Viel Wind um Materialien: Wie Model V2 und Grey V4 im Präzisionsdruck standhalten
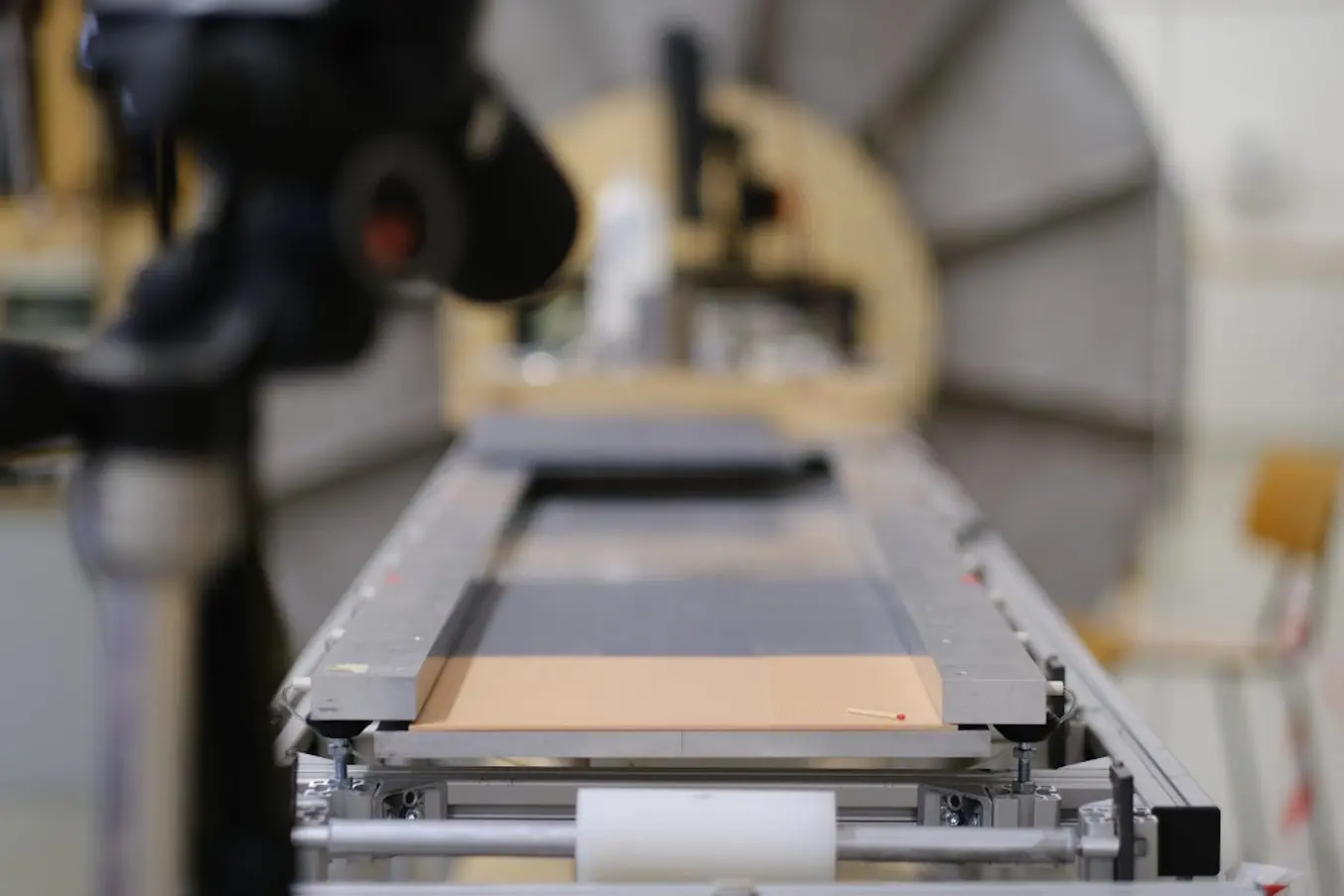
Als Forschungsuniversität der Helmholtz-Gemeinschaft bietet das Karlsruher Institut für Technologie (KIT) rund 25.000 Studierenden pro Jahr Raum für Forschung und Entwicklung. Die Exzellenzuniversität umfasst sieben Forschungsbereiche, unter anderem die Energie-, Umwelt- und Mobilitätsforschung.
Doktorand Lars von Deyn gehört aktuell zu den Wissenschaftlern aus dem Bereich Maschinenbau und Elektrotechnik, er ist wissenschaftlicher Mitarbeiter am Institut für Strömungsmechanik (ISTM). Die Forschenden am ISTM beschäftigen sich im Allgemein mit der Charakterisierung, physikalischen Interpretation und Optimierung von natürlichen und technischen Strömungsphänomenen. Im Speziellen möchte Lars von Deyn einen Beitrag zum Verständnis und der Vorhersage von turbulenten Strömungen leisten, in dem er mittels eines Windkanals und 3D-gedruckten Strukturen Messdaten erzeugt und analysiert.
Da derartige Messungen ein hohes Maß an Genauigkeit und Reproduzierbarkeit erfordern, ist das richtige Material bei der Herstellung von großer Bedeutung. Lars von Deyn hat deshalb den Stereolithographie (SLA) 3D-Drucker Form 3L sowie die gedruckten Oberflächen der Materialien Model V2 und Grey V4 für seine Forschung getestet und mit konventionell CNC-gefrästen Oberflächenstrukturen verglichen.
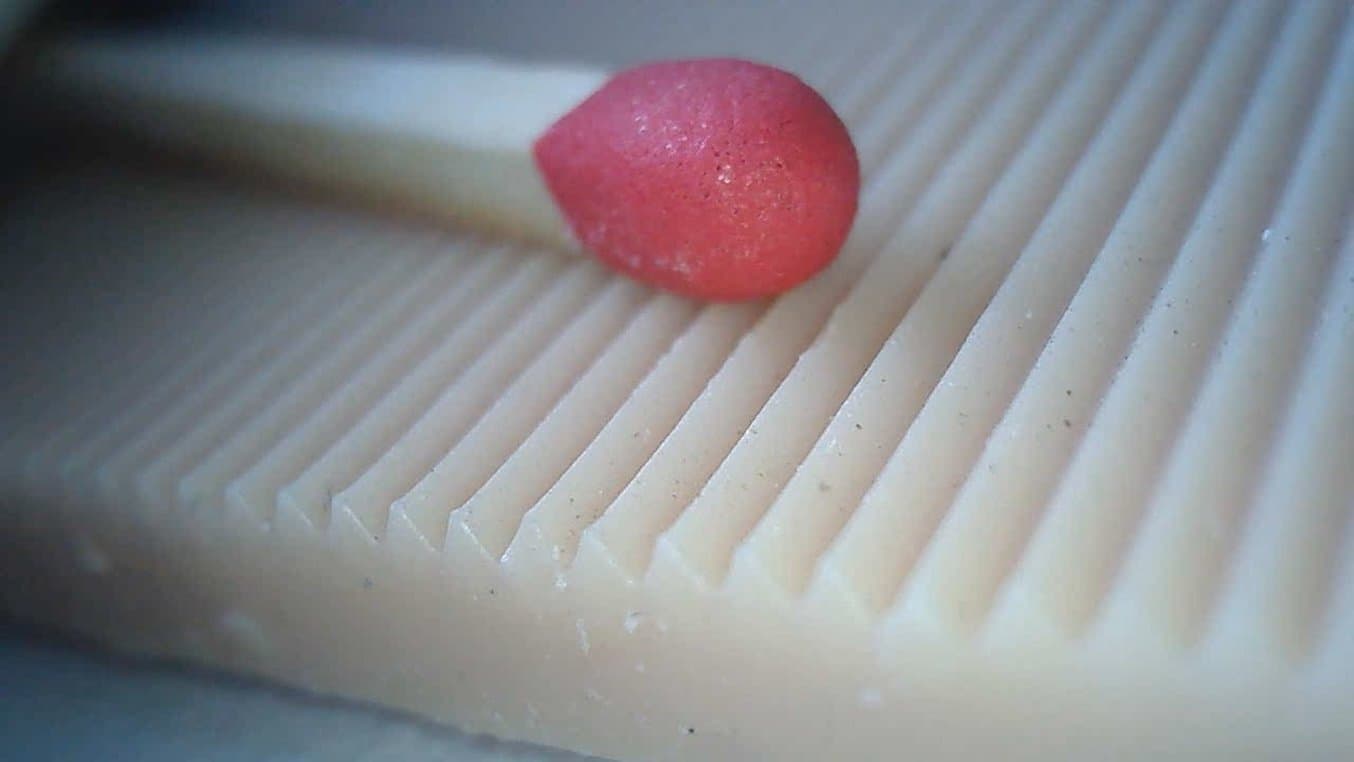
Als Teststruktur wurden sogenannte Riblets gewählt. Diese in Hauptströmung ausgerichteten Längsrillen mit einer scharfen Spitze sind ideal, um die Oberflächenreibung von turbulenten Strömungen zu reduzieren.
Das Projekt
Um technische und natürliche Strömungen systematisch zu untersuchen, werden in einer Vielzahl von Forschungsprojekten Windkanäle eingesetzt. Diese bieten reproduzierbare und messtechnisch gut zugängliche Rahmenbedingungen. Bekannte Beispiele sind industrielle Windkanäle zur Untersuchung der Aerodynamik von Autos und Flugzeugen.
Aufgrund der meist komplexen Strömungsverhältnisse insbesondere in der Mobilität, werden Forschungsobjekte oftmals abstrahiert, um zielgerichtet einzelne Aspekte zu untersuchen. Dies ist auch im Projekt von Lars von Deyn der Fall. Der Doktorand konzentriert sich unter anderem auf die Analyse von einzelnen Strukturen zur Reduzierung von Reibung in der Mobilität.
Vor dem Start des eigentlichen Forschungsprojekts galt es zunächst anhand einer Teststruktur das richtige Herstellungsverfahren und Material zu finden. Lars von Deyn wählte mit der Hauptströmung ausgerichtete Längsrillen, sogenannte Riblets. Diese Strukturen sind bereits gut erforscht, sodass Referenzwerte in ausreichendem Maße vorhanden sind. Außerdem ist die Herstellung der spitzen Strukturen eine besondere Herausforderung an die Herstellung, da scharfe Ecken für gewöhnlich schwer herzustellen, aber für die reibungsmindernde Wirkung der Riblets besonders wichtig sind.
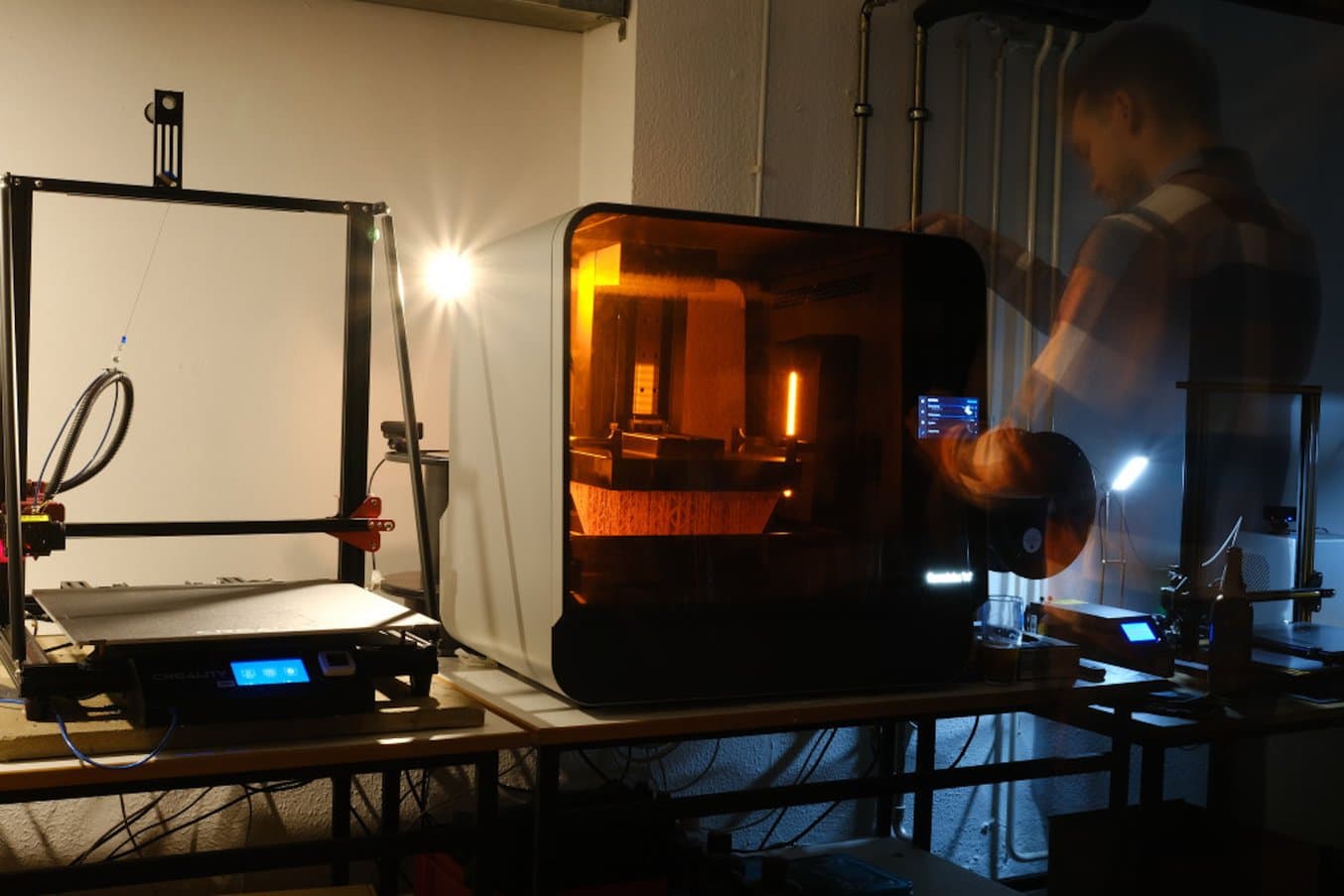
Die richtige Fertigungsmethode
Um für die Forschung verwertbare Messdaten zu erhalten, muss im Windkanal eine Fläche von 1.5 m x 0.3 m mit den zu untersuchenden Strukturen ausgestattet werden. Des Weiteren muss die gewählte Fertigungsmethode eine über die gesamte Fläche gleichbleibende Genauigkeit aufweisen sowie die gewünschte Oberflächenstruktur präzise abbilden können.
Die konventionelle Fertigung per CNC-Fräse stößt dabei an ihre Grenzen, diese Anforderungen an Bauraum und Detaillierungsgrad der Strukturen zu erfüllen. „Ich möchte Strukturen untersuchen, die sehr schwer mit spanenden Fertigungsverfahren herzustellen sind“, sagt Lars von Deyn. Die Suche nach geeigneten Fertigungsverfahren, die den Kriterien des Forschungsprojekts entsprechen, führte zur Wahl des SLA-3D-Drucks.
„Mit dem SLA 3D-Druck kann man sehr gute Genauigkeiten erreichen und sehr feine Details abbilden. Für mich ist die größte Herausforderung, hochpräzise Strukturen auf einer großen Fläche herzustellen. Der Form 3L bietet die nötigen Rahmenbedingungen dafür.“
Lars von Deyn, Wissenschaftler, Karlsruher Institut für Technologie (KIT)
Aufgrund des Bauvolumens und der damit verbundenen Anzahl der benötigten Drucke entschied er sich für den Form 3L. Das Bauvolumen des Form 3L von 330 mm x 200 mm x 300 mm erlaubt es, Platten mit den Maßen 310 mm x 3 mm x 260 mm zu drucken. Bei zwei Platten pro Druck sind sechs Druckvorgänge nötig, um die Messstrecke ausreichend abzudecken.
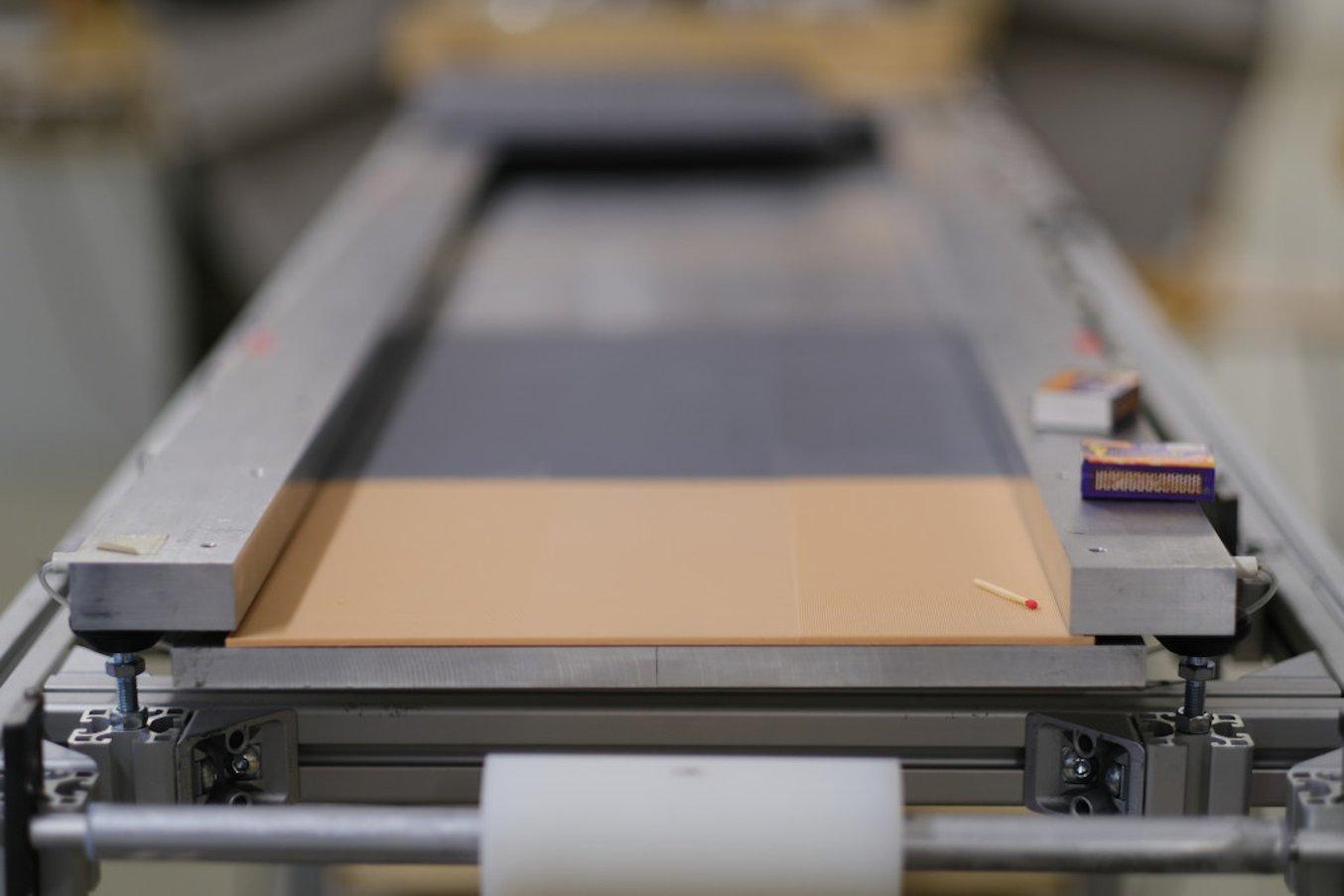
Das richtige Material
Um die erfolgreiche Umsetzung seines Forschungsprojekts zu garantieren, suchte Lars von Deyn nach Materialien, mit denen sich Details gut abbilden lassen und gleichzeitig eine möglichst glatte Oberfläche erreicht werden kann.
Basierend auf diesen Anforderungen sowie auf den Eigenschaften des Form 3L empfahl das Formlabs-Support-Team Lars von Deyn die Verwendung von Formlabs Grey Resin. Neben einem hohen Detailgrad, der für das Projekt notwendig ist, erfordert es zudem keine Nachbearbeitung. Als zweites Material wurde das Modell V2 Resin vorgeschlagen. Dieses zeichnet sich ebenfalls durch einen hohen Detailgrad sowie eine glatte Oberfläche aus.
Die beiden Materialien wurden anschließend anhand von zwei verschieden großen Riblet-Testgeometrien sowie unterschiedlichen Schichtdicken getestet und miteinander verglichen.
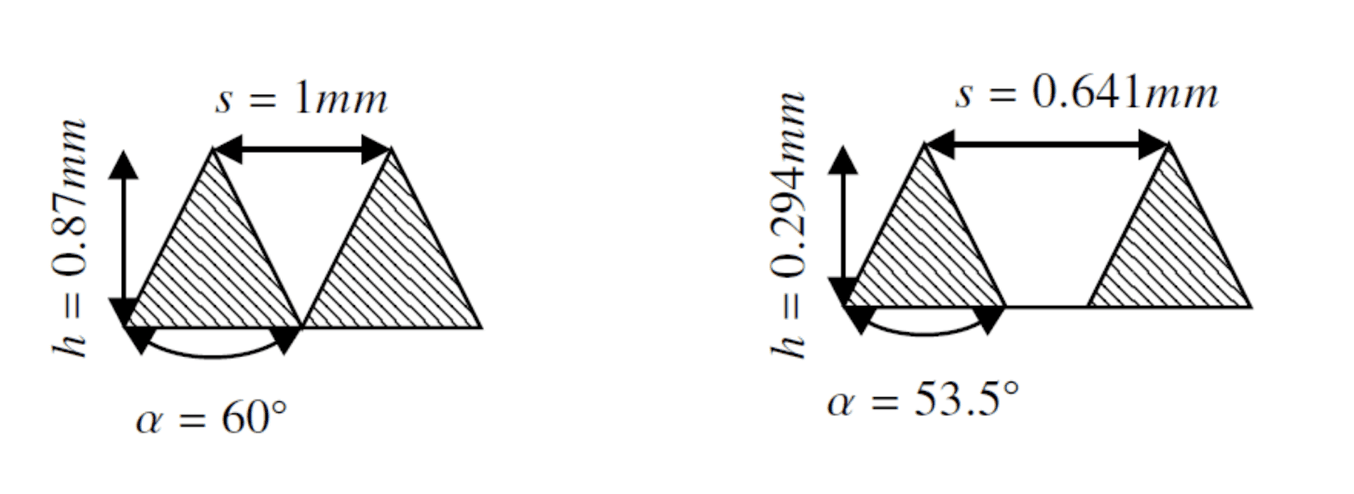
Die Teststrukturen wurden mit unterschiedlichen Abmessungen in Bezug auf Spitzenwinkel, Anstand und Höhe gedruckt und sind für set1 links und für set2 rechts dargestellt.
Die Analyse
Die Analyse der 3D-gedruckten Ergebnisse im Vergleich zu den CNC-gefrästen Strukturen gibt Aufschluss darüber, welches Material mit welchen Druck-Parametern die beste Maßhaltigkeit und Oberflächenqualität aufweist. Hierfür wurde ein 3D-Profilometer vom Hersteller Sensofar S neox verwendet.
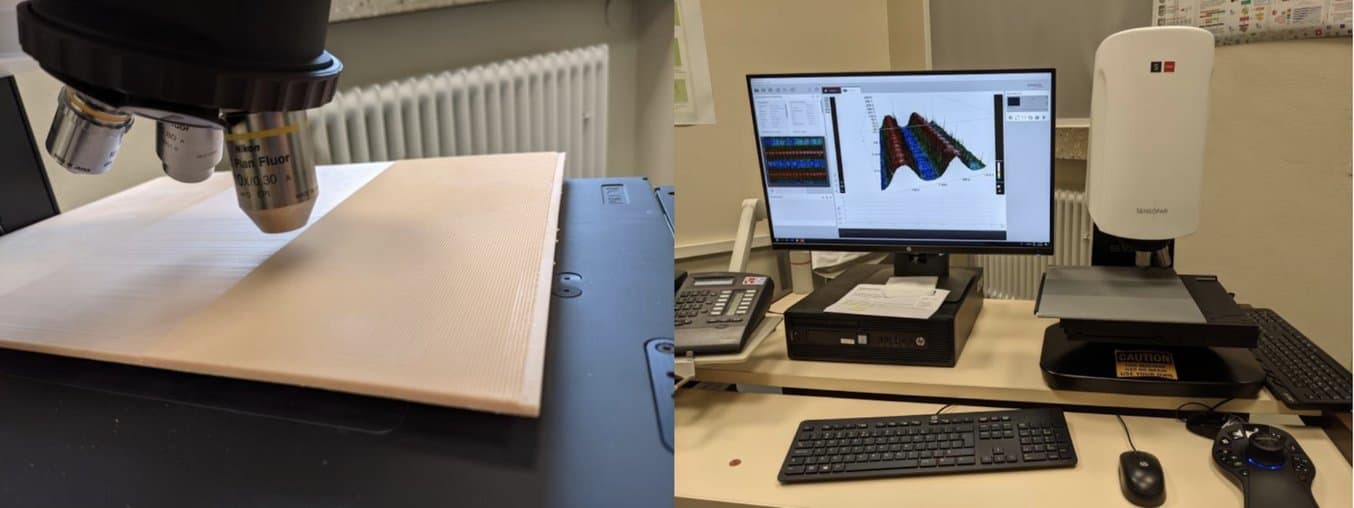
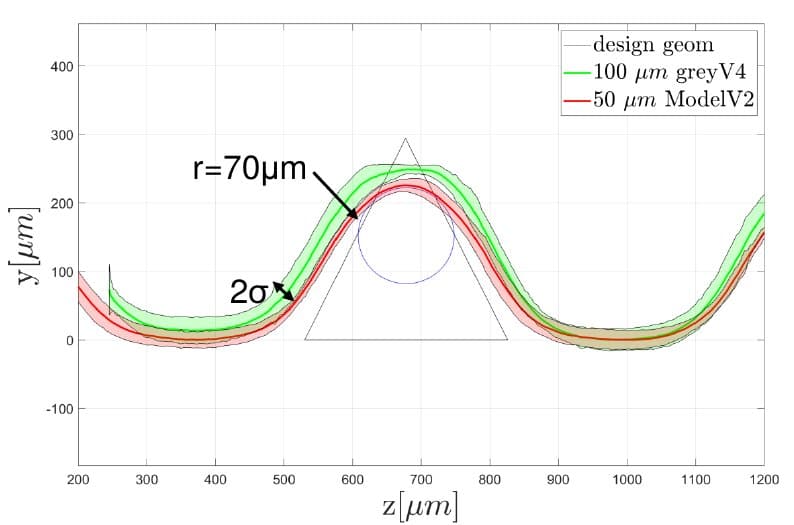
Die Auswertung mit einem 3D-Profilometer gibt Ausschluss auf die erreichte Oberflächengenauigkeiten der 3D-gedruckten Strukturen. Links sind die Ergebnisse für Set 1 aus dem SLA 3D Druckverfahren im Vergleich zur CNC-gefrästen Geometrie dargestellt. Rechts im Bild sind die Ergebnisse für das kleinere Set 2 zu sehen. Mit 𝝈 ist die Standardabweichung bezeichnet.
Die Auswertung der Untersuchungen sowie ein Vergleich der verschiedenen Materialien sind nachfolgend aufgelistet.
Set 2
Grey V4 | Model V2 | Model V2 | |
---|---|---|---|
Schichtdicke | 100mu | 25mu | 50mu |
Herstellungsmethode | Form 3L | Form 3 | Form 3L |
Standardabweichung | 8.9 mm | 6.2 mm | |
Radius | 70 mu | 70 mu | |
Maße | 310 mm x 3 mm x 260 mm | 100 mm x 3 mm x 100 mm | 310 mm x 3 mm x 260 mm |
Materialverbrauch | 422 ml | 374 ml | |
Produktionszeit | 2 Tage, 2 Stunden | 3 Tage, 2 Stunden |
Set 1
Aluminium | Grey V4 | Grey V4 | Model V2 | |
---|---|---|---|---|
Schichtdicke | 50mu | 100mu | 50mu | |
Herstellungsmethode | CNC-Fräse | Form 3L | Form 3L | Form 3L |
Standardabweichung | 7.9 mm | 18.6 mm | ||
Radius | 70 mu | 70 mu | 70 mu | 70 mu |
Maße | 500 mm x 5 mm x 350 mm | 310 mm x 3 mm x 260 mm | 310 mm x 3 mm x 260 mm | 310 mm x 3 mm x 260 mm |
Materialverbrauch | 421 ml | 422 ml | 374 ml | |
Produktionszeit | 10 Stunden Maschinenzeit | 2 Tage, 15 Stunden | 2 Tage, 2 Stunden | 3 Tage, 2 Stunden |
Die Auswertung
Der Versuch zeigt, dass 100 mu und 50 mu Schichtdicke die gewünschte Riblet-Geometrie ähnlich gut abbilden. Der Haupteinfluss der Schichtdicke spiegelt sich in der Welligkeit der Oberfläche wider, die durch die Standardabweichung 𝝈 quantifiziert ist. 𝝈 lässt sich durch die statistische Auswertung des 3D-Oberflächenscans bestimmen – als Mittelung des Scans in Längsrichtung der Struktur. Die Standardabweichung von Set 1 ist bei 50 𝜇m Schichtdicke etwa 50 Prozent kleiner als bei 100 𝜇m Schichtdicke. Die gemessene Welligkeit ist als einhüllendes Farbband um den Mittelwert in der obenstehenden Abbildung dargestellt. Das gewählte Intervall von 2𝝈 entspricht einem Konfidenzintervall von 95 Prozent. Das bedeutet, dass 95 Prozent aller gemessenen Werte innerhalb des 2𝝈-Intervalls liegen.
Beim 3D-Druck entsteht eine systematische Abweichung. Die Riblet-Geometrie in Set 1 wird etwa 30 Prozent kleiner gedruckt als vorgegeben. Nachfolgende Versuche haben gezeigt, dass diese systematische Abweichung jedoch leicht korrigiert werden kann. Die kleinere Struktur in Set 2 wird im Hinblick auf die Riblet-Höhe besser aufgelöst.
Auch beim SLA-Druck können wie erwartet scharfe Ecken nicht exakt abgebildet werden. Die Dreieckspitze wird abgerundet, es entsteht eine in etwa kreisrunde Spitze mit einem Radius von 70 𝜇m. Dieser Spitzenradius entspricht auch dem Radius der CNC-gefrästen Geometrie. In dieser Hinsicht wird folglich ein ähnlich gutes Ergebnis erreicht.
Für die Umsetzung wurde schließlich das Material Grey V4 bei einer Schichtdicke von 50 𝜇m gewählt. Da die Oberflächenqualität als eine zentrale Anforderung an das Druckverfahren definiert wurde, wird somit die längere Druckzeit im Vergleich zu 100 𝜇m Schichten in Kauf genommen, um eine weniger wellige Oberfläche zu erreichen. Grey V4 erwies sich durch die einfache Handhabung und schnell fortschreitende Softwareentwicklung als vorteilhaft. Zu beachten ist weiterhin, dass sich eine genaue Maßhaltigkeit von Präzisions-Strukturen nur in Kombination mit Oberflächen-Scans durch eine iterative Optimierung erreichen lassen. Bei richtiger Handhabung lassen sich so exzellente Druckergebnisse erzielen.