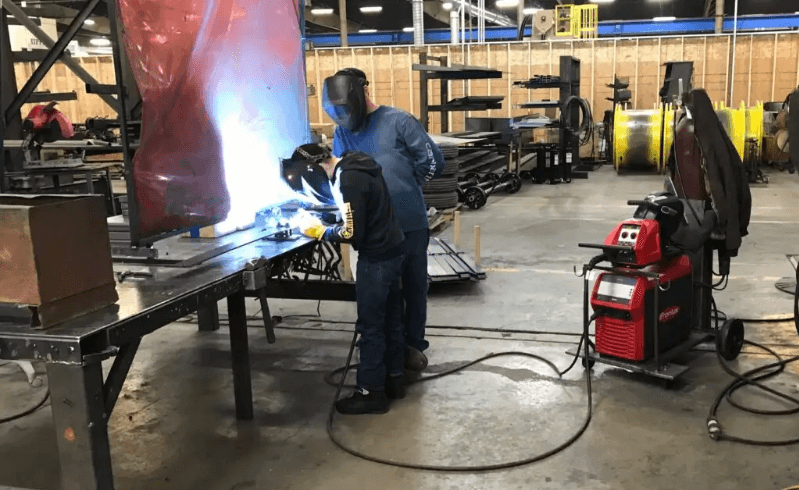
Manufacturing aids like jigs and fixtures are critical in metalworking to ensure precision, repeatability, and efficiency. But producing jigs and fixtures with traditional methods can take a couple of weeks, cost upwards of $1,000, and limit geometries. Red Oak Fabrication is a machine shop in Southwest Iowa that uses stereolithography (SLA) 3D printing to produce custom jigs in hours, for a tenth of the price of CNC machining, and in complex geometries and organic shapes.
Red Oak Fabrication manufactures products in steel, stainless steel, and aluminum. They specialize in precision plasma, laser, and water jet cutting, CNC operations, steel blasting, powder coating, sheet metal forming, and advanced robotic welding. Welding, primarily metal inert gas (MIG) welding, is a large part of their activity, with 15 manual welding stations and three automated robotic welding cells.
“3D printing has opened up an easy middle ground. I can go from design to a finished jig in a couple of days instead of a couple of months.”
Taylor Smith, Drafting and Engineering Manager at Red Oak Fabrication
Prior to 3D printing, Red Oak Fabrication had two in-house methods for making welding jigs:
- Mounting sheet metal parts together: easy and affordable but inaccurate.
- CNC machining to fabricate high-quality metal jigs, but at high costs and long lead times.
This left them at a loss for small-to-medium orders that required quicker turnarounds. To address this gap, they brought in a Form 3L SLA 3D printer to 3D print accurate and robust jigs and fixtures in one day, at up to 90% less of the cost and time of previous methods.
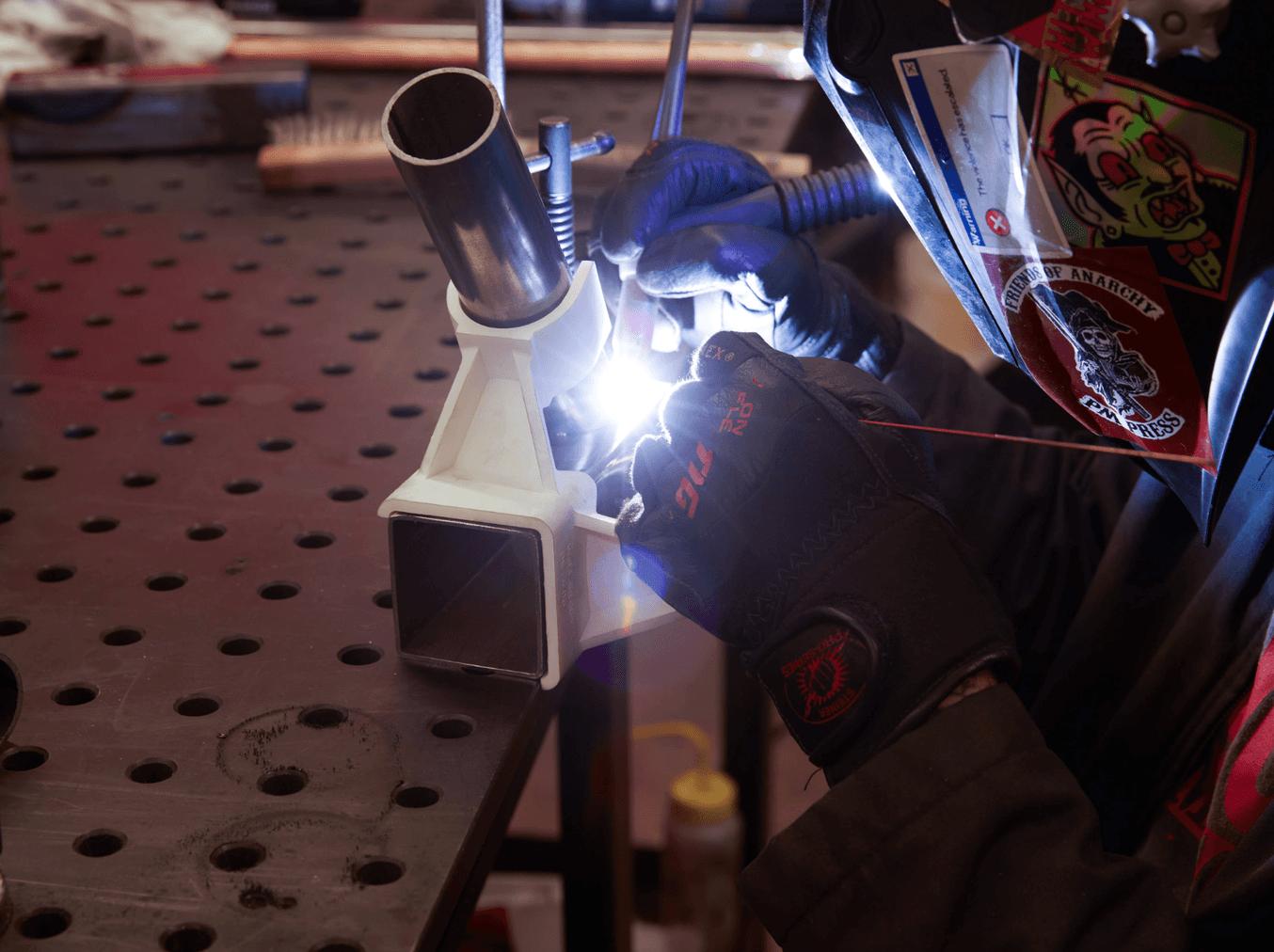
Low-Cost and Rapid Jigs and Fixtures for Metal Fabrication
This white paper outlines a methodology for using 3D printers to produce jigs, fixtures, and other tools for metalworking. Real-world case studies show how Formlabs printers create durable, precise, and heat-resistant tools that perform well in demanding environments. It highlights how companies can cut lead times and costs by up to 90% while improving tool customization and complexity.
Achieving Organic Shapes & Complex Geometries
“The jig that goes on a pipe would be almost impossible to machine because it’s so organic. You would spend forever making one of these in a way other than 3D printing. If we made a jig out of metal it would be lower quality and significantly less reliable. It’d be more work for the operator. 3D printing streamlines the process.”
Taylor Smith, Drafting and Engineering Manager at Red Oak Fabrication
CNC machining can limit the geometries of jigs it’s possible to produce. In contrast, organic geometries are easily attained with 3D printing. SLA 3D printing can be used to create intricate internal features like channels, undercuts, and hollow structures, and allows for precise, intricate designs with wall thicknesses around 2-3 mm. Additionally, SLA is optimal for fine details and smooth surfaces, which can improve performance and reduce costs.
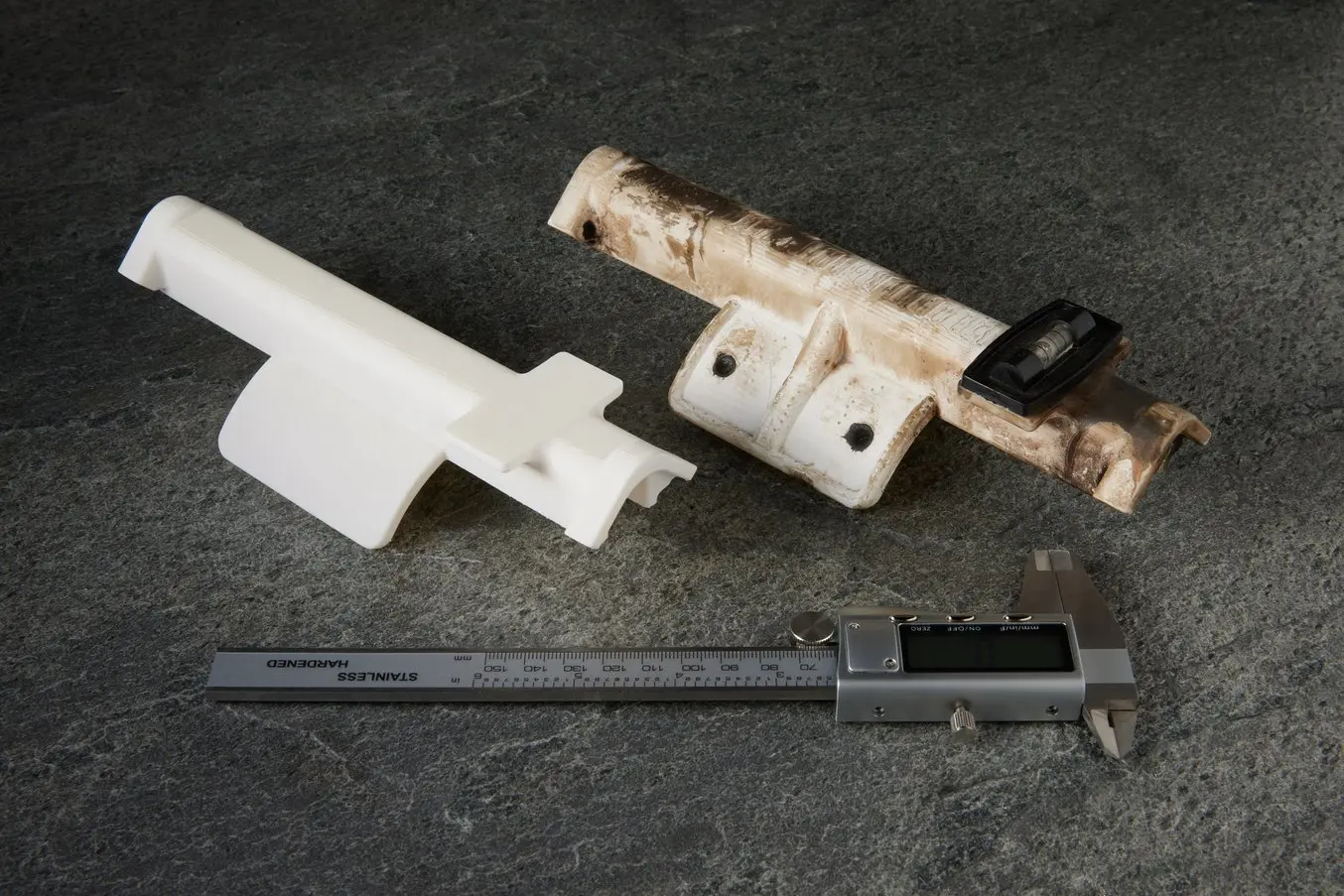
This geometry is complex with an organic shape that would be challenging to machine. This jig ran thousands of welds and is still functional, though its color turned from white to black over time, due to its proximity to the weld.
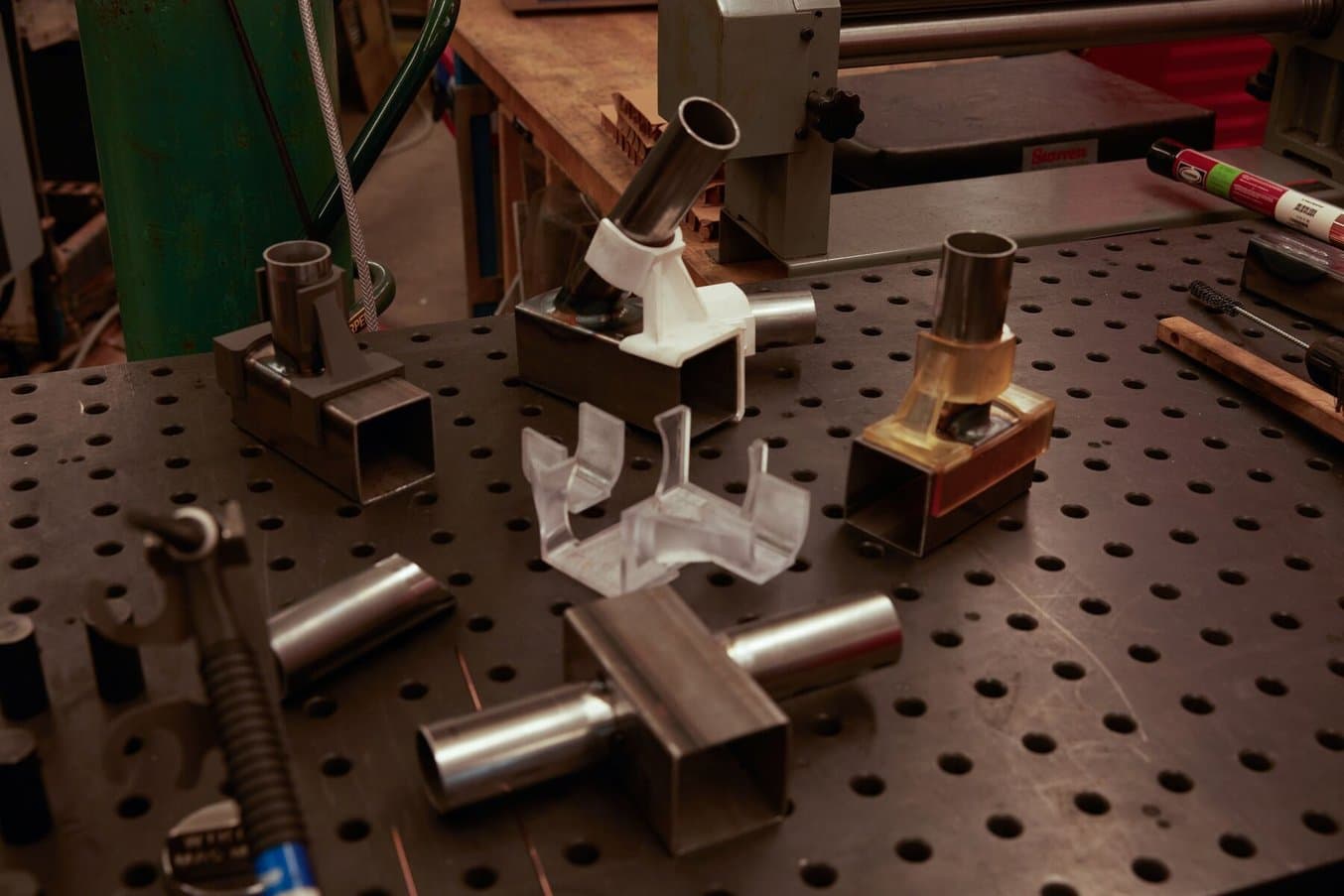
Low-Cost and Rapid Jigs and Fixtures for Metal Fabrication
The Factory Amsterdam (TFA), a CNC Machine Shop focused on automation, leverages Formlabs SLS technology to gain flexibility and adapt faster to customer needs. This webinar provides an overview of the step-by-step method as well as practical examples with cost analysis, design considerations, and best practices to 3D print jigs, fixtures, and other tools.
3D Printing Jigs: A Tenth of the Cost in Days Over Months
The time it takes to design and machine a jig takes the same amount of time regardless of how many parts are going to be produced with it. For Red Oak Fabrication, it would take just as long, and cost just as much, to produce jigs for small to medium jobs as for large ones.
However, with 3D printing, Red Oak Fabrication found they could save almost 90% of costs, and reduce the turnaround time of jig production from months to days. Additionally, if changes were needed to the design, these could be easily implemented and printed, without wasting time and at minimal costs.
Welding Jig Cost Analysis
Alternative Method | 3D Printing In-House | |
---|---|---|
Equipment | Metal CNC machined in-house | Form 3L, Rigid 10K Resin |
Cost | $1,000 | $100 |
Time | Months | Days* |
*With Form 4L, the next generation of Form 3L, print time for these parts would be hours instead of days. Learn more about Form 4L here.
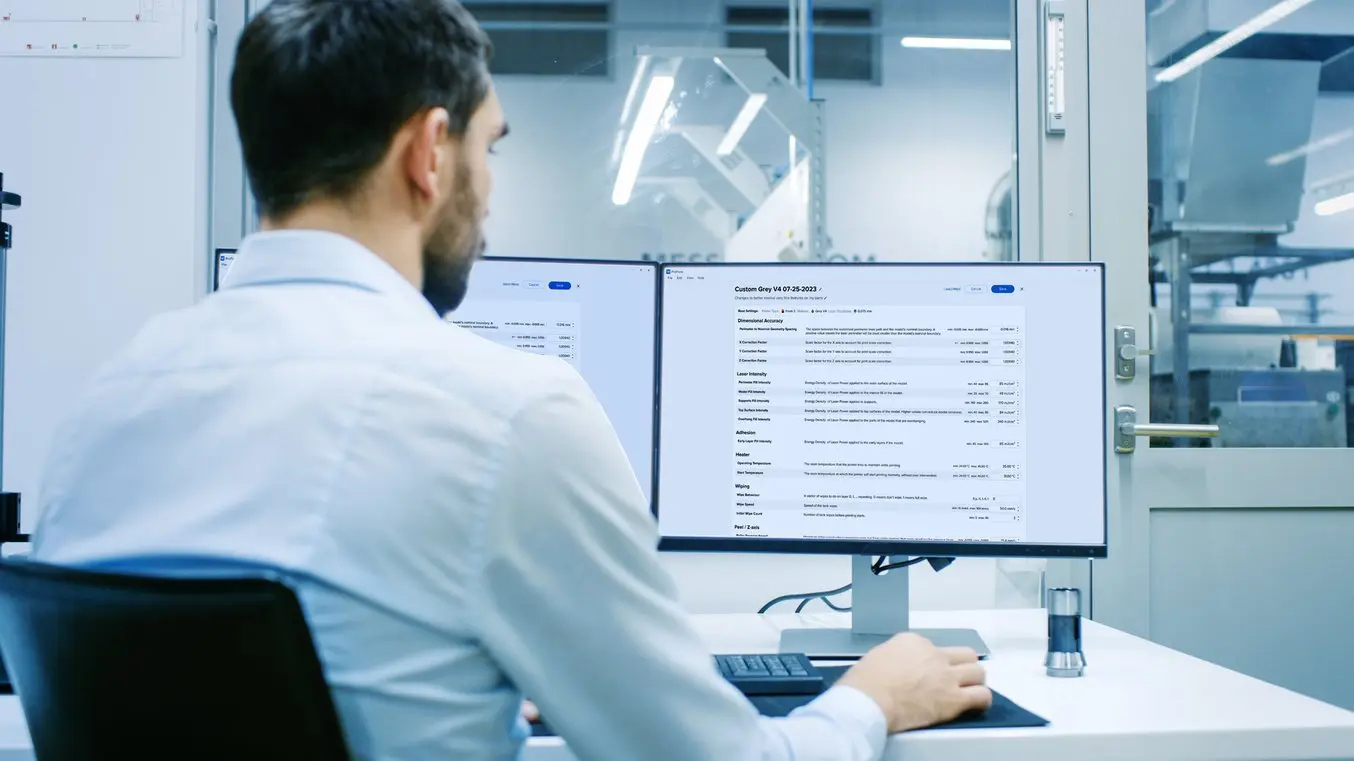
Talk to Our Sales Team
Whether you need to prototype at speed, or are producing end-use parts, we’re here to help. The Formlabs Sales team is composed of dedicated specialists who know exactly how to support you and your company's needs.
A Material That Meets Production Demands: Rigid 10K Resin
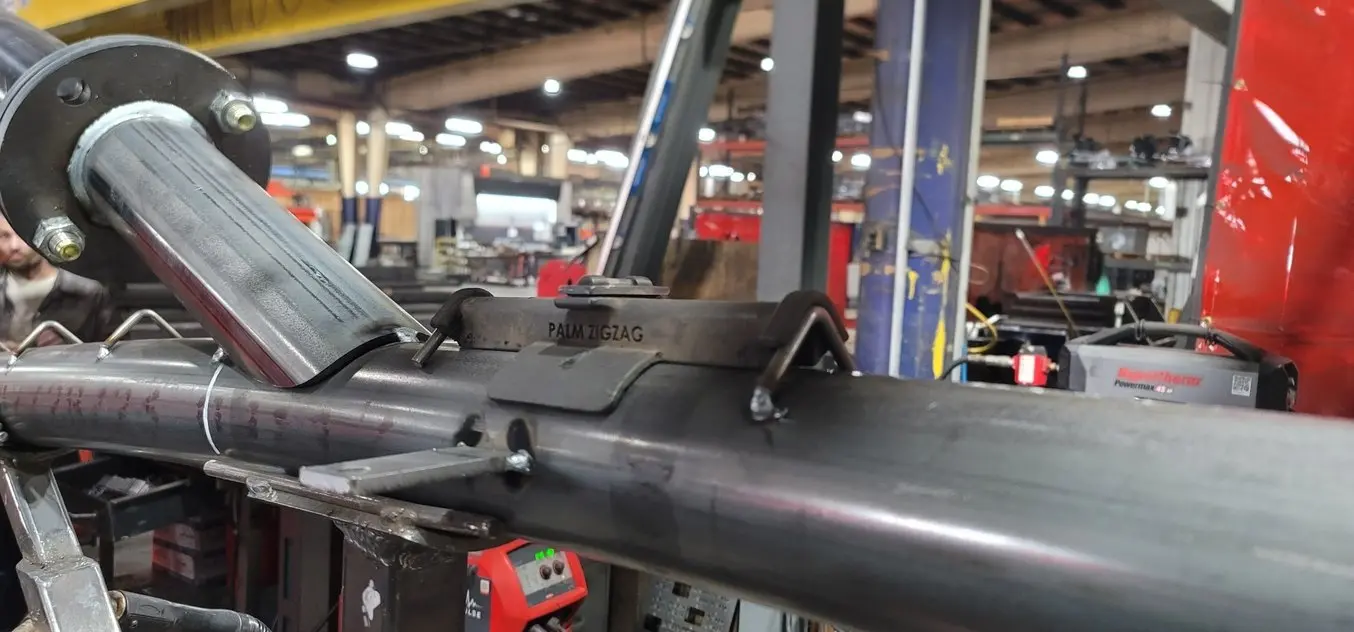
The zigzag jig welds 20 round bars along a pipe and is positioned close to the weld, resulting in its black color.
Welding operations typically reach temperatures of a few thousand degrees Celsius, which is a challenging environment for polymeric tooling. Therefore the team chose to print with Rigid 10K Resin, a stiff, glass-filled material offering a heat deflection temperature (HDT) of 238 °C @ 0.45 MPa that was recommended by Formlabs.
Because the jigs are not directly in contact with the weld, and the processing time is only about 10 seconds, the tools do not heat up in excess. Some blackening occurs on the white material, but it does not affect performance. However, in the case that a jig breaks, a replacement can be reprinted in just a few hours.
90% of the welding is done with steel, plus some aluminum and stainless steel. Unlike with metal jigs, welding BBs — the liquid metal bits formed from splattered molten metal — don’t stick to 3D printed plastic jigs, meaning 3D printed jigs don’t need to be cleaned.
Note: For low-heat welding processes such as ultrasonic welding or spot welding, jigs can be 3D printed with Nylon 12 Powder on Fuse Series selective laser sintering (SLS) 3D printers.
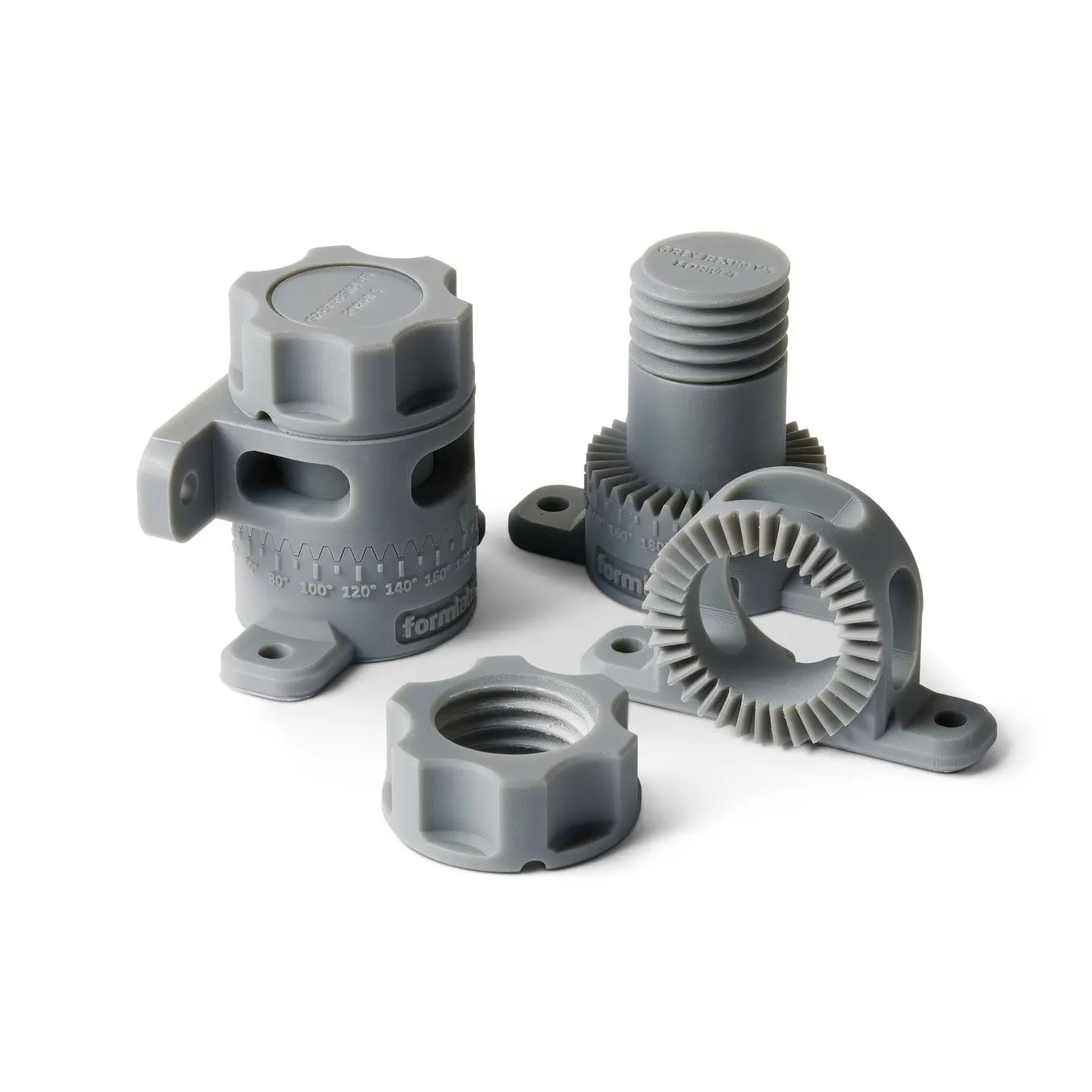
Request a Free Sample Part
See and feel Formlabs quality firsthand. We’ll ship a free 3D printed sample part to your office.
Jigs That Are Up to the Job
At Red Oak Fabrication, most individual welding jigs are used over 1,000 times a month, and the jigs 3D printed using Rigid 10K Resin stand up to frequent use.
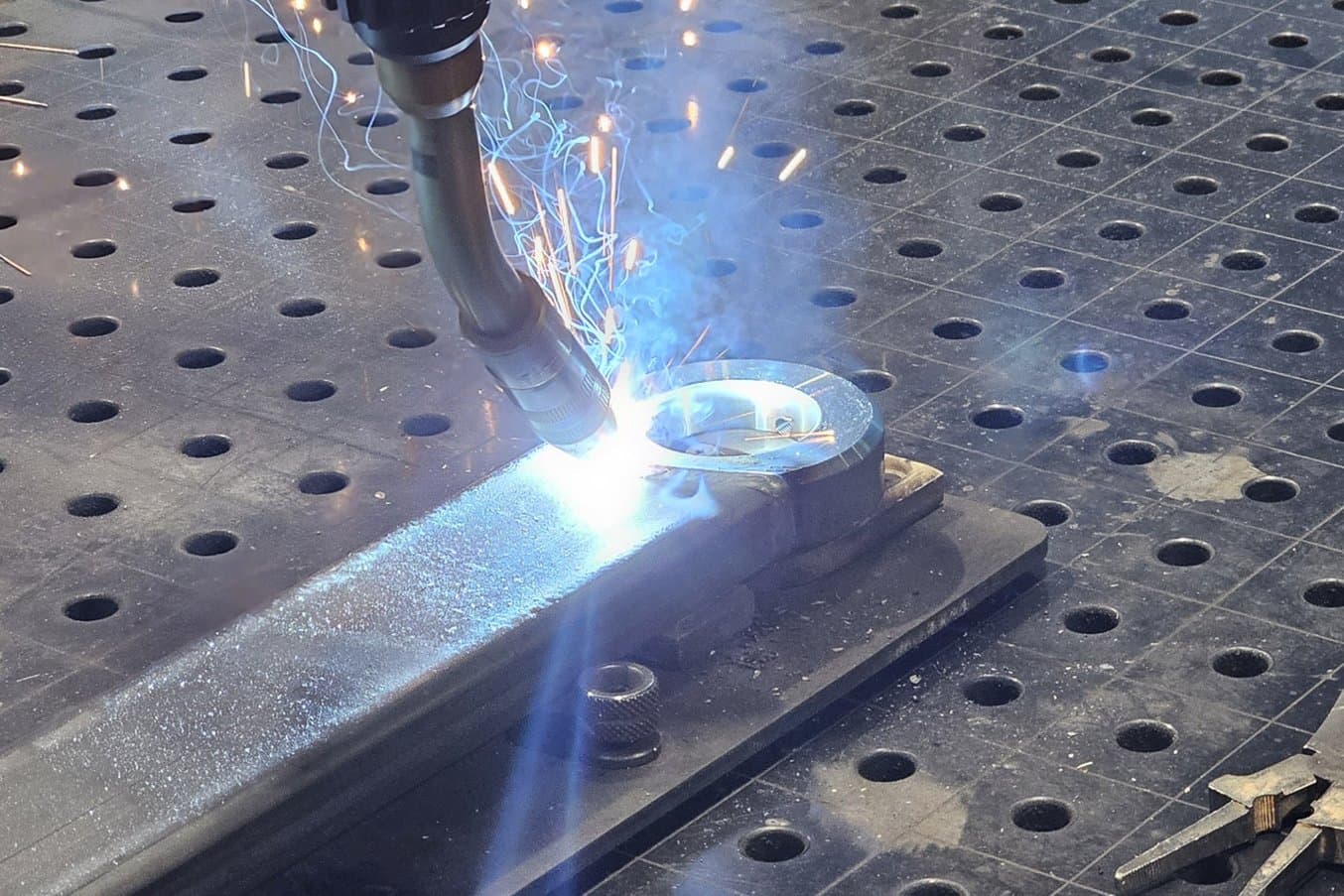
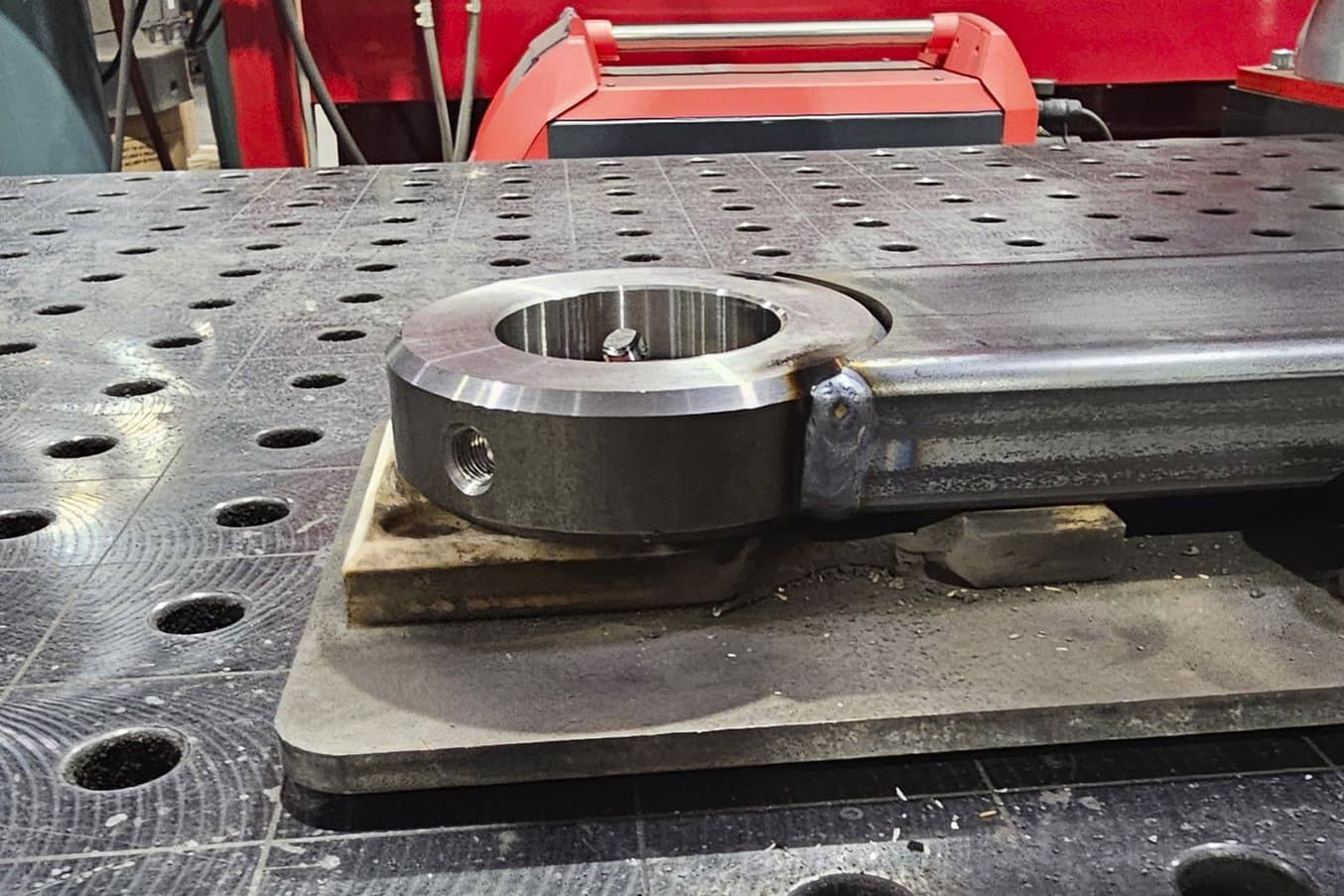
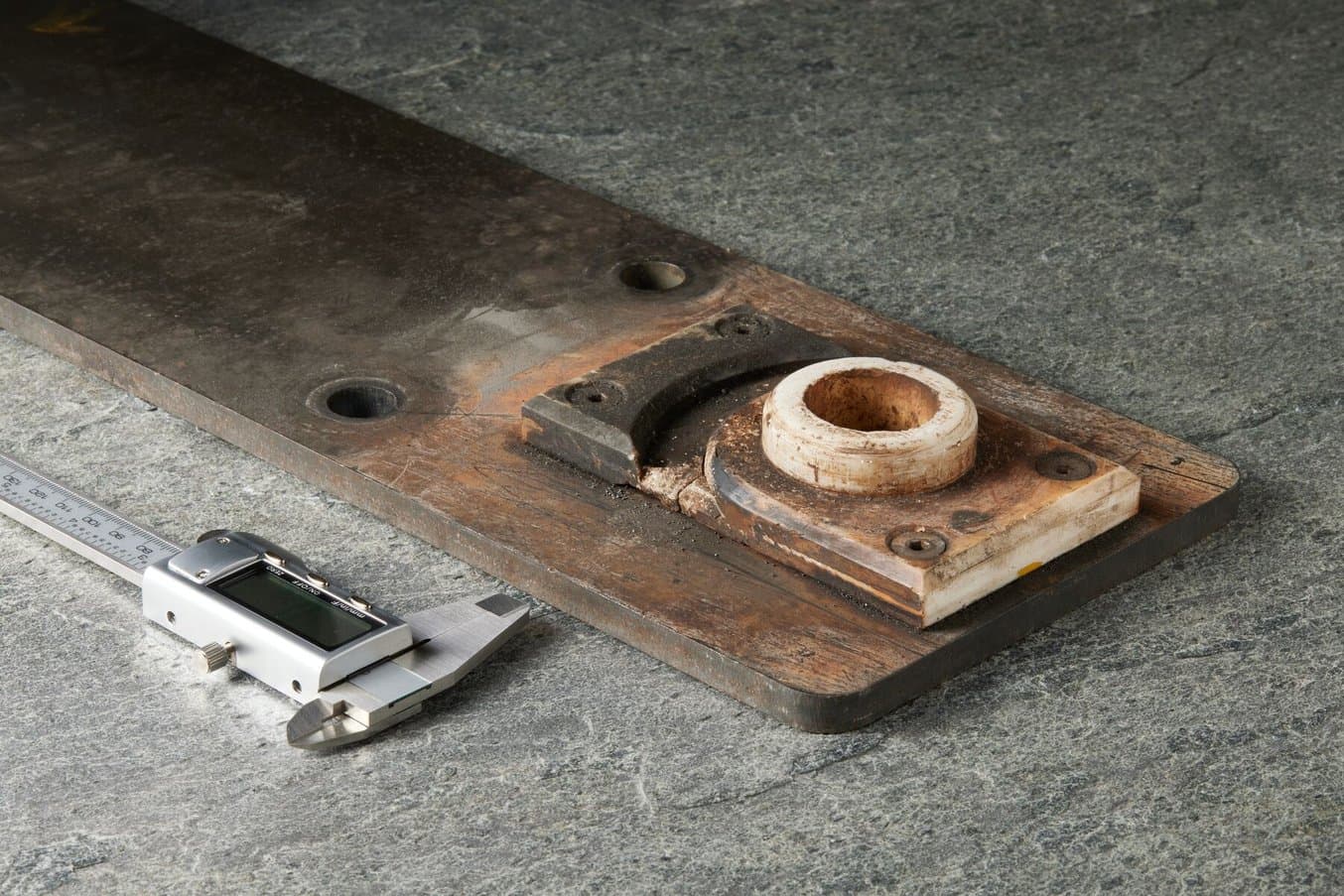
The straight arm jig is made of two small 3D printed parts mounted over a steel plate. The geometry is complex, with organic shapes that would be challenging to machine. Additionally, the team needed the tool in one day. After running about 2,000 welds on the jig it is still functional, even though some welds have been dropped on the jigs by accident, causing marks.
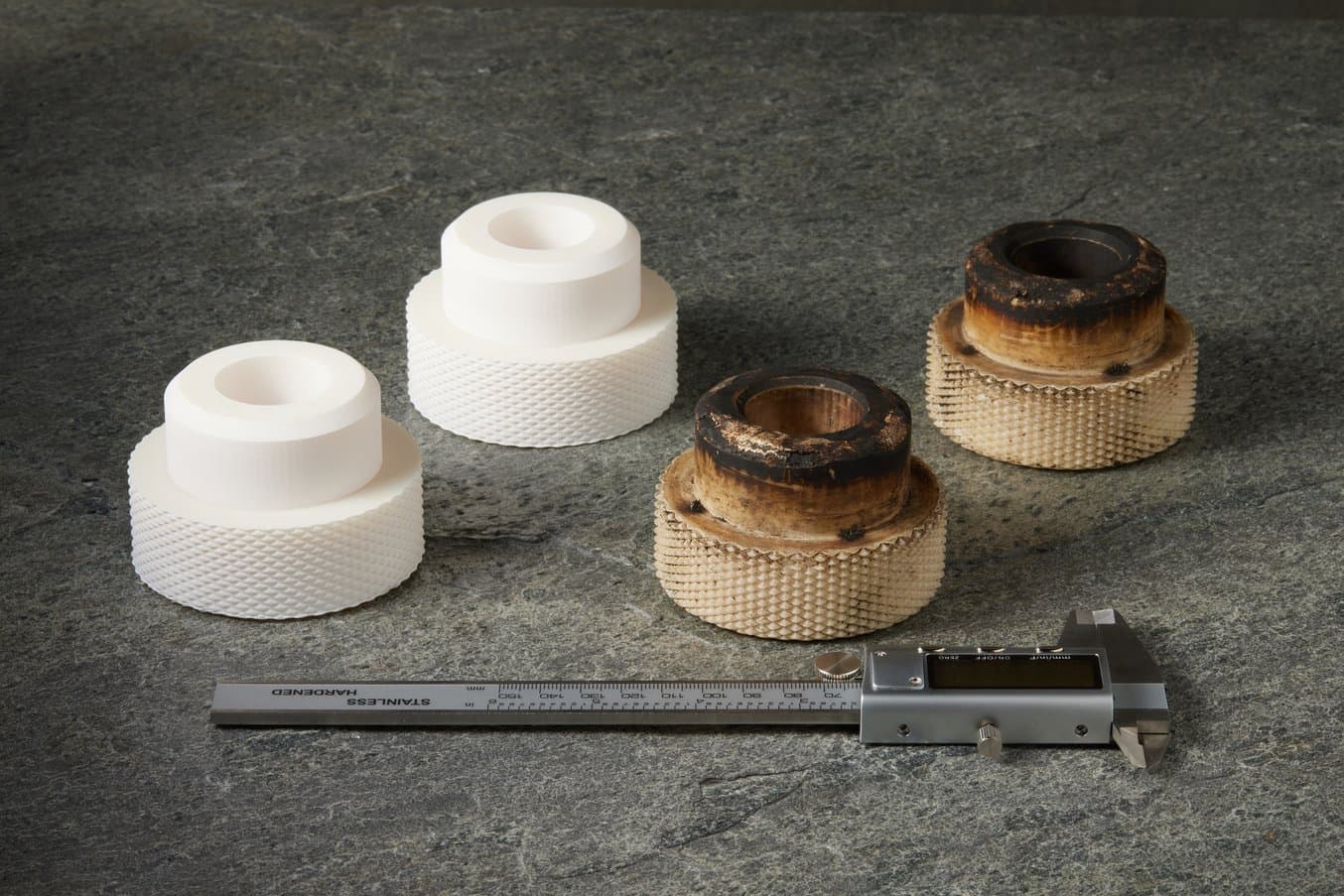
Protective plugs before (left) and after (right) use. They are placed inside a steel half coupling with magnets to protect the internal thread while a pipe is being welded onto it. Protective plugs prevent the weld and slag from going inside the half coupling and ruining the thread. After running about 3,000 welds on that jig, they are still functional.
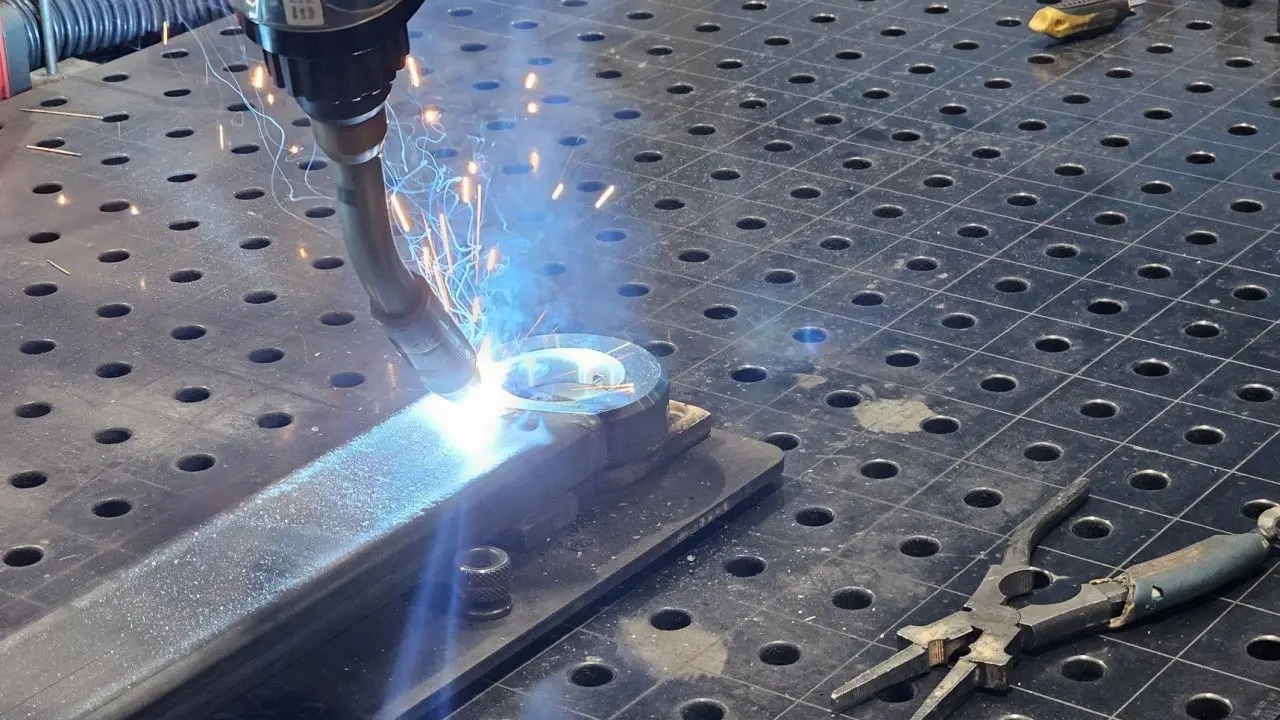
Quick Custom Welding Fixtures With 3D Printing
Discover how to streamline your tooling process to accelerate rapid prototyping and low-volume production of metal parts with quick and modulable welding fixtures. Our R&D machine shop coordinator shares methods and best practices for 3D printing welding fixtures, including design guidelines, tool temperature study, practical examples, and cost analysis.
Start 3D Printing Jigs and Fixtures
3D printing jigs has saved time and costs for Red Oak Fabrication while enabling the production of jigs with complex geometries and organic shapes that could not be achieved with CNC machining. The large build volume of Formlabs Form 3L SLA 3D printer means Red Oak Fabrication can print large jigs in one build or multiple small jigs, so that multiple welding stations can simultaneously start working.
Explore additional case studies and learn how to print 3D jigs and fixtures in our white paper, or contact sales to discuss your application.