L'ivresse de la vitesse : Foil Drive produit des équipements de surf avec la Form 3L et la série Fuse
Le « surf foil », ou tout simplement « foil » est une nouvelle variation du surf qui consiste à soulever de courtes planches de surf sur un mât avec des ailes sous-marines au-dessus des vagues, à la manière des hydroglisseurs.
Foil Drive est un fabricant d'équipement électronique de foil qui connaît bien la technologie 3D. L'équipe utilise l'impression 3D à chaque étape du processus de développement et produit chaque semaine jusqu'à un millier de pièces finales à l'aide de la série Fuse et de ses imprimantes grand format Form 3L. Avec l'explosion de la popularité du foil, l'impression 3D offre la solution idéale pour la fabrication, car elle est rapide et réactive. C'est la seule façon de maintenir des produits de haute performance disponibles et abordables pour un public toujours à la recherche de nouvelles sensations fortes.
« Il y a une infinité de configurations possibles que vous pouvez essayer. C'est dynamique ; il y a toujours quelque chose à améliorer ou à concevoir dans le cadre d'une expérience de surf en 3D », explique Paul Martin, fondateur et PDG de Foil Drive. Ce qui n'était au départ qu'un moyen pour M. Martin d'essayer de nouvelles configurations est devenu une entreprise mondiale de plusieurs millions de dollars au cours de sa deuxième année d'existence, et l'impression 3D a contribué au succès de Foil Drive depuis le début.
Les débuts
Bien que le foil élimine une partie du stress au niveau des épaules que chaque surfeur endure en pagayant constamment, il s'agit toujours d'un sport très exigeant sur le plan physique. Pour générer la vitesse qui vous propulsera sur l'eau et hors de l'eau, le surfer doit pagayer énergiquement.
Souffrant d'une ancienne blessure à l'épaule, M. Martin a saisi l'occasion d'utiliser ses compétences en ingénierie pour passer à la vitesse supérieure. Il a conçu un système de propulsion électrique petit mais puissant qui se fixe en tête de mât et génère suffisamment de vitesse pour soulever facilement les planches et les sortir de l'eau. « C'était la suite logique des choses. J'imprime en 3D depuis 20 ans et j'ai donc pu réaliser quelques premiers prototypes qui ont fonctionné. Dès le départ, le produit a vu le jour parce que l'impression 3D était à ma disposition », explique M. Martin.
Les tests itératifs ont nécessité beaucoup de temps sur l'eau, et le design a commencé à attirer l'attention d'autres surfers. Les gens lui ont demandé s'il pouvait leur fabriquer un système de propulsion semblable au sien. Et tandis que M. Martin expérimentait différents designs, il s'est rendu compte qu'il ne lui manquait que de plus grandes capacités de production pour rendre son produit commercialement viable.
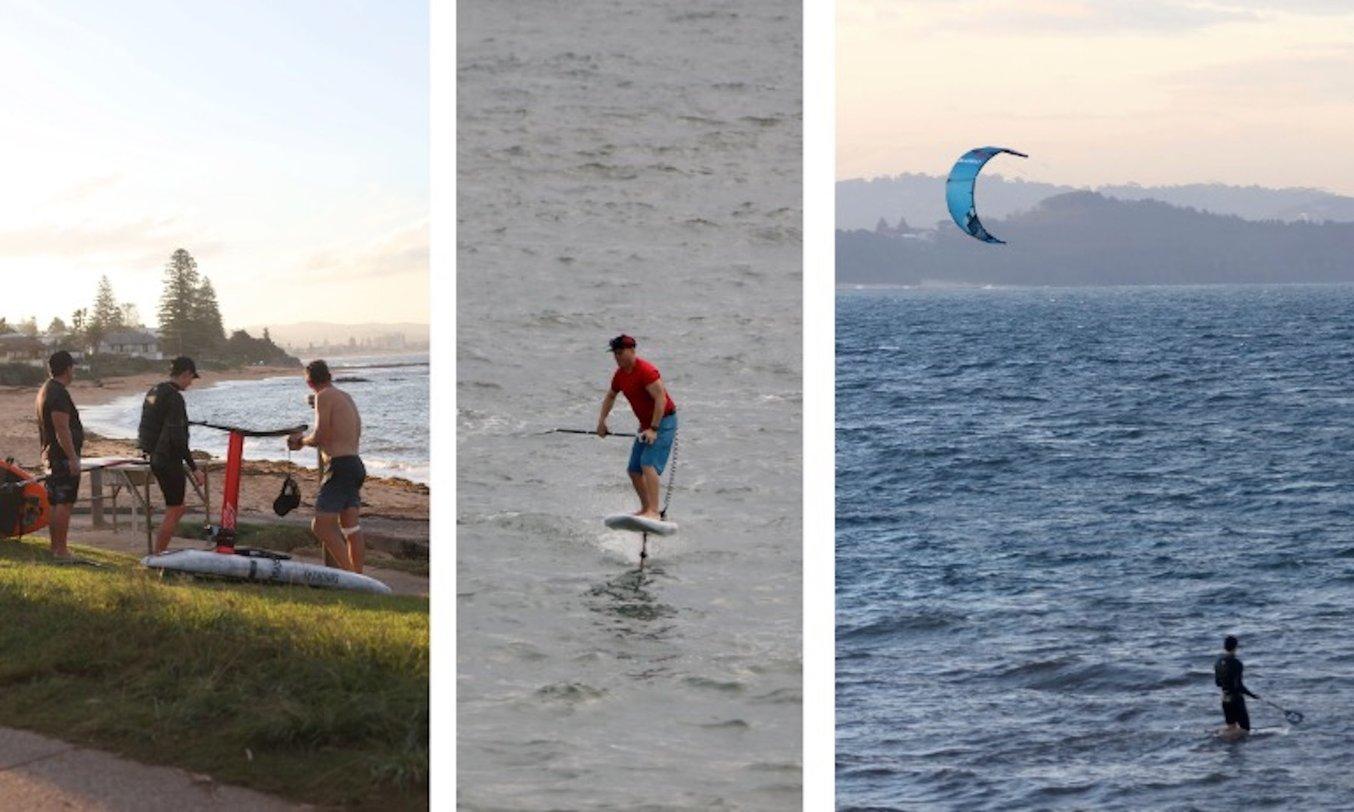
Le surf foil est l'un des sports qui connaît la plus forte croissance au monde. La demande pour des équipements personnalisables et modernes augmente de manière exponentielle.
Trouver le bon matériau pour une hélice
Le poids et la taille sont extrêmement importants pour le foil, où l'élan est primordial. Si les composants sont trop grands ou trop lourds, l'hélice ne peut pas générer une vitesse suffisante pour soulever la planche hors de l'eau. Les conceptions devaient passer par de nombreuses étapes itératives pour trouver l'équilibre parfait entre puissance et taille, et l'impression 3D était donc parfaitementement adaptée. M. Martin a eu accès au FDM et à des unités SLA à bas prix, et a été en mesure de procéder à des itérations rapides. « Il est possible de microfabriquer des pièces très compliquées en interne sans avoir à dépenser des sommes considérables pour les développer », explique M. Martin.
Cependant, au cours des essais, il s'est avéré qu'il devait trouver une solution d'impression 3D offrant des propriétés mécaniques plus solides. La charge des pales de l'hélice est un défi particulier. Elles tournent à 3000 tr/min et plongent et sortent sans cesse de l'eau ; à cela s'ajoutent la force et le couple du moteur électrique. Bien qu'elles ne pèsent que neuf grammes, les pales doivent être extrêmement résistantes pour supporter une telle force. « On attend d'une pale d'hélice qu'elle soit capable de faire face à ces forces extrêmement brutales », explique M. Martin.
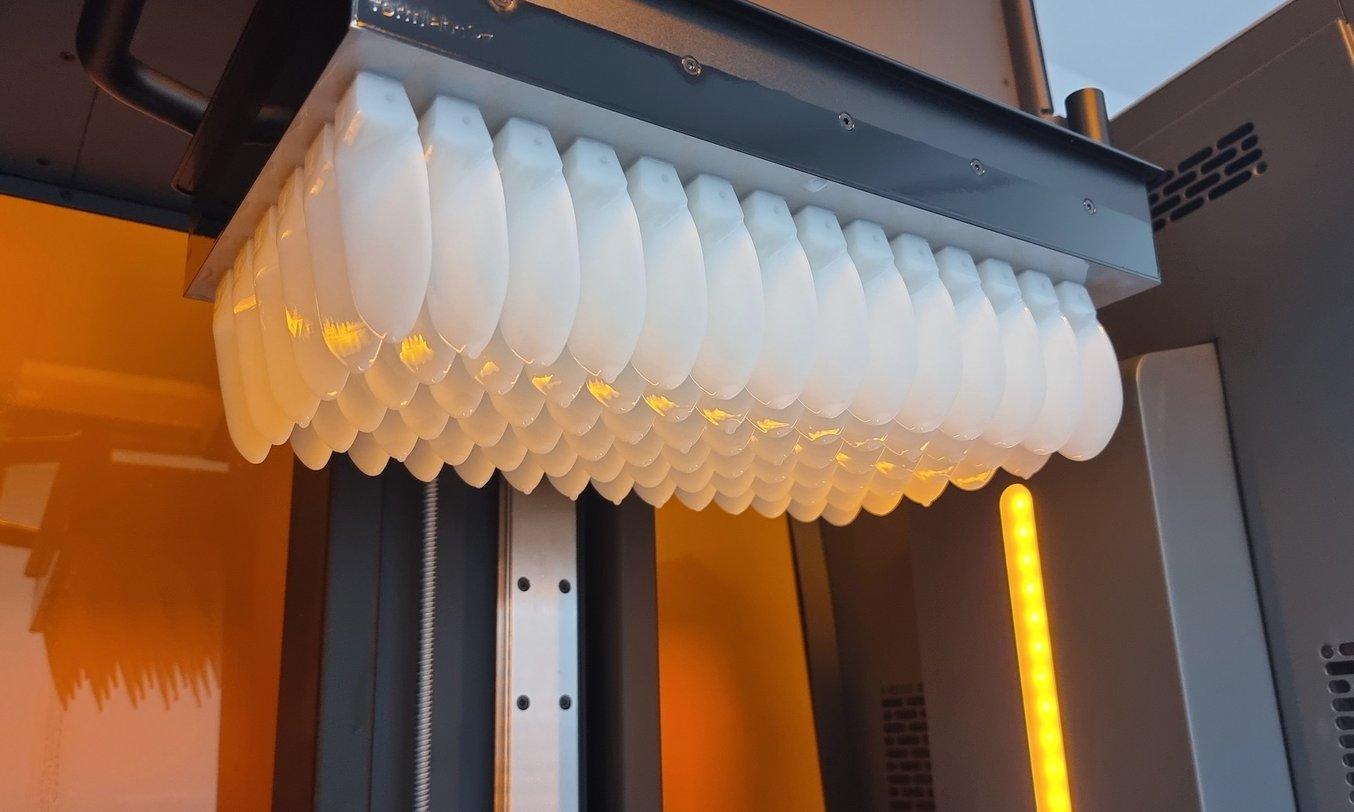
Le design final des pales de l'hélice, imprimé sur la Form 3L avec Rigid 4000 Resin.
L'outillage pour une pale en métal coûterait des dizaines de milliers de dollars et limiterait sa capacité à modifier la conception ultérieurement. « Je dois fabriquer ces petites hélices en petites quantités, à un prix qui permette de les vendre. Il n'y a aucun moyen de le faire si ce n'est de les imprimer en 3D », explique M. Martin.
Après avoir essayé plusieurs imprimantes 3D résine, M. Martin a rencontré des difficultés pour obtenir des lots de matériaux uniformes présentant des propriétés fiables. La constance est payante pour une petite entreprise comme Foil Drive : un mauvais lot de matériau entraînerait des défaillances de pièces dans l'eau et laisserait quelqu'un sur le banc de touche. M. Martin couvre tous ses produits avec une garantie à toute épreuve, mais le service et l'expédition des pièces de rechange lui coûtaient plus cher que le coût des marchandises. « Il fallait mettre un terme à ces pièces qui se cassaient sans arrêt » Finalement, il a pu tester sa conception en utilisant le matériau à charge de verre Rigid 4000 Resin sur une imprimante SLA Form 3+, et a travaillé avec le fournisseur Thinglab, basé à Melbourne, pour tester des pièces et finalement acheter plusieurs machines.
Ce n'est que lorsque nous avons essayé Rigid 4000 Resin que tout a fonctionné. Elle nous a permis de fabriquer des milliers de pales d'hélice et de les envoyer dans le monde entier.
Paul Martin, fondateur et PDG de Foil Drive
Plus de supports cassés
L'équipe de Foil Drive a utilisé des imprimantes résine plus grandes et peu coûteuses pour des pièces autres que les hélices, comme les supports du contrôleur. Après les avoir produits et expédiés dans le monde entier, certains clients ont commencé à trop serrer les supports et à les casser. Martin a décidé de commencer la production avec la Form 3L et Tough 2000 Resin, qui pouvait supporter le mouvement de serrage des supports et une utilisation répétée. « À partir de là, nous n'avons plus eu un seul dommage matériel. Le retour sur investissement a été immédiat. On en a pour son argent, et avec la Form 3L, nous pouvons régler la machine et la laisser tourner », explique M. Martin.
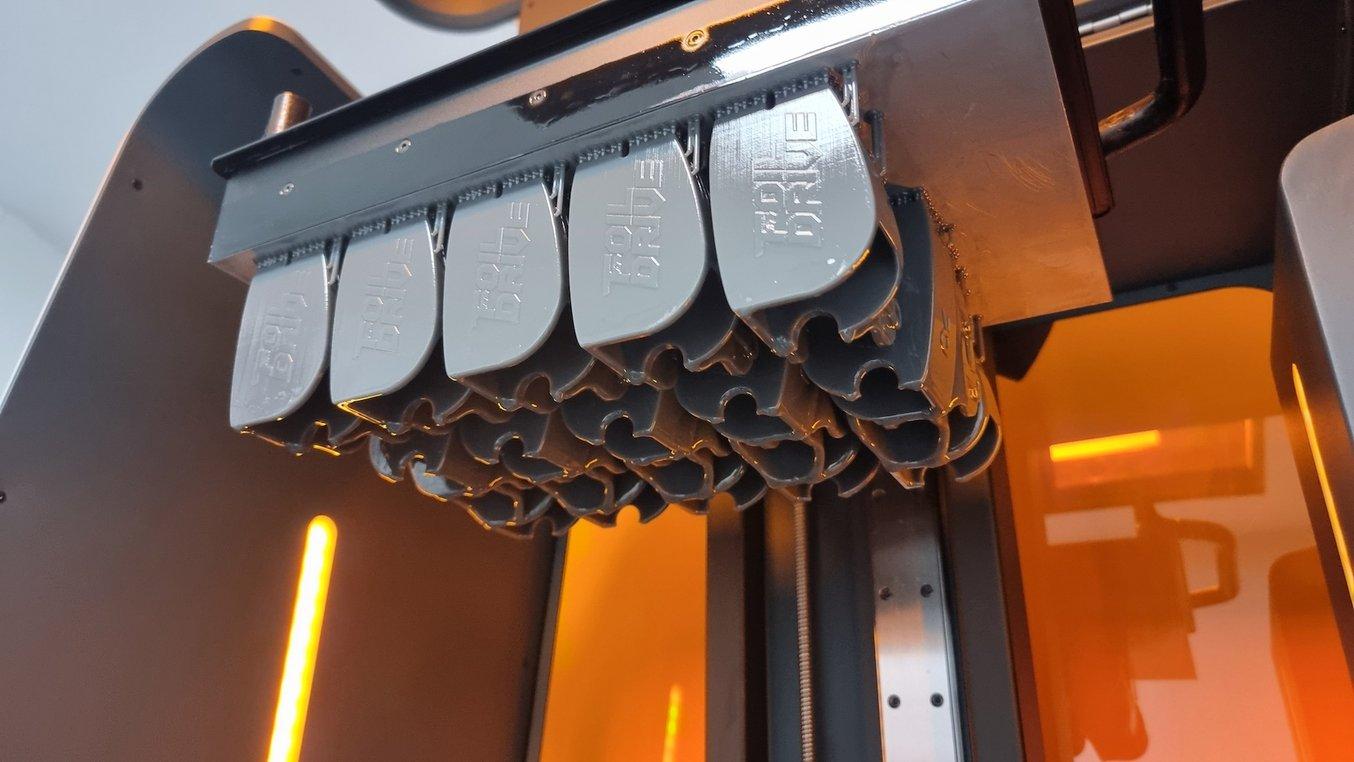
Tough 2000 Resin offre résistance et durabilité, même après des mois dans l'eau de mer et des opérations répétées de serrage et de desserrage.
Cette Form 3L présentait les avantages de la fiabilité et des propriétés mécaniques avancées, mais lorsque les commandes des clients ont commencé à affluer, Foil Drive a commencé à voir encore plus grand. Pour produire des quantités plus importantes et expérimenter de nouvelles géométries tout en conservant l'agilité que permet l'impression 3D, ils avaient besoin d'un outil doté d'une puissance industrielle. Le SLS interne et puissant était la solution.
Nous en sommes arrivés au point où nous vendions beaucoup de systèmes, et nous voulions aussi concevoir des formes différentes sans supports. La Fuse nous a permis de fabriquer plus de pièces en plus grande quantité avec des coûts de matériaux plus faibles.
Paul Martin, fondateur et PDG de Foil Drive
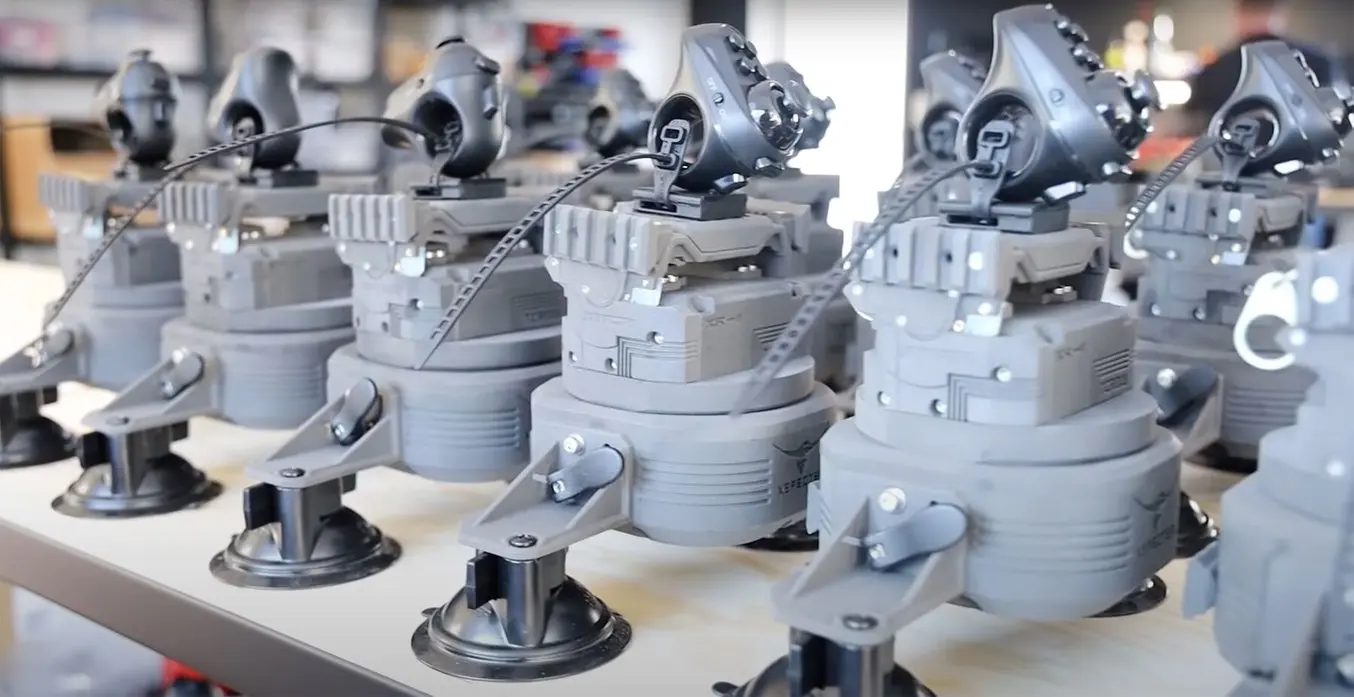
Le SLS pour la production finale
L'impression 3D pour la production finale n'est pas seulement accessible : elle est aussi plus abordable, plus agile et plus évolutive que jamais grâce à l'écosystème SLS Fuse. Explorez notre page dédiée à la production SLS pour comparer les différentes méthodes de fabrication, consulter les tarifs des poudres en vrac et découvrir comment 15 fabricants exploitent actuellement les imprimantes de la série Fuse.
La puissance au service de la souplesse et de la vitesse
L'équipe a commencé avec 100 pièces par semaine, puis 200, et maintenant, avec une deuxième imprimante Fuse 1+ 30W, environ 650 pièces en Nylon 12 Powder chaque semaine. Foil Drive a été en mesure d'adapter sa production à la croissance de sa clientèle, alors que la popularité de ce sport ne cesse de prendre de l'ampleur. « Les imprimantes Fuse nous ont vraiment offert le rendement et l'évolutivité que nous souhaitions. Elles fonctionnent 24/7 », explique M. Martin.
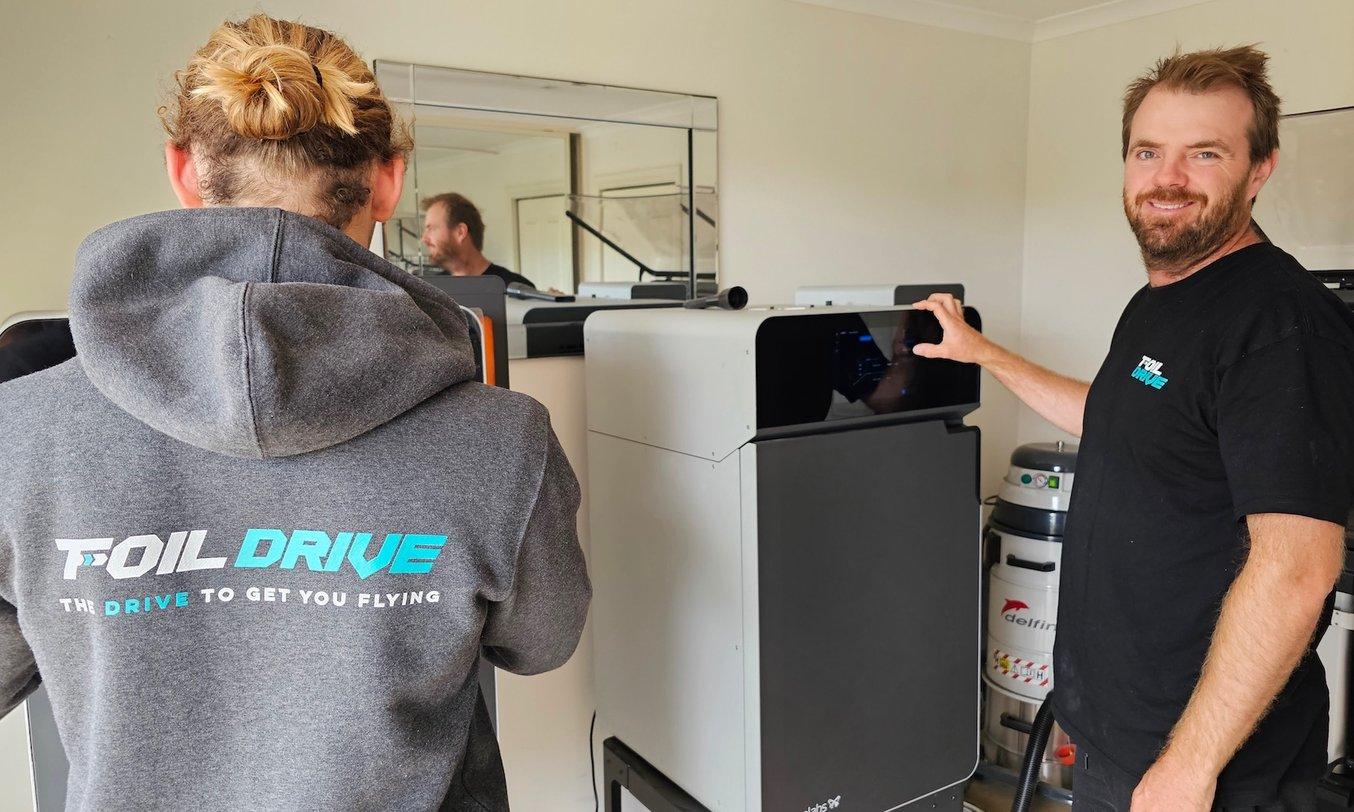
Paul Martin (à droite) et son équipe font tourner les imprimantes SLS de la série Fuse 24/7, pour répondre à la forte demande de leurs systèmes électriques de surf foil.
Pour de tels volumes, de nombreux fabricants songeraient à mouler leurs composants de manière traditionnelle pour réduire le coût par pièce, mais M. Martin a compris les avantages d'un flux de travail intégré verticalement lors des problèmes de chaîne d'approvisionnement de ces dernières années. Lors d'une grave pénurie de puces silicone , Foil Drive a dû changer de fournisseur, et le composant qui contenait la puce n'était plus adapté. S'ils avaient utilisé des composants moulés en série comme certains de leurs concurrents, il y aurait eu un énorme gaspillage. Au lieu de cela, Martin a été en mesure de s'adapter rapidement, de modifier la conception et d'éviter tout gaspillage de composants.
Pour nous, il s'agissait d'une chose triviale : modifier quelques éléments, les envoyer à PreForm, les imprimer et obtenir le lendemain des éléments parfaitement adaptés à la nouvelle puce », explique M. Martin. « Le fait d'être intégré verticalement nous a donné un contrôle total : nous pouvions virer de bord à tout moment.
Paul Martin, fondateur et PDG de Foil Drive
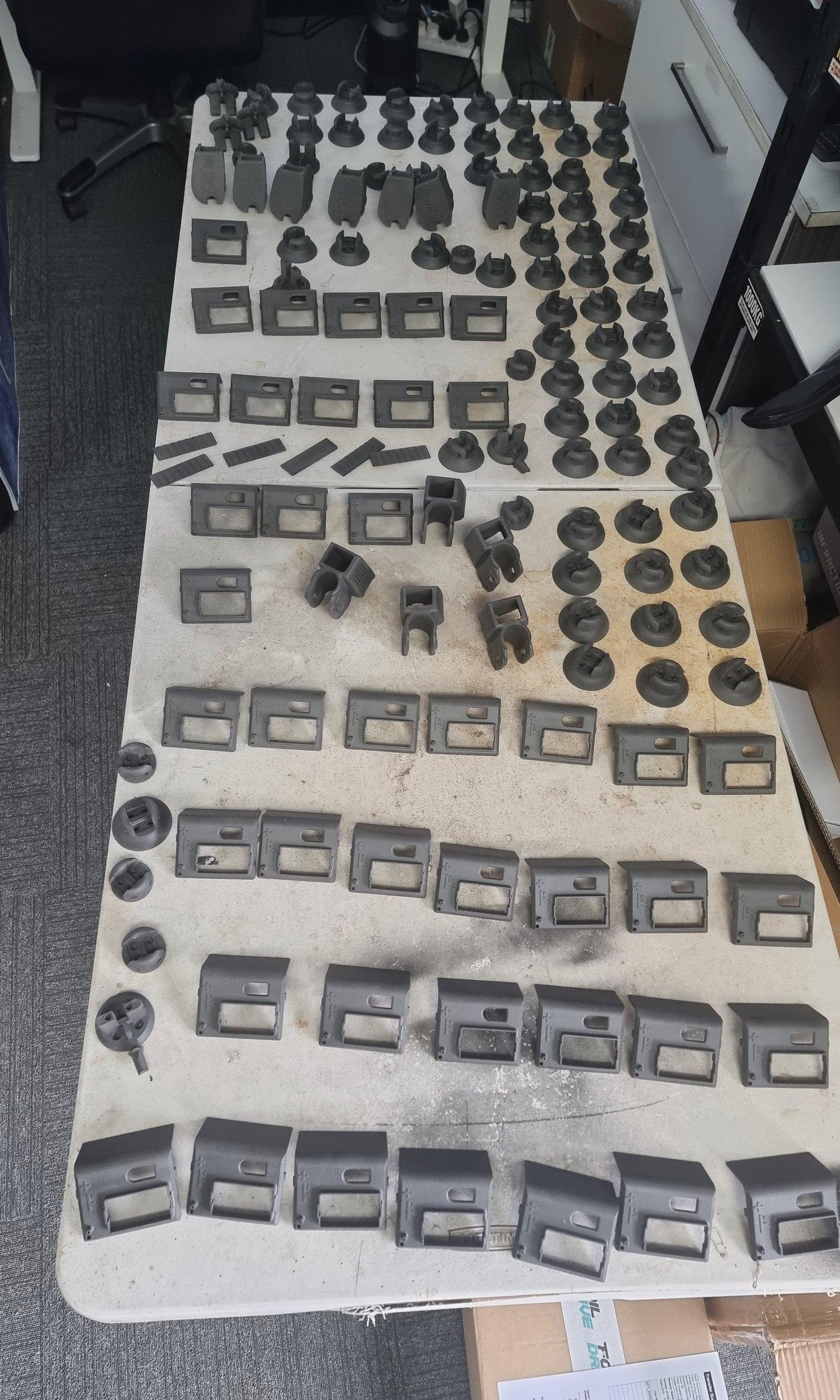
Foil Drive utilise la technologie SLS de la série Fuse pour imprimer de nombreux composants d'utilisation finale pour leurs cartes.
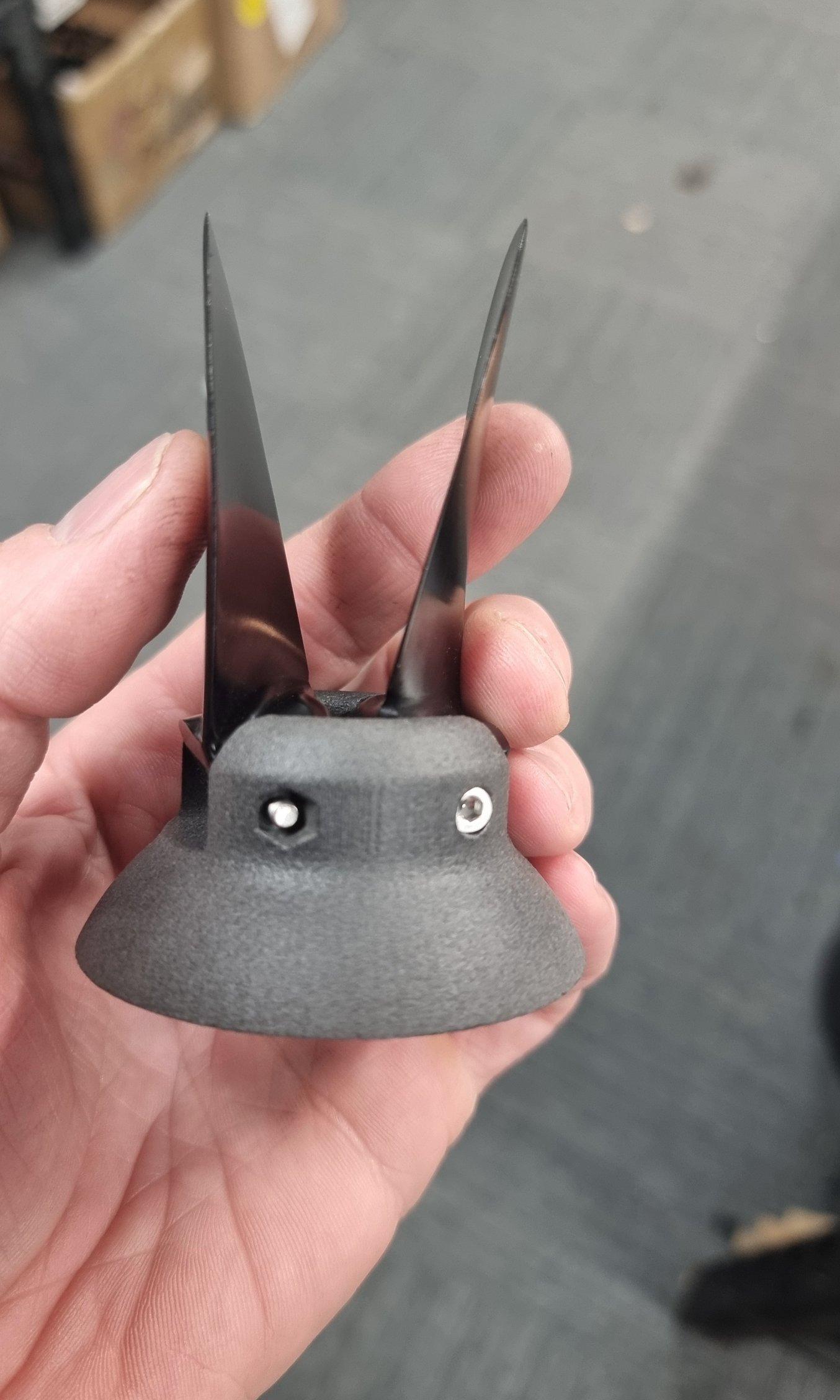
L'assemblage de l'hélice pliable utilise la résistance et l'usinabilité de Nylon 12 Powder pour créer une pièce robuste.
Volumes de production avec la série Fuse et la Form 3L
Imprimante/Matériel | Pièces par impression | Pièces par mois | Aspects à prendre en compte : | |
---|---|---|---|---|
Assemblage de l'hélice pliable | Fuse 1+ 30W avec Nylon 12 Powder | ~60 | ~200 assemblages | Capacité de vissage, légère flexion, capacité de production, durabilité, robustesse, capacité d'utilisation finale |
Pale de l'hélice | Form 3L avec Rigid 4000 Resin | 84 | ~300-350 | Solidité, capacité itérative, rigidité, résistance à la pression sous-marine à 3000 tours/minute, arêtes vives/fines |
Support | Form 3L avec Tough 2000 Resin | 15 | ~200 | |
Prendre de l'élan
Le succès dans le domaine du foil est une question d'élan : vous avez besoin de vitesse pour vous lever et sortir de l'eau, tout comme vous avez besoin de vitesse pour lancer un nouveau produit sur le marché. L'impression 3D vous permet de faire les deux. La résistance de matériaux tels que Rigid 4000 Resin ou Nylon 12 Powder facilite la production de machines durables destinées à une utilisation finale. En permettant une production souple, les imprimantes Form 3+, Form 3L et Fuse Series ont aidé Foil Drive à développer une activité de plusieurs millions de dollars en seulement trois ans.
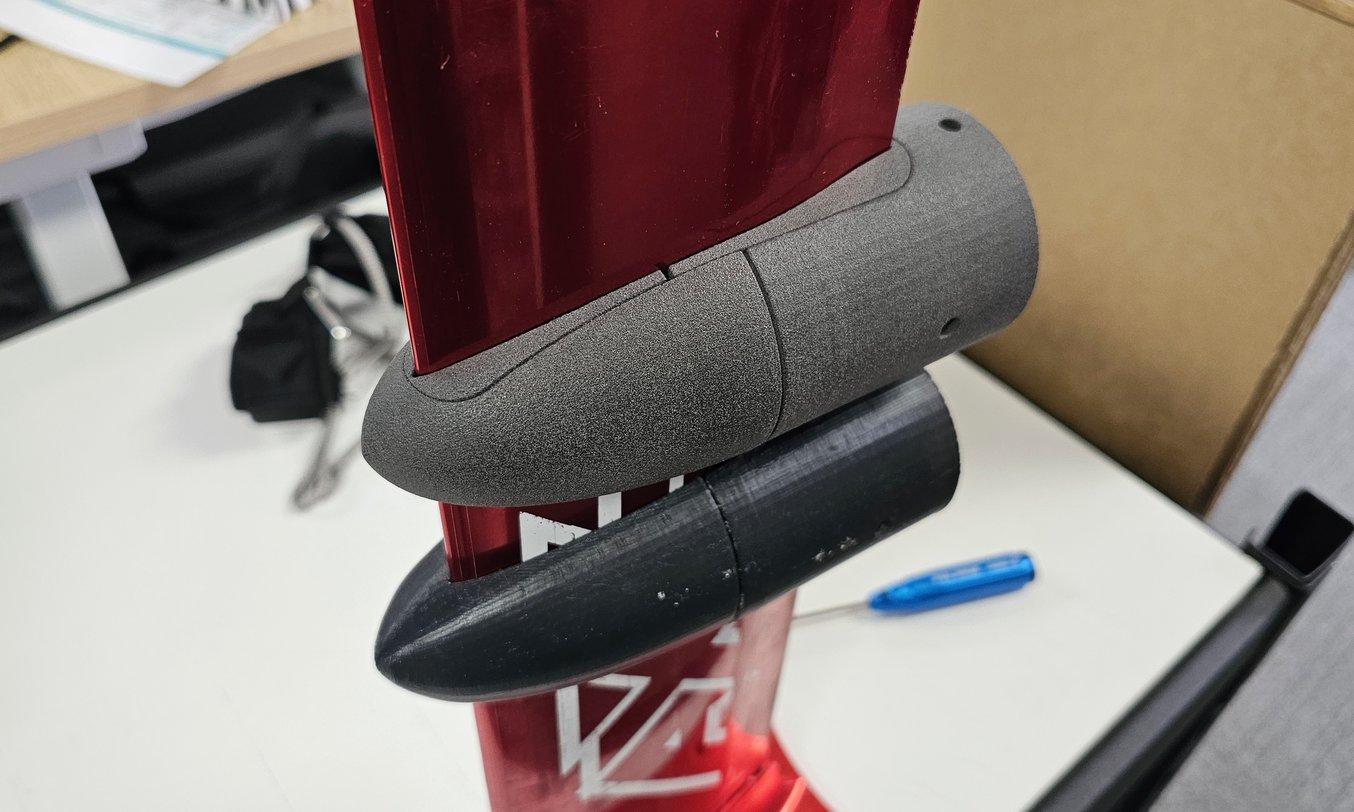
En haut, un boîtier de moteur électrique en Nylon 12 Powder (imprimé avec la série Fuse) et en bas en Tough 1500 Resin.
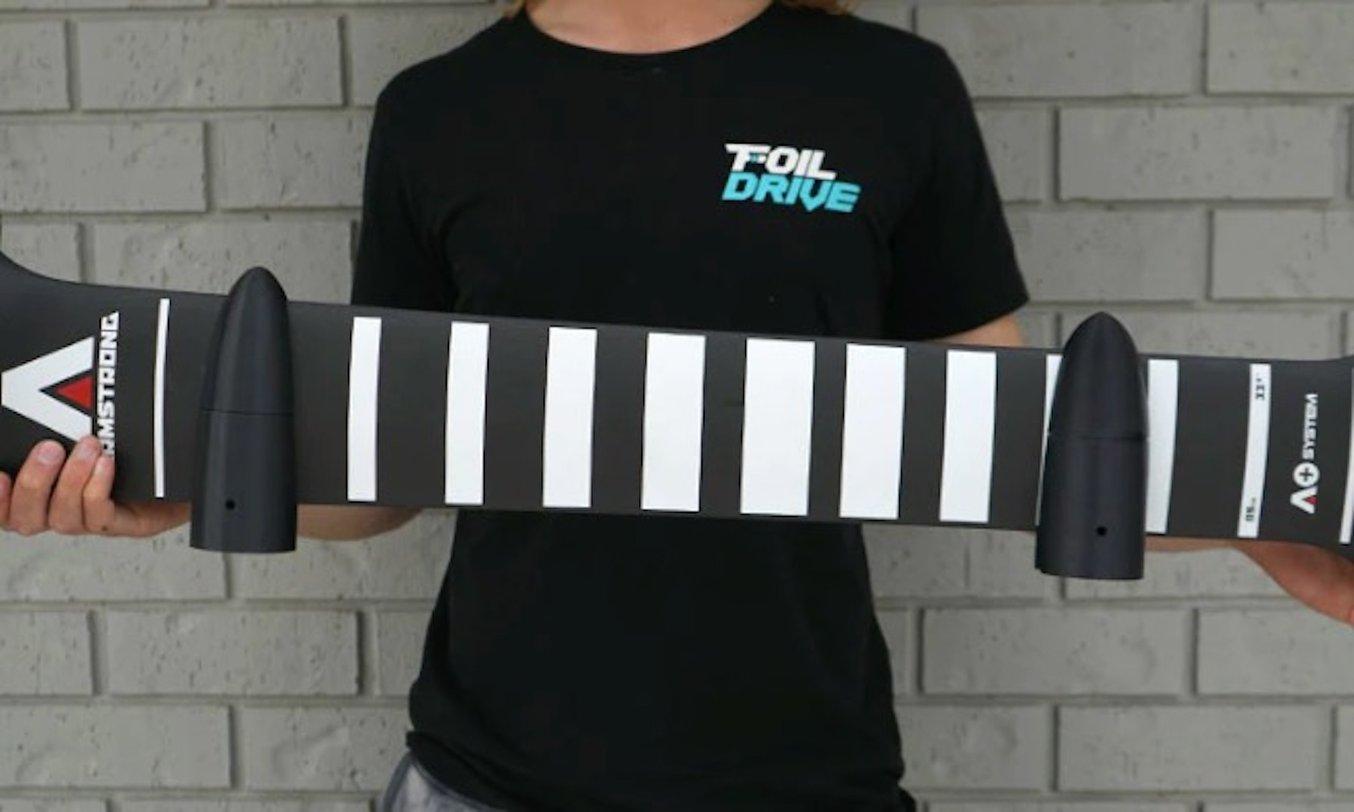
Les boîtiers de moteurs peuvent être personnalisés pour s'adapter à une large gamme de mâts de différentes marques, même ceux qui ont une construction conique, comme celui-ci d'Armstrong.
« Les volumes dont nous avons besoin, les formes, les tailles et les géométries, les variations, le fait qu'aucun des articles dont nous avions besoin n'était disponible sur le marché,... Tous ces éléments vont à l'encontre de la fabrication traditionnelle. Mais avec cette technologie, tous ces problèmes disparaissent.
Paul Martin, fondateur et PDG de Foil Drive
Les imprimantes SLA et SLS de Formlabs ouvrent la voie à de nouvelles méthodes de production, qu'il s'agisse d'intégrer verticalement votre chaîne d'approvisionnement pour améliorer l'agilité de la fabrication ou de créer un produit entièrement nouveau en éliminant les obstacles de l'outillage traditionnel. Pour en savoir plus sur la production avec les imprimantes Formlabs, contactez un spécialiste dès aujourd'hui.