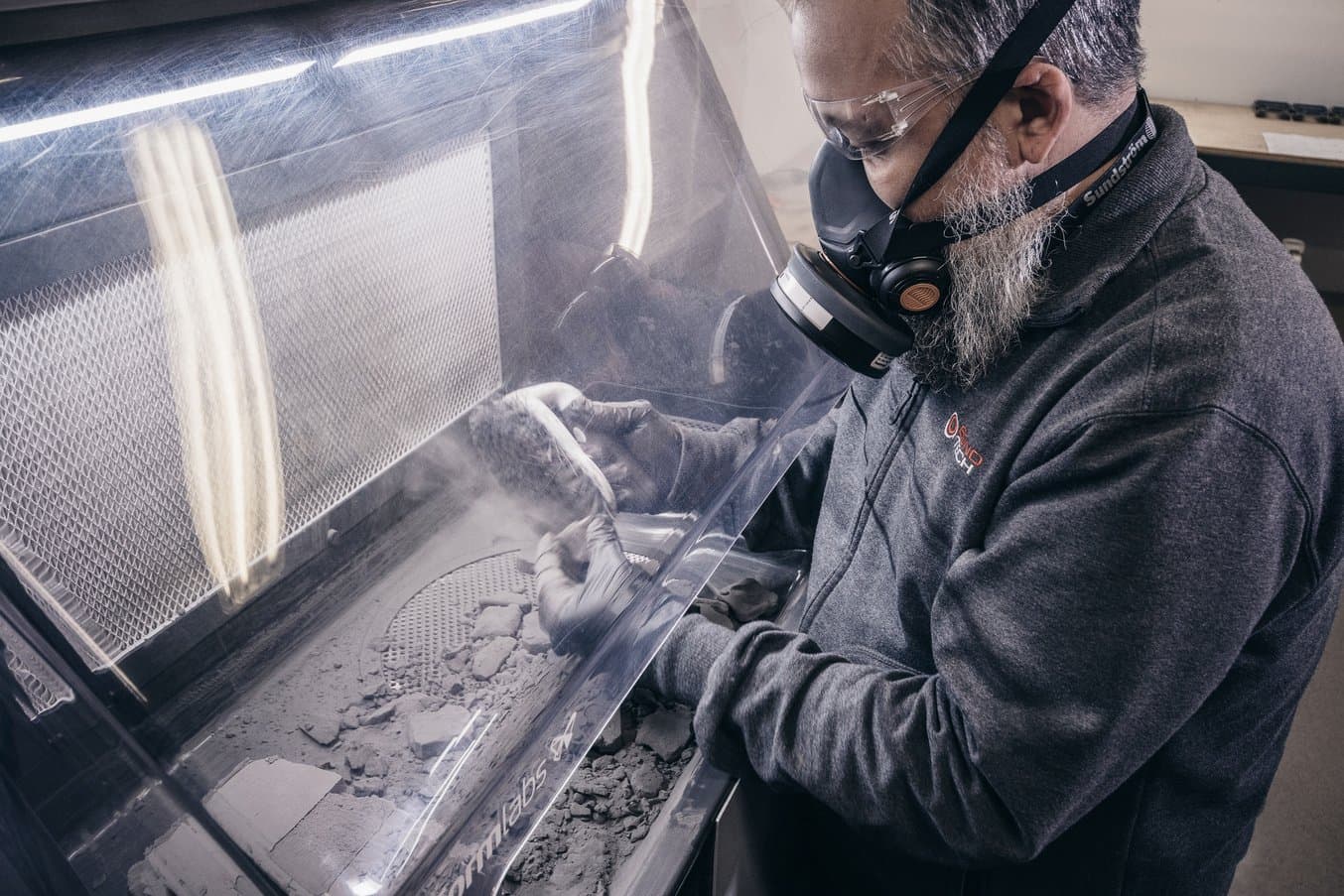
In den vergangenen paar Jahren sind Hersteller mit der unangenehmen Realität konfrontiert worden, dass Globalisierung und vernetzte Lieferketten manchmal eher schädlich als hilfreich sein können. Viele von ihnen stiegen als Übergangslösung erstmals auf 3D-Druck um, während andere Unternehmen, beispielsweise Hersteller von 3D-Druckern, bereits von Anfang an auf eine solche vertikale Integration bauten.
Bondtech ist ein schwedisches Unternehmen, das für die Produktion marktführender Dual-Extruder für FDM-3D-Drucker (Schmelzschichtung) bekannt ist. Im 2014 von Martin Bondéus gegründeten Unternehmen herrscht die Überzeugung, dass 3D-Druck Fertigungsprozessen Agilität, Flexibilität und Kontrolle verleiht, weshalb der Konzern für die betriebsinterne Fertigung von Endverbrauchsteilen den SLS-3D-Drucker (selektives Lasersintern) Fuse 1+ 30W von Formlabs erworben hat.
Indem Bondtech sich vom Prototyping bis zur Produktion im gesamten Prozess auf 3D-Druck stützt, beweist das Unternehmen, dass ein derartiger schlanker Fertigungsansatz sowohl für Produzenten als auch für Kunden hohe Dividenden erbringen kann.
Von Frustration zu Innovation
Als Bondéus 2014 als Produktentwickler tätig war, bereitete ihm sein primäres Prototyping-Hilfsmittel, ein FDM-Drucker, immer mehr Frust. Indem er das Gerät auseinandernahm und bestimmte Bauteile auszutauschen versuchte, konnte er das zugrundeliegende Problem ausfindig machen – nämlich ungleichmäßige Erhitzung und Extrusion. Bondéus sah Wege, den Vorgang zu verbessern, und entwickelte eine Technologie zur dualen Extrusion von FDM-Filament, die mit bestehenden Druckern kompatibel ist.
Heute stellt Bondtech zwei zentrale Produktlinien von Extrudern her, LGX und LGX Lite, sowie eine Vielzahl weiterer Komponenten von FDM-Druckern, für Erstausrüster wie auch für Kunden, die ihre Geräte aufrüsten möchten. In einer Branche, deren Technologie sich rasant verändert und die mit hohen Kosten für die Hardware-Fertigung zu kämpfen hat, ist es Bondtech gelungen, ein Hilfsmittel für enormes Wachstum, aber auch Stabilität zu entwickeln. Das Geheimnis? Natürlich 3D-Druck. Bondéus erklärt uns: „Die additive Fertigung ermöglicht uns Flexibilität bei der Kreation und Aktualisierung neuer Modelle und der Veröffentlichung neuer Produkte. Der Designzyklus ist sehr kurz, weil wir nur auf uns selbst angewiesen sind. Dadurch erreichen wir eine sehr, sehr kurze Markteinführungszeit.“
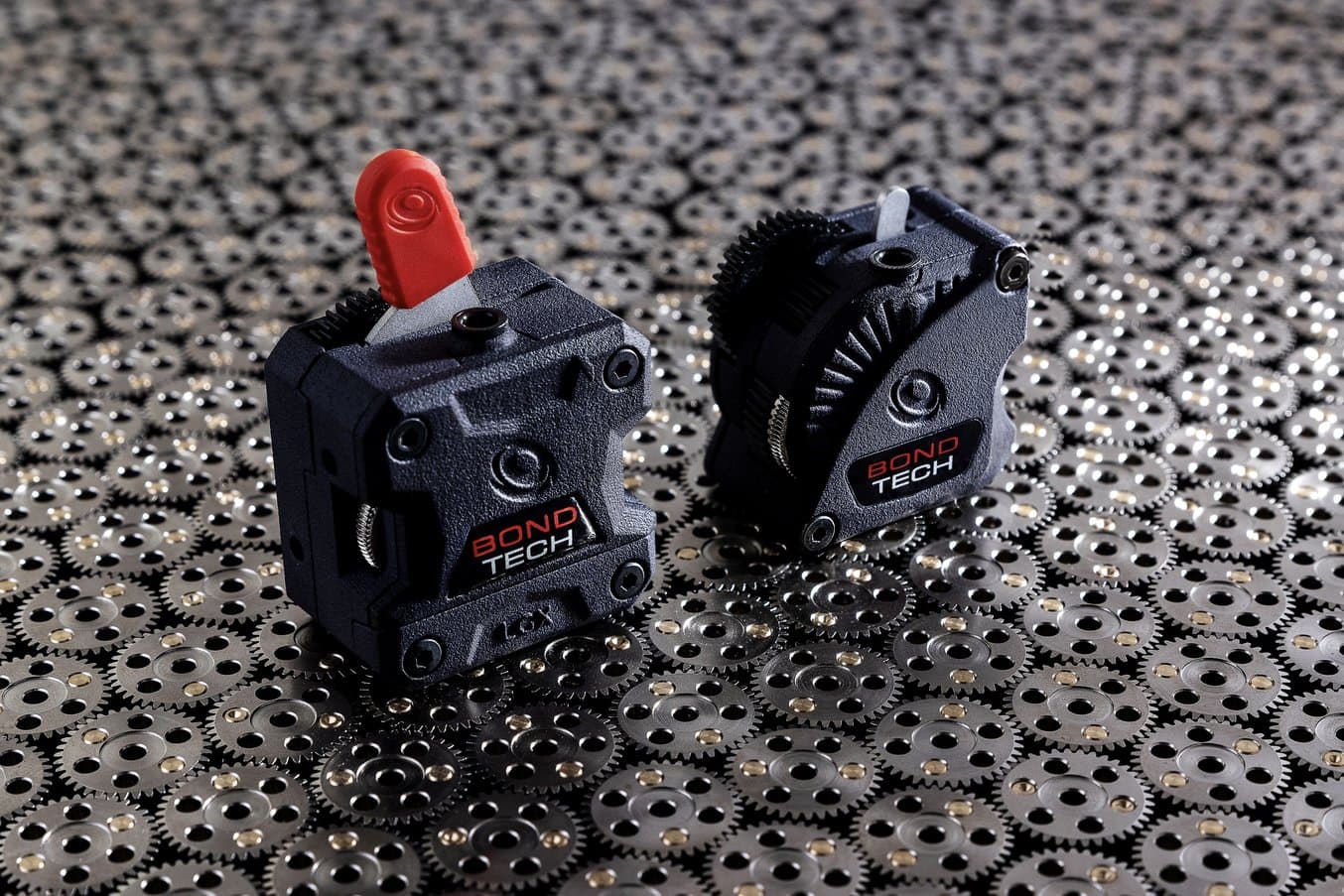
Der LGX und der LGX Lite, beide mit SLS-3D-gedruckten Gehäusen.
Unabhängigkeit als Philosophie
Es ist kein Zufall, dass die Konstruktion von Bondtech darauf ausgelegt ist, Komplikationen wie Lieferverzögerungen oder auch einer globalen Pandemie standzuhalten. „Bei der Fertigung lautet unsere Philosophie: Unabhängigkeit, Agilität und die Fähigkeit, uns vollkommen auf uns selbst zu verlassen“, so das Team von Bondtech. „Im Sinne unserer Selbstständigkeit integrieren wir so viele Prozesse wie möglich vertikal.“ In den frühen Jahren erstellte das Team Prototypen auf FDM-Druckern und forderte die finalen Prototypen und Komponenten für die Endverwendung von Fertigungsdienstleistern an, die über große industrielle SLS- und MJF-Drucker verfügten. „Als wir die Fuse-1-Drucker von Formlabs sahen, dachten wir, das könnte eine gute Lösung für Insourcing sein“, berichtet das Entwicklungsteam von Bondtech.
Indem Bondtech die Produktion von Endverbrauchsteilen fast vollständig in den eigenen Betrieb verlegte (und auch Kapazitäten zur Zerspanung von Metall hinzufügte), konnte das Unternehmen überschaubar und agil bleiben. Das Team kann fast unverzüglich auf Kundenanfragen und Marktresonanz reagieren, ganz ohne die Abfälle und Verluste, die typische Hardware-Produzenten bei einer solchen Umstellung zu befürchten hätten. „Weil wir ein kleines Unternehmen mit einem schlanken Produktentwicklungskonzept sind, kann das Produkt sich durch eine Reihe kleiner Iterationen und Mikro-Verbesserungen weiterentwickeln, ohne an die hohen Produktionsmengen gebunden zu sein, die der Werkzeugbau notwendig macht", so Bondéus.
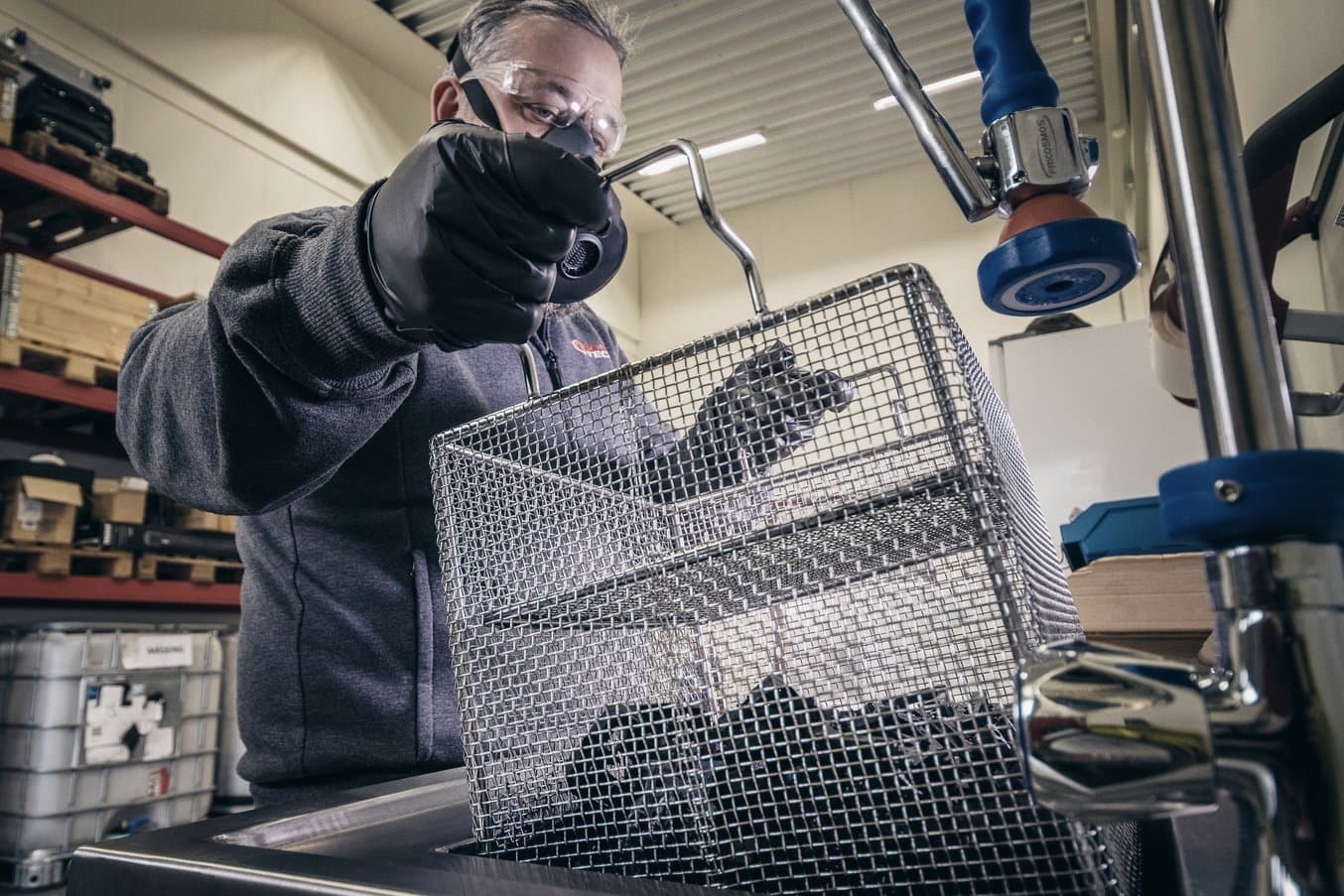
Mit einem betriebsinternen Drucker der Fuse-Serie für die Serienproduktion von Endverbrauchsteilen kann Bondtech eine agile, reaktionsfähige Lieferkette unterhalten, die vom globalen Lieferkettenchaos unberührt bleibt.
Einfach mit dem Drucken loslegen
Der Markt für FDM-3D-Drucker strotzt vor lauter Optionen, von preiswerten DIY-Kits bis hin zu kostspieligen industriellen Varianten. Es sind zahllose Zubehörteile, Tipps, Erweiterungen und Leitfäden zur Optimierung der Filament-Extrusion verfügbar. Der Eintritt in diese noch so überfüllte Nischenbranche ist schwierig. Junge Unternehmen müssen typischerweise zunächst ausgiebige Marktforschung betreiben, um zu ermitteln, ob der Markt Platz für ihr Produkt bietet.
Einer der Vorteile eines vollständig betriebsinternen SLS-Workflows ist Entwickler Nuno Santiago zufolge der, dass die Beurteilung des Marktes nicht abgewartet werden muss. „Es ist schwer, den Erfolg eines neuen Produktes vorherzusagen. Welches Interesse wird wohl auf dem Markt bestehen? Mit betriebsinterner SLS-Produktion beginnen wir einfach mit dem Druck des Produkts. Wir brauchen ja nicht drei Monate lang auf Werkzeug zu warten.“
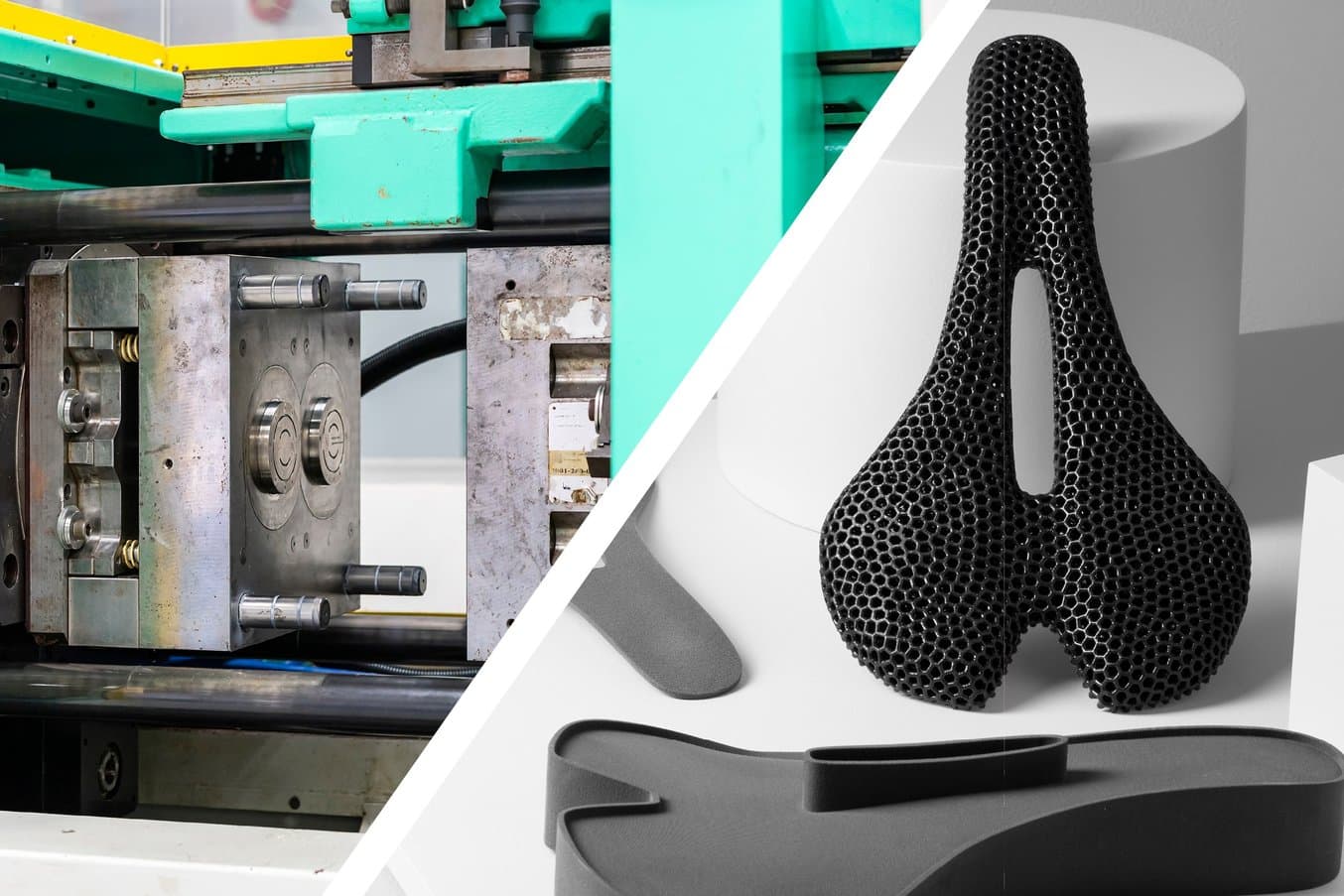
SLS-3D-Druck oder Spritzguss: Wann sollte man Spritzgussteile durch 3D-Druck ersetzen?
Dieses Whitepaper zeigt die Kostendynamik für Anwendungsfälle aus der Praxis und stellt Leitfäden vor für den Einsatz von SLS-3D-Druck, Spritzguss oder einer Kombination beider Verfahren.
Die Fähigkeit, neue Dinge auszuprobieren und die Fertigung je nach Kundenfeedback umzustellen, ist in einer so wachstumsstarken und umkämpften Branche von unschätzbarem Wert. Je mehr neue, leistungsstarke Materialien Hersteller von FDM-Druckern auf den Markt bringen, desto mehr Drucker mit beheizten Druckkammern werden veröffentlicht. Diese neuen Funktionen stellen die Extruder-Komponenten vor eine Herausforderung. Unternehmen, die in bestehendes Produktionswerkzeug investiert haben, können das Design womöglich nicht einfach ändern, um es an die neuen Temperaturen anzupassen – doch Bondtech kann solche Änderungen dank seiner In-house-Produktion leicht umsetzen. „Wir hätten gern eine höhere Steifigkeit bei Produkten, die erhöhten Temperaturen ausgesetzt sind. Deshalb ziehen wir einen Wechsel zu Nylon 12 GF Powder auf den Fuse-Druckern in Betracht“, erklärt Santiago.
Schnell, erschwinglich, effizient
Die Dual-Extruder LGX und LGX Lite sind derzeit zwar die zwei wesentlichen Extruder im Sortiment, doch von Zeit zu Zeit arbeitet Bondtech auch direkt mit den Erstausrüstern oder OEMs (Original Equipment Manufacturer) der FDM-Drucker zusammen, um neue Designs zu entwickeln. Die OEMs stellen Anfragen wie etwa eine etwas andere Montageoption, die an ihr Druckergehäuse angepasst ist, und Bondtech kann innerhalb von Tagen Prototypen liefern. „Mit betriebsinternem SLS erhält man seine Teile in extrem kurzer Zeit. Wir haben sie am nächsten Tag bereit, das ist Wahnsinn. Wir arbeiten nach wie vor mit guten externen Dienstleistern zusammen, aber manchmal benötigt ein Prototyp so immer noch über eine Woche. Mit dem betriebsinternen SLS-Drucker können wir schnell und einfach reagieren“, erzählt das Bondtech-Team. Die kurze Durchlaufzeit ermöglicht es Bondtech, gründlicher zu iterieren, ohne seine Kosten zu erhöhen – was ein Vorteil ist, den das Unternehmen an seine OEM-Kunden weitergeben kann.
"Preislich sparen wir etwa 50–70 % an den Prototypen, indem wir sie betriebsintern mit den Fuse-Druckern herstellen."
Nuno Santiago
Die Skalierung des Betriebs
Dank der dichten Packung von Druckteilen im Fertigungsvolumen der Drucker der Fuse-Serie lassen sich Hunderte von Teilen zugleich produzieren – sogar ineinander verschachtelt, damit jeder Quadratzentimeter des Pulverbettes optimal ausgenutzt wird. Die SLS-Drucker Fuse 1+ 30W sind bei Bondtech rund um die Uhr in Betrieb, und falls das Unternehmen seine Kapazität steigern muss, kann effizient weiter skaliert werden. „Wir drucken auf jedem Drucker in Druckzyklen von 24 Stunden zwischen 50 und 200 Teile, und übers Wochenende starten wir einen großen 48-Stunden-Druck. Wir ordnen unsere Teile sehr eng an und nutzen das gekaufte Pulver bis auf den letzten Rest aus“, berichtet Bondéus.
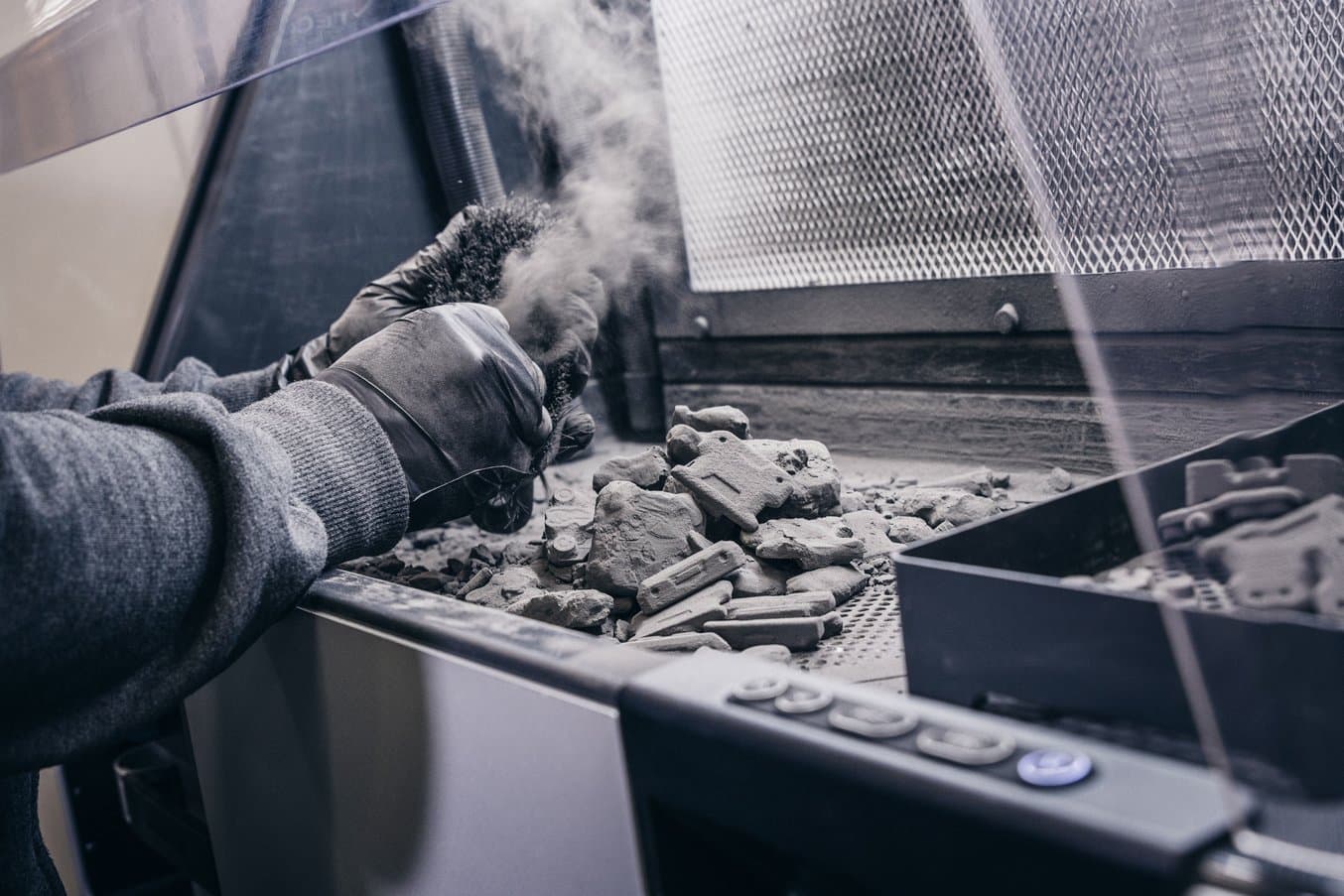
Bondtech nutzt den Fuse Sift, um aus jeder Pulverkartusche das Meiste herauszuholen.
Schon jetzt plant Bondtech die Ausweitung seines Produktangebots und seiner Kundenbasis und hat dabei keinerlei Sorgen, die Produktion nicht entsprechend der Nachfrage skalieren zu können. „Wenn wir uns Designiterationen überlegen, sind wir sofort für die Produktion bereit. Wir können jetzt immer mehr Produkte auf dem Fuse herstellen und neue Materialien ausprobieren. Und wenn wir zehnmal schneller drucken müssen, können wir neun zusätzliche Fuse-Drucker zum Preis einer Maschine von EOS anschaffen“, so Santiago.
Umso mehr Herstellern bewusst wird, dass ihre Kontakte zu weltweiten Zulieferern anfälliger sind als gedacht, werden vertikale Integration, digitale Inventare, In-House-Produktion und Unabhängigkeit immer attraktiver. Herstellern von 3D-Druckern waren die Vorteile der Technologie jedoch schon seit Jahren bekannt, weshalb sie die perfekte Fallstudie darstellen, die anderen Hardware-Produzenten zum Vorbild dienen kann.
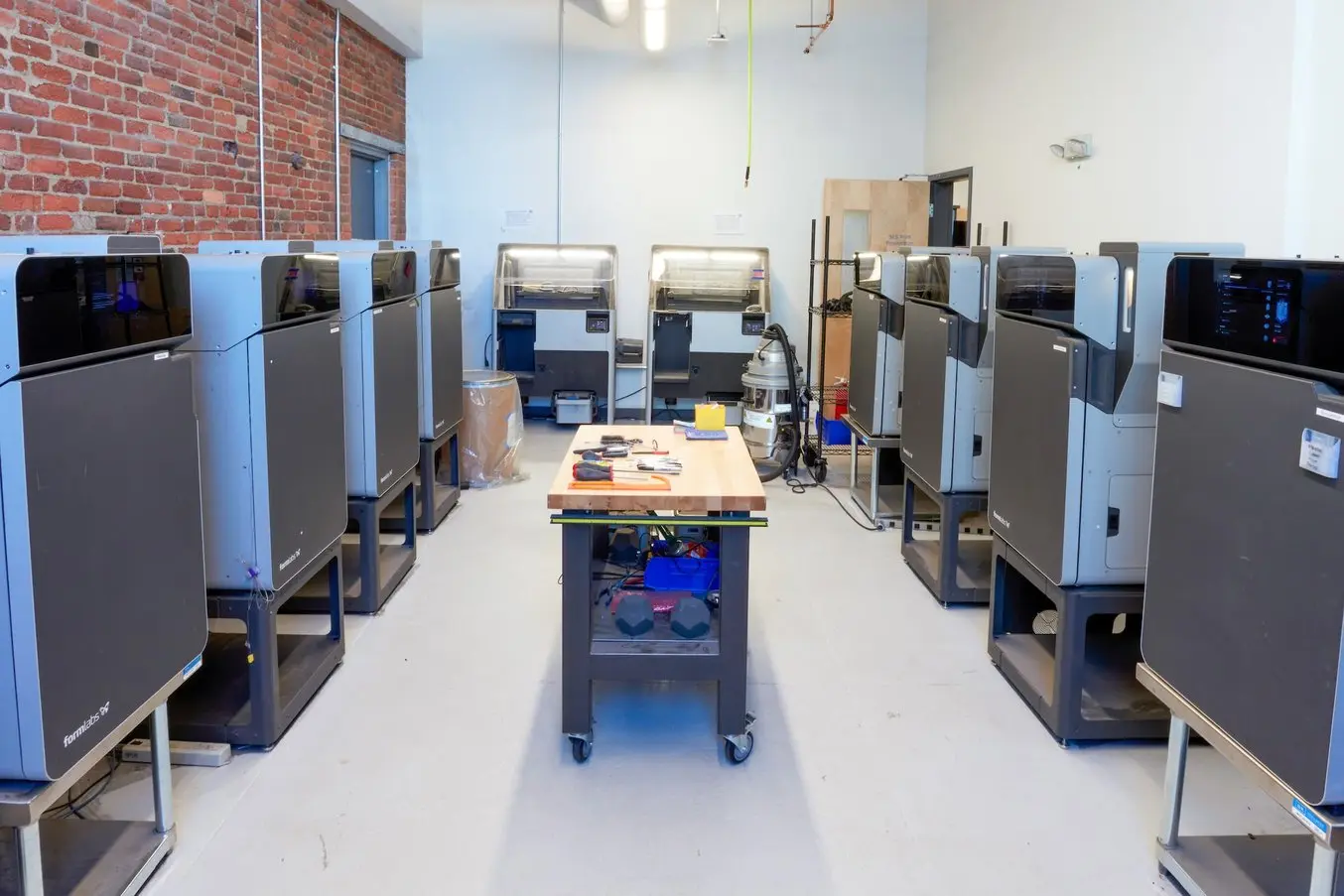
Die Verwaltung von 3D-Druckerflotten
Die Verwaltung mehrerer SLA- und SLS-3D-Drucker muss nicht zwingend kompliziert sein, jedes Unternehmen kann in nur ein oder zwei Tagen eine ganze Flotte von SLA- und SLS-Druckern in Betrieb nehmen. In diesem Leitfaden stellen wir vier verschiedene Fertigungsszenarien mit mehreren Druckern vor, um Ihnen bei der Zusammenstellung eines effizienten Prozesses für jegliches Bauteil oder Produktionsvolumen zu helfen.