Tapestry leverages 3D printing for product design like footwear.
What happens when fashion and 3D printing join forces? It is becoming increasingly likely that the fashion you see on the runway and the products—from hardware and jewelry to shoes —you see at stores have been prototyped using Formlabs 3D printers. At Tapestry, the first New York-based fashion house of modern luxury brands and the parent company of well known high fashion brands Coach, Kate Spade, and Stuart Weitzman, 3D printing drives early stages of product development.
Long before Tapestry and shortly after graduating with a degree in industrial design, Tomer Emmar, established a jewelry design company called Studio Forty Seven where he had his first exposure to 3D printing. There, he combined metal fabrication techniques with 3D printing for the first time in his career. “After doing due diligence integrating 3D printing into the process, it became very clear to me that 3D printing was going to enable any design process to be more effective. It helps in validating concepts quickly and producing work on demand; you can be assured concepts will work out and the work can be produced without needing space dedicated for holding inventory,” Emmar said.
After relocating to New York, Tomer was employed at a 3D printing service bureau where he learned to operate various 3D printing technologies including Formlabs SLA printers before taking a role at Tapestry.
What role does Formlabs play in driving products at Tapestry? In this blog post we’ll cover the following:
- 3D Printing as a Communication Tool.
- How the Form 3L, Formlabs’ large-format SLA 3D printer changed the game.
- The future of 3D printing for Tapestry.
3D Printing as a Communication Tool: Design Intent + Mechanical Functionality
As Rapid Prototyping Manager at Tapestry, Tomer Emmar manages the 3D printing lab in New York and a team of prototyping experts utilizing various additive manufacturing technologies to expedite both the design and product development processes prototyping products across multiple categories. “We are using 3D printing early and often in the product design and development process. 3D printing is used to validate the aesthetic, functionality, and aid in the early phases of product development. The technology compliments traditional methods of fabrication early on,” Emmar said.
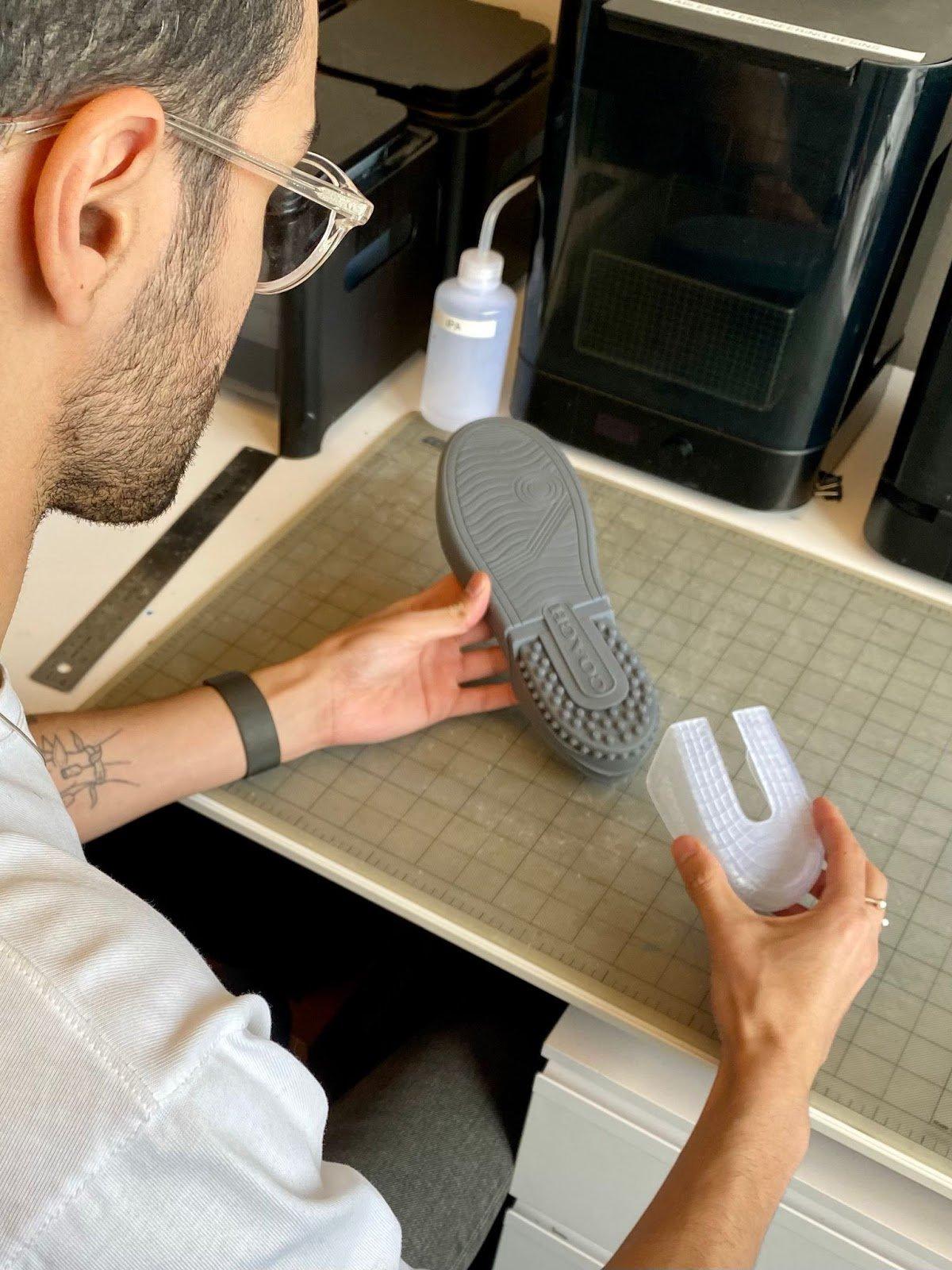
Now at Tapestry, 3D printing is an essential part of the business. The team uses Formlabs 3D printers daily. “We have the Form 2, we have the Form 3, and we have the Form 3L; hoping to get another Form 3L soon,” Emmar explained. “We're using them for prototyping early and often to validate the aesthetics and functionality to aid in the preliminary phases of the product development process.”
The 3D Team at Tapestry employs 3D printing workflows to communicate design intent as well as mechanical functionality to speed up time to market. They provide technical and global manufacturing guidance using digital product creation solutions to streamline the product development-to-commercialization process.
Printing Full-Size Outsoles: The Form 3L Changes the Game
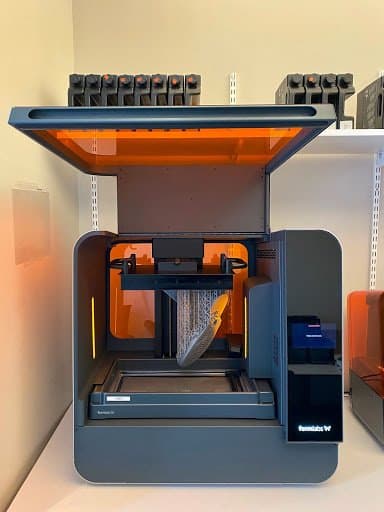
The Form 3L is an integral component of Tapestry’s daily operations
The Form 3L enabled Tapestry to print bigger parts. According to Emmar, the Form 3 didn’t have the capacity to print a full outsole, leaving the team to print the outsole in two parts. This negatively impacted dimensional accuracy.
“When you assemble prototypes in parts, you compromise the dimensional accuracy because then you have two separate parts being glued together,” Emmar said. “It usually was one to two millimeters off. And that's kind of critical for something like footwear; when you go half a size up, it makes a difference. So one to two millimeters could really make a difference in the prototype.”
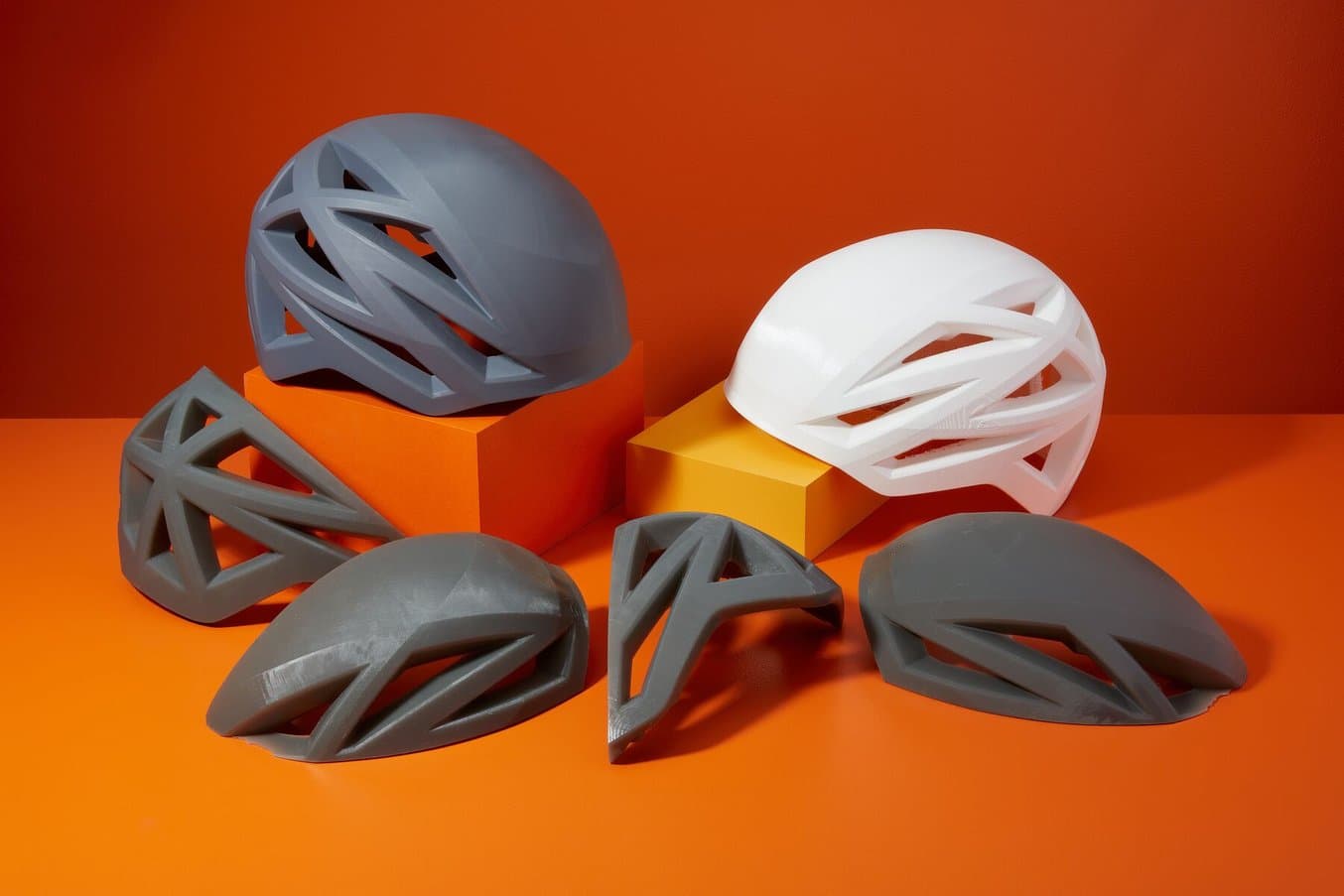
Why Large-Format Printing Matters
Want to learn more about the Form 3L and Form 3BL ecosystem, and how they compare to other methods of creating large prints?
In this free report, we look at how in-house large-format 3D printing with the Form 3L stacks up against other methods of production, chiefly outsourcing and using FDM printers. We also compare costs between methods, and review when it would be best to bring the Form 3L in-house.
Dimensional accuracy improved with the Form 3L. According to Emmar, the Form 3L enabled him to assess the dimensional accuracy within 0.1 of a millimeter. “It's much, much closer to the final product. The variance is not as large, if I print something and it's one to two millimeters bigger, it could be a completely different shoe size,” he said.
The Form 3L proved to be intuitive. “The Form 3L was quite familiar from the moment it was unboxed. I reserved it for myself for a couple weeks before opening up the capacity to my cross-functional partners but quickly learned that it really didn’t need that much time. It is very straightforward and familiar to operate. The surface quality, even at 200 microns, is incredibly smooth.” Emmar said.
Emmar took advantage of Formlabs’ large materials library, using Draft Resin for larger projects and those that require less detail. His team also uses Tough 1500 Resin to prototype functional parts when the assembly requires parts to be deform and deflect back to its original shape.
Whenever Formlabs releases a new material, Emmar acquires it for the team in an effort to expand their library of materials. To figure out the most suitable material, the team employs various research and development methodologies looking into the qualities and characteristics of new materials. “[The material we choose] depends on the use case of the prototype we are 3D printing and the needs of our internal customers. We do quite a bit of R&D on new material releases to evaluate whether it could potentially be a useful offering to our cross-functional partners. If it adds value to the process, we include it in our resin library and offer it based on the use case of the specific request,” Emmar said.
The Future of 3D Printing for Tapestry
Tapestry benefited greatly from 3D printing to meet the demands of the fast-paced fashion industry, enabling the team to turn around prototypes overnight, which is faster and more cost effective than relying on overseas factories. Tapestry designers also benefit from the flexibility and speed the technology offers by being able to make more informed decisions more quickly. Lastly, 3D printing is helping the company achieve their sustainability goals by keeping prototyping in-house. “It allows us to reduce the consumption of raw materials and decrease freight of samples from overseas. Making less and making better,” Emmar said.
With distributed prototyping capabilities abroad, 3D printing helps Tapestry facilitate communication between global offices. “3D printing enables our company to embrace distributed prototyping capabilities around the world. COVID-19 was the catalyst that accelerated the adoption of 3D printing. It highlighted the importance of agility and the ability to prototype locally and regionally. We are able to print the parts on demand when and where they are needed for evaluation,” Emmar said.
The Form 3L will play an integral role in Tapestry’s future. “The Form 3L has increased our capacity significantly and it also opened up new opportunities to prototype larger parts. Before the 3L, we had to cut large parts and assemble them afterwards. This compromise affected the dimensional accuracy of the prototype. We no longer need to compromise with the 3L when it comes to printing larger objects and we can continue to accommodate the growing prototyping needs of our internal customers,” Emmar said.
Tapestry is currently expanding their rapid prototyping capabilities and establishing new ways of working with new cross functional partners across all brands. With an ultimate goal to bring the benefits of 3D printing to all existing and future Tapestry brands across all categories, 3D printing is proving its value in fashion.