte Arbeitsablauf kann von einer Person allein durchgeführt werden, und das in einem Bruchteil der Zeit, die es nach herkömmlichen Verfahren gedauert hätte. Das setzt Arbeitskräfte frei, die sich nun auf den Schritt konzentrieren können, der hinsichtlich des Produktionswertes am wichtigsten ist: den Feinschliff. Dank dieses effizienteren Arbeitsablaufes bleibt ausreichend Zeit für die letzten Phasen zur Fertigstellung des Produktes. Bisher endete dieser Abschnitt fast immer in Gehetze, weil das traditionelle Verfahren zu arbeitsintensiv war.
Schon an diesem einen Beispiel ist deutlich zu sehen, was für eine bahnbrechende Neuerung der 3D-Druck darstellt. Wir schließen unsere Arbeit in kürzerer Zeit ab, sind produktiver und sparen an traditionellen Materialien und Arbeitskräften. Der Form 3L hat unseren Arbeitsablauf schneller, besser und günstiger gemacht.
#2: Kreation komplexer Formen – Silikonmaske
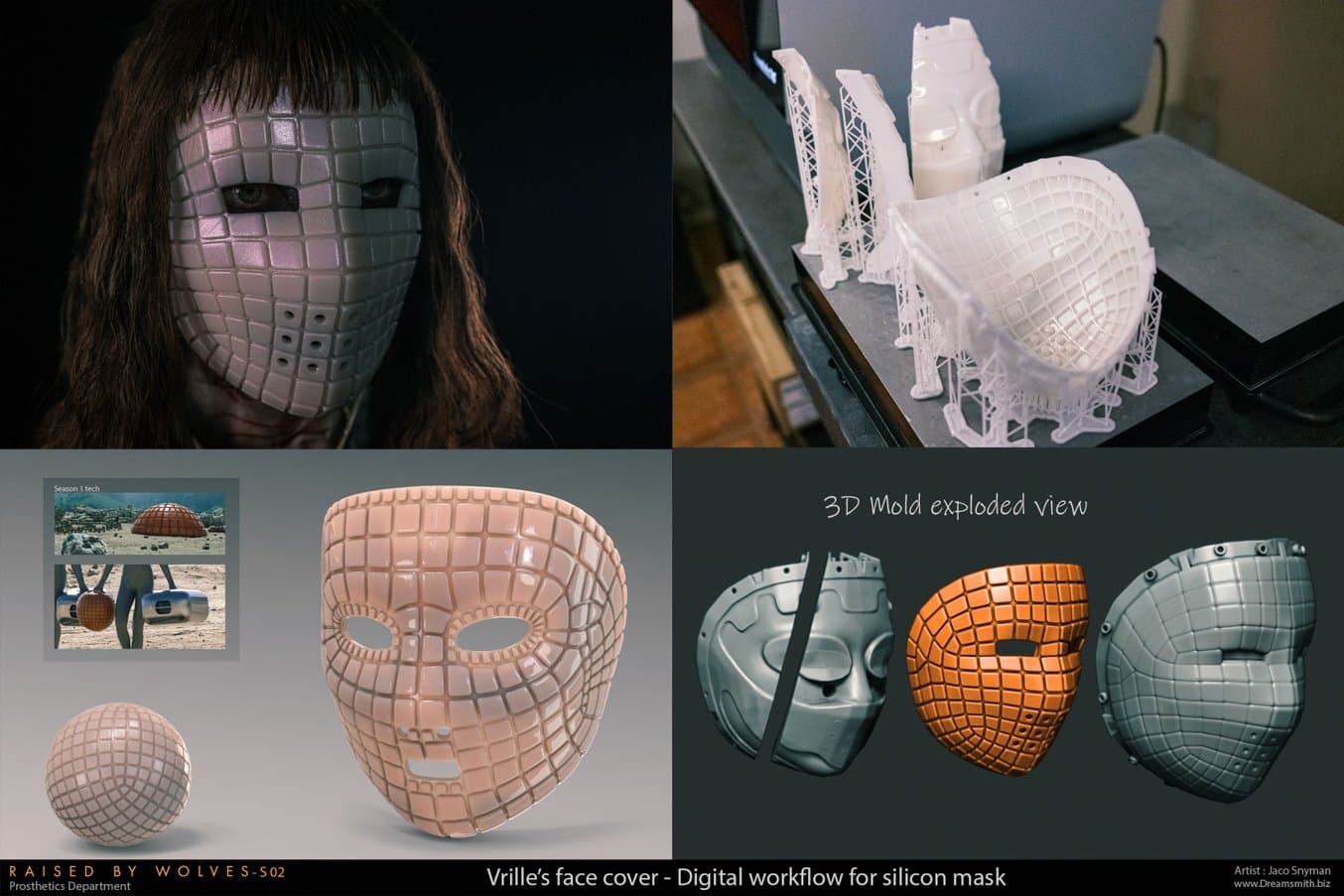
Design und Druck einer komplexen Form und hochdetaillierten Silikonmaske mittels 3D-Druck.
Bestimmte Designelemente profitieren sehr stark von CAD (computer-aided design). Manche Aufträge sind von Hand schlichtweg unmöglich zu kreieren oder so umständlich und zeitaufwendig, dass es an das Unmögliche grenzt. Traditionellerweise hätten wir die Herstellung solcher Teile an eine Fräswerkstatt auslagern oder den Auftrag einfach ganz ablehnen müssen. Der 3D-Druck erschien immer als potenzielle Lösung für diese Probleme, doch die Technologie musste erst ein Niveau erreichen, auf dem sowohl Druckqualität als auch Preis akzeptabel waren.
Genau diese Ansprüche erfüllte der Form 3L für uns. Wir sind jetzt viel weniger durch traditionelle Fertigungsverfahren eingeschränkt und können erheblich mehr Probleme betriebsintern lösen, ohne auf teures Outsourcing angewiesen zu sein. Die Grenzen unserer Fantasie sind von jetzt an unsere größte Hürde, und das ist eine aufregende Ausgangslage!
Im oben geschilderten Beispiel hatten wir Anweisungen, die ohne 3D-Druck sehr schwer umzusetzen gewesen wären. Bei der Maske von Vrille gab es gleich zwei einzigartige Probleme zu lösen.
Einerseits mussten darin sowohl organische als auch geometrische Details inkorporiert werden; die äußere Schicht der Maske sollte makellose geometrische Formen aufweisen, aber all das auf der Grundlage der organischen, asymmetrischen Gesichtsform der Schauspielerin.
Das zweite Problem war das Material: Die endgültige Maske sollte aus Silikon bestehen, also brauchten wir eine Form, da wir aus Silikon nicht drucken können.
Das Verfahren Schritt für Schritt
Dieser Auftrag illustriert gut die verschiedenen technologischen Fortschritte, die für seine Fertigstellung nötig waren. Wir brauchten einen 3D-Scan der Schauspielerin, die Software für die Erstellung der digitalen Datei und den Entwurf der Form sowie einen 3D-Drucker, der groß und präzise genug war, um die Form zu drucken.
In der obrigen Aufgliederung des Prozesses ist zu sehen, dass die komplette Form auf eine Konstruktionsplattform passte, wodurch wir unsere Druckzeit drastisch verkürzen konnten. Auch die Innovationen bei den Druckmaterialien spielten eine große Rolle. Durch den Druck mit Formlabs' Rigid 10K Resin war die endgültige Form extrem präzise, sodass wir letztendlich eine nahezu perfekte Maske erhielten, wie oben zu sehen ist.
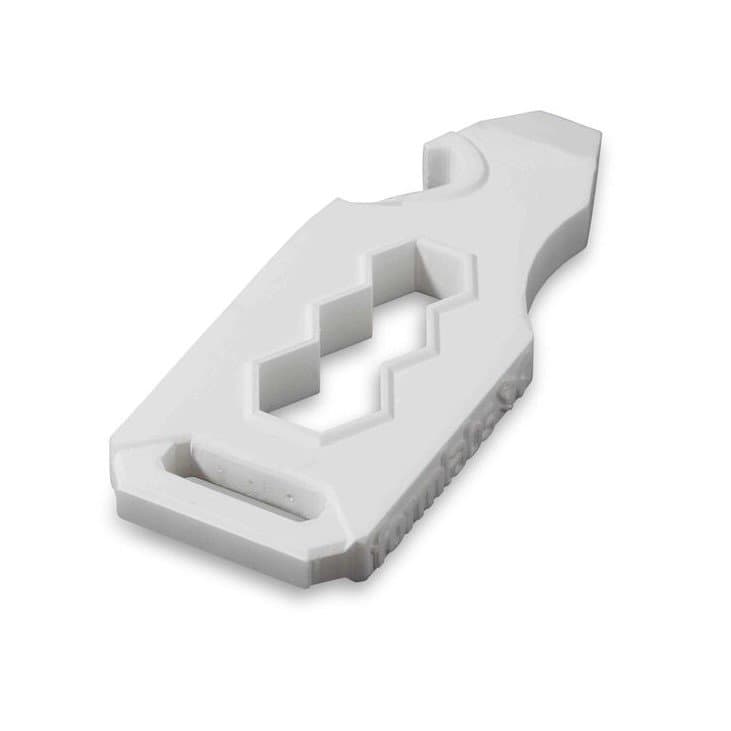
3D-Probedruck aus Rigid 10K Resin anfordern
Sehen und fühlen Sie selbst die Qualität von Formlabs. Wir senden Ihnen einen kostenlosen Probedruck an Ihren Arbeitsplatz.
#3: Unmögliche Formen drucken – Biomechanisches Skelett
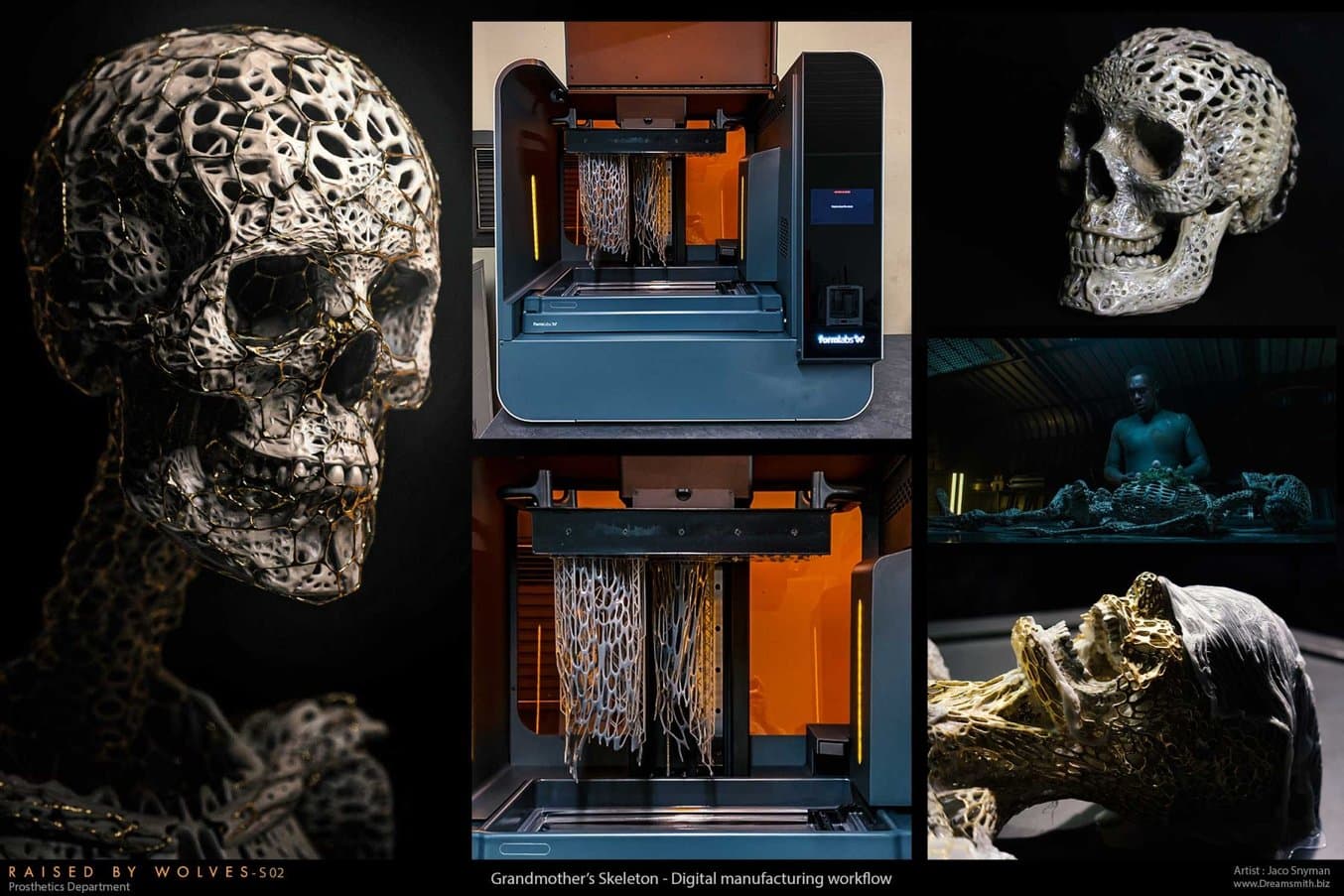
Ein großformatiges biomechanisches Modell eines Skeletts, 3D-gedruckt auf dem Form 3L.
Einige Designs sind mit 3D-Druck leichter umzusetzen, andere werden dadurch überhaupt erst möglich.
Beim oben abgebildeten Design handelt es sich zum Beispiel um ein lebensgroßes biomechanisches Skelett. Eine Requisite mit feinen Details und geometrischen Formen, die aus Ton qualvoll schwierig zu modellieren gewesen wäre, und für die sich mit traditionellen Methoden praktisch unmöglich eine Form herstellen ließe.
Das Skelett der Großmutter ist ein perfektes Beispiel eines Designs, dessen Kreation nur möglich war, weil wir es 3D-drucken konnten. Der 3D-Druck wird schon seit einiger Zeit für unmögliche Formen und Verzahnungen genutzt, doch für uns war es wichtig, auch in größerem Maßstab hohe Genauigkeit zu erreichen. Wir brauchten ja ein Skelett in Lebensgröße! Mit dem großen Fertigungsvolumen des Form 3L konnten wir die gesamte Requisite in Einzelteilen von praktischer Größe und in hoher Auflösung drucken.
Das Verfahren Schritt für Schritt
Ohne den Form 3L wäre so eine Requisite aus praktischer und finanzieller Sicht unmöglich herzustellen gewesen.
#4: Große Teile schnell drucken – Nachbildung einer Schauspielerin als Dummy
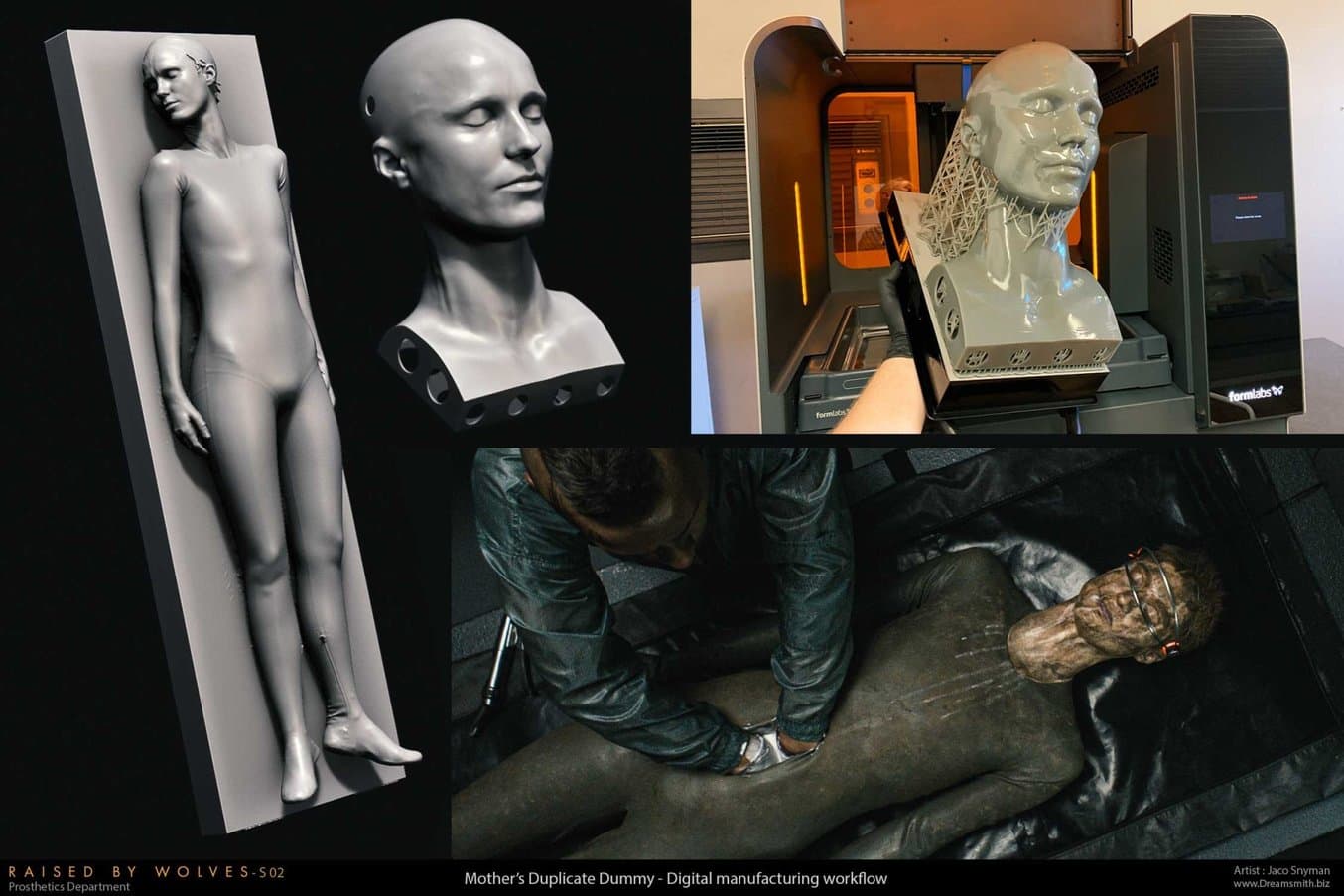
Der Kopf der Schauspielerin Amanda Collin, aus Draft Resin auf dem Form 3L innerhalb von 12 Stunden 3D-gedruckt.
Beim Fertigungsvolumen kommt es besonders auf die Größe an. Eine unserer Anforderungen bei der Wahl des Druckers war, dass er einen kompletten menschlichen Schädel drucken können sollte. Jede Aufteilung einer Form in kleinere Teile generiert zusätzlichen Aufwand bei der Fertigstellung. Jede Verbindung oder Nahtlinie auf der Form muss sorgsam nachbearbeitet und neu texturiert werden, damit eine makellose Requisite entsteht.
Die oben abgebildete Dummy-Nachbildung von Mutter ist ein perfektes Beispiel dafür. Wir konnten den Kopf auf dem Form 3L in einem Stück drucken und erhielten so ein perfektes Kunstharz-Duplikat des Gesichts der Schauspielerin, das wir nach Bedarf bemalen konnten.
Mit traditionellen Methoden wäre das ein extrem zeitaufwendiger Vorgang gewesen, für den wir einen Lebendabdruck, handgefertigte Epoxidharzformen und schließlich den endgültigen Silikonguss erstellt hätten. Zum Vergleich: Für eine andere Dummy-Nachbildung, die wir noch vor der Anschaffung des Form 3L kreiert haben, brauchte unser gesamtes Team einen ganzen Monat. In diesem Fall konnten wir innerhalb einer Woche das Gesicht von Mutter drucken und ihren Körper maschinell fräsen, sodass die endgültige Requisite innerhalb von zwei Wochen bemalt und einsatzbereit war.
Das Verfahren Schritt für Schritt
Es ist wichtig zu erwähnen, dass diese Requisite für Nahaufnahmen nicht geeignet gewesen wäre; sie wurde speziell für die oben dargestellte Aufnahme kreiert. Deshalb konnten wir den Kunstharzdruck aus dem Form 3L direkt einsetzen, da er detailliert genug für eine Aufnahme aus solcher Entfernung war. So sparten wir eine Menge Zeit, Material und Geld.
Mit traditionellen Umform- und Gussverfahren hätte dieser Dummy unabhängig vom Detailgrad des Endproduktes immer gleich viel Zeit in Anspruch genommen. Dank des Form 3L ließ sich unser Ansatz realisieren, ein mittleres Maß an Detailliertheit zu halten. Wir konnten eine Requisite erstellen, die zu den spezifischen Anforderungen der Szene passte. So können wir in kürzerer Zeit und zu geringeren Kosten mehr Aufträge annehmen, was in der budgetbewussten Welt der Filmindustrie von unschätzbarem Wert ist.
#5: Hybride Arbeitsabläufe – Pauls Bioangriff-Make-up
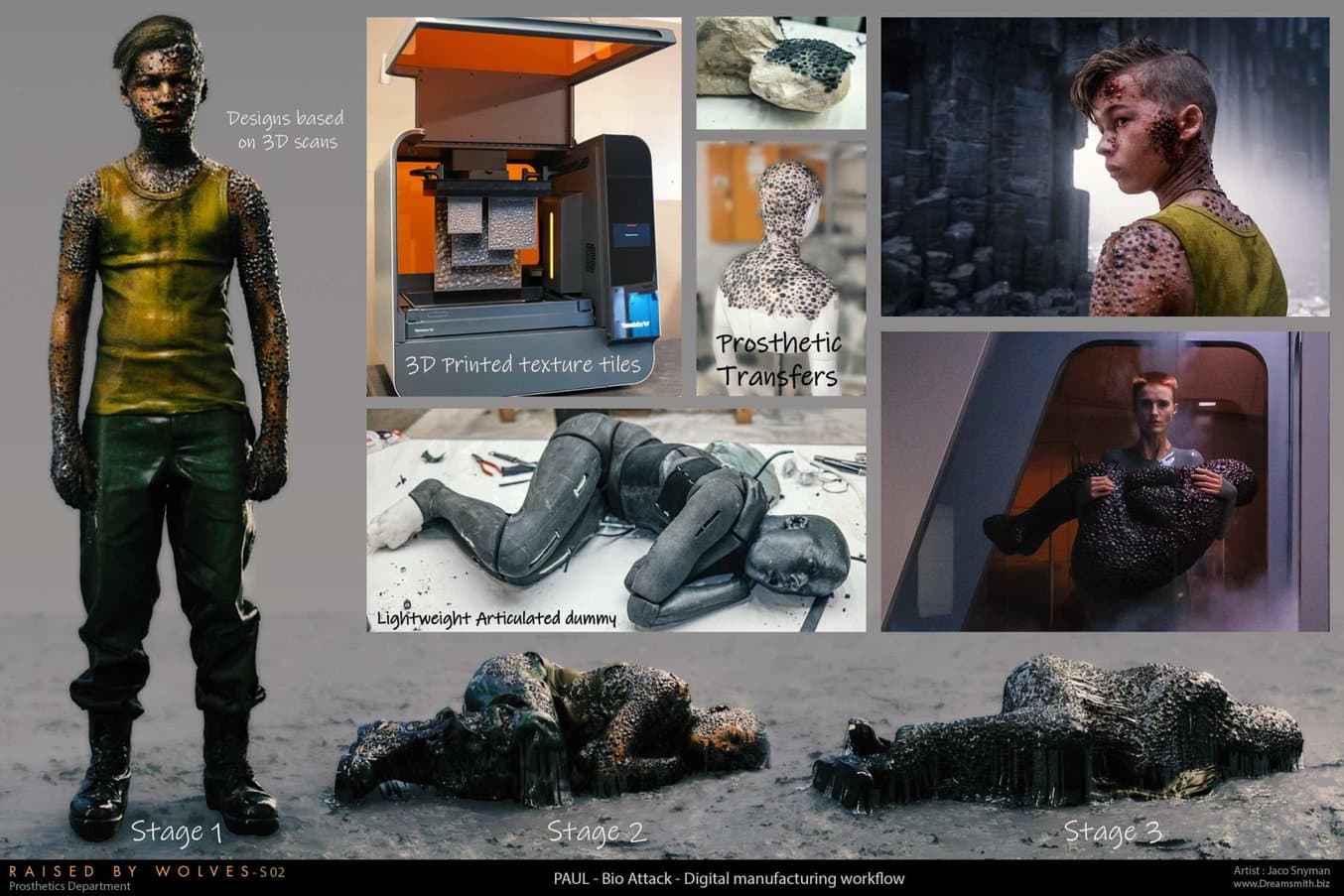
Kombination 3D-gedruckter Texturplättchen mit traditionellen Methoden der Dummyherstellung.
Der 3D-Druck muss konventionelle Verfahren nicht immer komplett ersetzen. Als wir den Form 3L zur Verfügung hatten, war es spannend, uns neue, hybride Arbeitsabläufe zu überlegen, die die Vorteile beider Fertigungsansätze vereinen.
Der Kokon von Paul veranschaulicht, wie wir traditionelle Fertigungstechniken mit 3D-Druck kombiniert haben, um etwas zu erschaffen, das mit einer Technik allein sehr schwierig gewesen wäre.
Jaco Snyman, Gründer von Dreamsmith Studio
Für den Kokon brauchten wir eine biegsame, schuppige Haut, die den Bewegungen des Dummys im Inneren folgt. Dafür wäre normalerweise eine sehr große und kostspielige Form nötig gewesen, doch da die Schuppen organisch sind und wie ein Puzzle zusammengesetzt werden können, machte es Sinn, die Haut per Hand über den Dummy zu ziehen, was die Form überflüssig machte.
Allerdings benötigten wir dafür eine große Menge schuppenartiger Plättchen, aus denen wir den Kokon zusammensetzen konnten. Für diesen Teil des Prozesses bot sich der 3D-Druck an, da sich filigrane Details damit präzise und schnell reproduzieren lassen. Wir druckten eine Reihe von Formen für flache, schuppenartige Strukturen verschiedener Größen, mit denen wir Schuppen aus Silikon gießen konnten. Aus diesen Silikonplättchen formten wir dann den Kokon.
Das Verfahren Schritt für Schritt
Dank des Form 3L und der breiten Palette an Kunstharzen, die uns zur Verfügung stehen, sind solche hybriden Verfahren möglich. Das ist in der Filmbranche, wo man täglich vor neue Probleme gestellt wird, unglaublich viel wert.
Hinter den Kulissen der zweiten Staffel von „Raised by Wolves“: Dreamsmiths Fazit
Staffel 2 von „Raised by Wolves“ war für uns ein Wendepunkt: Es war das erste Mal, dass wir uns massiv auf 3D-Druck gestützt haben. Viele der genannten Beispiele waren lange nur Theorie, bevor wir sie schließlich zu einer festen Frist realisieren mussten.
Solche Unterfangen sind normalerweise sehr anfällig für Fehler und unvorhergesehene Ergebnisse. Obwohl beides zur Genüge aufgetreten ist, war unsere Erfahrung mit dem Form 3L insgesamt doch mustergültig, und unser Vertrauen in das Gerät ist mit jedem erfolgreichen Projekt weiter gewachsen.
Seine Zuverlässigkeit hat uns gezeigt, dass wir auf diesem Weg fortschreiten und das Gelernte auch in größeren und anspruchsvolleren Projekten anwenden können. Wir haben unsere Flotte inzwischen um vier zusätzliche Form 3L erweitert, und dank dieser gesteigerten Kapazität konnten wir einen Produktivitätsgrad erreichen, den wir zuvor nicht für möglich gehalten hätten.
Dieser komplett digitale Arbeitsablauf lässt sogar Fernarbeit zu. Wir können die komplette Prothetik für Charaktere von überall 3D-scannen, designen, modellieren und formen und sie dann in alle Welt verschicken, ohne dass unser Team persönlich anreisen müsste oder der Kunde auf die Ankunft zerbrechlicher Lieferungen wartet. Wenn Sie mehr über diesen Service erfahren möchten, kontaktieren Sie uns gerne unter [email protected].
Seit der Arbeit an der zweiten Staffel von „Raised by Wolves“ haben wir unseren Erfahrungsschatz noch weiter ausgebaut und freuen uns darauf, zu gegebenem Anlass von unseren neueren Projekten zu berichten. Wenn wir auf diese ersten paar Versuche zurückblicken und in Betracht ziehen, wie stark wir uns derzeit auf den 3D-Druck verlassen, ist es ganz offensichtlich, wie sehr der Form 3L unsere Arbeit revolutioniert hat.
Folgen Sie Dreamsmith auf Instagram unter @dreamsmith_,um über die neuesten Produktionen auf dem Laufenden zu bleiben.
Vielen Dank an Jaco Snyman und Mathew Howard-Tripp für das Verfassen dieses Beitrags, sowie an unseren Partner in Südafrika, BuildVolume.
Ein Blick in die Zukunft: Ein vollkommen digitaler Designprozess in der prothetischen Maskenbildnerei
Seit Snyman und sein Team in einen Form 3L investierten und mit verschiedenen Kunstharzen der Materialbibliothek von Formlabs experimentierten, haben sie den idealen Weg gefunden, Formen für prothetisches Make-up für ihr aktuelles Geheimprojekt zu erstellen, das 2023 erscheint.
Sie sind zu einem komplett digitalen Verfahren zur Kreation von Make-up-Effekten übergegangen. Angefangen wird mit einem 3D-Scan des Schauspielers, dann wird das prothetische Make-up digital modelliert und mittels einer hybriden Silikongusstechnik gefertigt, wobei eine dünne Silikonschicht zwischen eine 3D-gedruckte Form und ein 3D-gedrucktes Modell gepresst wird.
Dem Team zufolge bedeutet das eine bahnbrechende Neuerung ihrer Arbeitsweise, da sie prothetisches Make-up jetzt in einem Sechstel der Zeit und zu erschwinglichen Kosten produzieren können. Weitere Vorteile sind unter anderem die Option, das Gesicht eines Schauspielers von überall auf der Welt zu scannen, wodurch die Arbeit an einem Projekt noch vor den stressigen Dreharbeiten aus der Ferne möglich ist.
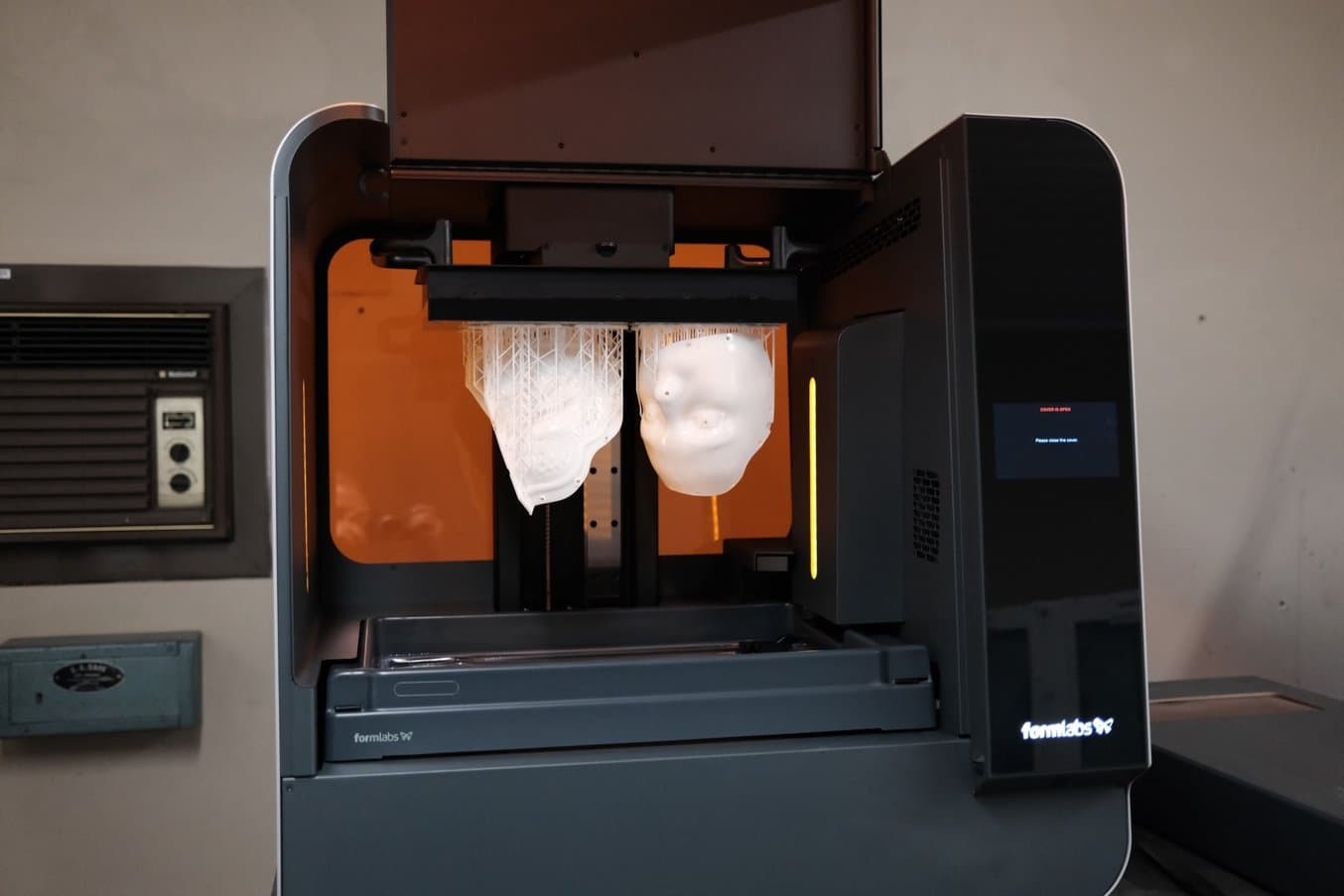
Versuche zur Formenherstellung für prothetisches Make-up mit Rigid 10K Resin und dem 3D-Drucker Form 3L.
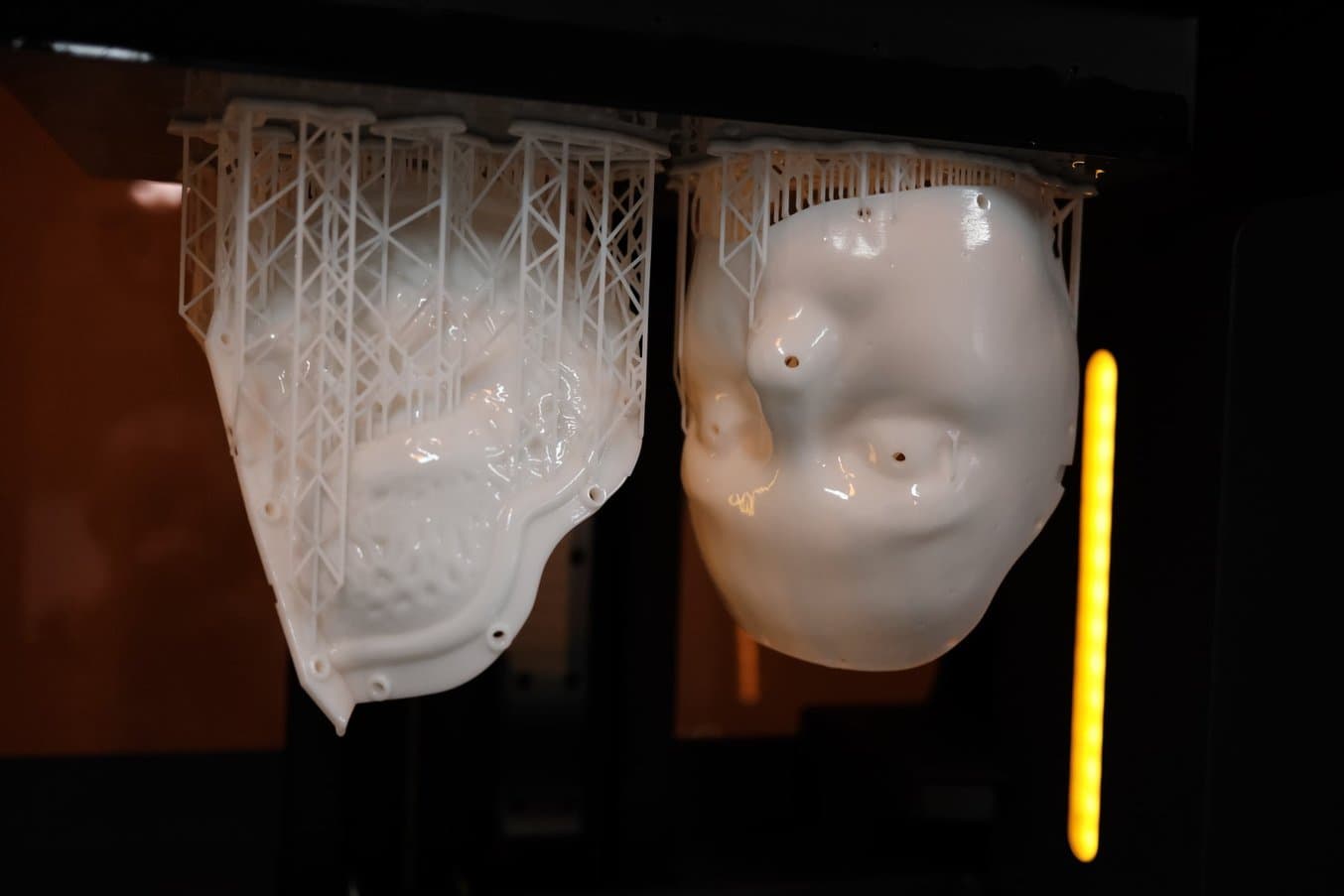
Snyman und sein Team arbeiten unermüdlich daran, alle Möglichkeiten zur Nutzung des 3D-Drucks in der Unterhaltungsbranche aufzudecken. Dreamsmith will den 3D-Druck auch für zukünftige Projekte mit Begeisterung einsetzen. Seien Sie gespannt auf ihre kommenden Projekte mit dem Form 3L.