Medical Device Startup Achieves Fast, Under-Budget FDA Clearance With Help From Formlabs RAQA Team
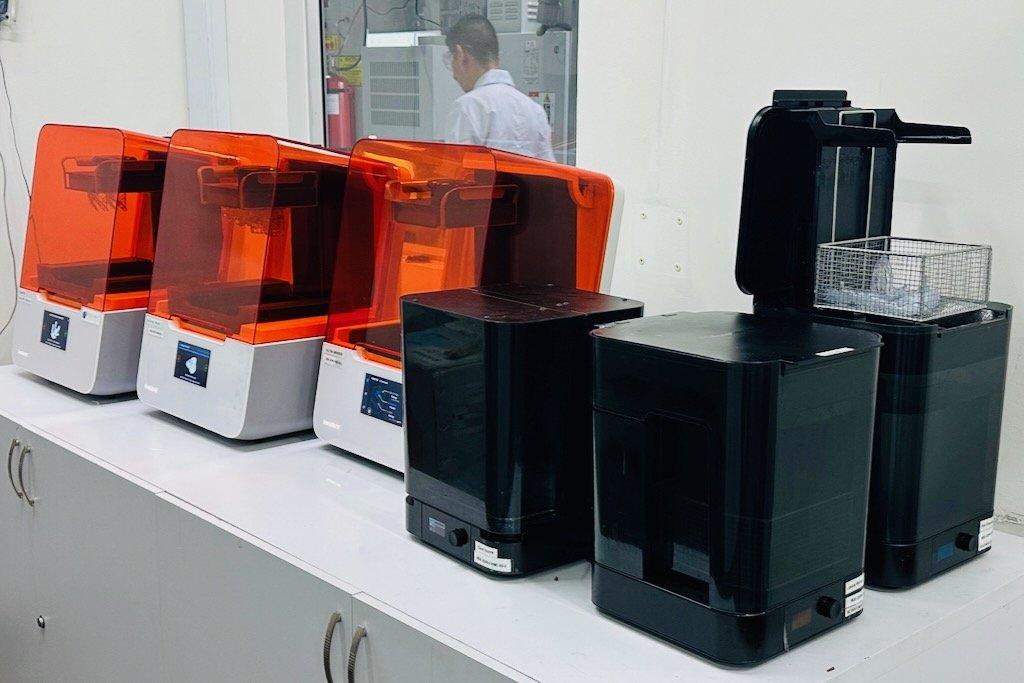
When TechFit Digital Surgery received FDA clearance for its novel digital orthognathic (jaw) surgery system in June 2023, they knew they’d reached a major milestone. As a small medical device company entering the US market, FDA clearance was critical to their success.
“FDA clearance allows us to have our product in the largest market in the world,” says Mauricio Toro, TechFit co-founder and CEO. “Now we can work with the top surgeons and the top teams in the most competitive and innovative medical industry.”
As a small spinout of a larger Latin American company, TechFit lacked the resources that large medtech manufacturers use to push new products through the US regulatory process. However, with the support of the Formlabs Regulatory Affairs and Quality Assurance (RAQA) team, TechFit secured FDA clearance ahead of schedule and at a cost hundreds of thousands of dollars lower than expected.
TechFit already leveraged the Form 3B+ stereolithography (SLA) 3D printer to produce patient-specific models and guides for clinicians in other markets, so it was the natural choice to develop their new product, the Digitally Integrated Surgical Reconstruction Platform (DISRP®), using the Formlabs platform. However, the process of receiving an FDA clearance also required the hardware, materials, and software expertise and capabilities. TechFit’s due date for regulatory approval was approaching fast — Toro had set an ambitious timeline of 12 months.
By partnering with the Formlabs RAQA team, that goal proved to be well within reach.
“We had committed to our potential investors that we would get a 510(k) within 12 months,” says Toro. “And we did it in six.” Toro walked us through the process TechFit and Formlabs’ RAQA team went through to fast-track clearance for their new Digitally Integrated Surgical Reconstruction Platform (DISRP®).
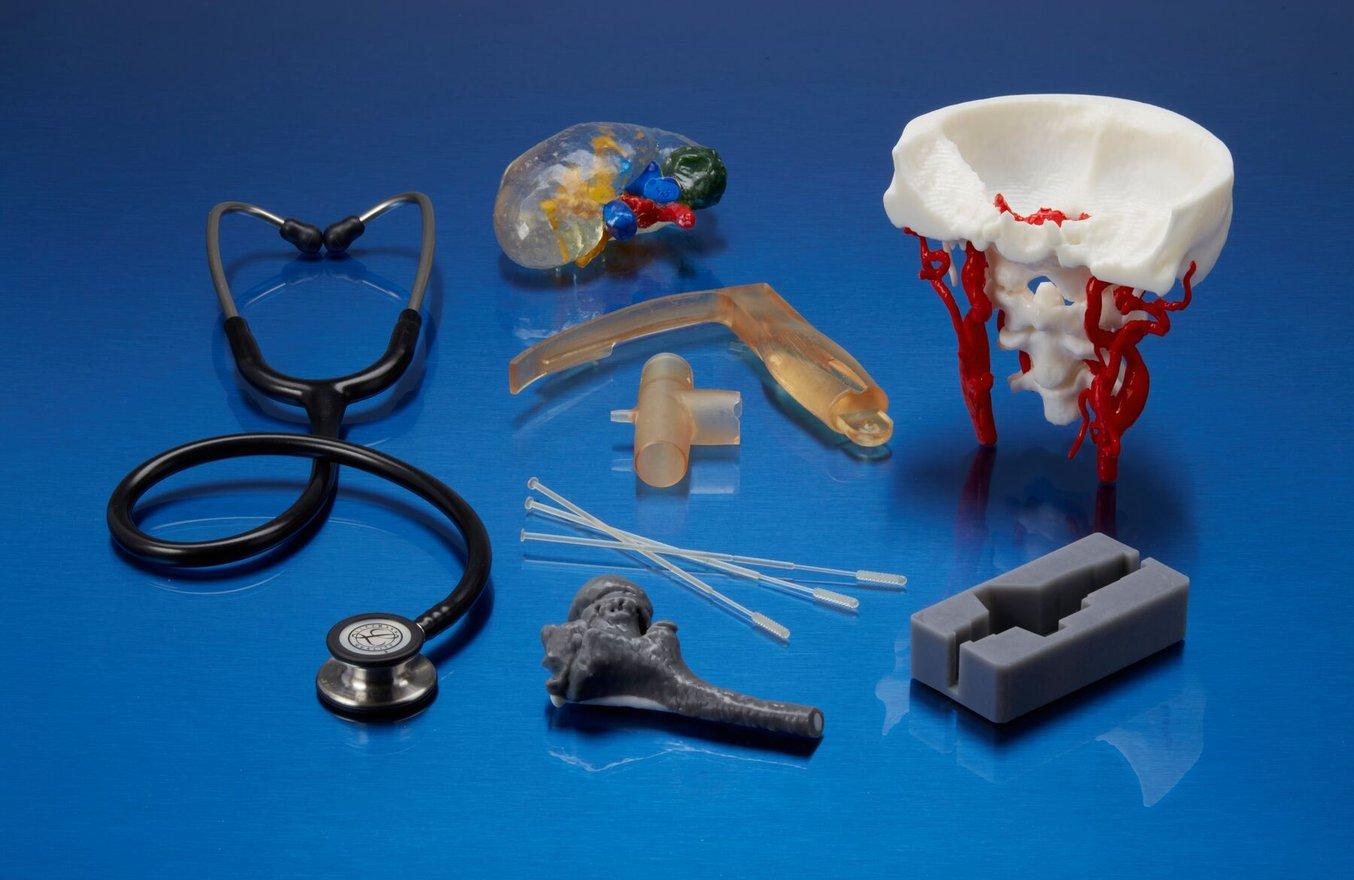
The Ultimate Guide to Quality Assurance and Regulatory Affairs in Medical 3D Printing
This document aims to guide users in the medical device industry through every stage of the product development process.
FDA Clearance: Make or Break for TechFit
DISRP® is TechFit’s first end-to-end digital surgery solution and its primary product. Without FDA clearance, TechFit could not market its solutions, and surgeons in the US would not be able to use DISRP®.
For TechFit, failure to obtain clearance would have prevented access to the largest market for their product and the loss of millions of dollars in funding, as potential investors required a clearance before closing equity financing. In other words, it would have threatened TechFit’s entire growth plan. To gain FDA clearance, TechFit had budgeted hundreds of thousands of dollars. Additionally, TechFit had told potential investors they expected to obtain an FDA clearance within one year.
With so much hanging in the balance, TechFit turned to the Formlabs RAQA team. Together with Formlabs, TechFit was able to receive FDA clearance in approximately six months at a fraction of the cost they’d anticipated.
A Formlabs FDA Master File, in addition to extensive documentation and the assistance of the Formlabs RAQA team, allowed TechFit to forgo performing chemical characterization tests for the BioMed Clear Resin material themselves. Toro estimates the savings from that alone at $70,000-$80,000. “And then we may have had to do it multiple times,” says Toro. “We’ve seen 510(k)s start with a budget of $150,000 and end up costing $500,000 because of the retesting and additional, unexpected testing needed.”
“The confidence [that the Master File gave us] made it a $150,000 510(k) as opposed to a $500,000 510(k). This wouldn’t be as good of a story without such a solid Master File to start with.”
Mauricio Toro, co-founder and CEO, TechFit
Formlabs manufactures biocompatible resins at its ISO 13485 certified, FDA-registered facility in Ohio, allowing complete control, traceability, and documentation of the resin manufacturing process. A wide range of ISO 10993, ISO 18562, and USP Class VI certifications, sterilization reports, chemical characterization reports, and other documentation are available for the BioMed resins.
Laura Buitrago, Technical Director at TechFit, agrees that comprehensive documentation was crucial to the efficiency of the process. “The chemical characterization was in the Master File,” she says. “It would have been so expensive, but we didn’t have to repeat it.”
Like many medical device startups, TechFit was only able to employ regulatory experts part-time at first. Buitrago began working as an advisor with TechFit in 2020 to help with regulatory affairs and processes. In 2021, when TechFit developed a strategy for approaching the US market, she assumed her full-time leadership role at TechFit.
“The FDA paid a lot of attention to 3D printing,” says Buitrago, who led the FDA clearance application process. In particular, she noted that the FDA closely reviewed the material properties and the printing process of the Form 3B+.
“Every time we received questions from the FDA that were related to the printing process, we would reach out to Formlabs. Every time, the answers and documentation provided by Formlabs enabled us to give the FDA exactly what they needed.”
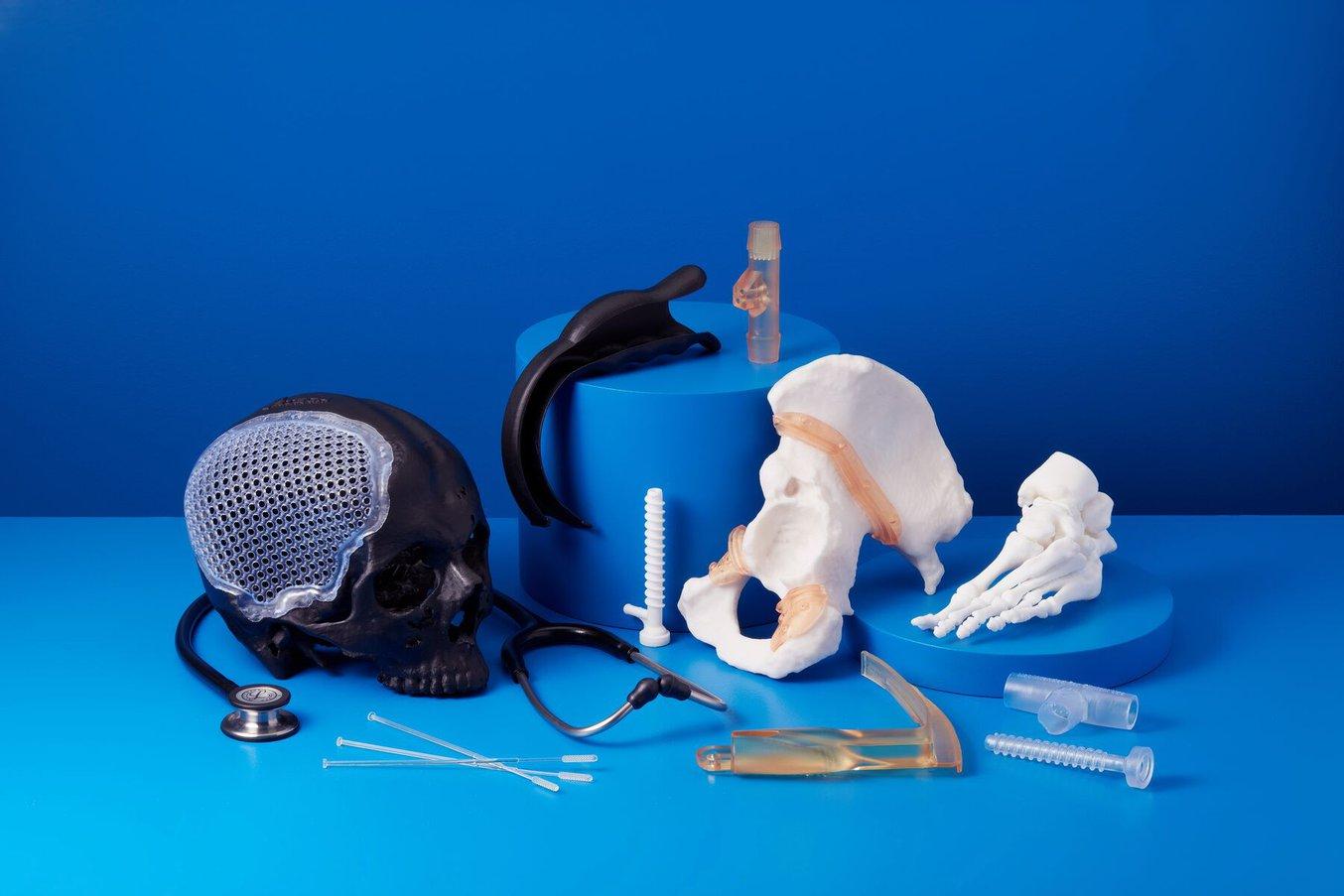
Biocompatibility: What Is It & Why You Need to Know About It
What is biocompatibility, and what does it mean for our users? Join our Biocompatibility QA Director for a walk-through of our biocompatible printers, resins, and applications.
Improving Surgery Outcomes Through Disruptive Technology
Mauricio Toro co-founded TechFit in 2018 to use advanced digital surgical planning and 3D printing technologies to improve surgery outcomes. Therefore, it was necessary for TechFit to select a quality 3D printer with the capability to print biocompatible materials accurately and consistently. Importantly, the team behind that 3D printer had to be ready to support TechFit as they applied for regulatory clearance.
“We realized quickly that we needed a technology that had a specific number of features,” says Toro. “It needed to be easy to use, repeatable, and accurate. It also needed to be part of an ecosystem that was portable and easy to set up in a distributed manufacturing setting. Finally, it needed to meet the standards for creating Class II medical devices in terms of accurate documentation, biocompatibility, and in terms of track record for use on similar parts. Most important for us was the ability to go to the FDA and not come back needing a test that would cost double our budget.”
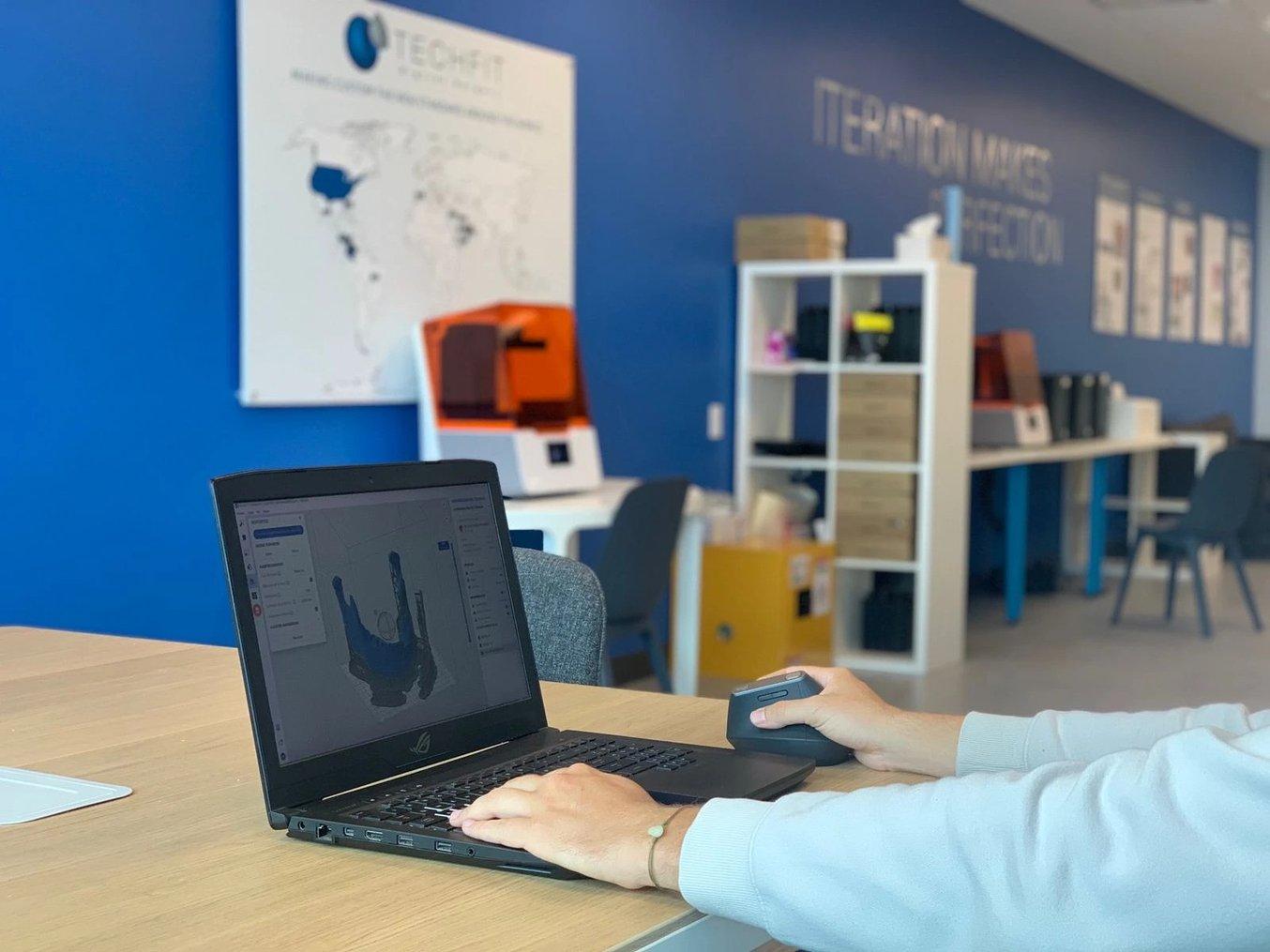
The TechFit DISRP® system is used for designs which are then printed on Form 3B+ SLA 3D printers.
DISRP® is TechFit’s first end-to-end solution. The cloud-based DISRP® system leverages advanced software and 3D printing techniques to improve the accuracy of surgeons performing orthognathic surgery. Patients see dramatically improved outcomes.
Says Toro, “It gives surgeons an ability beyond what their hands and eyes can achieve normally.”
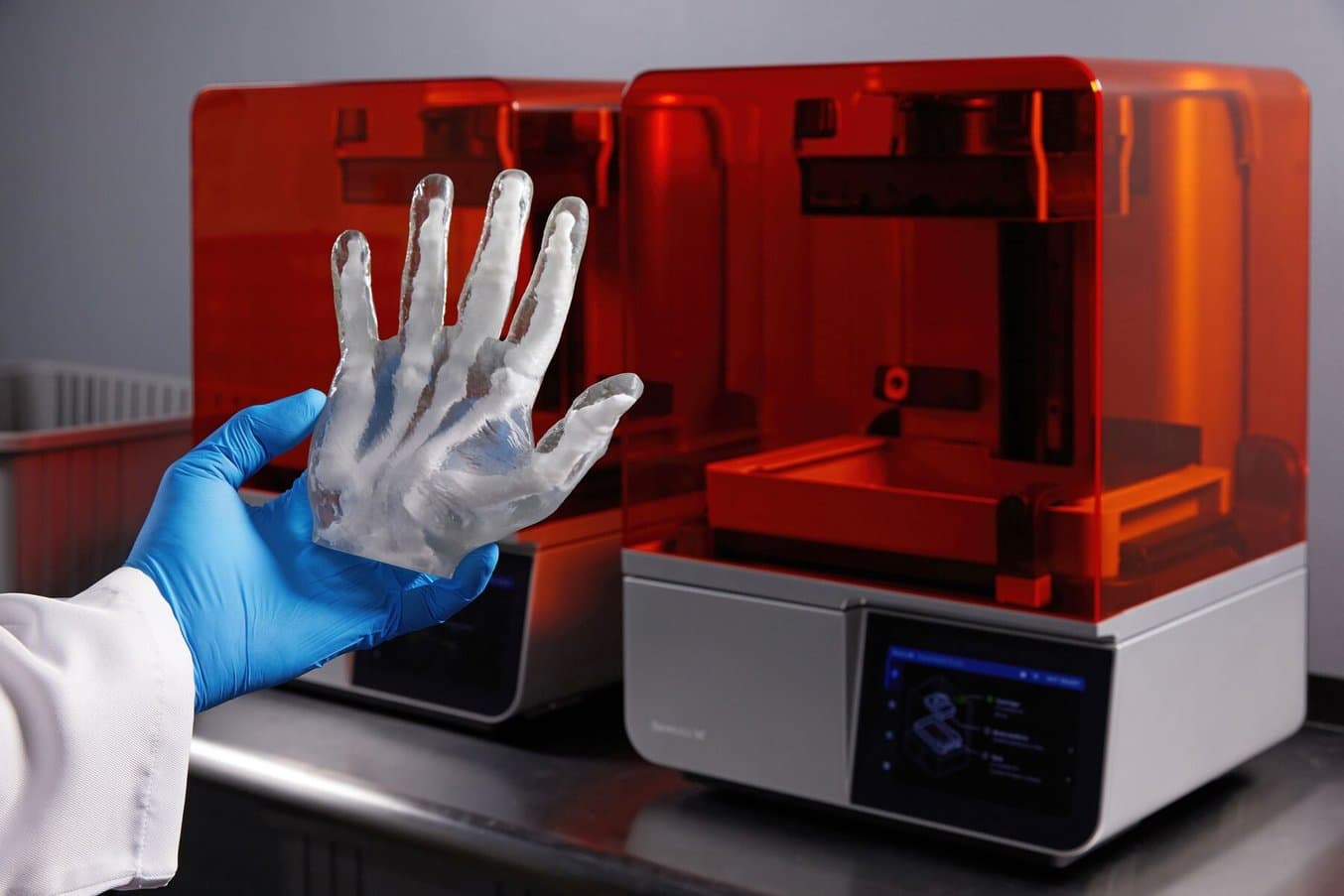
Formlabs Biocompatible Resins: A Comprehensive Guide To Choosing the Right Material
Formlabs currently offers more than 40 unique materials for stereolithography (SLA) 3D printing. This paper helps users compare and contrast our biocompatible offerings, and determine the best fit for their medical applications.
3D Printing Enables New Supply Chains and Techniques
In the DISRP® workflow, surgeons send patient 3D bone scans to TechFit. TechFit reviews the surgery plan and consults with the surgeon before processing the scan and creating an STL file of a custom guide. In most cases, TechFit prints the surgical guide on a Form 3B+ and ships it to the surgeon. In more time-sensitive cases, DISRP® leverages Formlabs remote printing capabilities to print the guide on a Form 3B+ that is housed within the point-of-care institution.
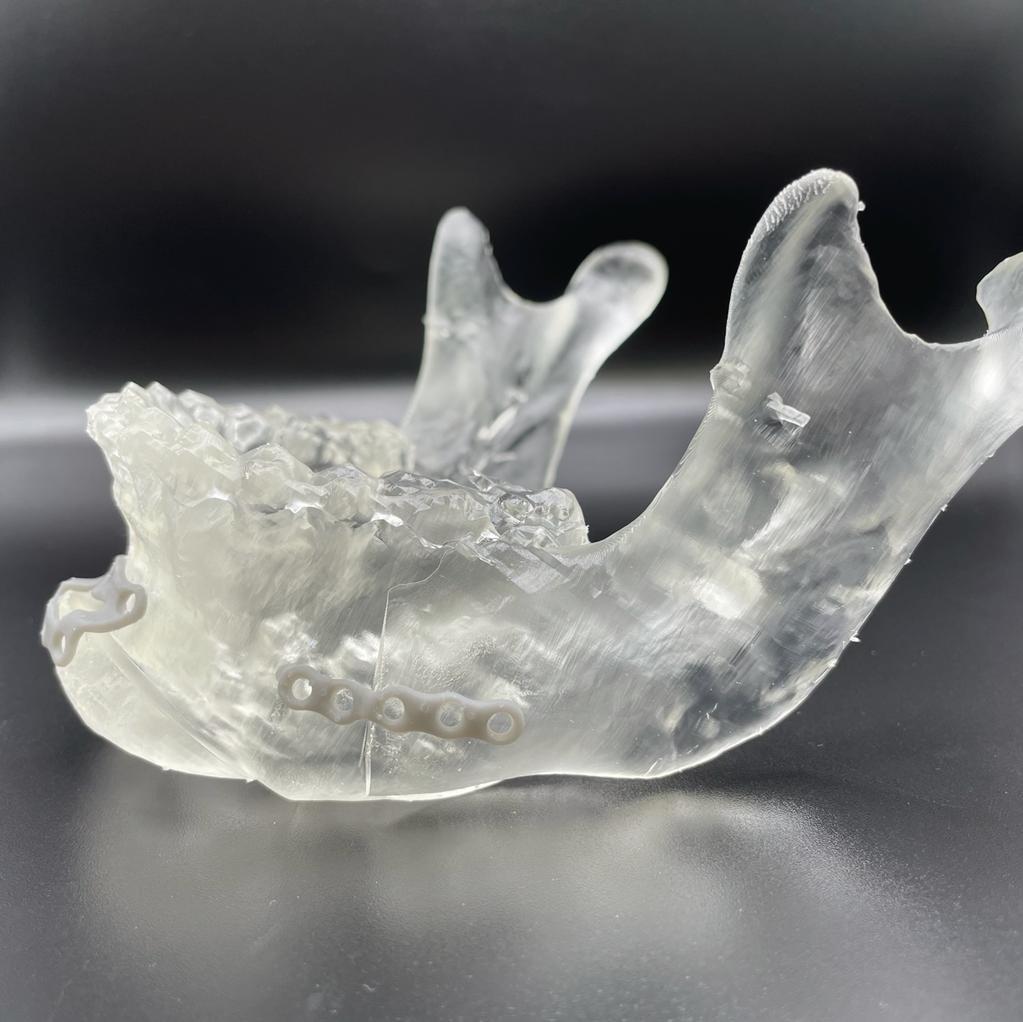
3D printed anatomical models are representations of the human body or specific body parts.
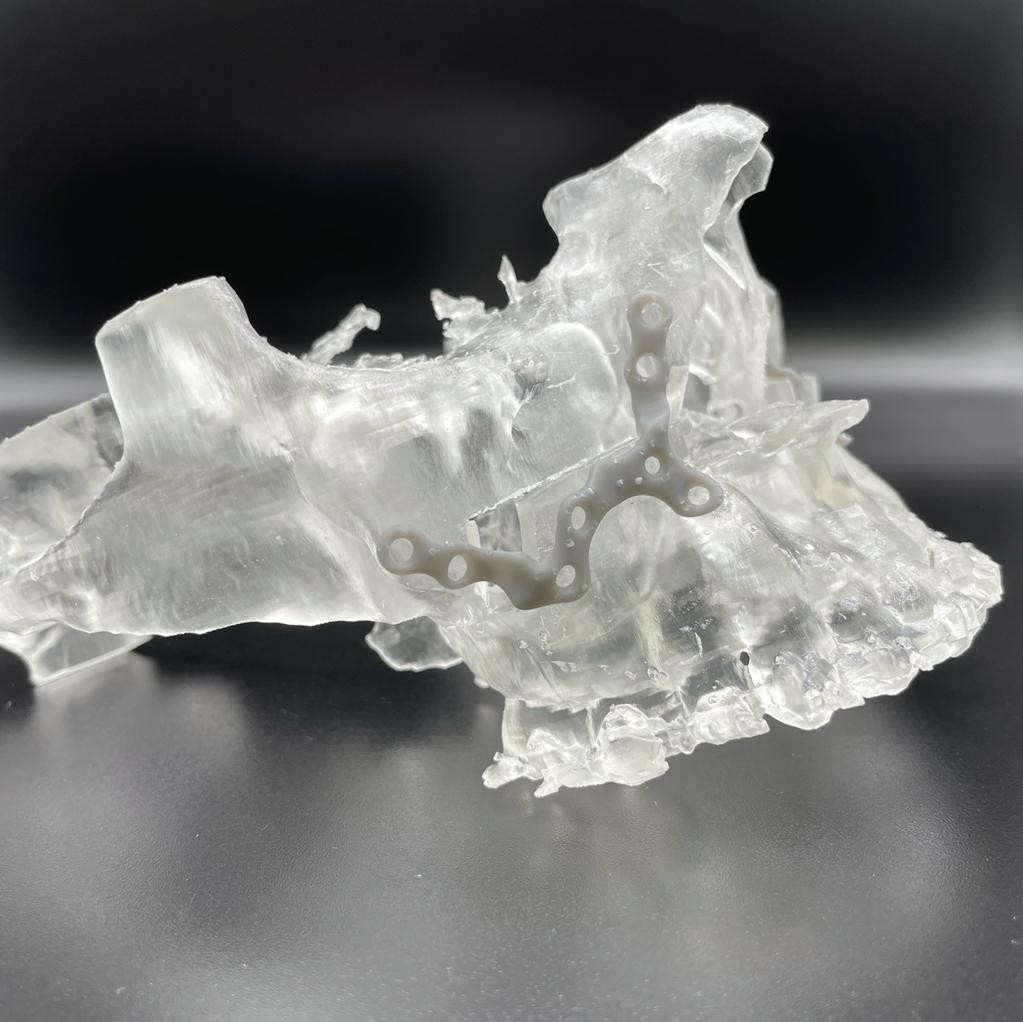
Models are used for educational, instructional, and medical purposes.
“Instead of waiting for the guides to be printed by us and shipped and put into a printing queue and taking four or five days, you can have guides the same day if you have the printer in your office,” explains Toro.
Traditionally, orthognathic surgeons have used metal plates that come in standard sizes, like shoes, for affixing bones. Using custom guides for orthognathic surgery makes a big difference in patient outcomes. Toro references a paper published by the Orthopaedic Research Society International Section of Fracture Repair. The paper showed that without a custom guide, surgeons were between 78 and 98 percent accurate. With a guide, says Toro, “Everything we measured was over 99 percent accurate.”
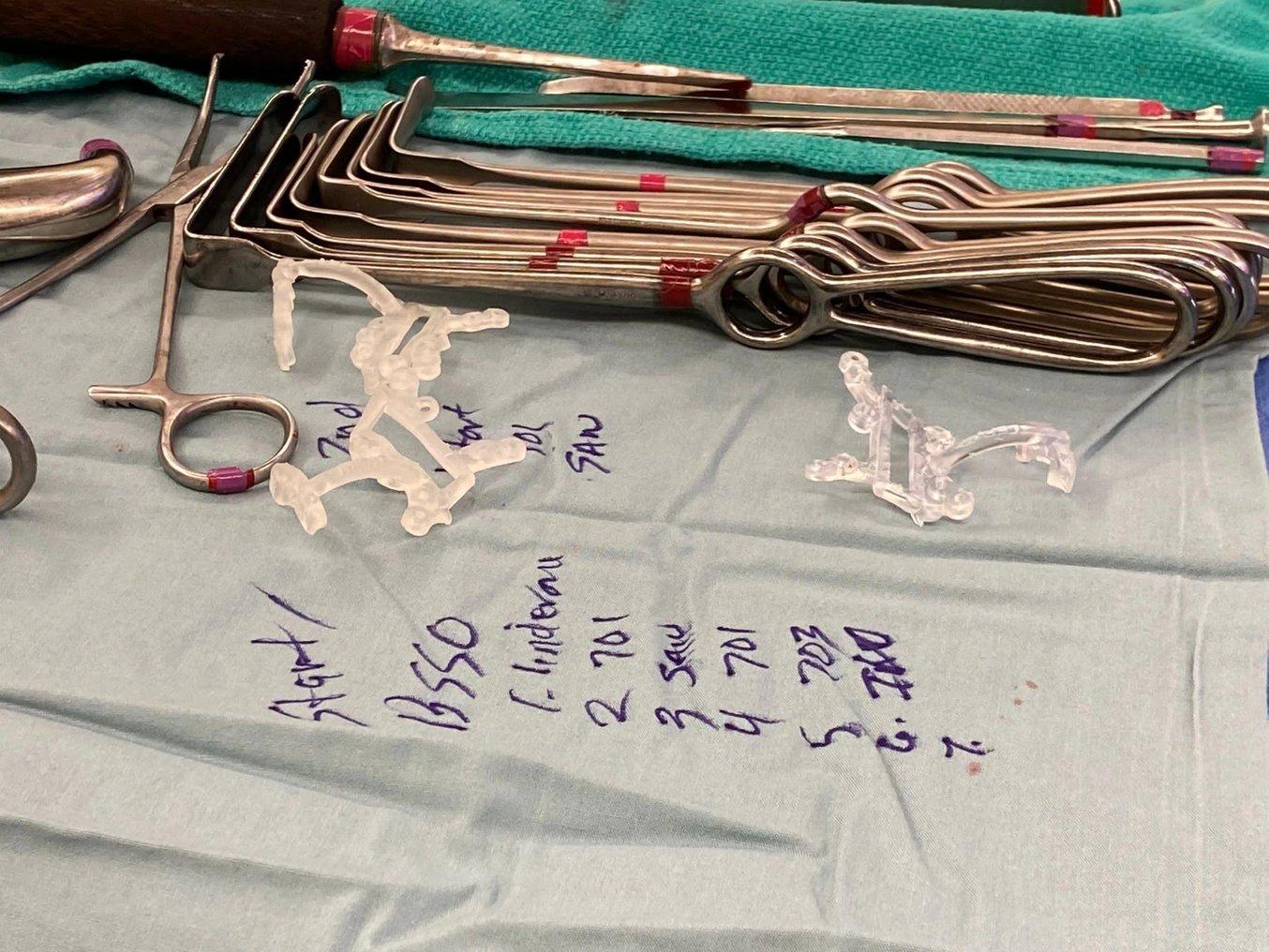
3D printed surgical cutting guides printed in BioMed Clear Resin and Clear Resin.
TechFit customers have been able to adapt quickly to the new digital workflow enabled by DISRP®. The assurance provided by extensive testing plays a major role. “Doctors are very happy with the end product. 3D printing in healthcare has a lot of implications and a lot can go wrong with bad technology choices and procedures,” says Toro. “To know all the testing that has been done gives doctors a lot of confidence.”
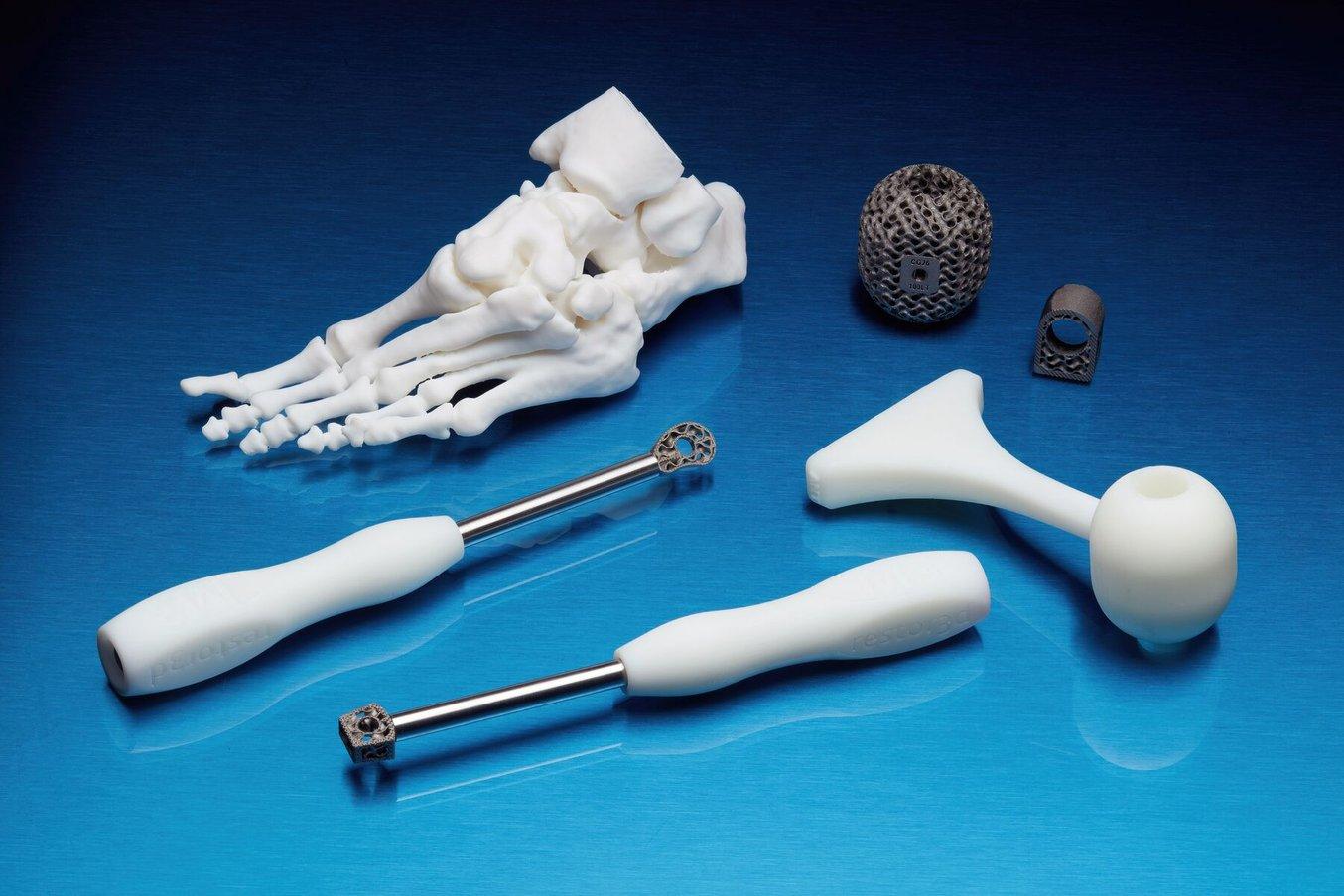
Proven Regulatory Strategies & Quality Recommendations to Use for Additive Manufacturing
Learn how top medical device companies are utilizing 3D printing today, including proven regulatory strategies and quality recommendations.
As the need for patient-matched surgical tools continues to increase, TechFit has seen rising demand. “In the past six quarters, we’ve been growing at 23 percent quarter over quarter,” reports Toro. “We are now having distribution conversations with people who wouldn't have picked up the phone before we were FDA cleared.”
FDA clearance for their DISRP® system enables access to TechFit’s most important market. In the United States, there are 2.3 million musculoskeletal reconstructive surgeries performed annually. In addition to cranial maxillofacial surgery — the type of surgery DISRP® is FDA-cleared to support — Toro believes 3D planning and 3D printing can improve outcomes for orthopedic and thoracic surgeries.
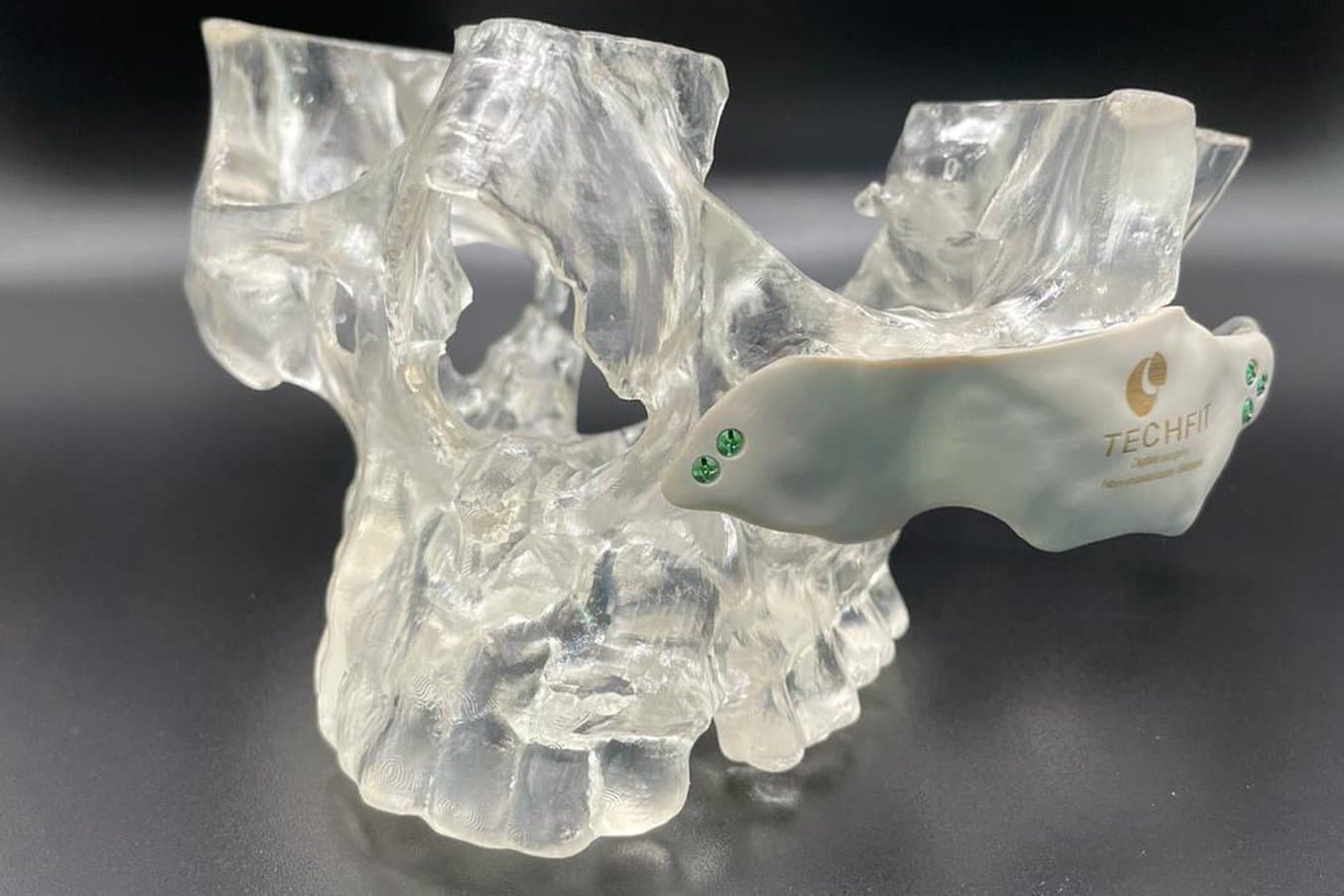
Anatomical models can be used to fit plates for surgery and practice surgeries prior to entering the OR.
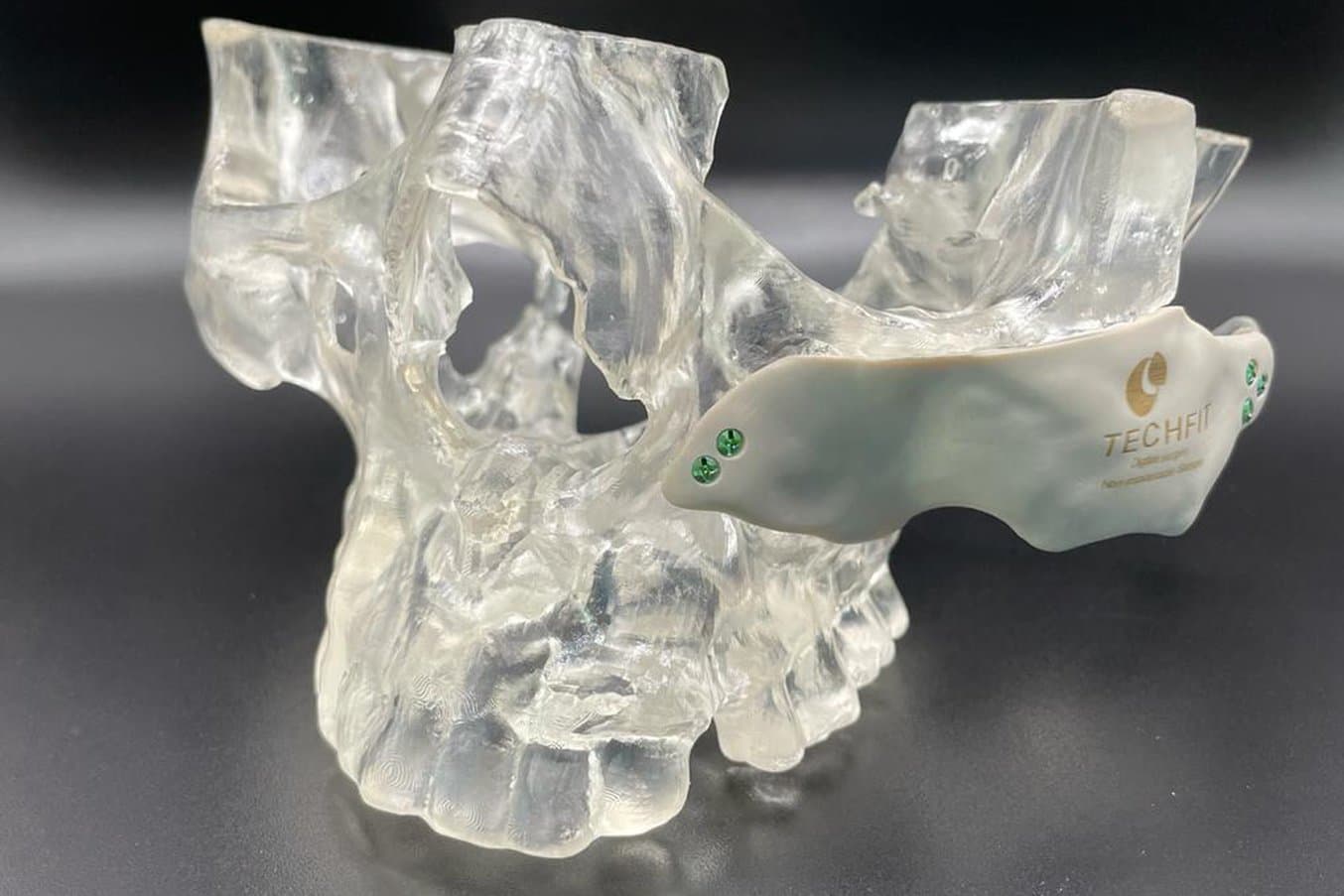
An example of an anatomical model for surgery preparation.
“We are convinced that 100 percent of musculoskeletal surgeries will eventually benefit from 3D printing and 3D planning in one form or another,” he says. Toro believes that the Formlabs Form 3B+ is an ideal option for startup companies like TechFit who seek to help surgeons improve outcomes using digital planning and customized 3D printed guides.
“We became Formlabs champions because we started interacting with the regulatory team and found a printer that was incredibly capable for the budget. And then when we got into the testing and the documentation, we found it to be very complete.”
Mauricio Toro, co-founder and CEO, TechFit
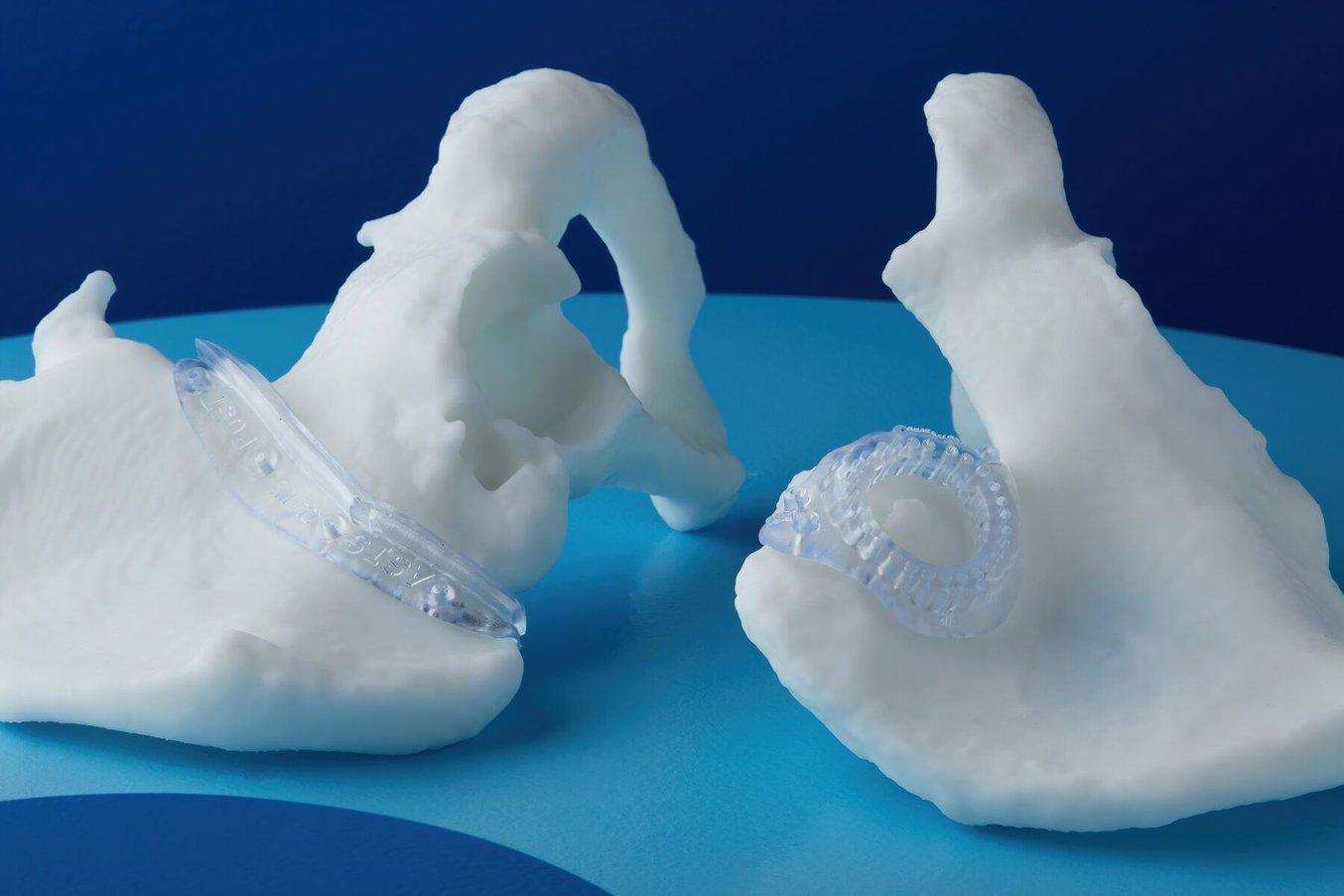
BioMed Durable Resin: Announcing Formlabs Most Impact-Resistant Material
Walk through the key benefits and applications of BioMed Durable Resin with Mauricio Toro, CEO and Co-Founder of TechFit. This biocompatible material for medical devices can withstand impact, rough handling, and pressure.
What is Formlabs RAQA?
3D printing in healthcare, already a multibillion-dollar industry, is forecast to grow at a rate of nearly 20% over the next decade. Much of the innovation in healthcare 3D printing will require devices that are prototyped, cleared, and commercialized using a single additive manufacturing platform, similar to the journey taken by TechFit.
In order to support companies who need help with quality or regulatory processes for 3D printing in healthcare, Formlabs is offering complimentary consultations with its RAQA leadership.
With 30,000 3D printers in healthcare settings and over 150 million end-use prints used clinically, Formlabs is the world leader in stereolithography (SLA) printing for healthcare. The RAQA team at Formlabs utilizes over 35 years of experience, including writing dozens of successful 510(k)s, to help customers overcome some of their most critical business challenges. The team is also experienced with global requirements, including EU MDR, and received the first Emergency Use Authorization (EUA) issued to a 3D printing company for devices produced during the pandemic.
Formlabs owns and operates its ISO13485-certified, FDA-registered, US-based manufacturing facility that has produced over 1 million liters of resin. The RAQA team manages a comprehensive documentation library covering all 45+ Formlabs proprietary materials as well as the 3D printing hardware and processes used to make medical devices and other 3D printed parts for healthcare. Additionally, the RAQA team can provide FDA Master Files, ISO and USP testing, sterilization testing, equivalency statements, accuracy reports, and more documentation to help startups and larger medtech OEMs bring revolutionary new medical technology to market.
Like TechFit, many small companies with innovative ideas for the medical industry lack the means to effectively navigate the regulatory process. With help from the Formlabs RAQA team, startups can access tools that clarify, accelerate, and reduce the cost of the regulatory process. For Mauricio Toro and TechFit, that support made all the difference.
“Choosing a printing platform for a 510(k) is a multi-hundred thousand dollar decision. Knowing that Formlabs has done that gives you the confidence to commit.”
Mauricio Toro, co-founder and CEO, TechFit
Do you have a revolutionary product or idea and need help navigating the quality or regulatory environment? Reach out to the Formlabs RAQA team today.