Herstellung von komplexen Greiferhalterungen für einen Pick-and-Place-Roboter
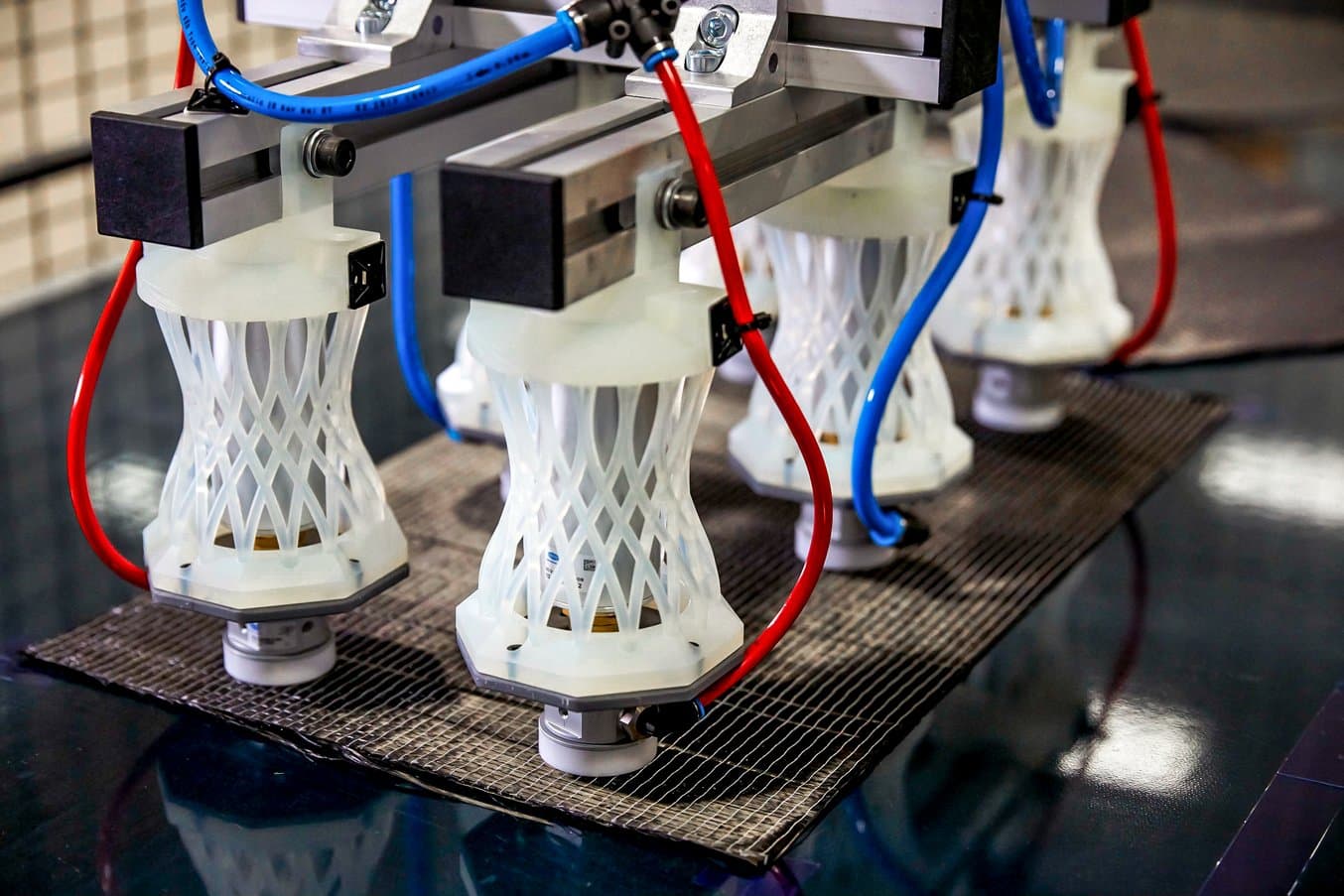
Glasfasern und Kohlenstofffasern werden immer häufiger in der Luft- und Raumfahrt, dem Schiffbau, dem Automobilsektor und anderen Branchen mit hoher Wertschöpfung eingesetzt, da sie hohe Festigkeit und geringes Gewicht bieten. Auf der anderen Seite bergen Sie viele Herausforderungen bei der Fertigung. Das Composites Centre des Advanced Manufacturing Research Centre (AMRC) der University of Sheffield führt Forschungen durch, bei denen hochmodernen Methoden eingesetzt werden, um diese Herausforderungen zu lösen.
In einem aktuellen Projekt untersuchen die Forscher das automatische Verlegen von Kohlefaserplatten mit hoher Genauigkeit und Geschwindigkeit mithilfe eines Pick-and-Place-Roboters. Nach längerem Einsatz begannen jedoch die L-förmigen Halterungen der Druckluftgreifer des Roboters, sich entlang ihrer Schweißnaht zu verformen. Dies führte zu Ausfällen und zwang die Forscher, nach einer neuen Lösung zu suchen.
Erfahren Sie von Matthew Williams, dem Verbundwerkstoff-Techniker für dieses Projekt, welche Designherausforderungen sich ihm stellten, als er ein maßgefertigtes Federbauteil gestaltete, und wie es das Team schaffte, in wenigen Tagen mithilfe von 3D-Druck fünf Iterationen des komplexen Designs herzustellen.
Sehen Sie sich unser Video mit dem Verbundwerkstoff-Techniker Matthew Williams an, um den Pick-and-Place-Roboter in Aktion zu sehen.
Williams arbeitete an der frei zugänglichen additiven Fertigungsstation des AMRC, um die erforderlichen Teile herzustellen. Lesen Sie unsere Fallstudie, um zu erfahren, wie der freie Zugang zu 3D-Druck hunderten von Ingenieuren an einem Standort helfen kann.
Die Anforderung an Genauigkeit bei der Herstellung von Verbundwerkstoffen
Verbundwerkstoffe erhalten ihre hohe Festigkeit und ihr leichtes Gewicht von der Art und Weise, wie die Faserstränge gewebt und in den Teilen verlegt sind. So können die Ingenieure das Design mithilfe der berechneten Belastungen des Bauteils genau optimieren. Doch dadurch wird die Herstellung von Verbundwerkstoffen auch zu einem hochkomplexen Arbeitsprozess.
Das Verlegen von Kohlefasern erfolgt in der Regel manuell, aber die Arbeit von Menschenhand sorgt für einige Abweichungen, da die Platten verformt werden oder nicht richtig liegen. Ein Versatz von nur wenigen Millimetern kann zu fehlerhaften Teilen und zur Vergeudung des teuren Materials führen.
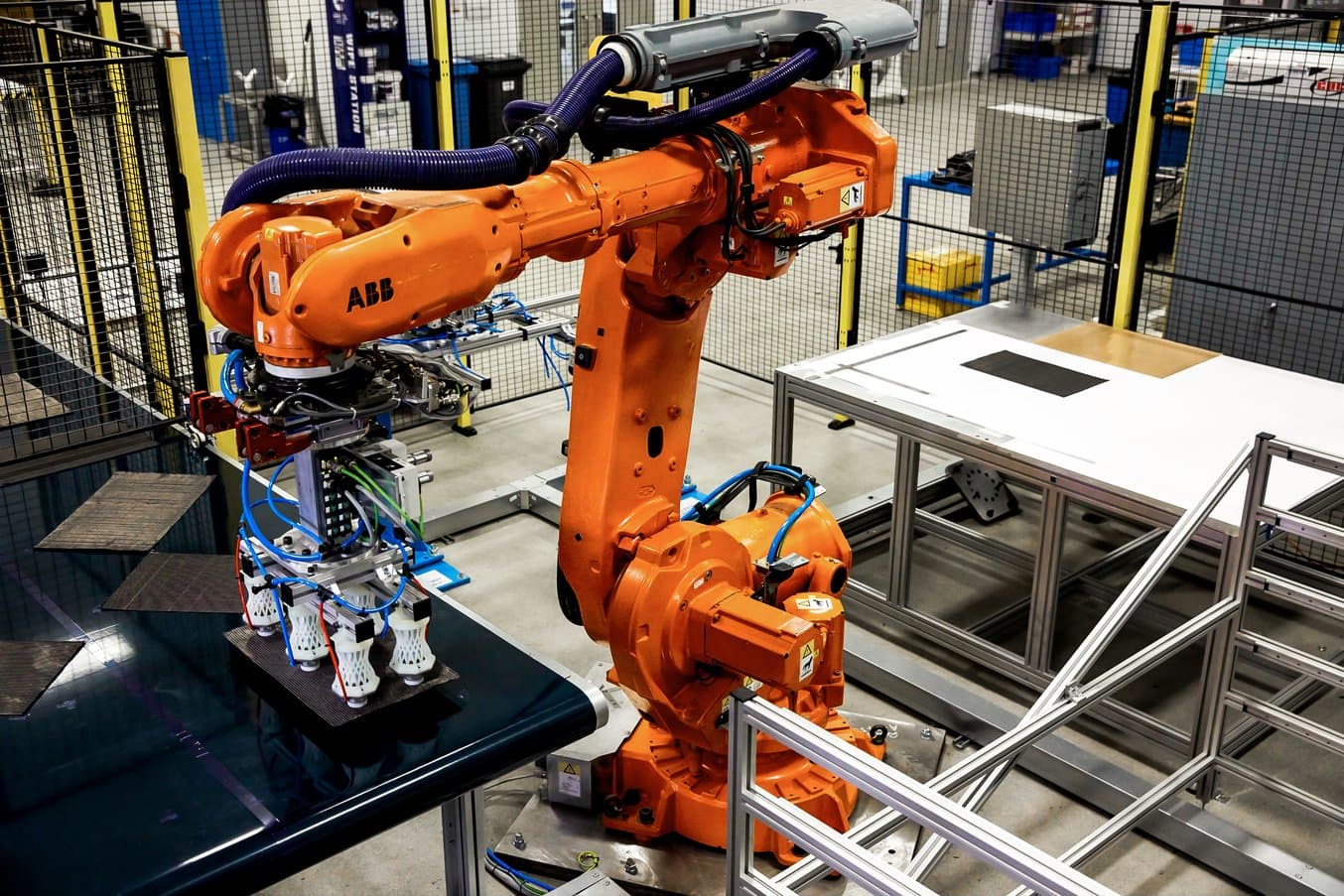
Mit einer Pick-and-Place-Roboterzelle für einen automatisierten Arbeitsprozess zielen die Forscher darauf ab, Ausschuss zu reduzieren und die Geschwindigkeit und Genauigkeit des Prozesses zu erhöhen. Vorgeschnittene Platten gelangen auf einem Förderband in die Zelle, wo sie mit den sechs Druckluftgreifern eines fünfachsigen ABB-Roboters aufgenommen werden, der sie überträgt und mit hoher Genauigkeit auf einem Tisch in der Zelle aufeinanderstapelt.
Die Halterungen, die ursprünglich am Roboter montiert waren, um die Greifer aufzunehmen, waren L-förmige Halterungen aus Aluminium, die an der Seite des Endeffektors des Roboters montiert waren. Da die einzelnen Ausrüstungsteile in der Zelle jedoch nicht vollkommen eben waren, verformten sich die Halterungen nach längerer Anwendung entlang ihrer Schweißnaht. Nach einiger Zeit war die Verformung so stark, dass der Greifer die Platten nicht mehr vom Förderband aufnahm.
Von einer einfachen L-förmigen Halterung zu einem komplexen Design
Ein Bauteil mit genau dem richtigen Grad an Elastizität herzustellen, wurde zu einer ziemlich anspruchsvollen Herausforderung, und Williams benötigte fünf Iterationen.
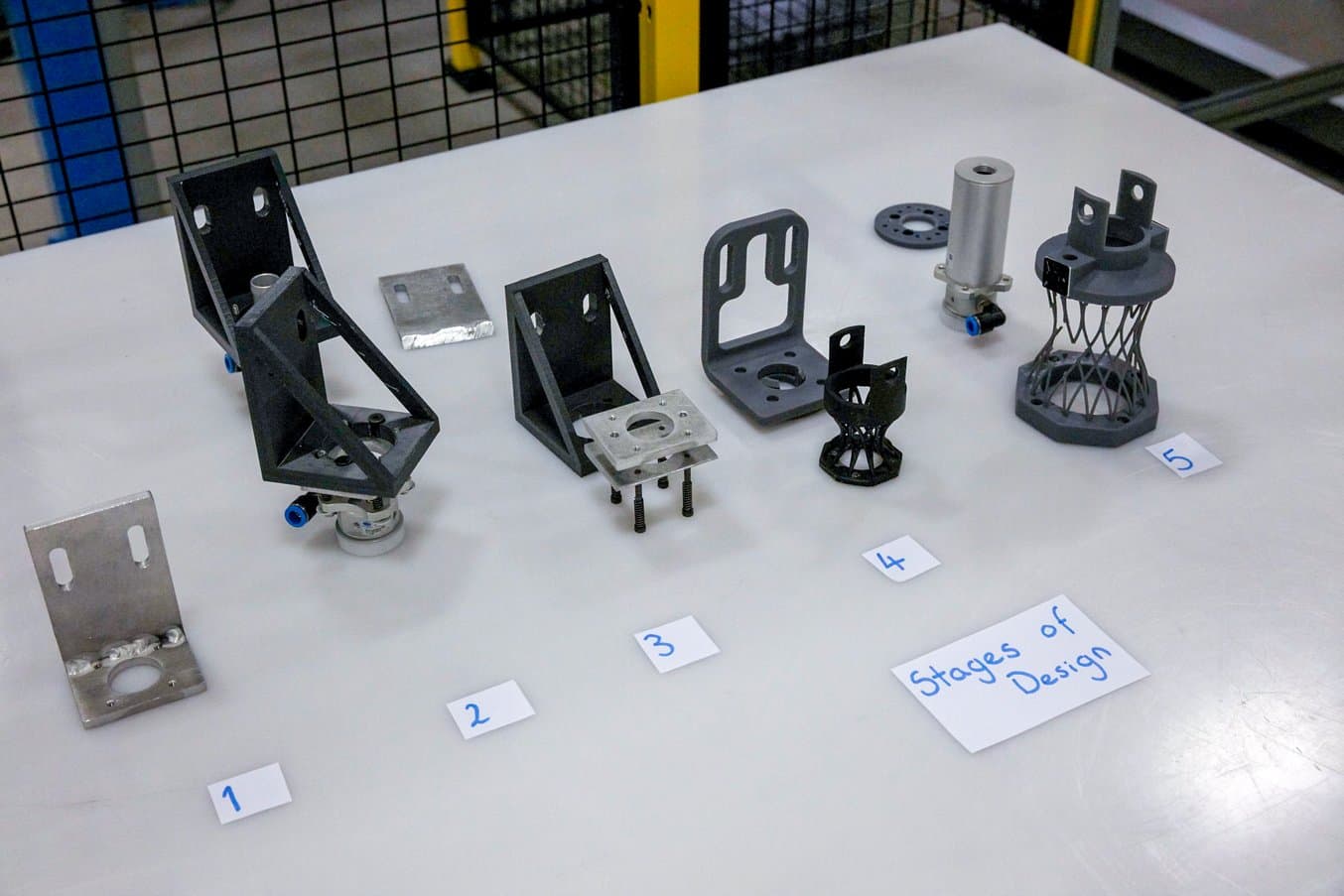
„Ich begann mit einer L-förmigen Halterung aus Aluminium, die nur aus zwei Platten bestand, die durch Heftschweißung miteinander verbunden wurden. Da es sich um eine Schweißnaht handelt, biegt sie sich nicht mehr zurück, sobald sie sich einmal verformt hat. Sie bleibt verbogen und verformt. Darum versuchte ich es mit Plastik, da es sich nach Kompression wieder zurückverformt. Es gab allerdings deutlich mehr nach als das Aluminium und [die Greifer] verlegten plötzlich einzelne Fasern auf dem Tisch. Wir machten das Problem also erst schlimmer, bevor es besser wurde“, so Williams.
Der Forscher entschied sich daraufhin für ein neues Design. Anstatt an der Seite der Halterung befestigt zu sein, befinden sich die Druckluftgreifer nun unter der Halterung. Wenn Kraft unterhalb der Halterung aufgewendet wird, verbiegt diese sich nicht, sondern wird wie eine Feder komprimiert. Mit fortschreitender Forschung fand Williams heraus, dass die Greifer für zu viel Lärm sorgten und darum nicht sicher in einer Arbeitsumgebung eingesetzt werden konnten. Die Greifer benötigten einen Schalldämpfer, wodurch wiederum eine größere Halterung zur Aufnahme des Schalldämpfers erforderlich wurde.
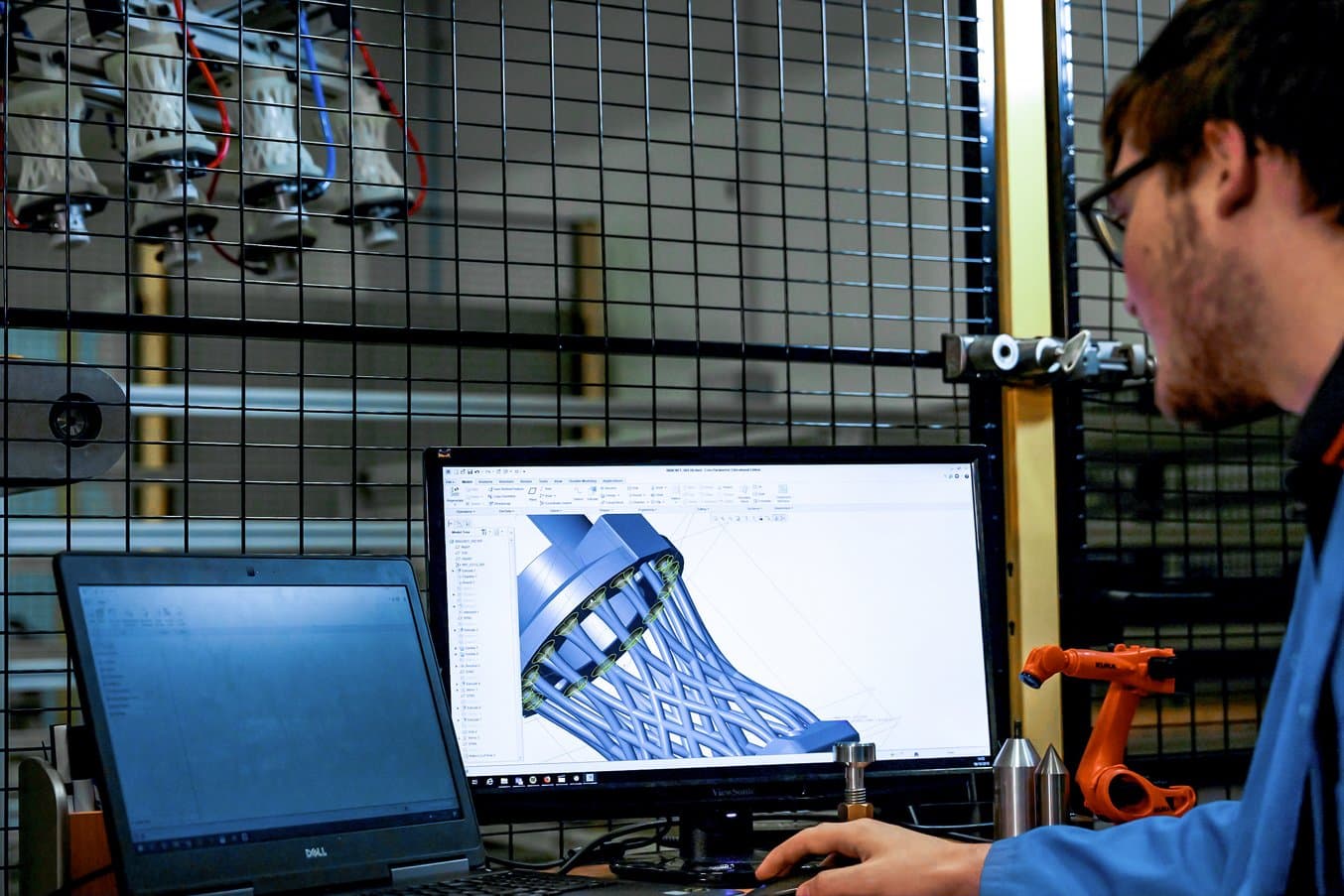
„Ich habe die Struktur verstärkt und sie aus einem robusterem Material gemacht, was deutlich besser funktioniert, da so die Elastizität sogar noch verstärkt wird. Es nimmt sofort wieder seine ursprüngliche Position ein und funktioniert perfekt“, sagt Williams.
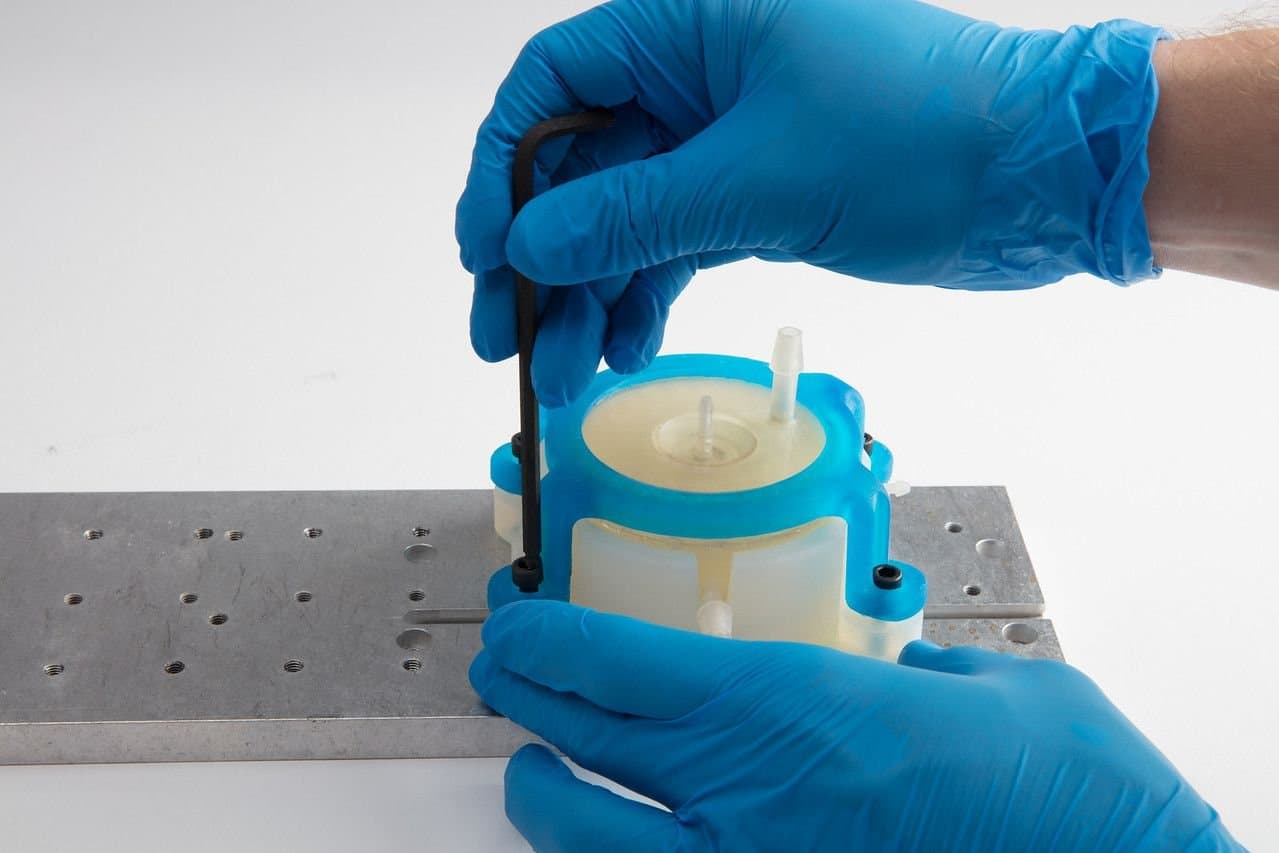
3D-gedrucke Haltevorrichtungen
Laden Sie unser Whitepaper herunter, um zu erfahren, wie Sie mit 3D-gedruckten HaltevorrichtungenKosten reduzieren, die Entwicklungszeit verkürzen und besser optimierte Arbeitsprozesse schaffen können.
White Paper herunterladen
Designfreiheit und schnelle Iterationen mit 3D-Druck
„3D-Druck gibt mir mehr Freiheiten beim Entwerfen eines Teils. Ich kann so gut wie jede Form entwerfen und sie auch herstellen, da diese Geräte so flexibel sind. Er eignet sich viel besser für komplexe Formen wie die, die ich herstellen musste, um dieses Problem zu lösen“, so Williams.
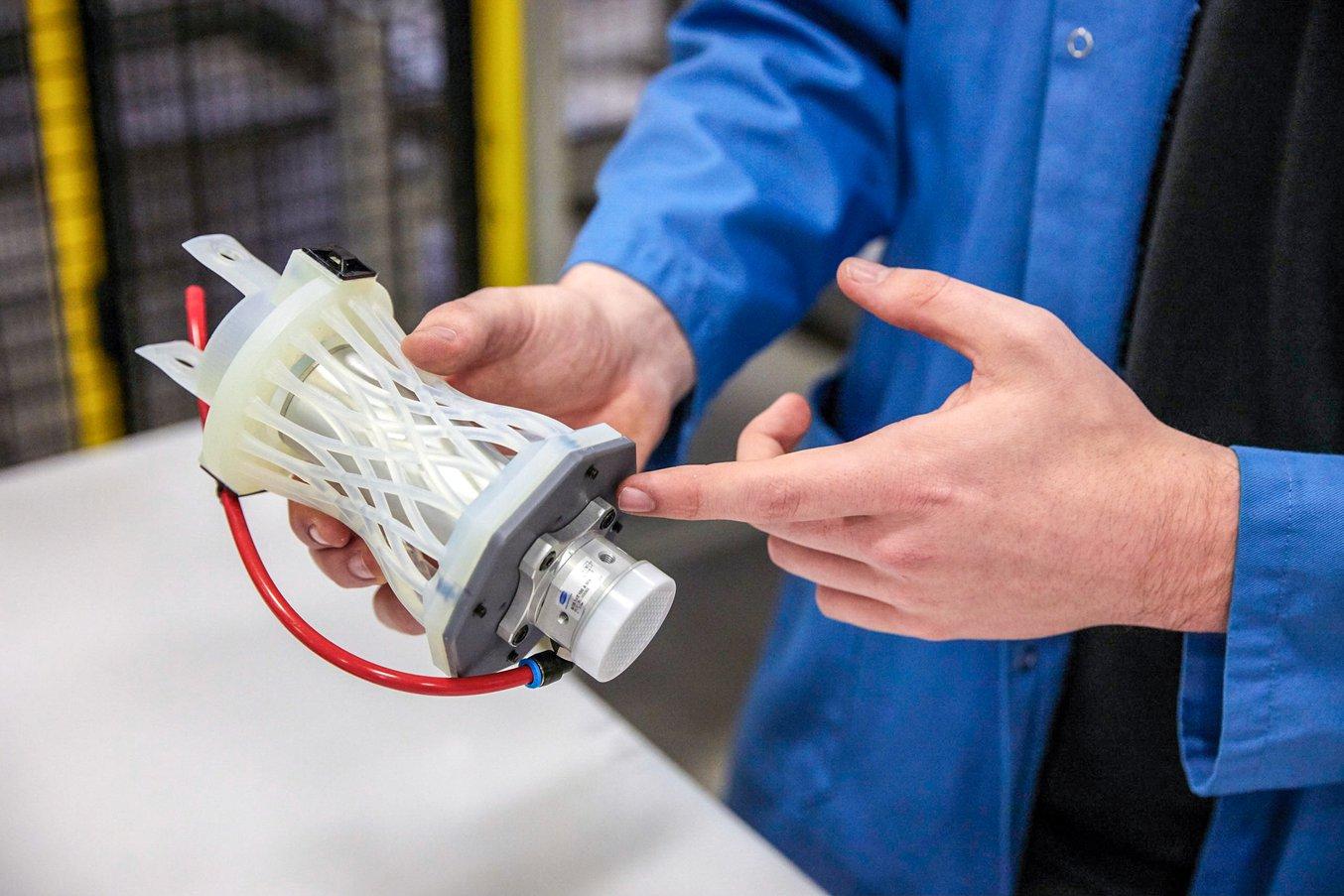
Durch den 3D-Druck konnte Williams im Designprozess kreativer und agiler handeln, und wurde nicht von den Designrichtlinien herkömmlicher Fertigungsverfahren beschränkt.
„Wenn man etwas entwirft, das durch spanende Bearbeitung hergestellt werden soll, muss man viele andere Aspekte berücksichtigen, etwa, wie man es befestigt und wie das Werkzeug an eine bestimmte Stelle gelangen kann. Das Teil ist im Inneren ziemlich komplex, sodass das erforderliche Spiel des Werkzeugs zum Herstellen von Hohlräumen und Details auf der Innenseite wohl nicht ausreichen würde. Ich müsste das Design vereinfachen oder ein neues kompliziertes Design entwerfen. Es würde möglicherweise nicht so gut funktionieren, und es wäre teurer und zeitaufwändiger“, erklärt Williams.
Durch den Zugang zu 3D-Druckern vor Ort konnte Williams Iterationen auch schnell ausführen und Monate an Durchlaufzeit im Verlauf des gesamten Projekts sparen.
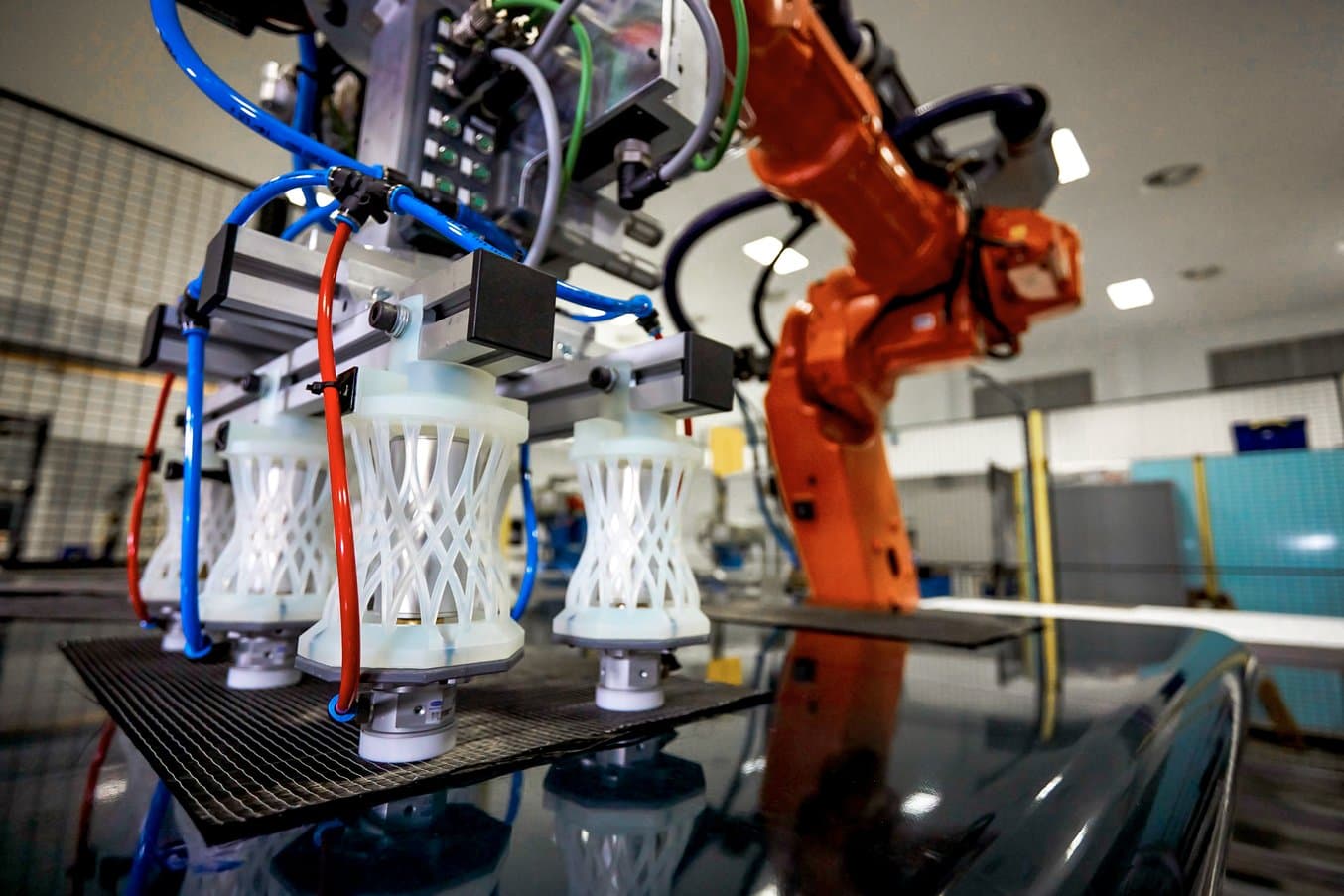
„Ich habe fünf Iterationen des Satzes aus sechs Greifern durchgeführt, was mit Zerspanung 10 bis 15 Wochen dauern könnte, und das ganz ohne jegliche Testläufe“, so Williams.
„Es dauert nur sechs Stunden, um eine Halterung zu drucken, und wenn eine Iteration nicht funktioniert, kann ich ein neues Design im Verlauf meines Arbeitstags erstellen. Wenn ich abends nach Hause gehe, kann ich den Drucker einschalten, und am morgen ist sie dann fertig, wodurch ich dann den ganzen Tag mit dem neuen Teil arbeiten kann“, sagt Williams weiter.
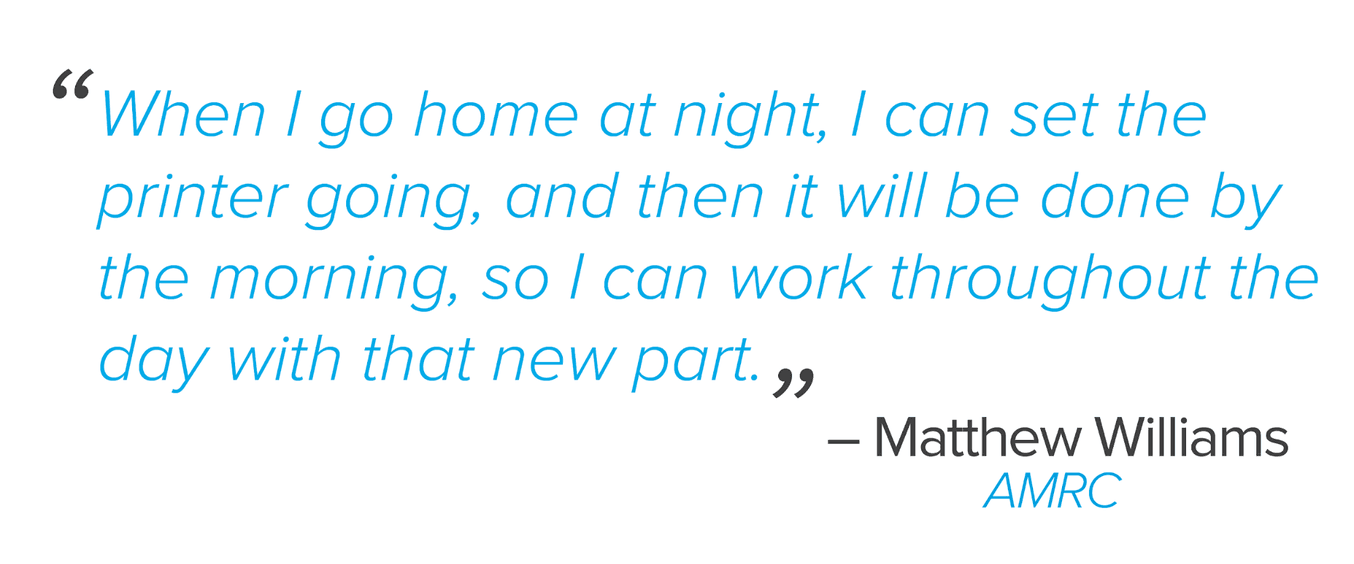
Erfahren Sie, wie eine 3D-Druckstation hunderte von Ingenieuren im AMRC unterstützt
Williams hat mit der Design and Prototyping Group des AMRC zusammengearbeitet, um die 3D-Druckteile herzustellen. Die Gruppe hat vor kurzem eine neue additive Fertigungsstation mit einer Flotte von 12 Form 2 Stereolithografie (SLA) 3D-Druckern installiert, die allen Ingenieuren am Standort freien Zugang zum 3D-Druck bietet.
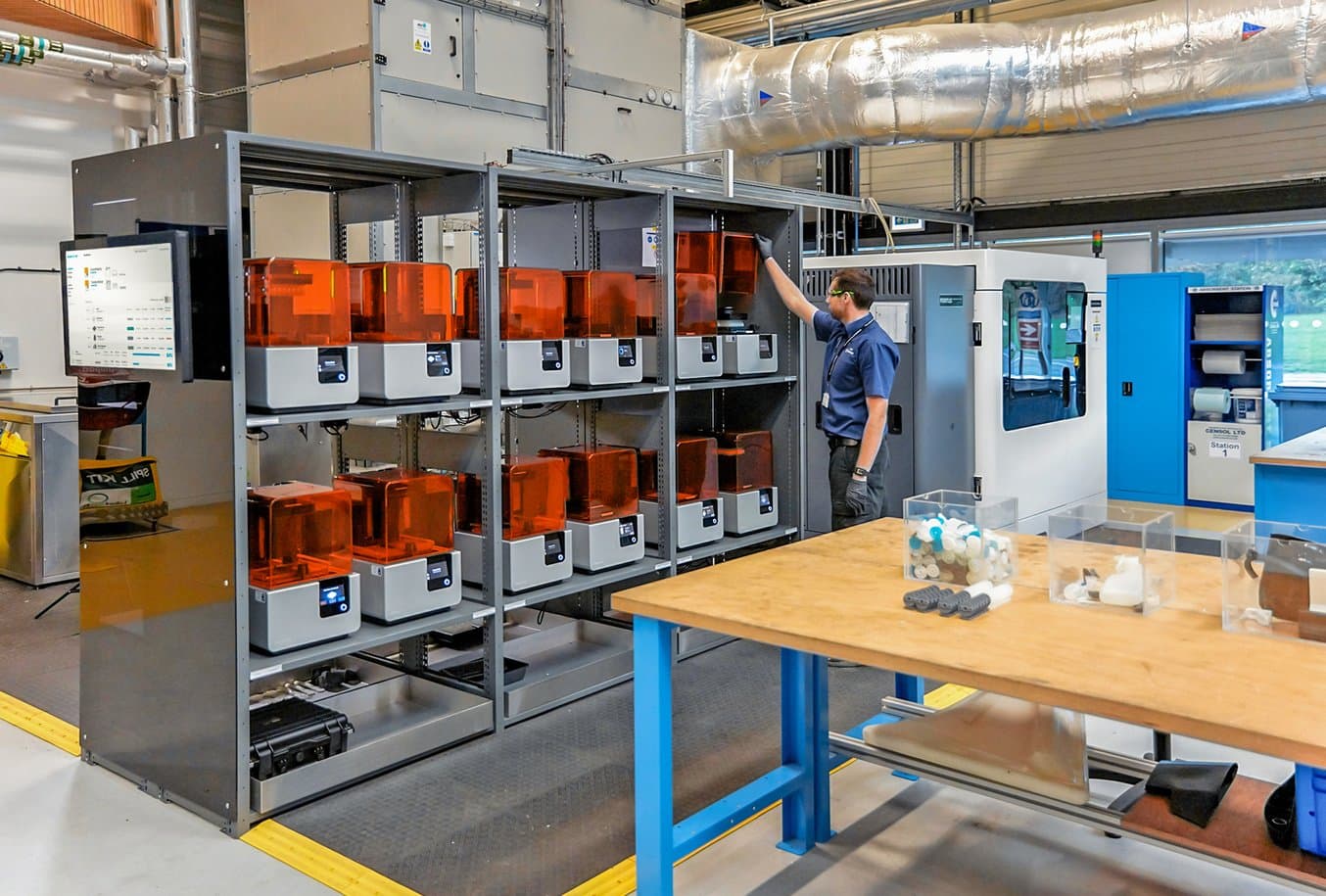
Williams hat mit der Design and Prototyping Group des AMRC zusammengearbeitet, um die 3D-Druckteile herzustellen. Die Gruppe hat vor kurzem eine neue additive Fertigungsstation mit einer Flotte von 12 Form 2 Stereolithografie (SLA) 3D-Druckern installiert, die allen Ingenieuren am Standort freien Zugang zum 3D-Druck bietet.
Erfahren Sie mehr über die 3D-Druckstation des AMRC und über andere Anwendungen wie den Seriendruck von 500 hochpräzisen Bohrkappen für Bohrversuche für Airbus, eine temperaturbeständige Sensorhalterung für eine Schweißanwendung und maßgeschneiderten Rollen für die Faserwicklung bei der Herstellung von Verbundwerkstoffen.
Möchten Sie mehr über die Drucker und die Technologie hinter der 3D-Druckstation des AMRC erfahren? Lernen Sie den Form 3, den großformatigen Form 3L und die Bibliothek an technischen Kunstharzen von Formlabs für Ihr eigenes Projekt kennen, oder fordern Sie einen kostenlosen Probedruck an, um sich selbst einen Eindruck von den Materialien zu verschaffen.