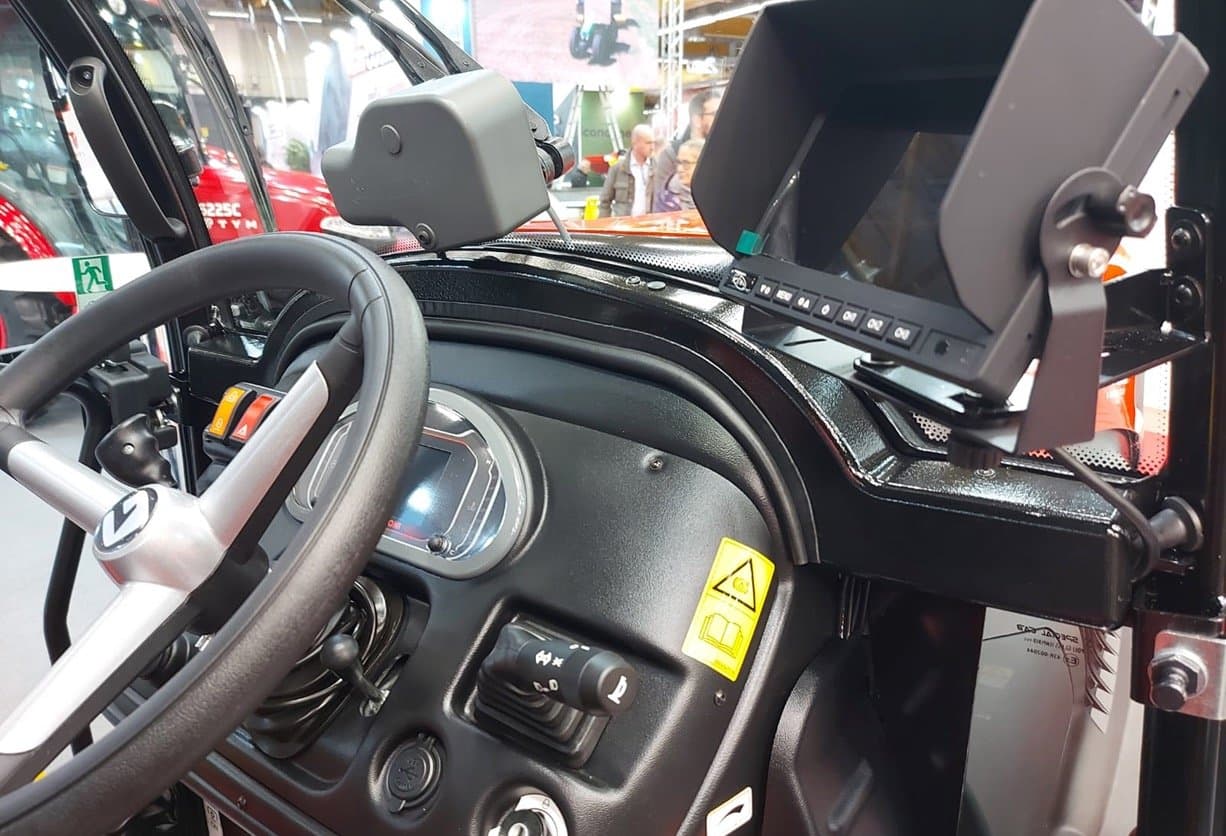
Mechinno, a consulting and engineering company based in Bologna, Italy, has built a reputation for delivering highly intricate, performative solutions for the automotive industry, among others.
Their work, for brands like Lamborghini, Ferrari, and Ducati, runs the gamut from early-stage prototyping to production runs of end-use parts. “These brands, they all have internal 3D printing capabilities, but they’re always busy in certain departments, so to speed up styling or prototyping, they prefer to go to external providers, like us,” says Gianni Del Gobbo, Technical Director at Mechinno.
To successfully juggle their packed schedule and deliver complex orders for a variety of partners, Mechinno has made sure to equip their design and manufacturing teams with the latest technologies and most cutting-edge tools. Among them is the Formlabs Fuse Series, a selective laser sintering (SLS) ecosystem that helps them produce end-use quality nylon parts that can seamlessly integrate into high-end cars, trucks, and industrial machinery. We talked with Del Gobbo about how they chose the Fuse Series and how bringing it in-house has affected their business.
“On the market, there were many suppliers of 3D printers, but the best ratio of quality and price, I found, was specifically the Fuse 1+ 30W — the cost was good, and when we evaluated the quality of the parts, we decided to invest with Formlabs.”
Gianni Del Gobbo, Mechinno Technical Director
Choosing the Fuse Over Competitors
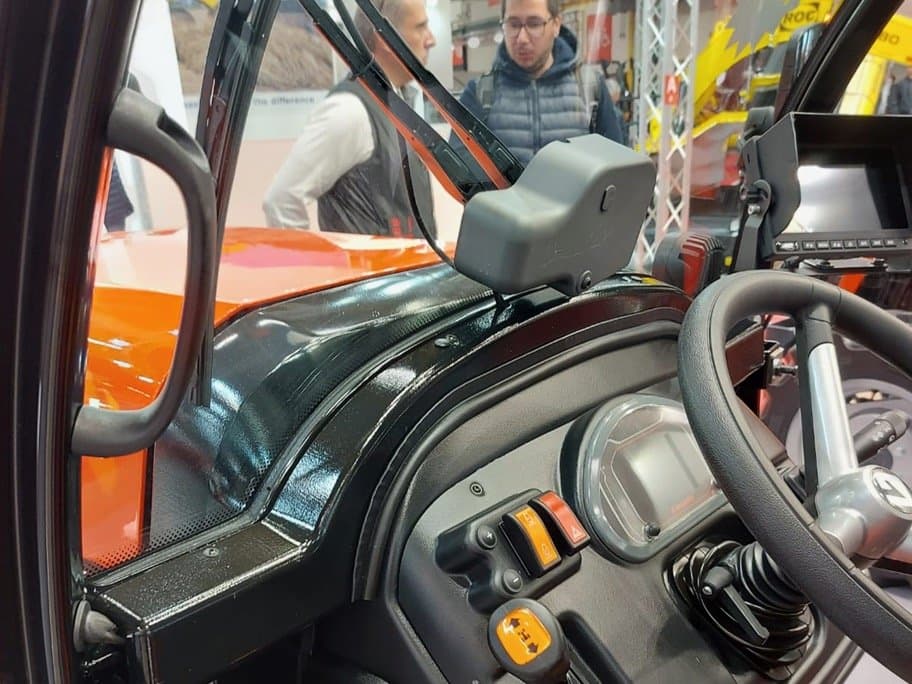
The smooth surface finish of SLS 3D printed parts is helpful for the final models that Mechinno shows their clients — painted Fuse parts are nearly indistinguishable from the injection molded plastics surrounding them.
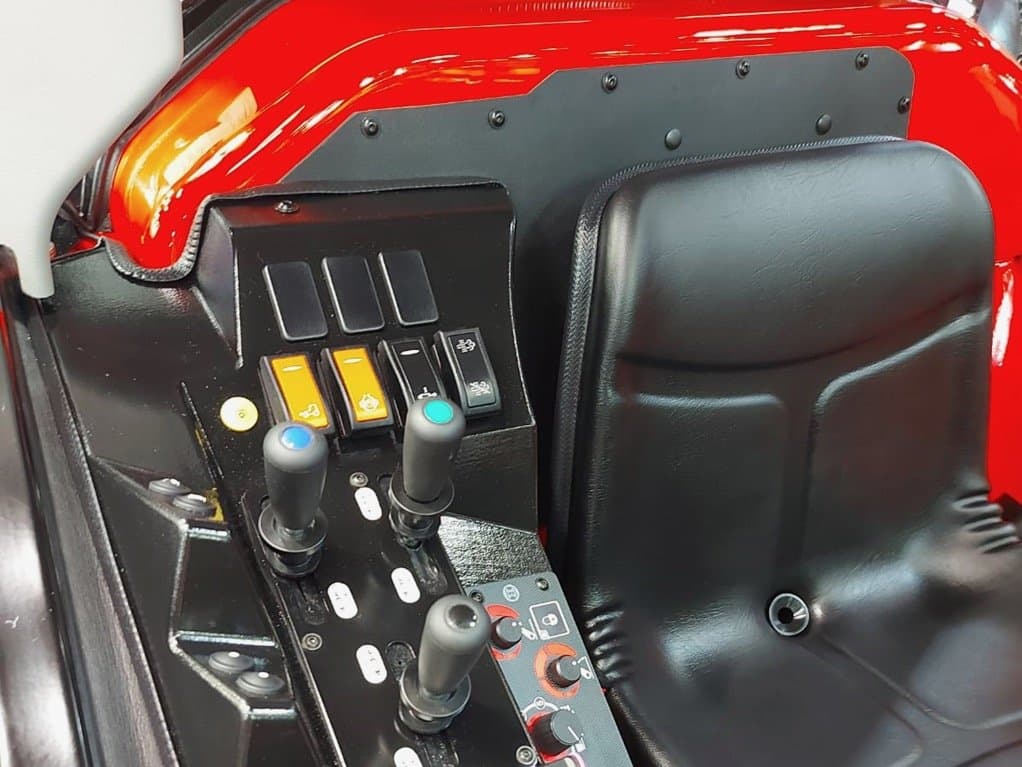
Good dimensional accuracy and repeatable, consistent tolerances are necessary for components like these joysticks and control panel hardware that need to integrate with the existing equipment.
Del Gobbo and the Mechinno team had been using fused deposition modeling (FDM) 3D printers for years, but began to get more and more frequent requests from their customers for SLS parts. “In the automotive field, they’re always asking for SLS technology — many of them started working with us because of us having that technology,” explained Del Gobbo.
Fuse Series SLS 3D printed parts offer industrial-quality strength and a variety of industry-standard thermoplastics, like nylon 12, TPU, and carbon fiber composite nylon. Though many FDM 3D printers offer the same thermoplastics, SLS 3D printers like the Fuse Series offer parts with a surface finish without highly visible layer lines, and can easily be post-processed into parts resembling injection molded plastics. “For the final surface of the parts, automotive companies prefer SLS to FDM. We evaluated new printers based on surface finish, accuracy, and print speed,” says Del Gobbo.
Though SLS isn’t faster than other FDM or stereolithography (SLA) solutions in terms of layers printed per minute, it can often come out on top in terms of throughput. The ability to nest parts within one another and stack parts throughout the build chamber — supported by the unsintered powder surrounding them — makes it possible to print hundreds or thousands of small parts each day. Most businesses that have printing requests coming in throughout the workday end up running one smaller build during the day and one larger build overnight.
Comparing Fuse to HP 5200
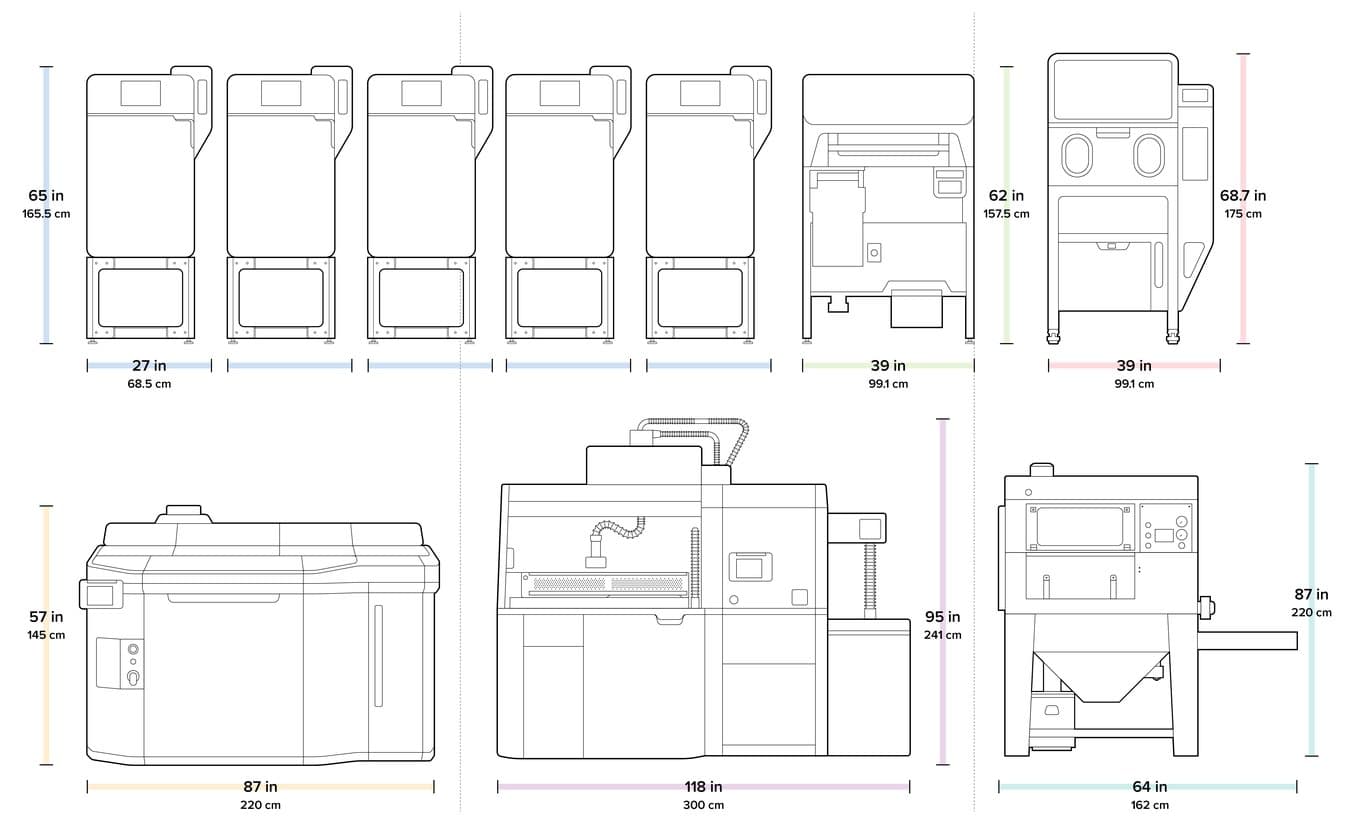
The Fuse Series allows businesses to scale as demand grows, rather than invest in a massive, industrial system all at once, with excessive up-front cost and high risk.
Monolithic, industrial powder bed systems like HP’s MJF 3D printers, like the Jet Fusion 5200 Series have large build chambers, and are often used in very high throughput situations, but Mechinno wanted the ability to scale as they go. They could start with SLS 3D printing without such a heavy up-front investment by choosing the Fuse, and then build incrementally from there. “The final decision was between the Fuse Series and the HP 5200, which was three times the cost, and its annual maintenance fee was also required. When we needed to scale up to meet demand, we just bought another Fuse,” says Del Gobbo.

These parts are prototypes of HVAC cover components for the cabin roof of a machinery vehicle. Creating parts larger than the build volume is possible through Mechinno’s ambient-temperature thermoplastic welding process.
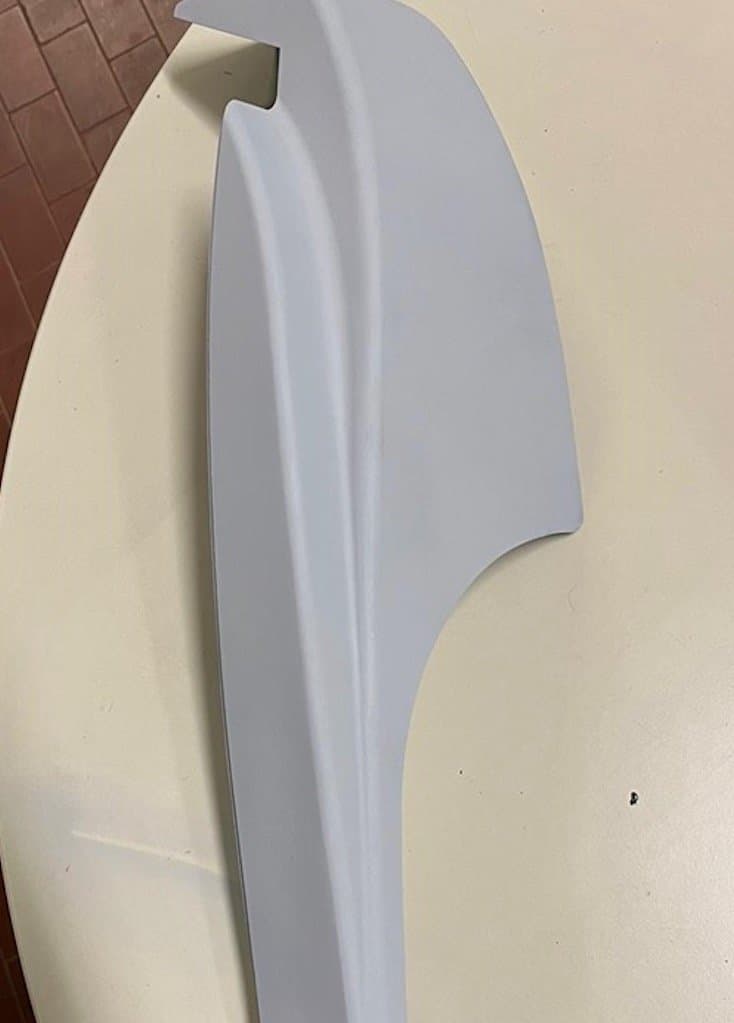
After printing and combining two components, Del Gobbo paints the part before installing it into the cabin roof.
Though the build chamber of the Fuse is smaller than many traditional industrial SLS and MJF systems, Mechinno has been able to create parts much larger than the build volume by using an ambient temperature thermoplastic welder to combine two parts together. Though he had some trepidation at first about how the parts would turn out, Del Gobbo has been pleasantly surprised by the quality of the end results. “In my opinion it is better to have more Fuse printers to speed up the printing process and then weld the parts together. The dimensional tolerances are such that the parts always match up, and our customers like the final result,” says Del Gobbo.
Flexibility and Switching Materials
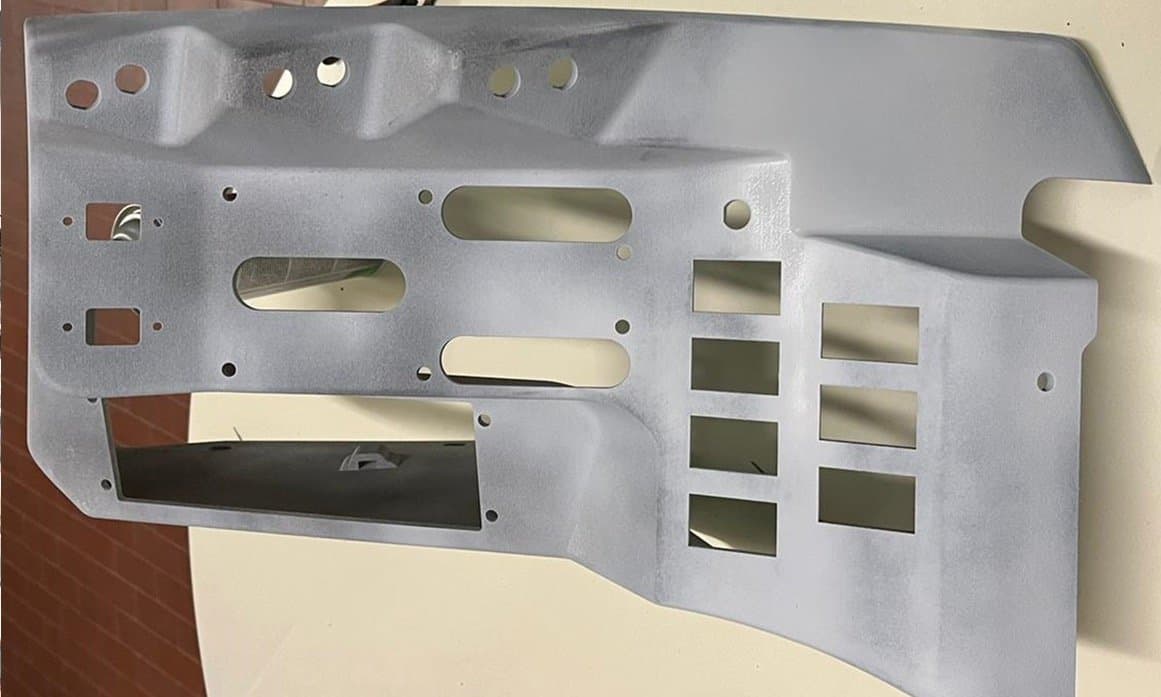
For parts like this control panel cover, dimensional tolerances and stiffness are important, so the team printed in Nylon 12 GF Powder for the additional rigidity compared to Nylon 12 Powder.
The price point and simplified workflow of the Fuse Series made it possible for Mechinno to scale incrementally as demand increased. They’ve even been able to try new materials on their second machine, increasing the number of applications and project types they can work on.
After evaluating samples printed in Nylon 12 GF Powder, the Mechinno team immediately ordered the new powder, and were able to perform a full clean-out of their Fuse 1+ 30W printer and Fuse Sift in two hours.
“Being able to switch materials is so convenient to speed up a lot of the parts you are working on — we’ll switch over both machines, so they can both work with the Fuse Sift.”
Gianni Del Gobbo, Mechinno Technical Director
Along with Del Gobbo, there are two other Mechinno employees who consistently operate the Fuse Series printers — everyone is able to receive files, make small design changes themselves, and work with customers to agree on a final quotation. Their shared Dashboard and the ease-of-use of the printer itself streamline their workflow, making it possible to handle the two to three project requests they handle each week.
The Fuse Series has helped Mechinno accept more orders and grow their business. When working with companies like Ferrari and Ducati, that have tight timelines and high standards for accuracy, surface finish, and speed, you need to trust your fabrication tools.
“We’ve gotten good customer feedback. They come back and request more SLS… the Fuse printers have increased our business.”
Gianni Del Gobbo, Mechinno Technical Director
To learn more about using the Fuse Series for automotive design and manufacturing, visit our website. To see the strength of Nylon 12 Powder or Nylon 12 GF Powder yourself, request a free SLS 3D printed sample.