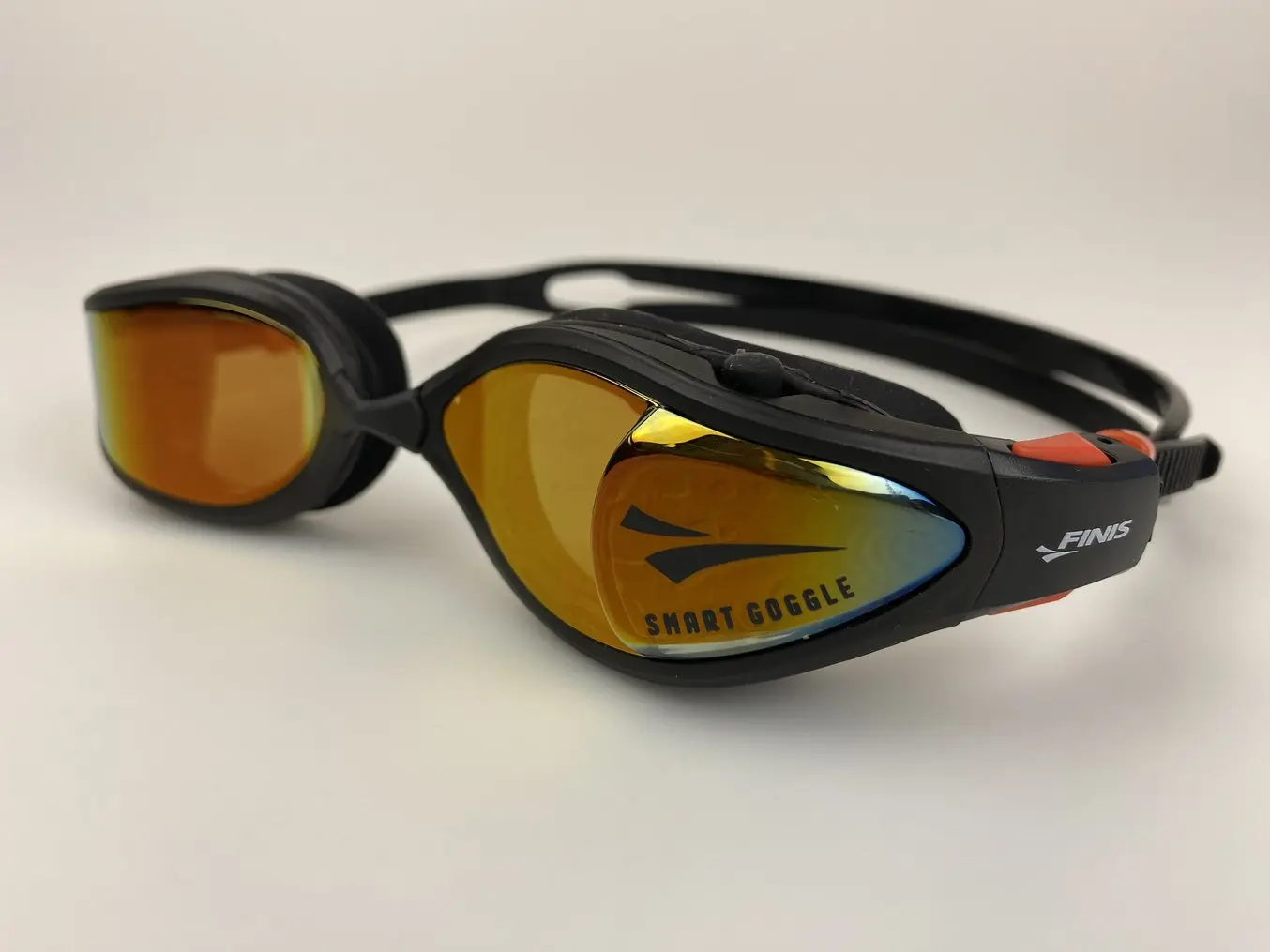
FINIS, Inc. ist auf die Entwicklung von Schwimm- und Wassersportausrüstung spezialisiert, einschließlich hochmoderner Hilfsmittel wie der intelligenten Schwimmbrille Smart Goggle Max.
FINIS, Inc. ist bekannt für seine wegweisenden Produkte, die aufgrund ihrer herausragenden Qualität und Leistung das Vertrauen zahlloser Schwimmer*innen gewinnen konnten – sowohl im Hobbybereich als auch im Profisport. Das in Kalifornien in den USA ansässige Unternehmen strebt danach, sein innovatives Produktangebot kontinuierlich zu verbessern, und behält dabei stets den Fokus auf den sich wandelnden Bedürfnissen seitens Sportler*innen und Trainer*innen.
David Beittel ist leitender Designer bei FINIS und für das Management der Produktentwicklung zuständig. Gemeinsam mit seinem Team nutzte er für das Rapid Prototyping zunächst Filament-3D-Druck, stellte aber schnell fest, dass er isotrope Teile mit mehr Details benötigte. Den Filament-Druck nutzt das Team im Entwicklungsprozess zwar weiterhin, doch für die Fertigung von Prototypen auf Produktniveau stützt es sich jetzt auf Formlabs' Stereolithografie-3D-Drucker (SLA) des Typs Form 3+, wobei es auch von der „phänomenalen Auswahl an Materialien“ beeindruckt war. Da die wichtigsten Produktlinien von FINIS allerdings Schwimmflossen, Schwimmbrillen und Trainingsausrüstung umfassen, fehlte dem Team eines: nämlich ein haltbares, reines Silikon zur Herstellung von Teilen, die nah an die endgültigen Produktionsmaterialien herankommen.
In der Vergangenheit wurden Silikonteile bei FINIS, Inc. mithilfe von Formen gegossen, was ein arbeitsintensiver Prozess mit langen Durchlaufzeiten war. Jetzt ist das Team mit den 3D-Druckern des Typs Form 3+ und dem neuen Silicone 40A Resin ausgerüstet, dem ersten erschwinglichen Kunstharz aus 100 % Silikon für weiche, biegsame und robuste Teile. Damit kann das Team Änderungen in kurzer Zeit umsetzen und über Nacht funktionale Prototypen drucken.
„Es dauert ungefähr einen Monat, bis ein Werkzeug fertig ist. [Mit Silicone 40A Resin] kann ich mir neue Ideen einfallen lassen, Änderungen vornehmen und über Nacht drucken. Am nächsten Tag komme ich in den Dienst, entnehme das Teil, reinige es und kann es sofort im Pool testen. Was früher Wochen gedauert hat, schaffe ich jetzt innerhalb von Stunden, und das ist der wahre Vorteil für mich.“
David Beittel, Senior Designer bei FINIS, Inc.
Für seine interne Testphase, wo die Teile wiederholt unter Wasser geraten, hebt das Team die bemerkenswerte Wasserdichtigkeit des Materials hervor, wie auch seine unvergleichliche Rückprallelastizität, die andere silikonähnliche 3D-Druckmaterialien weit übertreffen. Das Produktentwicklungsteam ist beeindruckt, wie nah es dank der Elastizität von Silicone 40A Resin an die Charakteristika des letztendlichen Produktionsmaterials herankommt. Das macht es zum unschätzbaren Hilfsmittel für die Anpassung von Produktdesigns und unterstützt sie dabei, in allen Phasen des Entwicklungsprozesses optimale Leistung zu gewährleisten.
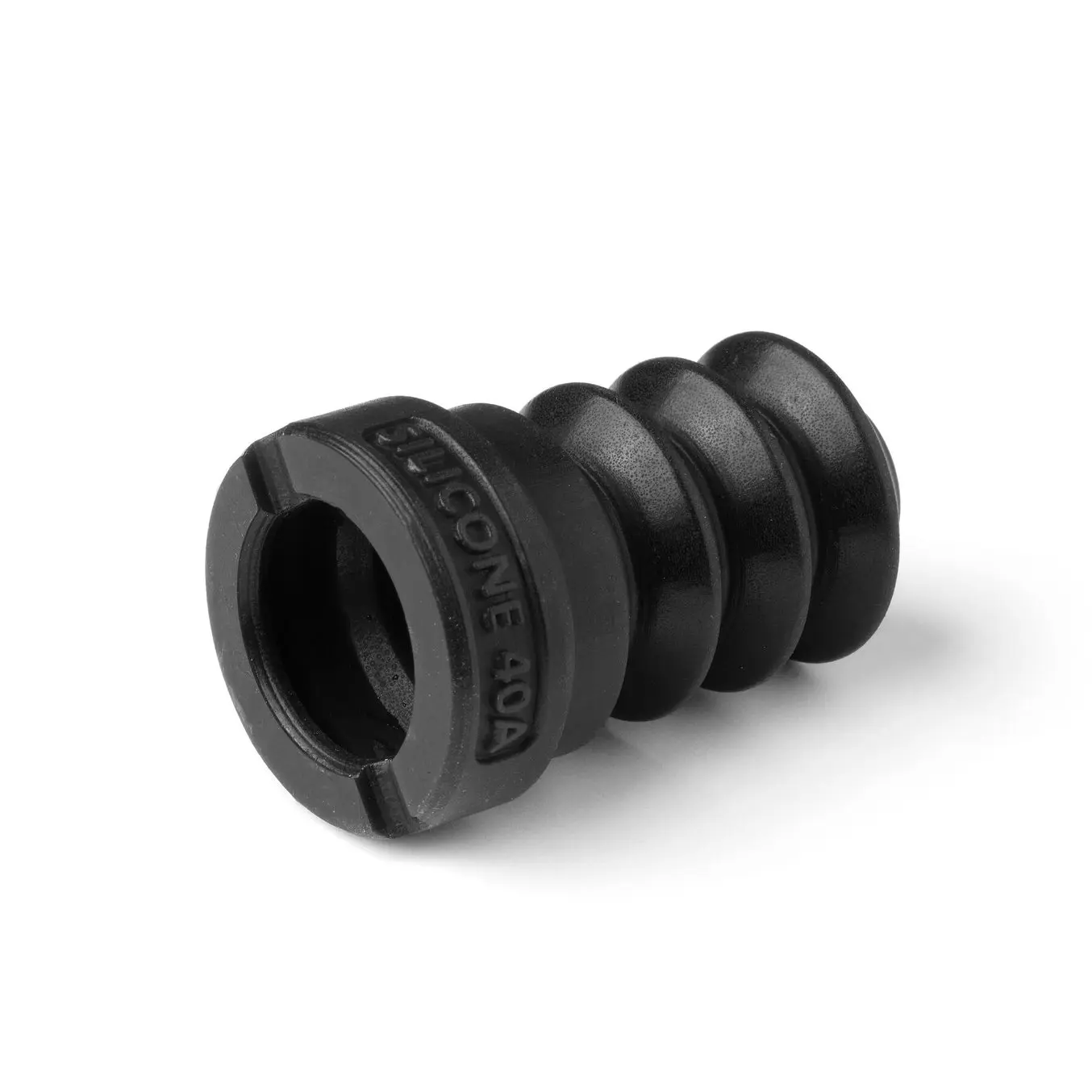
Kostenlosen Probedruck anfordern
Sehen und fühlen Sie selbst die Qualität von Formlabs. Wir senden Ihnen einen kostenlosen Probedruck aus Silicone 40A Resin an Ihren Arbeitsplatz.
Prototypen von Dichtungen: Ein neuer Ansatz mit Silicone 40A Resin
Typischerweise würde das Team zur Massenproduktion von Silikonteilen auf Spritzguss oder Formpressen zurückgreifen. Diese konventionellen Verfahren gehen jedoch mit kostspieligem Stahlwerkzeug und langen Durchlaufzeiten einher, die sich oft über Monate hinziehen. Deshalb lagert das Team den Urethanguss für Beta-Prototypen und Vorproduktionsteile bei der Produktentwicklung meist aus. Dies ist zwar ein beliebter Ansatz für die Produktion von Teilen im Dutzend, doch die Lieferzeiten betragen noch immer zwei bis drei Wochen, wodurch für Prototyping und schnelle Designiterationen nur eingeschränkte Möglichkeiten bestehen.
Um diese Herausforderung zu bewältigen, hat das Team den 3D-Druck in den Entwicklungszyklus integriert, was ihm die Möglichkeit gibt, Designs abzuändern und interne Tests durchzuführen, bevor es Produktionswerkzeug für die Testphase durch Anwender*innen herstellt. So kann das Unternehmen nun mehrere Schleifen von „Entwurf, Test und Überarbeitung“ durchlaufen und somit bessere Produkte abliefern.
Im Zuge der Entwicklung seiner neuesten intelligenten Schwimmbrille sah sich das Team von Finish, Inc. beim Prototyping der neuen Dichtungen mit einem Problem konfrontiert. Das kleine Modul, das die Runden, die Schwimmzüge und die Zwischenzeiten misst und in die Schwimmbrille hineinpassen soll, muss sich leicht ein- und ausschalten lassen. Die Aufgabe war also, eine Dichtung mit integriertem Druckknopf zu entwickeln, der über dem Knopf dieses Moduls ausgerichtet ist, ohne dass die Wasserdichtigkeit beeinträchtigt wird.
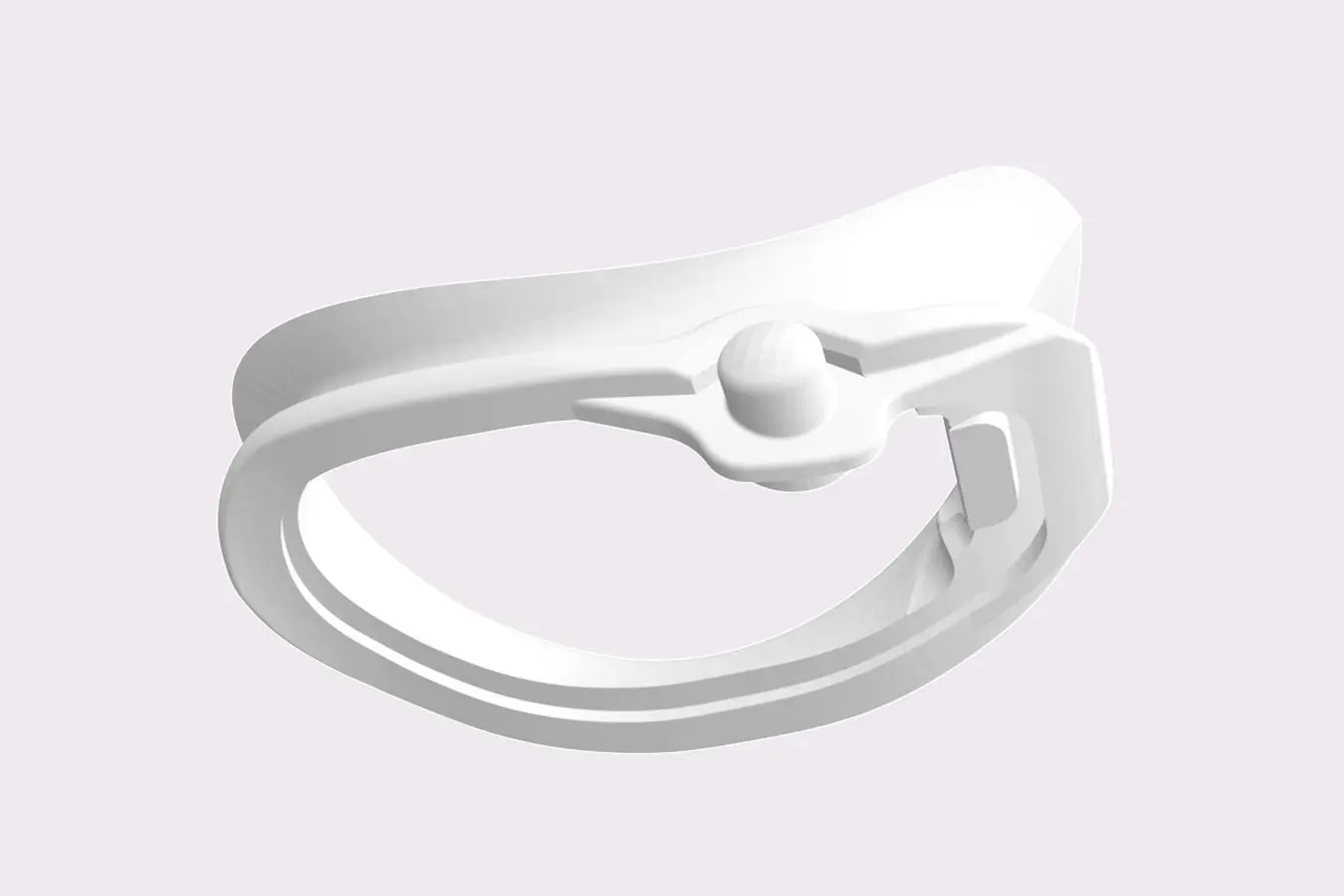
Die neue Smart Goggle hat eine komplexe Geometrie, da ein Druckknopf integriert werden musste.
Bevor es zum Urethanguss für die Beta-Testphase übergehen konnte, musste das Team das Design iterieren. „Der Druckknopf war ein kniffliges Design und eine Herausforderung im Prototyping“, erzählt Beittel. Früher hätte das Team Prototypen für solche Dichtungen aus Elastic 50A Resin 3D-gedruckt. Allerdings haben silikonähnliche 3D-Druckmaterialien nicht genug Federkraft und kehren nicht so wie Silikon in ihre Form zurück. Elastic 50A Resin eignete sich zwar gut für die ersten Prototypen, doch schließlich war ein Material gefragt, dass nah an das Silikonmaterial für die endgültige Produktion herankommt. „Für die Dichtungen brauchten wir ein Material für Rapid Prototyping mit etwas Federkraft. Andere Materialien konnten zwar gebogen werden, aber sie sprangen nicht wie Silikon zurück.“
Produktion von Dichtungsprototypen für Schwimmbrillen
Durchlaufzeit | Kosten | |
---|---|---|
Urethanguss | 2–3 Wochen | 1220 € für ein Set von 2 Dichtungen |
3D-Druck mit Silicone 40A Resin | 8 Stunden | 10 € pro Dichtung |
Als Beittel und sein Team schließlich Silicone 40A Resin zur Verfügung hatten, wurden die Prototypen zunehmend besser. Das neue Material hat eine deutlich höhere Rückprallelastizität und ist damit dem Produktionsmaterial sehr ähnlich. Das Team verwendete die aus Silicone 40A Resin 3D-gedruckte Dichtung für interne Tests und war begeistert davon, wie gut das Material an der Augenpartie abschloss und wie wasserdicht es war. Beittel berichtet: „Es war am Ende eine schöne Bestätigung, dass ich dadurch tatsächlich erste Schüsse in einem Produktionswerkzeug ersetzen konnte und das Material sehr vergleichbar war.“
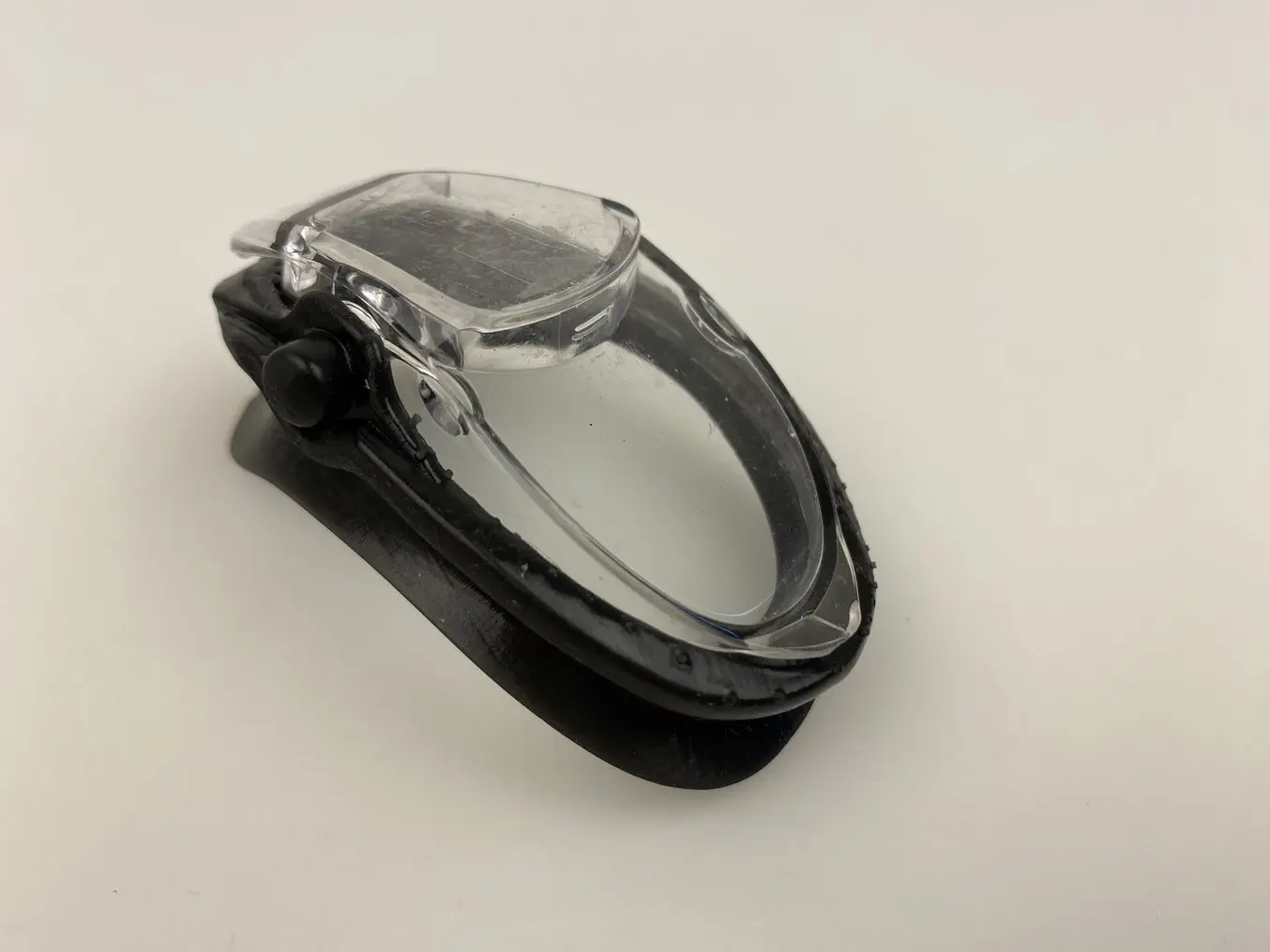
Das Team verwendete die aus Silicone 40A Resin 3D-gedruckte Dichtung für interne Tests und war begeistert davon, wie gut das Material an der Augenpartie abschloss und wie wasserdicht es war.
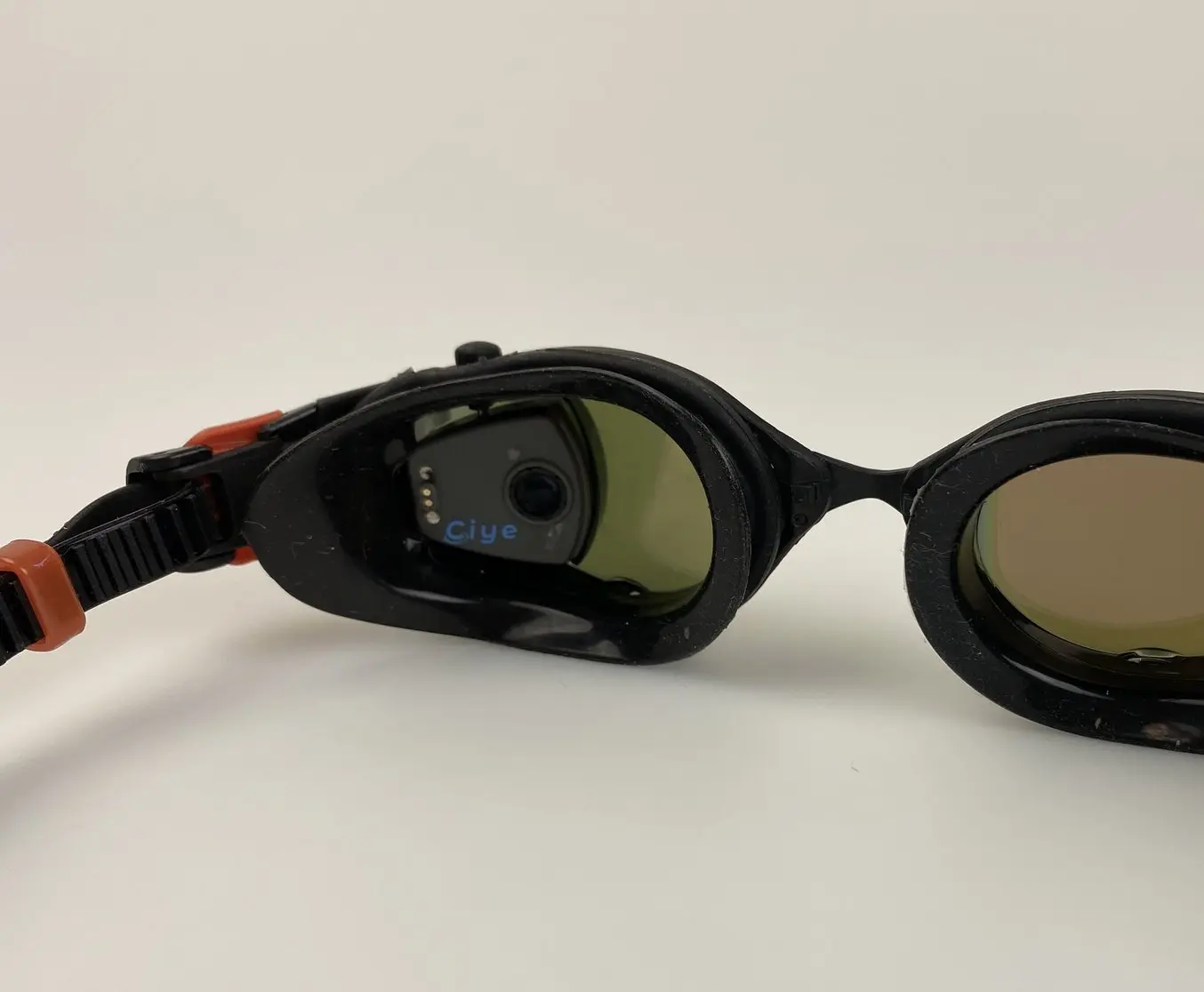
„Ich habe die neue Dichtung aus [Silicone 40A Resin] eingesetzt, bin ein paar Wochen lang damit geschwommen und war beeindruckt. Sie war ein bisschen weicher als das Produktionsmaterial, aber sie versiegelte die Augenpartie sehr gut. Ich hatte überhaupt keine Undichtigkeiten und war überrascht, dass das Material ohne zusätzlichen Klebstoff um die Linse und den Druckknopf herum dicht hielt.“
David Beittel, Senior Designer bei FINIS, Inc.
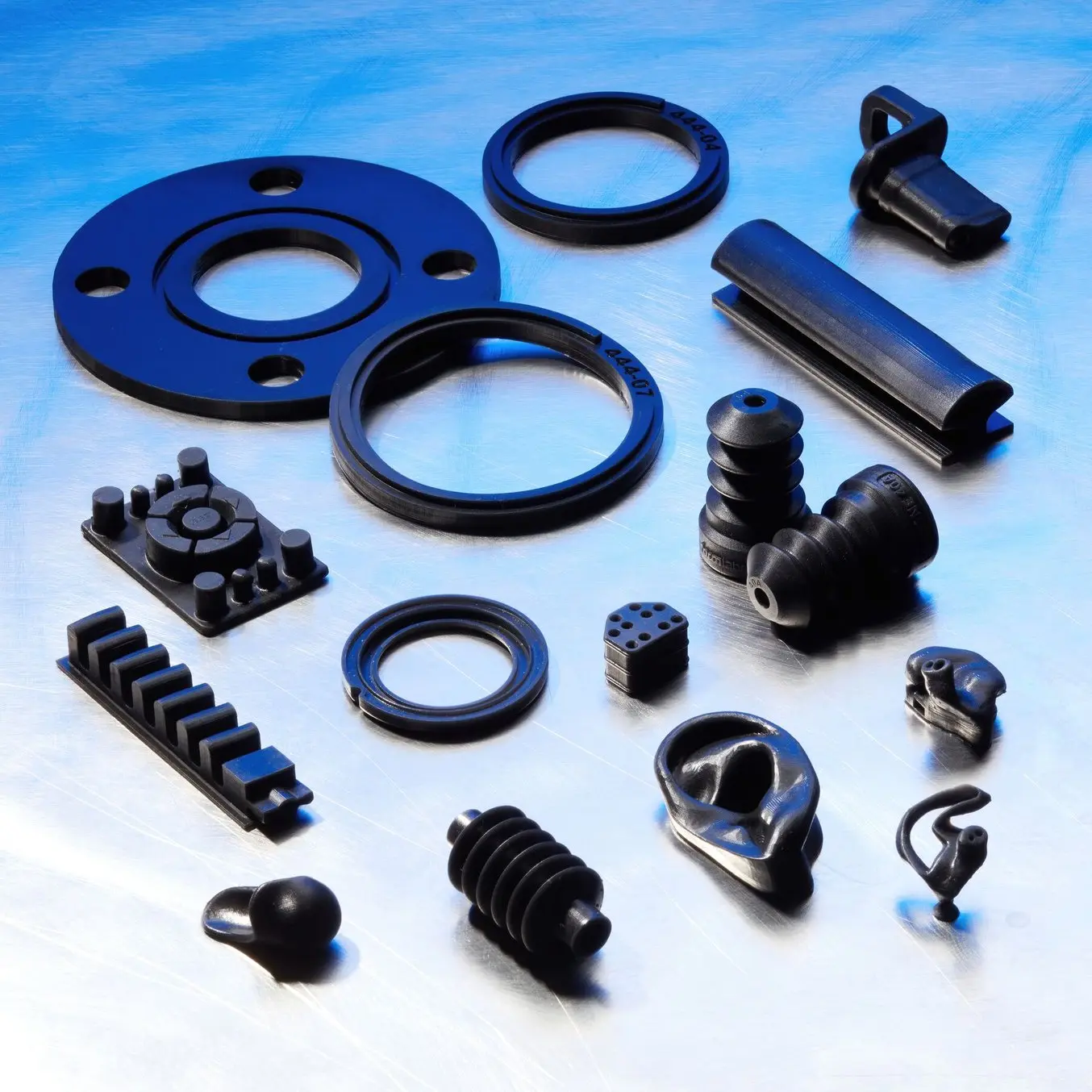
Einführung in Silicone 40A Resin
In diesem Webinar führt Sie unser Expertenteam für 3D-Druck durch die zentralen Vorteile und Anwendungsbereiche von Silicone 40A Resin und stellt die Materialeigenschaften und den Arbeitsprozess dieses Kunstharzes vor.
Flexibel und schnell: Entwicklung von Schwimmausrüstung mit SLA-3D-Druckern
Eines der beliebtesten Produkte von FINIS, Inc. ist der MP3-Player mit Knochenschallleitung für unter Wasser. Aufgrund der Popularität des Produkts begann das Team an einer neuen, kompakteren Version zum Tragen über dem Ohr zu forschen. Eine Schwierigkeit hierbei war jedoch, dass das Headset leicht instabil war, wenn die Schwimmer*innen abrupte Bewegungen ausführten, wie etwa das Abstoßen von der Beckenwand bei der Rollwende. Beittel und sein Team versuchten das Problem zu lösen, indem sie einen kleinen Zusatz aus Silikon entwickelten, der sicher am Headset angebracht werden kann, sodass der Halteriemen der Schwimmbrille darüber geführt wird und das Headset stabilisiert.
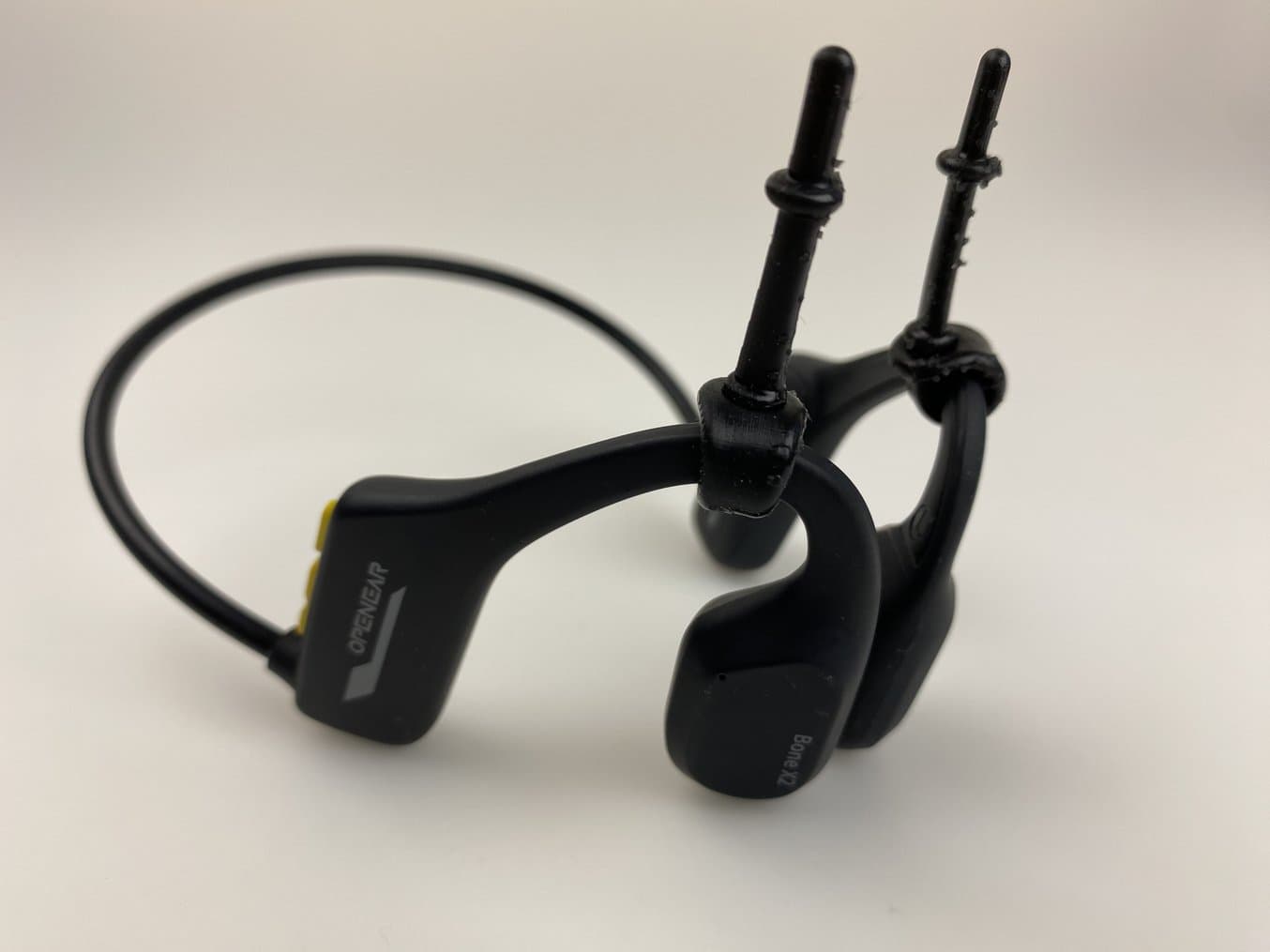
Das Team entwickelte ein kleines Zubehörteil aus Silikon, um das Headset zu fixieren und ihm Stabilität zu geben.
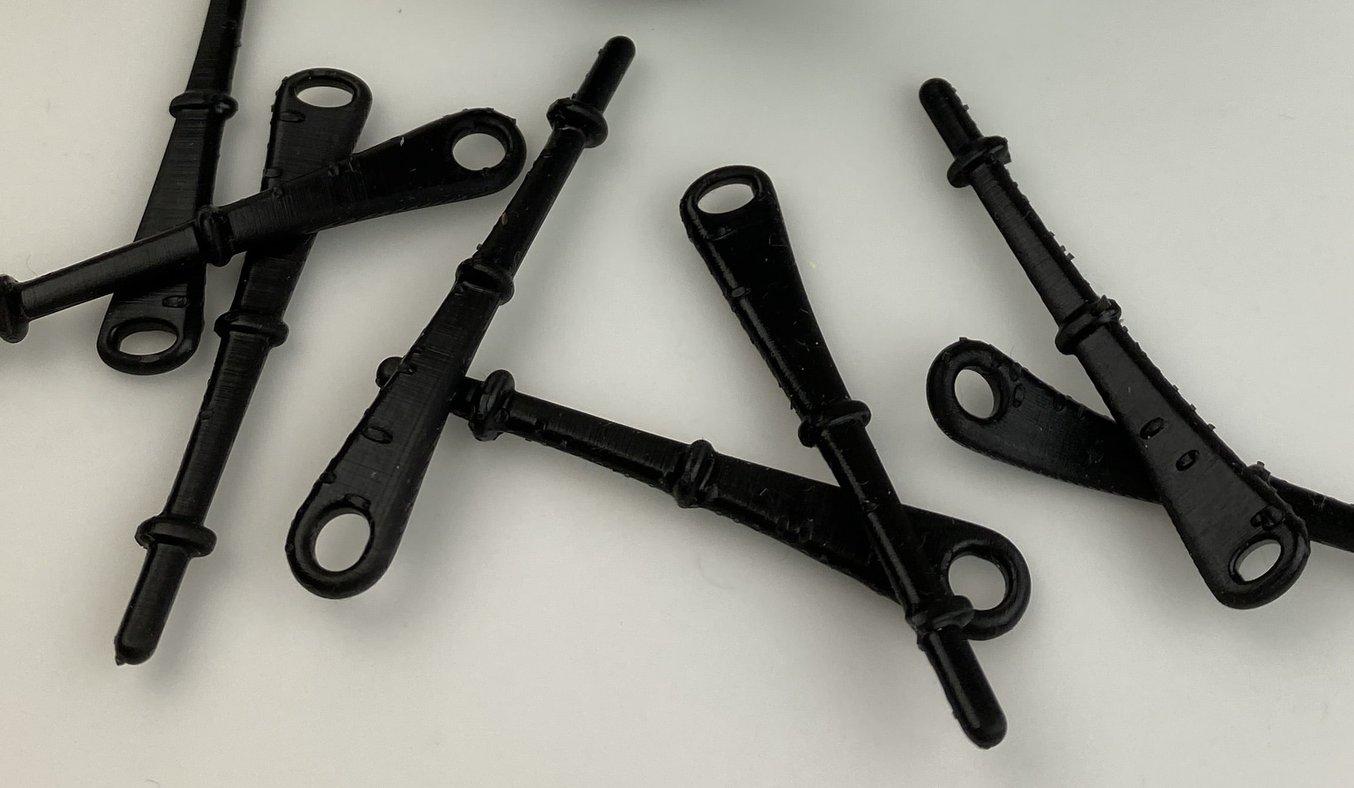
Das Produktentwicklerteam testete verschiedene 3D-gedruckte Iterationen, um diesen Zusatz zu optimieren. „Wir führten kleine Veränderungen durch, um zu sehen, welche Variante für die Anwender am leichtesten aufzusetzen war, welche im Becken gut funktionierte“, erzählt Beittel. Früher nutzte das Team silikonähnliche Materialien aus Formlabs' Materialbibliothek, stellte jedoch fest, dass diese nicht die nötige Elastizität hatten, um durch die Löcher zu passen und für einen festen Sitz am Headset zu sorgen. Außerdem waren Sie rissanfälliger.
Die Elastizität und Robustheit von Silicone 40A Resin hat den Prozess der Prototypenentwicklung stark verbessert und konnte beide Probleme effektiv lösen. Wie Beittel hinzufügt, ist ihm auch wichtig, wie ein Material aussieht, wie es sich anfühlt und sich verhält, damit er beurteilen kann, wie ähnlich es dem Produktionsmaterial ist. Ihm gefällt besonders, dass dieses Kunstharz sich nicht setzt, sondern seine Form auch nach wiederholtem Einsatz beibehält.
„Es hat die Haptik und die Eigenschaften eines Produktionsmaterials. Mir gefällt, dass es leicht federt, es springt viel besser in seine Form zurück, statt sich zu setzen. Ich glaube, es kommt einigen unserer Produktionsmaterialien nahe – allemal nahe genug, um es in der Entwicklungsphase einzusetzen.“
David Beittel, Senior Designer bei FINIS, Inc.
Ohne den 3D-Druck hätte sich das Team auf den Spritzguss mit einem kleinen Werkzeug gestützt und die Gussform bei Bedarf angepasst. Das hätte den Prozess allerdings erheblich verlangsamt, da jede Iteration mindestens einen Monat Durchlaufzeit erfordert hätte. Beittel betont, dass Silicone 40 Resin einen schnellen Entwicklungszyklus möglich macht, denn Entscheidungen können getroffen werden und Druckteile werden sofort produziert und getestet.
Auf diese Weise kann das Team die Modelle konkretisieren und sicherstellen, dass sie ordnungsgemäß funktionieren, bevor es das endgültige Produktionswerkzeug bestellt. „Sobald man mit dem Werkzeugbau beginnt, ist man eingeschränkt. Man kann zwar noch ein paar Änderungen vornehmen, aber die dauern meist lange, sind teuer und verringern die Qualität des Werkzeugs.“
Eine weitere Anwendung, die stark auf die Elastizität von Silicone 40A Resin angewiesen war, sind die Meerjungfrauflossen, die in den vergangenen Jahren große Popularität erlangt haben. Je mehr Menschen in die „Welt der Meerjungfrauen“ eintreten, wie Beittel es ausdrückt, umso wichtiger wird es für das Unternehmen, Trends zu folgen und das Produkt auch an die größeren Fußgrößen der Männer anpassen zu können, die nun ebenfalls mit Meerjungfrauen schwimmen. Das Team wollte den Markt testen, bevor es mehrere Versionen dieses Produktes massenproduzierte. Hierfür entwarf das Entwicklerteam eine Riemenerweiterung, die an die Fußöffnung angefügt werden kann, um diese für jegliche Füße geeignet zu machen.
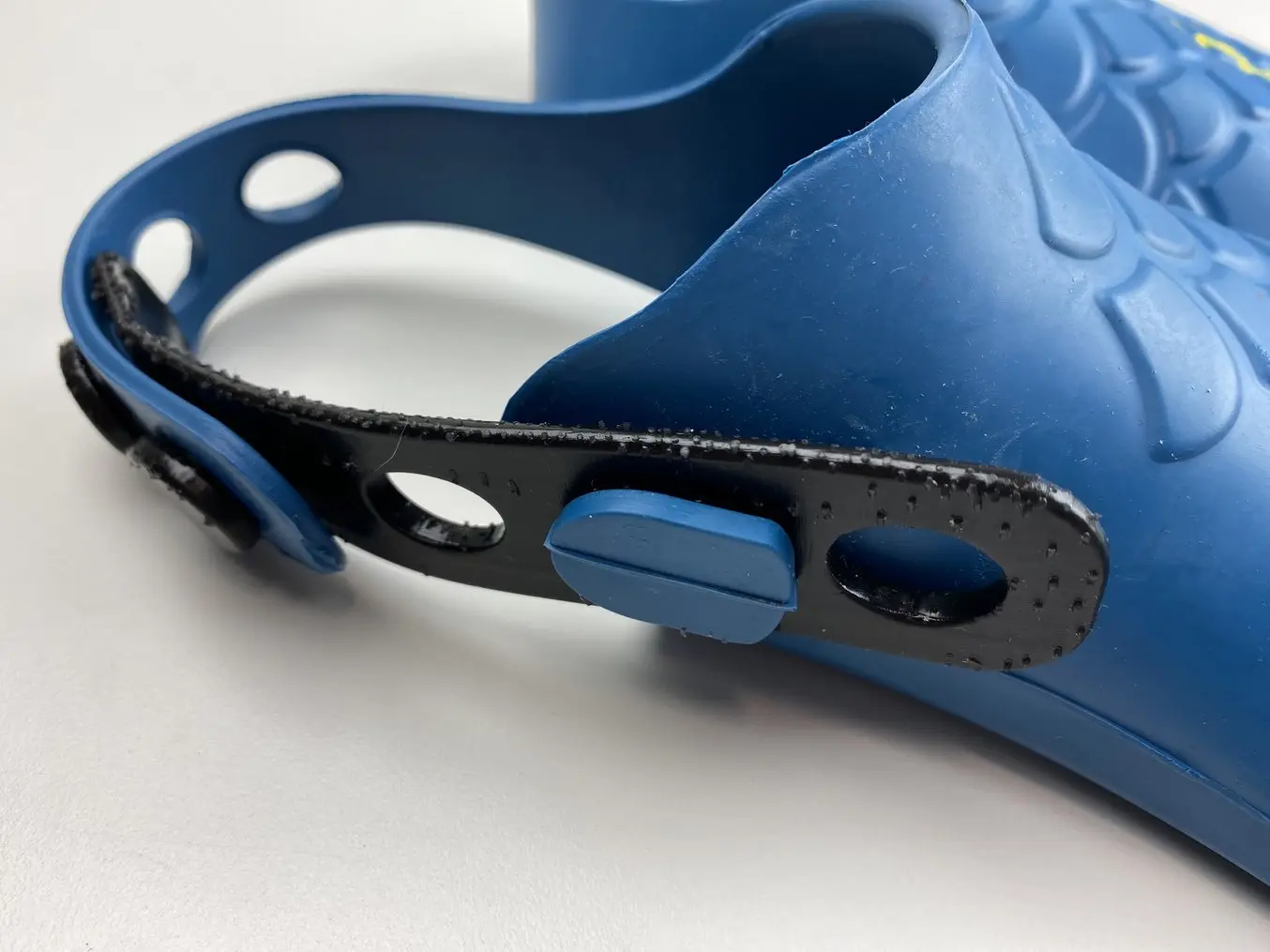
Das Produktentwicklungsteam entwickelte eine Riemenerweiterung zur Anpassung an alle Fußgrößen.
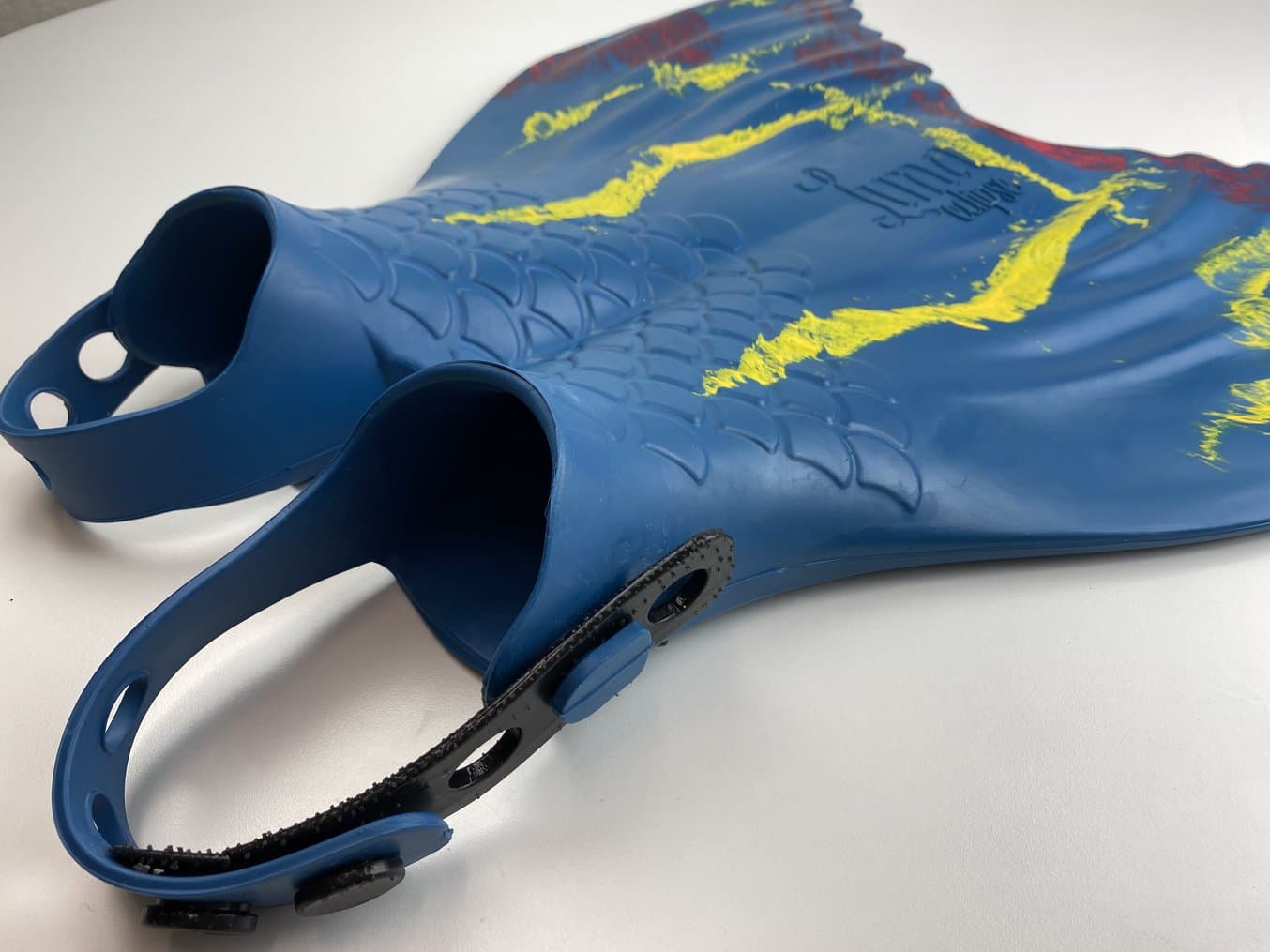
Wie schon beim vorigen Fall, testete das Team hierfür zunächst andere flexible Materialien, bevor es Zugang zu Silicone 40A Resin erlangte, und es steht außer Frage, dass das neue Material eine ganz eigene Klasse darstellt. Flexible 80A Resin und Elastic 50A Resin eignen sich zwar gut für erste Prototypen und Designiterationen, aber sie sind nicht in der Lage, wiederholter Spannung und Belastung standzuhalten, sodass es bei Tests oft zu Rissen kommt, während die Elastizität von Silicone 40A Resin beispiellos hoch bleibt.
Der Kopfsprung in die Zukunft der Schwimmausrüstung
„Für diesen Preis einen betriebsinternen SLA-Drucker zu haben, ist einfach klasse. Ich hätte nie geglaubt, dass das einmal möglich wäre“, meint Beittel.
Seine Arbeitsprozesse durch Silicone 40A Resin zu ergänzen, erlaubte dem Produktentwicklerteam von FINIS ein noch schnelleres Prototyping. Beittel war begeistert, wie gut sich das Material für funktionale Prototypen eignete und dass es dank seiner hervorragenden mechanischen Eigenschaften selbst internen Tests von Schwimmbrillendichtungen und verschiedenen anderen Gummikomponenten standhielt.