Wie die Konzeptfahrzeuge von morgen mithilfe von 3D-Druck das Licht der Welt erblicken
Vital Auto ist ein industrielles Designstudio im Herzen der britischen Automobilbranche mit umfassender Expertise im Fahrzeugdesign. Zur illustren Kundschaft dieses Unternehmens gehören viele der wichtigsten Automobilhersteller wie beispielsweise Volvo, Nissan, Lotus, McLaren, Geely, TATA und darüber hinaus.
„Die Kunden kommen oft zu uns, um die Grenzen des Möglichen auszuweiten, die Ihnen die heutige Technologie setzt“, berichtet Shay Moradi, VP of Innovation & Experiential Technology bei Vital Auto. Wenn die Hersteller selbst keine Zeit für Experimente haben, verlassen sie sich bei dieser Herausforderung auf Vital Auto, wo Ideen, Zeichnungen oder technische Spezifikationen Gestalt annehmen und umgesetzt werden.
Im Folgenden erfahren Sie, wie Vital Auto originalgetreue Prototypen und Konzeptfahrzeuge erstellt und mit einer Vielzahl fortschrittlicher Werkzeuge – darunter eine große Flotte von 3D-Druckern des Typs Form 3L und Fuse 1 – schnelle Iterationen durchführt.
Die Herstellung eines Konzeptfahrzeugs
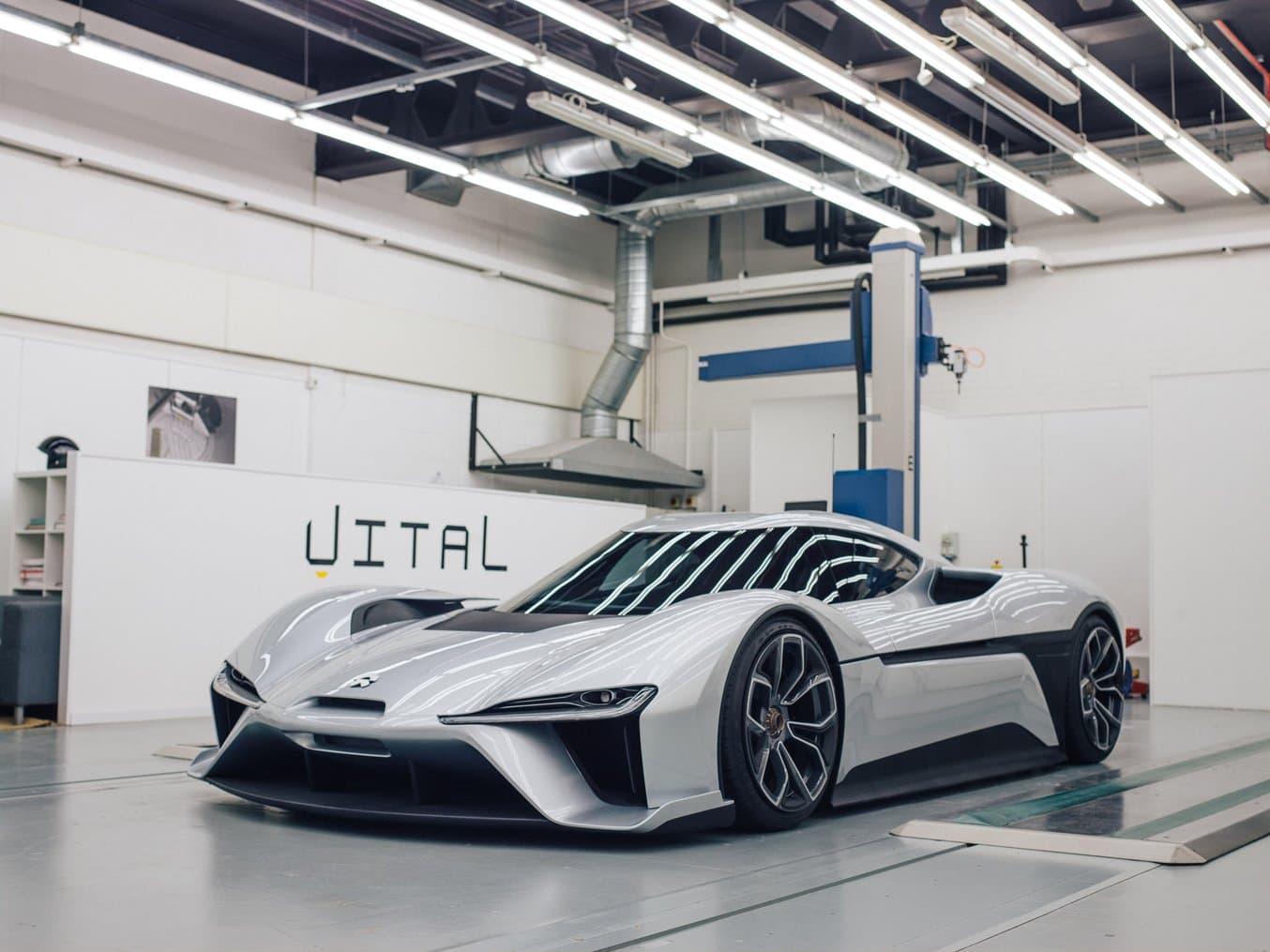
Vital Auto wurde 2015 gegründet, als sich drei Freunde dazu entschlossen, zu kündigen und gemeinsam ein Unternehmen zu gründen – passenderweise in einer Garage. Einer der ersten Aufträge des Unternehmens kam für den Konzept-Supersportwagen NIO EP9. Dabei musste das Team gleich extrem realistische Fahrzeugteilprototypen mit hoher Originaltreue anfertigen.
Abhängig vom jeweiligen Kunden und Projekt setzt das Team bei einer einfachen Zeichnung auf Papier an oder bei einem fertigen Fahrzeugentwurf. Es entwickelt Autos von Grund auf, entwirft alle Rahmen, alle Außen- und Innenelemente, Ein- und Ausstiege, Klappen und Öffnungen sowie interaktive Elemente. Zwischen 5 und 30 Leute arbeiten an einem einzelnen Konzept. Ein durchschnittliches Projekt dauert etwa drei bis zwölf Monate.
In einer solchen Zeit durchläuft ein typisches Präsentationsauto bis zu ein Dutzend Designiterationen. Wobei zu jeder oftmals weitere Iterationen kleinerer Komponenten gehören, bis das Design ganz den Vorstellungen des Kunden entspricht.
„Es gehört zu unserer Branche, ein Produkt anhand der virtuellen Eigenschaften zu bewerten, bevor es auf den Markt gelangt. Jedoch glaube ich, dass auch handfeste Teile immer einen gewissen Stellenwert einnehmen werden. Es geht einfach nichts darüber, ein Objekt in seiner Hand zu halten, es zu fühlen, das korrekte Gewicht zu spüren – mit den korrekten Proportionen und der Dynamik, mit der die reale Umgebung die Auffassung des realen Objekts beeinflusst“, so Moradi.
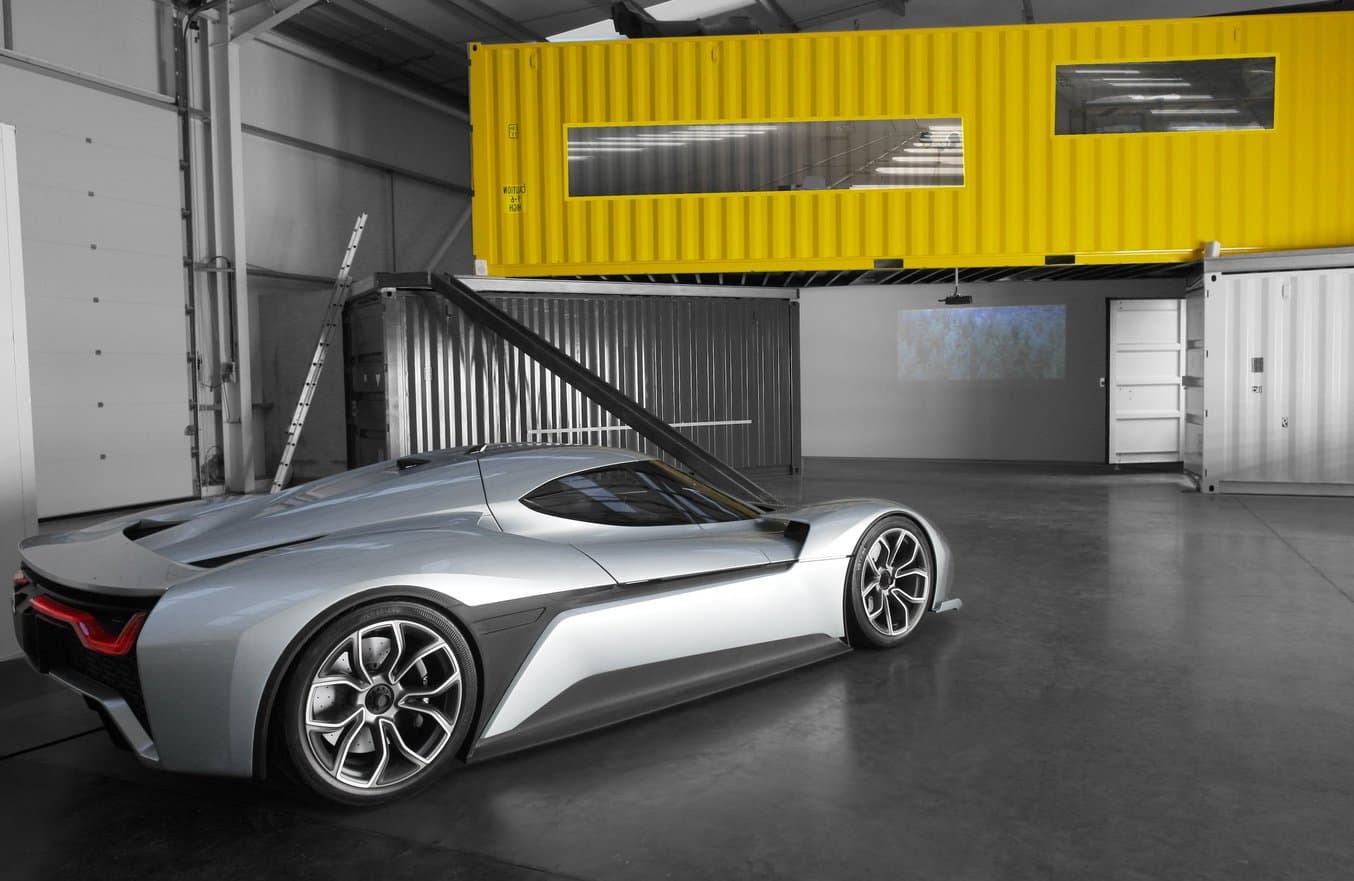
„Die meisten unserer Kunden kommen mit einer neuartigen Idee zu uns, einer Innovation, etwas, das es noch nie gab. Also sehen wir uns jeden Tag neuen Herausforderungen gegenüber, die kein Ende nehmen“, erklärt Anthony Barnicott, Design Engineer und Leiter der additiven Fertigung. „Diese Herausforderungen reichen von der Produktion der gewünschten Teilanzahl in der gegebenen Zeit bis zur Nachhaltigkeit des Produkt oder zum Erreichen des gewünschten Gewichts trotz bestimmter Leistungsanforderungen.“
Herkömmliche Präsentationsautos werden normalerweise nur aus Ton gefräst. Das Team verwendet darüber hinaus aber auch Drei- und Fünf-Achsen-CNC-Fräsmaschinen, Handmodellierung, handgefertigte Tonmodelle und glasfaserverstärkte Verbundwerkstoffe. Diese traditionellen Prozesse sind jedoch oft nicht ideal für die Produktion maßgefertigter Teile für Einmalkonzepte.
„Wir nutzen 3D-Druck schon vom ersten Tag an. Wir wollten ihn in unseren Fertigungsprozess integrieren, nicht nur, um die Kosten zu senken, sondern auch damit wir den Kunden mehr Abwechslung und Vielseitigkeit bieten, was Designs und Ideen angeht“, gibt Barnicott an.
Heute leitet Barnicott eine ganze 3D-Druckabteilung mit zehn großformatigen FDM-Druckern, drei großformatigen SLA-Druckern des Typs Formlabs Form 3L und fünf SLS-Druckern des Typs Fuse 1.
„Was die Kapazität angeht, laufen all diese Drucker rund um die Uhr immer auf 100 %, und das von Anfang an. Wir setzen die Drucker in allen Bereichen unserer Konzepte und Designs ein. Üblicherweise nutzen wir den Fuse 1 dabei für unsere Produktionsteile und den Form 3L für unsere Konzeptteile“, erklärt Barnicott.
Die Herstellung komplexer Designs aus mehreren Materialien mit dem Form 3L
„Wir nutzen den Form 3L für alles, das eine erstklassige Oberfläche benötigt. Im Automobilkontext also im Innenbereich für Teile, die nicht mit Leder oder Alcantara oder sonstigem Stoff verkleidet werden. Die Materialien von Formlabs geben uns dabei eine schöne, glatte Oberfläche, mit der unsere Lackierer arbeiten können. Wir setzen die Teile direkt aus dem Drucker in das Fahrzeug ein“, erläutert Barnicott.
„Was mir am Form 3L am besten gefällt, ist dessen Vielseitigkeit, dass ich ein Material in weniger als fünf Minuten wechseln kann. Die große Bandbreite dieser Materialien von weich und flexibel bis hart und robust ist für uns ebenfalls von unschätzbarem Wert“, hebt Barnicott hervor.
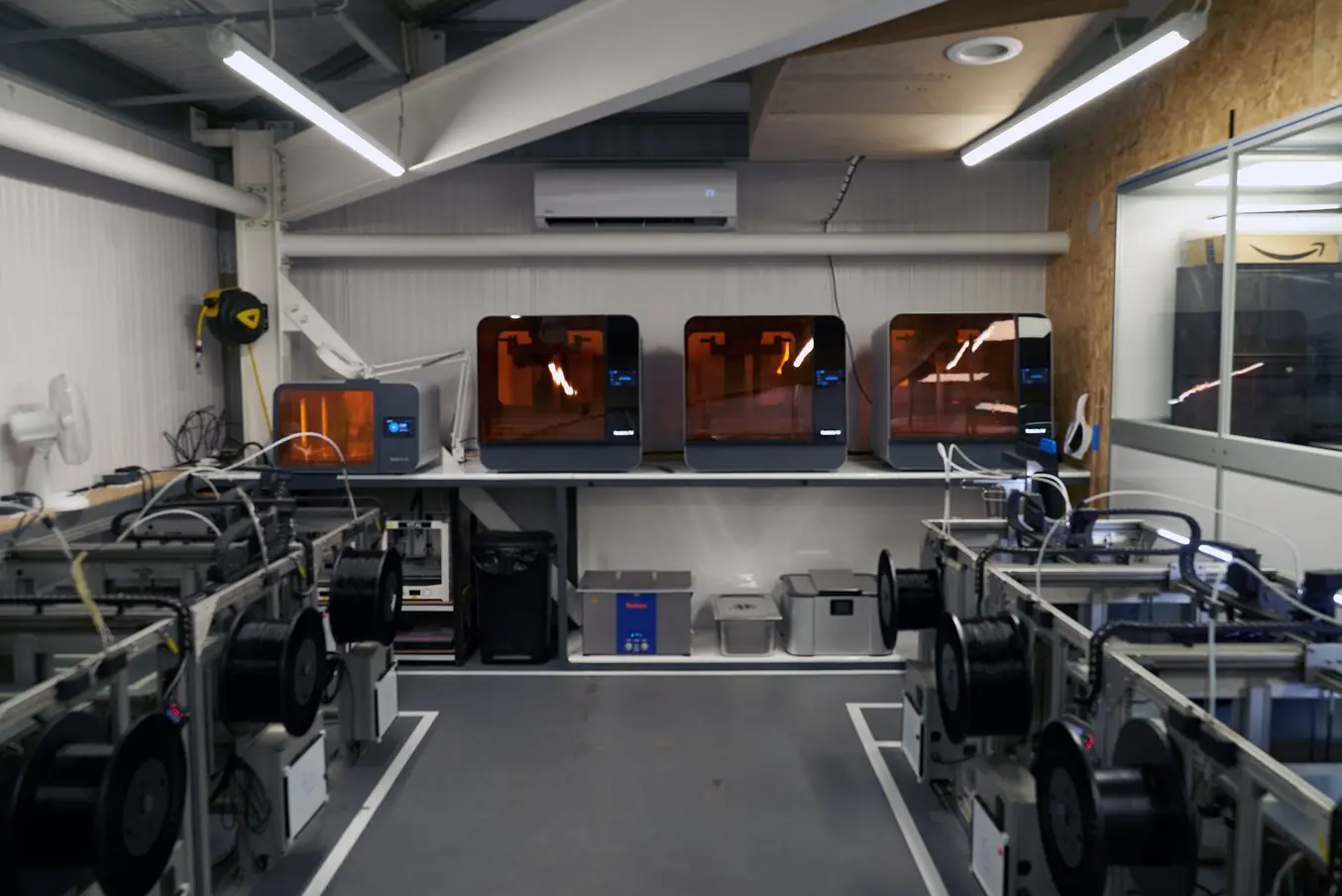
Das Team nutzt den Form 3L mit verschiedenen Materialien für zahlreiche Anwendungen. Hier sind einige Beispiele:
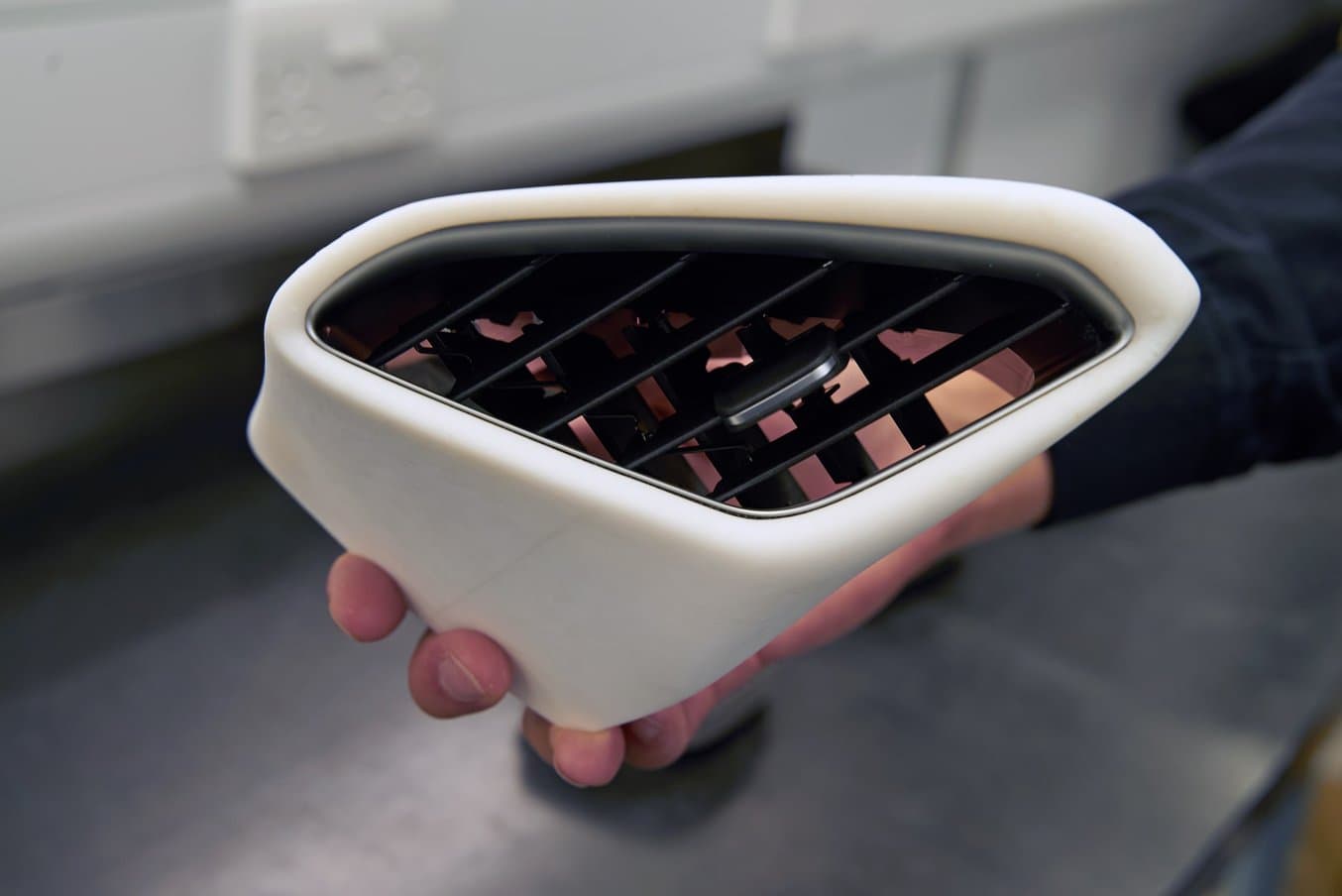
Lüftungen
„Als Unternehmen haben wir oft die Herausforderung, dass Kunden mit einem Produkt zu uns kommen, das ihnen nicht gehört, es aber in ihre eigenen Designs einarbeiten wollen. Einmal brachte uns ein Kunde die Lüftungsöffnung eines anderen Fahrzeugs und wollte sie in seinem eigenen Innenraum verbauen. Wir haben das Teil 3D-gescannt und so digital nachgebaut. Danach haben wir eine neue Außenhaut dafür erstellt. Zuerst verwendeten wir dafür Draft Resin, um das Design zu testen und es vom Kunden prüfen zu lassen. Danach sind wir zu White Resin übergegangen, um ein produktionsfertiges Teil herzustellen.“
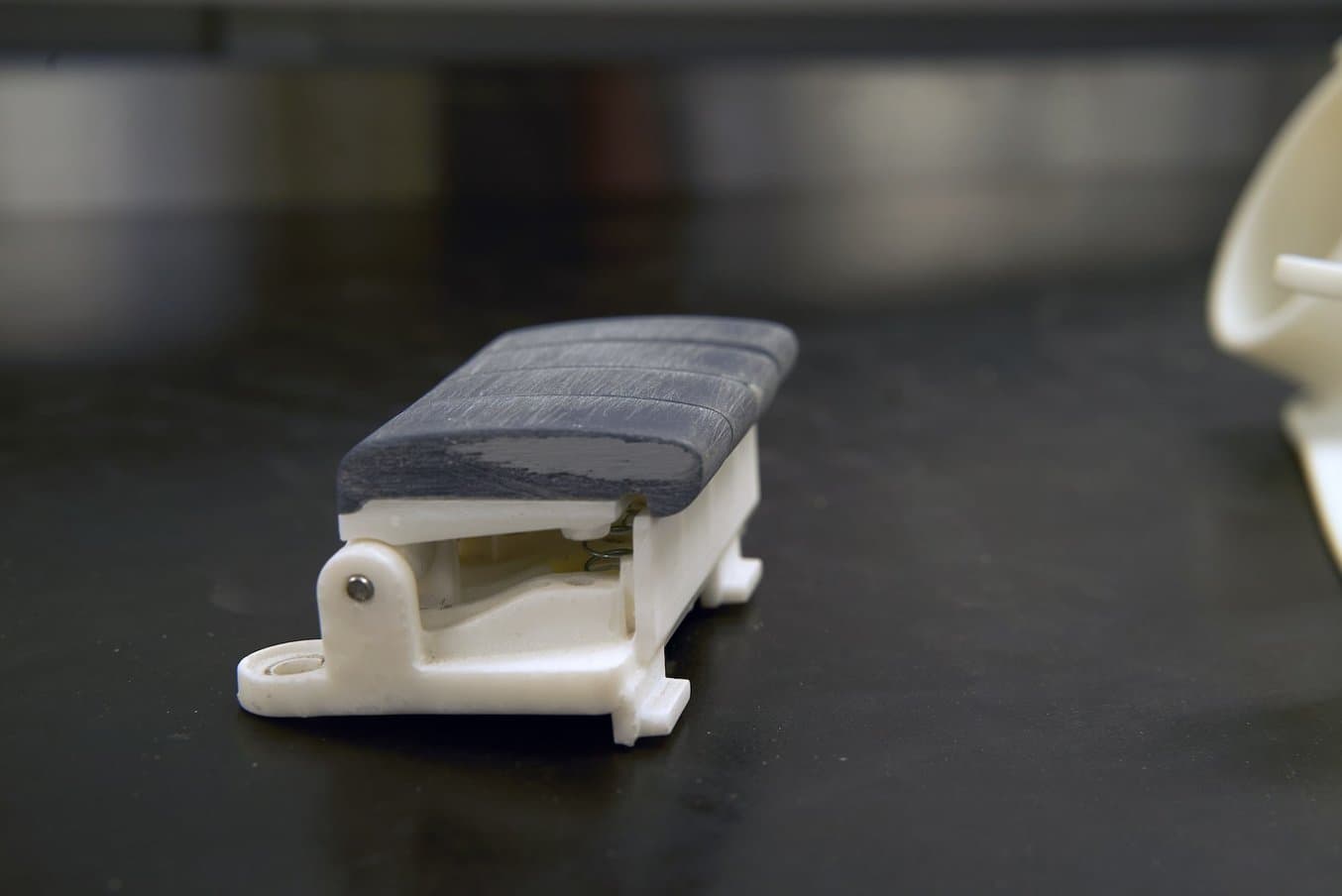
Schalterelemente
„Wenn wir mit unglaublich filigranen Designs arbeiten, wie z. B. bei Schalterelementen, dann verwenden wir mehrere Materialien, um ein mechanisches Produkt zu schaffen, dass nicht nur korrekt funktioniert, sondern auch in der realweltlichen Umgebung eingesetzt werden kann. [Für diese Schalterelemente] haben wir harte Materialien wie Tough 2000 Resin für die Oberfläche verwendet und leichtere, kostengünstigere Materialien für den Innenbereich.“
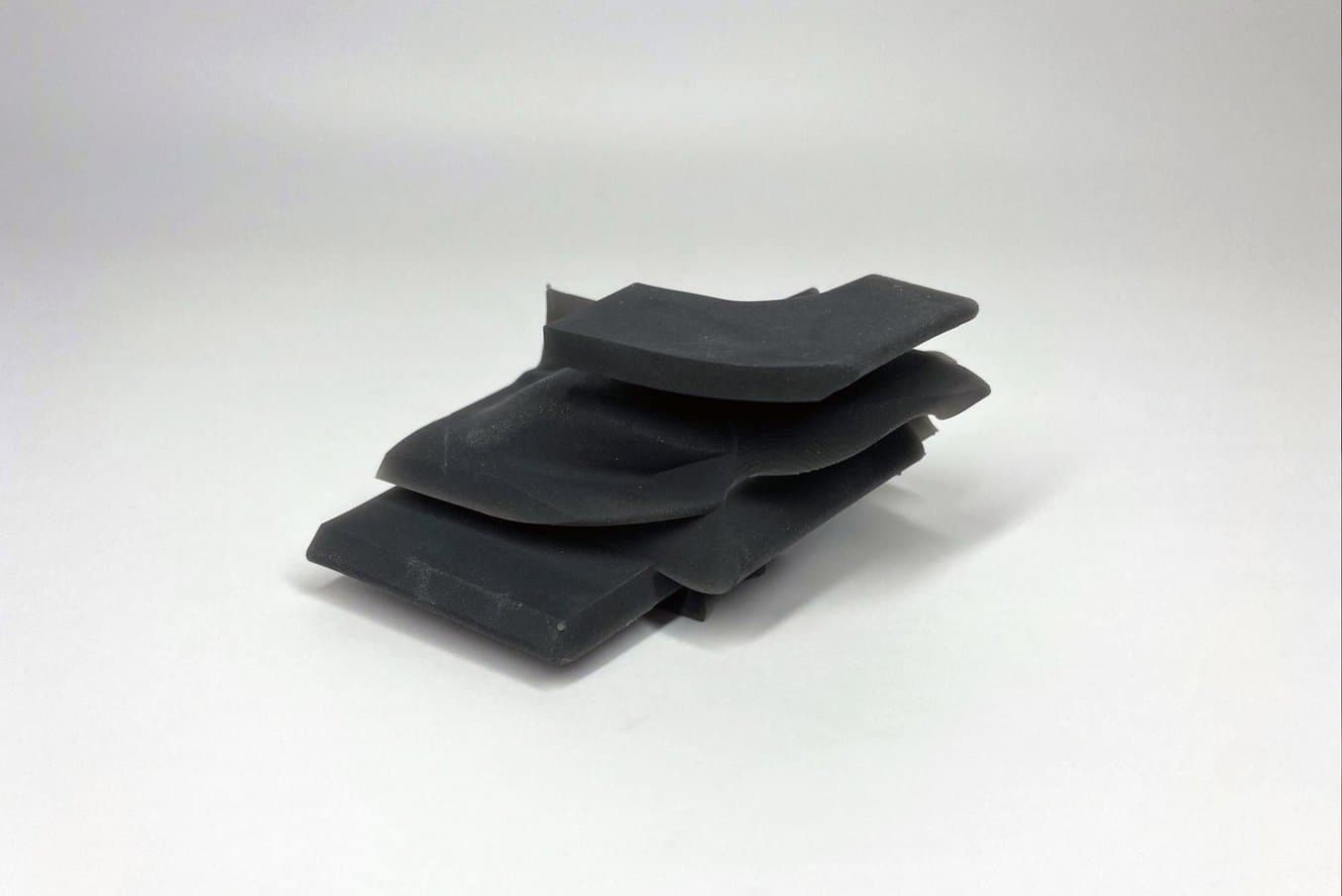
Türdichtungen
„Die Produktion von Türdichtungen im Automobilbereich ist üblicherweise unglaublich kostspielig. Es gibt einfach keine alternative Fertigungsmethode zur Extrusion. Das bedeutet nicht nur extrem hohe Werkzeugbestückungskosten, sondern auch lange Durchlaufzeiten. Wir konnten aber mit einem von Formlabs' neuesten Materialien experimentieren: Flexible 80A Resin. Mit dem Form 3L konnten wir Abschnitte dieser Türdichtungen über Nacht produzieren und verschiedene Geometrien testen. Dabei lag der Druck innerhalb von 50 Mikrometern vom ursprünglichen Design.“
Dank des Form 3L kann das Team mehrere Iterationen der Teile produzieren, meistens schon in 24 Stunden. Es erwarb drei verschiedene Geräte, um bis zu drei Iterationen desselben Teils gleichzeitig zu produzieren – oft auch aus drei unterschiedlichen Materialien. Die Kosteneinsparungen kann es dann an den Kunden weitergeben oder als Mehrwert in Form verschiedener Designpräsentationen zum selben Preis anbieten.
„Mit das Beste an der Arbeit mit der additiven Fertigung ist die Verringerung des Zeitaufwands. Was macht man also mit der gewonnenen Zeit? Für uns ist es eine Art Erweiterung der Möglichkeiten. Wir überlegen uns mehr Alternativen, mehr Iterationen und drehen die Prozessspirale weiter“, so Moradi.
„Es gibt so viele Produkte, die wir ohne unseren Form 3L gar nicht herstellen könnten. Mit einigen der fortschrittlichsten Fertigungsverfahren wie beispielsweise Sieben-Achsen-CNC-Fräsen könnten wir diese Teile wohl anfertigen, aber das wären riesige, unwirtschaftliche Kosten“, sagt uns Barnicott.
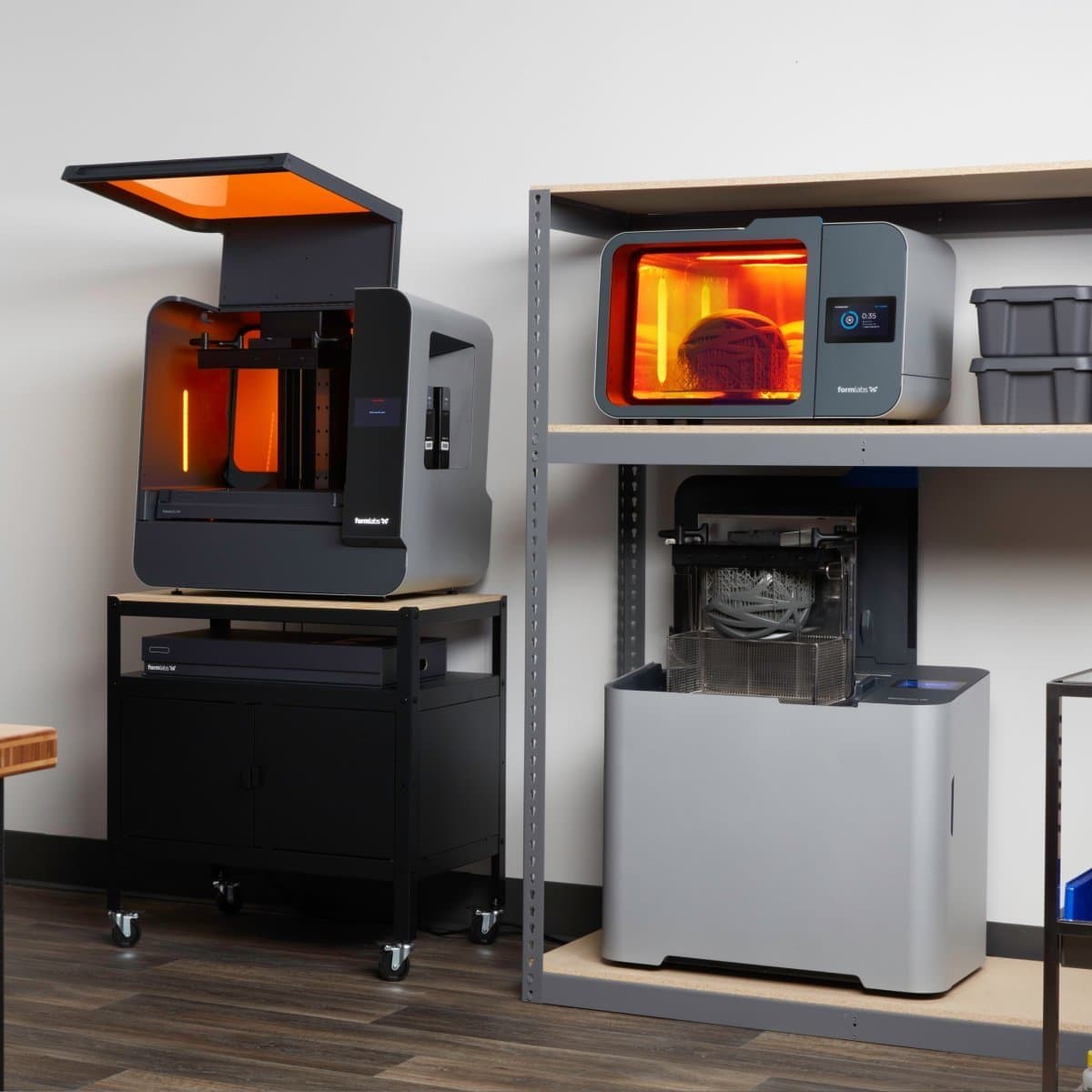
Vorführung des Ecosystems des Form 3L
Möchten Sie mehr über das Ecosystem des Form 3L und Form 3BL und die neuen großformatigen Nachbearbeitungsgeräte erfahren? In dieser Vorführung zeigen Ihnen Kyle und Chris den Arbeitsablauf des Form 3L von Anfang bis Ende, Nachbearbeitung eingeschlossen.
Unterstützung der CNC-Bearbeitung mechanischer Teile durch den Fuse 1
„Der Fuse 1 war unser erster Berührungspunkt mit SLS-Technologie. Als Kleinunternehmen hätten wir nie geglaubt, diese Technologie jemals selbst vor Ort zu haben. In Form des Fuse 1 haben wir jetzt nicht nur ein solches Gerät, wir haben gleich fünf vor Ort. Mithilfe dieser Geräte produzieren wir strukturelle mechanische Teile in sehr kurzer Zeit. Nicht nur für Tests, sondern direkt für die Anwendungen vieler unserer Konzepte. Dieser Prozess wäre sonst üblicherweise mittels CNC-Bearbeitung durchgeführt worden, entweder direkt bei uns oder außer Haus. Das hängt von der Geometrie ab. Und dann müssten wir zwei bis vier Tage warten, bis wir die Teile endlich in der Hand halten. Dank des Fuse 1 schaffen wir alles vor Ort und halten die Teile in den meisten Fällen schon nach 24 Stunden in den Händen“, berichtet Barnicott.
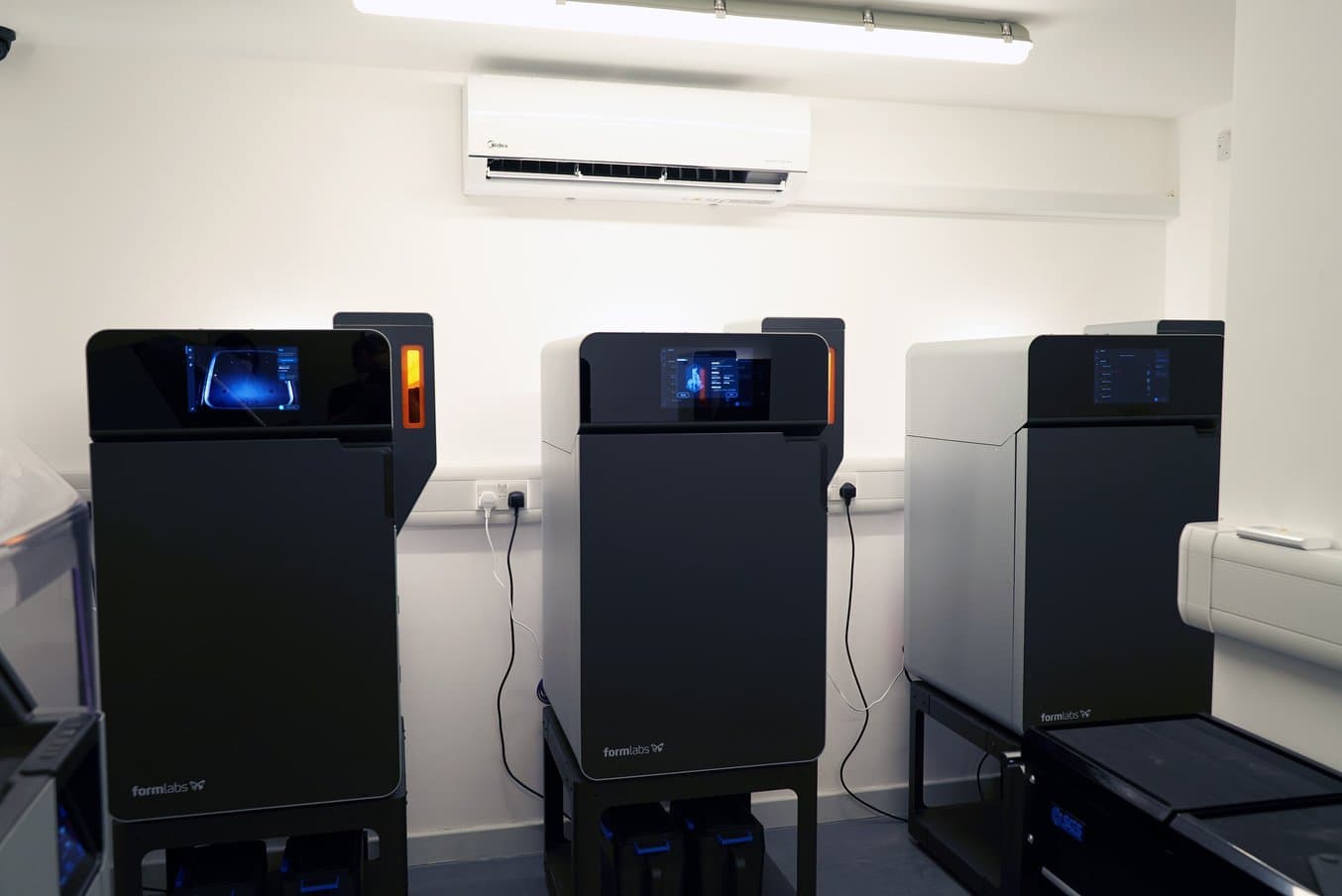
Das Team benutzt den Fuse 1 zumeist für mechanische Teile wie etwa Türscharniere, Türgriffkolben, das Innenleben der Türen und strukturelle Anwendungen. Die Teile kommen direkt nach dem Druck zum Einsatz, mit minimaler Fertigstellung. Das Team hat den Fuse 1 unter anderem für folgende Anwendungen eingesetzt:
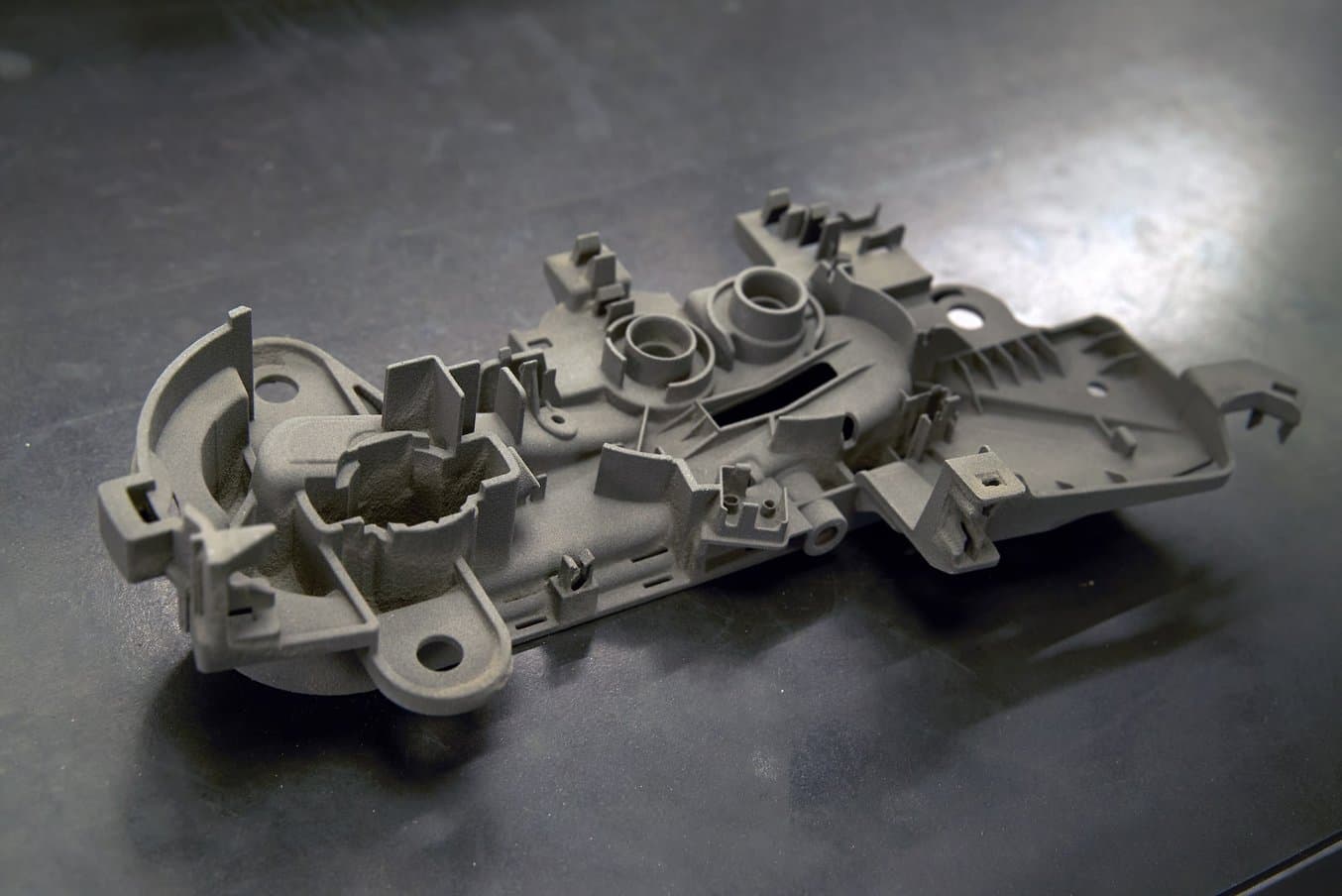
Luftkanal
„Viele Innenteile im Automobilbereich sind schwer zu produzieren, wenn man nicht auf traditionellen Spritzguss zurückgreift. Dazu zählen beispielsweise interne Luftkanäle und Belüftungsöffnungen. Die sieht man nicht, ihre Produktion kostet jedoch einiges. Wir stellen diese Teile mit dem Fuse 1 her. So sind wir viel flexibler bei den Designs, die wir im Fahrzeug verbauen, ganz ohne die typischen exorbitanten Kosten.“
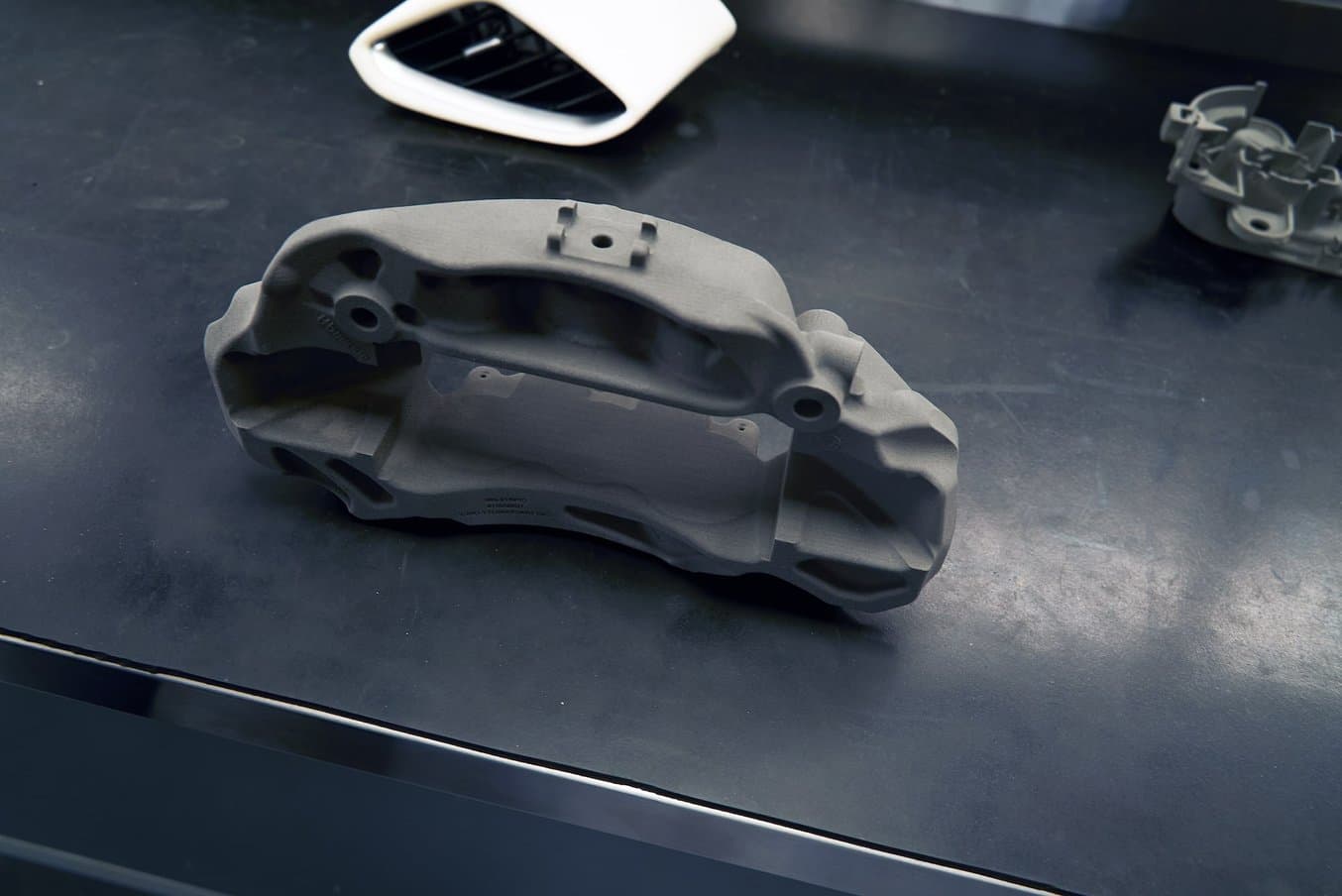
Bremssattel
„Manchmal produzieren wir die Teile nur, weil der Kunde sein Logo auf eben diesem Teil sehen möchte. Für uns heißt das, dass wir die Teile relativ schnell umsetzen müssen, damit wir noch das Kundenbranding anbringen können. Für solche Teile nutzen wir auch den Fuse 1, wie z. B. für einen Bremssattel. Dabei können wir das Logo an unterschiedlichen Stellen des Bremssattels anbringen oder in unterschiedlichen Farben und der Kunde prüft das anschließend.“
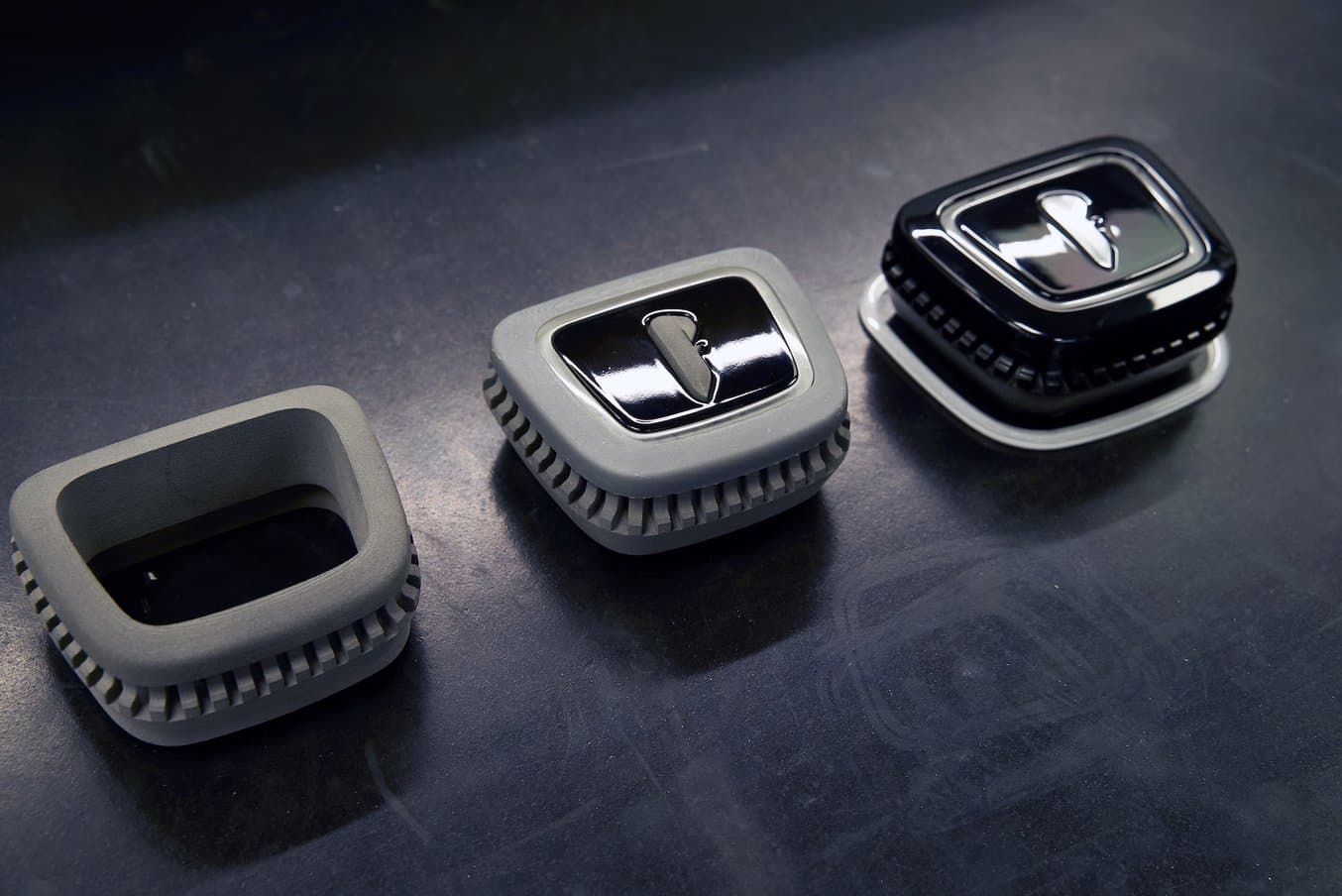
Interaktive Konzepte für einen Supersportwagen
„Dank des 3D-Drucks konnten wir bei einem spezifischen Projekt SLA und SLS kombinieren und uns durch verschiedene Designiterationen arbeiten. Wir konnten schnell unterschiedliche Iterationen produzieren, beide Prozesse kombinieren und für spezielle Eigenschaften nutzen, um zum fertigen Design zu gelangen. Dabei handelt es sich um alles Mögliche, von mechanischen Teilen bis zu transparenten Teilen, um die optische Qualität und die Leistung zu prüfen.“
Es wird oft behauptet, additive Fertigung würde subtraktive Fertigung ganz ersetzen. Bei Vital Auto sieht man jedoch die Vorteile beider Technologien, um die jeweils besten Eigenschaften auszunutzen.
„Wir verwenden beide Prozesse im Einklang, damit sie sich gegenseitig unterstützen. Wir haben recht viele Teile, bei denen subtraktive Fertigung zum Einsatz kommt und für die dann filigranere Details mithilfe additiver Fertigung hergestellt werden. Das macht die Produktion vieler unserer Konzeptmodelle wesentlich kostengünstiger“, führt Barnicott an.
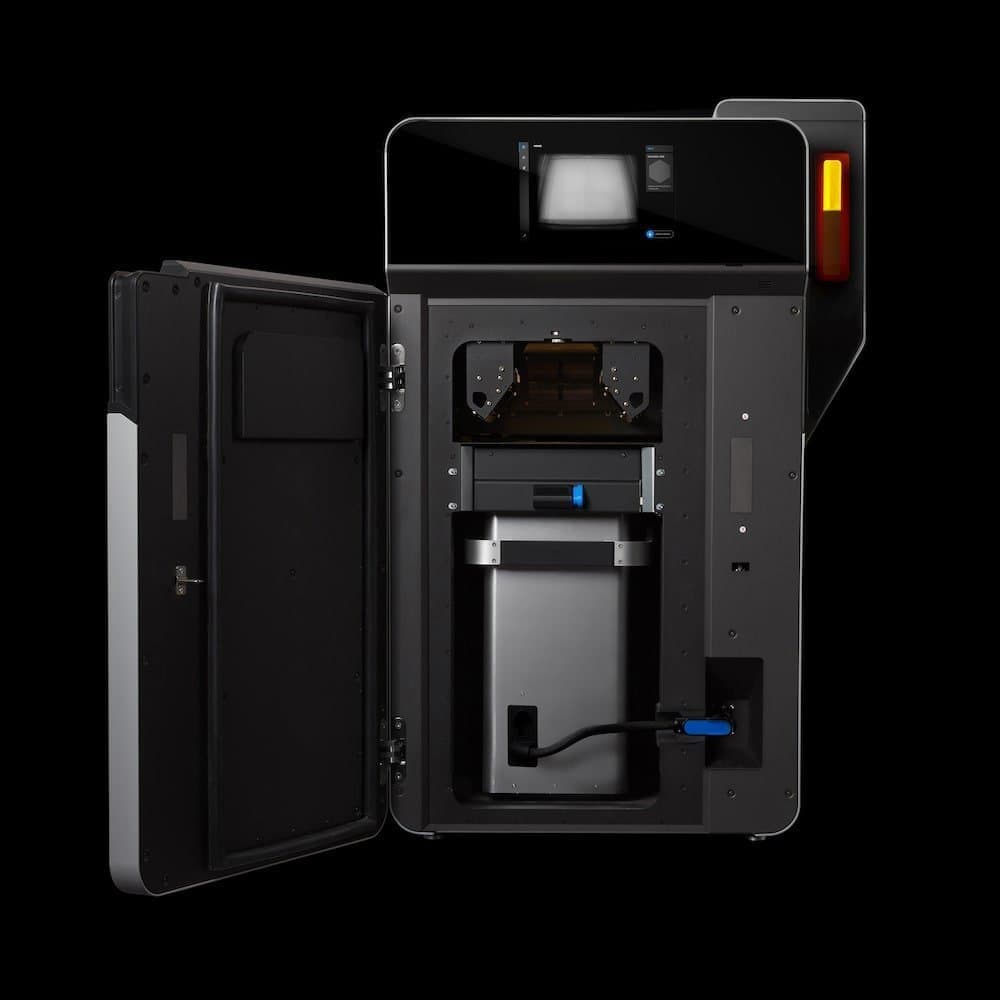
Produktvorführung des Fuse 1
Schauen Sie unsere Produktvorführung, in der Ihnen die Experten von Formlabs den Fuse 1 und den SLS-3D-Druck erklären.
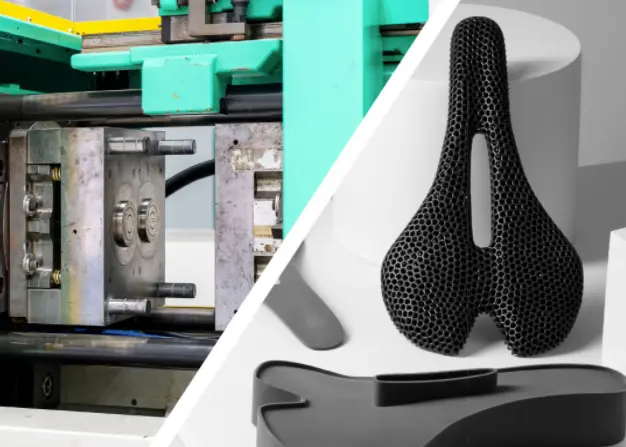
SLS-3D-Druck oder Spritzguss: Wann sollte man Spritzgussteile durch 3D-Druck ersetzen?
In diesem Whitepaper werden der Spritzguss und seine Vor- und Nachteile erörtert sowie der SLS-3D-Druck und die Anwendungen vorgestellt, bei denen er als ergänzende Technologie eingesetzt werden kann.
Die Erstellung originalgetreuer Konzeptfahrzeuge mithilfe des 3D-Drucks
„Die Fortschritte der letzten 10 Jahre in der Technologie und im 3D-Druck sind phänomenal. Als ich damals angefangen habe mit diesen Kleinserien für Nischenfahrzeuge, da wären einige der heute hergestellten Produkte undenkbar gewesen. Und heute kann ich diese Teile nicht nur herstellen, es kostet mich auch noch sehr wenig und geht sehr schnell“, meint Barnicott.
Der 3D-Druck erstellt für das Team nicht nur bessere Produkte in kürzerer Zeit, er zieht auch neue Kunden an. Viele Kunden kommen gerade deshalb zu Vital Auto, weil sie mit den neuesten Technologien arbeiten möchten und weil die Produkte aus den neuesten Hochleistungsmaterialien bestehen sollen.
„Es gibt ein paar Dinge, die man einfach nicht mehr als aufkeimende Technologien klassifizieren kann. 3D-Druck ist eines davon. Er ist so weit fortgeschritten, dass alle von uns produzierten Waren gut genug für die letztendliche Präsentationsphase sind, mit allen zusätzlichen Herstellungsschritten die darauf noch folgen. 3D-Druck ist von einer Quasi-Neuheit zu etwas geworden, das aus unserer Arbeit nicht mehr wegzudenken ist“, so Moradi.