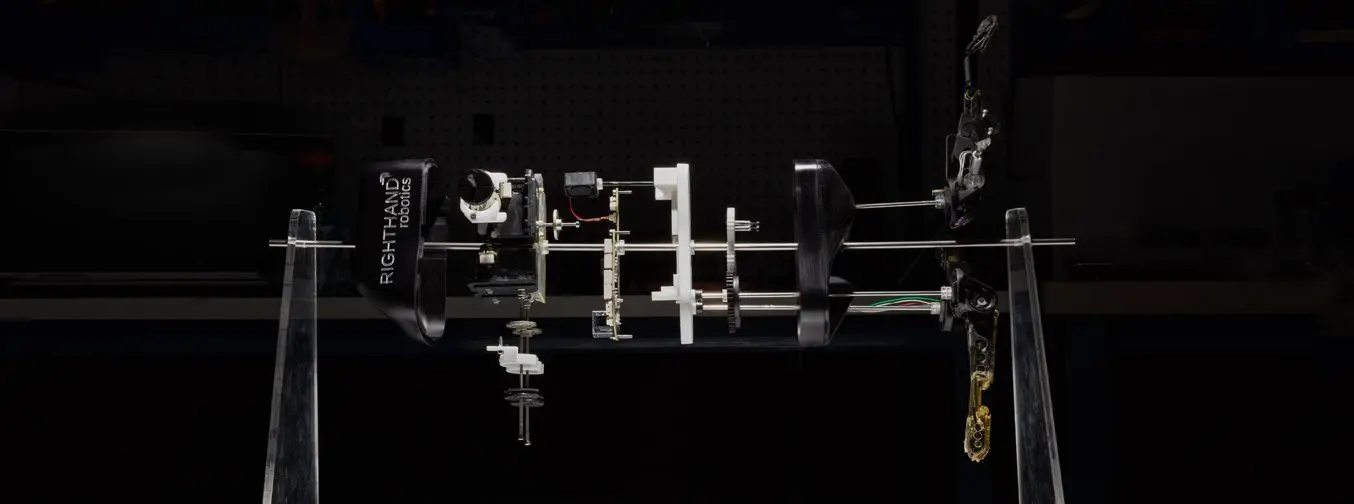
Les plastiques sont les matériaux les plus courants pour produire tout type de pièces et de produits finis, allant de simples produits de consommation à des dispositifs médicaux. Les plastiques constituent une catégorie de matériaux très polyvalents, avec des milliers de combinaisons polymères possibles, chacun présentant des propriétés mécaniques spécifiques. Mais comment les pièces en plastique sont-elles fabriquées ?
Différents procédés de production de plastique ont été mis au point pour un large éventail d'applications, de géométries et de types de plastique. Tout concepteur ou ingénieur travaillant en développement de produits se doit de bien connaître les options de production industrielle existant aujourd'hui, ainsi que les nouvelles qui présagent des processus futurs.
Ce guide présente l'ensemble des processus de fabrication les plus courants pour la production de pièces en plastique, ainsi que des conseils pour choisir celui qui conviendra le mieux à votre application.
Comment choisir le processus de fabrication adéquat ?
Lorsque vous décidez du processus de production à utiliser pour votre produit, tenez compte des facteurs suivants:
Forme : Vos pièces présentent-elles des caractéristiques internes complexes ou des exigences de tolérance strictes ? Les options possibles de fabrication peuvent être contraintes par la géométrie de la pièce. Il peut aussi être nécessaire de réaliser une optimisation de conception en vue de la fabrication (design for manufacturing ou DFM) afin de rendre leur production plus économique.
Volume/coût : Quel est le volume total ou annuel de pièces que vous comptez fabriquer ? Certains processus présentent des coûts initiaux élevés pour l'outillage et la mise en place, mais le coût par pièce produite est bas. En revanche, des procédés de production à faible volume peuvent avoir des coûts de lancement faibles, mais le coût par pièce reste constant ou décroît marginalement lorsque le volume total croît, en raison de temps de cycle plus longs, d'une moindre automatisation et d'opérations manuelles plus importantes.
Délai de production : Dans quel délai devez-vous produire des pièces ou des produits finis ? Certains procédés permettent de fabriquer des pièces en 24 heures, d'autres prennent des mois en raison de l'outillage et de la mise au point nécessaires à une production à volume élevé.
Matériau : À quelles contraintes et déformations devront résister vos pièces ? Le matériau optimal pour une application donnée est déterminé par de nombreux facteurs. Il faut trouver l'équilibre entre le coût et les contraintes fonctionnelles et esthétiques. Considérez les caractéristiques idéales recherchées pour votre application et comparez-les avec les résultats possibles d'un procédé donné.
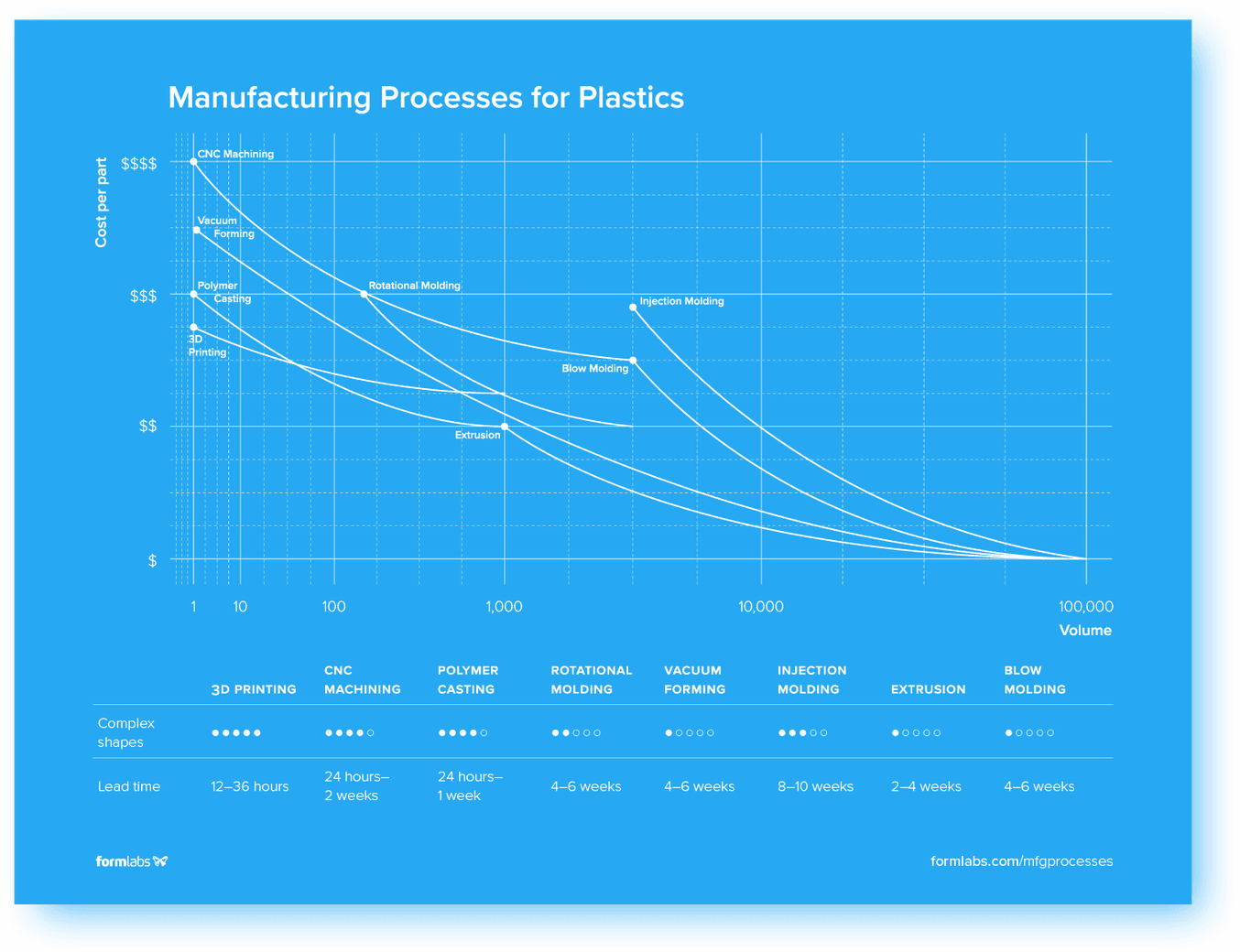
Téléchargez la version haute résolution de cette infographie ici.
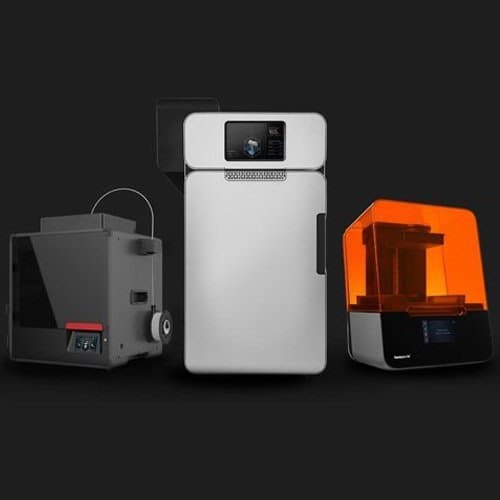
Comment choisir une technique d’impression 3D
Vous avez des difficultés à trouver la meilleure technique d’impression 3D qui réponde à vos besoins ? Dans ce guide vidéo, nous comparons les procédés FDM, SLA et SLS selon plusieurs critères d’achat courants.
Types de plastiques
Des milliers de types de plastiques sont proposés avec des produits chimiques de base, des additifs et des dérivés différents. Ils sont formulés pour présenter une large gamme de propriétés fonctionnelles et esthétiques.
Pour simplifier le choix du matériau le mieux adapté à une pièce ou un produit donnés, nous allons regarder d'abord les deux principales catégories de plastiques existantes : les thermoplastiques et les plastiques thermodurcissables.
Thermoplastiques
Les thermoplastiques sont les plus utilisés. La caractéristique principale qui les différencie des plastiques thermodurcissables est qu'ils peuvent subir de nombreux cycles de fusion et de durcissement sans dégradation importante de leurs propriétés. Les thermoplastiques se présentent généralement sous forme de petits granulés ou de feuilles, qui sont chauffés et mis en forme par divers procédés. Le processus est complètement réversible parce qu'il ne fait pas intervenir de liaisons chimiques, ce qui permet le recyclage ou la fusion, et la réutilisation.
Types courants de matériaux thermoplastiques:
- Acrylique (PMMA)
- Acrylonitrile butadiène styrène (ABS)
- Polyamide (PA)
- Acide polylactique (PLA)
- Polycarbonate (PC)
- Polyétheréthercétone (PEEK)
- Polyéthylène (PE)
- Polypropylène (PP)
- Polychlorure de vinyle (PVC)
Plastiques thermodurcissables
Contrairement aux thermoplastiques, les plastiques thermodurcissables conservent leur état solide après polymérisation. Les liaisons chimiques des polymères des matériaux thermodurcissables s'établissent pendant la polymérisation, qui est déclenchée par la chaleur, la lumière ou une irradiation appropriée. La polymérisation forme des liaisons chimiques irréversibles. Les thermodurcissables se décomposent à la chaleur plutôt qu'ils ne fondent, et ils ne se reforment pas lorsqu'ils sont refroidis. Le recyclage ou le retour aux composants d’origine du matériau thermodurcissable est impossible.
Types courants de matériaux thermoplastiques:
- Ester de cyanate
- Époxy
- Polyester
- Polyuréthane
- Silicone
- Caoutchouc vulcanisé
Types de procédés de fabrication
Impression 3D
Les imprimantes 3D professionnelles fabriquent des pièces tridimensionnelles directement à partir de modèles CAO, en déposant le matériau couche par couche jusqu'à fabrication complète de la pièce.
Processus de fabrication
- Configuration de l'impression : Un logiciel de préparation d'impression est utilisé pour orienter et disposer les modèles à l'intérieur d'un volume d'impression, ajouter des structures de support si nécessaire, et découper en couches le modèle avec ses supports.
- Impression : L'impression dépend du type de technique d'impression 3D utilisé : le dépôt de fil fondu (FDM) fait fondre un filament de plastique, la stéréolithographie (SLA) polymérise une résine liquide, et le frittage sélectif par laser (SLS) fait fondre un plastique en poudre.
- Post-traitement : À la fin de l'impression, les pièces sont retirées de l'imprimante, nettoyées ou lavées, post-polymérisées (selon la technologie) et, enfin, les structures de support sont enlevées le cas échéant.
Comme les imprimantes 3D ne requièrent aucun outillage et sont configurées très rapidement pour imprimer un nouveau modèle, le coût de production d'une pièce sur mesure est négligeable comparé à celui des procédés traditionnels.
Les procédés d'impression 3D sont généralement plus lents et nécessitent plus de main d'œuvre que des procédés industriels utilisés en production de masse.
Les procédés d'impression 3D s'améliorant, le coût par pièce continue à diminuer et de nombreuses applications à volume de production faible à moyen sont alors envisageables.
Impression 3D | |
---|---|
Form | Grande liberté de conception |
Délai de production | Moins de 24 heures |
Durée de cycle | De moins d'une heure à plusieurs heures en fonction de la taille et du volume de la pièce |
Coût de mise en œuvre | € |
Coût par pièce | €€€ |
Volume | Volumes faibles à moyens (~1-1000 pièces) |
Alors que la plupart des procédés de fabrication avec des plastiques requièrent des machines industrielles coûteuses, des locaux dédiés et des opérateurs qualifiés, l'impression 3D permet aux entreprises de fabriquer facilement en interne des pièces et des prototypes rapides en plastique.
Les systèmes compacts d'impression 3D d'atelier ou sur table de fabrication de pièces en plastique sont abordables et demandent peu de place et pas de compétences particulières. Cela permet à des professionnels, ingénieurs, concepteurs et fabricants d'augmenter le nombre d'itérations et d'accélérer les cycles de production, passant de quelques jours ou semaines à quelques heures.
Matériaux
Il existe sur le marché de nombreux types d'imprimantes et de procédés d'impression 3D, et les matériaux utilisés varient en fonction du procédé.
Matériaux d'impression 3D | |
---|---|
Dépôt de fil fondu (FDM) | Plusieurs thermoplastiques, surtout ABS et PLA |
Stéréolithographie (SLA) | Résines thermodurcissables |
Frittage sélectif par laser (SLS, de l'anglais « Selective Laser Sintering ») | Thermoplastiques, généralement le nylon et ses composites |
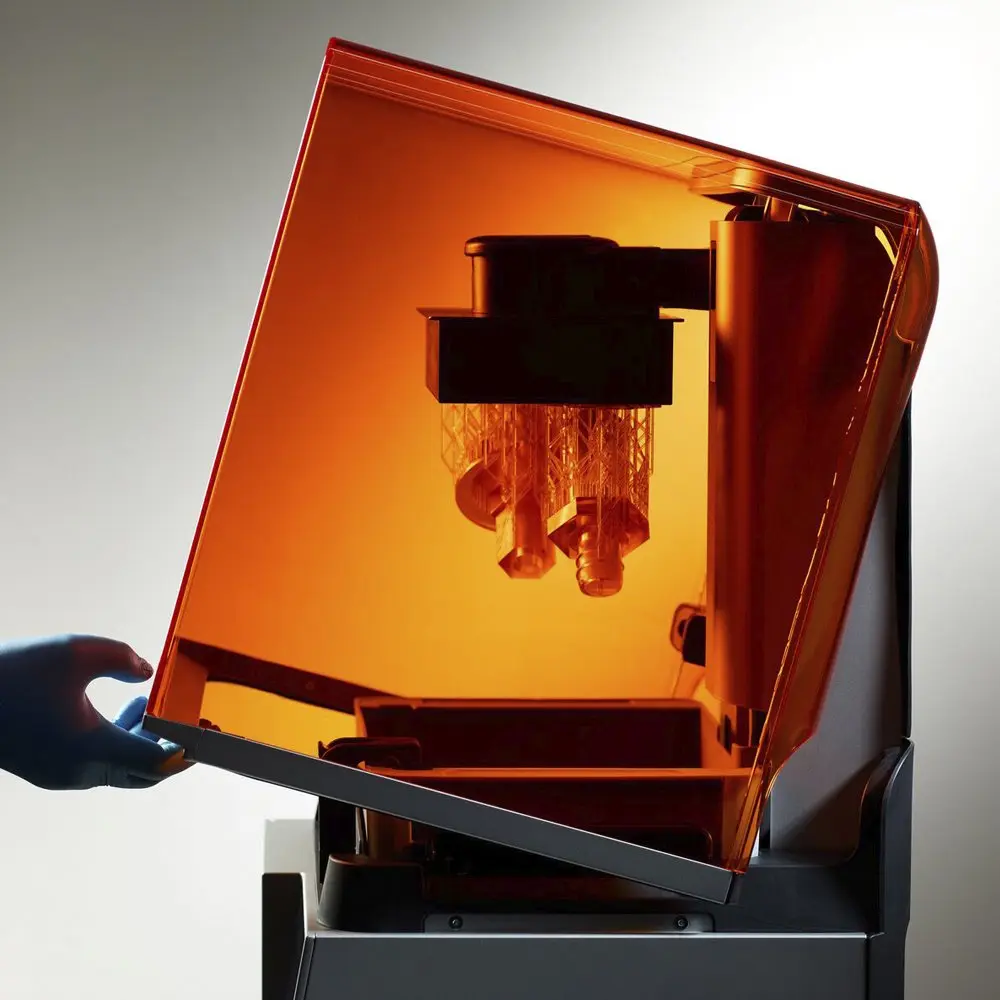
Introduction à l’impression 3D avec la stéréolithographie de bureau (SLA)
Vous cherchez une imprimante 3D résine pour créer des modèles 3D haute résolution ? Téléchargez notre livre blanc pour découvrir comment fonctionne l'impression SLA et pourquoi elle est tant utilisée pour créer des modèles aux détails incroyables.
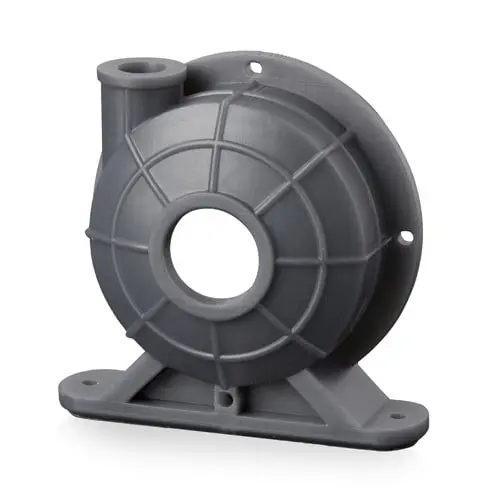
Commander un échantillon gratuit
Examinez et constatez par vous-même la qualité Formlabs. Nous enverrons un échantillon gratuit à votre bureau.
Usinage CNC
L'usinage CNC recouvre le fraisage, le tournage et d'autres procédés de fabrication soustractive commandés par ordinateur. Ces procédés s'appliquent à des blocs, de barres ou des tiges solides, de métal ou de plastique, auxquels on enlève de la matière pour les mettre en forme, par découpe, alésage, forage et ponçage.
Contrairement à la plupart des procédés de fabrication, l'usinage CNC est soustractif. De la matière est enlevée à la pièce soit par un outil tournant, la pièce restant fixe (fraisage), soit en faisant tourner la pièce, l'outil restant fixe (tournage).
Processus de fabrication
- Configuration de la tâche : Les machines CNC requièrent une étape intermédiaire consistant à créer et valider la trajectoire de l'outil (CAO à FAO). Les trajectoires d'outil commandent le trajet de l'outil, les vitesses de déplacement et d'éventuels changements d'outils.
- Usinage : Les trajectoires d'outil sont envoyées à la machine, qui commence le procédé soustractif. En fonction de la forme souhaitée du produit fini, la position de la pièce peut être modifiée de façon à ce que l'outil atteigne d'autres zones.
- Post-traitement : À la fin de l'usinage, la pièce est nettoyée, ébavurée et découpée.
L'usinage est idéal pour de petites séries de pièces en plastique requérant des tolérances serrées et présentant des formes difficiles à mouler. Les applications usuelles en sont, entre autres, le prototypage et la fabrication de pièces finies, comme des poulies, des engrenages et des roulements.
L'usinage CNC présente des coûts faibles à modérés et permet de produire des composants en plastique avec temps de production rapides à partir de nombreux matériaux.
L'usinage est soumis à plus de contraintes de géométrie des pièces que l'impression 3D. Le coût par pièce usinée augmente avec la complexité de la pièce. Des contre-dépouilles, des passages et des motifs particuliers sur plusieurs faces de la pièce contribuent à cette augmentation.
Les procédés d'usinage nécessitent des marges de tolérances pour l'accès des outils, et certaines géométries de la pièce, comme des canaux internes incurvés, sont difficiles voire impossibles à obtenir avec les méthodes soustractives conventionnelles.
Usinage CNC | |
---|---|
Form | Liberté de conception moyenne |
Délai de production | Moins de 24 heures |
Durée de cycle | De moins d'une heure à plusieurs heures en fonction de la taille, du modèle et de la complexité de la pièce |
Coût de mise en œuvre | €€ |
Coût par pièce | $$$$ |
Volume | Faible à élevé (~1-5000 pièces) |
Matériaux
La plupart des plastiques sont usinables, plus ou moins facilement. Des plastiques thermodurcissables plus souples requièrent des outils spéciaux pour tenir les pièces pendant l'usinage. Certains plastiques avec additifs peuvent être abrasifs et user plus rapidement l'outil.
Les plastiques suivants sont habituellement usinables :
- Acrylique (PMMA)
- Acrylonitrile butadiène styrène (ABS)
- Nylon polyamide (PA)
- Acide polylactique (PLA)
- Polycarbonate (PC)
- Polyétheréthercétone (PEEK)
- Polyéthylène (PE)
- Polypropylène (PP)
- Polychlorure de vinyle (PVC)
- Polycarbonate (PC)
- Polystyrène (PS)
- Polyoxyméthylène (POM)
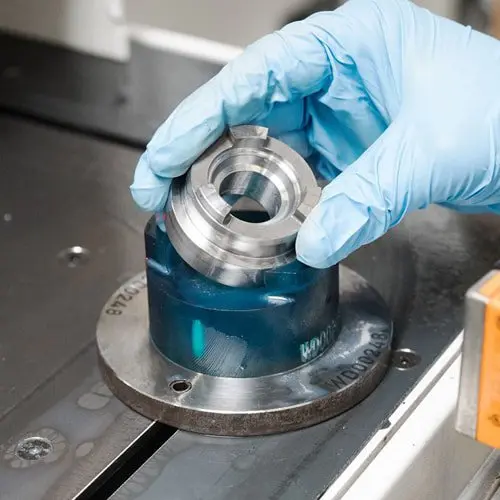
Innovation dans l'atelier de production : gabarits et fixations imprimés en 3D
Suivez ce webinaire pour apprendre comment concevoir et imprimer en 3D des gabarits et des fixations pour remplacer les pièces fabriquées par usinage, ainsi que cinq façons d'améliorer l'efficacité de votre usine de production grâce à l'impression 3D.
Coulée de polymères
Avec ce procédé, un moule est rempli d'une résine liquide ou de caoutchouc, qui réagissent chimiquement et se solidifient. Les polymères les plus utilisés dans ce procédé sont notamment le polyuréthane, l'époxy, la silicone et l'acrylique.
Processus de fabrication
- Préparation de moule : Le moule est enduit d'un produit qui facilite le démoulage. Il est souvent chauffé préalablement à une température qui dépend du matériau.
- Moulage : La résine synthétique est mélangée à un agent de polymérisation, puis versée ou injectée pour remplir la cavité du moule.
- Polymérisation : La résine polymérise dans le moule jusqu'à solidification (chauffer le moule peut accélérer le processus de polymérisation pour certain polymères).
- Démoulage : Le moule est ouvert et la pièce durcie est retirée.
- Découpe : Des artefacts formés au cours de la coulée, tels que des bavures, des carottes et des joints, sont éliminés par découpe ou ponçage.
Les moules flexibles en caoutchouc de latex ou de silicone RTV (vulcanisé à température ambiante) sont bien moins coûteux que des moules durs plus élaborés, mais ils ne peuvent être utilisés que pour un nombre limité de coulées (25 à 100, approximativement), en raison de la détérioration de leur surface par réaction chimique avec les uréthanes, les résines époxy, les polyesters et les acryliques.
Les moules en silicone RTV permettent d'obtenir des pièces moulées de grande qualité, à haut niveau de détail. L'impression 3D stéréolithographique est couramment utilisée pour fabriquer directement des masters de moules à partir de modèles CAO, parce qu'elle présente une haute précision et permet également d'obtenir des pièces présentant des détails très fins.
Ce procédé est relativement peu coûteux et nécessite peu d'investissement initial. Mais les polymères thermodurcissables utilisables sont généralement plus coûteux que leurs équivalents thermoplastiques, et la main d'œuvre requise pour le traitement des pièces est plus importante. Il faut traiter chaque pièce à la main après fabrication, ce qui accroit le coût par pièce lorsqu'on le compare à des méthodes de production automatisées comme le moulage par injection.
Le moulage des polymères est habituellement utilisé pour le prototypage, la production de petites séries et certaines applications dentaires ou de joaillerie.
Coulée de polymères | |
---|---|
Form | Grande liberté de conception |
Délai de production | Moins de 24 heures à quelques jours |
Durée de cycle | De quelques minutes à plusieurs jours, selon la durée de polymérisation |
Coût de mise en œuvre | € |
Coût par pièce | €€ |
Volume | Volumes faibles à moyens (~1-1000 pièces) |
Matériaux
- Polyuréthane
- Époxy
- Polyéther
- Polyesters
- Acrylique
- Silicone
Moulage par rotation
Le moulage par rotation (aussi appelé rotomoulage) est un procédé dans lequel un moule creux est chauffé et rempli de thermoplastique en poudre, puis mis en rotation selon deux axes. Il est surtout utilisé pour produire de grandes pièces creuses. Il existe également des procédés de rotomoulage avec des plastiques thermodurcissables, mais ils sont moins courants.
Processus de fabrication
- Charge : La cavité du moule est chargée en poudre de plastique. Les autres parties du moule sont installées pour le fermer afin de le chauffer.
- Chauffage : Le moule est chauffé jusqu'à ce que la poudre de plastique fonde et adhère à ses parois, pendant qu'il est mis en rotation selon deux axes perpendiculaires pour assurer l'uniformité du dépôt de plastique.
- Refroidissement : Le moule est refroidi lentement, toujours en mouvement, pour assurer que la peau de la pièce ne s'affaisse ni ne tombe avant sa solidification complète.
- Retrait des pièces : La pièce est retirée du moule et toute bavure en est éliminée.
Le moulage par rotation nécessite un outillage moins coûteux que les autres procédés de moulage parce qu'il utilise la force centrifuge plutôt que la pression pour remplir le moule. Les moules peuvent être fabriqués, usinés par machine CNC, fondus ou moulés à partir d'époxy ou d'aluminium, à un coût inférieur et beaucoup plus rapidement que les outillages nécessaires aux autres procédés, particulièrement lorsqu'il s'agit de grandes pièces.
Le rotomoulage permet de fabriquer des pièces avec des parois d'épaisseur à peu près uniforme. Après mise en place de l'outillage et du processus, le coût par pièce est très bas par rapport à la taille de la pièce. Il est également possible de rajouter au moule des pièces finies, telles que des fils métalliques, des tuyaux internes et d'autres structures.
Ces facteurs font du moulage par rotation un procédé qui convient parfaitement à la production de petites séries, ou une alternative au moulage par soufflage pour de petits volumes. Parmi les produits habituellement moulés par rotation, on peut citer des citernes, des bouées, de grands conteneurs, des jouets, des casques et des coques de canoë.
Le moulage par rotation impose certaines contraintes à la conception et les produis finis présentent des tolérances plus faibles que d'autres procédés. Comme le moule doit être chauffé et refroidi en entier, le procédé présente aussi de longs temps de cycle et il nécessite une main d'œuvre assez importante, ce qui limite son efficacité pour des applications à volume élevé.
Moulage par rotation | |
---|---|
Form | Liberté de conception moyenne, idéal pour des pièces creuses de grande taille |
Délai de production | De quelques jours à quelques semaines |
Durée de cycle | Habituellement < 1 heure |
Coût de mise en œuvre | €€€ |
Coût par pièce | €€ |
Volume | Moyen (~200-5000 pièces) |
Matériaux
Le matériau le plus couramment utilisé en moulage par rotation est le polyéthylène (PE), dans 80 % des cas, surtout parce qu'il peut être facilement réduit en poudre à température ambiante.
Les plastiques les plus couramment utilisés en rotomoulage sont notamment :
- Polyéthylène (PE)
- Polypropylène
- Polychlorure de vinyle
- Nylon
- Polycarbonate
Formage sous vide
Le formage sous vide ou thermoformage est un procédé de fabrication dans lequel un plastique est chauffé et mis en forme, généralement à l'aide d'un moule. Les équipements de moulage sous vide varient en taille et complexité, allant d'appareils sur table peu coûteux à des machines industrielles automatisées. Le procédé-type de moulage sous vide industriel est décrit étape par étape ci-dessous.
Processus de fabrication
- Cadre : Une feuille de plastique est installée dans un cadre.
- Chauffage : Le cadre avec la feuille sont placés à proximité d'éléments chauffants, pour ramollir le plastique et le rendre déformable.
- Vide : Le cadre est abaissé et le plastique est étiré sur le moule pendant que le vide est fait entre le plastique et le moule par aspiration de l'air, ce qui forme la pièce.
- Refroidissement et retrait : Une fois formée, la pièce doit refroidir avant de pouvoir être retirée. Des ventilateurs ou des vaporisateurs sont parfois utilisés pour réduire le temps de cycle.
- Découpe : Une fois la pièce retirée du moule, le matériau en excès est éliminé à la main ou par usinage CNC.
Les coûts d'outillage pour le moulage sous vide sont bas comparés à ceux d'autres procédés, parce que les forces et pressions nécessaires sont faibles. Les moules sont faits en bois, en plâtre ou imprimés en 3D en résine, pour fabriquer de petites séries ou des pièces sur mesure. Pour des volumes de production plus importants, les fabricants utilisent des outils en métal plus durables.
En raison du grand choix de machines de thermoformage et de moulage sous vide et des possibilités d'automatisation des machines haut de gamme, le thermoformage convient à toutes les applications, de la production de pièces sur mesure et de prototypes à la production de masse. Cependant, le procédé est limité en conception et permet uniquement la fabrication de pièces à parois relativement minces et à formes géométriques simples.
Parmi les pièces les plus courantes fabriquées par moulage sous vide, on trouve des emballages, des bacs à douche, des panneaux de portes de voiture, des coques de bateau, ainsi que des dispositifs sur mesure comme des plaques occlusales dentaires.
Formage sous vide | |
---|---|
Form | Liberté de conception réduite : pas de formes géométriques complexes, pièces à parois minces uniquement |
Délai de production | Moins de 24 heures à plusieurs semaines |
Durée de cycle | Quelques secondes à quelques minutes, selon l'équipement |
Coût de mise en œuvre | $-$$$$ |
Coût par pièce | $-$$$ |
Volume | Tout volume |
Matériaux
La plupart des thermoplastiques sont utilisables en thermoformage, ce qui offre un large choix de matériaux.
Les plastiques les plus couramment utilisés en thermoformage sont notamment :
- Acrylique (PMMA)
- Acrylonitrile butadiène styrène (ABS)
- Polytéréphtalate d'éthylène-glycol (PETG)
- Polystyrène (PS)
- Polycarbonate (PC)
- Polypropylène (PP)
- Polyéthylène (PE)
- Polychlorure de vinyle (PVC)
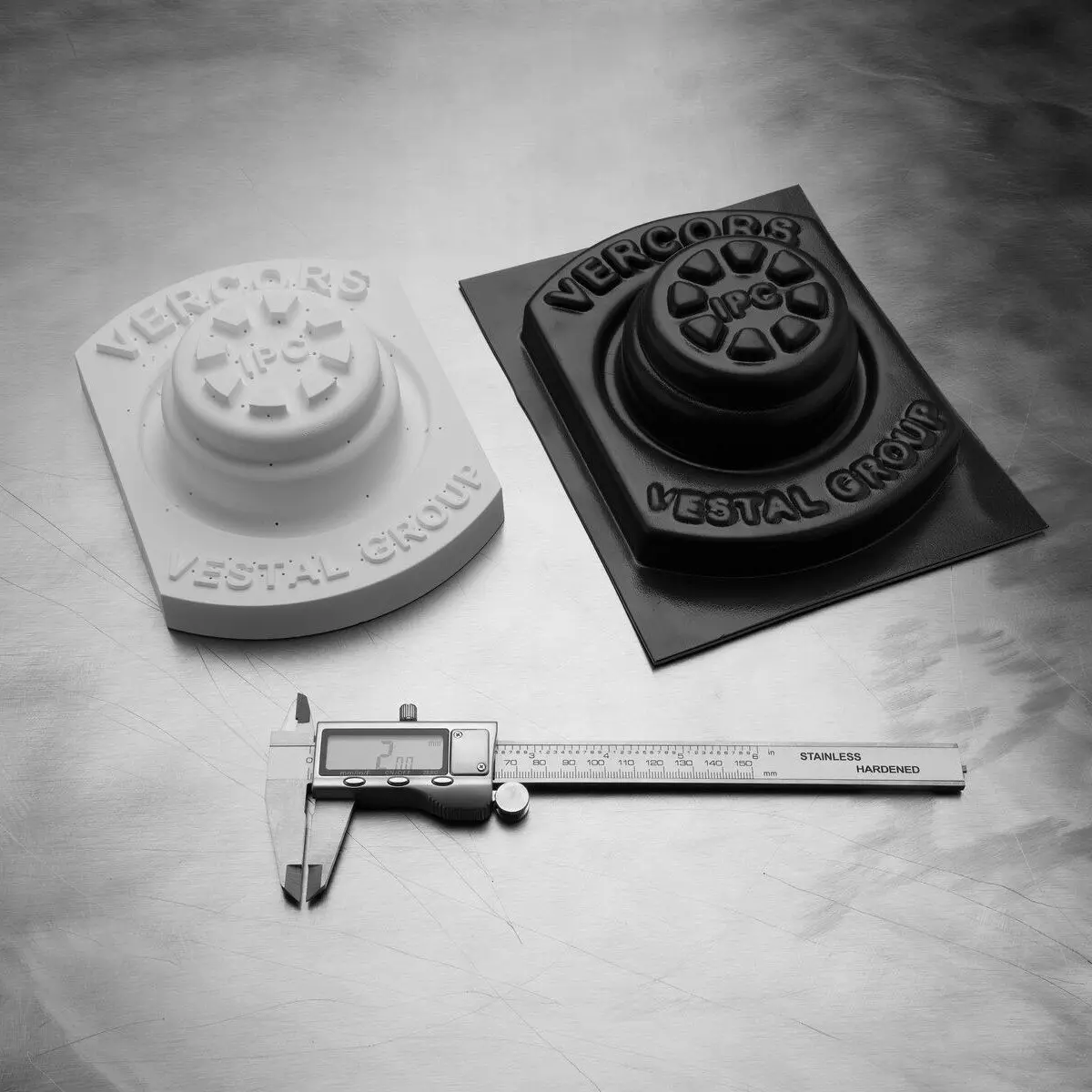
Le thermoformage rapide de petites séries avec des moules imprimés en 3D
Téléchargez notre livre blanc pour apprendre comment créer rapidement des moules complexes grâce à l’impression 3D et pour obtenir des conseils et des recommandations à suivre lors de la préparation des pièces de moule.
Moulage par injection
Le moulage par injection consiste à injecter un thermoplastique fondu dans un moule. C'est le procédé le plus utilisé pour la fabrication de masse de pièces en plastique.
Processus de fabrication
- Configuration du moule : Si la pièce comporte des inserts, ceux-ci sont ajoutés manuellement ou par un robot. Le moule est fermé par une presse hydraulique.
- Extrusion plastique : De petits granulés de plastique sont fondus et extrudés par entrainement par vis sans fin dans un fourreau chauffant.
- Moulage : Le plastique fondu est injecté dans le moule.
- Refroidissement et retrait : La pièce refroidit dans le moule jusqu'à ce qu'elle soit suffisamment solide pour être éjectée, mécaniquement ou avec de l'air comprimé.
- Post-traitement : Les carottes et les canaux d'injection, ainsi que les éventuelles bavures sont éliminés de la pièce, souvent automatiquement à l'ouverture du moule.
Les moules pour l'injection sont extrêmement complexes et doivent respecter des tolérances serrées pour produire des pièces de grande qualité. En raison des fortes températures et pressions auxquelles ils sont soumis, ces moules doivent être usinés à partir de métaux tels que l'acier renforcé. Des moules en aluminium sont moins coûteux mais ils s'usent plus vite et sont donc utilisés pour la production de plus petites séries.
Le moulage par injection peut produire des pièces extrêmement complexes mais certaines formes géométriques vont augmenter significativement le coût. Les coûts d'outillage pourront rester à des niveaux raisonnables en suivant les instructions de conception en vue de la fabrication (design for manufacturing ou DFM). La fabrication de nouveaux moules d'injection peut prendre des mois et leur coût peut atteindre des nombres à cinq ou six chiffres.
Malgré des coûts initiaux élevés et des cadences lentes, le moulage par injection n'a pas de concurrent pour des applications à gros volume de production. Une fois que l'outillage est prêt et fonctionne, les temps de cycles sont de l'ordre de quelques secondes et des millions de pièces peuvent être produites pour un coût réduit par rapport à tous les autres procédés de fabrication.
Moulage par injection | |
---|---|
Form | Liberté de conception modérée à grande |
Délai de production | 2 à 4 mois |
Durée de cycle | Secondes |
Coût de mise en œuvre | $$$$$ |
Coût par pièce | € |
Volume | Grand volume (5000 pièces et plus) |
Matériaux
Le moulage par injection convient à pratiquement tous les types de thermoplastiques. Un procédé similaire, appelé moulage par injection et réaction (RIM), est utilisé pour fabriquer des pièces avec des thermodurcissables.
Les plastiques les plus couramment utilisés en moulage par injection sont notamment :
- Acrylique (PMMA)
- Acrylonitrile butadiène styrène (ABS)
- Polyamide (PA)
- Polytéréphtalate d'éthylène-glycol (PETG)
- Polystyrène (PS)
- Polycarbonate (PC)
- Polypropylène (PP)
- Polyéthylène (PE)
- Polychlorure de vinyle (PVC)
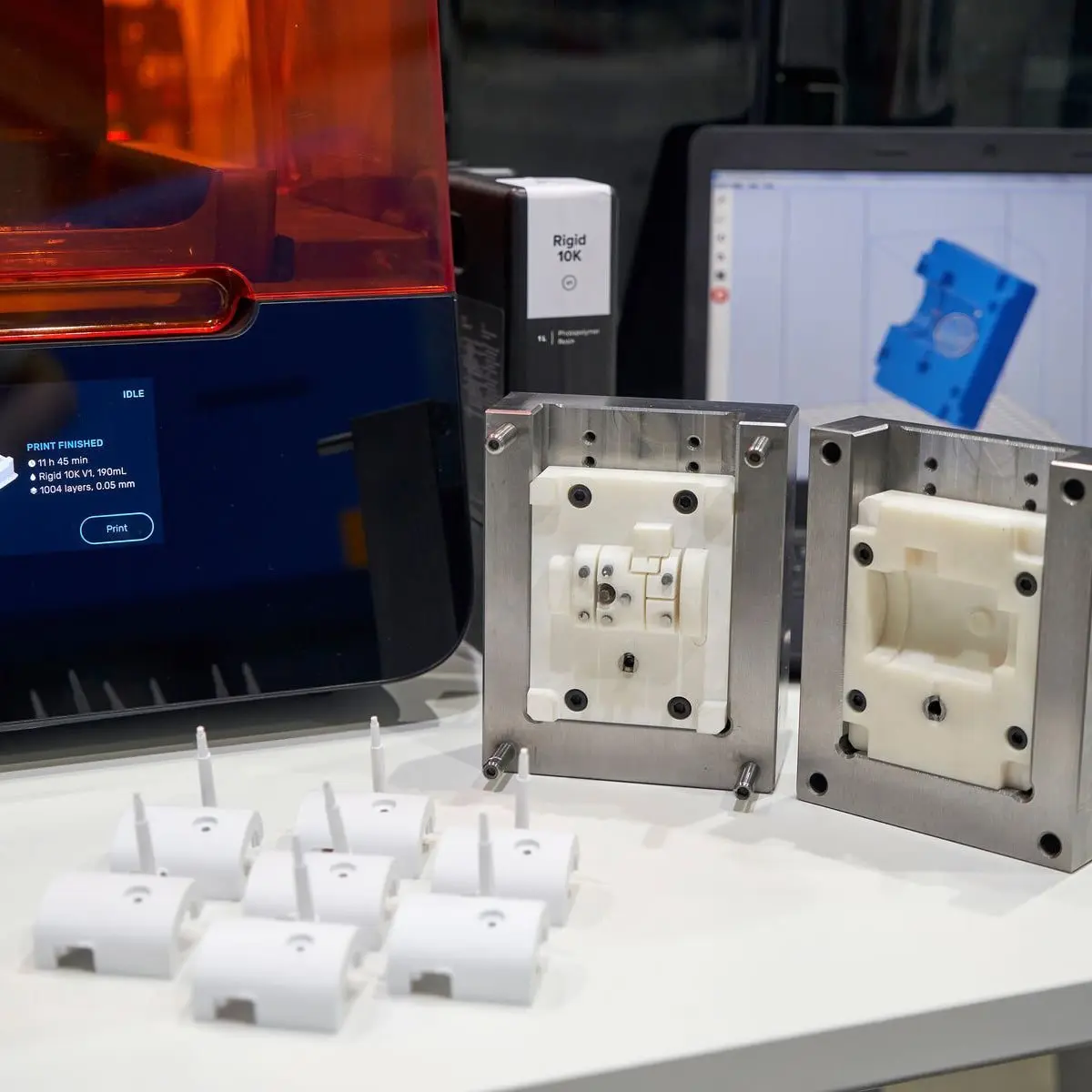
Le moulage par injection rapide de petites séries avec des moules imprimés en 3D
Téléchargez ce livre blanc pour savoir comment utiliser des moules imprimés en 3D pour le processus de moulage par injection, et ainsi réduire les coûts et les délais de production. Vous y trouverez des études de cas réels, réalisées chez Braskem, Holimaker et Novus Applications.
Filage
Le principe de fonctionnement du moulage par filage et de pousser un plastique à travers une filière. La forme de la filière correspond à la section de la pièce finie.
Processus de fabrication
- Extrusion plastique : Le plastique est fondu et extrudé par entrainement par vis sans fin dans un fourreau chauffant.
- Moulage : Le plastique est forcé à travers une filière qui donne sa forme à la pièce.
- Refroidissement : Le plastique extrudé est refroidi.
- Coupe ou enroulage : La forme fabriquée en continu est embobinée ou découpée en morceaux.
L'équipement en machines pour le filage est relativement bas, comparé à celui des machines industrielles CNC ou de moulage par injection, parce qu'il est moins complexe et ne requiert pas un niveau de précision des machines aussi élevé. En raison de la simplicité de leurs formes, les dies sont également bien moins coûteuses que les moules nécessaires à l'injection.
Comme le moulage par injection, le filage est un procédé pratiquement continu, ce qui réduit beaucoup le prix des pièces produites.
Le filage se limite à la production de pièces de formes particulières, présentant des profils continus en T, I, L ou U, et des sections circulaires ou carrées. Il s'utilise généralement pour fabriquer des conduites, des flexibles, des pailles et des cadres de fenêtres.
Filage | |
---|---|
Form | Limitée à des formes longues et continues |
Délai de production | Quelques semaines |
Durée de cycle | Quelques secondes (ou en continu) |
Coût de mise en œuvre | €€€ |
Coût par pièce | € |
Volume | Moyen à grand (1000 pièces et plus) |
Matériaux
Pratiquement tous les types de thermoplastiques et notamment :
- Acrylique (PMMA)
- Acrylonitrile butadiène styrène (ABS)
- Polyamide (PA)
- Polytéréphtalate d'éthylène-glycol (PETG)
- Polystyrène (PS)
- Polycarbonate (PC)
- Polypropylène (PP)
- Polyéthylène (PE)
- Polychlorure de vinyle (PVC)
Moulage par soufflage
Le moulage par soufflage permet de fabriquer des pièces creuses en plastique, en gonflant un tube de plastique chauffé à l'intérieur d'un moule, jusqu'à ce qu'il lui donne la forme souhaitée.
Processus de fabrication
- Configuration du moule : De petits granulés de plastique sont fondus et mis en forme dans un tube creux, appelé paraison ou préforme (en fonction du type de moulage par soufflage).
- Moulage : La paraison est fixée dans un moule et gonflée à l'air comprimé jusqu'à prendre la forme intérieure du moule.
- Refroidissement et retrait : La pièce refroidit dans le moule jusqu'à ce qu'elle soit suffisamment solide pour être éjectée.
Le moulage par soufflage fonctionne à des pressions bien moins élevées que le moulage par injection, ce qui contribue à faire baisser le coût d'outillage. Comme le moulage par injection ou le filage, le moulage par soufflage est un procédé continu qui peut être complètement automatisé, ce qui augmente le rythme de production et diminue les coûts des unités.
Le moulage par soufflage est le procédé le plus utilisé pour fabriquer des produits en plastique à grande échelle. Il est utilisé notamment pour la fabrication de bouteilles, de jouets, de composants automobile, de pièces industrielles et d'emballages.
Moulage par soufflage | |
---|---|
Form | Liberté de conception réduite : formes creuses à parois minces uniquement, pas de formes géométriques complexes |
Délai de production | Quelques semaines |
Durée de cycle | Secondes |
Coût de mise en œuvre | $$$$ |
Coût par pièce | € |
Volume | Grand volume (5000 pièces et plus) |
Matériaux
Le moulage par soufflage s'applique à de nombreux thermoplastiques, les plus courants étant :
- Polytéréphtalate d'éthylène (PET)
- Polypropylène (PP)
- Polychlorure de vinyle (PVC)
- Polystyrène (PS)
- Polycarbonate (PC)
- Acrylonitrile butadiène styrène (ABS)
Fabrication rapide de pièces en plastique avec l'impression 3D
Les processus de production des matières plastiques sont en constante évolution et les points d'inflexion à partir desquels il est judicieux de passer d'une technique à l'autre se déplacent, en raison des améliorations apportées aux équipements, aux matériaux et aux économies d'échelle.
L'impression 3D est un ensemble de technologies plus récentes, mais qui se développent rapidement et qui s 'ouvrent à un plus large éventail d'applications de faible à moyen volume à mesure que le matériel et les matériaux s'améliorent et que le coût par pièce continue de baisser.
En savoir plus sur la manière dont les fabricants leaders du secteur se servent l'impression 3D pour réduire les coûts et les temps de réalisation, de la conception à la production.