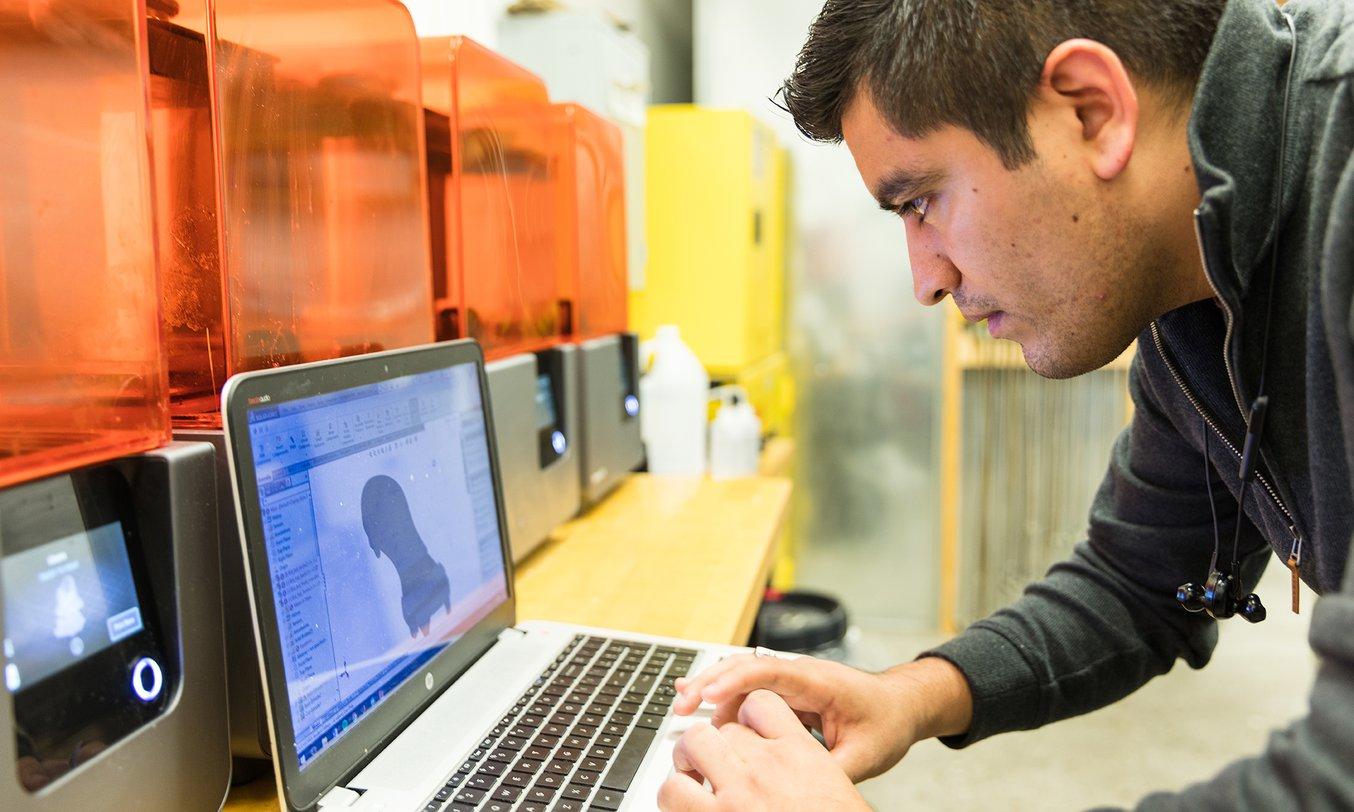
Richard Huizar has always loved building things. That’s why he chose to major in mechanical engineering, and also why he’d like to pursue a career in product design.
Design Studio: Objects and Interaction, a class at Massachusetts Institute of Technology (MIT), is helping Huizar gain the skills he needs to achieve that goal. The class mixes classic principles of design with advanced prototyping technologies to inspire students to think beyond their discipline.
Training Future Designers
Part of MIT’s new minor in design, Design Objects and Interaction encourages undergraduates to think more broadly about design. The curriculum incorporates modern technology and tools that not only help students realize their vision, but also allow and inspire students to create designs that were previously impossible.
Undergraduate MIT students used advanced prototyping technology, including a row of Form 2 stereolithography 3D printers, to test and build their designs. Learn more about 3D printing applications in education.
“You have to think about how to design 30 years from now, not just today,” said Marcelo Coelho, who co-teaches the class with Jessica Rosenkrantz, co-founder and creative director at Nervous System. “We’re training future designers.”
In Design Objects and Interaction, a class of 25 students used:
- 4 Form 2 3D printers
- 2 Finish Kits
- 4 L of Clear Resin
- 2 L of Flexible Resin
Technology-Inspired Design Thinking
Covering the fundamental skills required from modern designers, students were briefed to create a textile and wearable that could only be accomplished through 3D printing.
Inspired by how cells align with each other, MIT junior Lucia Liu, a mechanical engineering major, coded an algorithm to produce a cell-like textile pattern.

“3D printing helped me think of design in a different way,” Liu said. “I was really inspired by the ability of the 3D printers to create organic shapes just as easily as geometric shapes. My goal was to create a 3D printed wearable that explored how different cell shapes perform different functions.”
Liu used the Form 2 to iterate prototypes of the small hinge mechanism in her textile, made to be as small as possible given the minimum tolerances and clearances of the Form 2. She printed the full textile as a single, pre-assembled print.


Meanwhile, Huizar’s project was inspired by his love of soccer. His goal was to design customizable cleats, with bottom pieces that could be swapped out based on a player’s style and techniques.
When he first started working in CAD, Huizar wasn’t sure how well his design would translate to a final product.
“When you’re looking at the computer, you can’t tell how the design will fit a foot,” Huizar said. “Once printed, I could see and adjust the sizing, the stiffness, and thickness. There is no way to do that CAD. You need something physical.”
Coelho explained that one of the biggest challenges in the class was this process—creating a design in CAD that will become a functional physical object.
“Many students will model a design with no grasp of what it will be in reality; how it will bend, how pieces will fit together,” Coelho said. “3D printing the physical design helps students work through pragmatic solutions. It’s a reality check.”

Rapid Prototyping in the Classroom
Both Huizar and Liu had access to 3D printers in previous classes, but had not been exposed to desktop stereolithography (SLA) 3D printers, or had the chance to work so hands-on with the technology.
Liu had previously worked through a graduate student, who acted as a middleman to operate the 3D printer and print her designs.
“When I was working through someone else, the technology had been a little intimidating,” Liu said. “Now that I know and have used the process, I find it much easier to use.”

Huizar used Formlabs’ Clear Resin to print most of the bottom of his cleats and Flexible to print the pieces of the shoes that needed give. He designed the shoe to have three layers: A top layer that stays solid, and would be attached to whatever soft material the body of the shoe would be made of; a second layer of parts that move (the joints); and a bottom that interlocks and sandwiches the flexible pieces together, so that it all becomes one piece.

Request a free sample part of any of Formlabs’ resins.
“Because of the Form 2’s accuracy, I was able to create pieces made to fit perfectly together,” Huizar said. “I knew if I were to take this and decide to machine it or injection mold it, the accuracies would be very comparative to the 3D prints.”

Managing 3D Printer Use with Dashboard
Easy-to-manage machines are essential to successfully integrating advanced technology in classrooms and student labs. Formlabs’ Dashboard is designed to help users and administrators manage multiple printers and consumables.
Formlabs' Dashboard is a cloud-based tool that helps users maximize machine use. Dashboard tracks the printing process, sends a notification when prints are finished, organizes a team’s print history, and monitors materials usage so that it’s clear when it’s time to restock.
“Having the Dashboard is super useful,” Coelho said. “Students can see when machines are running, what’s going on, when they can be the next one to go in and print. It makes the whole process of managing the machines easier.”

Preparing for the Future
Huizar and Liu agree that access to 3D printing and other advanced technologies will help them define and find success in their career paths.
“We should be not scared of technology that may be very useful for our future paths or careers,” Liu said. “Having more opportunities to explore new technologies has opened the door to fields and applications I hadn’t thought of before.”
“Universities should prepare students for the future—not just for what current technologies allow, but what they open the doors to,” Huzier said.
“Someone can get a mechanical engineering degree and know about current and past fabrication methods and make those slightly better, which is definitely a great thing, but the only way to make bigger changes is disrupting that. Find a new fabrication method, a new way do this or that. The only way you can get a sense of or start thinking about that is if those technologies are available to you.”
Webinar: Leveraging 3D Printing in Education
Interested in learning more about how 3D printing is changing education, and how you can get started? Watch our webinar recording to learn how educators at universities and colleges around the country benefit from access to 3D printing technology.

If you're curious about 3D printing and the possibilities of a Formlabs 3D printer, request a free sample part.