Wie das GreenTeam Stuttgart mit 3D-gedruckten SLS-Bauteilen an die Spitze der Weltrangliste kletterte
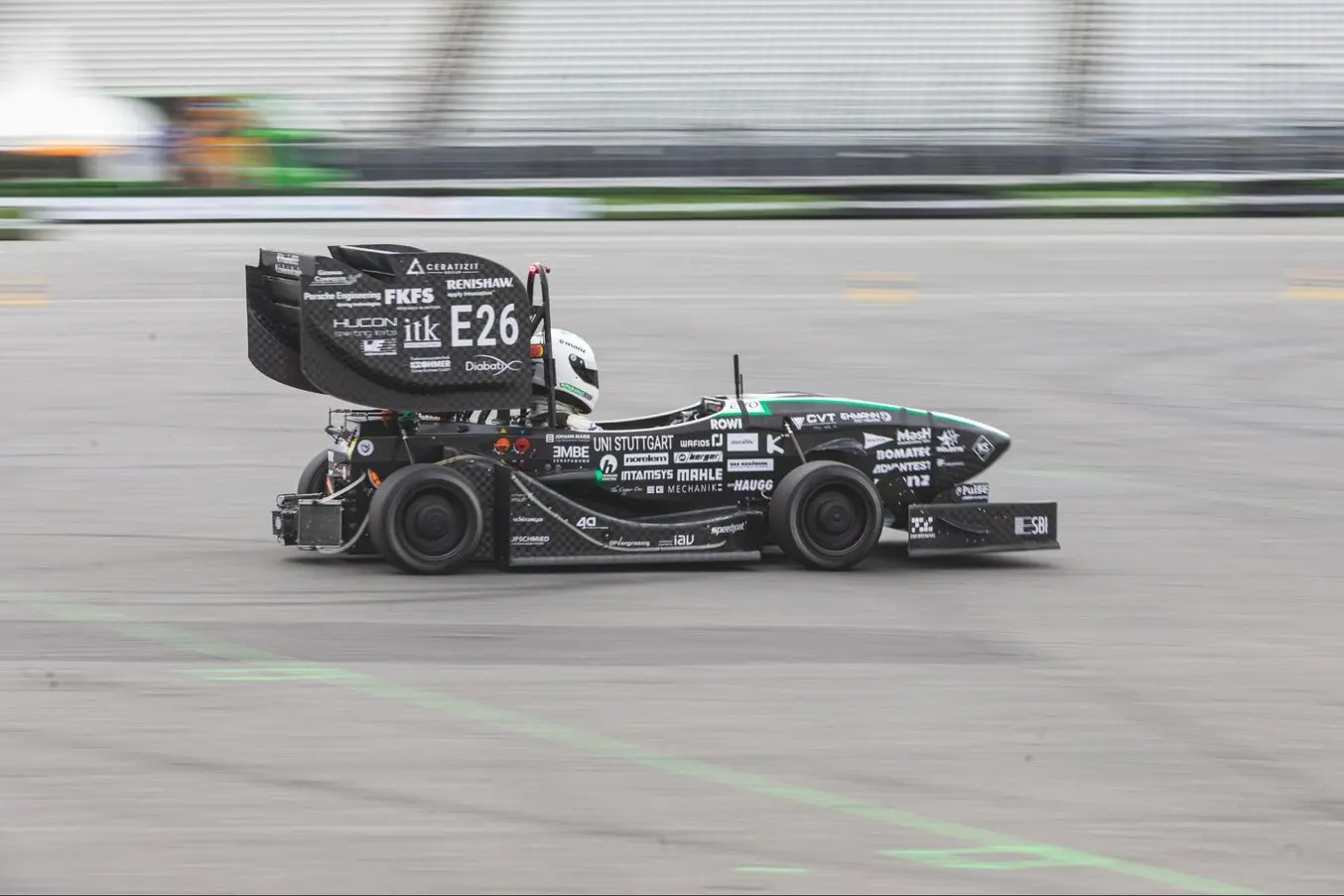
Bei dem Bau eines Rennwagens geht es immer um maximale Gewichtseinsparung, Beschleunigung und Flexibilität. Im Rahmen des Motorsportwettbewerbs Formula Student versucht das GreenTeam der Universität Stuttgart jede Saison genau diese Bereiche bei ihrem Prototypenfahrzeug bis hin zur Perfektion umzusetzen, um im Wettbewerb gegenüber anderen studentischen Teams aus aller Welt herauszustechen.
In der Konstruktion ihres Fahrzeugs verwendet das Team die SLS 3D-Drucktechnologie für verschiedene Bauteile und Verbindungselemente.
Wie Formlabs das GreenTeam in ihrem Vorhaben unterstützt und welche Vorteile der 3D-Druck im Wettbewerb und während der Entwicklungsphase für die Studierenden hat, haben wir im Interview mit Fahrzeug-, und Motorentechnik-Student und GreenTeam-Leiter Oliver Spengel besprochen.
An die Spitze der Weltrangliste mit Elektropower
Die Formula Student ist ein internationaler studentischer Motorsport- und Konstruktionswettbewerb, in dem Teams aus der ganzen Welt mit selbst konstruierten und -gefertigten Formelrennwagen in verschiedenen Klassen gegeneinander antreten.
Bei der Formula Student Germany (FSG) im Sommer 2021 stellte das GreenTeam der Universität Stuttgart einen neuen Punkterekord in der elektrischen Klasse mit insgesamt 936 von 1.000 Punkten auf. Durch diesen und weiteren Erfolgen bei Formula Student Wettbewerben in ganz Europa steht das renommierte Team in der Klasse Formula Student Electric derzeit auf Platz 1 der Weltrangliste.
“Im Prinzip deckt sich der Ablauf mit dem im realen Motorsport, nur natürlich runtergebrochen auf einen Umfang den Studierende bewältigen können. Man hat ein Jahr Zeit ein Prototypenfahrzeug zu entwickeln und tritt damit dann gegen Formula Student Teams aus der ganzen Welt an”, erklärt Spengel.
Die Bewertung erfolgt durch eine Fachjury in sowohl statischen als auch dynamischen Disziplinen und lässt damit kein Detail der studentischen Arbeit außer Acht. Um die Höchstpunktzahl von 1.000 Punkten zu erreichen, muss in den einzelnen Bewertungsfaktoren wie beispielsweise Beschleunigung, Konstruktion und Finanzierung des Wagens, alles perfekt sitzen.
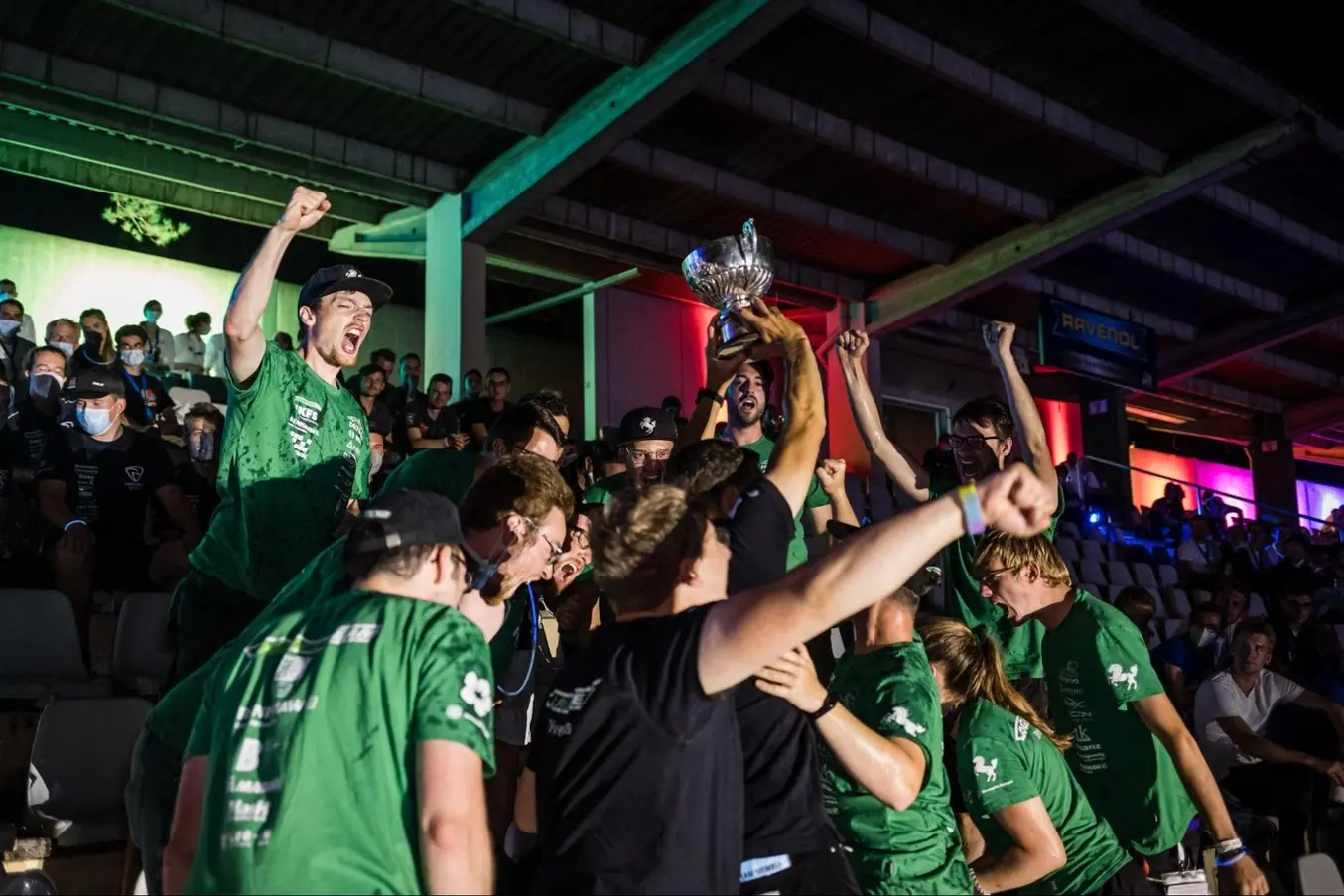
Mit 3D-Druck federleichte und komplexe Komponenten bauen
Seit mehreren Jahren wendet das GreenTeam schon 3D-gedruckte Teile in der Fertigung ihrer Fahrzeuge an. Hierdurch können sie mehrere grundlegende Herausforderungen wie Zeitdruck, knappe finanzielle Ressourcen und Gewichtseinsparung an dem Rennwagen gleichzeitig bewältigen.
Das Team nutzt 3D-Druck mit selektivem Lasersintern (SLS) für Komponenten im Kühlungssystem und in Antriebseinheiten sowie als Verbindungselemente am Wagen.
“Zum größten Teil kommen diese Teile im Kühlsystem zum Einsatz, weil man dort sehr komplexe Kleinteile braucht, die mit anderen Fertigungsverfahren so nicht hergestellt werden können oder nur mit sehr großem Aufwand und hohem Gewicht”, erläutert Spengel.
“Das ist auch generell der große Vorteil am 3D-Druck. Man hat sehr viel Freiheit in der Gestaltung, man kann sehr gewichtssparend bauen und die Fertigung ist extrem zeitsparend und auch kostensparend.”
Oliver Spengel
Die Komplexität der Teile wird vor allem bei Komponenten für die Luftkühlung deutlich.
Um einen möglichst effizienten Luftstrom zu garantieren, werden hier durchdachte Leitelemente eingesetzt, welche die Luft schnellstmöglich zu internen Ventilatoren lenken oder aus den Komponenten herausführen sollen.
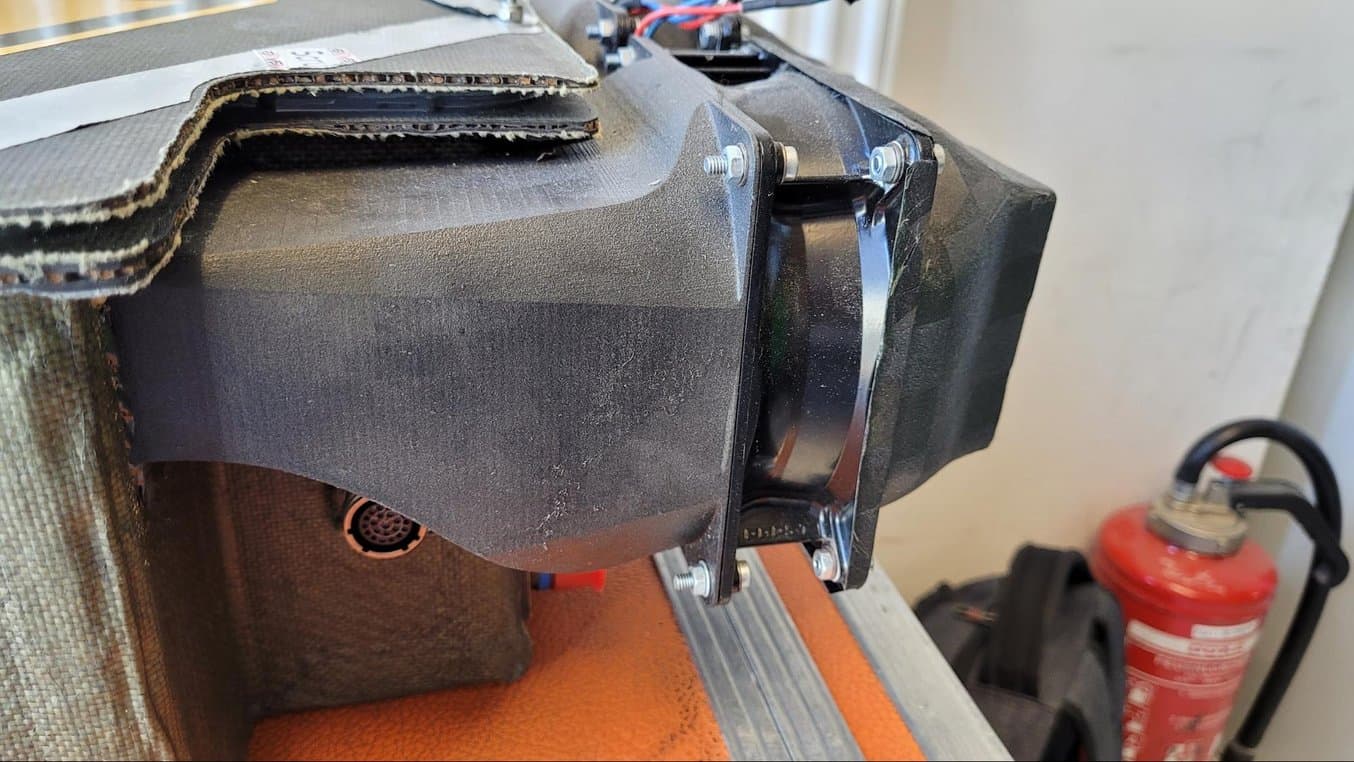
An den HV Akkumulator gebaute Airducts aus Nylon 12 zur Luftkühlung der Einheit (hinteres Teil der angebauten Komponente)
Eine effiziente Luftkühlung des HV-Akkus, der den Antrieb des GreenTeam Elektrofahrzeugs darstellt, ist entscheidend um einen möglichen Leistungsverlust des Antriebes entgegenzuwirken.
“Es geht immer darum möglichst wenig Leistungsschwund zu haben, denn Verlust bedeutet für uns immer, dass wir mehr Energie benötigen. Das heißt im Umkehrschluss, dass wir einen größeren Akku brauchen, wodurch das Auto wiederum schwerer und langsamer wird”, sagt Spengel.
Neben der Effizienz der Kleinteile wird durch das bei SLS 3D-Druck verwendete Nylonmaterial zudem sichergestellt, dass die Teile keinen erheblichen Einfluss auf das Gesamtgewicht des Fahrzeugs haben.
“Bei der Herstellung von derart komplexen Teilen, ist der 3D-Druck für uns die einzige Fertigungsmethode, die es uns ermöglicht das Fahrzeug in dieser kurzen Zeit und entsprechend unserer Qualitätsvorstellungen zu bauen.”
Oliver Spengel
Vorteile gegenüber herkömmlichen Methoden
Durch die jahrelange Erfahrung des GreenTeams im Automobilsport, kann Oliver Spengel als Teamleiter heute Vergleiche zwischen der Herstellung von Einzelteilen mit SLS 3D-Druck und herkömmlichen Methoden ziehen.
Wie schon angeführt liegen die Vorteile des SLS 3D-Drucks vor allem bei der Gewichts-, Zeit- und Kostenersparnis. Beispielhaft für diese drei Bereiche ist hier der direkte Vergleich von herkömmlichen Fertigungsmethoden zu 3D-Drucktechnologien bei Kleinteilen wie den Halterungen für die in den Seitenflügeln sitzenden Kühlungspumpen.
“Die Halterung für unsere Kühlungspumpe würde man ansonsten aus Blech konstruieren, was an sich schon sehr schwer ist. Man müsste das Blech lasern und anschließend biegen lassen. Das heißt, man benötigt hierfür bereits zwei Fertigungspartner. Danach müsste es zusätzlich noch nachbearbeitet und gegebenenfalls beschichten werden”, erklärt Spengel.
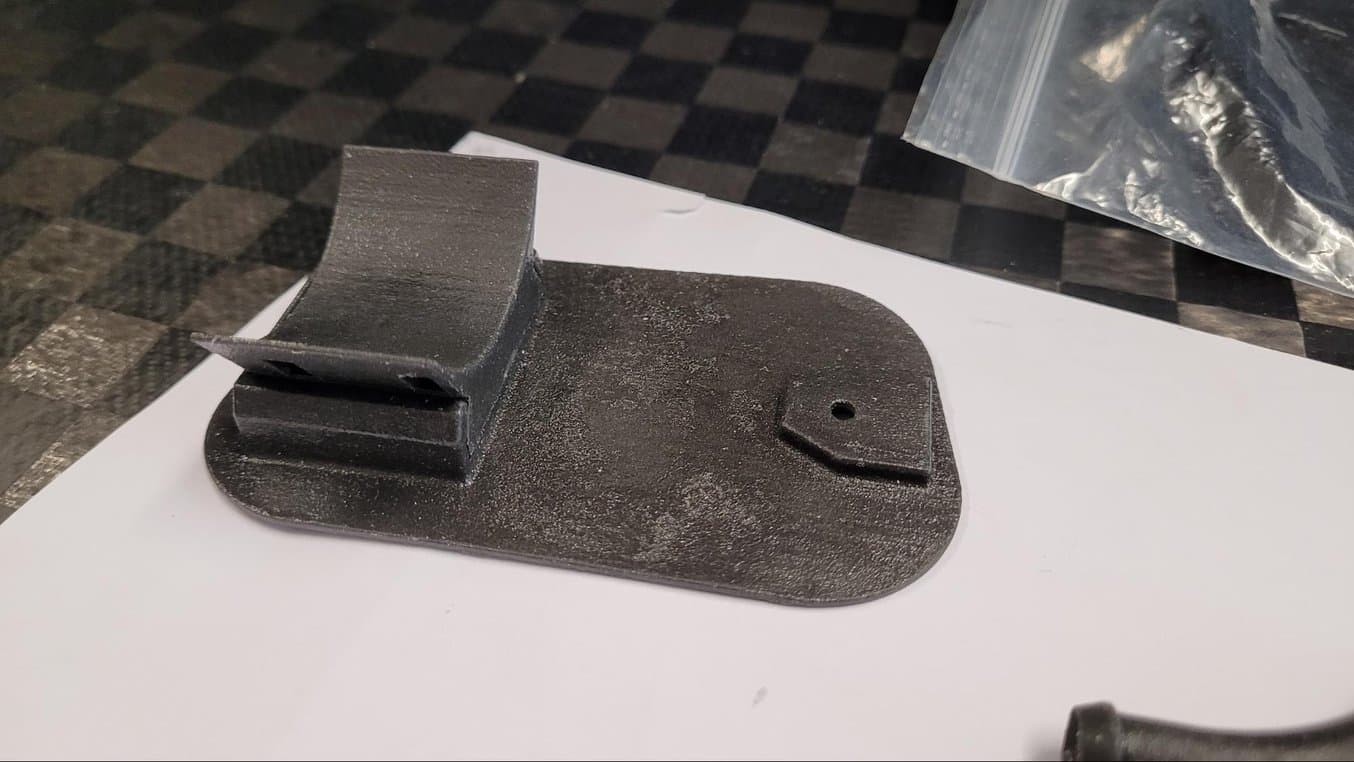
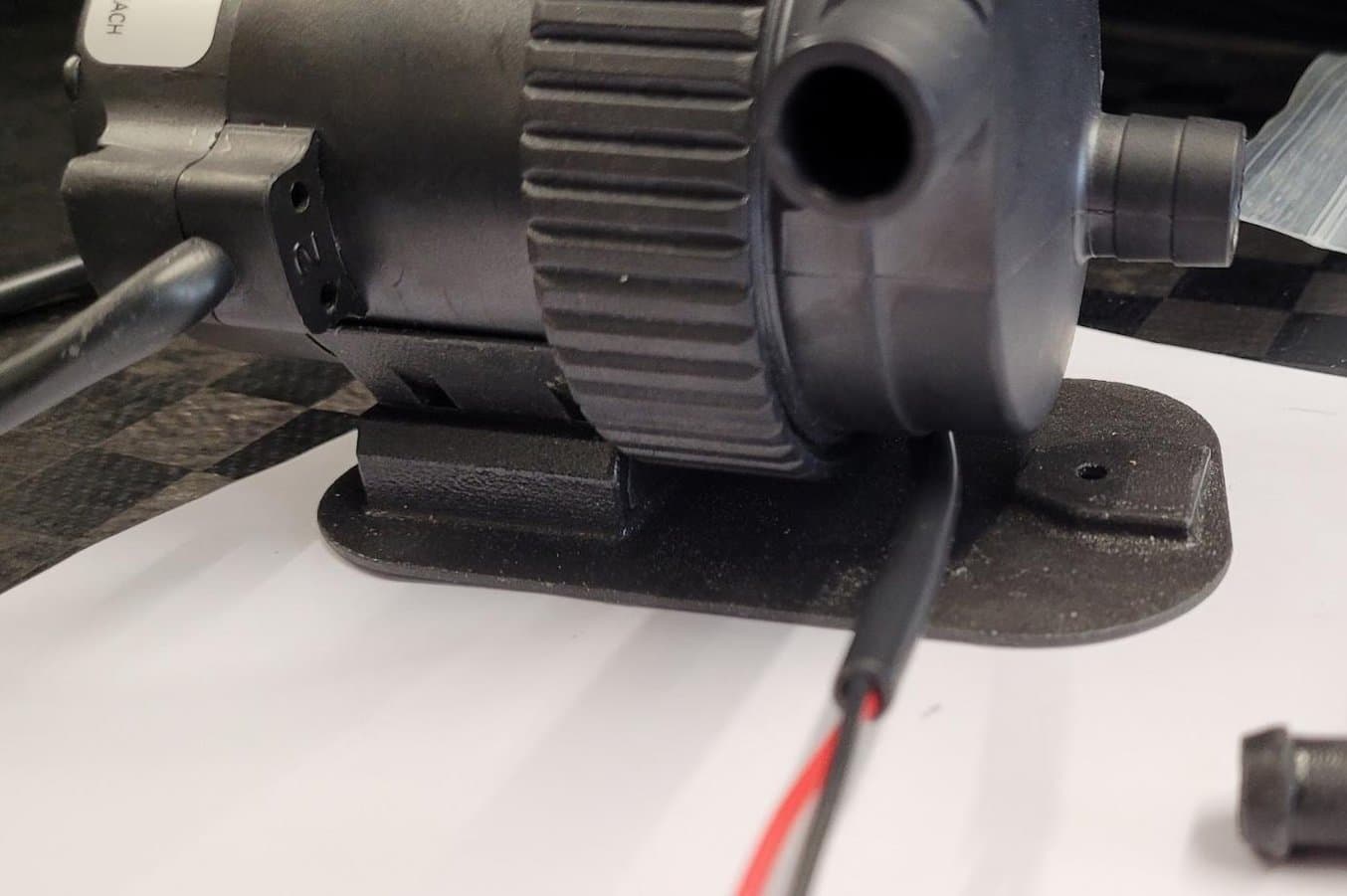
Kleinteilige Halterung für die Kühlungspumpe im Seitenflügel des Fahrzeugs, gedruckt auf dem Fuse 1
“Da ist SLS 3D-Druck natürlich deutlich einfacher und wir sind relativ frei in der Konstruktion. Man gibt die Dateien nur an den Drucker weiter, das Teil wird gedruckt, man nimmt es raus und es ist fertig zum Einsatz im Fahrzeug.”
Oliver Spengel
Vorteile des Nylon Materials
Außerdem ist die Form- und Chemikalienbeständigkeit der Nylon Komponenten essentiell, die auch bei teils extremen Temperaturunterschieden im Betrieb des Rennwagens bestehen bleiben muss.
“Im Betireb erreicht das Wasser unserer Wasserkühlung Temperaturen um die 60 bis 80 Grad Celsius. Bei derartigen Temperaturschwankungen neigen Metalle zu Korrosion. Diese Korrosionsrückstände können empfindliche Bauteile, wie die Wasserpumpen beschädigen. Mit SLS-gedruckten Kunststoffteilen können wir genau das an vielen Stellen vermeiden”, sagt Oliver Spengel.
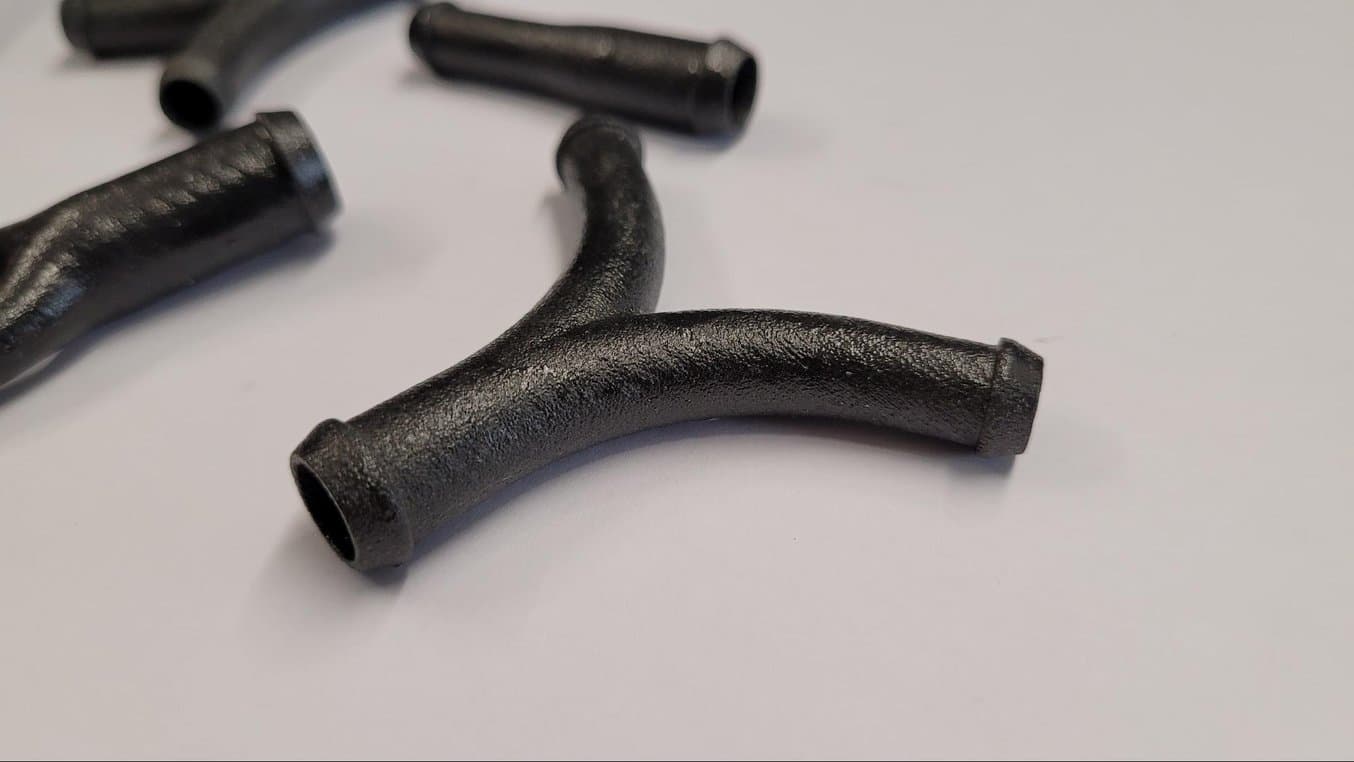
SLS 3D-gedruckte und imprägnierte Schlauchverbinderstücke für die Wasserkühlung
Für den Einsatz in der Wasserkühlung werden die Nylon Komponenten in der Nachbearbeitung imprägniert, um das Risiko zu reduzieren, dass Wasser in die Kunststoffteile eindringen kann oder Undichtigkeiten entstehen.
Neben dem SLS 3D-Druck wurde bei dem Stuttgarter Studierendenteam auch FDM-Druck für einfachere Prototypenelemente verwendet. Für die tatsächlich am Fahrzeug verbauten Teile griffen sie aufgrund der Materialeigenschaften des Formlabs Nylon 12 jedoch größtenteils zum SLS 3D-Druck.
“Materialien beim FDM-Druck haben das Problem, dass die einzelnen Schichten sich voneinander ablösen können, sodass das Teil undicht wird, was für uns extrem problematisch ist”, erklärt Spengel.
Der SLS 3D-Druck hat gegenüber dem FDM-Druck den maßgeblichen Vorteil isotropische Teile drucken zu können. Diese halten vielen äußeren Einflüssen im späteren Betrieb des Rennwagens besser stand, da sie sehr korrosionsbeständig sind.
Durch die angeführten positiven Eigenschaften der Nylon Elemente werden derartige Applikationen schon vermehrt als Endbauteile in der Automobil- und Luftfahrtbranche eingesetzt. Die Formularennwagen des GreenTeam Stuttgarts sind hierfür exemplarisch.
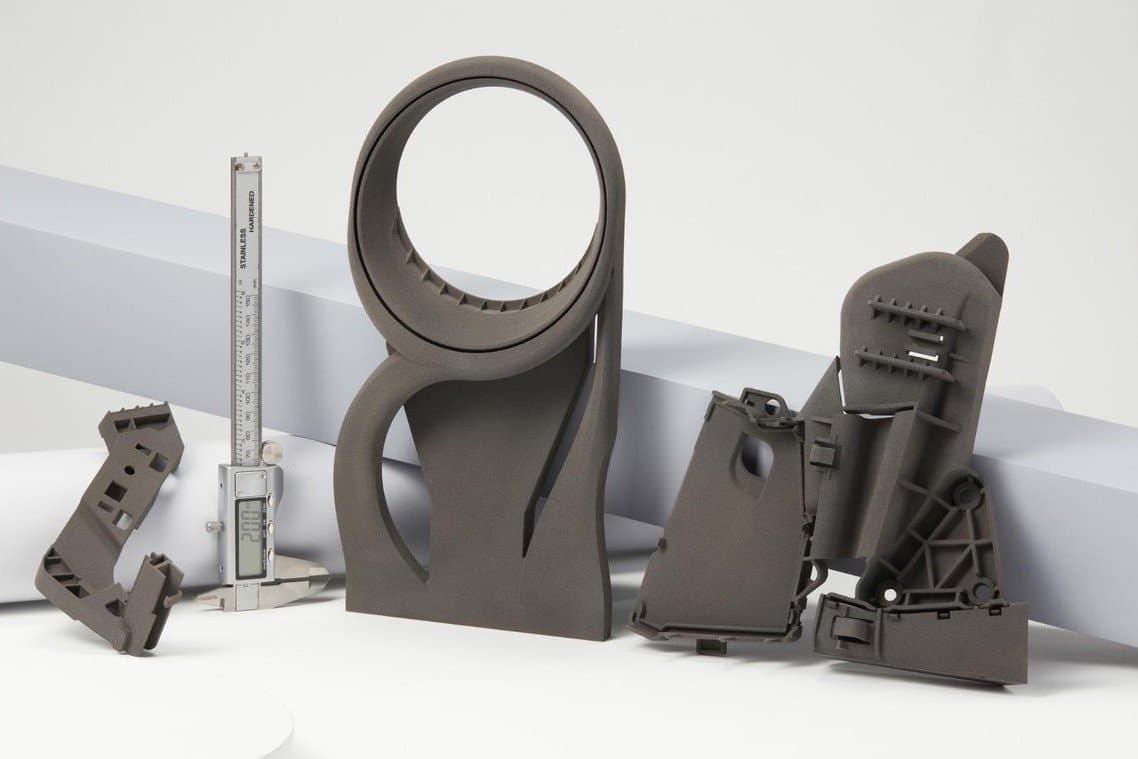
Globaler Automobilzulieferer Brose nutzt SLS 3D-Druck, um Endverbrauchsteile herzustellen
Erfahren Sie, wie Brose, einer der weltweit größten Tier-1-Automobilzulieferer in Familienbesitz, den Einsatz des Fuse 1 und des SLS 3D-Drucks für die Serienfertigung plant.
Die Inhalte dieses Whitepapers:
- Einsatz des Fuse 1 in einer industriellen Umgebung
- SLS für die Endverwendung: Ersatzteile und Teile für End-of-Life-Produkte
- Die Zukunft von SLS in der Serienfertigung
Nächster Schritt: Titelverteidigung
Nachdem sich das Formula Student Team der Universität Stuttgart schon für 5 Wettbewerbe in diesem Jahr qualifiziert hat, steht der neuen Saison nichts mehr im Weg. Dem strammen Zeitplan folgend wird anschließend an die letzten Anpassungen der Konstruktion am Zusammenbau des Rennwagens gearbeitet, bevor dieser dann zeitnah das erste Mal für Testfahrten bewegt werden soll.
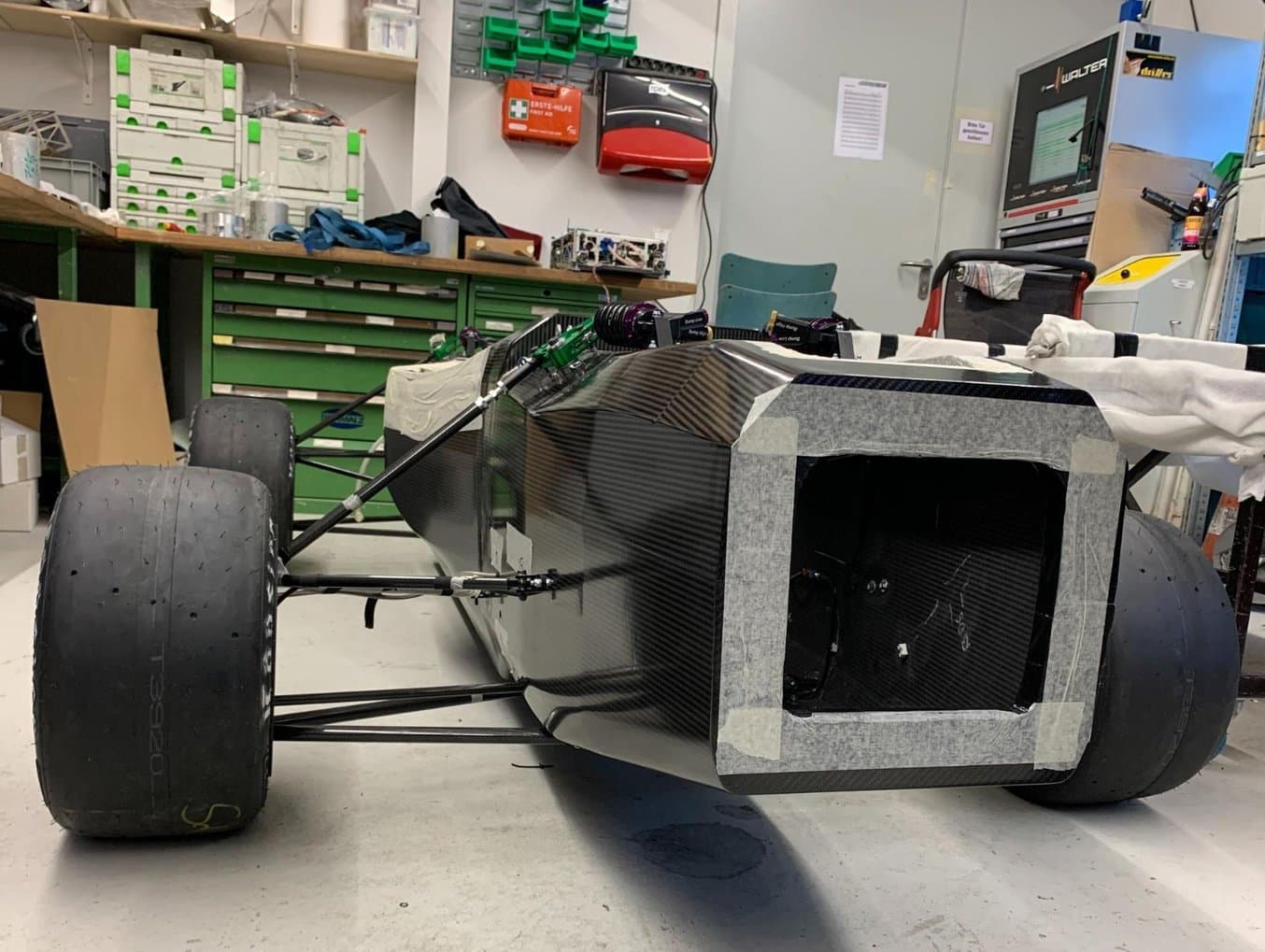
Das Gewinnerfahrzeug der letzten Saison, E11 Evo, zum ersten Mal auf eigenen Rädern
Neben Endbauteilen in der Automobilbranche sowie in der Luft- und Raumfahrt kommt SLS 3D-Druck auch im Prototyping für Produktionswerkzeuge oder im Produktdesign zum Einsatz.