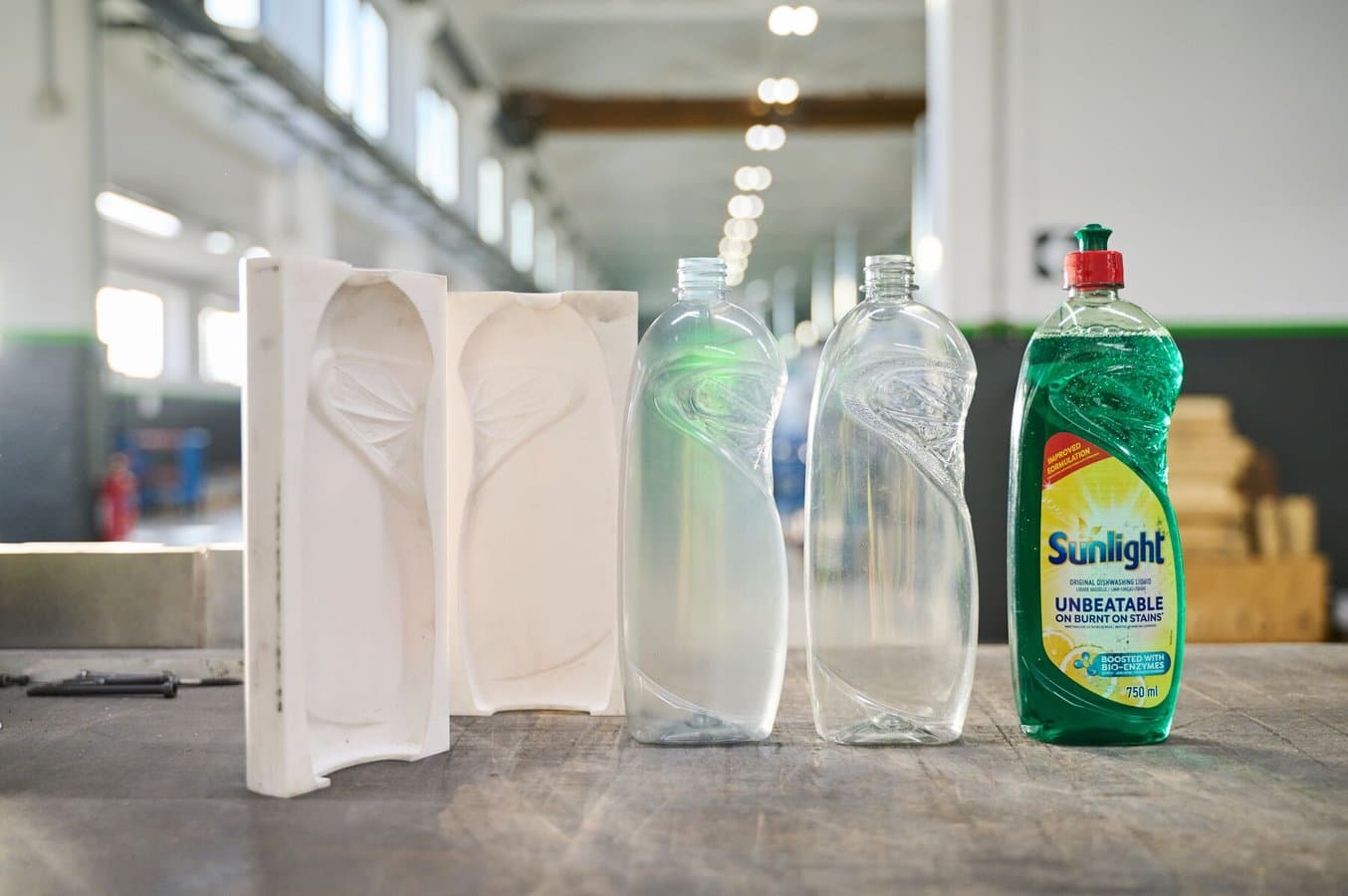
En tant que procédé de fabrication moderne conçu pour la production à grande échelle de corps creux en plastique, le moulage par soufflage existe depuis 1938, lorsque les inventeurs américains Enoch Ferngren et William Kopitke ont déposé un brevet pour un « dispositif pour le moulage de corps creux en plastique organique. » Cependant, les principes du moulage par soufflage existent depuis au moins le 1er siècle avant J.-C., lorsque le soufflage du verre s'est développé dans la Syrie antique. Aujourd'hui, l'impression 3D et d'autres technologies de fabrication avancées améliorent l'efficacité du moulage par soufflage du plastique et le rendent plus accessible à une grande variété de fabricants.
Les trois principaux types de moulage par soufflage – extrusion-soufflage (EBM), injection-soufflage (IBM) et injection-étirage-soufflage (ISBM) – consistent tous à gonfler une préforme plastique chauffée pour qu'elle prenne les contours du moule qui l'entoure. Si l'EBM permet généralement d'obtenir le coût le plus bas par pièce, l'IBM et l'ISBM sont capables de fabriquer des produits plus complexes et d'atteindre des objectifs fonctionnels que les pièces produites par EBM ne peuvent pas atteindre. En particulier, l'ISBM est souvent utilisé pour fabriquer des produits qui nécessitent des degrés élevés de résistance et de clarté.
Cet article fournit une description détaillée des différents types de procédés de moulage de plastique par soufflage, des polymères les plus couramment utilisés pour les produits moulés par soufflage et de la manière dont vous pouvez vous lancer dans le moulage par soufflage.
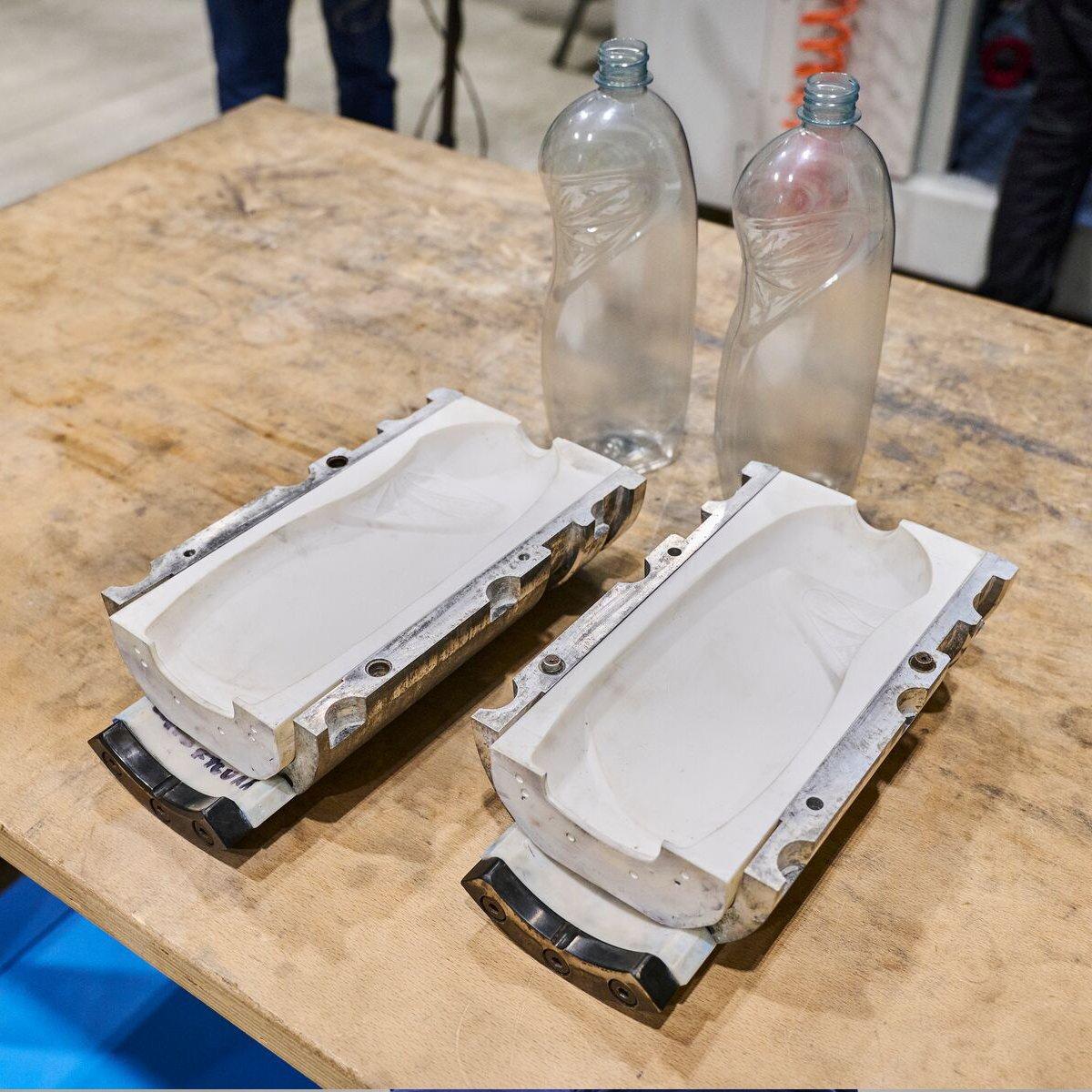
Moulage par étirage-soufflage rapide de petites séries avec des moules imprimés en 3D
Ce livre blanc fournit des méthodes et des lignes directrices pour l'utilisation de moules imprimés en 3D SLA dans le processus de moulage par étirage-soufflage afin de réduire les coûts et les délais pendant la préproduction. Des considérations de conception au flux de travail en passant par les conditions de moulage, nous vous présentons une étude de faisabilité menée par les experts du secteur Unilever et Serioplast.
Qu'est-ce que le moulage par soufflage ?
Le moulage par soufflage est un procédé de fabrication industrielle utilisé pour créer des pièces creuses en plastique. De nombreuses industries utilisent le moulage plastique par soufflage, notamment l'industrie automobile (par exemple pour les réservoirs, les assemblages d'admission et les conduits, etc.) et l'industrie agricole, pour les conteneurs en vrac, les pièces d'irrigation et les réservoirs de fluides. Mais l'utilisation la plus connue du moulage par soufflage est sans doute l'industrie de l'emballage. Ce procédé y est utilisé pour fabriquer des bouteilles en plastique et d'autres contenants pour différents produits allant de l'eau aux produits cosmétiques jusqu'aux produits de nettoyage.
Le moulage par soufflage de plastique est une méthode fiable et abordable pour créer des pièces en plastique à grande échelle. Comme pour de nombreux procédés de fabrication, les coûts initiaux de démarrage peuvent être élevés, de sorte que le moulage par soufflage ne devient souvent rentable que lorsqu'un fabricant doit produire des milliers d'exemplaires d'une même pièce. Si certaines méthodes permettent une plus grande complexité que d'autres, le moulage par soufflage est probablement le plus efficace pour les formes creuses à parois minces.
Par rapport au moulage par injection, le moulage par soufflage du plastique a généralement un coût d'outillage inférieur. De même, de nombreux matériaux différents peuvent être moulés par soufflage, ce qui en fait un procédé approprié pour une grande variété d'applications.
Pour la production en petite série et la conception itérative de produits, les appareils dont les coûts d'acquisition sont moins élevés et qui offrent une plus grande flexibilité de conception, comme les imprimantes 3D, sont donc généralement plus adaptés. Toutefois, certains leaders de l'industrie commencent à utiliser les deux technologies dans leurs processus de fabrication en concevant des moules de soufflage à l'aide d'imprimantes 3D stéréolithographiques, ce qui permet de réduire le coût de l'outillage et d'améliorer la qualité du produit final.
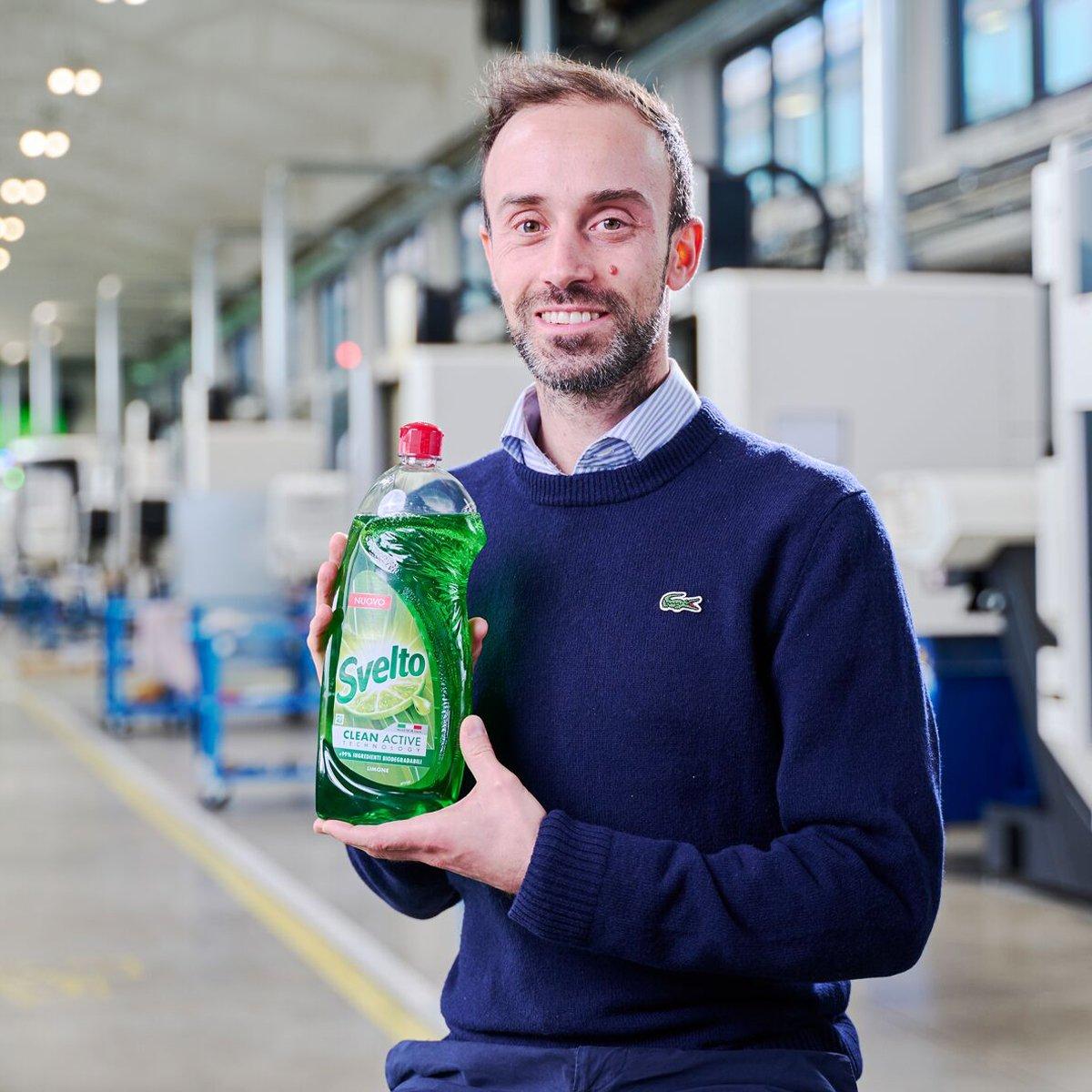
Réduisez les coûts et les délais pour les tests d'emballages moulés par soufflage
Dans ce webinaire, l'expert en moulage par soufflage Flavio Migliarelli vous présentera le processus de travail étape par étape et vous expliquera les principaux avantages et domaines d'application des moules imprimés en 3D pour le moulage par étirage-soufflage.
Comment fonctionne le moulage par soufflage ?
Dans le processus de moulage par soufflage, de l'air sous pression est injecté par une buse dans une préforme en plastique chauffée, qui se dilate pour épouser les contours d'un moule. Grâce à ce processus, une fine paroi en plastique est formée dans la forme d'un moule, laissant une cavité creuse. Le plastique est ensuite refroidi jusqu'à ce qu'il n'ait plus besoin du moule pour conserver sa forme. Enfin, le moule est retiré, l'excédent de plastique est découpé et la qualité de la pièce en plastique est testée avant la livraison.
1. Chauffage des préformes
La façon dont une préforme est créée diffère selon les trois principaux procédés de moulage par soufflage : EBM, IBM et ISBM. Cet article décrit ces différences en détail dans la section « Types de procédés de moulage par soufflage ».
Une fois la préforme créée, elle doit être chauffée à une température spécifique qui lui permet de conserver son intégrité lorsqu'elle est remplie d'air sous pression. Selon le procédé et le type de plastique, la préforme peut déjà être chauffée à une température qui lui permet de se dilater pour s'adapter au moule. Dans d'autres cas, des outils tels que des bandes chauffantes et des anneaux chauffants sont utilisés pour amener la préforme dans la plage de température thermoélastique.
La température appropriée varie en fonction du matériau, de la méthodologie et du produit fini souhaité. Le polyéthylène téréphtalate (PET), un matériau souvent utilisé pour créer des récipients pour boissons, est généralement chauffé à environ 100 °C. Pour obtenir une épaisseur de paroi constante et éviter d'endommager le produit final, il est très important de veiller à ce que la préforme soit chauffée de manière homogène.
2. Moulage
Une fois que la préforme est malléable, de l'air sous pression est envoyé par une buse. Comme un ballon, la préforme se gonfle jusqu'à ce que les fines parois en plastique épousent les contours de la cavité. Les moules peuvent donner à la bouteille des formes et des textures différentes et inclure des logos et des lettres. Comme pour d'autres types de moulage, notamment le moulage par compression et le moulage par injection, les moules de soufflage permettent à l'excès de plastique de s'échapper du moule afin d'éviter l'accumulation de pression et de garantir des résultats cohérents.
L'air comprimé doit être fourni à un rythme constant, permettant à la préforme de se dilater sans fissurer ni se déchirer. Des moules plus complexes peuvent augmenter le temps de production par pièce, ce qui entraîne une augmentation des coûts.
3. Refroidissement et solidification
Une fois le corps creux créé, celui-ci doit être refroidi jusqu'à ce qu'il ne soit plus dans la zone thermoélastique afin qu'il conserve sa forme après le démoulage. Par conséquent, un système de refroidissement efficace et performant peut avoir un impact important sur l'efficacité de tout processus de moulage par soufflage.
Comme pour le chauffage et le moulage, le refroidissement et la solidification doivent être effectués de manière uniforme pour éviter les dommages. En outre, un refroidissement trop rapide peut entraîner des déformations et des défauts dans la pièce finie. De nombreuses machines de moulage par soufflage utilisent de l'air comprimé réfrigéré et/ou des canaux de refroidissement des fluides pour accroître l'efficacité du processus de moulage par soufflage.
4. Démoulage et post-traitement
Lorsque la température est tombée en dessous de la plage thermoélastique, le corps creux peut être démoulé et transféré vers une ligne de production où il peut être dégonflé, découpé, testé pour détecter d'éventuelles fuites, soumis à un contrôle de qualité et emballé pour l'expédition.
Dans de nombreuses chaînes de fabrication modernes, le démoulage et le post-traitement, y compris le découpage et la vérification de l'étanchéité, peuvent être presque entièrement automatisés, même si des modèles particulièrement grands ou personnalisés peuvent nécessiter une finition manuelle. Toutefois, la surveillance humaine reste un élément essentiel de la plupart des processus de moulage par soufflage, tant pour le contrôle de la qualité que pour l'emballage final.
Types de procédés de moulage par soufflage
Il existe trois principaux types de moulage par soufflage : le moulage par extrusion-soufflage (EBM), le moulage par injection-soufflage (IBM) et le moulage par injection-étirage-soufflage (ISBM). Les principales différences entre ces trois types résident dans la manière dont la préforme en plastique est formée.
Extrusion-soufflage (EBM)
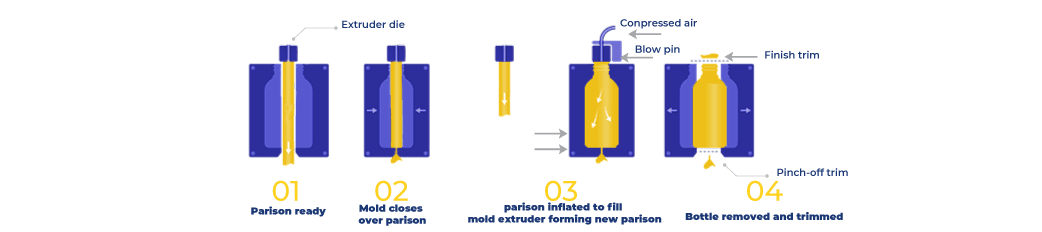
Source : GAP Polymers
Le moulage par extrusion-soufflage (EBM), le type de moulage par soufflage le plus courant, est également le plus simple et le moins coûteux. Cependant, les produits créés par EBM sont généralement limités en termes de complexité structurelle et de détails.
Dans l'EBM, le plastique fondu est poussé à travers une extrudeuse, ce qui forme un tube creux : la préforme. Le moule se referme ensuite autour de la préforme. Ensuite, de l'air sous pression est utilisé pour gonfler la préforme jusqu'à ce qu'elle remplisse complètement la cavité du moule, en épousant les contours intérieurs du moule.
Une fois la préforme entièrement gonflée, le processus de refroidissement et de solidification a lieu, souvent avec l'aide de canaux de refroidissement fluides ou d'air comprimé. Toutefois, l'EBM étant le type de moulage par soufflage le plus élémentaire, certaines machines EBM s'appuient simplement sur un refroidissement naturel.
Le moulage par extrusion-soufflage est souvent utilisé avec le polyéthylène (PE), un plastique populaire pour les réservoirs agricoles, les bouteilles de liquides automobiles (tels que l'huile de moteur et le liquide de refroidissement), les bouteilles de shampoing et de nombreux autres produits courants. L'EBM est également la méthode la plus courante de moulage par soufflage du nylon.
Outre la complexité structurelle et le niveau de détail limités, il peut également être difficile d'atteindre l'épaisseur de paroi requise pour le produit. Dans de tels cas, les fabricants sont contraints de se tourner vers IBM ou ISBM. Cependant, pour de nombreuses applications telles que les récipients simples et les bouteilles, l'EBM est suffisant.
En outre, bien que l'EBM ne permette qu'un taux de gonflement petit à moyen, la pièce finale produite par EBM peut être assez grande, ce qui en fait la méthode préférée pour la production de produits tels que les fûts industriels, les caisses de transport et les réservoirs de carburant.
Moulage par injection-soufflage (IBM)
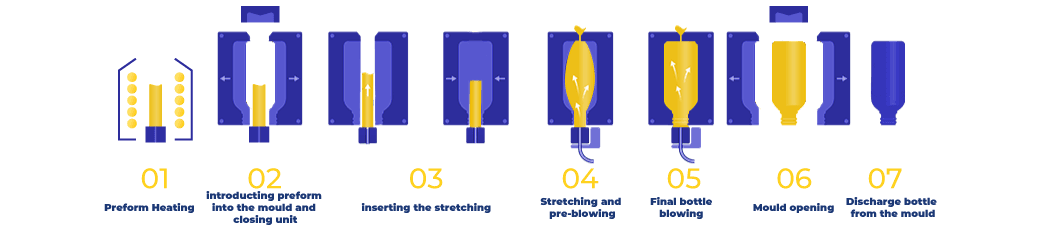
Source : GAP Polymers
Le moulage par injection-soufflage (IBM) combine le moulage par injection et le moulage par soufflage. Tout d'abord, la préforme est créée en injectant du plastique fondu dans un moule, puis en le refroidissant pour créer une préforme. La préforme est ensuite transférée dans la cavité du moule de soufflage, réchauffée et remplie d'air comprimé jusqu'à ce qu'elle se dilate pour remplir la cavité du moule de soufflage. À partir de là, le processus est très similaire à celui de l'EBM : le plastique moulé est refroidi, démoulé, découpé et expédié.
Toutefois, l'étape du moulage par soufflage ne nécessite pas toujours que la préforme soit chauffée à la même température que lorsqu'elle a été moulée par injection. Cela fait souvent du moulage par injection-soufflage le premier choix des fabricants travaillant avec des matériaux avec un long temps de séchage tels que le PET, un matériau que l'on trouve le plus souvent dans les bouteilles d'eau et de boissons gazeuses.
L'IBM est également mieux adapté que l'EBM pour les formes complexes ou les produits présentant des tolérances plus étroites (par exemple, les flacons de médicaments qui ont une tolérance stricte au niveau du col). Les fabricants des industries cosmétiques et pharmaceutiques sont donc susceptibles de se tourner vers le moulage par injection-soufflage en raison de sa précision accrue. Toutefois, en raison du processus en plusieurs étapes et de la complexité accrue de la conception, l'outillage peut être beaucoup plus coûteux et le temps total nécessaire pour chaque pièce dépasse généralement celui de l'EBM.
Moulage par injection-étirage-soufflage (ISBM)

Source : GAP Polymers
Comme l'IBM, le moulage par injection-étirage-soufflage (ISBM) permet d'obtenir des pièces plus complexes et une plus grande précision dimensionnelle que l'EBM. Souvent, surtout lorsqu'il s'agit de plastique PET, l'ISBM permet d'obtenir des détails encore plus précis et des caractéristiques de conception plus fines que l'IBM. En outre, certains procédés de fabrication de l'ISBM réduisent ou éliminent l'excès de plastique, ce qui permet de réduire les déchets et d'obtenir un produit fini plus lisse.
L'ISBM est très similaire à l'IBM en ce sens qu'il s'agit d'un processus en deux étapes qui commence par le moulage par injection pour créer la préforme. Cependant, une fois la préforme transférée dans le moule de soufflage et chauffée, une tige verticale est déployée pour étirer la préforme avant l'injection d'air sous pression. Cette étape supplémentaire cruciale permet à l'ISBM de produire des formes ovoïdes, carrées et polygonales avec lesquelles d'autres méthodes peuvent avoir des difficultés.
L'ISBM implique une étape supplémentaire par rapport à l'IBM : l'étirement. Il se traduit par des temps de traitement légèrement plus longs et, en moyenne, par les coûts d'outillage les plus élevés des trois principales méthodes de moulage par soufflage de plastique.
Matériaux de moulage par soufflage
Matériau | Caractéristiques | Coût | Module de flexion (approximatif)* | Température de fléchissement sous charge (TFC) (approximative)* | Applications |
---|---|---|---|---|---|
Polyéthylène haute densité (PEHD) | Translucide, dureté moyenne, facile à teindre | $ | 1170 MPa | 71 °C | Réservoirs agricoles, fûts industriels, mallettes de transport, bouteilles de liquide automobile, bouteilles de shampoing |
Polyéthylène basse densité (LDPE) | Translucide, doux à dureté modérée, facilement teintable | $$ | 275 MPa | 60 °C | Bouteilles à presser, défenses de bateau, film soufflé pour sacs en plastique |
Polyéthylène téréphtalate (PET) | Transparent, assez dur, facile à teindre, forte barrière à l'humidité | $$ | 3400 MPa | 79 °C | Bouteilles de boissons gazeuses et d'eau, boîtes en plastique |
Polypropylène (PP) | Translucide (mais certains mélanges peuvent être presque transparents), dureté modérée à dure, facilement teintable, stérilisable en autoclave | $ | 1030 MPa | 77 °C | Tubes pour l'automobile et l'électroménager, récipients alimentaires, bacs de stockage en plastique |
Polychlorure de vinyle (PVC) | Transparent (mais facilement teinté jusqu'à l'opacité), grande variabilité de la dureté, durable | $$ | 2300 MPa | 79 °C | Soufflets, cônes de signalisation, tuyaux, raccords |
Nylon (polyamide, PA) | Translucide, dureté modérée, solide, résistant aux chocs | $$$$ | 2900 MPa | 169 °C | Tubes et réservoirs automobiles |
Polycarbonate (PC) | Transparent, assez dur, facilement teinté, très résistant, résistant aux chocs | $$$ | 2350 MPa | 143 °C | Grandes bouteilles d'eau, récipients de stockage d'aliments, seringues |
Copolymère de cycline et d'oléfine (COC) | Transparent, dur, stérilisable en autoclave, forte barrière à l'humidité | $$$$ | 2480 MPa | 77 °C | Film soufflé, emballage sous film, seringues, stockage médical (alternative au verre) |
Acrylonitrile butadiène styrène (ABS) | Opaque, dur, solide, résistant aux chocs | $$$ | 2680 MPa | 88 °C | Boîtiers pour l'électronique, pare-chocs de voiture, mallettes de transport, tuyaux et flexibles |
*Les valeurs de TFC et de module de flexion dépendent des ingrédients spécifiques et du procédé de fabrication de chaque lot.
Développement de produits pour le moulage par soufflage avec l'impression 3D
En raison des coûts de démarrage élevés, des processus d'outillage compliqués et coûteux et du manque d'expertise en matière de fabrication, de nombreuses entreprises qui ont besoin de produire des pièces moulées par soufflage externalisent actuellement la conception et la production. Les moules eux-mêmes sont souvent fabriqués à partir d'alliages d'aluminium, de zinc ou d'acier, dont l'usinage est coûteux. Même si une entreprise externe est en mesure de créer des prototypes de moules, ces services de conception sont souvent coûteux et impliquent un long délai d'exécution, ce qui rend impossible un véritable prototypage itératif.
Grâce à l'impression 3D, les entreprises peuvent désormais concevoir des prototypes et des outils de moulage en interne, réduisant ainsi les coûts et les délais de développement d'emballages plastiques creux pour leurs produits. Si de nombreuses entreprises choisissent encore d'externaliser la production, l'impression 3D leur permet de mieux contrôler le produit fini, dans des délais plus courts et à un coût nettement inférieur.
Unilever s'est récemment tourné vers l'impression 3D pour réduire les coûts et accélérer le processus de conception des emballages plastiques. Avec leur partenaire de fabrication Serioplast, ils ont validé les moules imprimés en 3D pour le moulage par étirage-soufflage de petites séries en utilisant l'imprimante 3D stéréolithographique (SLA) Form 3L de Formlabs et Rigid 10K Resin de Formlabs.
« Avec le moule imprimé en 3D, nous pouvons économiser jusqu'à 70 % de temps et 90 % de coûts par rapport au moule standard. Auparavant, [les clients] devaient attendre jusqu'à 12 semaines pour un seul design, alors que maintenant nous pouvons en faire cinq.
Flavio Migliarelli, responsable de la conception R&D, Serioplast Global Services
Comme une imprimante 3D peut produire des pièces en quelques heures et que les moules ne coûtent qu'une fraction de l'outillage métallique, les entreprises disposent désormais d'un plus grand degré de contrôle lorsqu'il s'agit de développer des pièces creuses en plastique. Les modèles de moules peuvent être créés numériquement à l'aide de la CAO et exportés vers une imprimante 3D, qui peut produire un outillage rapide très détaillé en utilisant des matériaux suffisamment solides et résistants à la température pour être utilisés dans une machine de moulage par soufflage industrielle, ce qui permet aux entreprises de prototyper à la fois le moule et la pièce finie. Si une modification de la conception est nécessaire, les entreprises sont en mesure d'imprimer rapidement et à moindre coût le nouveau moule.
« On peut fabriquer une vraie bouteille avant de produire le moule final. On peut ainsi savoir immédiatement si l'on est sur la bonne voie en matière de développement ou si quelque chose doit être modifié pour éviter des erreurs qui pourraient nous coûter cher. »
Stefano Cademartiri, responsable CAO et prototypage, Unilever
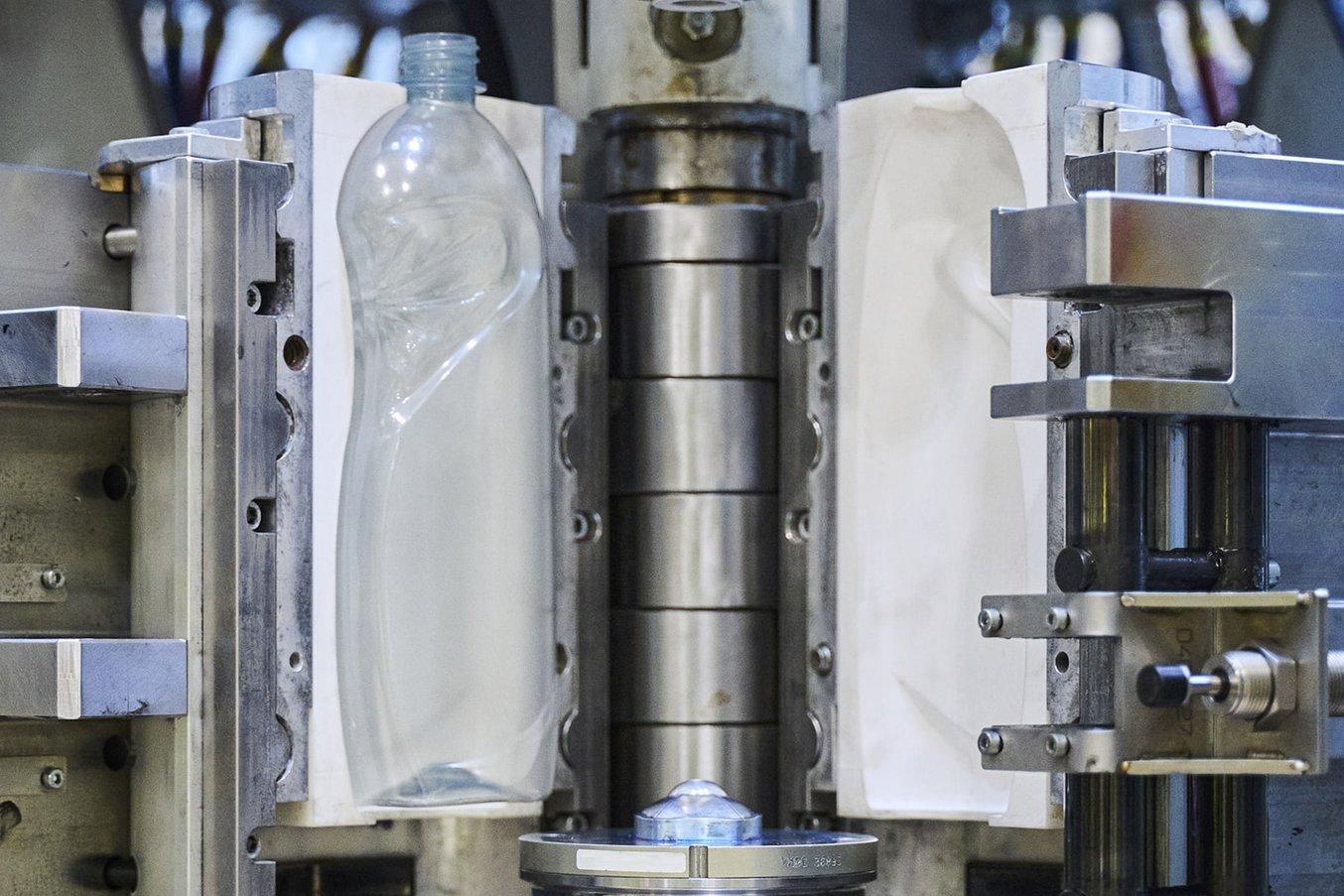
Moule imprimé en 3D avec Rigid 10K Resin pour la bouteille Unilever Slice 750 mL installé sur le porte-moule de la machine. Comme l'équipe peut utiliser la même fenêtre de processus qu'avec des moules pilotes standard, le processus final peut être vérifié de manière fiable.
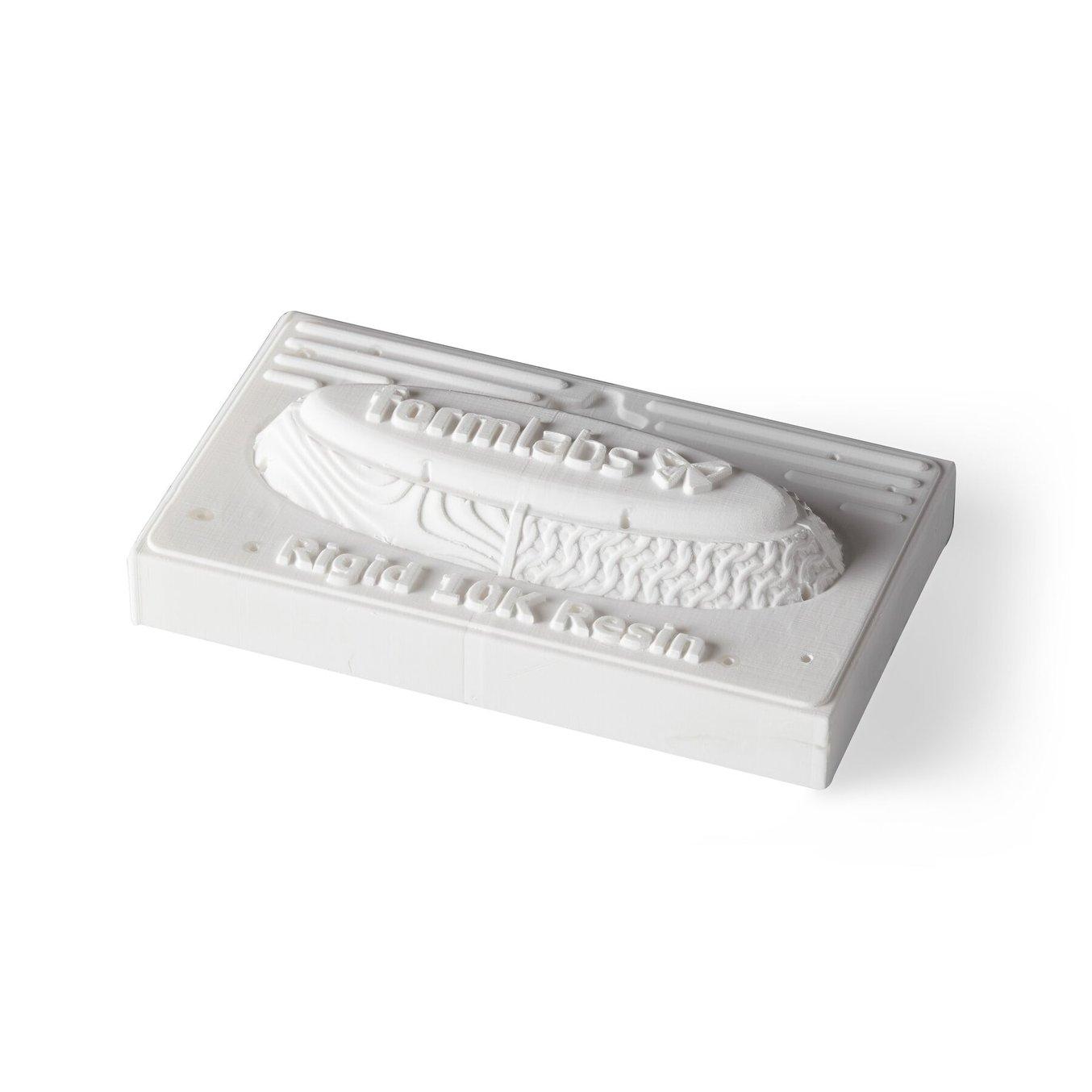
Commander un échantillon gratuit
Examinez et constatez par vous-même la qualité Formlabs. Nous enverrons un échantillon gratuit à votre bureau.
Débuter avec le moulage par soufflage
Le moulage par soufflage de plastique est un procédé de fabrication populaire utilisé dans un grand nombre de secteurs et qui permet d'utiliser un certain nombre de matériaux courants. Avec le moulage par soufflage, le plastique thermoélastique est étiré et mis en forme à l'aide d'air comprimé. Une fois qu'il a atteint la forme souhaitée, il est refroidi, post-traité et expédié au client.
Les matériaux les plus courants pour le moulage par soufflage sont le polyéthylène (PE), le polyéthylène téréphtalate (PET) et le polypropylène (PP). Sa large gamme de matériaux disponibles, son évolutivité et sa fiabilité font du moulage par soufflage l'un des principaux procédés de fabrication d'emballages, de conteneurs de stockage et de composants de machines, entre autres pour les industries des biens de consommation, de l'automobile, de l'agriculture, de la pharmacie et des cosmétiques.
Aujourd'hui, des technologies telles que l'impression 3D abaissent les barrières à l'entrée du moulage par soufflage pour les petits et les grands fabricants, principalement en permettant le prototypage itératif de moules. Les concepteurs de produits et les petits fabricants qui ont dû externaliser la conception et la production de moules de soufflage peuvent utiliser l'impression 3D en interne pour mieux contrôler le processus à un coût réduit.
En fonction de l'application, ceux qui se lancent dans le moulage par soufflage peuvent choisir entre le moulage par extrusion-soufflage (EBM), le moulage par injection-soufflage (IBM) et le moulage par injection-étirage-soufflage (ISBM). En général, l'EBM offre des délais d'exécution plus courts et une plus grande variété de tailles, tout en limitant le niveau de détail et la complexité de la conception. L'IBM permet un haut niveau de détail dans la conception, mais la taille de la pièce finale peut être limitée. L'ISBM, à son tour, peut offrir une plus grande variété d'options en ce qui concerne les formes. L'EBM a tendance à coûter moins cher que l'IBM et l'ISBM.
Vous voulez en savoir plus sur le moulage par soufflage avec des moules imprimés en 3D ? Téléchargez notre livre blanc pour obtenir des conseils détaillés sur l'utilisation de moules imprimés en 3D dans le processus de moulage par soufflage, ainsi qu'une étude de cas réelle approfondie avec Unilever et Serioplast.