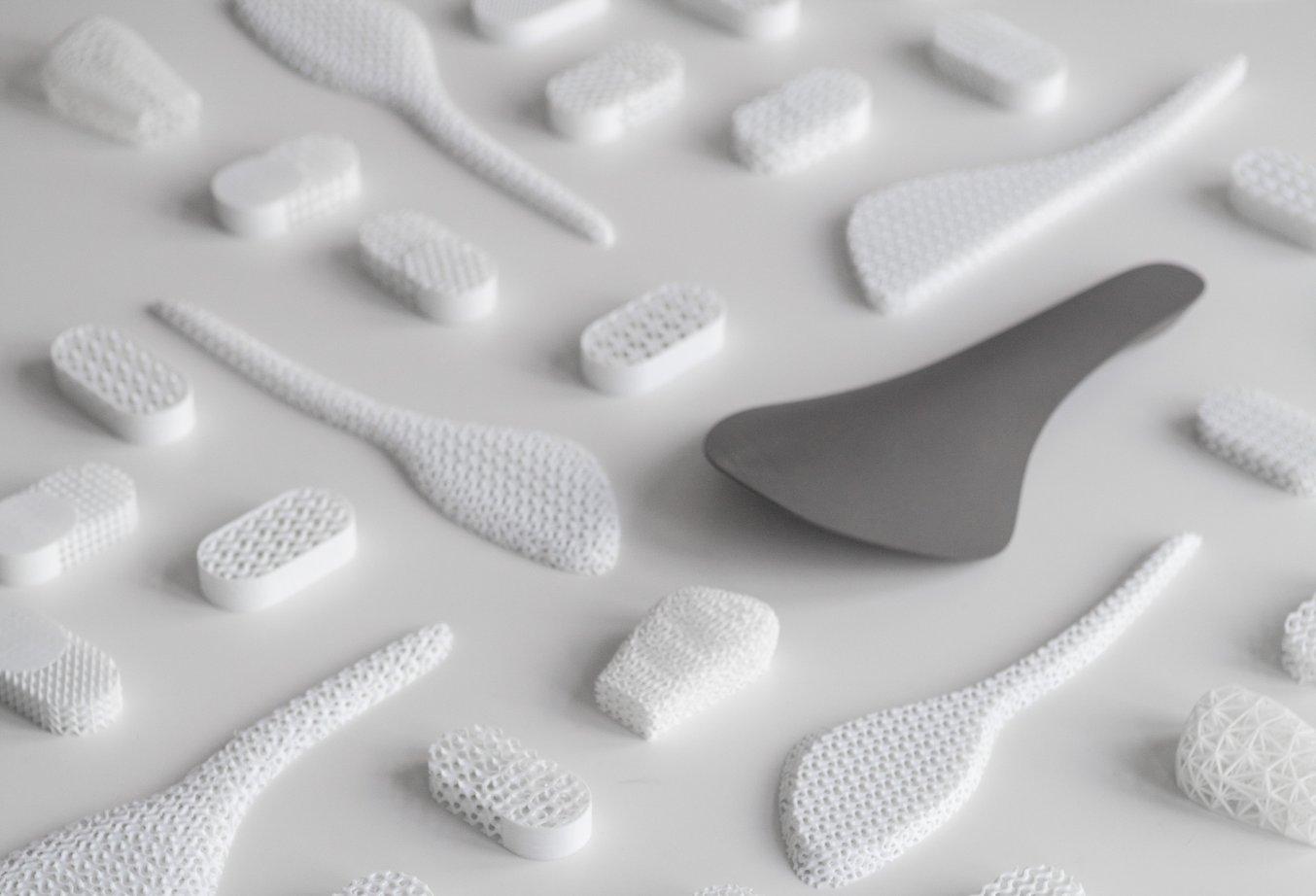
In recent years, there have been repeated efforts in various areas of the economy to overcome gender-specific norms. However, there are still significant differences in society's perception of masculinity and femininity. One of the areas where this is still strongly noticeable is ergonomic products, which are often still designed based on gender stereotypes. This is where modern technologies such as 3D printing can be particularly helpful in designing products that are tailored to the individual.
Industrial design student Tim Schütze became aware of this while at university. As part of his bachelor's thesis, he therefore focused on promoting equality and diversity through gender-sensitive design. The result is a gender-sensitive bike saddle 3D printed partially using selective laser sintering (SLS) on the Fuse 1.
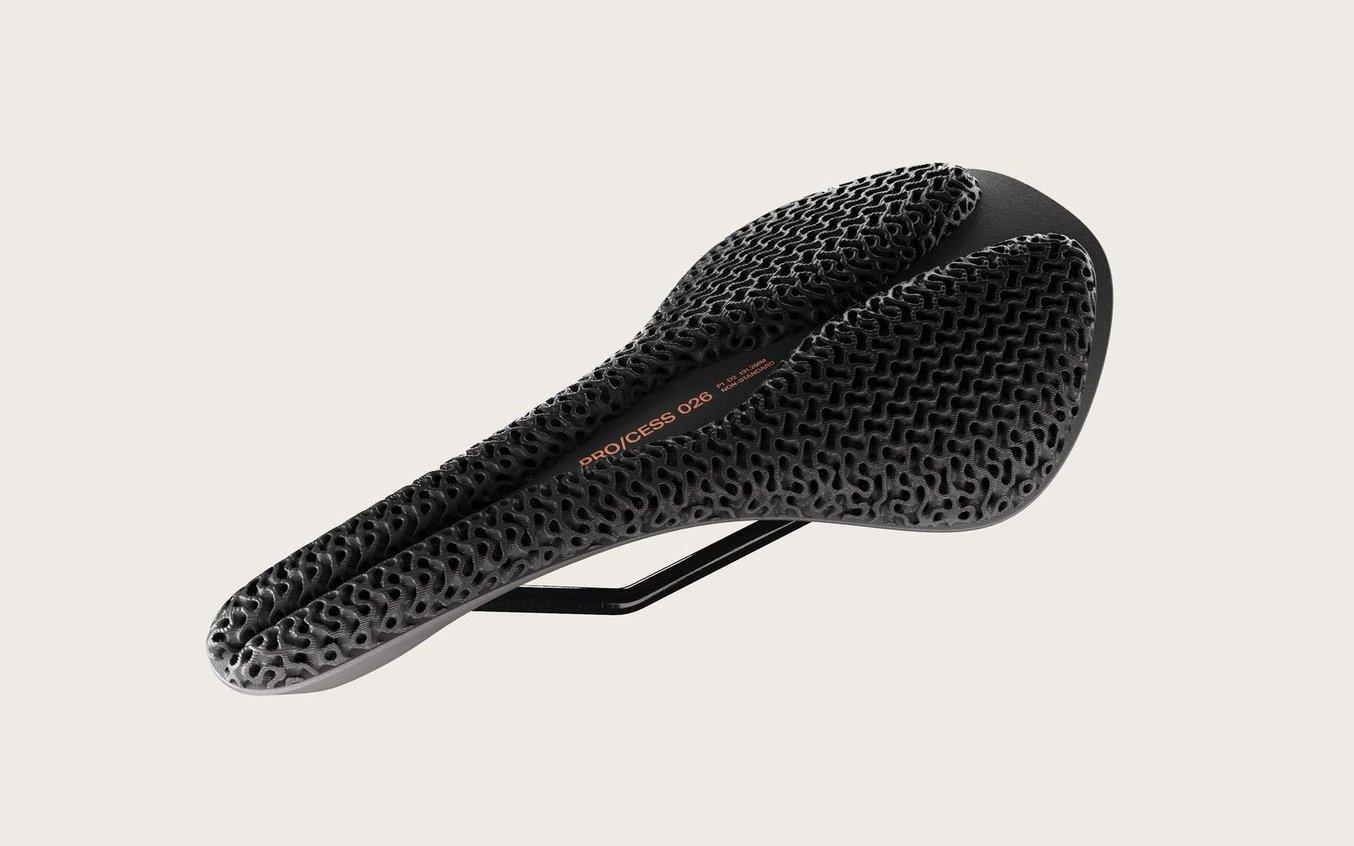
For his bachelor's thesis, industrial design student Tim Schütze specialized in the production of gender-sensitive and individualized designs - the result is a gender-sensitive bicycle saddle that is partially made with selective laser sintering.
"I wanted to create something that I fully support," Tim says about his choice of topic. He decided to take up equality and diversity of gender-sensitive designs for his design-theoretical study — a topic he is also actively involved in outside of his studies: "I noticed that there are incredibly great difficulties, problems and inaccessibilities in gender-sensitive design—but at the same time, great potential". Combined with his passion for cycling, the topic of his bachelor thesis was decided.
"Bike saddles are extremely symptomatic of gender-specific assumptions—namely, that male and female anatomy can be divided into exactly two categories. This is a false prejudice that desperately needs to change."
- Tim Schütze, Industrial Design Student
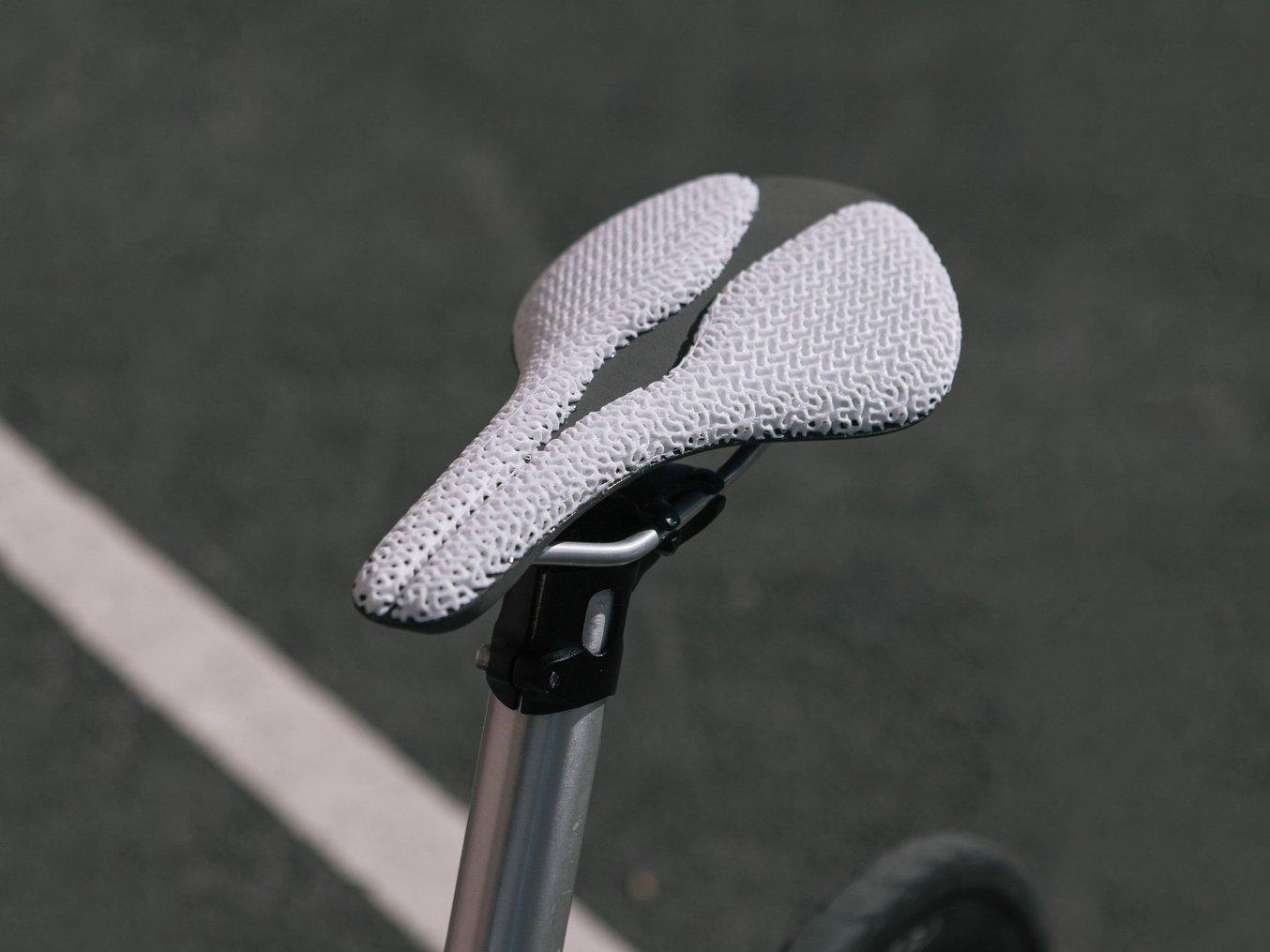
According to Tim Schütze, bike saddles in particular are extremely symptomatic of gender-specific assumptions
The Need for Gender-Sensitive Designs
The conception and design of ergonomic products is often based on norms by which they are designed. For instance, products for male-identified individuals are mainly dynamic, heavy, and designed for performance. Variants for female-identified individuals, on the other hand, are often a toned-down version of the latter.
The problem, says Tim Schütze, starts with conceptualizing and designing products according to "norms." Those who speak of norms assume a consistent component, and that's precisely what body shapes are not, he explains further. "Even if you combine the data of 100,000 people, and distinguish between female-identified and male-identified individuals, you can of course map certain trends. However, that still says nothing about the individual. There will always be people who deviate strongly from those trends and are not suitable for them."
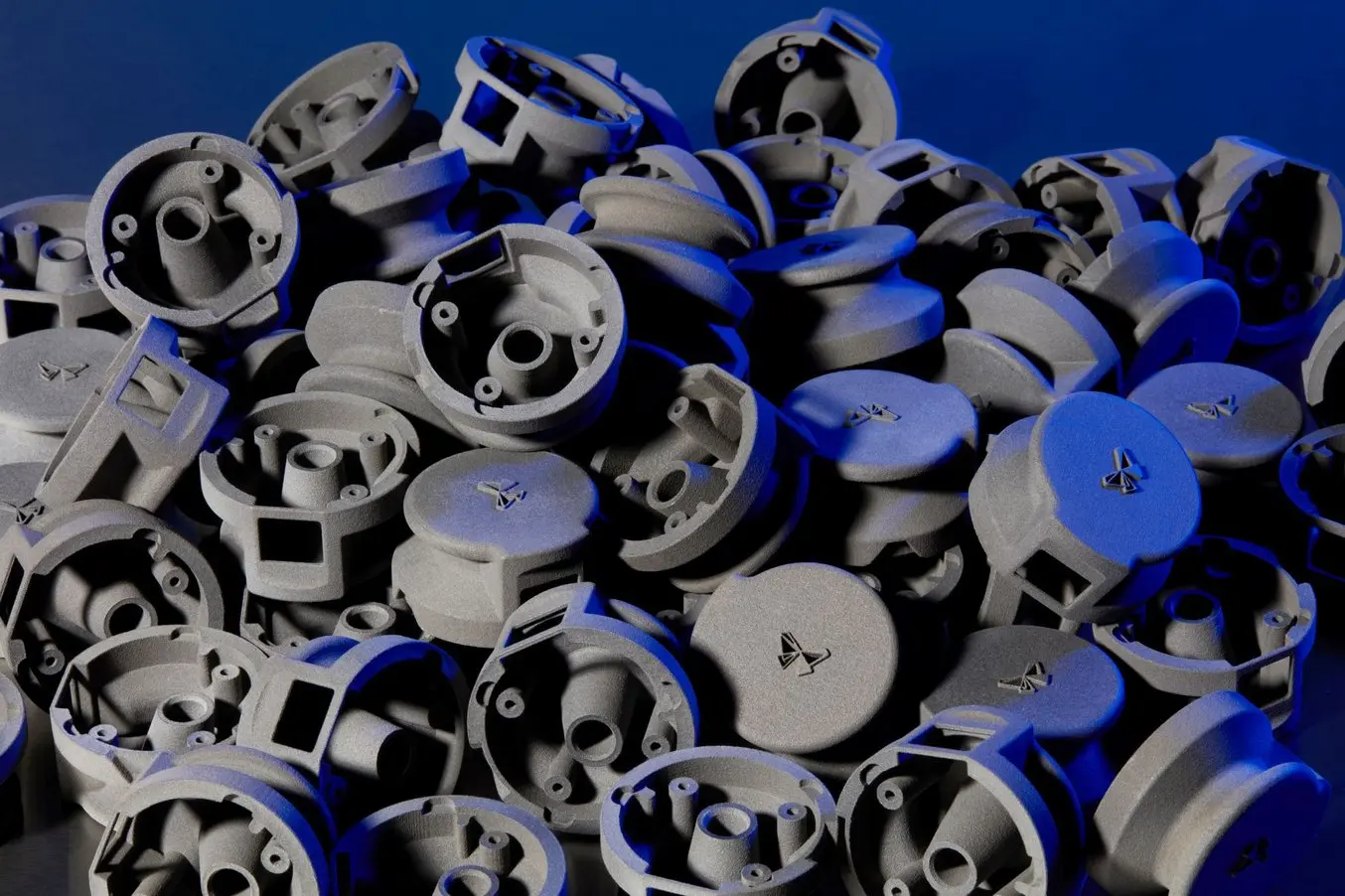
Fuse 1 SLS Design Guide
Success in selective laser sintering (SLS) starts with parts that are optimized for the SLS 3D printing process. This guide covers the important dimensions and design considerations to keep in mind when designing parts for the Fuse 1.
From the Idea to the Process
Under the principle "We don't need products, we need processes", the implementation of his work began. "It was always really important to me that the end result of the project was not a finished saddle, but a process", Tim Schütze explains his vision. The use of modern technologies such as the reading of personalized data, the creation of designs based on algorithms and the use of 3D printing were to make this possible.
To start the process and verify its conceptual basis, the first step was to collect ergonomic data and preferences from volunteers. The 30 or so participants would print out a print design, sit on it according to the instructions, and photograph it at the specified angles.
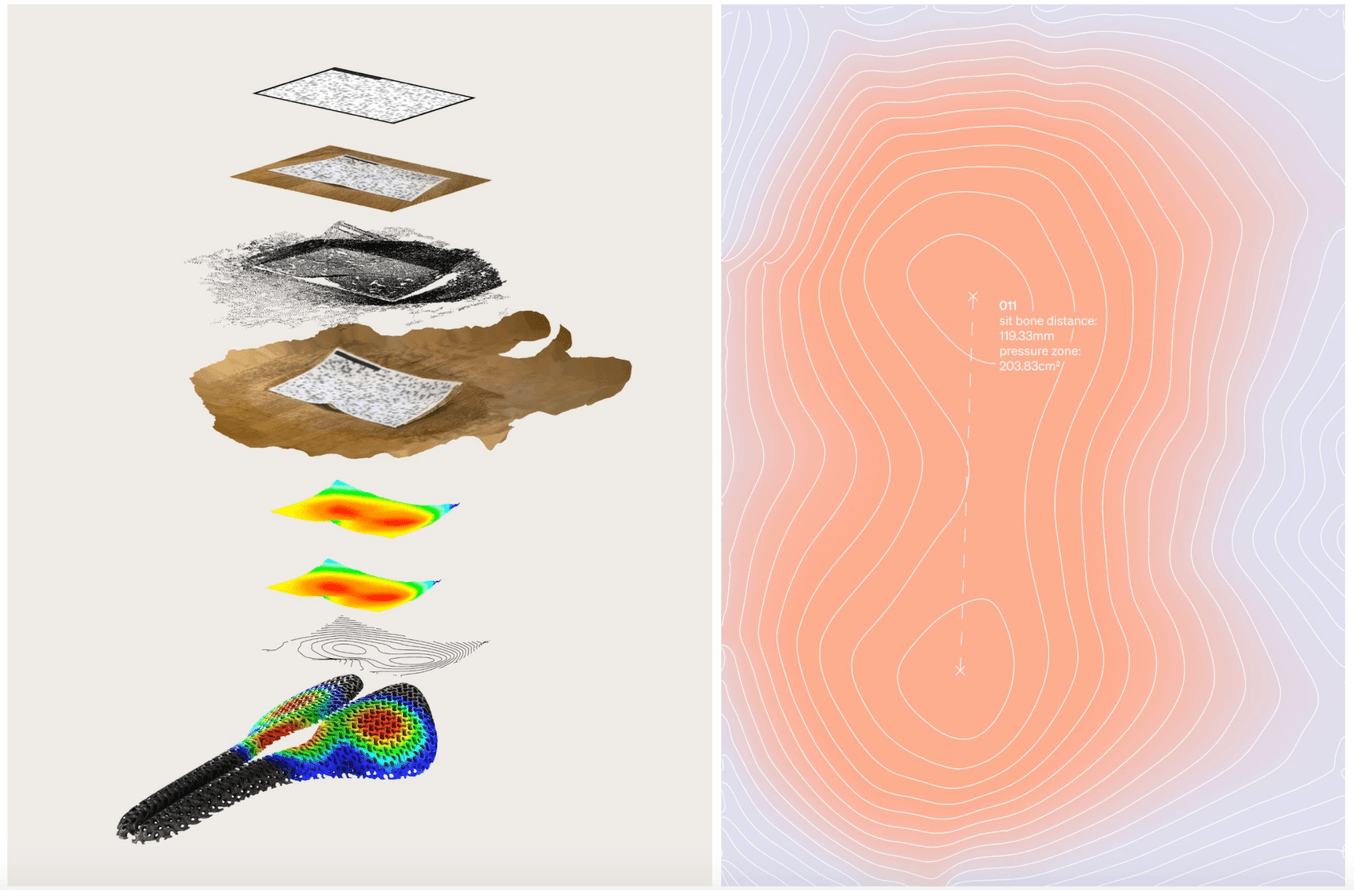
The structure-for-motion image recognition process is used to create three-dimensional impressions that provide information about distances between the sitting bones and the extent of pressure points of the individual persons and serve as a basis for the saddle.
Using the image recognition method Structure for Motion, the two-dimensional images were converted into three-dimensional point clouds—a collection of measurement points that produced a three-dimensional image of the impression. These provided information on criteria such as the distances between the sitting bones and the dimensions of pressure points of the individual, and served as the basis for the later to be created model.
"The collection of data also served as a proof of concept. Even with this relatively small sample, I noticed that there was simply no trend that could be identified and that the need for customization is there."
- Tim Schütze, Industrial Design Student

The bicycle saddle to be created consists of two 3D printed cushions, a base printed from Nylon 12 and a rail.
For the purpose of his bachelor thesis, Tim Schütze first created three different models, all of which consist of a 3D printed cushion and base as well as a rail.
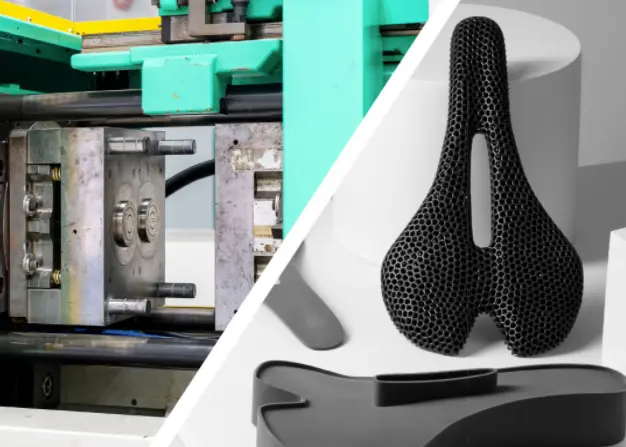
SLS 3D Printing vs. Injection Molding: When to Replace Molded Parts With 3D Printing?
This white paper showcases the cost-dynamics for real-life use cases, and presents guidelines for using SLS 3D printing, injection molding, or both.
3D Printing as a Technology for Personalization
That 3D printing would be part of his process was clear to Tim Schütze right from the start of his project "I wanted to be hands-on and guide my work through the process myself," he explains.
"In my opinion, 3D printing is indispensable as a technology of the future and allows for a great deal of accessibility compared to other manufacturing methods."
- Tim Schütze, Industrial Design Student
At the beginning of his work with 3D printing, the industrial design student initially used an FDM printer. Due to the cost-effective and fast production with FDM as well as the required elasticity of the overlays, they continue to be printed with Shore 72A hard TPU to this day. However, FDM quickly reached its limits as a manufacturing process for the base of the saddle. "The quality and reliability of the print, the support structures and handling, as well as the material properties simply don't fit the application," he explains.
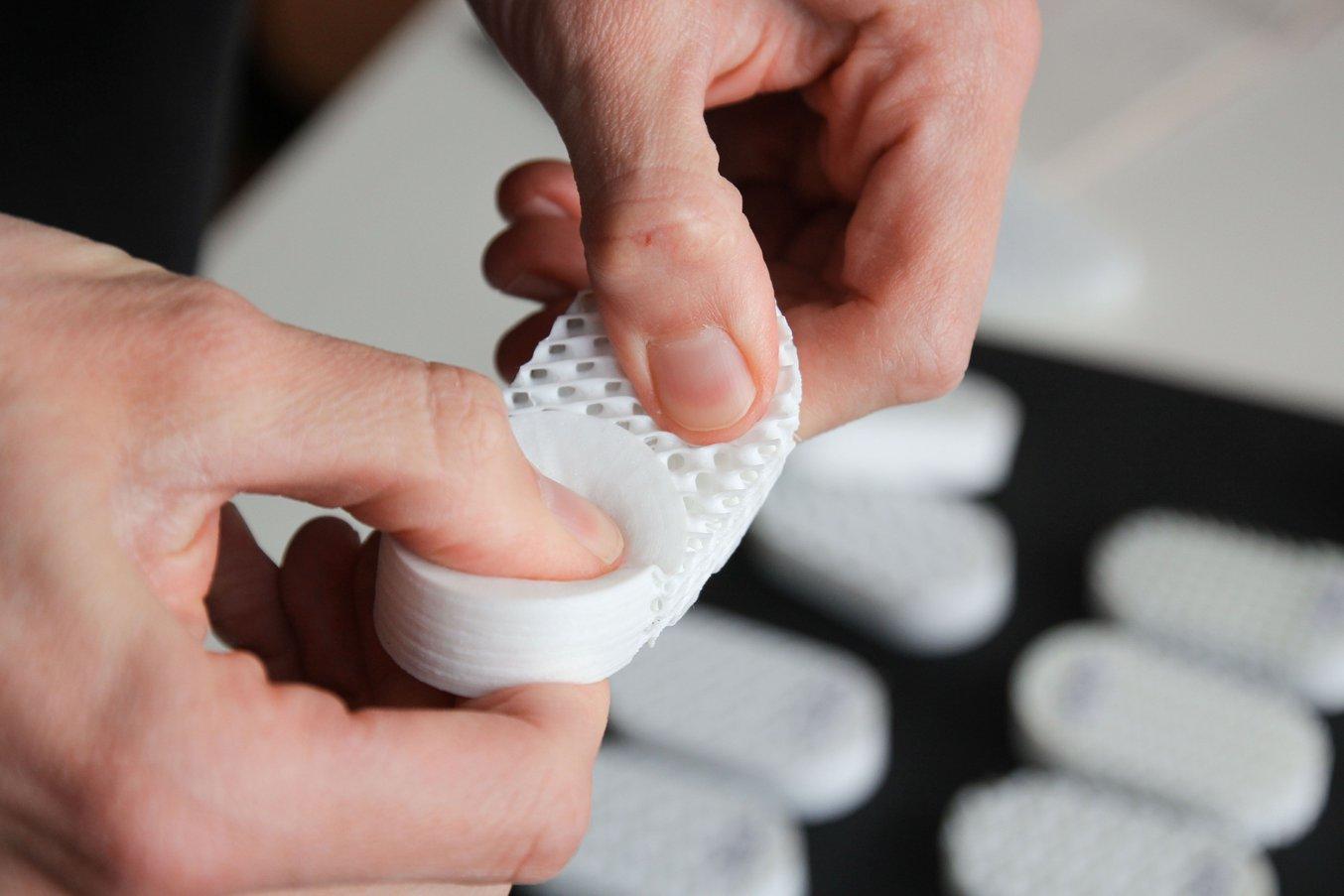
The cushions for the saddle were produced with FDM due to the required elasticity as well as the cost-effective and fast production.
In search of a new solution for manufacturing the base, Tim Schütze turned to Formlabs' team in Berlin for support. "I was super happy to get such a positive response," he says.
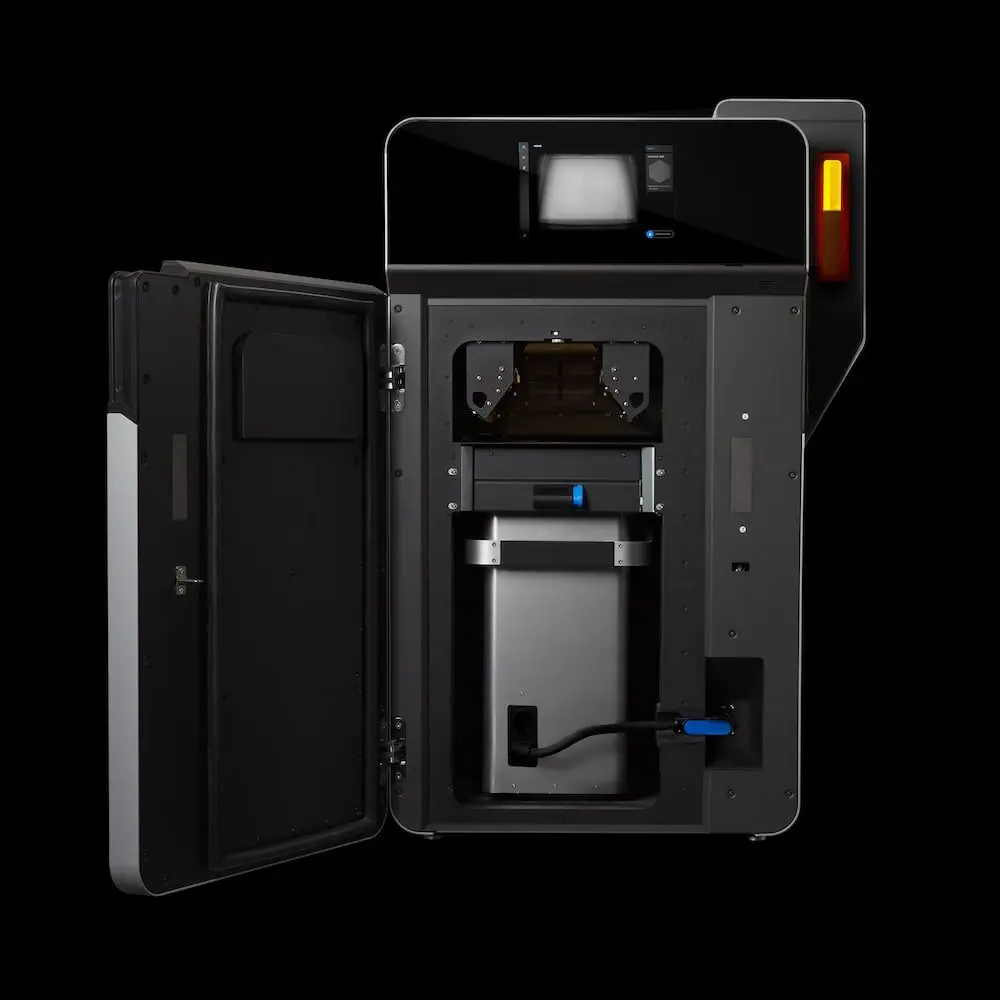
Introducing the Fuse 1: Learn How it Works
Watch our product demonstration and let our expert guide you through the versatility of the Fuse 1 and SLS 3D printing.
Due to the required resilience and quality, the engineering team at Formlabs and Tim Schütze jointly decided on 3D printing the base with SLS. Following a tour through the Berlin office, he was able to remove his freshly printed models out of the Fuse 1 himself. "The very first results were already amazing," Schütze recalls.

The base was printed using the Fuse 1 and Nylon 12, which is characterized by its high tensile strength, ductility and stability that the saddle needs.
The material used was Nylon 12 Powder, which is characterized by its high tensile strength and stability that is ideal for the production of end-use parts - something Tim Schütze was able to assure himself of right away: "I rode the SLS-printed saddle myself for several weeks, accepting that it might break, but everything worked wonderfully. That really impressed me."
After five intensive months, numerous data sets and prototypes, the process was completed by early May. The result: three individualized models, printed on the Fuse 1 and ready for use.
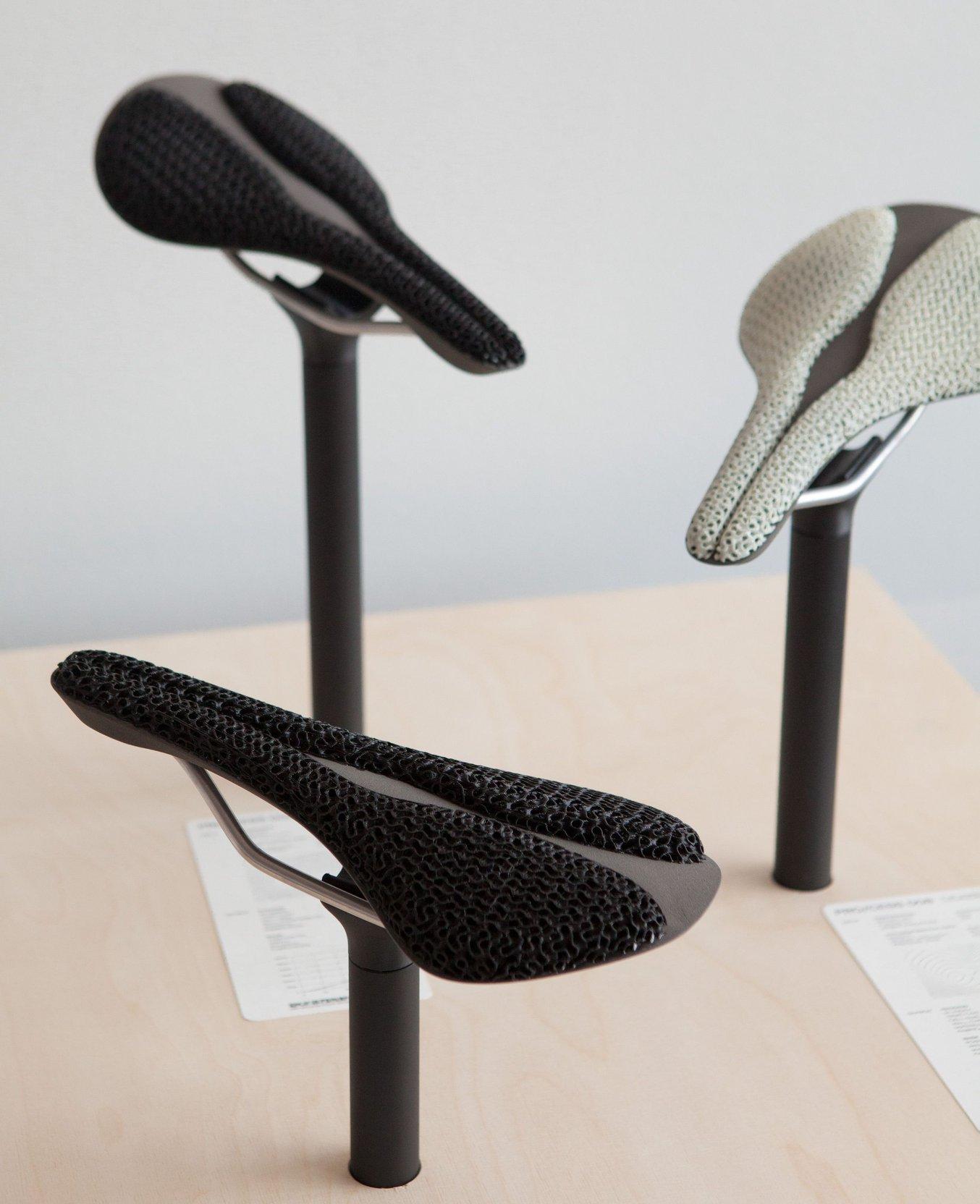
At the end of his bachelor's thesis, Tim Schütze had three gender-sensitive, individualized and ready-to-use bicycle saddles and an open-source process.