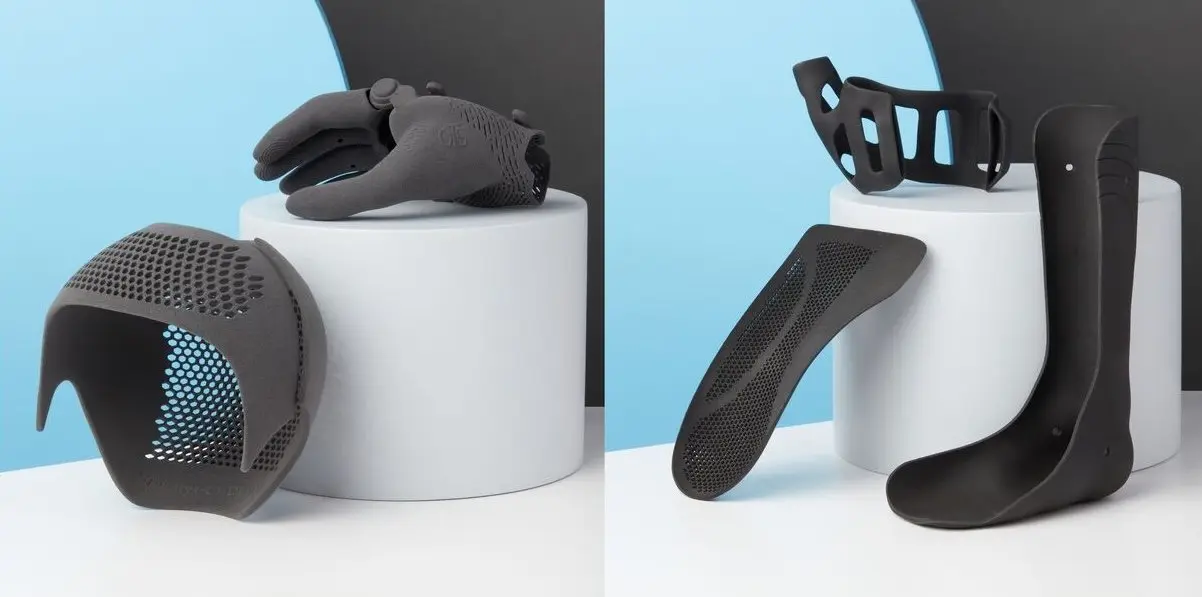
Les orthèses sont des dispositifs médicaux externes créés pour traiter ou assister les déformations musculaires ou squelettiques. Outre le confort et le support qu'ils procurent, ils peuvent faciliter la mobilité ou la récupération, aider à soulager la douleur et prévenir l'apparition de problèmes plus permanents.
Voici quelques exemples d'orthèses courantes :
- Les genouillères réduisent la pression et la charge exercées sur les genoux lors d'activités physiques.
- Les orthèses cheville-pied stabilisent le pied et améliorent le maintien.
- Les orthèses pour le poignet et la main supportent les articulations de ces régions et l'utilisation du membre.
Aujourd'hui, les dimensions du marché du secteur des orthèses sont d'environ 6,5 milliards de dollars, avec un taux de croissance annuel prévu de 4,2 %. La croissance de ce secteur de la santé s'explique par la nécessité d'améliorer les soins aux patients grâce à des solutions d'ajustement personnalisées. Les plaintes des patients et les problèmes de santé causés par l'inadéquation des solutions standardisées font partie des défis habituels. La personnalisation permet de répondre à ces préoccupations et d'offrir une solution adaptée au patient, mais l'utilisation de méthodes traditionnelles de production personnalisée s'accompagne de coûts supplémentaires et de longues durées de production.
De nombreux professionnels de la santé adoptent maintenant l'impression 3D pour les orthèses, en imprimant des solutions orthopédiques personnalisées. En suivant des flux de travail éprouvés, l'impression 3D peut faire gagner du temps et des ressources, ce qui permet de produire des orthèses spécifiques au patient en un temps record. Vous trouverez ci-dessous des informations complémentaires sur la manière dont les orthèses individuelles imprimées en 3D améliorent à la fois l'expérience du patient et l'efficacité de la production.
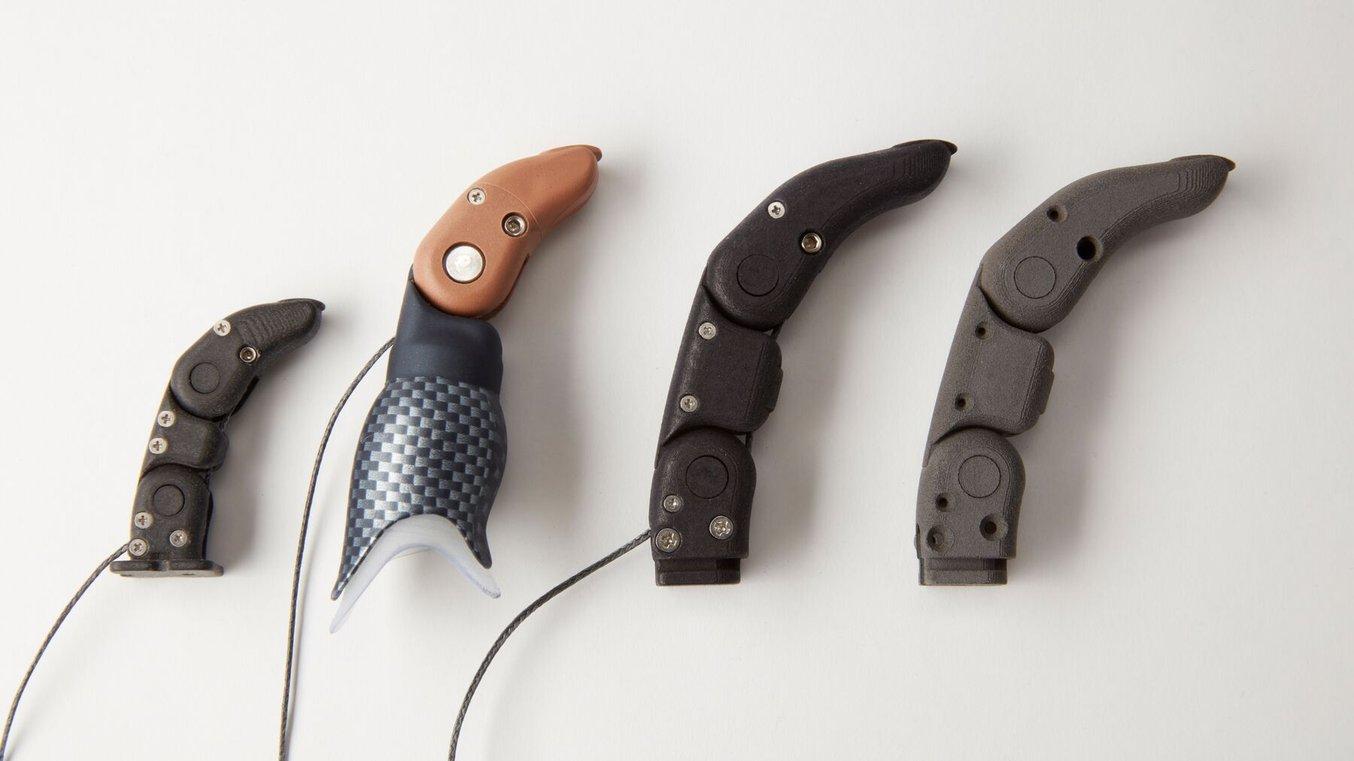
L'impression 3D dans l'industrie des orthèses et des prothèses
Ce livre blanc est une introduction à l'utilisation de la technologie d'impression 3D pour créer des orthèses et des prothèses de nouvelle génération.
Comment l'impression 3D révolutionne les orthèses
La fabrication conventionnelle d'orthèses s'appuyait sur le principe suivant : « Ne pas réparer ce qui n'est pas cassé ». Caractérisés par des exigences élevées en termes de main-d'œuvre et de durée, les processus de travail traditionnels produisent des orthèses que les patients attendent, mais avec des coûts ajoutés, ce qui indique qu'il existe une marge d'amélioration importante.
Les flux de travail numériques pour les orthèses sur mesure englobent de nouvelles options de conception, d'essai et de fabrication visant à réduire les coûts de personnalisation et à accélérer les cycles de production pour des délais de production plus courts, des appareils mieux ajustés et de meilleurs résultats pour les patients. Connue pour sa production rapide et ses processus relativement abordables, l'impression 3D offre aux acteurs du secteur des orthèses une solution puissante qui permet de fournir des orthèses personnalisables rapidement et à moindre coût.
Orthèses traditionnelles et orthèses imprimées en 3D
Les orthèses sont fabriquées de différentes manières en fonction de la pièce finale. Pour la fabrication d'orthèses, on peut utiliser des procédés de fabrication traditionnels tels que le moulage en plâtre, le moulage en mousse à empreinte, l'usinage conventionnel, le thermoformage et le moulage en cire.
Indépendamment des méthodes utilisées, les processus de travail peuvent être résumés comme suit :
- Une carte du patient est créée à partir d'une empreinte ou d'un moulage, de dessins techniques et de mesures. Cette opération peut durer jusqu'à une heure.
- Un modèle de développement est créé à partir de la carte topographique. Selon le procédé utilisé, cette opération peut durer entre une et deux heures.
- Le modèle est ajusté et sculpté pour s'assurer qu'il convient au patient. Ce processus peut nécessiter plusieurs rendez-vous au fur et à mesure des ajustements apportés au modèle. Ces rendez-vous peuvent durer jusqu'à plusieurs heures sur plusieurs semaines en fonction du plan de traitement.
- Enfin, l'orthèse fait l'objet d'un post-traitement et d'une finition en vue de son utilisation.
Au cours de ce processus manuel, les erreurs potentielles peuvent s'accumuler à chaque étape du flux de travail. Des erreurs de moulage, des mesures imprécises et des défauts de conception peuvent prolonger un processus déjà long, ce qui entraîne un surcroît de travail, des délais de fabrication plus longs et des rendez-vous supplémentaires pour les patients. En outre, ce flux de travail manuel nécessite une main-d'œuvre spécialisée dans un environnement rempli de poussière et de vapeurs chimiques. Au total, il faut compter entre trois et six semaines pour réaliser une seule personnalisation.
Avantages de l'impression 3D pour les orthèses
Le degré fin de personnalisation des orthèses imprimées en 3D permet d'améliorer la précision biomécanique et le confort du patient. Ces conceptions sont adaptées directement aux besoins du patient, ce qui permet un traitement et un confort optimaux.
« Les orthèses doivent être personnalisées en fonction de chaque individu, afin de cibler les symptômes spécifiques plutôt que d'appliquer des solutions standardisées qui risquent de réduire la personne à un simple cas type. »
Matej Vlašič, aNImaKe
L'efficacité et le caractère abordable des orthèses imprimées en 3D rendent les solutions d'ajustement personnalisées accessibles à davantage de patients et avantageuses pour ceux qui produisent des orthèses. Après avoir découvert de nouveaux flux de travail, l'adoption de l'impression 3D pour les orthèses s'est systématiquement affichée comme un moyen d'augmenter la productivité tout en réduisant les coûts.
Des gains de durée : Les flux de travail numériques permettent des gains de temps pour les orthoprothésistes et les patients. Grâce à des processus de travail simples et efficaces, les équipes de technique orthopédique passent moins de temps à créer des modèles et à les retravailler et ont plus de temps à consacrer à des tâches de plus grande valeur. Pour les patients, cela signifie moins de rendez-vous pour les ajustements, et la prise d’empreintes ainsi que des mesures demande moins de temps.
Économies de temps : Réduisez les coûts de production, de main-d'œuvre, de matériaux, de stockage et d'expédition en numérisant et en simplifiant votre flux de travail grâce à l'impression 3D. Avec les processus de travail traditionnels, des matériaux supplémentaires sont nécessaires pour la prise d'empreinte et la fabrication des moules, sans parler du stockage de tous ces matériaux. L'impression 3D permet de s'affranchir de ces contraintes. En outre, le post-traitement des orthèses 3D permet de réaliser des économies de main-d'œuvre pour une plus grande efficacité.
Flux de travail simplifié : Les processus numériques sont moins exigeants en main-d'œuvre et comprennent moins d'étapes, ce qui permet de supprimer des procédures manuelles entières, comme par exemple les visites aux patients pour l'ajustement. De plus, l'impression par lots permet d'imprimer plusieurs orthèses à la fois, en fonction des dimensions et des dispositifs à imprimer.
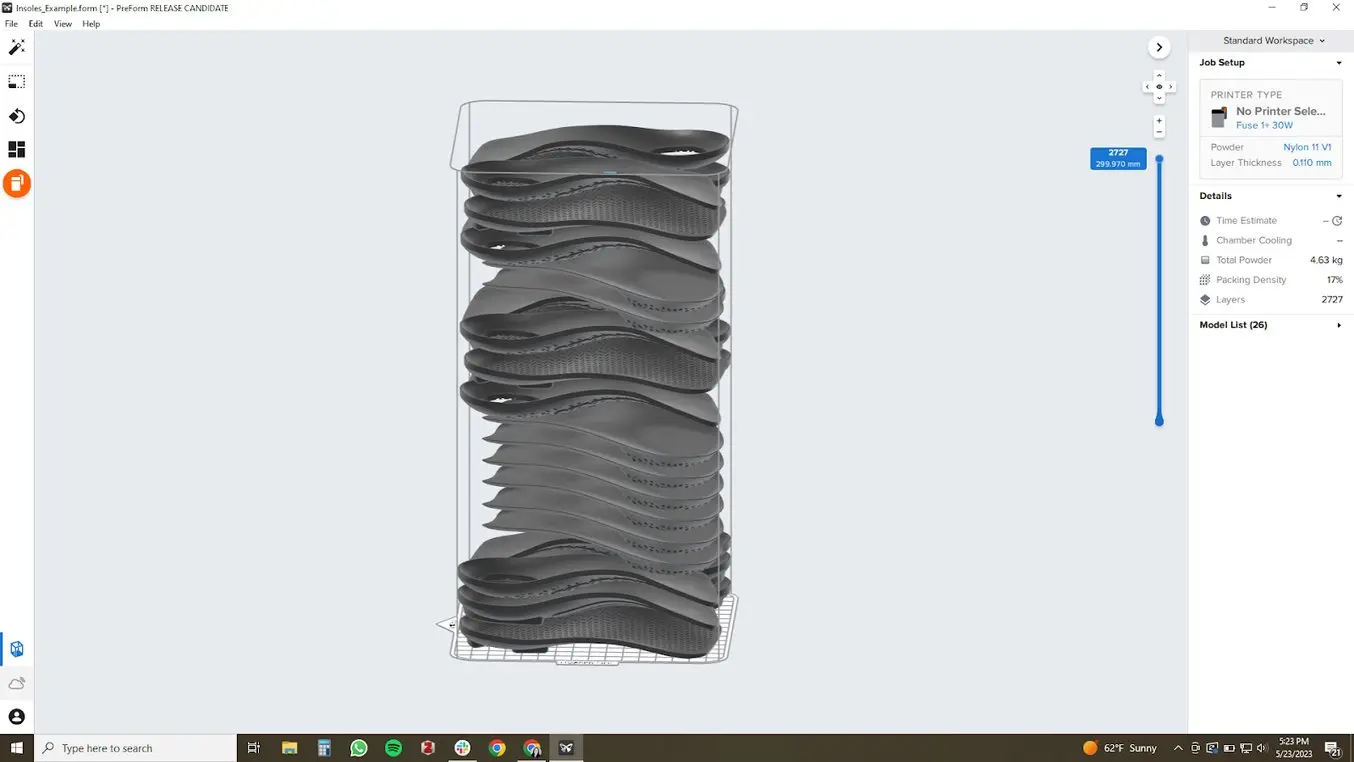
L'impression 3D SLS permet d'imprimer de nombreuses pièces en une seule fois, ce qui améliore l'efficacité et réduit les coûts.
Amélioration de la logistique : La numérisation simplifie la gestion logistique. Un scan 3D peut être pris n'importe où, puis envoyé à distance pour la modélisation numérique et la conception. Une fois conçus, les fichiers numériques peuvent être envoyés directement à l'imprimante – sur place ou à l'extérieur.
Durabilité : Avec le flux de travail numérique, beaucoup moins de matériaux bruts sont nécessaires pour produire le produit fini, car la création d'un modèle physique ou d'une réplique est éliminée. L'impression 3D par frittage sélectif par laser (SLS), utilisée pour la production de plusieurs types d'orthèses, permet le recyclage de la poudre dans l'impression suivante pour la réduction, voire l'élimination des déchets. Contrairement aux méthodes de production traditionnelles, où les modèles et les plastiques doivent être éliminés, l'impression 3D minimise les déchets et réduit l'utilisation de produits chimiques agressifs.
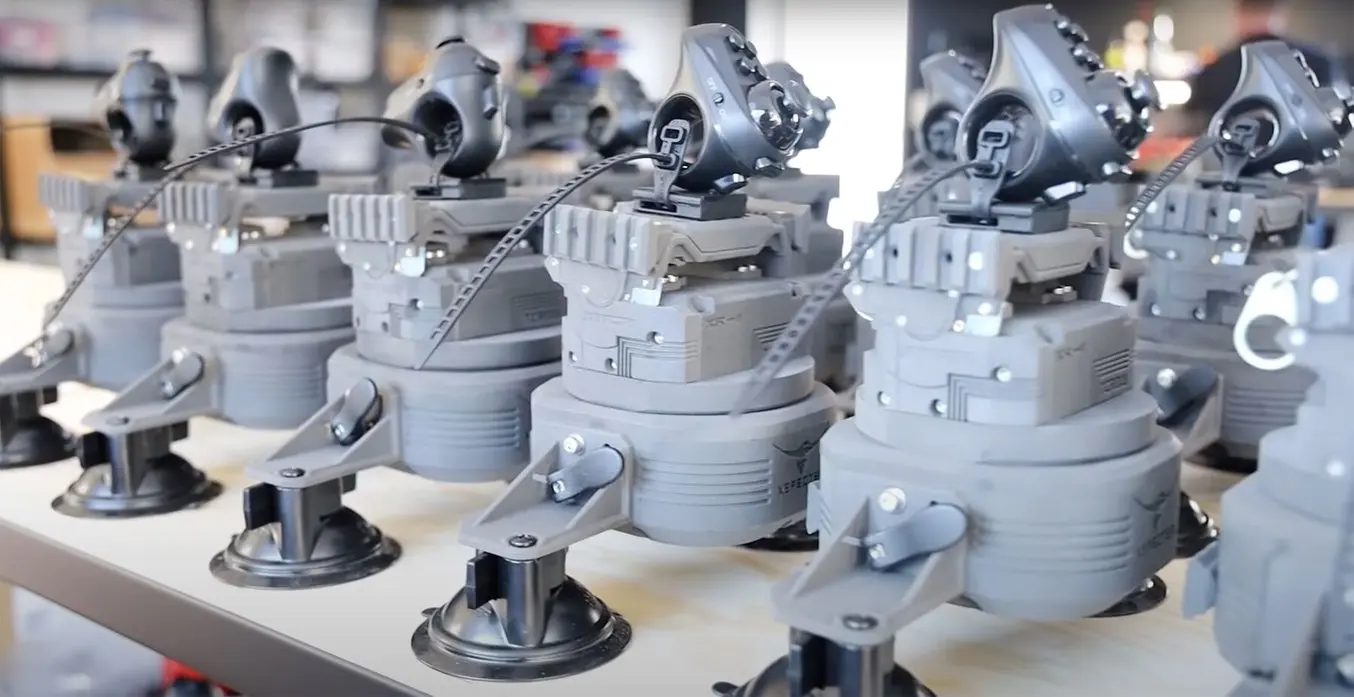
Le SLS pour la production finale
L'impression 3D pour la production finale n'est pas seulement accessible : elle est aussi plus abordable, plus agile et plus évolutive que jamais grâce à l'écosystème SLS Fuse. Explorez notre page dédiée à la production SLS pour comparer les différentes méthodes de fabrication, consulter les tarifs des poudres en vrac et découvrir comment 15 fabricants exploitent actuellement les imprimantes de la série Fuse.
Applications des orthèses imprimées en 3D
Il existe des orthèses pour traiter divers problèmes. Les différences de dimensions et de forme de l'anatomie du patient, ainsi que les exigences de l'orthèse, font que les orthèses normales peuvent être inconfortables et mal ajustées, ce qui peut avoir un impact sur la portabilité et l'efficacité, et même causer des problèmes secondaires. Les orthèses standard sont traditionnellement moins chères que les solutions personnalisées en raison de la production en masse de dimensions uniformes. Toutefois, cela se fait au détriment du confort du patient et, souvent, de l'efficacité. C'est pourquoi les orthèses personnalisées sont nécessaires pour un certain nombre d'applications clés, notamment les suivantes.
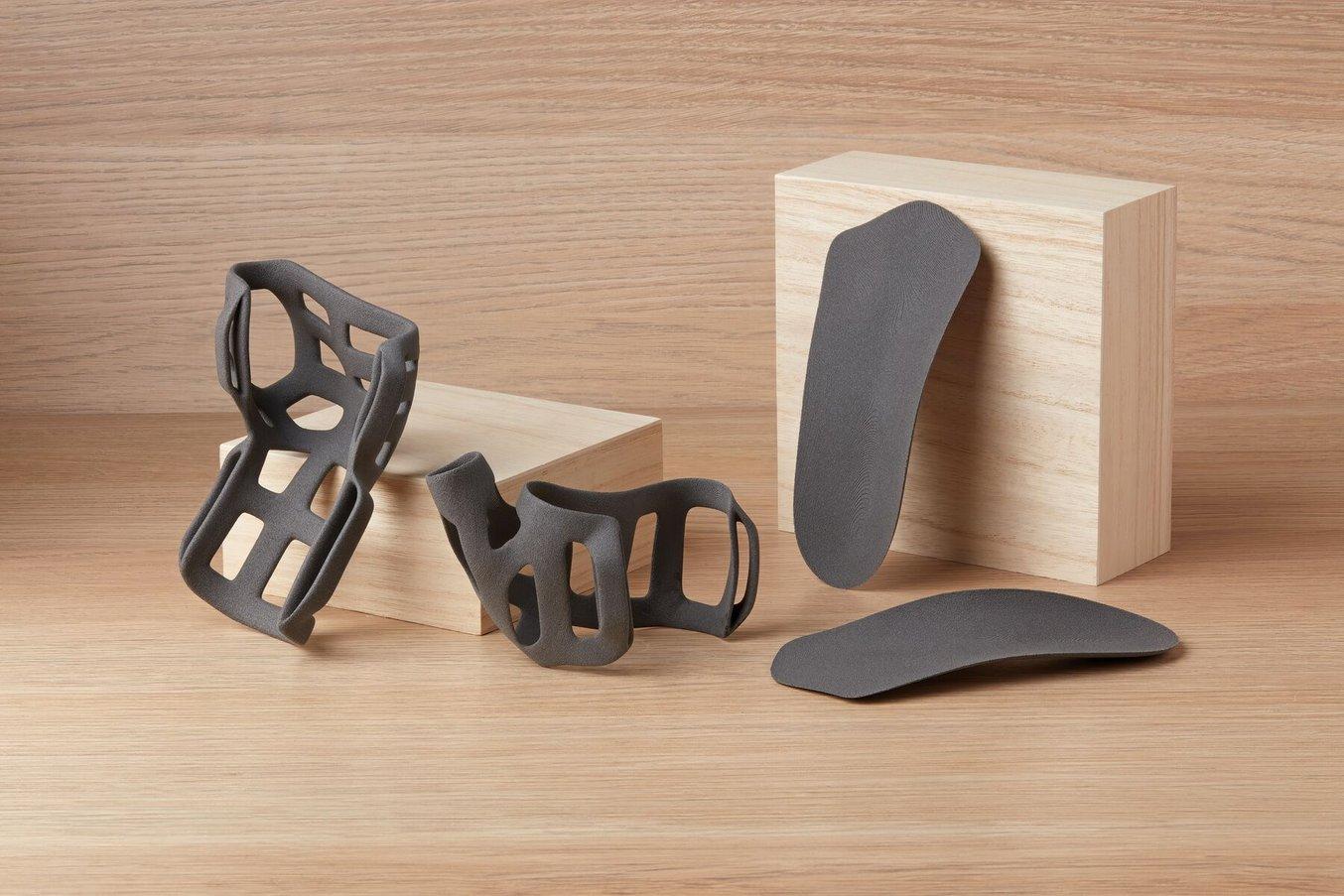
Exemples d'une orthèse de poignet, d'une orthèse de main et de semelles orthopédiques imprimées à l'aide de l'imprimante SLS Fuse 1+ 30W.
Semelles : Les semelles orthopédiques ou orthèses plantaires sont insérées dans la chaussure pour apporter un support. Elles peuvent corriger les problèmes liés au pied et réduire la douleur. Les semelles orthopédiques peuvent être prescrites aux personnes souffrant de douleurs ou de gênes dues à des oignons, de l'arthrite, de voûtes plantaires hautes ou de fasciite plantaire.
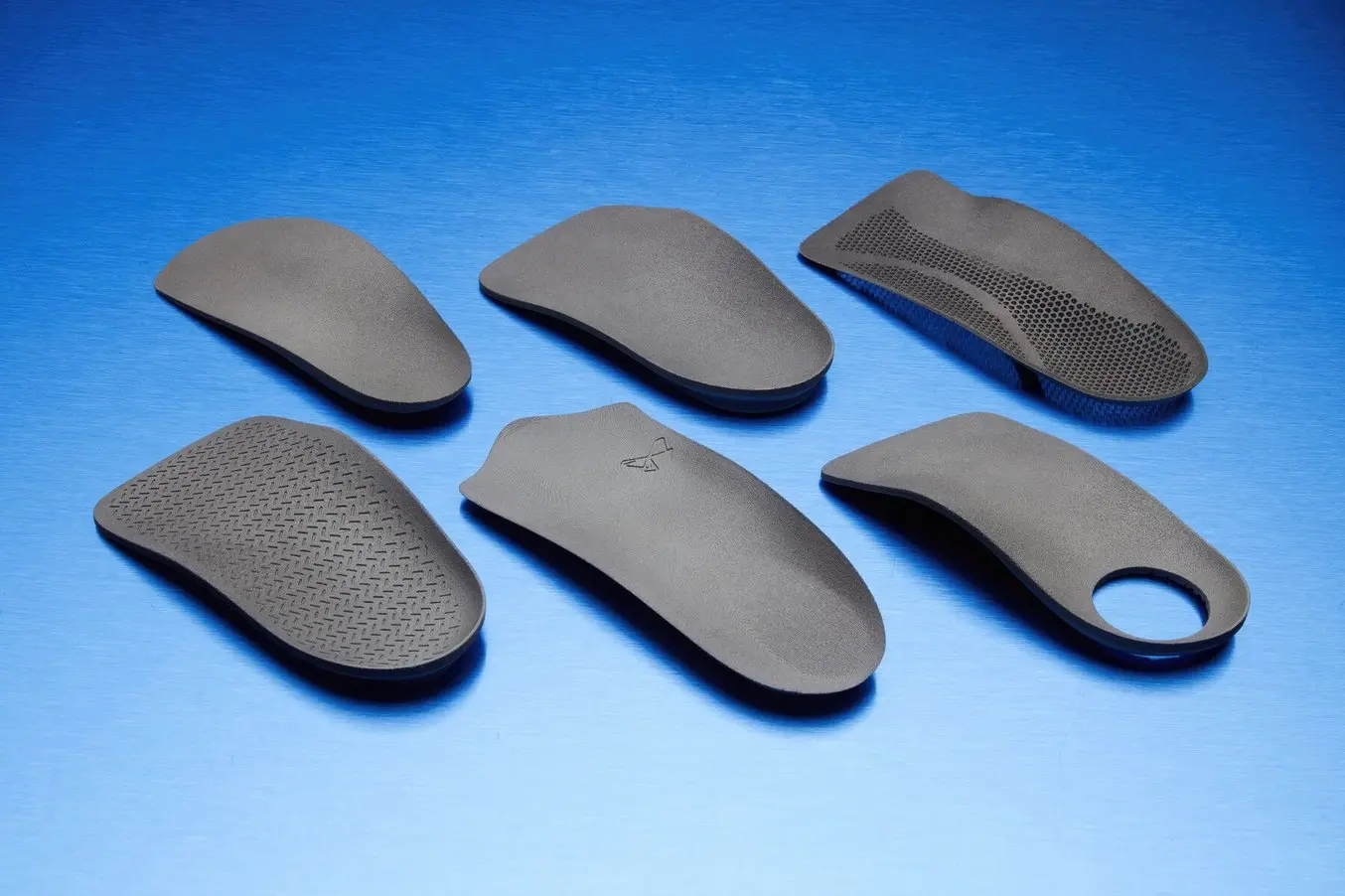
Révolutionnez votre production de semelles avec la Fuse 1+ 30W de Formlabs
Augmentez votre production de semelles tout en économisant du temps et de l'argent. Dans ce webinaire, nous expliquons pourquoi la Fuse 1+ 30W de Formlabs est la solution idéale pour commencer à passer à la fabrication numérique ou à augmenter votre production de manière abordable et efficace.
Orthèses du poignet et de la main : Les orthèses pour le poignet et la main immobilisent les articulations pour le traitement de certains problèmes, notamment les fractures, l'arthrite, les lésions ligamentaires, les greffes de peau, les déformations, les tendinites et les entorses. Une orthèse peut être limitée au pouce ou aux doigts, à la main ou à l'ensemble du bras, en fonction du plan de traitement.
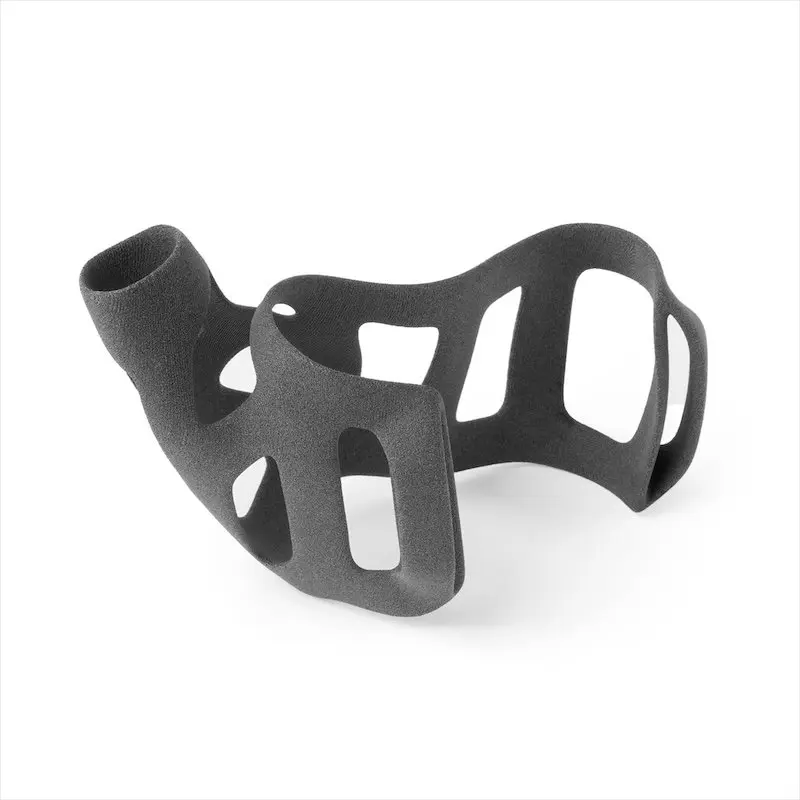
Orthèse de main pour immobiliser le pouce.
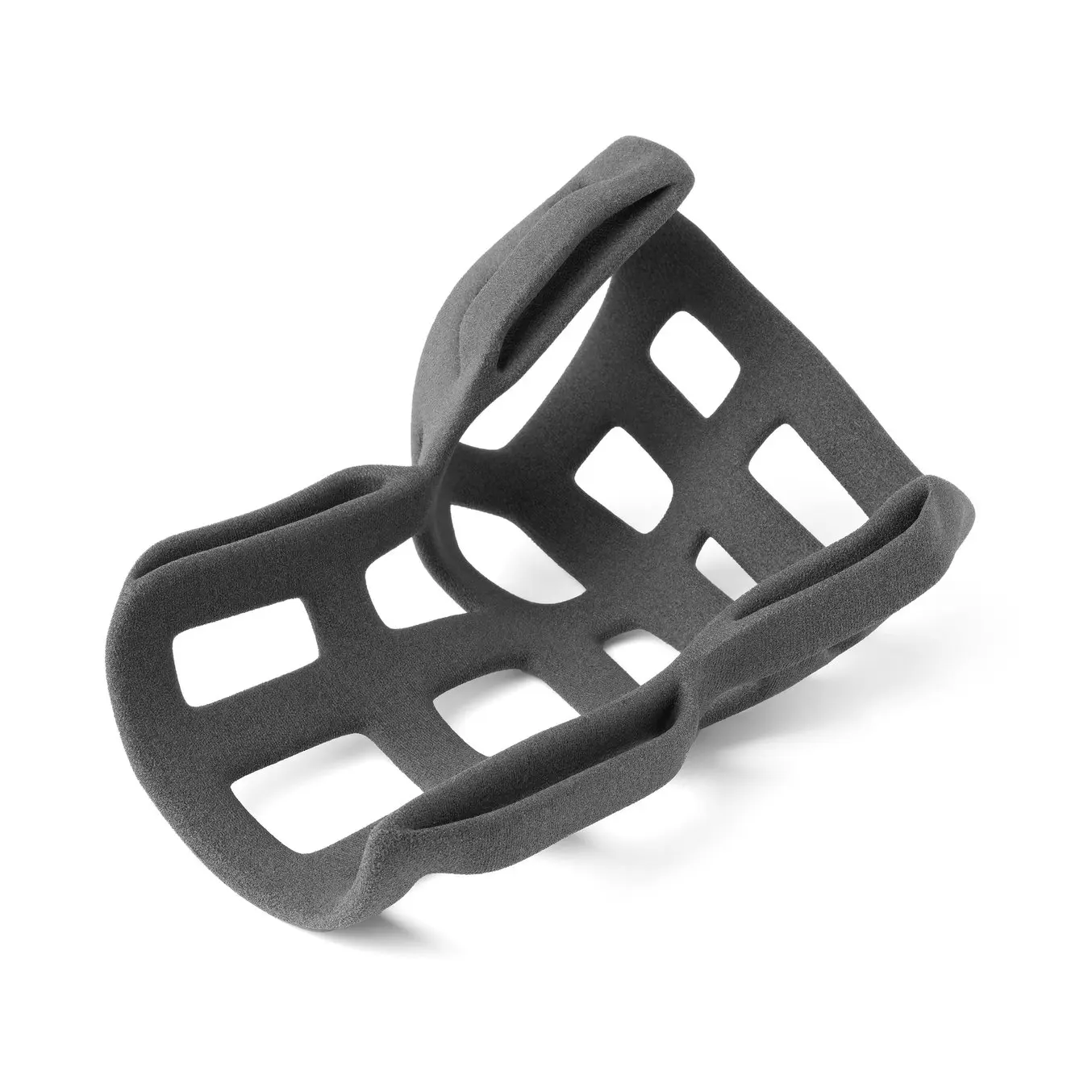
Orthèse de poignet imprimée à l'aide de l'imprimante SLS Fuse 1+ 30W.
Orthèses cheville-pied : Pour faciliter la mobilité des patients souffrant de troubles du contrôle moteur des membres inférieurs, des orthèses cheville-pied (AFO) peuvent être prescrites pour corriger l'alignement ou apporter un support. Ces conditions peuvent résulter d'une variété de troubles neurologiques et musculo-squelettiques, y compris les accidents vasculaires cérébraux, la paralysie cérébrale et la sclérose en plaques, et affectent les personnes de tous âges.
Casques de remodelage crânien : Ces orthèses sont des dispositifs ressemblant à des casques pour les nourrissons de moins de 18 mois souffrant de plagiocéphalie, ou de déformation de la tête (le plus souvent causée par une trop longue durée passée sur l'arrière), et servent à corriger et à protéger la tête. Nylon 11 Powder, imprimée à l'aide de l'imprimante 3D Fuse 1+ 30W pour le frittage sélectif par laser (SLS), peut être utilisée pour les composants extérieurs rigides. À l'intérieur, TPU 90A Powder peut être utilisé pour une couche par couche de matelassage.
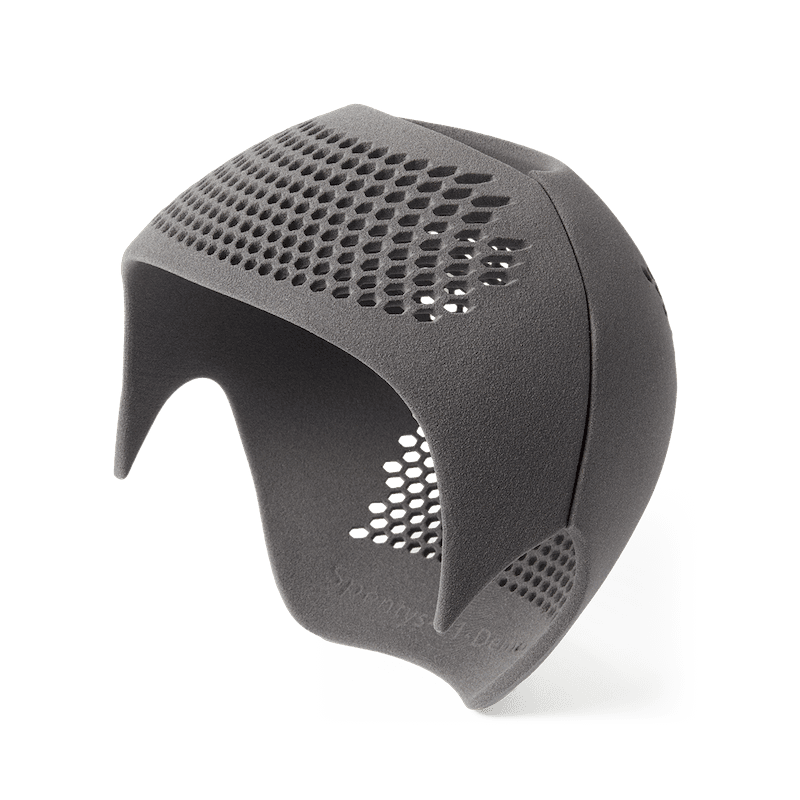
Un casque de remodelage du crâne imprimé en TPU 90A Powder.
Masques de protection du nez : Les résines de protection du nez ou du visage sont souvent prescrites après une fracture du nez ou d'une autre partie de l'anatomie faciale. L'impression 3D SLS de Nylon 11 Powder peut être utilisée pour imprimer des masques de protection du nez. Les masques transparents, souvent demandés pour des raisons esthétiques, peuvent être imprimés avec l'impression 3D stéréolithographique (SLA). Si vous imprimez avec le SLA, BioMed Durable Resin est une option transparente et résistante aux chocs pour les imprimantes 3D Form 3+/3L.
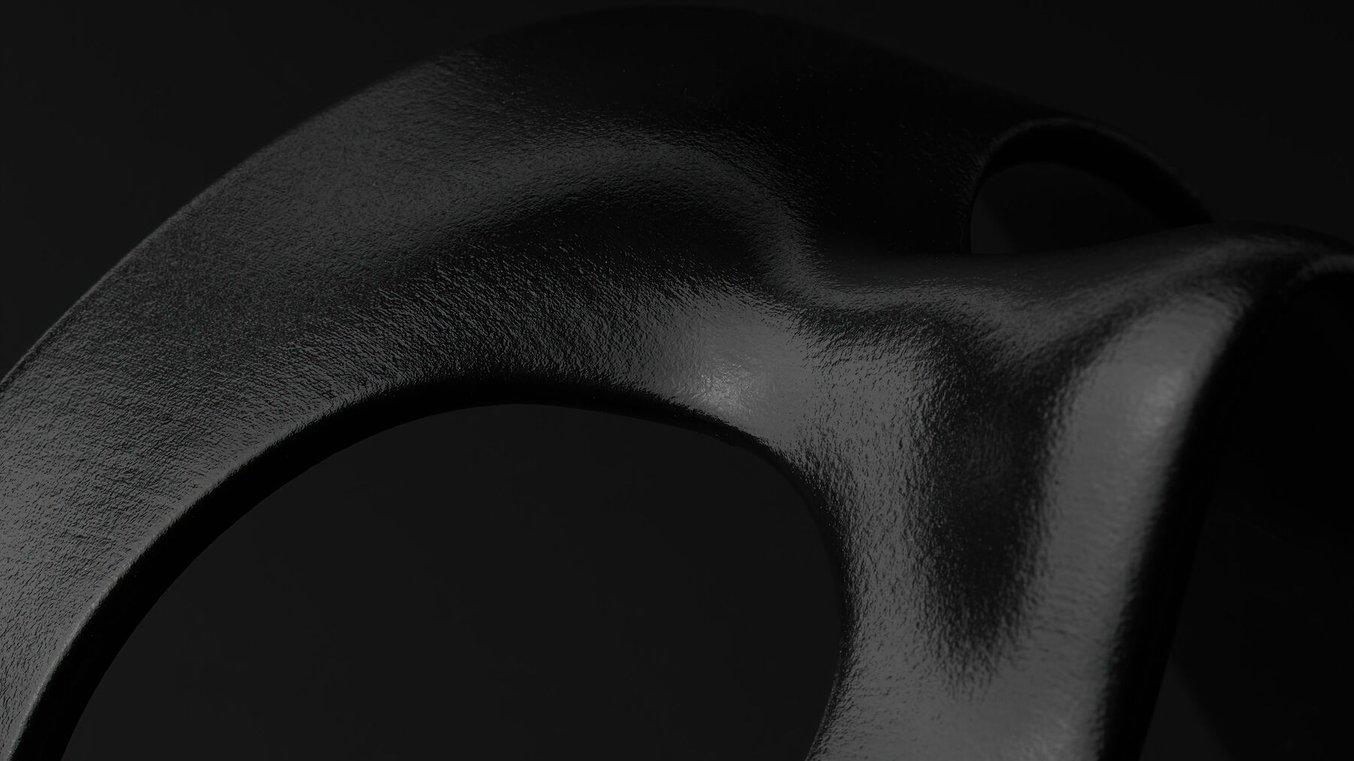
Gros plan d'un masque de protection nasale imprimé avec Nylon 11 Powder qui a fait l'objet d'un post-traitement par lissage à la vapeur.
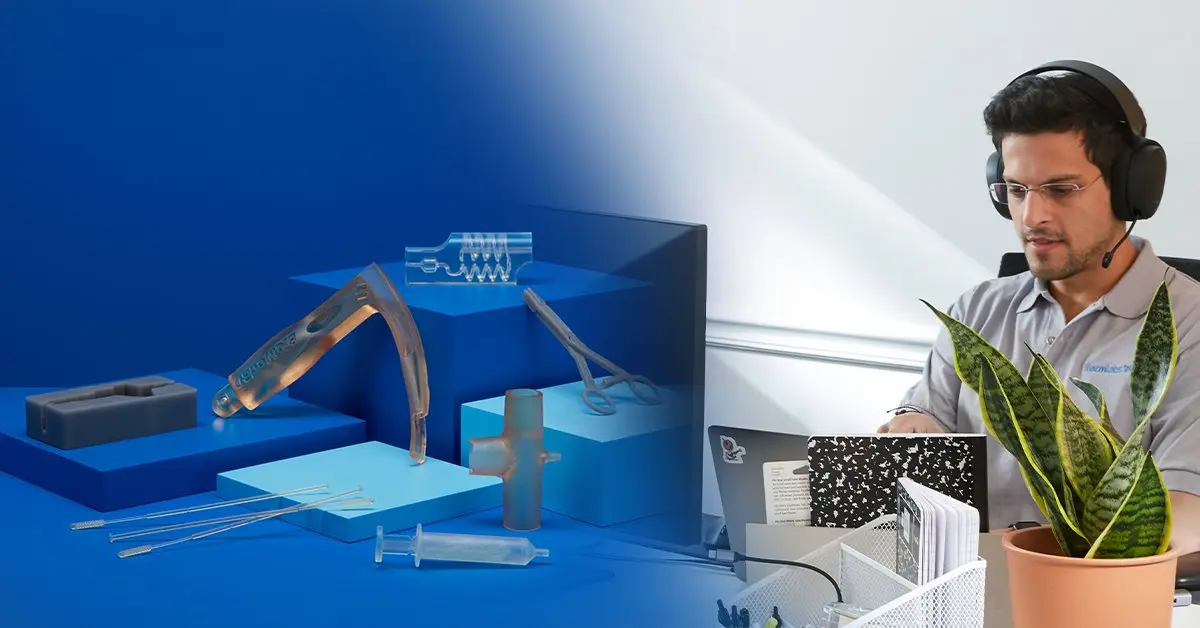
Discutez avec notre équipe commerciale médicale
Que vous deviez fabriquer des outils chirurgicaux adaptés aux patients ou un prototype de dispositif médical cardiaque, nous sommes là pour vous aider. L'équipe médicale de Formlabs est composée de spécialistes dévoués qui savent exactement comment vous soutenir et répondre aux besoins de votre entreprise.
Flux numériques pour la fabrication d'orthèses personnalisées grâce à l'impression 3D
La fabrication d'orthèses personnalisées à l'aide de l'impression 3D nécessite un scanner 3D, un logiciel CAO et une imprimante 3D avec un matériau compatible. Il existe toute une série d'options pour chacune d'entre elles, en fonction du type d'orthèse, du volume de production, des utilisations prévues, du flux de travail, de l'espace et de l'investissement initial. Cependant, l'utilisation de l'impression 3D pour créer des orthèses personnalisées est maintenant plus accessible que jamais.
1. Le scan
La première étape pour créer des orthèses imprimées en 3D est une capture d'image ou un scan de l'anatomie spécifique du patient. Ces données anatomiques sont ensuite traduites en un modèle 3D numérique, qui peut être utilisé pour concevoir l'orthèse.
Par rapport aux processus traditionnels de prise d'empreinte et de création de modèles, la numérisation 3D offre une grande précision, une vitesse de capture accrue, une réduction de la main-d'œuvre et une grande souplesse dans le choix des lieux de capture. Plusieurs fabricants de scanners numériques proposent des solutions pour créer des orthèses imprimées en 3D. Les scanners 3D destinés aux applications orthopédiques couvrent une large gamme de prix et de technologies, notamment le LiDAR, la numérisation 3D en charge, l'infrarouge et le laser. En savoir plus sur les options disponibles spécifiquement pour les semelles orthèses dans ce guide.
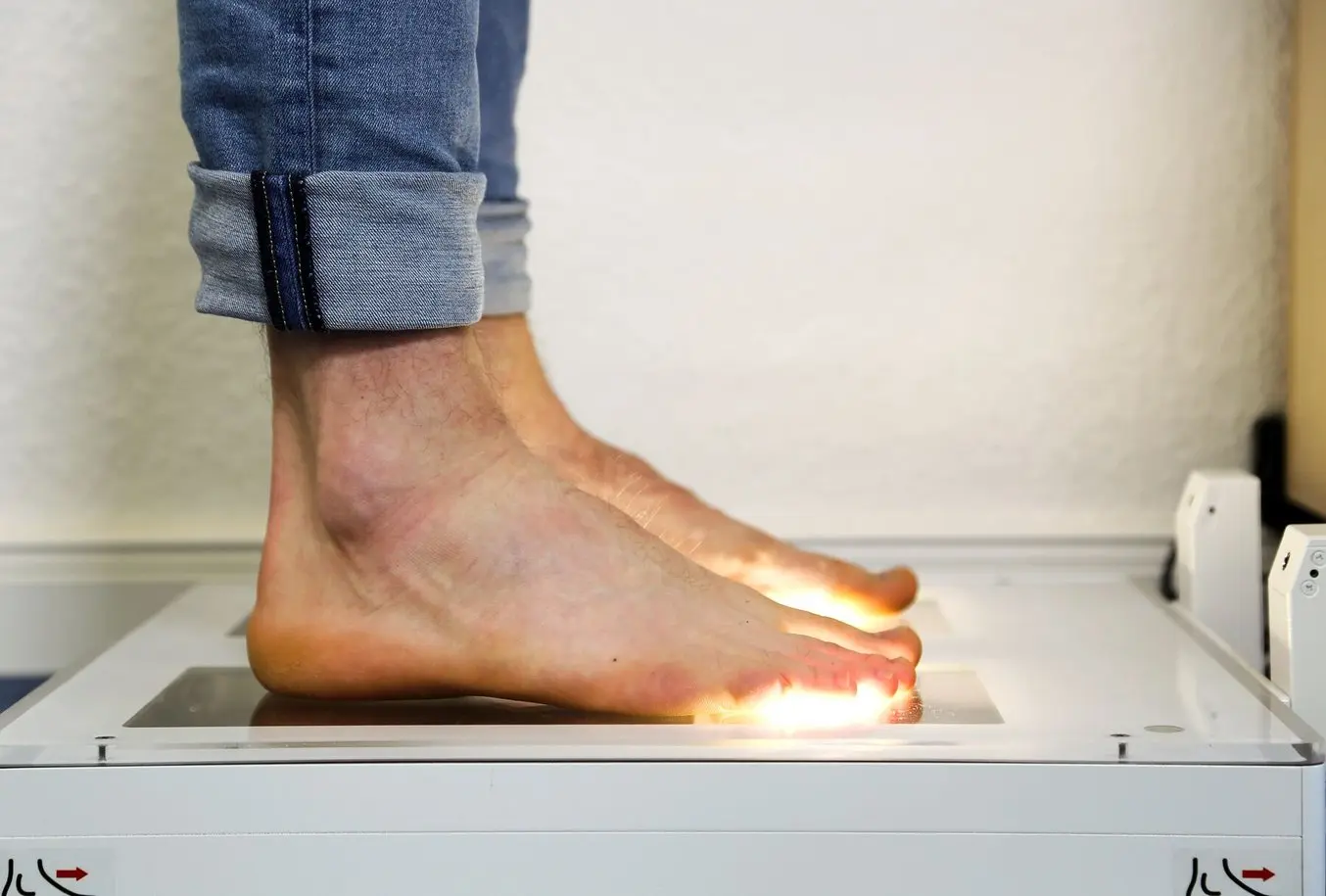
La numérisation 3D permet de prendre une empreinte plus précise et plus complète du pied que les méthodes traditionnelles.
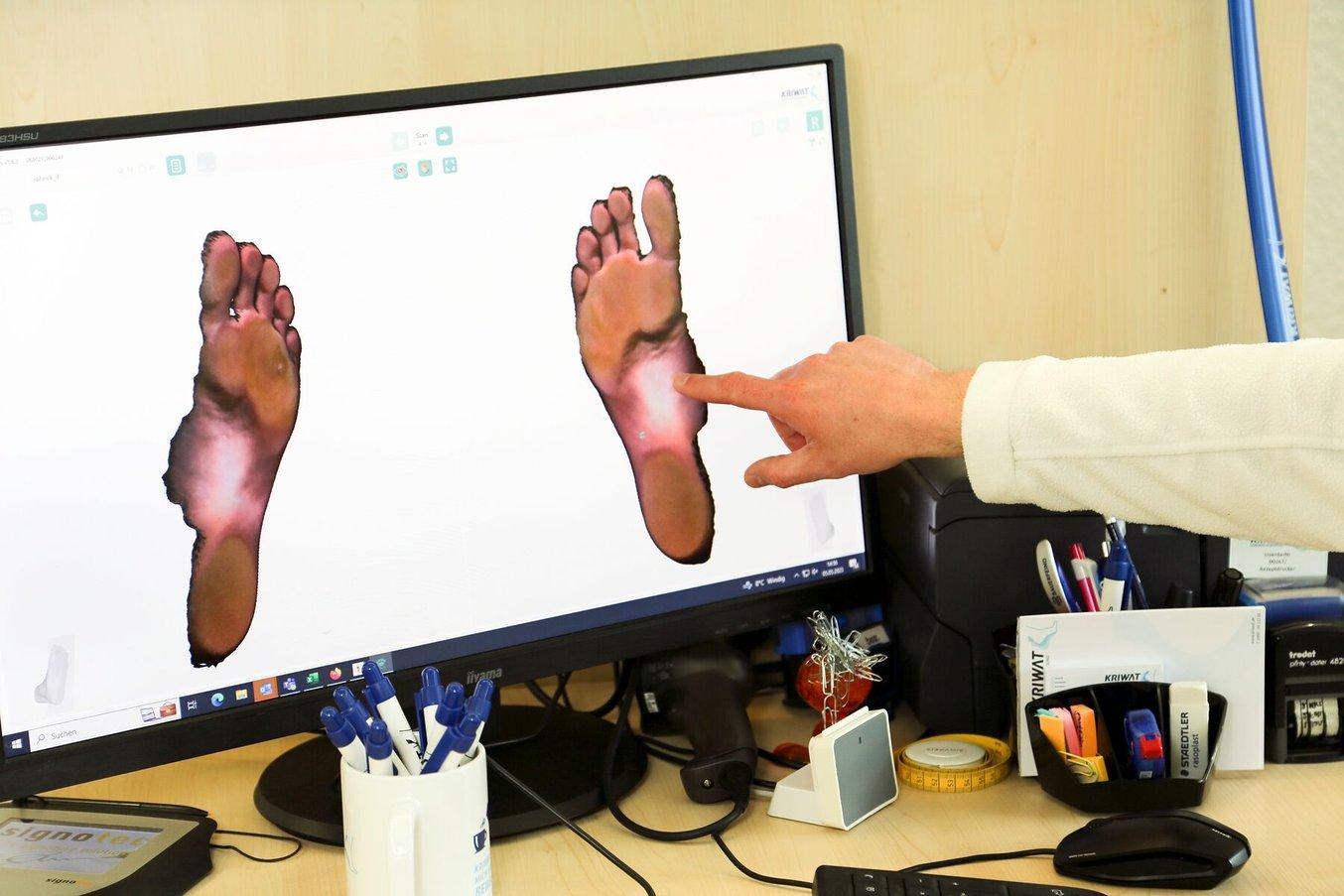
Le scan permet d'envoyer facilement les données sous forme numérique pour la conception et l'impression.
2. Modélisation numérique
Une fois que le scan a capturé les données requises, un modèle précis doit être développé à l'aide d'un logiciel CAO ou FAO. Divers modèles de logiciels peuvent être utilisés pour la conception en fonction de l'application et sont disponibles auprès de plusieurs fournisseurs. Axés sur la précision, la facilité d'utilisation et la personnalisation, certains de ces programmes permettent de concevoir une orthèse en quelques minutes. Pour en savoir plus sur les différents programmes de CAO disponibles pour la conception spécifique des semelles orthèses, lisez notre guide.
Dans la plupart des cas, les données acquises doivent être modifiées par des réparations de maillage afin d'élaborer des modèles imprimables en 3D pour l'étape suivante du processus de personnalisation. Une fois la conception terminée, elle est enregistrée sous forme de fichier .STL, .OBJ ou .3MF et importée dans un logiciel PreForm pour la préparation à l'impression.
Pour optimiser le flux de travail, plusieurs orthèses peuvent être imprimées en une seule fois, en fonction de leurs dimensions et de leur orientation.
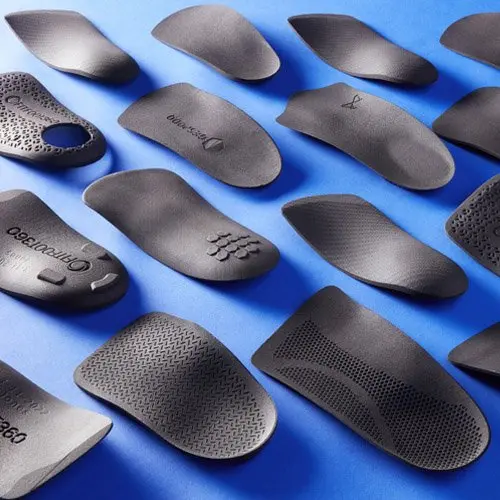
Impression 3D de semelles rigides
Découvrez comment produire des semelles intérieures solides et ductiles dépassant les 4 millions de cycles de pliage grâce à l'écosystème SLS compact et abordable de Formlabs. Ce guide complet vous aidera à vous lancer dans la production d'enveloppes de semelles sur la Fuse 1+ 30W.
3. Impression 3D d'orthèses
Les fournisseurs de services orthopédiques et de santé peuvent tirer parti des diverses techniques d'impression 3D disponibles pour produire des dispositifs finis. L'application de la pièce finale, sa dimension, son volume de production et la complexité de sa conception sont quelques-uns des critères importants à prendre en compte lors du choix d'une technologie d'impression.
Pour les orthèses personnalisées imprimées en 3D, l'impression 3D SLS est une solution de qualité et rentable. Les imprimantes SLS ont la capacité d'imprimer plusieurs dispositifs en un seul lot et disposent d'une large gamme de matériaux biocompatibles, y compris des options flexibles et rigides. Avec le SLS, il est possible de produire des orthèses durables et des géométries complexes avec une grande précision. Contrairement à d'autres types d'impression 3D, le SLS ne nécessite pas de structures de support et a permis d'optimiser le flux de travail de bout en bout, de la configuration aux pièces terminées.
L'impression 3D par fusion multijet (MJF) est une alternative similaire au SLS. Bien qu'elle produise des pièces de haute qualité, elle a des coûts d'investissement initiaux beaucoup plus élevés que le SLS, ce qui signifie qu'elle n'est accessible qu'aux plus grands laboratoires et fabricants d'orthèses.
Pour certaines applications, notamment l'intérieur des casques de moulage crânien ou lorsqu'un masque de protection nasale transparent est nécessaire, on a souvent recours à l'impression 3D SLA. Enfin, le dépôt de fil fondu (FDM) est une technique d'impression 3D peu coûteuse qui peut être utilisée pour le prototypage, mais qui n'a pas la durabilité requise pour les orthèses d'utilisation finale.
Adressez-vous à un expert en impression 3D pour découvrir la technique la mieux adaptée à vos objectifs.
Sélection des matériaux pour l'impression 3D d'orthèses
Lors de la sélection des matériaux pour les orthèses imprimées en 3D avec le SLS, des propriétés spécifiques doivent être prises en compte en fonction de l'application et des besoins du patient, notamment la durabilité, la flexibilité, l'élasticité et la rigidité. Deux matériaux de la gamme de matériaux Formlabs, TPU 90A Powder et Nylon 11 Powder, sont idéaux pour la production d'orthèses.
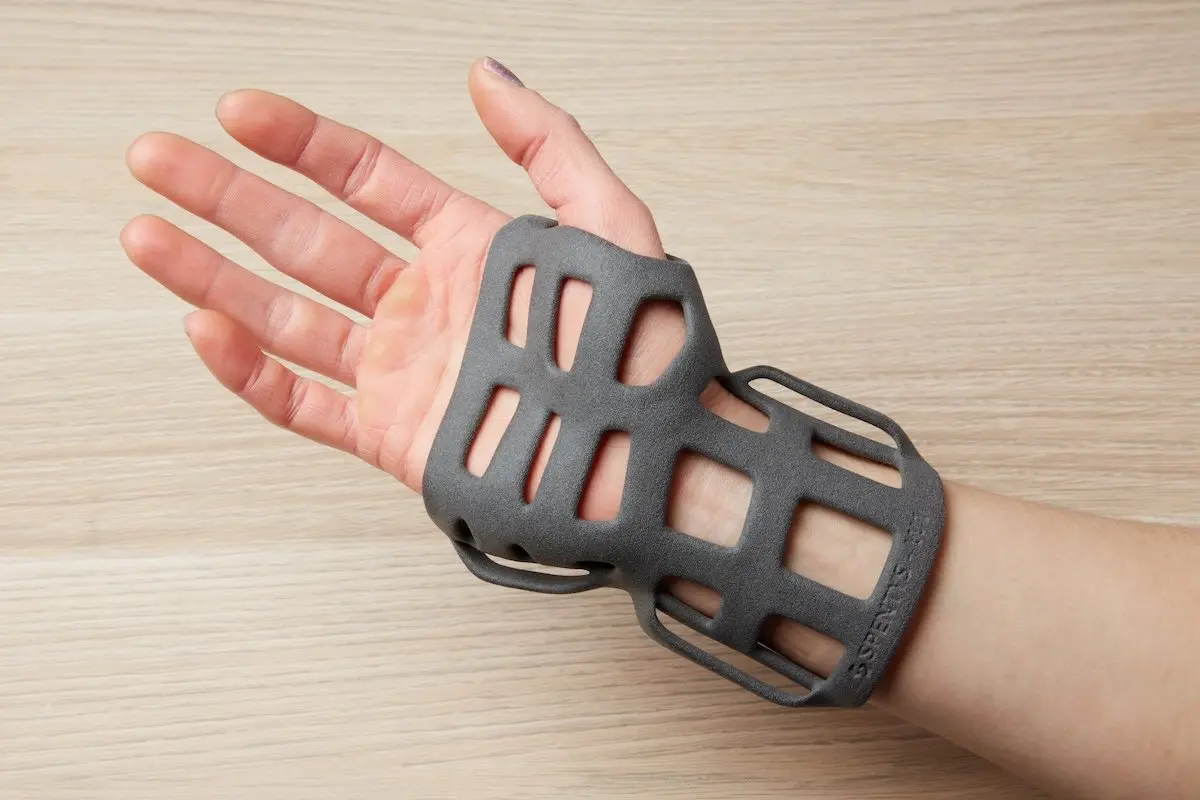
Une orthèse de poignet imprimée sur l'imprimante 3D SLS Fuse 1+ 30W.
TPU 90A Powder est un élastomère flexible qui combine une résistance à la déchirure et un allongement à la rupture élevés avec la liberté de conception et la durabilité de l'impression 3D SLS. Le TPU, ou polyuréthane thermoplastique, est un thermoplastique élastomère couramment utilisé. Dans les orthèses, ce matériau sûr pour la peau est souvent utilisé dans les cas suivants :
- Composants et dispositifs médicaux d'utilisation finale, prototypes
- Orthèses et tiges de prothèse
- Objets de technologie portable
- Casques de remodelage crânien
Nylon 11 Powder est un matériau idéal pour imprimer des semelles rigides, y compris des semelles partielles, avec une rigidité, une ductilité élevée et une stabilité à long terme sur la Fuse 1+ 30W. En outre, les pièces imprimées avec Nylon 11 Powder sont écologiquement stables, absorbent très peu d'humidité et présentent une résistance à la lumière, à la chaleur et aux produits chimiques. Certifiées biocompatibles, les orthèses imprimées avec Nylon 11 Powder peuvent entrer en contact avec la peau, ce qui en fait un matériau idéal pour les masques de protection du nez. Ce matériau durable et sûr pour la peau est souvent utilisé pour les orthèses et dispositifs médicaux suivants :
- Semelles athlétiques et correctives
- Orthèses de la cheville et du pied
- Résines de masquage
- Gouttières
- Composants et dispositifs médicaux d'utilisation finale, prototypes
Pour démontrer la résilience de Nylon 11 Powder, les semelles Formlabs imprimées avec celle-ci ont été comparées à des semelles en polypropylène fabriquées de manière traditionnelle. Les semelles Formlabs ont fait preuve d'une durabilité et d'une résistivité exceptionnelles en cas d'utilisation intensive, tout en maintenant une rigidité constante. Lors d'un essai dynamique de flexion en 3 points, les semelles Formlabs imprimées avec Nylon 11 Powder ont survécu à l'équivalent de 10 959 pas par jour pendant 365 jours, ce qui dépasse de loin les pas effectués par un adulte moyen. Pour voir les résultats complets de l'analyse des performances mécaniques, téléchargez le livre blanc.
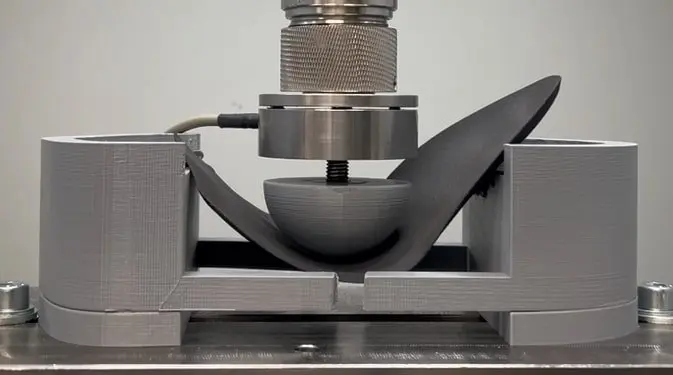
Analyse des performances mécaniques de semelles rigides imprimées en 3D et fabriquées de manière traditionnelle
Cette étude compare les propriétés mécaniques et les méthodes de fabrication utilisés pour produire des semelles orthopédiques personnalisées : la Fuse 1+ 30W de Formlabs et Nylon 11 Powder, HP 3D High Reusability PA 11, et un polypropylène fabriqué de façon traditionnelle.
4. Finition et post-traitement
Les orthèses imprimées en 3D nécessitent un post-traitement, et elles sont aussi souvent assemblées avec des composants du commerce, comme des couvercles et des coussinets. Les processus de post-traitement varient en fonction du type d'impression et de la finition désirée. Des sangles, des rembourrages et du tissu peuvent également être ajoutés en fonction des exigences de l'orthèse finale.
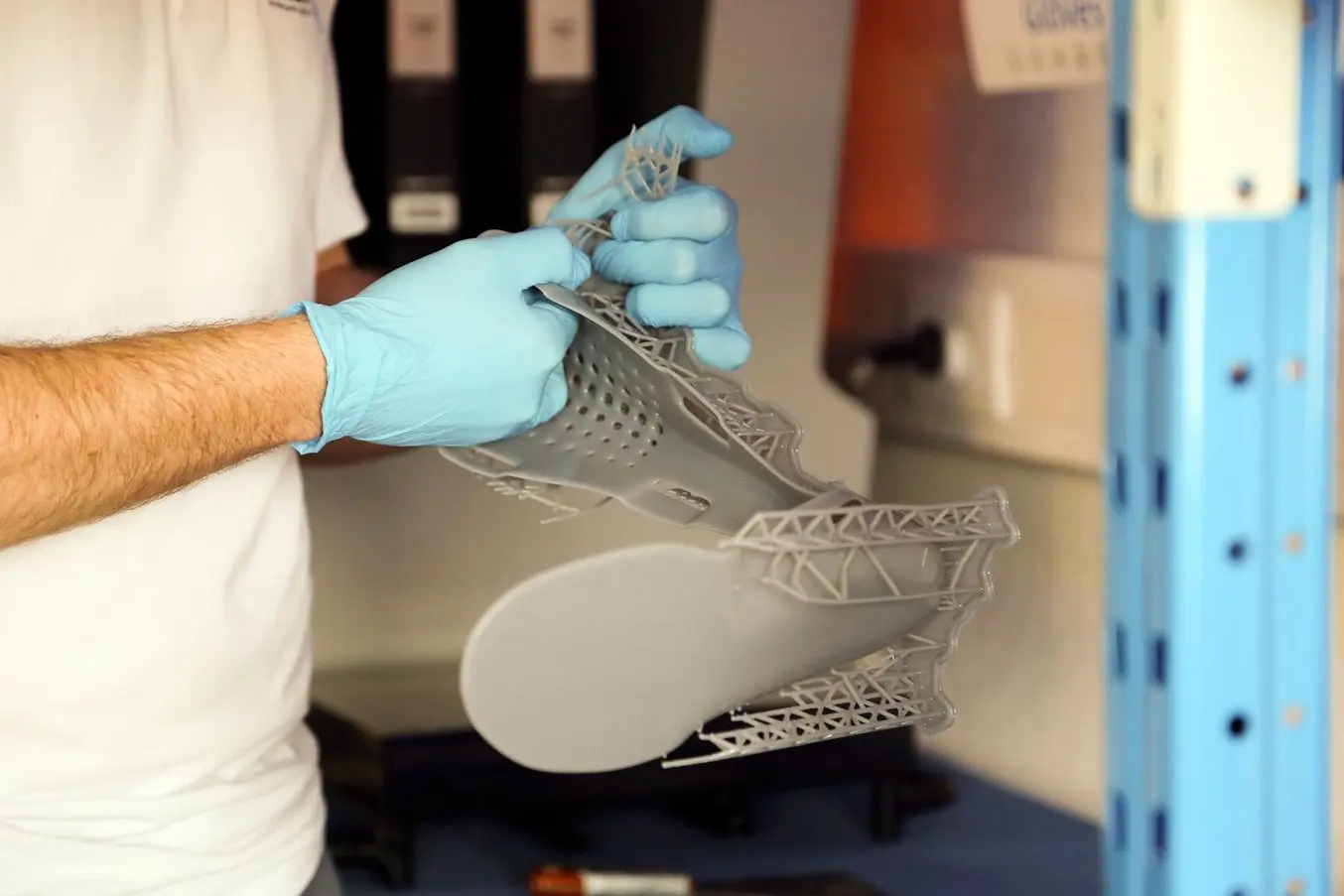
Retrait des supports d'une orthèse imprimée sur une imprimante 3D SLA Form 3BL.
Les orthèses imprimées en SLA sont lavées dans de l'IPA avant que les supports imprimés ne soient retirés. Les pièces sont ensuite polymérisées pendant une durée déterminée en fonction de la résine utilisée pour l'impression. Explorez les instructions complètes de post-traitement pour les imprimantes SLA Form 3+/3BL ici.
Pour l'impression 3D SLS avec la Fuse 1+ 30W, la Fuse Sift offre un système complet de gestion de la poudre, qui dispose d'une ventilation et qui filtre la poudre excédentaire. Les pièces finies sortent de la Fuse Sift avec une surface légèrement rugueuse, idéale pour les additifs de collage et les solutions de revêtement, qui peuvent être ajoutés pour créer le produit fini.
Pour une solution de nettoyage et de polissage entièrement automatisée, la Fuse Blast permet un nettoyage automatique ou manuel, le nettoyage automatisé permettant d'obtenir des pièces propres au toucher en seulement 10 minutes. La fonction automatisée ne demande aucune intervention et comprend des routines préprogrammées pour rendre la production encore plus facile. Une fonction de polissage supplémentaire permet également d'obtenir une finition lisse des pièces.
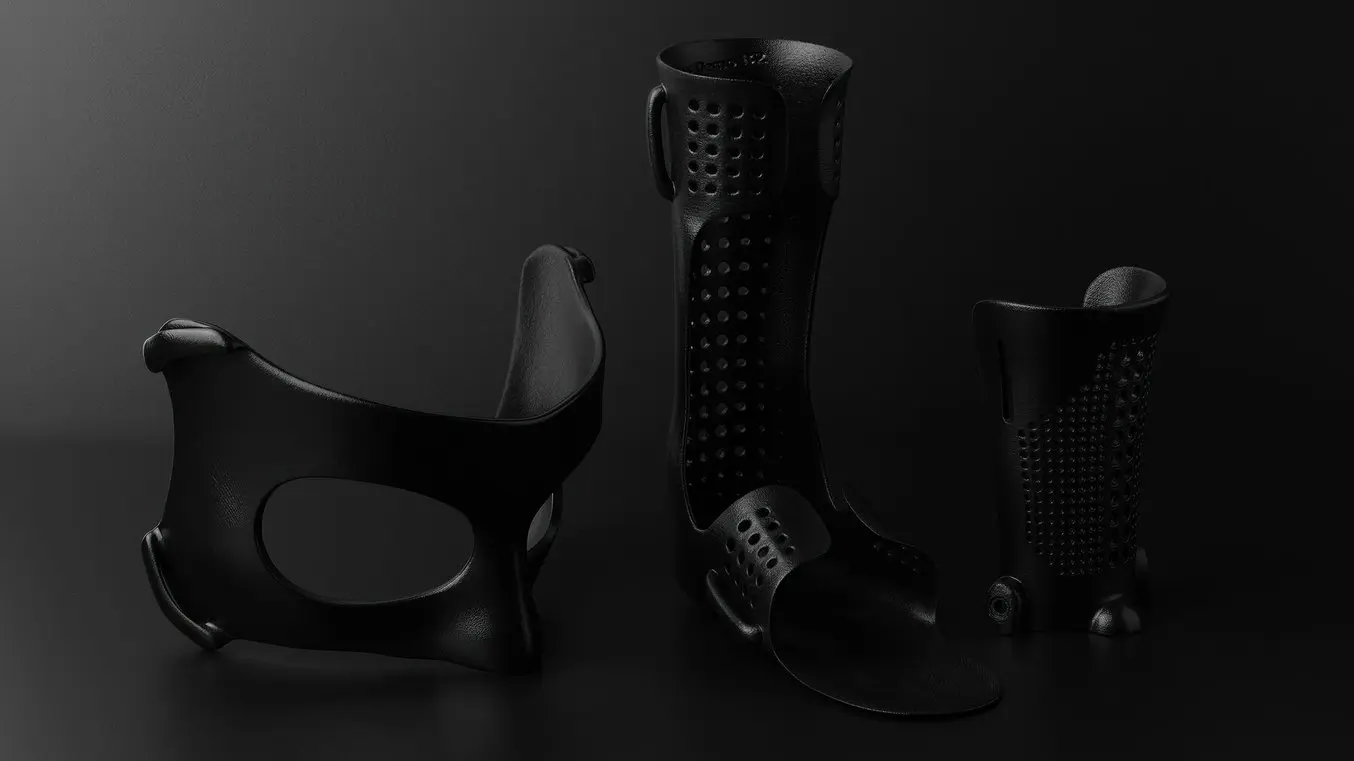
Orthèses imprimées avec Nylon 11 Powder qui ont été finies avec un lissage à la vapeur.
Pour les orthèses qui nécessitent une finition de surface lisse, le lissage à la vapeur est une étape de post-traitement courante pour les pièces imprimées en 3D par SLS qui permet d'améliorer la porosité et de réduire la rugosité. Le lissage à la vapeur réduit aussi considérablement le frottement superficiel que peuvent ressentir les patients portant des orthèses. Ce processus chimique consiste à exposer la surface d'une pièce imprimée en 3D SLS à une vapeur de solvant. Grâce au lissage à la vapeur, les pièces SLS peuvent atteindre une qualité de surface et une durabilité comparables à celles des pièces moulées par injection, sans parler de la réduction de la prolifération des bactéries et de l'absorption de l'humidité.
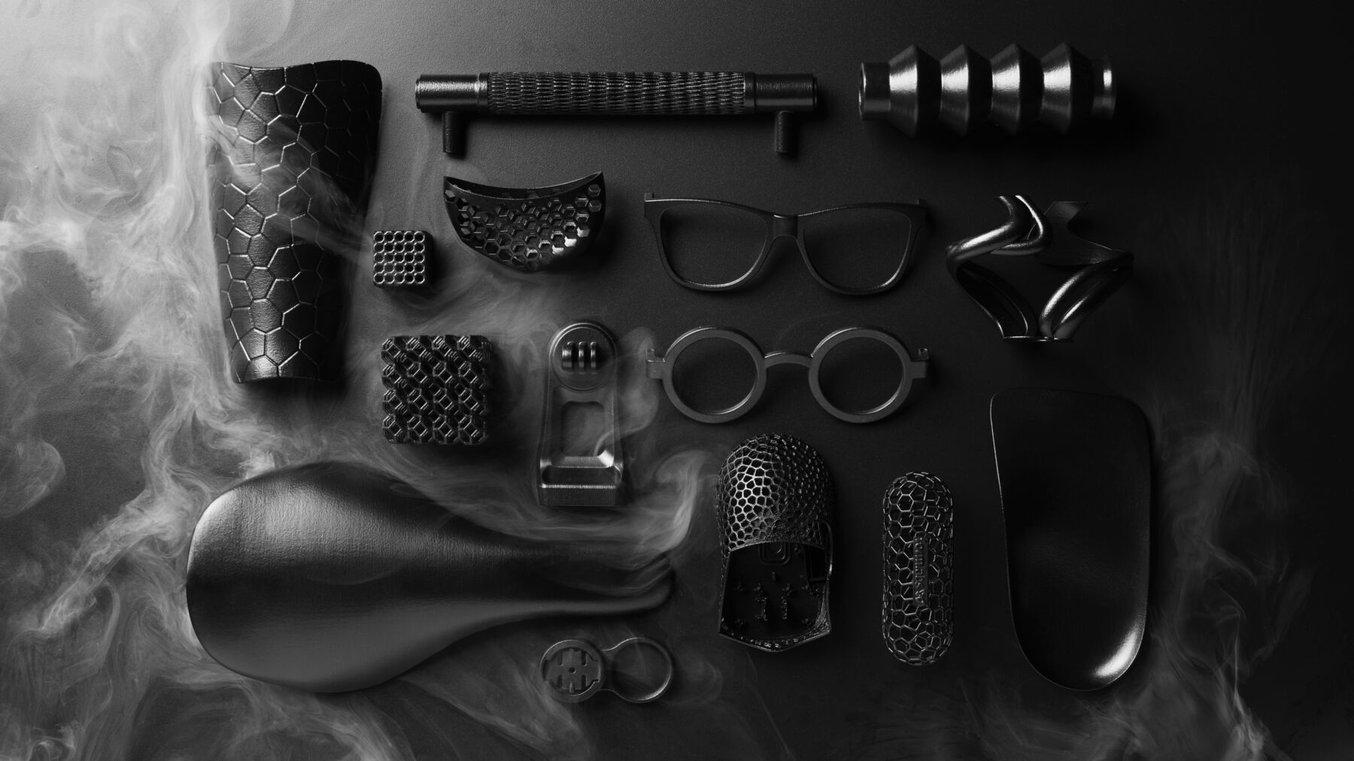
Améliorer la qualité de surface des pièces imprimées en 3D par SLS grâce au lissage à la vapeur : une étude collaborative de Formlabs et AMT
Dans ce livre blanc, nous passerons en revue les étapes à suivre et les avantages du lissage à la vapeur, nous présenterons les résultats des tests effectués avec les poudres SLS de Formlabs et le système de lissage à la vapeur d'AMT.
Se lancer avec des orthèses imprimées en 3D
L'impression 3D a révolutionné la conception des orthèses, permettant de produire des orthèses spécifiques aux patients avec des flux de travail optimisés qui permettent d'économiser du temps et des ressources. Pour les patients, cela signifie moins de rendez-vous, des délais de fabrication rapides et une personnalisation précise pour un confort accru, le tout à un coût inférieur à celui des méthodes traditionnelles de production d'orthèses sur mesure. Pour les orthoprothésistes et les fabricants, les processus de travail en 3D enregistrent des gains de temps et de ressources tout en permettant un environnement de travail plus confortable.
L'impression 3D SLS a fait ses preuves en tant que méthode fiable et efficace de fabrication d'orthèses et l'imprimante 3D SLS Fuse 1+ 30W de Formlabs associe la puissance industrielle à un flux de travail abordable et accessible. Comme il s'agit d'une imprimante SLS compacte, la Fuse 1+ 30W peut facilement s'ajuster à un espace de production existant. En outre, la gamme de matériaux de la Fuse 1+ 30W comprend Nylon 11 Powder, un matériau résistant et flexible qui reproduit fidèlement les propriétés des orthèses finales actuelles, et TPU 90A Powder, un matériau sûr pour la peau.
Vous souhaitez en savoir plus ? Pour un aperçu complet des flux de travail numériques et de l'impression 3D dans le secteur des orthèses et des prothèses, téléchargez notre livre blanc ou adressez-vous à un expert Formlabs pour trouver la solution qui vous convient.