L’impression 3D aide Dorman à suivre le rythme des équipementiers automobiles
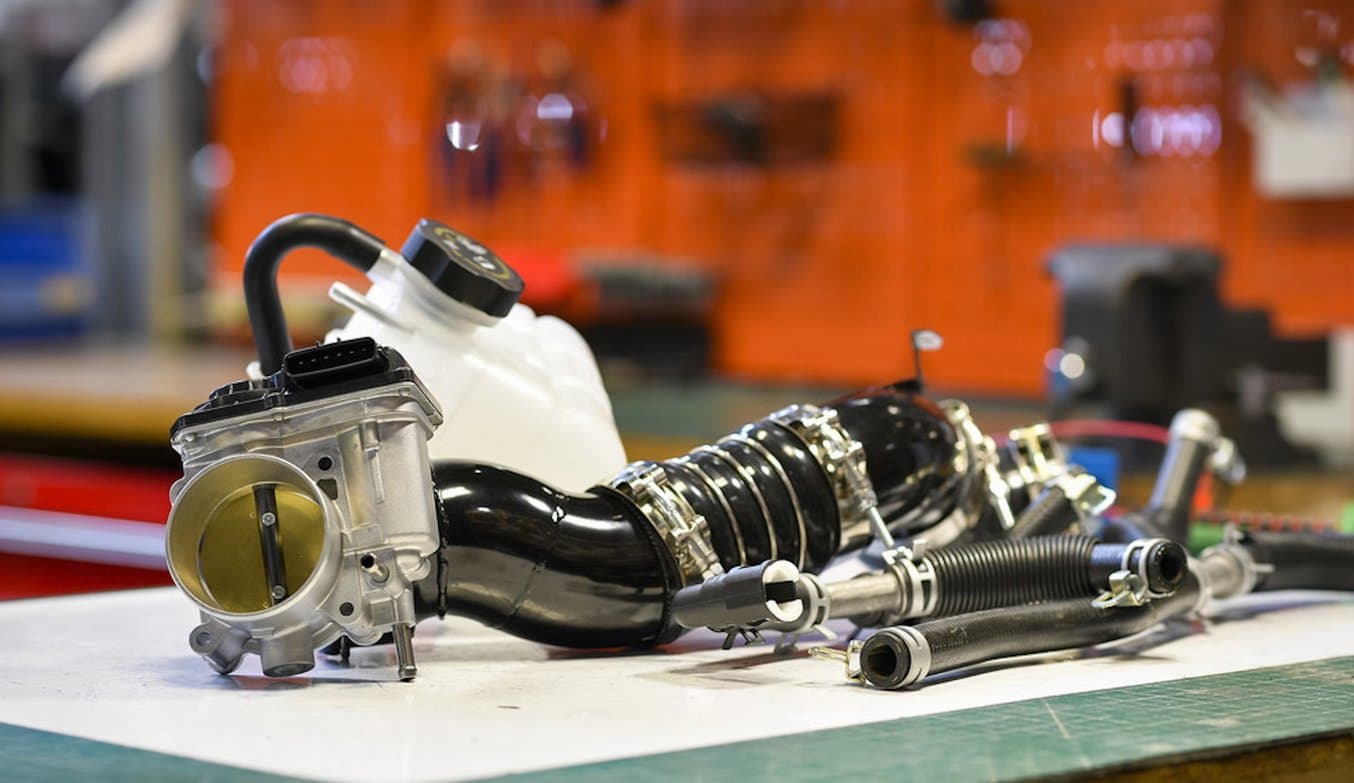
Les prix des voitures neuves et d'occasion ont grimpé en flèche au cours des deux dernières années, en raison des pénuries généralisées de puces informatiques, des retards d'expédition et des fermetures d'usines. Les propriétaires de véhicules ne sont souvent pas en mesure d'acheter une nouvelle voiture ou un nouveau camion après l'expiration de la garantie de leur véhicule actuel, de sorte que les rendez-vous d'entretien et de service de routine deviennent de plus en plus importants pour maintenir le bon fonctionnement de leur véhicule. Les constructeurs automobiles vendent des pièces détachées et assurent le service après-vente chez leurs concessionnaires, mais ces derniers sont également confrontés aux mêmes problèmes de chaîne d'approvisionnement et, parfois, ils ne sont tout simplement pas aussi abordables pour l'automobiliste moyen qu'un atelier de réparation indépendant.
Dorman Products est une société centenaire de fabrication de pièces détachées pour véhicules personnels et utilitaires. Son équipe s'est tournée vers l'impression 3D pour accélérer les délais de production et améliorer la qualité. Ils comptent sur leurs douze imprimantes 3D, réparties sur deux sites, pour les aider à suivre le rythme des fabricants d'équipement d'origine (OEM) qui lancent constamment de nouvelles marques et de nouveaux modèles.
Chris Allebach, responsable de la fabrication additive chez Dorman, et Eric Tryson, responsable de l'équipe de conception mécanique, utilisent les imprimantes stéréolithographiques (SLA) Form 2, Form 3 et Form 3L, ainsi que plusieurs imprimantes FDM, pour prototyper rapidement de nouveaux objets et créer des gabarits et des fixations personnalisés pour leurs processus de validation.
« Les équipementiers disposent d’équipes travaillant chacune sur la conception d’une pièce unique, parfois jusqu’à deux ans avant le lancement d’une nouvelle voiture. Nous devons nous assurer que nos pièces détachées sont fiables tout en garantissant une mise sur le marché rapide. La possibilité d'itérer et d'apporter rapidement des modifications grâce à l'impression 3D a ouvert la voie à des projets que nous n'aurions pas pu réaliser dans le passé. Le fait de savoir qu'il s'agira d'une pièce de qualité nous rend plus confiants dans ce que nous faisons », explique M. Allebach.
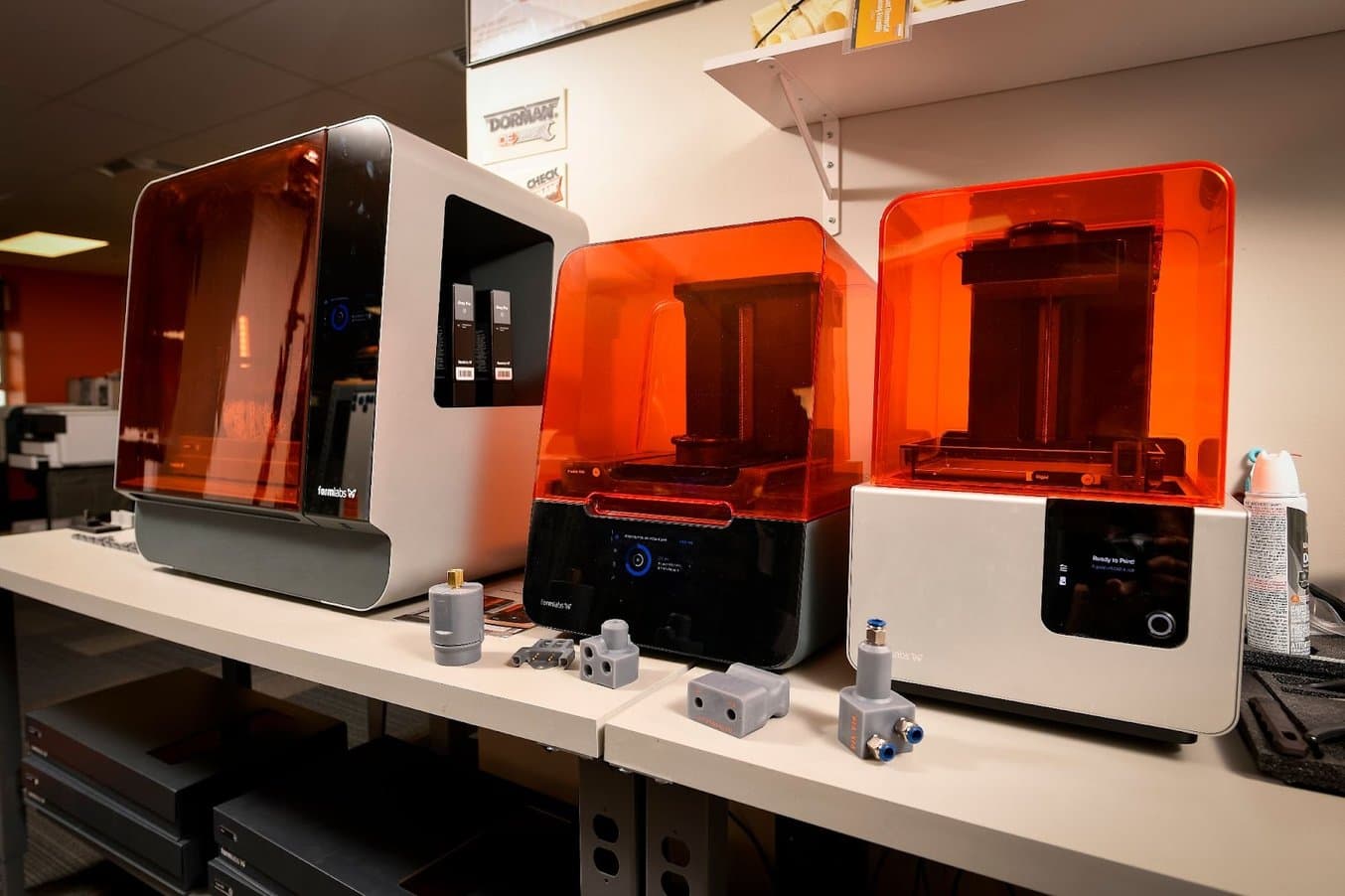
Les ingénieurs de Dorman utilisent les imprimantes Form 2, Form 3+ et Form 3L.
Créer plus de 100 000 produits différents
La gamme de produits offerts par Dorman est stupéfiante : ils conçoivent et gèrent une base de données de 118 000 pièces distinctes (le 25 décembre 2021) pour des centaines de véhicules différents ; « Nous proposons une large gamme de produits pour pratiquement toutes les pièces de voitures, et nous lançons entre 4000 et 5000 nouvelles pièces chaque année », dit M. Tryson.
Les produits proposés par Dorman vont des porte-clés et des composants de base du moteur aux modules électroniques complexes et aux pièces pour poids lourds. Dorman analyse les défaillances des pièces d'origine et procède à une rétro-ingénierie du produit, dans certains cas en repensant et en améliorant complètement la conception. Ils vont souvent chercher la pièce d'origine, parfois en achetant des voitures entières afin de bien comprendre l'ensemble du système et de valider la conception améliorée.
Le processus de conception nécessite d'abord que la pièce soit recréée numériquement afin de pouvoir modifier la conception. Les pièces sont ensuite envoyées au laboratoire de métrologie de Dorman, qui utilise soit un scan laser sans contact, soit une sonde de contact pour les pièces plus détaillées. Les données de référence sont ensuite renvoyées à l'équipe de MM. Allebach et Tryson, qui utilise Solidworks pour procéder à la rétroconception des pièces.
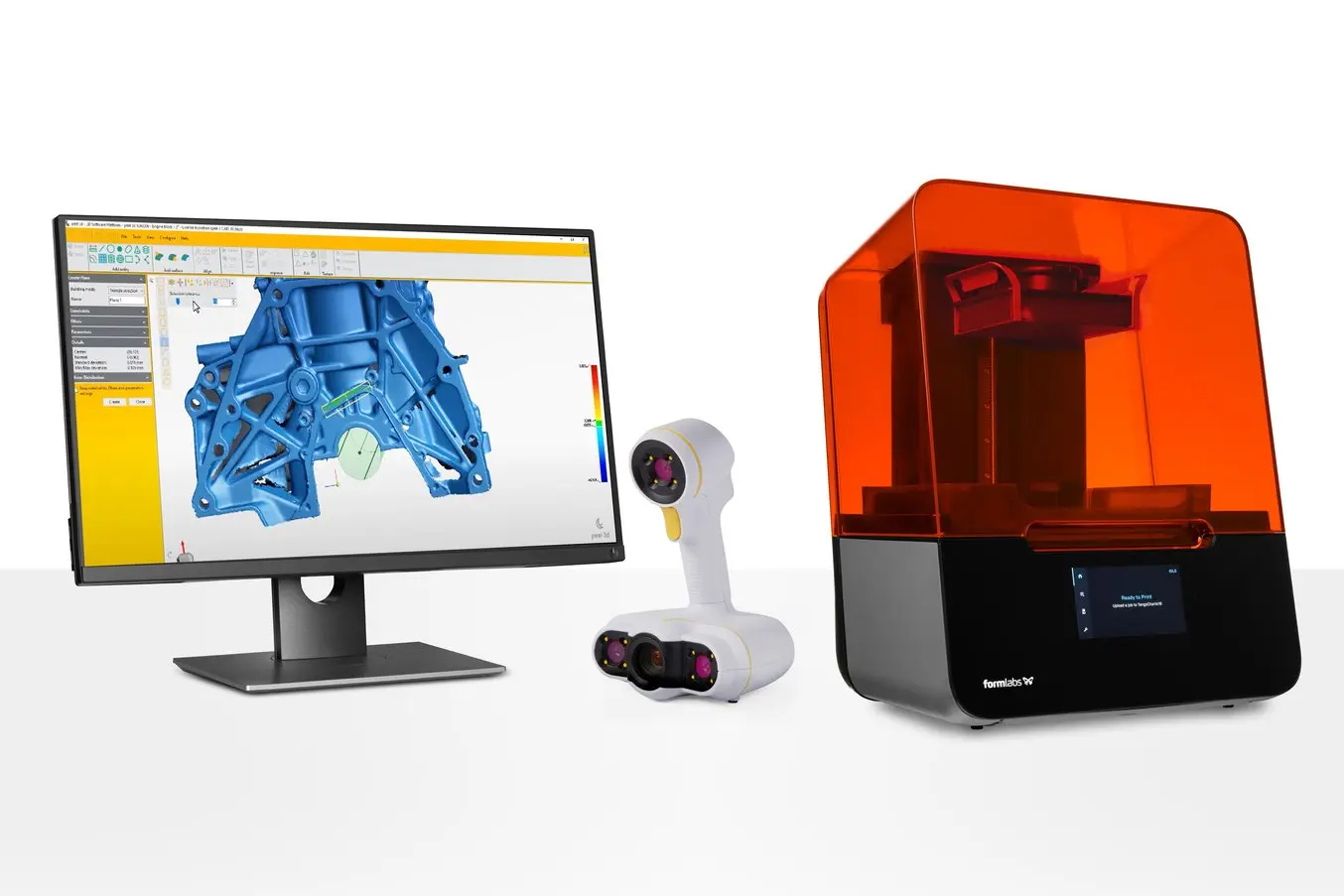
Numérisation et impression 3D pour la rétro-ingénierie et d’autres applications
Dans ce rapport, nous vous présentons des cas d’utilisation de ces deux technologies et vous proposons une vue d’ensemble du marché des scanners 3D.
« Nous réalisons un prototype rapide pour que le concepteur puisse s'assurer que la géométrie et les dimensions sont correctes, puis nous imprimons en 3D un autre prototype, qui est envoyé à l'ingénieur produit pour être examiné. Ils veulent avoir la pièce en main et pouvoir l'examiner ou l'essayer avec les autres composants du véhicule pour s'assurer qu'elle est adaptée », explique M. Tryson.
Mais le département de MM. Allebach et Tryson ne se contente pas de remplacer la pièce. Dans le cas de la ligne OE FIX™ de Dorman, ils essaient également d'améliorer la conception originale. « Il ne s’agit pas simplement de rétro-ingénierie. Nous analysons la pièce, nous déterminons la raison de sa défaillance et nous cherchons à l’améliorer. Nous pouvons être amenés à choisir un autre matériau ou à modifier toute la conception. Si nous apportons des modifications, nous devons créer des prototypes, puis effectuer des tests fonctionnels », explique M. Tryson.
Prototypage d'une pièce OE FIX™
Un composant de moteur en particulier a posé problème à de nombreux propriétaires de voitures. Il était à l'origine en plastique et se fissurait à la suite d'une exposition continue à la chaleur produite par le moteur. L'équipe de Dorman a analysé la pièce, l'a faite scanner par son équipe de métrologie et a décidé de la reconfigurer en aluminium moulé. Concevoir le produit dans un matériau différent n'était pas un simple changement de matériau : la pièce devait être adaptée au coulage sous pression. Pour s'assurer que les performances de la pièce restaient les mêmes avec la nouvelle conception, ils ont dû réaliser de nombreux prototypes et tester chaque itération.
« Chaque itération prend deux heures à peine : nous pouvons ainsi réaliser deux itérations dans la même journée. C’est vraiment très utile. Avant l'impression 3D, on ne pouvait qu'espérer réussir du premier coup. Si ce n'était pas le cas, on perdait des semaines voire des mois à recevoir les pièces, avant de nous rendre compte qu'il fallait les retoucher et les renvoyer », explique M. Tryson.
Une fois le prototype réalisé en interne, Dorman a effectué des tests fonctionnels pour vérifier que la pièce fonctionnait toujours de la même manière.
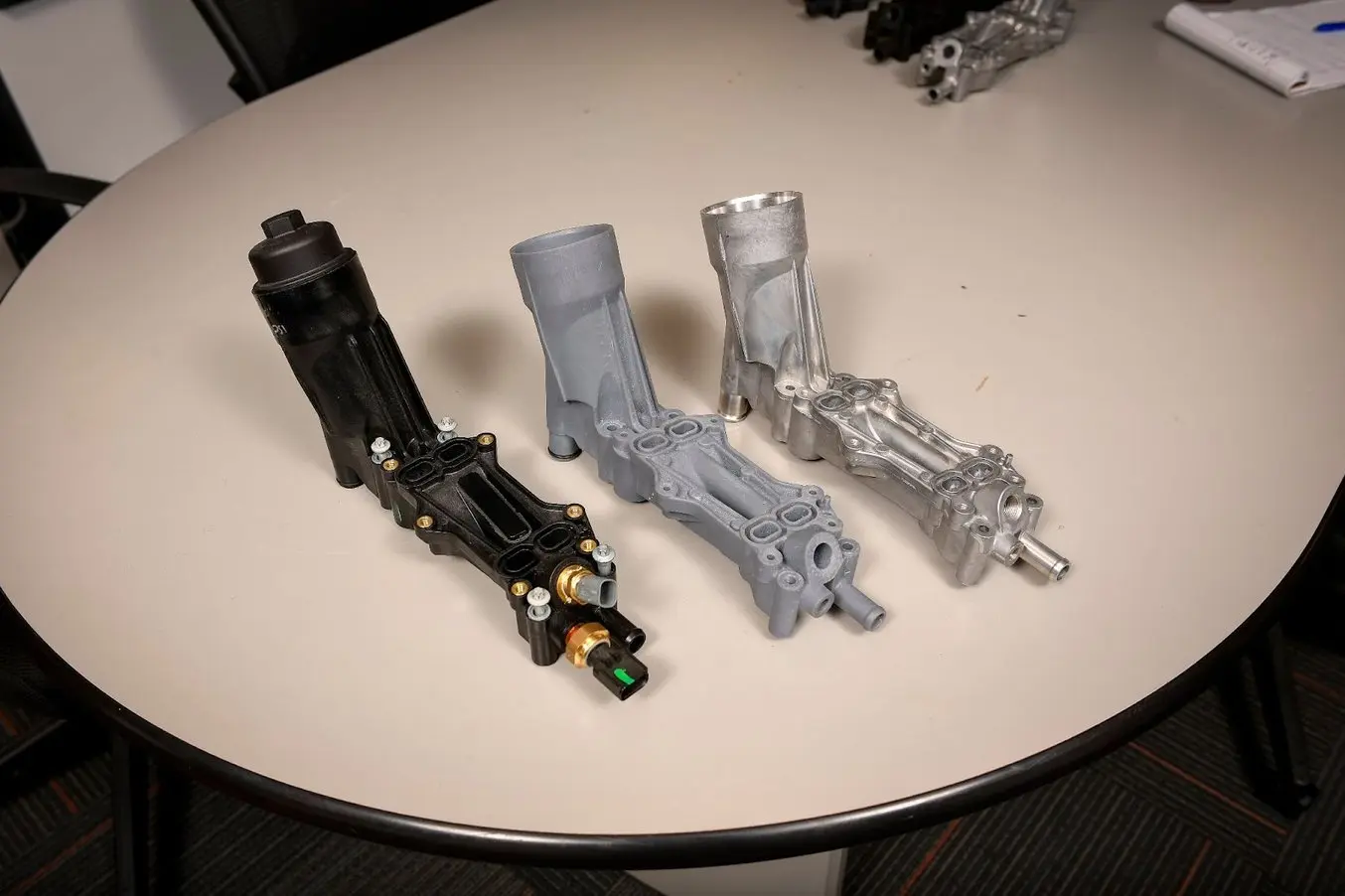
Ce composant de moteur a été défaillant pour de nombreux propriétaires de voitures : les itérations de la nouvelle conception de Dorman sont montrées ici.
Le processus de validation
Chaque produit ayant une fonction différente, chaque protocole d'essai et processus de validation est unique. Même si les processus de validation de deux pièces différentes prévoient des tests d'écoulement des fluides, ils nécessiteront des fixations différentes pour les maintenir en place en raison de leur géométrie différente.
La création de fixations de test est la spécialité des imprimantes Formlabs. On peut utiliser tous les matériaux : d'Elastic Resin jusqu'à Rigid 10K Resin. Elle nous permettent de diminuer drastiquement les coûts et les délais.
Chris Allebach, responsable de la fabrication additive, Dorman Products
Avant d'intégrer les imprimantes 3D dans leur flux de travail, cette demande de fixations personnalisées était un obstacle à un développement rapide. Pour une entreprise comme Dorman, qui doit s'adapter aux nouveaux modèles que lancent chaque année les équipementiers, tout ralentissement peut leur faire prendre du retard sur de nouveaux produits.
Les fixations étant spécifiques à chaque produit, elles ne pouvaient pas être commandées en grandes quantités, ce qui excluait le moulage par injection. La seule option était de les faire usiner, ce qui était à la fois coûteux et chronophage. Ils devaient s'assurer que la conception était parfaite, puis l'envoyer et attendre des semaines avant de pouvoir valider leurs pièces.
« Pour les fixations et les calibres, nous devions faire appel à un atelier d'usinage, ce qui prenait entre cinq et six semaines. Le coût est de cinq à dix fois supérieur à celui d'une pièce, et la géométrie est limitée par les techniques de fabrication conventionnelles. Avec les imprimantes 3D, nous pouvons maintenant développer des fixations et calibres de test tout en travaillant sur le prototype du produit. Ainsi, lorsque la conception est finalisée, la fixation est également prête pour les tests. Nous essayons d’être aussi proactifs que possible », explique M. Allebach.
Un processus de validation a nécessité deux fixations imprimées en 3D pour tester un tuyau sous pression. Un dispositif a été mis en place pour boucher le tuyau à une extrémité et y faire passer du liquide afin de déterminer les limites de sa pressurisation. L'autre fixation a été réalisée pour simuler la partie accouplée de ce qui serait dans la réalité un grand radiateur sous le capot de la voiture. Le fait de ne pouvoir imprimer en 3D que la pièce accouplée du radiateur a permis à l'équipe de test de profiter d'une plus grande maniabilité, mais aussi d'envoyer la pièce à la chaîne de fabrication et de lui faire effectuer des tests de validation au fur et à mesure que les pièces sortaient de la chaîne, dans le cadre d'un processus supplémentaire de contrôle de la qualité.
« Si le composant correspondant est un radiateur géant, vous n'allez pas en acheter plusieurs et les expédier pour n'en couper qu'une toute petite partie. De cette manière, nous fabriquons ce que nous voulons, nous les produisons en masse et nous les distribuons. En fin de compte, si l'un d'entre eux se casse, cela représente quelques dollars et nous pouvons simplement en imprimer un autre », explique M. Tryson.
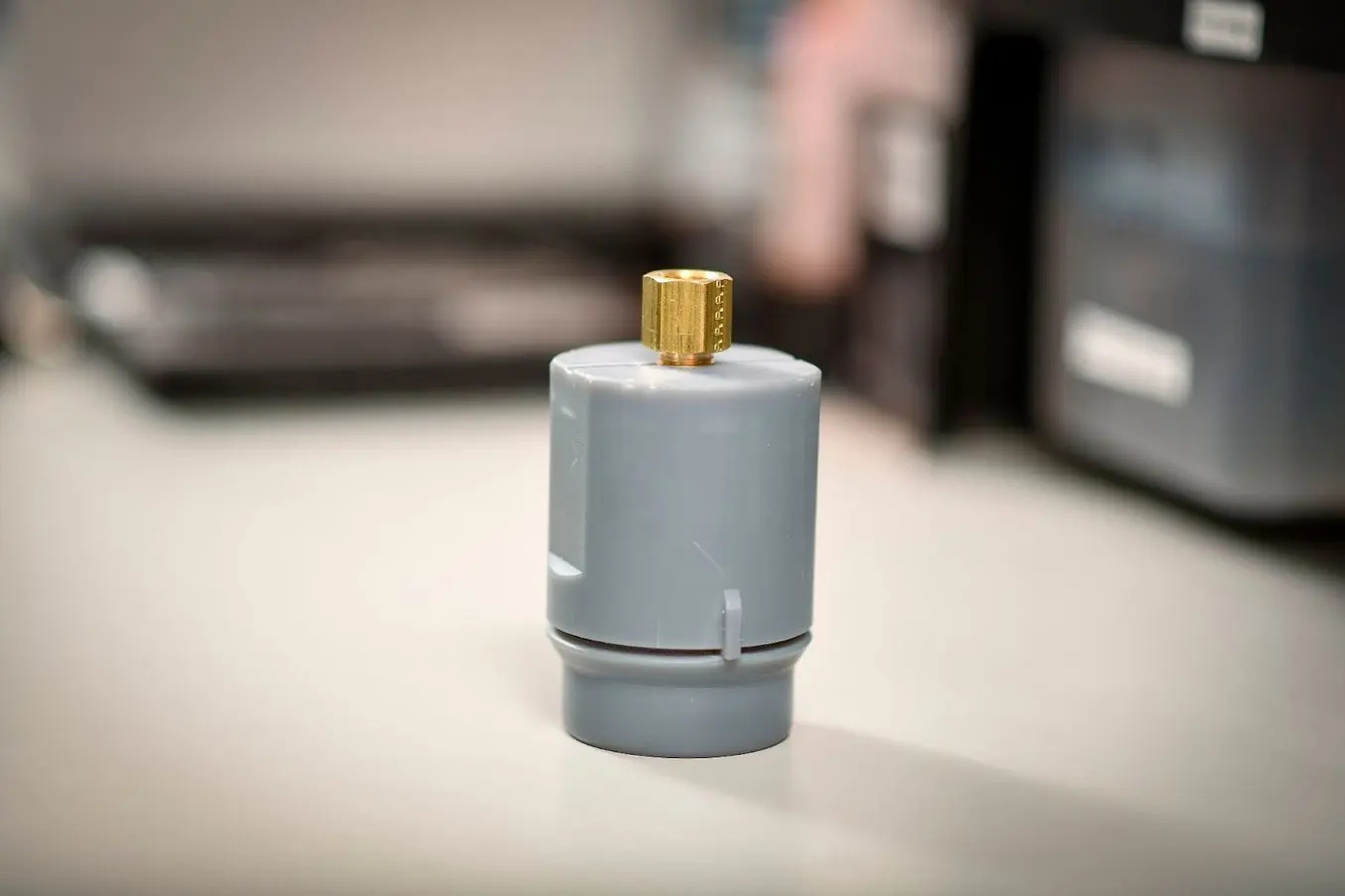
L'une des deux fixations d'essai pour le test du tuyau sous pression.
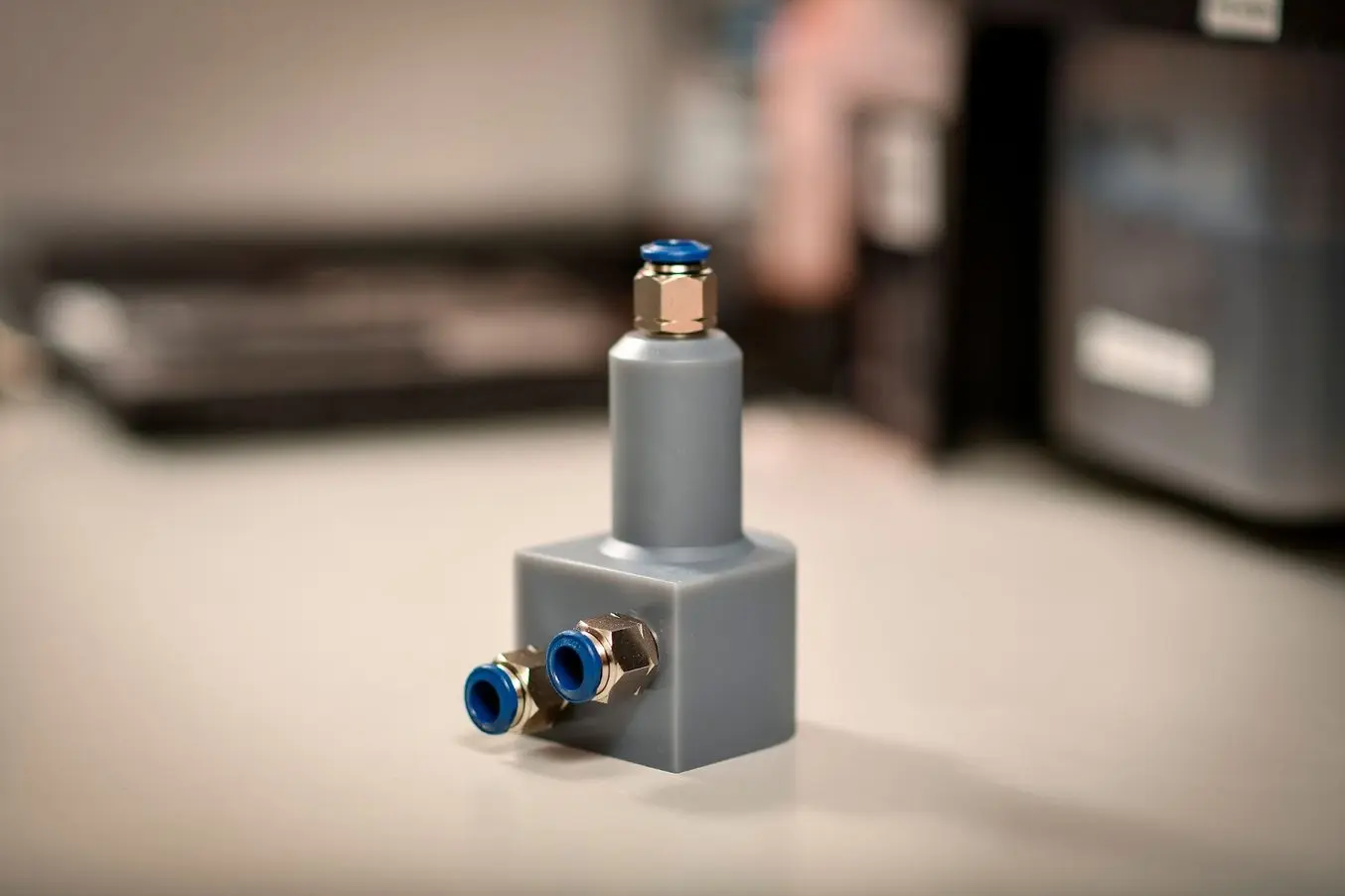
La fixation personnalisée permet de tester la géométrie de la partie accouplée, ce qui évite de devoir fabriquer un radiateur entier.
Tolérances serrées pour les tests Go/No Go
Avant que ces produits ne soient commercialisés et installés dans les voitures des clients, l'équipe de Dorman doit savoir exactement quel type de variation dimensionnelle ces pièces peuvent tolérer. Elle effectue donc une analyse dimensionnelle pour déterminer si une pièce peut être utilisée ou non. Certaines pièces peuvent nécessiter des tolérances serrées, et MM. Tryson et Allebach n'étaient pas sûrs que des calibres imprimés en 3D puissent être adaptés avant de recevoir leurs imprimantes Form 3+ et Form 3L.
« Nous réalisons beaucoup de calibres à limites avec les imprimantes Formlabs, en raison des tolérances que nous pouvons atteindre. Un jour, notre ingénieur est venu nous voir et nous a dit que le calibre devait avoir une tolérance de +/- 0,05 mm sur un diamètre. Nous avons pu l'imprimer avec un diamètre ayant une tolérance de 0,025 mm sur un faux-rond. Je n'arrivais pas à croire que j'étais capable d'obtenir une telle tolérance avec une Form 3L », explique M. Allebach.
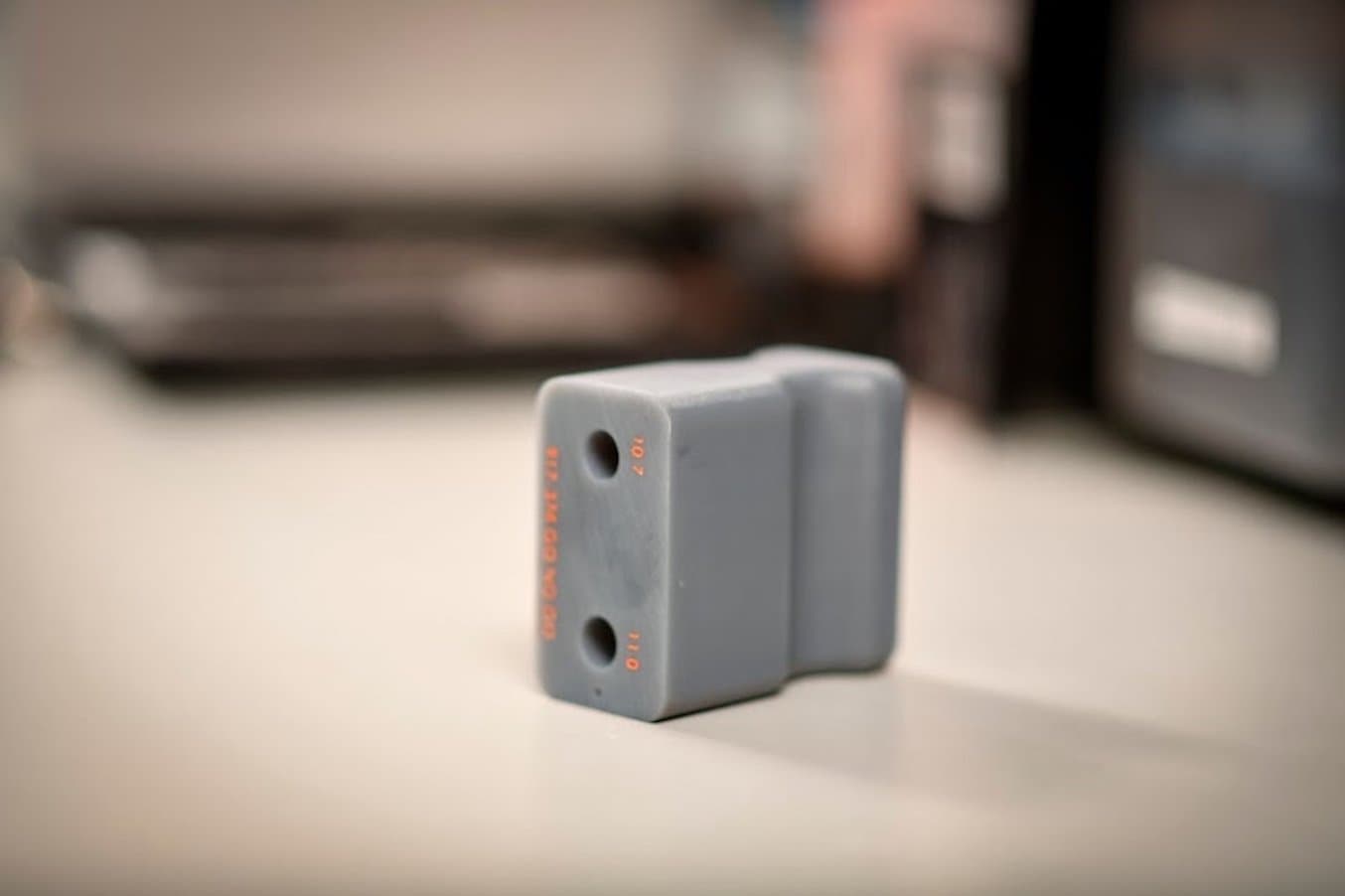
Un calibre à limites imprimé avec Grey Resin.
Impression 3D de silicone pour produire des joints destinés à des essais de pression
Quand elle doit tester sous pression des composants de nouveaux designs, l'équipe doit être en mesure de sceller certains trous et surfaces. Mais ils n'ont pas toujours la forme exacte pour sceller chaque pièce, de sorte que l'équipe doit trouver des idées créatives, qui se résument la plupart du temps à la fabrication de joints et de fixations sur mesure.
Auparavant, ils mesuraient les composants dans leur laboratoire, faisaient fabriquer des matrices métalliques, puis découpaient les joints sur mesure en utilisant les matrices dans une presse à arbre. « C'était comme découper des biscuits dans de la pâte. C'était très inefficace en termes d'utilisation de matériaux et prenait beaucoup de temps à nos techniciens de laboratoire », explique M. Allebach.
Le passage à l'impression 3D permet à l'équipe de réduire considérablement les délais et les coûts, surtout si l'on considère le grand nombre de nouveaux composants. « Nous avons imprimé des centaines de joints personnalisés pour notre testeur de boîtier papillon afin d'étanchéifier les deux extrémités du corps du boîtier et d'effectuer des tests de débit », nous dit M. Allebach.
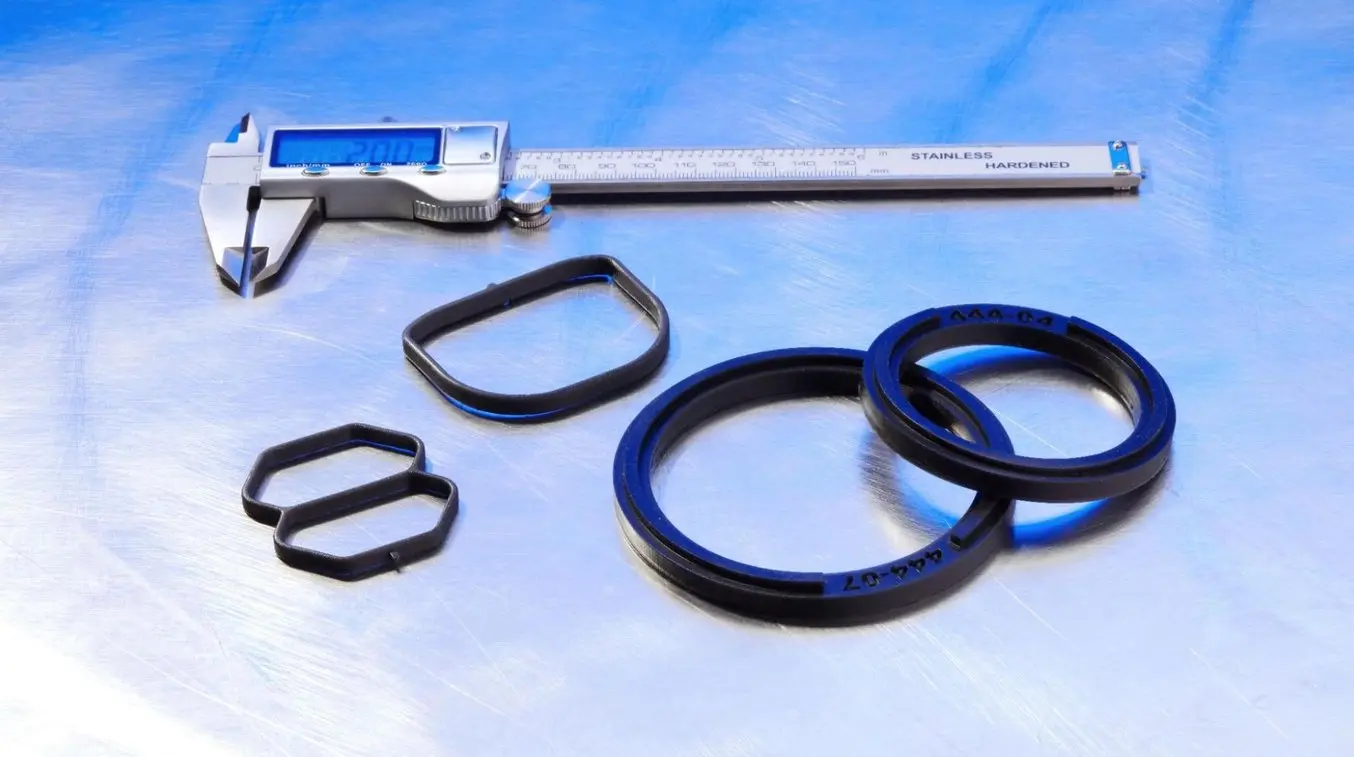
Joints sur mesure imprimés en 3D avec Silicone 40A Resin par Dorman Products.
Si le matériau de type silicone Elastic 50A Resin de Formlabs convenait parfois à cet usage, la nouvelle Silicone 40A Resin, le premier matériau accessible d'impression 3D en silicone, élargit la gamme d'applications disponibles.« Il est incroyable de constater à quel point Silicone 40A Resin est plus durable [que les autres matériaux d'impression 3D de type silicone », ]déclare M. Allebach. « Comme il s'agit d'une résine de silicone, je m'attendais à ce qu'elle possède des propriétés similaires, mais pas à ce qu'elle se comporte vraiment comme un silicone moulé par injection.
La résistance chimique et thermique sont deux propriétés clés qu'ils recherchaient dans Silicone 40A Resin. Pendant deux mois, ils ont effectué des tests chimiques sur les pièces imprimées en 3D avec de l'huile et du liquide lave-glace, des tests environnementaux aux UV, puis des tests de compression. Le retour élastique et les autres propriétés mécaniques ont répondu à leurs exigences.
Joints pour essais de validation
Délai de production | Coût | |
---|---|---|
Découpe de feuilles de silicone à l'aide de matrices métalliques usinées | 2 semaines par série | 250 € par série |
Impression 3D SLA avec Silicone 40A Resin | 3 heures par série | 12 € par série |
« Les avantages sont colossaux, surtout pour nous : nous pouvons à présent fabriquer des joints sur mesure qui seront testés dans un four de vieillissement thermique, les sceller dans un espace qui reproduira le compartiment moteur pour les essais, ou les tester dans l'air, l'eau, le liquide de refroidissement, l'huile, bref tout ce avec quoi la pièce entrera en contact dans la vie réelle. »
Chris Allebach, responsable de la fabrication additive, Dorman Products
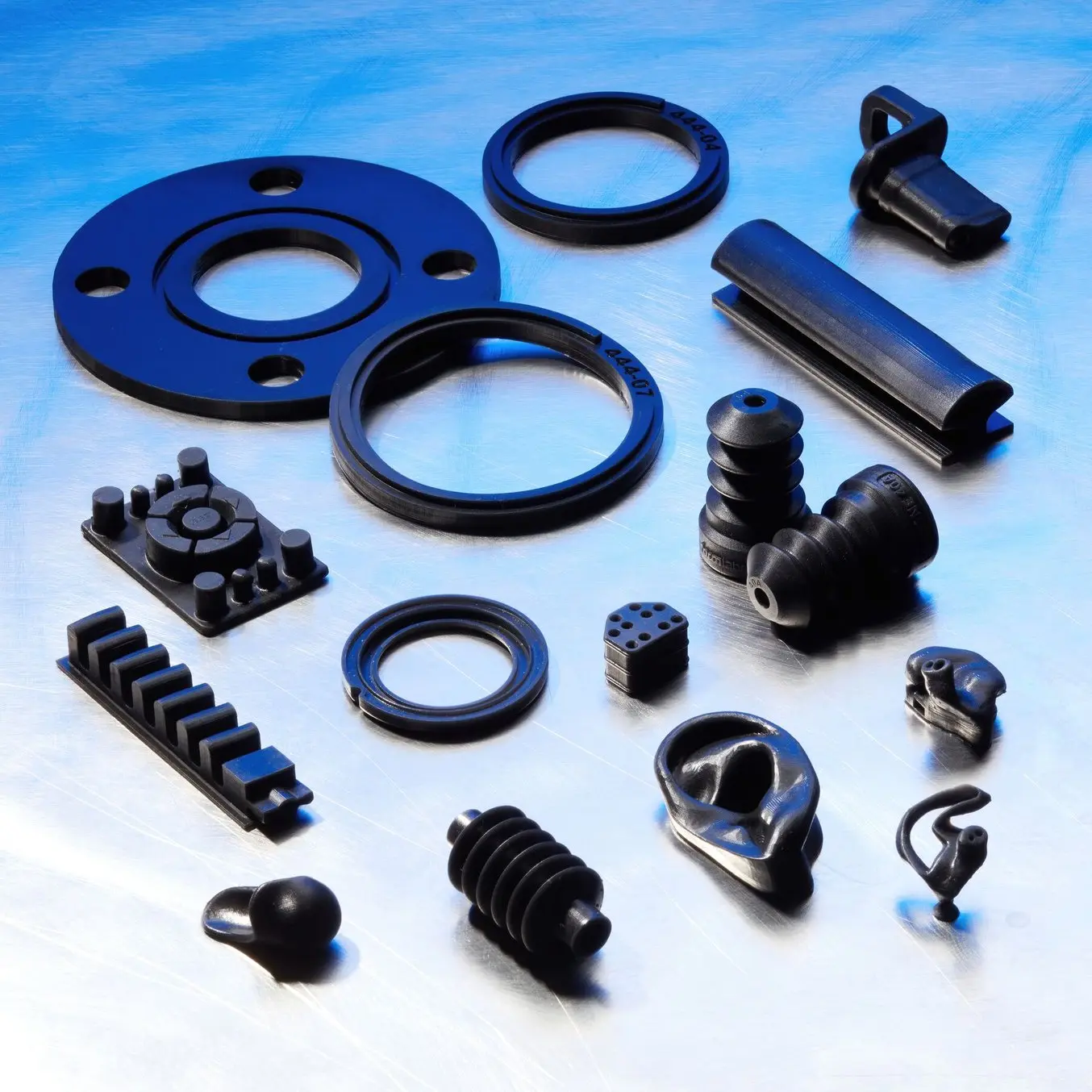
Présentation de Silicone 40A Resin
Au cours de ce webinaire, nos experts en impression 3D vous expliqueront les principaux avantages et applications de Silicone 40A Resin, et vous présenteront les flux de travail ainsi que les propriétés de ce matériau.
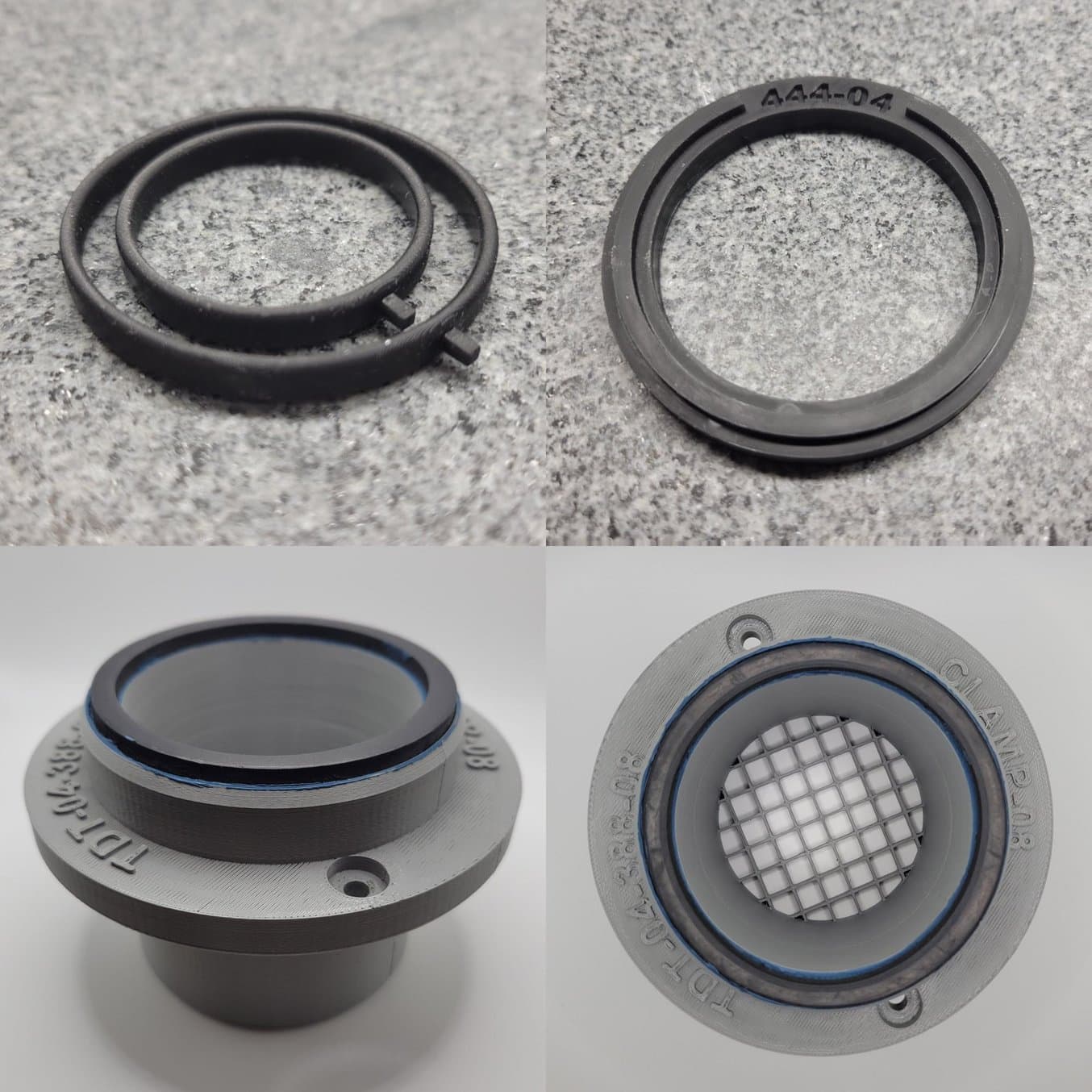
Joints de collecteur d'admission personnalisés et adaptateur de test du flux d'air imprimé en 3D.
M. Allebach a également été époustouflé par la liberté de conception sans précédent des matériaux d'impression 3D flexibles.
« Cette résine s'imprime incroyablement facilement. Je ne pensais pas qu'un matériau aussi souple serait capable d'imprimer des détails aussi fins. Nous avons réussi à imprimer des pièces que nous n'aurions jamais espéré fabriquer avec un matériau 40A. Elles étaient toujours moulées par injection. Nous avons donc poussé l'imprimabilité jusqu'aux limites les plus extrêmes. Je n'en croyais pas mes yeux quand j'ai vu la qualité des détails des pièces imprimées. Tout le monde a été époustouflé par le toucher du matériau et par son élasticité. »
Chris Allebach, responsable de la fabrication additive, Dorman Products
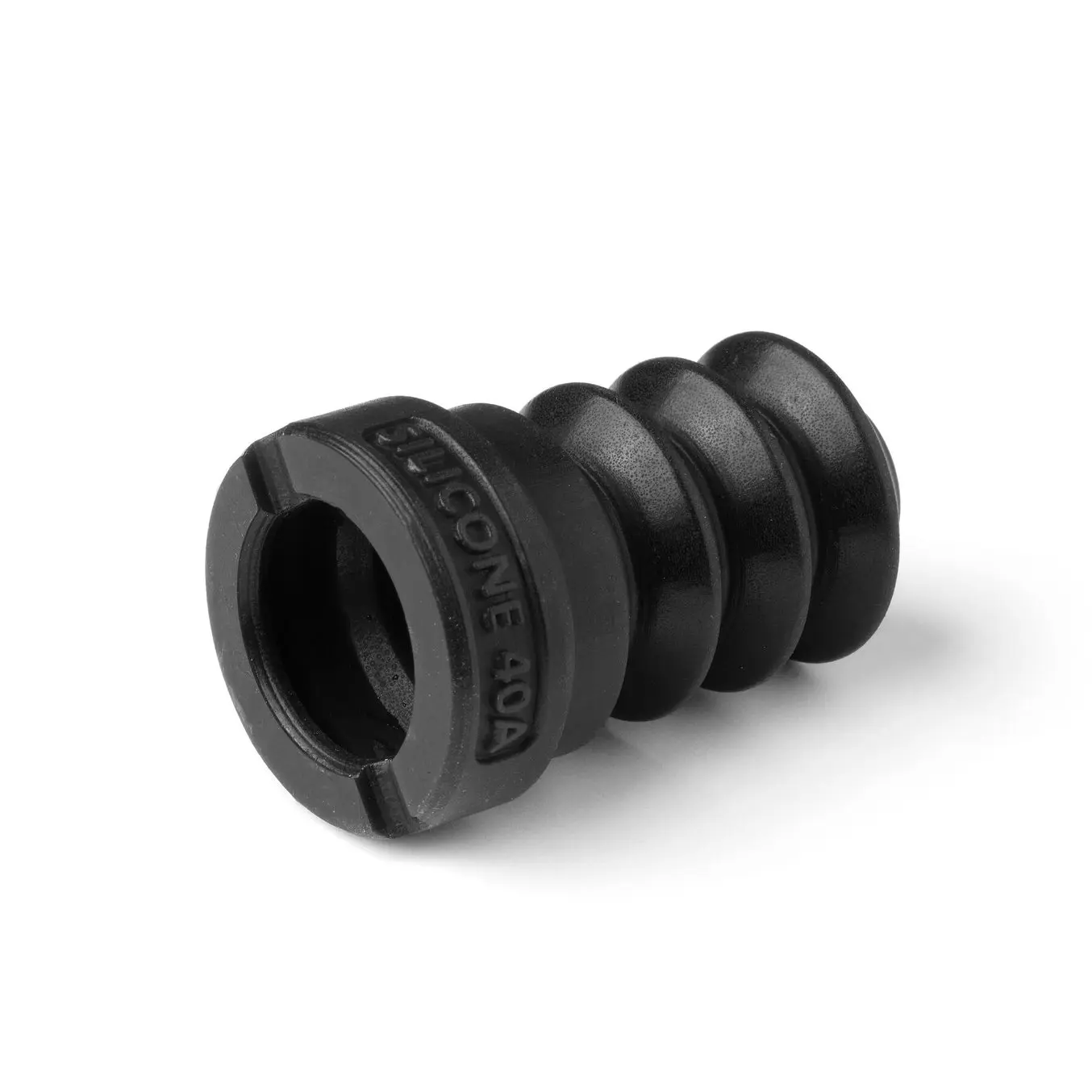
Commander un échantillon gratuit
Examinez et constatez par vous-même la qualité Formlabs. Nous enverrons un échantillon gratuit imprimé avec Silicone 40A Resin à votre bureau.
Des pièces métalliques trop belles pour être vraies
MM. Tryson et Allebach procèdent souvent à un post-traitement supplémentaire des pièces avant de les envoyer aux équipes de marketing et de vente de Dorman. Pour une pièce qui sera finalement produite en série avec du métal, ils font généralement passer la pièce SLA par un processus de finition avant de la remettre à leurs services en contact avec la clientèle. Récemment, ils ont imprimé des crampons à billes pour châssis avec Grey Pro Resin, puis les ont fait plaquer par galvanoplastie avant de les donner à leurs collègues pour réaliser des matériaux marketing (galvanoplastie réalisée par Repliform INC). Il n'y avait qu'un seul problème : la surface des pièces était presque trop belle ! « L'équipe marketing nous a dit que ces pièces étaient généralement forgées ou moulées, puis zinguées. Si nous utilisons ceci, ce sera encore mieux que la pièce livrée dans la boîte », explique M. Allebach.
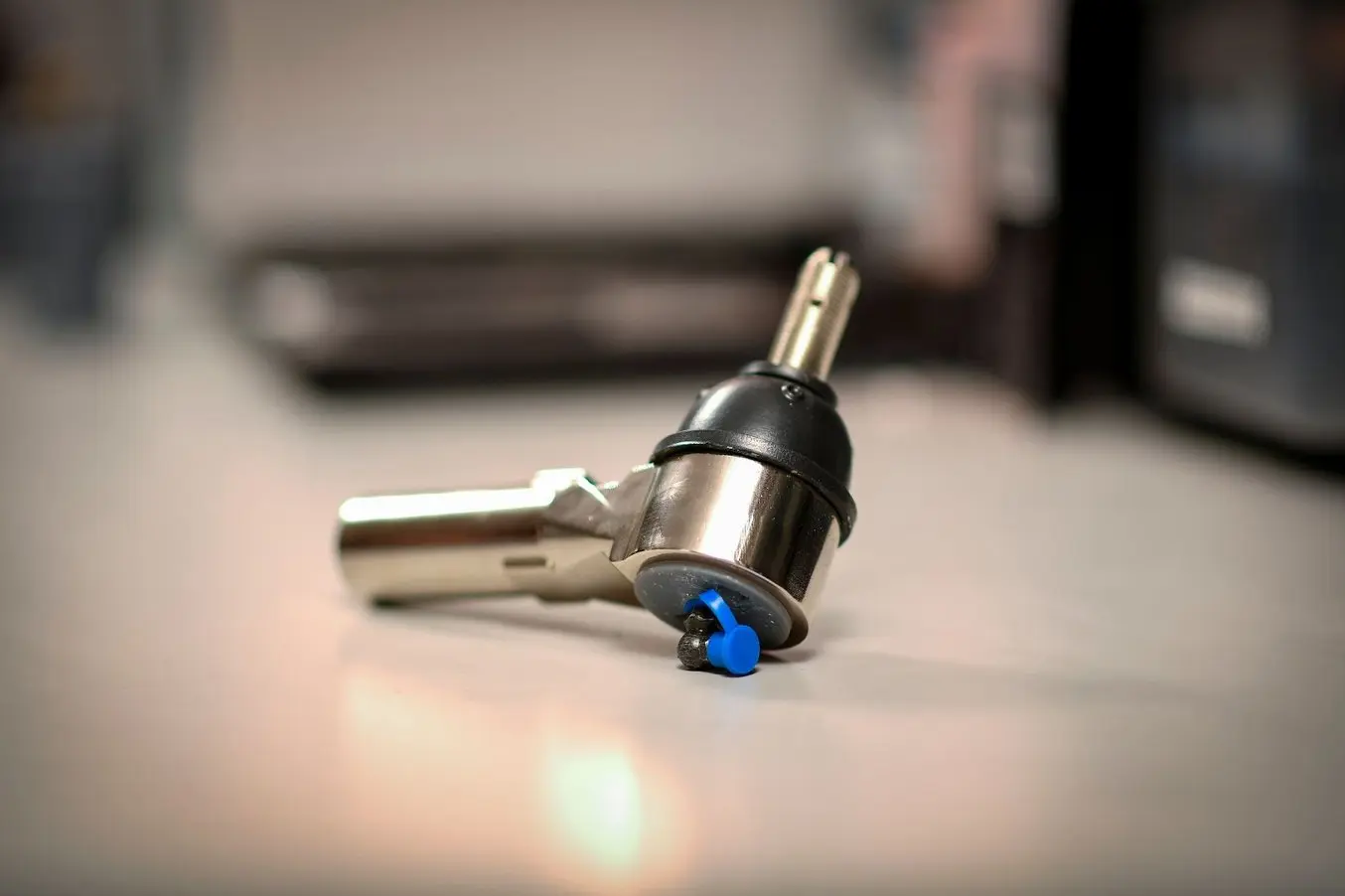
Un assemblage plaqué par galvanoplastie.
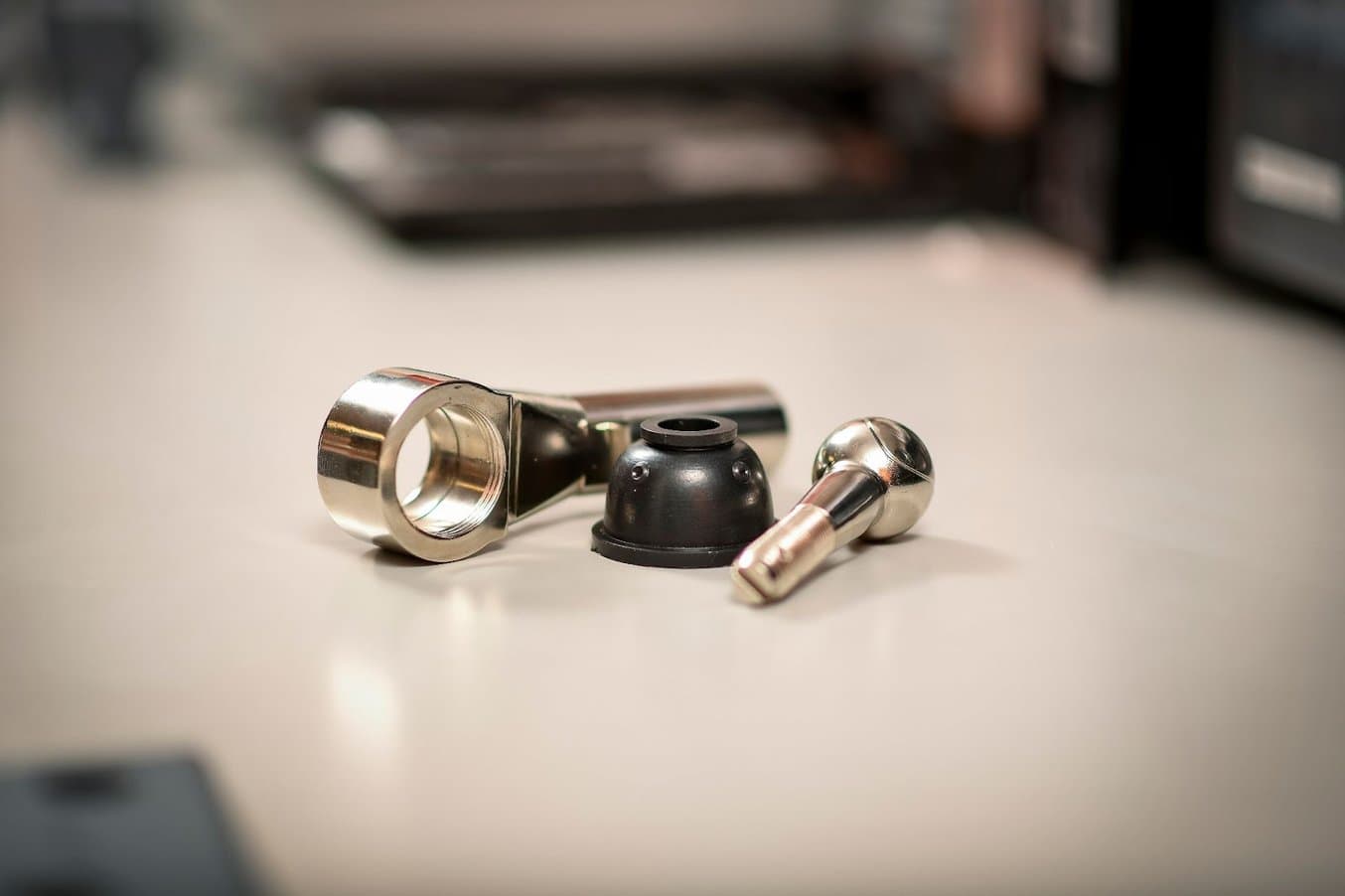
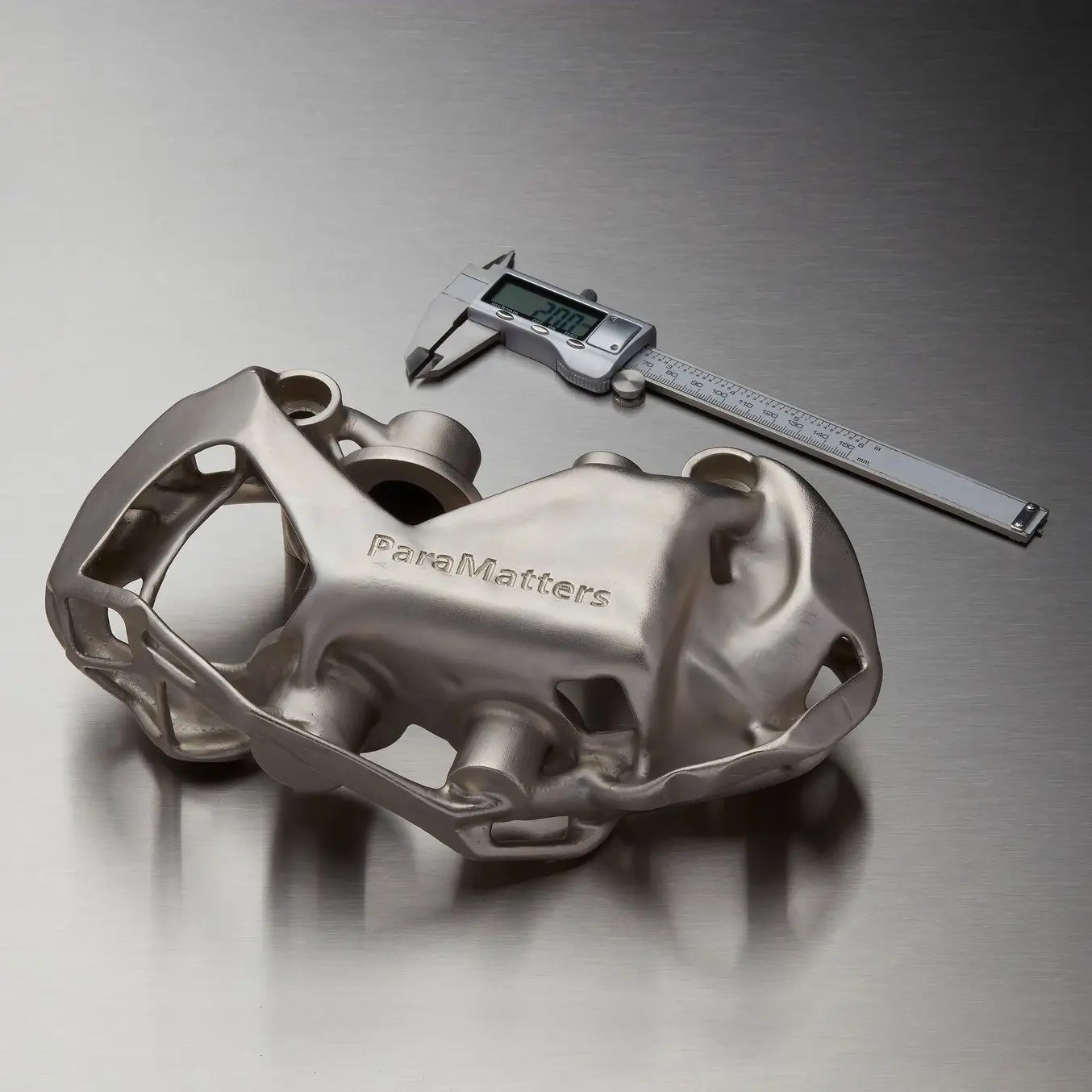
La résistance du métal : stratégies et exemples d'utilisation pour la galvanoplastie de pièces SLA
Lisez la suite pour savoir comment les ingénieurs ajoutent du métal aux impressions 3D en résine et à quelles applications surprenantes les pièces métalliques hybrides peuvent donner accès, permettant notamment (mais pas seulement) d'augmenter la résistance et la durabilité.
La puissance des imprimantes facilite le retour sur investissement
Depuis que Dorman a acquis sa première imprimante 3D FDM il y a dix ans, MM. Allebach et Tryson ont régulièrement ajouté de nouvelles machines et optimisé les capacités de leurs unités existantes. Ils ont également profité de toute la gamme de matériaux disponibles sur leurs imprimantes SLA Formlabs.
Bien que les ventes annuelles globales de Dorman s'élèvent à près de 1,35 milliard de dollars (le 25 décembre 2021), les achats d'équipement doivent toujours être justifiés. « Nous avons décidé d'opter pour la Form 2 pour la finition de surface et la précision dimensionnelle, et nous avons constaté que dans notre cas, elle a été amortie en l'espace de deux mois. Lorsque nous devons justifier l’achat ou le retour sur investissement d’une imprimante Formlabs, nous pouvons démontrer que quelques mois suffisent à la rentabiliser. Cela donne à nos dirigeants la certitude que l’impression 3D est un investissement rentable », explique M. Tryson.
Cette confiance a permis à MM. Tryson et Allebach d'investir dans leur première imprimante grand format, la Form 3L, il y a un peu plus d'un an. Comme les autres imprimantes, elle fonctionne 10 à 12 heures par jour, et parfois toute la nuit. Comme ils utilisent toutes les résines de notre gamme de matériaux, le fait de pouvoir fabriquer des pièces grandes ou petites avec les propriétés mécaniques voulues a optimisé leur flux de travail.
La possibilité d'imprimer des grandes pièces SLA pour seulement 10 000 $ vaut bien cet investissement. C'est une situation unique sur ce marché. Dans notre cas, les imprimantes ont été rapidement rentabilisées par le gain de temps et d'argent qu'elles ont permis de réaliser sur quelques pièces seulement.
Eric Tryson, responsable de l'équipe de conception mécanique, Dorman Products
L'impression 3D, un atout pour l'avenir
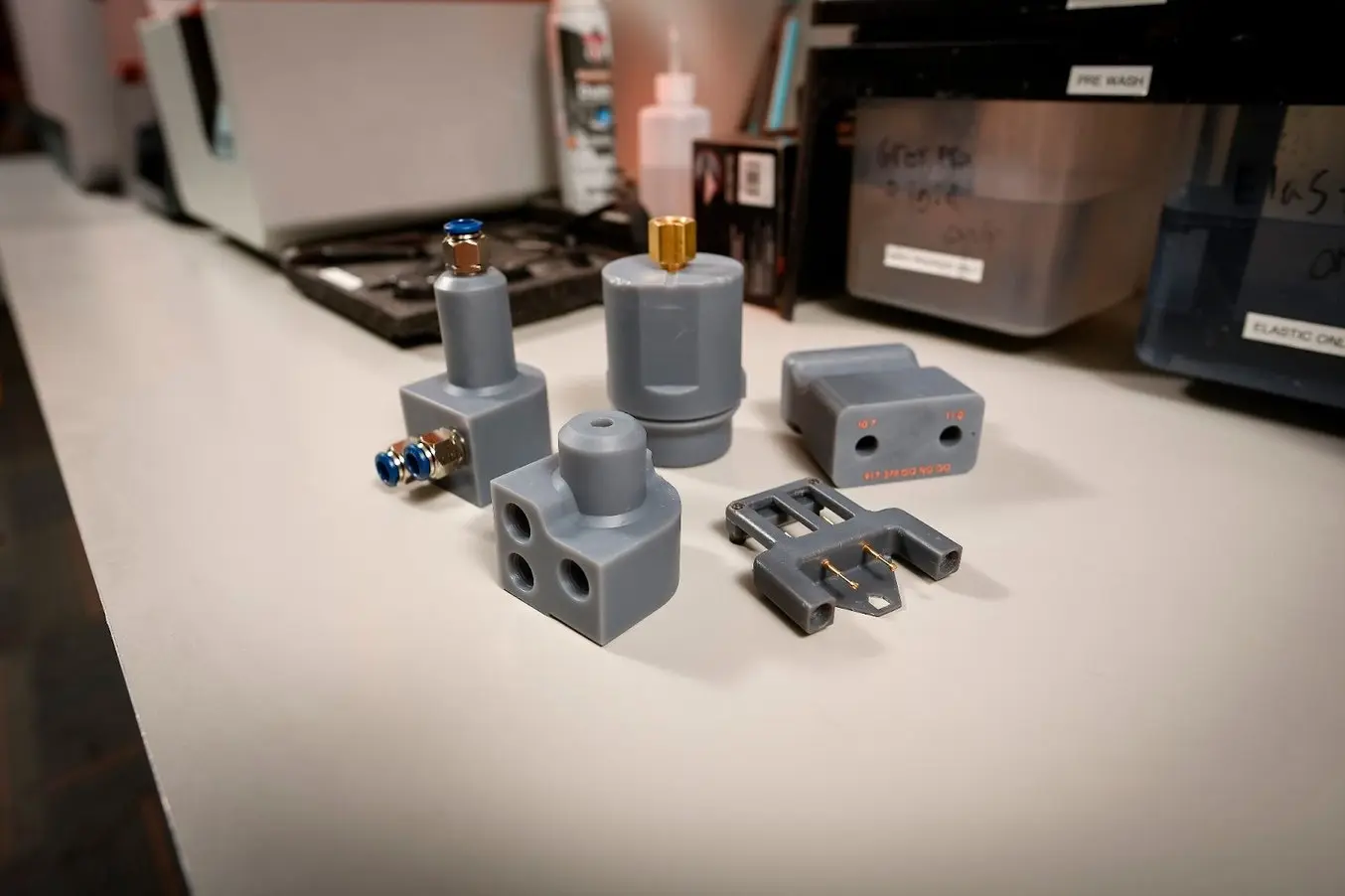
Les problèmes de chaîne d'approvisionnement ne semblent pas près de se résorber, et les prix des voitures, neuves ou d'occasion, restent élevés. Alors que de plus en plus d'équipementiers se tournent vers la fabrication de véhicules électriques, les pièces des nouveaux modèles deviennent plus légères, optimisées pour les nouvelles techniques de fabrication (souvent additives) et fabriquées à partir de matériaux non conventionnels. L'industrie automobile dépend de plus en plus de la technologie de fabrication additive, tant pour la conception originale que pour le marché des pièces détachées. Dorman Products a déjà pris de l'avance grâce à son installation actuelle, mais MM. Allebach et Tryson sont toujours tournés vers l'avenir.
« Nous pouvons concevoir et créer facilement des pièces, nous ne sommes en général pas limités par les processus de fabrication traditionnels. Nous avons également appris aux autres services que l’ajout de contre-dépouilles ou d’arêtes n’implique plus de coûts supplémentaires, comme c’était le cas avec l’usinage. Pouvoir créer une fixation exactement comme notre équipe l’imagine ouvre grand le champ des possibles », explique M. Allebach.
Le retour sur investissement étant solidement établi et les technologies FDM et SLA devenant de plus en plus familières au sein de l'entreprise, l'équipe est prête à également adopter l'impression sur lit de poudre.« Nous avons la rapidité d'exécution avec le FDM, la haute précision et la durabilité avec le SLA, mais lorsqu'il s'agit de pièces plus fonctionnelles, de petites séries de composants fonctionnels, nous aurions besoin du SLS », déclare M. Tryson.