Formpressen ist ein vielseitiges Fertigungsverfahren, das sowohl von kleinen als auch von großen Fertigungsunternehmen eingesetzt wird – für eine große Bandbreite an Teilen von großformatigen Flugzeugkomponenten bis zu den Saugern von Babyfläschchen.
In diesem Leitfaden bieten wir eine Einleitung in das Formpressen mit dessen Vorzügen und Anwendungsbereichen. Dann zeigen wir auf, wie jeder auch ohne Vorkenntnisse diesen Prozess für Prototypen nutzen kann oder zur Massenproduktion oder für jede andere beliebige Anwendung.
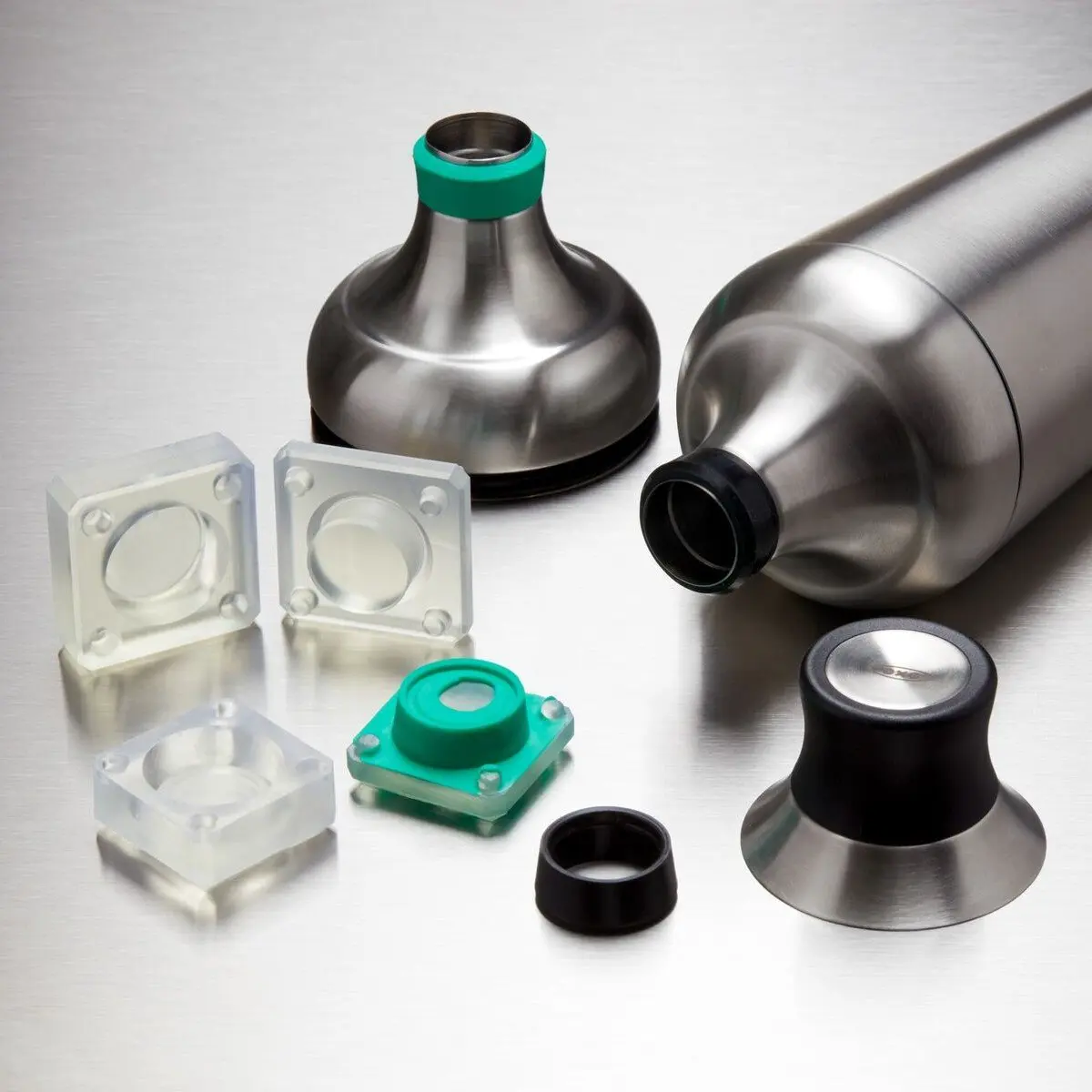
Herstellung von Silikonteilen mit 3D-gedruckten Werkzeugen
Dieser Bericht bietet eine schrittweise Anleitung zu 3D-gedruckten Formwerkzeugen für die Produktion von Silikonteilen, einschließlich bewährter Praktiken beim Formendesign und Fallstudien von Kunden.
Was genau ist Formpressen?
Formpressen ist ein Fertigungsverfahren, bei dem eine bestimmte Menge Formmasse (Rohling genannt) üblicherweise vorgeheizt und dann mit Druck zwischen zwei beheizten Hohlformen (Gesenke genannt) gepresst wird, bis die gewünschte Form erreicht ist.
Wie funktioniert Formpressen?
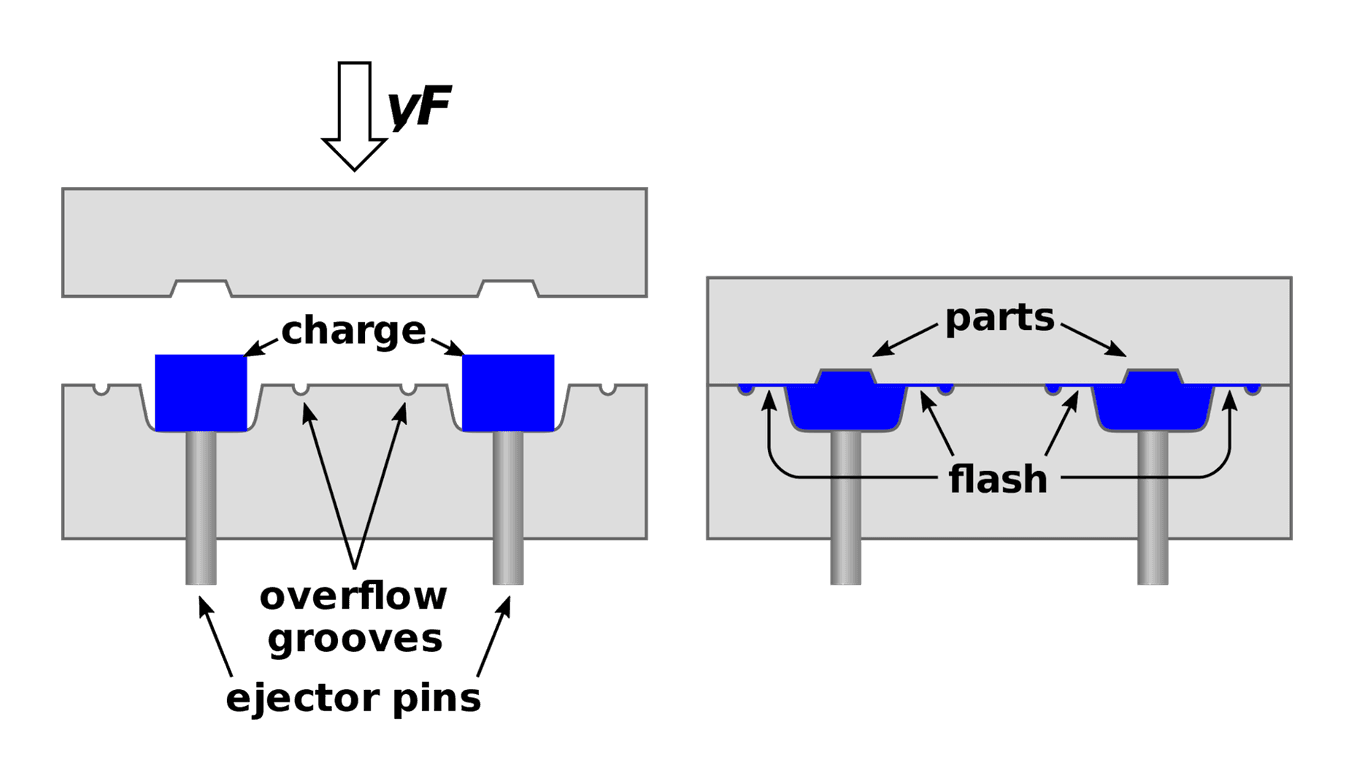
Ein vereinfachtes Diagramm des Formpressverfahrens. (Bildquelle)
Schritt für Schritt sieht der Formpressprozess so aus:
-
Formen (Gesenke) erstellen – Diese Werkzeuge lassen sich auf vielfältige Art herstellen, z. B. via Zerspanung, Druckgießverfahren oder 3D-Druck.
-
Maschine einrichten – Abhängig von der Maschine oder dem Gerät gehört dazu z. B. die Reinigung der Gesenke, das Einschalten der Heizkomponenten oder andere Schritte.
-
Rohling vorbereiten – Wählen Sie das gewünschte Material aus und bestimmen Sie die benötigte Menge. Bei einem zu großen Rohling tritt überschüssiges Material aus und bildet einen Grat, der manuell entfernt werden muss.
-
Rohling positionieren – Platzieren Sie den Rohling in der Mitte des Untergesenks.
-
Teil in Form pressen – Schließen Sie mit dem Obergesenk ab und üben Sie Druck aus. Warten Sie, bis das Teil seine Form annimmt. Viele Hersteller führen bei der Kompression auch Hitze zu, um das Rohmaterial weicher zu machen und die Produktion zu beschleunigen.
-
Teil entnehmen – Entnehmen Sie das fertige Teil aus der Form.
-
Teil reinigen – Ein eventueller Grat an den Kanten muss manuell abgeschnitten oder anderweitig entfernt werden. Außerdem muss das Teil vor der Montage gegebenenfalls gereinigt werden.
Formpressen vs. Spritzguss
Formpressen und Spritzguss sind sich sehr ähnlich, doch gibt es einen entscheidenden Unterschied. Beim Formpressen werden die Formen um das Rohmaterial herumgedrückt, beim Spritzguss hingegen wird das Rohmaterial in den Hohlraum der Form hineingespritzt.
In der heutigen Zeit verwenden Hersteller meist sowohl Formpressen als auch Spritzguss, aber für unterschiedliche Arten von Teilen. Spritzguss bietet sich üblicherweise für komplexere Teile an, wohingegen sich Formpressen sehr gut für relativ einfache Teile eignet – dazu zählen ultragroßformatige Grundformen, die sich mit Extrusionstechniken nicht herstellen ließen.
Spritzguss hat kürzere Zyklen als Formpressen, sodass er bei der Produktion großer Chargen meist schneller und kostengünstiger ist. Dem gegenüber wirken beim Formpressen allgemein niedrigere Druckkräfte, weshalb die Werkzeugbestückung oft billiger ist. Außerdem hält sich die Materialverschwendung in Grenzen, was gerade bei der Arbeit mit teuren Materialien ein Vorteil ist.
Die Faustregel besagt, für Großserienfertigung ist Spritzguss geeigneter, für kleine und mittelgroße Serien bietet sich eher Formpressen an.
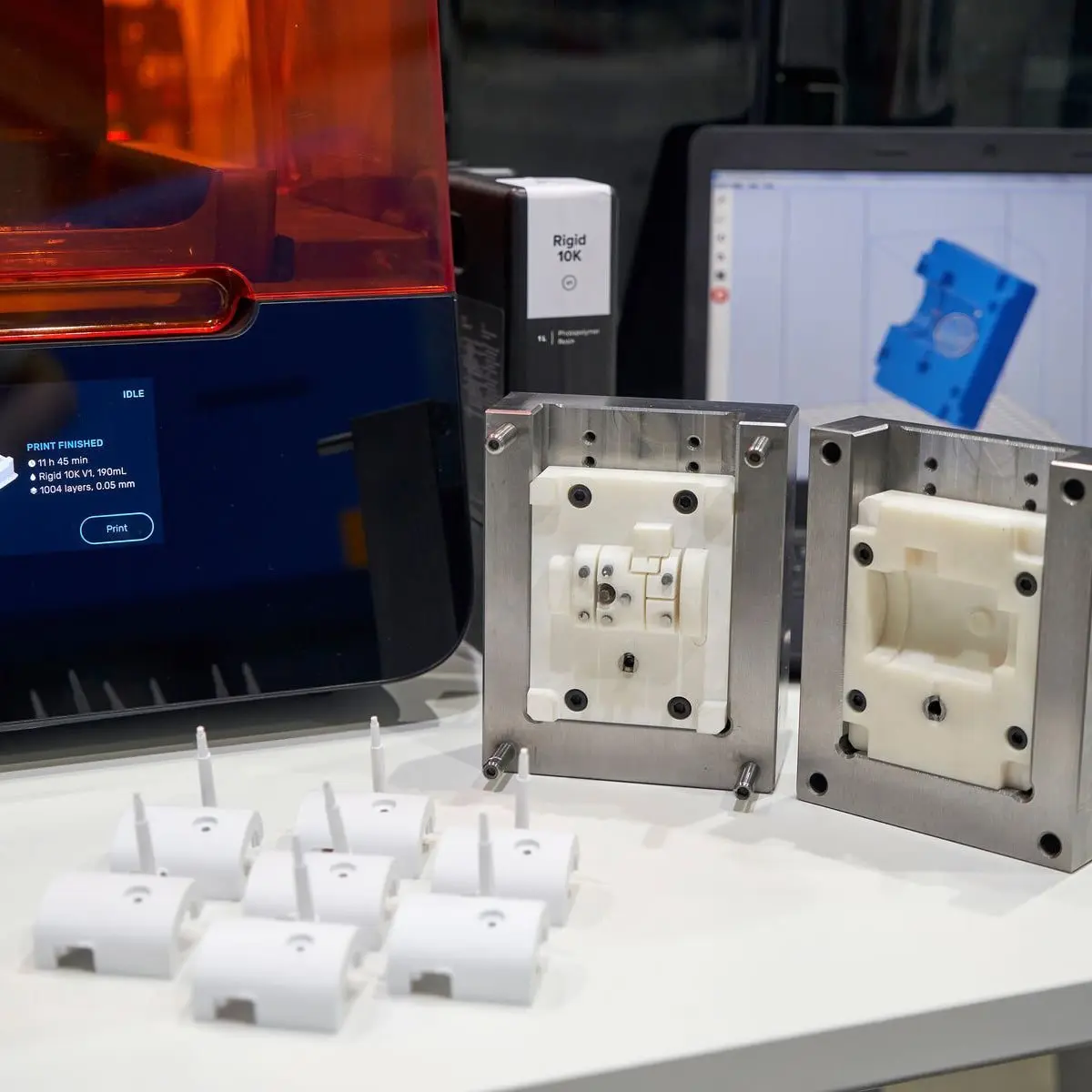
Schnelles Spritzgießen von Kleinserien mit Formen aus dem 3D-Drucker
Laden Sie dieses Whitepaper herunter und erfahren Sie mehr über die Methoden und Richtlinien zur Herstellung 3D-gedruckter Spritzgussformen, um die Kosten zu senken und Lieferzeiten zu verkürzen. Es enthält Fallstudien aus der Praxis von Braskem, Holimaker und Novus Applications.
Die Vor- und Nachteile des Formpressens
Nun, da wir das Formpressverfahren mit dem Spritzguss verglichen haben, werfen wir gemeinsam einen Blick auf die speziellen Vorzüge und Einschränkungen dieses Fertigungsprozesses.
Kostengünstige Produktion
Formpressen ist oft die kostengünstigste Fertigungsmethode, wenn es um einfache, große und vorwiegend flache Teile geht. Biegungen und Mulden in den Designs lassen sich via Formpressen umsetzen, extreme Winkel und große Vertiefungen sind hingegen eine Herausforderung. Dank des vergleichsweise niedrigen Drucks bleibt die Werkzeugbestückung erschwinglich und die Formen halten für gewöhnlich recht lange, ohne sich zu verformen oder ausgetauscht werden zu müssen. Um der langen Zyklusdauer beim Formpressen entgegenzuwirken, nutzen Hersteller Formen mit mehreren Hohlräumen, um verschiedene Teile gleichzeitig im selben Zyklus herzustellen.
Herstellung stabiler Teile
Beim Formpressen entstehen feste Teile ohne Fließspuren oder Nähte. Auch die strukturelle Integrität formgepresster Teile ist äußerst hoch. Da dieses Verfahren mit Verbundwerkstoffen funktioniert, lassen sich auch ganz einfach haltbare und korrosionsbeständige Teile und Produkte produzieren.
Designfreiheit
Formpressen ist eine großartige Fertigungsmethode für Ingenieure und Produktentwickler. So lässt sich beispielsweise die Prototypenentwicklung mit diesem kostengünstigen Verfahren durchführen. Einfache Gesenke können mittels CAD-Software (computer-aided design, engl. für computerunterstütztes Entwerfen) entworfen und dann 3D-gedruckt werden, um verschiedene Materialien schon mit einem handelsüblichen Schraubstock in Form zu bringen. Ein Beispiel von OXO für eine solche Anwendung finden Sie weiter unten in diesem Artikel.
Einschränkungen
Formpressen bietet eine Vielzahl von Vorteilen, stößt jedoch auch an einige Grenzen. Formpressverfahren sind ungeeignet für die Produktion komplexer Teile, beispielsweise mit schrägen Winkeln oder kleinen Details. Die Zyklen sind mit mehreren Minuten vergleichsweise langsam gegenüber Verfahren für die Großserienproduktion. Beim Spritzguss zum Beispiel beträgt die Zyklusdauer oft nur wenige Sekunden.
Gleichermaßen kostet Formpressen auch mehr Arbeitszeit, bedingt durch die verhältnismäßig lange Zyklusdauer. Grate und Überfänge müssen manuell entfernt werden von den formgepressten Teilen, wodurch mehr Zeit und Material verloren gehen. Trotz all dieser Einschränkungen ist Formpressen eine wichtige Fertigungsmethode, mit der eine Fülle an Produkten unseres täglichen Lebens hergestellt werden.
Anwendungen des Formpressens
Die Anwendungsbereiche des Formpressens sind vielschichtig. Hier sind ein paar Beispiele für die Vielzahl an formgepressten Teilen, mit der wir es tagtäglich zu tun haben:
-
Fahrzeugteile – Viele große Teile und Verkleidungen für Autos, Traktoren und andere Fahrzeuge werden mittels Formpressen hergestellt. Auch viele der Kunststoffteile im Fahrzeuginnenraum oder von Motorkomponenten lassen sich formpressen.
-
Computer- und Gaming-Zubehör – Komponenten für Videospiel-Controller, Tastaturen und vieles mehr werden oft formgepresst.
-
Kochgeschirr – Viele Küchenutensilien und -Geräte haben formgepresste Teile. Essgeschirr wie Schüsseln, Tassen, Teller und andere – insbesondere aus Melamin – wird oft mittels Formpressen hergestellt.
-
Elektrische Komponenten – Formpressen wird oft für Steckdosen, Lichtschalter, Verkleidungen und Messgeräte verwendet.
-
Teile von medizinischem und zahnmedizinischem Gerät – Viele Kunststoff- und Silikonteile im medizinischen Sektor werden formgepresst, z. B. Kolbenstopfen von Spritzen oder Beatmungsmasken.
Formpressen zur Herstellung von Küchenzubehör.
Die verschiedenen Arten der Formpressmaschinen
Formpressgeräte gibt es in allen Größen, von industriellen Maschinen bis zu kleinen selbstgebauten Lösungen. Dabei stehen die Formpressmaschinen den auf ihnen produzierten Teilen in nichts nach und sind ebenso vielfältig wie die Designer und Ingenieure, die sie sich ausgedacht haben. Im nächsten Abschnitt besprechen wir einige Beispiele.
Industrielle Hydraulik-Formpressmaschinen
Große, industrielle Formpressmaschinen eignen sich am besten für große Verbraucherteile.
Hydraulische Hebesysteme bieten viel Druck zur Herstellung großer Einheitsteile. Die Arbeiter überwachen dabei den Prozess von einer separaten Steuerkonsole aus.
Benchtop-Pressen
Kleinere Pressmaschinen für den Benchtop eignen sich ideal für die Herstellung kleiner und mittelgroßer Teile und Produkte. Die Benchtop-Pressen von Beckwood beanspruchen weniger Platz als große Industriepressen, eignen sich aber dennoch für Großserien. Mehrere Zugriffspunkte erleichtern Arbeitern die Entnahme der Teile und das Entfernen des Grats. Durch die geringere Größe lassen sich solche Maschinen auch in kleineren Lagerhäusern und Fabriken einsetzen.
Kaltformpressmaschinen (ohne Hitzezuführung)
Wie schon angesprochen, lässt sich das Formpressen auch ohne Hitzezuführung durchführen. Dies gilt für Formpressmaschinen aller Größen. Einige Hersteller nutzen bewusst Kaltformpressmaschinen, erwärmen aber den Rohling, bevor er im Gesenk platziert wird. Die Zuführung von Hitze zu bestimmten Zeitpunkten steuert die Aushärtung des fertigen Produkt und verkürzt so die Produktionszyklen.
Nassformpressmaschinen
Nassformpressmaschinen kommen zum Einsatz, um Kunstharze, Epoxyden und andere flüssige Substanzen mit festen Gewebestoffen zu kombinieren.
Nasspressung ist zu einem festem Bestandteil der Herstellung robuster Autoteile und -komponenten geworden. Konzerne wie BMW nutzen Nassformpressmaschinen in ihrer Produktion.
Selbstgebaute Formpressgeräte
Formpressen eignet sich außerdem für Designer und Bastler zuhause. Weiche Materialien wie Urethan lassen sich schon bei relativ geringem Druck formpressen. Mit einem 3D-Drucker und CAD-Software stellt man problemlos komplexe Gesenke her. Bei vielen kleinen Projekten genügt zur Druckerzeugung schon ein herkömmlicher Schraubstock oder ein Hebelklemmsystem.
Materialien zum Formpressen
Sowohl Thermoplaste als auch Duroplaste sind mit dem Formpressverfahren kompatibel. Thermoplaste sind Kunststoffe, die bei Erwärmung weicher und biegsamer werden und bei Abkühlung aushärten. Ein Thermoplast kann mehrfach erhitzt und abgekühlt (oder in neue Formen gebracht) werden.
Duroplaste hingegen sind Kunststoffe und andere Polymere, die nach Hitzeeinwirkung definitiv aushärten – d. h. sie lassen sich nur einmal formen. Beim Formpressverfahren wechseln Duroplaste ihre chemische Struktur auf eine Weise, die sich nicht ändern oder wiederholen lässt.
Zu den gängigsten Materialien beim Formpressen zählen:
-
Diallylphthalat (DAP)
-
Epoxidharz
-
Ultrahochmolekulares Polyethylen (HDPE)
-
Melamin
-
Polyamidimide (PAI)
-
Polyetheretherketon (PEEK)
-
Polyurethan (PU)
-
Polyphenylensulfid (PPS)
-
Phenoplaste (PF)
-
Polytetrafluorethylen (PTFE)
-
Silikon
-
Harnstoffharze (UF-Harze)
-
Urethan
Gesenke zum Formpressen erstellen
Abhängig vom zu formenden Material bzw. Rohling gibt es verschiedene Möglichkeiten des Formenbaus. Der Schlüssel zum Erfolg ist hierbei, dass die Gesenke dem gesamten Formpressprozess standhalten. Wenn Sie also mit Hitze arbeiten, müssen Sie Gesenke verwenden, die extreme Temperaturschwankungen tolerieren. Außerdem müssen die Gesenke natürlich dem aufgebrachten Pressdruck widerstehen.
Druckguss
Druckguss zählt zu den beliebtesten Formenbaumethoden für Formpressgesenke und andere Fertigungsverfahren. Dies begründet sich darin, dass Druckguss robuste Metallteile zu günstigeren Preisen liefert als alternative Fertigungsmethoden. Dabei stammen die Stümpfe für den Druckguss zumeist aus der CNC-Bearbeitung, da diese beiden Fertigungsverfahren oft Hand in Hand gehen.
CNC-Bearbeitung
CNC-Bearbeitung ist die beste Wahl für detailreiche Formpressgesenke. Die computergestützte Steuerung der CNC-Bearbeitung gibt Ingenieuren mehr Kontrolle über das Design. Werkzeugbestückung auf diese Weise kann jedoch ins Geld gehen. Einige Hersteller fallen deshalb auf eine Kombination aus Druckguss und CNC-Bearbeitung zurück, um kostengünstigere Formen anzufertigen.
3D-Druck
Die Werkzeuge zum Formpressen lassen sich auch mit 3D-Druck anfertigen. Bei der Prototypenentwicklung kleinerer Teile ist 3D-Druck wahrscheinlich die billigste und schnellste Lösung zur Gesenkfabrikation. In der CAD-Software lassen sich schnell mehrere Iterationen erstellen, die dann gedruckt und getestet werden. 3D-Druck kommt dabei am häufigsten für Formpressgesenke zum Einsatz, die ohne Hitzezuführung auskommen.
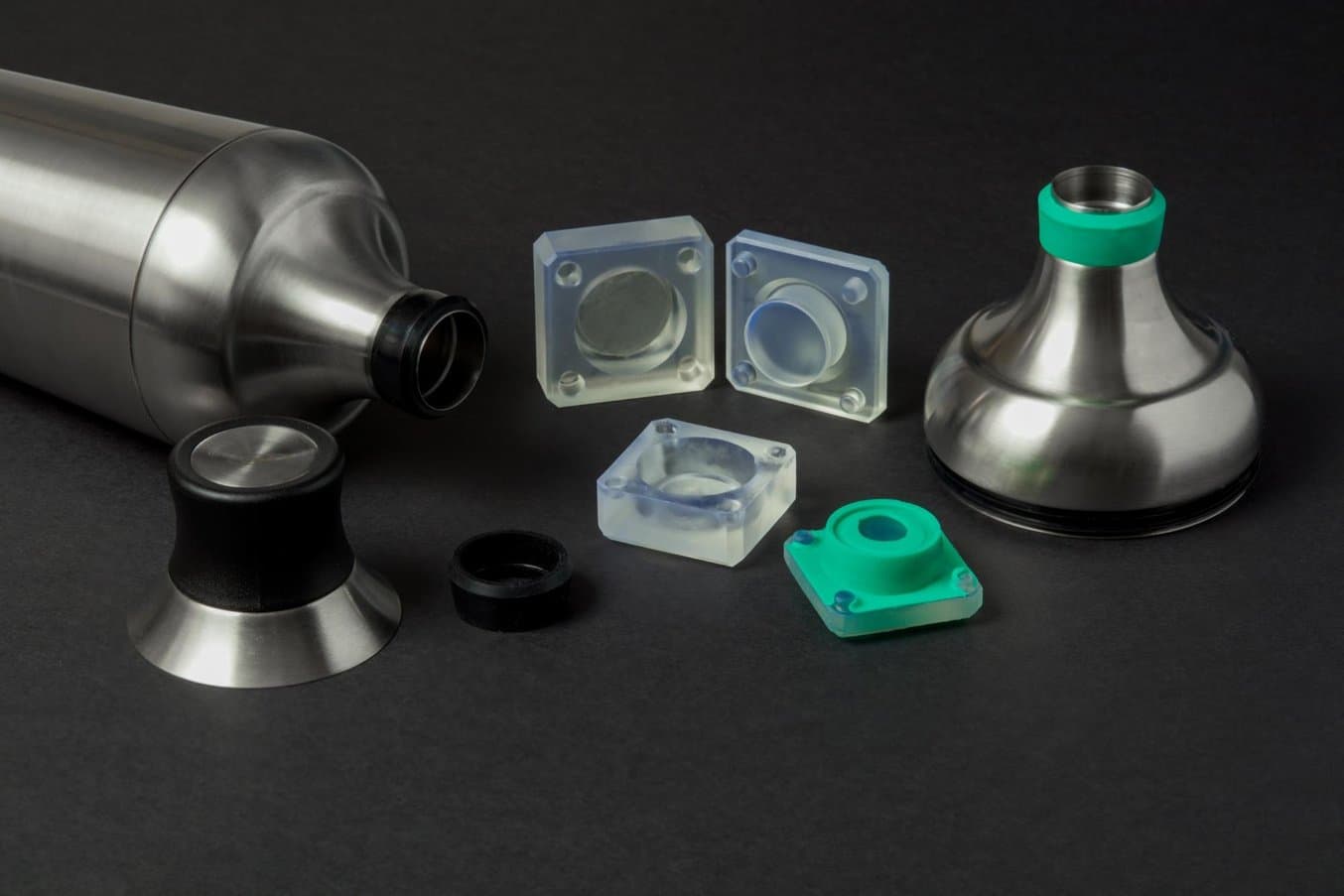
3D-Druck ist eine schnelle und billige Methode zur Anfertigung von Formpressgesenken.
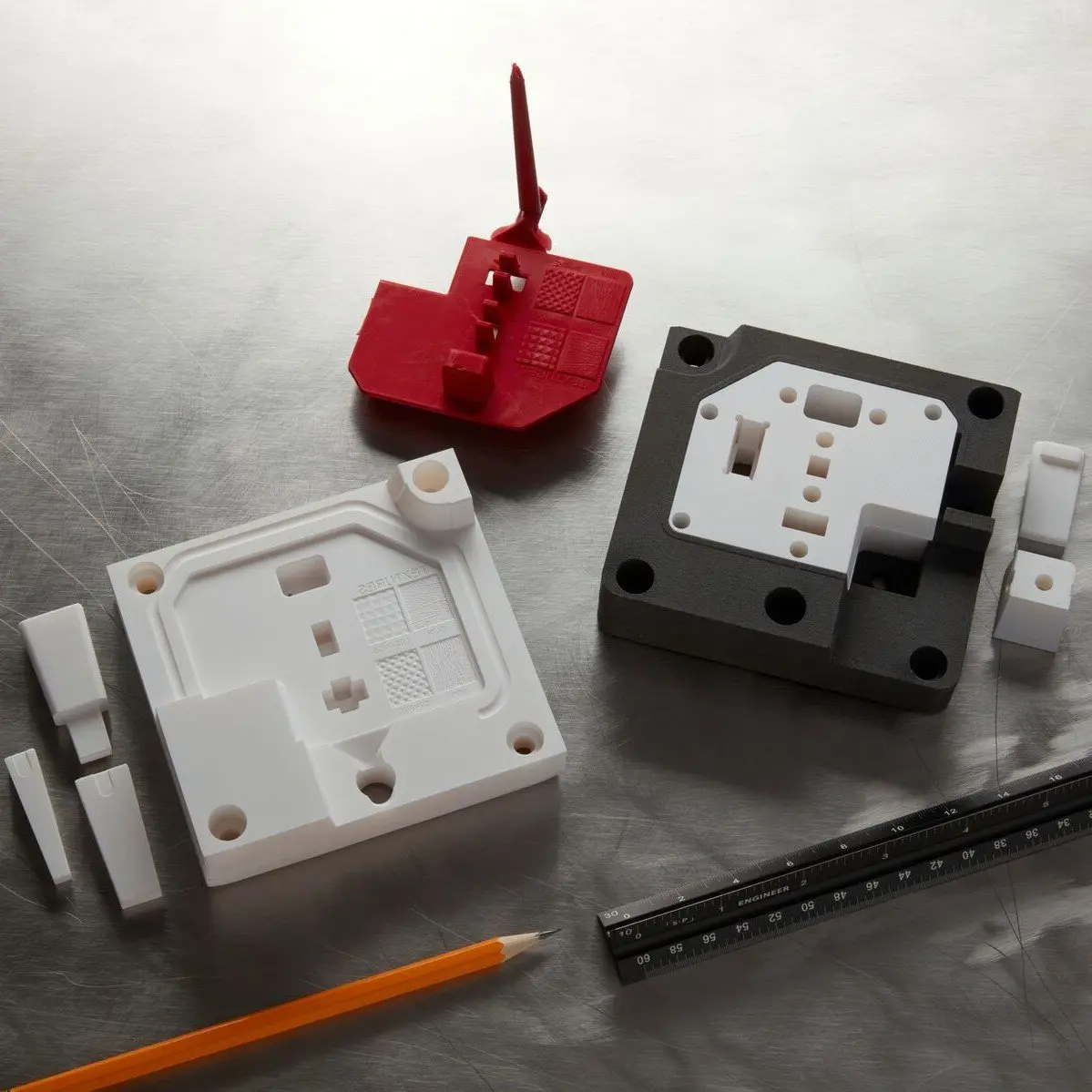
Leitfaden zum Rapid Tooling
In diesem Whitepaper sprechen wir über die Kombination von Rapid Tooling mit traditionellen Herstellungsverfahren wie Spritzguss, Thermoformen oder anderen Gießverfahren.
Wie OXO Prototypenentwicklung via Formpressen betreibt
OXO ist eine Marke mit Sitz in den USA, die ergonomische und praktische Gegenstände für den Haushalt herstellt, einschließlich einiger ikonischer Küchengeräte und -utensilien. Die Produktentwickler bei OXO verwenden Stereolithografie-3D-Druck (SLA) für Prototypen sowohl in Form als auch in Funktion. Bei der Prototypenentwicklung kautschukartiger Komponenten wie Dichtungsringe sind jedoch Hybridverfahren unverzichtbar.
Die Ingenieure bei OXO mussten einen funktionsfähigen Prototypen einer Schüttelbecherdichtung anfertigen, die für einen wasserdichten Verschluss der Teile sorgt. Nachdem sie viele verfügbare Silikone getestet hatten, entschieden sie sich für ein Formpressverfahren mit dem Zwei-Komponenten-Silikonkitt Castaldo Quick-Sil. So sollte ein wasserdichter Prototyp mit den Eigenschaften der fertigen Dichtung angefertigt werden. Die Gesenke dieses Prototoypen sind allgemein ein gutes Beispiel für die Methode und das Formdesign in der Dichtungsfertigung.
Die Ingenieure bei OXO erstellten ihre Gesenke aus Clear Resin mit einem SLA-3D-Drucker von Formlabs. Nachdem die Gesenke gewaschen und ausgehärtet wurden, bereitete man sie zum Formpressen vor. Die Innenseite wurde mit einem Formtrennmittel beschichtet. Als nächstes wurde die vorbereitete Silikonmasse im Gesenk platziert.

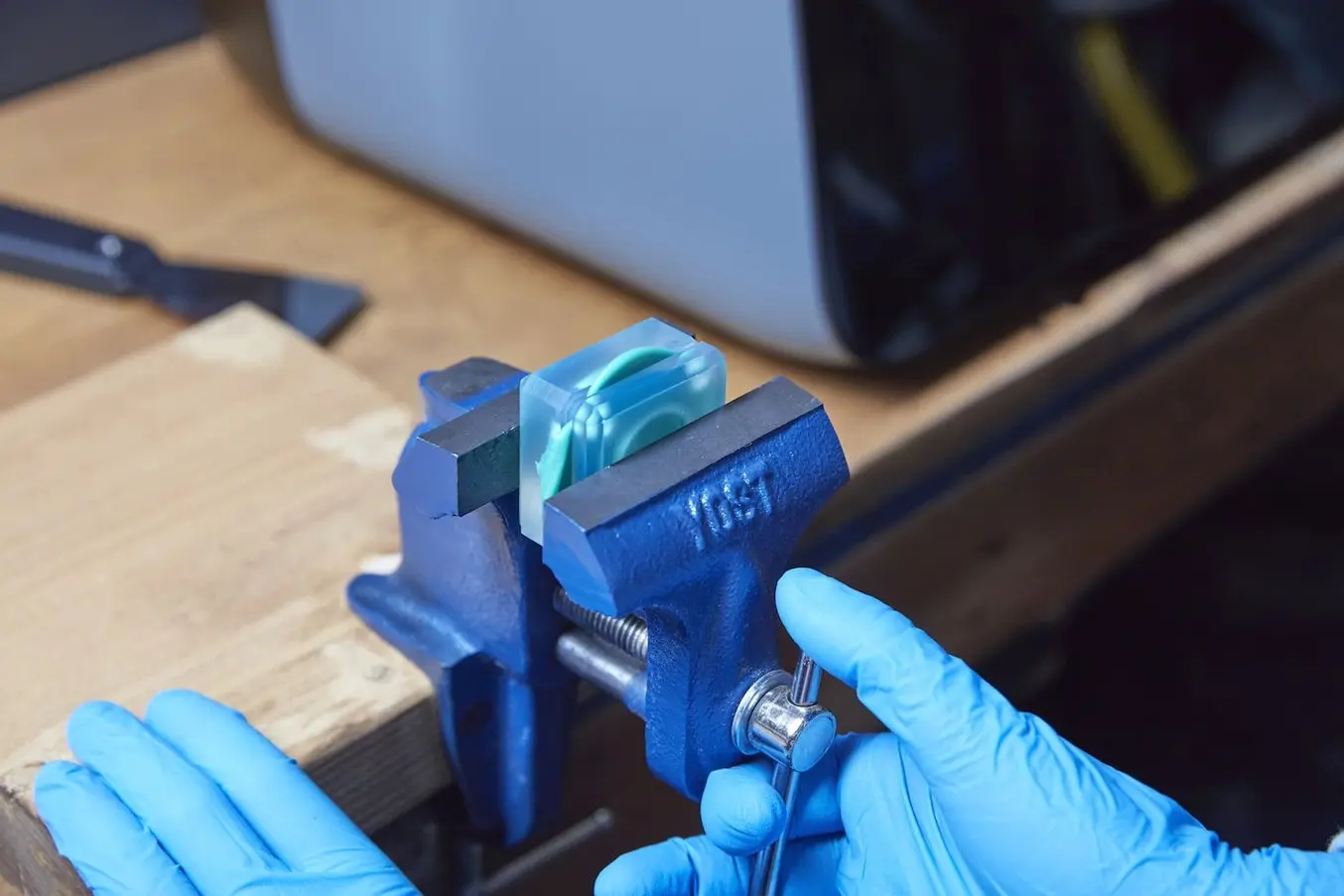
Links: Die Silikonmischung wird im 3D-gedruckten Gesenk platziert. Rechts: Die Gesenke werden in einen Schraubstock gespannt.
Danach wurde das Obergesenk aufgesetzt und die Ingenieure spannten die beiden Gesenke in einen Schraubstock ein, um die gewünschte Menge Druck auszuüben. Nachdem das Teil ausgehärtet war, wurde es aus dem Gesenk entnommen und zugeschnitten. Sie können diesen Prozess leicht für Ihre Belange ummünzen, indem Sie dem schrittweisen Leitfaden in unserem Whitepaper folgen.
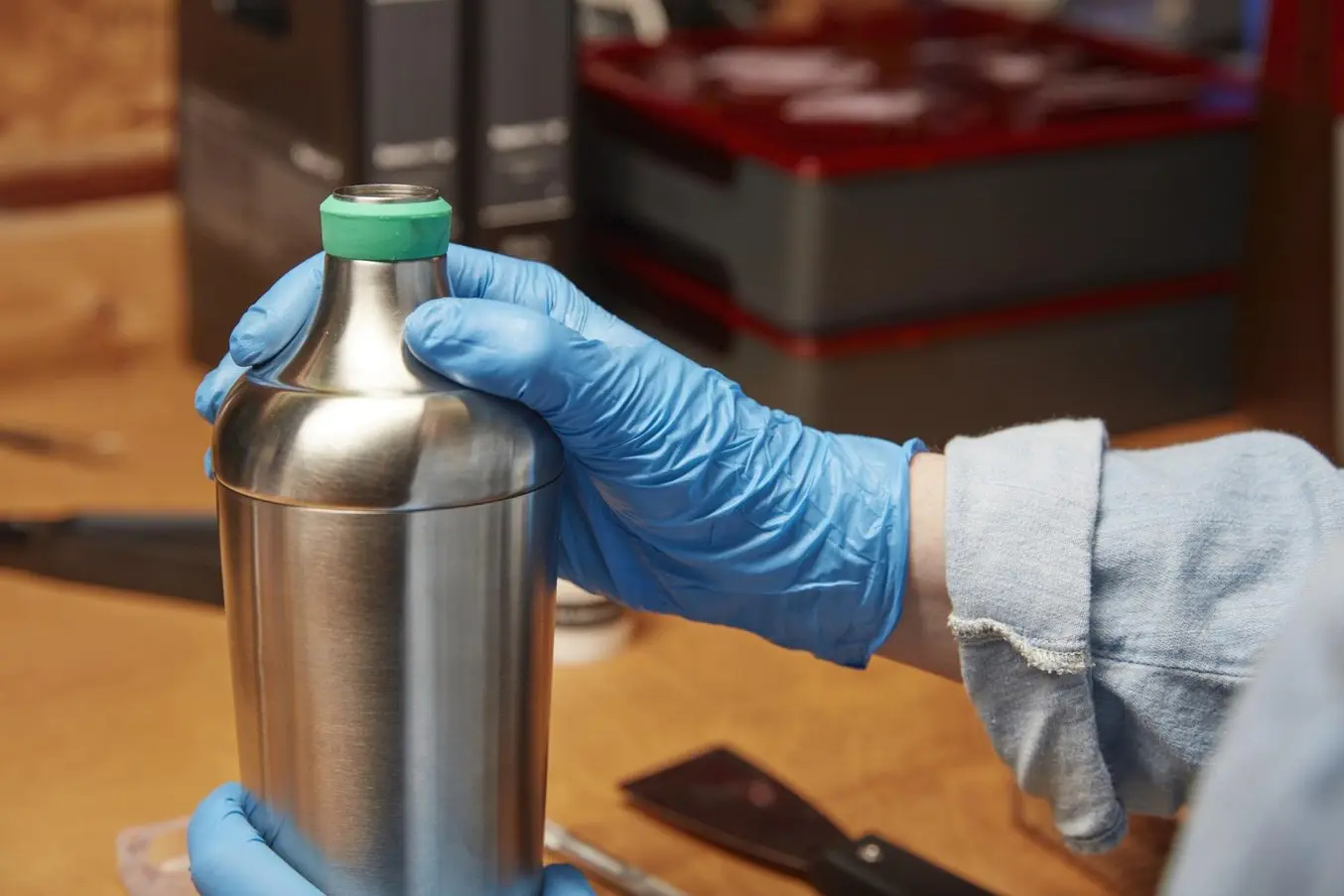
Der finale Prototyp der Schüttelbecherdichtung.
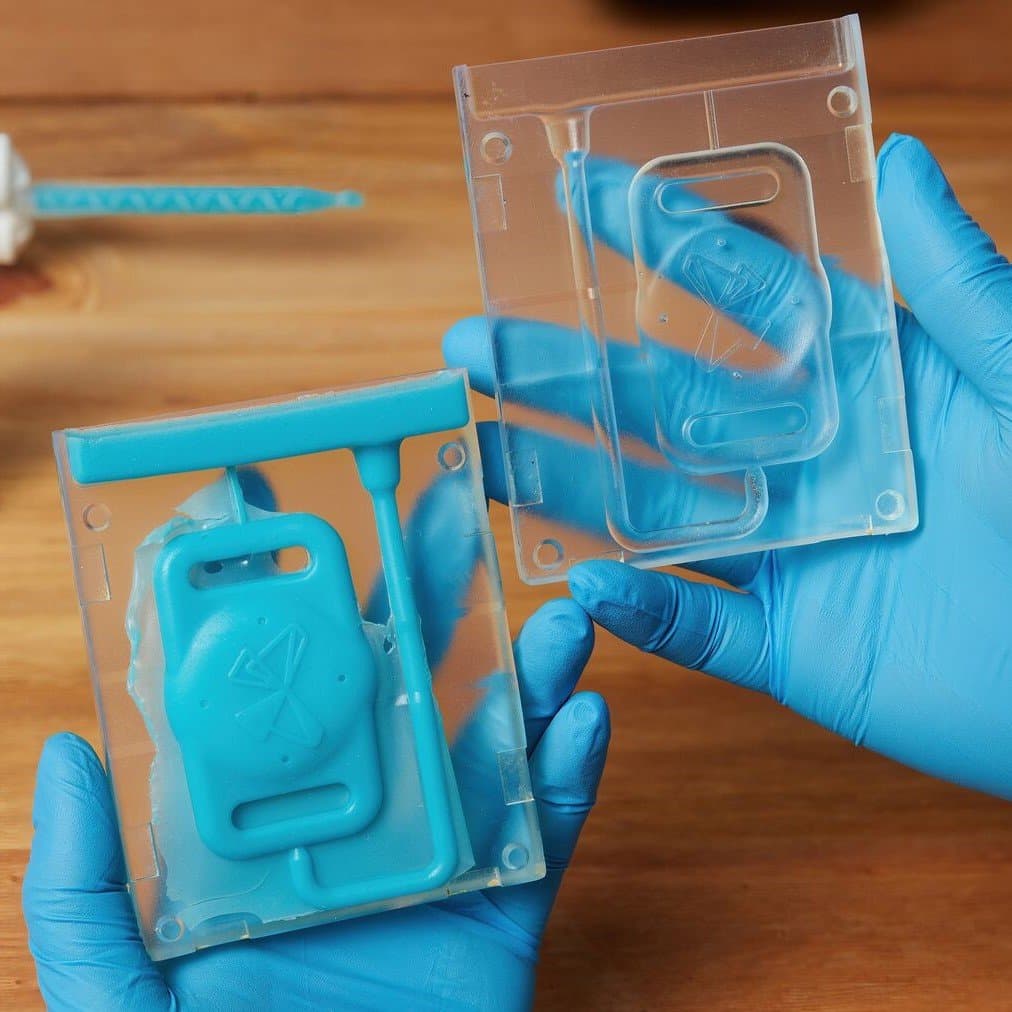
Wie man Silikonteile mit 3D-gedrucktem Werkzeug produziert
In diesem Webinar stellen wir ihn ein detailliertes Beispiel eines Umspritzvorgangs durch Schwerkraftguss vor, bei dem die Form aus Formlabs' Clear Resin gedruckt wurde. Wir besprechen auch die Auswahl der richtigen Form für Ihre Anwendung, die Kompatibilität von Silikon und Kunstharz und bewährte Praktiken beim Silikonguss.
Formpressen, Spritzgießen, Vakuumformen und Silikongießen mit 3D-Druck
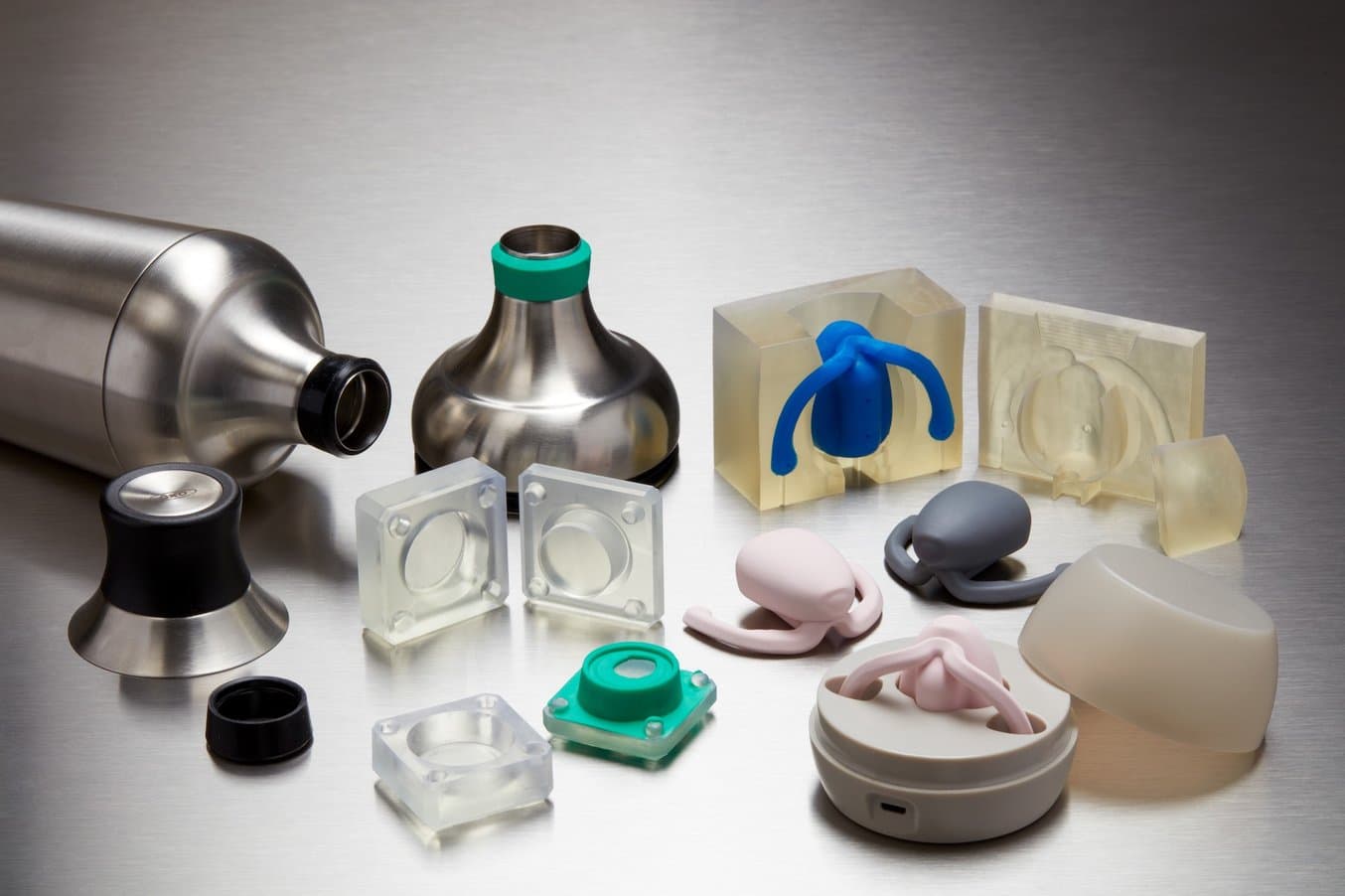
Falls Sie sich für Schritt-für-Schritt-Anleitungen zum Formenbau mit 3D-Druck interessieren, schauen Sie doch unsere kostenlosen Lehrwebinare und laden sie unsere kostenlosen Whitepaper herunter:
-
Schauen Sie unser Webinar über die Grundlagen des Formendesigns und wie sich diese auf 3D-gedruckte Formen auswirken. Sehen Sie Beispiele realer Prototypenformen sowie 3D-gedruckter Formen in der Produktion.
-
Unser Whitepaper bietet eine schrittweise Anleitung zu 3D-gedruckten Formwerkzeugen für die Produktion von Silikonteilen, einschließlich bewährter Praktiken beim Formendesign und Fallstudien von Kunden.
-
Laden Sie dieses Whitepaper herunter und erhalten Sie Einblicke in drei Formenbaustrategien für die Prototypenentwicklung und die Produktion: Spritzguss, Thermoformen und Gießen mit Elastomeren.