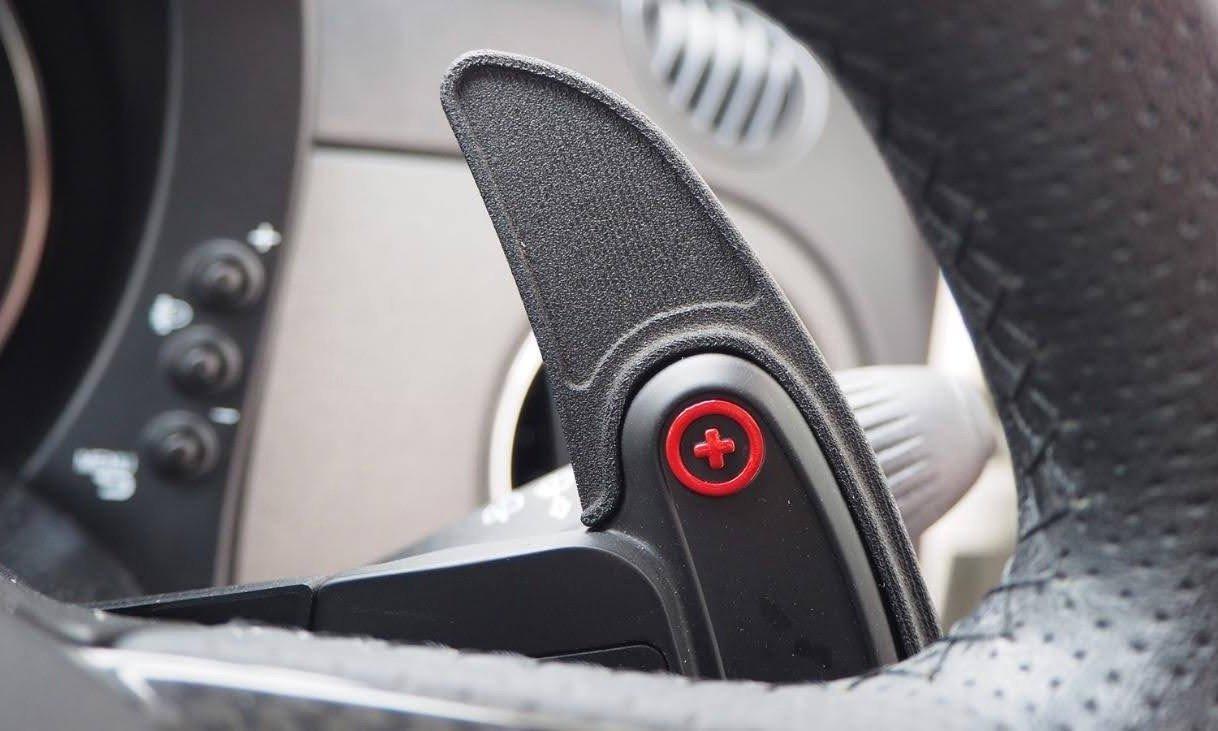
Japan has been at the center of automotive innovation for decades. Lean manufacturing principles that come from Japanese automaker philosophies — like ‘kaizen,’ or continuous improvement — are currently taught by executive training programs across the world and touted as foundational protocols for all types of manufacturers. The spirit of innovation and continuous development that started at those large OEMs is also very much alive at Japanese aftermarket automotive manufacturer, Codetech CAM.
Codetech has carved out a niche in the competitive Japanese automotive industry by providing aftermarket solutions for imported cars. Though the customer base may be small, imported car enthusiasts have strong preferences, and demand for personalization and luxury add-ons is growing.
Codetech answers that demand by creating a responsive and agile manufacturing model based on high performance 3D printed parts. Using both stereolithography (SLA) and selective laser sintering (SLS) technology, Codetech has been able to provide customers with solutions that enhance their driving experience as well as their imported car’s aesthetics. “With the well-founded understanding of the customers’ needs, and the technical capabilities to implement them, there are still plenty of opportunities for creating interesting products,” Masato Uchida, Design Lab Manager at Codetech, told us.
Finding the Gap in the Imported Cars Market
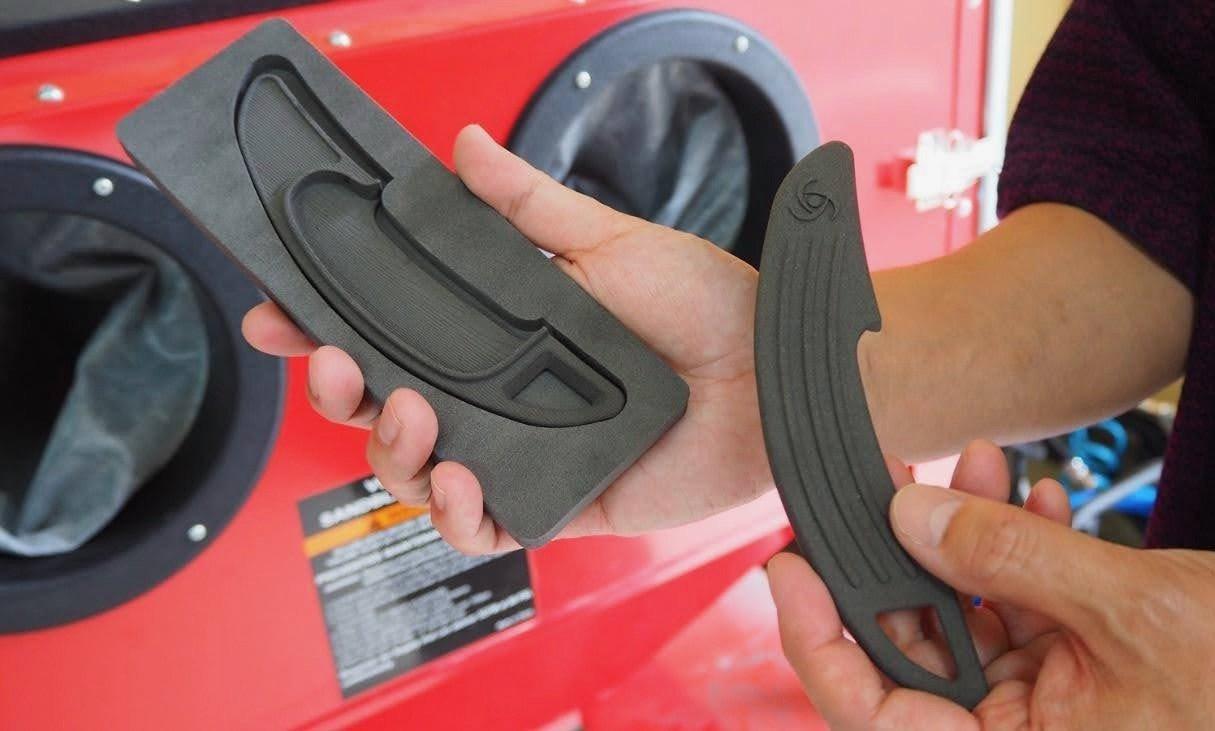
Extending Abarth's original steering wheel paddle shifters makes for a more comfortable size and texture for fingers, these Core OBJ Paddle Shifter Extensions are a popular product for Codetech.
Japanese automakers like Toyota, Honda, and Nissan, control the vast majority of market share in Japan, but European brands like BMW or Volkswagen are prized by a small group of consumers as luxury items. These car owners want customized accessories and aftermarket parts, but finding car part manufacturers that cover a broad range of original equipment manufacturer (OEM) brands is nearly impossible.
As automotive software systems become more sophisticated, finding those aftermarket parts becomes harder. Electrical components are often updated as software systems change with each new car model, rendering aftermarket add-ons obsolete.
Codetech is able to step in where other aftermarket manufacturers cannot because they rely on a more agile production method — 3D printing.
How 3D Printing Enables Reverse-Manufacturing
Traditional techniques in automotive manufacturing, like injection molding, CNC machining, blow-molding, or sand casting, are efficient mass production methods for OEMs. For aftermarket manufacturers, who have to reverse engineer components in order to adjust or reproduce them, these methods make it impossible to manufacture cost-effectively.
The Codetech team knew from the beginning that in order to consistently and cost-effectively produce parts that were compatible with mass-manufactured imported cars, they would have to use a more agile and flexible fabrication method.
Uchida and the Design Lab team started with the Form 1 stereolithography (SLA) 3D printer, adding the Form 2, Form 3, and now Fuse 1+ 30W SLS printer, growing their capacity as the demand from their niche customer base increased. When the team receives a request for a new part, they can reverse engineer the OEM component through 3D scanning and CAD design. Once Uchida has the file, he can print immediately, and deliver an end-use part that’s been manufactured without the need for expensive tooling. “One of the things I like about the Fuse 1 is that I can print a nearly final product from the start,” says Uchida.
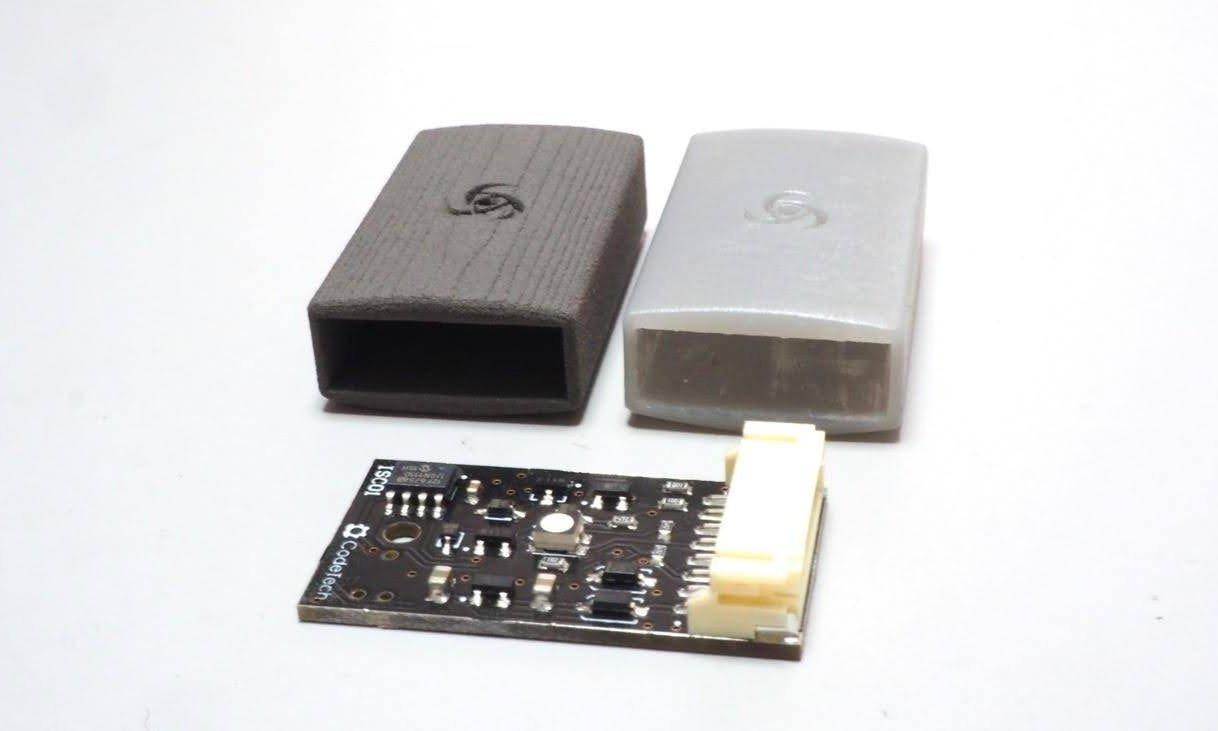
These electronics enclosures were quickly prototyped on a Form 3 SLA printer in Draft Resin, then printed as an end-use part on the Fuse 1+ 30W SLS printer.
This commercial viability of 3D printed SLS parts was validated at a recent automotive exhibition. Uchida had quickly designed a computer chip enclosure and printed a prototype on the Form 3 in Draft Resin as a small demonstration of what Codetech could do. At the exhibition, he received unexpected positive feedback — people wanted to know when the product would be available for purchase. Uchida returned to the Design Lab and ran a production run on the Fuse 1+ 30W in Nylon 12 Powder.
“The exhibition happened only because I was able to create an almost final product with the Fuse 1 straight after modeling. I find this speed is needed, and fits in with the times we live in."
Masato Uchida, Design Lab Manager at Codetech
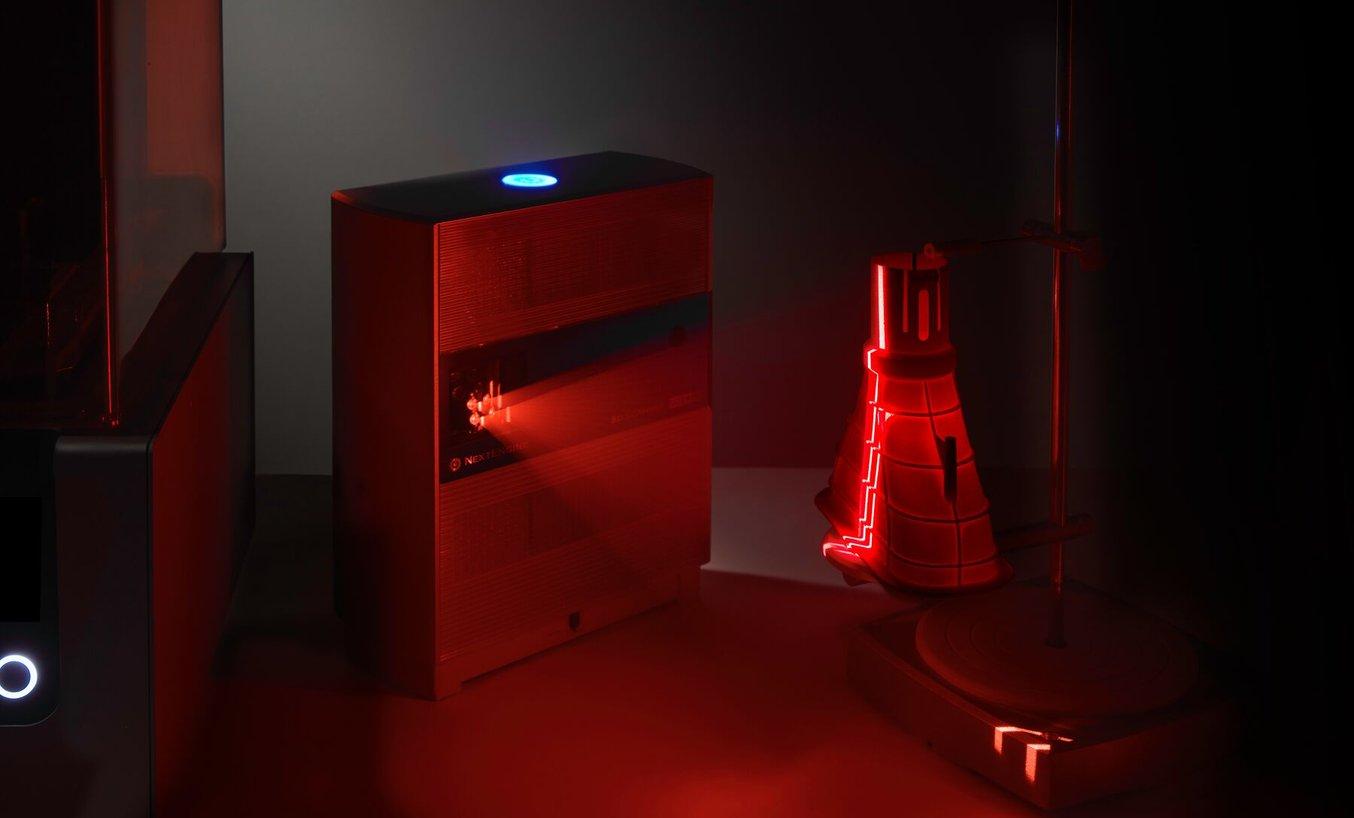
3D Scanning and 3D Printing for Reverse Engineering and Other Applications
3D scanning and 3D printing workflows can be applied to replication and restoration, reverse engineering, metrology, and more. Download our white paper to explore these applications and learn how to get started.
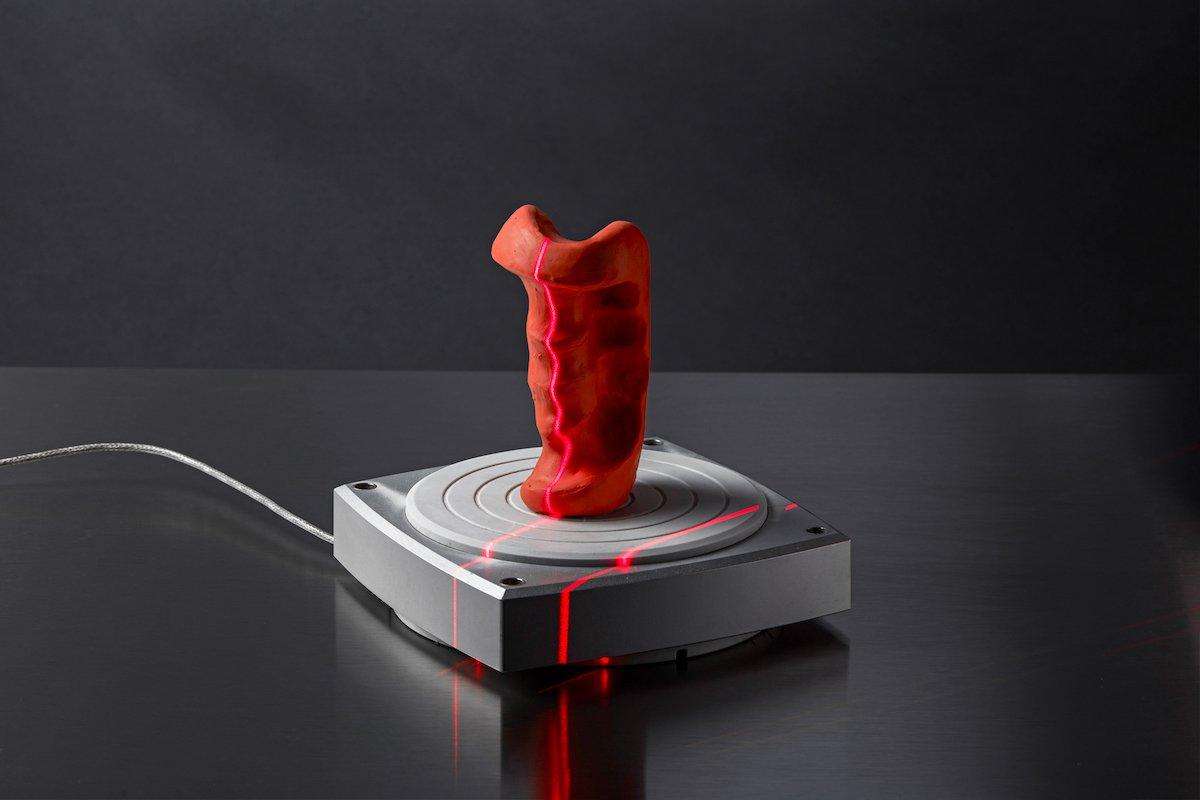
3D Scan to 3D Print: Rapid Reverse Engineering for Machine Restoration, Assembly Jigs, and Aftermarket Products
Watch this webinar for a detailed look at how to start using 3D scanning to improve part design and production when paired with reverse engineering CAD and 3D printing.
Flexible Supply and Online Orders
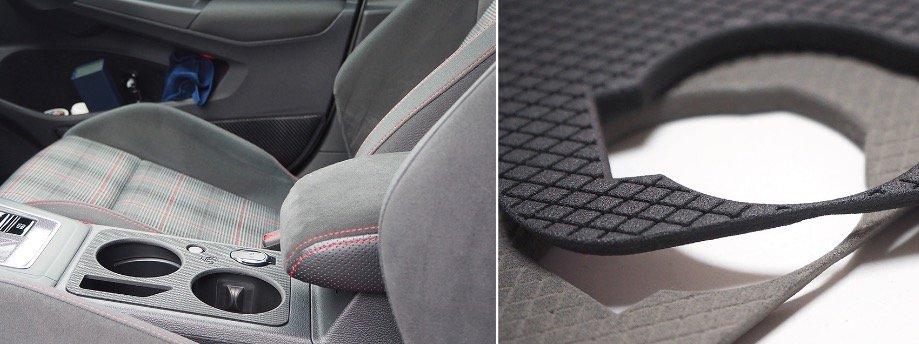
The cup holders for the Volkswagen Golf 8 are sandblasted and then finished with a matte black urethane coating (left). The thin edge of the holder (shown at right) would be impossible through traditional manufacturing methods; 3D printing in-house makes it possible to create parts with these tight tolerances and small features.
Having a digital inventory and 3D printing production processes also lets Codetech respond quickly to changes in demand, and protects them from having to build large physical inventories. Designing and producing one-off items, then advertising them online, lets Codetech gauge demand before moving into production. They can operate more flexibly and efficiently, and can avoid expending resources on products that won’t sell. When the demand is there, they can switch their production workflow to answer it immediately.
In the case of a cup holder created to fit into a Volkswagen center console, Codetech advertised the product first, then switched their production workflow to match. Uchida packs each build chamber with 25 cup holders; the Fuse Series packing algorithm and powder recycling workflow make low volume production series like these possible. The cup holder design gained immediate popularity because its thin outer edges fit perfectly into an existing VW console, but would be too thin to mold through traditional processes — a case where additive manufacturing not only replicates parts, but improves upon them.
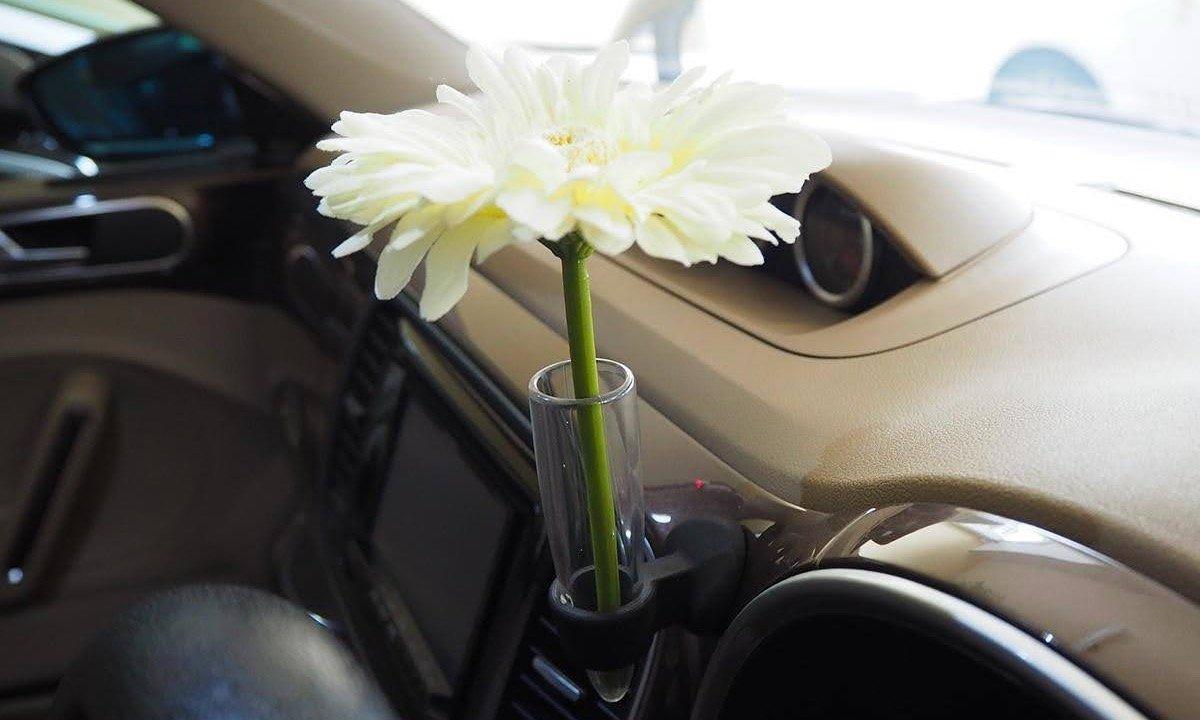
Aftermarket parts can help with personalization, like this flower vase attachment with a 3D printed attachment fixture.
To make end-use SLS parts like these even more appealing to consumers, the Design Lab team employs advanced post-processing techniques to smooth the surface of the nylon parts. The cup holders were depowdered in the Fuse Sift, sandblasted, and then finished with a matte black urethane coating, making it fit seamlessly with the Volkswagen’s interior finishes.
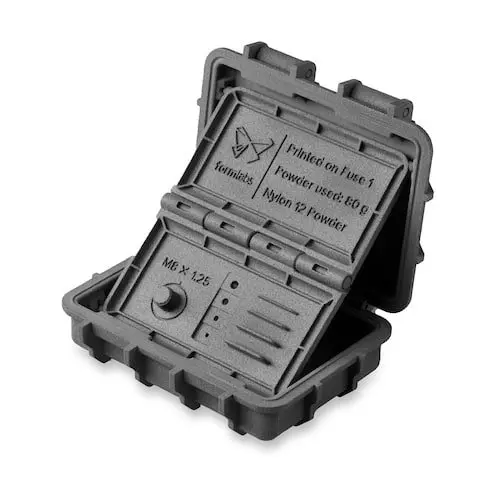
Request a Free SLS Sample Part
See and feel Formlabs quality firsthand. We’ll ship a free SLS sample part printed on the Fuse 1+ 30W to your office.
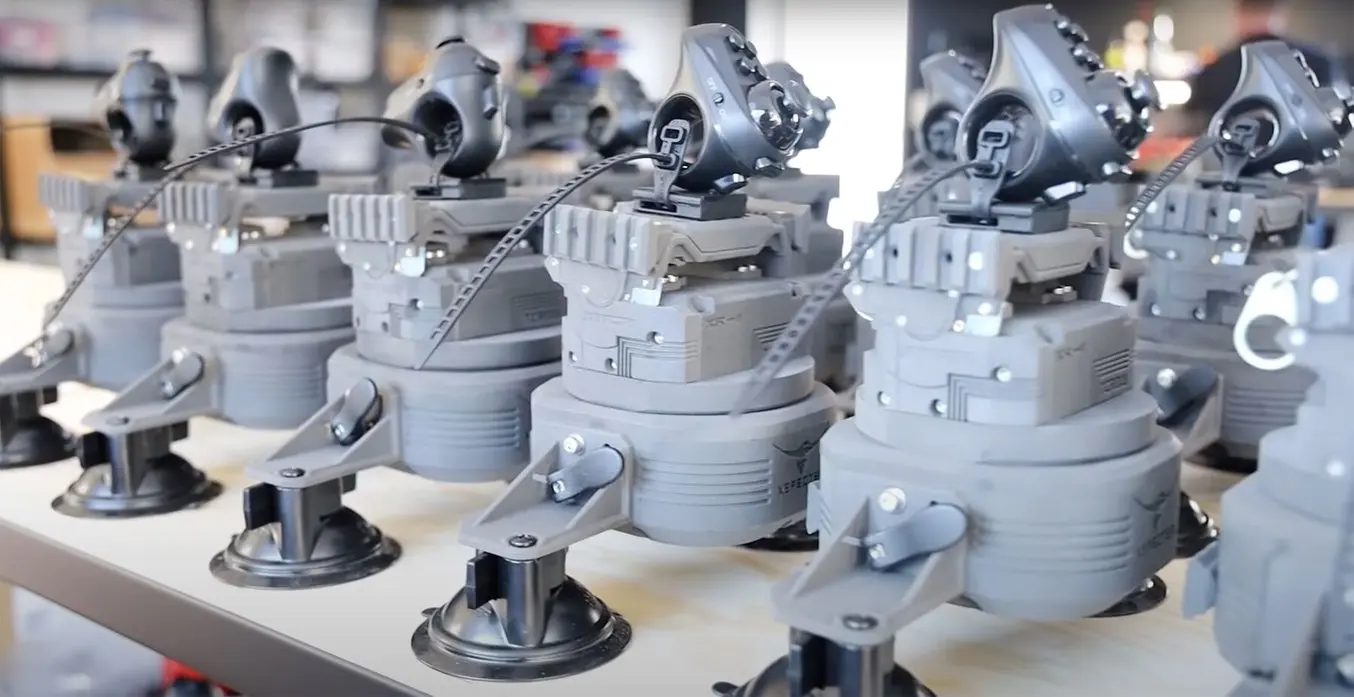
SLS for End-Use Production
3D printing for end-use production is not only possible, it's more affordable, agile, and scalable than ever with the Fuse SLS Ecosystem. Visit our SLS for Production page to compare production methods, learn about bulk powder pricing, and see production in action for 15 different manufacturers currently using the Fuse Series.
Moving Forward With AM
Uchida and his colleagues at Codetech are committed to continuously innovating, and developing products that can address constantly shifting consumer demands. Leveraging Formlabs printers, which Uchida finds “intuitive and easy to use,” the Codetech team can create a flexible and responsive manufacturing process. On-demand production of end-use parts with the Fuse 1+ 30W allows the business to avoid spending money and time on expensive traditional fabrication or the maintenance of high volumes of physical inventory.
To learn more about 3D printing in the automotive industry, explore our auto applications and case studies. To see how SLA or SLS 3D printing can benefit your workflow, contact our automotive experts.