Unveiling the Magic: How Formlabs 3D Printers Shape Blockbuster Movie Props
Did you know that Formlabs 3D printers have played a major role in bringing some of your favorite movies and TV shows to life? We often underestimate the hard work and talent behind the scenes, where dedicated individuals combine traditional craftsmanship with cutting-edge technologies like 3D printing to bring props to life. From the epic Marvel Cinematic Universe to the far, far away galaxies of Star Wars, and even the creepy Upside Down from Stranger Things, our printers have helped bring fantastical worlds to life!
Read on to discover how a touch of Formlabs 3D printing technology can feel like magic.
Crafting Imagination: 3D Printing Transforms Prop Creation in Entertainment
The entertainment industry is always looking for the next big thing and the best technology to work seamlessly and effectively. Russell Bobbitt, Property Master at Marvel Studios, known for his work on Iron Man, Avengers: Endgame and Guardians of the Galaxy Vol. 2, says that “3D printing is just an everyday event. It’s a very useful tool” in the entertainment industry.
Marvel's Prop-Making Marvels: The 3D Printing Magic Behind the Scenes
The Marvel Cinematic Universe has made use of 3D printers on many occasions during the prop-making process. On average, Bobbitt estimates that about 100 props per film involve 3D printing.
The famous prop master gives the example of Thor’s new hammer, Stormbreaker, seen for the first time in Avengers: Infinity War. The iconic prop was 3D printed in 34 different pieces that were then assembled similarly to a trophy.
Additionally, Bobbit mentions Tony Stark’s Arc Reactor, which he defines as the most labor intensive prop he’s ever made. Indeed, this legendary prop that makes Iron Man who he is takes quite some time to develop. It’s a lot of back and forth, especially since Robert Downey Jr. is very involved in the development and design of the Arc Reactor. Bobbit and Downey Jr. worked together on the initial drawing and design, Bobbitt 3D printed it, and together they tested it for visual and mechanical performance.
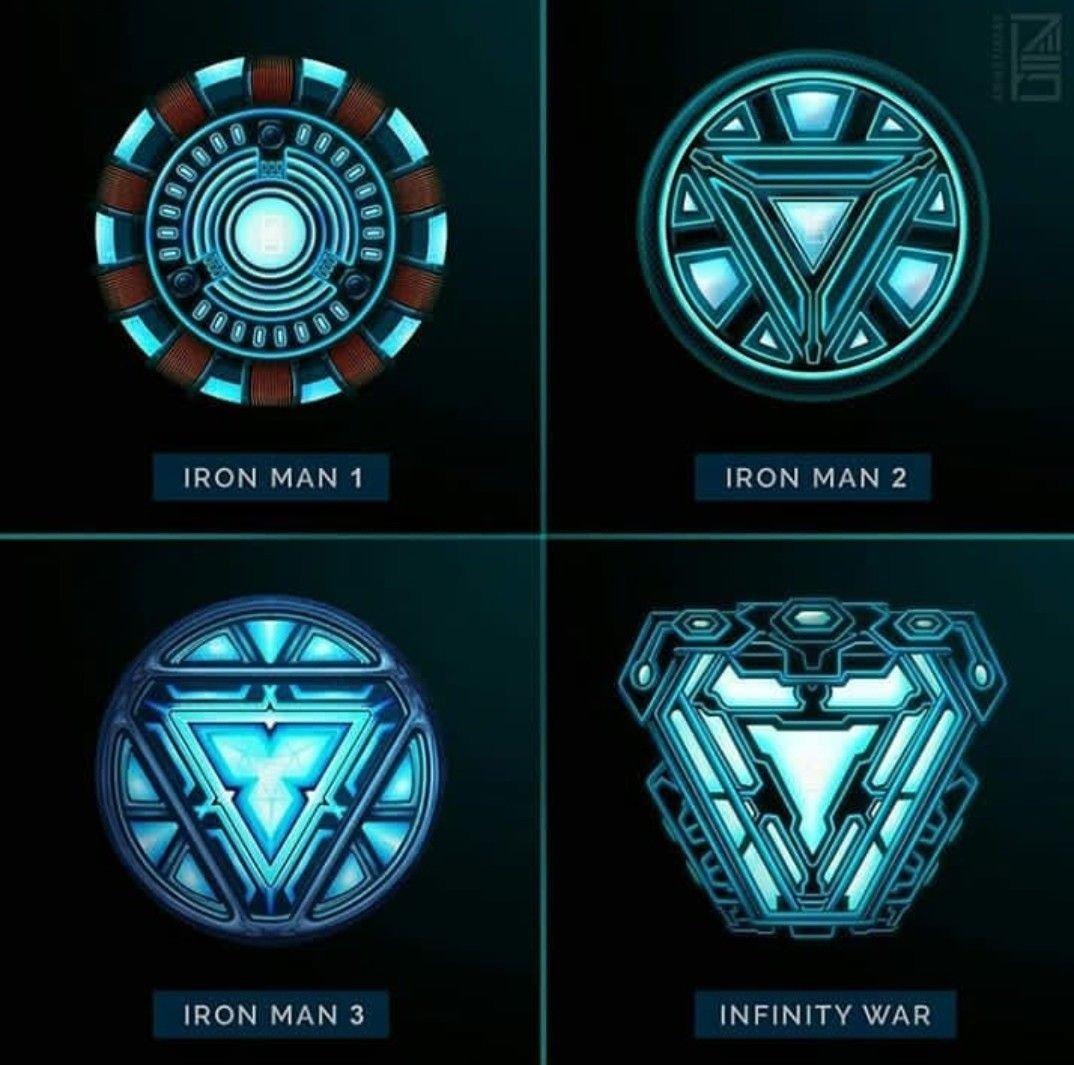
The different Arc Reactors for each Iron Man movie or appearance
“This is probably the most intricate prop that we make,” Bobbitt states. “The Arc Reactors are the most difficult parts we make, but they’re also the closest to my heart.”
Fang-tastic Secrets: 3D Printing in the Making of Renfield
Another popular movie that benefitted from 3D printing during its production is the long-awaited 2023 comedy-horror film, Renfield. Inspired by the 1897 novel Dracula by Bram Stoker, the film follows Renfield, a lawyer played by Nicholas Hoult, as he attempts to escape his boss’s clutches, the legendary character, Count Dracula (played by Nicholas Cage).
In order to get into character and adopt the ghoulish appearance that characterizes the well-known vampire, Cage had to go through three hours of preparation, every day. This lengthy process included applying prosthetics, makeup, adding hairpieces, and most importantly, putting on the dentures that define Dracula. The dentures were custom-made by a dental technician who scanned Cage’s teeth to design the iconic fangs, and then printed them on the Form 3B+.
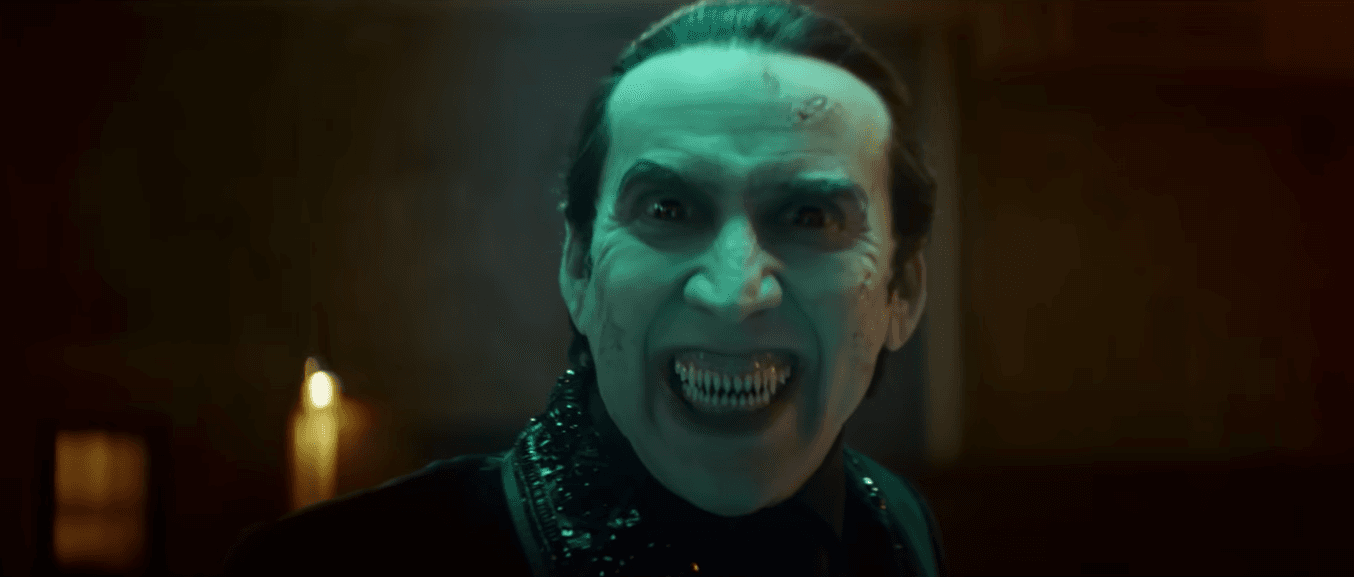
Source: Renfield (2023)
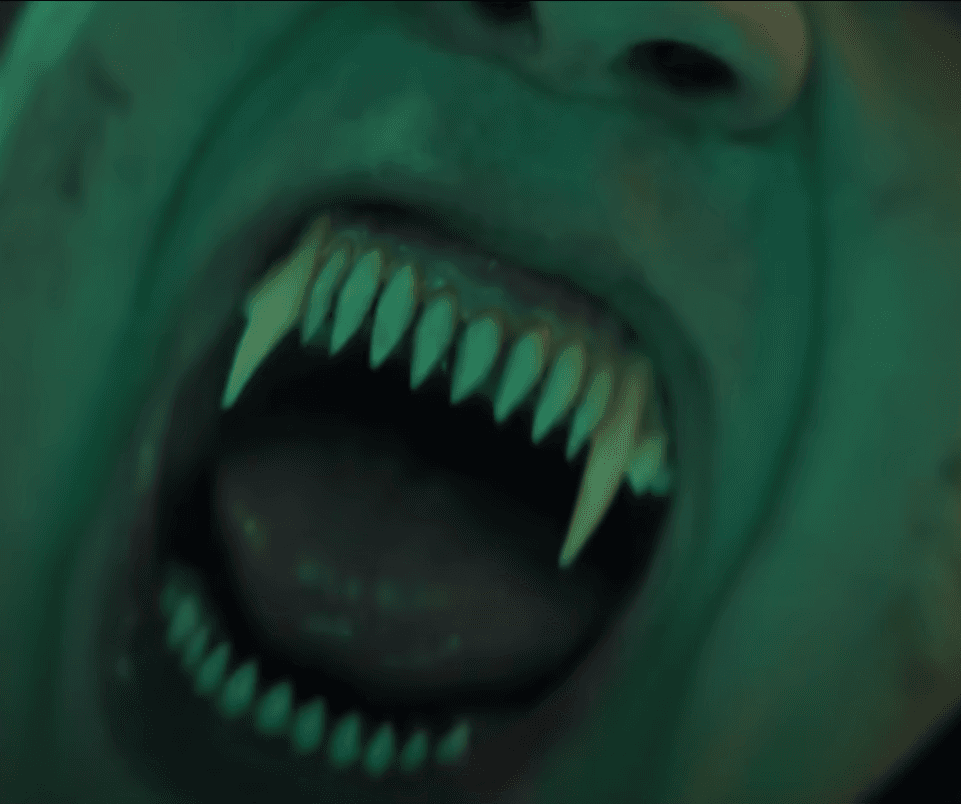
The custom-fit and lifelike design of the dentures gave Cage the ability to speak clearly and fully embody the spirit of Dracula, without the inconvenience of cumbersome prosthetics.
Formlabs Empowers VFX Magic at Aaron Sims Creative
Can you guess what Wonder Woman, Teenage Mutant Ninja Turtles, Aquaman, Stranger Things, and Ready Player One have in common? These productions and many more have called on Aaron Sims Creative, an award-winning visual effects studio, to help develop their unforgettable worlds and creatures.
The company started in 2005 as a design studio and quickly evolved into a VFX company. Since then, their team of creatives have worked on some of Hollywood’s biggest blockbusters and streaming services biggest hits, bringing superheroes and monsters to life.
The workflow at Aaron Sims Creative relies heavily on their fleet of Formlabs 3D printers. When working on new projects, the team receives a design brief based on the script and works alongside the director to develop creatures and environments. After developing the first drawings, the team prints the creature and shares their vision with the team.
One of their first projects on the Formlabs printer, and probably one of their most famous endeavors, is the creation of the Stranger Things Demogorgon. ASC printed and painted their vision of the Demogorgon to introduce it to the producers of the show. Steffen Reichstadt, Creative Director at Aaron Sims Creative, insists on the impact of creating a physical model, saying, “Printing something off for clients really helps them solidify that that concept is where they’re going to go.” He adds, “They’re going to spend a couple hundred million dollars on the film, they want to know that the design they’re picking is the correct one.”
From Pixels to Print: The Mandalorian's 3D-Printed Razor Crest
The overwhelming success of Stranger Things was one of the first examples of streaming services' investment into high quality content paying off. More recent programs have followed, like Disney+'s The Mandalorian, which also benefits from the use of 3D printing in prop technology. In fact, a number of well-known small-screen productions have benefited from Formlabs technology over the years.
The new Star Wars series has captivated audiences worldwide with its compelling storytelling and immersive visuals. Many have praised it for its ability to capture the essence of the original Star Wars trilogy while offering a fresh narrative.
Combining iconic elements of the original productions with new characters and storylines have turned it into a hugely successful addition to the Star Wars universe. According to the team at Industrial Light & Magic, the renowned visual effects company founded by George Lucas in 1975, one of the most exciting elements they had the chance of developing for the Mandalorian was the new spaceship, the Razor Crest.
Today's technology allows for many visual effects to be done digitally, but when the production team suggested building a miniature big enough to shoot for the show, Landis Fields, Virtual Production Visualization Supervisor at ILM, stepped in and offered to 3D print it.
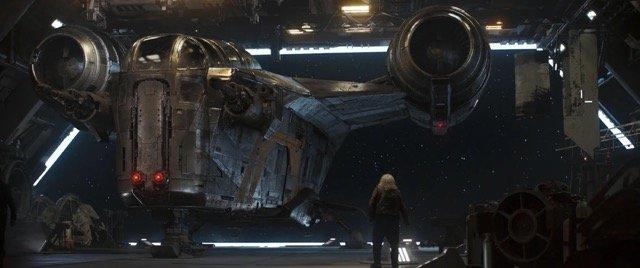
The Razor Crest from The Mandalorian
Using the Form 2, Fields printed many different parts that would eventually be assembled by John Goodson, the model maker, to become the impressive piece of machinery that is the Razor Crest. It took a tremendous team effort and the crew combined new and old motion control techniques to shoot the different scenes, which made the project all the more exciting. In the end, the crew used quite a few shots of the miniature in the show and it is quite difficult to tell them apart from the CGI-generated shots. Can you tell the difference?
The Art of Sci-Fi Prop Making: "Raised by Wolves" and 3D Printing
"Raised by Wolves," the 2020 dystopian TV show set in a future where Earth has been destroyed, is another prime example of how Formlabs 3D printers have been instrumental in creating captivating visuals. Jaco Snyman, the founder of Dreamsmith and lead Prosthetics Designer of the series, and his team faced the daunting task of bringing the sci-fi world to life.
In Season 1 of the show, the Dreamsmith team used a fleet of Form 2s and Form 3s to bring their vision to reality. From mold making to end-use parts, the precision and versatility of Formlabs 3D printers enabled them to enhance their workflow quickly in response to testing or script changes. Snyman attests that, “3D printing has definitely enhanced the manufacturing of sci-fi themed props” in a significant way.
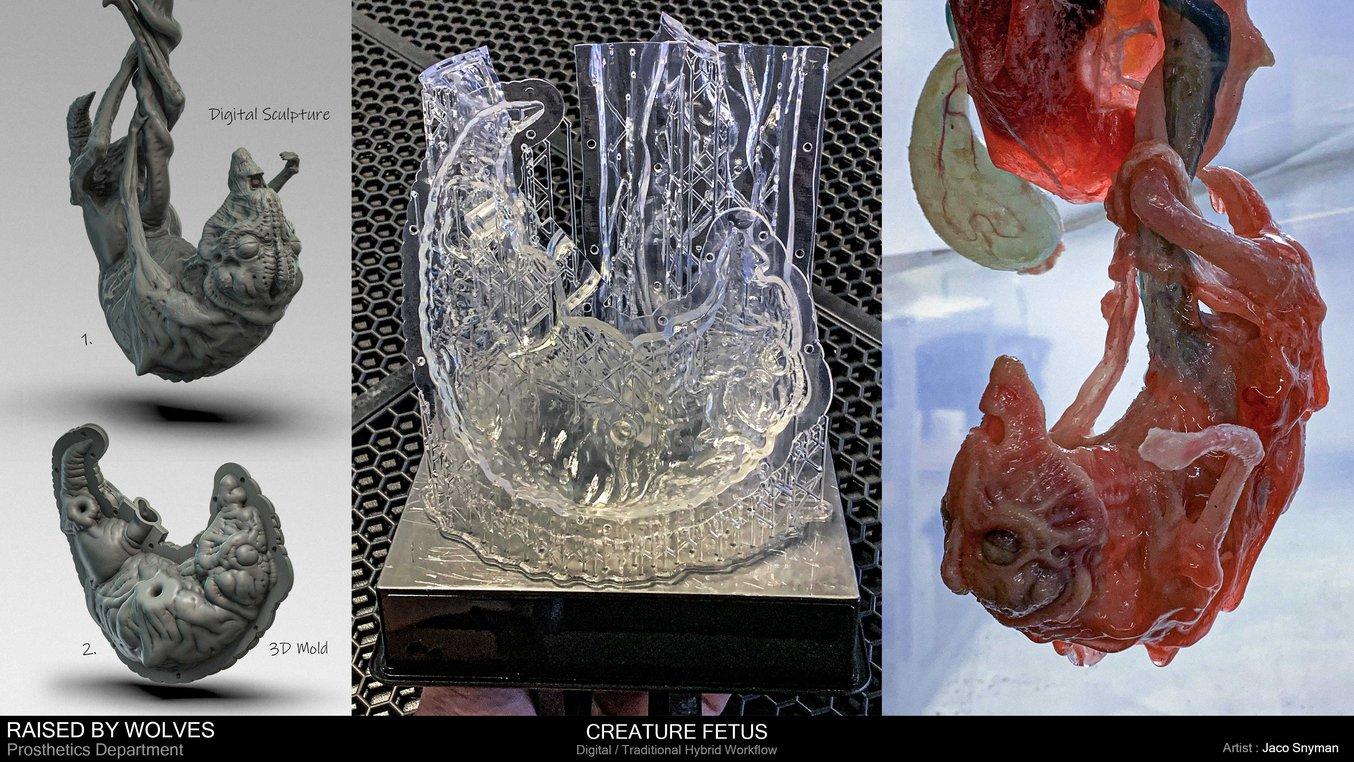
Digital sculpture and digital 3D mold (left), 3D printed mold (middle), and the final silicone part (right).
For example, in order to get creative approval from the director, this alien fetus was sculpted digitally and then 3D printed. Once it was approved, the Dreamsmith team designed and printed a negative mold that would enable them to generate the final piece in silicone.
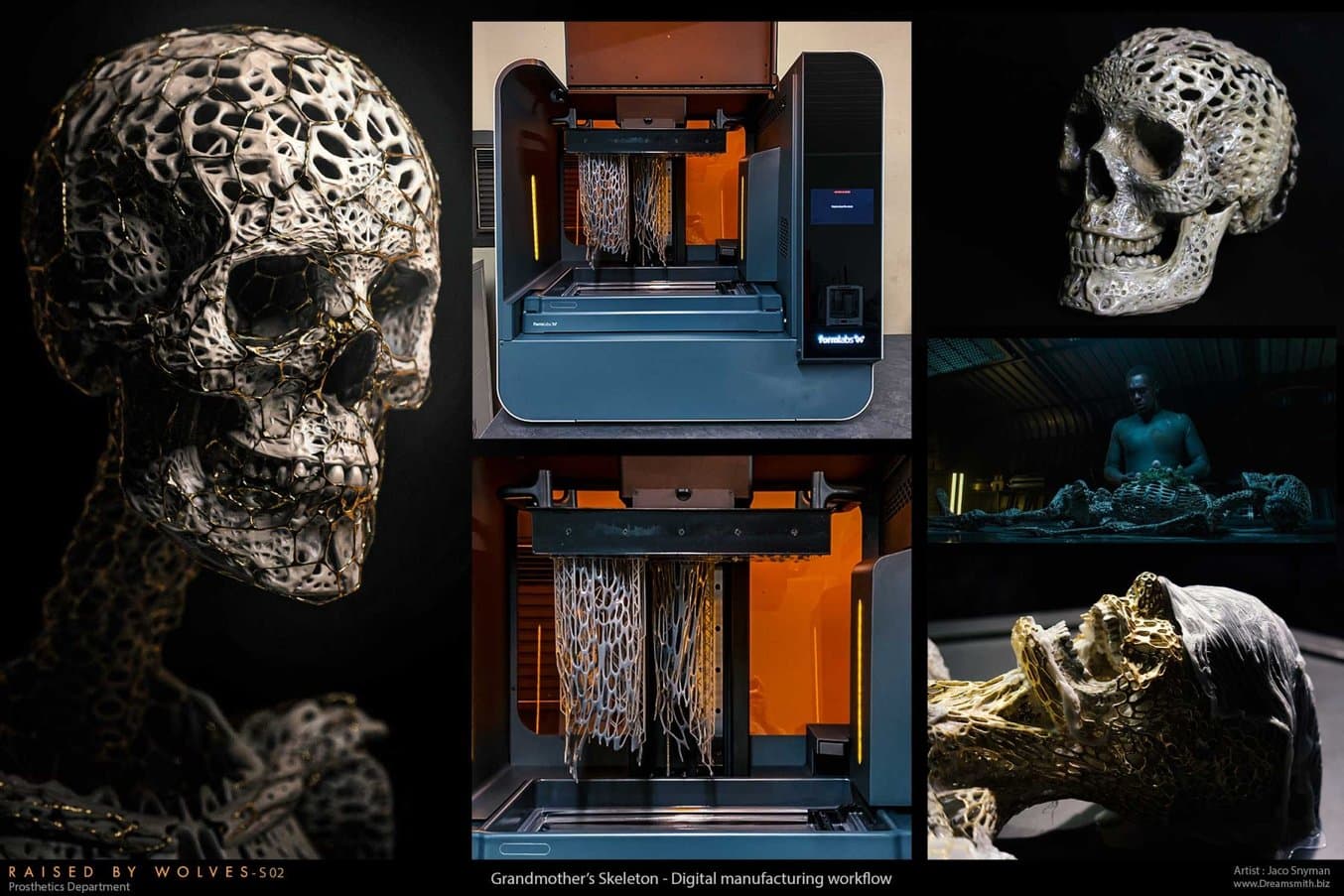
Biomechanical skeleton 3D printed on the Form 3L.
As Season 2 of “Raised by Wolves” approached, the Dreamsmith team recognized the value of the Form 3L and expanded their fleet by acquiring four Form 3L’s. This upgrade allowed the team to print large-scale pieces for the show, therefore providing extra flexibility and creative freedom in the design process. Calling the Form 3L an “incredibly powerful tool,” Snyman raves about how significantly it has impacted their workflow in two short years.
“This is a prop that would have been practically and financially impossible to create without the use of the Form 3L” says Snyman in regards to the 3D printed skull seen above. The geometric flow and the intricate details would have made this prop almost impossible to sculpt out of clay, or using traditional techniques. Thanks to the Form 3L, the team was able to print the prop in practical chunks at high resolution.
Chase Me: Embracing Fear in a Fully 3D Printed Film
So far we’ve listed many productions that used 3D printing to develop their props and optimize their workflow throughout production, but what if we told you that there is a film that was fully created on a 3D printer?
This is the case for Chase Me, produced by Gilles-Alexandre Deschaud, it is a three minute short-film that was entirely printed on a Form 1+ using 80 liters of Formlabs Clear, Black, and Grey resin. The film started as an animated film which was then printed frame by frame with each second of film consisting of 15 different frames. This amazing project took two years and included 6000 hours of printing, 2500 prints, and 300 hand-painted prints.
“Chase Me is a story about embracing your fears, and turning them into something beautiful,” says Gilles-Alexandre Deschaud.
Formlabs 3D Printing in the Entertainment Industry
The impact of Formlabs 3D printing technology on the entertainment industry, specifically in prop creation, has been nothing short of remarkable. From blockbuster movies to highly anticipated TV shows, the seamless integration of 3D printing has brought fantastical worlds, iconic characters, and intricate details to life.
Not only has 3D printing enhanced the visual quality and realism of props, it has also streamlined production workflows, enabling creative teams to iterate quickly, receive client approvals, and ultimately deliver stunning results. From the design phase to the final product, Formlabs has become a useful tool empowering prop makers, visual effects artists, and filmmakers to push the boundaries of reality.