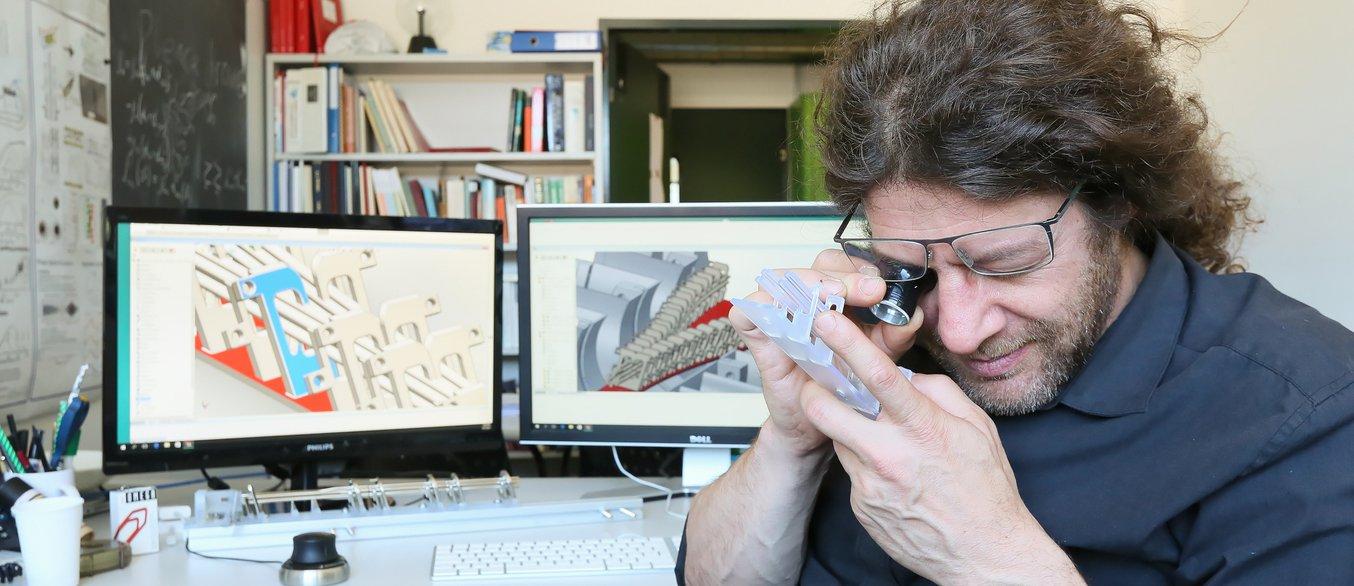
Andreas Osterwalder nennt sein Büro ein Museum: Was wie eine Sammlung von kleinen Maschinen aussieht, sind teilweise metallbeschichtete – genauer: galvanisierte – 3D-Drucke, die der Forscher für seine Experimente an der Schweizer Eidgenössischen Technischen Hochschule in Lausanne (EPFL) nutzt.
Ein Versuchsaufbau wie Osterwalders Strahlteiler fungiert als eine hochkomplexe Maschine. Zwischen der Forschungsidee und dem eigentlichen Experiment können Monate oder sogar Jahre liegen. Ein Engpass stellt oft die eigentliche Fertigung von spezifischen, maßgefertigten Komponenten dar.
Gemeinsam mit einem Beschichtungsunternehmen, das sich auf die Galvanisierung von Rapid-Prototyping-Teile spezialisiert hat, ist es Osterwalder gelungen, 3D-Drucktechnologie und Galvanik-Methode so zu kombinieren, dass er komplexe Experimente mit großen Zeit- und Kostenersparnissen realisieren kann.

Osterwalders Forschung ist Teil eines relativ neuen Feldes, der sogenannten kalten Chemie. Bei Raumtemperatur oder höheren Temperaturen kann man eine starke Bewegung von Moleküle oder Atome beobachten. Treffen diese aufeinander, finden chemische Reaktionen statt. Doch auch bei weitaus niedrigen Temperaturen lassen sich Reaktionen beobachten – selbst bei fast nicht vorhandener Bewegung.
Das Ziel in Osterwalders Forschung ist es, Chemie am absoluten Temperaturtiefpunkt, -273,15°C, zu untersuchen, um einige der grundlegendsten Aspekte von intermolekularen Interaktionen zu verstehen. Damit man die Moleküle bei solch niedrigen Temperaturen untersuchen und kontrollieren zu kann, ist es essentiell, Ihre Bewegung genau zu steuern. “Man kann sich die Molekülstrahlen wie einen Wasserstrahl vorstellen, nur als Gasphasenmoleküle im Vakuum. Unter diesen Bedingungen können wir beginnen, diesen Strahl in seiner Bewegung zu kontrollieren”, so Osterwalder, der für dieses Experiment einen makroskopischen Strahlteiler herstellte.
Ein erster Schritt in Richtung 3D-gedruckter Versuchsaufbau
Ein Forscher kann eine komplexe, technische Zeichnung in kürzester Zeit anfertigen. Die Herstellung des Versuchsaufbau hängt allerdings von Feintechnikern ab und dauert mit traditionellen Fertigungsmethoden wie CNC-Fräsen oder Zerspanung in der Regel mehrere Monate. Osterwalder wollte eine schnellere, kosteneffizientere Methode finden, um von der Idee zum Experiment zu kommen.
Für 3D-Druck begann er sich 2009 zu interessieren, aber die damals erhältliche 3D-Drucker für Fused Deposition Modelling (FDM), Stereolithografie (SLA) und Metal Sintering waren entweder nicht präzise genug oder zu teuer für seine Zwecke.
Stereolithografie ist eine 3D-Drucktechnologie, die mithilfe eines Laser Kunstharz zu einem fertigen Druck zu erhärtet. Mehr lernen über SLA und wie es benutzt wird.
Von dem SLA 3D-Drucker Form 2 , den Osterwalder 2015 kaufte, sobald er auf dem Markt kam, war er schließlich überzeugt: “Stereolithografie bietet die Auflösung, die ich brauche”, sagt Osterwalder. “So kann ich mich auf darauf fokussieren, komplexe Strukturen zu entwerfen, und weiß, dass sie genau so aus dem Drucker kommen.”
Ein 3D-gedruckter und metallisierter Strahlteiler, in Tagen statt in Monaten hergestellt
Osterwalders 3D-gedruckter und galvanisierter Strahlteiler erlaubt ihm, einen Strom von Gasphasenmolekülen in zwei Ströme zu spalten, ohne die Moleküle zu berühren. Die Metallstruktur wird verwendet, um starke elektrische Felder zu erzeugen, in denen Spannungen in der Größenordnung von 10.000 Volt angelegt werden. Diese Felder erzeugen dann eine Kraft, die dann auf die Moleküle wirkt. Strahlteiler sind einfach zu konstruieren für Licht - zum Beispiel ein teilweise reflektierendes Fenster -, aber sind viel schwerer für Moleküle zu erreichen.

Mit der Kombination von 3D-Druck und Metallbeschichtung durch Galvanisierung konnte Osterwalder die Produktionszeit dieses Versuchsaufbaus von mehreren Monaten auf unter eine Woche reduzieren. Osterwalder brauchte ein paar Tage, um den Strahlteiler zu entwerfen und nur 36 Stunden für den 3D-Druck in seinem eigenen Labor. Das Beschichtung der Struktur mit Nickel dauerte nur noch einen Tag. Am Ende, dauerte das Versenden der-3D gedruckten Teile hin und zurück von dem Galvanik-Unternehmen länger als alles andere.
Galvanisieren von 3D-Druckteilen
Verchromte Wasserhähne oder die Stoßstange eines Autos - mit Metall beschichtete, galvanische Teile sind überall: Sie sind mit Chrom, Silber oder einem anderen hochwertigen Metall durch Elektrolyse beschichtet, um das Aussehen und die Materialeigenschaften wie Verschleißfestigkeit und elektrische Leitfähigkeit zu verbessern.
Galvanotechnik bei Kunststoffen funktioniert nicht ohne Weiteres, da Kunststoffe in der Regel nicht leitfähig sind, was für den Galvanisierungsprozess unerlässlich ist. Eine chemische Vorbehandlung kann dieses Problem lösen, aber bis in die frühen 2000er Jahre zeigte dieser Prozess nur mit wenigen Kunststoffen wie ABS Erfolg. Osterwalder wandte sich an die Schweizer Firma Swiss company Galvotec.
“Die Herausforderung auch andere Materialien galvanisch beschichten zu können hat mich schon immer interessiert und dementsprechend motiviert”, sagte Rico Schuhmacher, Gründer von Galvotec. “Deshalb hatte ich im Jahr 2009 bereits eifrig geforscht und experimentiert, um auch andere Materialien als nur ABS beschichten zu können, im Jahr 2011 war ich dann erfolgreich und habe 2012 Galovtec gegründet.”
Es gibt nur wenige Galvanik-Unternehmen, die sich auf Rapid Prototyping weltweit spezialisiert haben und Galvotec ist das einzige in der Schweiz. “Herr Osterwalders Teile mussten teilweise beschichtet werden: das bedeutet, dass einige Bereiche galvanisiert werden müssen und andere nicht. Durch das Erstellen von Masken haben wir dieses Ergebnis erreicht ”, erinnert sich Schuhmacher. “Eine weitere Herausforderung war, den elektrischen Kontakt zwischen zwei Flächen zu verhindern, also mussten wir die Beschichtung für sie separat machen.”

Laut Schuhmacher kann das Anwendungsgebiet von 3D-Druckteilen durch Metallbeschichtung enorm ausgeweitet werden. Die neuen Materialeigenschaften, die dadurch erreicht werden können, reichen von elektrischer Leitfähigkeit, elektromagnetischer Verträglichkeit, Verschleißbeständigkeit, besserer Formbeständigkeit, Magnetismus, Temperaturbeständigkeit bis hin zu einer ganzen Palette an dekorativen Beschichtungen, zum Beispiel in Gold.
Schnelles, flexibles, replizierbares Experimentieren
Das Galvanisieren von 3D-gedruckten Teilen ist immer noch eine Neuheit. Während es offensichtliche Vorteile für Ingenieure birgt, sieht Osterwalder auch ein großes Potenzial für wissenschaftliche Anwendungen.
“Unsere Experimente sind richtige Maschinen, mit vielen Rohren und Pumpen, und sehr komplex zu fertigen für traditionelle Methoden wie Zerspanung oder CNC-Fräsen. Viele dieser Komponenten können in einer viel kürzeren Zeit und mit größerer Flexibilität 3D-gedruckt werden.”

Der Wissenschaftler ist überzeugt, dass die Kombination von 3D-Drucktechnologie und Metallbeschichtung durch Galvanisierung ausgedehnt werden kann, um sonst unmögliche Experimente zu konstruieren.
Osterwalder und Gordons Paper lesen und mehr über Galvanisierung von 3D-gedruckten Teilen zu erfahren.
Mit Blick auf die Zukunft, glaubt Osterwalder nicht, dass diese Vorteile auf seine spezifische Forschung beschränkt sind. Für ihn ist die Frage nicht, was man mit einem 3D-gedruckten und galvanisierten Strahlteiler machen soll, sondern wie seine Methode für andere Experimente reproduziert werden kann.
“Es ist egal in welcher Forschung wichtig, dass man ein Experiment reproduzieren kann, identisch in einem anderen Labor, um es zu wiederholen und zu verifizieren. Man kann sich vorstellen, dass man ein Art Legosystem entwickeln könnte, um mit 3D-gedruckten, galvanisierten Teilen ein Experimente aufzubauen”, so Osterwalder.
Seine Vision ist es, Forschungsinstitute und Labore auf der ganzen Welt zu befähigen, Experimente durchzuführen und zu reproduzieren, indem sie einfach eine .STL-Datei verschicken.
Potential für 3D-Druck und Wissenschaft ausschöpfen
Sind Sie von Osterwalder’s 3D-gedruckten Strahlteiler inspiriert? Lernen Sie 3D-Druck als treibende Kraft für Wissenschaft und Forschung kennen.