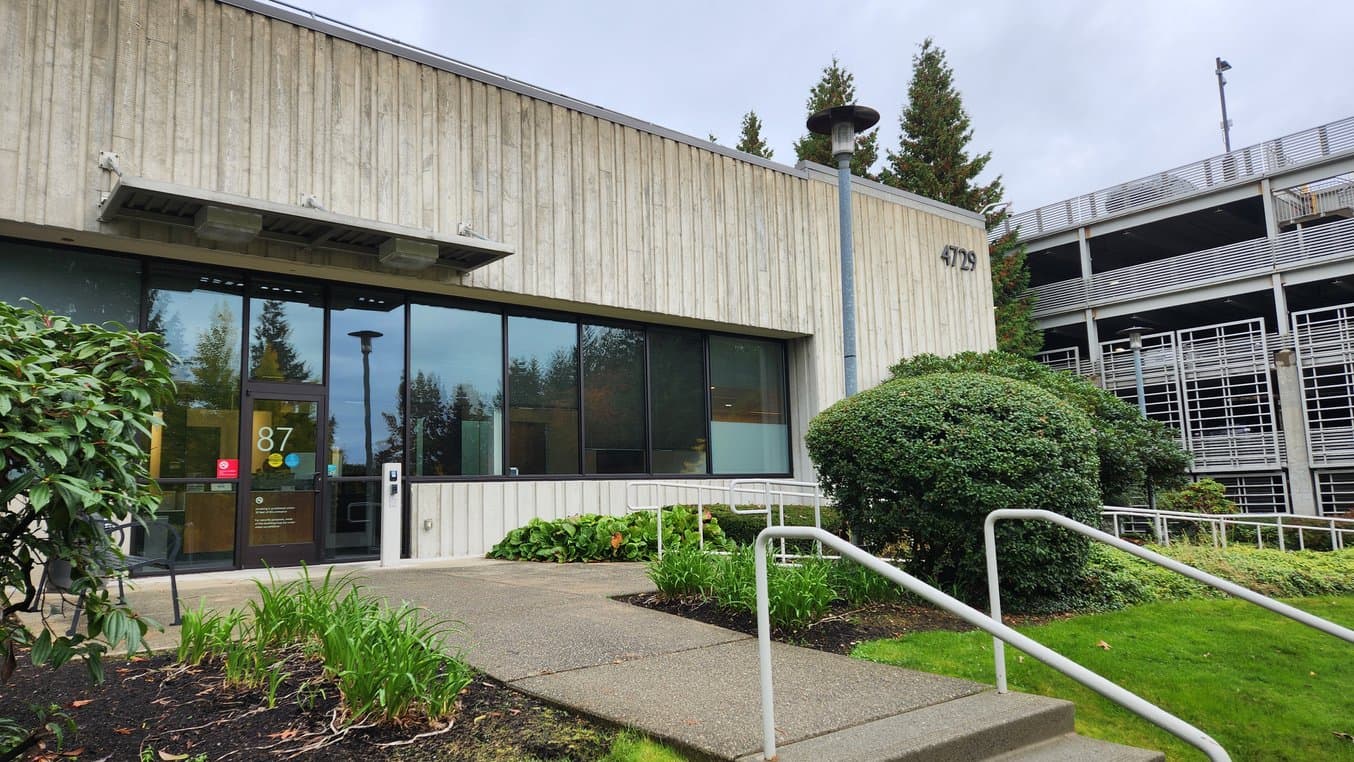
There are multiple reasons Microsoft, a member of the tech industry vanguard, has stayed so long at the cutting edge of both hardware and software. Being a leader in a fast-paced industry requires speed without compromise, an obsession with pursuing the highest quality ideas, and a commitment to holding every part to an exacting standard.
For eight years, Mark Honschke has led rapid prototyping at Microsoft’s Advanced Prototyping Center (APC), where 95% of the tech giant’s hardware products are designed, tested, or developed. The APC stays true to Microsoft’s commitment to speed — Honschke likens the center’s work to ‘running a marathon at a sprinter’s pace.’ His team takes in requests from over 80 hardware categories — and multiple teams within those categories — while consistently delivering on a 24-hour turnaround time.
Adding Form 4 and Form 4L to the fleet has enabled Honschke to run more printing shifts — switching over some builds from overnight to a ‘day build’ schedule to accelerate iteration and improve productivity. In addition to their desktop and benchtop stereolithography (SLA) printers from Formlabs, the APC also runs two Fuse Series selective laser sintering (SLS) printers for end-use quality, functional nylon parts.
"Form 4 is our go-to choice for projects needing tight tolerances and engineering-grade materials. It produces high-performance parts with amazingly fast print times and makes it possible for our model makers to produce multiple iterations in a 24-hour period.”
Mark Honschke, Additive Prototyping Lead at Microsoft’s Advanced Prototyping Center
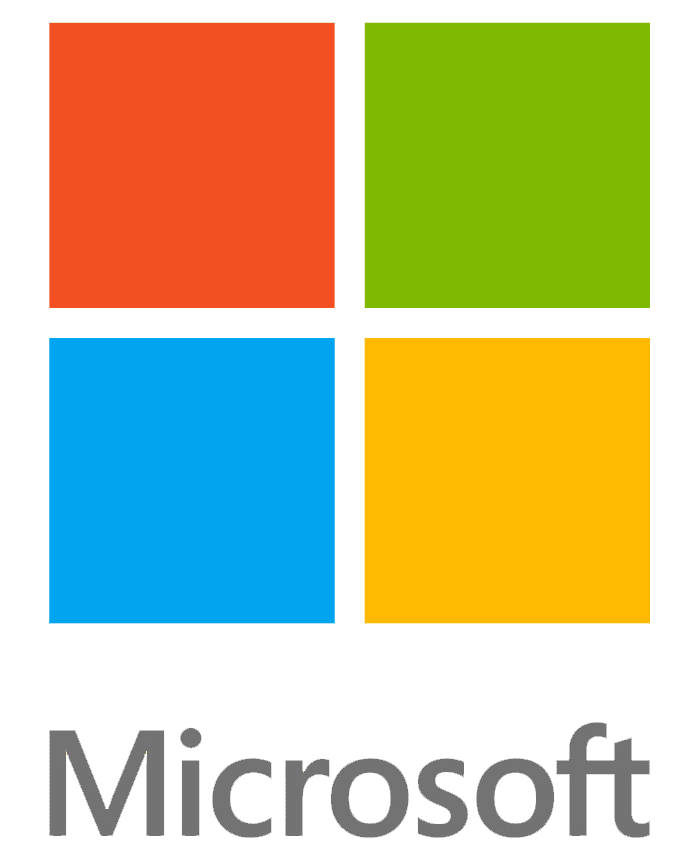
Inside Microsoft’s Advanced Prototyping Center: Where Prototypes Are Printed in 3D
In this discussion and Q+A, you'll get an exclusive look at the APC’s service bureau model — a centralized hub that functions as an internal production service for Microsoft’s hardware teams.
How Formlabs 3D Printers Fit In At Microsoft
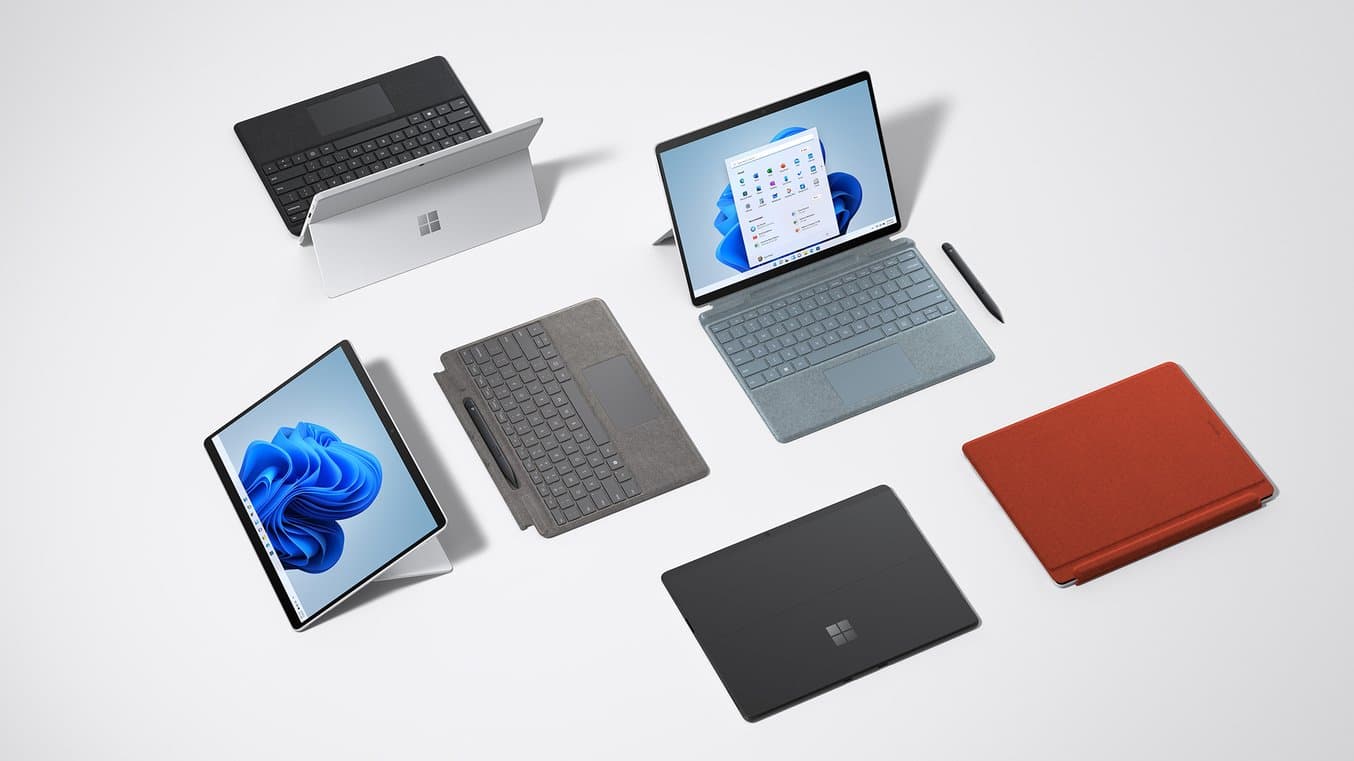
The APC used Formlabs 3D printers to fulfill requests for proof of concept (POC) assembled builds for Surface tablets.
The APC has multiple printers running every day and every night. With 80 product categories and different projects within those categories, each day might bring different parts, but the volume stays constant. To handle the consistent stream of requests, the APC has several fused deposition modeling (FDM) printers, two Formlabs selective laser sintering (SLS) Fuse 1+ 30W printers, seven full-color PolyJet machines, and five Formlabs SLA 3D printers, including Form 4 and Form 4L.
Honschke’s team operates as an internal service bureau; they decide which material and machine will be the best fit for a part and discuss it with the requester before setting it up, printing, post-processing, and delivering, all within 24 hours.
This service bureau model, though incredibly fast, was still not fast enough for a specific group within Microsoft — the Architects. “The Architects live between the designers and the engineers. They’ll take information from the design team and create a sketch, then prototype until the designers are satisfied with how that product is experienced. Then they’ll hand it to the engineers to become a producer of that product,” says Honschke. “They’re constantly working in this blue sky area, and not always on the same schedule.”
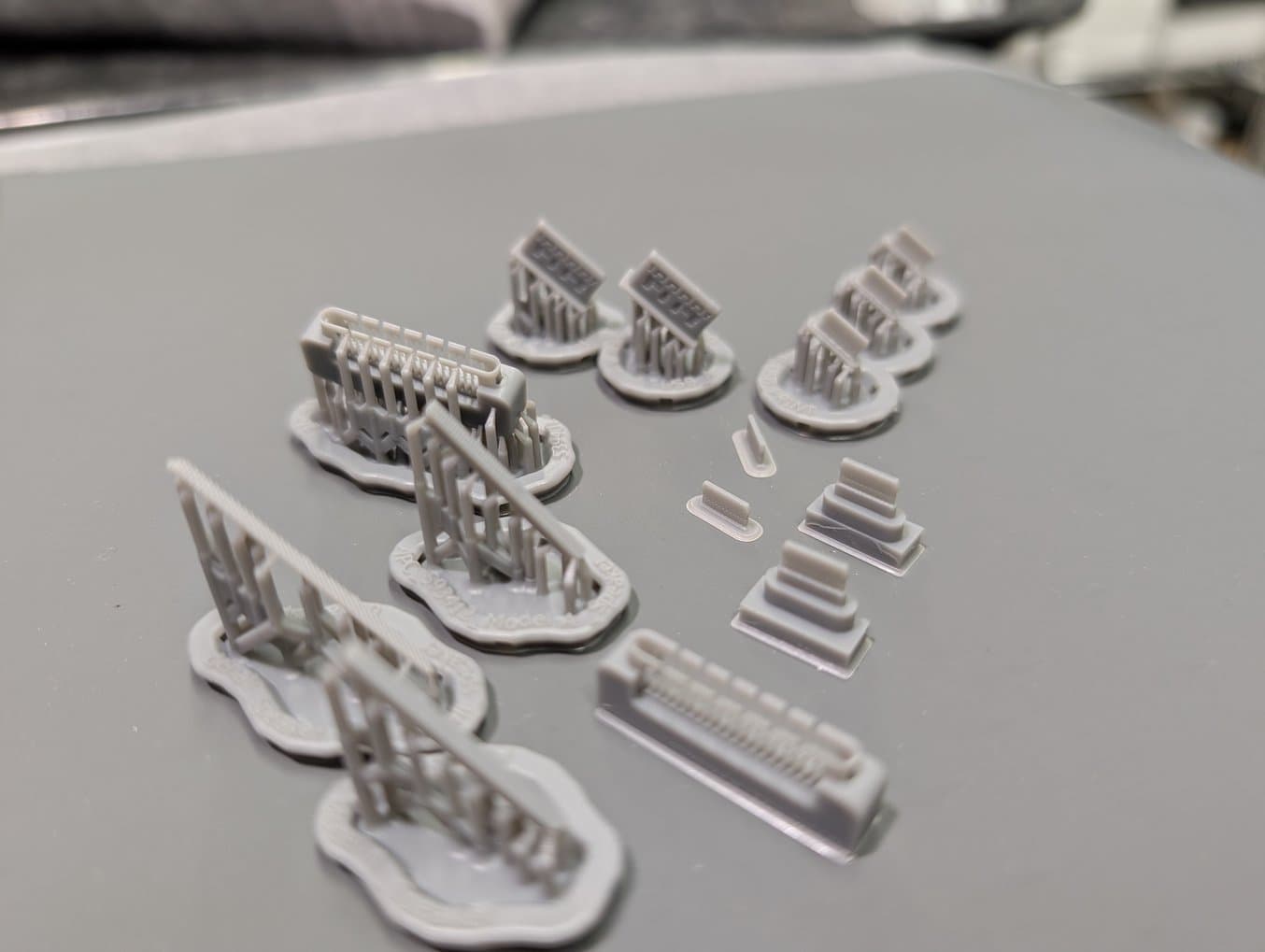
SLA 3D printing is ideal for prototyping components that require high accuracy, such as these connectors.
The APC needed extra printing capacity that was easy to use, affordable, fast, and could deliver high-quality parts in a range of materials. One Architect who had used Formlabs machines at a previous job suggested Form 3, though that grew quickly to include Form 3L, Fuse 1+ 30W, Form 4, and now Form 4L.
“For me, the Formlabs technology is pretty much a tool that we have to have. A big portion of my job is looking at the fleet of printers in comparison to the types of requests we’re getting, then finding the holes in our capabilities and finding the right technology to fill those holes. Formlabs fills a very specific role for us. It’s not general 3D printing, though Formlabs does that very well. It’s very much engineering-grade materials at a high resolution and a quality surface finish.”
Mark Honschke, Additive Prototyping Lead at Microsoft’s Advanced Prototyping Center
The material versatility and range of mechanical properties available through the Formlabs ecosystem let the team pick the right resin for each specific job. Being able to easily switch between the materials, even multiple times a day with Form 4 and Form 4L’s fast print times, means Honschke’s team can choose the best resin for the job — not print with whatever’s set up on the printer for the sake of expediency.
“Tough 2000 Resin is our mainstay material. Grey Pro and Tough 2000 are engineering grade strength at super high resolution, which we really can’t get in almost any other technology,” says Honschke.
Adding Form 4 to the Microsoft APC
At the APC, Honschke will take requests until about 4:00 PM before starting the printers to run overnight. In the morning, after the prints are taken off, post-processed, and delivered, they’ll look for new requests that can be completed as day-builds. A high-accuracy printer that can turn a part from an overnight into a day-build can dramatically improve the fleet’s productivity.
“One part I ran on Form 3+ was an 8 hour 19 minute print. On Form 4 it was just over two hours. So now we can utilize these printers for day-builds, especially with the new speed that we’re seeing — Form 3+ wasn’t considered day-build technology,” says Honschke.
For a lab dealing with the enormous volume that the APC does — hundreds of parts a week — running a day-build instead of waiting overnight helps the Microsoft workflow stay streamlined. Some parts may be new products that are still in the early design stages where a light-bulb moment might not last overnight. Others are factory fixes and re-designs that could keep production running or save time and money in the assembly process.
“Being able to iterate multiple times in a 24-hour period is our lab’s goal. Everybody’s putting in a request, and some of those answers are very time-based. They need to understand why this part may be failing so they can get back to the factory and tell them, ‘Here’s the change in the geometry to make this work,’” Honschke told us.
Since adding Form 4 into the workflow, the team has been printing multiple times a day, and was able to switch over some capacity from other SLA printers right away. “We were printing within minutes of turning the machine on. The setup was pretty straightforward. We really like the new wiper design and the new lock-in mechanism for the resin tanks,” says Honschke.
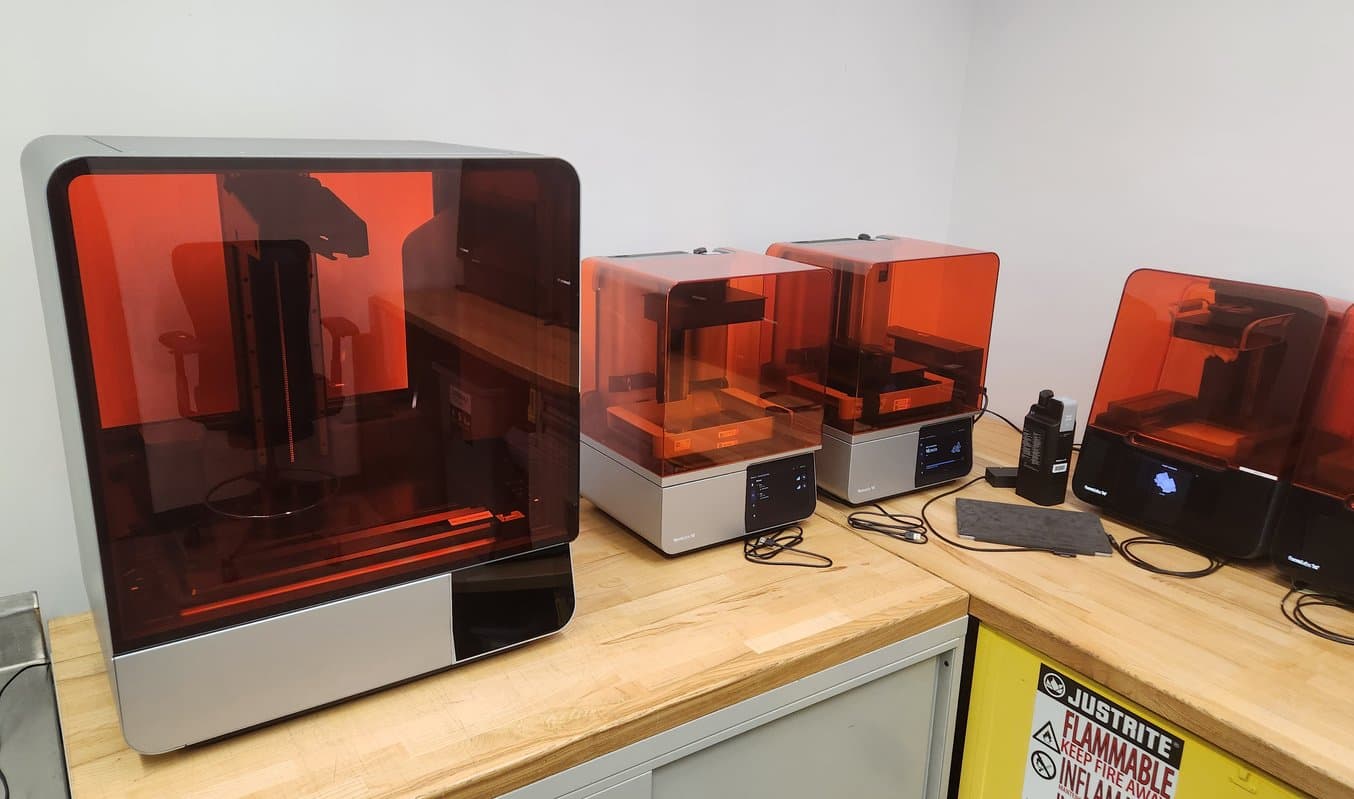
APC now runs five Formlabs resin 3D printers, including two Form 4s and a Form 4L.
Speed and ease of use aren’t everything when it comes to successful prints, however. Surface finish and print quality are still of utmost importance — many of these parts will go on to be final design approval units or mock-ups, and they need to look the part.
“On some small parts, I noticed the surfacing tends to be better than previous printers. For transparent parts we’ll go Formlabs because you get less of that layered refraction, and you’ll get a more genuinely clear part — I’ve told people, it’s the closest thing you can get to completely clear in SLA resin,” says Honschke.
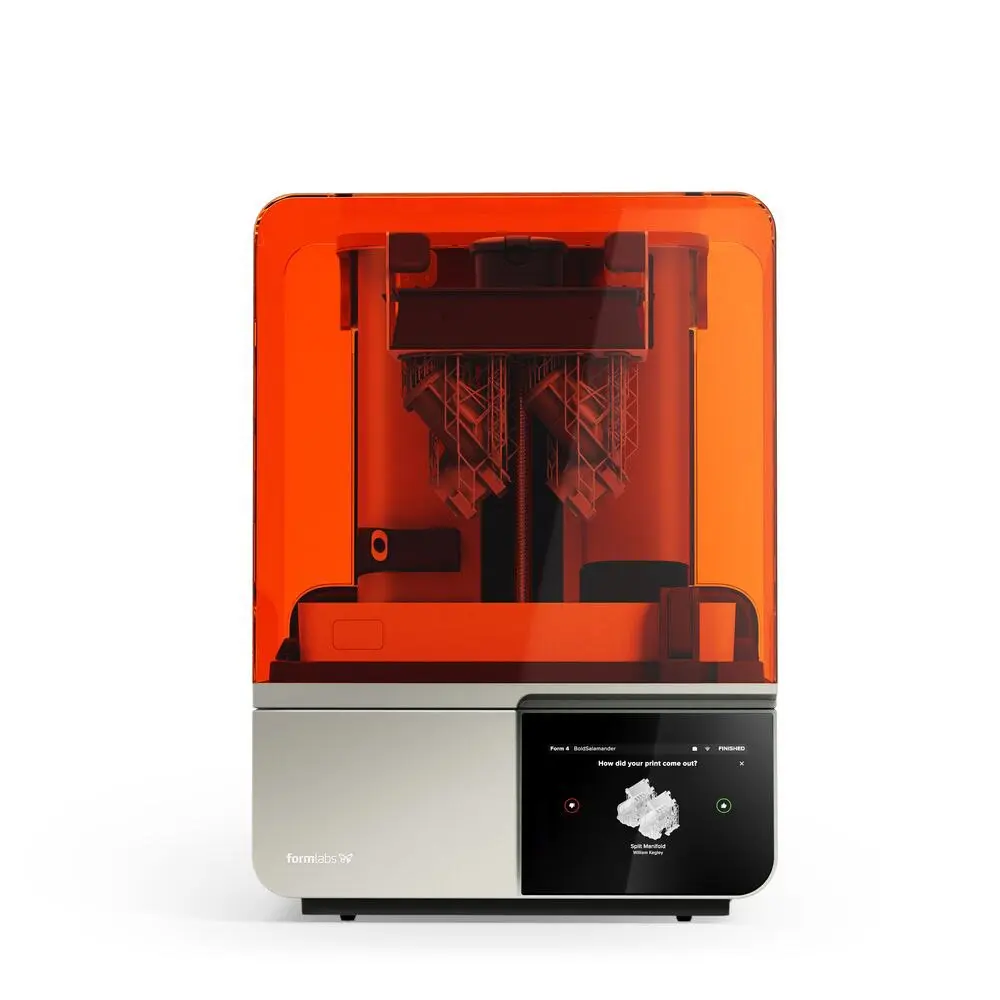
Product Demo: Form 4
See how Form 4 can enable new levels of productivity and innovation through its unmatched speed, accuracy, and reliability.
Form 4L: Increasing Form Factor at the APC
Since adding Form 4L to the APC, Honschke and his colleague Ryan Laprise have been able to take in more jobs and increase the throughput of the center.
A colleague recently requested a tablet enclosure that was larger than the build volume of the lab’s Form 4 printers and needed to be done fast. “This is a build we couldn’t do before Form 4L, the turnaround time would have taken too long, and 3D printing wouldn’t be an option. It would have slowed down the iterative process,” says Honschke. The 3D printing team put the prototypes on Form 4L and delivered the parts that same afternoon. “At four hours, it’s a game changer if we can get it,” says Honschke.
But print time isn’t the full story — it’s the pre-process and post-process time that can also have an impact on a team’s productivity and efficiency. Form 4L has simplified the workflow for resin 3D printing for the APC, shortening both prep work and finishing work to help them get parts from concept to delivery even faster.
The Form 4L build volume makes breaking pieces in half a thing of the past, and gives the team an option for quick parts during the day as well as higher volumes overnight. In post-processing, smaller touchpoint tips for the supports have shortened the time it takes to get parts finished.
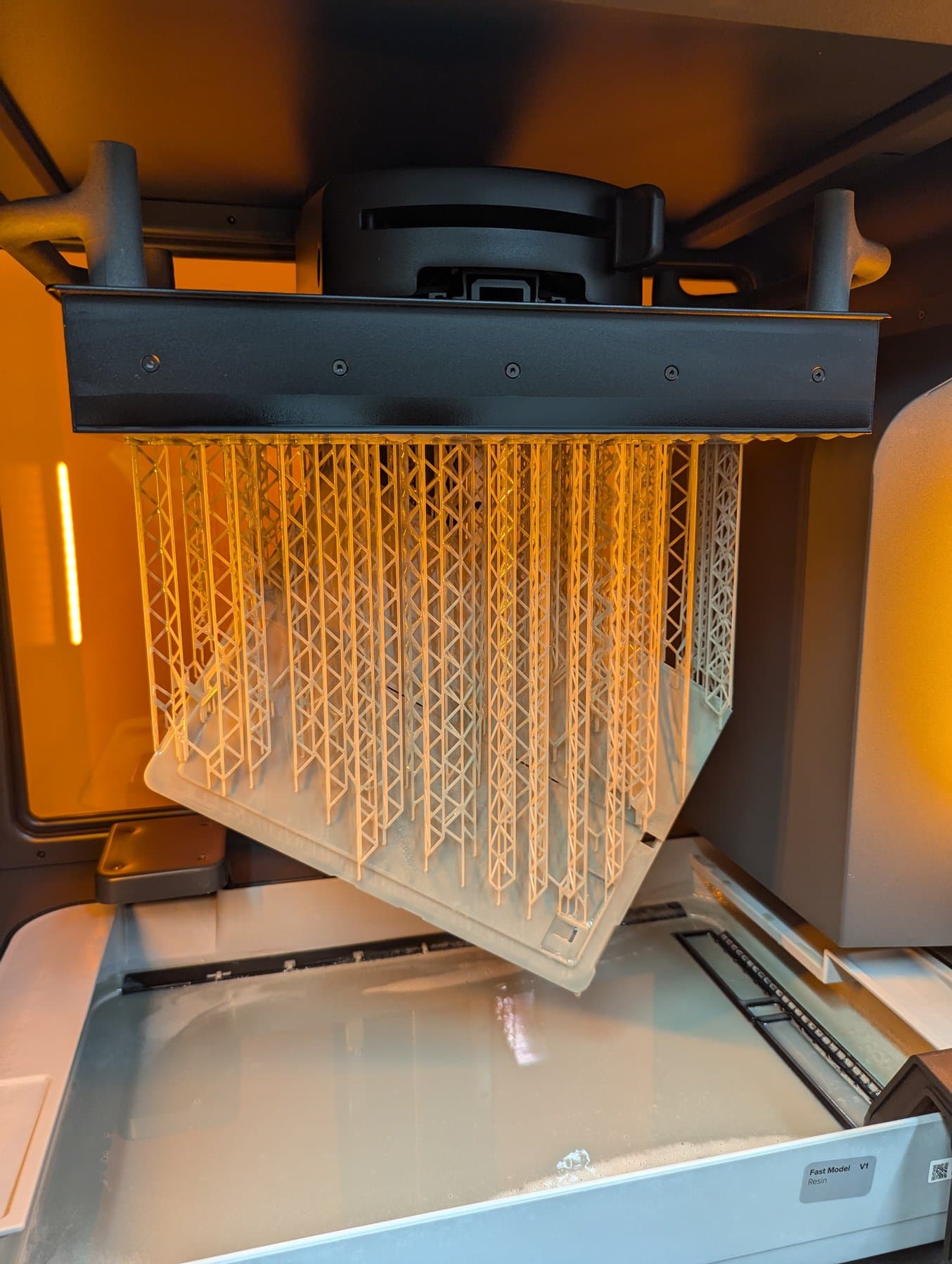
Form 4L's large build volume can fit a wide variety of components found in Microsoft's hardware products, enabling the team to prototype devices such as this Surface Pro X case.
The APC often fulfills requests for proof of concept (POC) assembled builds that range from Xbox to Surface tablets to headsets and more. But because the components aren’t manufactured at the same time, 3D printing has to step in. “They might get the circuit boards one week, but not the midframes for another three weeks. And we need to figure out, ‘Oh the circuit board is half a millimeter too thick, so now we can’t close this case cover,’ so when we do these builds, it’s not onesies, twosies, it’s 50 to 100 builds,” says Honschke.
A recent POC request came in for Xbox midframes, quantity 50, because there were some issues with outsourcing some of the internal components. “I said, ‘Yes we can supply your 50 parts, but we can’t clean them up.’ But with Form 4L, it wasn’t actually much of an issue because the supports were so much easier to remove.”
“We were able to do three full builds in three days instead of a week and a half. So Form 4L already paid for itself in that build alone.”
Mark Honschke, Additive Prototyping Lead at Microsoft’s Advanced Prototyping Center
Together, Form 4 and Form 4L have opened up a new opportunity for the APC — if they can get these high-quality parts at such high speeds, they’ll be able to provide more services in-house for large POC builds. “Xbox does one to two POC builds each year, Surface does two to three, and if we can provide that service in-house, A) it’s better security-wise, and B) if we’re faster we can find issues faster. I think there’s a good business opportunity for Form 4 and Form 4L, I think it will prove out that it would make sense to bring staff in just to run them,” says Honschke.
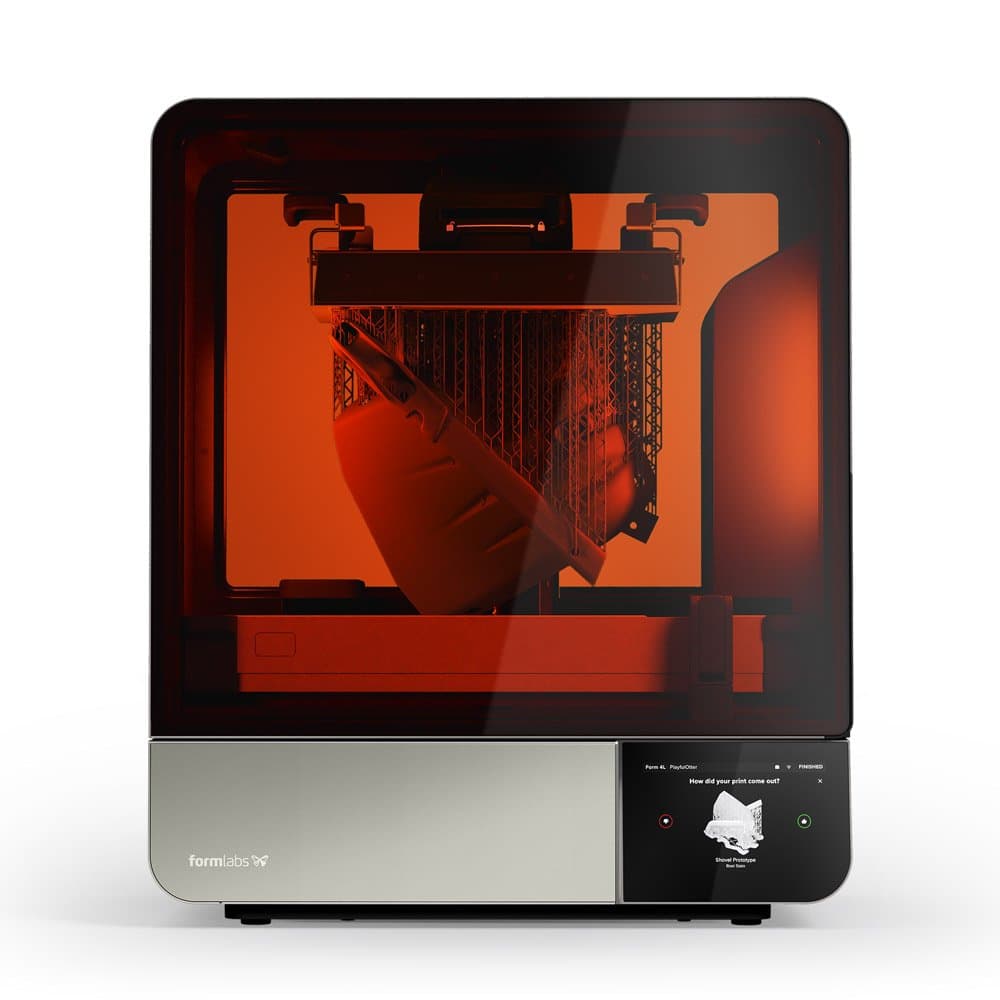
Product Demo: Form 4L
See how Form 4L, our next-generation large-format resin 3D printer, takes the speed, accuracy, and reliability of Form 4 to a completely new scale.
How the Fuse Series Makes Functional Parts As Painless As Possible
Though Form 4 and Form 4L’s speed has helped increase throughput for Honschke’s team and helped them take on some higher volume prototype orders, they use different technologies when end-use functionality and more rugged functional prototypes are called for.
As the set of products under Microsoft’s umbrella has grown, the APC has needed to adapt. Adding technologies that excel in different applications is one way they’ve been able to keep up with the increasing volume of requests from new product categories. “As Microsoft expanded product categories, we found there was a demand for high-resolution prototypes that could withstand practical use, from headphone bands to controller bodies. SLS was the best option for producing these prototypes,” says Honschke.
SLS 3D printers or other powder bed fusion technologies like MJF are relied upon for functional prototyping parts — products that can be printed with high dimensional accuracy but also withstand the rigors of being bent, stretched, sat on, or stuffed incorrectly into a carrying case. When the APC began to evaluate which type of powder printer they should add to their fleet, the Fuse Series’ small footprint and ease of use helped make the case.
“Most standard SLS systems require a large amount of space, high installation facilities costs, and are generally very dirty to operate. Besides the compact nature of the printer, Formlabs’ user-centric system feels designed to eliminate the drawbacks of standard SLS systems and their ongoing improvements make creating SLS parts as painless as possible.”
Mark Honschke, Additive Prototyping Lead at Microsoft’s Advanced Prototyping Center
The Fuse Series has helped manufacturing engineering teams usher products through the final stages of approval before they head to mass manufacturing. For most of Microsoft’s products, complex, multi-piece assemblies could all be manufactured in different locations, and getting final proof of concept builds together at one time is difficult. Relying on the timelines of logistics companies and teams from around the world means parts may not arrive at once — even if the approval deadline is looming. The Fuse Series helps teams create final POC builds to simulate the end-use manufactured product, so they can analyze any potential issues and make quick changes before any tooling is ordered.
“Manually assembling a full set of parts helps the engineers understand the fit and assembly issues that may delay production. Frequently due to part manufacturing delays or shipping issues, it can be difficult to get all of the parts to run the POC to deliver at the right time, and that is where Fuse shines. It helps fill in with parts that simulate traditionally manufactured parts,” says Honschke.
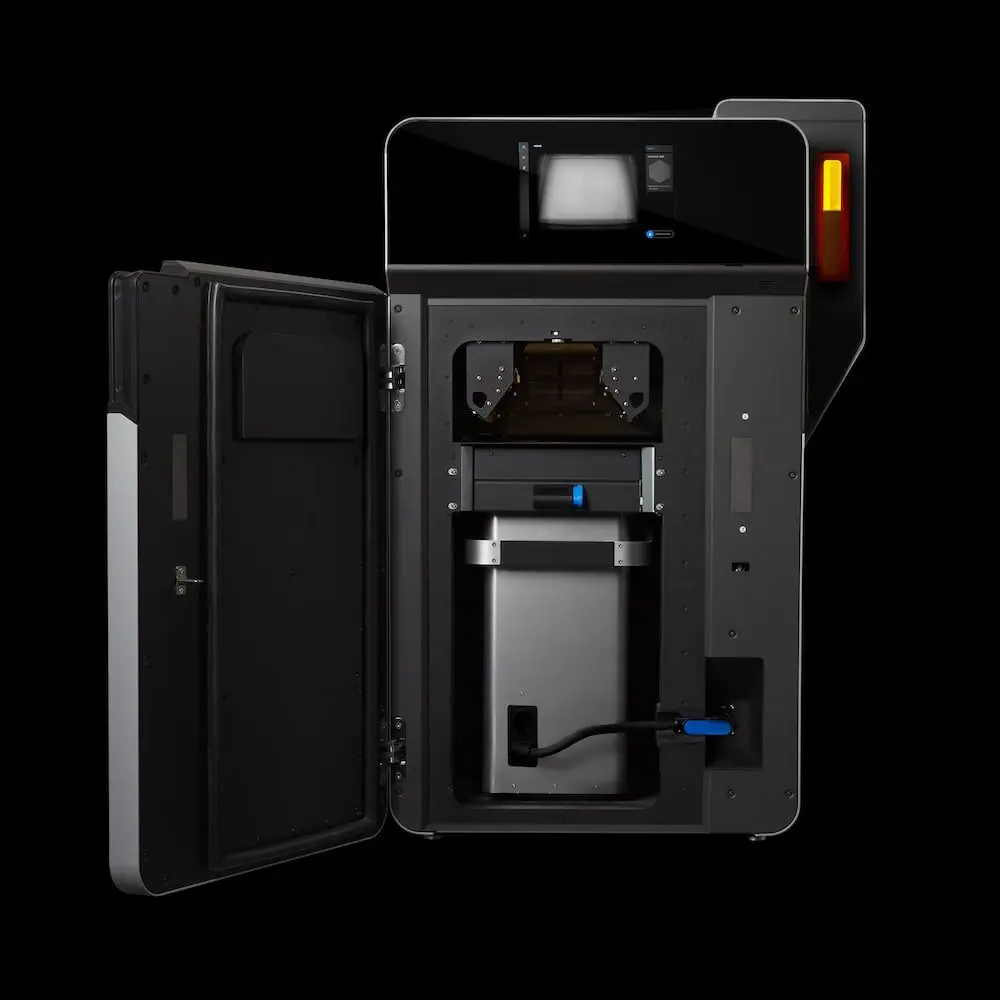
Rapid SLS Production of High Performance Parts with the New Fuse 1+ 30W
Watch our product demo for a walkthrough of the Fuse 1+ 30W and SLS 3D printing with Formlabs experts.
Formlabs' Improvements Over Time
A big part of Honschke’s job is to make sure the APC has the right tools on hand for wide-ranging, ever-changing requests and projects. Scaling up with Formlabs, both SLA and SLS technologies, has helped them answer more questions, faster.
The technological advances made for Form 4 and Form 4L have meant that Microsoft can get more done in a day, and the Fuse Series comes in to mitigate any supply chain difficulties before end-use manufacturing gets underway. For a company that runs a marathon at a sprinter’s pace — and has done so for decades at the front of the tech pack — these printers’ speed and reliability might make it a little easier.
“We’ve had all our prints be pretty successful, and since we spun Form 4L up, we’ve printed pretty much exclusively on that. I think it’s on par with what you expect of a next-generation printer. When we go to change out our printers, we’ll be changing over to more Form 4 and Form 4L printers,” says Honschke.
To see the quality of SLA or SLS parts yourself, request a free 3D printed sample. To learn more about Microsoft’s workflow, watch the webinar on-demand now.