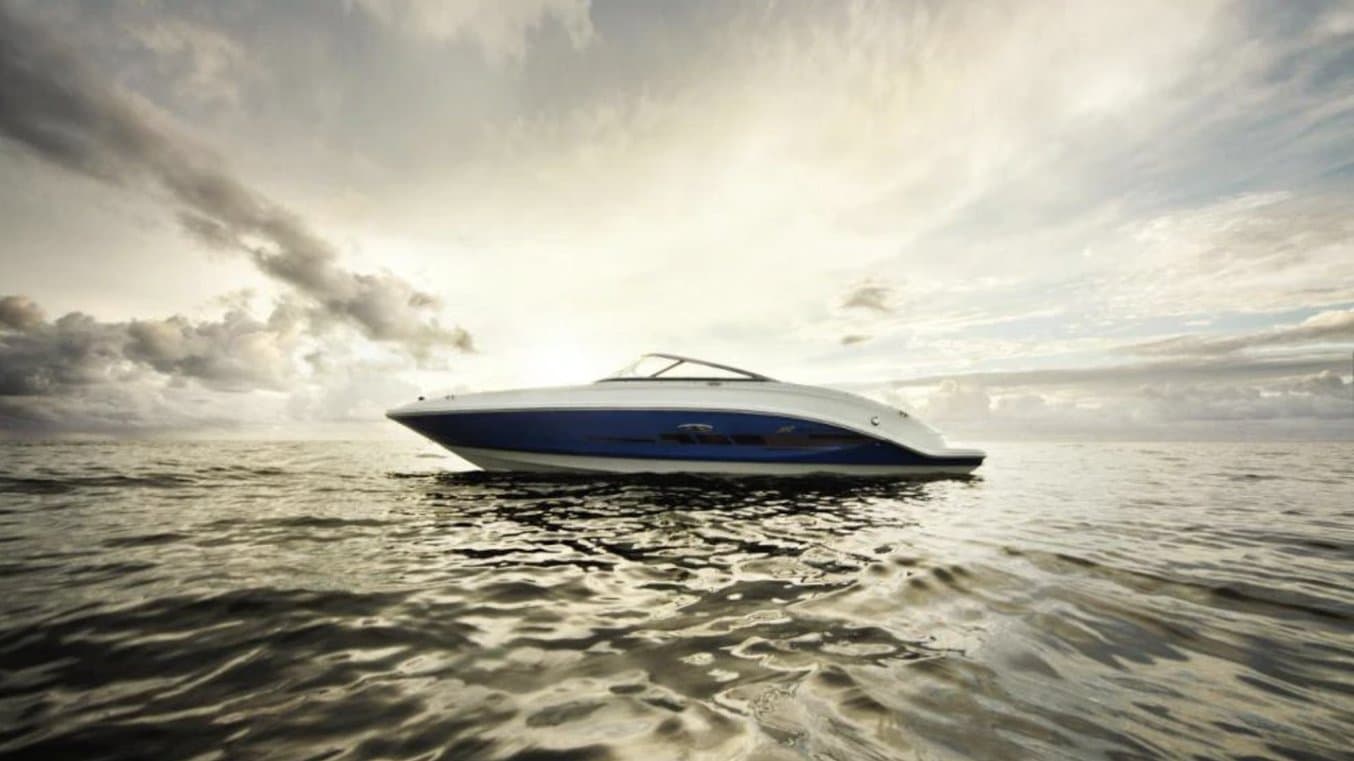
JetBoatPilot ist ein Hersteller von Zubehör- und Nachrüstteilen mit speziellem Fokus auf Wasserfahrzeugen. Einen Namen hat sich das Unternehmen mit seinen Produkten zur Nachrüstung von Jetbooten gemacht, die die Leistung und insbesondere die Manövrierbarkeit dieser Bootsklasse bei niedrigen Geschwindigkeiten verbessern. Denn aufgrund ihres Wasserstrahlantriebs verhalten sich Jetboote bei langsamer Fahrt etwa zum Anlegen oder in Ruhezonen deutlich anders als Motorboote, die über einen klassischen Heckantrieb verfügen. Wer mit diesen Manövern weniger vertraut ist, rüstet daher häufig speziell für Jetboote konzipierte Lenkhilfen nach, um die Steuerung bei niedriger Geschwindigkeit zu erleichtern.
Genau hierauf sind die Produkte von JetBoatPilot ausgelegt: Durch Verbesserung der Steuereigenschaften von Jetbooten helfen sie den Seefahrern dabei, bei langsamer Fahrt sicherer zu navigieren. Bei der Entwicklung von Prototypen sowie auch bei der Fertigung der Endprodukte hat JetBoatPilot seinerseits Hilfe zur Hand: 3D-Drucktechnologie ermöglicht es dem Unternehmen, mit agilen Fertigungsprozessen schnell auf die Kundennachfragen und das Produktangebot zu reagieren.
Als Hersteller von Zubehör und Nachrüstungen operiert JetBoatPilot im Aftermarket und produziert daher in der Regel vergleichsweise geringe Stückzahlen. Zudem muss das Unternehmen sicherstellen, dass seine Teile immer den Neuerungen und Weiterentwicklungen der ursprünglichen Bootshersteller folgen. Für ein solches Geschäftsmodell ist Agilität in der Fertigung entscheidend: Es braucht eine Lösung, mit der sich die Iteration ebenso wie die Produktion von Hochleistungsteilen nicht nur schnell, sondern auch kosteneffizient und ohne teure Werkzeugbestückung umsetzen lassen.
Genau dies erreicht JetBoatPilot mit den 3D-Druckern von Formlabs. So setzt das Unternehmen mit dem Form 3 auf Stereolithographie (SLA) und mit dem Fuse 1 auf selektives Lasersintern (SLS) und nutzt beide Drucker für die Entwicklung der Prototypen wie auch bei der Fertigung seiner Aftermarket-Produkte. So etwa auch für den Lateral Thruster 2.0: Design und Fertigung dieses neu konzipierten Produkts, das inzwischen zu den Verkaufsschlagern des Unternehmens gehört, erfolgten mit dem Fuse 1 – und zwar äußerst effizient. Mit dem Fuse 1 und Nylon 12 Powder als Fertigungsmaterial betrugen die Kosten gerade einmal ein Sechstel von dem, was JetBoatPilot mit seinen früheren Produktionsverfahren veranschlagen musste.
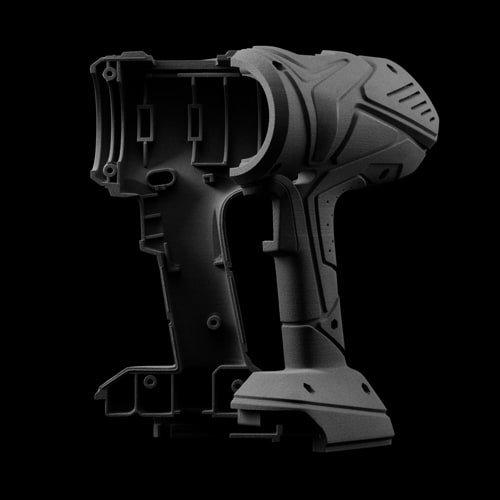
Einführung in den 3D-Druck mit selektivem Lasersintern (SLS)
Suchen Sie nach einem 3D-Drucker, mit dem Sie starke, funktionsfähige Teile herstellen können? Laden Sie unser Whitepaper herunter und erfahren Sie, wie SLS-Druck funktioniert und wieso es ein beliebtes 3D-Druckverfahren für funktionales Prototyping und die Produktion von Teilen für die Endverwendung ist.
Ein Problem als Gründungsmoment
Die Idee zur Gründung von JetBoatPilot entstand im Jahr 2010, als Will Owen im Rahmen seiner damaligen Tätigkeit als Yamaha-Vertreter selbst noch Jetboote in Panama City (Florida) verkaufte. Da das Bootsgeschäft in der Nebensaison eher ruhig läuft, beschloss er, kurze Tutorial-Videos für Yamaha-Kunden zu erstellen. Gedacht waren diese in erster Linie als Anleitung zur Optimierung der Leistung der Boote. Doch allmählich entwickelte sich rund um diese Videos eine Community aus Bootsbesitzern, die ihre Erfahrungen austauschten. So kanalisierte sich dort logischerweise auch ihr Frust über häufig erlebte Probleme. Dabei fiel Owen auf: Ganz gleich, aus welchen Landesteilen die Bootsbesitzer stammten, ihr Unmut drehte sich immer wieder um die gleiche Problematik.
„Man hörte immer wieder dasselbe: ‚Wunderbar wendig bei voller Fahrt, bei niedriger Geschwindigkeit kaum steuerbar‘“, fasst Owen den allgemeinen Tenor zusammen. Damit war dann auch die Idee für JetBoatPilot geboren, um Nachrüstteile für Jetboote zu entwickeln, mit denen sich Ansprechverhalten und Vorhersehbarkeit der Steuerung verbessern ließen.
„Jedes erfolgreiche Produkt hat seinen Ursprung in einem Problem, für das es noch keine adäquate Lösung gibt“, weiß Owen.
Konzentration auf die Lösung und erster Erfolg
Wasserstrahl- bzw. Jetantriebe findet man in aller Regel bei Sportbooten, Waverunnern oder Jetskis. Sie sorgen für eine enorm hohe Wendigkeit und Manövrierfähigkeit bei hohen Geschwindigkeiten. Ganz anders jedoch bei langsamer Fahrt. Da das Boot dann nicht unter Schub steht, ist die Wirkung des Antriebs stark eingeschränkt. Bei Manövern wie dem Einsteuern in Anlegestellen oder der Fahrt im Leerlauf in der Nähe eines anderen Wasserfahrzeugs ist die Fortbewegung des Bootes dadurch deutlich schwerer kontrollier- und voraussehbar. Entsprechend erhöht sich also das Risiko für potenziell kostspielige Reparaturen.
„In Hafen- und Anlegebereichen oder beim Umfahren anderer Boote mehr Kontrolle zu bekommen, das ist für Bootsbesitzer sogar ganz immens wichtig. Denn wer hohe fünfstellige Beträge für ein Boot ausgibt, will schließlich sicher sein, dass der Bootsausflug mit den Liebsten nichts anderes wird als großartig. Für uns besteht hier also enormes Potenzial“, kommentiert Owen.
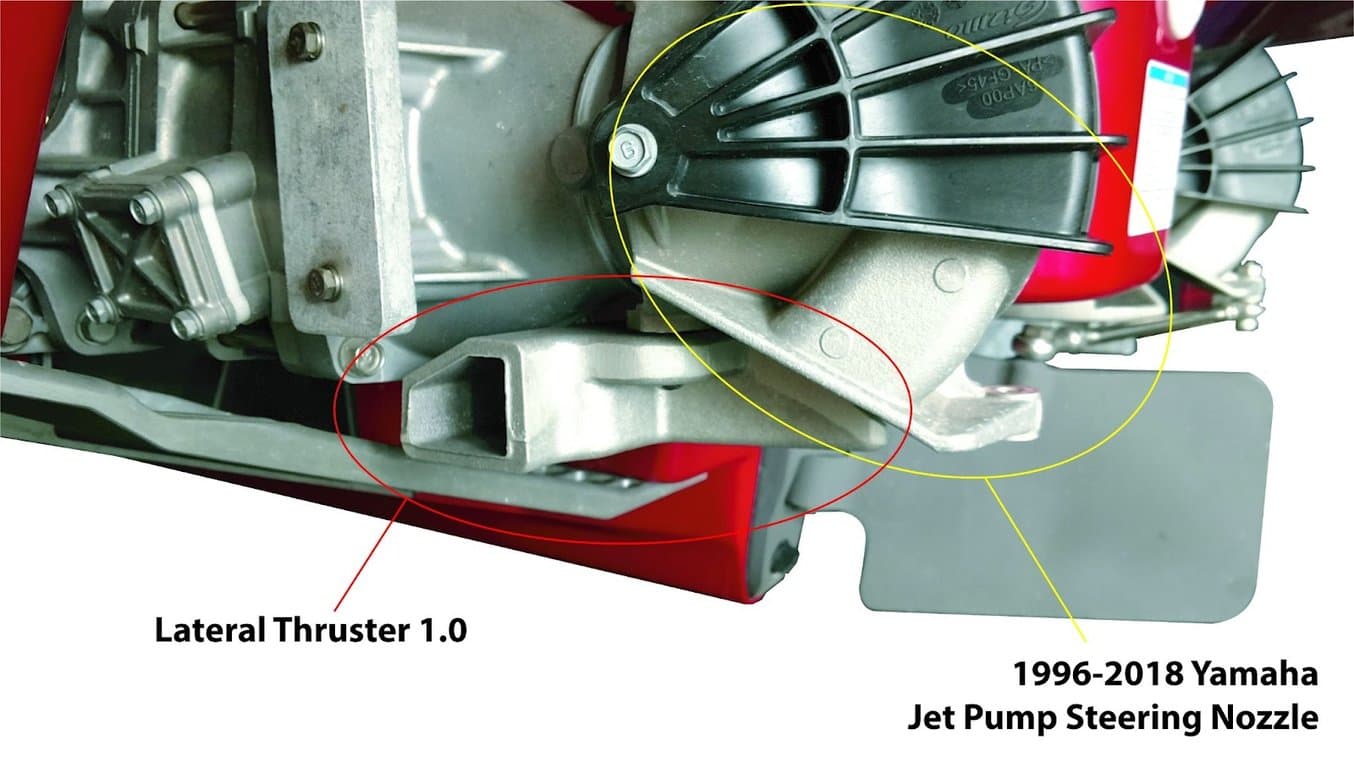
Version 1 des Lateral Thrusters, CNC-gefertigt aus Aluminium
Die ersten Produkte rund um Rudersteuerungen speziell zur Verbesserung der Kontrolle bei Rückwärtsfahrten stellte JetBoatPilot dann im Jahr 2018 vor. Dazu zählte auch die erste Ausführung des Lateral Thrusters, den das Unternehmen an Kunden weltweit auslieferte. Gefertigt wurde das Nachrüstteil im Sandgussverfahren aus Aluminium, seine Montage wurde über bestehende Verschraubungspunkte unter der Jetpumpe von Yamaha-Jetbooten gelöst. Indem der Lateral Thruster einen Teil des Heckstrahls im Vergleich zum werksseitigen Rudersystem weiter seitlich herauslenkte, stärkte er die Kontrolle, die die Steuerdüse zu liefern vermochte. Dies bestätigte auch die in höchstem Maße positive Resonanz der Kunden. So ließ der Lateral Thruster schon bald alle anderen Produkte von JetBoatPilot in puncto Absatzzahlen hinter sich.
Der erste Rückschlag
Die Einführung des Lateral Thrusters war gerade ein Jahr her gewesen, als Yamaha eine neue Entwicklung seiner Steuerdüse vorstellte, die das Nachrüstteil von JetBoatPilot als veraltet degradieren sollte.
„Bis dato hatten wir mit der ersten Ausführung ja nur knapp ein Jahr lang Umsätze generieren können. So war für uns eigentlich klar: So schnell, wie alles begonnen hatte, so abrupt war auch unser Aus besiegelt worden“, beschreibt Owen die damalige Stimmung.
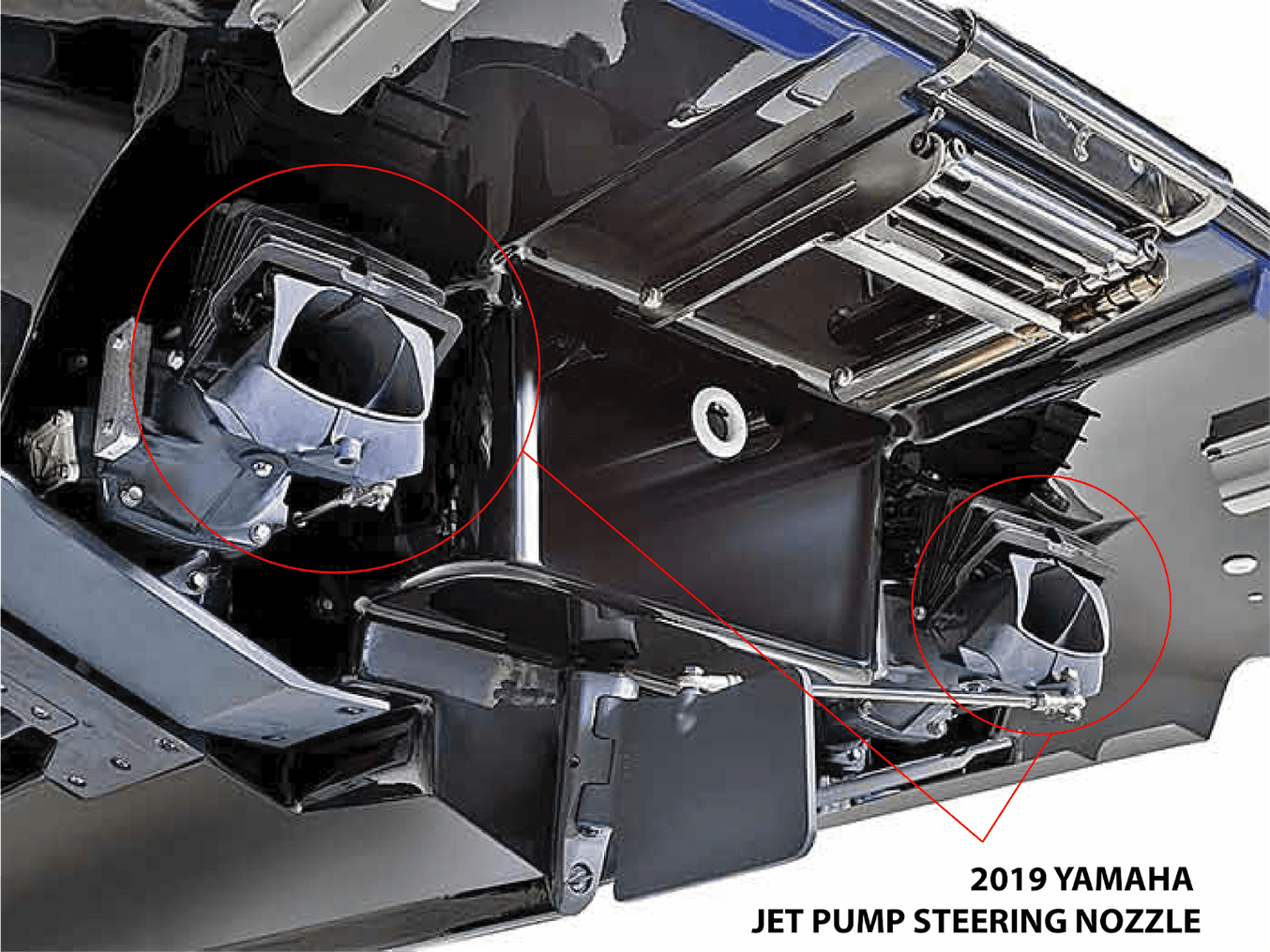
Doch kaum war die neue Yamaha-Steuerdüse marktweit verfügbar, gingen bei Owen bereits die ersten Anrufe und E-Mails seiner ehemaligen Kunden ein, die auf das neue Modell aufgerüstet hatten. Ihr neues Boot böte verglichen mit dem Lateral Thruster des Vorgängers nicht dieselbe Kontrolle, hieß es. Sie verlangten nach einer neuen Version des Lateral Thrusters.
Neuer Anlauf mit 3D-Druck
So machte sich das Team schließlich an die Entwicklung eines neuen Designs – dieses Mal jedoch gestützt auf 3D-Druck, um die Vorteile rund um Prozessgeschwindigkeit und Vielfalt der Materialauswahl auszunutzen. „3D-Druck war für uns sofort die Antwort, denn nur damit konnten wir die Prototypen innerhalb kürzester Zeit realisieren. Ich wusste, wir könnten so schnell die Passung der Teile testen. Nun habe ich einen Form 3 in meinem Büro. Im SLA-Verfahren fertigten wir die ersten Prototypen, die uns dann auch die perfekte Passung lieferten“, so Owen.
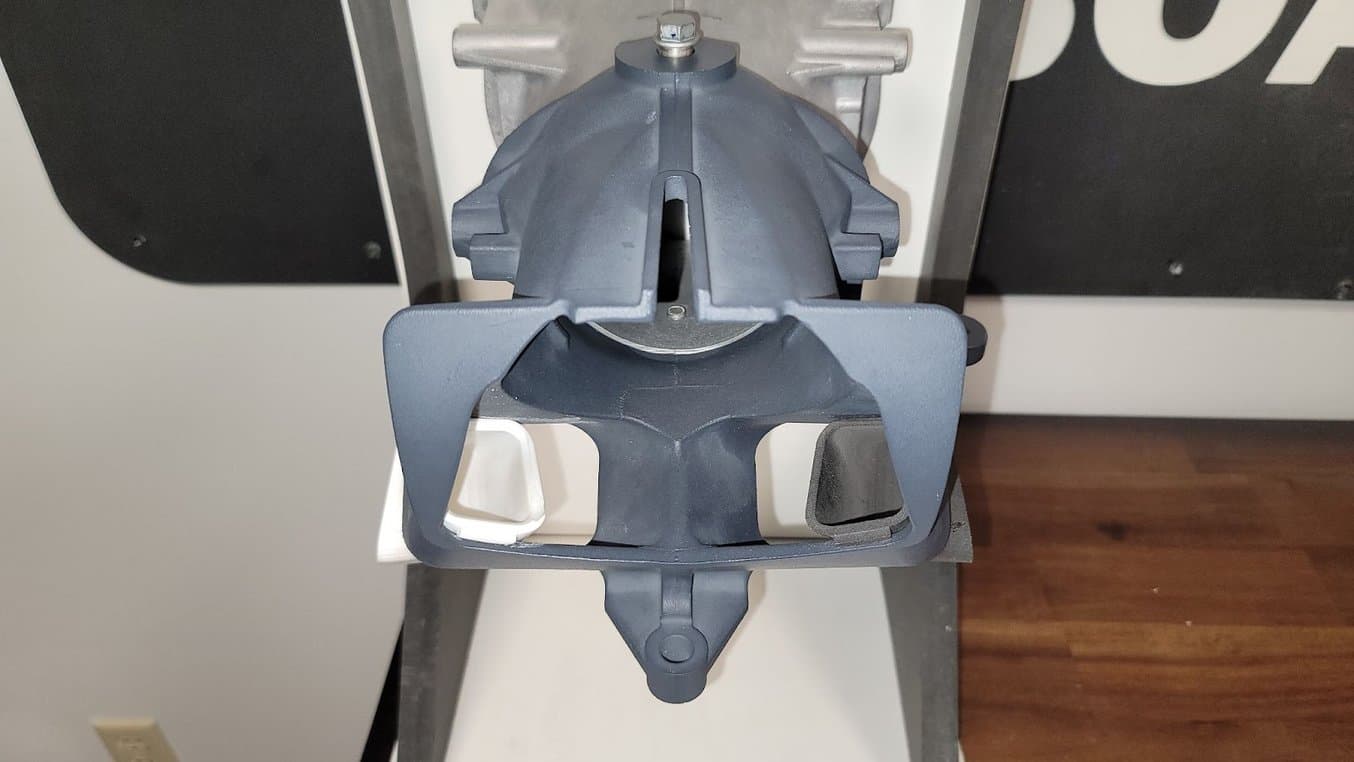
Prototyp des Thrusters 2.0 aus Rigid 10K Resin (die weiße Komponente an der linken Seite)
Um eine ähnlich hohe Steifigkeit wie bei Teilen zu erzielen, die durch Zerspanung gefertigt werden, druckten Owen und sein Team das Design des Lateral Thrusters aus Tough 1500 Resin und Rigid 10K Resin. Beim anschließenden Test des Designs mit der neuen Version der Yamaha-Motoren zeigte sich ein weiterer Vorteil des 3D-Drucks. Zerspante Aluminiumteile müssen perfekt an den Motor passen, doch aufgrund der inhärenten Flexibilität von SLA-Teilen waren diese auch in Motoren mit geringfügig abweichenden Toleranzen verwendbar.
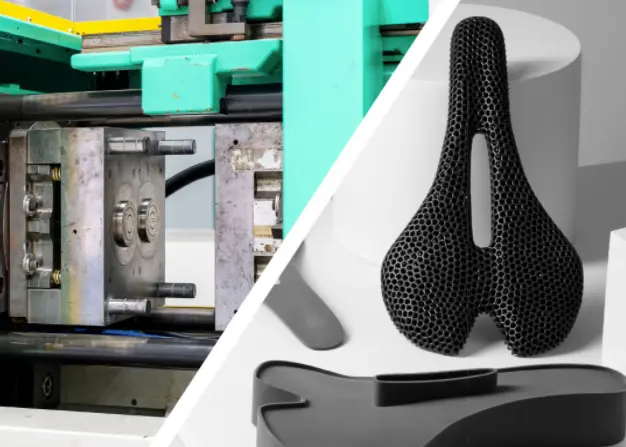
SLS-3D-Druck oder Spritzguss: Wann sollte man Spritzgussteile durch 3D-Druck ersetzen?
In diesem Whitepaper werden der Spritzguss und seine Vor- und Nachteile erörtert sowie der SLS-3D-Druck und die Anwendungen vorgestellt, bei denen er als ergänzende Technologie eingesetzt werden kann.
Nächste Station: SLS
Nach Verifizierung der Passung und mehreren Iterationen befand das Team, dass das Design des Lateral Thrusters nun für seine erste „Jungfernfahrt“ bereit war. Owen fehlte noch ein Material, dessen Eigenschaften näher an die der zerspanten Teile der ersten Version des Thrusters herankam. Er sagt dazu: „Wir fassten den Umstieg zur Fertigung auf dem Fuse 1 ins Auge. So konnten wir direkt die nötige Qualität für den Einsatz unter Realbedingungen bzw. beim Endkunden gewährleisten.“
Der Testdruck aus dem Fuse 1, den das Team bei Formlabs in Auftrag gab, erfüllte dies vollumfänglich: Der Lateral Thruster überzeugte durch volle Eignung zum Einsatz im Wasser – und gab so auch den Anstoß für JetBoatPilot, die Kapazitäten in Sachen 3D-Druck eine Stufe höher zu heben.
„Wir probierten es aus und das Ding funktionierte. Und das absolut tadellos. Mit dem Fuse 1 kann ich das Teil sogar in eine Düse mit etwas engerer Geometrie einpassen. Ich kann es biegen und verziehen und dann sitzt es. Es kehrt stets in seine ursprüngliche Form zurück, ganz ohne Einbußen an Belastbarkeit und Funktionalität. Davon höchst beeindruckt, wagten wir uns dann auch an etwas kühnere Experimente heran“, gibt Owen zu Protokoll.
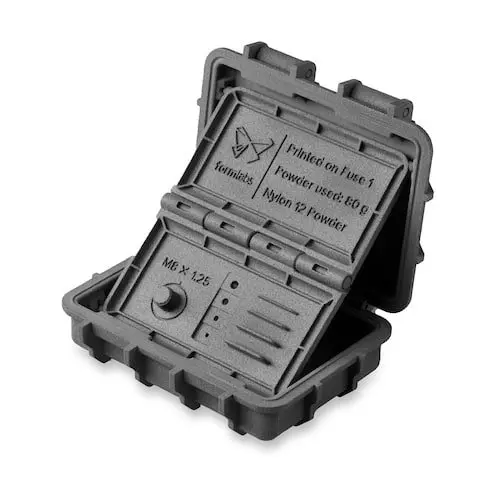
Kostenlosen Probedruck anfordern
Sehen und fühlen Sie selbst die SLS-Qualität von Formlabs. Wir schicken Ihnen einen kostenlosen Probedruck an Ihren Arbeitsplatz.
Nach Anschaffung des Fuse 1 begann JetBoatPilot weitere Iterationen, in deren Rahmen das Unternehmen Prototypen intensiven betriebsinternen Testläufen unterzog und diese zudem auch an Kunden auslieferte, um direktes Anwender-Feedback zu erhalten.
„Wir wollten es wirklich wissen, trieben das Boot etwa im Rückwärtsgang auf 4000 U/min hoch und ließen es einfach so laufen. Kaputt gekriegt haben wir bis dato aber noch kein einziges Teil. Das ist mitunter wohl auch das Entscheidende für uns: die Bestätigung, dass jeder einzelne Druck seinen Zweck absolut erfüllt“, befindet Owen.
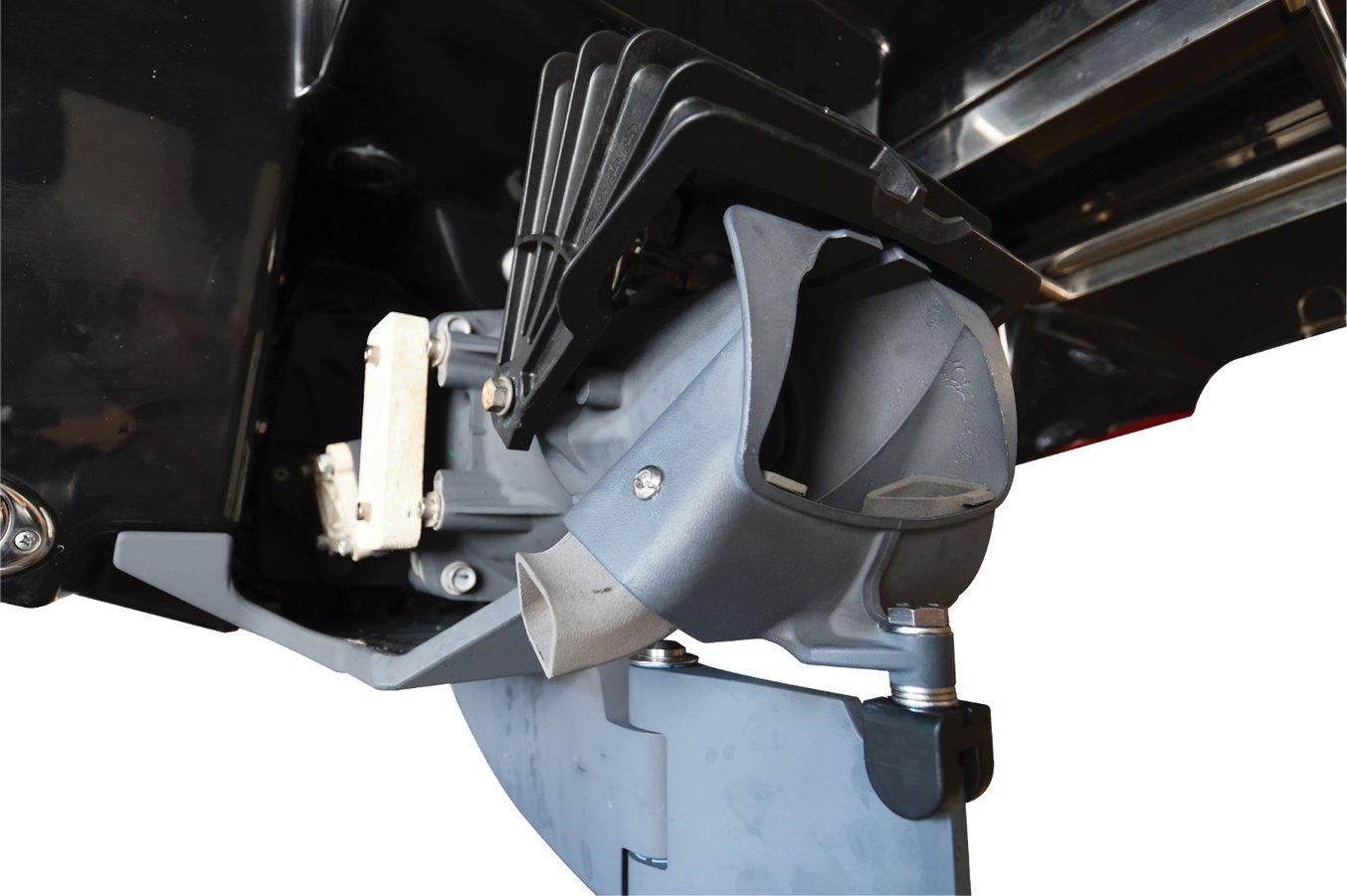
Teil des Thrusters 2.0 in finaler Ausführung zur Endanwendung, gedruckt auf dem Fuse 1 (die Komponente in Hellgrau)
Kosteneinsparungen durch betriebsinterne Fertigung
Die Zeiteinsparungen im Iterationsprozess waren unschwer zu übersehen, musste JetBoatPilot doch zu keiner Zeit mehr eine Werkstatt beauftragen. Von Design und Druck bis hin zu Test und Iteration konnte das Unternehmen für jedes Teil sämtliche Prozessschritte intern und so innerhalb von nur einer Woche abwickeln und nicht erst nach einem ganzen Monat.
Die dadurch realisierten Ablaufeffizienzen waren zwar durchaus beachtlich. Noch deutlich stärker zum Tragen kommen jedoch die Vorteile, die sich bei den Fertigungskosten ergeben. Denn für den kompletten Bausatz des Lateral Thrusters 2.0, der neben zwei Teilen aus Nylon 12 Powder einen Satz von Schrauben inklusive Schraubenschlüssel sowie einen Aufkleber umfasst, belaufen sich die Materialkosten für JetBoatPilot auf gerade einmal 11 USD.
Für denselben Bausatz fiel bei Version 1.0 des Lateral Thrusters dagegen das 6-fache an. Einen erheblichen Anteil daran hatte die Fertigung der Aluminiumteile durch eine externe Werkstatt. Denn das hohe Maß, in dem sie den Prozessfortschritt verlangsamte, spiegelte sich auch in den mit ihr verbundenen Kosten wider. Und die müssen dann an die Kunden weitergegeben werden.
„Bei einer Fertigung aus Aluminium würde ich für die neue Version im Verkauf wohl um die 400 USD ansetzen. Vielleicht auch 600 USD, wenn ich die Margen bis ganz nach oben ausreize – wobei ich dann allerdings kaum dieselbe Menge verkaufen würde. Jetzt biete ich es dagegen zu einem Preispunkt von gerade einmal 199 USD an und meine Kunden sind gänzlich zufrieden. Das ist wohlgemerkt das 20-fache von dem, was meine Fertigungskosten ausmachen“, betont Owen.
Nesting-Algorithmen als Kostenoptimierer einer kompletten Produktpalette
Der Fuse 1 hat jedoch noch einen weiteren Vorteil im Gepäck. Dank des 3D-Packalgorithmus wird es Owen möglich, die Konstruktionskammer des Druckers im Sinne maximal effizienter Raumnutzung zu befüllen. So bringt er in der Konstruktionskammer 34 Teile bzw. 17 komplette Bausätze unter und findet in den Freiräumen zudem noch Platz für Teile eines weiteren Produkts namens Kickstand. Mit zunehmender Packdichte gehen weitere Einsparungen bei den Materialkosten einher.
„Aktuell lassen wir den Kickstand noch aus PE-HMW-Kunststoff fräsen. Wir arbeiten jedoch bereits daran, ihn künftig im Spritzgussverfahren zu fertigen, wobei wir die hierzu nötigen Formen und Werkzeuge im 3D-Drucker realisieren. Diese passen in die Freiräume zwischen den Teilen des Lateral Thrusters. So erhalten wir mit jeder Charge aus 34 Lateral Thrusters zusätzlich noch 34 Kickstands.“
Agile Fertigung
Mit dem Fuse 1 im Mittelpunkt der betriebsinternen Fertigungsprozesse hat JetBoatPilot eine reaktionsschnelle und dynamische Produktion geschaffen. So macht sich das Unternehmen etwa die enge Vernetzung der Bootsbesitzer-Community zunutze, um auf schnellem Wege unverfälschtes Feedback von seiner Kundenbasis zu erhalten. Sind dann Design-Anpassungen aufgrund des Kundenfeedbacks oder beispielsweise auch im Zuge der Einführung eines neuen Yamaha-Motors vonnöten, kann JetBoatPilot seine höchst agilen Abläufe präzise daran ausrichten und dem Bedarf entsprechend weiterentwickeln.
„Da ich meine Hand stets am Puls der Anwender meiner Produkte habe – schließlich bin ich selbst der Designer, der Programmierer –, kann ich das Design im Handumdrehen ändern. Und dank des Fuse 1 muss ich dabei dann auch kein altes Formwerkzeug wegwerfen. Wenn nötig, sind wir in kürzester Zeit bereit für Neues“, erläutert Owen.
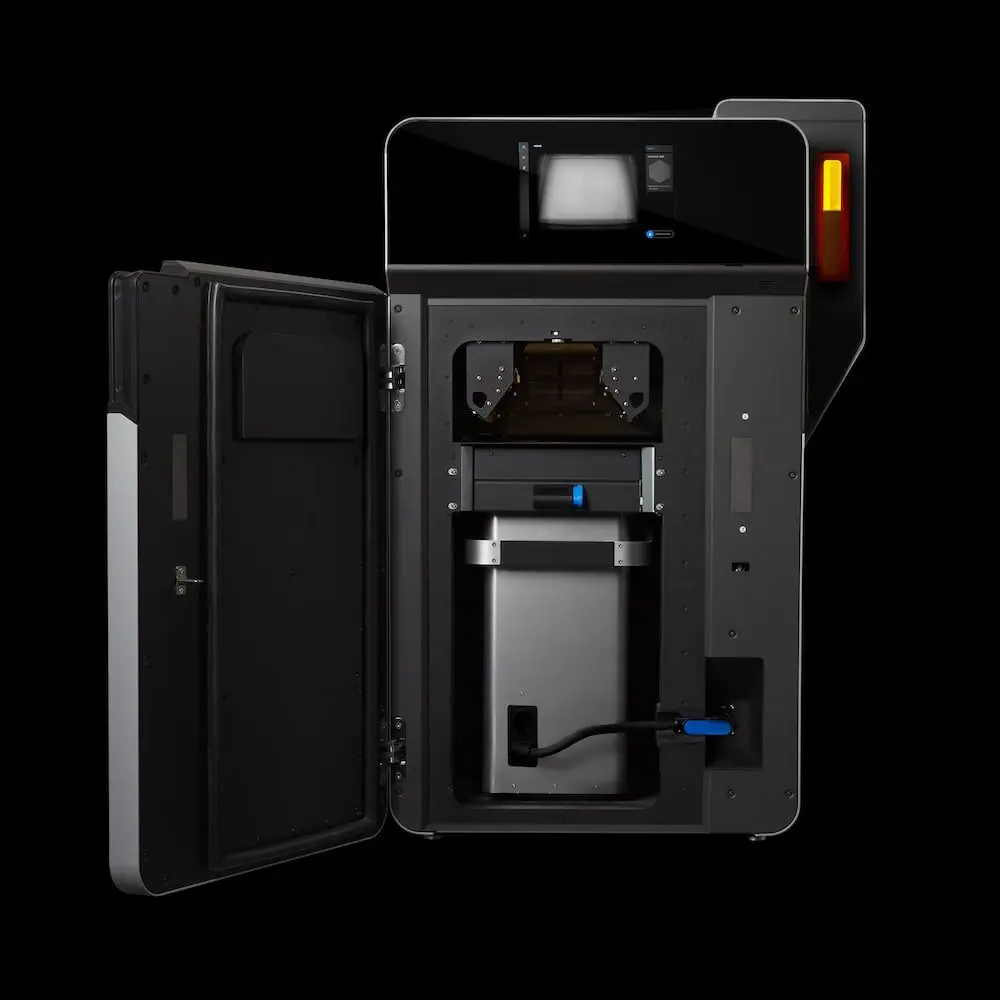
Produktvorführung des Fuse 1
Sehen Sie sich unsere Produktvorführung an und lassen Sie sich den Fuse 1 und den SLS-3D-Druck durch einen Formlabs-Experten erklären.