Schmelzschichtung (FDM) und Stereolithografie (SLA) gehören zu den beliebtesten 3D-Drucktechnologien auf dem Markt. Beide Technologien bieten ihre eigenen Vorteile und Stärken in Sachen Druckqualität, Materialien, Anwendungen, Arbeitsprozess, Geschwindigkeit, Kosten und mehr.
Abhängig von Ihrer Anwendung eignet sich eine Technologie für spezifische Teile möglicherweise besser als die andere. Aber wieso kombinieren Sie sie nicht einfach, um das Beste aus beiden Welten zu erhalten?
In diesem Beitrag sehen wir uns an, wie drei Nutzer FDM und SLA als sich ergänzende Technologien betrachten und erfahren, wie sie beide nutzen, um ihre Projekte zu optimieren.
Gleichgewicht zwischen Detail und Druckgröße bei Achterbahnmodellen
Matt Schmotzer bastelt seit fast 10 Jahren mit 3D-Druck. Aktuell baut er Miniatur-Achterbahnen. Bislang hat er drei vollfunktionale Modelle aus Schienen und hochdetaillierten Wagenbaugruppen gebaut. Matt nutzt sowohl FDM als auch SLA und setzt die Stärken beider Technologien ein, um funktionalere Modelle zu erreichen. Seit kurzem ist er mit seinen Achterbahnen unterwegs und führt sie in Schulen vor, um zukünftige Ingenieure zu inspirieren.
Matts ehrgeizigste Projekte umfassen mehr als 700 einzelne Querträger. Flache geometrische Träger werden zur inneren Abstützung eingesetzt und durch Klebemittel von Loctite mit einem hölzernen Gerüst verbunden. Da eine hohe Detailtreue nicht das Hauptanliegen ist und eine große Anzahl von Druckteilen benötigt wird, nutzt Matt FDM, um den Großteil der Träger schnell zu drucken. FDM-Druckteile bieten zudem eine fast unbegrenzte Auswahl an Farboptionen, wodurch Matt mehr kreative Freiheit bei der endgültigen Montage der Achterbahn hat.
Die Wagen selbst bringen ihre eigenen einzigartigen Herausforderungen mit sich. Die Wagenmodelle werden mit SLA Geräten gedruckt, da die kleinen Teile mit einer Abmessung von 1,5 × 3” realistisch aussehen müssen. Für diese Aufgabe nutzt Matt Grey Pro Resin auf seinem Formlabs Drucker. SLA-Drucker zeichnen sich durch hochwertige Endverbraucherteile aus, und die Wagenmodelle sollen so realistisch wie möglich aussehen – bis hin zu den winzigen Griffen an den Türen!
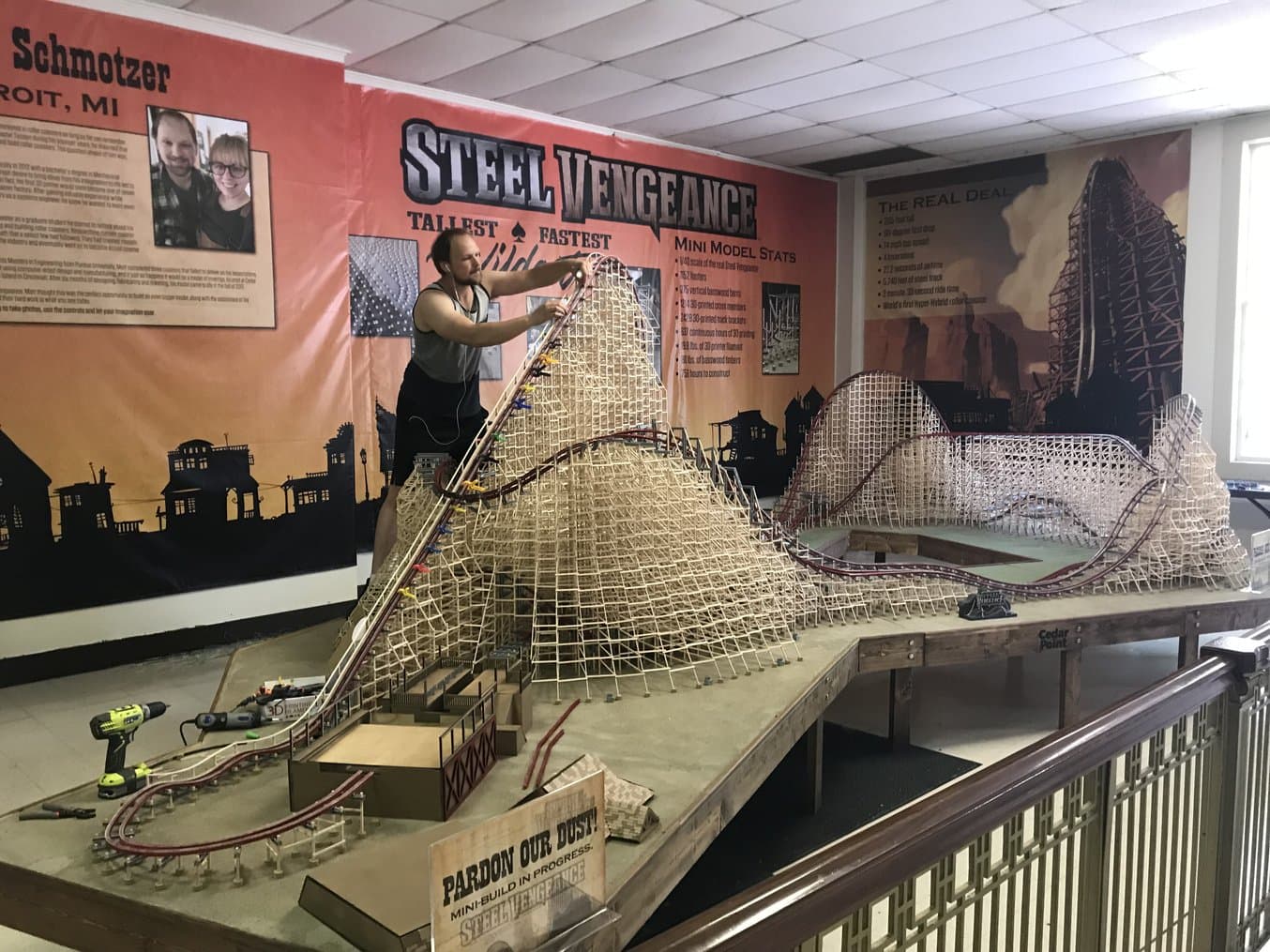
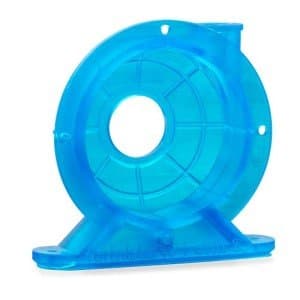
Kostenloses Probeteil anfordern
Sehen und fühlen Sie die Qualität von Formlabs selbst. Wir schicken Ihnen einen kostenlosen Probedruck an Ihren Arbeitsplatz.
Kostenloses Probeteil anfordernHelfen Sie als 3D-Druckdienstleister Ihren Kunden, Projektziele zu erreichen
Christina Perla hat vor zwei Jahren Makelab, ein 3D-Druckbüro in Brooklyn, gegründet. Makelab ist nicht einfach nur eine Druckerfarm, sondern ein Beratungsunternehmen, das Gespräche führt, um Kunden bei der Erreichung ihrer Projektziele zu helfen.
Das Unternehmen arbeitet sowohl mit SLA- als auch mit FDM-Technologie und schlägt Kunden die Druckmethode vor, die ihre Projektbedürfnisse erfüllt. Aktuell erhält es die eine Hälfte der Aufträge durch FDM-Anfragen und die andere durch SLA-Projekte. Makelab bietet alle Formlabs Kunstharze an; 2018 war High Temp Resin das beliebteste Material.
„Da wir ein Druckdienstleister sind, endet unser Einfluss auf den Designprozess des Kunden mit dem 3D-Druck. Wir betrachten SLA als hochwertiges Angebot zur Ergänzung von FDM. Wir bieten bei Makelab seit Anfang an Formlabs Kunstharze als Materialoption an. Wir haben schon immer den Wert gesehen und den Mehrwert, den es für die Kunden bringt.“
Christina Perla
Christina bevorzugt nach eigenen Aussagen zwar meist SLA, doch FDM eignet sich immer noch für große Mengen und wenn große Druckteilabmessungen die Konstruktionsvolumina der meisten SLA-Drucker übersteigen. Christina bevorzugt FDM-Druck ebenfalls, wenn das Teil als einfacher interner Konzeptnachweis dient. Für Investorentreffen, Kunden-Pitches oder abschließende Präsentationen für Projekte, die genehmigt werden müssen, verwendet Makelab SLA.
Christina findet es nützlich, eine 3D-Druckermarke für die jeweilige Technologie zu nutzen und in das Ökosystem dieses Unternehmens zu investieren. So kann sie den Druck mit einem bestimmten Gerät meistern, die bestmöglichen Drucke anbieten und eine Beziehung zu den Druckermarken entwickeln, wenn sie Hilfe benötigen sollte.
„Halten Sie es so minimalistisch wie möglich, indem Sie sich für eine Marke pro Technologie entscheiden und innerhalb dieser Ökosysteme arbeiten. Stellen Sie sicher, dass die Unternehmen, deren Geräte Sie nutzen, auch einen herausragenden Support anbieten. Bei nur zwei Kundenserviceteams, zwei Telefonnummern und zwei Ersatzteilsätzen wird einfach der gesamte Prozess optimiert.“
Christina Perla
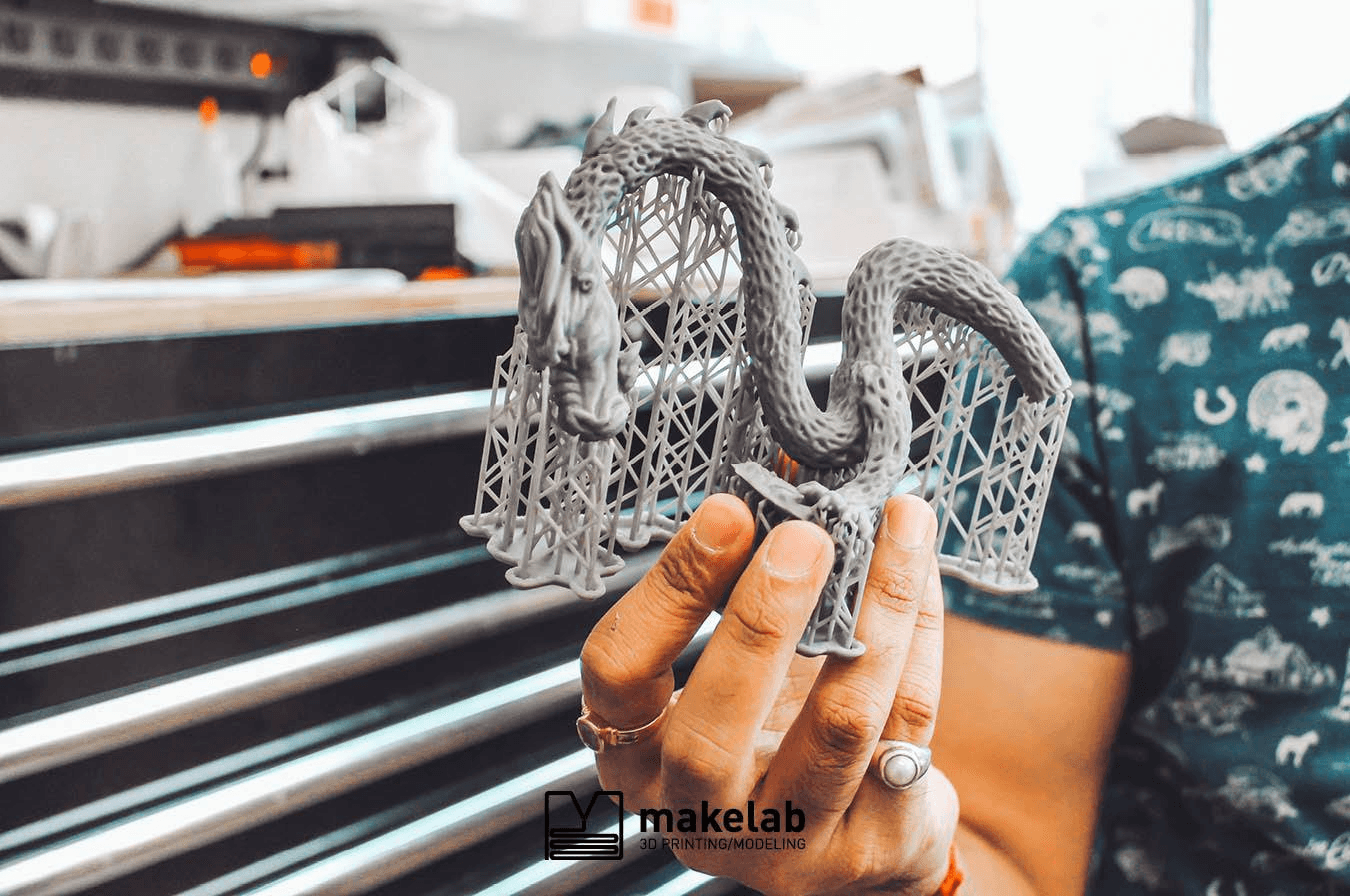
Auswahl der richtigen flexiblen Materialien für den dritten Daumen
Dani Clode ist die Gründerin des Third Thumb Projekt, in dessen Rahmen sie mit The Plasticity Lab des Institute of Cognitive Neuroscience at University College London zusammenarbeitet. Die Daumenprothese wird vom Fuß des Nutzers gesteuert, wodurch die Möglichkeiten der menschlichen Hand erheblich erweitert werden. Das Ziel des Projekts ist es, die Bedienbarkeit und Steuerung von Prothesen zu verbessern.
Ein einzigartiger Aspekt des Projekts ist, dass der Daumen sowohl aus SLA- als auch aus FDM-Komponenten besteht. Das Armband besteht aus Formlabs Grey Resin, das fest und gleichzeitig leicht ist und über eine glatte Oberfläche verfügt, die sich gut an die Konturen des menschlichen Körpers anpasst. Dani hat versucht, dieses Teil mit selektivem Lasersintern zu drucken, ist dann aber wieder auf SLA mit Grey Resin umgestiegen. Sie hat sich an Grey Resin gewöhnt und verwendet das Material, seit sie 3D-Druck das erste Mal für die Prototypenfertigung genutzt hat.
Der Daumen selbst wurde mit FDM gedruckt, während die Fingerspitze aus Formlabs Elastic Resin besteht. Dani kombiniert für den Daumen und das Armband verschiedene Teile umsichtig miteinander und wählt dabei für beide Komponenten die besten Materialien aus. Durch Experimente mit beiden Technologien konnte Dani Möglichkeiten finden, durch die FDM und SLA einander ergänzen und so ein komplexes Projekt ermöglichen, das sonst nicht realisiert werden könnte.
„Der Daumen selbst ist aus thermoplastischem Polyurethan mit geringer Druckfüllung auf einem FDM-Drucker hergestellt worden. FDM Flex lässt sich schwer verarbeiten, ist aber aktuell die beste Option für den Daumen. Er wird dadurch auch leicht und fest. Die Fingerspitzen sind aus Formlabs Elastic Resin, weil ich ein hochauflösendes flexibles Material benötige, das dünn gedruckt werden kann, seine Form behält und gut greifen kann. Ich finde es auch toll, dass es im Gegensatz zu Silikon leicht an meinen anderen Materialien befestigt werden kann. SLA ist das einzige Druckverfahren, das meine feinen internen Leitungen, mit denen der Daumen gesteuert wird, herstellen kann.
Dani Clode
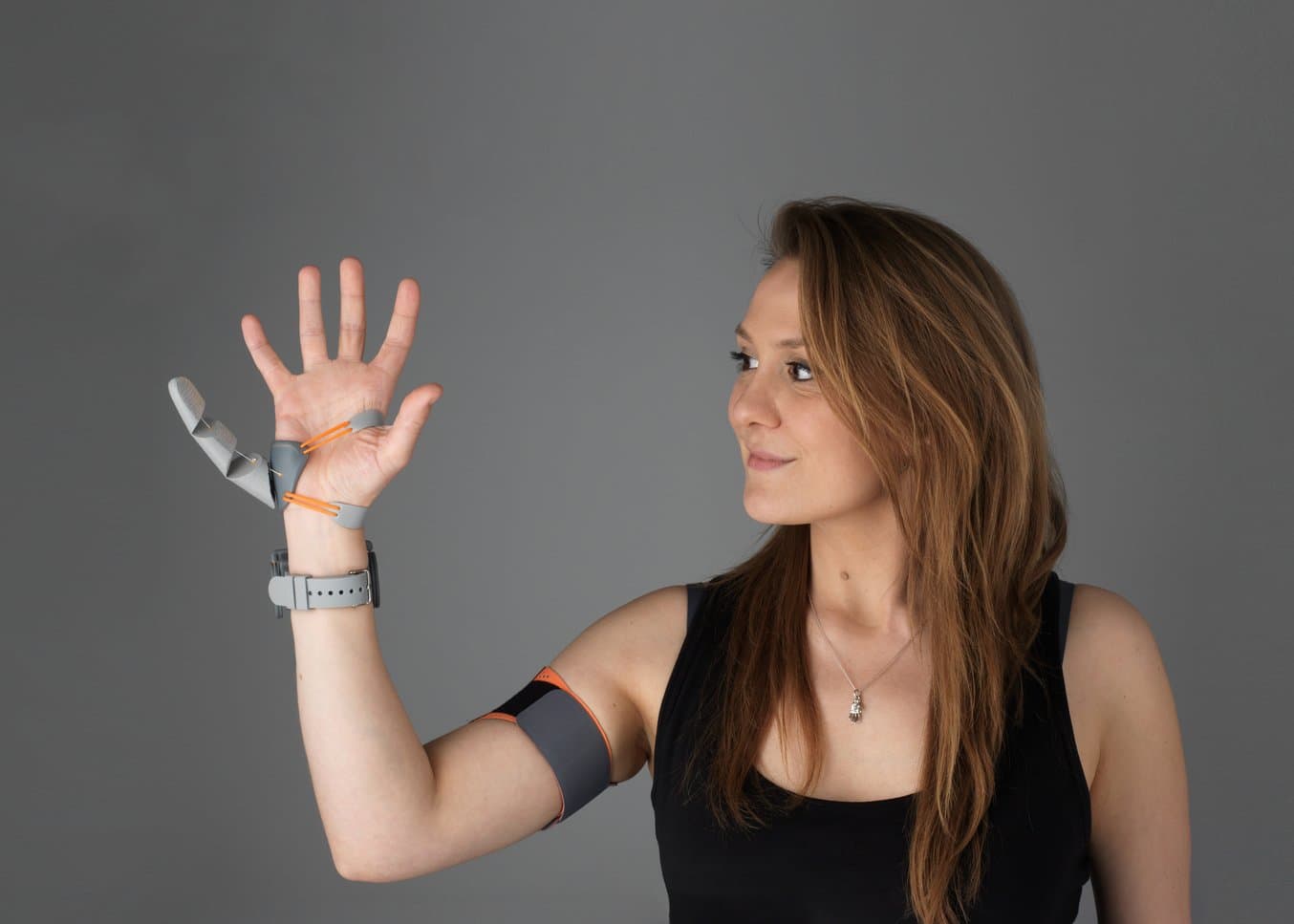
Sie haben interessante Projekte, die durch beide Technologien ermöglicht werden? Taggen Sie @Formlabs in Ihren Beiträgen in den sozialen Medien!