Neuroscience meets Design: Wie air up 3D-gedrucktes Rapid Tooling für den Prototypenbau lebensmittelechter Trinkflaschen einsetzt
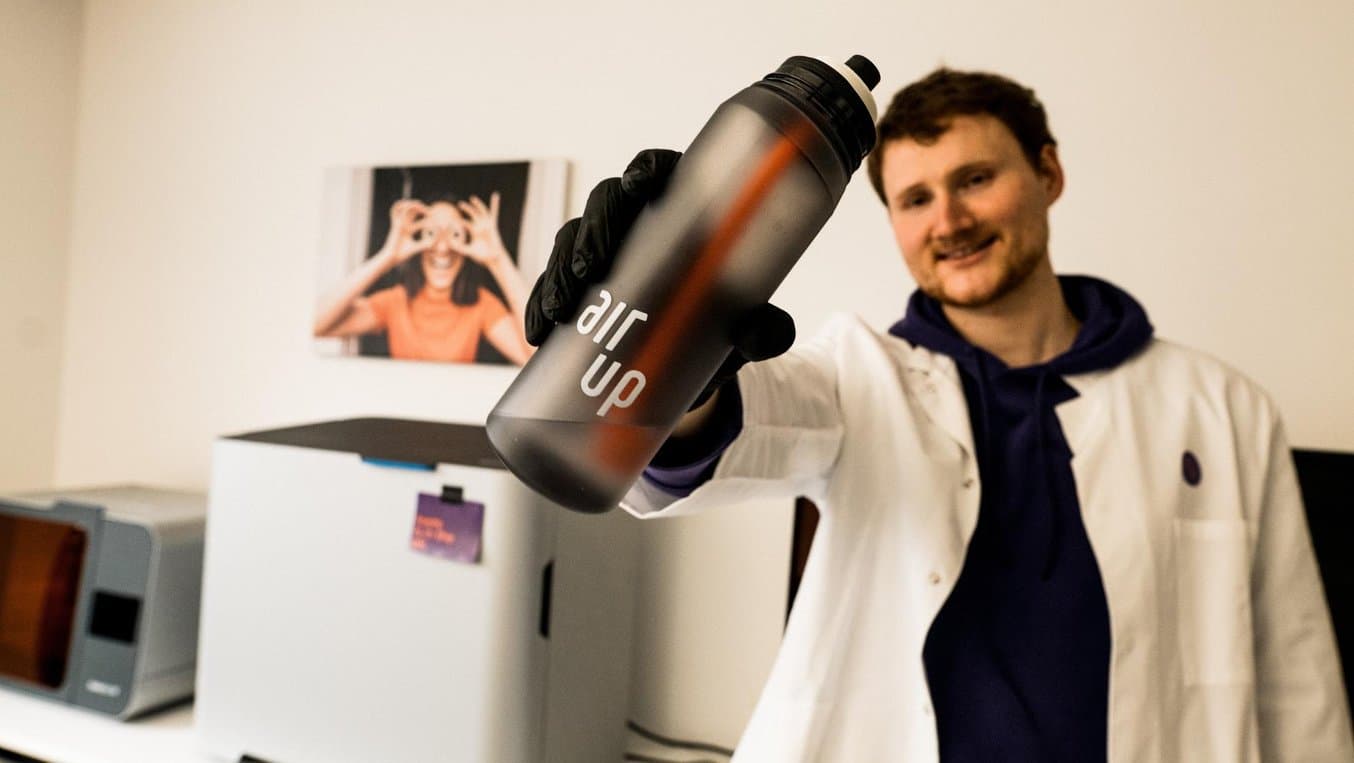
Das Münchner Scale-up air up hat durch den Verkauf von Trinkflaschen, die Wasser nur durch Duft aromatisieren, einen neuen Trend für gesunde Getränke gesetzt. Dafür haben sie sich das Prinzip des sogenannten retronasalen Riechens zu Nutze gemacht.
Nur zwei Jahre nach seiner Gründung feierte air up den Meilenstein von 1 Mio. Kund:innen und konnte bis März 2022 auf heute rund 240 Mitarbeitende anwachsen.
Der 3D-Druck spielte im Entwicklungsprozess eine Schlüsselrolle, sowohl für den direkten Druck von Prototypen als auch für das Rapid Tooling für den Silikonformenbau, um lebensmittelechte Prototypen herzustellen. So konnte das junge Scale-up Zeit und Geld sparen und es ermöglichte ihnen einen schnelleren Markteintritt.
In diesem Interview spricht Tim Jäger, einer der fünf Gründer und heutiger CTO des Unternehmens, über die Entstehung der Idee, die Technologie und wie sie ihre Form 3 und Form 3L Stereolithographie (SLA) 3D-Drucker zur Herstellung detaillierter Funktionsprototypen einsetzten, um ihr Design zu perfektionieren.
Neuroscience Meets Design
Tim Jäger und seine Mitgründerin Lena Jüngst hatten während ihres Bachelorstudiums in Produktdesign die Vision eines Produktes mit positivem Einfluss auf Gesundheit und Nachhaltigkeit. Beide Themen spielen in unserer heutigen Gesellschaft eine zentrale Rolle und sind dadurch auch stetig wachsende wirtschaftliche Erfolgsfaktoren neuer Produkte.
Krankheiten wie Diabetes, die häufig durch ungesundes Ess- und Trinkverhalten verursacht werden, fielen dabei besonders auf. Beim Trinkverhalten ist der ausschlaggebende Punkt oft der versteckte Zuckergehalt in den Getränken, welcher von Konsument:innen häufig nicht wahrgenommen wird. Im Austausch mit Ärzt:innen und Patient:innen fiel zudem auf, dass vielen Menschen pures Wasser schlichtweg nicht schmeckt, und sie daher häufig zu gezuckerten Getränken mit mehr Geschmack wie Limonaden und Säften greifen.
Unter dem Motto “make a healthy and sustainable lifestyle the most attractive choice”, wollten Jäger und Jüngst damals einen Kompromiss finden, welcher Wasser für mehr Menschen attraktiver macht - ja vielleicht sogar dazu anregt, mehr davon zu trinken.
“Was viele Konsumenten nicht wissen ist, dass bis zu 80 Prozent unseres Geschmacks nicht durch den Mund oder durch die Zunge definiert wird, sondern durch die Nase. Sozusagen durch die Luft, die wir ausatmen während wir etwas schmecken”, erläutert Jäger.
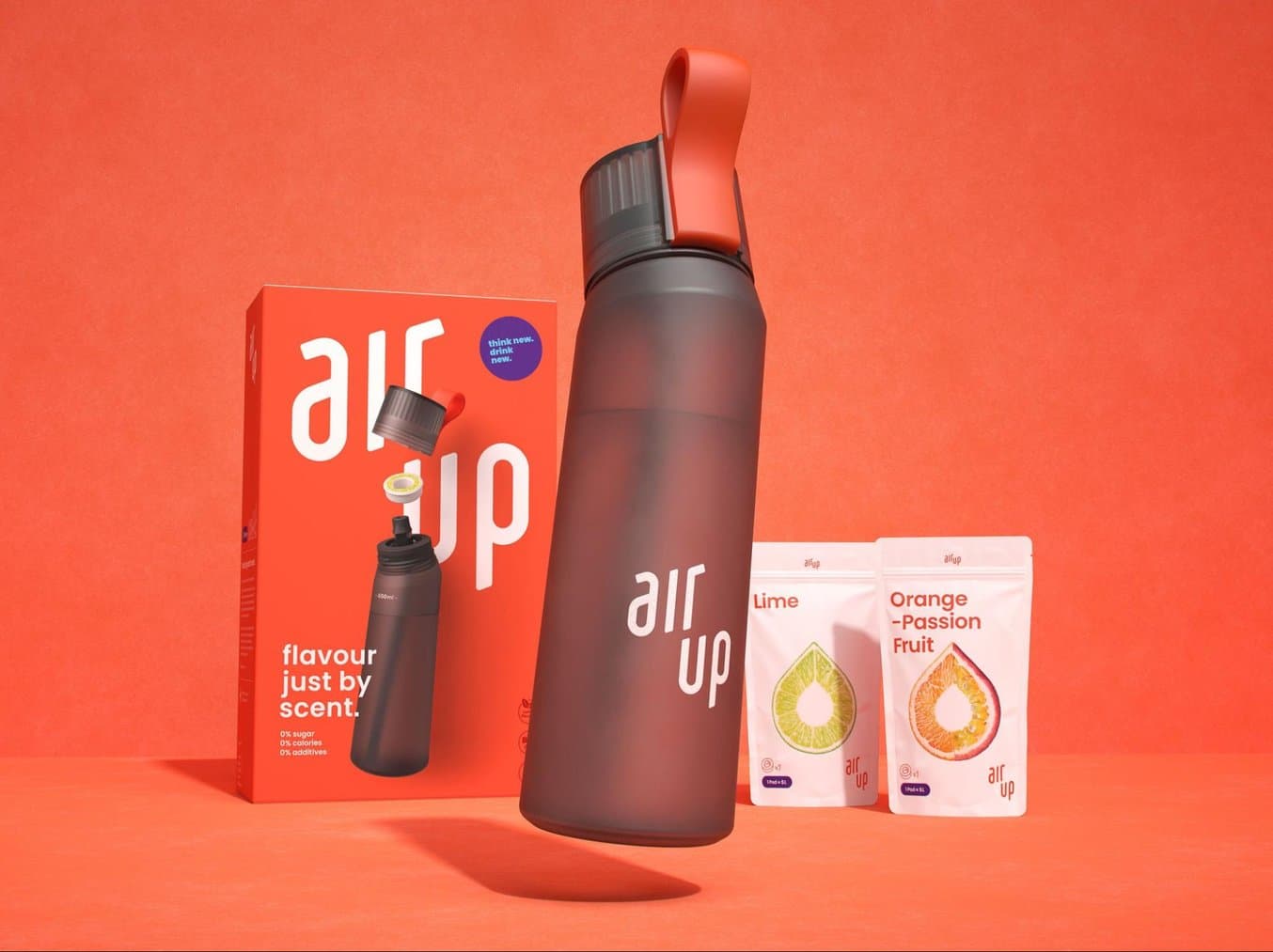
Das Produkt air up besteht aus einem Trinksystem und abwechslungsreichen Aromapods
Dieses Phänomen des sogenannten retronasalen Riechens haben sich die beiden für die Technologie ihrer neuen Wasserflasche zu Nutze gemacht. Durch die Aromapods am Mundstück steigen aromatisierte Luftblasen beim Trinken in den Mundraum, welche über unseren Rachenraum zu den Riechrezeptoren gelangen. Diese sind dafür zuständig, den Geruch an das Gehirn weiterzugeben. Da das Aroma des Duftpods aus dem Rachenraum stammt, erkennt unser Gehirn den Geruch, jedoch wird dieser als Geschmack wahrgenommen.
So wird das pure Wasser attraktiver zum Trinken, bleibt jedoch gesund und frei von jeglichen versteckten Zuckerzusätzen.
Außerdem können die Duftpods mindestens 5-7 Liter Wasser aromatisieren, wodurch Verbraucher:innen weniger auf fertig abgefüllte PET-Einwegplastikflaschen zurückgreifen.
Die richtige Methode zum Prototyping wählen
Für Jäger spielte 3D-Druck schon länger eine essentielle Rolle, um schnell und kosteneffizient von einem Konzept auf das finale Produkt zu kommen.
Nach der Entscheidung ihr Bachelorarbeitsthema tatsächlich in die Tat umzusetzen, mussten Jäger und Jüngst zunächst das richtige 3D-Druck Verfahren auswählen, um erste Prototypen der Trinkflasche nach ihren Anforderungen zu bauen.
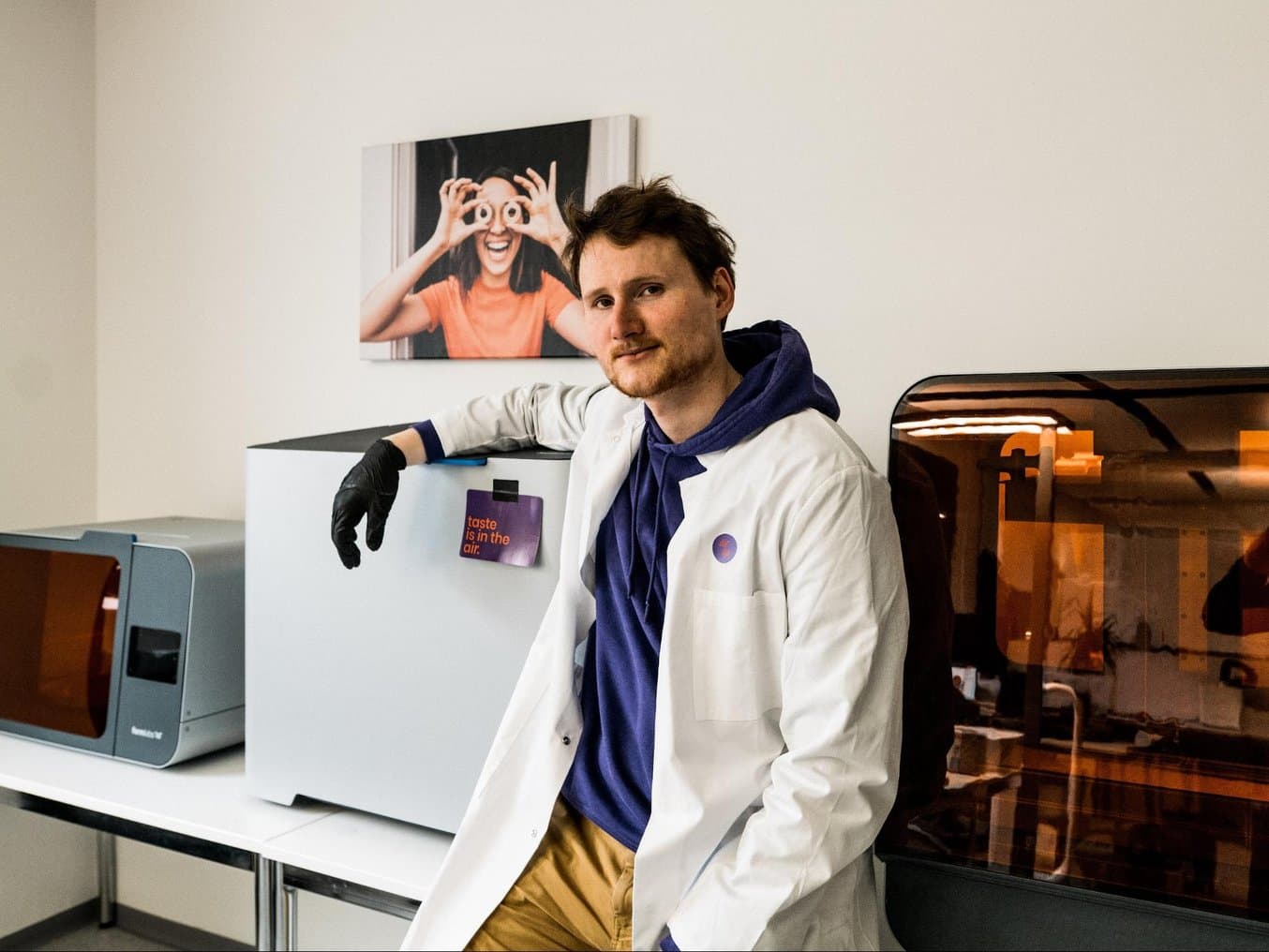
Das Prototyping-Labor von air up ist mit einem Form 3L-Großformat SLA 3D-Drucker und Form 3 Desktop Druckern ausgestattet.
Grundsätzlich war es wichtig, dass die Prototyp-Materialien wasserdichte Teile bauen können.
“Darüber hinaus brauchen wir natürlich auch luftdichte und eben lebensmittelechte Teile. Und insbesondere die Verwendung von lebensmittelechten Teilen gestaltet sich beim 3D-Druck oft schwierig. Durch Rapid Tooling mit 3D-Druck konnte ich lebensmittelechte Teile deutlich besser und vor allem viel schneller herstellen”, erklärt Jäger.
Rapid Tooling kombiniert 3D-gedruckte Werkzeuge mit traditionellen Fertigungsverfahren wie Spritzguss, Thermoformung oder Silikonguss. Das erlaubte Jäger und seinem Team mit Silikon zu arbeiten, welches später tatsächlich für das Endverbrauer Stück benutzt werden sollte. Außerdem konnten Designänderungen der Prototypen flexibel, blitzschnell und kosteneffizient umgesetzt werden.
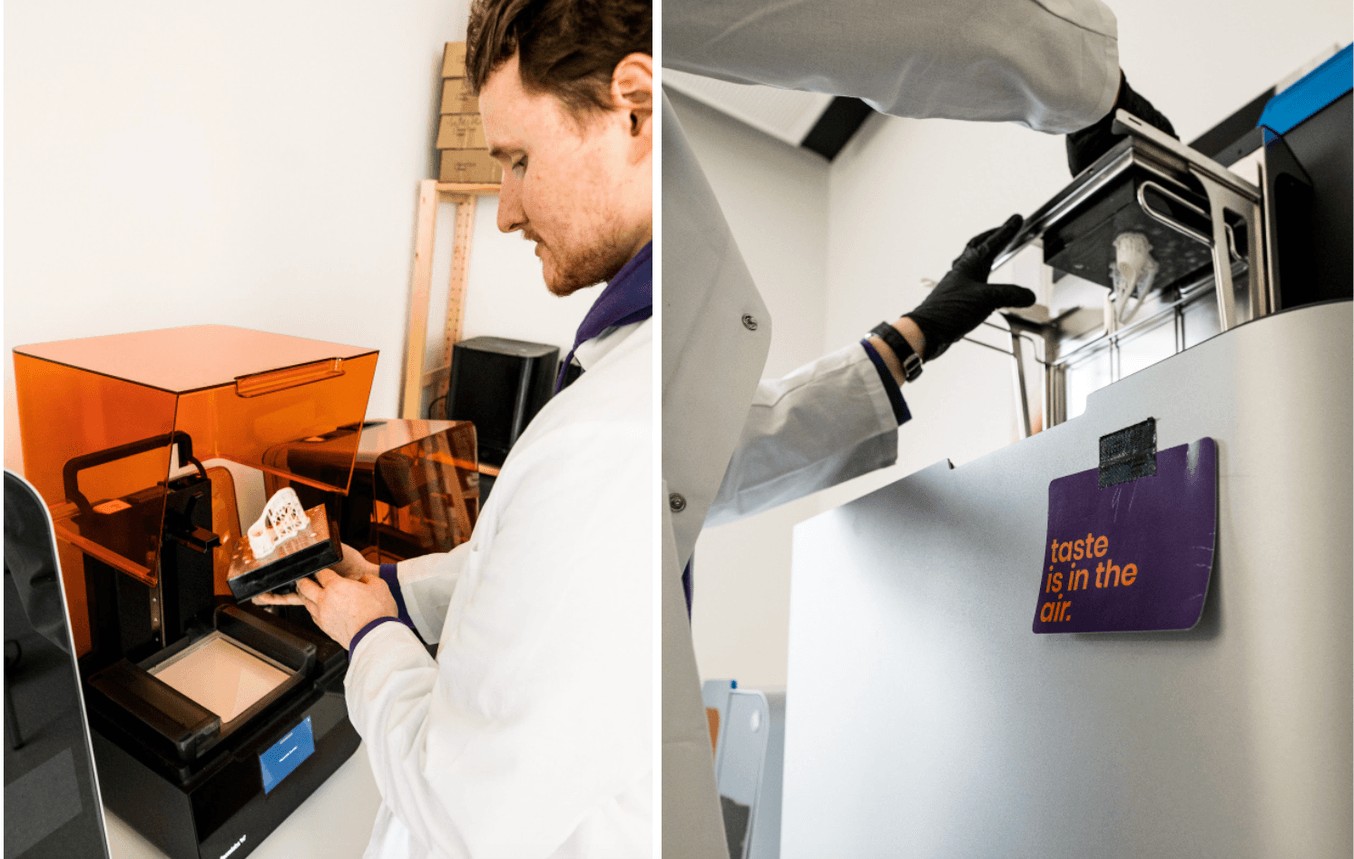
Ein in White Resin hergestellter Prototyp werden nach dem Druck mit dem Form Wash L gewaschen.
Das Gründerteam arbeitete hierbei eng mit dem Formlabs Partner Beta2Shape zusammen. Durch die vielseitige Erfahrung im Bereich des 3D-Drucks unterstützen sie das junge Team mit professioneller Beratung sowie Anleitungen zum Verfahren und steigerten damit die Produktivität in den ersten Schritten des Entwicklungsprozesses enorm.
Zunächst legten die air up Gründer:innen sich einen Form 2 zu und bauten ihre eigene Druckmöglichkeiten dann im Laufe der Produktentwicklung mit Form 3 und Form 3L 3D-Druckern weiter aus.
Neben dem Silikonformenbau der komplexen Mundstücke, wurden die Formlabs SLA 3D-Drucker auch für andere Teile, wie zur Herstellung von Prototypen der Pod-Vorrichtungen und Strohhalme eingesetzt.
“Das Spannendste am Einsatz der 3D-Druck Verfahren war die Zeit, die eingespart werden konnte. Am Ende konnte ich innerhalb von 24 Stunden einen kompletten Serienswitch machen.”
Tim Jäger
Auch heute hilft Beta2Shape dem Jungunternehmen bei dem weiteren Ausbau ihrer 3D-Druck Expertise für neue Projekte, die Rapid Tooling und Rapid Prototyping involvieren.
Lebensmittelechte Prototypen mithilfe von Silikonformenbau
Zur Verwirklichung der Technologie durch die Konsument:innen mittels retronasalen Riechens puren und abwechslungsreichen Trinkgenuss genießen sollten, bedurfte es besonderen Anforderungen in Bezug auf das Design von Mundstück und Duftpod.
Diese löste Jäger folgendermaßen: „Ich habe mittels dem 3D-Druck eine Form gebaut, in die ich dann Silikon gießen konnte. Davon habe ich hunderte Iterationen getestet und konnte immer Prototypen in einem wirklich finalen Material iterieren.”
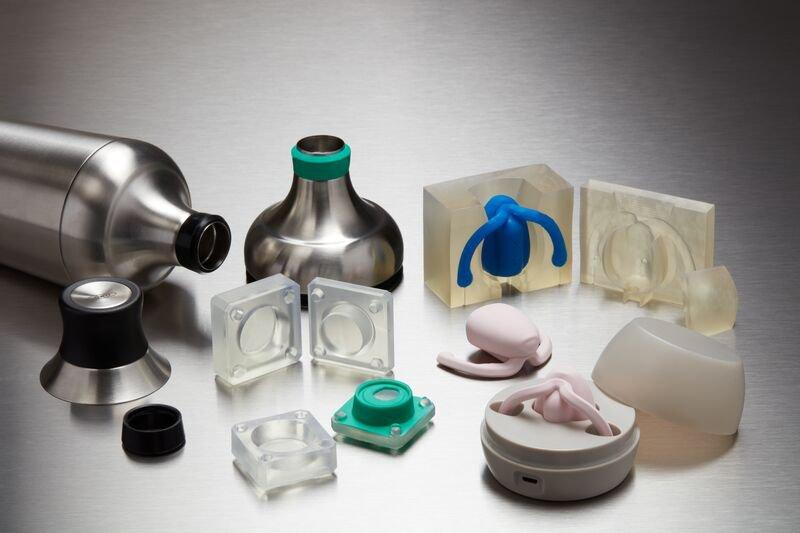
Silikonformenbau für das Produktdesign
Dieses Whitepaper umfasst Fallstudien der Unternehmen OXO, Tinta Crayons und Dame Products und legt drei unterschiedliche Umsetzungen des Silikongusses für das Produktdesign und die Fertigung dar.
Das Zusammenspiel aus den 3D-gedruckten Formen und dem Gießsilikon erlaubte Jäger besondere Detail- und Maßgenauigkeit, ohne dabei Zeit einbüßen zu müssen.
“Formlabs hat uns durch ihre Technologie das Rapid Tooling überhaupt erst möglich gemacht. Die Genauigkeit, die ich dort brauche, die kann ich mit einem FDM 3D-Drucker nicht abbilden”, sagte Jäger.
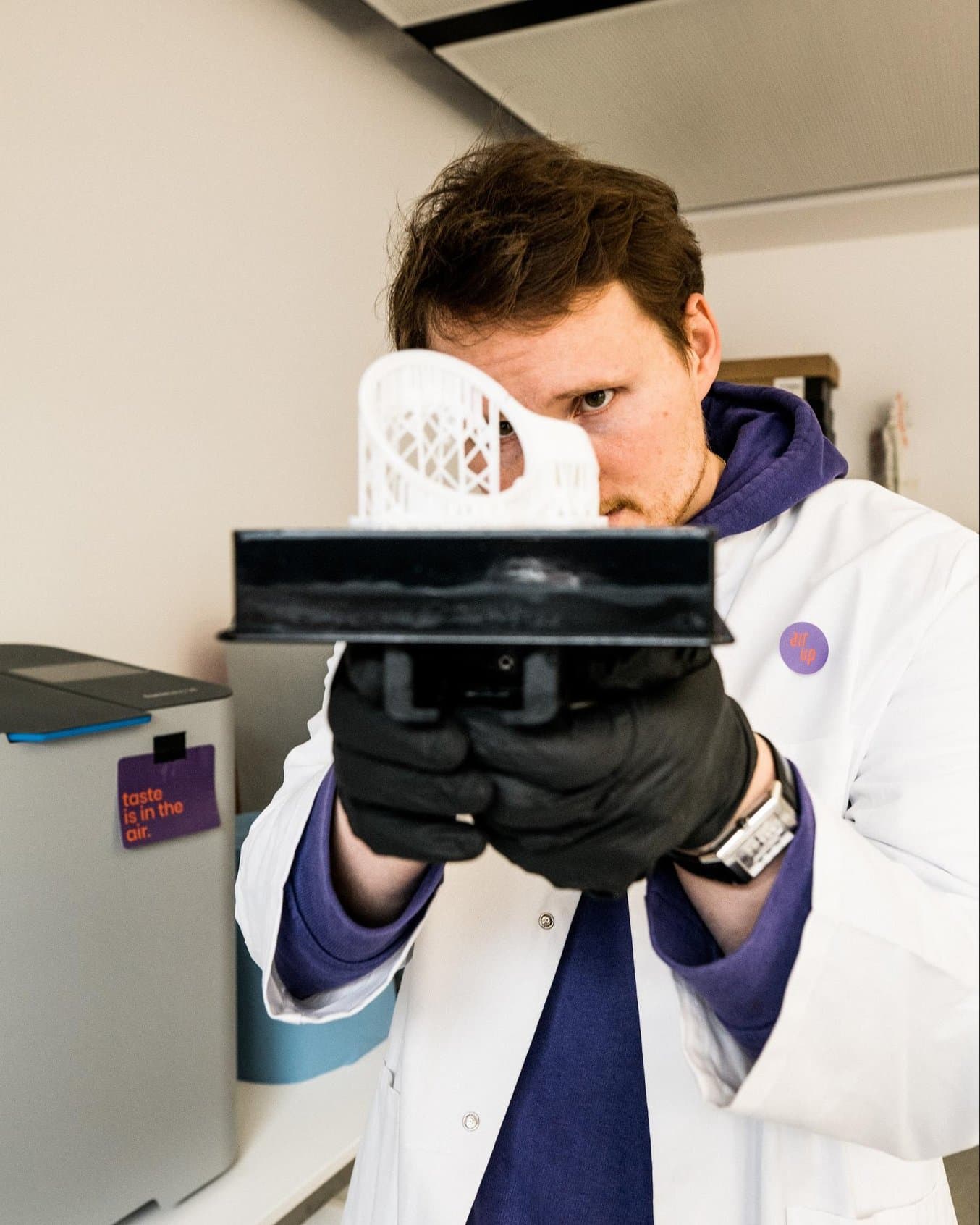
Ein 3D-gedrucktes Prototypenteil aus White Resin
Die Materialauswahl im Prototyping bei air up fiel vorrangig auf White Resin, da es gerade am Anfang von dem Design Prozess sehr universell einsetzbar war. Auch biokompatible Harze und Model Resin aus der Formlabs Dentalmaterialien Bibliothek wurden gelegentlich für das Rapid Prototyping verwendet.
Design Power statt Maschinenpark
“Uns war es wichtig, dass wir hier keinen Maschinenpark aufbauen, sondern wirklich dem Designer die Power in die Hand geben.“
Durch die einfache Handhabung der Formlabs 3D-Drucker konnten die Designer selbst aus ihren Entwürfen Prototypen anfertigen, sie direkt testen und flexibel und agile Änderungen vornehmen.
Jäger betonte außerdem, wie viel Bedeutung in dem Design mit einem 3D-Drucker liegen kann: “Was wie ich glaube oft unterschätzt wird ist, dass erst wenn man den Drucker hat, es dem Designer in seinem Gedankenprozess überhaupt möglich ist zu sehen, was man machen kann, weil dir das einen komplett neuen Horizont eröffnet.”
Des Weiteren zog er den quantitativen Vergleich zwischen dem Rapid Tooling mit ihren hausinternen 3D-Druckern und ausgelagertem Prototyping mit Silikonformenbau. Eine Iteration mit Rapid Tooling hat intern 24 Stunden und ca. 16 € Materialkosten erfordert. Demgegenüber nahm ein Outsourcing des Prozesses vier Wochen in Anspruch und bedurfte ca. 20.000 €.
“Wir konnten unfassbar viele Fehler [durch das Rapid Tooling mit dem 3D-Druck] vermeiden und so viel schneller an die finale Version für unseren Launch kommen.”
Tim Jäger
Rapid Tooling mit 3D-Druck
Mittels des Form 3 und des Form 3L konnte air up einen großen Teil ihres Produktentwicklungsprozesses mit Rapid Tooling realisieren. Durch hausinterne Iterationen und Prototypentests konnten die Münchner nicht nur Zeit und Geld einsparen, sondern auch die Qualität ihrer Produkte kontinuierlich zu verbessern.
Neben dem von ihnen benutzten Silikonformenbau sind auch andere Verfahren des Rapid Toolings wie Thermoformen oder Spritzguss mit SLA gedruckten Formen möglich.