Holimaker produziert mit 3D-gedruckten Spritzgussformen Hunderte von Prototypen und Vorproduktionsteilen
Das französische Startup Holimaker möchte die Produktion von Kunststoffteilen durch die Herstellung von kleinem Industriewerkzeug für die Kunststoffverarbeitung erleichtern. Sein Hauptprodukt, die Holipress, ist eine manuelle Spritzgießmaschine, die Ingenieuren und Produktdesignern die Möglichkeit bietet, Kunststoffteile auf ihrem Arbeitstisch für die Herstellung von geringen Mengen an Prototypen, Pilot-Produktionen oder auch limitierten Reihen von Endverbrauchsteilen zu verwenden.
Holimaker offeriert seinen Kunden Machbarkeitsstudien unter Einsatz 3D-gedruckter Formen für einen schnellen und erschwinglichen Durchsatz verwendet werden. Auf diese Weise lassen sich in der Pilotphase einer neuen Produkteinführung schnell und erschwinglich Prototypen erstellen, um auf deren Basis die Endbedingungen für die Fertigung zu validieren. Durch die Verwendung derselben Fertigungsmethode, einschließlich des Entwurfs und der Materialien der Form, können diese Teile in der Praxis getestet und dabei deren Tauglichkeit für die Massenproduktion sichergestellt werden. Die 3D-gedruckten Formentwürfe können dann während der Massenproduktion einfach an den Werkzeugstahl angepasst werden.
Holimaker verwendet in 80 bis 90 % seiner derzeitigen Projekte 3D-gedruckte Spritzgussformen. Wir haben mit Geschäftsführer Aurélien Stoky und Marketingleiter Vivien Salamone gesprochen, um zu erfahren, wie sie beide Technologien verbinden.
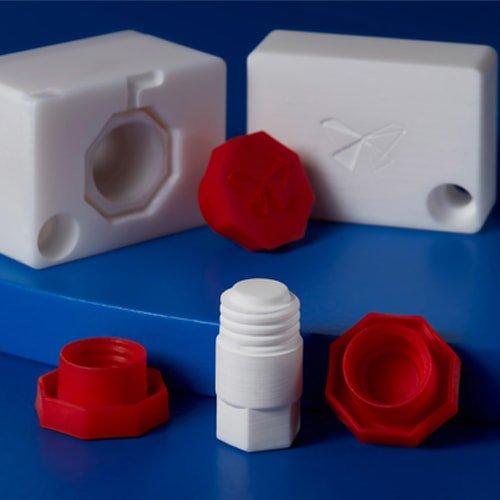
Schnelles Spritzgießen von Kleinserien mit Formen aus dem 3D-Drucker
Laden Sie dieses Whitepaper herunter und erfahren Sie mehr über die Methoden und Richtlinien für die Herstellung von 3D-gedruckten Spritzgussformen, um Kosten zu senken und Lieferzeiten zu verkürzen. Es enthält Fallstudien aus der Praxis von Braskem, Holimaker und Novus Applications.
Wieso 3D-gedruckte Spritzgussformen?
Für gewöhnlich kommen für die Produktion von Spritzgussformen kostspielige industrielle Verfahren wie etwa CNC-Bearbeitung oder Funkenerosion (EDM) zum Eunsatz. Für kleinere Produktionsmengen sind der Kosten- und Zeitaufwand sowie das spezielle Gerät und Fachwissen, das für die Herstellung der Form aus üblichen Werkzeugmetallen erforderlich sind, jedoch ein Hindernis und machen es für viele Unternehmen unmöglich, den Spritzguss als Verfahren für die Massenproduktion zu nutzen.Durch die Herstellung von Spritzgussmodellen via 3D-Druck dagegen lassen sich Prototypen für die Kleinserienproduktion dagegen deutlich einfacher erstellen als mit Metallformen. Zudem zeichnen sich die so produzierten Teile durch hohe Qualität aus und sind problemlos wiederholbar.
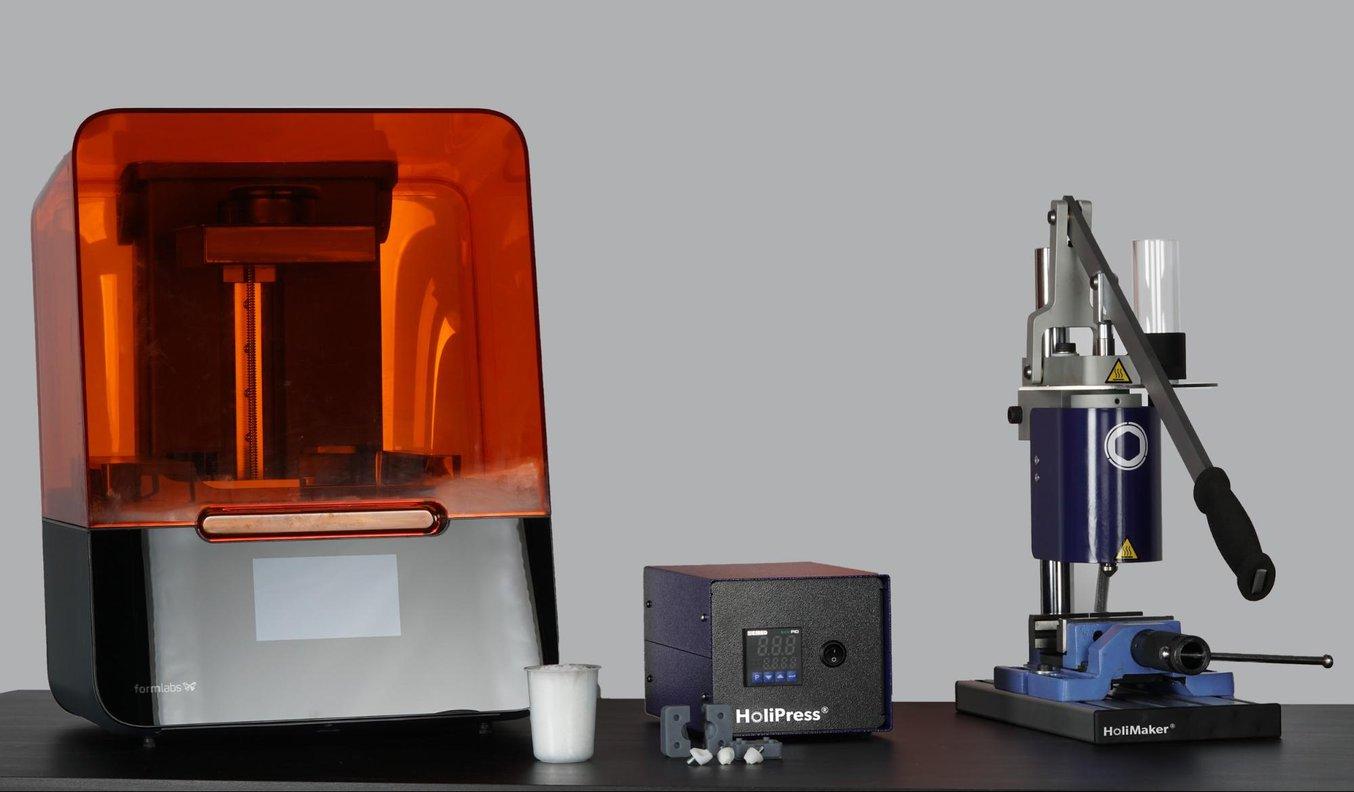
Die Holipress neben dem Form 3 Drucker.
„Das Problem beim Spritzgießen ist die Herstellung der Form. Um das Spritzgießen zu demokratisieren und allgemein zugänglich zu machen, benötigten wir eine ergänzende Technologie zur Anfertigung unserer Form. Der Desktop-Druck war die ideale Lösung für uns. Wir kombinieren die Flexibilität des 3D-Drucks mit der Produktivität und Qualität von spritzgegossenem Kunststoff“, erklärten Stoky und Salamone.
Dabei entscheidend: Der Prozess verkürzt die Zeit von der Produktidee bis zur Produktion und ermöglicht es zugleich, Teileserien aus herkömmlichen Thermoplasten zu liefern. So können Unternehmen dank der Holipress Kleinserien von Prototypen und Vorproduktionsteilen produzieren, um das endgültige Material und die Produktionslinie für die Massenproduktion zu testen, und sogar limitierte Mengen an Endverbrauchsteilen produzieren. Und dank Desktop-Stereolithografie-3D-Druck (SLA) können sie dies in wenigen Tagen mit sehr wenig Ausrüstung und ohne speziell ausgebildete Fachkräfte schaffen.
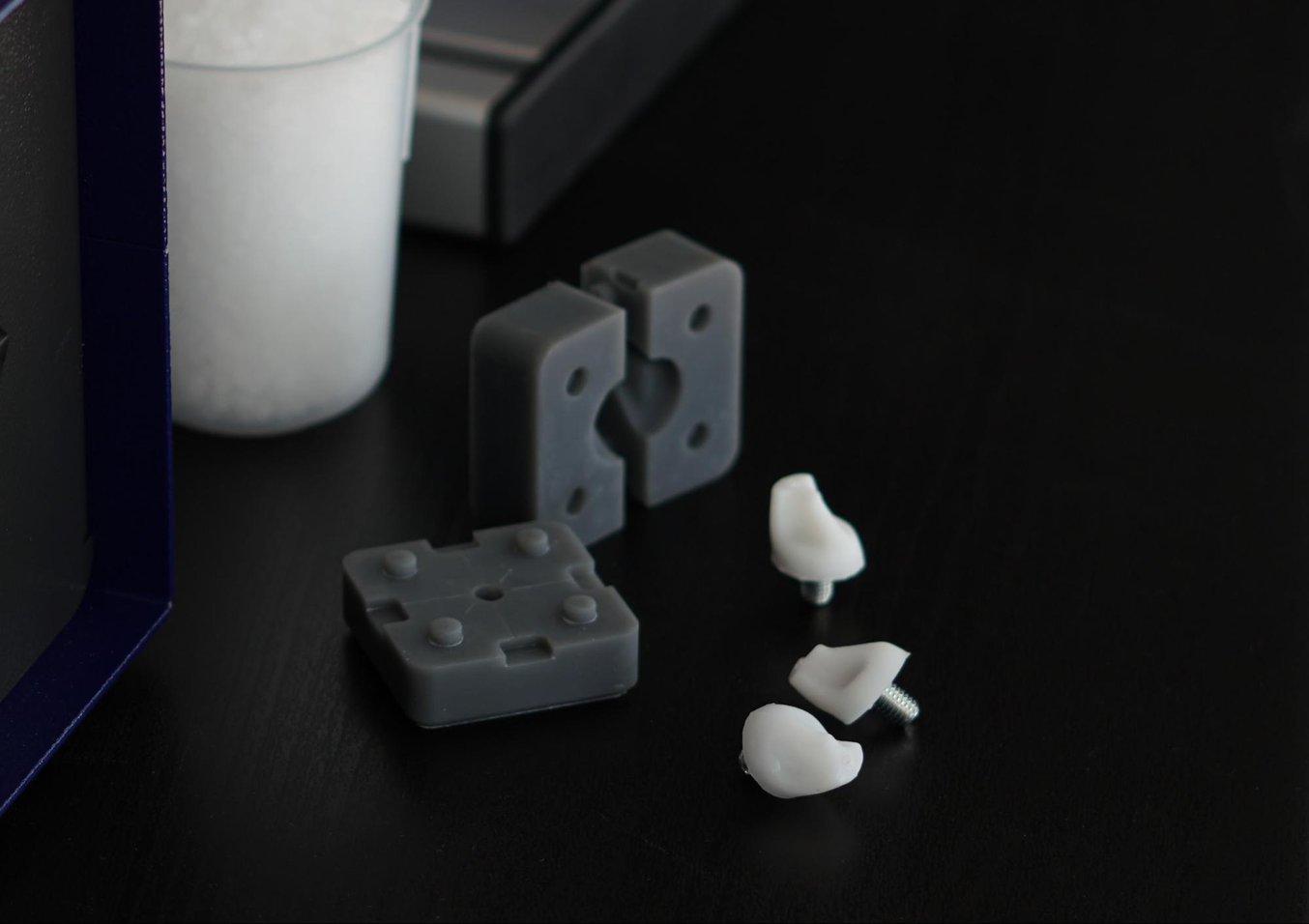
Die Vorproduktionsprototypen dieser Stollen wurden in 3D-gedruckten Formen mit drei unterschiedlichen Thermoplasten spritzgegossen, nämlich POM (180 °C), PA 6.6 (270 °C) und PP (210 °C).
Mit 3D-gedruckten Formen kann das Team von Holimaker die Durchlaufzeiten beim Formenbau deutlich verkürzen und neue Designs zur Optimierung der Geometrie innerhalb eines Tages iterieren.
„Wir entwerfen die Form oft am Vormittag, drucken sie tagsüber und testen das Spritzgießen am Nachmittag, um das Design zu ändern und über Nacht einen zweiten Druck zu starten.“ Mit der herkömmlichen Methode würden wir die Form erneut spanend bearbeiten müssen, was Wochen dauern würde“, erklärt Stoky.
Holimaker hat alternative Wege der Formenherstellung erkundet. Für Aufträge von mehr als tausend Teilen würden sie eine gefräste Aluminiumform verwenden, aber für kleinere Mengen betreiben sie die Presse mit 3D-gedruckten Formen. In manchen Fällen kombinieren sie beides: Für große Mengen mit anspruchsvollen Geometrien fräsen sie die Außenseite der Form und stellen mittels 3D-Druck den Einsatz her, der mit der Zeit ersetzt wird.
Betriebsinterner 3D-Druck hat es Holimaker auch ermöglicht, über die Grenzen der Zerspanungstechnik hinauszugehen. In vielen Projekten haben sie komplexe Formendesigns umsetzen können, die auf herkömmliche Weise nur schwer herstellbar sind, wodurch ihre Kunden sogar noch weitere Innovationen umsetzen konnten.
„Was die Geometrie anbelangt, wären manche unserer Projekte nicht ohne 3D-Druck möglich gewesen“, so Stoky.
Der Prozess Schritt für Schritt
Design
Üblicherweise entwickelt das Team drei bis vier Modellversionen pro Projekt, um das Design zu optimieren. Dabei folgt es den allgemeinen Empfehlungen für den Formenbau und Design for Manufacturing, wie die Aufnahme von Entformungsschrägen. Meist arbeitet es an kleinen Teilen und fügt 0,1 mm große Lüftungsöffnungen und 0,5-mm-Kanäle hinzu.
Zusätzlich beachtet es einige 3D-Druckregeln, wie das Anfasen zur Erleichterung der Entnahme des Teils von der Konstruktionsplattform, einschließlich der Nutzung von Zentrierstiften zur Ausrichtung der Formhälften und dem Hinzufügen von Kerben zum leichteren Öffnen der Form mit einem Schraubendreher. Im Allgemeinen verwendet es 10 mm dicke Formen und vermeidet dünne Querschnitte. Teile, die nur 1–2 mm dick sind, halten den hohen Temperaturen nicht stand.
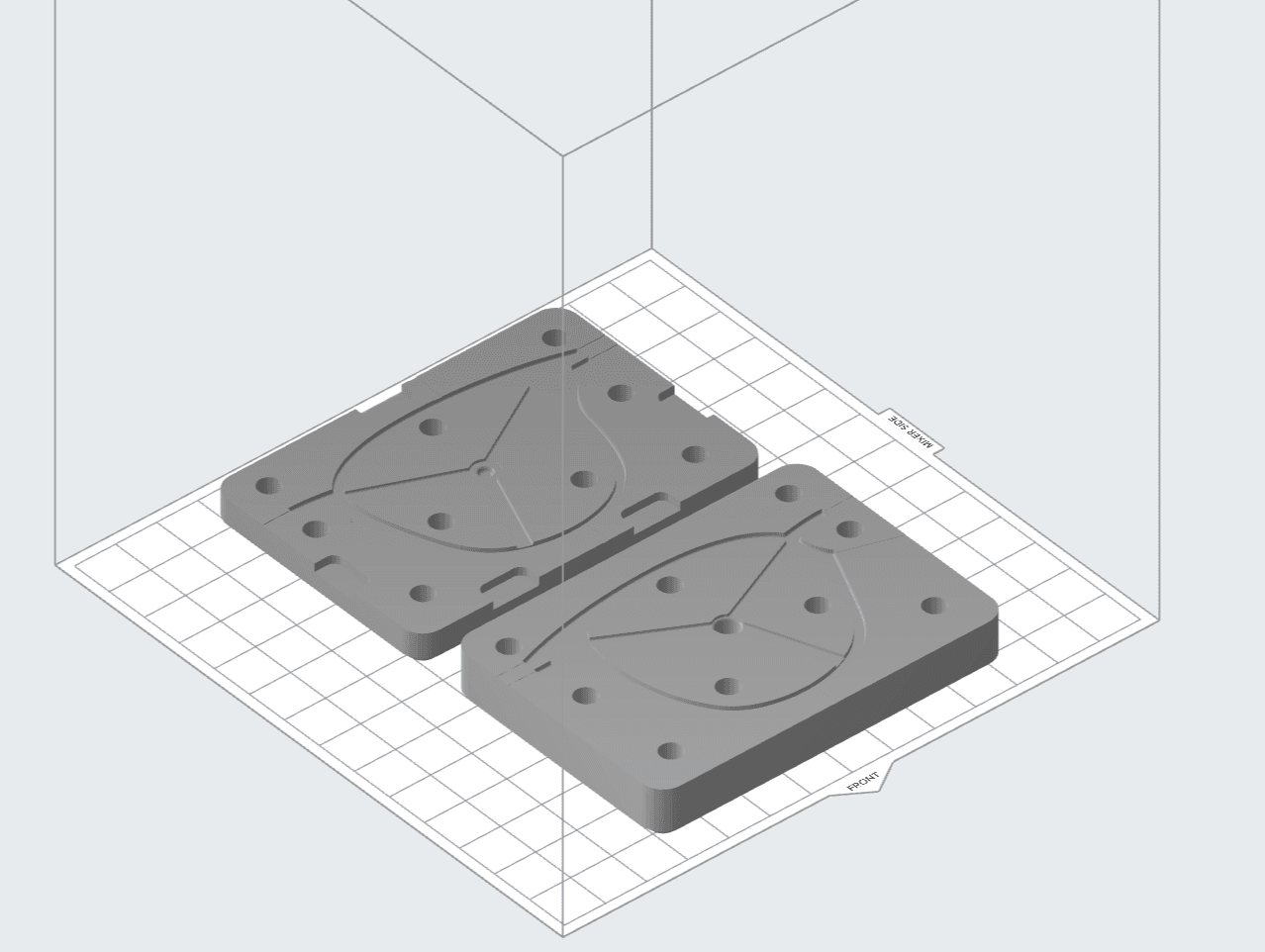
Verschiedene Spritzgussdesigns in der Druckvorbereitungssoftware PreForm von Formlabs.
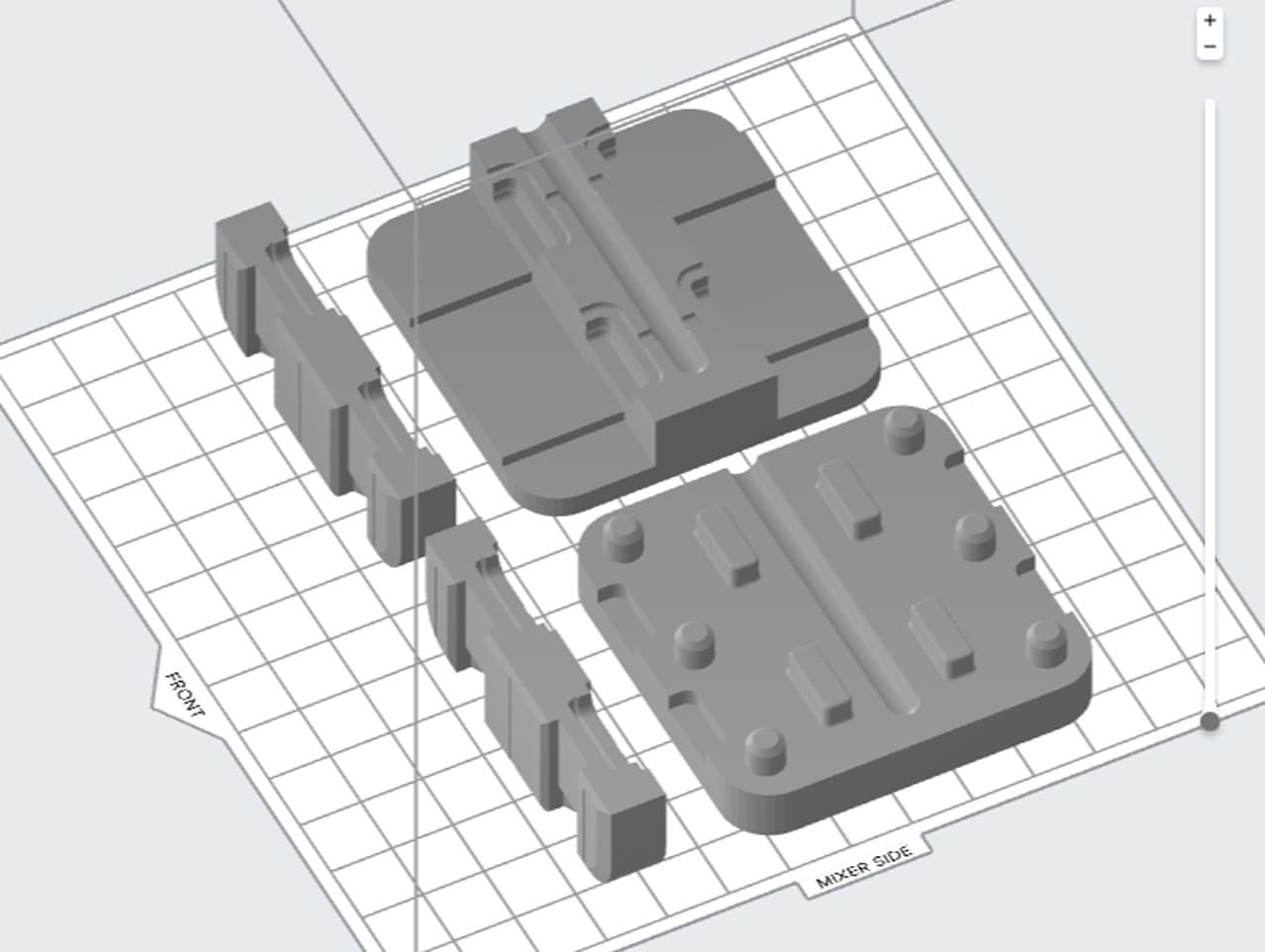
3D-gedruckte Formen für die Kleinserienproduktion lassen sich nahtlos in zerspante Metallformen für die Massenproduktion überführen. Einzig einige einfache Modifikationen an Entformungsschrägen, Angüssen oder Lüftungsöffnungsabmessungen sind bisweilen nötig.
3D-Druck
Das Team von Holimaker druckt die Formen direkt auf der Konstruktionsplattform mit einer Schichtstärke von 50 Mikrometern. Diese Ausrichtung spart Druckzeit und Harz durch den Verzicht auf Stützstrukturen; außerdem hat das Team an den Oberflächen der Form eine bessere Maßgenauigkeit nach dem Aushärten festgestellt. Dimensionsabweichungen treten, wenn überhaupt, dann meist an der Blockaußenseite auf, die es durch manuelles Schleifen nachbearbeitet, um die Form an die Standardmetallrahmen anzupassen, die zusätzlich stützen.
Formlabs empfiehlt für gewöhnlich Rigid 10K Resin und High Temp Resin für den Spritzguss. Dieser Fall zeigt, wie Grey Pro Resin eine Alternative bei Formversagen durch anspruchsvolle geometrische Formen darstellen kann. Wenn die Abkühlzeit keine Priorität darstellt, ist Grey Pro Resin eine gute Option zur Verlängerung der Formstandzeit.
Holimaker bevorzugt Grey Pro Resin für die meisten seiner Studien. Dieses Material weist zwar eine niedrigere Temperaturbeständigkeit auf als High Temp Resin und Rigid 10K Resin, ist dabei aber weniger spröde und erlaubt zudem eine höhere Anzahl an Zyklen bei schwierigen Geometrien. Grey Pro Resin kann auch gebohrt und mehrmals gehandhabt werden und könnte in Standard-Spritzgießmaschinen eingesetzt werden.
Spritzgießen
Das Team verwendet die Spritzgießmaschine Holipress in all seinen Studien. Dabei handelt es sich um eine kleine, einfach einsetzbare, manuelle Spritzgießmaschine, die zu einem Zehntel der Kosten einer industriellen Spritzgießmaschine erhältlich ist.
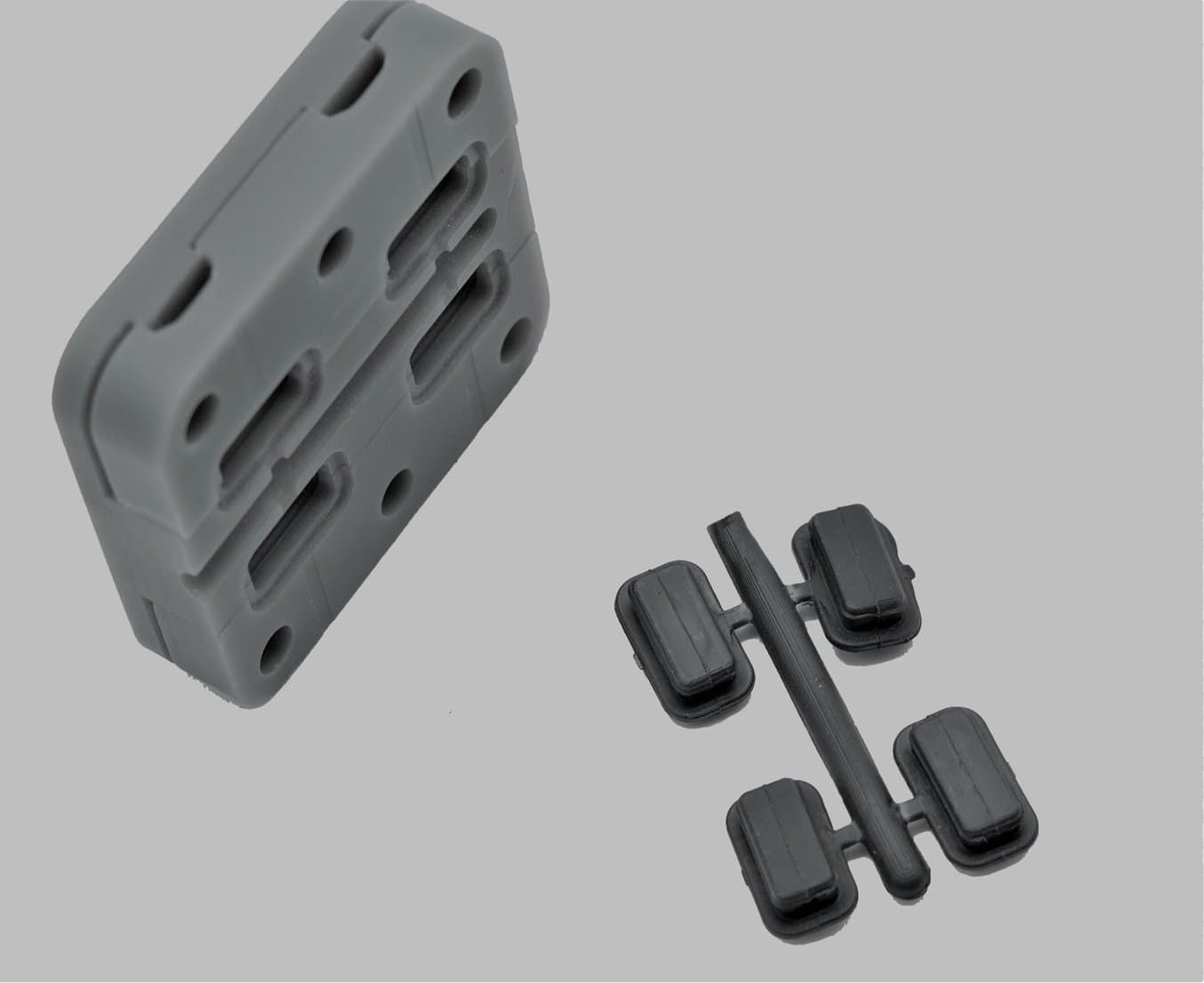
Diese Gesichtsschutzschilder wurden mit PP spritzgegossen (lebensmittelecht, 220 °C).
Die Formen werden in einen vorgefertigten Aluminiumrahmen platziert, der dem Druck besser standhält und sicherstellt, dass die Spritzgussdüse nicht in direkten Kontakt zur gedruckten Form kommt.
Mit den mit Formlabs gedruckten Formen verarbeitet Holimaker eine breite Palette an Thermoplasten mit verschiedenen Härtegraden, von Shorehärte 40A bis 90A, bei Zykluszeiten von drei bis fünf Minuten. Die Anzahl der Zyklen pro Form reicht von etwa 10 Teilen für PA, das mit 270 °C verarbeitet wird, bis zu Hunderten von Teilen für Kunststoffe aus PP, TPE oder POM, die bei niedrigeren Temperaturen verarbeitet werden. Holimaker entwickelt ein integriertes Kühlsystem zur Reduzierung der Abkühlzeit vor dem Entformen.
Ergebnisse
Das Team hat den SLA-3D-Druck von Formlabs aufgrund seiner Benutzerfreundlichkeit und der Qualität der Teile gewählt.
„Die Qualität unserer spritzgegossenen Teile ist dank der hochwertigen Formen sehr gut. Und wenn ich am Abend einen Druck starte, können wir fast sicher sein, dass wir am nächsten Tag eine gute Form haben,“ so Stoky.
Stoky und Salamone hatten zuvor eine andere Desktop-Drucktechnologie verwendet, jedoch eine zu starke Verformung der Drucke festgestellt, sogar noch vor dem Spritzguss.
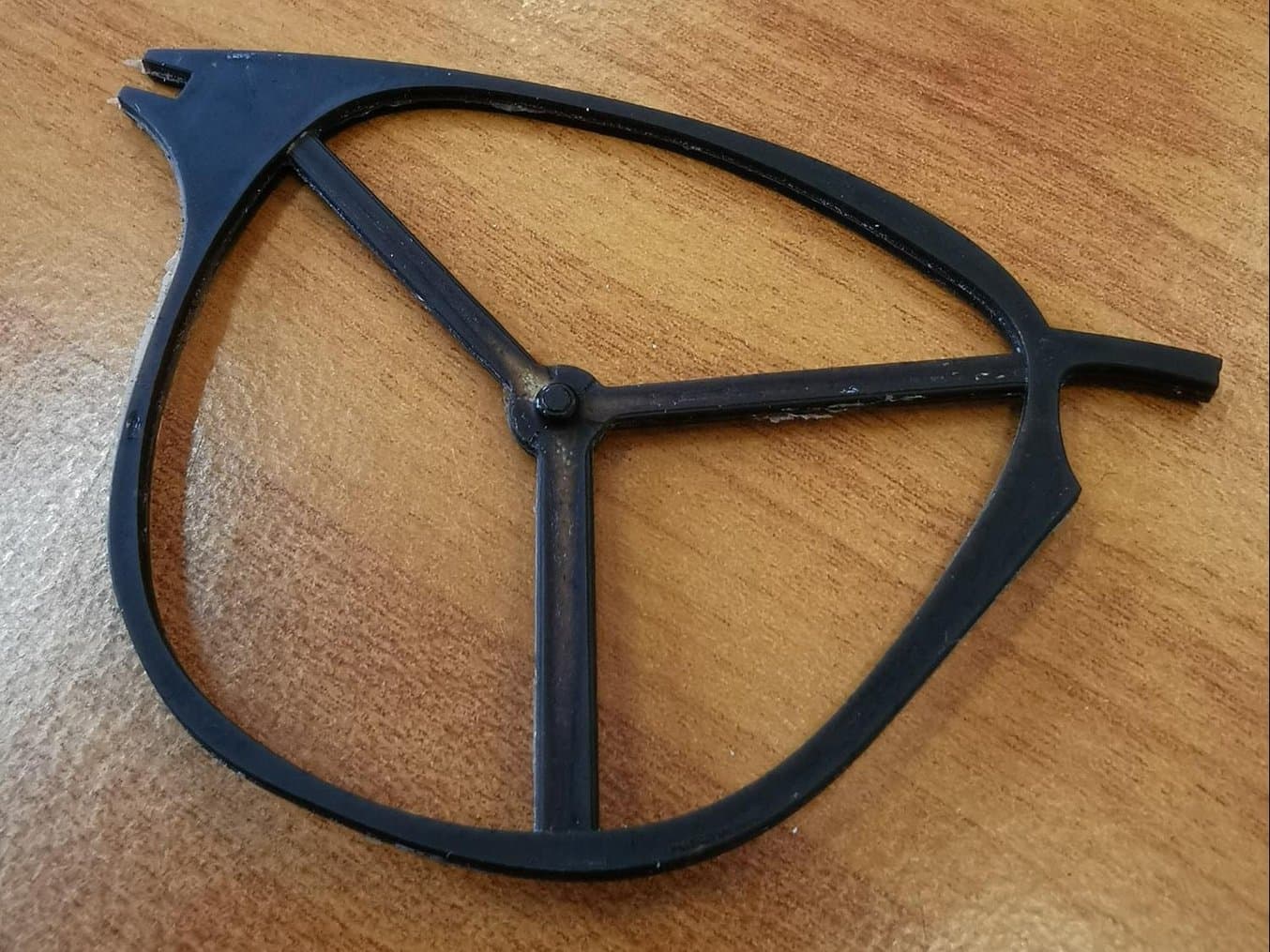
Ein Brillenrahmen, der mit 3D-gedruckten Formen hergestellt wurde.
„Formlabs-Teile bieten hervorragende Maßgenauigkeit und Oberflächengüte. Wenn ein Dimensionsfehler auftritt, ist er sehr klein und in den drei Achsen gleich, sodass wir ihn vorhersehen und nachbearbeiten können. Mit anderen Desktop-Druckern konnten wir die Verformung nicht steuern,“ sagte Stoky.
Das Team schätzt auch den einfachen, leicht zu erlernenden und durchzuführenden Arbeitsablauf, einschließlich der automatisierten Fertigstellungswerkzeuge Form Wash und Form Cure.
Holimaker bot uns Einblick in einige wenige Kundenfälle, um uns ein besseres Verständnis der Teile, der Gussbedingungen und der Ergebnisse ihrer Machbarkeitsstudien zu ermöglichen.
Unternehmen | Smart Power | FERME 3D | Brillenhersteller | |
---|---|---|---|---|
Produkt | Fußballschuhstollen | Schutzvisierklammer | Brillenfassung | |
Anforderung | Vorserie von Prototypen aus verschiedenen Thermoplasten für die Felderprobung und die Auswahl des endgültigen Materials für die Massenproduktion. | Erprobung einer Lösung zur Produktion einer Serie von mehreren 10 000 Teilen in kurzer Zeit. | Erprobung der Kompatibilität von Brillenmaterial mit gedruckten Formen zur Produktion einer Serie von 200 Fassungen | |
Spritzgussmaterialien | POM (180 °C), PA 6.6 (270 °C), PP (210 °C) | PP (lebensmittelecht, 220 °C) | ASA (240 °C), PA (240 °C) | |
Anzahl der Teile aus einer Form | 60 | 100 | 70 | |
Zykluszeit | 2 Minuten | 2 Minuten | 2 Minuten | |
Durchlaufzeit des Projekts | 1 Woche | 1 Woche | 2 Wochen |
Zeit und Kosten sparen mit 3D-gedruckten Spritzgussformen
Die Verwendung von betriebsintern 3D-gedruckten Formen bietet erhebliche Zeit- und Kosteneinsparungen gegenüber dem Outsourcing von gefrästen Metallformen.
Extern hergestellte, gefräste Metallform | Betriebsintern 3D-gedruckte Form | |||
---|---|---|---|---|
Ausrüstung | Holipress, Thermoplaste | Holipress, Thermoplaste, Form 3 Drucker, Grey Pro Resin | ||
Zeitaufwand für die Formherstellung | 3 bis 4 Wochen | 1 Woche | ||
Kosten der Formherstellung | Vier- bis fünffach | Einfach |
Das Rapid Tooling mit Desktop-Spritzguss und 3D-gedruckten Formen ermöglicht es Holimaker, Kleinserien von thermoplastischen Teilen schnell und auf Abruf zu drucken.
„Wir können die Zeit zwischen dem Entwurf des Objekts und dem fertigen Spritzgussteil verkürzen. Wir erzielen Flexibilität und sparen Zeit und Geld“, so Stoky.
Laden Sie unser kostenloses Whitepaper herunter oder sehen Sie sich das Webinar an und erfahren Sie mehr über den genauen Prozessablauf, die Designrichtlinien sowie weitere bewährte Praktiken für die Herstellung von 3D-gedruckten Spritzgussformen. Es enthält zusätzliche Fallstudien aus der Praxis von Braskem und Novus Applications.und erfahren Sie mehr über den genauen Prozessablauf, die Designrichtlinien sowie weitere bewährte Praktiken für die Herstellung von 3D-gedruckten Spritzgussformen. Es enthält zusätzliche Fallstudien aus der Praxis von Braskem und Novus Applications.