Wie SiOCAST den Markt für Miniaturen mit 3D-gedruckten Urmodellen revolutioniert
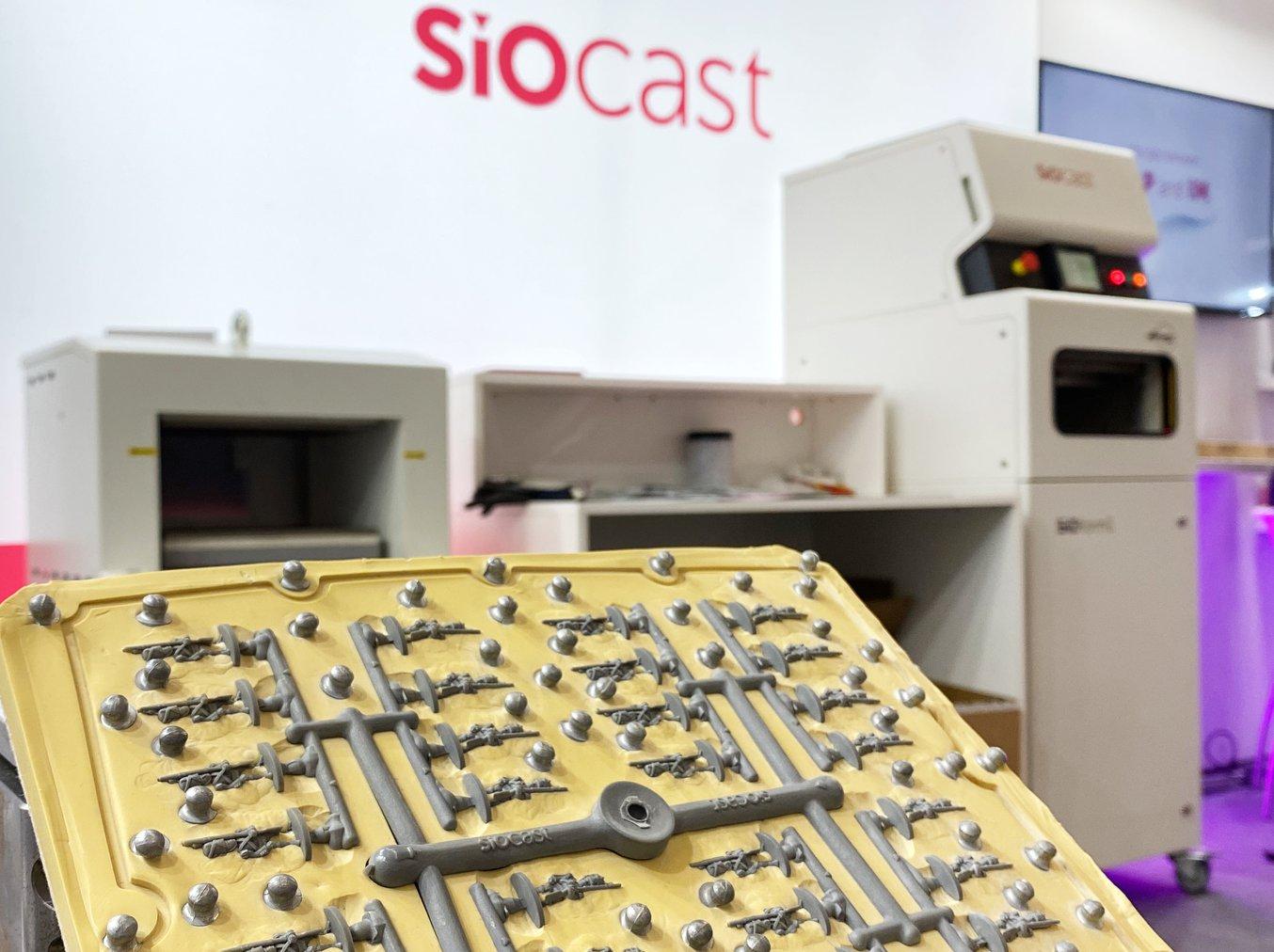
SiOCAST ist auf dem besten Weg, die Zukunft der Miniaturenfertigung neu zu gestalten, indem es sein eigenes agiles Produktionssystem einschließlich eigener Geräte und Materialien nutzt, um hochwertige, nicht-toxische Teile zu erschwinglichen Kosten betriebsintern herzustellen.
SiOCASTs Technologie, bei der über einen speziellen Prozess, der die Vorteile von 3D-Druck, Silikonformenbau und Spritzguss vereint, Silikonformen mittels 3D-gedruckten Urformen produziert werden, ist bereits weit verbreitet – von kleinen Studios bis zu den größten Miniaturherstellern der Branche wie Monster Fight Club (The Witcher, Cyberpunk RED), Reaper Miniatures (Bones) und Warlord Games (Blood Red Skies, Bolt Action).
In diesem Artikel führt uns Ferran Navarro, Geschäftsführer und Mitgründer von SiOCAST, durch den Prozess zur Fertigung von Miniaturen und kleinen Thermoplastteilen mit dem sogenannten Alemany System und erklärt, wie sein Team für dieses Verfahren 3D-Drucker von Formlabs einsetzt.
SiOCASTs neue Technologie schließt die Lücke zwischen 3D-Druck und Spritzguss
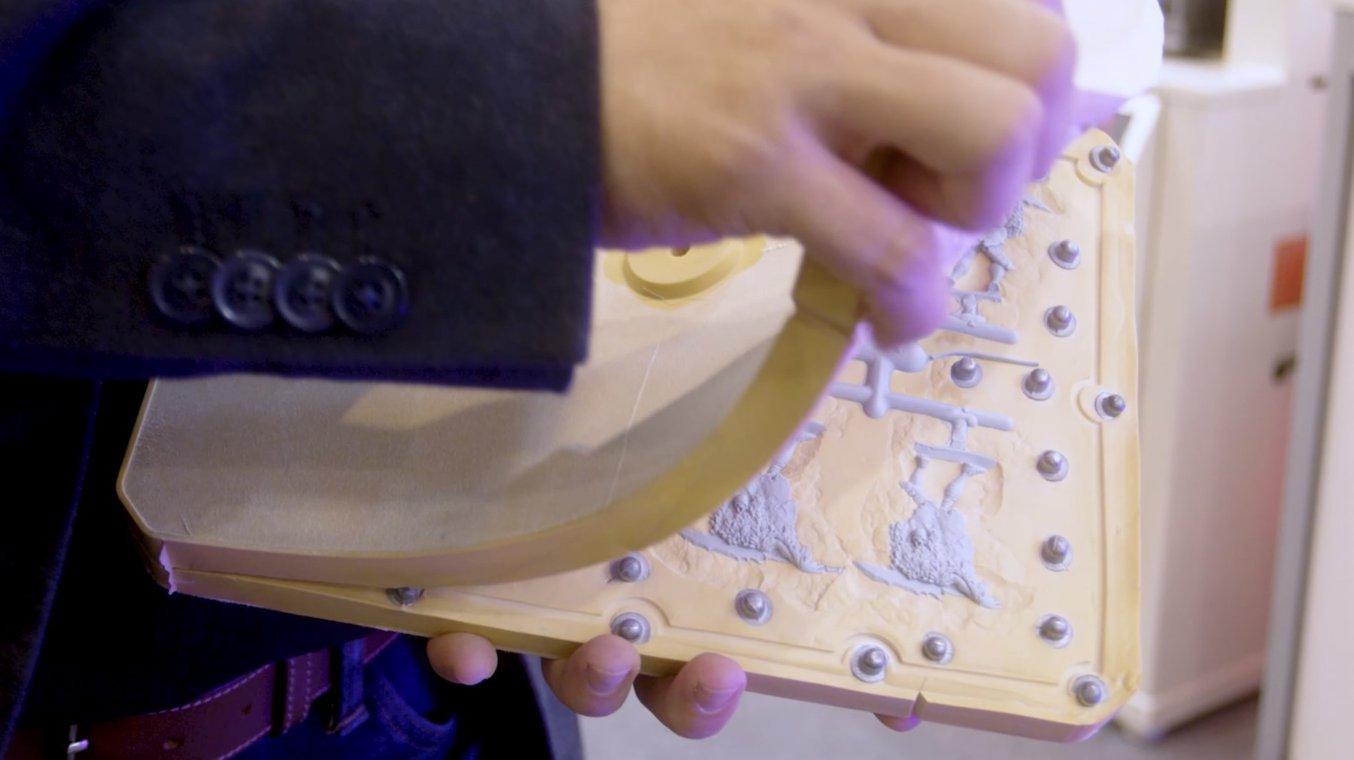
Herkömmliche Techniken zur Fertigung von Miniaturen in großen Stückzahlen sind oft kostspielig, erzielen eine mangelhafte Qualität und lassen sich schwer skalieren. Eines der beliebtesten Verfahren, der Spritzguss, erreicht bis zu siebenstellige Stückzahlen, ist aber für seine hohen Werkzeugkosten und langen Durchlaufzeiten bekannt, sodass die Einstiegsinvestition und die hohe Gewinnschwelle für kleinere Unternehmen eine große Markteintrittshürde darstellen. Auch für größere Akteure in der Miniaturenfertigung ist dies ein erhebliches Hindernis, denn die Veröffentlichung neuer Miniaturendesigns ist so mit hohem Risiko verbunden.
Die andere Seite der Medaille sind die direkt 3D-gedruckten Miniaturen: Mit Technologien wie dem Stereolithografie-3D-Druck (SLA) lässt sich ein extrem hoher Detailgrad erzielen, bei niedrigeren Einstiegshürden. Bei der Produktion großer Stückzahlen kann der 3D-Druck jedoch nicht mit Spritzguss konkurrieren. Miniaturenhersteller nutzen 3D-Druck üblicherweise für Einzelstücke, stark limitierte Serien oder Teile aus kundenindividueller Massenproduktion.
Andere verbreitete Techniken zur Miniaturenfertigung, wie Schleuderguss oder Kunstharzguss, sind häufig arbeitsintensiv und schwer skalierbar, gehen mit viel Unordnung einher und nutzen toxische Materialien, weshalb sie sich für die industrielle Produktion schwierig anpassen lassen.
SiOCAST wurde gegründet, um diese Probleme zu lösen. Als Tochterunternehmen der spanischen Unternehmensgruppe Coniex, die sich seit mehr als 35 Jahren auf Lösungen für die Bereiche Schleuderguss und Silikonformung spezialisiert, geht SiOCAST auf acht Jahre interner Forschungs- und Entwicklungsprozesse zurück, um die Produktivitätslücke zwischen 3D-Druck und Spritzguss zu schließen. Es lassen sich damit nämlich Produktionsvolumen von 50 bis 50 000 individuellen Teilen erreichen oder sogar bis zu 400 000 Teile produzieren.
SiOCAST bietet ein patentiertes System zum Einspritzen von thermoplastischem Kunstharz, das Formen aus bei hohen Temperaturen vulkanisiertem Silikonkautschuk einsetzt, welche anhand von hochdetaillierten 3D-gedruckten Urformen hergestellt werden. So können kleine Teile mit feinen Details aus einem für Spielzeug geeigneten, haltbaren Material produziert werden.
Der gesamte Prozess ist umweltfreundlich und kann lokal durchgeführt werden, ohne Zulieferer aus Übersee. In weniger als vier Jahren hat das SiOCAST-System sich als rentabel erwiesen und wird bereits von Unternehmen in mehreren Ländern und Regionen eingesetzt, unter anderem in den Vereinigten Staaten, dem Vereinigten Königreich, Asien und der EU.
Das Verfahren ist eine neuartige Technologie an der Schnittstelle von Schleuderguss, Kunstharzguss und Spritzguss. Wir haben es viel weiterentwickelt, damit es so simpel wie möglich ist und jeder die Technologie anwenden kann. Durch Automation ist es uns gelungen, dieselbe Produktivität wie großformatige Spritzgussmaschinen zu erreichen, mit dem Vorteil, dass unser Silikon sehr günstig, sicher und lokal produziert ist.
Ferran Navarro, Geschäftsführer und Mitgründer von SiOCAST
Silikonformenbau mit 3D-gedrucktem Rapid Tooling
Der Silikonformenbau beinhaltet konventionellerweise die Fertigung von Formen aus einem physischen Urmodell oder einer Urform, welche üblicherweise durch Modellieren von Hand, Schleuderguss oder CNC-Zerspanung hergestellt werden.
Dank der Fortschritte im hochwertigen und erschwinglichen SLA-3D-Druck, etwa mit den 3D-Druckern von Formlabs, war SiOCAST jedoch in der Lage, seinen Prozess zuverlässig auf hochdetaillierte 3D-gedruckte Urmodelle zu stützen.
Der Formenbauprozess von SiOCAST.
Der Prozess von SiOCAST umfasst die folgenden Schritte:
1. Design des digitalen Modells
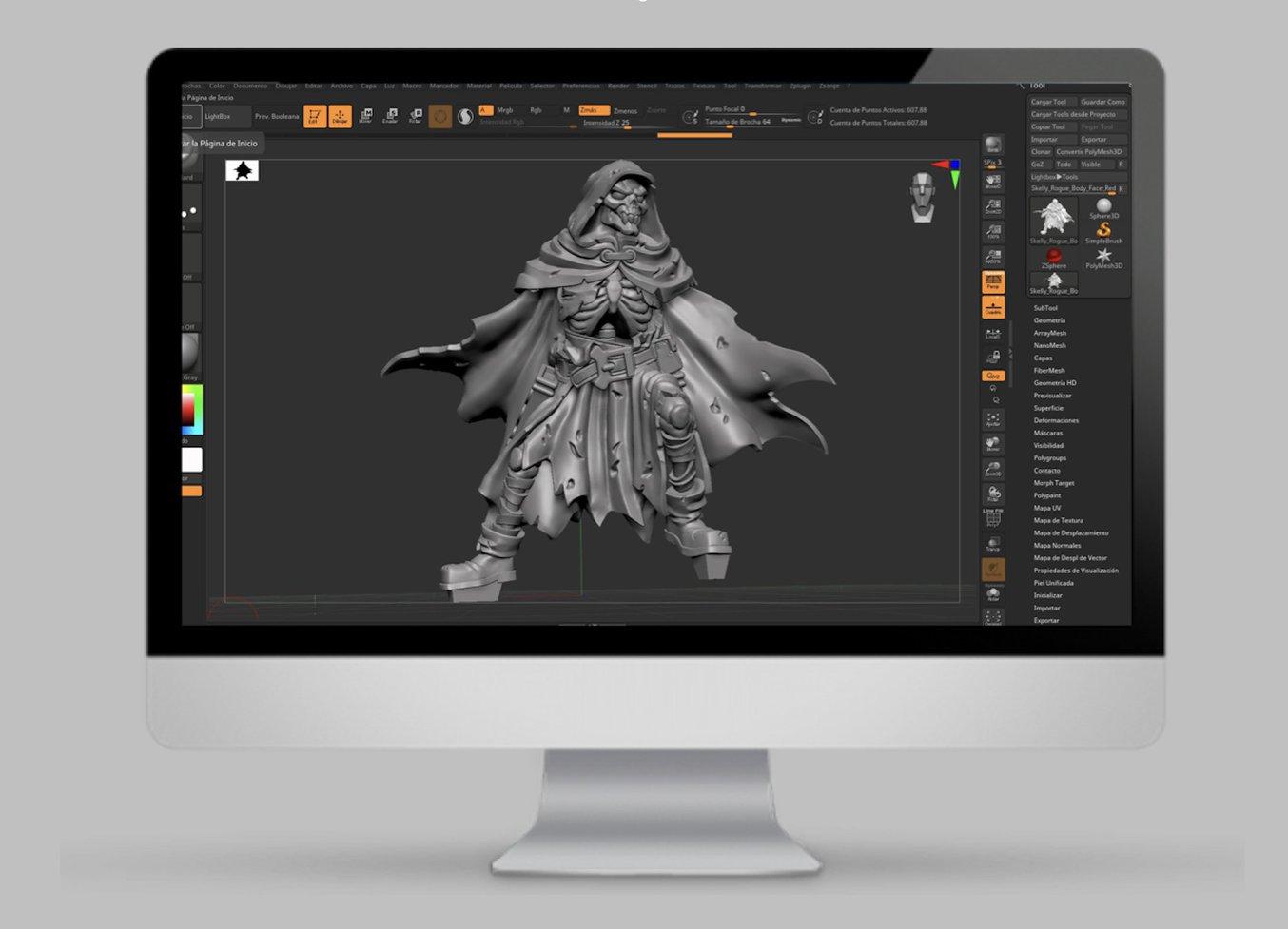
Design eines 3D-Modells von Broken Anvil Miniatures.
Mithilfe von CAD-Software modellieren Designteams die Teile so genau wie möglich, da die Details auf dem 3D-gedruckten Teil abgebildet, dann auf die SiOCAST-Form und schließlich auf das fertige Gussteil übertragen werden. Auch Designs mit starken Hinterschneidungen lassen sich mit dem SiOCAST-Verfahren fertigen. Derzeit liegt die maximale Dicke von Teilen aus dem SiOform1 bei 40 mm. Während des Prozesses werden aus der standardisierten Dateibibliothek auch die Angüsse für den Spritzguss hinzugefügt.
2. 3D-Druck der Urmodelle und Angusskanäle
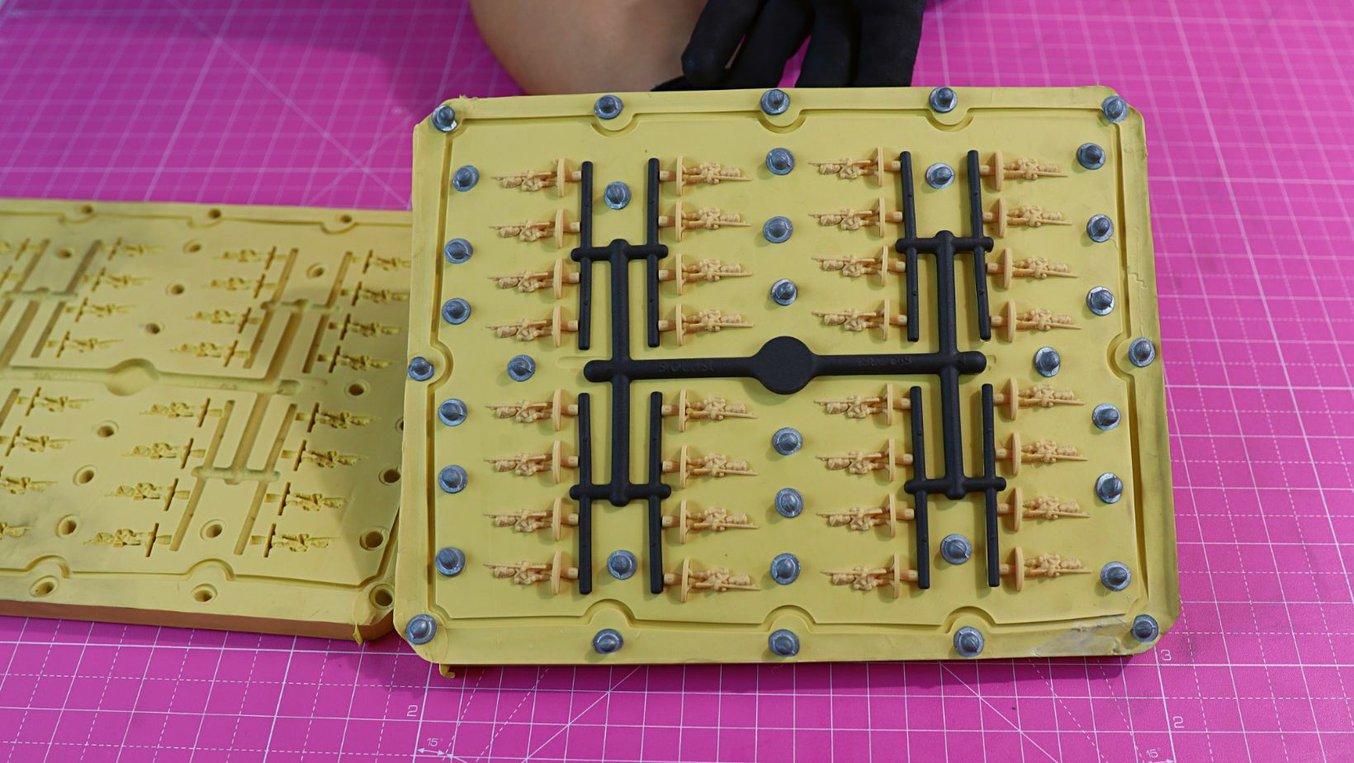
3D-gedruckte Urmodelle aus dem Form 3+ und Angusskanäle aus dem Fuse 1.
Sobald die digitale Form fertiggestellt ist, druckt SiOCAST mithilfe von Formlabs' Druckvorbereitungssoftware PreForm und dem SLA-3D-Drucker Form 3+ die Urmodelle aus Model V2 Resin, da dieses Material hohen Temperaturen standhält und geeignete mechanische Eigenschaften für den Vulkanisationsprozess bietet.
Die Teile werden in einem Winkel von etwa 45 Grad ausgerichtet. Schließen flache Oberflächen an die Konstruktionsplattform an, schrägt das Team die Kanten ab, um eine Beschädigung der Teile durch die Schaber zu vermeiden.
„Wir haben vier Formlabs-Drucker und die sind durchgehend im Einsatz. Auch bei unseren Kunden – sie besorgen sich das SiOCAST-System und brauchen einen oder zwei Formlabs-Drucker, um ihren Bedarf an Urmodellen abzudecken. Einige Kunden besitzen bis zu vier Formlabs-Geräte, weil sie einen so hohen Druckbedarf haben“, berichtet Ferran.
Mit dem SLA-3D-Drucker Form 3+ lassen sich in nur wenigen Stunden kostengünstige, hochwertige Urmodelle erstellen. Um den höchstmöglichen Detailgrad zu erreichen, druckt das Unternehmen Miniaturen bei einer Schichthöhe von 25 Mikrometern.
Wir haben bereits verschiedene Technologien und 3D-Drucker ausprobiert, DLP, SLA und SLS. Einige Kunden setzen für feinere Details auf DLP, aber dafür sind die Kunstharze womöglich weniger haltbar. Wir nutzen die Formlabs-SLA-Drucker größtenteils für Anwendungen, die einen hohen Detailgrad und Robustheit für die Vulkanisation erfordern. Jetzt weiten wir das auch auf technische Komponenten aus, und die 25 Mikrometer Schichthöhe des Form 3+ reicht für solche Arten von Modellen vollkommen aus.
Ferran Navarro, Geschäftsführer und Mitgründer von SiOCAST
Nach dem Druck der Teile werden sie mit den automatisierten Reinigungs- und Nachhärtesystemen von Formlabs nachbearbeitet, dem Form Wash und Form Cure.
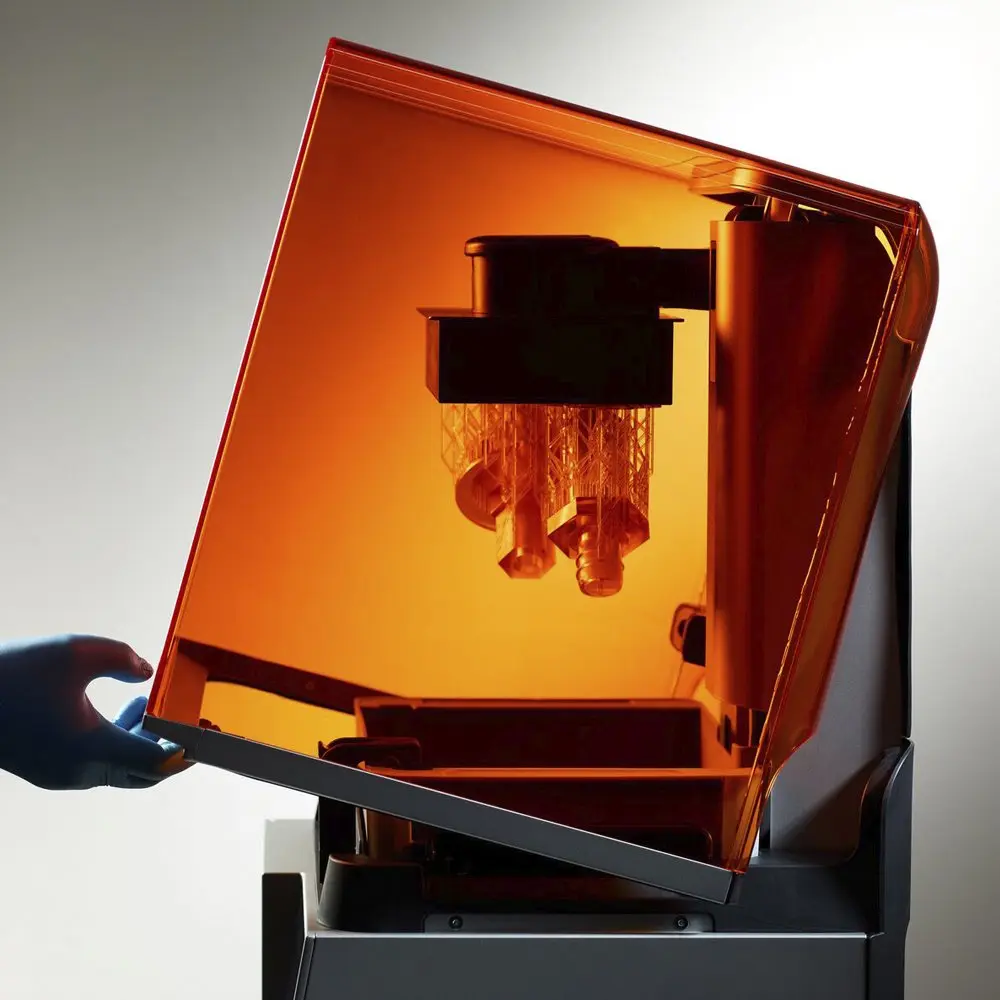
Einführung in den 3D-Druck mit Desktop-Stereolithografie (SLA)
Sie suchen einen 3D-Drucker, der Ihre 3D-Modelle in hochauflösender Qualität Wirklichkeit werden lässt? Lernen Sie in diesem Whitepaper das Verfahren der Stereolithografie (SLA) näher kennen – von seiner Funktionsweise bis hin zu den Gründen für seinen Status als populärste 3D-Drucktechnologie für die Umsetzung hochgradig detailtreuer Modelle.
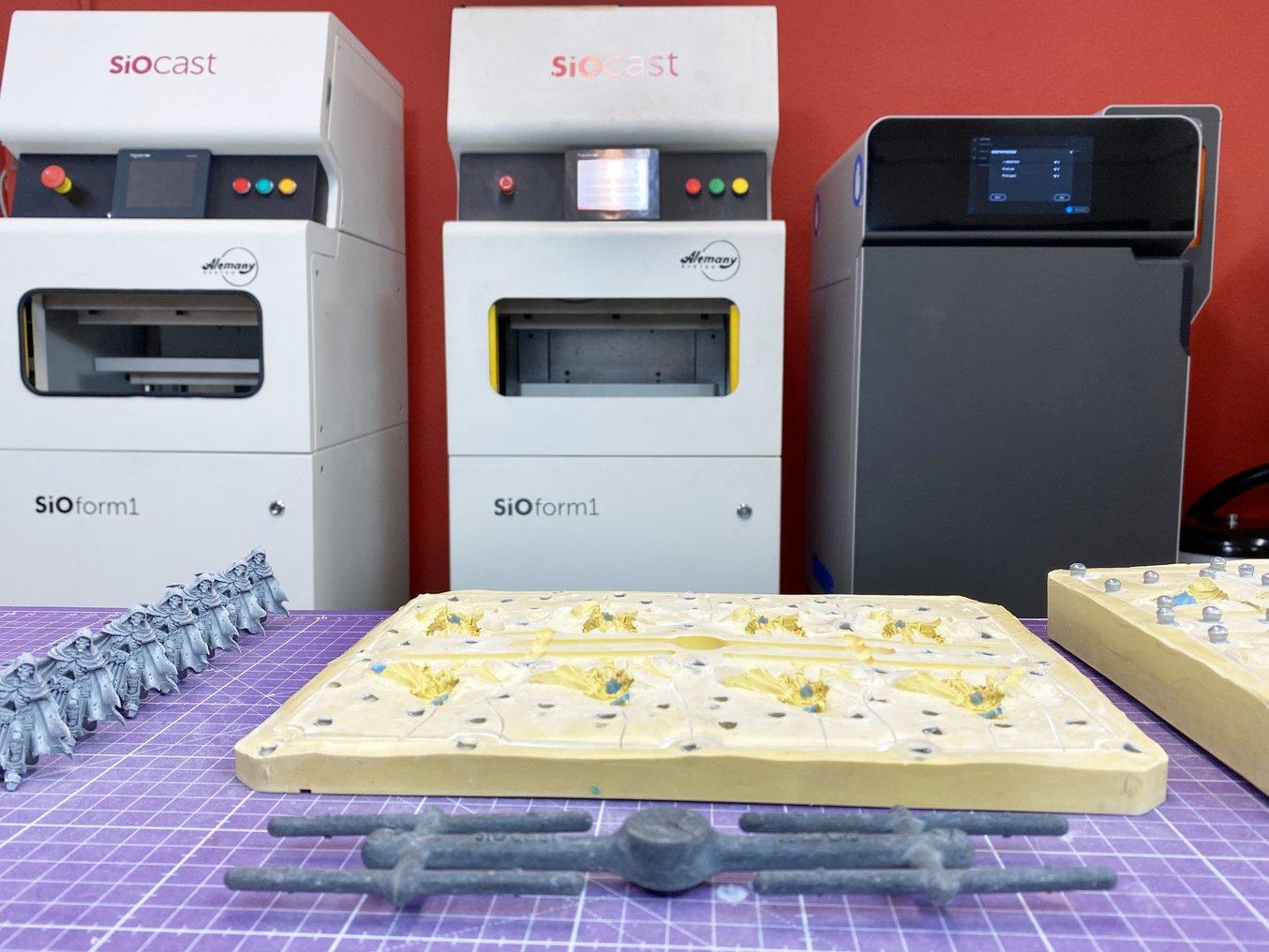
3D-gedruckte Angusskanäle aus dem Fuse 1.
SiOCAST setzt den 3D-Druck nicht nur bei der Herstellung von Urmodellen ein, sondern auch für die im Gussprozess benötigten Angusskanäle. Für diese Anwendung nutzt das Team einen Formlabs-3D-Drucker für selektives Lasersintern (SLS), den Fuse 1. Die SLS-Angusskanäle sind robust und können ohne Stützstrukturen zu großer Zahl in der Konstruktionskammer untergebracht werden, sodass SiOCAST seine Kundschaft auf der ganzen Welt damit versorgen kann.
Der Fuse 1 beschleunigt unsere Designprozesse, sodass wir zahlreiche Iterationen der Kanäle durchführen können. In einem internen F&E-Projekt sind wir in den vergangenen zwei Wochen weiter vorangekommen als in den letzten zwei Jahren.
Ferran Navarro, Geschäftsführer und Mitgründer von SiOCAST
Der Prozess des 3D-Drucks mit SLS ist ähnlich wie das SLA-Verfahren: Die Druckdatei wird in PreForm vorbereitet und dann auf dem 3D-Drucker Fuse 1 aus Nylon 12 Powder gedruckt. Danach werden im Fuse Sift die Nachbearbeitungsschritte erledigt. SiOCAST verwendet außerdem die Nachbearbeitungslösung Abrast von Coniex zur Reinigung der Oberfläche, die speziell für additiv gefertigte Teile entwickelt wurde.
3. Silikonformenbau mit Vulkanisation
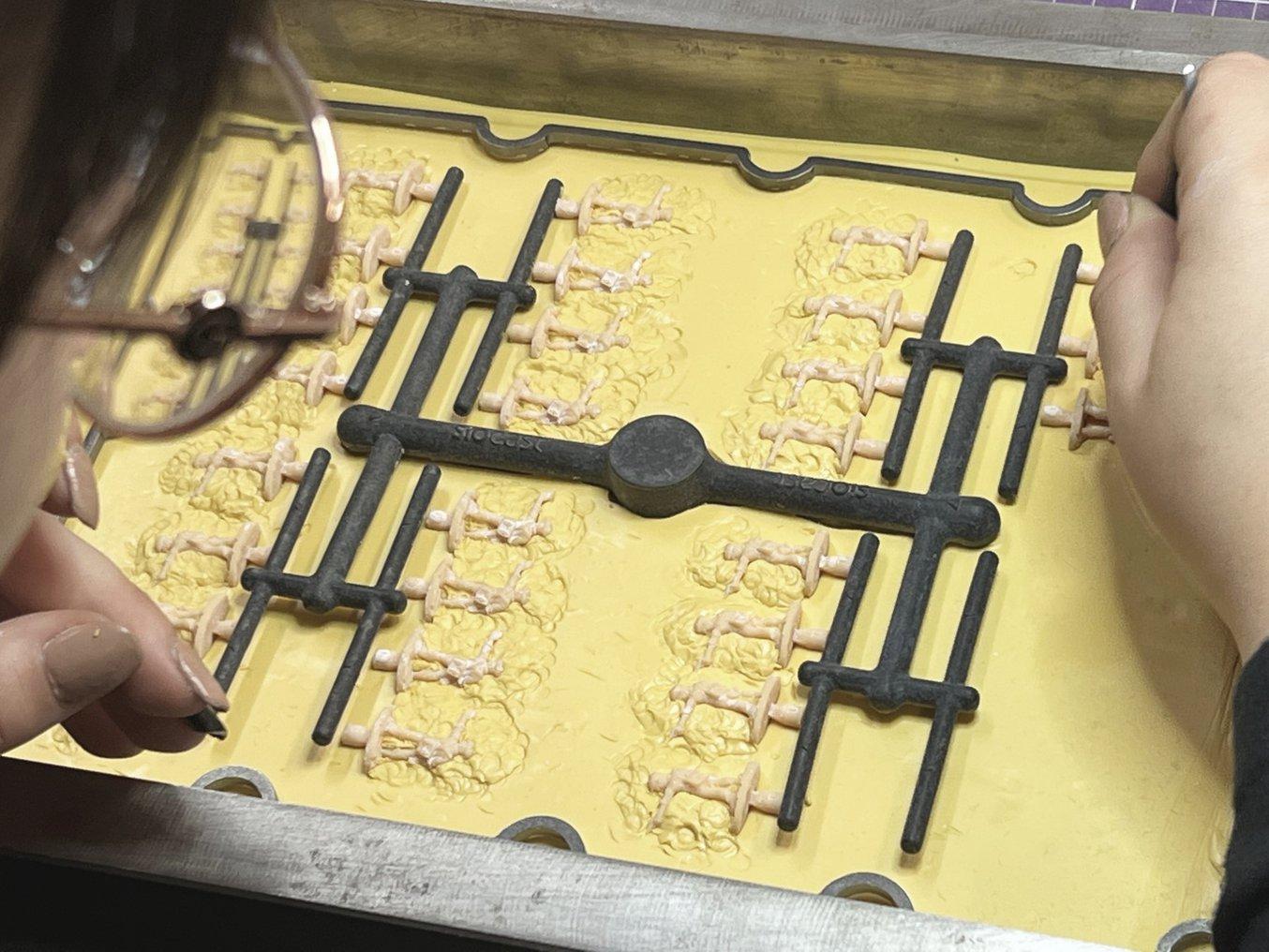
Vorbereitung der Form für die Vulkanisation.
Stehen die 3D-gedruckten Urmodelle und Angusskanäle erst einmal bereit, ist der nächste Schritt die Herstellung der Formen mit dem Silikonkautschuk SiOmold. Das ist SiOCASTs hartes HTV-Silikonmaterial (bei hohen Temperaturen vulkanisiert) mit einer Shore-Härte von 65A oder 80A, das aus einem von der CONIEX-Gruppe speziell hergestellten Elastomer mit überragender thermischer und mechanischer Beständigkeit besteht. Das Silikonlaminat wird in einen starren, präzisen Metallrahmen eingefüllt, der über CNC-Zerspanung gefertigt wird. Dann werden die 3D-gedruckten Urmodelle gleichmäßig auf dem Silikon platziert und vorsichtig eingebettet, indem mehr Silikon um sie herum eingefüllt wird, um die gewünschte Trennlinie zu erzielen. Die SLS-3D-gedruckten Angusskanäle werden ebenfalls eingelegt und in die entstehende Platte gedrückt.
Zentrierhilfen werden eingefügt, um die zwei Hälften der Form zusammenzuhalten. Anschließend wird die Oberfläche mit Talkum bedeckt, das als Trennmittel dient und verhindert, dass die zwei Seiten der Silikonform aneinander haften. Die obere Silikonschicht wird eingefüllt und der kastenförmige Metallrahmen wird geschlossen. Je nach der Komplexität der Form kann dieser Prozess einen Zeitraum von zehn Minuten bis zu zwei oder drei Stunden umfassen.
Der Metallrahmen wird dann in die Vulkanisierpresse SiOpress eingesetzt, wo das Silikon und die 3D-gedruckten Modelle einem Druck von 10 bar und einer Temperatur von 120 °C ausgesetzt werden, um Luft zu entlassen. Während des Vulkanisationsprozesses von 40 bis 60 Minuten verflüssigt sich das Silikon, wobei es sämtliche Oberflächendetails der 3D-gedruckten Urmodelle genau erfasst, um schließlich durch das Verbinden der Elastomerketten zu einer vulkanisierten Form auszuhärten.
Nach der Abkühlung wird die Form geöffnet und die 3D-gedruckten Urmodelle werden aus den Hohlräumen entnommen, sodass nur die endgültige Gussform zurückbleibt, die in der SiOCAST-Maschine verwendet wird. Die 3D-gedruckten Urmodelle können für weitere Durchgänge der Vulkanisation wiederverwendet werden.
Wir nutzen ein spezielles Trennmittel, damit die 3D-gedruckten Modelle nach der Vulkanisation nicht am Silikon haften und für die Herstellung der nächsten Form wiederverwendet werden können. Generell halten Urmodelle aus Formlabs-3D-Druckern insgesamt drei bis vier oder sogar mehr Vulkanisationen aus.
Ferran Navarro, Geschäftsführer und Mitgründer von SiOCAST
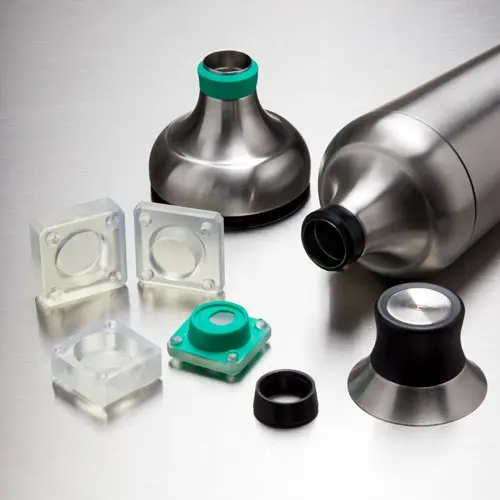
Silikonformenbau für das Produktdesign
Laden Sie diesen Bericht mit Fallstudien von OXO, Tinta Crayons und Dame Products herunter, um von drei verschiedenen Umsetzungen des Silikonformenbaus in Produktdesign und Fertigung zu erfahren, einschließlich Umspritzung und Insert-Molding.
4. Produktion von Miniaturen mit dem SiOform1
Im SiOform1 werden die beiden Hälften der vulkanisierten Silikonform aneinandergefügt und im Gerät platziert, das Material zum Spritzguss wird ausgewählt und mit einem Knopfdruck ist die Maschine bereits in Betrieb: Sie entzieht die Luft aus der Form und spritzt das flüssige thermoplastische Kunstharz bei einer Temperatur von 240 °C ein.
Nachdem die Form abgekühlt ist, kann sie aus der Maschine entfernt werden. Dieser Teil des Verfahrens dauert nur etwa 30 Sekunden (oder bis zu einer Minute bei dickeren Formen) und es kann sofort eine neue Form für die nächste Charge eingesetzt werden.
Nach ein paar Minuten Abkühlzeit außerhalb des Geräts kann die erste Charge Miniaturen entformt und aus den Angusskanälen gelöst werden. Dank der Kombination von SiOCASTs thermoplastischem Kunstharz mit dem intern entwickelten Silikonkautschuk lassen sich die Miniaturen leicht aus der Form entfernen.
Jeder Guss ergibt durchschnittlich vier bis 64 Miniaturen, abhängig von der Größe der Teile und dem Volumen, das auf 100 g pro Schuss begrenzt ist. Der gesamte Prozess ist etwa zehn bis zwanzigmal schneller als traditioneller Kunstharzguss.
Die Formen können während der Abkühlphase rotiert werden, statt sie direkt wieder in die Maschine einzusetzen. Normalerweise arbeitet man mit drei bis neun verschiedenen Formen in Rotation. Es können 25-40 Güsse pro Stunde durchgeführt werden. Wenn es ein Automatisierungssystem gibt, schaffen wir es auf bis zu 60-80 Schüsse pro Stunde, was 100 bis 1000 Teile pro Stunde ergibt, alle mit demselben Detailgrad wie das ursprüngliche 3D-gedruckte Modell.
Ferran Navarro, Geschäftsführer und Mitgründer von SiOCAST
Jede Silikonform ist 210 x 270 Millimeter groß und kann bis zu 50 Millimeter dick sein, wodurch sich Teile mit einer Dicke von bis zu 40 Millimetern unterbringen lassen. Die Formen halten etwa 300-500 Güssen stand und sind somit eine taugliche Option sowohl für Klein- als auch Großserien.
Kunden können von SiOCAST entweder über den readyCAST-Service direkt fertige Silikonformen erwerben oder ihre eigenen Formen herstellen, was die allgemein bevorzugte Option ist. Das Unternehmen bietet ein komplettes Schulungspaket an, um Neukunden durch jeden Schritt ihres Einstiegs zu führen.
Ein System, das die Branche revolutioniert
Der direkte 3D-Druck von Miniaturen ist für den Hobbybereich und Einzelstücke oder kleine Serien immer noch eine tolle Option, doch für die professionelle Miniaturenfertigung hat SiOCAST einen neuen Maßstab gesetzt.
Endkunden berichten, dass sie haltbarere, detailreichere Teile erhalten, die sich leichter bemalen lassen, und dass Kunstharzguss, Metallminiaturen oder Spritzgussteile keine vergleichbaren Ergebnisse liefern.
Unternehmen wie Monster Fight Club (The Witcher, Cyberpunk RED), Warlord Games (Blood Red Skies, Bolt Action), Reaper Miniatures (Bones USA), Titan Forge Miniatures, Corvus Belli (Infinity the Universe), Yedharo Models und Creature Caster sind einige der Akteure der Branche, die auf das System von SiOCAST umgestiegen sind.
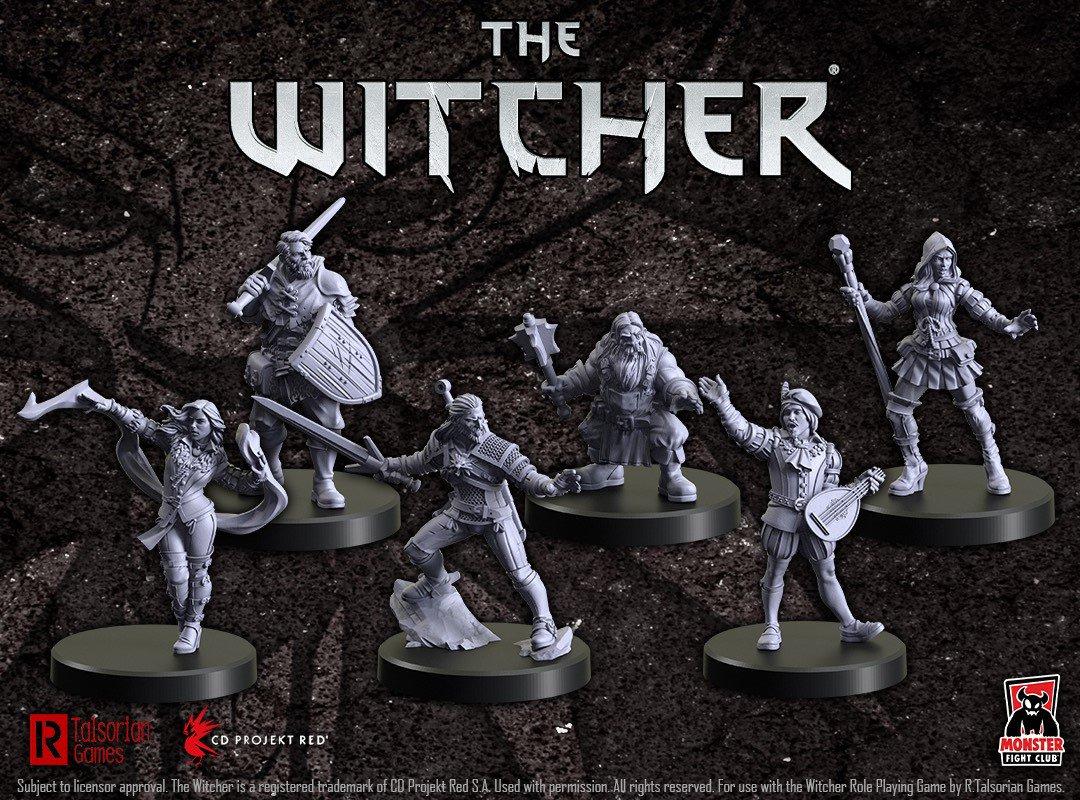
Monster Fight Club Miniaturen von The Witcher.
Der Miniaturmarkt, aber auch die Anime- und Manga-Branche haben das System von SiOCAST sehr gut aufgenommen.
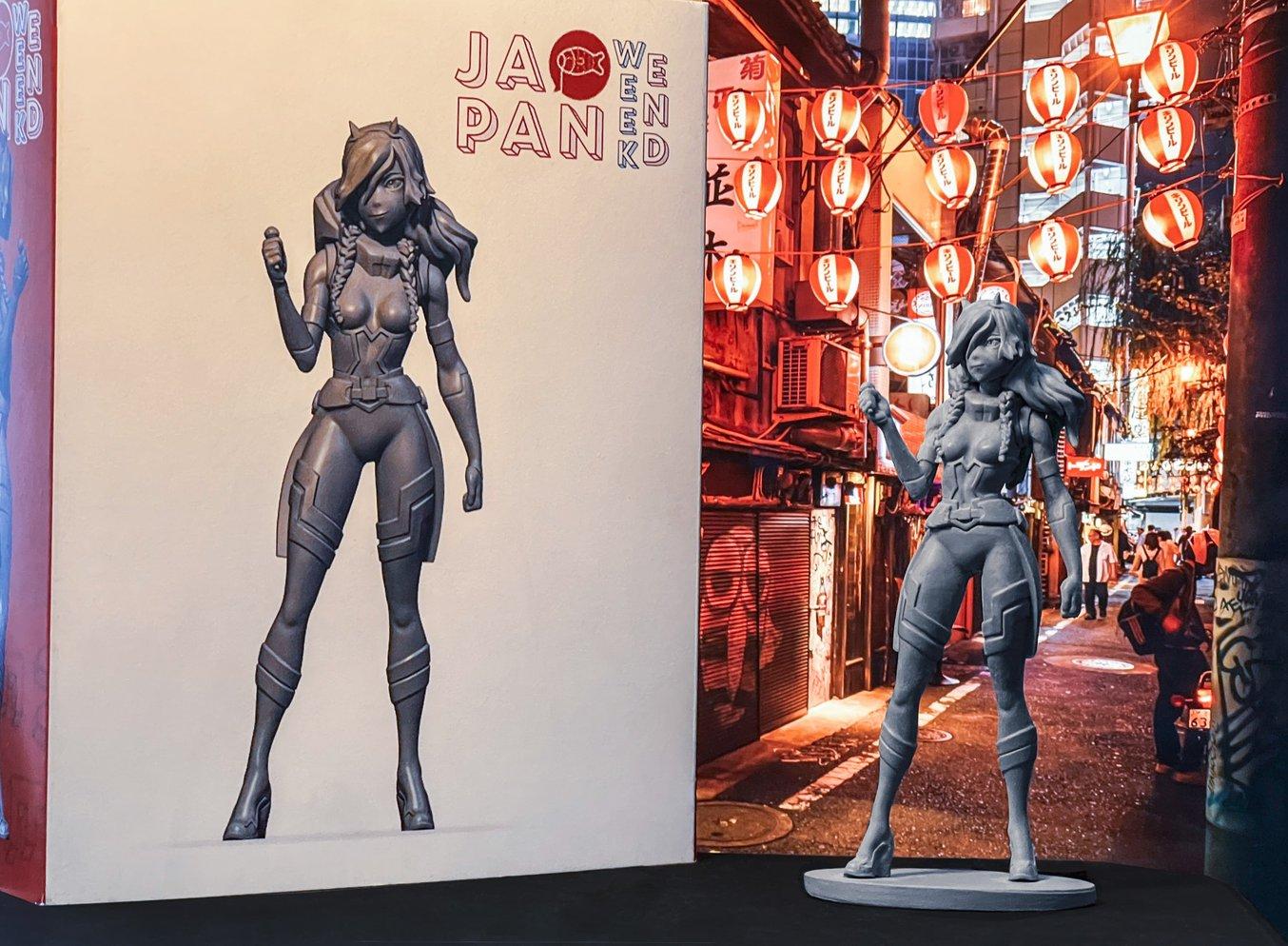
Miniatur von Japan Weekend, hergestellt mit SiOCAST.
Das Unternehmen expandiert außerdem in den Markt der Modelllandschaften und hat bereits mit einigen maßgeblichen Herstellern im Bereich Landschaftsmodellierung zusammengearbeitet.
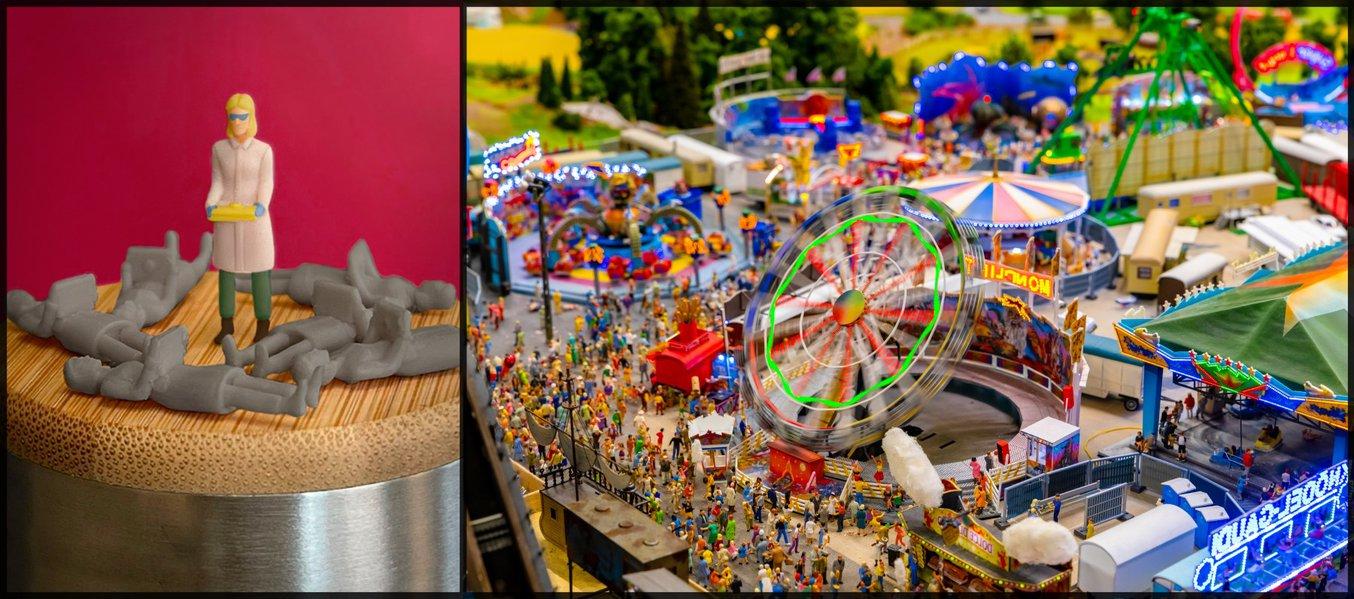
Modelllandschaft des Miniatur Wunderlands.
Einige Hersteller von Rollenspielen wie Galladoria Games übertragen die Vorteile des SiOCAST-Systems auch auf den Markt für Geländeteile und Szenografie. Die Zahl der Unternehmen in der Miniaturbranche, die zum System von SiOCAST wechseln, steigt täglich weiter an.
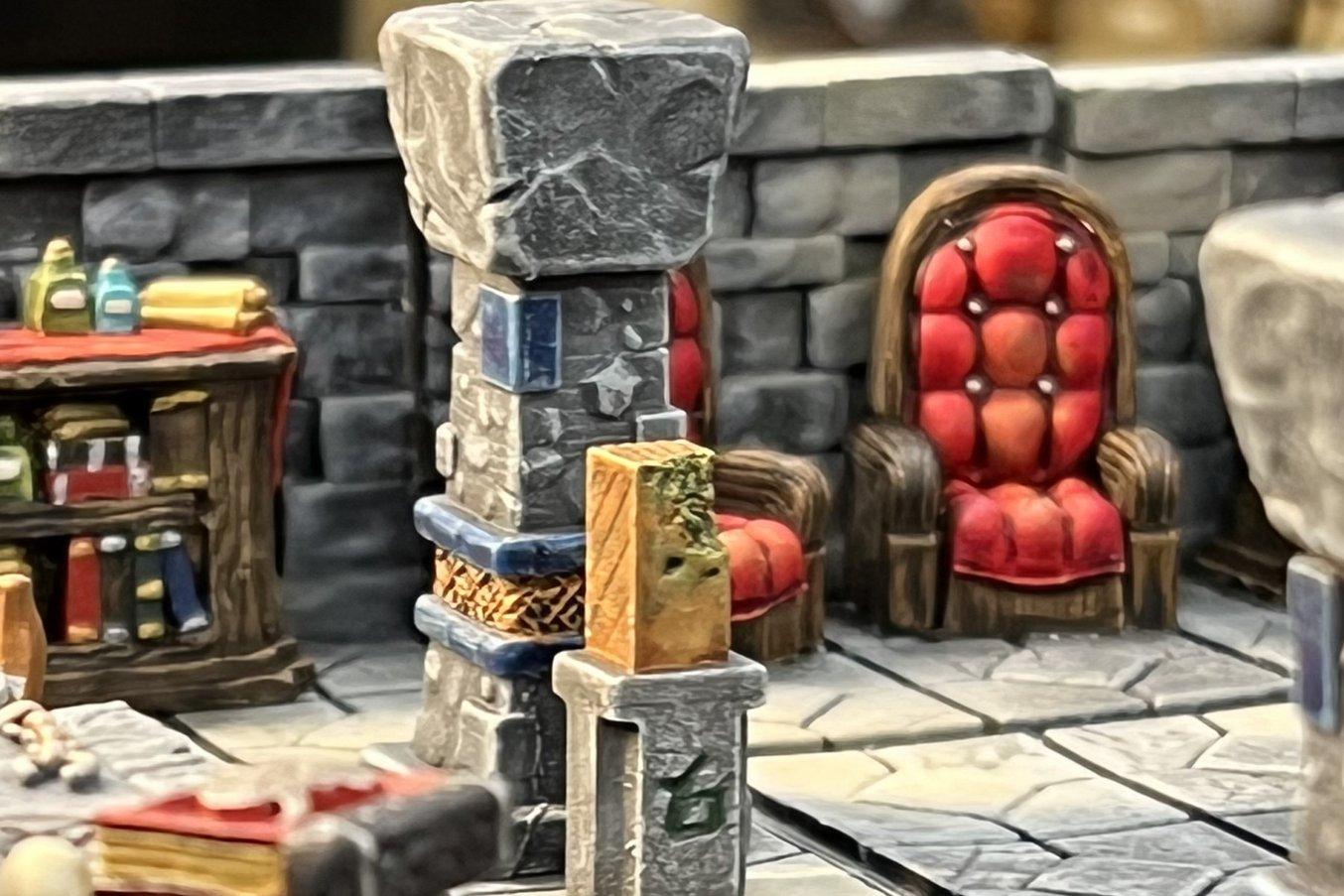
Gelände für D&D von Galladoria.
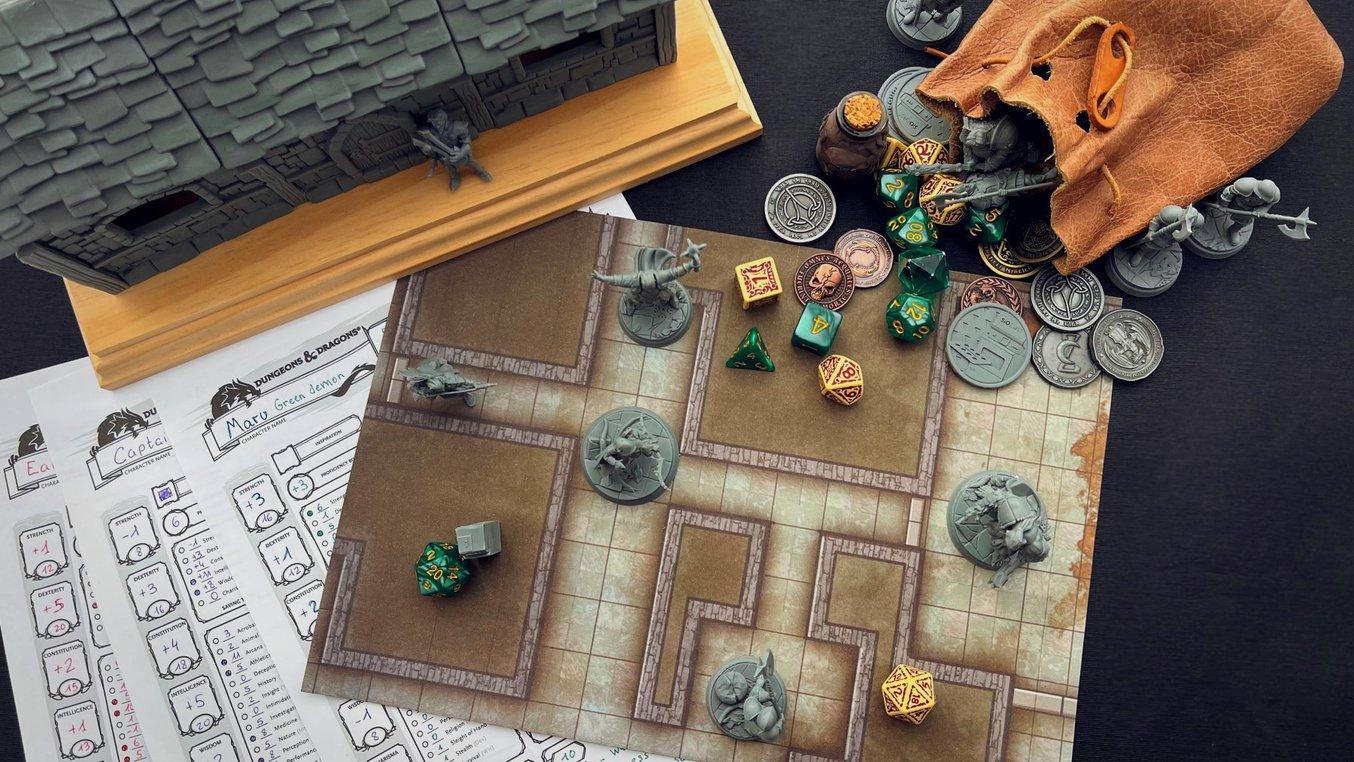
Teile für Dungeons & Dragons, hergestellt mit SiOCAST.
Lokal gefertigt
Das neue Produktionssystem bringt die Räder der Branche richtig ins Rollen. Wie Ferran anmerkt, können nur ein paar Miniaturenhersteller auf der Welt ihre Kunststofffertigung vollständig betriebsintern umsetzen, wenn konventionelle Verfahren genutzt werden. Die meisten Unternehmen sind auf Zulieferung von China angewiesen, was üblicherweise mit hohen Logistikkosten sowie langen Lieferzeiten und hohen Mindestbestellmengen verbunden ist. Dank SiOCAST können nun jedoch Unternehmen jeder Größenordnung ihre Produktion in den eigenen Betrieb verlegen.
So stellt etwa die Kollektion Bones USA von Reaper Miniature nicht nur einen Umstieg von Metallminiaturen zu Thermoplastminiaturen mit SiOCAST dar, sondern bedeutete auch eine Umsiedlung der Produktion von China in die Vereinigten Staaten.
Umweltfreundlich und abfallfrei
SiOCAST betont außerdem, dass ihre intern entwickelten Kunststoffmaterialien SiOres nicht toxisch und nach EN-71 als sicher für Spielzeug zertifiziert sind, sowie dass das Produktionssystem umweltfreundlich ist. Das für den Guss von Miniaturen verwendete Kunstharz ist wiederverwendbar, sodass misslungene Gussteile oder Angusskanäle zermahlen und mit neuem Material vermischt werden können – damit ist das Kunststoffsystem abfallfrei.
Die lokale Produktion mit einem nach Bedarf anpassbaren System macht Inventarbestände oder Abfälle durch unverkaufte Produkte überflüssig. Zusammen mit der Kompaktheit der Geräte, die für die Miniaturenproduktion benötigt werden, sorgt das für einen geringen Platzbedarf.
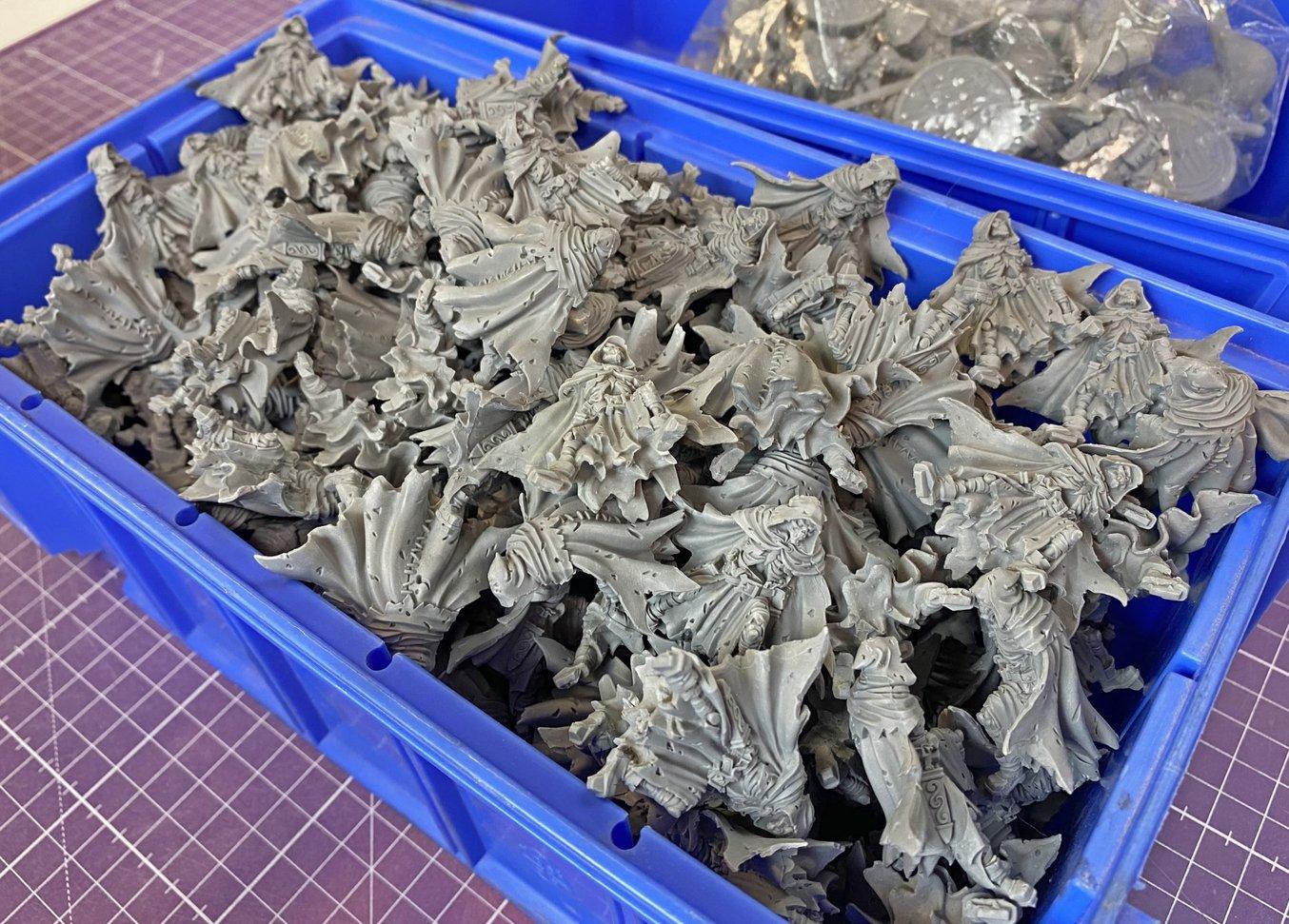
Örtlich produzierte, hochwertige Miniaturen von Broken Anvil Miniature.
Ferran erklärt, selbst in einem Raum von gerade einmal zehn Quadratmetern könne man „seine eigene Fertigungsanlage mit hohem Durchsatz betreiben. Das ist mit Spritzgussmaschinen mit manueller Tischpresse nicht möglich; das sind wirklich schöne Maschinen, aber hinsichtlich Größe und Kapazität sind sie sehr eingeschränkt.“
„Beim Spritzguss fällt durch die Angusskanäle viel Abfall an. Etwa 20 % des Kunststoffs landen im Müll. Die Miniaturen werden normalerweise im Ausland hergestellt und müssen erst ins Inland geliefert werden. Außerdem muss der Hersteller gleich 20 000 Einheiten fertigen, von denen er vielleicht die Hälfte verkauft, während er den Rest entsorgt. Spritzguss lohnt sich also für große Mengen, es ist kosteneffizient, aber nicht besonders umweltfreundlich und hat eine hohe CO2-Bilanz. Bei Kunstharzgusssystemen entstehen etwa 20-mal mehr Silikonrückstände als mit SiOCAST, und außerdem werden etwa 30-40 % des toxischen Kunstharzes für Angusskanäle verschwendet, die niemals genutzt werden“, fügt Ferran hinzu.
Hochwertige detailreiche Teile zu erschwinglichen Preisen
Wenn es um die Frage geht, was den Kunden bei Miniaturen wichtig ist, nennen sie an erster Stelle immer den Detailgrad.
Ein so hohes Maß an Detailliertheit zu erschwinglichen Kosten zu erreichen ist jedoch eine wahre Herausforderung. Ferran erläutert: „Worauf es allen bei jeder Anwendung ankommt, ist, die Vorteile des günstigen Werkzeugbaus und des hohen Detailgrads, der sich mit Silikon abbilden lässt, mit der Produktivität industrieller Technologien wie Spritzguss zu vereinen.“
Ein weiteres Erfolgsbeispiel ist das Unternehmen Warlord Games, das mit dem SiOCAST-Verfahren über 400 000 Einheiten eines Flugzeugs für Blood Red Skies in vier verschiedenen Farben herstellen konnte. Eine derartige Großserienproduktion wäre üblicherweise nur mit Spritzguss möglich gewesen, hätte dabei jedoch nicht denselben Detailgrad erzielt.
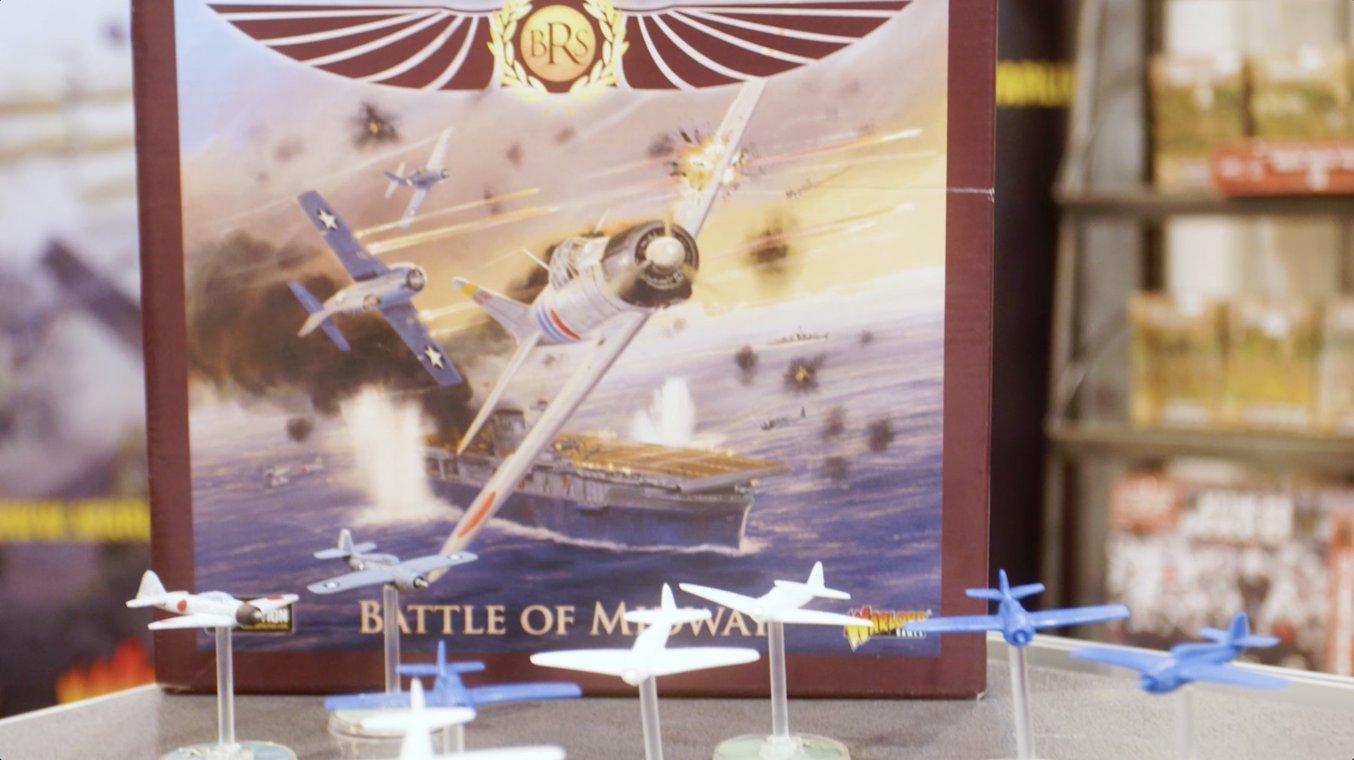
Mehr als 400 000 Einheiten des Flugzeugs für Blood Red Skies wurden mit SiOCAST hergestellt.
Beim Spritzguss liegt die Gewinnschwelle bei etwa 10 bis 15 Tausend Einheiten eines einzigen Produktes, da die Kosten der Gussform sich auf fünf bis zehntausend Euro belaufen können. Spritzgusskunststoffe sind natürlich sehr günstig, doch zum Materialpreis kommen noch Lieferzeiten, Verfügbarkeit und der Detailgrad hinzu. Selbst die qualitativ hochwertigsten Miniaturenhersteller der Branche, die mit Spritzguss arbeiten, erzielen nicht solche Details, wie sie mit Silikon erreicht werden. Es ist ein ziemlich deutlicher Unterschied.
Ferran Navarro, Geschäftsführer und Mitgründer von SiOCAST
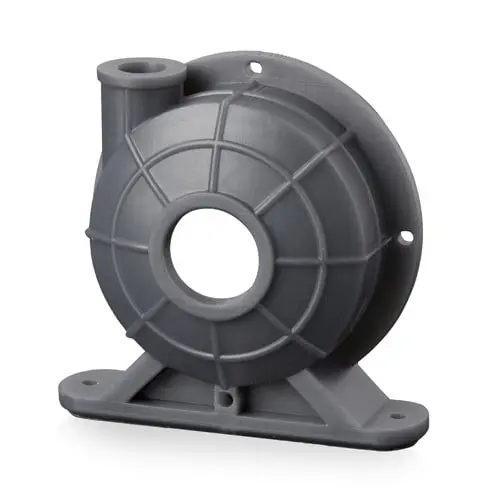
Fordern Sie einen kostenlosen 3D-Probedruck an
Begutachten Sie ein 3D-gedrucktes Modell in hoher Auflösung aus erster Hand. Wir senden Ihnen einen kostenlosen Probedruck an Ihren Arbeitsplatz.
Die Ausdehnung auf neue Anwendungen
Das SiOCAST-System erzielte auch in anderen Branchen und Anwendungsbereichen gute Resonanz, wie etwa in der Herstellung von Schuhen, Tastenabdeckungen, medizinischen Verbindungsteilen, Komponenten für Umspritzung und sonstigen weichen, robusten Teilen. Einer der Kunden stellt zum Beispiel Räder und Schalter für einen Flugsimulator her, wofür er Modelle nutzte, die auf dem Fuse 1 und Form 3+ 3D-gedruckt wurden. Die Vorteile von SiOCAST ermöglichen diesem Unternehmen die Produktion von Endverbrauchsteilen mit hoher Oberflächenqualität, bei lokaler Fertigung mit kurzen Durchlaufzeiten und zu geringen Kosten. Diese Kriterien werden derzeit von keiner anderen Technologie erfüllt.
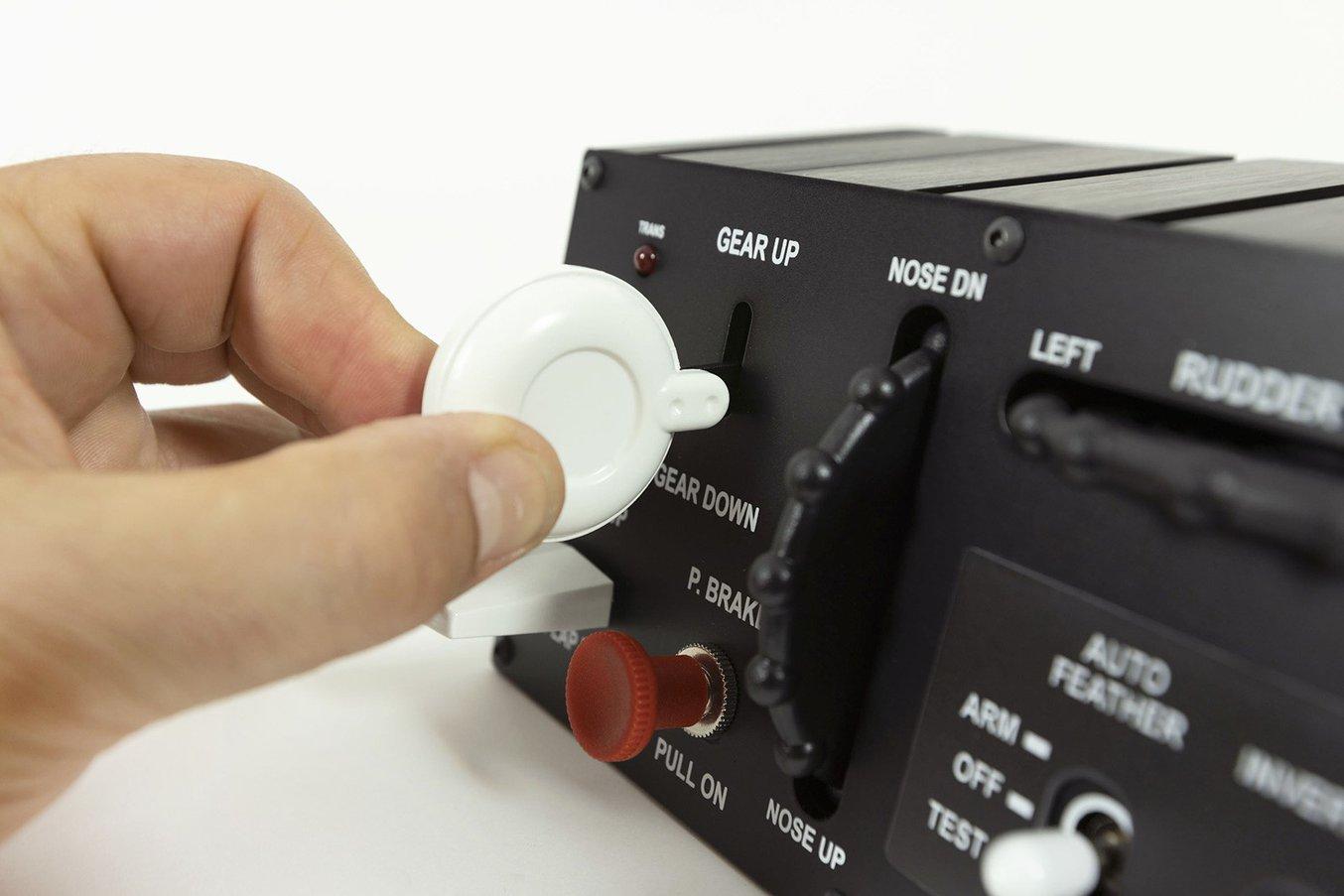
Komponente eines Flugsimulators von Aplica Design, hergestellt mit SiOCAST.
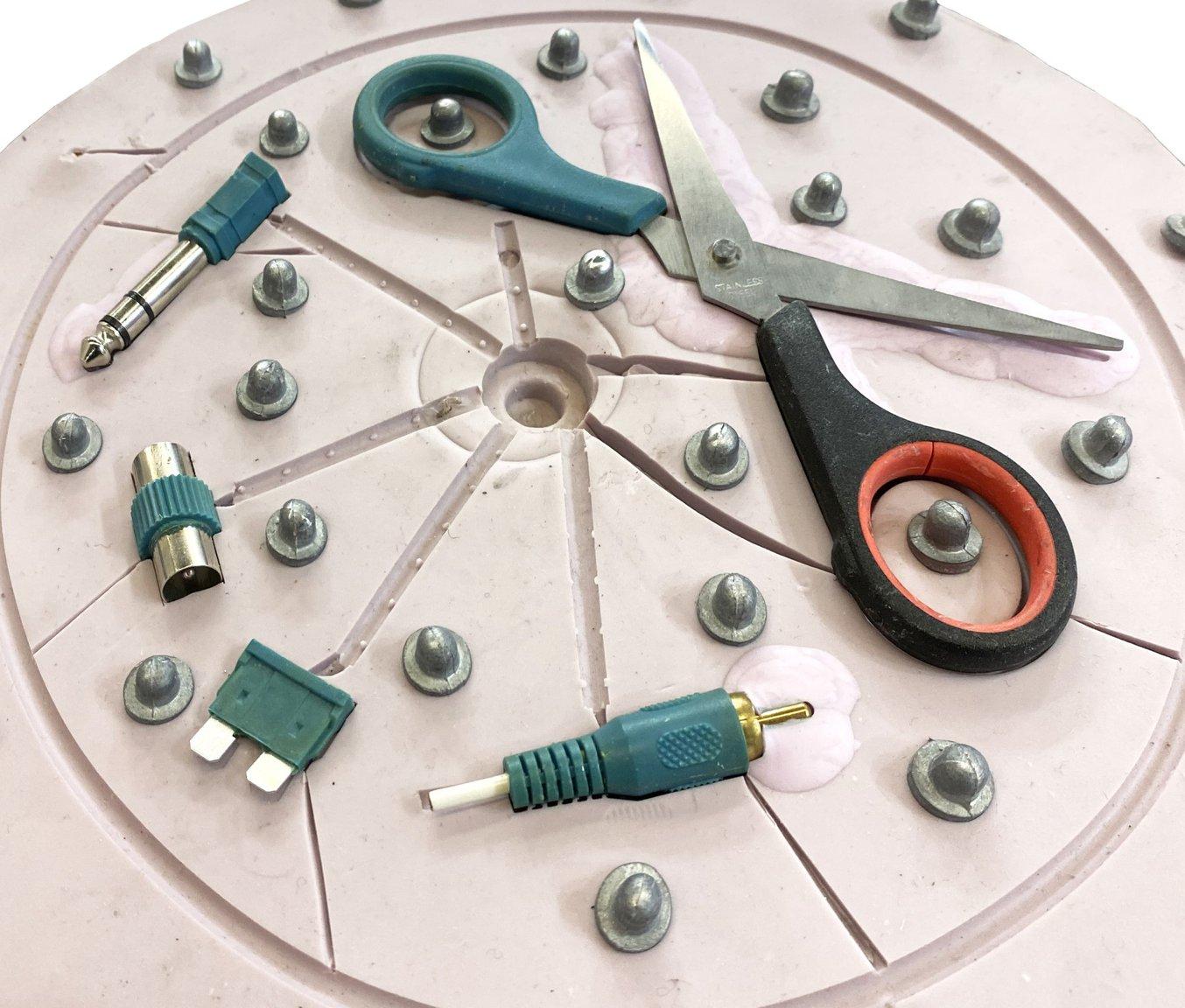
Umspritzung mit SiOCAST-Formen.
„Dass Miniaturen unser erster Geschäftsbereich waren, lag daran, dass wir uns damit bereits auskannten, aber es gibt noch Tausende weitere Anwendungsmöglichkeiten“, so Ferran.