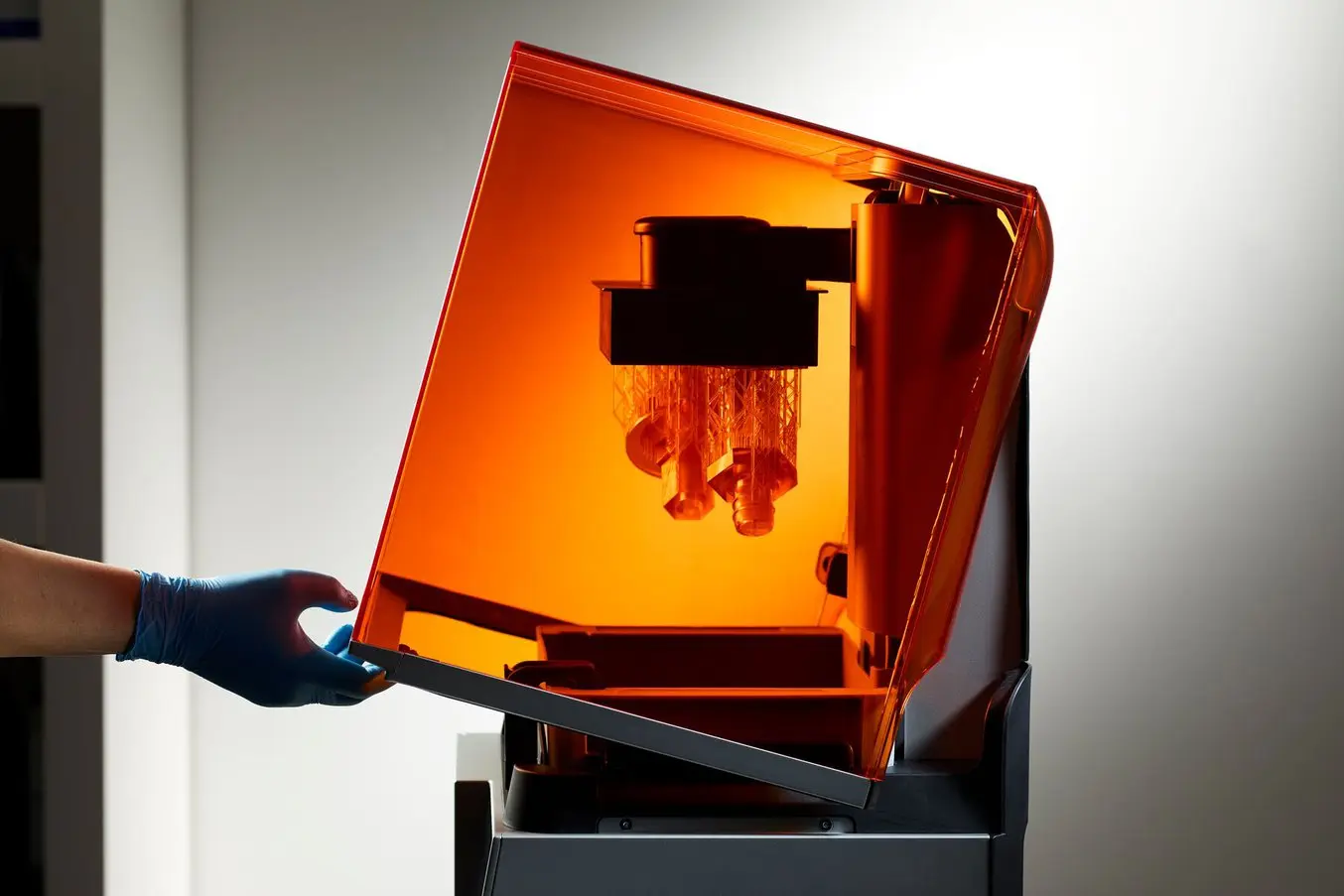
Stereolithografie-3D-Druck (SLA) ist der am weitesten verbreitete Kunstharz-3D-Druckprozess und äußerst beliebt, da er hochgenaue, isotrope und wasserdichte Prototypen und Endverbrauchsteile ermöglicht. SLA-3D-Drucker produzieren Teile mit verschiedenen fortschrittlichen Materialeigenschaften, glatter Oberflächenbeschaffenheit und feinen Details.
In diesem umfassenden Leitfaden erfahren Sie, wie Kunstharz-3D-Drucker der SLA-Technologie funktionieren, warum tausende professionelle Anwender*innen heutzutage diesen Prozess nutzen und wie auch Sie bei Ihrer Arbeit von SLA-3D-Druck profitieren.
Was ist Stereolithografie-3D-Druck (SLA)?
Stereolithografie wird auch als badbasierte Photopolymerisation, Behälterphotopolymerisation oder Vat-Photopolymerisation bezeichnet. Auch die Bezeichnung Kunstharz-3D-Druck ist gängig. Diese Technologie ist ein additives Fertigungsverfahren, bei dem eine Lichtquelle flüssiges Kunstharz zu festem Kunststoff aushärtet.
SLA-3D-Druck bietet die höchste Druckgeschwindigkeit, die höchste Auflösung und Genauigkeit, den höchsten Detailgrad und die glatteste Oberflächenbeschaffenheit aller 3D-Drucktechnologien. Ein weiterer großer Vorteil des Kunstharz-3D-Drucks ist die große Vielfalt an verfügbaren Materialien. Materialhersteller haben innovative SLA-Kunstharzformulierungen entwickelt, die unterschiedliche optische, mechanische und thermische Eigenschaften bieten und denen von Standard-, technischen und industriellen Thermoplasten in nichts nachstehen.
Die Fortschritte bei 3D-Druck-Hardware und -Software sowie in der Materialwissenschaft haben die SLA-Technologie erschwinglicher und zugänglicher gemacht denn je. Das verändert die Möglichkeiten, die den Unternehmen bei der Prototypenfertigung, bei Tests und in der Produktion zur Verfügung stehen.
SLA-Drucke kommen in jeder Branche als Endverwendungsteile zum Einsatz, z. B. als Ersatzteile, als Fertigungshilfsmittel, als Produktionswerkzeuge und darüber hinaus. Durch die glatte Oberflächenbeschaffenheit und die engen Toleranzen eignen sie sich ideal für mehrteilige Baugruppen, Konsumgüter oder die finale Designevaluierung.
Dank der erschwinglichen und benutzerfreundlichen Arbeitsabläufe können Unternehmen jeder Größe sich hochqualitativen 3D-Druck betriebsintern zunutze machen. Der Einsatz dieser Technologie hat bereits Hunderttausenden geholfen, ihre Betriebskosten zu senken, die Effizienz zu verbessern und ganz neue Geschäftsmodelle zu erschließen.
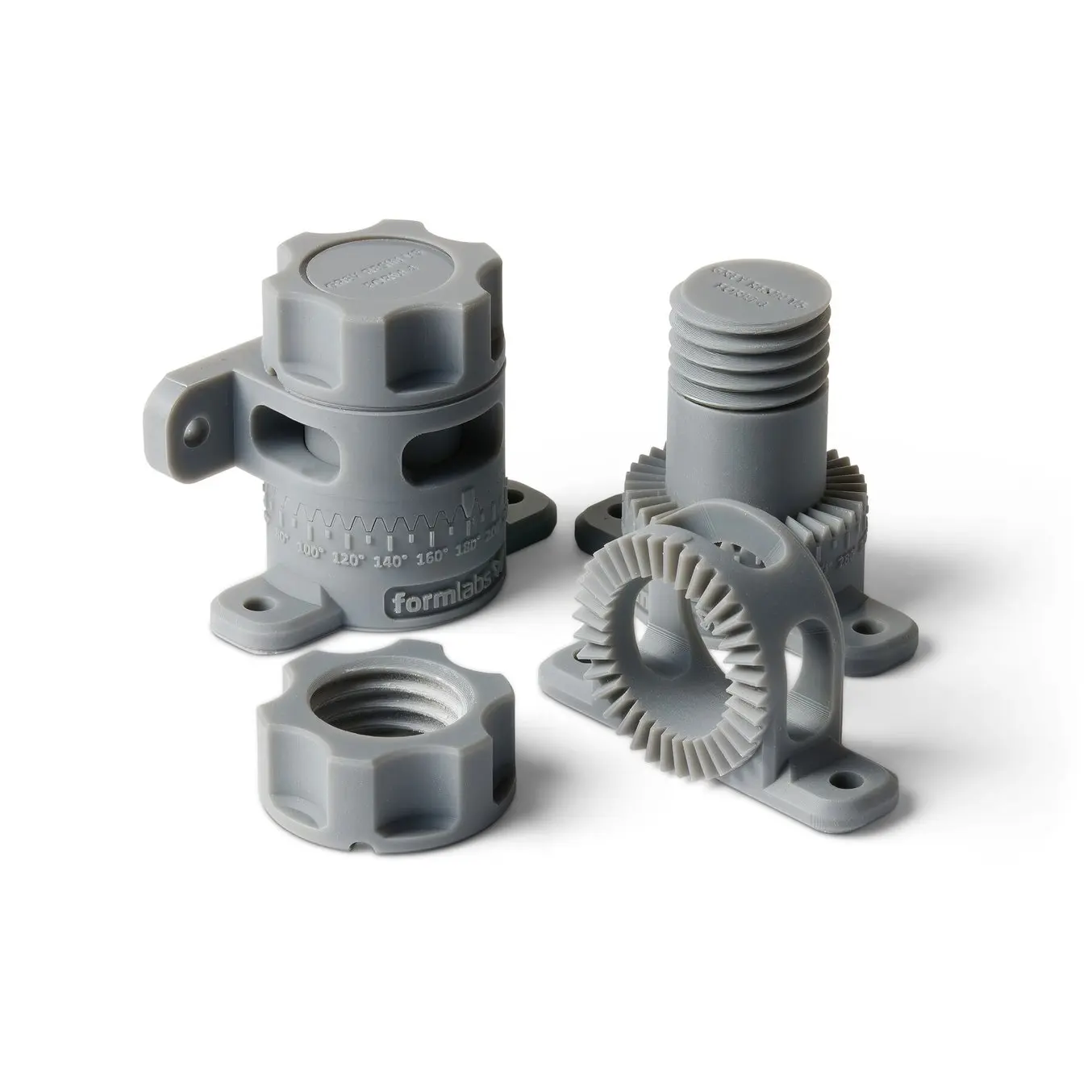
Kostenlosen Probedruck anfordern
Sehen und fühlen Sie die Qualität von Formlabs aus erster Hand. Wir senden Ihnen einen kostenlosen 3D-Probedruck an Ihren Arbeitsplatz.
Wie funktioniert SLA-3D-Druck?
SLA-3D-Druck verwendet eine Lichtquelle, um flüssiges Kunstharz zu dreidimensionalen Objekten auszuhärten. Traditionell befand sich die Lichtquelle bei SLA-Druckern über dem mit Kunstharz gefülltem Tank. Die invertierte Stereolithografie wurde erst 2011 von Formlabs eingeführt. Die Firmengründer Max Lobovsky, David Cranor und Natan Linde positionierten die Lichtquelle unter dem Harztank. Ein Querschnitt des Objekts wird am Boden des Tanks vom Licht abgetastet, und wenn sich die Konstruktionsplattform nach oben hebt, läuft neues Kunstharz unter die zuvor ausgehärtete Schicht.
Die Erfindung der umgedrehten Stereolithografie bedurfte einiger wichtiger Innovationen, nicht zuletzt des transparenten (und später flexiblen) Bodens des Harztanks. Dieses neue Design mit flexibler Oberfläche des Tanks verringert die Abzugskraft beim Anheben der Konstruktionsplattform und ermöglicht somit den Bau größerer invertierter SLA-3D-Drucker.
SLA-3D-Drucker nutzen duroplastische Materialien, die als „Resins“, „Resine“ oder Kunstharze bekannt sind und mit Licht reagieren, wobei sie aushärten. Wenn SLA-Kunstharze bestimmten Lichtwellenlängen ausgesetzt werden, verbinden sich deren kurze Molekülketten. Die Monomere und Oligomere polymerisieren und bilden steife oder flexible Geometrien.
Im letzten Jahrzehnt wurden mehrere neue Kunstharz-3D-Druckverfahren entwickelt, die sich primär anhand der verwendeten Lichtquelle unterscheiden. Dazu zählen: Laser-Stereolithografie (SLA), Digital Light Processing (DLP) sowie Maskierte Stereolithografie (MSLA), auch bekannt als LCD-3D-Druck.
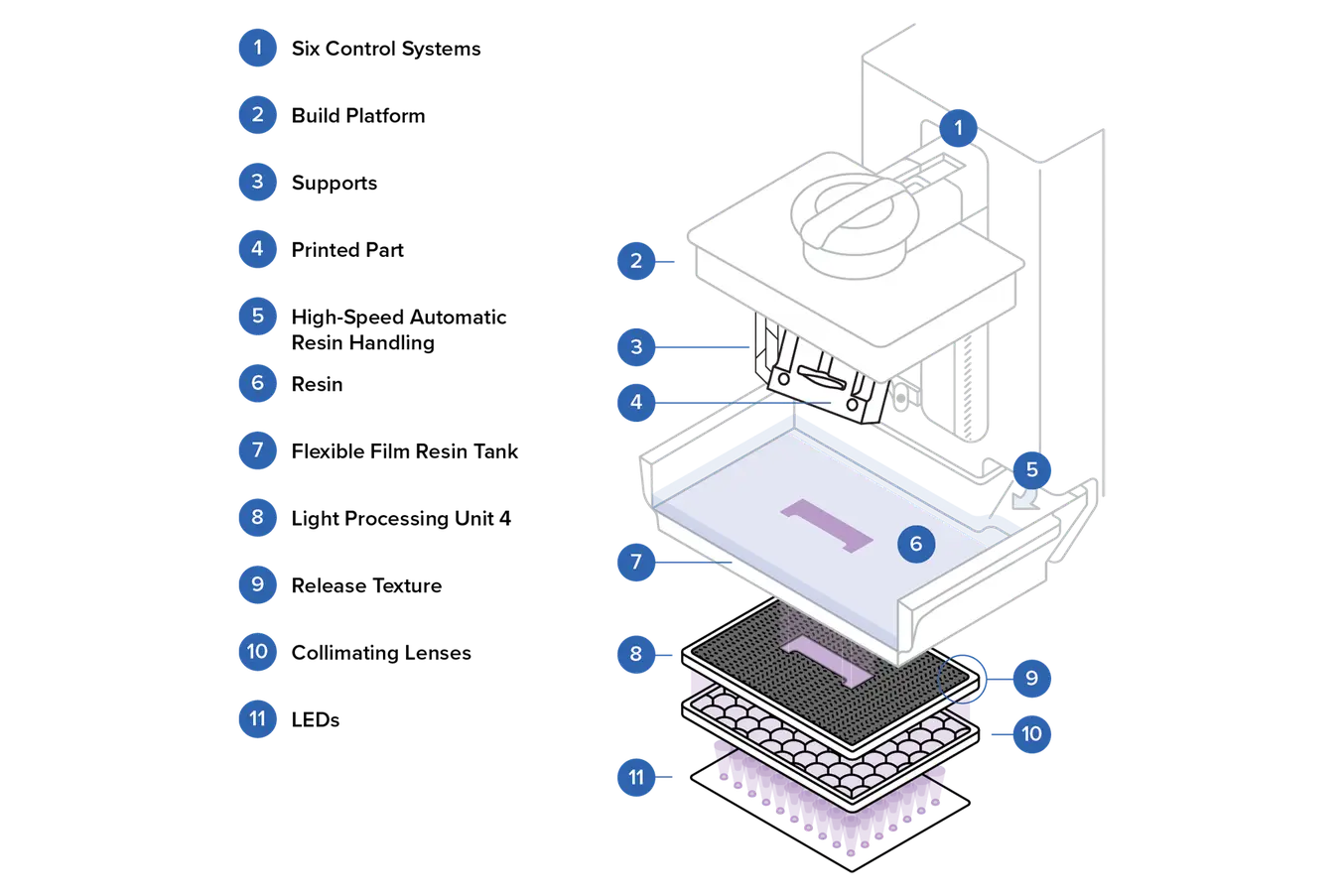
Grafische Darstellung von Formlabs' Drucksystem Low Force Display™ (LFD), einer fortgeschrittenen Form des MSLA-3D-Drucks
Unabhängig von der Ausrichtung oder Art der Lichtquelle ist der SLA-Druck ein überschaubarer Prozess. Nach dem Druck müssen die Teile mit Alkohol oder Ether gewaschen werden, um flüssige Harzreste von der Oberfläche zu entfernen. Dann wird abhängig vom Material eine Nachhärtung benötigt, um die Polymerisierung abzuschließen. Dies bildet die Materialeigenschaften vollständig aus. Spezifische Anwendungen oder ästhetische Anforderungen verlangen dann noch weitere Nachbearbeitung wie Lackierung, Beschichtung oder Galvanisierung.
Eine kurze Geschichte der Stereolithografie
Stereolithografie (SLA) wurde in den frühen 1980er Jahren erfunden, als der japanische Forscher Dr. Hideo Kodama den modernen Schichtaufbau für die Stereolithografie erfand und dabei UV-Licht nutzte, um lichtempfindliche Polymere zu härten. Der Begriff Stereolithografie wurde von Charles (Chuck) W. Hull erfunden, der die Technologie 1986 patentieren ließ und 3D Systems gründete, um sie zu kommerzialisieren. Hull beschrieb die Methode als das Herstellen von dreidimensionalen Modellen durch das aufeinanderfolgende „Drucken“ dünner Schichten aus einem Material, das sich durch ultraviolettes Licht härten lässt. Diese ersten SLA-Drucker waren riesige Industriemaschinen, die oft mehr als 100 000 $ kosteten und komplizierte Infrastruktur- und Wartungsanforderungen hatten.
SLA-3D-Druck war jedoch nicht die erste 3D-Drucktechnologie, die sich großer Beliebtheit erfreute. Als die Patente verschiedener 3D-Drucktechnologien Ende der 2000er Jahre ausliefen, erleichterten kleinformatige Schmelzschichtungsdrucker (FDM = Fused Deposition Modeling) den Zugang zur additiven Fertigung. Die kostengünstige Extrusionstechnologie entfachte die erste Welle weitgreifender Implementierung und steigerte die Bekanntheit des 3D-Drucks. Doch FDM-3D-Drucker konnten den gesamten professionellen Bedarf nicht decken.
Revolution in Form Desktop-großer SLA-3D-Drucker
Desktop-SLA-3D-Drucker versprachen hochauflösenden 3D-Druck, wie er zuvor auf klotzige industrielle Systeme beschränkt war. So gab es nun eine Lösung für all jene, die nach einem viel kleineren und erschwinglicheren Setup suchten. Mit dem Form 1 – der ersten invertierten Stereolithografie-Lösung – war es nun für Kunden aller Hintergründe und Budgets möglich, diese fortschrittliche Technologie zu nutzen.
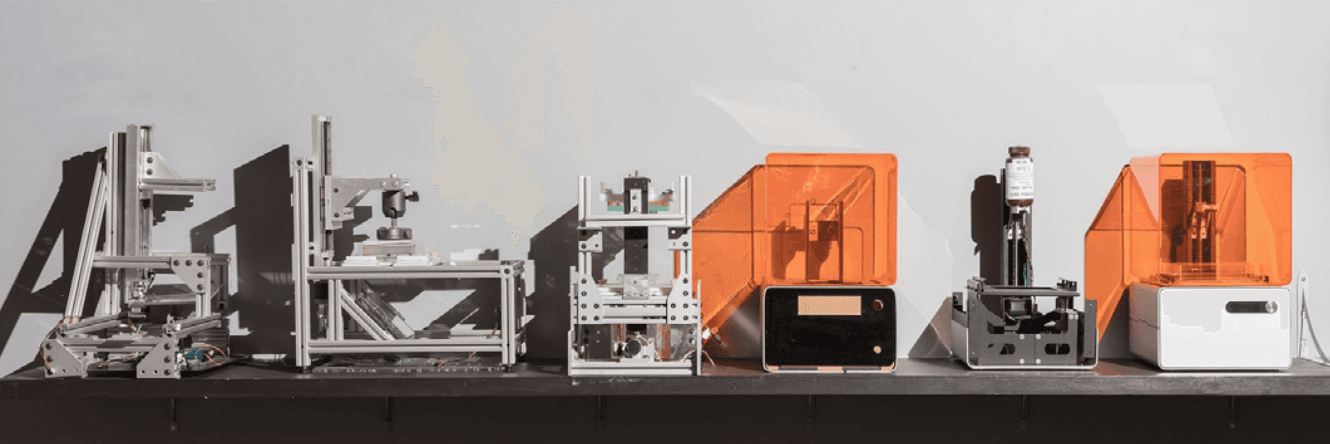
Prototypen des Form 1, des ersten SLA-3D-Druckers für den Desktop
Formlabs veröffentlichte den Form 2 im Jahr 2015. Und mit der anschließenden Veröffentlichung einer breiteren Materialpalette wurde der SLA-3D-Druck für professionelle Anwender*innen in den verschiedensten Bereichen zu einer brauchbaren Lösung. 2019 präsentierte Formlabs mit dem Form 3 und dem Form 3L die Low Force Stereolithography™ (LFS) – ein Verfahren, das einen Harztank mit flexiblem Boden verwendet, um die Abzugskräfte beim Ablösen des gehärteten Teils vom Tankboden drastisch zu verringern.
Diese Eigenschaften brachten den 3D-Druck zu einer Vielzahl verschiedener Spezial- und Hochpräzisionsanwendungen, z. B. im Bereich des Ingenieurwesens, des Produktdesigns und der Fertigung sowie in der Dental- und Schmuckbranche und anderen Industriezweigen.
Mit wachsenden Anwendungen erlangte die Technologie an Popularität und wurde weitläufig implementiert. Heutzutage ist Stereolithografie neben der Schmelzschichtung (FDM) und dem selektiven Lasersintern (SLS) eines der drei etabliertesten Kunststoff-3D-Druckverfahren. Durch nachfolgende Iterationen hat sich die Form-Serie als die weltweit führenden professionellen Kunstharz-3D-Drucker etabliert, mit 140 000 verkauften Geräten und über 400 Millionen gedruckten Teilen (Stand 2024).
Das nächste Kapitel: LFD-Drucksystem
Im Jahr 2024 ist Formlabs auf dem Gebiet des leistungsstarken, erschwinglichen Kunstharz-3D-Drucks noch einen Schritt weiter gegangen, mit der Veröffentlichung des Desktop-Druckers Form 4 und seiner biokompatiblen Version Form 4B sowie den großformatigen Kunstharz-Druckern Form 4L und Form 4BL. Diese neuesten Iterationen von Formlabs' Kunstharz-3D-Druckern der Form-Serie basieren auf unserem MSLA-Drucksystem der nächsten Generation, Low Force Display™ (LFD).
Die Benutzerfreundlichkeit und Erschwinglichkeit leistungsstarker Desktop- und Benchtop-Geräte haben ganz neue Produktionsmethoden ermöglicht. Unternehmen skalieren dadurch die 3D-Druckkapazitäten schrittweise, integrieren ihre Lieferkette und steigern die Flexibilität sowie Anpassungsfähigkeit inmitten unsicherer Marktbedingungen. Und durch neue Materialien erschließen Unternehmen außerdem neue Anwendungen.
Den Kern des LFD-Drucksystems bildet die Beleuchtungseinheit. Die Beleuchtungseinheit generiert mithilfe von LEDs und Kollimatorlinsen eine uniforme Flächenprojektion von extrem starkem Licht. Das Licht wird durch ein Feld von Linsen kollimiert, also in parallelere Bahnen geleitet. Zudem wird die Lichtintensität gleichmäßiger, sodass keine dunkleren oder helleren Punkte auftreten.
Von dort aus passiert das Licht die Light Processing Unit (LPU) 4, wo Filter und Abdeckungen das Licht in der Form der Druckschicht maskieren. Sobald das Licht das flüssige Kunstharz im Harztank erreicht, härtet die gesamte belichtete Fläche sofort zu einer festen Schicht aus. Die Konstruktionsplattform hebt sich dann aus dem Kunstharz und die Z-Achse löst die gedruckte Schicht präzise vom Boden des Harztanks ab.
In der Vergangenheit stellten Abzugskräfte beim Kunstharz-3D-Druck eine erhebliche Schwachstelle dar, denn sie führten dazu, dass Anwender*innen sich bei der Auswahl eines Druckers zwischen Druckteilqualität, Zuverlässigkeit und Schnelligkeit entscheiden mussten. Form 4 und Form 4L minimieren die Abzugskräfte mithilfe ihres neugestalteten Harztanks mit flexiblem Film und der innovativen Ablösetextur – einem eigens entwickelten, mikrotexturieren optischen Film, der mittels Luftstrom das Anhaften des Harztanks an der LPU verhindert.
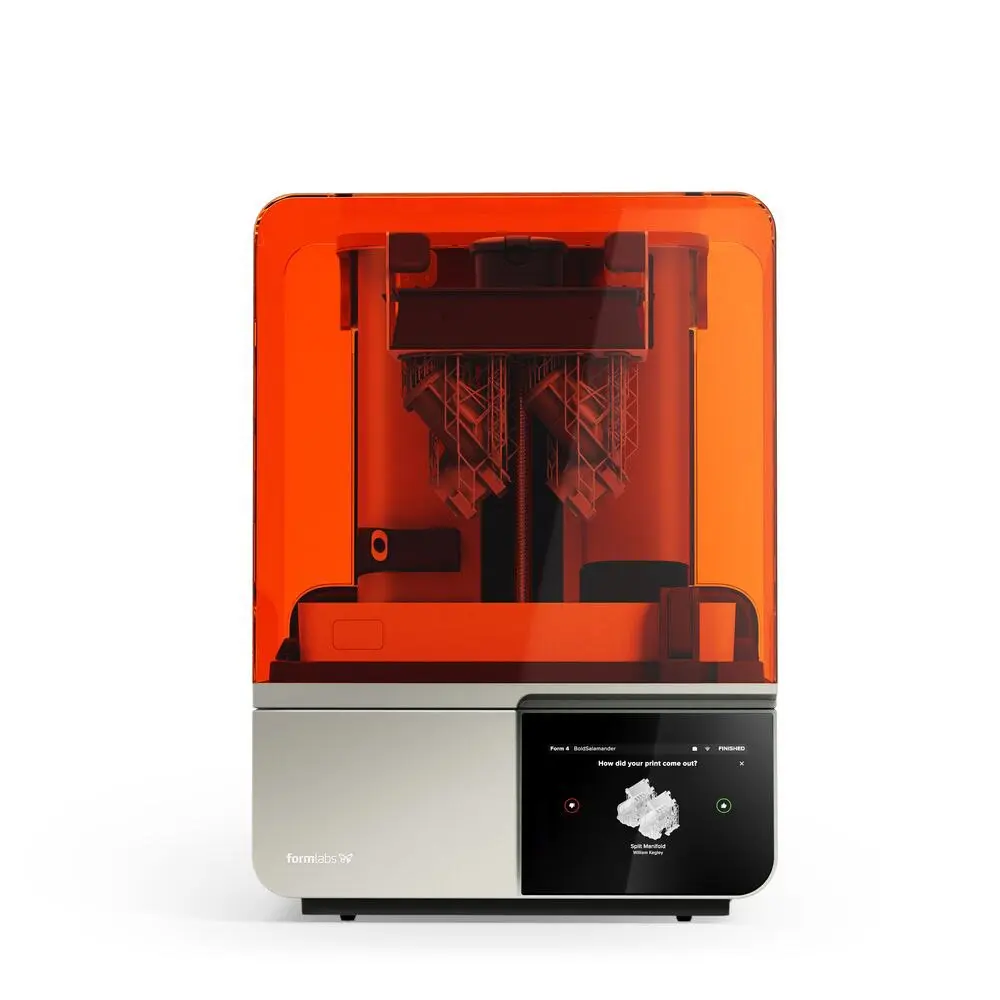
Produktdemo: Form 4
Entdecken Sie, wie der Form 4 neue Maßstäbe der Produktivität und Innovation setzt, dank beispielloser Schnelligkeit, Genauigkeit und Zuverlässigkeit.
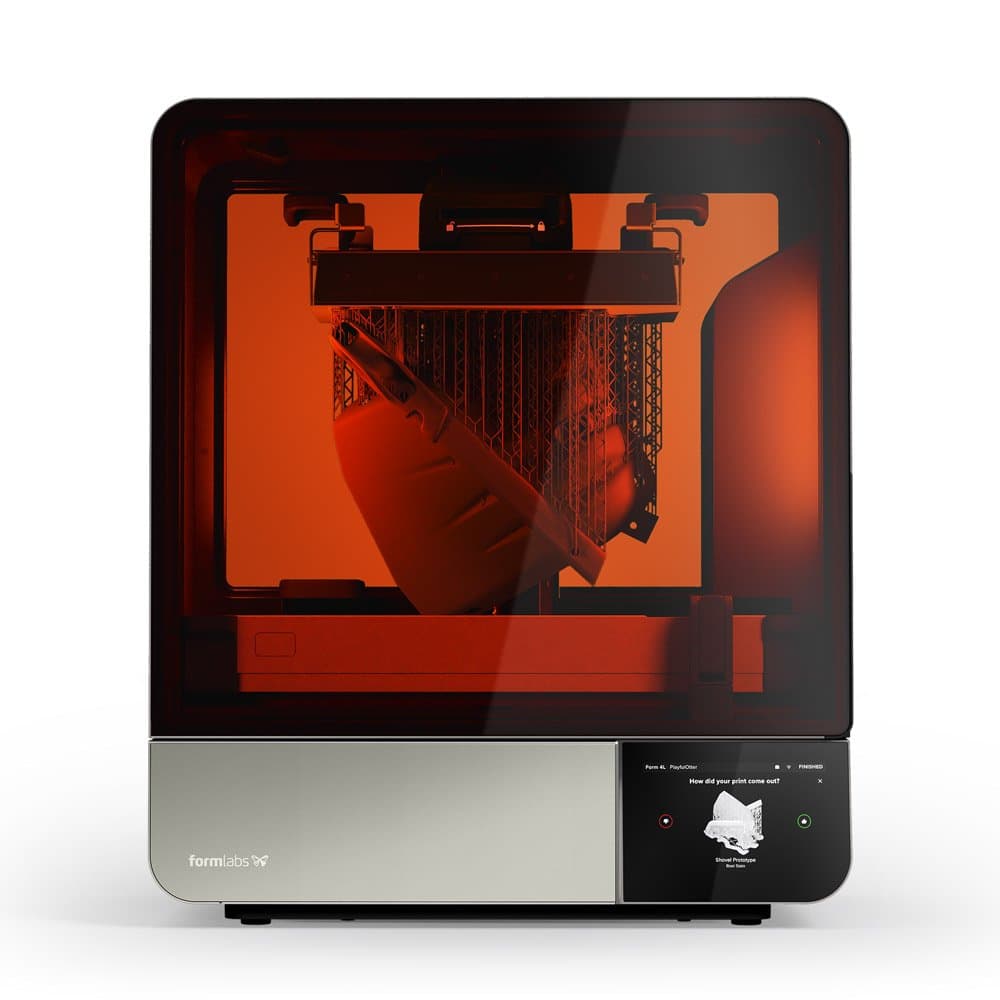
Produktdemo: Form 4L
Entdecken Sie, wie der neue Form 4L, unser großformatiger Kunstharz-3D-Drucker der nächsten Generation, die Schnelligkeit, Genauigkeit und Zuverlässigkeit des Form 4 in einem völlig neuen Maßstab eröffnet.
Arbeitsablauf für den SLA-3D-Druck
1. Design
Konstruieren Sie Ihr Modell mit einer beliebigen CAD-Software oder aus 3D-Scandaten und exportieren Sie es in einem für den 3D-Druck geeigneten Dateiformat (STL oder OBJ). Importieren Sie das digitale Design dann in Ihre Druckvorbereitungssoftware, um die Druckeinstellungen zu konfigurieren und das Modell zum Druck in Schichten aufzuteilen. Formlabs' Druckvorbereitungssoftware PreForm ist kostenlos, erstellt automatisch Stützstrukturen und richtet das Modell aus.
Fortgeschrittene Nutzer können Modelle speziell für den SLA-Prozess entwerfen und z. B. Teile aushöhlen, um Material zu sparen.
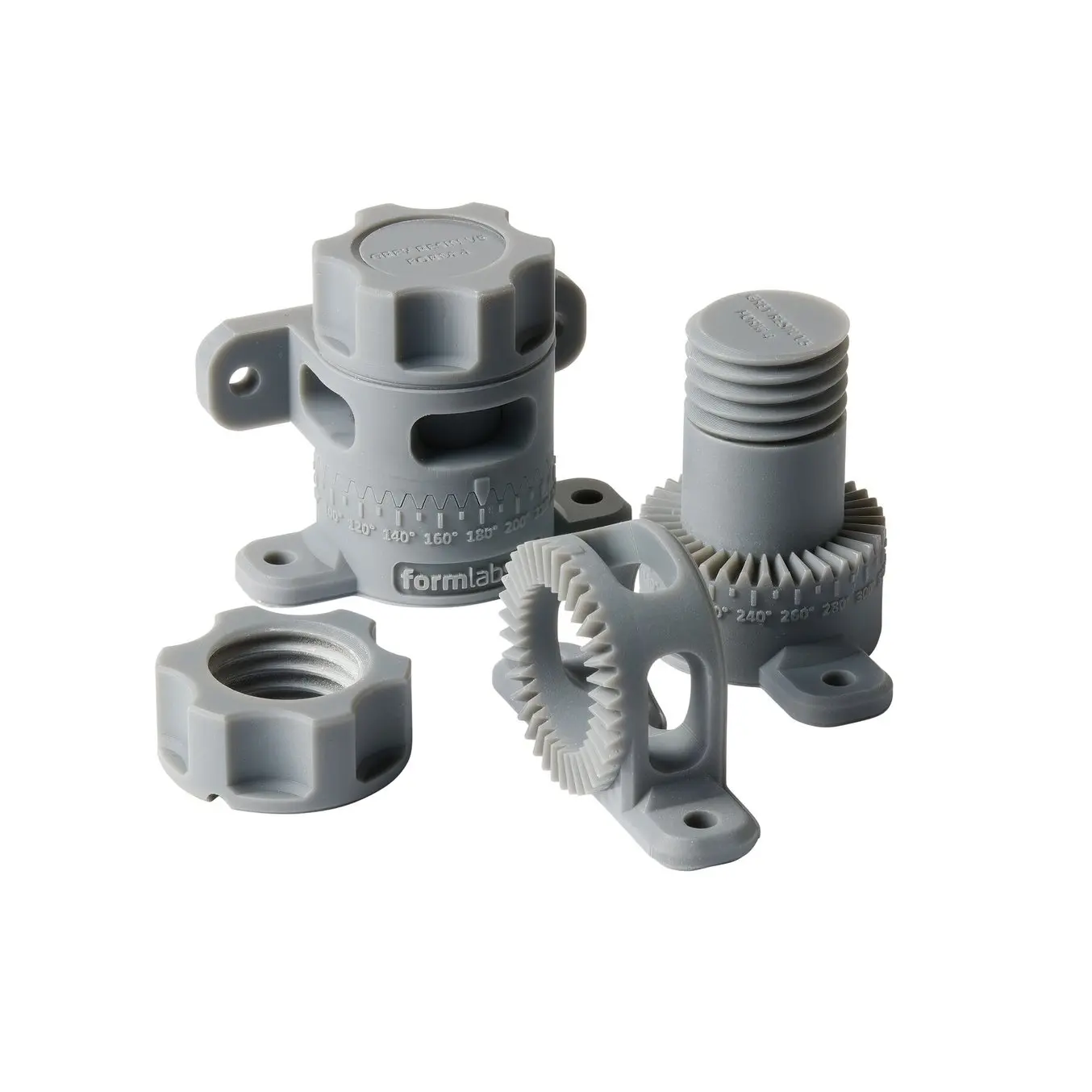
Design-Leitfaden für die Serie Form 4
Ein erfolgreicher 3D-Druck beginnt mit einem passenden Modelldesign. Befolgen Sie unsere bewährten Praktiken, um Designs zu optimieren und Fehler zu vermeiden.
2. Druck
Die Druckvorbereitungssoftware sendet das Druckteil an den Drucker, entweder über WLAN oder kabelgebunden über USB oder Ethernet.
Invertierte SLA-Drucker verwenden herausnehmbare Harztanks und Konstruktionsplattformen. Das erleichtert den Materialwechsel und den Start eines neuen Drucks. Fortgeschrittenere SLA-Drucker – wie die Form-Serie von Formlabs – verwenden zudem ein Kartuschen-System, das das Material während des Druckvorgangs automatisch nachfüllt. So beginnt jeder neue Druckvorgang nach einer kurzen Überprüfung der korrekten Einrichtung. Danach arbeitet das Gerät bis zum Druckabschluss unbeaufsichtigt.
Die 3D-Drucker von Formlabs werden außerdem von einem webbasierten Dashboard begleitet, das die Fernverwaltung von Druckern, Materialien und Arbeitsgruppen erlaubt.
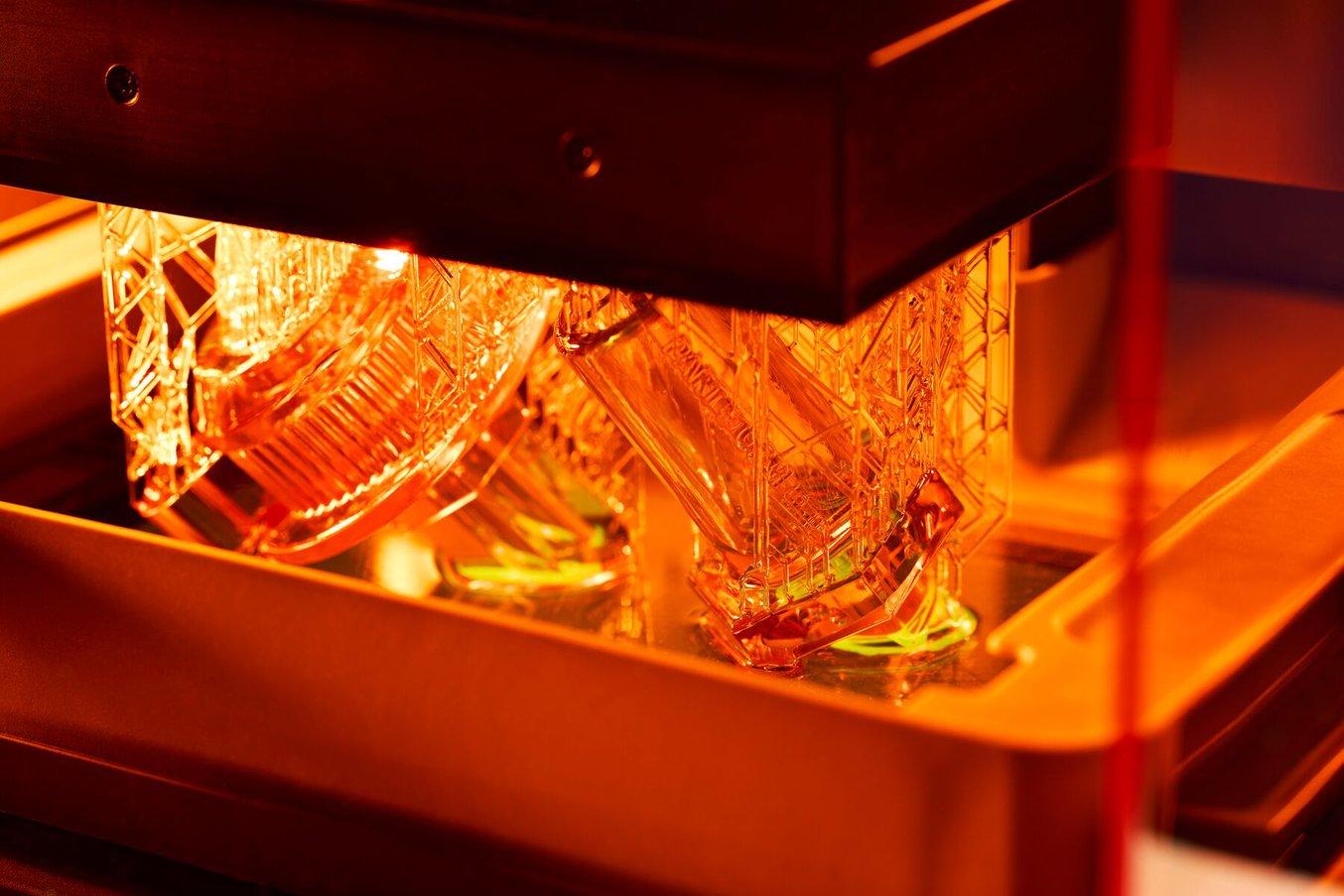
3. Nachbearbeitung
Um Teile von der Konstruktionsplattform zu entfernen, verwenden verschiedene SLA-3D-Drucker unterschiedliche Methoden. Die meisten davon sind manuell und erfordern das Abkratzen der Teile. Mit Formlabs' Build Platform Flex und Build Platform Flex L hingegen lassen sich Teile schnell und einfach von der Konstruktionsplattform ablösen. Gleichzeitig werden Schäden wie Absplitterungen oder Kratzer vermieden.
Nachdem die Teile von der Konstruktionsplattform entfernt wurden, müssen sie in Isopropylalkohol (IPA) oder einem Etherbad gespült werden, um flüssige Kunstharzreste von ihrer Oberfläche zu waschen. Formlabs’ Waschstation Form Wash und der großformatige Form Wash L wurden entwickelt, um den Waschprozess zu optimieren, Kunstharzrückstände einfach zu entfernen und die Nachbearbeitungszeit zu verkürzen.
Nachdem die gespülten Teile getrocknet sind, erfordern einige Materialien eine Nachhärtung. Dieses Verfahren trägt dazu bei, die Festigkeit und Leistung der Teile zu verbessern und ihre optimalen Materialeigenschaften auszubilden. Formlabs’ Nachhärtungsstation Form Cure und der großformatige Form Cure L kontrollieren Temperatur und Licht präzise, um eine gleichmäßige, hochintensive Aushärtung zu gewährleisten.
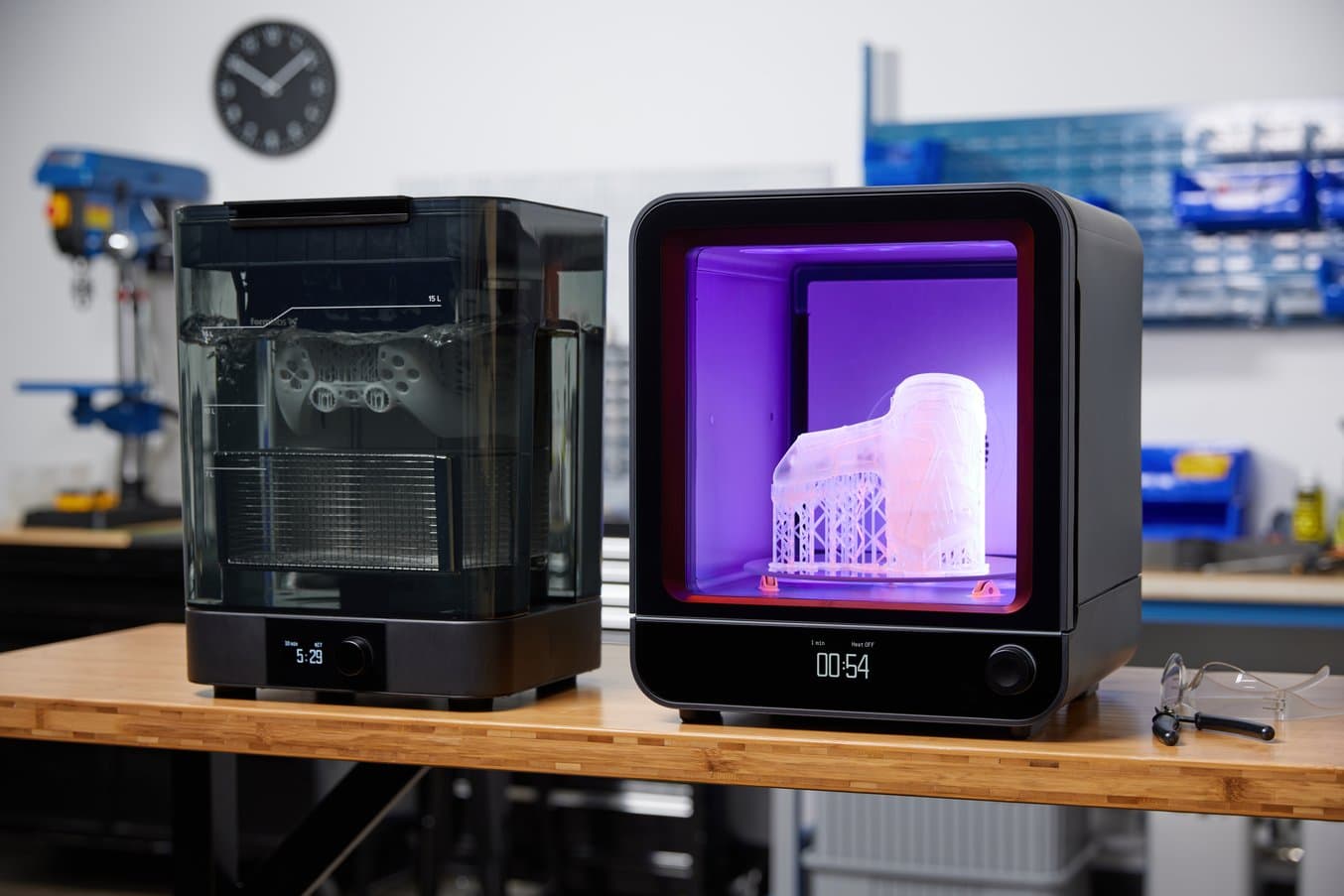
Der Form Wash (links) reinigt Kunstharz-3D-Drucke automatisch und gründlich dank der verbesserten Umspülung mit Lösungsmittel. Der Form Cure (rechts) kann Kunstharz-3D-Drucke mit bisher unerreichter Geschwindigkeit und Konsistenz in nur 60 Sekunden nachhärten.
Abschließend werden die Stützen vom Teil entfernt und die verbleibenden Stützspuren sauber abgeschliffen. SLA-Teile können leicht für spezifische Anwendungen oder Oberflächengüten spanend bearbeitet, grundiert oder lackiert werden oder lassen sich als Baugruppen montieren.
Darüber hinaus können Druckteile durch zusätzliche Schritte wie Schleifen, Beschichten, Galvanisieren oder Sandstrahlen weiter aufgewertet werden. Mit solchen fortschrittlichen Nachbearbeitungsmethoden für Kunstharz lassen sich verschiedenste Ergebnisse erzielen. So können Teile etwa durch die Steigerung der UV-Beständigkeit besser auf Anwendungen im Freien vorbereitet werden, während Galvanisierung oder Keramikbeschichtungen wie Cerakote für bessere mechanische Festigkeit sorgen.
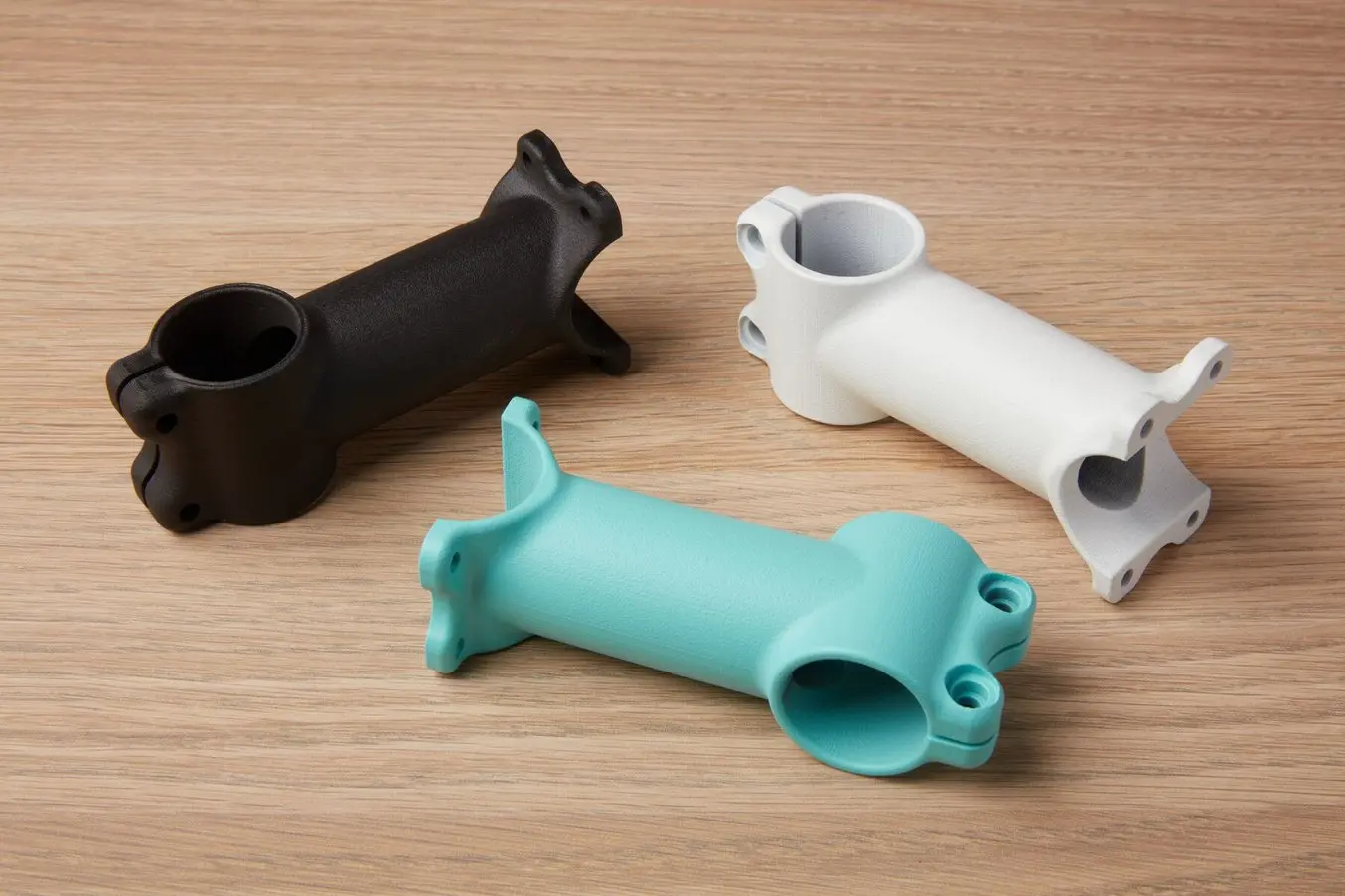
Durch Beschichtungen wie Cerakote werden SLA-3D-gedruckte Teile stärker, widerstandsfähiger und ästhetisch ansprechender.
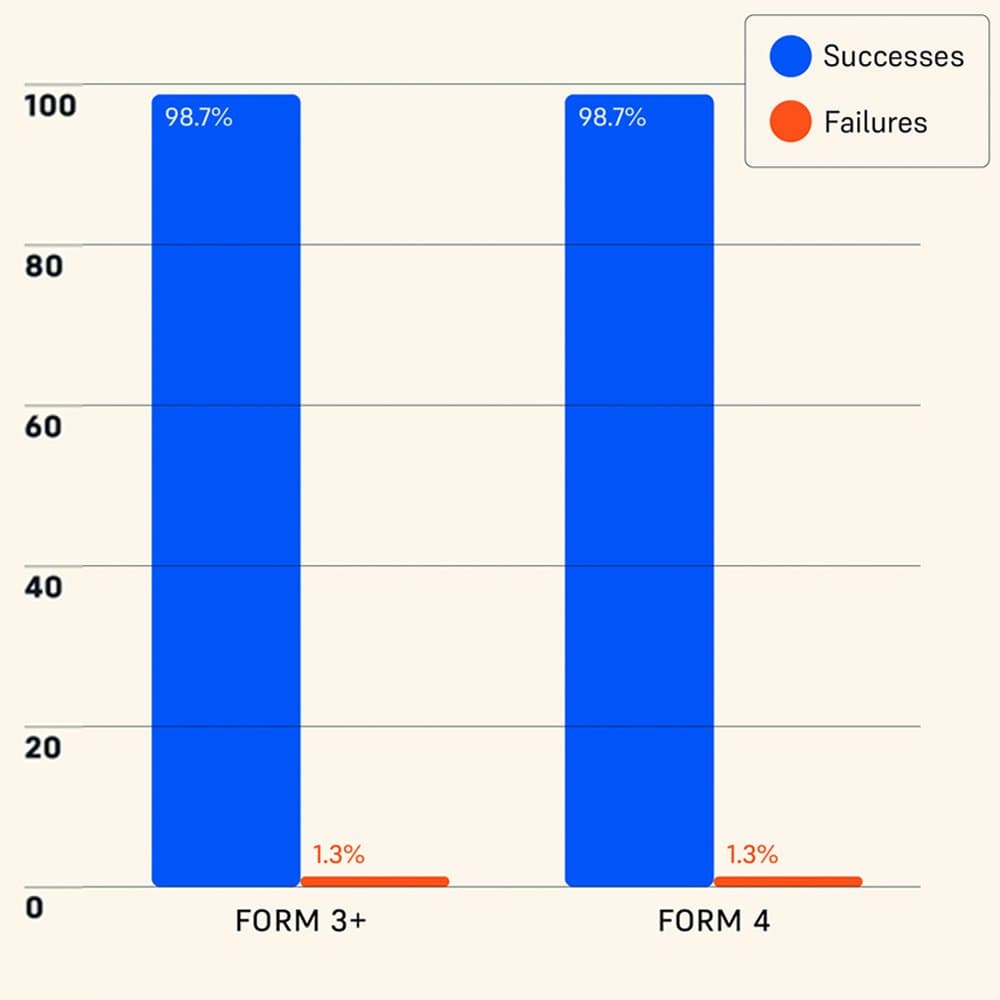
Zuverlässigkeit von Form 4 und anderen Kunstharz-3D-Druckern unabhängig getestet
Der Form 4 von Formlabs erreichte in einer Untersuchung eines unabhängigen, weltweit führenden Produkttesters eine Druckerfolgsrate von 98,7 %. Eine vollständige Beschreibung der Testmethode und die Ergebnisse finden Sie in unserem Whitepaper.
Welche Gründe sprechen für SLA-3D-Druck?
Fachleute entscheiden sich für SLA-3D-Druck wegen seiner Fähigkeit, schnell Teile mit feinen Details herzustellen, mit glatten Oberflächen, exzellenter Präzision, überlegenen mechanischen Eigenschaften, Isotropie, Wasserdichtheit und Materialvielseitigkeit.
Geschwindigkeit und Durchsatz
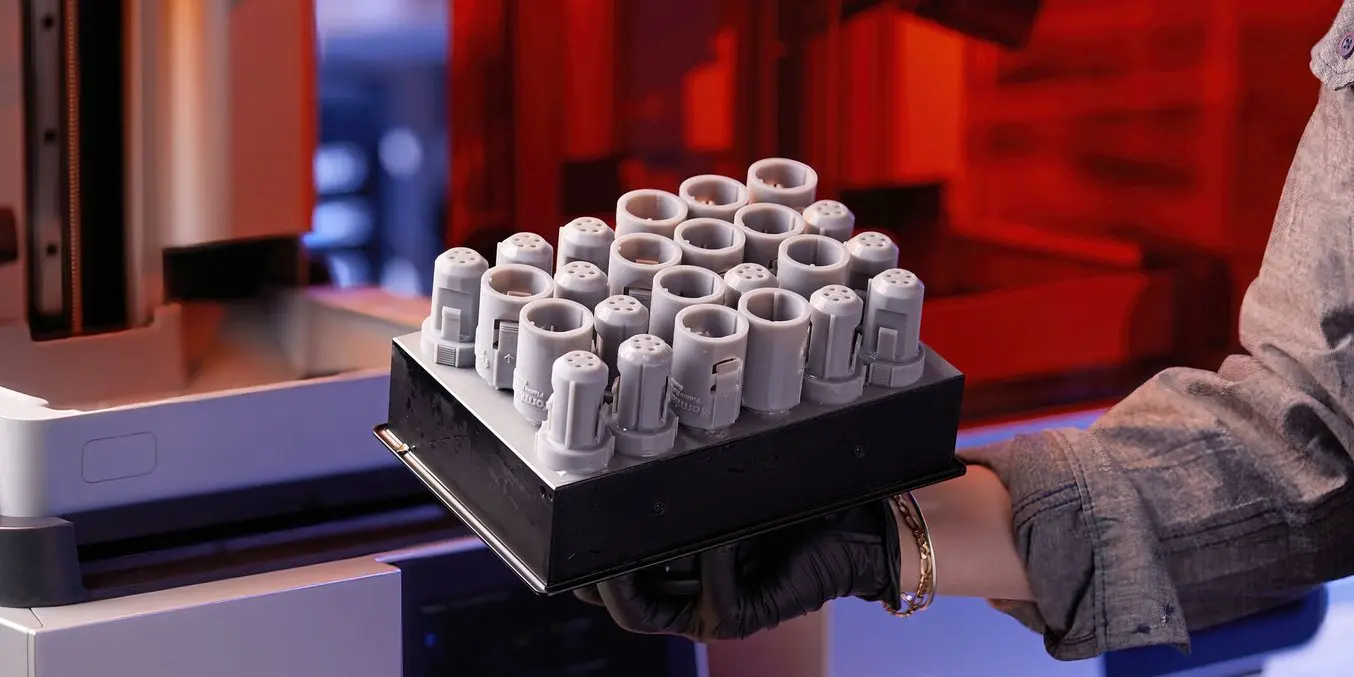
Druckgeschwindigkeit im Vergleich: Elektrischer Verbinder
FDM-3D-Druck wählen | SLA-3D-Druck | SLS-3D-Druck | |
---|---|---|---|
1 Baugruppe (2 Teile) | 2 h 38 min | 1 h 3 min | 3 h 30 min Druck (6 h 27 min Abkühlung) |
50 Baugruppen (100 Teile) | 84 h | 13 h 2 min | 12 h 59 min Druck (13 h 49 min Abkühlung) |
Vergleich von Druckern und Druckparametern:
- FDM-3D-Drucker: Bambu Lab X1, PLA Basic, 120 Mikrometer Schichthöhe, 15 % Fülldichte
- SLA-3D-Drucker: Form 4, Grey Resin, 100 Mikrometer Schichthöhe
- SLS-3D-Drucker: Fuse 1+ 30W, Nylon 12 Powder, 110 Mikrometer Schichthöhe
Da mehr Unternehmen sich zur Produktion und zur schnellen Designiteration auf 3D-Druck stützen, gewinnt die Druckgeschwindigkeit bei der Auswahl der Technologie an Bedeutung. Obwohl es in allen Technologien Fortschritte bei der 3D-Druckgeschwindigkeit gegeben hat, hat sich SLA-3D-Druck als der klare Spitzenreiter für den schnellsten verfügbaren 3D-Druckprozess etabliert.
Einige Kunstharz-3D-Druckverfahren sind schneller als andere. Laserbasierte SLA härtet im Allgemeinen jede Schicht langsamer aus als DLP-, MSLA- oder LCD-Technologien, die einen gesamten Querschnitt mit einer schnellen Belichtung aushärten.
Formlabs hat branchenführende Druckgeschwindigkeiten priorisiert. Form 4 und Form 4L wurden entwickelt, um Teile mit einer Geschwindigkeit von bis zu 100 mm pro Stunde mit speziell entwickelten Materialien wie Fast Model Resin herzustellen. Die meisten Drucke mit dem Form 4 sind in weniger als zwei Stunden fertig, ganz unabhängig vom verwendeten Material. Das lässt mehrere Designiterationen am selben Tag zu.
Der großformatige SLA-3D-Druck erlaubt Design und Konstruktion im lebensgroßen Maßstab, und mit dem Form 4L geht dies nun ganz ohne Geschwindigskeitseinbußen. Die meisten Drucke sind mit dem Form 4L in weniger als sechs Stunden abgeschlossen. Selbst Drucke, die die volle Höhe des Druckers erreichen, oder Großserien, die die gesamte Konstruktionsplattform mit Teilen vollpacken, werden in weniger als einem Tag gedruckt. Das eröffnet gleichzeitige Iterationen großer Teile oder die Produktion in hohen Stückzahlen.
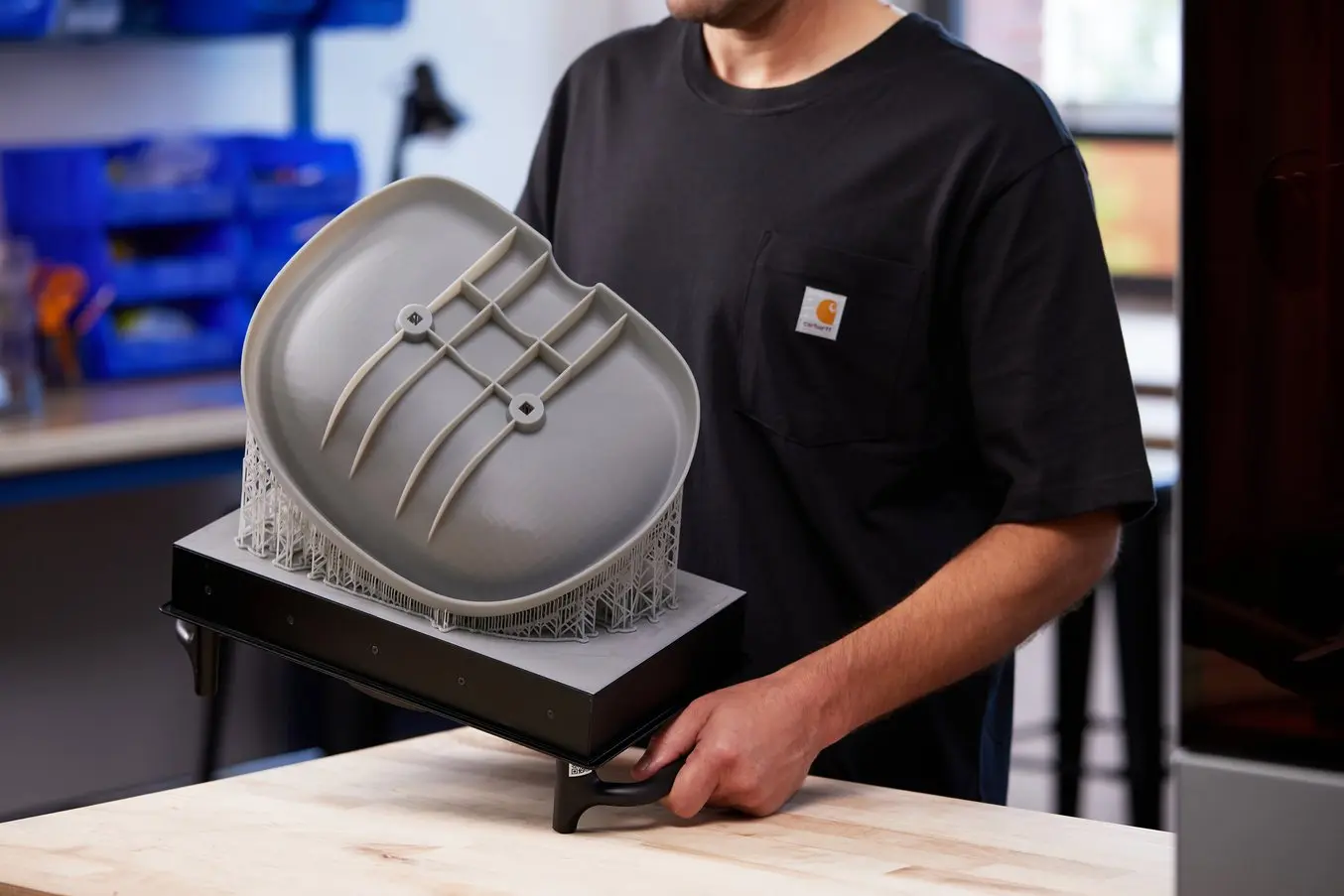
Druckgeschwindigkeit im Vergleich: Sitzprototyp von Radio Flyer
FDM-3D-Druck wählen | SLA-3D-Druck | |
---|---|---|
Druckzeit | 42 h 3 min | 2 h 37 min |
Vergleich von Druckern und Druckparametern:
- FDM-3D-Drucker: Ultimaker S7, PLA, 100 Mikrometer Schichthöhe, 20 % Fülldichte
- SLA-3D-Drucker: Form 4, Fast Model Resin, 200 Mikrometer Schichthöhe
Wenn diese Geschwindigkeit Tag für Tag und Woche für Woche addiert wird, sind die Durchsatzvorteile außergewöhnlich. Der Form 4 und Form 4L halten jetzt mit Hochdurchsatz-Technologien wie dem Spritzguss mit. Der Druck voller Konstruktionsvolumen im Laufe von wenigen Stunden, mehrmals am Tag, kann die Produktion einer Spritzgussmaschine mit mittlerem Volumen erreichen – ohne die hohen Anfangskosten für die Produktionswerkzeuge.
Materialvielfalt
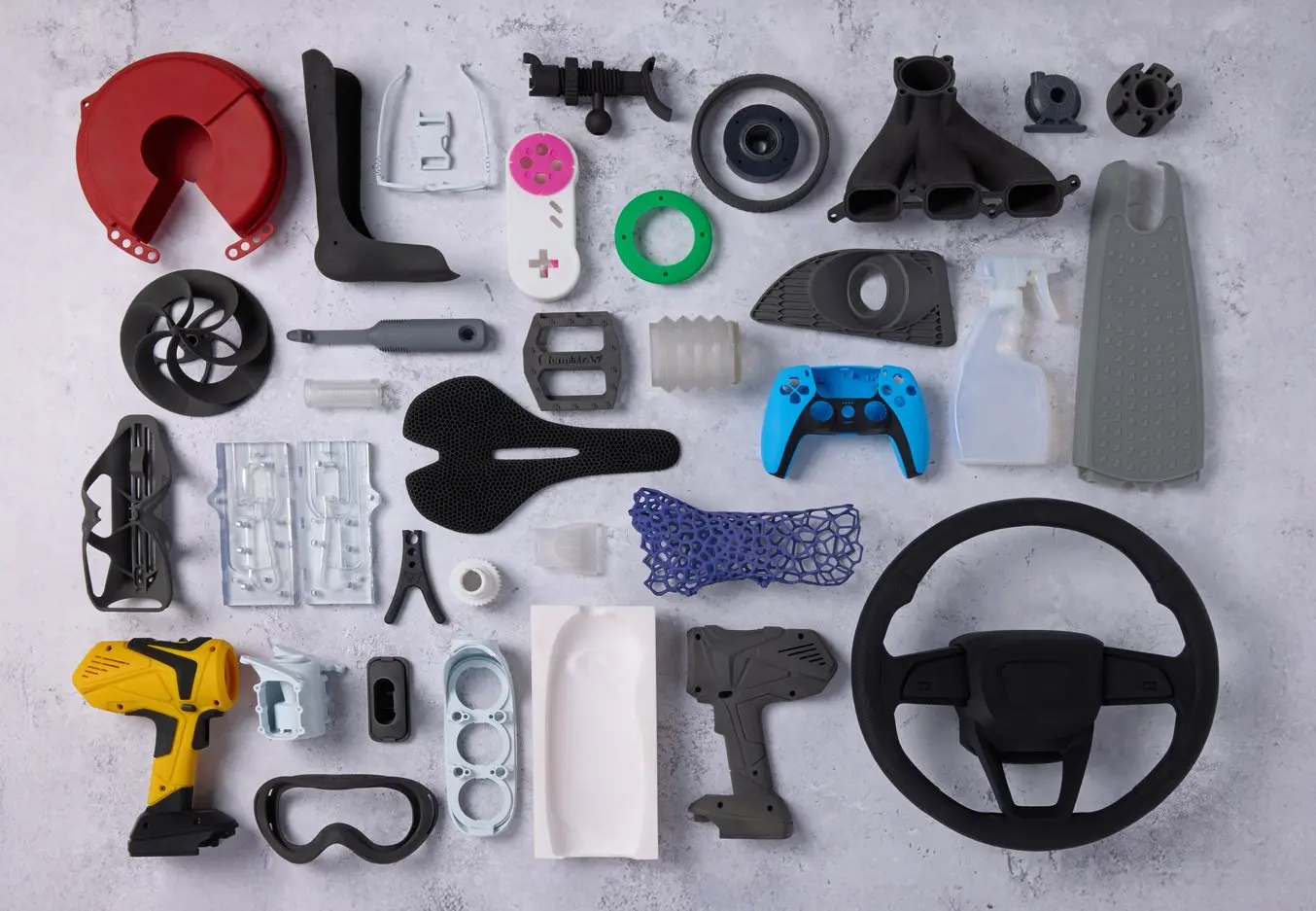
SLA bietet die größte Materialauswahl aller Kunststoff-Drucktechnologien.
SLA-Kunstharze sind unglaublich vielseitig, und es sind Hunderte von verschiedenen Formulierungen erhältlich. Die SLA-Materialien können weich oder hart sein, stark mit sekundären Materialien wie Glas oder Keramik gefüllt sein oder über mechanische Eigenschaften wie eine hohe Wärmeformbeständigkeitstemperatur oder Schlagzähigkeit verfügen. Die Materialien reichen in ihren Anwendungen von Branchenspezifikationen wie jene für Zahnersatz bis hin zu Kunstharzen, die bei der Prototypenfertigung das Endprodukt nachahmen und umfangreichen Tests und großer Belastung standhalten.
Viele Hersteller von SLA-Druckern formulieren und produzieren auch ihre eigenen Kunstharze für den Einsatz in einem geschlossenen System. Einige bieten jedoch eine offene Plattform an, auf der jedes Kunstharz verwendet werden kann, während andere die Kunstharze dritter Unternehmen unter eigenem Namen vertreiben.
Da diese Kunstharze speziell für SLA-3D-Drucker entwickelt sind, entsprechen sie nicht gänzlich den bekannten Thermoplasten wie Nylon oder ABS, die in traditionellen Kunststoff-Fertigungsverfahren wie dem Spritzguss verwendet werden. Um das beste Kunstharz für eine spezifische Anwendung zu bestimmen, können einige Tests und das Studium von Datenblättern und Anwendungsleitfäden nötig sein. Die enorme Vielfalt an mechanischen und ästhetischen Eigenschaften macht es jedoch einfach, einen optimierten und effizienten Arbeitsablauf aufzustellen.
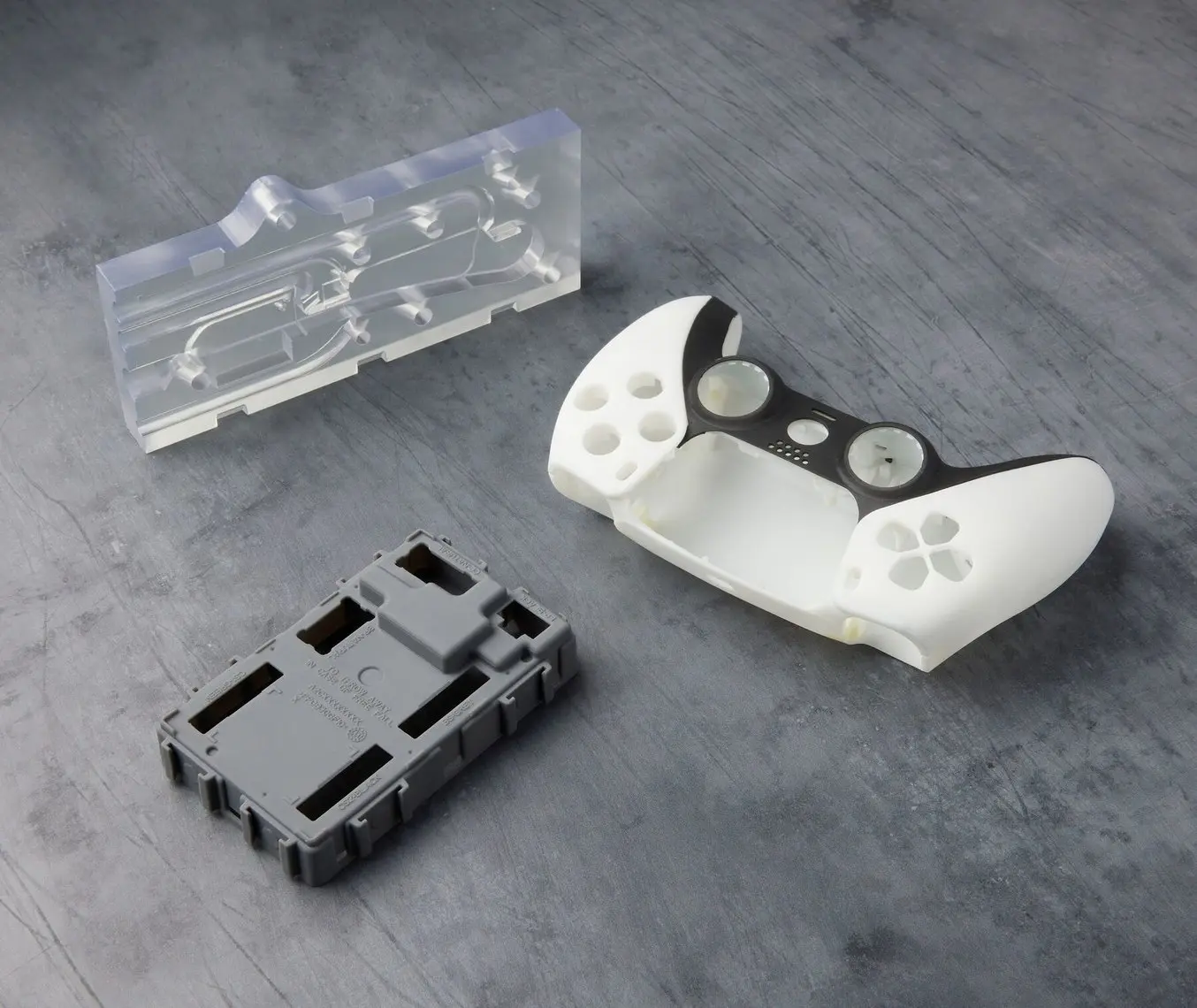
Materialleitfaden zum Form 4
Erfahren Sie mehr über alle Hochleistungsmaterialien, die auf dem Form 4 nutzbar sind, und lernen Sie, wie Sie das richtige Material für Ihre Anwendung auswählen.
Genauigkeit und Präzision
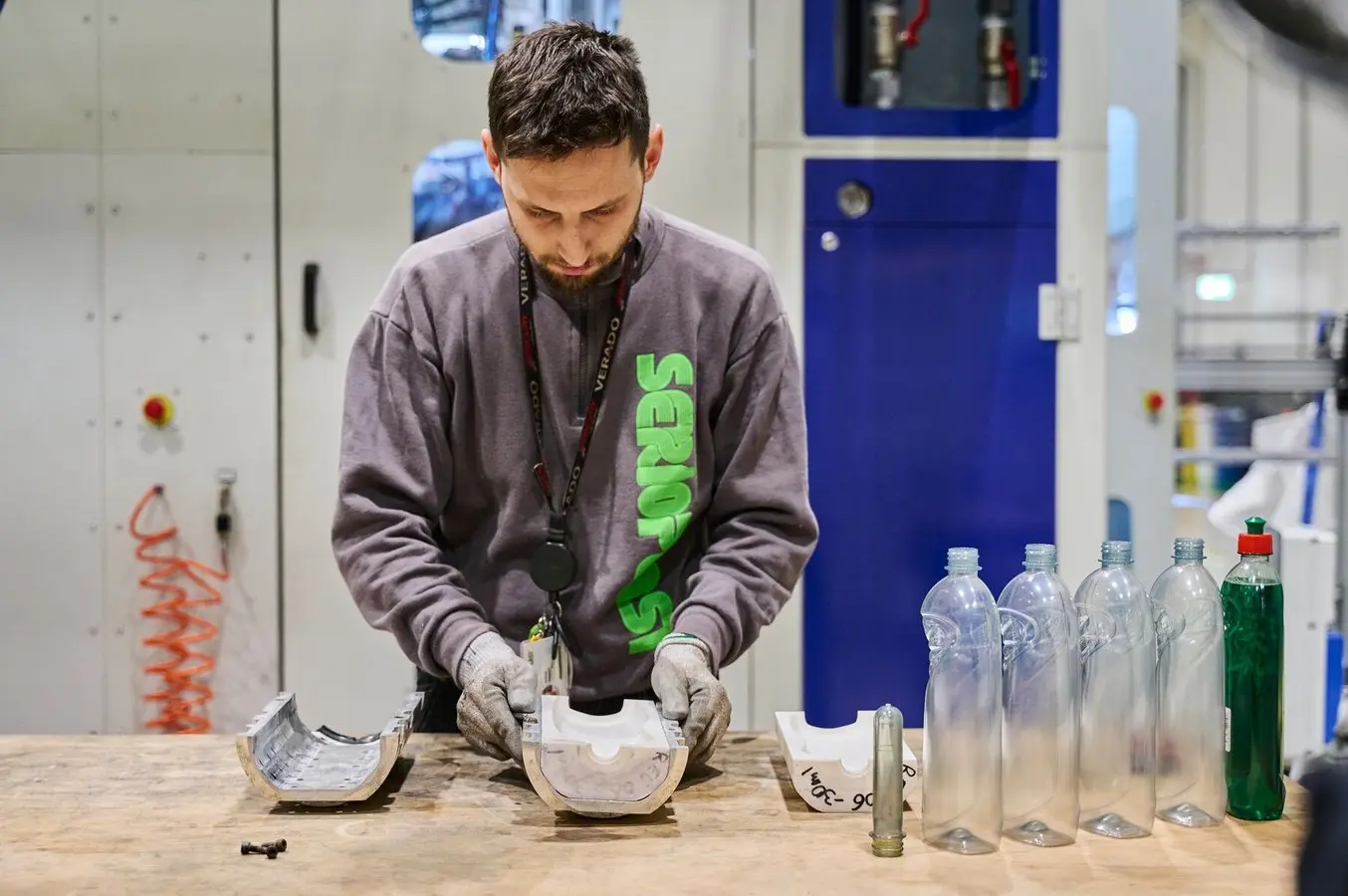
3D-gedruckte Formen für das Streckblasen, hergestellt aus Rigid 10K Resin, weisen so glatte Oberflächen und hohe Maßgenauigkeit auf, dass sie Flaschen erzeugen können, die kaum von denen aus traditionellen Stahlformen zu unterscheiden sind.
Genauigkeit und Präzision sind in allen Branchen, von der Fertigung bis zur Zahnmedizin, von größter Bedeutung. Und derzeit ist der SLA-Druck eine der genauesten 3D-Drucklösungen auf dem Markt.
Genauigkeit bezieht sich dabei darauf, wie exakt die Abmessungen des CAD-Modells abgebildet werden, während Präzision die konsistente Wiederholbarkeit der Dimensionen beschreibt. Im Vergleich zur Genauigkeit der zerspanenden Bearbeitung liegen SLA-3D-Drucker zwischen der Standardbearbeitung und der Feinbearbeitung. Die Genauigkeit variiert jedoch zwischen den Herstellern von Kunstharz-3D-Druckern und kann von der Art der Lichtquelle abhängen, die zur Aushärtung des Harzes verwendet wird, von der Qualität der Komponenten und von der Ingenieur- und Kalibrierungsarbeit, die in die Funktionalität dieser Komponenten einfließt. Auch das Material spielt eine Rolle – starre Materialien sind genauer und einfacher zu drucken als flexible Materialien.
Zum Beispiel eröffnen der Form 4/B und der Form 4L/4BL den Druck mit Precision Model Resin – einem hochgenauen Material zur Fertigung von Zahnersatzmodellen, bei denen die gedruckte Oberfläche zu über 99 % in einem Toleranzbereich von 100 μm zum digitalen Modell liegt. Beim 3D-Druck größerer Modelle (Merkmale mit 81–150 mm) beträgt die typische Maßtoleranz von Grey Resin ±0,3 % (untere Grenze: ±0,15 mm).
Die Kombination aus beheiztem Harztank und geschlossener Konstruktionsumgebung gewährleistet nahezu identische Bedingungen für jeden Druckauftrag. Die höhere Genauigkeit lässt sich darauf zurückführen, dass mit niedrigeren Drucktemperaturen gearbeitet wird als bei Thermoplasttechnologien, bei denen das Rohmaterial geschmolzen wird. Da SLA statt Wärme Licht einsetzt, erfolgt der Druckvorgang nahezu bei Raumtemperatur. Aus diesem Grund kommt es bei den Druckteilen nicht zu Artefakten durch Wärmeausdehnung und Kontraktion.
Das LFD-Drucksystem des Form 4 und Form 4L, insbesondere die hochauflösende Flüssigkristallanzeige und die kollimierenden Linsen in der LPU 4, erzeugt hypergenaue Querschnitte jedes Teils. Dank der geringen Abzugskräfte der Ablösetextur und des flexiblen Harztankfilms ist die Genauigkeit wiederholbar und führt zu hochpräzisen Teilen.
Filigrane Details und makellose Oberflächenbeschaffenheit
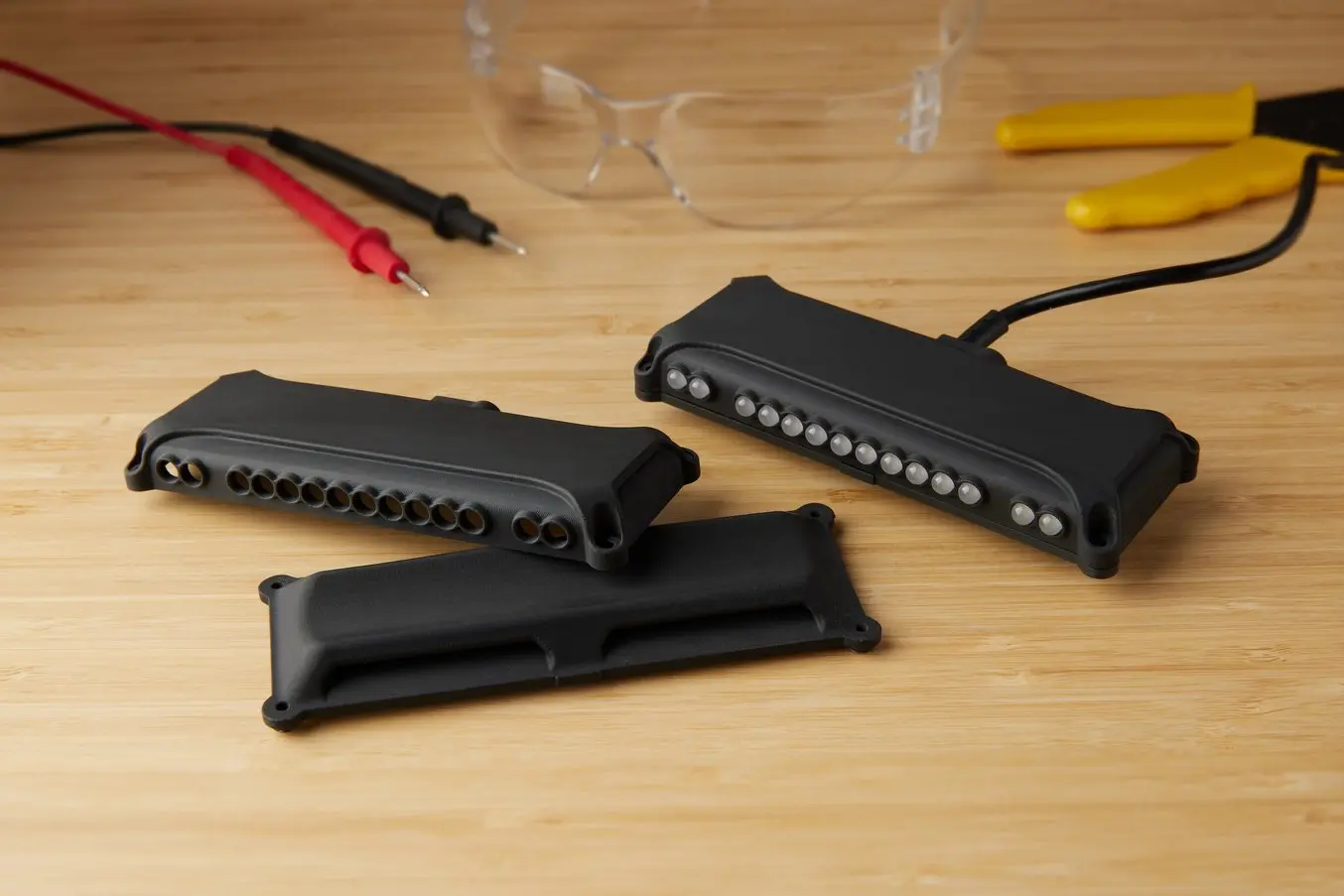
Kunstharz-3D-Drucker erstellen Teile mit einer glatten Oberflächenbeschaffenheit, sodass auch auf komplexen Strukturen wie gekrümmten Oberflächen kaum Schichtlinien sichtbar sind.
SLA-3D-Drucker gelten als das Maß der Dinge in der Herstellung von Teilen mit glatten Oberflächen und feinen Details. 3D-gedruckte Kunstharzteile haben ein Erscheinungsbild, das mit traditionellen Herstellungsverfahren wie dem Spritzguss vergleichbar ist – und das bei minimaler Nachbearbeitung. Im Gegensatz dazu haben FDM-Teile oft sichtbare Schichtlinien und SLS-Teile weisen oft eine körnige, leicht raue Textur auf der Oberfläche auf.
Die Oberflächenqualität von SLA-Teilen eignet sich hervorragend zur Herstellung von Endverwendungsteilen, die aussehen und sich anfühlen wie in Massenproduktion hergestellte Konsumgüter. Außerdem ermöglicht SLA sekundäre Prozesse wie Rapid Tooling.
Im Vergleich zu FDM-3D-Druckern erreichen SLA-3D-Drucker feinere Details und kleinere Mindeststrukturgrößen, ähnlich wie SLS-3D-Drucker. Das Licht in Kunstharz-3D-Druckern kann in viel präzisere Formen gesteuert werden als ein Filamentextruder, was kleinere Details oder dünnere Wände erlaubt. Außerdem arbeiten SLA-Lichtquellen auch mit geringerer Leistung als die Laser in SLS-3D-Druckern, was zu einer größeren Präzision und kleineren Merkmalen führt.
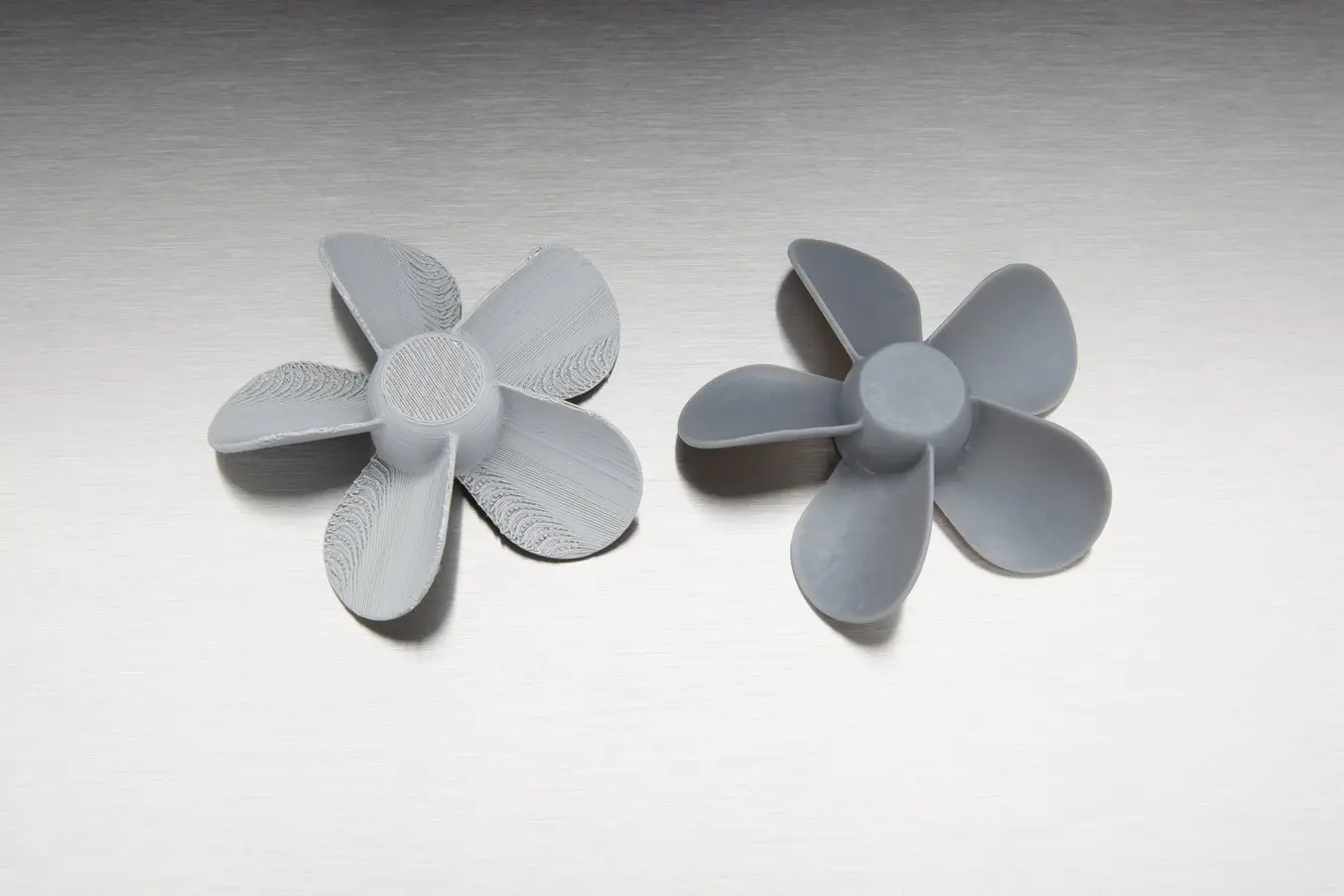
Während bei FDM-Druckteilen häufig Schichtlinien sichtbar sind und um komplexe Merkmale herum Ungenauigkeiten aufweisen, haben SLA-Druckteile scharfe Kanten, eine glatte Oberfläche und nur minimal sichtbare Schichtlinien.
Isotropie
Da beim 3D-Druck die Teile schichtweise gefertigt werden, gibt es bei den fertigen Druckteilen abhängig von der Ausrichtung des Teils zum Druckprozess möglicherweise Unterschiede in der Festigkeit. Dabei weisen die Teile in den X-, Y- und Z-Achsen unterschiedliche Eigenschaften auf.
Extrusionsbasierte Druckprozesse wie Schmelzschichtung (FDM) sind aufgrund der beim Druckprozess entstehenden Unterschiede von Schicht zu Schicht als anisotrop bekannt. Diese Anisotropie begrenzt die Nutzbarkeit von FDM bei bestimmten Eigenschaften oder macht zusätzliche Anpassungen bei der Druckgeometrie erforderlich, um sie zu kompensieren.
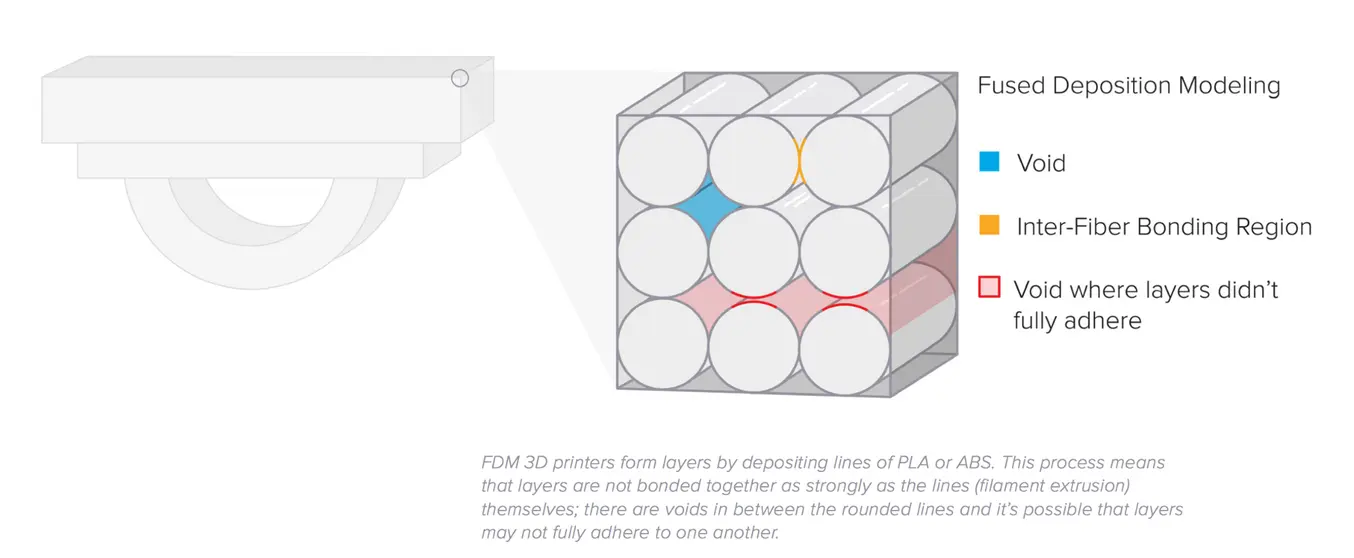
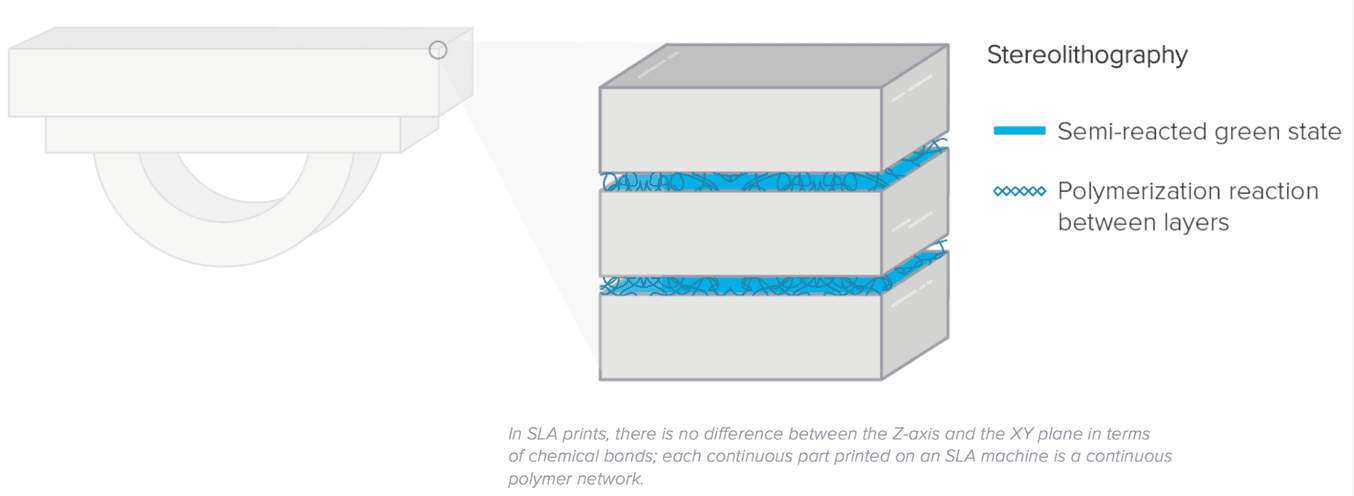
Im Gegensatz dazu sorgen Kunstharz-Drucker für hochgradig isotrope Teile. Die Isotropie hängt von verschiedenen Faktoren ab, die über die Integration der Materialchemie in den Druckprozess genau gesteuert werden können. Während des Druckvorgangs bilden die Harzbestandteile kovalente Bindungen, doch von Schicht zu Schicht bleibt das Teil ein halb reagiertes „Grünteil“.
In diesem Grünteilzustand bleiben im Kunstharz polymerisierbare Gruppen zurück, die Verbindungen über Schichten hinweg eingehen können. Bei der finalen Nachhärtung werden dem Teil so Isotropie und Wasserdichtigkeit verliehen. Auf molekularer Ebene gibt es dadurch keine Unterschiede zwischen den X-, Y- oder Z-Schichten. Dies führt zu Teilen mit vorhersehbaren mechanischen Eigenschaften, wie sie für Anwendungen wie Halterungen und Vorrichtungen, Endverbrauchsteile und funktionsfähige Prototypen erforderlich sind.
Wasserdichtigkeit
SLA-Druckteile sind durchgehend vernetzt – unabhängig davon, ob Geometrien mit soliden Details oder internen Kanälen erzeugt werden. Die Wasserdichtigkeit ist wichtig für ingenieurtechnische und fertigungstechnische Anwendungen, bei denen der Luft- oder Fluidfluss kontrolliert und vorhersehbar sein muss. Ingenieure und Designer nutzen die Wasserdichtigkeit von SLA, um den Herausforderungen bei Luft- und Flüssigkeitsströmen in der Automobiltechnik und der biomedizinischen Forschung zu begegnen und Teiledesigns für Produkte wie Küchengeräte zu validieren.
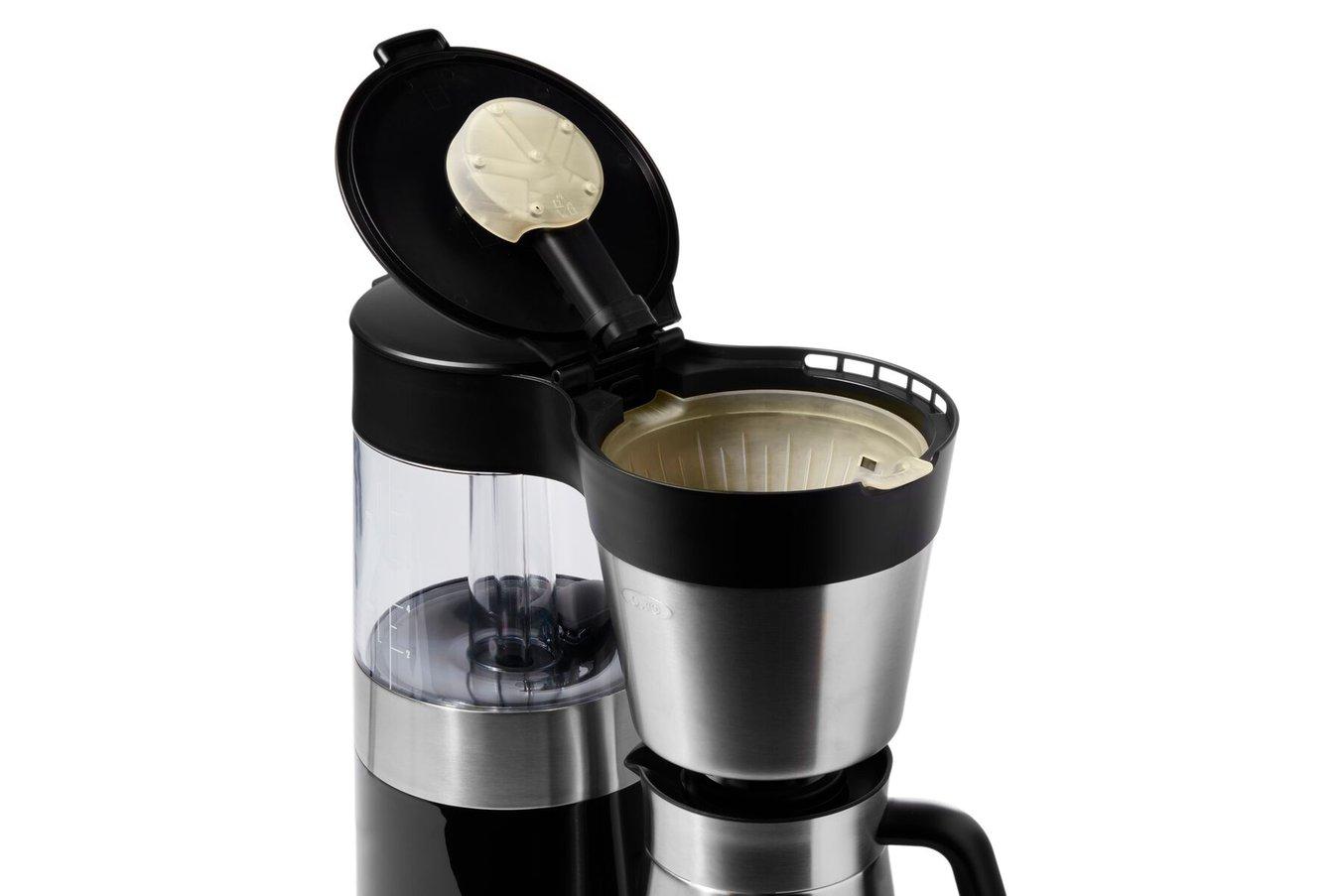
OXO verlässt sich auf die Wasserdichtigkeit von SLA-Druck, um robuste funktionsfähige Prototypen für Produkte mit Luft- oder Fluidfluss zu fertigen – wie diese Kaffeemaschine.
Maßanfertigungen oder Kleinserien wasserdichter und gasdichter Teile sind in vielen Branchen gefragt, darunter die Meeresforschung, Unterwasserrobotik, nachhaltige Technologieentwicklung, Öl- und Gasindustrie sowie Verteidigung. Obwohl einige 3D-Drucktechnologien eine ideale Lösung für diese Teile bieten, besteht oft die Meinung, dass additiv hergestellte Teile porös seien und nicht in Umgebungen mit hohem Druck eingesetzt werden können.
In den letzten Jahren wurde diese Annahme jedoch gründlich widerlegt. SLA-Drucker erstellen wasserdichte Gehäuse und gänzlich wasserfeste Teile. Einrichtungen wie die National Oceanic and Atmospheric Administration (NOAA) oder die University of Rhode Island haben mit kostengünstiger und qualitativ hochwertiger gedruckter Test- und Forschungsausrüstung enorme Fortschritte in der Meeresforschung erzielt.
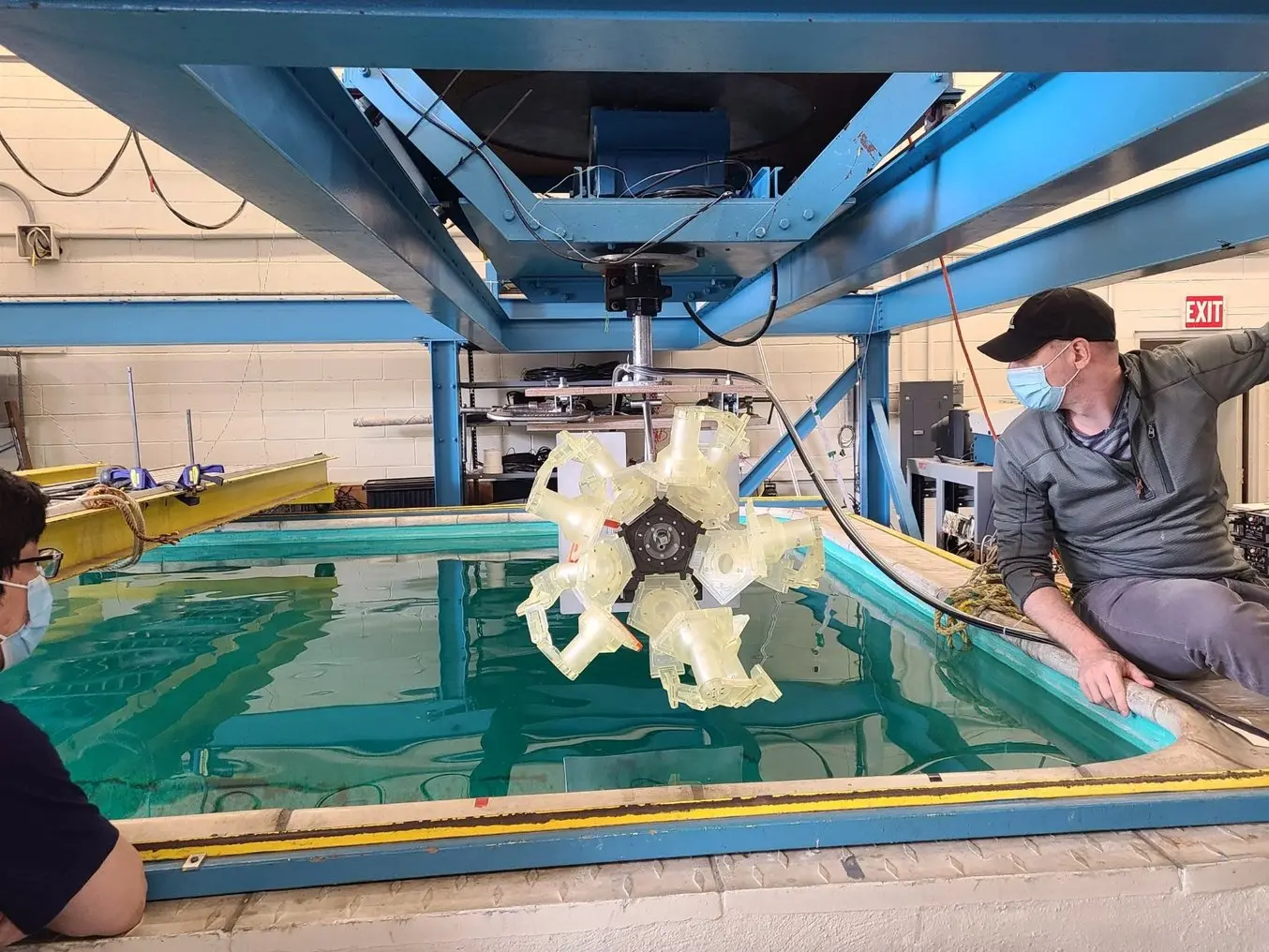
Dank 3D-Druck können neue und komplexe Formen für Testgeräte und Probensammler ausprobiert werden – wie dieses Werkzeug mit Komponenten aus Clear Resin.
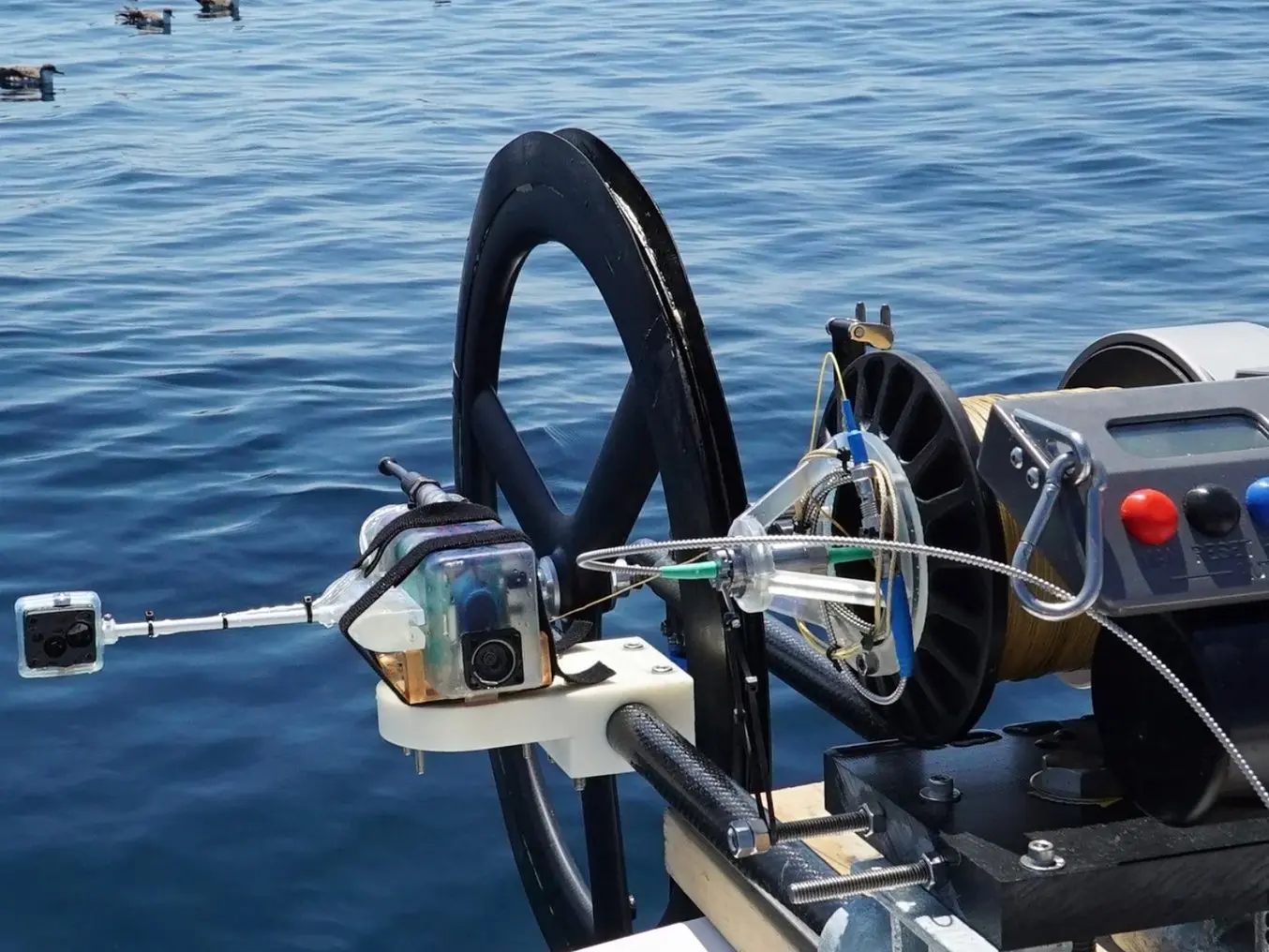
Die Reaktionsfähigkeit des bedarfsgesteuerten 3D-Drucks macht maßgefertigte Halterungen und Vorrichtungen zur See kostengünstig und überhaupt erst möglich.
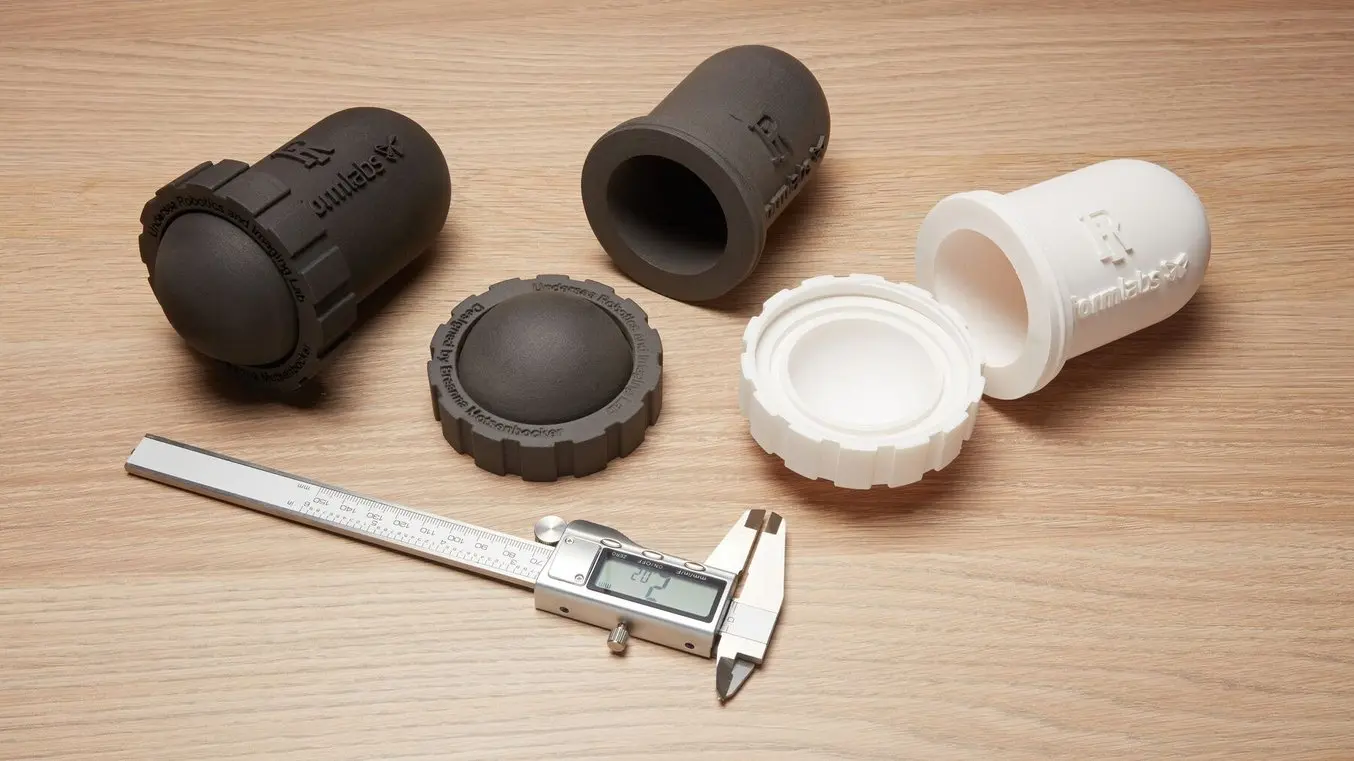
3D-Druck wasserdichter Behälter und Ergebnisse von Druckprüfungen
In diesem Whitepaper stellen wir die Testergebnisse vor und geben klare Richtlinien zum kostengünstigen 3D-Druck individueller wasserdichter Behälter.
Anwendungsbereiche des SLA-3D-Drucks
Teile aus 3D-gedrucktem Kunstharz treiben Innovationen voran und unterstützen Unternehmen in einer breiten Palette von Branchen und Anwendungen. Fortschrittliche Materialien, unglaubliche Maßgenauigkeit und intuitive Arbeitsabläufe ermöglichen Teile für jedes Stadium, vom Prototyping bis zur Produktion. Mit sinkenden Kosten und einer gleichzeitigen Verbesserung der Technologie werden Endanwendungen und kundenindividuelle Massenfertigung zunehmend zur Norm, nicht zur Ausnahme.
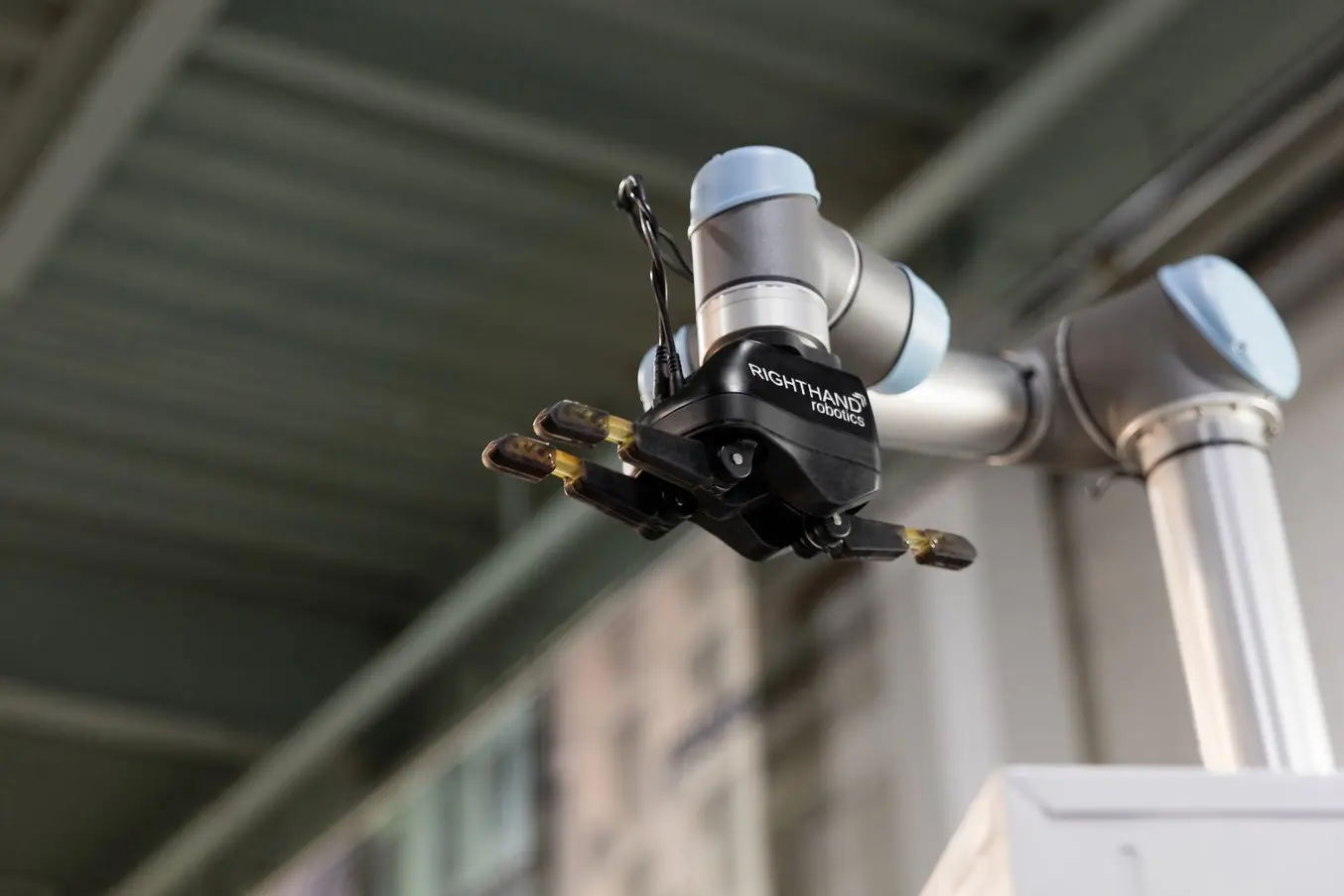
Maschinenbau und Produktdesign
Mittels Rapid Prototyping und 3D-Druck verwandeln Ingenieur- und Produktdesignteams Ideen in realistische Konzeptnachweise, entwickeln diese Konzepte zu Prototypen, die wie Endprodukte aussehen und funktionieren, und führen Produkte durch eine Reihe von Validierungsstufen bis zur Massenproduktion.
Anwendungen:
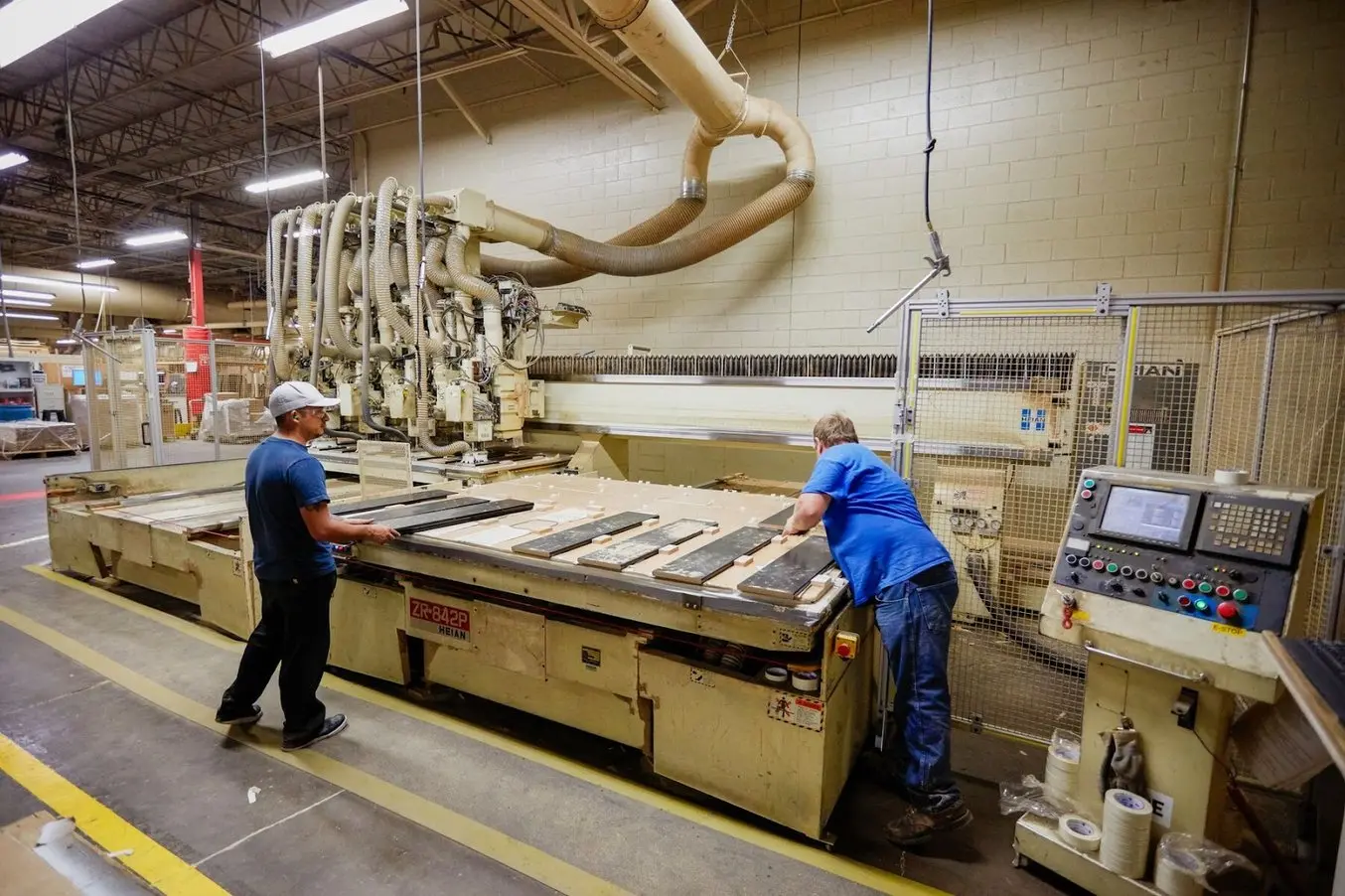
Fertigung
Hersteller automatisieren Produktionsprozesse und optimieren Arbeitsabläufe durch die Herstellung von Prototypenwerkzeugen und den direkten 3D-Druck von maßgefertigten Werkzeugen, Formen und Fertigungshilfsmitteln zu deutlich niedrigeren Kosten und Durchlaufzeiten als bei der traditionellen Fertigung. Dies reduziert die Fertigungskosten und -fehler, erhöht die Qualität, beschleunigt die Montage und maximiert die Arbeitseffektivität.
Anwendungen:
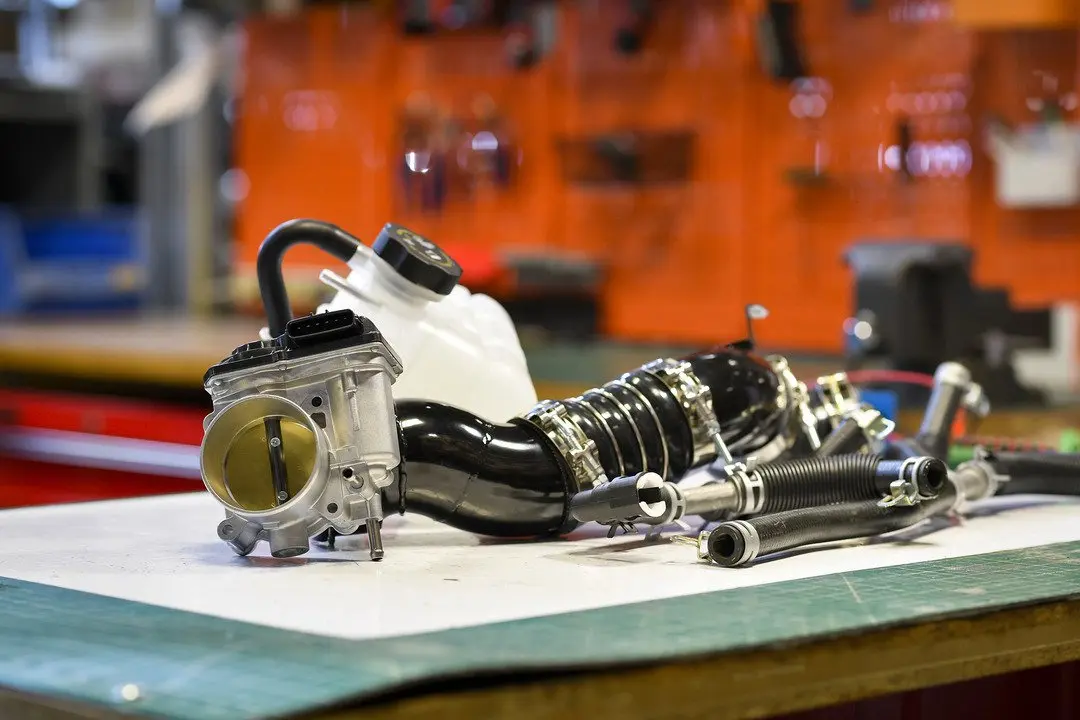
Automobilindustrie
Automobildesignteams, Herstellerfirmen und Maschinenbauabteilungen nutzen SLA-3D-Druck für eine Vielzahl an Teilen im gesamten Prozess. Von Konzeptmodellen bis Aftermarket finden sich SLA-Teile überall – bei der Entwicklung und Produktion jedes Straßenfahrzeugs.
- Rapid Prototyping (Konzeptmodell, funktionales Prototyping, Validierungstests)
- Rapid Tooling
- Fertigungshilfen Teile für
- Endverwendung, Aftermarket und Individualisierung
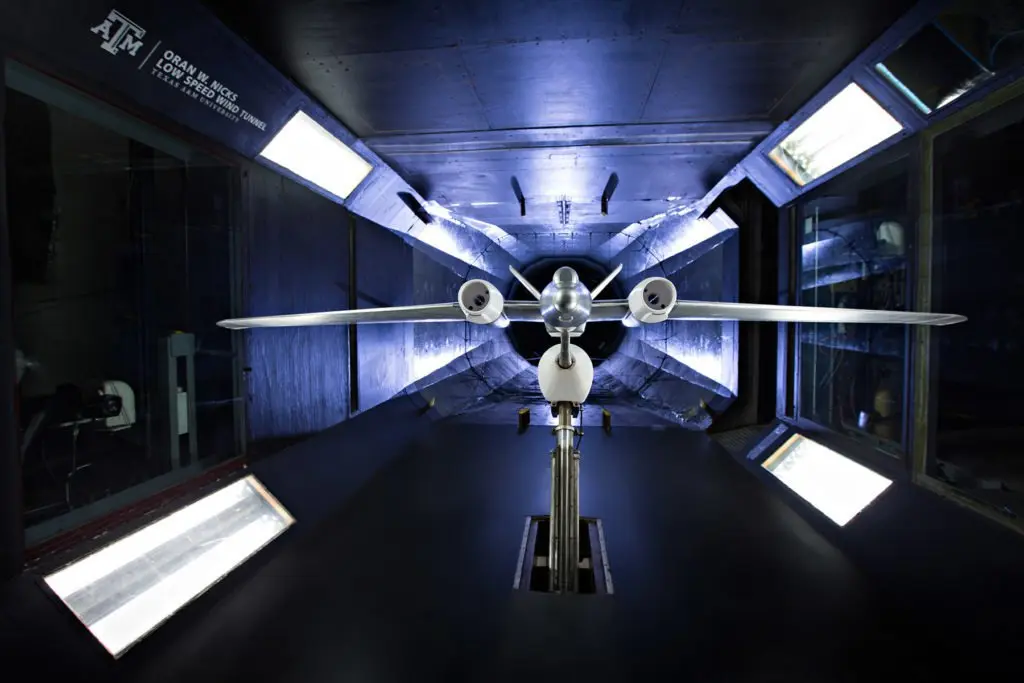
Luft- und Raumfahrt
SLA-3D-gedruckte Teile wurden bereits für Tests auf der Internationalen Raumstation eingesetzt, dienen in der Fertigung für kommerzielle Fluglinien und finden weltweit Anwendung in Tests, Prototypenbau und Fertigung sowohl in der privaten als auch staatlichen Luft- und Raumfahrtindustrie. Von Vorrichtungen, die beim Bau von Laseranlagen für Weltraummissionen helfen, bis hin zu Keramikteilen, die in Tests mit Flugzeugtreibstoff verwendet werden, tragen SLA-Teile dazu bei, dass wir die letzte Grenze erreichen.
- Rapid Prototyping (Windkanaltests)
- Rapid Tooling
- Fertigungshilfsmittel
- Endverwendung, Ersatzteile und Sonderanfertigungen
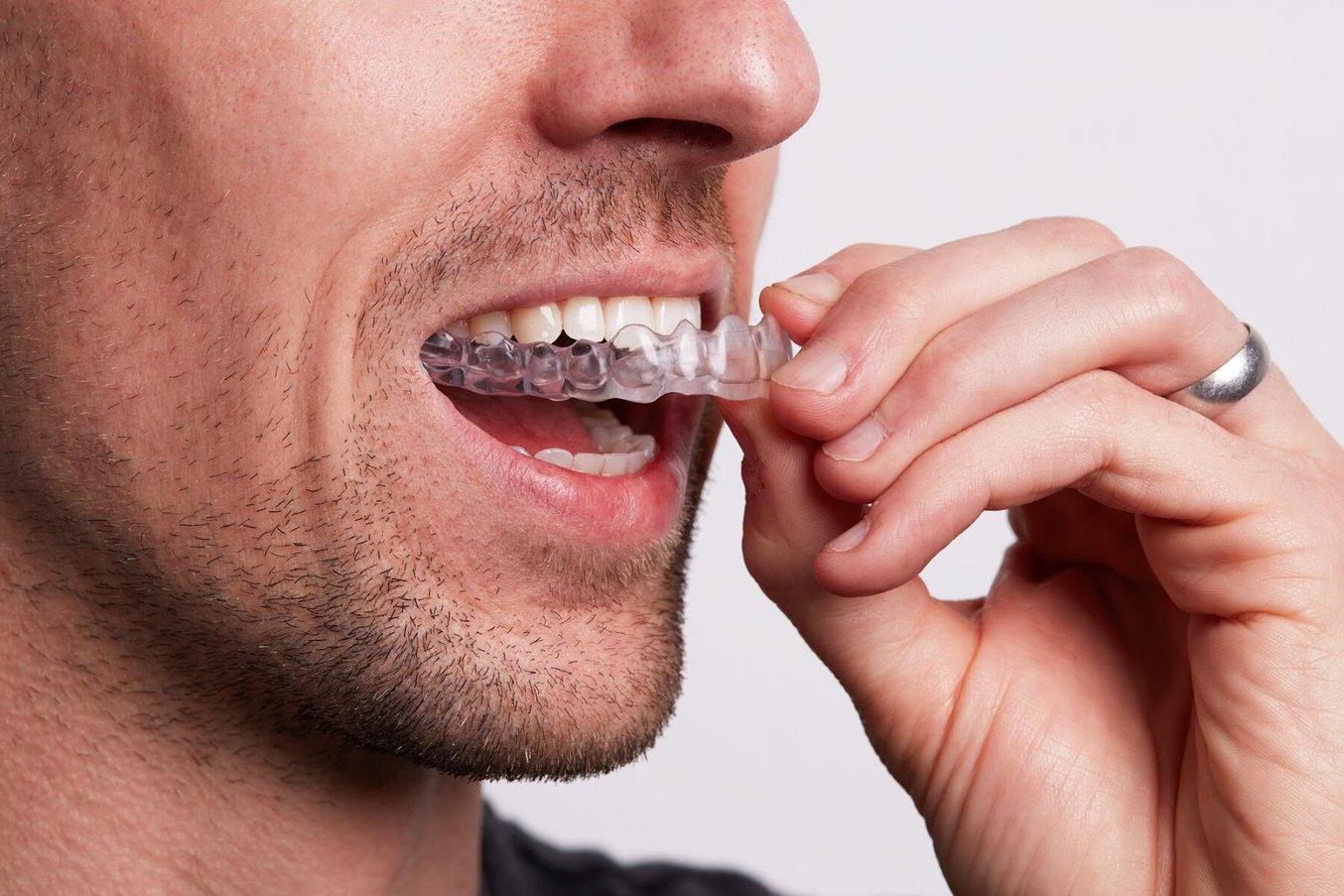
Zahnmedizin
Die digitale Zahnmedizin verringert die durch menschliche Faktoren verursachten Risiken und Unsicherheiten und bietet in jeder Phase des Arbeitsablaufs höhere Gleichmäßigkeit, Genauigkeit und Präzision zur besseren Versorgung der Patient*innen. 3D-Drucker produzieren eine Reihe hochwertiger und maßgefertigter Produkte und Anwendungen zu niedrigen Stückkosten mit hervorragender Passform und wiederholbaren Ergebnissen.
Anwendungen:
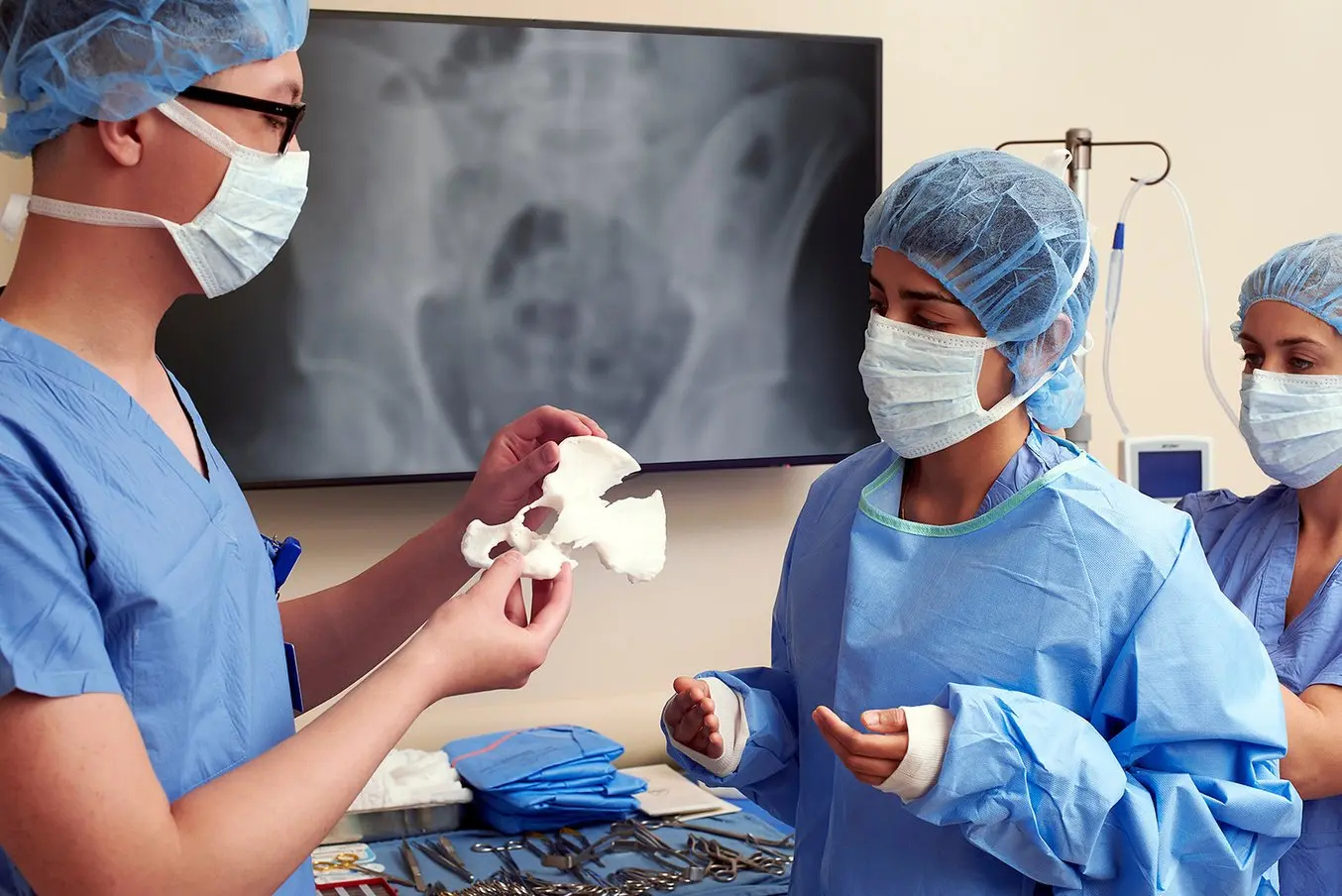
Gesundheitswesen
Mithilfe des erschwinglichen, professionellen Desktop-3D-Drucks passen Ärzte Behandlungen und Geräte höchst individuell auf die einzelnen Patient*innen an. So bieten sie hochleistungsfähige medizinische Anwendungen und sparen den Einrichtungen gleichzeitig viel Zeit und Geld.
Anwendungen:
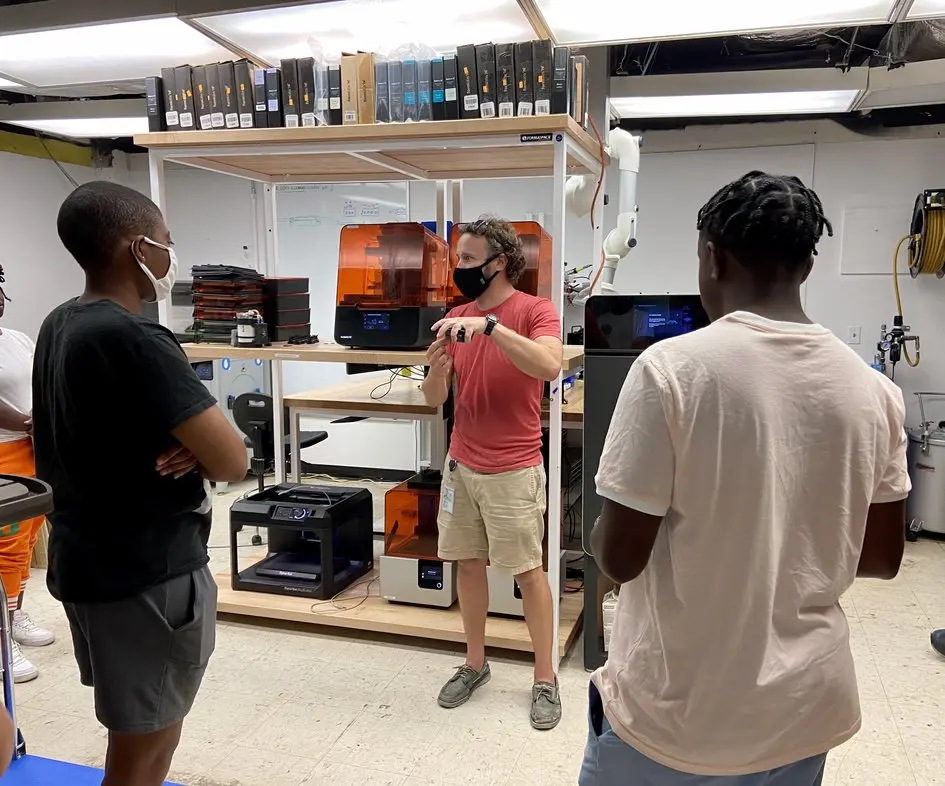
Weiterbildung
3D-Drucker sind multifunktionale Werkzeuge für immersives Lernen und innovative Forschung. Sie fördern die Kreativität und machen die Lernenden vertraut mit Technologien auf professionellem Niveau. Dabei unterstützen sie die Lehrpläne für Naturwissenschaften, Maschinenbau, Kunst und Design.
Anwendungen:
- Forschung und Entwicklung
- FabLabs und Makerspaces
- Disziplinenübergreifende Lehre von Werkzeugen
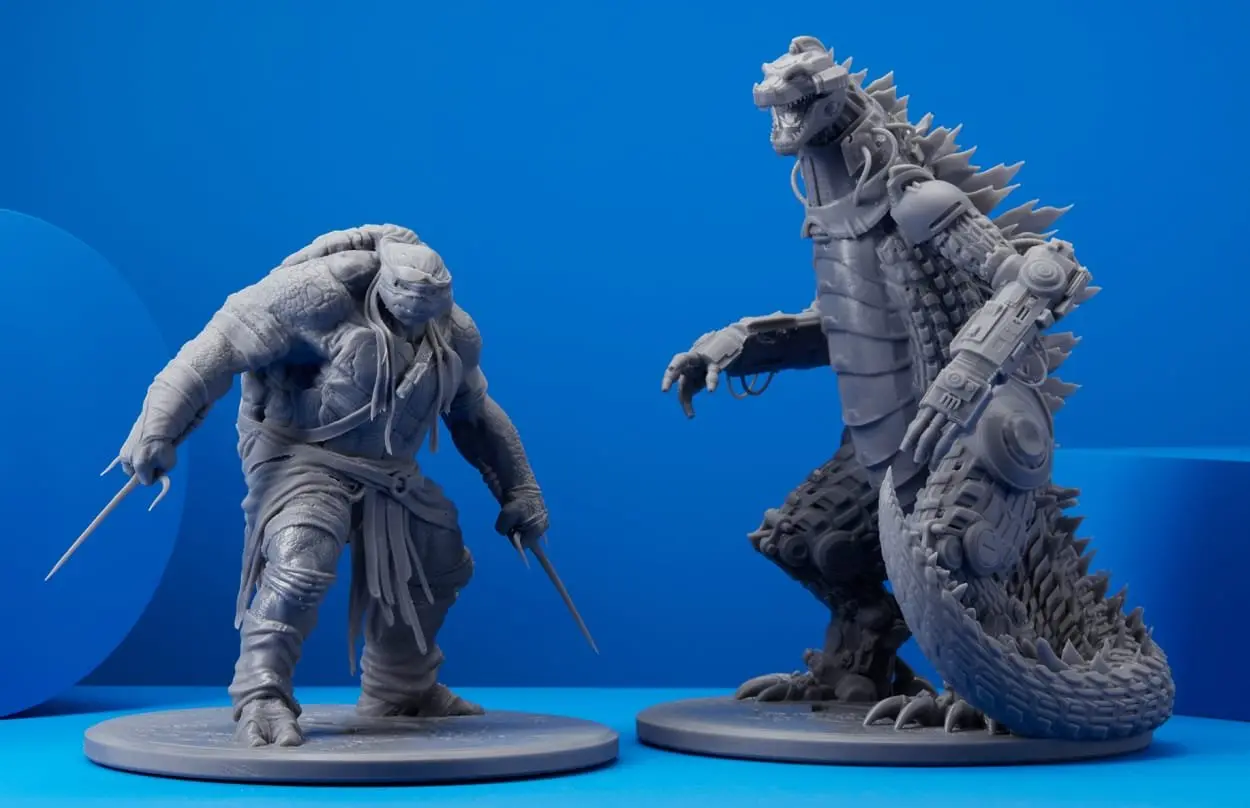
Unterhaltungsindustrie
Hochauflösende physische Modelle kommen oft zum Einsatz bei Skulpturen, der Charaktermodellierung sowie bei Requisiten. 3D-Druckteile spielen eine wichtige Rolle in Stop-Motion-Filmen, Videospielen, bei maßgeschneiderten Kostümen und sogar bei Spezialeffekten in Blockbusterfilmen.
Anwendungen:
- Hyperrealistische Skulpturen
- Charaktermodelle
- Requisiten
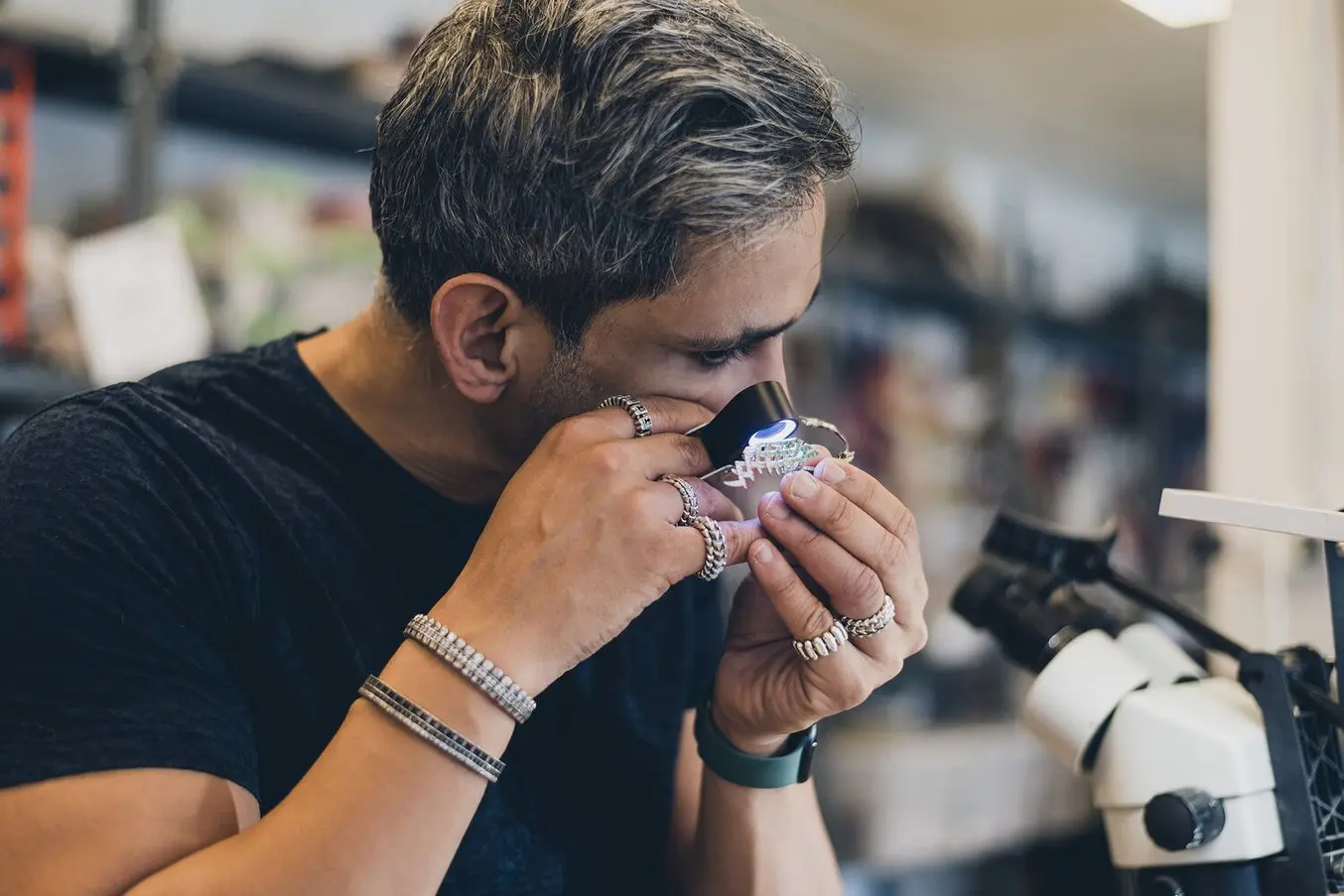
Schmuck
Juwelierfachleute verwenden CAD und 3D-Druck, um schnell Prototypendesigns zu erstellen, der Kundschaft Passstücke anzubieten und große Chargen von gussfertigen Teilen herzustellen. Digitale Hilfsmittel ermöglichen das Erstellen gleichmäßiger, detailreicher Stücke ohne die mühselige Kleinarbeit und Abweichung, die mit dem Wachsschnitzen einhergehen.
Anwendungen:
- Wachsausschmelzguss (Feinguss)
- Lebensechte Prototypen von Sonderanfertigungen
- Urmodelle für den Formenbau mit Kautschuk
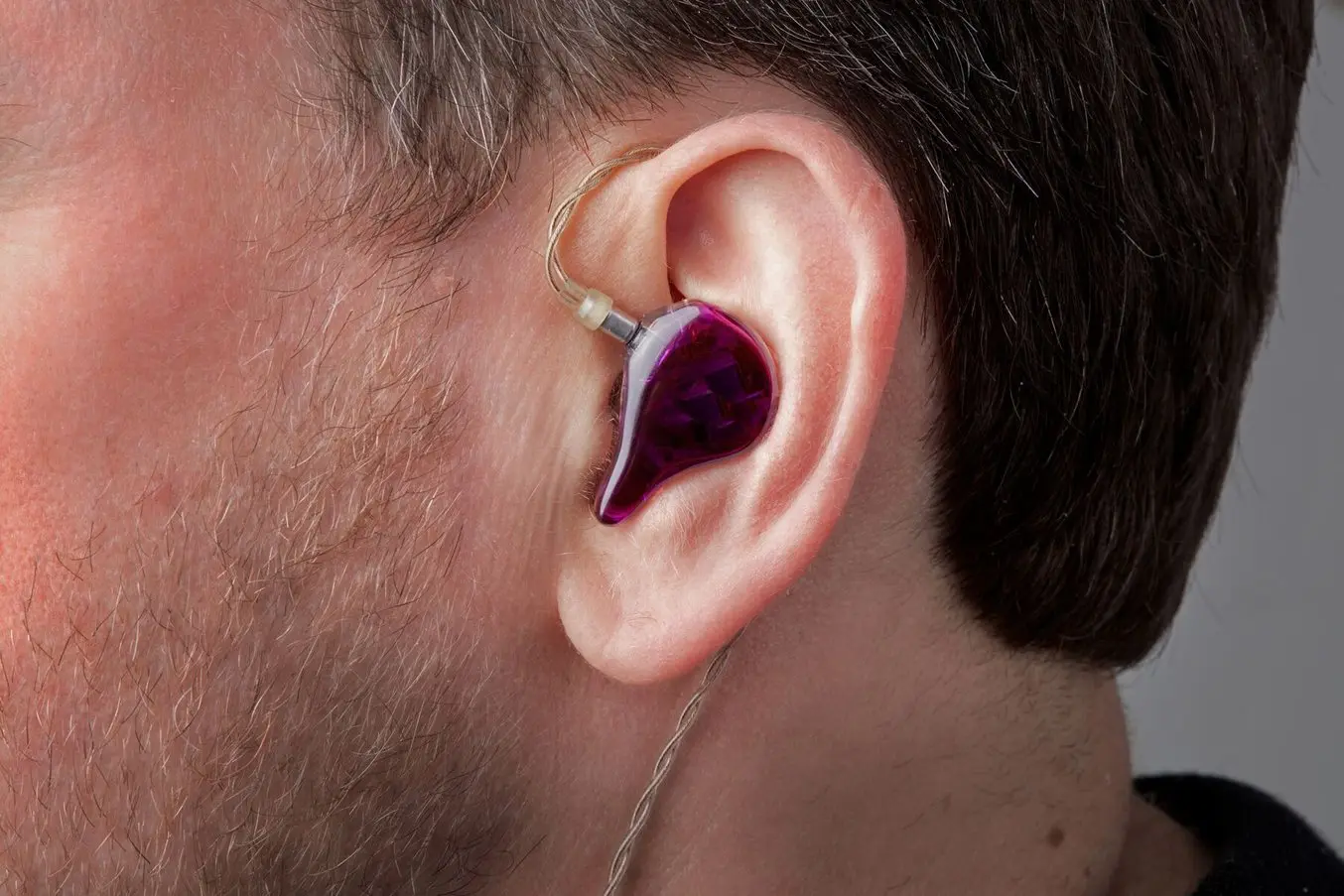
Audiologie
Hörakustiker*innen und Otoplastiklabore nutzen digitale Workflows und 3D-Druck, um qualitativ hochwertigere, maßgefertigte Ohrpassstücke gleichmäßiger und in höheren Stückzahlen für Anwendungen wie Hinterohr-Hörgeräte, Gehörschutz und individuell angepasste Ohrhörer und -stöpsel herzustellen.
Anwendungen:
- Hörgeräte
- Gehörschutz
- Audio-Anwendungen für den Endverbrauch
Beliebte SLA-3D-Druckmaterialien
SLA-3D-Druckmaterialien sind äußerst vielseitig. Die Kunstharzformulierungen stehen in Sachen optischen, mechanischen und thermischen Eigenschaften herkömmlichen technischen oder industriellen Thermoplasten in nichts nach. Es gibt Kunstharze, die speziell für Herstellungsanforderungen wie elektrostatische Entladung oder Brandschutz formuliert sind, sowie Kunstharze, die die mechanischen Eigenschaften branchenbekannter Kunststoffe nachahmen. Abhängig von der Formulierung und Chemie dienen einige Kunstharze auch zur Herstellung reiner Silikon-, Polyurethan- oder Keramikteile. Der Kunstharzdruck bietet zudem das breiteste Spektrum an biokompatiblen Materialien, was neue Möglichkeiten für Endprodukte eröffnet, für medizinisches Gerät, für den 3D-Druck am Point of Care und für Innovationen in medizinischen Verfahren.
Die konkrete Materialauswahl hängt in hohem Maße vom Hersteller und vom Druckertyp ab. Formlabs bietet mit über 40 Druckmaterialien mit einzigartigen Formulierungen die umfassendste Kunstharzbibliothek.
Die kostengünstige Herstellung komplexer geometrischer Teile durch 3D-Druck ist ein Katalysator für Innovationen. Mit den passenden Materialien lassen sich innovative Ideen testen, validieren und umsetzen. Formlabs’ Materialien begünstigen eine Vielzahl von Anwendungen, darunter massengefertigte Konsumgüter, chirurgische Instrumente, Zahnimplantate und dentale Anwendungen, Fertigungshilfsmittel, Rapid Tooling und mehr. Die Kunstharz-3D-Drucker von Formlabs erleichtern den Zugang zu diesen leistungsstarken Arbeitsabläufen.
Standard-Kunstharze
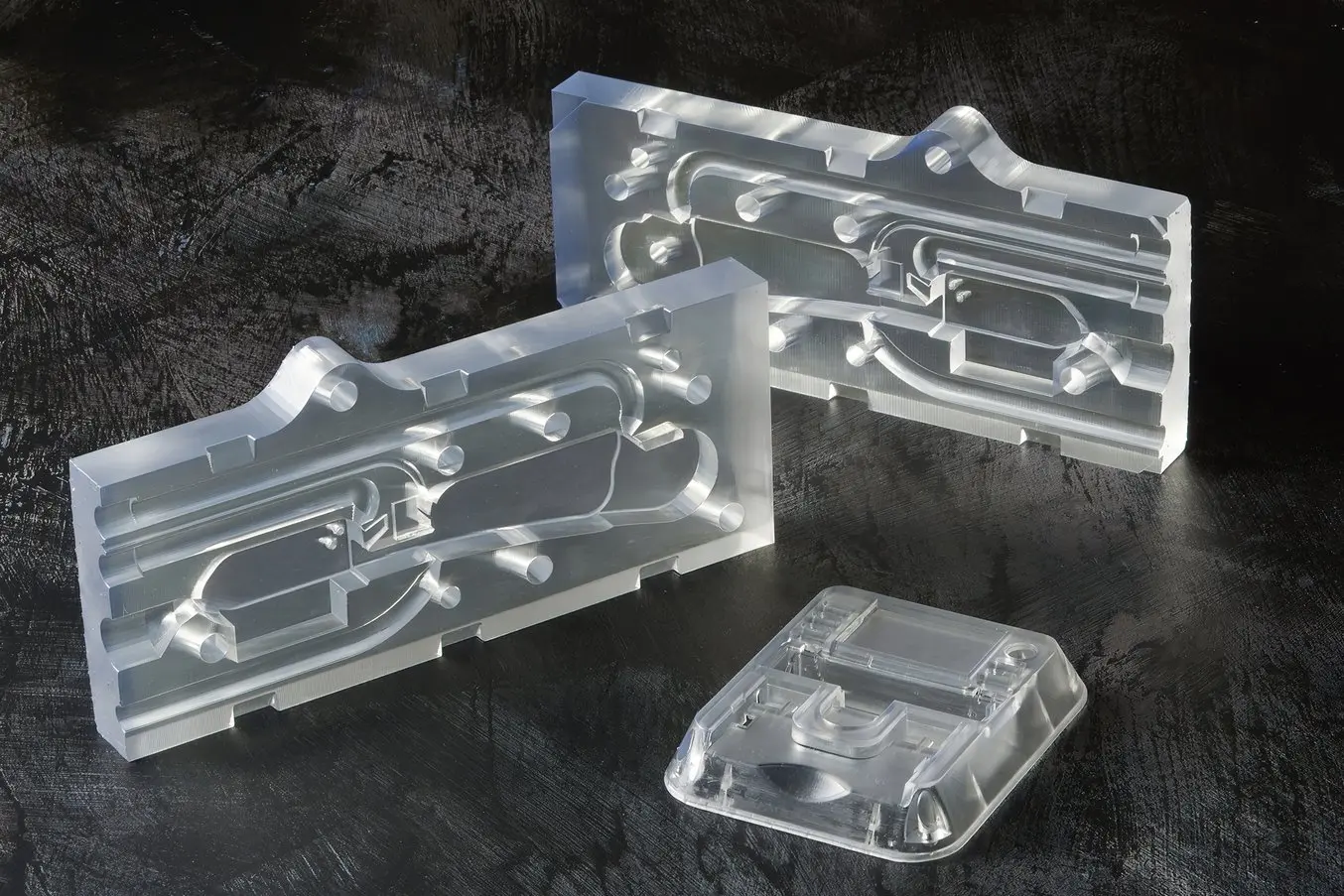
Mit Clear Resin fertigen Sie durchsichtige, farblose Teile, die sich auf nahezu vollkommene optische Transparenz polieren lassen. Bei Gussprozessen mit zweiteiligen Formen erleichtert diese Transparenz die Überwachung und Fehlerbehebung, da das Innere des Teils einsehbar ist.
Die Standard-Kunstharze von Formlabs sind auf Geschwindigkeit und Gleichmäßigkeit ausgelegt, um Teile für eine Vielzahl von Anwendungen und Branchen herzustellen. Sie reichen von matten Graustufen für Entwurfsprototypen bis hin zu transparenten Teilen aus Clear Resin für durchsichtige Modelle und Formen. Kurz: Die Standard-Kunstharze sind die Arbeitstiere des SLA-3D-Drucks. Formlabs' neueste Standard-Kunstharze für den Form 4 erreichen neue Höhen in Bezug auf Geschwindigkeit, mechanische Eigenschaften und Auflösung. Fast Model Resin lässt sich mit Geschwindigkeiten von 100 mm pro Stunde drucken und Grey Resin weist eine um 30 % höhere Schlagfestigkeit auf.
Material | Beschreibung | Anwendungen |
---|---|---|
Fast Model Resin | Druckgeschwindigkeit von bis zu 100 mm/h | Konzeptmodellierung Rapid Prototyping |
Clear Resin | Nach dem Polieren hochgradig transparent | Teile mit optischer Transparenz Rapid Prototyping Transparente Gussformen Millifluidik |
Grey Resin, Black Resin, White Resin | Glatte, matte Oberflächenbeschaffenheit Hohe Auflösung | Konzeptmodellierung Rapid Prototyping Halterungen und Vorrichtungen Maskierung |
Color Resin | Benutzerdefinierte Farben Helle, farbenfrohe Teile | Rapid Prototyping mit Abstimmung von Farbe, Material und Oberflächenbeschaffenheit (CMF) Farbcodierte Halterungen und Vorrichtungen Endbauteile in beliebigen Farben |
Maschinenbau und Fertigung
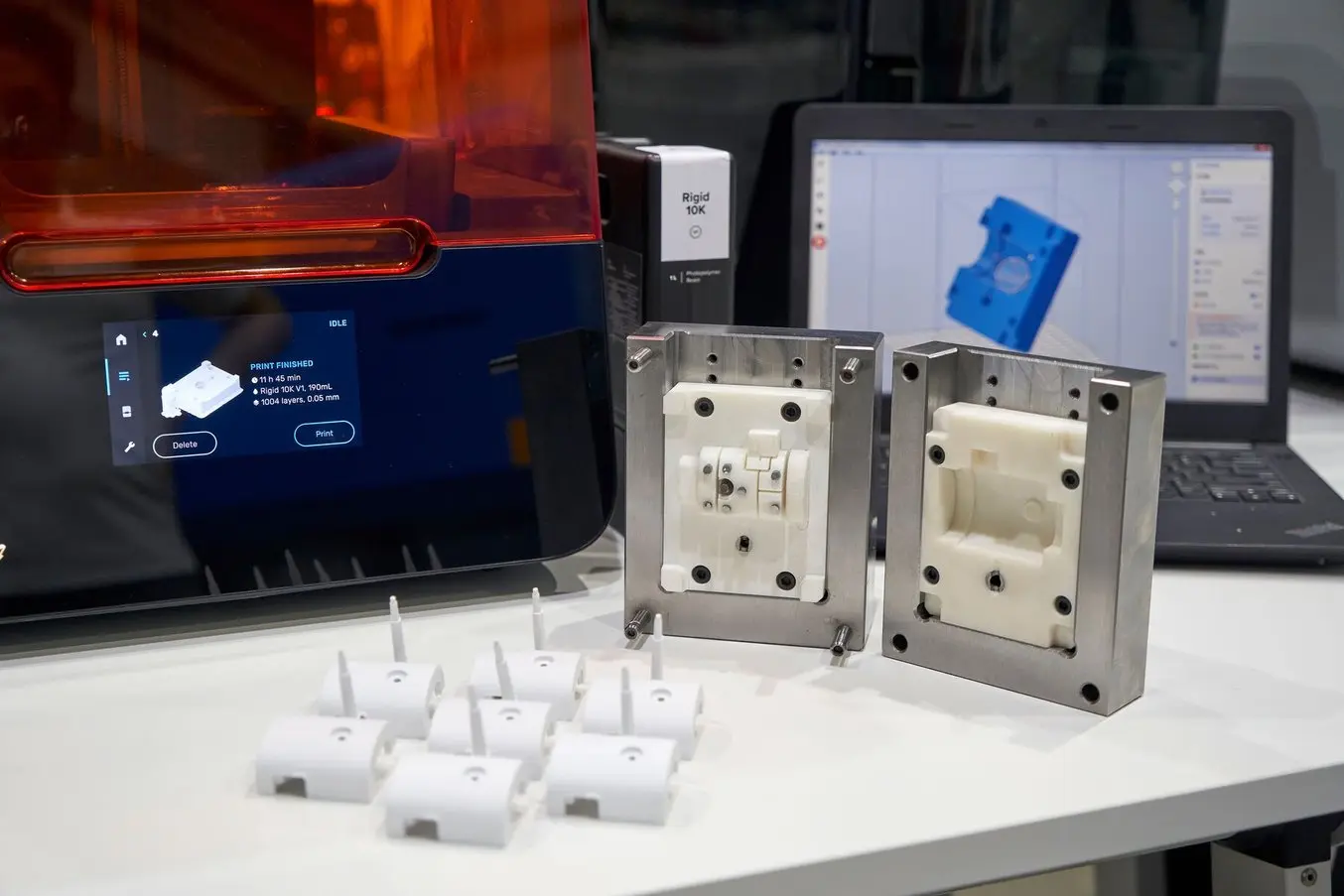
Rigid 10K Resin ist ein hochgradig glasgefülltes Material für Industrieteile, die erheblicher Belastung ohne Verformung standhalten müssen, beispielsweise für den Spritzguss.
Die technischen Kunstharze von Formlabs wurden speziell entwickelt, um Anforderungen in Maschinenbau- und Fertigungsprozessen zu erfüllen, neue Anwendungen zu ermöglichen, Betriebsabläufe zu optimieren und Feldtests zu vereinfachen. Diese Materialien sind darauf ausgelegt, die Leistung vertrauter Materialien wie ABS, Silikon oder PEEK nachzuahmen oder sogar zu übertreffen. Sie reichen von extrem starren und harten Materialien über robuste Materialien, die Stöße absorbieren, bis zu weichen und flexiblen Materialien, die Biegungen und Verformungen über viele Zyklen standhalten. Weiterhin gibt es einzigartige Spezialmaterialien wie ESD-sichere oder flammhemmende Kunstharze sowie technische Materialien, die zuvor im Desktop-3D-Druck nicht verfügbar waren, wie echter Keramik- und Silikon-3D-Druck.
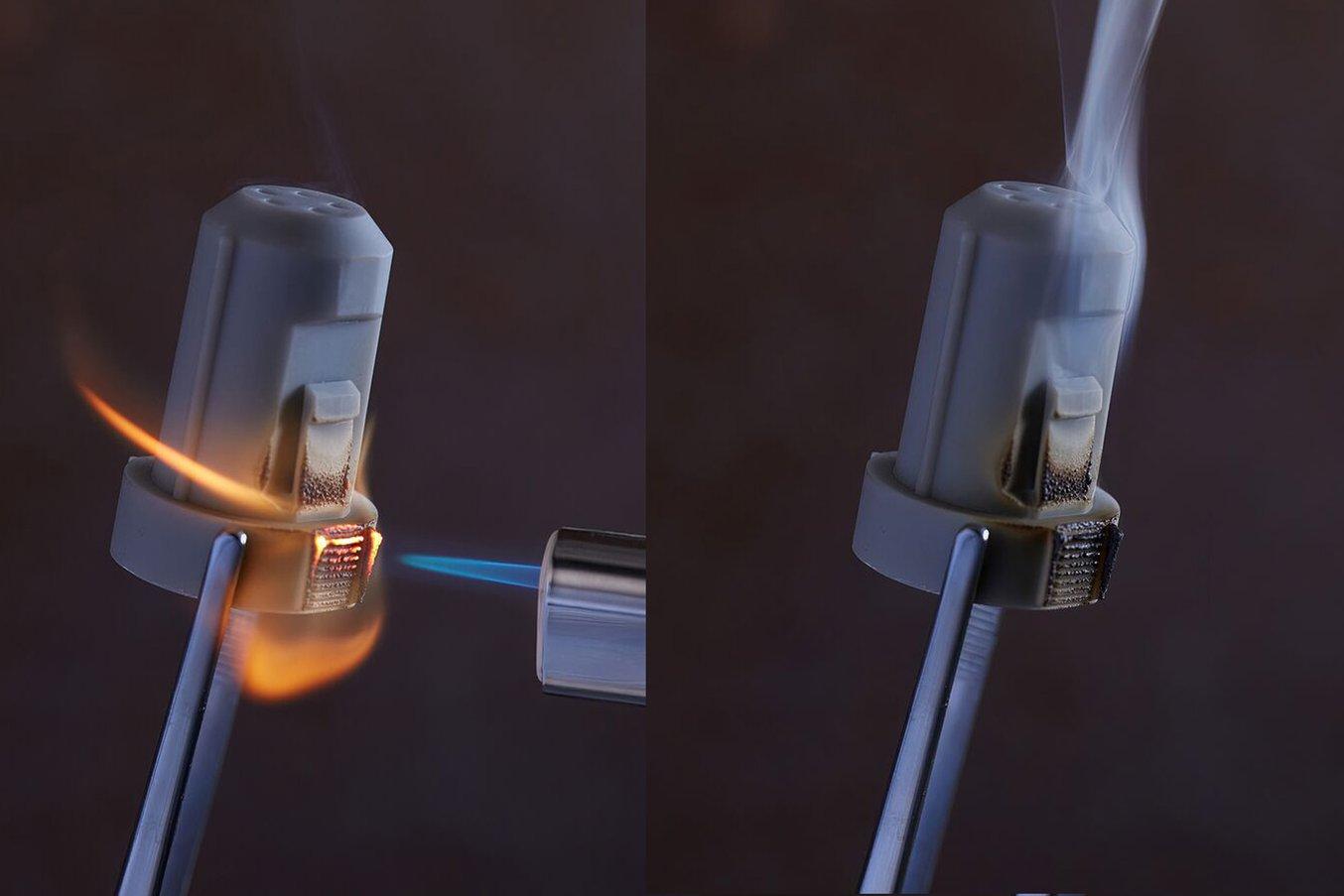
Formlabs' Flame Retardant Resin ist ein mit UL 94 Blue Card zertifiziertes Spezialkunstharz zur Herstellung selbstverlöschender, halogenfreier Teile.
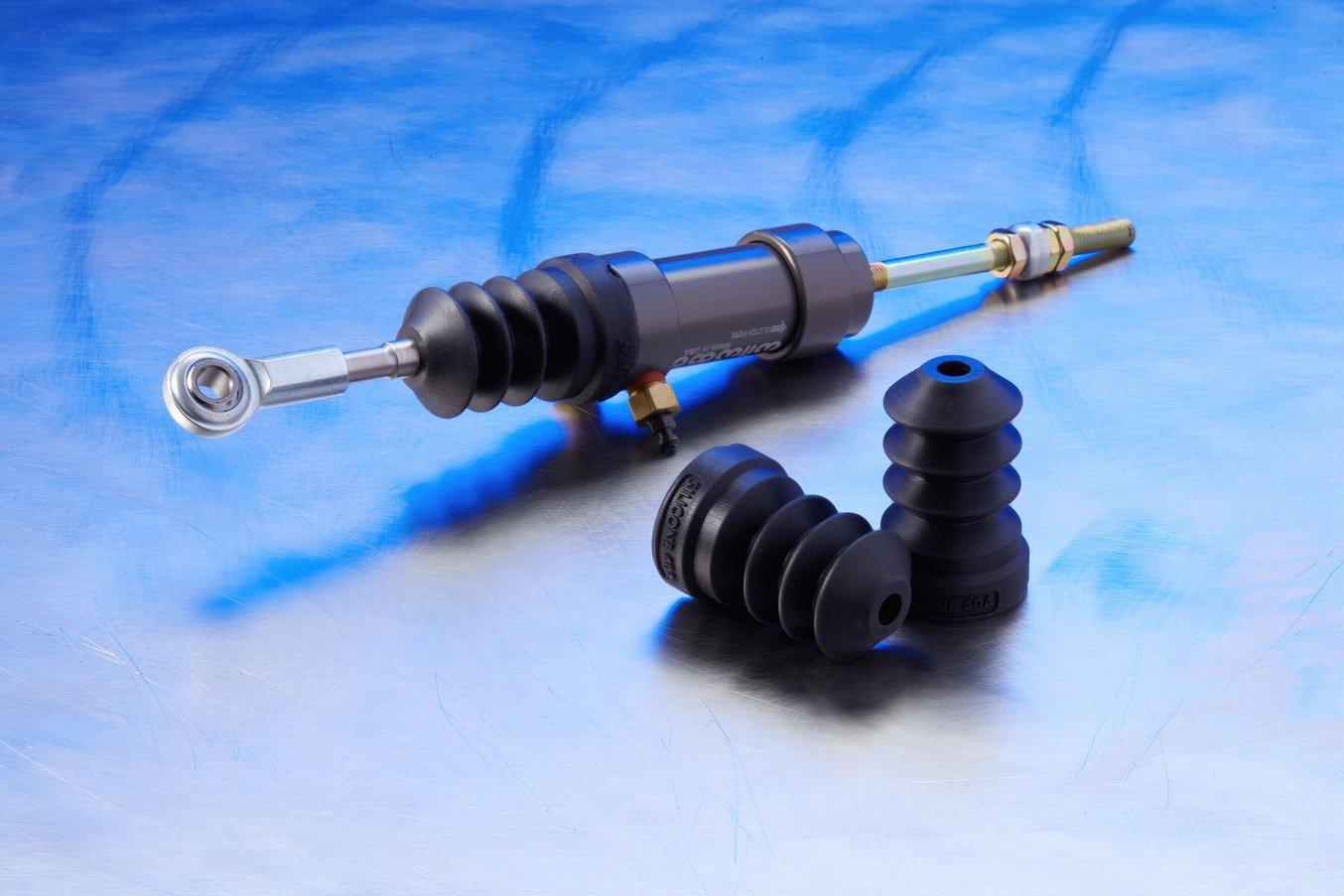
Silicone 40A Resin ist ein reines Silikon mit mechanischen Eigenschaften, die in Maschinenbau und Produktentwicklung altbekannt sind.
Material | Beschreibung | Anwendungen |
---|---|---|
Kunstharzfamilie Tough und Durable | Starke, robuste, funktionale und dynamische Materialien Halten wiederholter Kompression, Dehnung, Biegung und Schlagbelastung stand, ohne zu brechen Zahlreiche Materialien mit Eigenschaften ähnlich derer von ABS, PP und PE | Gehäuse Halterungen und Vorrichtungen Verbindungen Verschleißfeste Prototypen |
Kunstharzfamilie Rigid | Angereichertes, starkes und starres Material, das Biegungen widersteht Thermischer und chemischer Widerstand Maßhaltigkeit unter Belastung Ähnliche Steifigkeit wie PEEK oder glas- und fasergefüllte Thermoplaste | Halterungen, Vorrichtungen und Werkzeug Turbinen- und Lüfterflügel Komponenten für Flüssigkeiten- und Luftströme Elektrische Gehäuse und Automobilgehäuse |
Kunstharzfamilie Flexible und Elastic | Flexibilität von Kautschuk, TPU oder Silikon Hält Biegung und Kompression stand Übersteht wiederholte Verformungen ohne Risse | Prototypenentwicklung von Konsumgütern Konforme Elemente von Robotikanwendungen Medizinprodukte und anatomische Modelle Requisiten und Modelle für Spezialeffekte |
Silicone 40A Resin | Das erste erschwingliche 3D-Druckmaterial aus 100 % Silikon Die hervorragenden Materialeigenschaften von Gießsilikon | Funktionale Prototypen, Validierungseinheiten, Kleinserien von Silikonteilen Personalisierte Medizinprodukte Flexible Vorrichtungen, Maskierungshilfsmittel und weiche Formen für Urethan- oder Kunstharzguss |
High Temp Resin | Hohe Temperaturbeständigkeit Hohe Präzision | Heiße Luft-, Gas- und Flüssigkeitsströme Hitzebeständige Halterungen, Gehäuse und Vorrichtungen Gussformen und Einsätze |
Flame Retardant Resin | Flammhemmende, hitzebeständige, starre und kriechfeste Teile für Innenräume und industrielle Umgebungen mit hohen Temperaturen oder Zündquellen | Innenraumteile für Luft- und Raumfahrt sowie Automobilindustrie Schutz- und Innenkomponenten für Verbraucherprodukte oder medizinische Elektronik Maßgefertigte Halterungen, Vorrichtungen und Ersatzteile |
ESD Resin | ESD-ableitfähiges Material zur Verbesserung von Arbeitsabläufen in der Elektronikfertigung | Werkzeug & Vorrichtungen für die Elektronikfertigung Antistatische Prototypen und Endverbrauchsteile Maßgefertigte Behälter für Handhabung und Aufbewahrung von Komponenten |
Polyurethan-Kunstharze | Exzellente langfristige Haltbarkeit UV-, temperatur- und feuchtigkeitsbeständig Flammhemmend, sterilisierbar und chemikalien- sowie abrasionsbeständig | Leistungsstarke Automobil-, Luftfahrt- und Maschinenbauteile Robuste und widerstandsfähige Endverbrauchsteile Belastbare, langlebige funktionale Prototypen |
Alumina 4N Resin | Technische Keramik aus 99,99 % reinem Aluminiumoxid Erstklassige thermische und mechanische Eigenschaften und Leitfähigkeit | Hitzedämmung und elektrische Isolatoren Hochleistungswerkzeuge Chemikalien- und verschleißbeständige Bauteile |
Clear Cast Resin | Rückstandsloses Ausbrennen Geringe Wärmeausdehnung Hohe Genauigkeit | Betriebsinterne Fertigung industrieller Feingussmodelle für Endprodukte aus Metall |
Zahnmedizinische Kunstharze
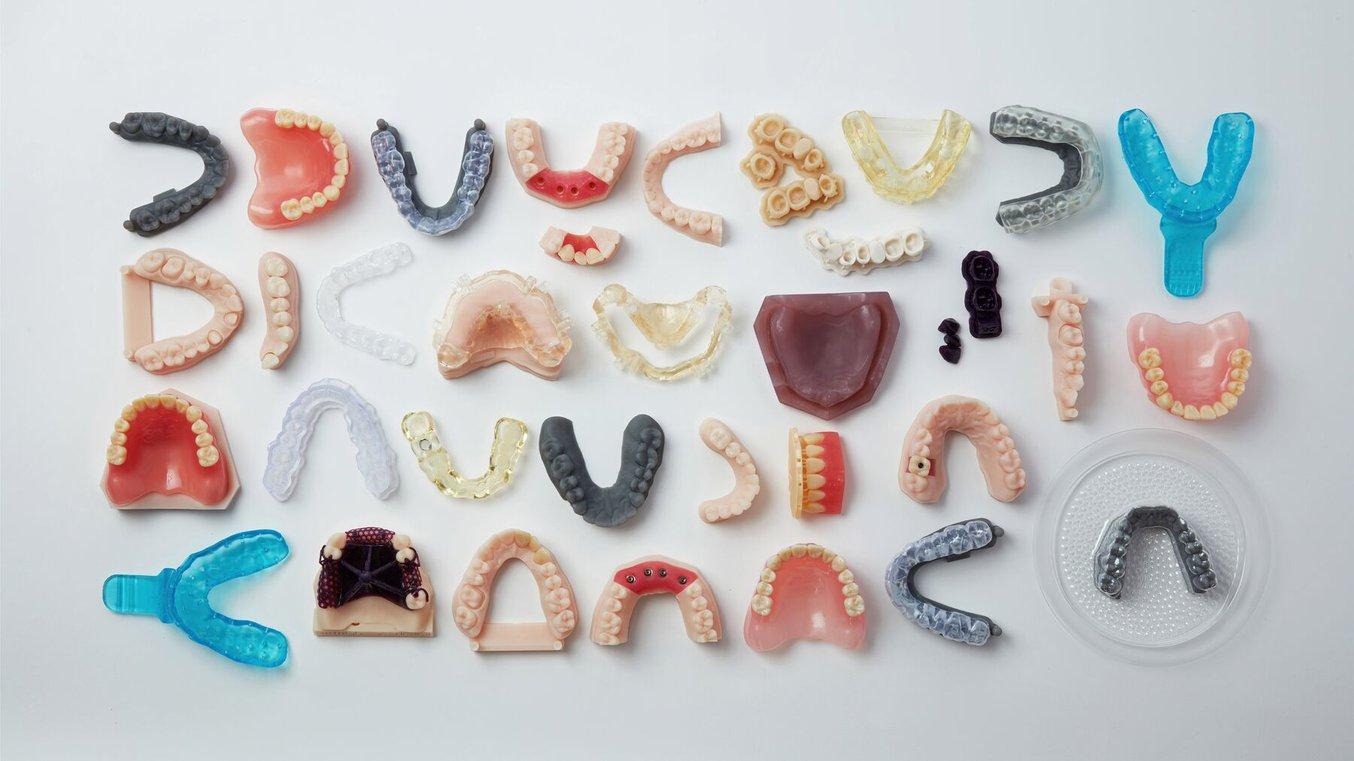
Mit den zahnmedizinischen Kunstharzen von Formlabs fertigen Zahnarztpraxen und Labore schnell transparente Aligner, biokompatible dentale Anwendungen wie Bohrschablonen oder Schienen und sogar fortschrittliche intraorale Anwendungen wie Vollprothesen oder dauerhafte Restaurationen.
Zahnmedizinischen Fachleuten bietet das Formlabs-Ecosystem einen vereinfachten, vollumfassenden Arbeitsprozess, der bei jedem Druck genaue Teile liefert – ganz ohne Anpassungen oder Kalibrierung. Von großen Laboren und Praxen mit verschiedenen dentalen Anwendungen bis hin zu kleineren Geschäften, die auf bestimmte Indikationen spezialisiert sind, bieten der Form 4B und unsere Bibliothek zahnmedizinischer Kunstharze für jeden die passende Lösung.
Material | Beschreibung | Anwendungen |
---|---|---|
Precision Model Resin | Hochgenaues Material zur Fertigung von Zahnersatzmodellen, bei denen die gedruckte Oberfläche zu mehr als 99 % in einem Toleranzbereich von 100 μm zum digitalen Modell liegt | Modelle mit herausnehmbaren Stümpfen Kronen- und Brückenmodelle Implantat-Analog-Modelle Diagnosemodelle |
Fast Model Resin | Formlabs' schnellstes zahnmedizinisches Material, das alle 49 Sekunden ein Dentalmodell druckt | Thermoformmodelle Kieferorthopädische Modelle |
Grey Resin | Bietet ein Gleichgewicht zwischen Schnelligkeit und Genauigkeit sowie exzellente Ästhetik | Diagnosemodelle Modelle zur Passungsprüfung |
Surgical Guide Resin | 3D-Druckmaterial der nächsten Generation für die Herstellung autoklavierbarer und biokompatibler chirurgischer Bohrschablonen für Implantate | Bohrschablonen Pilotbohrschablonen Bemaßungsvorlagen für Vorrichtungen |
Dental LT Clear Resin | Langfristig biokompatibles Material für harte Okklusions- und Knirscherschienen | Harte Okklusionsschienen Harte Knirscherschienen |
Dental LT Comfort Resin | Biokompatibles Material für Langzeitanwendungen, das sich leicht auf eine hohe optische Transparenz polieren lässt | Flexible Okklusionsschienen Flexible Knirscherschienen |
Digitaler Zahnersatz | Zugängliches und erschwingliches digitales Prothesenmaterial für langfristig biokompatible Prothesen der Klasse II | Vollprothesen Wax-ups |
Premium Teeth Resin | Nanokeramik der Klasse II mit verbesserten ästhetischen Merkmalen und überlegenen mechanischen Eigenschaften im Mundraum | Zahnprothesen Wax-ups Vollbogenrestaurationen |
Custom Tray Resin | Ein druckschnelles, biokompatibles Kunstharz für individuelle Abformlöffel | Individuelle Abformlöffel |
Temporary CB Resin | Zahnfarbenes Kunstharz in fünf Farbtönen mit exzellenter marginaler Adaptation, Festigkeit und Ästhetik | Kronen Brücken Inlays Veneers Onlays |
Permanent Crown Resin | Zahnfarbenes, mit Keramik gefülltes Kunstharz für langfristige Restaurationen mit hoher Festigkeit, erhältlich in vier VITA-Classical-Farbtönen | Einzelkronen Inlays Onlays Veneers |
IBT Flex Resin | Ein flexibles, biokompatibles Material für hochpräzise Transferschienen für die indirekte Verklebung und direkte Kompositrestaurationen | Transferschienen für indirekte Verklebung Transferschienen für direkte Kompositrestaurationen |
Soft-Tissue-Resin-Starterpaket | Ein flexibles Material für entnehmbare Weichgewebekomponenten | Weichgewebekomponenten von Implantatmodellen Zahnfleischmasken |
Medizinische Kunstharze
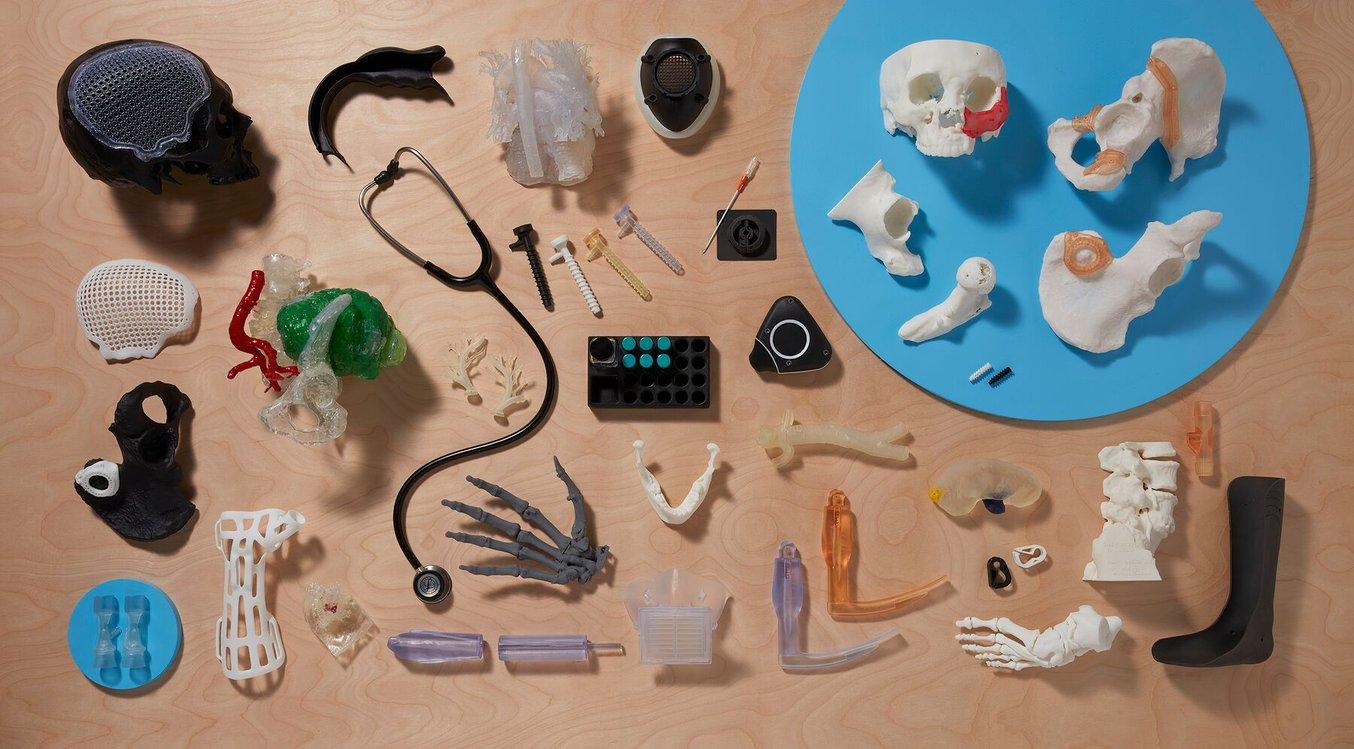
Mit Formlabs' BioMed-Kunstharzen fertigen Gesundheitsfachkräfte präzise, biokompatible und personalisierte Anatomiemodelle, chirurgische Instrumente und Medizinprodukte, die die Patientenversorgung verbessern.
Für das Gesundheitswesen bieten die BioMed-Kunstharze von Formlabs Materialien in medizinischer Qualität für eine breite Palette an Anwendungen, bei denen Leistung und Biokompatibilität entscheidend sind. Die Materialien der BioMed-Familie werden in unserer nach ISO 13485 zertifizierten Einrichtung hergestellt. Sie sind mit den gängigen Desinfektions- und Sterilisierungsmethoden kompatibel.
Material | Beschreibung | Anwendungen |
---|---|---|
BioMed White Resin | Starr und opak weiß. Zugelassen für langzeitigen Hautkontakt (> 30 Tage) und kurzzeitigen Kontakt mit Knochen, Gewebe, Dentin oder Schleimhäuten (< 24 Std.). | Medizinprodukte für die Endverwendung und deren Komponenten, patientenspezifische Modelle und Formen zur Implantatsgrößenbestimmung, Schnitt- und Bohrschablonen, chirurgische Instrumente und Schablonen, biokompatible Formen, Halterungen und Vorrichtungen, Anatomiemodelle, die im OP eingesetzt werden können. |
BioMed Black Resin | Starr und mattschwarz. Zugelassen für langzeitigen Hautkontakt (> 30 Tage) und kurzzeitigen Kontakt mit Schleimhäuten (< 24 Std.). | Medizinprodukte und deren Komponenten, biokompatible Formen, Halterungen und Vorrichtungen, Endverbrauchsteile mit Patientenkontakt, Konsumgüter. |
BioMed Amber Resin | Starr und halbtransparent. Zugelassen für langzeitigen Hautkontakt (> 30 Tage) und kurzzeitigen Kontakt mit Knochen, Gewebe, Dentin oder Schleimhäuten (< 24 Std.). | Medizinprodukte für die Endverwendung, Modelle zur Implantatsgrößenbestimmung, Schnitt- und Bohrschablonen. |
BioMed Clear Resin | Starr und transparent. Zugelassen für langzeitigen Hautkontakt (> 30 Tage), Kontakt mit Atemgaswegen und Schleimhäuten (> 30 Std.) und kurzzeitigen Kontakt mit Knochen, Gewebe oder Dentin (< 24 Std.). | Produkte für die Endverwendung, auch für die Atemgaswege, biokompatible Prototypen, Formen, Halterungen und Vorrichtungen, Modelle zur Visualisierung und Implantatsgrößenbestimmung, Vorrichtungen für Zellkulturen und Bioprozesse. |
BioMed Durable Resin | Schlag-, bruch- und abriebfest. Transparent. Zugelassen für langzeitigen Hautkontakt (> 30 Tage), Schleimhautkontakt (> 30 Std.) und kurzzeitigen Kontakt mit Knochen, Gewebe oder Dentin (< 24 Std.). | Patientenspezifische Instrumente, Einweginstrumente, Produkte und Komponenten für die Endverwendung, die Biokompatibilität und Schlagfestigkeit erfordern. |
BioMed Elastic 50A Resin | Weichsilikonähnlich. Lichtdurchlässig. Zugelassen für langzeitigen Hautkontakt (> 30 Tage) und kurzzeitigen Kontakt mit Schleimhäuten (< 24 Std.). | Komfortable Medizinprodukte für langzeitigen Hautkontakt, biokompatible Weichgewebemodelle, die im OP als Referenz dienen können. |
BioMed Flex 80A Resin | Hartgummiähnlich. Lichtdurchlässig. Zugelassen für langzeitigen Hautkontakt (> 30 Tage) und kurzzeitigen Kontakt mit Schleimhäuten (< 24 Std.). | Flexible biokompatible Medizinprodukte und deren Komponenten, Medizinprodukte für kurzzeitigen Schleimhautkontakt, feste Gewebemodelle zur Nutzung im OP. |
Juwelierkunstharze
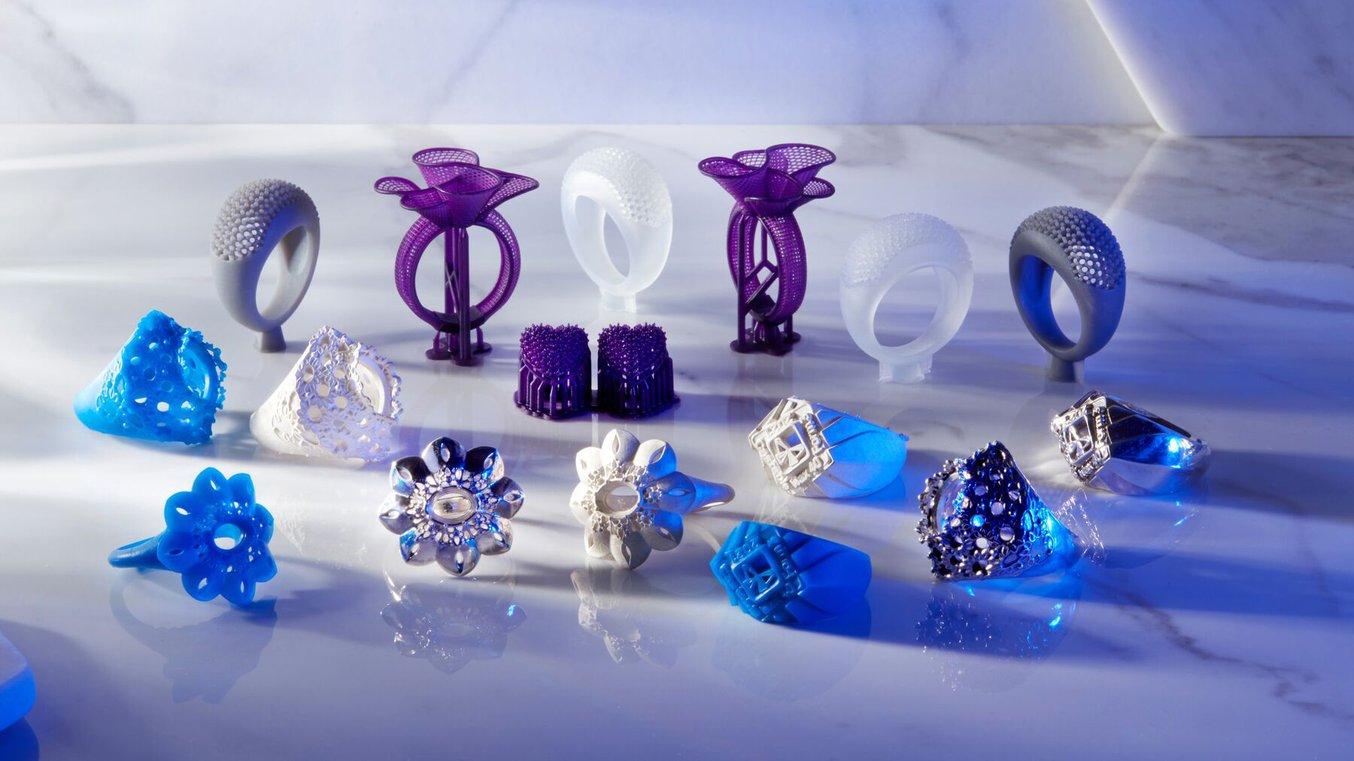
Juwelierkunstharze dienen der Prototypenfertigung und Produktion von maßgefertigtem Schmuck.
Die Juwelierkunstharze von Formlabs reproduzieren zuverlässig Schmuck mit genauen Fassungen, filigranen Krappen, glatten Schenkeln und feinen Oberflächendetails. Sie bieten Einzelhändlern und Designern die Möglichkeit, maßgefertigten Schmuck herzustellen. Gleichzeitig unterstützen sie große Gießereien, die in großem Maßstab produzieren, indem sie Anprobemodelle für Kunden, fertigen maßgefertigten Schmuck oder Urmodelle für wiederverwendbare Schmuckformen bereitstellen.
Material | Beschreibung | Anwendungen |
---|---|---|
Gießbare Kunstharze | Materialien für den Feinguss Für benutzerfreundlichen Guss mit filigranen Details und starke Formbeständigkeit | Personalisierter Schmuck |
High Temp Resin | Ein festes und temperaturbeständiges Material für Formenbau mit vulkanisiertem Kautschuk | Urmodelle für wiederverwendbare Formen |
Grey Resin | Ein Allzweckmaterial für hochdetaillierte Prototypen und individuelle Passstücke | Schmuckprototypen Anprobemodelle |
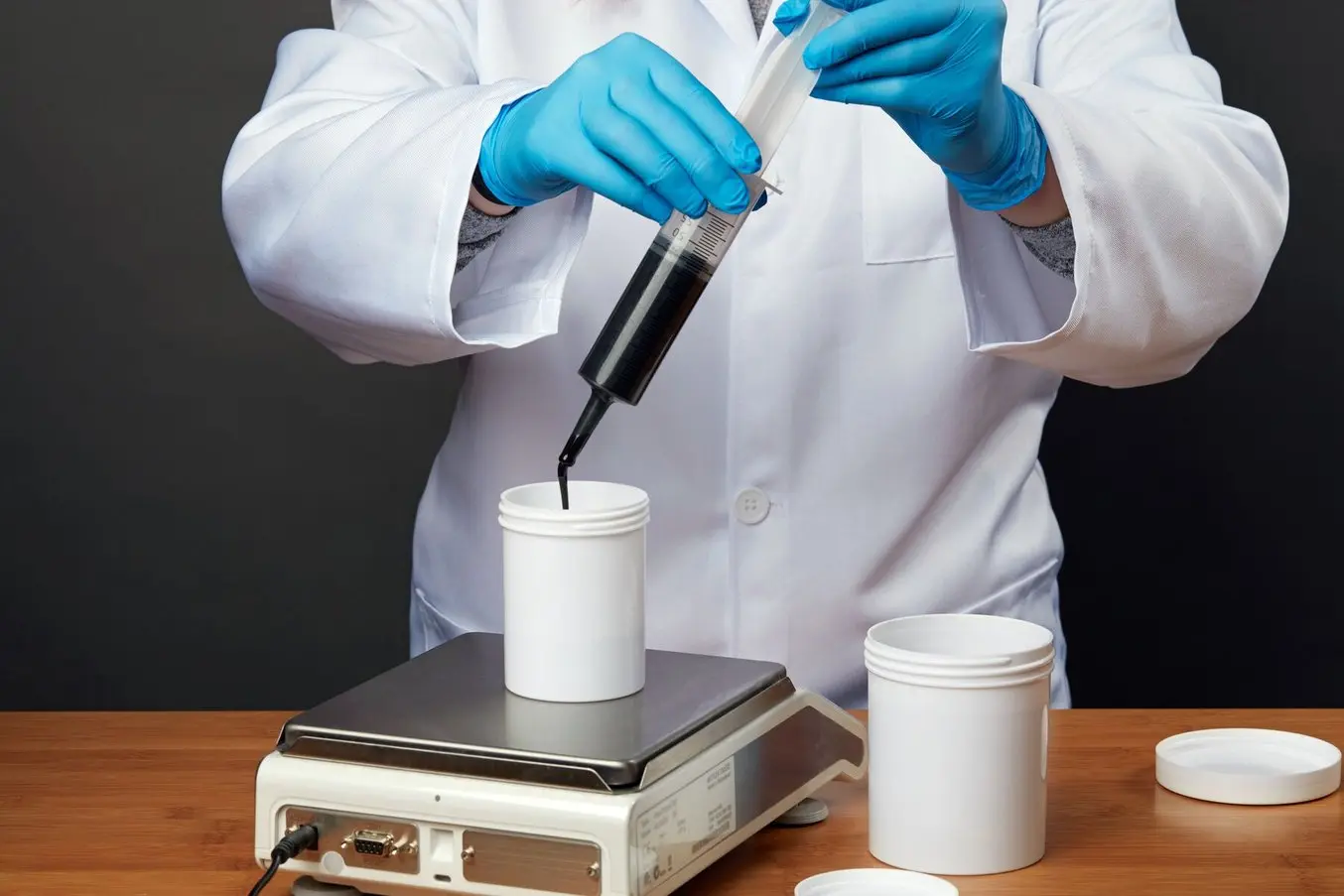
Formlabs als offene Plattform
Maximieren Sie das Potenzial Ihres 3D-Druckers mit Formlabs Developer Platform. Drucken Sie auf Formlabs-3D-Druckern mit jedem bei 405 nm härtenden Photopolymerharz bzw. jedem bei 1064 nm sinterbaren Pulver, legen Sie Ihre Druckeinstellungen individuell fest oder entwickeln Sie Softwareintegrationen.
Betriebsinterner SLA-3D-Druck
Verschiedene Faktoren haben den Anstieg der Zahl von Unternehmen beeinflusst, die auf betriebsinternen SLA-3D-Druck setzen. Hochwertiger SLA-3D-Druck ist erschwinglicher geworden, die Drucker selbst sind zuverlässiger und einfacher zu bedienen, und da die Materialien fortschrittlicher geworden sind, eröffnen sich neue Anwendungen. Ingenieure, Hersteller, Gesundheitspersonal und Unternehmen aller Art erkennen den Nutzen des betriebsinternen Kunstharz-3D-Drucks.
Obwohl die Vorteile dieser Technologie, wenn sie direkt zur Verfügung steht, in alle Bereiche einer Organisation reichen können, liegen die Hauptvorteile darin, dass der interne SLA-3D-Druck die Kosten senkt und die internen sowie kundenbezogenen Vorlaufzeiten verkürzt. Des Weiteren unterstützt er dabei, die Lieferketten von Unternehmen zu kontrollieren und abzusichern. Außerdem handelt es sich um eine skalierbare Technologie, die mit Ihrem Unternehmen mitwachsen kann.
Kosten senken und Durchlaufzeiten verringern
Mit SLA-Druck eliminieren Unternehmen die hohen Kosten und langen Vorlaufzeiten, die mit dem Outsourcing oder komplizierteren Alternativen wie der Zerspanung einhergehen. 3D-Druck braucht keine teure Werkzeugausstattung und Einrichtung. Es können dieselben Geräte verwendet werden, um schnell verschiedene Geometrien zu produzieren.
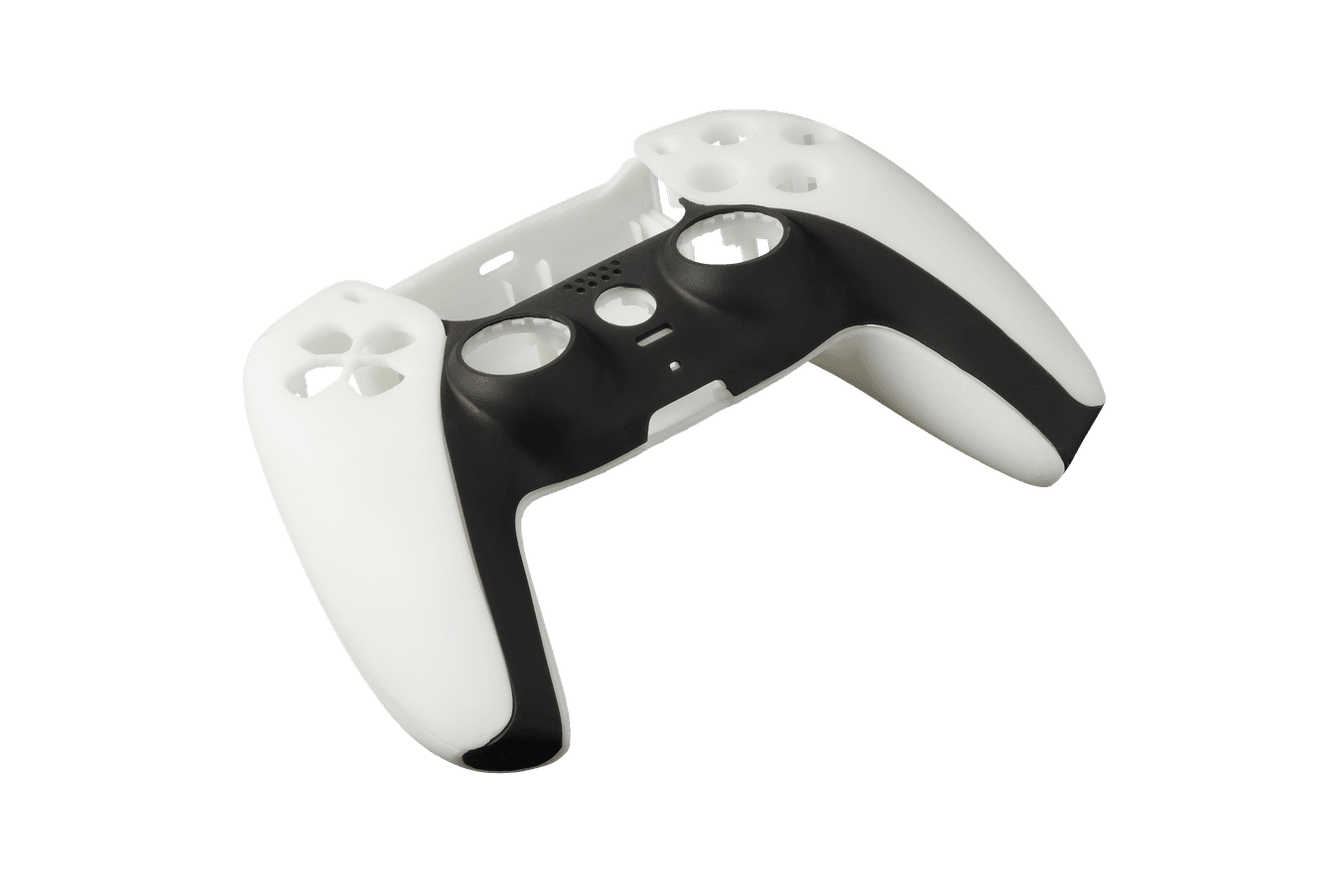
Eine dreiteilige Prototypenbaugruppe für einen Gaming-Controller, gedruckt mit zwei verschiedenen Materialien für kontrastierende Farben
Rapid Prototyping: Videospiel-Controller von Battle Beaver Customs
Dank der schnellen Druckgeschwindigkeit des Form 4 kann Battle Beaver Customs noch am selben Tag Prototypen erstellen, wodurch das Unternehmen neue Produkte schneller auf den Markt bringt und seine Konkurrenten überholt.
Baugruppe des Prototyps | Outsourcing | Betriebsinterner 3D-Druck |
---|---|---|
Ausrüstung | - | Form 4 White Resin und Black Resin |
Durchlaufzeit | 7 Tage | 5 Stunden |
Kosten | 250 € | 15 € |
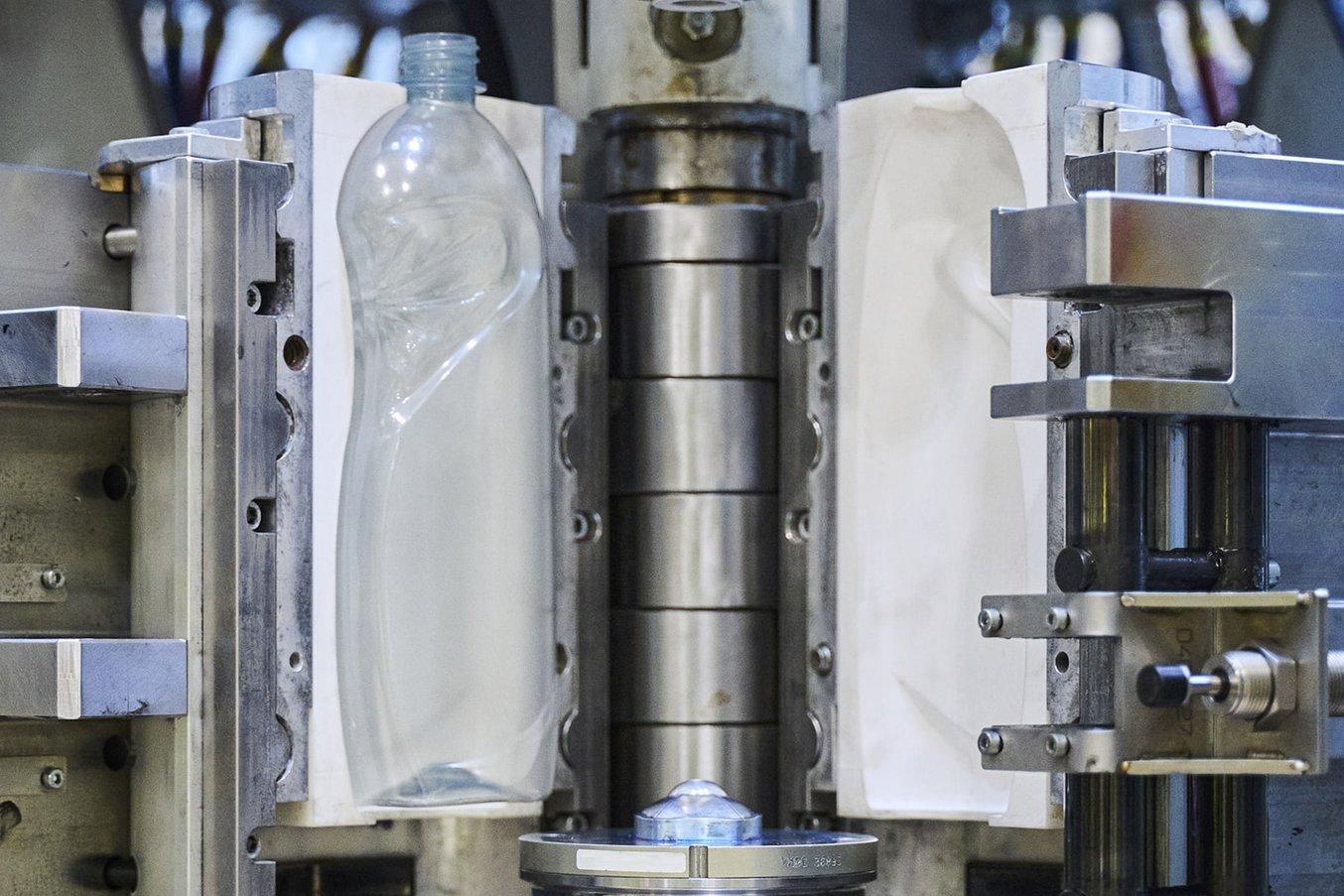
Für eine 750-ml-Flasche für Unilever Slice wurde eine Form aus Rigid 10K Resin 3D-gedruckt und in der Formenhalterung der Maschine installiert. Da das Team dasselbe Prozessfenster verwenden kann wie mit standardmäßigen Pilotformen, lässt sich der endgültige Prozess zuverlässig prüfen.
Rapid Tooling: Blasformung einer Flasche von Unilever
Unilever und Serioplast fertigen mit dem Benchtop-3D-Drucker Form 3L und Rigid 10K Resin schnell und effizient Formen für das Streckblasen (SBM), die den Druck herkömmlicher industrieller SBM-Maschinen bewältigen.
Produktion von 200 Teilen | Zerspante Metallform | 3D-gedruckte Form |
---|---|---|
Ausrüstung | Betriebsinterne CNC-Maschine oder Outsourcing | Form 3L Rigid 10K Resin |
Durchlaufzeit Pilottest | 6–8 Wochen | 2 Wochen |
Kosten des Werkzeugbaus | 2500–10 000 € | 500–1000 € |
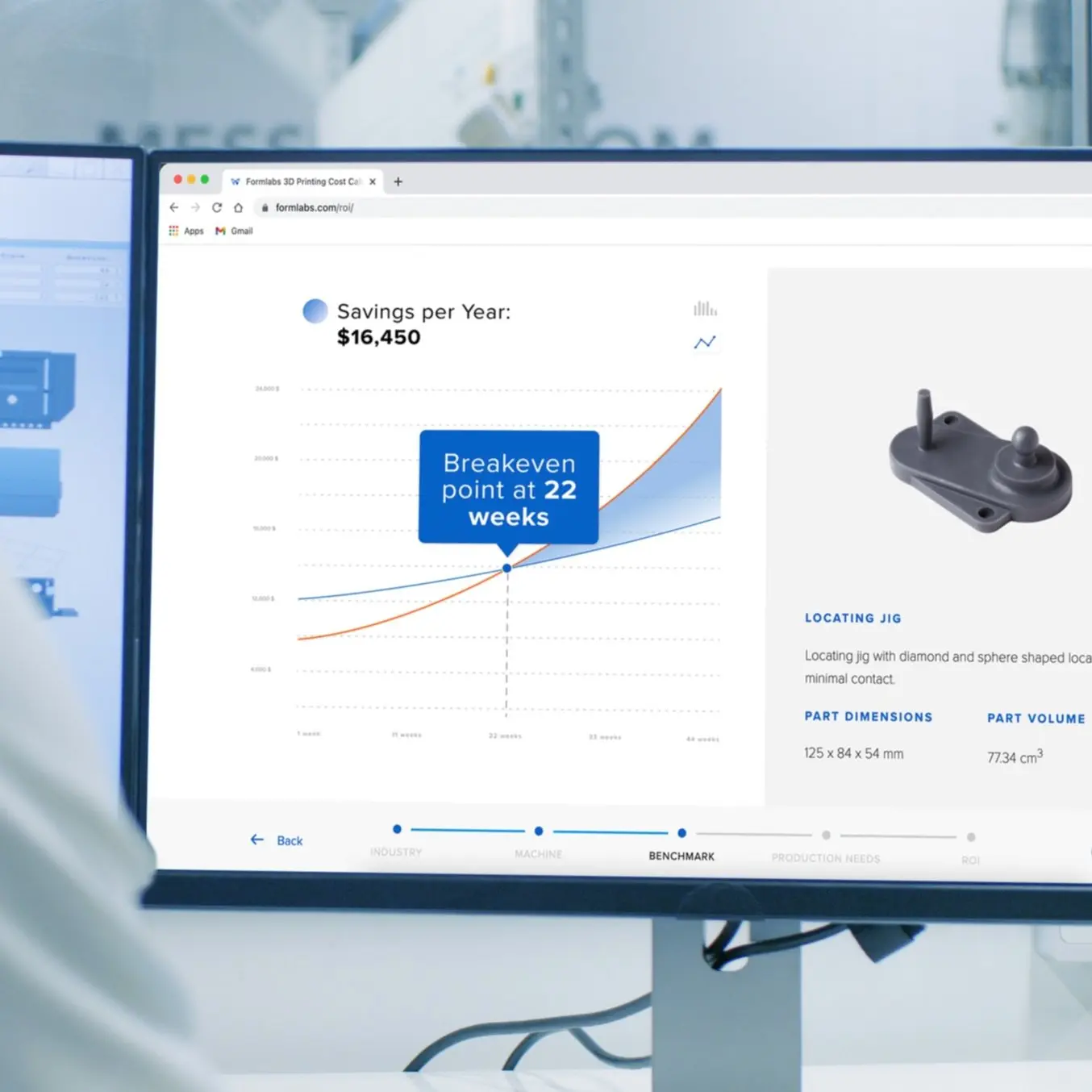
Berechnen Sie Ihre Zeit- und Kostenersparnis
Nutzen Sie unser interaktives ROI-Tool zur Berechnung Ihrer Zeit- und Kostenersparnis beim 3D-Druck mit einem Formlabs-Drucker.
Kontrolle über die Lieferkette
Betriebsinterner 3D-Druck sieht je nach Abteilung anders aus. Viele große Unternehmen wie Microsoft oder Rivian entscheiden sich für interne Dienstleistungsbüros, in denen Ingenieurteams, Designabteilungen und Fertigungsteams Teile aus einem zentralen Labor anfordern. Andere Unternehmen, insbesondere solche, die sich auf Design und Iteration konzentrieren und über hohe CAD-Expertise in ihrer Belegschaft verfügen, bevorzugen einen dezentralen Ansatz mit einem Drucker auf jedem Schreibtisch des Designteams. Zugängliche, erschwingliche Desktop-Geräte wie der Form 4 machen solche Arbeitsabläufe möglich und bieten agile Lösungen für eine sich verändernde Belegschaft und Büroumgebung.
Ob zentralisiert oder dezentralisiert, der betriebsinterne 3D-Druck gibt den Mitarbeitenden größere Kontrolle über ihre Arbeitsabläufe und reduziert Kosten und Unsicherheiten für das gesamte Unternehmen.
Einfache Skalierung mit steigendem Bedarf
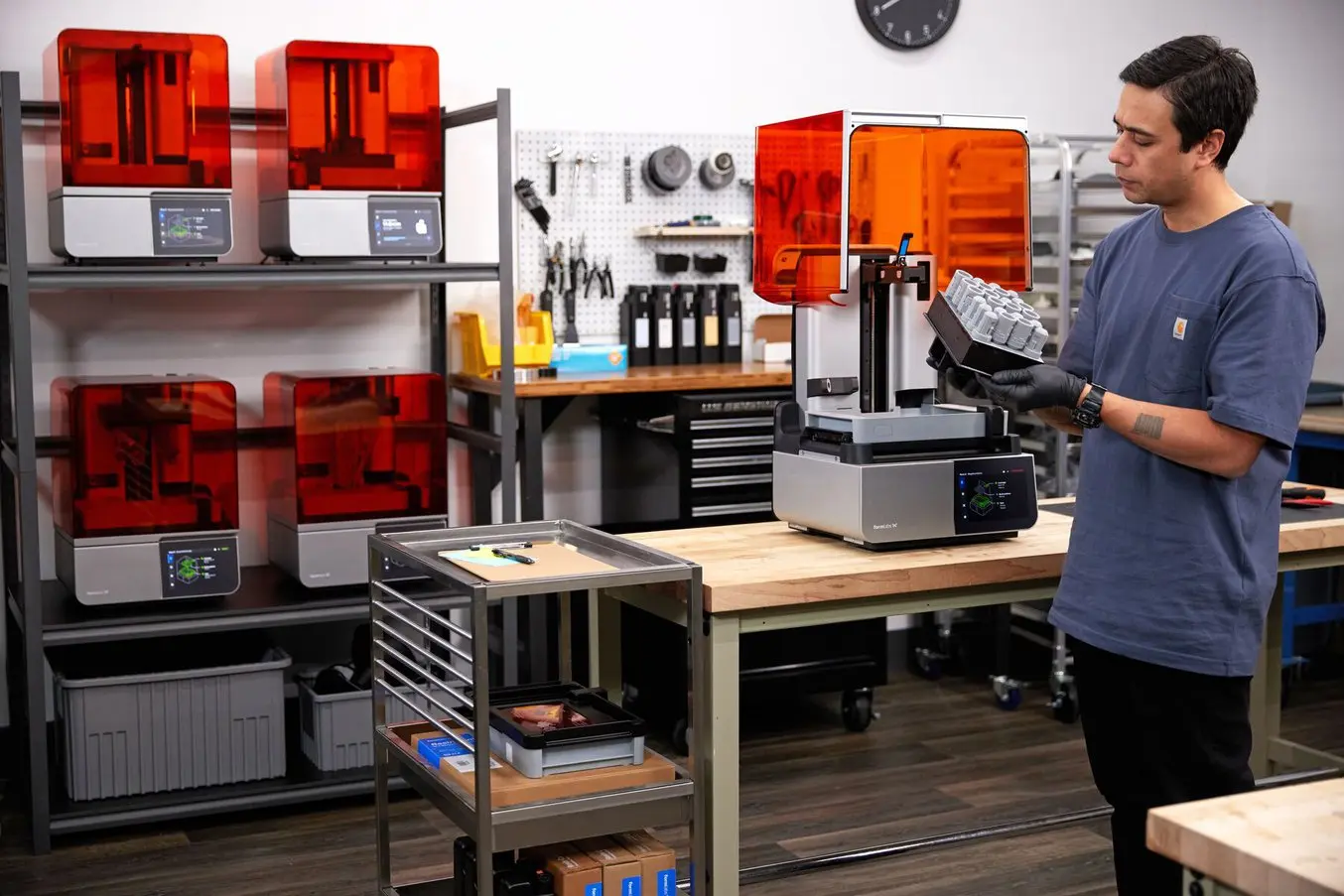
Desktop-3D-Drucker wie der Form 4 sind Plug&Play-Geräte, die jeder innerhalb von 15 Minuten erlernen kann.
Abhängig von der Anzahl der Teile und des Druckvolumens kann sich die Investition in einen kleinformatigen 3D-Drucker schon innerhalb von Monaten amortisieren. Mit solch kleinformatigen Geräten zahlen Sie nur für die Kapazität, die Ihr Unternehmen benötigt. Gleichzeitig lässt sich die Produktion durch zusätzliche Drucker leicht skalieren, wenn die Nachfrage wächst. Der Einsatz mehrerer 3D-Drucker bietet auch die Flexibilität, Teile aus verschiedenen Materialien zu drucken.
Um die Verwaltung mehrerer Kunstharz-3D-Drucker zu erleichtern, haben Sie bei Formlabs Zugriff auf zwei Softwareplattformen. Dashboard ist eine kostenlose Softwareplattform, über die Sie Ihre Drucker überwachen und die Arbeit optimieren. Fleet Control hingegen bietet erweiterte Funktionen und fortschrittliche Verwaltungstools, die mittels Automatisierung Druckaufträge automatisch zuweisen und den effizienten Umgang mit mehreren Druckern erleichtern.
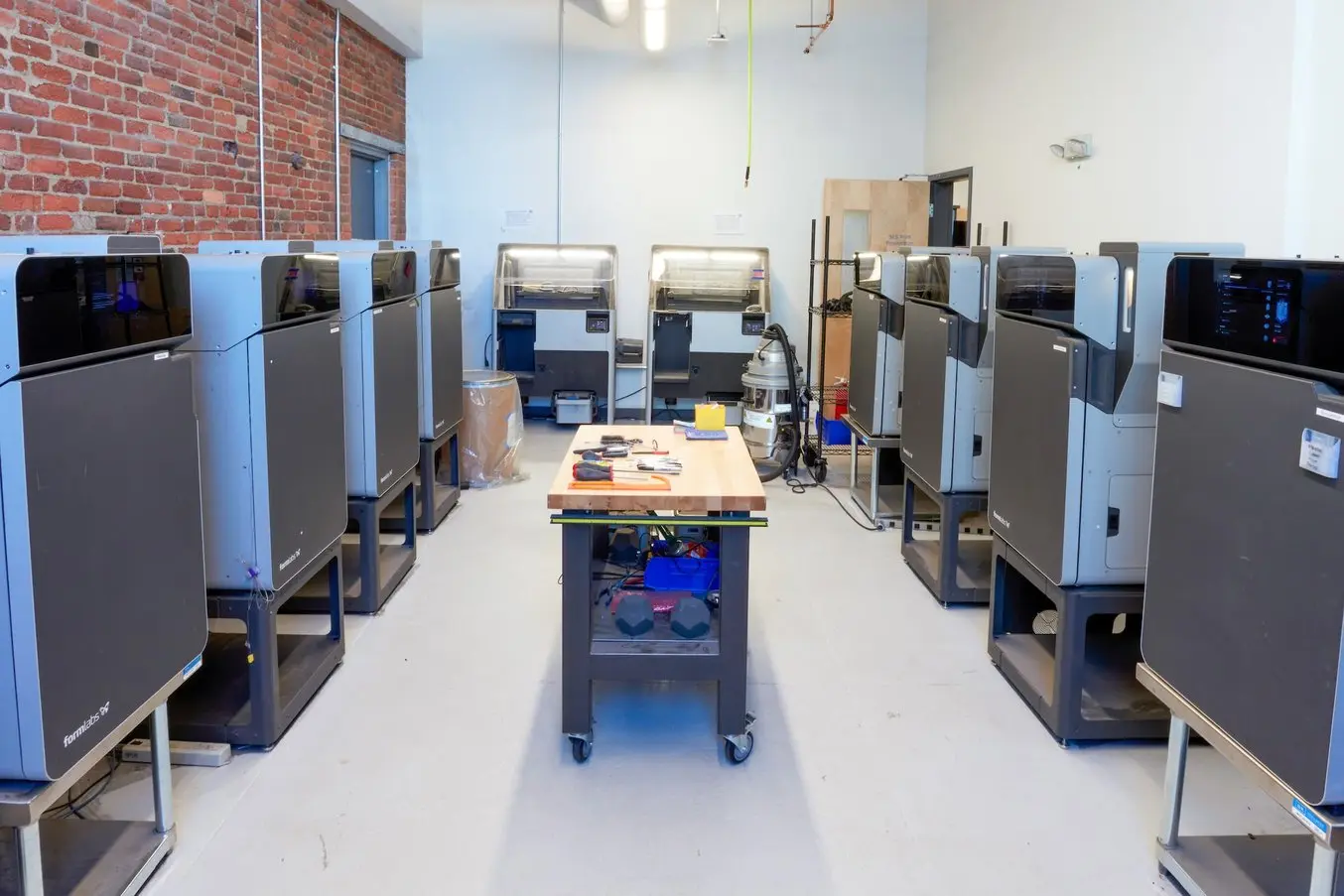
Die Verwaltung von 3D-Druckerflotten
Die Verwaltung mehrerer SLA- und SLS-3D-Drucker muss nicht zwingend kompliziert sein, jedes Unternehmen kann in nur ein oder zwei Tagen eine ganze Flotte von SLA- und SLS-Druckern in Betrieb nehmen. In diesem Leitfaden stellen wir vier verschiedene Fertigungsszenarien mit mehreren Druckern vor, um Ihnen bei der Zusammenstellung eines effizienten Prozesses für jegliches Bauteil oder Produktionsvolumen zu helfen.
Einstieg in den betriebsinternen SLA-3D-Druck
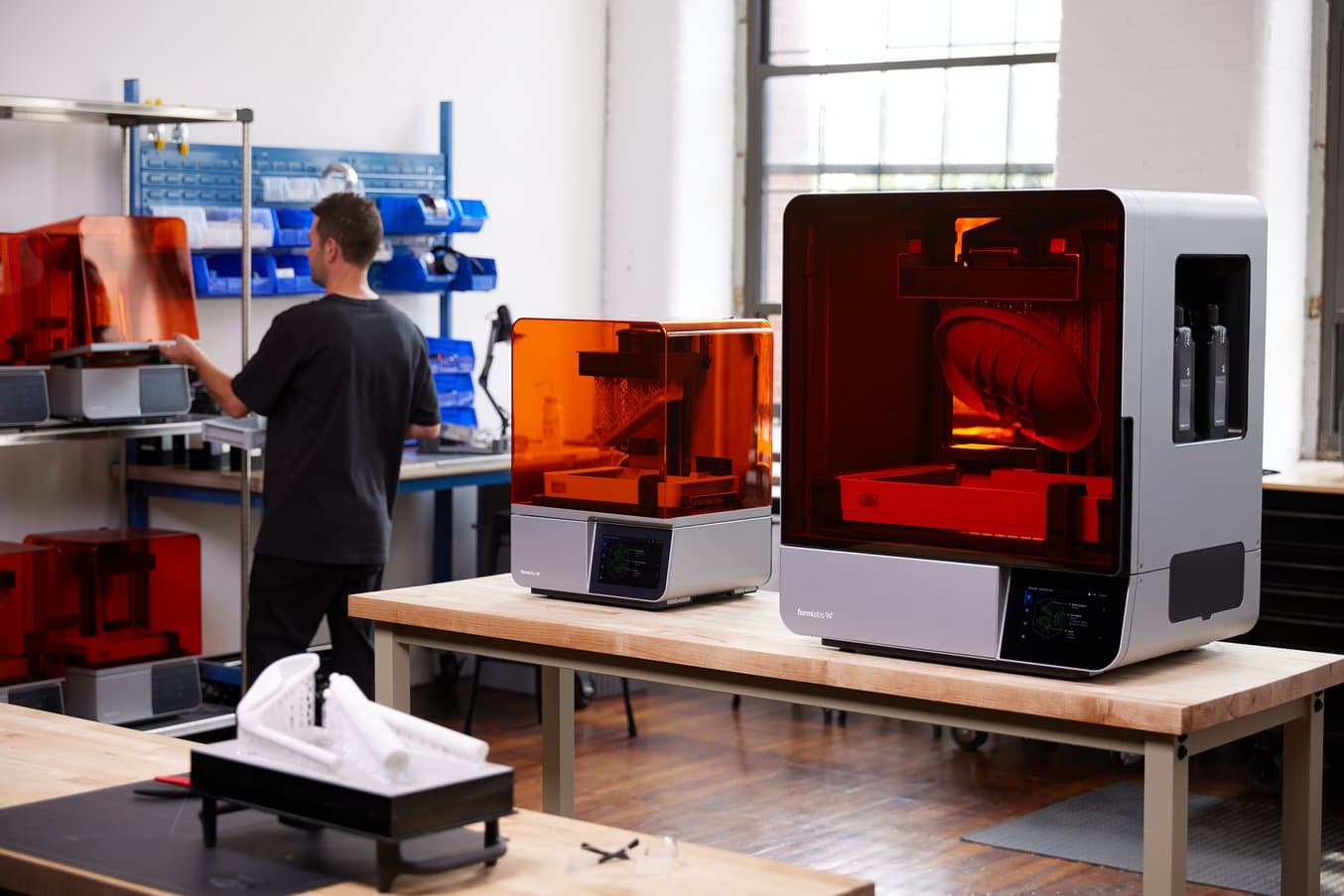
Form 4 und Form 4L sind rekordschnelle MSLA-3D-Drucker, der eine führende Materialauswahl und ein zuverlässiges, intuitives und präzises Drucksystem vereinen.
Formlabs bietet schnelle und kostengünstige Desktop- und Benchtop-SLA-3D-Drucker an, die hochwertige Teile mit einer Vielzahl von Materialeigenschaften fertigen. Das Formlabs-Ecosystem für den Kunstharz-3D-Druck ist auf Benutzerfreundlichkeit und möglichst wenige Berührungspunkte ausgelegt.
Um noch mehr über den SLA-Druck zu erfahren, fühlen Sie die Ergebnisse doch einmal selbst: Fordern Sie einen kostenlosen 3D-Probedruck an. Wählen Sie ein beliebiges Material aus und wir senden Ihnen einen Probedruck direkt nach Hause.