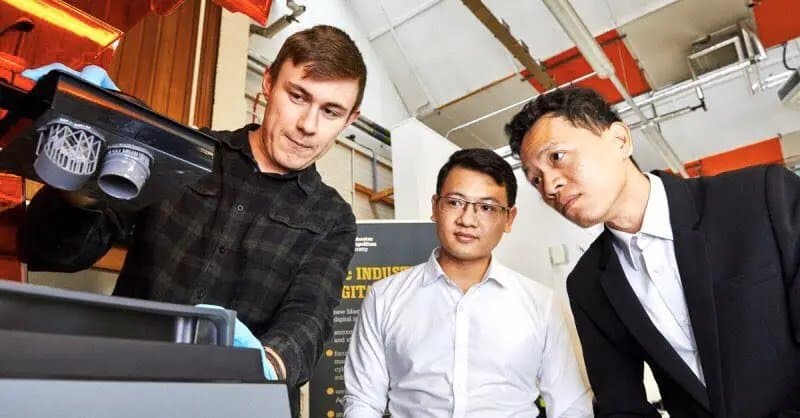
PrintCity ist eine Fertigungseinrichtung für 3D, additive Verfahren und Digitales in Manchester, einer Stadt mit einer reichen Industriegeschichte. Als Teil der Manchester Metropolitan University dient die Einrichtung zur Bildung, Ausbildung und auch als Beratung von Firmen aus der Umgebung von Manchester, aber auch aus der ganzen Welt. PrintCity ist außerdem auf dem Universitätscampus die Fertigungszentrale für den Magisterstudiengang in industrieller Digitalisierung.
Seit dem Startschuss 2018 ist PrintCity schnell gewachsen, von einem Mitarbeiter auf 23. Aktuell gibt es dort 65 Drucker verschiedenster Arten, von FDM über SLA bis zu Metalldruckern, welche allesamt bei Formlabs' größtem Partner im Vereinigten Königreich erworben wurden: Additive-X. Die Belegschaft von PrintCity berät Unternehmen jeder Größenordnung bezüglich der am besten geeigneten digitalen Technologien für die jeweilige Organisation und begleitet die F+E-Phase der Produkte sowie die Fertigung.
Wir haben uns jüngst (virtuell) mit Product Development Specialist Mark Chester getroffen und darüber gesprochen, wie PrintCity mit Programmen wie Fusion 360 und Werkzeugen wie dem Form 3 seine Kunden vom Zweck und Nutzen der digitalen Fertigung überzeugt.
In diesem Blogbeitrag beleuchten wir folgende Aspekte:
- Wie PrintCity die Kunden über die verschiedenen digitalen Werkzeuge aufklärt
- Wobei sich die Bildung und die Unternehmensberatung an der MMU überschneiden
- Wie der Wasserversorger United Utilities die Kombination aus optischen Scans, Fusion 360 und dem Form 3 für die bedarfsbasierte Produktion seiner Ersatzteile abwägte
Beratung von Kunden jeder Größenordnung
Der Startpunkt jedes Kundengesprächs zur digitalen Werkzeugen ist immer die breit gefächerte Flotte an 3D-Druckern. Mark sagt dazu: „Die Unternehmen, die zu uns kommen, haben vielleicht noch nie mit 3D-Druck zu tun gehabt. Die Technologie ist für sie noch komplett neu. Deshalb ist es für uns so wichtig, das breite Spektrum an verfügbaren Druckern aufzuzeigen.“ Mark arbeitet mit verschiedensten Firmen, vom Textildesign über Sportartikelhersteller und öffentliche Versorger bis hin zu Fertigungsunternehmen. Obgleich sich diese Unternehmen in Größe und Produkten unterscheiden, entdeckt er viele Gemeinsamkeiten beim Bedarf und bei den Bedenken seiner Kunden ― aber auch bei den Lösungen, die durch Werkzeuge wie Fusion 360 und den Form 3 erzielt werden.
Dabei verfolgt Mark für gewöhnlich den Ansatz, ein Problem aufzuspalten, sodass man mehrere Iterationen am selben Tag durchführen kann, anstatt eine Woche oder noch länger zu warten. Das verringert letztendlich die Zeit bis zur Markteinführung. Um solche Fälle anzugehen, druckt PrintCity die Prototypen für die Kunden am selben Tag, entweder mit einem FDM-Drucker oder auf dem Form 3 mit Draft Resin. Später kann man dann für hochwertigere Iterationen auf die Standard- oder die technischen Kunstharze von Formlabs umschwenken.
Die Designs vieler Unternehmen zielen auf den Spritzguss für die Massenproduktion ab. Für solche Fälle bietet sich Formlabs' Materialfamilie der Kunstharze Tough und Durable an, da diese eine gute Repräsentation der Endverbrauchsteile abbilden. Aber es steigt auch die Zahl jener Kunden, die über die direkte additive Fertigung von Endverbrauchsteilen nachdenken. Vor kurzem bewertete Mark Rigid Resin für ein Unternehmen, das Prägewalzen für Texturen bei Papiermedien entwirft. In diesem speziellen Fall benötigte der Kunde ein hochauflösendes Teil aus einem hochfesten Material.
„Fusion 360 hat eine flache Lernkurve, wenn der Kunde noch keine Erfahrung mit CAD hat. Außerdem ist es kostengünstig.“
Mark Chester, Product Development Specialist
Neben den handfesten Ergebnissen ist auch die Erschwinglichkeit ein entscheidender Faktor. „Ich glaube, bei allen Unternehmen ist das Budget eine der Hürden. Wir müssen jedes Mal eine Kosten-Nutzen-Analyse anfertigen, um die Vorteile der jeweiligen Technologie für das entsprechende Unternehmen zu bewerten.“ Der Form 3 schließt dabei die Lücke einer erschwinglichen Desktop-Lösung mit professionellen Ergebnissen. Selbiges gilt auch für Marks CAD-Programm erster Wahl ― Fusion 360 ―, das er sowohl für seine Kunden als auch privat nutzt. „Fusion 360 hat eine flache Lernkurve, wenn der Kunde noch keine Erfahrung mit CAD hat. Außerdem ist es kostengünstig.“ Mark merkte weiterhin an, dass Autodesk die Software auch regelmäßig verbessert und den Kunden neue Funktionen anbietet. „Autodesk hat immer ein offenes Ohr für die Kunden.“
Eine weitere einzigartige Herausforderung gilt es bei der Zusammenarbeit mit Großunternehmen zu überwinden: Mark stellt oft eine Ablehnung gegenüber Neuerungen fest. Ein Team, das sich seit vielen Jahren auf denselben Arbeitsprozess verlässt, steht dem Ausprobieren von Neuheiten oft zögerlich gegenüber. Um eben die Angst vor den Risiken der Veränderung zu nehmen, bietet Mark oft eine Machbarkeitsstudie an. Solche Studien beantworten die fundamentale Frage, ob die beabsichtigte Technologie auch die gewünschten Ergebnisse liefert und sich nahtlos in die bestehende Organisation einfügt.
Bedarfsbedingte Ersatzteilproduktion bei United Utilities
United Utilities ist der größte Wasserversorger des Vereinigten Königreichs. Dort wandte man sich an PrintCity zwecks einer Machbarkeitsstudie, um die passende Technologie ausfindig zu machen, mit der man die Kernaufgaben besser bewältigt. Mark arbeitete Hand in Hand mit dem Continuous-Improvement-Team dieses Versorgungsunternehmens und suchte nach Mitteln und Wegen, Ersatzteile zur Reparatur mechanischer Baugruppen zu produzieren. Wenn im Einsatz ein Problem auftritt, dauert es schon einmal Tage und Wochen, bis ein kaputtes Teil ausgetauscht werden kann. Das bedeutet für die Kunden oft langzeitige Unterbrechungen. Könnte man mit 3D-Scans und 3D-Druck nach Bedarf funktionsfähige Ersatzteile herstellen? Für diese Machbarkeitsstudie musste PrintCity also drei Technologien bewerten: die Scanmethode, den Druckprozess samt Materialien und die CAD-Software, die zwischen diesen beiden Schritten steht.
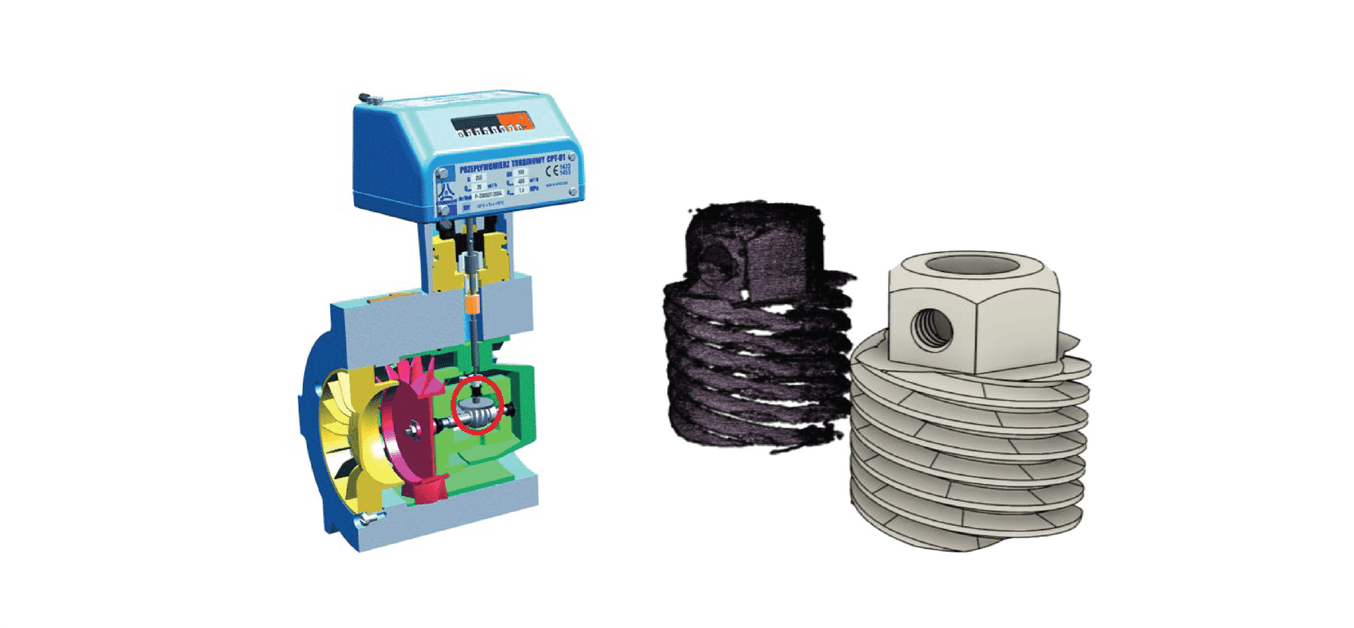
Ein Ersatzteil eines Durchflussmessgerät von United Utilities: Rohdaten eines 3D-Scans und das reparierte Parametermodell aus Fusion 360
Mark schlug einen Arbeitsablauf vor, bei dem zunächst das beschädigte Teil mit einem auf einem Stativ montierten Laserscanner namens Hexagon Absolute Romer Arm eingelesen wird. Dieser erfasst hochgenau die Oberflächendetails. Als nächstes werden die Rohdaten in Autodesk Fusion 360 importiert. Die Scandaten können technisch zwar direkt in eine STL-Datei für den 3D-Druck umgewandelt werden, doch formen die Rohdaten selten ein wasserdichtes Teil, das sich für die additive Fertigung eignet. Die für Mark wichtigste Funktion von Fusion 360 heißt „Mesh Workspace“ (Netz-Arbeitsbereich), über welche Nutzer den Scan direkt importieren und reparieren. Mit den leistungsstarken Modellierungsparametern von Fusion 360 konnte Mark ein scharfes Teil nachbauen, das die perfekte Geometrie für die Endverwendung aufwies.
Zum Schluss werden die Teile dann direkt von Fusion 360 an PreForm übermittelt, bevor man sie auf dem Form 3 druckt. Dank dieser Integration von Fusion 360 und PreForm kann die Wartungsmannschaft von United Utilities Scans importieren, reparieren und Teile drucken, alles direkt vor Ort, ohne STL-Dateien für Dutzende Teile zu speichern, die man nur einmal braucht.
Im Zuge dieser Studie stellte PrintCity dem Kunden auch eine ganze Reihe von Materialeigenschaften basierend auf der Materialbibliothek von Formlabs vor. Draft Resin eignet sich bestens für sehr schnelle Prototypen, bei denen es nur auf die Passform ankommt. Endverwendungsteile hingegen stellte man aus der Materialfamilie Tough und Durable her sowie aus Rigid Resin. Diese Kunstharze haben die mechanischen Eigenschaften der am häufigsten verwendeten Kunststoffe in der Wasserversorgung ― wie Acetal und ABS.
„Die Qualität der 3D-Drucke war ausgezeichnet. [Wir sind] äußerst beeindruckt, wie schnell PrintCity benötigte Änderungen umsetzt.“
Das Continuous-Improvement-Team von United Utilities
Mit Autodesk Fusion 360 und dem Form 3 kann Marks Team schnell umsetzbare Arbeitsabläufe identifizieren und sie den Kunden vorstellen, ganz gleich, wie groß die Organisation sein mag. Als Ergebnis dieser Machbarkeitsstudie übergab Mark einen Bericht an United Utilities, der den Arbeitsablauf vom 3D-Scan zum 3D-Druck aufschlüsselte sowie die damit verbundenen Kosten. Zum Zeitpunkt der Berichtübergabe standen die 3D-gedruckten Teile den Originalen in Sachen Funktion in nichts nach.
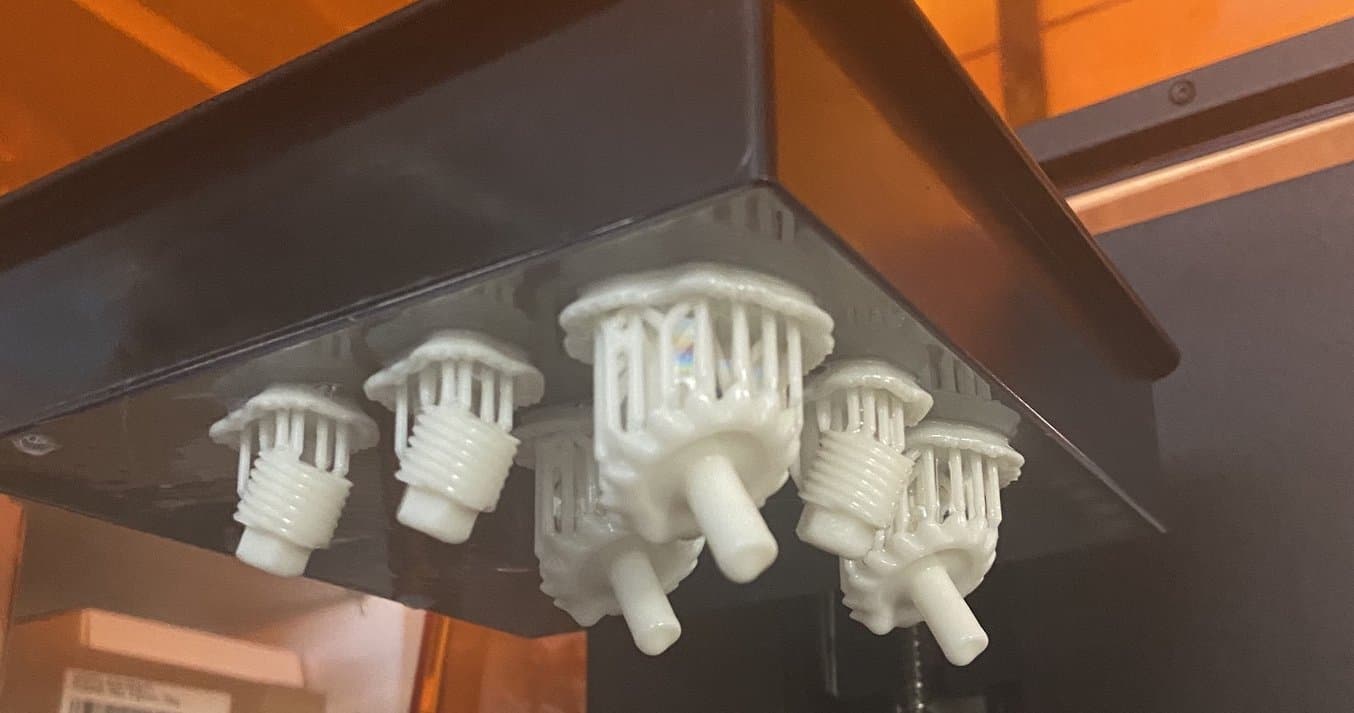
Zusammenarbeit aus der Ferne
Kommunikation über weite Strecken hinweg ist in vielen Berufen im Jahre 2020 und Anfang 2021 zum Standard geworden. Auch bei PrintCity erwies sich das als Herausforderung bei einem Geschäftsmodell, das sich normal auf persönliche Vorführungen und Besprechungen verlässt.
Mark zufolge macht das Indiehandnehmen eines 3D-gedruckten Prototyps einen himmelweiten Unterschied. Er freut sich, wenn dieser Aspekt seiner Arbeit endlich zurückkehrt. „Wenn man mit 3D-Druck arbeitet, muss man ein Druckteil wirklich in der Hand halten und es für sich selbst sehen. Das hat uns im letzten Jahr und darüber hinaus sehr gefehlt. Bei vielen unserer Kunden sieht man förmlich, wie ihnen ein Licht aufgeht, sobald sie erst einmal einen 3D-Druck in der Hand halten. Dann sagen sie: ‚Das ist genau das, was wir brauchen.‘“
In der Zwischenzeit ist PrintCity auf Versanddienste ausgewichen, um die Prototypen an die Kunden zu liefern. Zum Teil hat auch die Technologie direkt dabei geholfen, die Lücke zwischen Mark und seinen Kunden zu schließen. Ein besonderer Vorteil von Fusion 360 ist diesbezüglich, dass man Dateien über die Cloud digital mit den Kunden teilen kann. „Wir senden dem Kunden einen Link zu einem 3D-Modell. Dort kann man es dann prüfen, kommentieren und sogar herunterladen.“
Die Brücke zwischen Bildung und Industrie
Neben den Erkenntnissen, die man direkt von PrintCity erlangt, können sich die Unternehmen auch die großartigen Talente seitens der Studenten der MMU zunutze machen. In vielen Fällen ist der nächste logische Schritt nach der Machbarkeitsstudie, den Kontakt zwischen dem Unternehmen und einem Studenten zu knüpfen, der dort dann ein entsprechendes Praktikum durchführt. Mark sagt dazu: „Wir nennen das ‚umgedrehtes Mentoring‘. Die Studenten sind quasi die Lehrer und übertragen die von ihnen erlernten Kenntnisse ins Unternehmen.“ Viele der Studenten finden dann auch ihre erste Festanstellung in eben diesen Unternehmen und nutzen dabei weiter diese erschwinglichen Digitalwerkzeuge wie Fusion 360 oder den Form 3.
Zum Abschluss unseres Gesprächs gab uns Mark noch einen fantastischen Tipp für Produktentwickler, die sich neuen Problem gegenübersehen. Seinen Angaben nach ist es nicht ungewöhnlich, dass Unternehmen sich eine spezifische 3D-Drucktechnologie in den Kopf gesetzt haben, dann aber doch umschwenken, nachdem sie die verschiedenen Technologien kennengelernt haben. „Sammelt die Erfahrung. Fallt ruhig schnell und oft auf die Nase. Was bei einem Produkt oder Projekt ein Fehlschlag ist, ist bei einem anderen vielleicht genau das Richtige.“
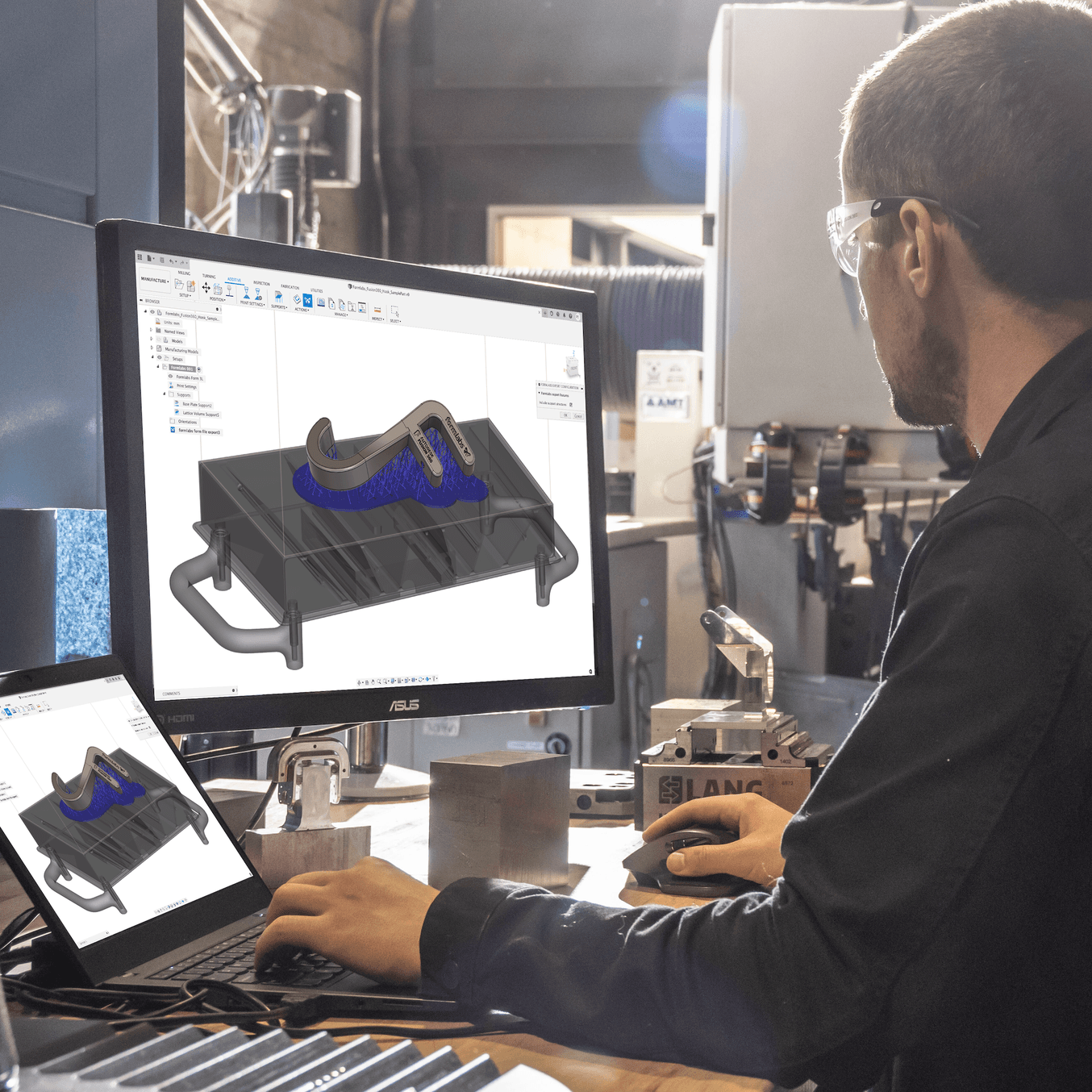
Integration von Formlabs und Fusion 360
Formlabs und Autodesk Fusion 360 arbeiten zusammen, um Ihren digitalen Arbeitsablauf zu optimieren ― mit einer neuen CAD-Software für 3D-Druck-Integration. Besuchen Sie unseren Integration Hub, um mehr über die neuesten SLA-Funktionen von Fusion 360 zu erfahren, weitere Geschichten unserer Nutzer zu lesen und unseren Design-Leitfaden herunterzuladen.