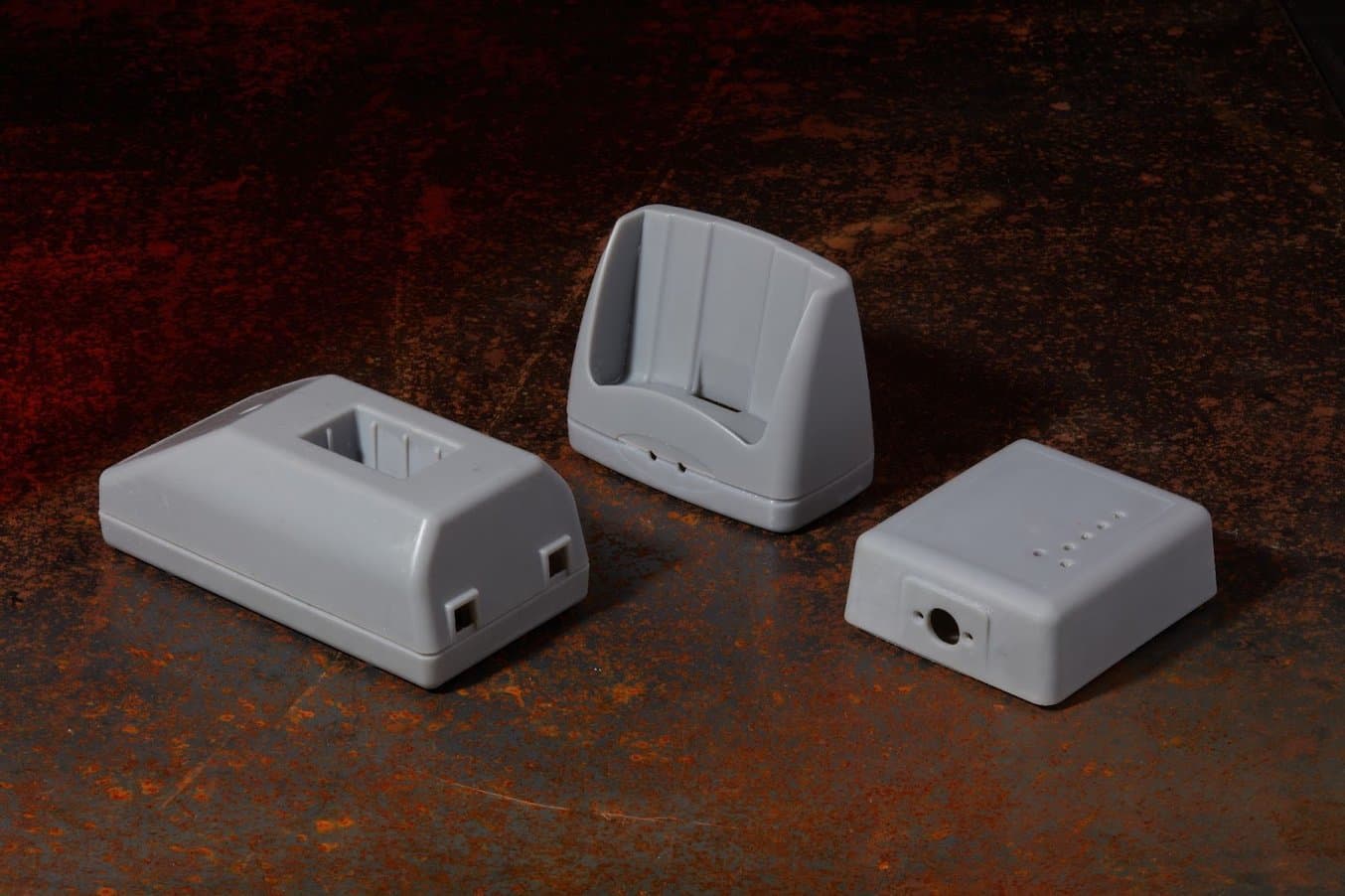
Avance Design, ein Beratungsunternehmen im Bereich Produktentwicklung und Maschinenbau in Indianapolis, Indiana, USA, nutzt 3D-Drucktechnologien bereits seit über zwei Jahrzehnten – dennoch entdeckt das Team in jedem neuentwickelten 3D-Druckmaterial neue Chancen und Anwendungsmöglichkeiten.
Abgesehen vom Guss, Spritzguss, Zerspanen und FDM-Druck nutzt Avance drei SLA-Drucker des Typs Form 3+ und zwei Form 3, um Produkte für die Gesundheits-, Robotik-, Architektur- und Elektronikbranche zu entwickeln. Seitdem das Unternehmen das neue Flame Retardant Resin von Formlabs im Einsatz hat, konnte Avance seinen Entwicklungszyklus beschleunigen und Kosten und Arbeitsaufwand bei der Produktion von UL-94-zertifizierten Teilen senken.
Tony Parker, Direktor bei Avance, hat sich mit uns über Kleinserienproduktion und Mass Customization unterhalten und von einem erfolgreichen Produktionslauf für einen Kunden berichtet, der durch Flame Retardant Resin möglich gemacht wurde.
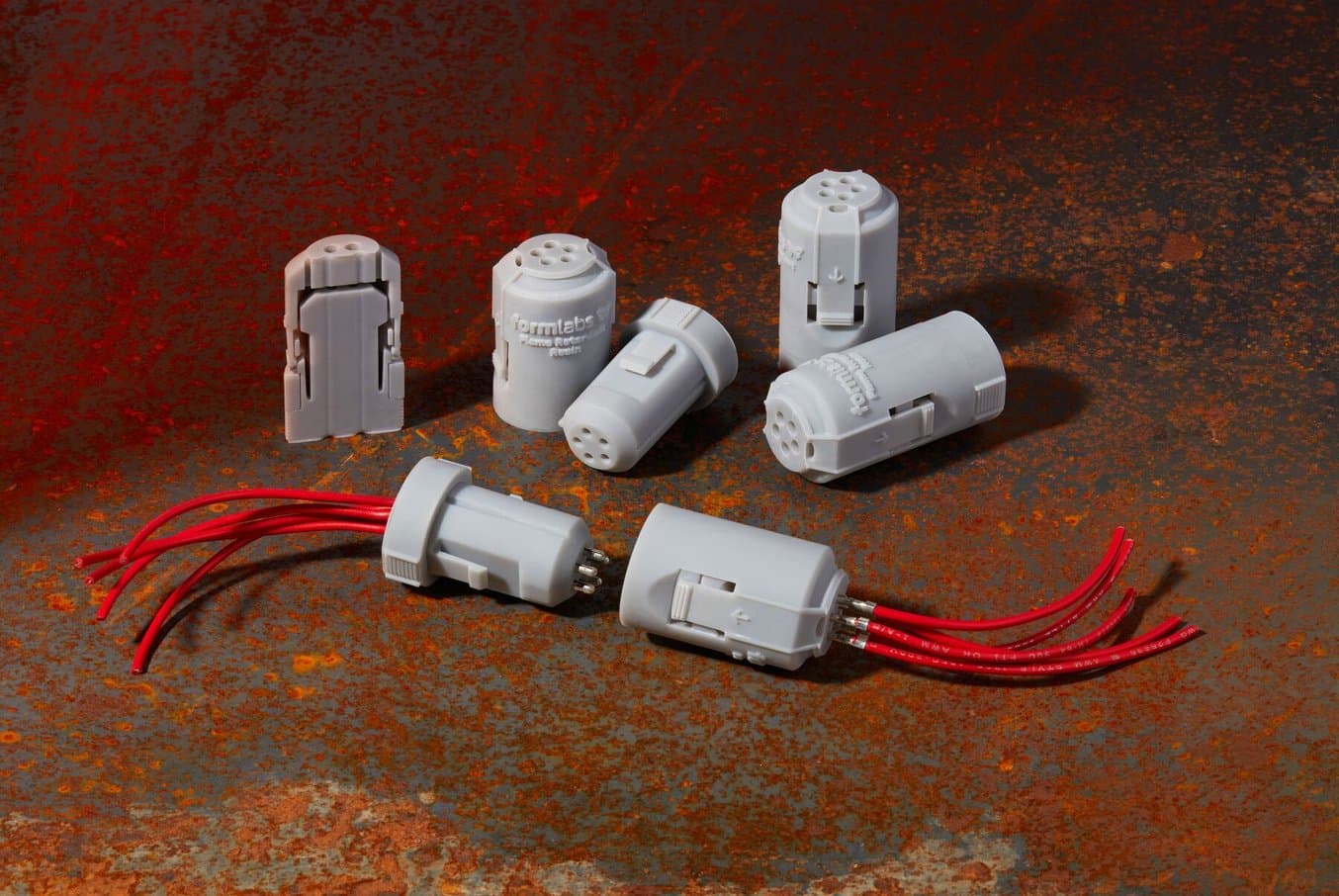
So eröffnet Flame Retardant Resin neue Anwendungen für Avance Design
Erfahren Sie, wie Sie mit Flame Retardant Resin mit Leichtigkeit flammhemmende, hitzebeständige, starre und kriechfeste Teile herstellen, die sich in Innenräumen und industriellen Umgebungen mit hohen Temperaturen oder Zündquellen auch langfristig bewähren.
Mit direktem 3D-Druck drei Wochen Produktionszeit auf eine verkürzen
Einer von Avance Designs Kunden ist Energy Access, ein Hersteller individueller Lösungen zur Batterieaufladung für elektronische Ausrüstung in den Branchen Medizin, Verteidigung, Schwerindustrie, Sicherheit und Robotik. Energy Access wandte sich an das Team von Avance, um Hilfe beim Design von Ladevorrichtungen zu erhalten, die in individuell entworfene und jeweils unterschiedlich geformte Batterien passen. „Meine Aufgabe ist es, ein Gehäuse zu entwerfen, in dem die Batterie für die Ladevorrichtung sicher gelagert und positioniert werden kann, sowie ein Fach zu designen, das diese Verbindung ermöglicht“, erklärt Parker.
Für Avance ist das Design und die Entwicklung von Produkten, die mit spezifischer, individuell geformter Ausrüstung integriert werden können, keine Herausforderung. Hindernisse treten erst auf, wenn es darum geht, die Materialeigenschaften des 3D-gedruckten, maßgefertigten Teils mit den massenproduzierten, spritzgegossenen Komponenten des Endproduktes in Einklang zu bringen.
Bei Energy Access ist es eine unternehmensweite Norm, dass alle Bauteile nach UL 94 zertifiziert sein müssen, um sich gegen jegliche unvorhergesehenen Umweltrisiken abzusichern. Daher muss Avance Teile bereitstellen, die nahtlos mit den bestehenden Produkten von Energy Access kompatibel sind. „Wir würden gern die gleichen Materialeigenschaften erreichen, denn so passen die Teile zur Methodologie der endgültigen Baugruppe und das macht es einfacher, die mechanischen Merkmale in das Endprodukt zu integrieren“, so Parker.
Um diese Materialeigenschaften zu erzielen – also Festigkeit, Glätte und Flammhemmung gemäß UL 94 –, musste Avance bisher auf ein Gussverfahren mit Polyurethan ausweichen. Hierfür stellte Tony Parker ein Modell über 3D-Druck oder Zerspanung her, konstruierte eine Silikonform um das Modell herum, beschaffte ein kommerziell verfügbares, UL-zertifiziertes Polyurethan und goss es in die Silikonform, um das Gussteil aus Polyurethan anschließend zu entnehmen und nachzubearbeiten. „Jedes einzelne Teil brauchte Tage, und wenn wir Bestellungen über 20 Stück hatten, beanspruchte das etwa drei Wochen“, erinnert sich Parker.
Dank Flame Retardant Resin kann Parker mehrere Arbeitsschritte überspringen und erheblich schneller vom CAD-Design zum fertigen Bauteil übergehen. „Dass ich das Teil direkt in Flame Retardant Resin 3D-drucken kann, verkürzt die Fertigungsdauer für alle 20 Teile auf ungefähr eine Woche“, so Parker.
Fertigungsmethoden für flammhemmende Gehäuse im Vergleich
Schritte | Durchlaufzeit für 20 Teile | Stückkosten | |
---|---|---|---|
SLA mit Flame Retardant Resin | Drucken, Waschen, Nachhärten, Entfernen der Stützstrukturen, Lackieren | 4–5 Tage | 19,80 $ (6,50 $ Materialkosten, 13,30 $ Arbeitskosten*) |
FDM mit Filament | Drucken, Auflösen der Stützstrukturen, Reinigen, Schleifen, Füllen, Grundieren, Lackieren | 5–6 Tage | 42 $ (7 $ Materialkosten, 35 $ Arbeitskosten*) |
Polyurethan-Guss | Drucken, Waschen, Nachhärten, Entfernen der Stützstrukturen, Gießen von Silikonformen, Gießen von Polyurethan, Reinigen, Lackieren | 21 Tage | 85 $ (25 $ für Modell, Form und Urethan, 60 $ Arbeitskosten*) |
Traditioneller Spritzguss | Outsourcing von Werkzeugbau und Spritzgießen | 20–30 Tage | 250 $ (5000 $ Werkzeug, danach 0,50 $ Stückkosten) |
*Labor costs are calculated at $80/hour.
Oberflächengüte und Bearbeitbarkeit
Dieser verkürzte Arbeitsablauf hatte einen großen Einfluss auf Parkers Entwicklungsprozess, doch ohne einige zusätzliche Überlegungen würde er noch keine Komplettlösung darstellen. Schließlich standen beim FDM-3D-Druck schon seit Jahren UL-zertifizierte Materialien zur Verfügung. Doch die Teile müssen auch eine erstklassige Oberflächenbeschaffenheit aufweisen, ohne deutliche Schichtlinien, wie sie auf FDM-Druckteilen typisch sind. „Ich war schwer beeindruckt von der Oberflächenqualität, die wir mit Flame Retardant Resin erreichen. Die Druckteile sehen fast aus wie grundierte Teile, und auch beim Schleifen verhalten sie sich, als hätten sie eine Grundierung. Sie lassen sich sehr leicht nachbearbeiten und für das Lackieren vorbereiten, was für uns ein echter Pluspunkt ist“, erzählt Parker.
Das Team von Avance muss außerdem sicherstellen, dass die Druckteile als Komponenten größerer Baugruppen fungieren können, weshalb sie sich für das Einfügen von Schraubgewinden eignen müssen. „Gewindeeinsätze zum Einpressen haben bestimmte Parameter, aber wir haben einfach die Empfehlungen für die gewünschte Lochgröße befolgt und ein kleines Presswerkzeug benutzt, um einen Basiseinsatz einzufügen, und das Teil hat das ohne Probleme mitgemacht. Es gab überhaupt keine Schwierigkeiten und die Druckteile haben die Gewindeeinsätze sehr gut aufgenommen“, berichtet Parker.
Eine so leichte Integration macht letzten Endes den Unterschied beim Montageprozess. Parker kann sich darauf verlassen, dass die Formlabs-Druckteile Tests gemäß UL bestehen, den anderen Teilen der Batterieladevorrichtung in Oberflächenglätte und Festigkeit ähneln und konsistent mit Gewindeverbindungen ausgestattet werden können. Obwohl sie aus dem 3D-Drucker stammen, lassen sich Bauteile aus Flame Retardant Resin reibungslos in die Methodologie der Baugruppe des Kunden integrieren. „Speziell Energy Access war davon begeistert, denn die Fertigungslösungen für flammhemmende Materialien mit FDM oder Guss hatten sie nicht überzeugt. Ihnen gefiel die Idee, bei der Entwicklung, Umsetzung von Änderungen und im gesamten Design- und Fertigungsprozess durchweg beim selben Material bleiben zu können“, so Parker.
3D-gedruckte Teile zu erhalten, die sich wirklich wie Thermoplaste verhalten, eine gute Oberfläche und feine Details aufweisen und ähnliche mechanische Eigenschaften bieten wie Spritzgussteile, ist ein großes Plus und spart viel Zeit. Mit Flame Retardant Resin können wir vom CAD-Design direkt zum fertigen Teil übergehen, ohne die zusätzlichen Arbeiten, die bei anderen Verfahren anfallen.
Tony Parker, Direktor bei Avance Design
Nutzung mehrerer Materialien für die Produktion
Avance Design arbeitet jenseits der Domäne von UL-zertifizierten Materialien noch an zahlreichen anderen Projekten. Jedes Projekt beginnt mit einer Diskussion und Analyse der Eigenschaften, die für den Kunden am wichtigsten sind, und für gewöhnlich kann Parker ein passendes Formlabs-Kunstharz ausfindig machen. „Wir haben zu jedem beliebigen Zeitpunkt etwa 20 bis 30 Kunstharzkartuschen hier stehen“, erzählt er. Kürzlich benötigte ein Kunde für sein Projekt ein flexibles Material für Simulationsvorrichtungen für die medizinische Ausbildung. Parker entwarf hierfür Teile aus Flexible 80A Resin. Die Teile überzeugten und Avance druckte mehr als 1000 Stück von ihnen auf ihren Druckern des Typs Form 3+, womit sie auch deren Eignung für die Kleinserienfertigung belegten.
Weitere Möglichkeiten ergeben sich aus der Architekturbranche, wo kleine Stückzahlen von Teilen wie Türenkomponenten benötigt werden, die an Stil und Dekor ihrer Umgebung angepasst sind. Kunden wenden sich an Avance auch für Teile wie individuell entworfene Elektronikgehäuse, die sich in Dekor und Stil eines Gebäudes einfügen. Um die Anforderungen an Festigkeit und Form für die Endverwendung zu erfüllen, gleichzeitig aber die Kosten von Guss oder Zerspanung zu umgehen, stützt sich Parker auf den Form 3+ und Form 3 zur Produktion von Endverbrauchsteilen in Kleinserie.
Bereit für neue Möglichkeiten
Mit dieser weiteren Ergänzung in seinem Materialdepot sieht Parker gespannt den Möglichkeiten entgegen, die sich durch die Anwendungen von Flame Retardant Resin ergeben. „Die Leute sind an Gussprozesse oder FDM-Druck gewöhnt, aber sobald sie sehen, dass dieses Kunstharz zur Verfügung steht, wird das einige Türen öffnen. Es ist ein schnellerer und kostengünstigerer Weg zum fertigen Teil“, meint Parker.
Einige Kunden von Avance hat das komplizierte Verfahren des Gießens nach Parkers Ansicht davon abgeschreckt, 3D-Druck in Anwendungen für die Gesundheitsbranche, den Maschinenbau oder die Robotik auszuprobieren. „Ich bin sicher, einige Kunden haben sich die Sache angesehen und waren der Meinung, als Teil des Gussprozesses lohne es sich nicht. Aber nun, da es einen Weg gibt, das in Branchen mit solchen Anforderungen direkt mit 3D-Druck umzusetzen, freue ich mich auf die neuen Möglichkeiten“, erzählt Parker.
Um zu erfahren, wie Sie selbst von Flame Retardant Resin profitieren können, besuchen Sie die Produktseite oder kontaktieren Sie unser Vertriebsteam für eine Beratung zu ihrem spezifischen Anwendungsfall.