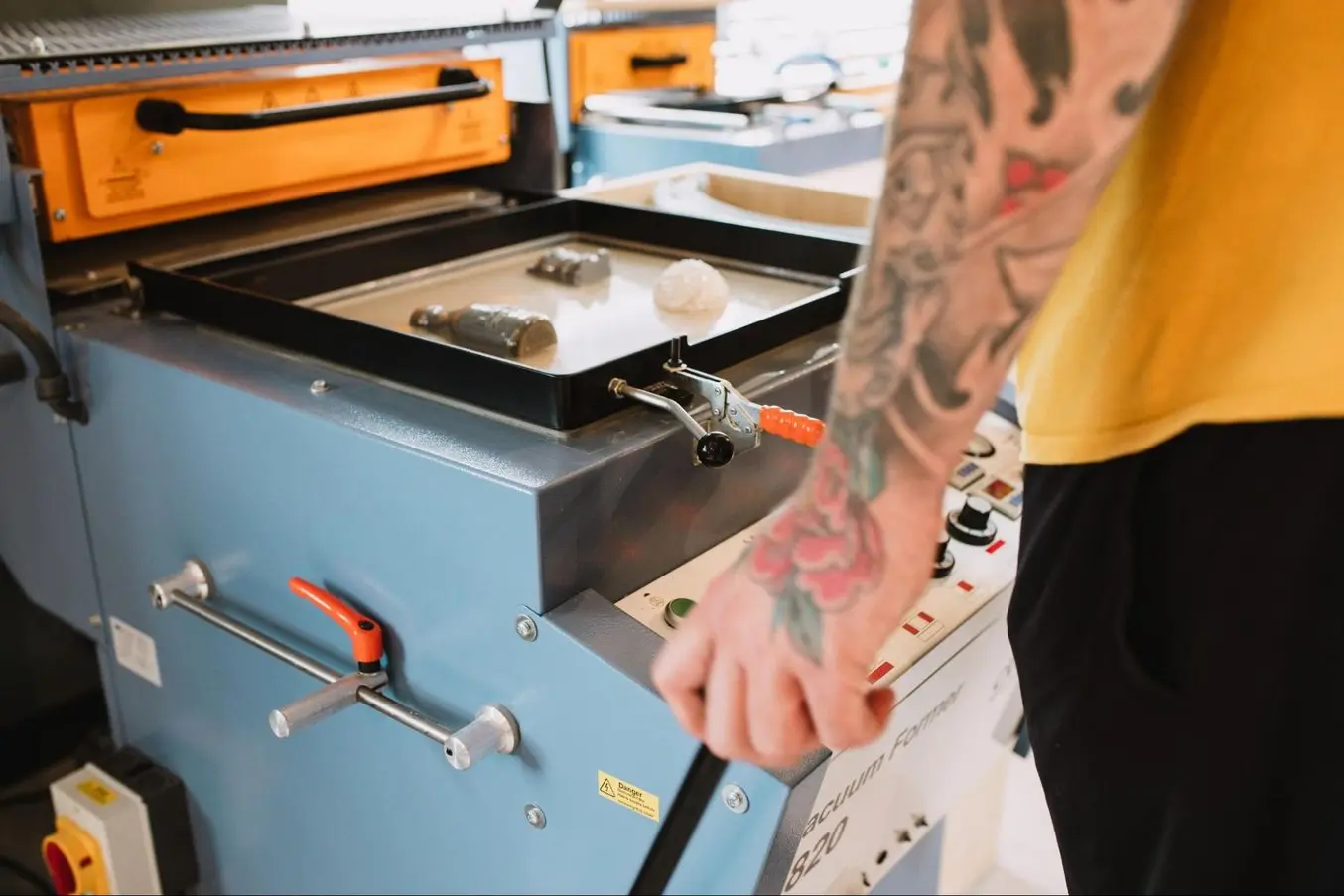
Il existe des plastiques de toutes tailles et couleurs, présentant toutes sortes de propriétés différentes. Cette grande diversité fait du plastique un excellent matériau pour les fabricants souhaitant produire des prototypes et des pièces d'utilisation finale. Le thermoformage est un procédé de fabrication qui offre aux fabricants une solution polyvalente pour traiter des feuilles de plastique.
Dans ce guide complet, découvrez différents procédés de thermoformage, les matériaux et équipements utilisés, et apprenez à créer des moules de thermoformage avec des techniques avancées telles que l'impression 3D.
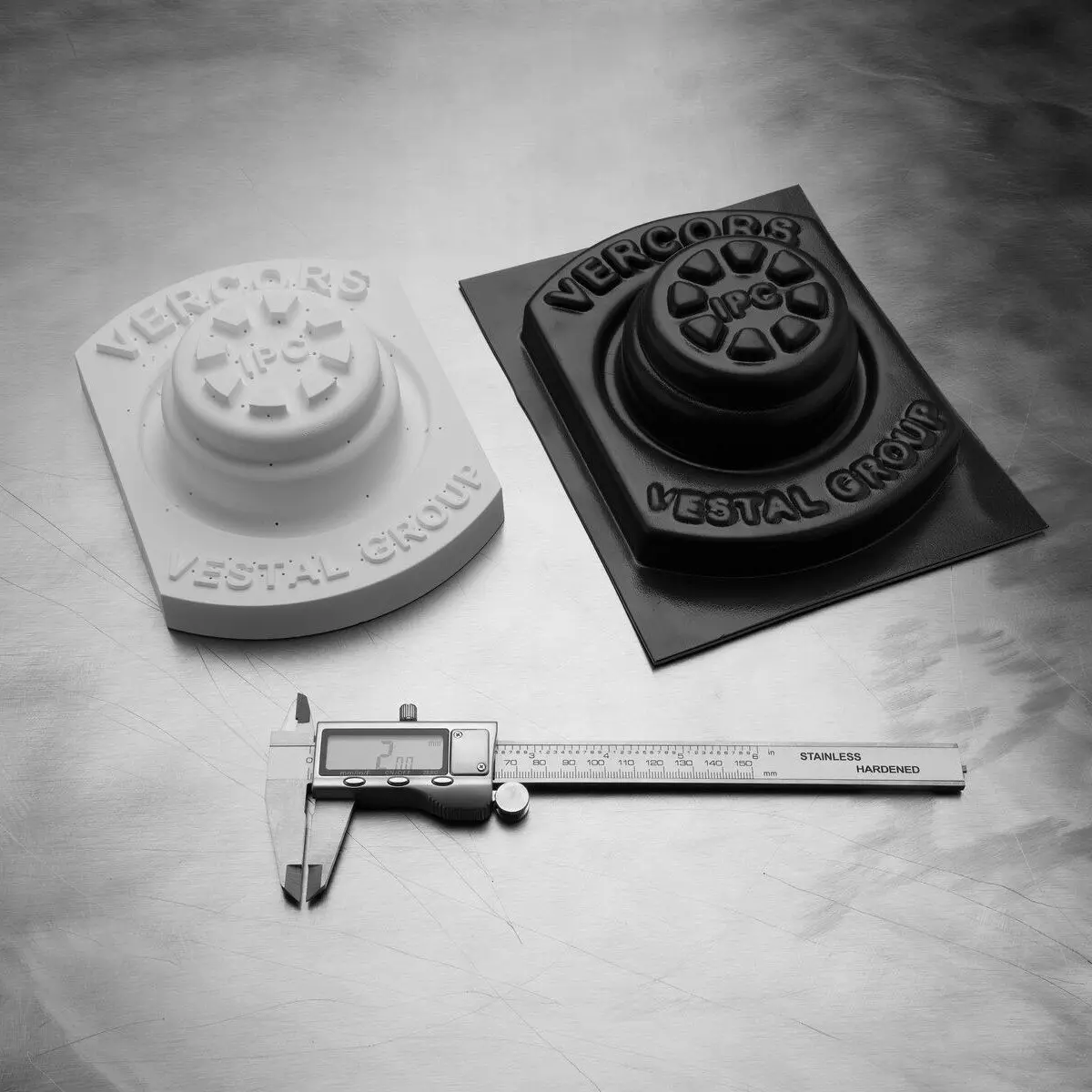
Le thermoformage rapide de petites séries avec des moules imprimés en 3D
Téléchargez notre livre blanc pour apprendre comment créer rapidement des moules complexes grâce à l’impression 3D et pour obtenir des conseils et des recommandations à suivre lors de la préparation des pièces de moule.
Qu'est-ce que le thermoformage ?
Le thermoformage est un procédé de fabrication de plastiques qui consiste à chauffer une feuille de plastique et à lui donner une forme spécifique à l'aide d'un moule. Le plastique formé est ensuite refroidi et découpé pour obtenir la pièce finale. Le processus est exécuté à l'aide d'une machine de thermoformage qui chauffe et étire la feuille thermoplastique souple sur le moule. Les machines de thermoformage modernes prennent généralement en charge le découpage de la feuille, tandis qu'avec des machines plus anciennes, le découpage et le refroidissement doivent être effectués en externe.
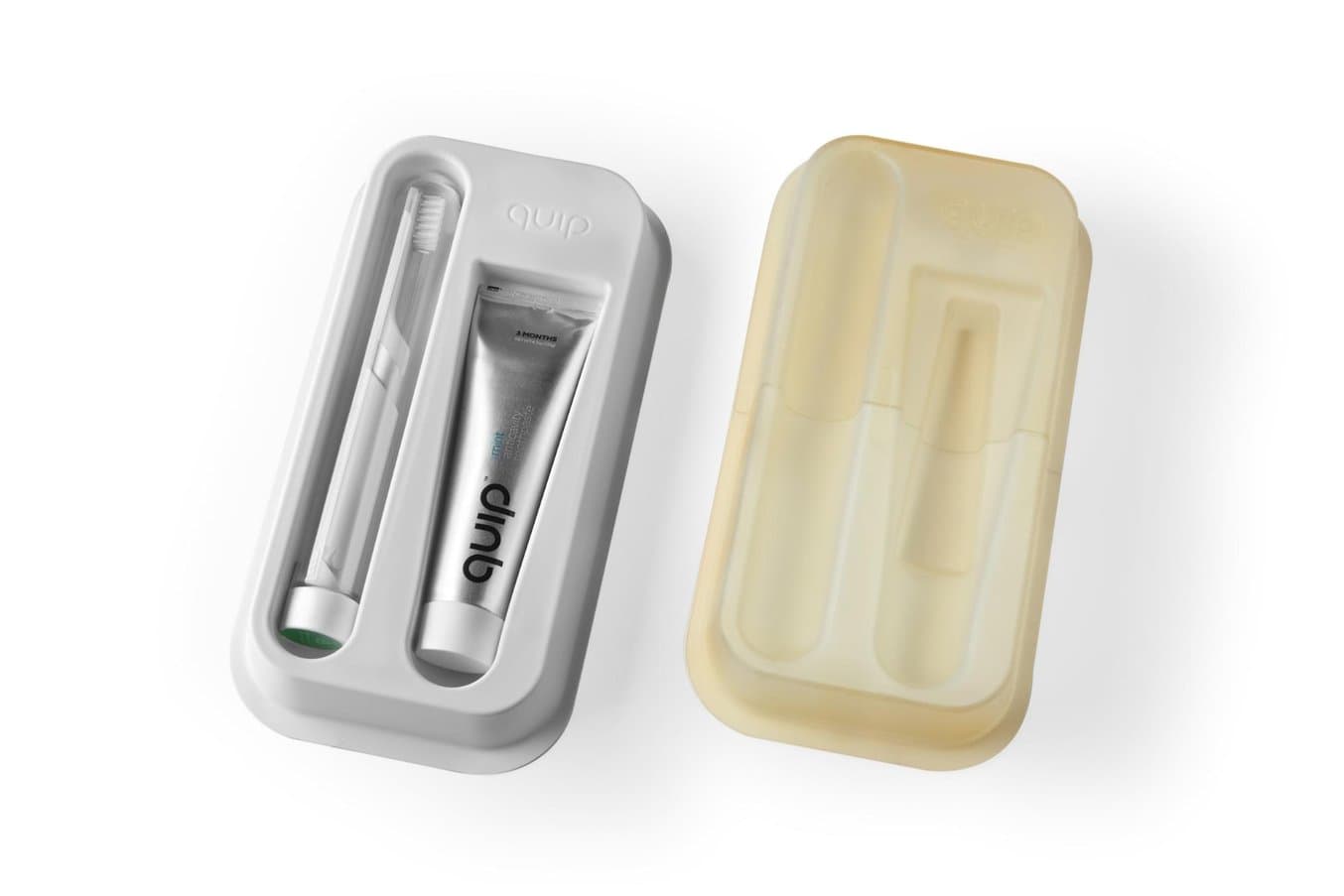
Le thermoformage est couramment utilisé pour produire des emballages en plastique.
Les thermoplastiques sont les matériaux utilisés pour le thermoformage. Ces matériaux comprennent l'ABS, le polystyrène, le polycarbonate, le PETP, etc. Le choix du matériau dépend du projet de fabrication et des caractéristiques que l'on veut donner au produit fini.
Le thermoformage est utilisé pour fabriquer des emballages pour des produits agricoles, des produits pharmaceutiques, des biens de consommation, des appareils ménagers, etc. Il est également utilisé pour fabriquer des pièces durables telles que des composants d'avions, des équipements de manutention, des intérieurs d'automobiles et des équipements médicaux.
Contrairement à d'autres procédés de fabrication conventionnels, le thermoformage permet aux fabricants de produire de petits ou de grands volumes d'emballages à un coût abordable. Autre avantage important : le thermoformage permet également d'utiliser presque tous les types de thermoplastiques pour produire rapidement des articles de haute qualité destinés à une utilisation finale.
Le thermoformage présente aussi certains inconvénients ; en effet, il ne peut produire que des modèles à paroi mince, les épaisseurs peuvent être inégales, et il n'est pas toujours adapté pour produire des pièces à géométrie complexe. Les fabricants qui souhaitent tirer parti du thermoformage peuvent utiliser ce guide pour comprendre comment l'utiliser au mieux, afin d'améliorer la productivité et de réduire les coûts.
Procédés de thermoformage
Le thermoformage est un processus de fabrication qui englobe toutes les différentes méthodes que les fabricants peuvent choisir pour former des feuilles de plastique chauffées. Le formage sous vide et le formage sous pression peuvent être très avantageux pour les fabricants.
Bien qu'il existe une multitude de procédés, les techniques de thermoformage les plus populaires sont les suivantes :
-
Formage sous vide : ce procédé de thermoformage utilise le vide pour façonner la feuille. Tout d'abord, on chauffe la feuille de plastique pour la rendre malléable. La machine de formage sous vide retire ensuite l'air, plaquant ainsi la feuille contre un moule. Le procédé sous vide est connu pour sa rentabilité et la rapidité du processus de fabrication.
-
Formage sous pression : le processus de formage sous pression implique également une feuille de plastique chauffée et l'utilisation du vide pour évacuer l'air et plaquer la feuille contre un moule. Mais il y a une étape supplémentaire. Une fois l'air retiré, un outil applique une pression sur le plastique formé afin de mieux lui imprimer sa forme finale. Le formage sous pression est utilisé lorsque la pièce thermoformée nécessite un niveau de détail plus élevé.
-
Formage mécanique : ce procédé implique l'utilisation d'une force mécanique directe pour façonner la feuille de plastique préchauffée. Un bouchon central force la feuille pliable à remplir un espace entre le bouchon et le moule, ce qui imprime les motifs de surface sur la feuille de plastique. Le thermoformage mécanique est utilisé lorsque la pièce finale doit être précise et détaillée.
-
Formage par drapage : dans le cas du drapage, la feuille de plastique chauffée est drapée sur un mandrin présentant des motifs spécifiques. Le mandrin est pressé sur la feuille de plastique pour former la pièce finie. Le procédé de formage par drapage est l'une des techniques de thermoformage les plus abordables, car il ne nécessite pas beaucoup d'outils. Comme l'épaisseur du matériau peut être maintenue, le processus n'entraîne pas de faiblesses dans les pièces.
-
Formage par moules appariés : ce procédé de thermoformage est utilisé pour fabriquer des objets très détaillés. Le processus de formage par moules appariés implique l'utilisation d'un moule mâle et d'un moule femelle pour façonner la feuille de plastique chauffée. La machine de formage applique une pression pour rassembler les moules sur la feuille de plastique. Les deux moules impriment ainsi leur forme ou motif à la feuille.
-
Formage double-coque : ce procédé consiste à former deux couches et à les combiner pour former un seul objet. Les feuilles de plastique sont chauffées simultanément, formées et assemblées pour produire un objet. Le procédé de formage double-coque est parfait pour fabriquer des objets creux ou à double paroi.
-
Formage par soufflage : le procédé de formage par soufflage est une technique de thermoformage à forme libre qui n'a pas recours à des moules pour façonner le plastique chauffé. La machine de formage utilise des jets d'air pour souffler le plastique dans une bulle jusqu'à ce que la pièce finale soit formée.
Processus de thermoformage | Rapport coût-efficacité | Volume de production | Application |
---|---|---|---|
Formage sous vide | Très abordable, processus de fabrication rapide | Faibles – grands volumes | Pour la production d'articles où la précision et l'exactitude ne jouent pas un rôle crucial, comme par exemple les articles ménagers et les emballages. |
Formage sous pression | Processus de fabrication abordable | Faibles – grands volumes | Pour produire des articles durables et uniformes |
Formage mécanique | Processus de fabrication abordable | Moyens – grands volumes | Utilisé pour la fabrication d'articles de haute qualité et précis |
Formage par drapage | Très abordable, processus de fabrication rapide | Moyens – grands volumes | Composants de grande taille et matériaux épais avec des formes courbes simples |
Formage de moules appariés | Processus de fabrication coûteux en raison de l'outillage nécessaire | Moyens – grands volumes | Utilisé pour fabriquer des pièces et des composants durables tels que des fixations et des accessoires de véhicules. |
Formage double-coque | Processus de fabrication abordable | Moyens – grands volumes | Utilisé pour fabriquer des articles d'emballage tels que les objets creux ou à double paroi |
Formage par soufflage | Plus cher que les autres options | Production en petite série | Utilisé pour la fabrication de lucarnes, de pièces bombées, etc. |
Matériaux de thermoformage
Le thermoformage est utilisé pour produire des emballages alimentaires, des composants d'avions, des jouets, des palettes et d'autres articles en plastique. Il est donc conseillé aux fabricants de prendre en considération diverses matières plastiques avant de lancer un cycle de production. Les plastiques les plus couramment utilisés en thermoformage sont :
-
Polypropylène (PP) : le polypropylène est le plastique le plus populaire pour le thermoformage, car il offre une bonne qualité et permet de fabriquer de gros volumes de pièces. Il est couramment utilisé dans la fabrication d'emballages, de ventilateurs, de jouets et d'autres articles en plastique. Le polypropylène est souvent utilisé en raison de son excellente résistance aux produits chimiques, à l'usure et à la chaleur. Le polypropylène est également un matériau abordable qui peut être utilisé pour les divers procédés de thermoformage présentés ici.
-
Polystyrène (PS) : ce polymère d'hydrocarbure aromatique est transparent et friable. Le polystyrène est souvent utilisé comme matériau d'emballage pour le thermoformage car il est résistant à l'eau et à l'air. Les fabricants utilisent le polystyrène pour fabriquer des emballages alimentaires, des écrins de bijoux, des boîtiers de CD et des articles ménagers.
-
Polytéréphtalate d'éthylène (PET) : le PET offre une excellente résistance aux alcools, aux huiles essentielles, aux produits chimiques, aux chocs et à la rupture sous traction. Il est couramment utilisé pour produire des contenants de boissons gazeuses, des bouteilles d'eau et de nombreux produits alimentaires.
-
Polyéthylène basse densité (PEBD) : le PEBD est un thermoplastique qui résiste aux produits chimiques et aux rayons UV. Ce plastique est flexible et possède une grande résistance à la traction. Les fabricants peuvent utiliser le PEBD pour fabriquer des films d'emballage, des DVD, des isolants pour câbles, des contenants et des articles résistant aux produits chimiques.
-
Polyéthylène haute densité (PEHD) : les caractéristiques de base du PEHD sont similaires à celles du PEBD. Il est également réputé pour sa résistance aux produits chimiques, aux rayons UV et à l'eau.
C'est un thermoplastique durable qui peut être utilisé pour fabriquer des films d'emballage, des bouteilles soufflées, des contenants, des tuyaux et des sacs en plastique.
-
Polychlorure de vinyle (PVC) : le PVC est un autre plastique populaire utilisé dans la fabrication de tuyaux, de cadres de fenêtres, d'intérieurs d'automobiles, d'articles domestiques, d'emballages et de chaussures.
Le PVC peut être développé pour être rigide ou flexible, selon les exigences du fabricant. Ce thermoplastique est également dense, durable et résistant à l'eau. Il est important de noter que le PVC n'est pas totalement résistant aux produits chimiques et peut réagir au chlore.
-
Polycarbonate (PC) : les polycarbonates sont des matériaux solides et résistants qui peuvent subir de grandes déformations sans se fissurer ou se casser.
Ils sont ignifuges et résistants à la chaleur. De plus, ils possèdent de bonnes propriétés d'isolation électrique. Certains types de PC sont également optiquement transparents. Les PC sont utilisés pour fabriquer des lentilles de contact en plastique, des dispositifs médicaux, des composants automobiles, des équipements de protection (lentilles, casques de sécurité), du verre pare-balles, des phares de voiture et des composants de construction.
-
Acétate de cellulose : l'acétate de cellulose est un matériau thermoplastique écologique.
Ce thermoplastique est fabriqué à partir de matériaux renouvelables telles que la pâte de bois transformée. L'acétate de cellulose est généralement incolore et transparent. Il est utilisé pour fabriquer des articles ménagers, des films d'emballage, des cadres en verre et des revêtements de pilules.
-
Polyméthacrylate de méthyle (PMMA) : le PMMA est solide, durable et transparent et résiste aux éléments climatiques.
Les fabricants utilisent le PMMA pour produire des lentilles, des phares de véhicules et des emballages transparents. La durabilité du PMMA permet aux pièces d'utilisation finale de résister à l'usure.
-
Acrylonitrile butadiène styrène (ABS) : l'ABS est rigide et est capable de résister à l'abrasion et aux basses températures.
Les fabricants peuvent tirer parti du thermoformage et de l'ABS pour produire des emballages électroniques, des contenants alimentaires et des appareils ménagers.
Parmi les autres matériaux que les fabricants peuvent utiliser figurent le polytétrafluoroéthylène (PTFE), le polyamide, le HIPS (polystyrène à impact élevé) et plus. La sélection du matériau dépend de la technique de thermoformage choisie et des exigences du projet. Le tableau des applications peut vous aider à faire le bon choix.
Applications | Matériaux | Techniques courantes de thermoformage |
---|---|---|
Emballages | ABS, PP, PMMA, PVC, PET, PEBD | Formage sous pression, formage sous vide, formage par moules appariés, formage double-coque, formage mécanique |
Articles ménagers et de consommation | ABS, PS, PVC, PP, PC | Formage sous pression, formage sous vide, formage mécanique |
Intérieurs et composants automobiles | PC, PMMA, PEHD, PEBD | Formage par drapage, formage par moules appariés, formage par pression |
Soins de santé et dispositifs médicaux | Acétate de cellulose, PEBD, PC | Formage sous pression, formage mécanique, formage sous vide |
Construction, CVC et plomberie | PVC, PEHD, PC | Formage mécanique, formage sous pression, formage sous vide, drapage |
Forte épaisseur vs. Thermoformage de fine épaisseur
Les variations dimensionnelles des feuilles de plastique utilisées dans le thermoformage constituent la différence entre le thermoformage de forte épaisseur et de fine épaisseur. Les équipements de thermoformage de fine épaisseur utilisent des feuilles fines provenant de bobines de plastique. Le thermoformage de forte épaisseur utilise quant à lui des feuilles de plastique épaisses. Les variations d'épaisseur jouent un rôle crucial dans le choix de l'équipement de thermoformage.
Par exemple, les fabricants qui ont l'intention de produire des gobelets en plastique et des emballages alimentaires utilisent le thermoformage de fine épaisseur pour produire des articles plus fins. À l'inverse, la production de palettes et de contenants nécessite un thermoformage de forte épaisseur et un équipement adapté. Les équipements de thermoformage de forte épaisseur sont conçus pour la production de faibles et de moyens volumes, tandis que les équipements de thermoformage de fine épaisseur sont conçus pour produire de gros volume.
Voici un aperçu des différences entre le thermoformage de forte et de faible épaisseur :
Thermoformage du plastique | Forte épaisseur | Fine épaisseur |
---|---|---|
Épaisseur de la pièce | .060–.375″ 1,5 – 9,5 mm | < .125” < 3 mm |
Type de machine | Feuilles de plastique | Bobines de plastique fin |
Matériaux thermoplastiques utilisés | ABS, PEHD, polypropylène | PETP, PET, PVC |
Volume de production | Faible – moyen | Moyen – élevé |
Exemples d'utilisation | Boîtiers électroniques, pièces intérieures, outillage industriel, composants structurels permanents, palettes, baignoires, bacs à douche, bagages. | Emballages jetables rigides ou semi-rigides, articles à usage unique (contenants alimentaires, tasses, assiettes et plateaux jetables) et petits emballages de dispositifs médicaux. |
Équipement de thermoformage
Chaque procédé de thermoformage nécessite un équipement spécifique. Différentes machines sont nécessaires pour le formage sous vide, le formage sous pression, le formage double-coque et le formage par drapage.
Les thermoformeuses peuvent être subdivisées en catégories en fonction de leurs cas d'utilisation. Il existe trois catégories : les thermoformeuses de bureau, industrielles et de bricolage. Les fabricants professionnels et les amateurs peuvent choisir parmi ces options en fonction de leurs application.
Pour choisir le bon équipement de thermoformage, il convient de tenir compte des spécifications produit suivantes :
-
Zone de formage : la zone de formage désigne l'espace de fabrication où le modèle ou la pièce en plastique est formé.
La zone de formage est équipée du ou des moules, du bouchon central, ou du mécanisme qui imprime les motifs sur la feuille de plastique préchauffée.
-
Profondeur d'emboutissage : la profondeur d'emboutissage est essentielle pour comprendre le processus de thermoformage.
Elle permet au fabricant de savoir quel type de plastique est nécessaire pour chaque projet de thermoformage. Le fabricant peut ainsi déterminer l'épaisseur de la pièce en plastique et la surface que la feuille de plastique doit couvrir pendant le processus de thermoformage.
-
Dimensions de la machine : les dimensions de l'équipement de thermoformage déterminent la taille des composants ou des pièces en plastique que l'équipement choisi peut produire.
Les équipements de thermoformage de bureau sont compacts et offrent donc des dimensions de formage limitées, alors que les machines industrielles sont beaucoup plus grandes.
-
Force de serrage : certaines machines de thermoformage – notamment les équipements de formage par pression, les équipements de formage double-coque et les équipements de formage par moules appariés – serrent la feuille de plastique pour former la pièce finie.
La force de serrage est un élément important car elle contribue à déterminer le type de matériau qui peut être utilisé.
-
Capacités de changement d'outils : cette caractéristique permet aux fabricants de déterminer à quelle vitesse ils peuvent changer d'outils.
Un changement d'outils plus rapide augmente l'efficacité et la rentabilité de l'équipement.
Types de thermoformeuses
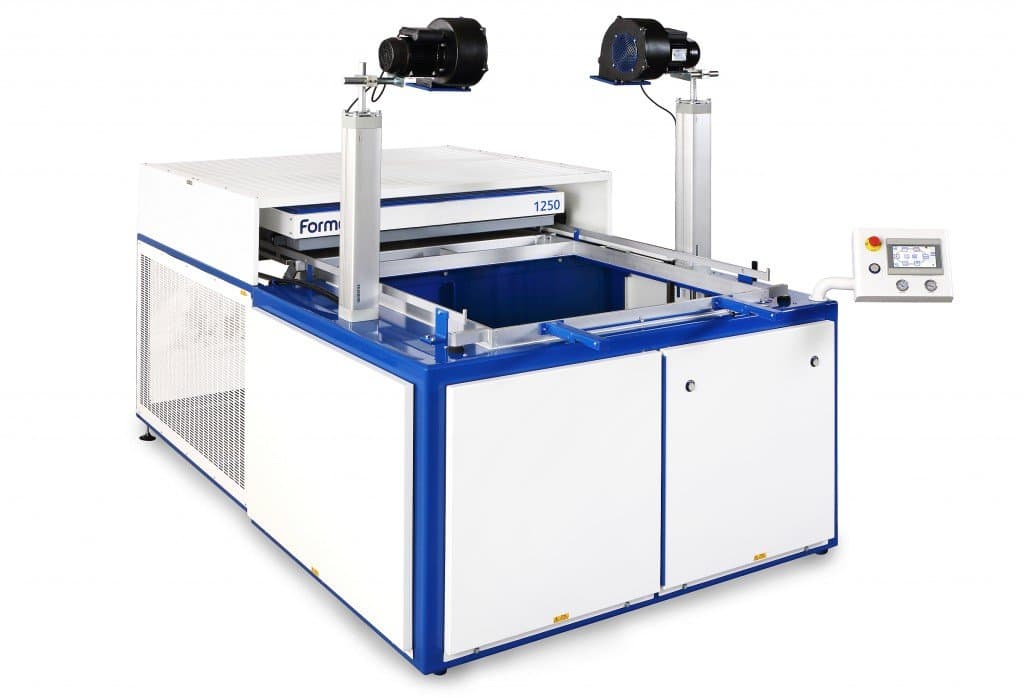
Thermoformeuse sous vide industrielle grand format de Formech.
Une fois ces caractéristiques connues, un fabricant peut choisir une thermoformeuse parmi ces catégories :
-
Thermoformeuse industrielle : il s'agit de machines de grande taille destinées à la production de moyens et grands volumes.
Les thermoformeuses sous vide industrielles sont compatibles avec une gamme plus large de matériaux et d'épaisseurs de tôle. Elles offrent également un emboutissage plus profond et disposent de forces ou de pressions de vide plus importantes pour créer des détails complexes et obtenir une qualité de pièce similaire au moulage par injection. Parmi les exemples d'équipement de thermoformage industriel, citons les thermoformeuses sous vide GN, Ridat, Formech et Belovac. Le prix d'une thermoformeuse industrielle commence à environ 10 000 €, et peut aller bien au-delà.
-
Thermoformeuse de bureau : les thermoformeuses de bureau ont des dimensions réduites, sont compatibles avec moins de matériaux et exercent des forces plus faibles.
Les fabricants, les développeurs de produits et les amateurs utilisent des thermoformeuses de bureau pour le prototypage, les pièces personnalisées et la production de petites séries. Le prix des thermoformeuses de bureau commence à moins de 1000 €, et beaucoup de machines coûtent moins de 10 000 €. Citons par exemple les thermoformeuses Formech, Mayku et Smartform.
-
Thermoformeuse de bricolage : les amateurs qui ont l'intention de s'essayer au thermoformage peuvent choisir de fabriquer leur propre thermoformeuse de bricolage pour produire de petits volumes.
L'équipement de bricolage est généralement plus abordable que l'équipement de thermoformage standard, mais il demande plus d'efforts et d'expertise.
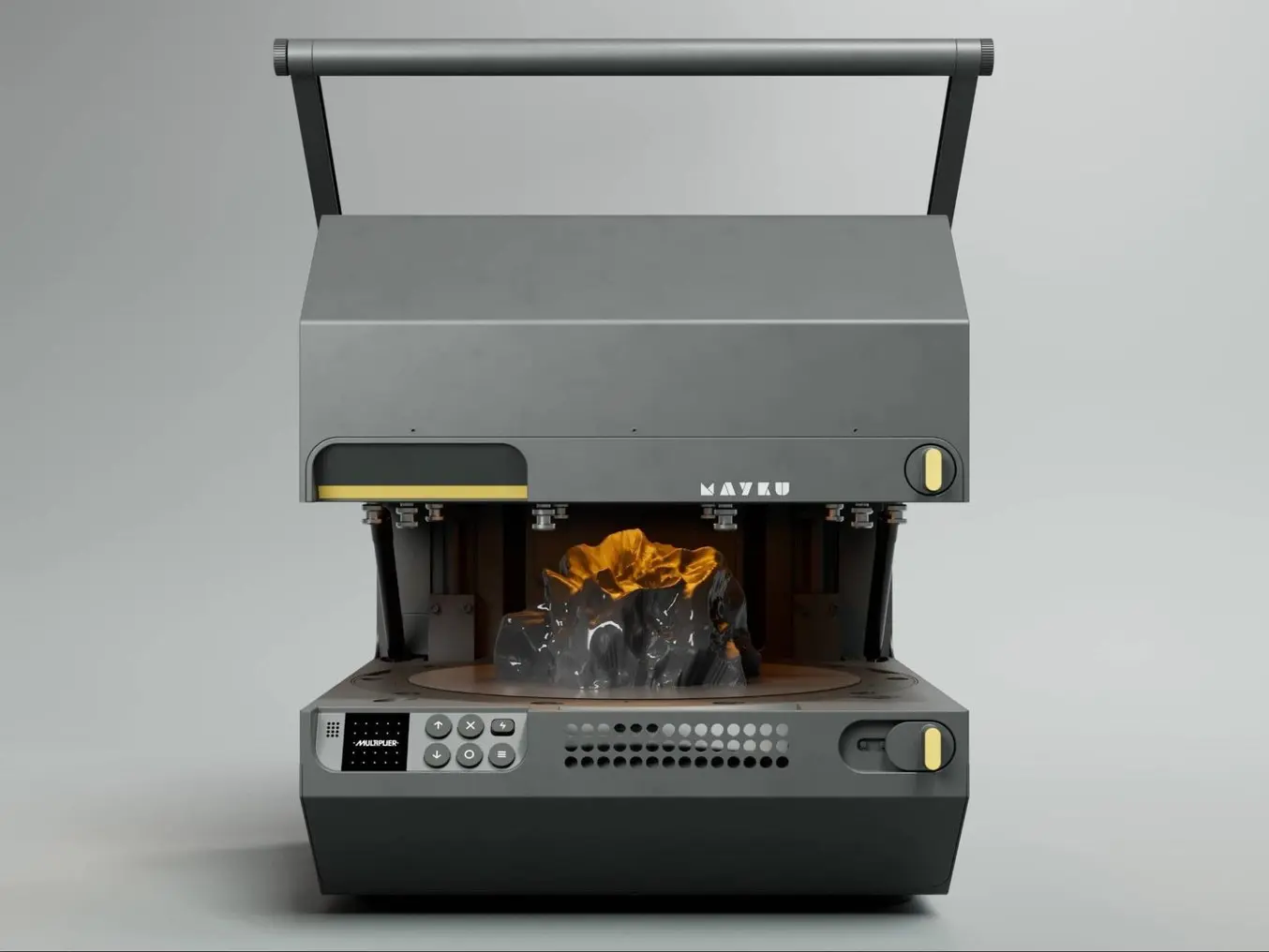
Une thermoformeuse par pression de bureau produite par Mayku.
Moules de thermoformage
Les techniques de thermoformage les plus courantes utilisent des moules à motifs pour transformer la feuille de plastique en pièce finie. C'est le cas du formage sous vide, du formage sous pression, du formage par moules appariés, du formage mécanique et du formage double-coque.
Les moules nécessaires au processus de thermoformage peuvent être développés à l'aide de divers procédés de fabrication, notamment la sculpture manuelle de bois, l'usinage CNC de plastique, de mousse structurelle, de fibre de verre, de composites techniques ou de métaux, l'impression 3D de polymères, ainsi que le moulage de plâtre ou de métal.
Pour choisir la bonne conception de moule et la bonne méthode de production, il convient de prendre en compte les facteurs suivants :
-
Volume de production : Les moules en bois, en plâtre, en matériaux composites et en plastique imprimés en 3D sont généralement les plus rentables pour les pièces personnalisées, les prototypes et les petites séries, tandis que les moules usinés, coulés ou imprimés en 3D avec des matériaux composites ou des polymères conviennent également pour les séries moyennes.
Pour la production de gros volumes, les moules métalliques sont les plus courants en raison de leur meilleure conductivité thermique et de leur résistance, ce qui permet de mieux contrôler la température de la surface du moule, d'obtenir une plus grande uniformité entre les pièces, de réduire les temps de cycle et d'améliorer la durabilité.
-
Conception de la pièce : sculpter des moules à partir de bois peut convenir pour des moules simples ; mais pour les pièces aux géométries complexes nécessitant une grande précision, le coulage ou des outils numériques comme l'usinage ou l'impression 3D sont mieux adaptés.
-
Température de thermoformage : en fonction du matériau thermoformé, le moule peut nécessiter une résistance thermique plus élevée.
L'inclusion de canaux de refroidissement dans le moule peut améliorer les taux de refroidissement, l'uniformité et réduire les temps de cycle.
-
Forces de thermoformage : l'outil doit être suffisamment solide pour résister aux forces de formage intervenant dans le processus, telles que les forces du vide, les forces de pression ou les actions mécaniques.
L'intensité de ces forces dépendra du type de matériau, de l'épaisseur de la feuille et des caractéristiques souhaitées pour la pièce (finition de surface, niveau de détail, etc.).
-
Caractéristiques de conception du moule : le moule doit comporter des caractéristiques essentielles telles que des trous de ventilation pour faire circuler l'air pendant le processus de formage, ainsi que des angles de tirage pour faciliter le démoulage de la pièce.
-
Finition de surface du moule : les exigences relatives à la qualité des pièces, telles que la finition de surface, le niveau de détail, la précision dimensionnelle et la stabilité doivent être prises en compte lors de la fabrication de l'outil.
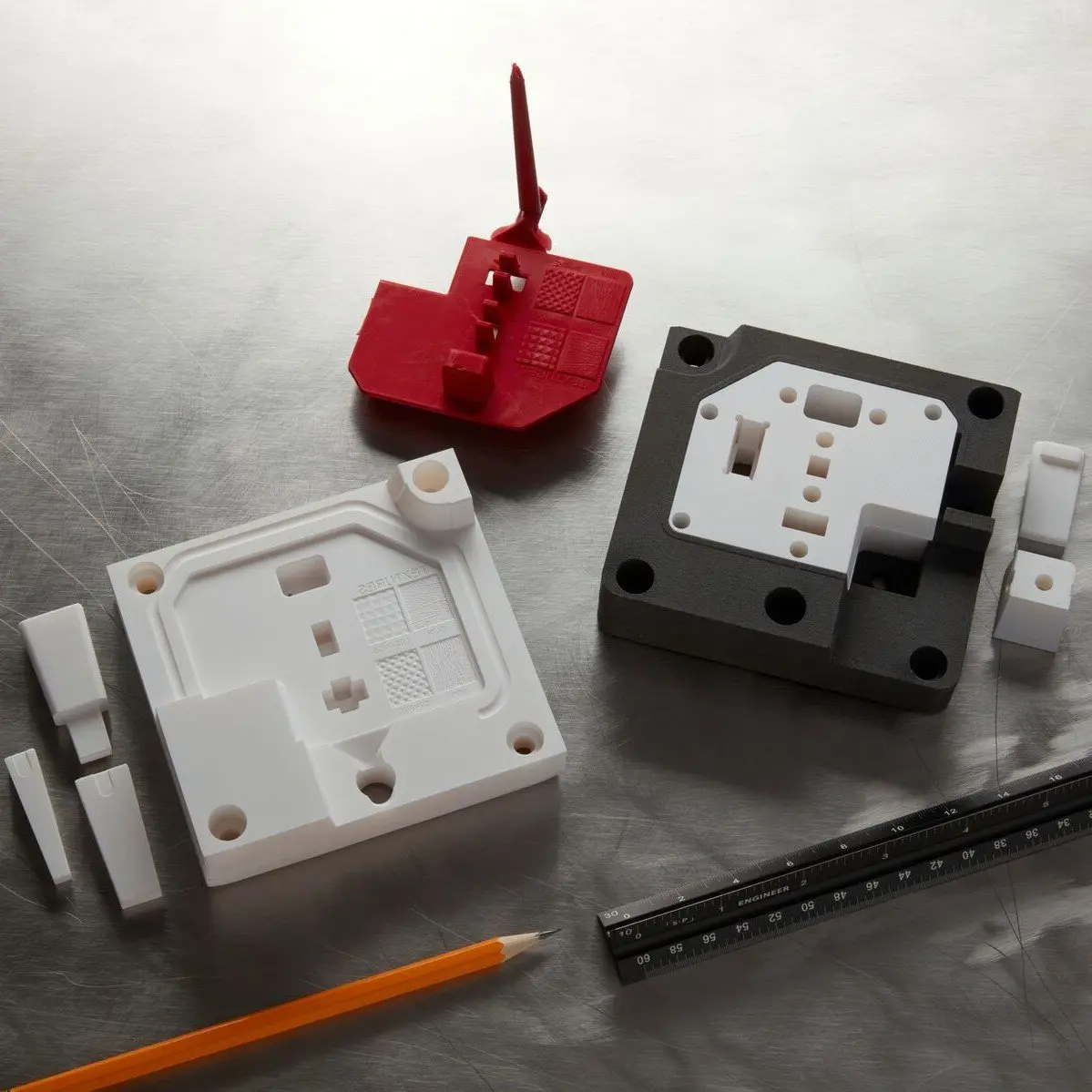
Guide de l'outillage rapide
Dans ce livre blanc, apprenez comment combiner l'outillage rapide imprimé en 3D avec des procédés de fabrication traditionnels tels que le moulage par injection, le formage sous vide ou la fonderie.
Fabrication de moules de thermoformage par impression 3D
Les méthodes traditionnelles de production de moules sont souvent coûteuses, demandent beaucoup d'efforts et ont des délais d'exécution longs, ce qui peut rendre les processus de thermoformage moins efficaces.
De nombreuses entreprises ont recours à l'impression 3D stéréolithographique (SLA) pour créer des moules destinés à des procédés de thermoformage. On les appelle aussi des outils rapides car ils permettent de réduire les délais de production et des coûts, surtout pour les petites séries, les pièces sur mesure et les modèles de prototypes. L'impression 3D offre également une liberté de conception inégalée pour créer des moules complexes et travaillés.Utilisez l'imprimante SLA de bureau Form 3+ pour produire des moules plus petits, et l'imprimante SLA grand format Form 3L pour des moules dont les dimensions peuvent aller jusqu'à 33,5 × 20 × 30 cm.
Les avantages de l'utilisation de l'impression 3D pour développer des moules de thermoformage sont les suivants :
-
Rapidité : les imprimantes 3D peuvent généralement créer des moules de petite ou moyenne taille pour le thermoformage en moins de 24 heures.
-
Rentabilité : l'impression 3D permet aux fabricants de réduire le coût de production des moules, ce qui augmente considérablement la rentabilité du thermoformage pour les petites séries et les pièces personnalisées.
-
Conceptions de moules complexes : l'impression 3D rend le développement de moules à géométrie complexe beaucoup plus simple qu'avec des techniques de fabrication traditionnelles.
Par exemple, l'impression 3D permet d'inclure des caractéristiques de conception qui seraient difficiles à usiner, et le processus de formage peut être amélioré en ajoutant plus d'évents pour un meilleur tirage ou une meilleure pression. Les fabricants peuvent également tirer parti de l'impression 3D pour développer des moules complexes pour les processus de thermoformage tels que le formage double-coque ou par moules appariés.
-
Prototypage rapide de moules : l'impression 3D permet aux fabricants d'itérer et de tester différents modèles de moules rapidement et à moindre coût.
Les moules imprimés en 3D peuvent ensuite être utilisés pour fabriquer des pièces personnalisées et de petites séries, par exemple comme solution temporaire jusqu'à la livraison du moule final.
-
Plus grand choix de matériaux : l'impression 3D offre une large gamme de matériaux, ce qui signifie que les fabricants peuvent expérimenter des moules avec des niveaux variables de coût, de qualité, de résistance à la chaleur et de durabilité.
-
Finition de surface : les technologies d'impression 3D SLA et à base de résine permettent une finition de surface lisse et un niveau de détail élevé.
- Facilité d'utilisation : les imprimantes 3D SLA de bureau et d'atelier peuvent être intégrées de manière optimale dans tout flux de travail de thermoformage, car elles sont faciles à mettre en œuvre, à utiliser et à entretenir, ce qui permet de gagner du temps et de laisser des opérateurs qualifiés se consacrer à d'autres tâches importantes.
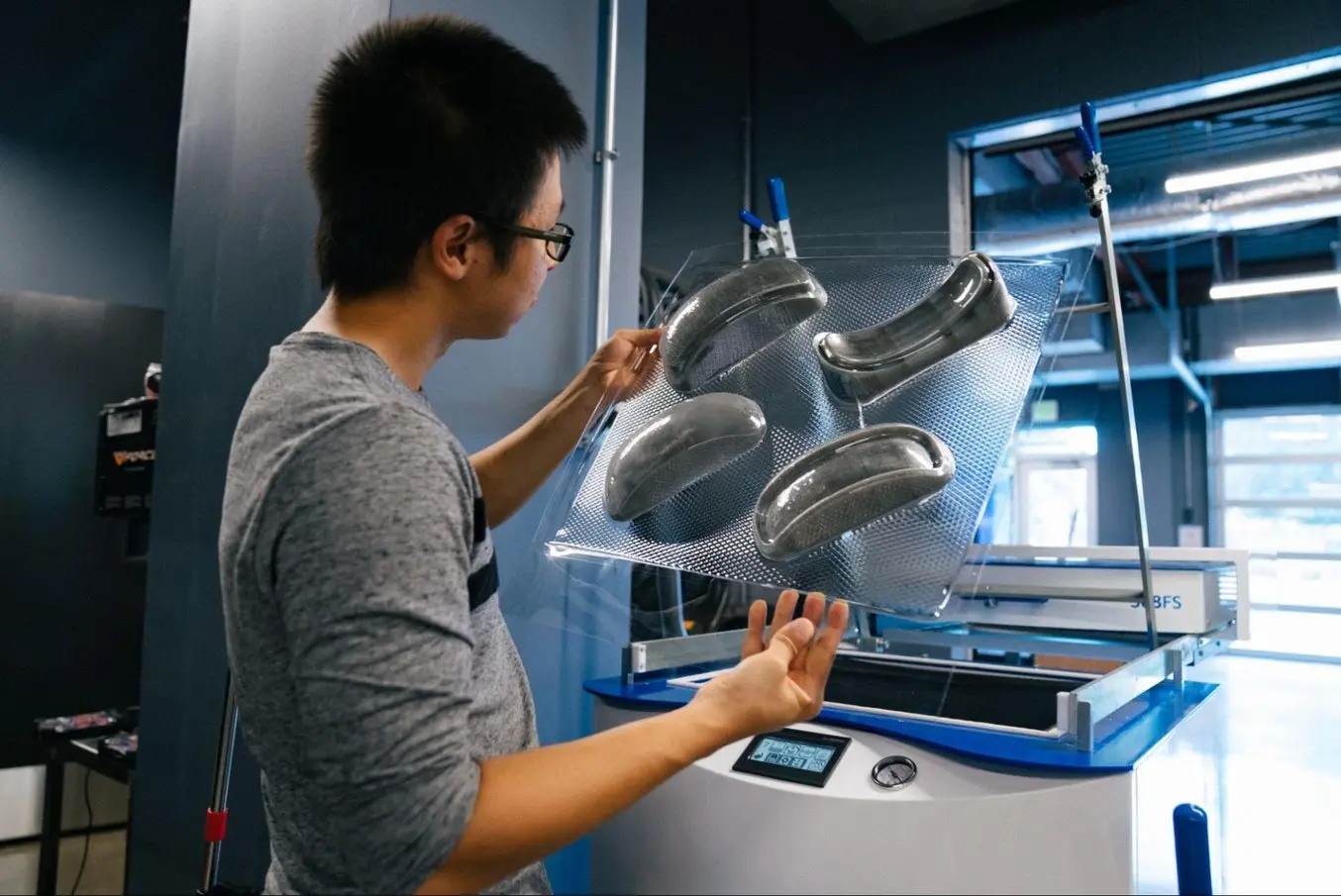
La société de développement de produits Glassboard utilise des moules imprimés en 3D pour thermoformer des prototypes de coques de casque ou d'emballages en polycarbonate.
Ils peuvent ainsi réaliser des formes de moules compliquées qui seraient difficiles à fabriquer de manière traditionnelle, avec de petites caractéristiques et des trous permettant une meilleure distribution de vide sur la surface.
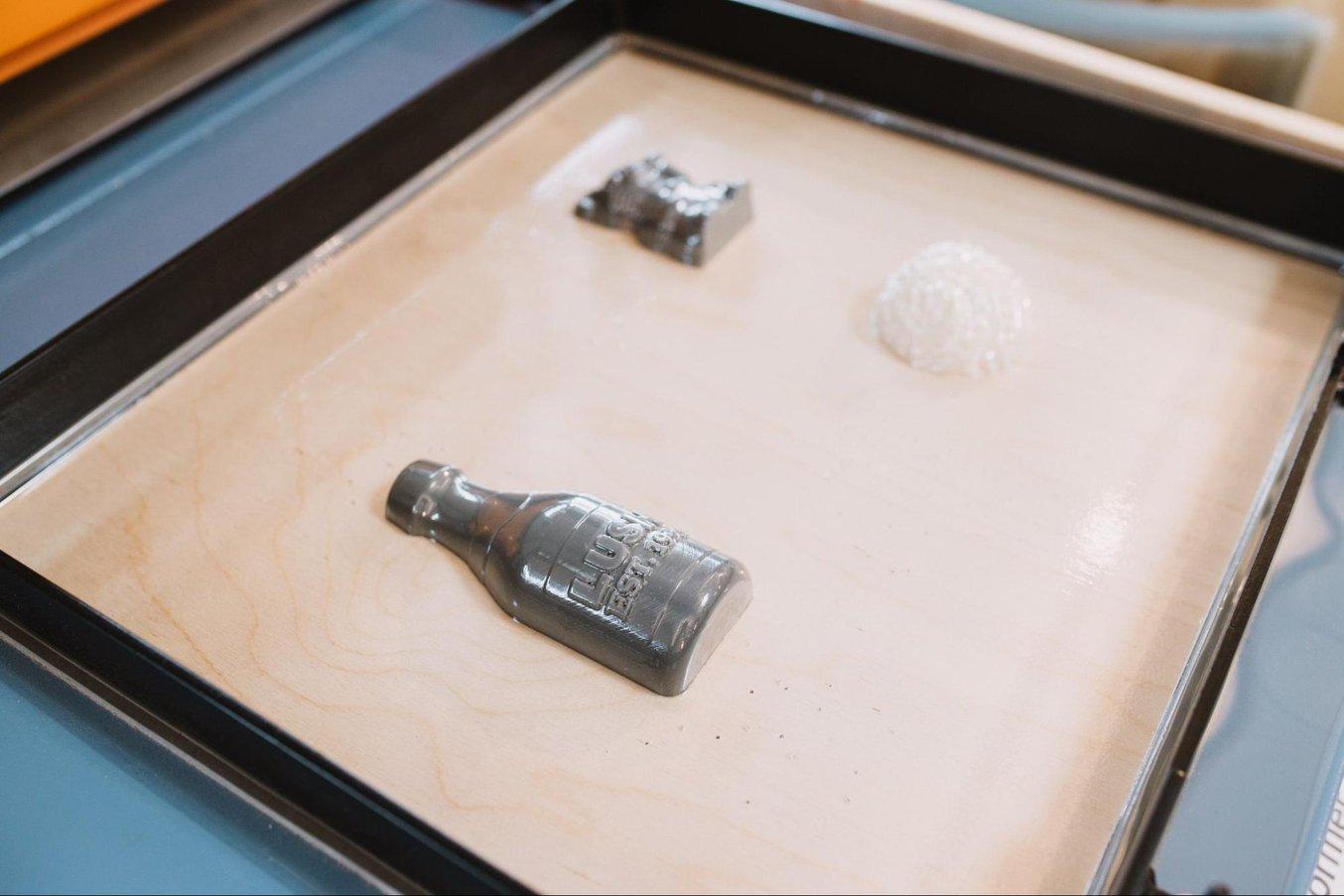
Le fabricant de cosmétiques Lush utilise l'impression 3D pour créer en 24 heures des moules de formage sous vide permettant d'obtenir des modèles détaillés et texturés.
Mais récemment, ils se sont tournés vers l'impression 3D pour créer des moules de formage sous vide et fabriquer des pièces détaillées et texturées, ce qui leur permet de donner vie à leurs idées en moins de 24 heures et de tester plus de mille idées de conception chaque année.
Les moules de thermoformage imprimés en 3D sont également parfaits pour fabriquer à petit prix des pièces finales personnalisées. Par exemple, le formage sous vide et le formage sous pression sur des modèles imprimés en 3D sont les méthodes les plus courantes pour produire des plaques occlusales transparentes en orthodontie.

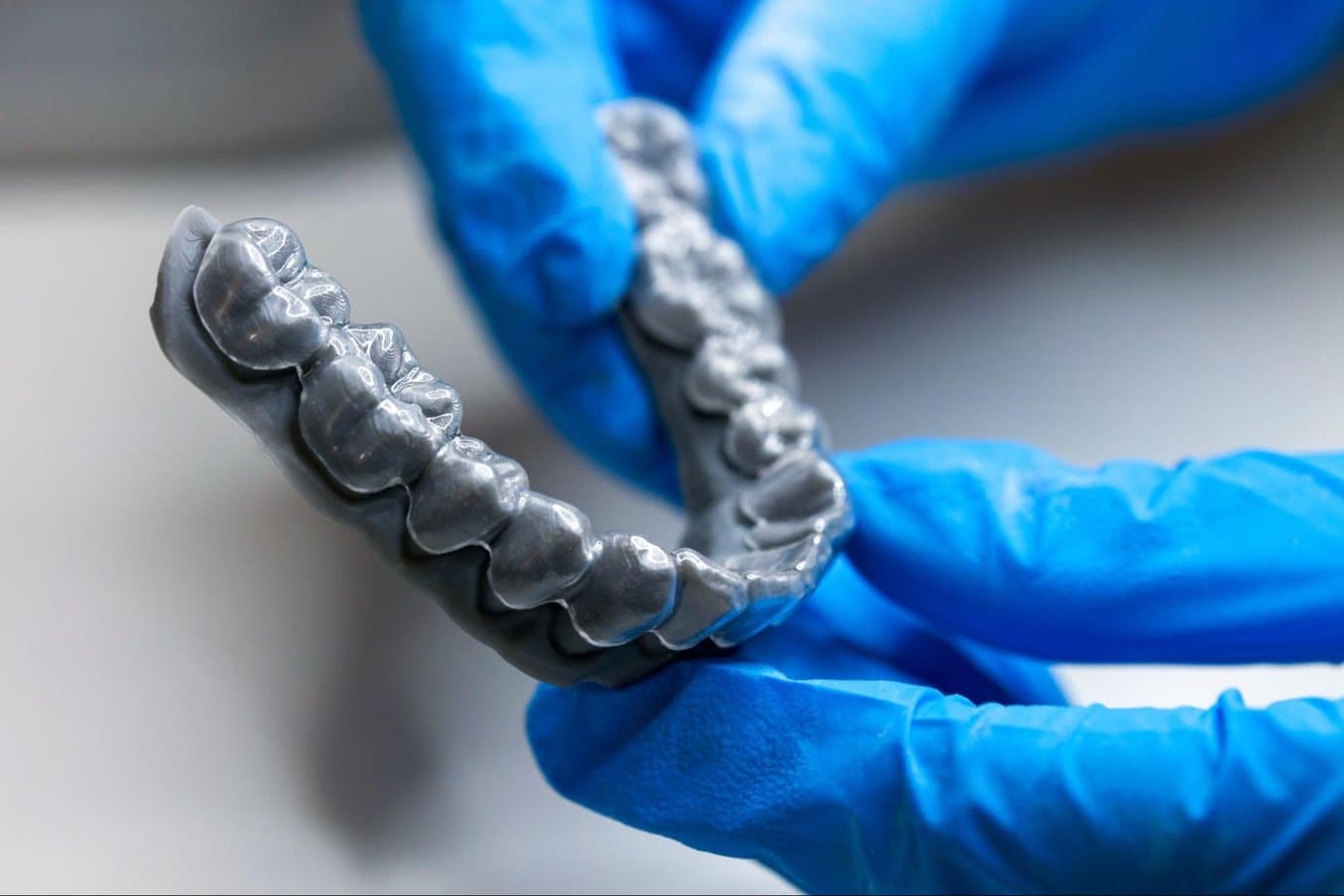
Le formage sous vide et le formage sous pression sur des modèles imprimés en 3D sont les méthodes les plus courantes pour produire des plaques occlusales transparentes en orthodontie.
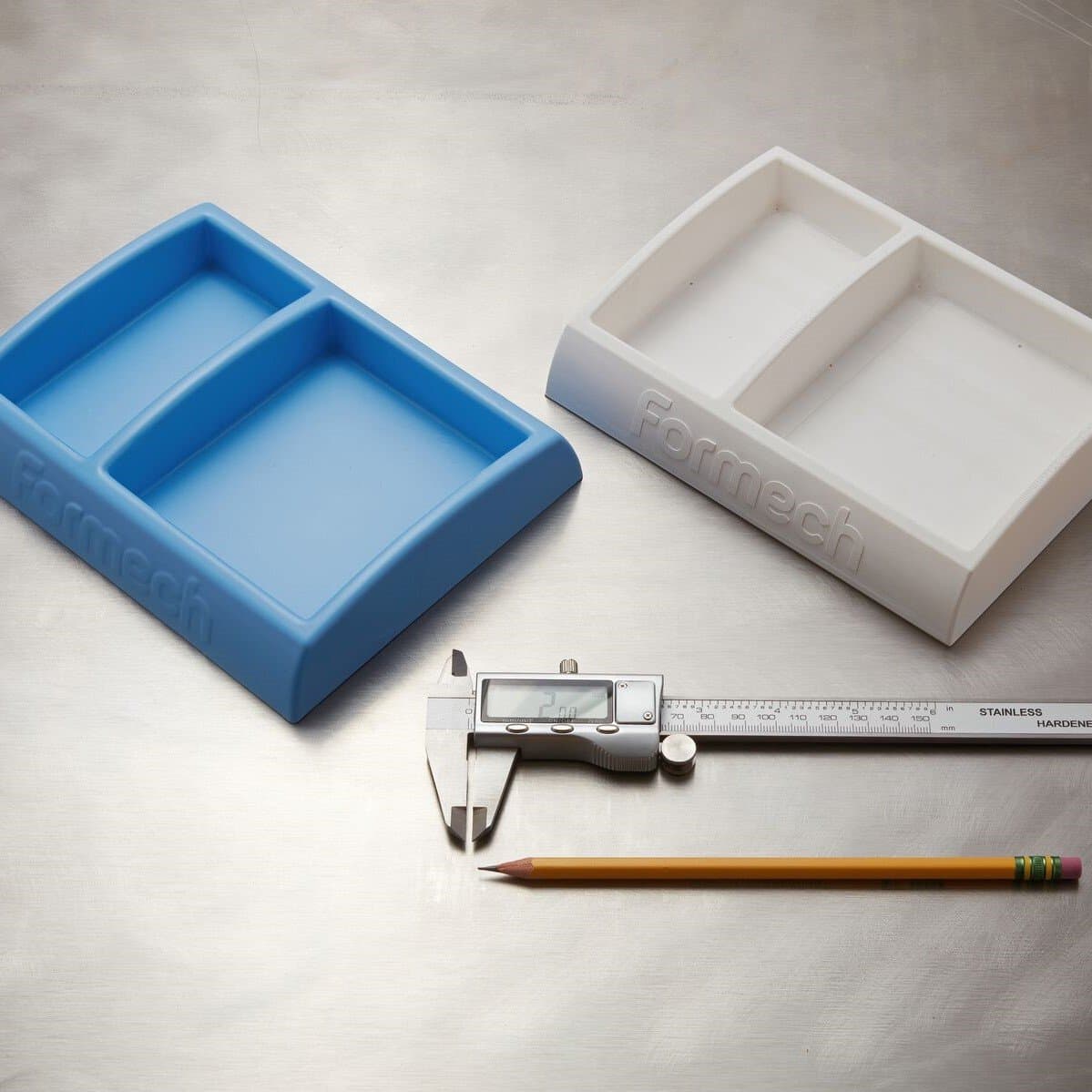
Le thermoformage avec des moules imprimés en 3D : un guide pratique
Accélérez le développement de produits, réduisez les coûts et les délais, et créez facilement des produits personnalisés ou de petites séries en combinant l'outillage rapide imprimé en 3D et le thermoformage.
Comment fabriquer des moules de thermoformage par impression 3D
L'intégration de l'impression 3D pour accélérer le processus de thermoformage révolutionne les flux de fabrication traditionnels mis en évidence ci-dessus. Le flux de travail avec l'impression 3D comprend les étapes suivantes :
-
Concevez le moule à l'aide d'un logiciel CAO.
- Choisissez la résine adéquate dans notre vaste gamme de matériaux et imprimez la pièce avec une imprimante 3D SLA de Formlabs.
-
Insérez le moule imprimé en 3D dans votre équipement de thermoformage et lancez le processus de production.
-
Retirez la pièce et effectuez toutes les étapes standard de post-traitement qui pourraient être nécessaires pour que l'article produit soit prêt à être utilisé.
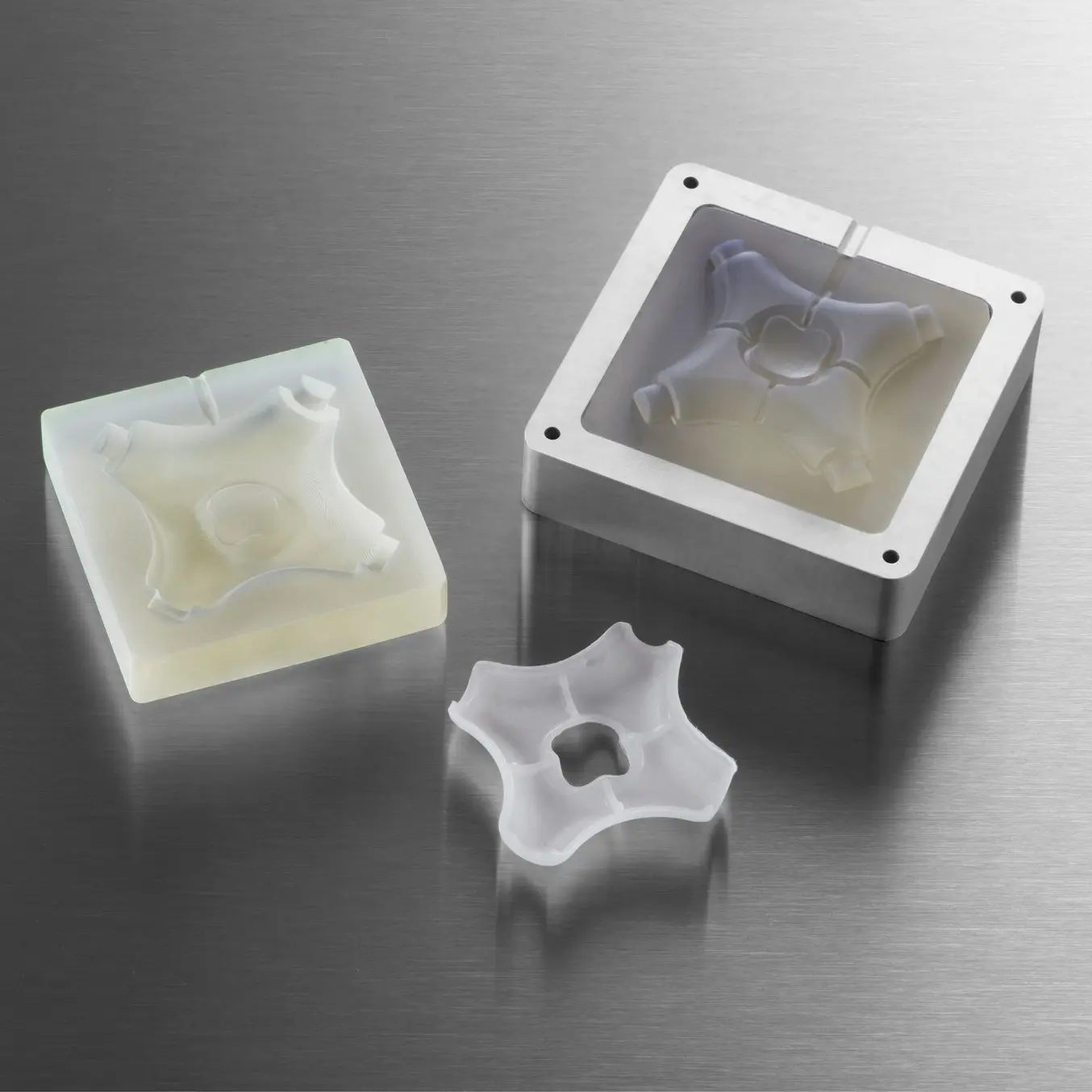
Fabrication de moules par impression 3D : techniques de prototypage et de production
Téléchargez notre livre blanc pour découvrir six procédés de fabrication de moules qui sont possibles avec une imprimante 3D SLA en interne, notamment le moulage par injection, le formage sous vide, le moulage en silicone, etc.
Lancez-vous dans l'impression 3D de moules de thermoformage
En combinant des moules imprimés en 3D avec le thermoformage, vous pouvez améliorer le processus de production en augmentant la flexibilité, l'agilité, l'évolutivité et la rentabilité. Grâce au thermoformage et aux moules imprimés en 3D, validez votre conception et vos matériaux avant de passer à la production en série, et produisez des pièces personnalisées ou des séries limitées de pièces finales.
Téléchargez notre livre blanc pour en savoir plus sur les directives de conception, les flux de travail détaillés, les conditions du processus de thermoformage et des études de cas réelles impliquant des moules de thermoformage imprimés en 3D.