Wie Makra Pro ein patentiertes Verfahren zur Schaumformung mit dem 3D-Druck entwickelte
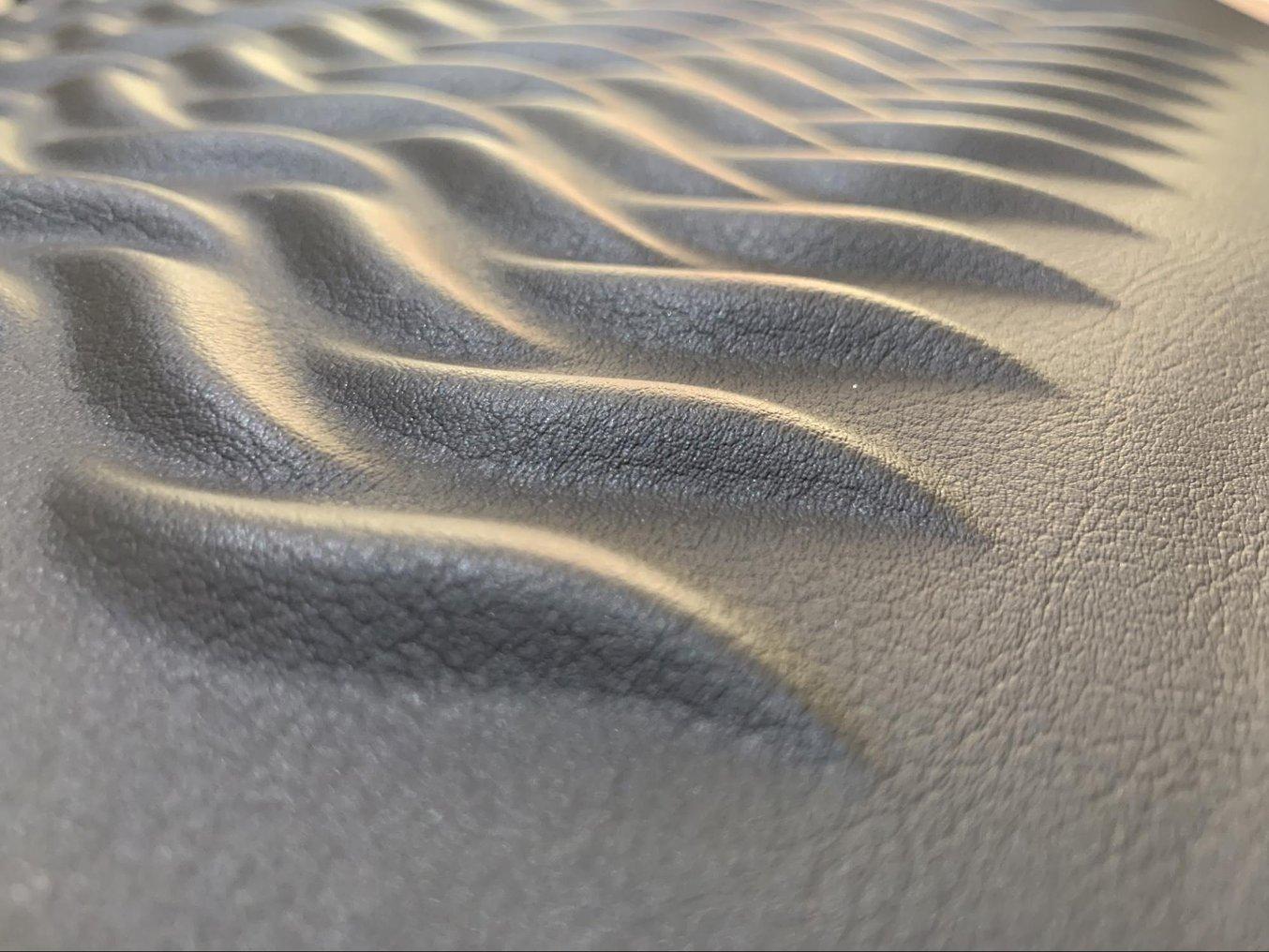
Die Anfrage eines namhaften Motorradherstellers öffnete an einem Freitagnachmittag im Juni 2018 bei Makra Pro die Tür für den 3D-Druck. Besagter Motorradhersteller versprach einen Großauftrag für Schaumteile von Motorradsitzen, wenn die Sitzwanne aus Kunststoff mitgeliefert würde. Damit wurde der Ehrgeiz und das Gespür für Innovationen von Matthias Krabel, Geschäftsführer von Makra Pro, geweckt.
Die Materialeigenschaften der Sitzwannen sollten dem Serienmaterial dabei sehr ähnlich sein, da diese für Testfahrten verwendet werden sollen. Für dieses Projekt kam bei Makra Pro zum ersten Mal der 3D-Druck zum Einsatz. Nach einiger Recherche im Internet fiel die Entscheidung auf den Form 2 mit Durable Resin, da dieses ähnliche Eigenschaften wie Polypropylen besitzt.
Dank des unermüdlichen Einsatzes unseres Vertriebs und des tatkräftigen Engagement unseres Kundenservices (falls es technische Hürden zu überwinden galt) wurde die Druckerflotte schnell auf 5 Form 2 erweitert und der Auftrag erfolgreich erfüllt. Dabei haben die Formlabs 3D-Drucker mit dem Material in vollem Maße überzeugt, sodass keine alternativen 3D-Drucker mehr in Frage kamen und das Ganze den Beginn einer langen Erfolgsgeschichte markierte.
Vom Prototyping über die Werkzeugentwicklung bis zur Vorserienfertigung
Inzwischen kommen bei Makra Pro 10 Form 2 und 8 Form 3 regelmäßig zum Einsatz. Je nach Auftragslage gibt es dabei Wochen, in denen alle 18 Drucker laufen und Rund um die Uhr Teile gedruckt, gewaschen und nachgehärtet werden. Makra Pro hat sich zur Innovationsschmiede im mittelfränkischen Markt Taschendorf entwickelt. Dabei hat sich das Team um Matthias Krabel smartes und schnelles Prototyping auf die Fahnen geschrieben.
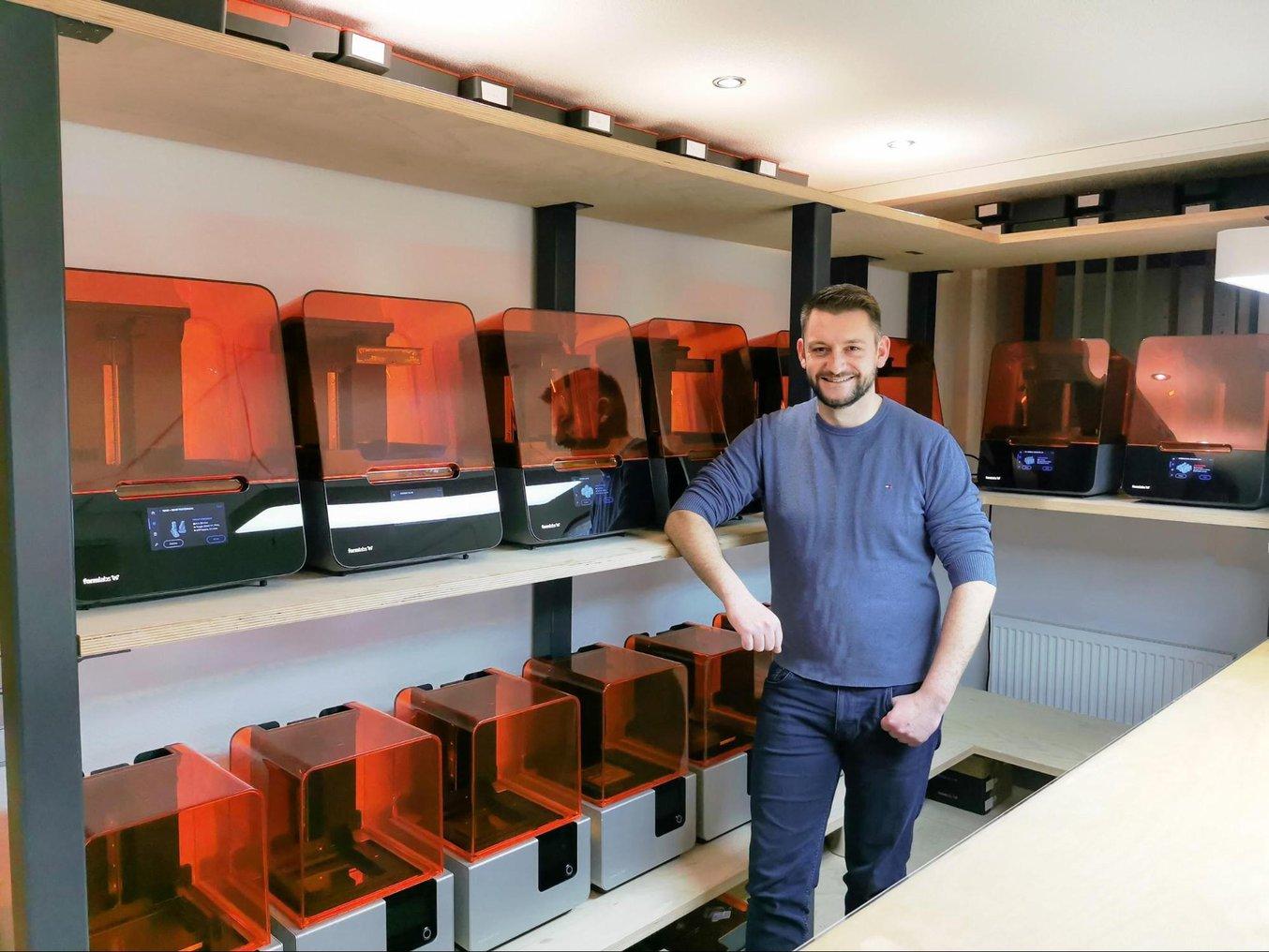
Matthias Krabel zeigt die Druckfarm von Makra Pro mit 18 3D-Druckern.
Der Fokus ihrer Arbeit liegt auf Prototypen- und Werkzeugentwicklung sowie der Vorserienfertigung, die mit Hilfe des 3D Drucks verbessert werden. Dabei werden nicht nur bestehende Verfahren verbessert, sondern auch komplett Neues entwickelt und etabliert. Inzwischen gehören Kunden aus verschiedensten Branchen wie dem Automobilbereich, der Medizintechnik, dem Agrarbereich und vielen mehr zu den Kunden von Makra Pro.
Die größte Herausforderung in der täglichen Projektentwicklung liegt in der Unsicherheit, ob die Ideen so umgesetzt werden können wie diese sich in den Köpfen des Teams entwickeln. Allerdings hilft das Durchhaltevermögen und der Willen zur Problemlösung immer eine passende Lösung oder Idee zu entwickeln. Auf den Desktop-3D-Druckern lassen sich diese schnell validieren und können notfalls angepasst werden.
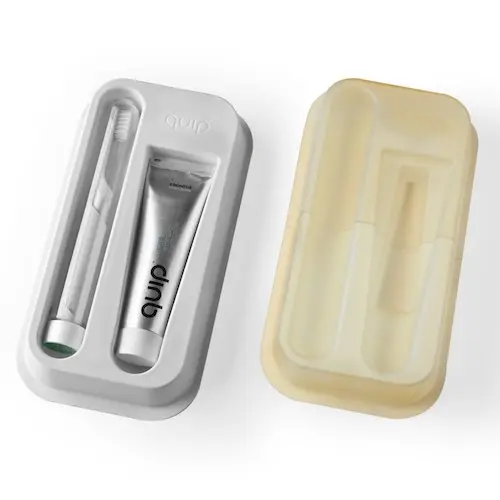
Formenherstellung mit 3D-Druck
Haben Sie Interesse an anderen Anwendungen von 3D-gedruckten Formen? Laden Sie unser Whitepaper herunter, welches unter anderem das Thermoformen und Gießen mit Elastomeren behandelt.
Ein neues Verfahren zur Schaumformung mit 3D-Druck
Die letzte Innovation von Makra Pro, welche mit den Formlabs 3D-Druckern realisiert wurde hat jetzt sogar zur Patentierung des Verfahrens geführt. Auch dabei wurde ein etabliertes Verfahren mit Hilfe des 3D-Drucks verbessert.
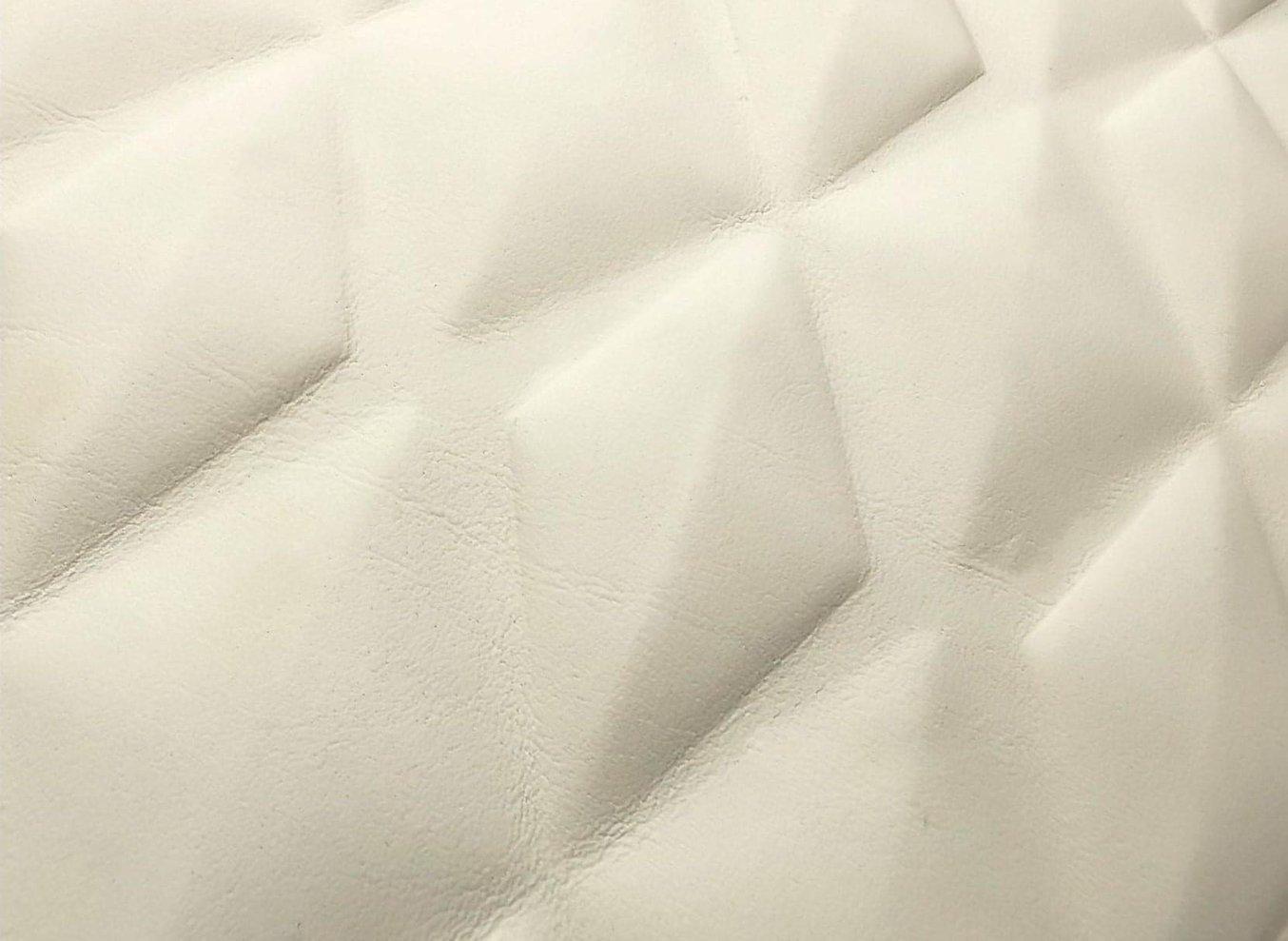
3D-Leder im Detail.
Echtes Leder ist eine sehr gefragtes Material unter anderem für Ausstattungen im Interieur von Fahrzeugen oder auch in der Inneneinrichtung von Immobilien. Deshalb wird Leder oft geprägt, bestickt oder kaschiert um gewünschte Muster zu erzielen. Das Team um Makra Pra stand aber vor der Herausforderung, dass eine 3D-Optik der Lederbezüge erzielt werden sollte, welches eine sehr große Herausforderung darstellte, da Echtleder nur schwer dehnbar ist.
Die bahnbrechende Idee kam Gründer und Geschäftsführer Matthias Krabel bei der Waffelzubereitung für das Frühstück am Sonntag. Ließe sich das Leder nicht mit Hilfe von Schaum, der sich in der Form verteilt wie der Waffelteig in Form bringen? Diese Idee wurde schlussendlich in die Tat umgesetzt und validiert.
Als erstes werden die Formen für das Werkzeug auf dem Form 3 mit einem eigens entwickelten Material gedruckt. Diese Formen werden in das Werkzeug eingesetzt, mit Leder ausgelegt und dann mit dem Schaum für die Formgebung ausgespritzt. Wenn das Werkzeug dann geschlossen wird und der Schaum aushärtet entsteht die 3D-Optik des Leders.
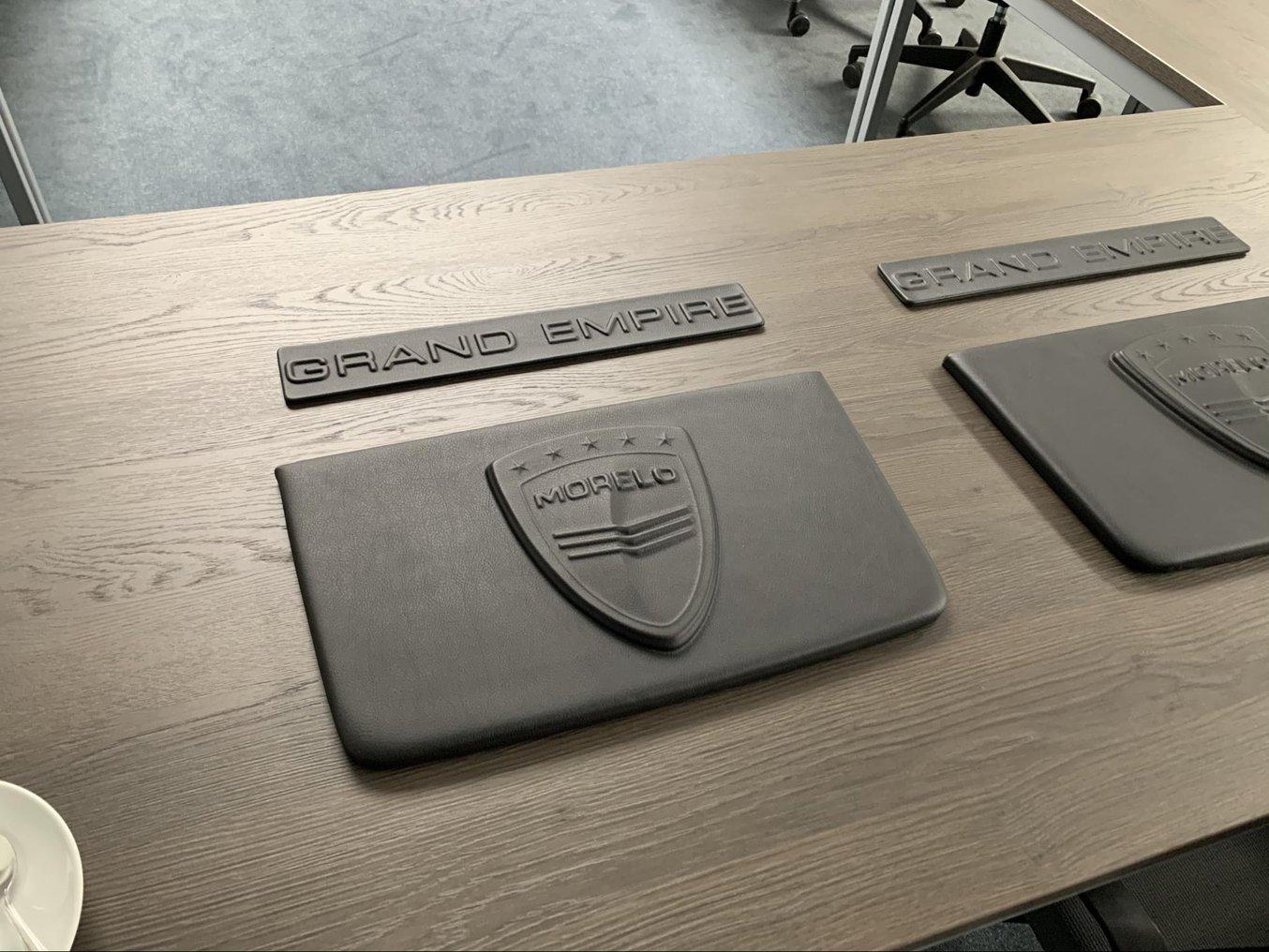
Individuelles 3D-Lederteilverfahren für ein von Morelo hergestelltes Luxus-Wohnmobil.
Die fertigen Lederteile werden dann beispielsweise auf die Türverkleidung im Auto aufgezogen oder auf dem Sitzbezug im Fahrzeug angebracht. Ein internationaler Veredler und Tuner von hochklassigen Automobilen setzt die Lederteile bei seiner Arbeit im Interieur der Fahrzeuge ein und wollte diese auf dem diesjährigen Genfer Autosalon dem Publikum präsentieren.
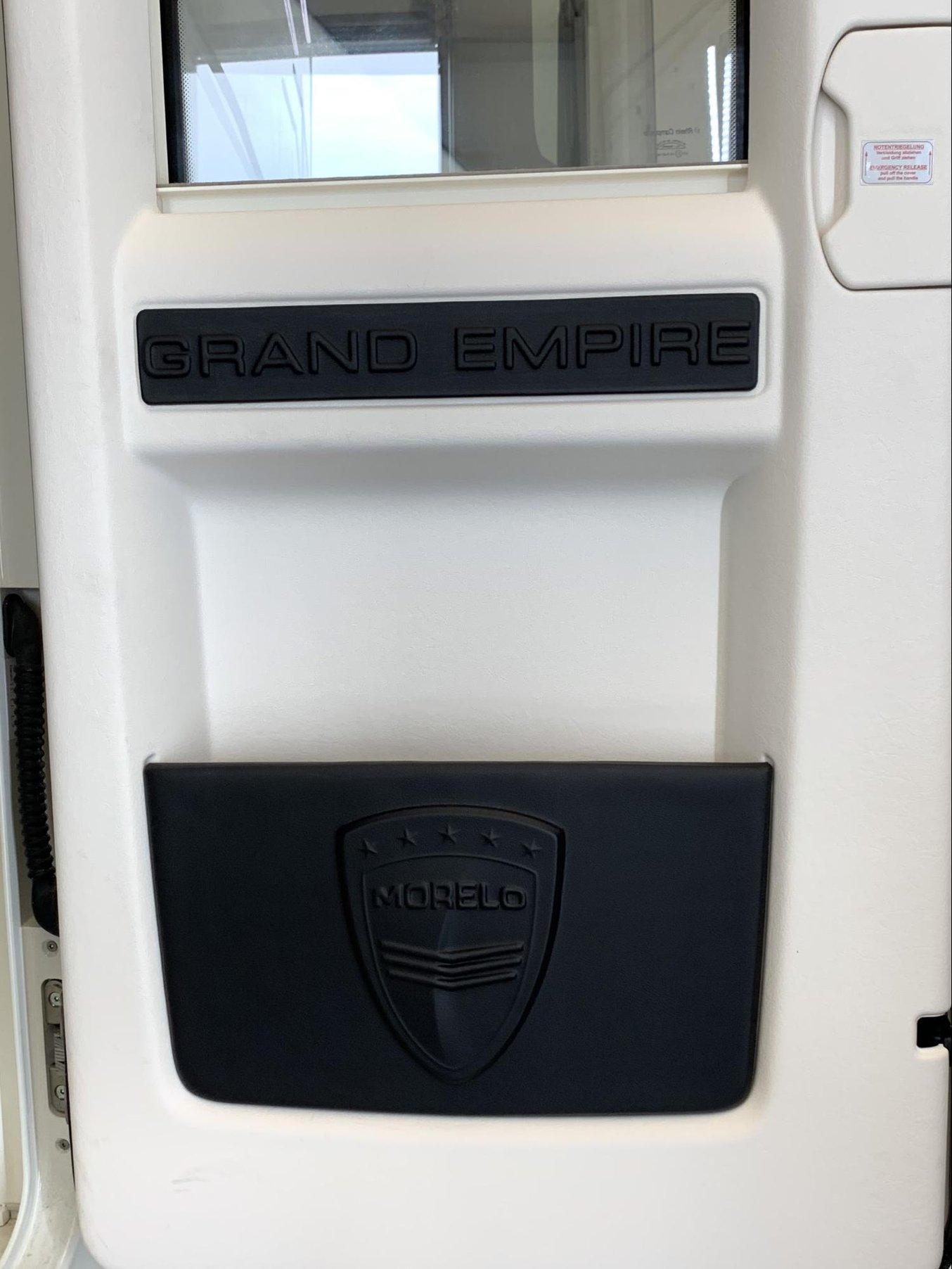
Die 3D-Leder-Teile eingesetzt in der Tür des Luxus-Wohnmobils.
Oft sind die Ausprägungen des Leders auf Kundenwunsch sehr filigran und kaum wahrnehmbar. Deshalb können Sie dank der Genauigkeit der LFS-Technologie (Ein Formlabs Patent) nur mit den 3D-gedruckten Werkzeug realisiert werden.
Da die Endteile des Leders meistens größer als die Form 3 Drucker sind, werden die Formen in mehreren Teilen gedruckt und dann im Werkzeug zusammengesetzt. Die größte Form bestand aus 160 Einzelteilen. Die Einzelteile werden dabei manchmal im Werkzeug zusammengeklebt. Oftmals wird das leder aber mit einer losen Form bearbeitet, um Teile der Form schnell und unkompliziert wechseln und personalisieren zu können. Allerdings ist die Variante mit den losen Formteilen sehr schwierig und erfordert viel Feinmotorik und Erfahrung.
Aufgrund der stetigen Weiterentwicklung der Formlabs-Produkte, vor allem im Materialbereich, kommen Matthias Krabel ständig neue Ideen, sodass wir noch viele spannende Projekte erwarten dürfen.