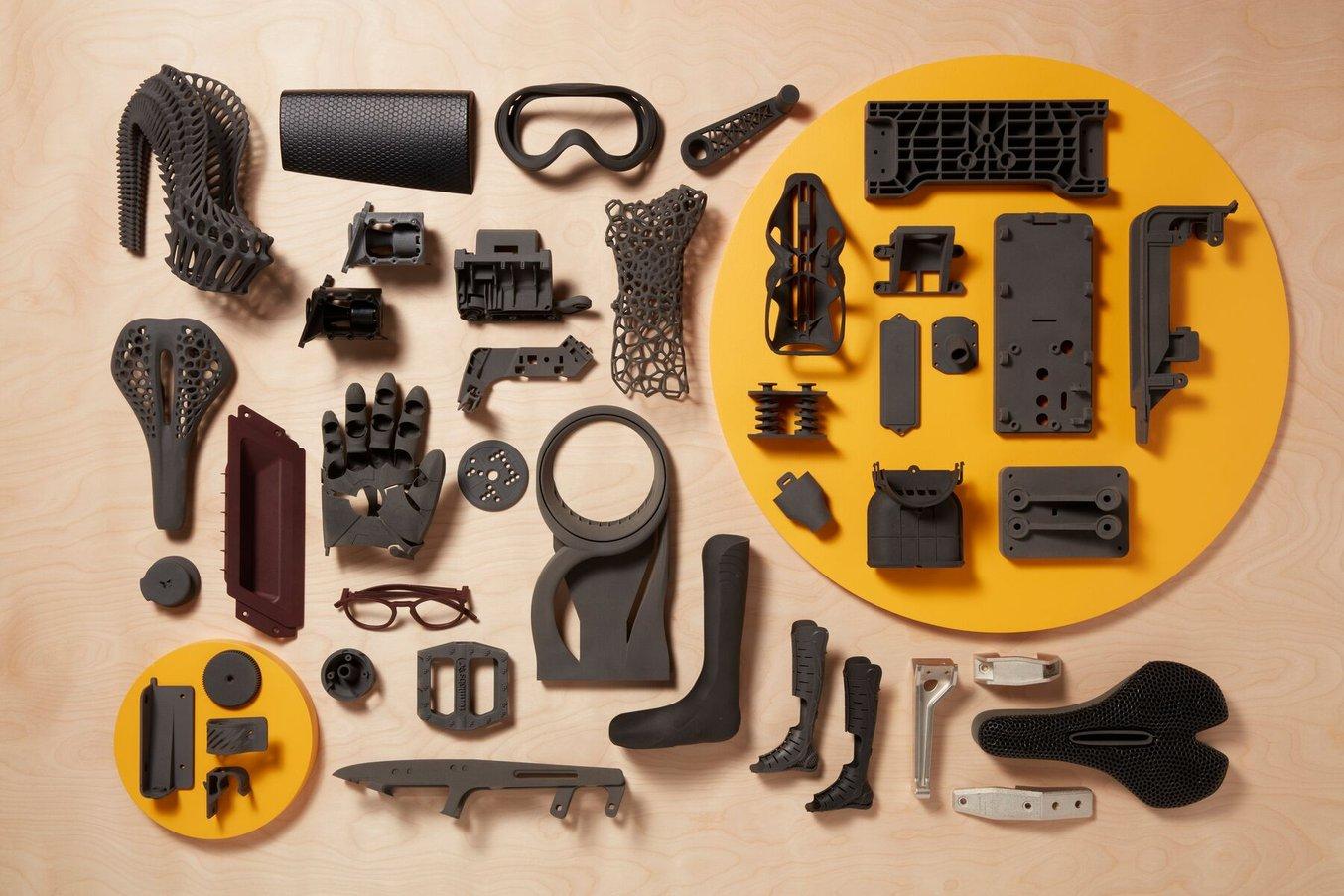
Nylon, also known as polyamide or PA, has been a popular material for manufacturers, engineers, and designers for a wide variety of applications ever since it first appeared commercially in 1938. Nylon’s strength, durability, toughness, and elasticity, as well as resistance to heat, chemicals, abrasion, and impact, have resulted in its high adoption rate across various industries.
Nylon is also one of the most popular 3D printing materials for producing strong, functional parts, including functional prototypes and end-use parts for electronics, automotive, aerospace, medical devices, consumer goods, and more.
Additive manufacturing processes capable of 3D printing with nylon include selective laser sintering (SLS), multi jet fusion (MJF), and fused deposition modeling (FDM). Choosing the right one requires a thorough understanding of nylon 3D printing processes and materials. Fortunately, we’ve created this comprehensive guide.
Why 3D Print Nylon?
Nylon: A Popular Plastic
Though nylon’s first commercial use came in toothbrushes in 1938, it made its first big splash at the 1939 World’s Fair as the primary material in a new kind of women’s stockings, which quickly became known as “nylons.” The same qualities that made it so appealing as a fiber in textiles — such as elasticity, durability, and abrasion resistance — made it useful to aerospace and automotive manufacturers, consumer goods companies, and anyone else who needed to produce long-lasting plastic parts.
Today, nylon is used in everything from residential and commercial ventilation systems, to fishing equipment, to battery housings. As it grew from “the material that won World War II” into everyday usage, innovative chemists and manufacturers continued to expand nylon’s applications.
Common implements such as washers, bolts, bearings, and gears can be found in everything from furniture and sporting equipment to cars and planes. Food packaging frequently contains nylon. Due to nylon’s temperature and electrical resistance, manufacturers often select it to house electronics, secure engine components, and support high-end engineering applications. For example, intake manifolds in cars are often made from nylon, as are the housings on most power tools.
Nylon comprises approximately 12% of all synthetic fabrics globally, and it remains the primary material used in many textiles, carpets, ropes, and nets.
Properties of Nylon
Nylon is the trade name for polyamide (PA), a class of engineering thermoplastics made when an amide link is created between a diacid monomer and a diamine monomer. Their crystalline structure gives polyamides high levels of isotropy and chemical resistance. Although different types of nylon exhibit different characteristics, nylon is generally known for its strength, high chemical resistance, durability, dimensional stability, and heat resistance.
Because nylon is stable and relatively easy to work with, manufacturers leverage many different techniques to create products from nylon. Nylon parts can be made using a variety of manufacturing processes, such as injection molding, extrusion, and now, 3D printing.
Nylon 3D Printing Materials
Naturally, as additive manufacturing grew in popularity and utility, nylon 3D printing became a major focus of innovation. 3D printing nylon provides value for functional prototypes, end-use manufacturing, and custom parts. Many of the world’s leading 3D printer manufacturers have developed systems to enable their customers to 3D print nylon.
Four particular types of polyamide are most frequently used in nylon 3D printing: PA-6, PA-66, PA-11, and PA-12. Nylon 3D printing materials can be reinforced with other materials, such as glass and carbon fiber, to increase their performance across specific dimensions such as strength or rigidity, or imbue it with certain properties like flame retardancy and electrostatic charge dissipation.
Many nylon parts, especially those reinforced with glass, can replace metal automotive, aerospace, or consumer goods parts. Additionally, due to electrical insulating properties, nylon is often used in electrical tubing and enclosures like circuit breakers. Certain nylons demonstrate high elasticity and flexural strength, such as nylon 11, which is bioengineered from castor oil.
Good abrasion resistance makes nylon valuable for applications such as bearings, snaps, and buckles. Likewise, nylon retains its performance characteristics very well over time compared with other thermoplastics. Nylon’s benefits have created a strong demand for nylon 3D printing technologies to improve manufacturing efficiency without sacrificing material performance.
Nylon 3D Printing Processes
Selective Laser Sintering (SLS) Nylon 3D Printers
SLS 3D printers use a high-powered laser to fuse small particles of polymer powder. The unfused powder supports the part during printing and eliminates the need for dedicated support structures. This makes SLS ideal for complex geometries, including interior features, undercuts, thin walls, and negative features. Parts produced with SLS printing have excellent mechanical characteristics, with strength resembling that of injection molded parts.
Nylon is the primary material used in SLS 3D printing. For most businesses and individuals looking to use additive manufacturing to leverage the benefits of nylon, SLS 3D printers will likely provide the best balance of affordability and functionality.
When the SLS print is finished, users empty the entire build chamber and extract the printed parts from the unused powder, which can be recycled to minimize waste. Additional SLS post-processing techniques can change the surface quality, color, or conductivity of SLS 3D printed nylon parts.
SLS 3D printing used to be excessively expensive, with a price tag in the range of $200,000, limiting powder-based nylon 3D printing processes to service bureaus and large enterprises. Recently, the latest industrial-grade benchtop SLS 3D printers, such as the Formlabs Fuse Series, now enable professionals to realize the benefits of 3D printing nylon with SLS technology starting just under $30,000. This has drastically reduced the barriers to entry and has enabled a greater number of businesses to use 3D printed nylon in their products and workflows, including small to medium businesses that could hardly get off the ground otherwise.
Pros & Cons of Using SLS for Nylon 3D Printing
Nylon 3D printed parts from an SLS 3D printing system are close to isotropic, which means they display similar material properties under stress along all axes. Importantly, many of the reasons for 3D printing with nylon — in particular, the material’s strength and durability — can only be realized if the parts are highly isotropic. FDM printers do not produce isotropic parts and often struggle to achieve an acceptable level of detail, making SLS or MJF the only option for many users. However, MJF and many traditional SLS options are prohibitively expensive.
Additionally, many of the parts ideally suited to nylon, such as snap-fit enclosures and electrical housing, require a moderate to high level of detail only found in parts produced by SLS or MJF 3D printers.
Nylon Powders for SLS 3D Printing
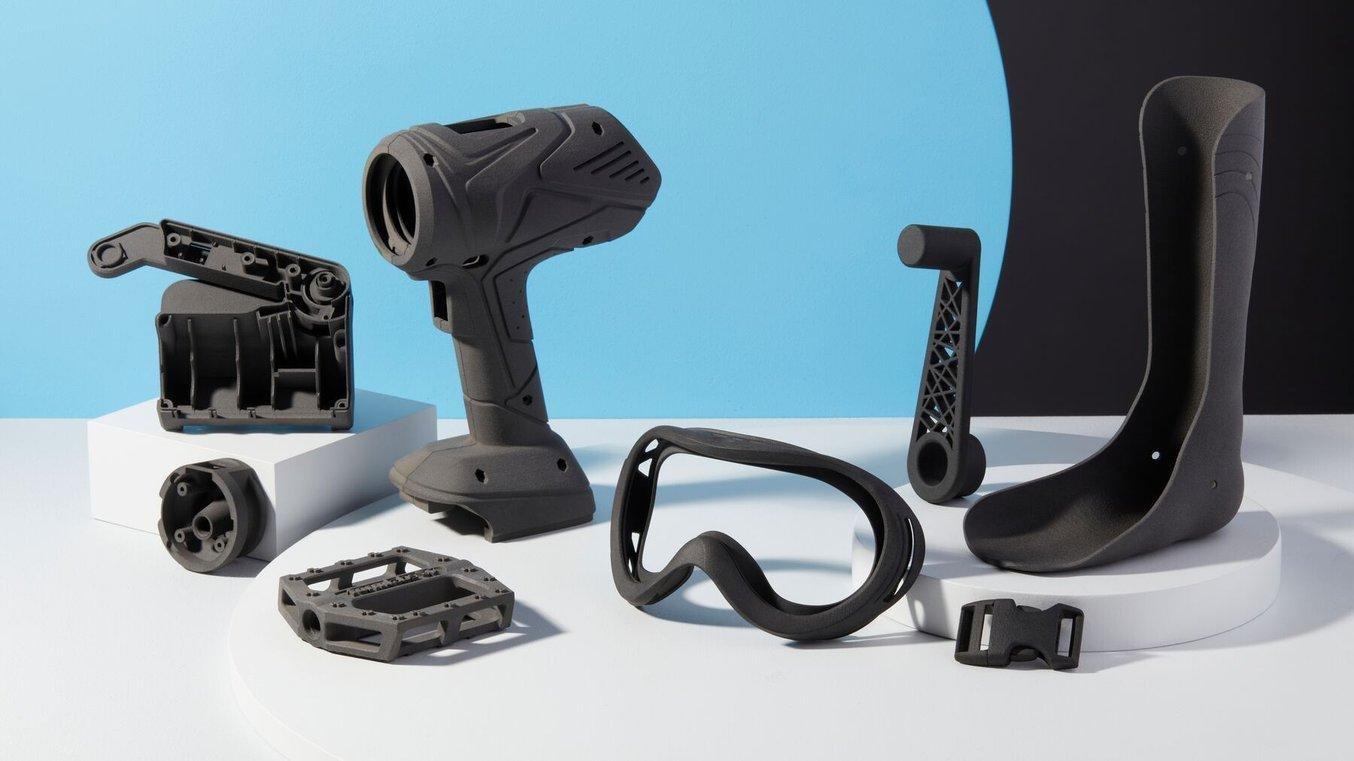
Nylon is ideal for a range of functional applications, from engineering consumer products to healthcare.
Nylon 12 and nylon 11 are the most common single-component powders for SLS 3D printing. Nylon 12 is the go-to material that is compatible with practically all SLS 3D printers, while nylon 11 requires a slightly more complicated infrastructure to print with.
Both variants can also be reinforced with other materials like glass or carbon fiber to create composites with specific properties, like added strength and rigidity, but the availability of these more niche materials is highly dependent on the type of printer.
The following materials are compatible with the Fuse 1+ 30W:
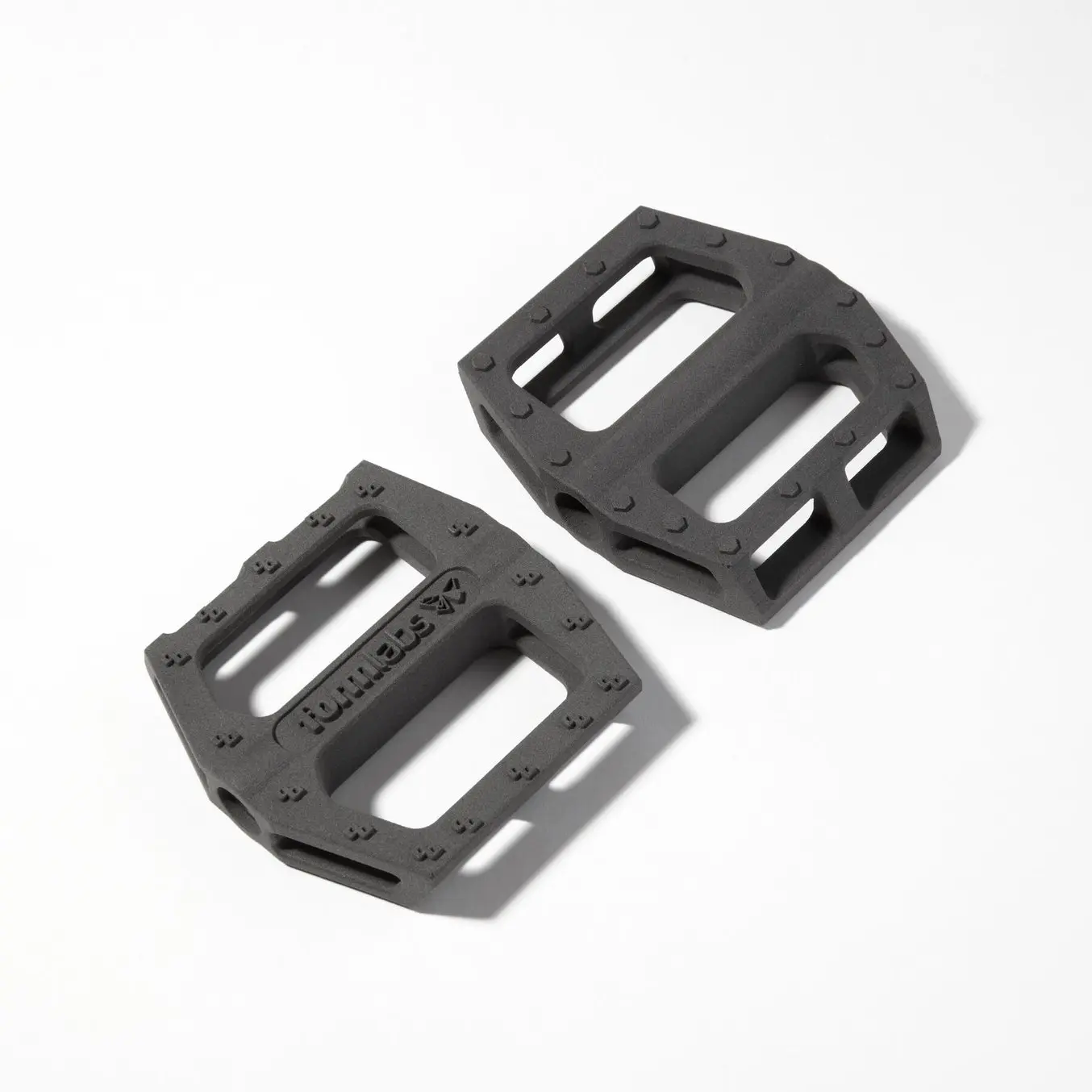
Nylon 12 Powder
General purpose, versatile material with high detail and great dimensional accuracy.
- High performance prototyping
- Small batch manufacturing
- Permanent jigs, fixtures, and tooling
- General SLS parts
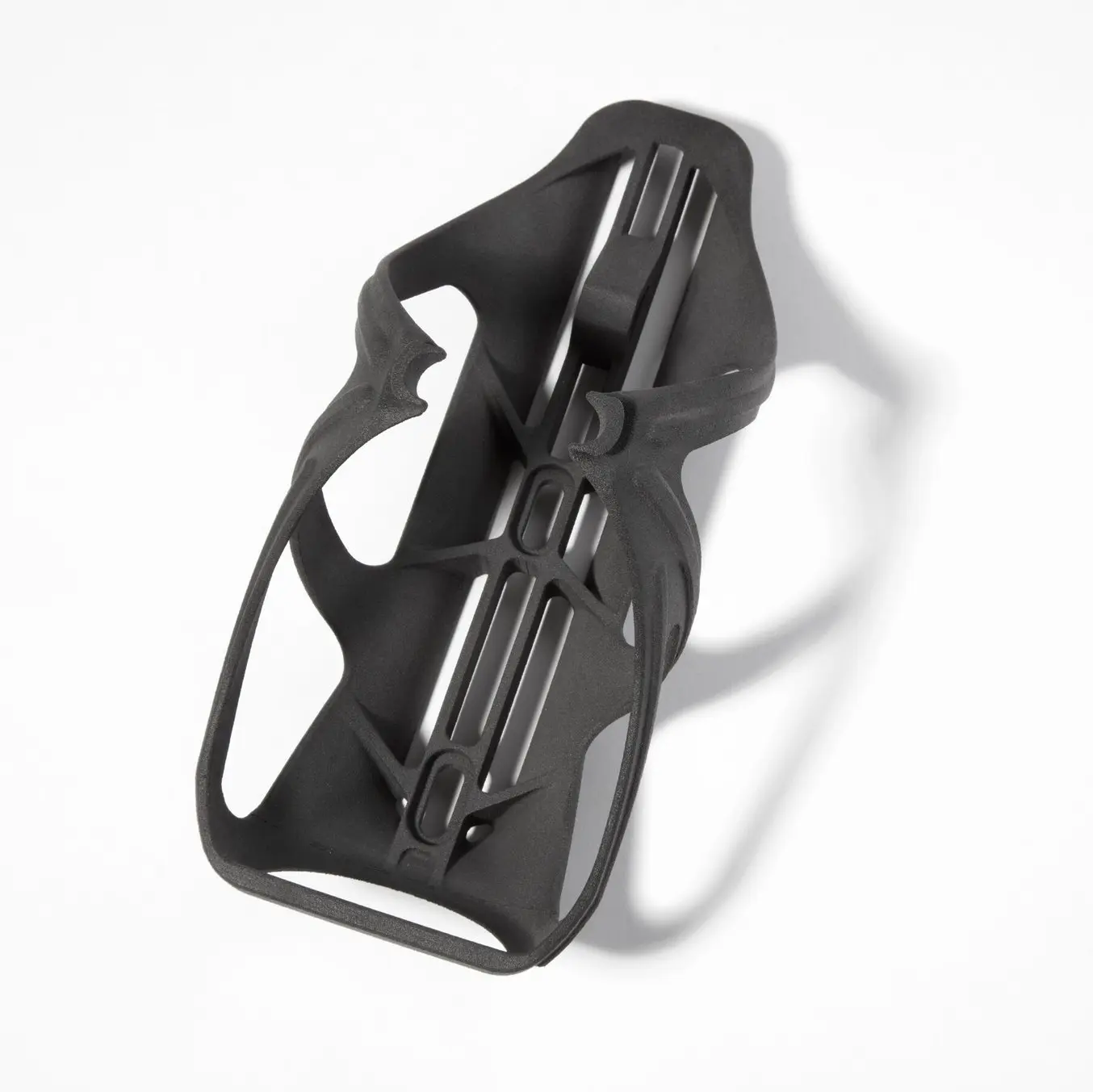
Nylon 11 Powder
Ductile, strong, flexible material for when durability and performance are key.
- Impact-resistant prototypes, jigs, and fixtures
- Thin-walled ducts and enclosures
- Snaps, clips, and hinges
- Orthotics and prosthetics*
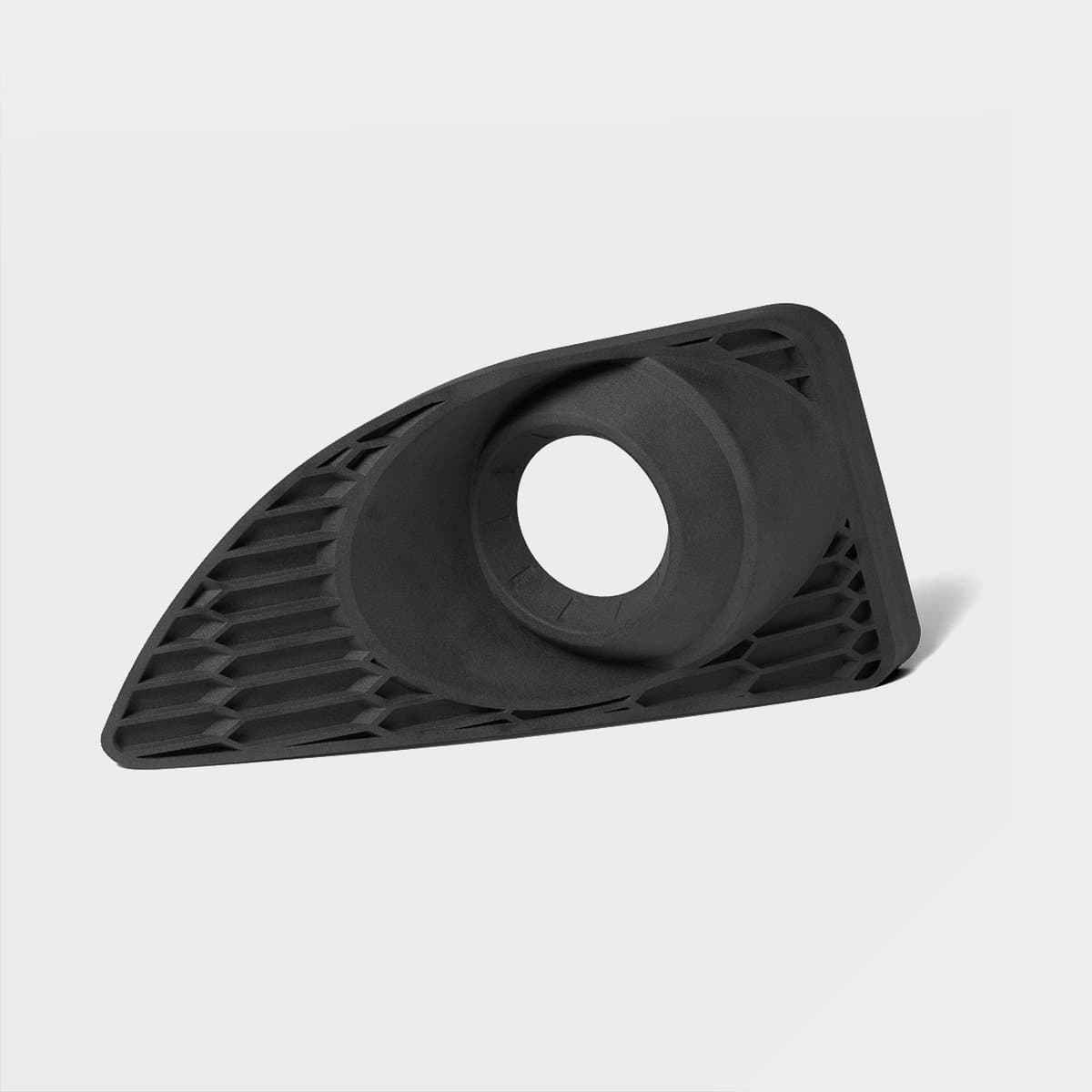
Nylon 12 GF
A glass-filled material with enhanced stiffness and thermal stability for demanding industrial environments.
- Robust jigs and fixtures and replacement parts
- Parts undergoing sustained loading
- Threads and sockets
- Parts subjected to high temperature
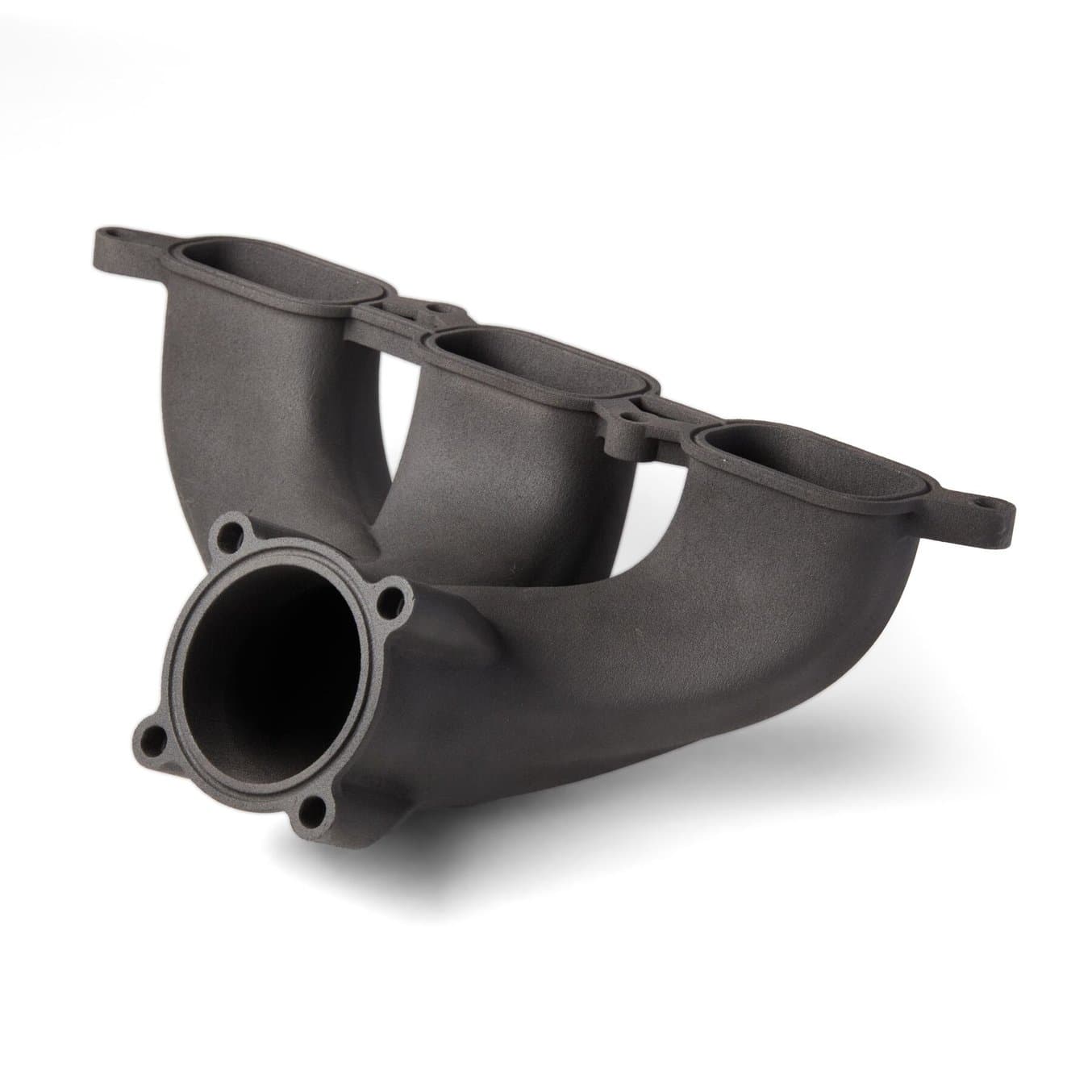
Nylon 11 CF Powder
Get the best of nylon and carbon fiber with this highly stable, lightweight, high-performance material.
- Replacement and spare alternatives to metal parts
- Tooling, jigs, fixtures
- High-impact equipment
- Functional composite prototypes
Requirements and Recommendations for Nylon 3D Printing With SLS
Because a wide range of SLS printer options exist on the market, there is no single set of guidelines to use for printing nylon with SLS. As a general rule of thumb, the larger, more expensive SLS printing systems may require specially regulated physical space, specialized power infrastructure, and an in-house 3D printer technician who has completed extensive training courses provided by the 3D printer manufacturer.
On the other hand, plug-and-print options such as the Formlabs Fuse Series may be used in normal workshop environments, can be operated after minimal training, and have a comparatively small footprint. To offer a compact, contained ecosystem and end-to-end powder handling, Fuse Series printers also come with Fuse Sift, which combines part extraction, powder recovery, storage, and mixing in a single free-standing device, and Fuse Blast, a fully automated cleaning and polishing solution.
The workflow of Formlabs' Fuse Series SLS 3D printers also allows switching between nylon powders relatively easily, after a thorough cleaning of the printer and accompanying post-processing unit. Switching materials on the Fuse Series can take less than three hours — so trying new nylon powders doesn’t have to be impossible or exorbitantly expensive. With the Fuse Series and Fuse Sift, users can try out any new material without having to purchase a completely new ecosystem.
Multi Jet Fusion (MJF) Nylon 3D Printers
Multi Jet Fusion 3D printing is a powder bed fusion additive manufacturing process that produces similar parts to SLS, using a slightly different process. To form parts, the printer dispenses a liquid binding agent from many small nozzles onto the powder bed, bringing the powders to a semi-solid state before finishing the process with heat. The infrared heat source then cures the semi-solid cross-shape before another layer of powder is deposited and the process repeats. MJF was patented by Hewlett Packard in 2016, and HP remains the only provider of MJF 3D printers.
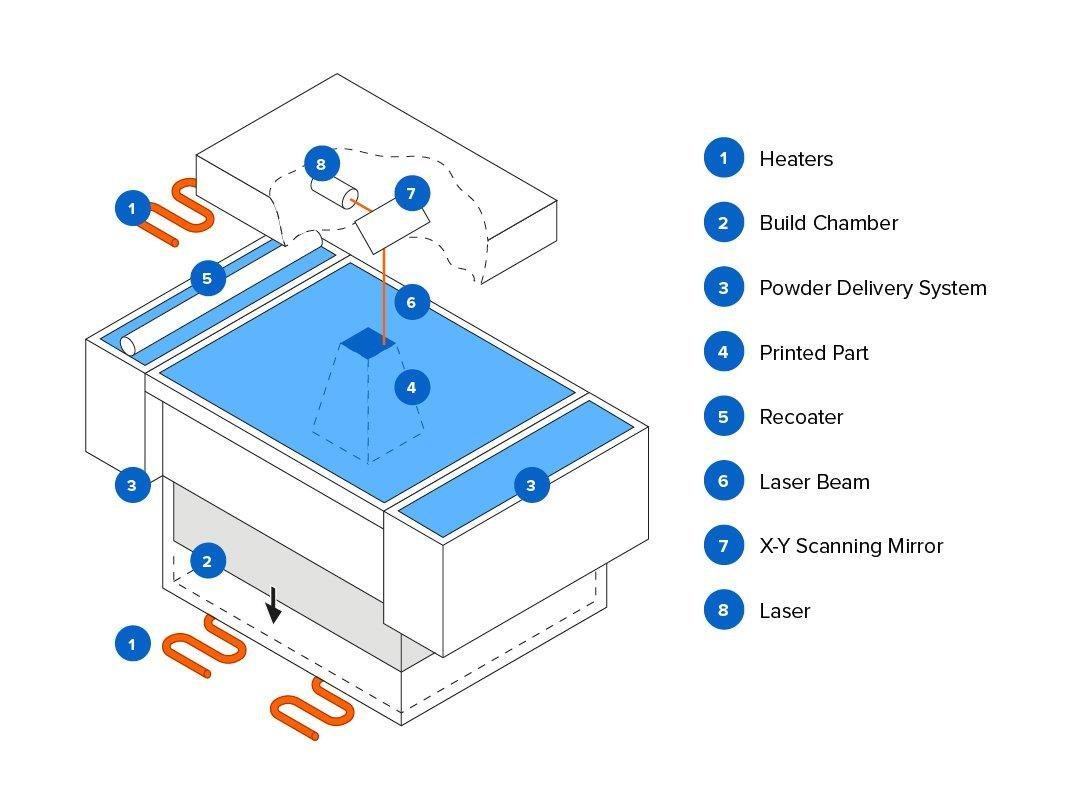
Schematic of the selective laser sintering process.
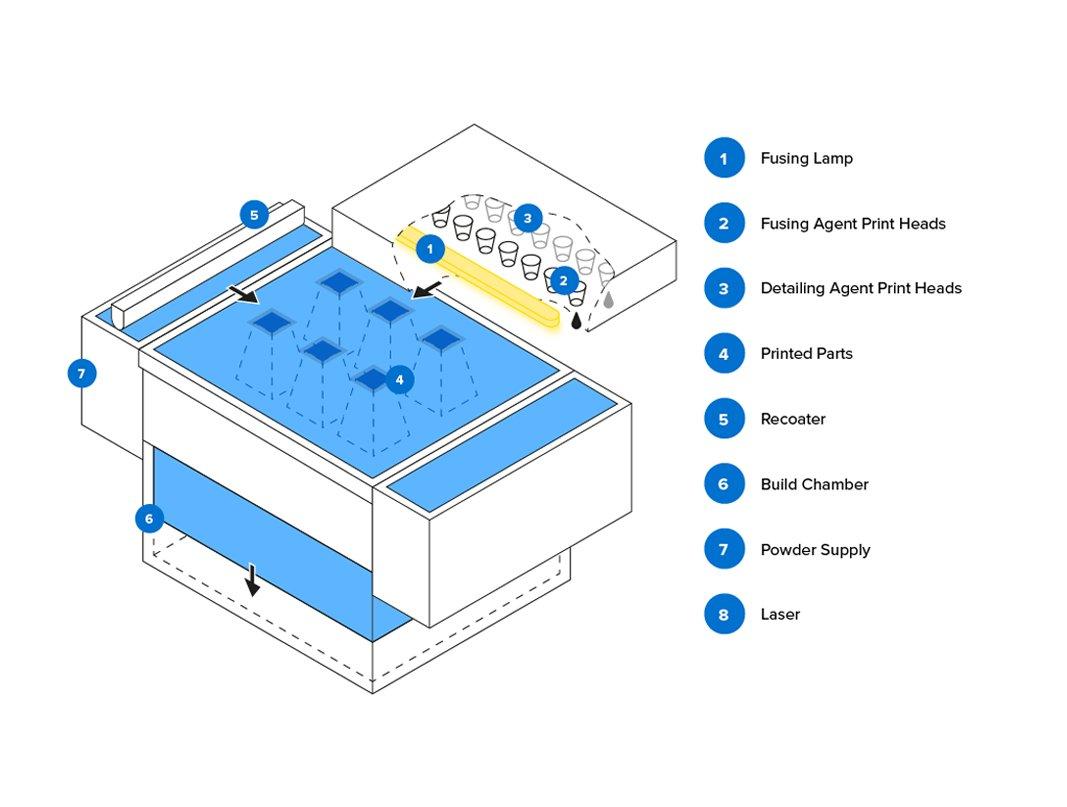
Schematic of the multi jet fusion process.
MJF printers are relatively quick, though the build chamber typically needs to cool for about twice as long as the print needs to complete. The MJF process is less efficient and generates more waste than SLS technology, as the parts cannot be packed closely together in the build chamber for printing.
While SLS 3D printers have become more affordable, MJF 3D printer prices range from about $350,000 to more than $600,000. As a result, they’re mostly used by service bureaus and large in-house additive manufacturing labs of Fortune 500 companies.
For an in-depth comparison of the two technologies, read our MJF vs. SLS guide.
Pros & Cons of Using MJF for Nylon 3D Printing
MJF and SLS share many advantages. Neither process results in support structures, saving users from complicated and costly post-processing steps. Just like SLS, 3D printing nylon parts using MJF printers results in parts with good surface finish and isotropic material properties.
Nylon Powders for MJF 3D Printing
Like SLS 3D printers, MJF 3D printers produce parts using nylon 12 and nylon 11 powders. HP also offers glass-reinforced nylon 12 for increased stiffness; however, there’s currently no carbon fiber reinforced nylon option for MJF 3D printing.
Material | Description | Applications |
---|---|---|
Nylon 12 | General purpose, versatile material | High performance prototyping Small batch manufacturing Permanent jigs, fixtures, and tooling General nylon parts |
Nylon 11 | Ductile, strong, flexible material | Impact-resistant prototypes, jigs, and fixtures Thin-walled ducts and enclosures Snaps, clips, and hinges Orthotics and prosthetics |
Nylon 12 GB | Glass bead filled nylon for stiff and dimensionally stable parts | Robust jigs and fixtures and replacement parts Parts undergoing sustained loading Threads and sockets Parts subjected to high temperature |
Requirements and Recommendations for Nylon 3D Printing With MJF
Running MJF technology in house requires a skilled 3D printing technician on staff. Professional technicians are also needed to both install and maintain the printer. HP MJF printers require a specialized power infrastructure and a large dedicated space to house the machines’ large footprint. Like SLS printers, MJF printer solutions include additional post-processing hardware for powder management and part recovery.
Fused Deposition Modeling (FDM) Nylon 3D Printers
Fused deposition modeling (FDM), also known as fused filament fabrication (FFF), is the most widely used form of 3D printing at the consumer level, fueled by the emergence of hobbyist 3D printers. FDM 3D printers build parts by melting and extruding thermoplastic filament through a printer nozzle that deposits the filament layer by layer in the build area.
FDM 3D printers generally use PLA and ABS filaments, but FDM machines more suited to professionals can often also print nylon. However, the benefits and drawbacks of FDM technology overall remain true, as FDM printers overall struggle to produce parts that capitalize on all the benefits of nylon.
Pros & Cons of Using FDM for Nylon 3D Printing
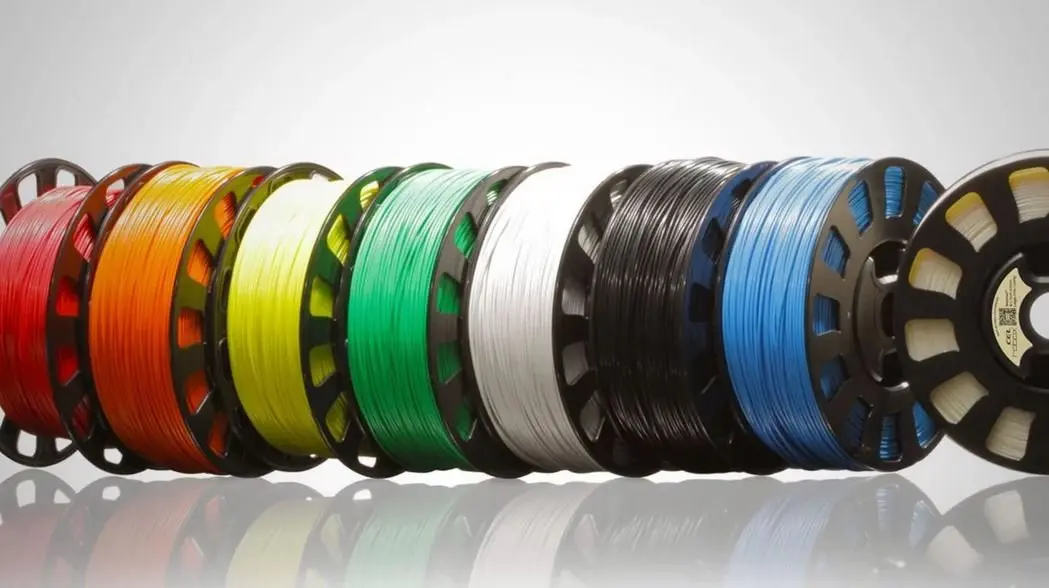
FDM filaments and blends offer various color options. (source: All3DP.com)
Because FDM prints are not isotropic along the Z-axis, many of the strength-related benefits of nylon are not achievable when using FDM to 3D print nylon. Nylon printed on an FDM machine also has a tendency to warp, just like ABS.
Additionally, because nylon is so hygroscopic, nylon filament may absorb water over the course of a long print, leaving layers printed in later stages with lower quality than the first layers. Accessories like a dry box are recommended to keep the filament from absorbing water during printing.
Similar to FDM printing with other materials, understanding the optimal settings for 3D printing with nylon typically involves extensive testing. Therefore, developing repeatable processes and generating consistent results across different types of nylon 3D printing materials can be difficult. The properties — including strength and accuracy — of finished parts may vary, so FDM is not recommended for extensive functional prototyping or end-use production with nylon.
FDM printing can be a good option for printing one-off and simple nylon parts quickly, but it’s not suitable for complex parts and higher volumes. Due to the use of support structures, it also generates considerably more waste than SLS or MJF printing.
Nylon Filaments for FDM 3D Printing
Nylon filaments are most commonly based on nylon 6 and nylon 66 as they’re slightly easier to print with, but there are also nylon 12 filaments available. Most nylons suitable for FDM printing come in glass- and carbon fiber-reinforced versions, which can increase stiffness, strength, and other critical mechanical properties.
Material | Description | Applications |
---|---|---|
Nylon 6 | General purpose, versatile material | Prototyping Enclosures and housings |
Nylon 66 | More rigid and abrasion resistant material | Prototyping Enclosures and housings |
Nylon 12 | General purpose, versatile material | Prototyping Enclosures and housings Tooling and fixtures |
Nylon composites | Glass or carbon fiber filled nylon | Parts undergoing sustained loading Robust jigs and fixtures |
Nylon 3D Printing FDM Requirements and Recommendations
Of the current options in the FDM market, many affordable models are equipped with the ability to 3D print nylon immediately upon receipt. However, even with these models, users must ensure that their hardware setup and printing process supports 3D printing nylon.
Hardware and settings recommendations for using FDM to 3D print nylon:
- All metal hot ends
- The ability to heat filament to 250° C or above
- Heated print bed (a glass bed is ideal) with glue applied
- Closed enclosure to avoid warping
- Filament drying system to achieve optimal results
Because of nylon’s high water absorption, filament spools must be kept in a plastic airtight container, and the use of a desiccant before printing with nylon can increase reliability and quality.
Comparison of Nylon 3D Printing Processes
Although FDM 3D printers provide a more affordable option, nylon parts from an FDM machine may not provide nylon’s desirable material properties. Most users who wish to leverage the benefits of nylon will select either SLS or MJF as their preferred technology.
SELECTIVE LASER SINTERING (SLS) | Multi Jet Fusion (MJF) | FUSED DEPOSITION MODELING (FDM) | |
---|---|---|---|
Resolution | ★★★★☆ | ★★★★☆ | ★★☆☆☆ |
Accuracy | ★★★★★ | ★★★★★ | ★★★★☆ |
Surface Finish | ★★★★☆ | ★★★★☆ | ★★☆☆☆ |
Throughput | ★★★★★ | ★★★★★ | ★★★☆☆ |
Complex Designs | ★★★★★ | ★★★★★ | ★★★☆☆ |
Ease of Use | ★★★★☆ | ★★★☆☆ | ★★★★☆ |
Material Properties | ★★★★★ | ★★★★★ | ★★★☆☆ |
Materials Available | Nylon 12, nylon 11, carbon and glass-filled nylon | Nylon 12, nylon 11, glass-filled nylon | Nylon 6, nylon 66, nylon 12, carbon and glass-filled nylon |
Cost | Benchtop industrial SLS 3D printers start just under $30,000 for the printer and $60,000 for the entire ecosystem, including powder management and cleaning stations. Traditional industrial SLS printers start at around $200,000. | Starting at $350,000. | Professional desktop FDM printers range from $2,000 to $8,000, and industrial systems are available from $15,000. |
Pros | Affordable High-quality parts Design freedom No need for support structures High throughput Simplified workflow Small footprint Low maintenance | Large build volume High-quality parts Design freedom No need for support structures High throughput | Low-cost consumer machines and materials Fast for simple, small parts Wide variety of colors |
Cons | Moderate build volume | Expensive machinery Large footprint Facility requirements Requires a dedicated operator | Low accuracy Lower quality parts Anisotropic Limited design freedom Requires supports |
Applications | Functional prototyping Short-run, bridge, or custom manufacturing Manufacturing aids (jigs, fixtures) | Functional prototyping Short-run, bridge, or custom manufacturing Manufacturing aids (jigs, fixtures) | Low-cost rapid prototyping Basic proof-of-concept models |
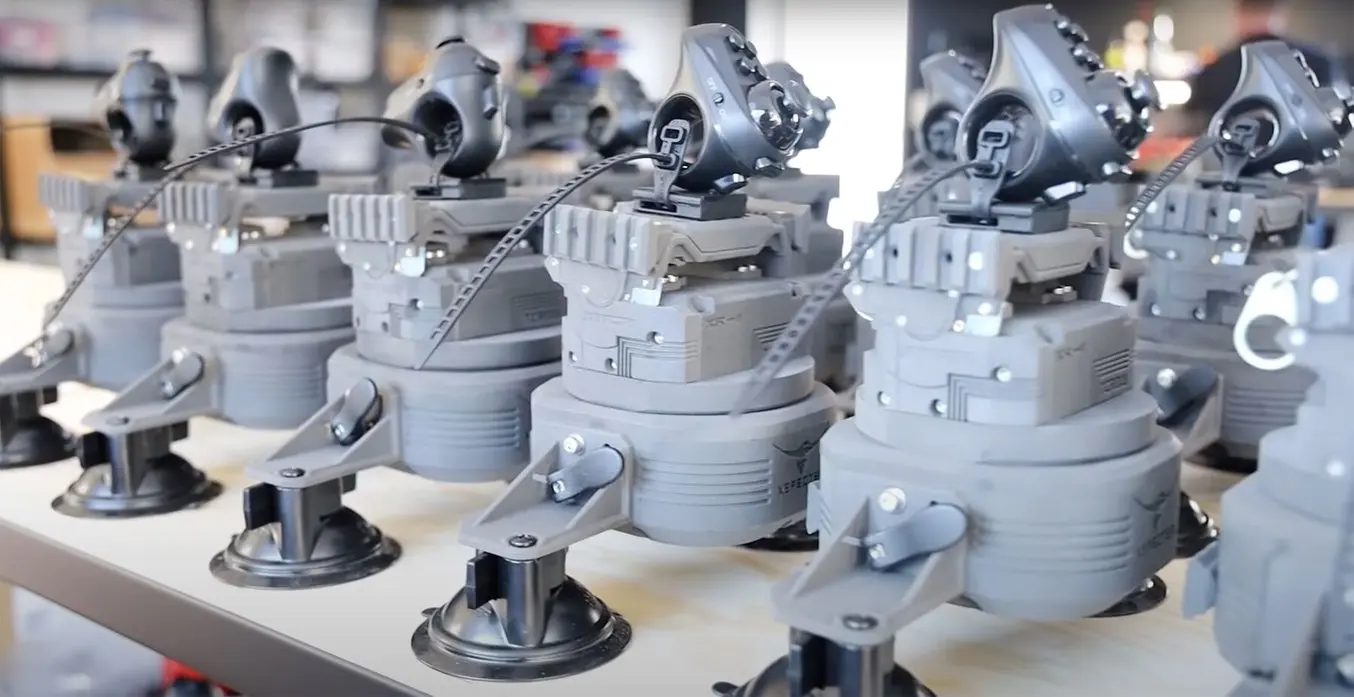
SLS for End-Use Production
3D printing for end-use production is not only possible, it's more affordable, agile, and scalable than ever with the Fuse SLS Ecosystem. Visit our SLS for Production page to compare production methods, learn about bulk powder pricing, and see production in action for 15 different manufacturers currently using the Fuse Series.
Get Started With Nylon 3D Printing
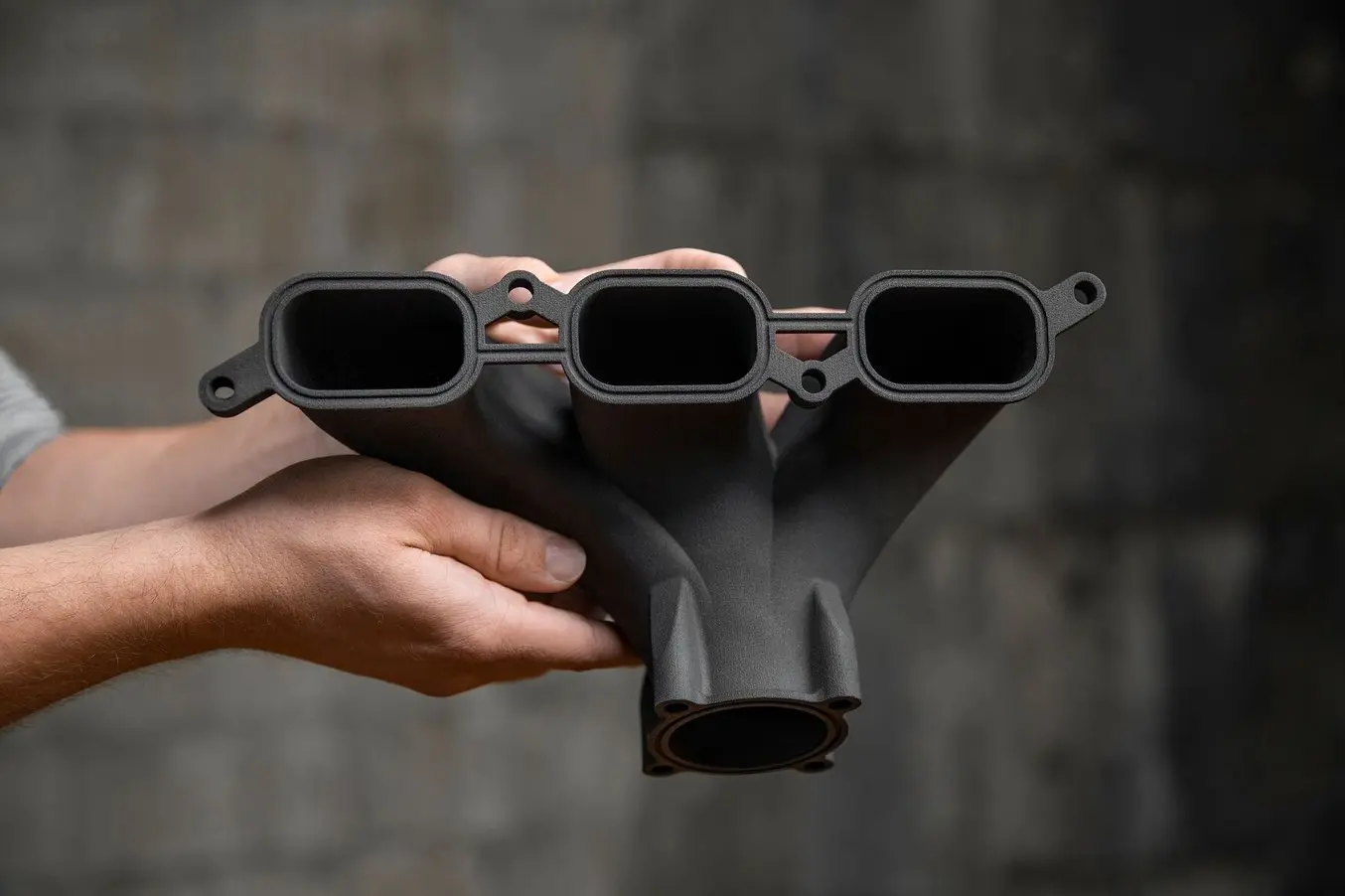
Nylon 3D printing is ideal for a variety of applications, from functional prototyping, to short-run, bridge, or custom manufacturing, as well as manufacturing aids (jigs, fixtures).
For many manufacturers, nylon 3D printing has replaced traditional processes, including high-end functional prototyping and small batch manufacturing. The same qualities that make nylon such a widely used material have led to its growth as a 3D printing material. However, not all nylon 3D printer technologies are created equal.
The three primary technologies used to 3D print with nylon are SLS, MJF, and FDM. While FDM printers typically have the lowest entry cost, the quality and consistency of parts printed on FDM machines prevent them from being a serious option for many nylon 3D printing applications.
On the other hand, SLS and MJF printers can generate high-quality parts but come at a cost well beyond the reach of many businesses. In addition to the high price tag, MJF and some SLS printers require significant floor space, expert technicians, and expensive ongoing support and maintenance that make them an impractical choice. However, a new type of SLS printing offers the benefits of high-quality nylon 3D printing while improving on ease of use, hardware and space requirements, and most importantly, cost: benchtop SLS.
Benchtop SLS combines affordability and quality. With many of the same materials options, including glass- and carbon fiber-reinforced nylon, options such as the Formlabs Fuse Series provide users with high-quality in-house 3D printed nylon parts at a fraction of the price.
Considering bringing nylon 3D printing capabilities in-house? Request a free sample of our high-performance nylon materials or speak with an SLS expert today.