Vingt mille lieues sous les mer : des boîtiers imprimés en 3D pour explorer les profondeurs océaniques
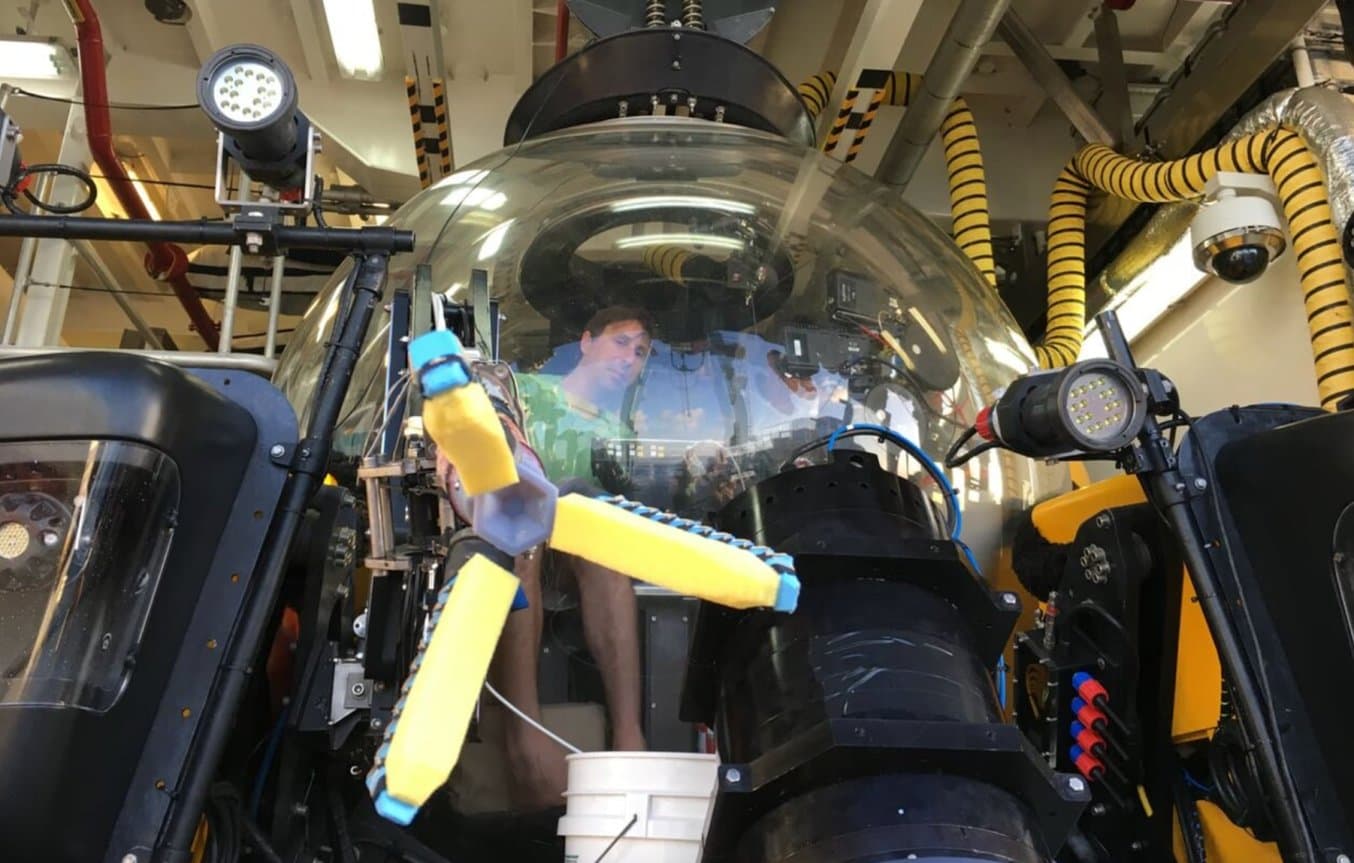
Brennan Phillips, chercheur principal du laboratoire de robotique en mer profonde de l'URI. Image credit David Gruber.
Les voyages dans l'espace suscitent toujours une grande ferveur dans le monde entier. Néanmoins, il existe encore sur notre planète une frontière que d'aucuns qualifient d'infranchissable. Malgré le fait que les océans couvrent plus de 70 % de la surface du globe, la National Oceanic and Atmospheric Administration (NOAA) estime que moins de 20 % de nos océans ont été entièrement explorés.1 Si on la compare à l'exploration spatiale, l'exploration des océans a été délaissée et sous-financée. Cependant, certains chercheurs persévèrent malgré ces difficultés, et se tournent vers l'impression 3D pour approfondir leurs recherches.
Au Undersea Robotics and Imaging Laboratory, qui fait partie du Bay Campus de l'université de Rhode Island, le professeur Brennan Phillips et ses étudiants construisent des outils capables d'effectuer des explorations des milliers de mètres sous la surface de l'océan. Grâce aux imprimantes stéréolithographiques (SLA) Form 3+ et Form 3L, le laboratoire imprime en 3D des boîtiers de caméra étanches et une grande variété d'outils de recherche.
Des pièces qui restent étanches sous pression
Pour cartographier les océans, il faut créer des outils qui soient non seulement étanches, mais qui le restent même sous l'immense pression exercée sous la surface de l'océan. M. Phillips et les étudiants du laboratoire ont commencé à concevoir un boîtier imprimé en 3D pour mettre au point une caméra capable de garder l'appareil complètement sec, même sous pression, et que l'on puisse facilement démonter pour récupérer les données par la suite. Après des dizaines d'itérations, l'équipe a opté pour ce design cylindrique imprimé en deux parties sur la Form 3+ avec Clear Resin. La structure interne du boîtier contient la carte de circuit imprimé et est remplie d'époxy, ce qui permet de suspendre l'objectif de l'appareil photo en l'air. Tout ce qui se trouve sous l'objectif est en époxy, qui est injecté par des trous intégrés dans le design du boîtier.
Le défi est le suivant : « Quelle est la caméra la plus petite et la moins chère que nous puissions fabriquer pour les grands fonds ? » Nous en avons donc imprimé des dizaines de formes différentes et, comme il s'agit d'un produit imprimable, nous pouvons lui donner la forme que nous voulons. Nous pouvons concevoir quelque chose rapidement, fabriquer les composants électroniques, optimiser la taille, puis couler l'époxy », explique M. Phillips.
L'impression 3D a permis au laboratoire de procéder à des itérations précises sans craindre de grever le budget, et a offert une plus grande souplesse de conception que ne le permettait l'usinage.
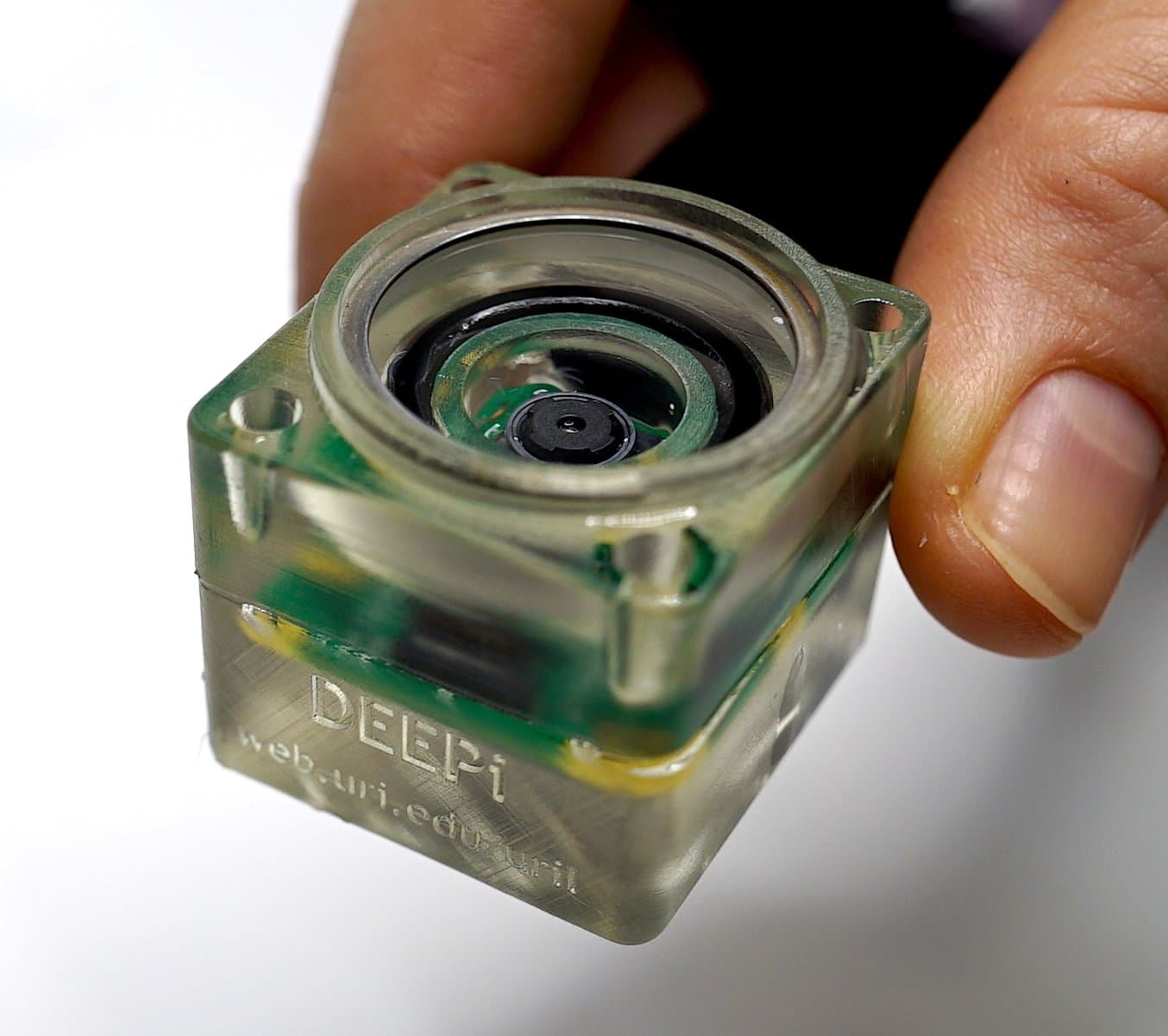
La caméra DEEPi utilise un moule hybride imprimé en 3D et un joint torique, ainsi qu'une partie remplie d'époxy pour les composants de la carte de circuit imprimé et un hublot externe en verre transparent (brevet américain n° 16/920 577) (Crédit photo : Brennan Phillips).
Le laboratoire utilise un réservoir sous pression pour simuler des environnements marins profonds. Après que M. Phillips et ses étudiants se sont mis d'accord sur le design en deux parties, ils ont placé les pièces dans une chambre à pression, puis augmenté la pression pour simuler un véritable environnement en eaux profondes. « Il s'agissait d'une expérience entièrement nouvelle : cela allait plus loin que nous ne l'avions jamais imaginé, à des milliers de mètres de profondeur », explique M. Phillips.
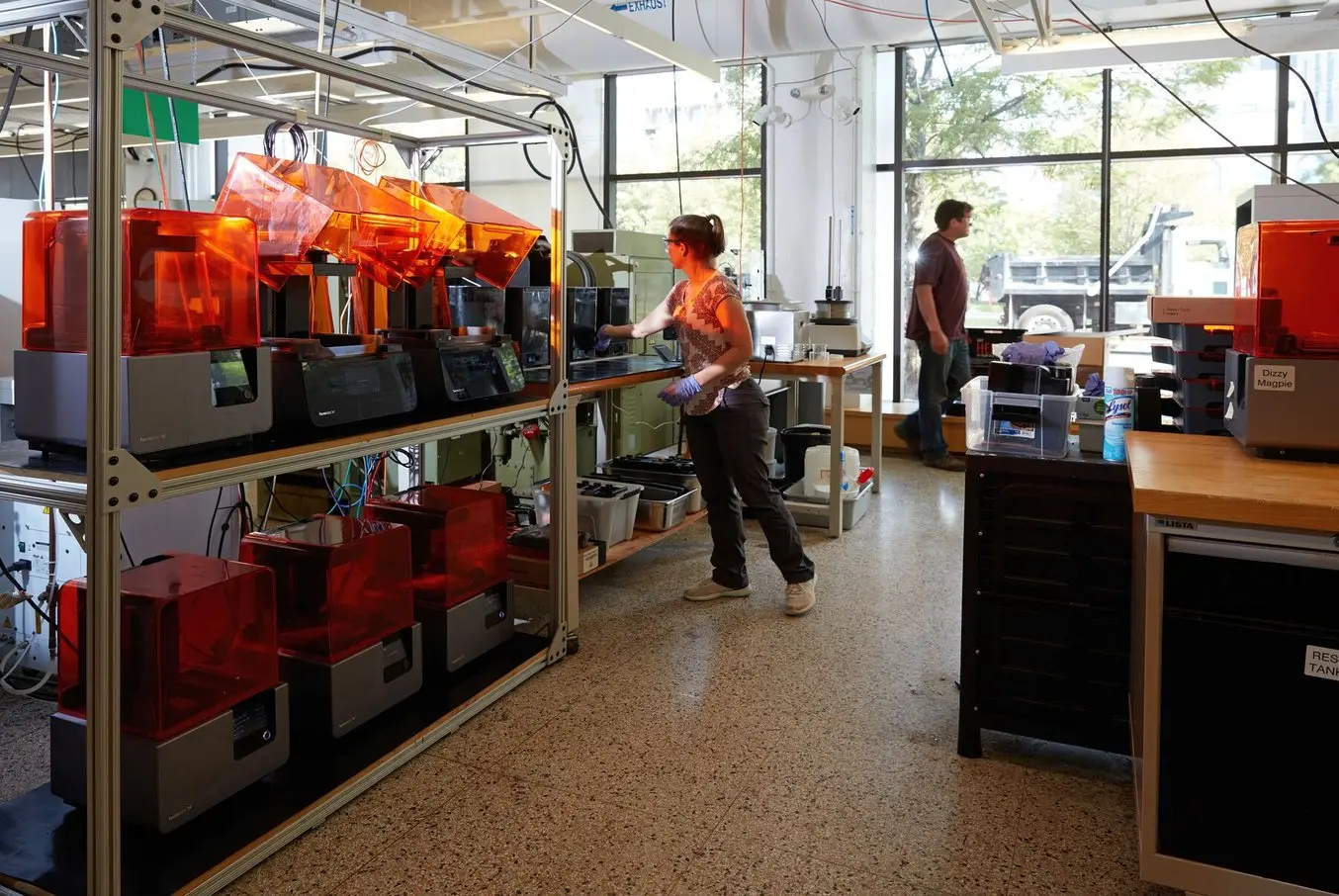
Prix spéciaux pour les organismes de formation
Les organismes de formation agréés peuvent bénéficier de tarifs spéciaux, qui comprennent une réduction de 10 % sur les imprimantes, le matériel et les accessoires sélectionnés, et un accès gratuit à Open Material Mode. Contactez Formlabs ou un revendeur agréé pour vérifier votre éligibilité.
Pourquoi le SLA est la solution idéale pour les robots en eaux profondes
Quand il a fallu choisir une imprimante 3D, la précision et les propriétés des matériaux étaient en tête de liste pour le laboratoire de M. Phillips. La nature isotrope des pièces imprimées en 3D par SLA signifie qu'elles ne sont pas poreuses et qu'elles ne fuient pas, comme cela peut être le cas pour les pièces imprimées par dépôt de fil fondu (FDM). Les finitions de surface lisses des pièces SLA garantissent également que les assemblages fonctionnels, tels que les boîtiers cylindriques en deux parties, peuvent s'emboîter sans qu'une surface rugueuse n'entraîne de fuites d'air. La précision et la haute résolution des pièces contribuent également à cette étanchéité. Des tolérances extrêmement serrées et des petites caractéristiques permettent aux utilisateurs d'imprimer des pas de vis directement dans le matériau, ce que le laboratoire de M. Phillips fait à la fois pour le boîtier en deux parties et pour les vis qui servent à renforcer la sécurité de la fixation.
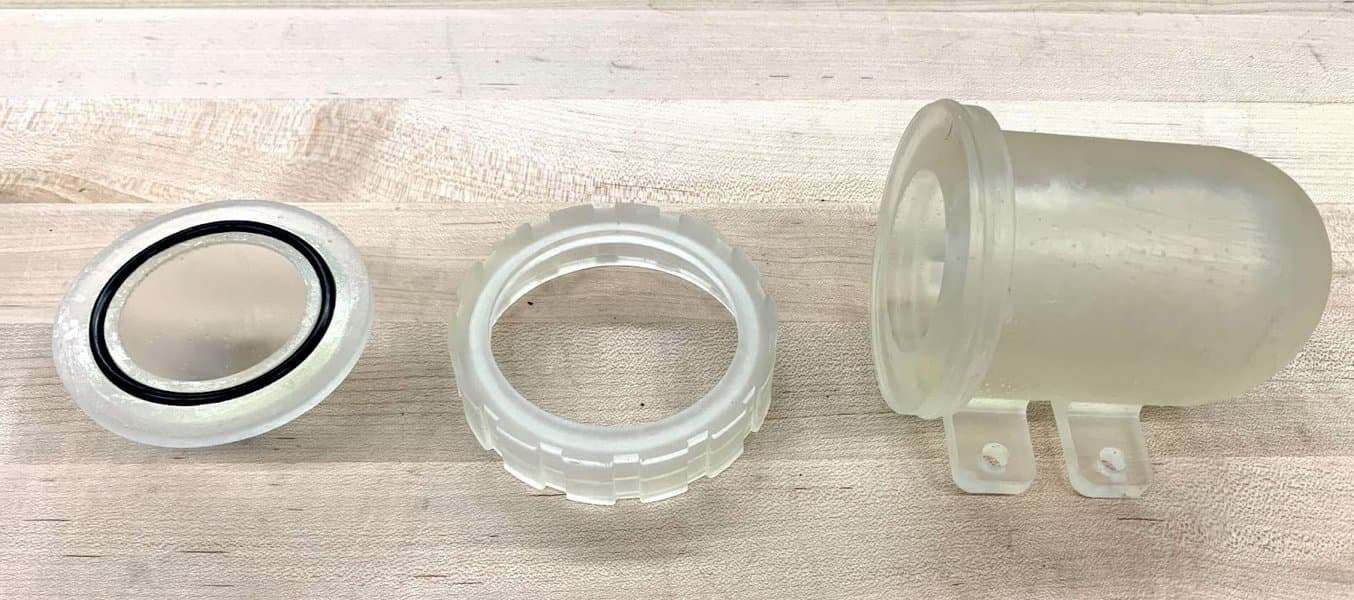
Un ensemble complet de boîtier imprimés en 3D, capable de protéger les composants électroniques de l'eau de mer à des profondeurs supérieures à 1000 mètres. Les joints toriques sont directement imprimés dans les pièces, et le boîtier est scellé à l'aide d'un cadran vissé à la main. Crédit photo et conception : Breanna Motsenbocker
« Avec le FDM, on pourrait peut-être obtenir un certain indice de protection IP, mais les pièces ne résisteraient pas au-delà de quelques mètres de pression. Deuxièmement, vous avez besoin d'une bonne résolution, afin que le joint torique entre les deux pièces soit parfaitement étanche. Quand ces pièces sortent de l'imprimante, nous avons juste à les poncer un peu. Comme nous les orientons de manière à ce que les surfaces importantes soient lisses, nous obtenons des joints parfaits », explique M. Phillips. « La troisième raison est que les propriétés des matériaux SLA sont bien supérieures : il n'y a généralement pas de comparaison possible. Ils sont bien meilleurs en termes de limite d'élasticité. Tous les modules sont tout simplement meilleurs que ceux des autres matériaux que nous avons testés. »
La précision et la disponibilité des matériaux des imprimantes de Formlabs ont permis au laboratoire de mettre au point ses boîtiers étanches pour les grands fonds et de prospérer sur terre comme dans les mers. En janvier 2020, M. Phillips et ses étudiants ont publié le procédé qu'ils ont utilisé en mer pour imprimer en 3D avec une plateforme de stabilisation installée sur la Form 2. Ils ont pu imprimer les mêmes boîtiers sans qu'il y ait de différence notable avec les pièces imprimées sur terre, ce qui signifie que ces dispositifs peuvent être imprimés et déployés sur des navires dans le monde entier. S'inscrivant dans la mission du laboratoire, qui consiste à démocratiser l'exploration sous-marine, cet article apporte la preuve que ces outils importants peuvent être fabriqués localement et à moindre coût.
Adopter la Form 3L
Lorsque Formlabs a annoncé le lancement de la Form 3L, M. Phillips et le laboratoire ont été parmi les premiers à s'y intéresser. « Nous avons été parmi les premiers à adopter la Form 3L », a déclaré M. Phillips. Le grand format de la Form 3L leur a permis d'expérimenter de plus grandes conceptions sous-marines et d'améliorer d'autres fonctions du laboratoire grâce à des outils de recherche innovants.
Pour déployer ces boîtiers et d'autres dispositifs sous-marins, le laboratoire doit utiliser et entretenir des milliers de mètres de câbles en fibre optique. Pour éviter les enchevêtrements ou les nœuds, ils ont d'abord utilisé des roues de vélo recyclées pour guider la fibre optique sur le côté d'un bateau. Mais grâce à leur imprimante SLA grand format, ils ont pu créer des prototypes pour réduire la taille et améliorer les performances de ce processus.
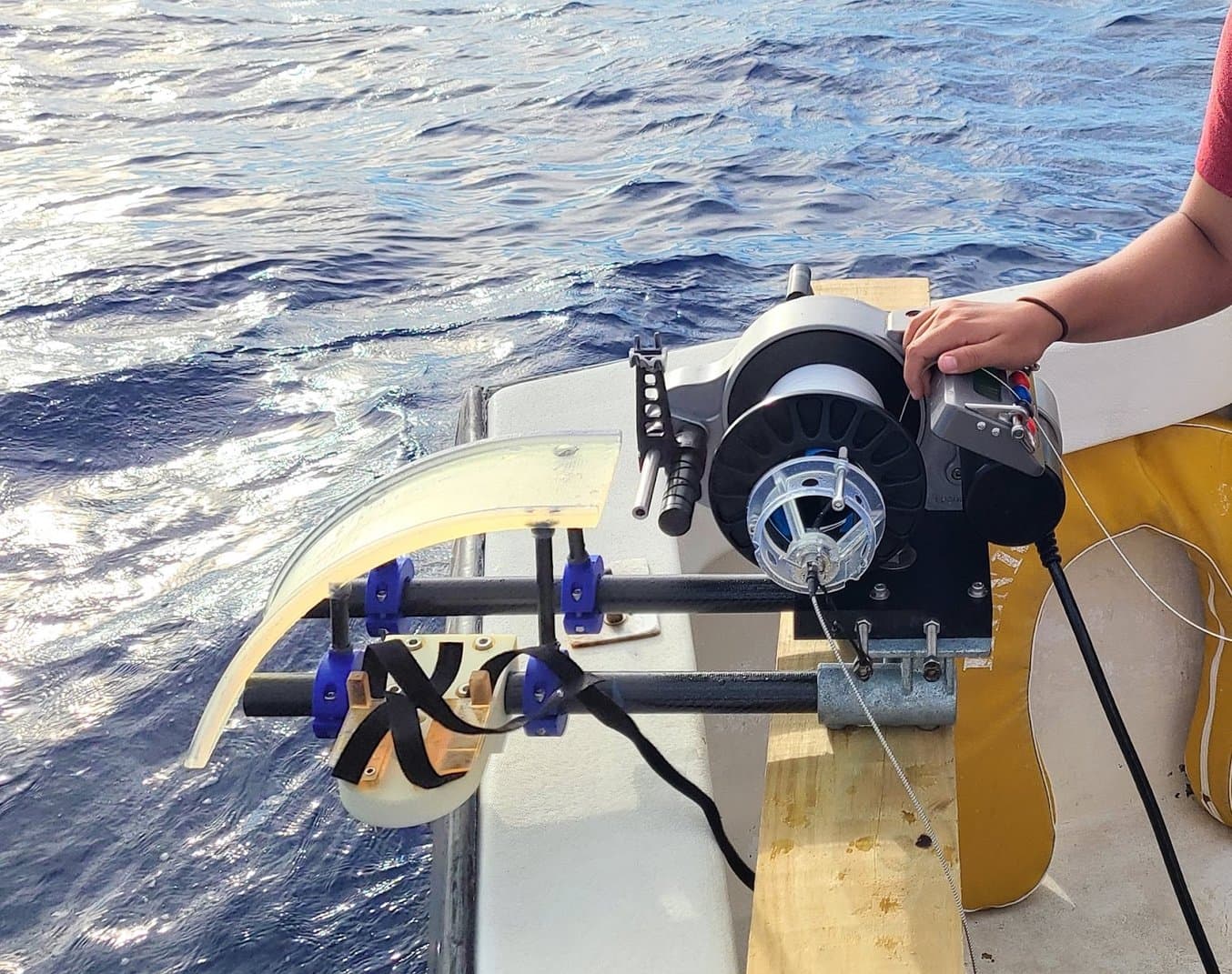
Un « toboggan » imprimée en 3D permet de guider en douceur les câbles de fibre optique sur le côté du bateau sans les emmêler ni les casser. (Image credit: Brennan Phillips)
« Pour ce fil de pêche, nous ne voulons pas utiliser de poulie tournante ou de roue. Nous avions besoin d'un toboggan. Nous avons donc imprimé trois ou quatre itérations de ce toboggan. La pièce est grande, belle et douce, et cette douceur est très utile pour les lignes plus fines », explique M. Phillips. Le toboggan imprimée sur la Form 3L avec Clear Resin réduit le temps nécessaire pour ranger soigneusement le fil de pêche, et réduit le nombre de fois où ils devront remplacer leur équipement.
Innovations dans le domaine de la fibre optique
Le fil de pêche, bien que laborieux à rembobiner, n'est pas le matériau le plus délicat. Les câbles en fibre optique, en revanche, ne peuvent pas être traités de la même manière et sont beaucoup plus coûteux à remplacer. Le laboratoire de M. Phillips, en partenariat avec Nautilus Defense LL, basé à Pawtucket RI, a été à l'origine de l'invention d'un nouveau type de ligne de pêche en fibre optique, ou FOFL (brevet américain en instance). « La fibre optique nous donne accès à l'Ethernet, à la vidéo en direct, etc. Il est très difficile de donner accès à ces services sans avoir recours à des câbles en cuivre installés sur de longues distances. Il existe donc aujourd'hui un nouveau fil de pêche en fibre optique », explique M. Phillips.
Mais le fil de pêche en fibre optique ne pouvait pas être utilisé seul : il avait besoin d'un point de terminaison mécanique pour que l'on puisse tirer dessus sans casser l'âme de la fibre optique. Les câbles de fibre optique ne pouvant être noués ou manipulés de la même manière que d'autres lignes plus durables, le laboratoire a dû inventer une fixation pour l'extrémité du câble.
Grâce à une pièce extrêmement précise imprimée en 3D avec les imprimantes SLA haute résolution de Formlabs, les tresses externes qui portent le fil de pêche peuvent être séparées du fragile noyau de fibre optique. Grâce à l'injection d'époxy, la ligne tressée adhère à la fixation imprimée en 3D, et la fibre optique passe dans un tube de furcation en métal qui peut être connecté à l'ordinateur pour recevoir les informations transportées par la fibre optique.
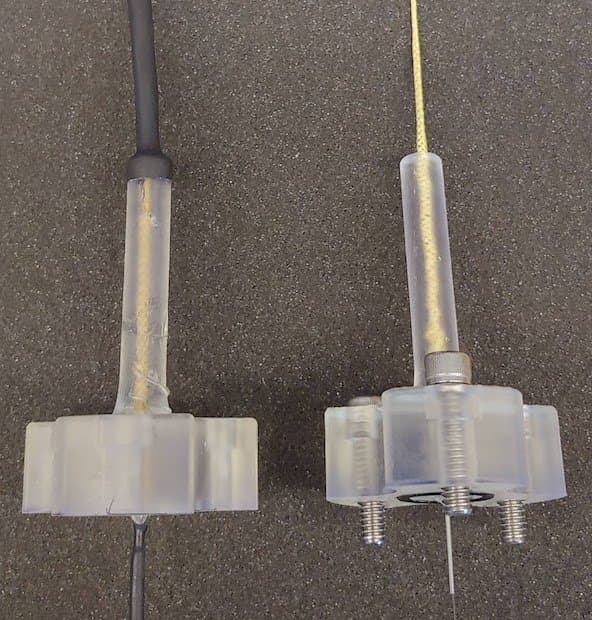
Les pièces SLA imprimées sont utilisées comme terminaisons mécaniques pour le « fil de pêche en fibre optique » ou FOFL (brevet américain en instance), séparant la tresse externe porteuse de la délicate âme de la fibre optique. Image credit Brennan Phillips
« Ce type d'attache est très solide : il résiste à au moins 45 kilos. Nous avons déposé une demande de brevet et nous l'avons également publié en libre accès », explique M. Phillips. « Sans l'impression 3D, ces produits pourraient coûter 3000 ou 4000 € s'ils étaient fabriqués avec des méthodes traditionnelles ; et nous avons dû procéder à plusieurs itérations avant de trouver le design final. Je ne pense pas que quelqu'un ait déjà essayé, parce que le coût de fabrication est bien trop élevé. C'est la combinaison de méthodes de prototypage rapide telles que les imprimantes Formlabs et la nouvelle ligne de fibres optiques qui permet de trouver de nouvelles idées comme celle-ci », explique M. Phillips.
Des joints d'abaissement imprimés en 3D à moindre coût
Avant l'impression 3D, le développement de ces outils était coûteux, ce qui dissuadait les chercheurs d'apporter les modifications nécessaires à la conception et empêchait les programmes sous-financés de les développer. Le laboratoire de robotique et d'imagerie sous-marines s'inscrit dans le cadre d'un mouvement mondial visant à démocratiser la science et à ouvrir l'accès à ces technologies, afin de mieux comprendre les océans qui nous entourent. « J'ai commencé à imprimer en 3D des embouts auxquels étaient intégrés des joints toriques, et cela a fonctionné. L'usinage coûte des centaines, voire des milliers de dollars, et les dessins doivent être très précis. Avec ces imprimantes, je peux en imprimer trois ou quatre et obtenir un ajustement parfait, pour une cinquantaine de dollars de matériel », explique M. Phillips.
L'équipe du laboratoire ne s'est pas limitée à imprimer des pièces d'utilisation finale ; grâce à Clear Resin, elle a également mis au point un flux de travail efficace pour imprimer des moules. Le résultat final est une méthode optimisée pour épisser rapidement les câbles sous-marins à l'aide de moules imprimés en 3D.
Des cas d'utilisation variés
Dans le laboratoire de M. Phillips, les imprimantes Formlabs sont utilisées pour créer des prototypes, des produits finis, de l'outillage rapide, des gabarits et des fixations, et même des appareils médicaux. Même dans un petit laboratoire de recherche, les applications et les possibilités sont sans cesse repoussées par l'esprit d'innovation de M. Phillips et de ses étudiants.
Pendant la pandémie de COVID-19, M. Phillips et ses étudiants ont réalisé qu'ils avaient la capacité d'améliorer drastiquement la façon dont les malades du Rhode Island étaient traités. Grâce à des tests approfondis et à des recherches exhaustives, le laboratoire a pu publier les résultats des dégagements gazeux chimiques de Formlabs Surgical Guide Resin utilisée dans les pièces de ventilateurs imprimées en 3D. Ils ont réussi l'exploit non seulement de publier des articles scientifiques, mais aussi de demander l'approbation de la FDA et de l'autorisation d'utilisation en cas d'urgence (EUA).
« Pendant la pandémie, beaucoup ont tenté d'innover, et nous voulions vraiment intervenir et aider là où nous le pouvions. Grâce à la qualité de ces imprimantes et à l'existence de Surgical Guide Resin, nous avons pu y contribuer », explique M. Phillips.
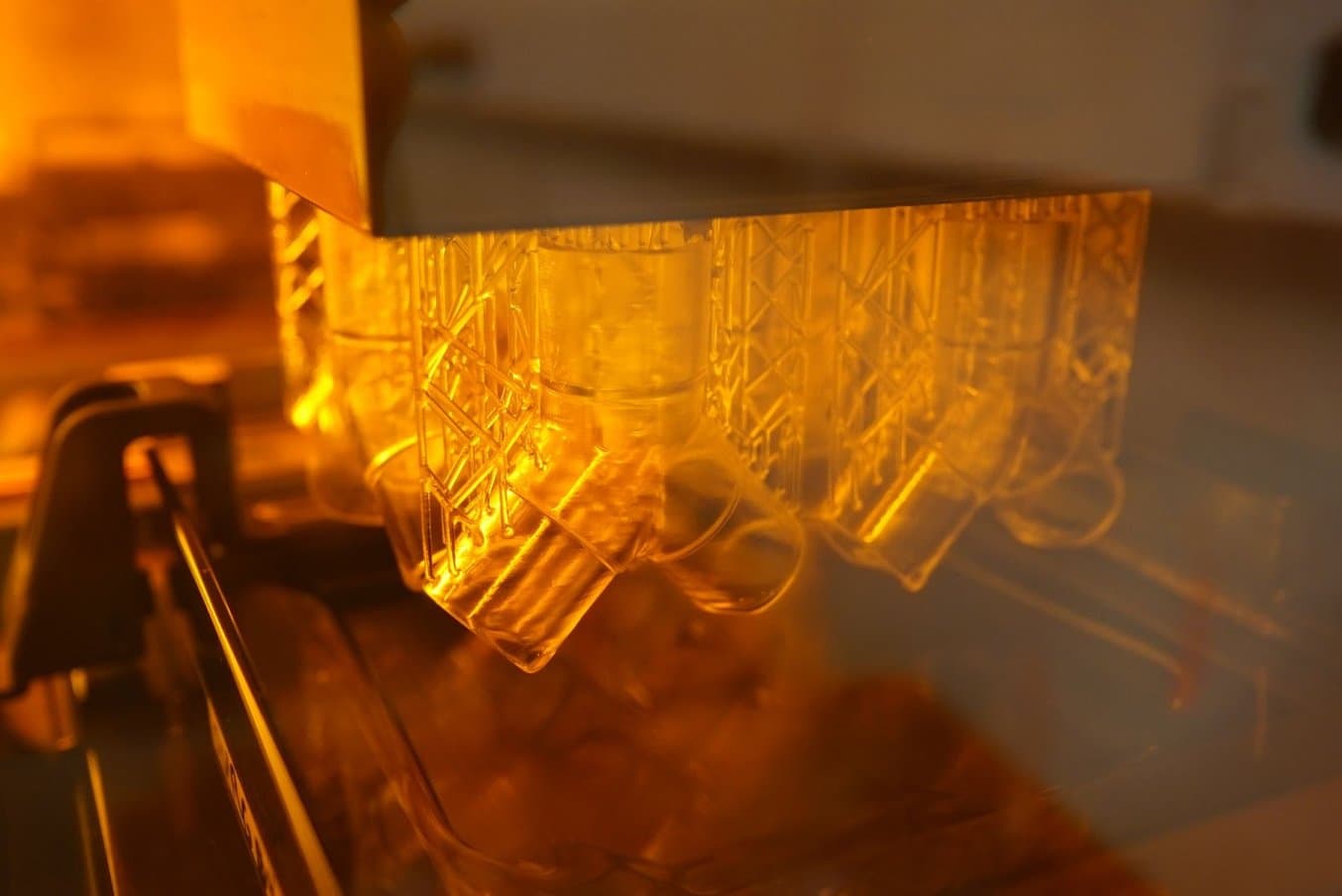
Les pièces du ventilateur en « Y », conçues en collaboration avec des chercheurs de l'université Brown et de l'hôpital de Rhode Island, sont imprimées en 3D à l'aide de Surgical Guide Resin pendant les premiers stades de la pandémie de COVID-19. Photo credit: Brennan Phillips
Rendre les profondeurs accessibles
Le coût réduit de la fabrication de ces pièces n'est pas seulement bénéfique pour le budget du laboratoire : il permet également aux étudiants d'avoir accès à ces machines, et d'ainsi tester leurs nouvelles idées. Les étudiants de premier cycle qui conçoivent des pièces pour la première fois peuvent accéder à la technologie et s'initier à l'impression 3D sans avoir peur de se tromper.
Les étudiants de deuxième année de l'URI ont la possibilité de concevoir et d'imprimer en 3D les boîtiers de pression chaque année, ce qui leur permet de contribuer à la recherche et d'acquérir de nouvelles compétences précieuses en matière de CAO et d'impression 3D. « Avant ces imprimantes 3D, les étudiants ne concevaient ou ne fabriquaient pas leurs propres boîtiers sous-marins avant d'être diplômés ou employés et de pouvoir suivre des formations spécialisées, car le coût et l'accès à cette technologie étaient hors de portée. Mais ces imprimantes ouvrent des horizons inimaginables : même un lycéen peut fabriquer un boîtier sous pression », explique M. Phillips.
Ces possibilités ne sont pas réservées aux seuls étudiants américains. M. Phillips fait partie d'une communauté internationale qui cherche à améliorer l'accès aux outils de recherche sous-marine et à les rendre plus abordables dans les pays côtiers sous-développés du monde entier. « Nous travaillons au développement de pays qui souhaitent effectuer leur propre exploration des grands fonds marins. L'argent est une restriction, la formation est une restriction, mais ces méthodes ont le potentiel d'ouvrir la voie et de démocratiser l'exploration des grands fonds marins », explique M. Phillips.
1 https://oceanservice.noaa.gov/facts/exploration.html
2 Brennan T. Phillips, Josh Allder, Grady Bolan, R. Sean Nagle, Allison Redington, Tess Hellebrekers, John Borden, Nikolai Pawlenko, Stephen Licht,
Additive manufacturing aboard a moving vessel at sea using passively stabilized stereolithography (SLA) 3D printing, Additive Manufacturing, Volume 31, 2020, 100969, ISSN 2214-8604, https://doi.org/10.1016/j.addma.2019.100969.