
Les lunettes, qu'il s'agisse de lunettes de lecture, de lunettes de protection ou de lunettes de soleil adoptées par les célébrités, sont le rare exemple d'un produit qui peut être personnalisé à l'infini, tant en termes de style que de fonctionnalité. Les fabricants de lunettes peuvent modifier chaque élément, qu'il s'agisse du matériau ou de différences de l'ordre du micron dans l'épaisseur des lentilles.
À mesure que la résolution, la précision, la polyvalence des matériaux et les processus de finition de l'impression 3D se perfectionnent, cette technologie devient une méthode rentable pour concevoir et fabriquer des lunettes.
Dans ce guide, nous aborderons les considérations relatives à la conception et aux matériaux, des études de cas de fabricants qui exploitent le potentiel de l'impression 3D dans ce secteur, et partagerons des calculs de retour sur investissement pour vous aider à monter un dossier commercial.
Introduction : L'arrivée des lunettes imprimées en 3D
L'impression 3D de lunettes a considérablement augmenté au cours des cinq dernières années : les petites entreprises comme les grandes marques tirent parti de la liberté de conception, de la capacité de production en petites séries et des avantages en termes de développement durable qu'offre l'impression 3D.
Qu'il s'agisse de lunettes correctrices, de protection ou de mode, l'impression 3D s'est imposée dans l'industrie de la lunetterie et a modifié la façon dont les concepteurs et les fabricants envisagent la production.
L'un des principaux avantages de l'impression 3D est qu'elle réduit les étapes d'assemblage au cours de la fabrication, et qu'elle permet de fabriquer des produits uniformes et de haute qualité. Certains fabricants de lunettes nous ont avoué que la production de montures en acétate peut nécessiter jusqu'à soixante étapes individuelles.
L'impression 3D permet de réduire considérablement la complexité de l'assemblage et la main-d'œuvre associée, grâce au processus de base suivant :
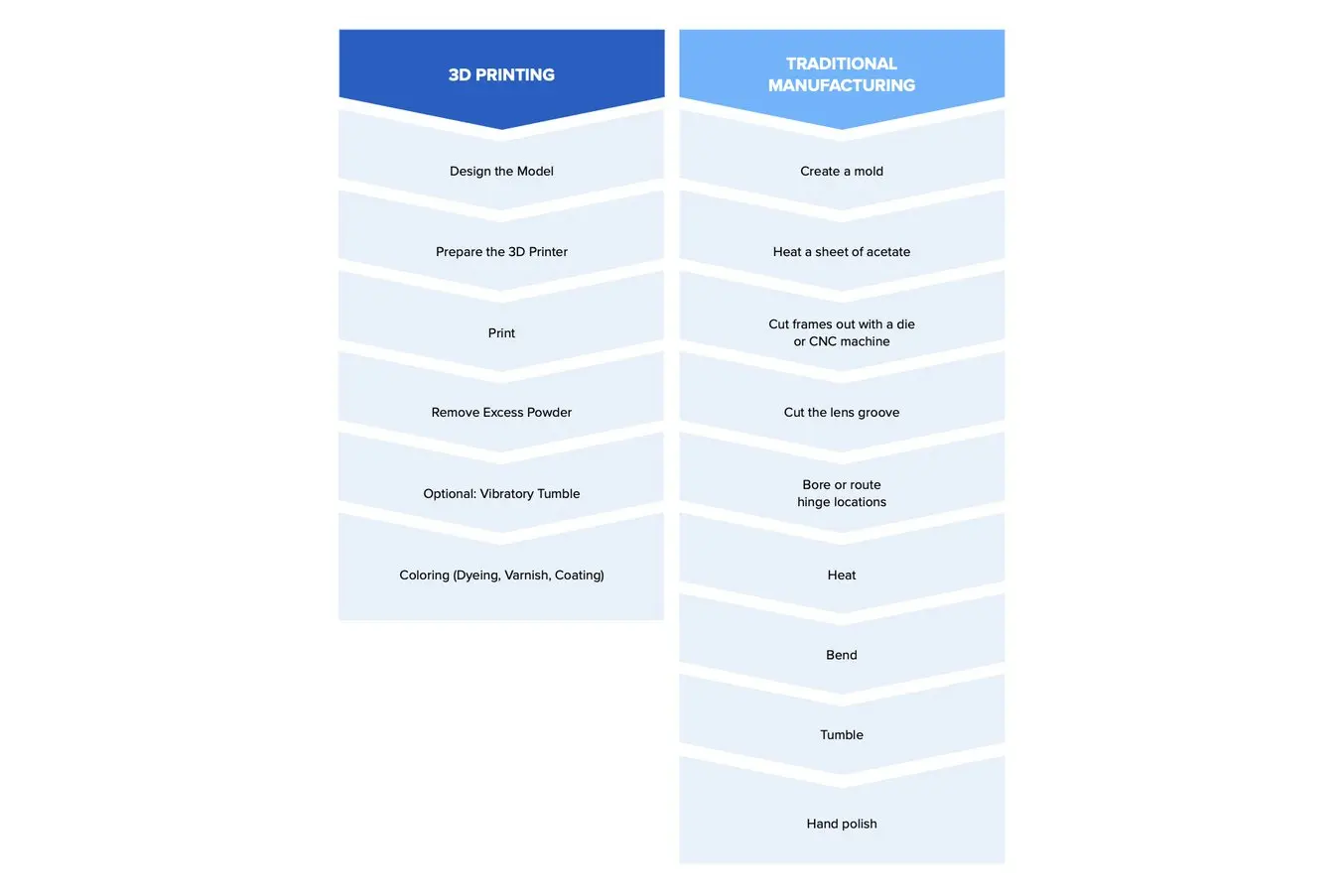
Le frittage sélectif par laser est la technologie de fabrication additive la plus courante pour les applications industrielles. Les ingénieurs et les fabricants de différents secteurs lui font confiance pour sa capacité à produire des pièces solides et fonctionnelles.
Les imprimantes 3D SLS utilisent un laser de forte puissance pour fritter de petites particules de poudre de polymère. La poudre non frittée supporte la pièce pendant l’opération, ce qui évite d’avoir à lui ajouter des structures de support. En cela, le procédé SLS est idéal pour des pièces à géométrie complexe, présentant des formes internes ou en creux, des contre-dépouilles ou des parois minces. Les pièces fabriquées par SLS présentent d’excellentes caractéristiques mécaniques, et leur résistance s’apparente à celle de pièces moulées par injection, ce qui rend ce processus idéal pour la production de lunettes.
Poursuivez votre lecture pour découvrir comment l'impression 3D peut accélérer la mise sur le marché, réduire la main-d'œuvre et éliminer le besoin de quantités minimales de commande pour les montures et les branches de lunettes.
Pourquoi imprimer des lunettes en 3D ?
Durabilité de la fabrication
La production actuelle de montures de lunettes est principalement réalisée par moulage par injection, découpage à l'emporte-pièce ou fraisage CNC de précision, ce qui oblige les fabricants à investir dans des moules et des équipements coûteux. L'externalisation de la production de moules ou de pièces usinées peut prendre des semaines et coûter des milliers de dollars. Pour justifier cette dépense, le fabricant doit s'engager dans la production de quantités très importantes
de produits, ce qui peut entraîner une baisse des bénéfices et des volumes importants de stocks invendables.
Ce système n'est pas viable, tant sur le plan financier qu'environnemental. L'impression 3D permet aux entreprises de prendre le contrôle de leur fabrication sans investir dans des moules, ce qui réduit considérablement les risques liés au lancement d'une nouvelle ligne de produits. L'impression 3D en interne permet aux fabricants de s'affranchir des quantités minimales de commande et des conceptions moins prisées en produisant de petits lots à la demande sans coûts de moulage initiaux.
Aujourd'hui, la plupart des lunettes sont créées par moulage par injection ou par un processus soustractif dans lequel l'acétate est découpé pour obtenir la forme souhaitée. Le processus de découpe consiste à prendre de grandes feuilles d'acétate et à découper la forme du cadre, ce qui entraîne le gaspillage de tout le matériau non utilisé.

Une monture traditionnelle en acétate créée par un procédé de découpe. Source: Visio Optical
L'impression 3D est quant à elle un processus additif, ce qui signifie que les pièces sont créées couche par couche à partir d'un matériau de base. Avec l'écosystème SLS de Formlabs, les poudres inutilisées peuvent être recyclées pour être réutilisées lors de l'impression suivante, ce qui permet de ne pas gaspiller de matériau.

Montures imprimées en 3D avec Nylon 11 Powder, extraites du cake de poudre dans le Fuse Sift.
Le faible encombrement et le prix abordable de l'écosystème SLS de la série Fuse permettent aux fabricants d'acheter plusieurs machines pour plusieurs sites, répartissant ainsi la capacité de production dans des régions physiquement proches des consommateurs. Cela a également pour effet de réduire la dépendance à l'égard des livraisons provenant de l'étranger, qui peuvent être ralenties par des problèmes au niveau de la chaîne d'approvisionnement mondiale. La distribution de la production permet également de réduire l'impact environnemental négatif associé à la surproduction et à l'expédition.
Liberté de conception
Contrairement à d'autres technologies d'impression 3D de polymères, les pièces produites par l'impression 3D SLS ne nécessitent pas de structures de support, car elles sont soutenues par le lit de poudre. Contrairement aux processus de moulage ou de découpe traditionnels, l'impression 3D ne nécessite pas de structures de support, de carottes ou de restrictions sur les angles de dépouille et les contre-dépouilles. Elle offre ainsi une liberté de conception presque illimitée, permettant des conceptions avancées qui étaient auparavant trop coûteuses, voire impossibles à produire.
Les restrictions de fabrication n'empêchent ainsi plus les fabricants de créer les modèles les plus fonctionnels, les mieux adaptés et les plus à la mode. Les lunettes imprimées en 3D permettent de réagir plus rapidement que jamais aux tendances de la consommation, ce qui permet aux marques de conquérir des marchés nouveaux et émergents.

Une branche complexe imprimée en 3D qu'il serait difficile, voire impossible, de produire efficacement avec des outils traditionnels.
Adaptation et personnalisation
De même, en l'absence d'exigences en matière d'outillage ou de quantités minimales de commande, la personnalisation des produits est enfin à portée de main, ce qui permet de choisir des tailles et des conceptions personnalisées pour offrir aux clients un produit totalement unique parfaitement adapté à leurs besoins.
L'impression 3D est déjà utilisée pour personnaliser des produits dans des domaines allant des orthèses aux figurines d'action en passant par l'audiologie. Elle rencontre généralement un énorme succès lorsque les consommateurs ont le sentiment que le produit est réellement amélioré pour être plus fonctionnel, ou plus attrayant sur le plan personnel. Compte tenu de la grande variété d'âges, d'ethnies et de caractéristiques faciales dans le monde d'aujourd'hui, les concepteurs de produits ne peuvent plus se conformer à une « taille unique », ce qui donne tout son sens à la personnalisation.
« Avec l'impression 3D, je peux tout faire immédiatement. Si vous connaissez la conception CAO, vous pouvez facilement apporter des ajustements au modèle 3D, le téléverser dans le logiciel et l'imprimer directement. En revanche, si je devais fraiser mes pièces, j'aurais toujours besoin de développer des outils individuels et coûteux pour maintenir les éléments dans la machine. »
Marcus Marienfeld, créateur et fabricant de lunettes
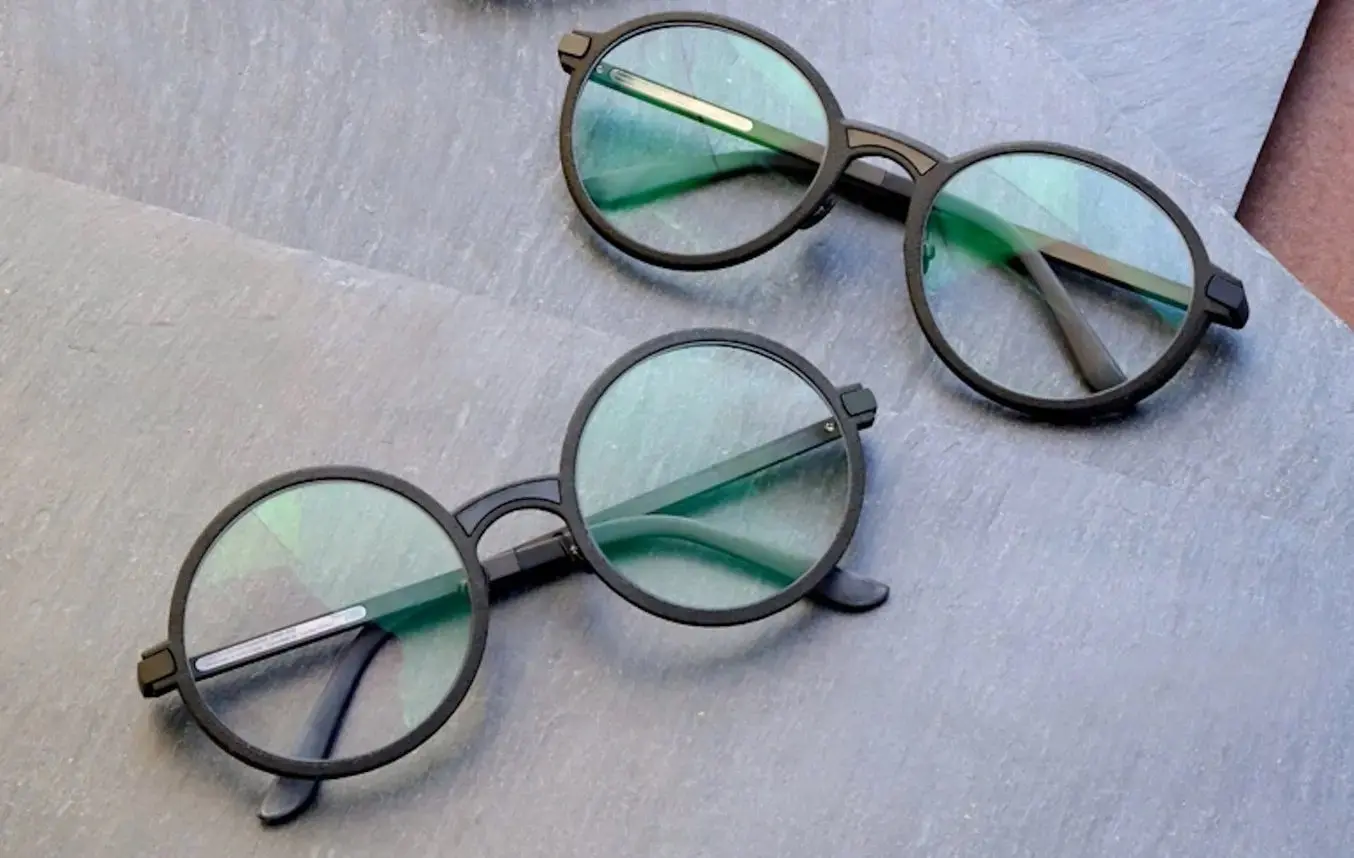
Le fabricant suisse de lunettes Marcus Marienfeld utilise l'imprimante 3D SLS Fuse 1+ 30W pour produire des lunettes imprimées en 3D à usage final, et notamment des produits personnalisés.
Comment fabriquer des lunettes imprimées en 3D
Conception
La création de lunettes finales grâce à l'impression 3D présente des avantages et des défis uniques. Dans cette section, nous aborderons la texture des pièces, les options de charnière, la conception de formes impossibles à mouler et la personnalisation.

Imprimées en 3D avec Nylon 12 Powder, ces montures sont teintes au bain-marie en noir et en marron.
Texture
Les pièces fabriquées de manière additive sont formées couche par couche, ce qui signifie que certaines surfaces peuvent présenter des lignes de couche visibles. Les lignes de couche peuvent être améliorées en optimisant l'orientation et la conception de la pièce, ainsi qu'en la post-traitant pour lisser la surface. L'ajout d'une texture en relief ou en creux à la surface des montures et des branches est une technique bien connue pour masquer les lignes de couche sur les produits finaux imprimés en 3D.
Formlabs recommande un embossage d'une hauteur minimale de 0,35 mm et un débossage d'une profondeur minimale de 0,15 mm, afin de garantir un masquage suffisant de toutes les lignes de la couche. Enfin, les lignes des couches partielles peuvent être utilisées pour augmenter l'adhérence et la friction, ce qui empêche les lunettes de glisser sur le visage.
Options de charnières
Les charnières de lunettes imprimées en 3D peuvent être réalisées de quatre manières principales :
- Vis traditionnelles
- Inserts thermofixés
- Assemblage par encliquetage
- Charnières à imprimer
Des filets de charnière peuvent être ajoutés à la conception des pièces imprimées en 3D, mais les filets de vis traditionnels des lunettes sont généralement trop petits pour offrir une résolution uniforme. Privilégiez des filets de vis d'au moins M6 ou plus.

Lunettes assemblées à l'aide d'un filet imprimé et d'une vis en métal.
Les poudres Nylon 11 Powder, Nylon 12 Powder et Nylon 12 White Powder permettent d'utiliser des inserts thermodurcis et des pièces filetées, qui peuvent être plus durables que d'autres options. Lisez le guide étape par étape ici.
Enfin, en raison de l'absence de structures de support, l'impression 3D SLS permet d'imprimer directement les branches. Les montures peuvent être conçues et imprimées avec les branches déjà fixées, sans qu'aucun autre assemblage ne soit nécessaire. Formlabs recommande un jeu de 0,3 mm pour les caractéristiques inférieures à 20 mm2 et de 0,6 mm pour les caractéristiques supérieures à 20 mm2. Lire l'intégralité du guide de conception SLS ici.
Formes non moulables

Les branches en Nylon 11 Powder sont conçues avec des options de treillis dans le logiciel nTopology.

Montures et branches de lunettes imprimées sur l'imprimante Fuse 1+ 30W, conçues et fabriquées par Alvaro Planchart.
L'impression 3D a permis aux designers de créer des modèles de lunettes non moulables et non découpables, principalement dans des applications plus axées sur la mode. Les formes non moulables, telles que les branches de l'image ci-dessus, peuvent donner de nouveaux moyens de s'exprimer à l'utilisateur ou, au contraire, permettre d'alléger considérablement les composants pour améliorer son confort.
Impression 3D
Une imprimante 3D pour lunettes
L'écosystème SLS de la série Fuse offre une solution de production accessible et évolutive pour les lunettes, grâce à son matériel fiable, ses matériaux de qualité industrielle et son interface utilisateur intuitive. Les sections ci-dessous présentent des conseils et des astuces spécifiques à la production de lunettes avec l'impression 3D SLS.
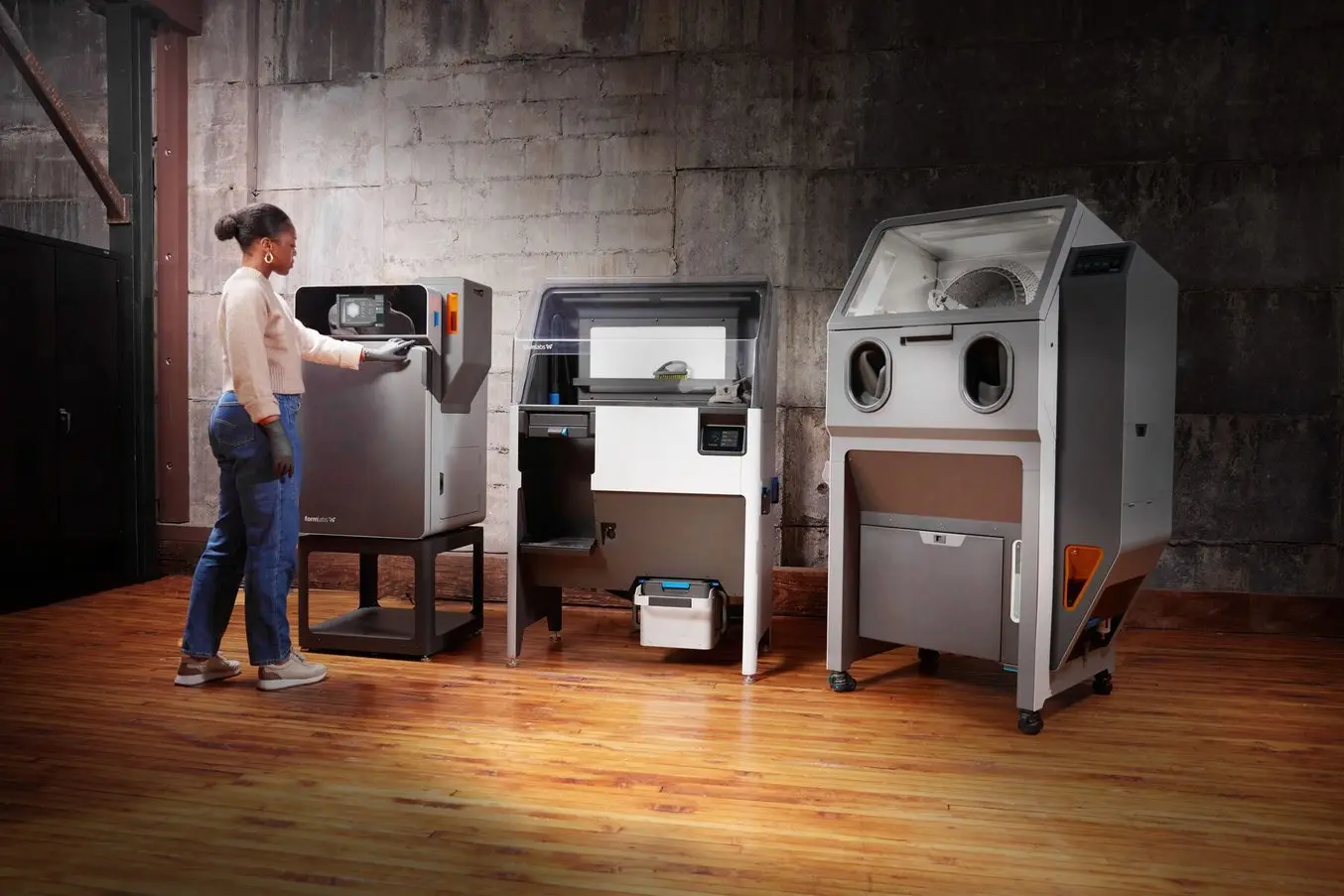
L'écosystème SLS de la série Fuse est composé de l'imprimante Fuse 1+ 30W, de la station de récupération de poudre Fuse Sift et de la solution automatisée de mélange abrasif et de polissage Fuse Blast.
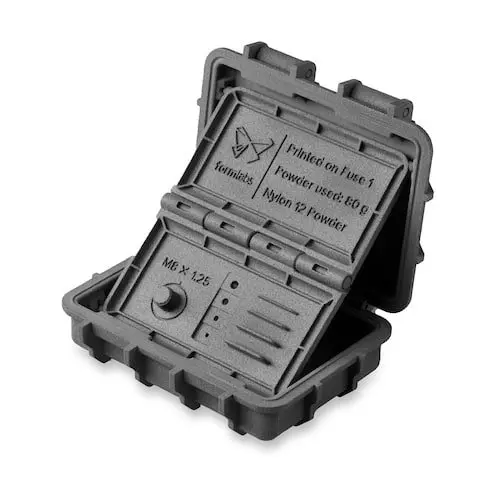
Commander un échantillon SLS gratuit
Examinez et constatez par vous-même la qualité Formlabs. Nous vous enverrons un échantillon gratuit imprimé sur la Fuse 1+ 30W à votre bureau.
Matériaux pour l'impression 3D de montures de lunettes
La série Fuse propose trois matériaux adaptés à la production de lunettes : Nylon 11 Powder, Nylon 12 Powder, et Nylon 12 White Powder. Ces trois matériaux sont des thermoplastiques, tout comme l'acétate, ce qui signifie que les opticiens peuvent chauffer les montures et les branches pour qu'elles s'adaptent mieux au visage après l'impression.
Lorsque l'on compare leurs performances fonctionnelles à celles de l'acétate, du TR90 et du polycarbonate, ces trois matériaux SLS leur sont extrêmement similaires. Certains clients préfèrent Nylon 11 Powder en raison de son allongement à la rupture supérieur et de ses avantages en termes de durabilité.
Acétate de cellulose* | Grilamid TR90** | Nylon 11 Powder | Nylon 12 Powder | Nylon 12 White Powder | |
---|---|---|---|---|---|
Résistance à la rupture par traction | 30 MPa | 60 MPa | 49 MPa | 50 MPa | 47 MPa |
Module de traction | 1700 MPa | 1500 MPa | 1600 MPa | 1850 MPa | 1950 MPa |
Allongement à la rupture | 30 % | 50 % | 40 % | 11 % | 8 % |
Résistance à la flexion | 40 MPa | N/A | 55 MPa | 66 MPa | 56 MPa |
Lors d'essais fonctionnels en conditions réelles, Nylon 11 Powder a fait preuve d'une ductilité et d'une résistance aux chocs impressionnantes :
D'autres propriétés environnementales et matérielles doivent être prises en compte si vous souhaitez créer un produit durable qui sera exposé aux éléments.
Acétate de cellulose* | Grilamid TR90** | Nylon 11 Powder | Nylon 12 Powder | Nylon 12 White Powder | |
---|---|---|---|---|---|
ISO 10993-10:2010/(R)2014,Tests d'irritation et de sécurité cutanée | Non irritant | Non irritant | Non irritant | Non irritant | Non irritant |
Contenu d'origine biologique | >50 % d'origine biologique | N/A | 100 % d'origine biologique | N/A | N/A |
Densité | 1,3 g/cm3 | 1,0 g/cm3 | 1,0 g/cm3 | 0,99 g/cm3 | 0,95 g/cm³ |
Absorption d’eau | 2,3 % | 3 % | 0,07 % | 0,66 % | 1,40 % |
Compatibilité avec les solvants, eau salée (3,5 % NaCL), prise de poids sur 24 heures | N/A | N/A | 0,1 % | 0,2 % | 0,1 % |
Température de fléchissement sous charge (TFC) à 0,45 MPa | 75 °C | 100 °C | 182 °C | 171 °C | 177 °C |
Inflammabilité, UL 94 Section 7 | N/A | HB | HB | HB | HB |
*Source : https://www.makeitfrom.com/material-properties/High-Plasticizer-CA
**Source : https://www.picoplast.nl/uploads/bab8c3f16780cb5b51b67be4baece673Grilamid%20TR90%20LX%20-%20MDS%20-%20EN.pdf
En raison de leur faible densité, de leur faible absorption d'eau et de leur résistance élevée à la chaleur et à l'inflammabilité, Nylon 11 Powder, Nylon 12 Powder et Nylon 12 White Powder peuvent être utilisées pour des applications plus fonctionnelles, telles que les lunettes de protection pour l'atelier ou le terrain, ce qui permet de créer des montures légères capables de résister à des conditions environnementales intenses.
Enfin, Nylon 11 Powder de Formlabs est un matériau renouvelable 100 % biologique, puisqu'il est fait à partir de graines de ricin durables qui offrent une option plus écologique que certains plastiques dérivés du pétrole. Par rapport à Nylon 12 Powder, Nylon 11 Powder possède une empreinte carbone 60 % moins élevée. Pour demander un rapport complet d'analyse du cycle de vie (ACV) de Nylon 11 Powder, contactez Formlabs.
Finition de surface
La finition de surface dépend fortement de la conception du modèle, et des orientations différentes donneront des états de surface différents. Formlabs a mené des tests approfondis sur l'orientation des pièces et a constaté qu'une monture ronde en Nylon 11 Powder, Nylon 12 Powder ou Nylon 12 White Powder offrait la meilleure finition de surface si elle était orientée à 45 degrés. Le côté de la pièce orienté vers le bas de la chambre de fabrication aura une finition de surface légèrement plus lisse.

Formlabs a constaté que l'impression des montures de lunettes à un angle de 45° par rapport au fond de la chambre de fabrication aide à obtenir une finition de surface plus lisse et plus homogène.
Capacité d'impression
Lorsqu'elles sont orientées à un angle de 45 degrés, 77 montures peuvent tenir dans la chambre de fabrication de la Fuse 1+ 30W. Ce scénario offre une densité d'agencement de 11 % et un temps de fabrication de seulement 11 heures en utilisant Nylon 12 Powder, selon les chiffres de mars 2023. Formlabs améliore continuellement ses paramètres d'impression. Pour recevoir une analyse de vos propres fichiers afin de déterminer le coût, le temps d'impression et le RSI, contactez notre équipe.

77 montures de lunettes agencées dans PreForm, le logiciel de préparation à l'impression de Formlabs, capable d'agencer automatiquement les fichiers pour une densité et une durée d'impression optimales.

PreForm peut également calculer le coût du matériau, y compris la poudre frittée et la poudre non frittée entourant les pièces, pour l'utiliser dans l'analyse du coût total de la poudre.
Nylon 12 Powder | Nylon 11 Powder | |
---|---|---|
Nombre de pièces par impression | 77 | 60* |
Densité d'agencement** | 10 % | 11 % |
Temps d’impression | 11 h | 22 h 30 min |
Production annuelle max. | 36 960*** | 14 000*** |
* Le nombre de pièces a été réduit pour obtenir un temps d'impression inférieur à 24 heures, ce qui a permis d'augmenter le rendement de la production. Avec Nylon 11 Powder, il est également possible d'imprimer 77 montures en une seule fois, mais avec un temps d'impression supérieur à 24 heures.
** Pour en savoir plus sur la densité d'agencement et le taux de rafraîchissement, cliquez ici.
*** En supposant une impression par jour, cinq jours par semaine, pendant 48 semaines par an. Une deuxième chambre de fabrication est nécessaire pour alterner rapidement et lancer de nouvelles impressions.
Options de finition
Nylon 11 Powder et de Nylon 12 Powder ont une couleur grise opaque avec une finition de surface plus rugueuse que celle de l'acétate poli. Nylon 12 White Powder présente une finition de surface similaire, plus rugueuse, de couleur blanc bleuté. Pour obtenir une finition plus proche de celle des lunettes traditionnelles en acétate ou en TR90, diverses options de finition peuvent être envisagées.

Montures imprimées en PA11, de gauche à droite : état brut à la sortie de l'imprimante ; polie par vibration ; lissée à la vapeur ; teintée en noir ; teintée en bleu ; recouverte de Cerakote blanc.
Préparation de la surface des pièces
Tout comme les montures en acétate traditionnelles qui sont souvent polies avec un agent en bois, les montures imprimées en 3D peuvent également bénéficier d'un polissage vibratoire de quelques heures. En utilisant des agents céramiques avec un lubrifiant, Formlabs a constaté une réduction de 80 % de la rugosité de la surface, ce qui donne une sensation de douceur au toucher. Formlabs utilise le tambour de polissage Mr. Deburr 300DB, une option peu coûteuse et facile à utiliser.
Délai | Nylon 11 Powder, Réduction de la rugosité de surface | Nylon 12 Powder, Réduction de la rugosité de surface | |
---|---|---|---|
Céramique* | 8 h | 80,87 % | 82,43 % |
Organique** | 24 h | 80,53 % | 82,77 % |
*Formes triangulaires en céramique, avec des dimensions latérales de ¼ de pouce, avec le composé de finition Kramco 1010
**Agents en coquille de noix 14/30 Maillage moyen

Montures imprimées en PA11 ; (en bas) polie par vibration ; (centre gauche) : revêtue de Cerakote ; (centre droit) lissée à la vapeur ; (en haut) revêtue de Cerakote.

Pièces polies avec des agents en coquille de noix pour lisser la surface.
Options de couleurs

Il est possible d'ajouter de la teinture aux couleurs gris foncé de Nylon 12 Powder et de Nylon 11 Powder, mais le résultat peut être assez sombre et terne.
Une option simple et rentable pour colorer ses pièces consiste à utiliser un système de teinture au bain-marie. Les pièces sont immergées dans un bain-marie avec un colorant qui pénètre toutes les surfaces de la pièce et en modifie la couleur de façon permanente. Bien que les poudres grises (Nylon 11 Powder et Nylon 12 Powder) puissent être teintées, l'impression avec la poudre Nylon 12 White Powder est le meilleur moyen de garantir l'obtention d'une gamme de couleurs éclatantes.
Il existe des options industrielles pour teinter les pièces imprimées en 3D par SLS, comme les appareils de DyeMansion. Ces derniers peuvent toutefois coûter des dizaines de milliers de dollars et, pour une production en petite série ou un prototypage, ils peuvent ne pas être judicieux. Pour en savoir plus sur l'utilisation d'une méthode de teinture peu coûteuse et efficace pour les pièces finales en Nylon 12 White Powder, regardez notre webinaire avec Ken Pillonel, ingénieur et concepteur de produits.
Formlabs utilise également le revêtement Cerakote pour améliorer les propriétés mécaniques de la pièce et permettre une grande variété de coloris. Le Cerakote est un revêtement céramique en couche mince dont l'épaisseur varie de 0,00635 mm à 0,0254 mm et qui ne nécessite pas d'apprêt.
Une fois recouvertes, les pièces imprimées en 3D par SLS peuvent mieux résister aux produits chimiques et aux rayures. Le Cerakote peut également être utilisé pour obtenir une finition de surface brillante, avec des couleurs allant du pastel jusqu'au métal. En outre, une fois revêtues, les pièces peuvent être sculptées au laser pour obtenir des motifs intéressants ou afficher des informations, telles que des logos ou des numéros de série.
Le Cerakote peut également être utilisé pour obtenir une finition brillante, grâce à ses programmes de post-polymérisation personnalisables.

Montures imprimées avec Nylon 11 Powder et revêtues de Cerakote H-Series.
L'hydro trempage est également possible avec les pièces imprimées en 3D par SLS. De même, les procédés de vernissage et de tampographie sont compatibles avec la technologie SLS.
Enfin, le lissage à la vapeur est un processus qui permet de sceller chimiquement et de lisser la surface des impressions 3D SLS. Le lissage à la vapeur permet d'obtenir une surface semblable à celle d'un produit moulé par injection, avec une rugosité de surface nettement améliorée, des finitions de surface brillantes, ainsi qu'une résistance à l'humidité et à la prolifération des bactéries.
Formlabs utilise Additive Manufacturing Technologies (AMT) pour lisser à la vapeur des composants de lunettes. En outre, les pièces peuvent être teintées dans un bain d'eau avant ou après le lissage à la vapeur, ce qui permet de donner plus de brillance à la nouvelle couleur de la pièce.

montures de lunettes lissées à la vapeur
Jugez vous-même
Si Formlabs a recherché et développé de nombreuses options de finition pour améliorer l'état de surface des pièces imprimées en 3D par SLS, il reste encore beaucoup d'autres voies à explorer. De nombreux clients ont commandé un échantillon gratuit de leurs lunettes et ont ensuite appliqué leurs propres techniques de finition (différents agents de polissage, vernis, revêtements, etc.) pour obtenir une esthétique unique.
Contactez notre équipe commerciale pour commander un échantillon gratuit de votre propre conception, ou pour commander une pièce d'échantillon standard en Nylon 11 Powder, Nylon 12 Powder ou Nylon 12 White Powder, sur laquelle vous pourrez essayer des techniques de finition confidentielles ou exclusives.
Autres utilisations de l'impression 3D dans l'industrie de la lunetterie
Outre ses capacités de production, la polyvalence du système Fuse 1+ 30W permet d'autres applications pour accroître la valeur de l'industrie de la lunetterie.
Prototypage
Les systèmes de la série Fuse et de la série Form peuvent être utilisés pour prototyper des lunettes afin d'en tester les dimensions, l'ajustement et la conception générale.
Choisissez des matériaux en nylon sur le système Fuse 1+ 30W pour créer des prototypes fonctionnels qui peuvent être portés et testés pendant de longues périodes. Choisissez le système Form 4 ou Form 4L pour créer des prototypes esthétiques qui présentent une translucidité similaire à celle de l'acétate et du polycarbonate. Les prototypes imprimés par SLA peuvent être portés pendant plusieurs semaines, mais ne conviennent pas pour une utilisation à long terme, à moins qu'ils ne soient recouverts d'un revêtement bloquant les UV.

Plastinax utilise l'imprimante SLA de la série Form pour produire des prototypes avec des matériaux semi-translucides.
Test utilisateur
Utilisez la Fuse 1+ 30W pour créer des lunettes qui peuvent être testées par les utilisateurs afin d'obtenir rapidement un retour d'information et d'itérer sur les dimensions et la conception.

Plastinax conçoit ses montures de lunettes personnalisées dans Fusion 360, puis les imprime directement sur l'imprimante 3D SLS Fuse 1+ 30W.

Montures en Nylon 12 Powder conçues et imprimées par Plastinax.
Lunettes intelligentes
Avec l'impression 3D, concevoir des pièces complexes n'entraîne aucun coût supplémentaire. Ajouter des boîtiers pour l'électronique ou des assemblages complexes ne pose aucun problème pour votre imprimante 3D. Privilégiez l'impression 3D SLS lorsque vous créez des boîtiers complexes pour des lunettes intelligentes qui seraient autrement difficiles à fabriquer à l'aide de moules d'injection coûteux en plusieurs parties.
Gabarits et fixations
En raison de leur résistance élevée aux chocs, Nylon 12 Powder, Nylon 12 White Powder et Nylon 11 Powder conviennent parfaitement à la fabrication de gabarits et de fixations sur mesure. Les poudres de nylon de Formlabs sont suffisamment résistantes pour plier certains métaux utilisés dans les montures et les branches traditionnelles, comme le titane, avec des pressions de plus de 90 kg.
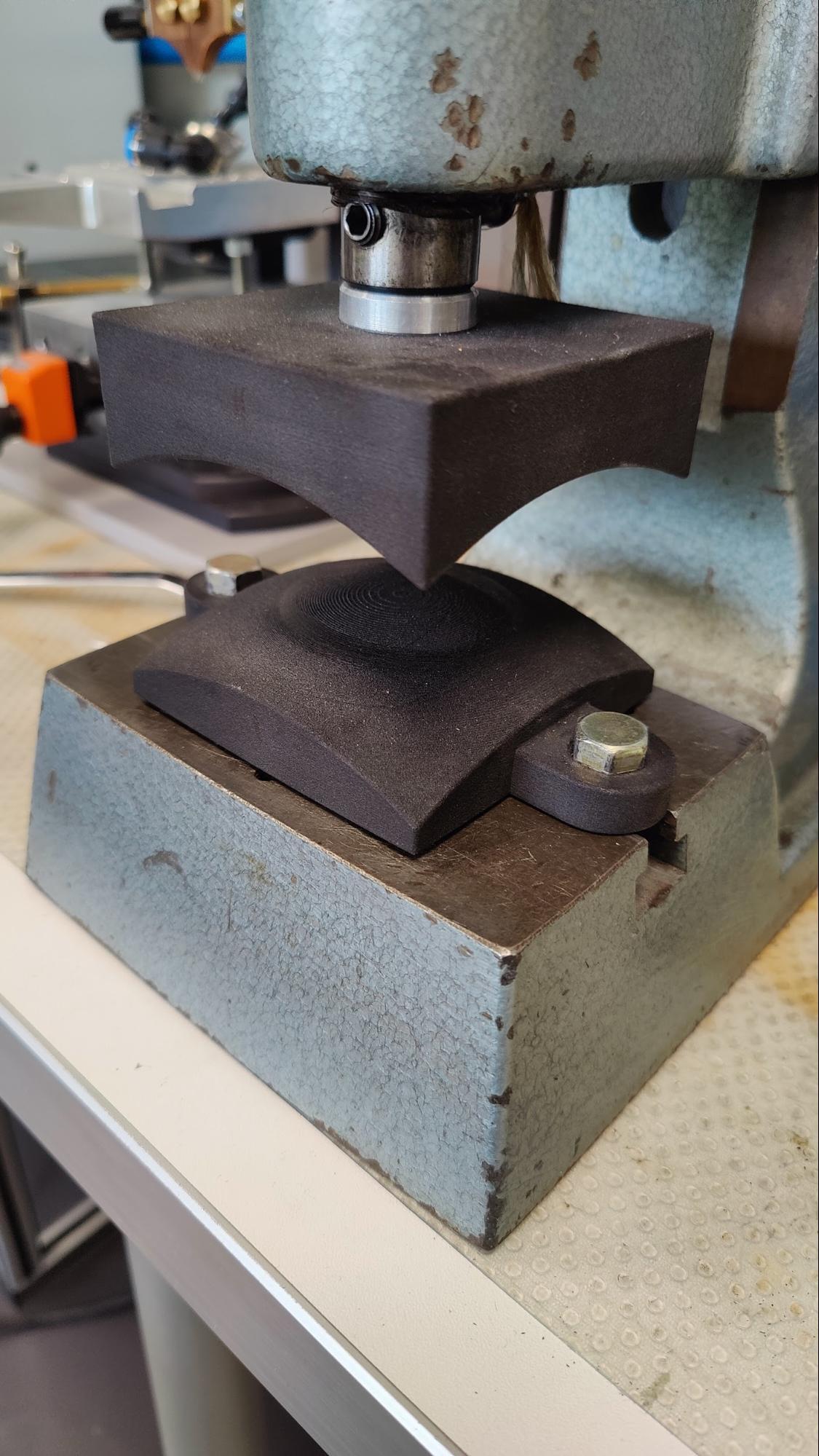
Outil de pressage imprimé en 3D par SLS avec Nylon 11 Powder pour plier les montures et les branches, vissé dans une presse à genouillère, par Marcus Marienfeld.
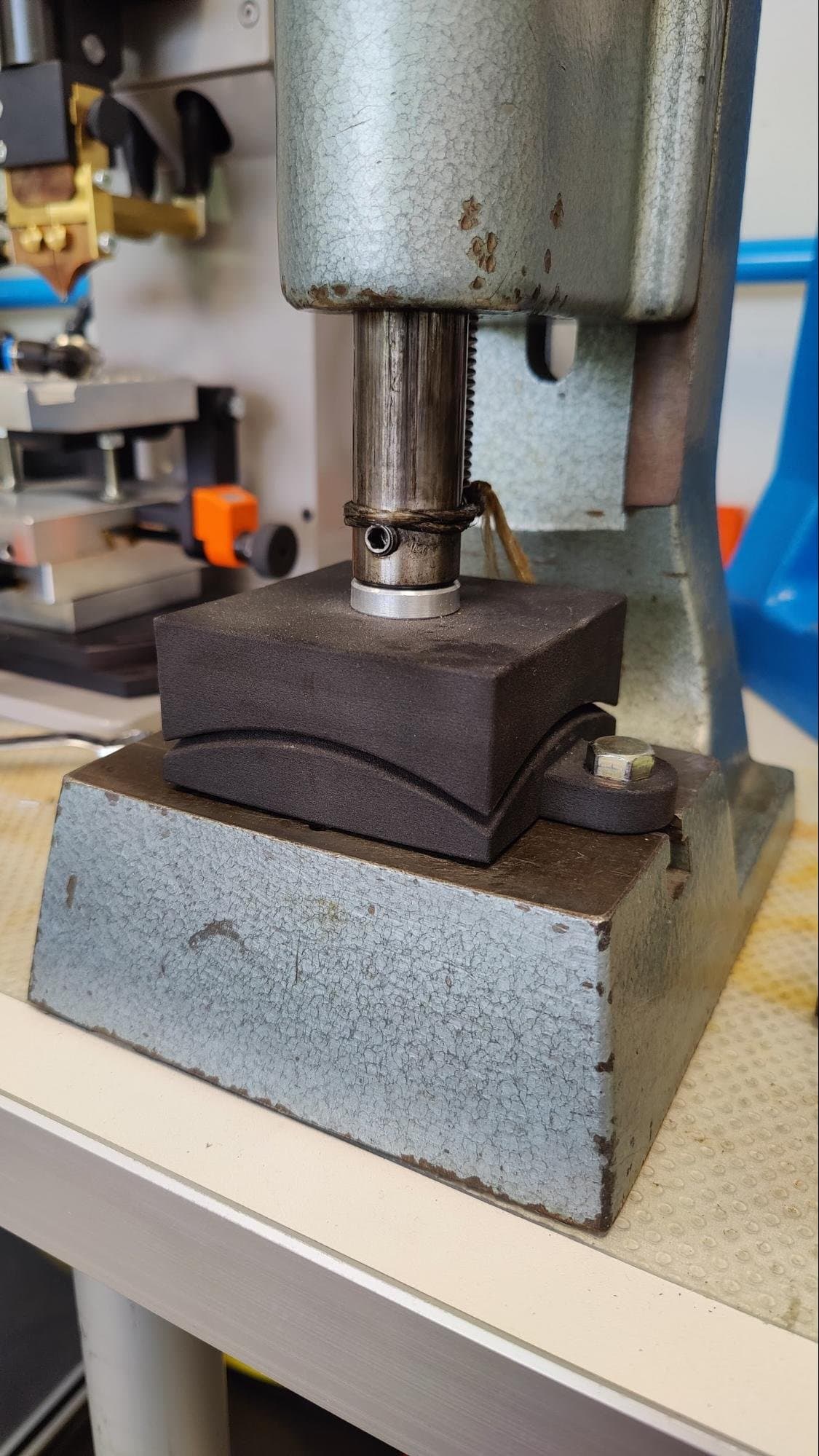
Moulage par injection et formage sous vide en petites séries
Utiliser des imprimantes 3D SLA Form 4 ou Form 4L et Rigid 10K Resin pour produire des moules d'injection est monnaie courante dans de nombreuses industries. En raison de sa haute résistance à la chaleur et de sa fine finition de surface, Rigid 10K Resin peut être utilisée pour le moulage par injection de petites séries de montures et de branches, ainsi que pour la fabrication de moules destinés à produire des emballages formés sous vide.

Moules imprimés en 3D pour le formage sous vide d'emballages fabriqués avec Rigid 10K Resin.
Bâtir un dossier commercial
Posséder une entreprise ou créer une nouvelle ligne de produits grâce à l'impression 3D devient de plus en plus accessible et rentable. Une seule imprimante 3D Fuse 1+ 30W peut produire plus de 19 000 montures par an ou plus de 50 000 branches par an, avec un calendrier de production non optimisé de cinq jours.
Montures en Nylon 12 Powder* | Coût par pièce** | |
---|---|---|
1 Fuse 1+ 30W | 36 960 | 1,27 € |
5 Fuse 1+ 30W | 184 800 | Nous contacter pour le prix |
10 Fuse 1+ 30W | 369 600 | Nous contacter pour le prix |
Branches en Nylon 12 Powder* | Coût par pièce** | |
---|---|---|
1 Fuse 1+ 30W | 87 840 | 0,29 € |
5 Fuse 1+ 30W | 439 200 | Nous contacter pour le prix |
10 Fuse 1+ 30W | 878 400 | Nous contacter pour le prix |
* En supposant une semaine de travail de cinq jours avec cinq tirages par semaine, pendant 48 semaines par an.
**Le coût du matériau est fixé à 69 €/kg, soit une remise de 30 %, typique pour les clients imprimant dans cette quantité.

Ces branches (gauches et droites) sont idéales pour une impression efficace, avec une densité d'agencement de 31 %, garantissant que toute la poudre non utilisée peut être recyclée dans la construction suivante, ce qui réduit considérablement le coût par pièce.

Ces montures de lunettes ne sont pas agencées aussi densément que les branches, ce qui se traduit par un taux de renouvellement légèrement moins bon et un coût par pièce plus élevé. Cependant, une seule imprimante peut tout de même produire près de 37 000 montures par an de manière rentable.
Option 1 : Prendre le contrôle de sa propre production
Le moyen le plus efficace et le plus rentable de produire des lunettes imprimées en 3D est de posséder l'équipement de production. Cela implique l'achat d'un écosystème SLS de la série Fuse.
Les avantages de l'intégration verticale de l'impression 3D sont notamment un retour sur investissement plus rapide, un contrôle plus étroit de la qualité, la possibilité de modifier la conception et de passer du prototypage à la production sur la même machine, et la capacité d'utiliser l'écosystème à d'autres fins, comme la création de gabarits et de fixations.
Conçu pour être aussi accessible que possible, l'écosystème SLS de la série Fuse est directement prêt à l'emploi, et la plupart des utilisateurs apprennent à se servir de l'équipement en quelques heures. De même, l'écosystème ne nécessite qu'une configuration minimale, ce qui permet de l'installer rapidement et de l'adapter facilement en fonction de l'augmentation de la demande.
Il est également important de noter qu'une nouvelle Fuse Sift ou Fuse Blast n'est pas nécessaire pour chaque imprimante Fuse 1+ 30W supplémentaire. La plupart des clients maintiennent un rapport de 4:1 entre les imprimantes et les stations de post-traitement. Le coût de l'intégration d'un écosystème complet d'impression SLS de Formlabs, comprenant une Fuse 1+ 30W, une unité de post-traitement Fuse Sift, un mélangeur abrasif Fuse Blast, deux chambres de fabrication, deux cartouches, 20 kg de matériau Nylon 12 Powder et deux ans d'assistance clientèle spécialisée, s'élève à environ 65 000 €.

Avec la série Fuse, l'évolution en fonction de la demande est facile et efficace.
Option 2 : Sous-traiter à un prestataire de service
Il existe de nombreux prestataires de services dans le monde, avec différents niveaux de capacités. Certains ne s'occupent que de l'impression 3D, tandis que d'autres offrent des services de conception, d'impression, de post-traitement et d'emballage.
Le coût par pièce est bien plus élevé lorsque vous travaillez avec un prestataire de services. Toutefois, cela peut être une bonne option pour ceux qui ne disposent pas de l'espace ou du capital nécessaires pour investir dans des équipements de production, ou pour ceux qui souhaitent imprimer de petites séries de pièces.

Les prestataires de services peuvent être de bonnes options pour les essais initiaux et la preuve de concept.
Lancez-vous dans l'impression de lunettes en 3D
Les lunettes constituent une application intéressante de l'impression 3D SLS. Les fabricants de lunettes peuvent modifier chaque élément, qu'il s'agisse du matériau ou de différences de l'ordre du micron dans l'épaisseur des lentilles. À mesure que la résolution, la précision, la polyvalence des matériaux et les processus de finition de l'impression 3D se perfectionnent, cette technologie devient une méthode rentable pour concevoir et fabriquer des lunettes.
Grâce à l'écosystème SLS de la série Fuse, les concepteurs et fabricants de lunettes ont la possibilité de réaliser des prototypes plus rapidement que jamais, et de produire des produits finis sans recourir à la sous-traitance ou à un fabricant d'outils. L'impression 3D SLS peut aider les entreprises à regrouper sous un même toit l'ensemble du flux de travail, de la conception à la production, ce qui permet de réduire les coûts et d'accroître l'efficacité.
Pour en savoir plus sur la série Fuse, visitez notre site internet. Pour tester vous-même l'une de nos poudres de nylon, demandez gratuitement un échantillon imprimé en 3D par SLS.