Tests de validation dans le développement de produits : POC, EVT, DVT, PVT et production de masse
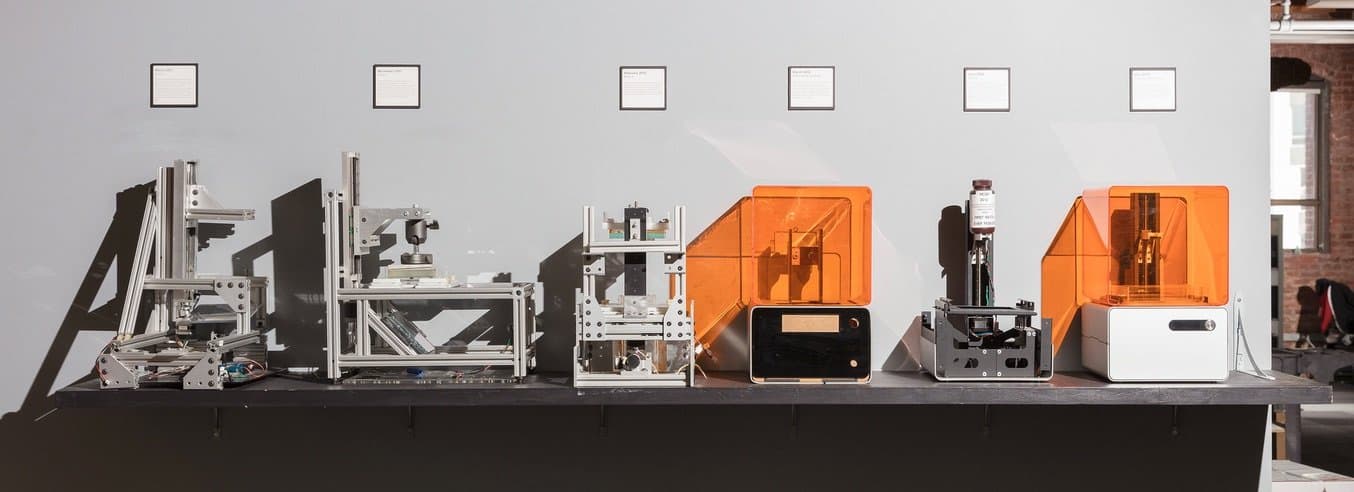
En règle générale, plus un produit est avancé dans son développement, plus il est coûteux d'y apporter des modifications. Par conséquent, l'un des principaux objectifs de toute initiative de développement de produit est de résoudre les problèmes assez tôt pour réduire le risque d'itérations coûteuses lors des étapes ultérieures.
C'est là que les tests de validation entrent en jeu. Les tests de validation consistent à déterminer si une pièce répond aux exigences correspondant à son stade de maturité et si elle est prête à passer au stade suivant. Au cours de ce processus, les concepteurs et les ingénieurs construisent de nombreux types de prototypes. Chaque étape laisse une place à l'apprentissage, à l'exploration et à l'adaptation, mais chaque produit passant au stade de développement suivant doit remplir des critères précis pour garantir une industrialisation réussie.
Dans cet article, nous expliquons comment optimiser le processus de développement en vue de la production de masse, et nous nous penchons sur les différentes phases de la maturité du produit, ainsi que les objectifs, les activités requises, les problèmes résolus, les prototypes produits et les critères de sortie.
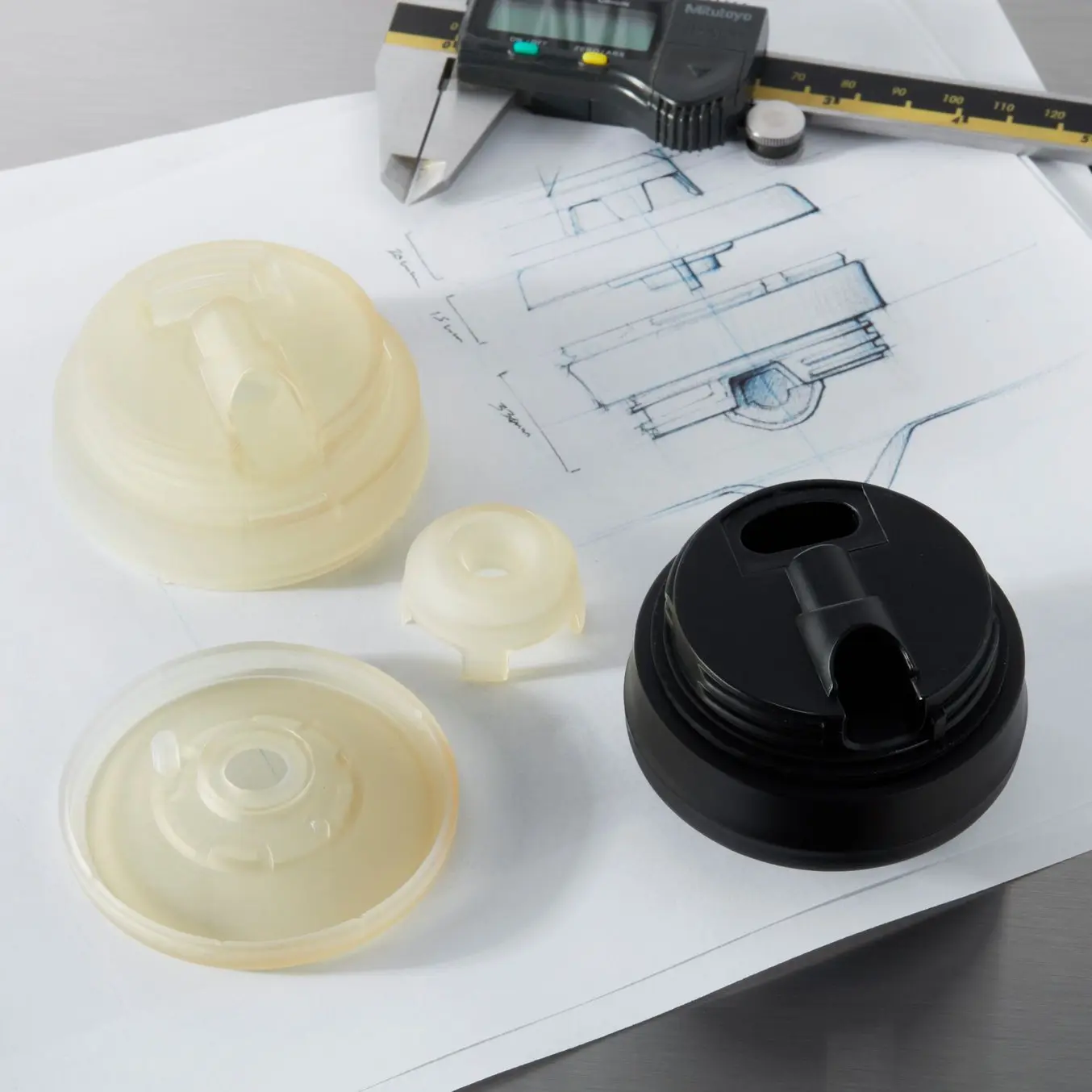
Guide de prototypage rapide pour le développement de produits
Dans ce guide, vous découvrirez comment le prototypage rapide s'intègre au processus de développement de produits, ses applications, et les outils de prototypage rapide dont les équipes de développement de produits disposent aujourd'hui.
Pourquoi effectuer des tests de validation ?
La conception d'un produit n'est pratiquement jamais prête à être produite dès le premier modèle CAO. Même un simple article en plastique peut présenter des marques d'enfoncement, des lignes d'écoulement ou des zones faibles en raison d'un refroidissement hétérogène après le moulage de la première série. Une zone peut s'avérer trop petite pour intégrer les étiquettes requises par la loi. Il peut parfois y avoir des problèmes de tolérance avec une pièce d'accouplement. Un groupe d'utilisateurs peut également proposer une nouvelle exigence hautement prioritaire, obligeant les concepteurs à entamer un nouveau cycle de développement.
Le processus de conception nécessite en permanence des modifications, des affinements et des pivots, ainsi que des études sur des aspects tels que la fabricabilité, l'estimation des coûts, la voix du client (VOC), la législation, la propriété intellectuelle et les normes de certification.
À mesure que le processus progresse vers la phase de production, le coût de ces itérations augmente de manière exponentielle. Alors qu'une série d'esquisses et de modèles en mousse réalisés par un concepteur au début du développement coûtera à l'entreprise 50 dollars en matériaux, un prototype rapide créé à partir de pièces imprimées en 3D, de pièces détachées et d'un surmoulage sous vide peut coûter à l'entreprise entre 500 et 1000 dollars. Changer d'outillage au cours de la phase de production peut entraîner un coût total allant jusqu'à 50 000 dollars et des retards de plusieurs semaines ou mois.
Pour les produits complexes, les investissements de production se chiffrent en millions. Les produits les plus difficiles à fabriquer, comme par exemple les avions, nécessitent des milliers d'employés et des milliards de dollars de coûts de production fixes. Afin d'éviter ces catastrophes aux effets exponentiels, les concepteurs et les ingénieurs veillent à itérer le plus possible à chaque étape pour garantir le succès du produit. Les tests de validation sont essentiels pour garantir que l'état de la conception répond au bon ensemble d'exigences à un stade donné. Le fait de délimiter chaque phase par des critères de sortie et des conditions claires garantit une utilisation optimale des ressources et une augmentation de la qualité.
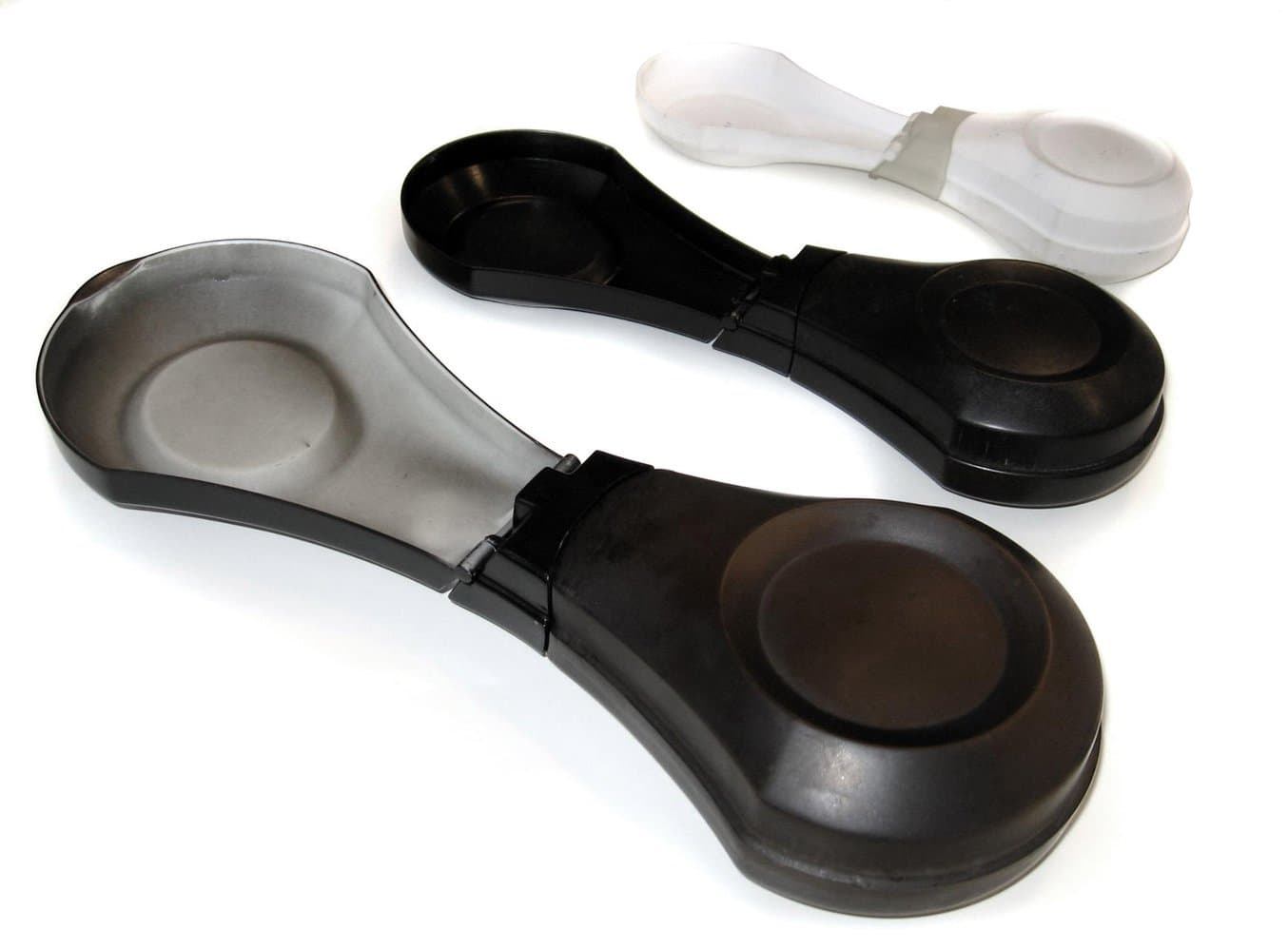
Un produit de consommation à différents stades de maturité du produit, au-delà de la maquette initiale. Arrière : modèle EVT fabriqué à l'aide de l'impression 3D SLS et SLA. Au milieu : première ébauche DVT fabriquée avec de l'outillage souple. Avant : modèle PVT fabriqué avec de l'outillage dur. Courtoisie : IDZone Product Design.
Les phases de maturité des produits
POC (preuve de concept) et prototypage
Une fois que les dirigeants de l'entreprise ont confirmé la planification du nouveau produit (NPP) en déterminant une opportunité de marché, un positionnement du produit, en effectuant une évaluation technologique, une stratégie de chaîne d'approvisionnement et une allocation de ressources, le processus de développement est généralement confié à une équipe produit qui doit traduire ces éléments dans un document sur les exigences du produit (PRD) et proposer des concepts viables.
Dans un premier temps, les prototypes de preuve de concept (POC) sont utilisés pour le test initial d'une idée, d'une méthode ou d'un produit afin de montrer son potentiel et sa faisabilité dans des situations réelles. Ces concepts sont ensuite convertis en prototypes, qui sont des modèles fonctionnels montrant exactement comment le produit fonctionnera en termes de mécanique, de conception, d'expérience utilisateur, etc.
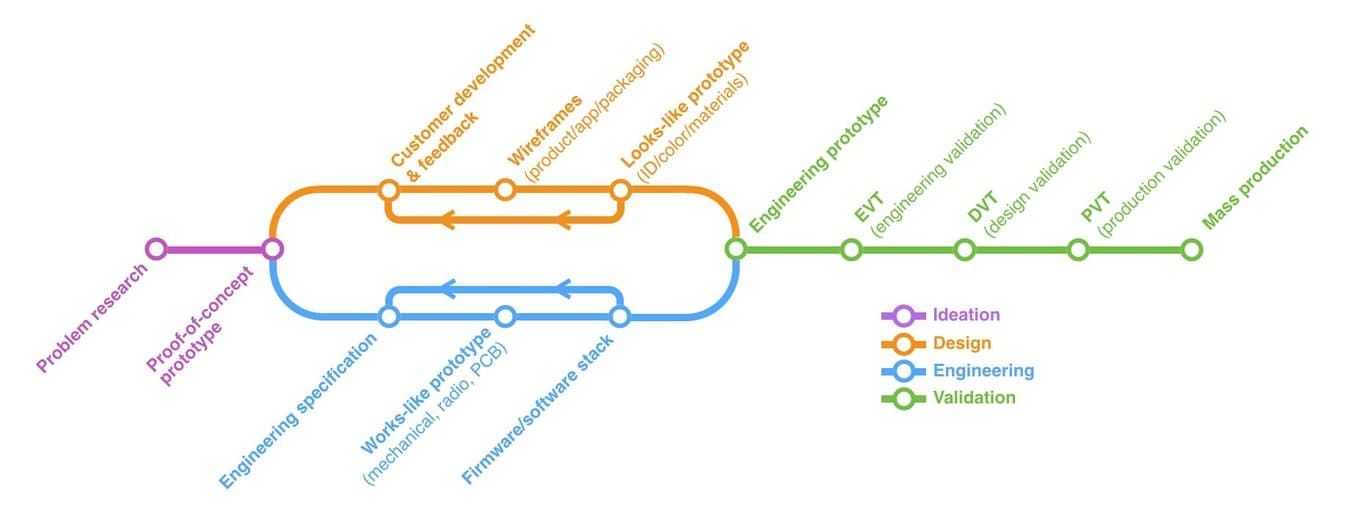
Les différentes étapes du développement d'un produit vers la production de masse. (source)
Un prototype est la représentation physique de la conception d'un produit qui peut être utilisée pour communiquer et évaluer sa valeur par rapport à certaines exigences. Les prototypes vont des modèles « mous » de faible fidélité fabriqués à la main avec des matériaux tels que l'argile, le carton, la mousse et le bois, aux prototypes fonctionnels de haute fidélité imprimés en 3D ou fabriqués dans l'atelier d'usinage. Les prototypes ciblés sont censés ne représenter qu'une partie des exigences du produit et peuvent être un modèle visuel, un modèle fonctionnel ou un modèle qui présente une forme et une fonction particulières afin de tester certaines sous-fonctionnalités. Lorsqu'un prototype intègre toutes les exigences et fonctionnalités de la conception, on l'appelle un prototype d'ingénierie.
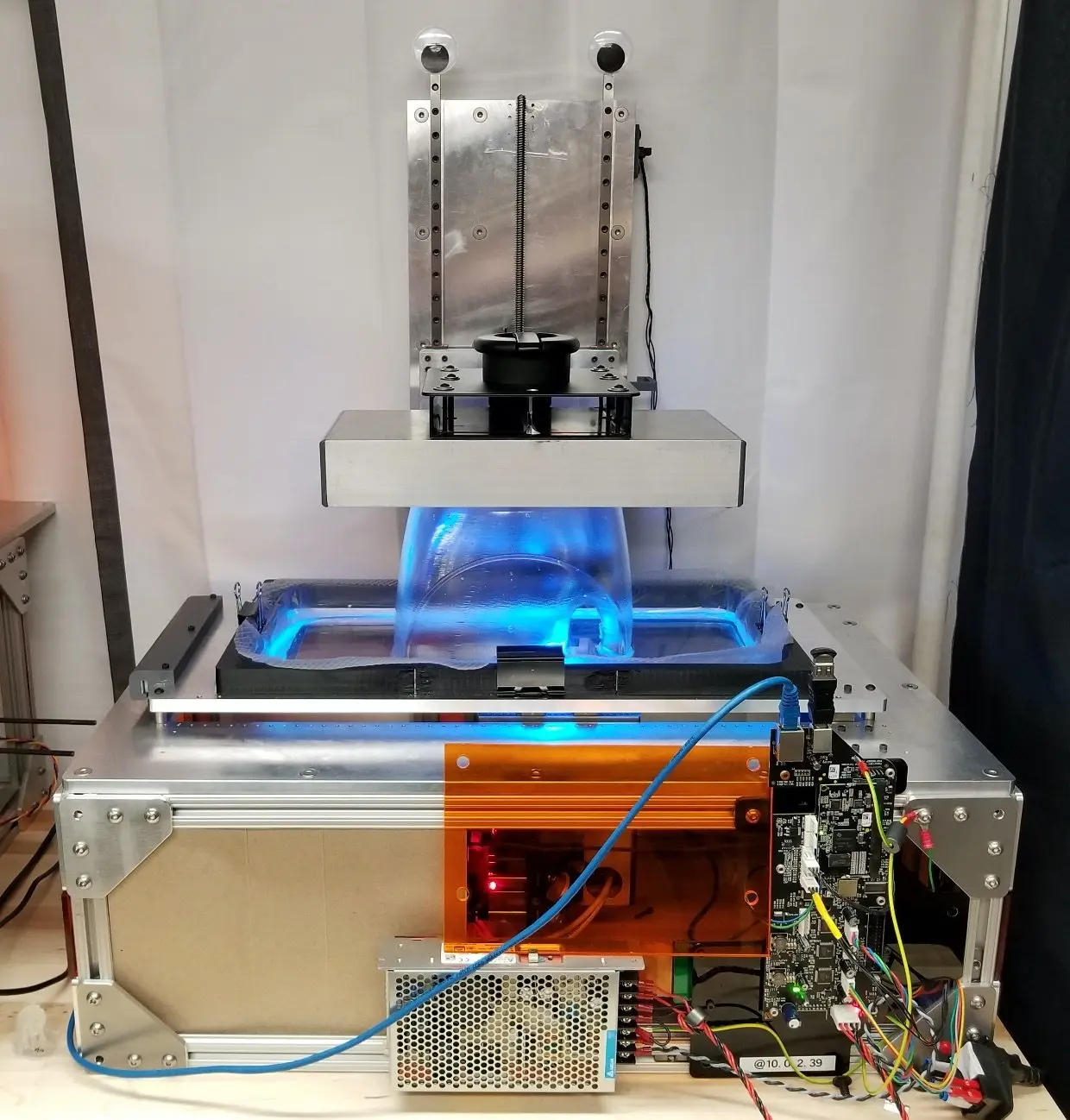
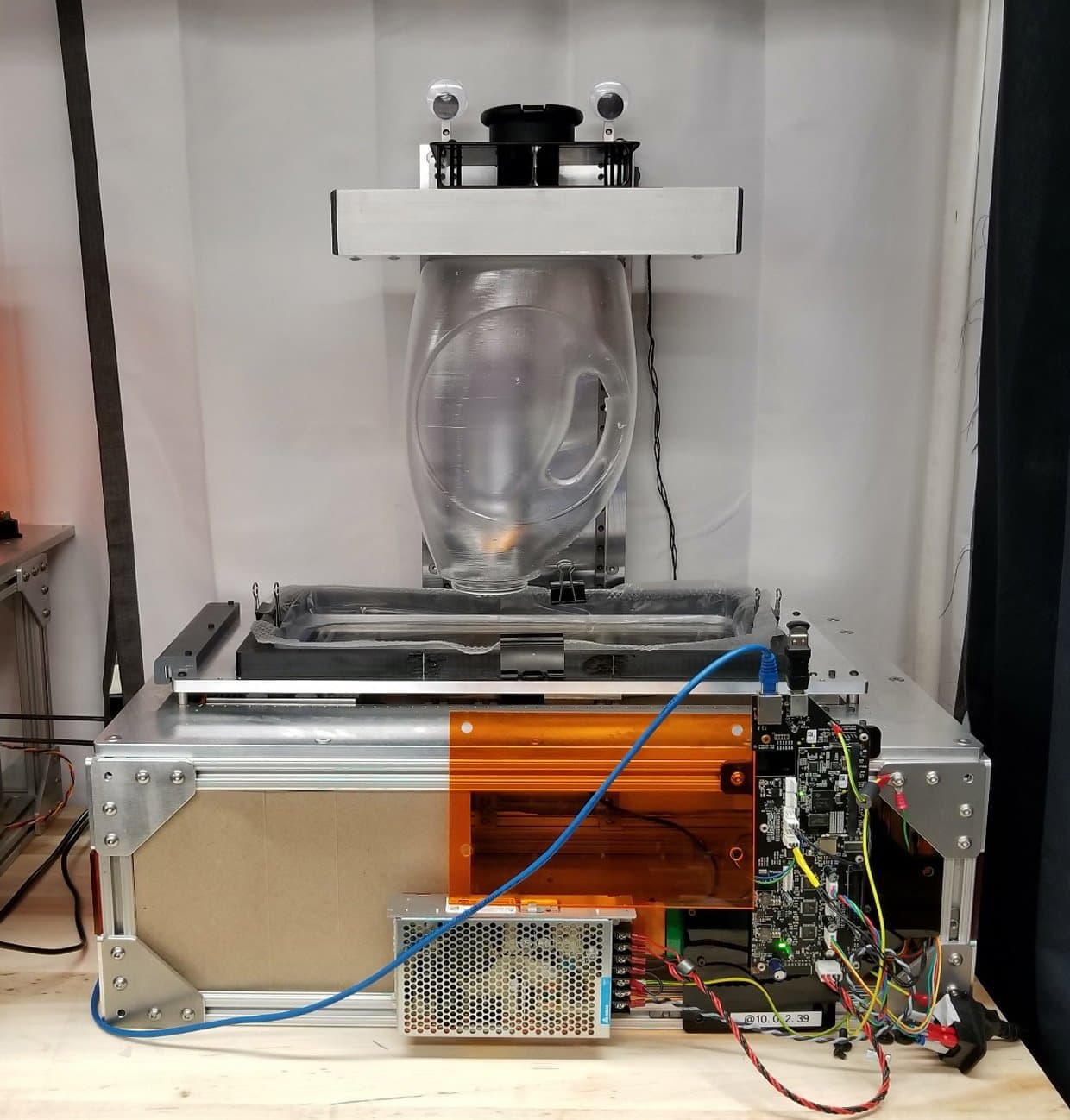
Un des premiers prototypes fonctionnels de l'imprimante 3D SLA grand format Form 3L.
Au cours de ce processus, il est possible de créer des modèles sans facteur de forme (NFF), qui sont en gros des versions géantes de la conception du produit destinées à accueillir des versions provisoires de tous les composants afin de développer un démonstrateur fonctionnel. Des versions rudimentaires de l'électronique sont incluses sous la forme de kits de développement matériel, de constructions Arduino ou Raspberry Pi.
Les prototypes analytiques ou virtuels sont des représentations non physiques du produit, comme par exemple un modèle 3D pour le rendu, la simulation mathématique ou l'analyse par éléments finis. Même une esquisse peut être considérée comme une forme grossière de prototype virtuel.
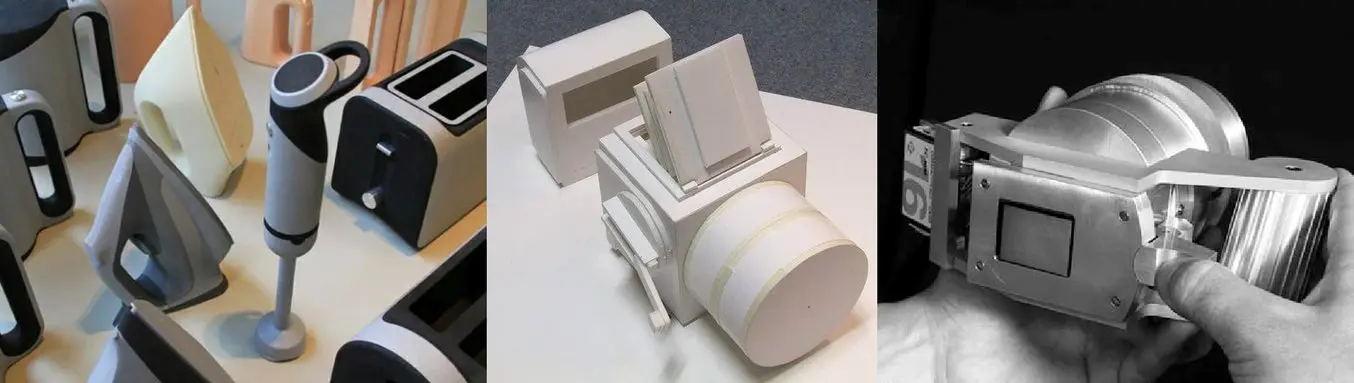
Prototypes alpha testables avec différentes fidélités. À gauche : modèles visuels en mousse d'appareils de cuisine. Courtoisie : Superior Prototype. Au milieu : maquette en carton/mousse montrant la forme partielle et l'interactivité. Courtoisie : Frits van Beek. À droite : prototype d'appareil photo numérique usiné et partiellement interactif. Notez qu'il s'agit d'un prototype alpha car il n'est pas encore conçu pour la production. Courtoisie : Joep Frens.
La phase de prototypage est essentielle pour clarifier les détails concernant la facilité d'utilisation, l'esthétique, les besoins cachés des utilisateurs, les opinions des autres concepteurs, des gestionnaires de produits, des experts en la matière, ainsi que les limites législatives et technologiques. Un processus de conception typique pour un produit électromécanique complexe comprend plusieurs concepts, chacun d'entre eux étant étayé par une pile de croquis d'exploration, une série de maquettes physiques et un ensemble de rendus en 3D.
Il a fallu à l'équipe de conception d'IDEO 80 modèles en mousse pour mettre au point la forme de la première souris d'ordinateur ergonomique pour Microsoft en 1987. Les processus plus risqués et plus complexes peuvent nécessiter jusqu'à 5127 prototypes, comme par exemple dans le cas de James Dyson qui a mis 15 ans à développer le premier aspirateur à technologie cyclone. Pour accélérer le processus de développement d'un nouveau produit et éviter d'être enseveli sous le matériel, il est primordial de centrer les prototypes sur les exigences clés, de tenir compte des risques que présenteront les étapes ultérieures et de planifier de manière appropriée les tests exploratoires des utilisateurs.
Dans l'ensemble, l'objectif de la phase de prototypage est de créer un prototype technique qui fonctionne et ressemble au produit final. Cette étape doit prouver que la technologie utilisée répond aux besoins du client, qu'il est possible de fabriquer le produit et qu'il fonctionnera comme prévu. Une fois ces éléments confirmés, l'objectif des étapes de validation suivantes est de s'assurer que le produit peut être fabriqué de manière cohérente et en grande quantité.
EVT (validation technique)
L'étape du test de validation technique (EVT) consiste à incorporer et à optimiser la portée fonctionnelle requise pour le produit. Alors que le résultat de l'étape de prototypage était un prototype alpha limité, ici, un prototype bêta de niveau technique sera développé et comprendra un ensemble plus complet de fonctionnalités, généralement déterminé par une liste. Le prototype d'ingénierie est une version minimale viable du produit final conçu pour la fabrication (DFM). Il est utilisé pour des essais en laboratoire avec un petit groupe d'utilisateurs, pour communiquer l'intention de production aux spécialistes de l'outillage lors des étapes ultérieures, et pour servir de démonstration lors des premières réunions de vente.
Une analyse « make-buy » est effectuée pour tous les composants de l'assemblage, l'ingénierie des composants est réalisée pour les pièces personnalisées et une nomenclature est établie pour les appels d'offres à l'intention des fabricants sous contrat afin qu'ils puissent se préparer à la première ligne d'assemblage et à l'outillage des premières injections. Pour les produits électroniques, les circuits imprimés haut de gamme essentiels sont développés à l'aide de processus industriels. Des tests de puissance, thermiques et EMI seront également effectués à ce stade.
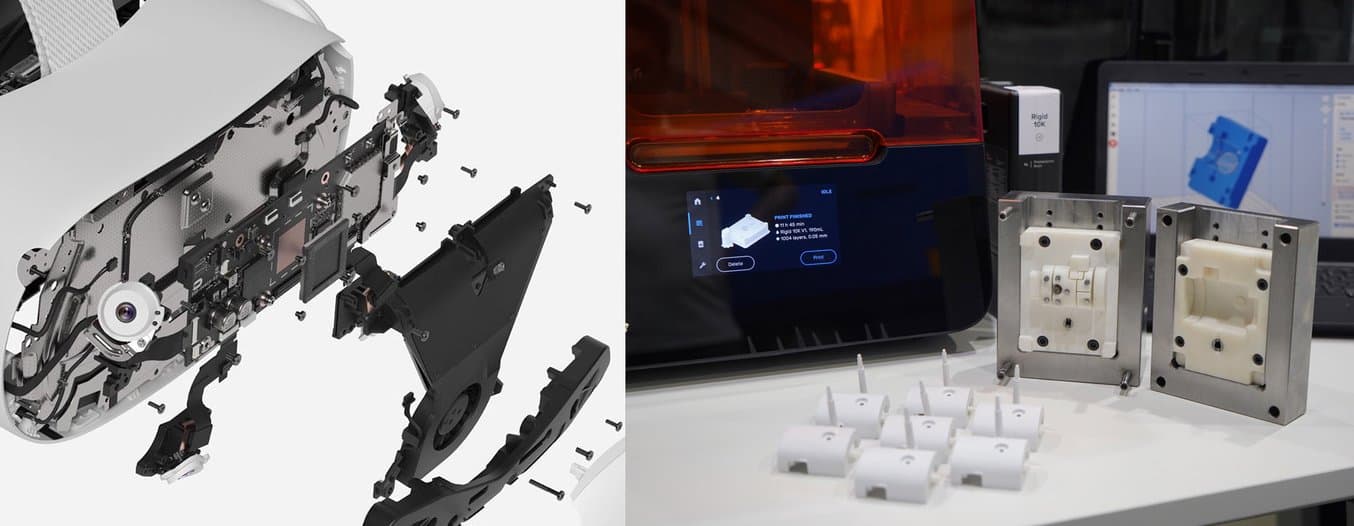
Activités typiques de la phase EVT. À gauche : rendu de la conception du produit montrant une vue éclatée au niveau de l'intention de production. Courtoisie : Oculus. À droite : Moulage par injection de petites séries à l'aide de moules imprimés en 3D.
Environ 20 à 50 unités sont produites à l'aide de procédés de haute précision tels que la fabrication additive et l'usinage CNC, ou d'une série de moulages basés sur un outillage souple tel que le silicone ou des moules imprimés en 3D. L'objectif global est de développer la conception avec une intention de production complète et d'aboutir à un petit nombre de prototypes techniques aptes à la production.
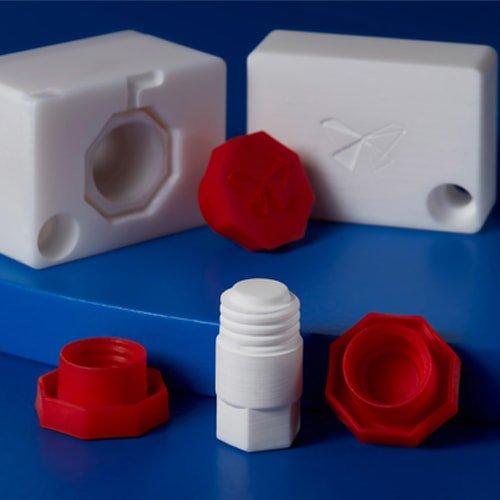
Le moulage par injection rapide en petite série avec des moules imprimés en 3D
Téléchargez ce livre blanc pour savoir comment utiliser des moules imprimés en 3D pour le processus de moulage par injection, et ainsi réduire les coûts et les délais de production. Vous y trouverez des études de cas réels, réalisées chez Braskem, Holimaker et Novus Applications.
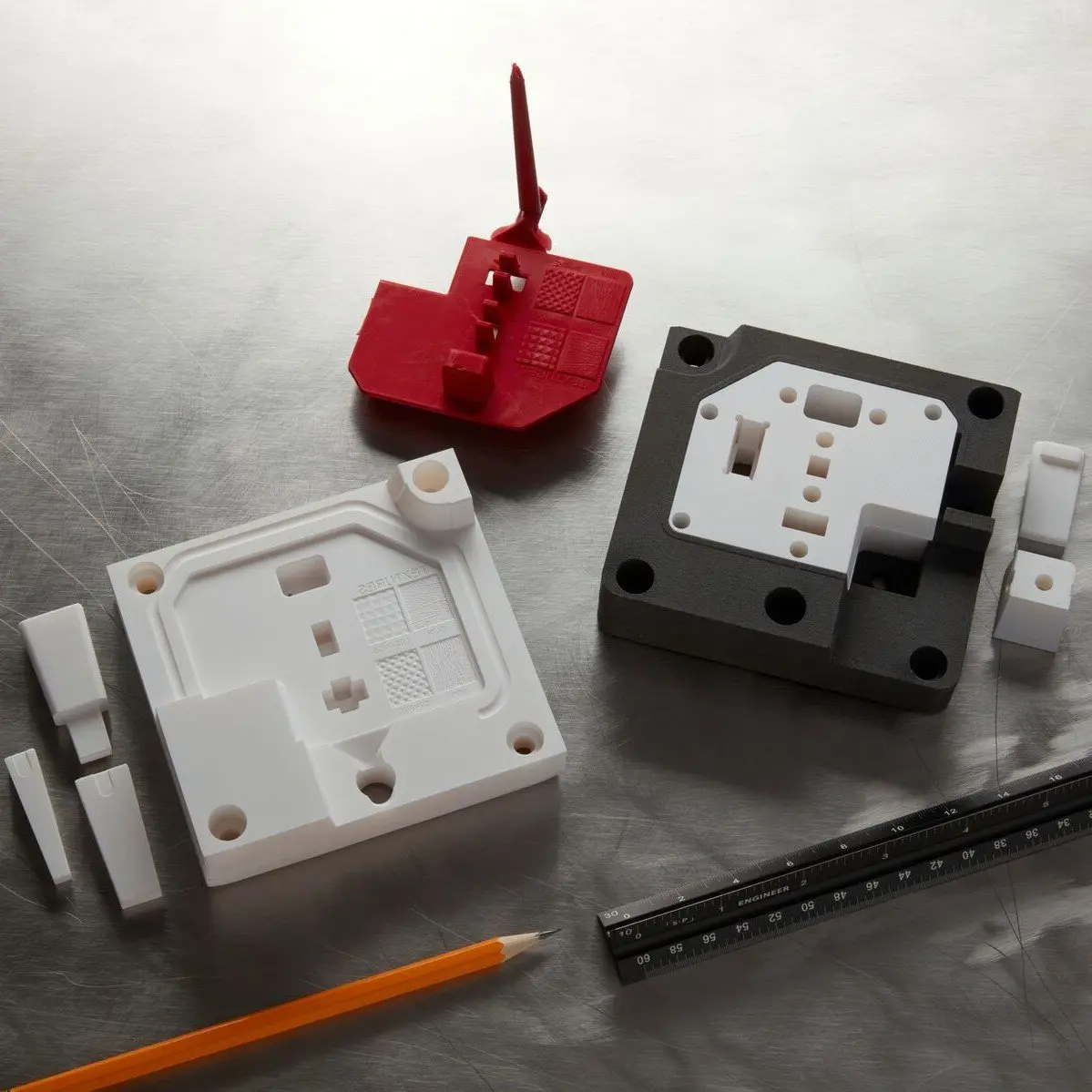
Guide de l'outillage rapide
Dans ce livre blanc, apprenez comment combiner l'outillage rapide imprimé en 3D avec des procédés de fabrication traditionnels tels que le moulage par injection, le thermoformage ou la fonderie.
DVT (validation conceptuelle)
L'étape de la validation conceptuelle (DVT) est celle où un produit commence véritablement à être industrialisé. Alors que l'EVT concerne la conception de l'architecture en vue de la fabrication, le DVT vise à régler les détails tout en progressant vers la première ligne de production de masse. C'est une étape marquée par l'expérimentation et l'optimisation. Les circuits imprimés sont itérés jusqu'à la perfection grâce aux efforts de débogage et de débruitage. Le fabricant sous contrat développera le premier outil dur pour chaque pièce fabriquée afin de vérifier les rendements de la production de masse. Les moules en aluminium peuvent être utilisés pour optimiser la conception en termes de finition de surface, de matériaux, de tolérances, et de configuration du moule (ex : ajout de curseurs et de cames, nouvelles méthodes d'assemblage, autres paramètres de processus, etc.).
Si, en général, 50 à 200 unités sont produites, il n'est pas rare de voir plus de 1000 unités produites pour les grands projets. Ces unités sont ensuite renvoyées pour des évaluations internes et la mise en œuvre de modifications techniques finales, tandis que d'autres sont envoyées comme unités bêta à des clients potentiels et à des experts. De nombreux tests seront effectués sur les premières unités de production : tests en chambre environnementale, cycles thermiques, vibrations, ESD, biocompatibilité, résistance chimique, certifications FDA, FCC, UL, CE, EC et RoHS, vieillissement, radiation, cosmétique, usure et tests de chute, et bien d'autres. Des tests utilisateurs approfondis sont effectués auprès d'une partie importante de la population dans un contexte réaliste.
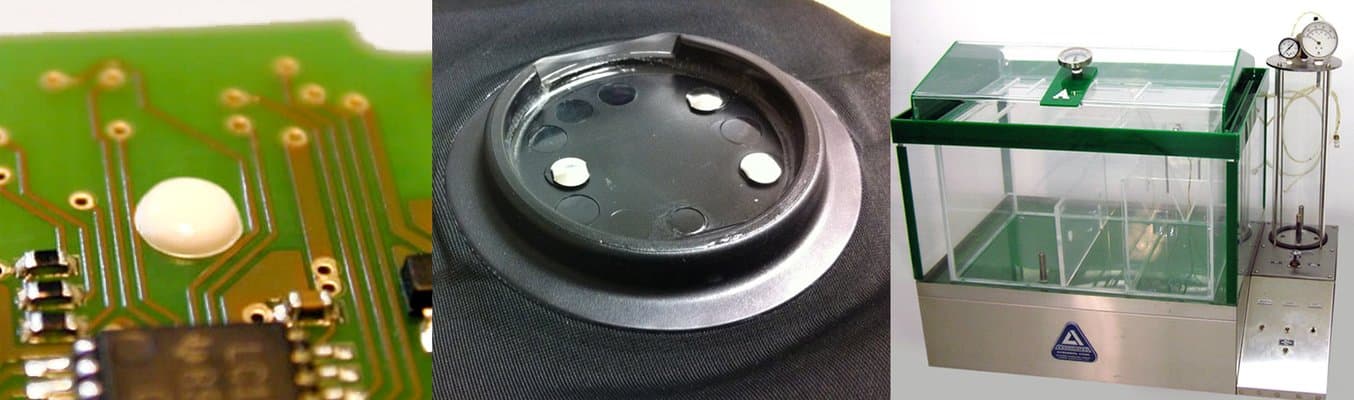
La phase DVT consiste à optimiser les détails. À gauche : circuit imprimé fixé à son boîtier plastique à l'aide de rivets intégrés. Courtoisie : Hartmann. Au milieu : expérience d'intégration d'un boîtier moulé par injection dans un substrat en tissu. Courtoisie : Bemis Sewfree. À droite : chambre environnementale AES pour les tests de corrosion par brouillard salin. Courtoisie : Associated Environmental Systems.
Pour accélérer le développement d'un produit, il est possible de contourner la phase DVT en investissant dans un outillage dur à la fin de la phase EVT, de sorte que le prototype d'ingénierie satisfait immédiatement non seulement au critère de sortie de la phase EVT, qui consiste à disposer d'un prototype apte à la production, mais aussi aux critères de sortie de la phase DVT, qui consistent en un outillage dur et une évaluation du rendement de la production en série. Toutefois, investir des ressources à l'échelle du PVT aussi rapidement comporte des risques énormes et il n'est pas, ou peu, conseillé de prendre des raccourcis de ce type.
PVT (validation de pré-production)
La validation de pré-production (PVT) est la phase finale avant le début de la production en série. L'outillage dur est fixe, ce qui signifie que l'on ne peut plus modifier ni la conception du produit ni les moules de production. Les gabarits, les montages et les bancs d'essai doivent être en place et validés pour que la production pilote puisse commencer. Les efforts déployés à ce stade visent à optimiser et à stabiliser les lignes de production et d'assemblage en termes de vitesse de ligne, d'expertise des opérateurs, de taux de rebut et de rendement journalier.
Les risques potentiels, tels que l'approvisionnement auprès d'une source unique (lorsqu'un composant ne peut être fabriqué que par un seul fabricant sous contrat sélectionné) seront identifiés par des protocoles de gestion des risques tels que l'AMDEC, l'AQ/CQ et le FAI. Les appareils électroniques sont allumés pour la première fois, les microprogrammes sont vérifiés, et l'emballage du produit ainsi que les manuels d'utilisation sont également créés à ce stade. À cette étape, la plupart des tâches sont exécutées par le fabricant sous contrat.
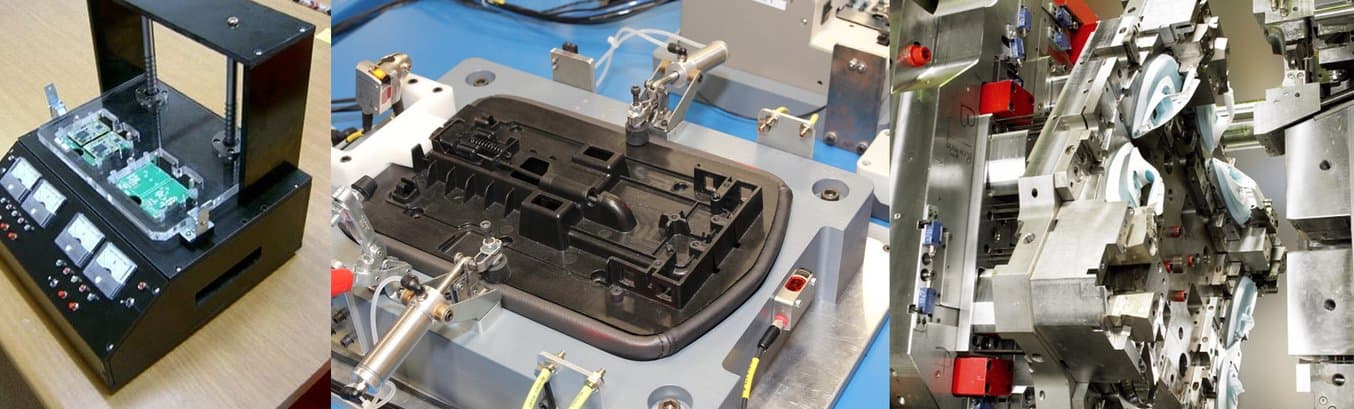
La phase PVT consiste à optimiser la ligne de production par le biais du contrôle des processus et de la qualité. À gauche : gabarit de test de panneaux pour plusieurs cartes de circuits imprimés. Courtoisie : Korea Jig. Au milieu : gabarit d'assemblage multi-stations pour un produit de consommation. Courtoisie : Aerosport Additive. À droite : moule rotatif complexe pour le moulage multi-matériaux. Courtoisie : Grosfilley In-Mold & Rotative Solutions.
Le résultat typique de l'étape PVT est plus de 500 unités ou au moins 5 % de la quantité de la première série de production. Les objectifs sont de vérifier les rendements de production de masse à des vitesses de production de masse et de créer des produits vendables. C'est à ce stade que de nombreuses entreprises vont créer un plan de vente et entamer leurs opérations avec les premiers acheteurs. La mise au point du modèle PVT est la dernière chance pour une entreprise d'ajuster le processus de production. On parle parfois de statut rouge, orange ou vert, en fonction de la conformité aux principaux paramètres de production. Lorsque la lumière verte s'allume, la véritable production de masse peut commencer.
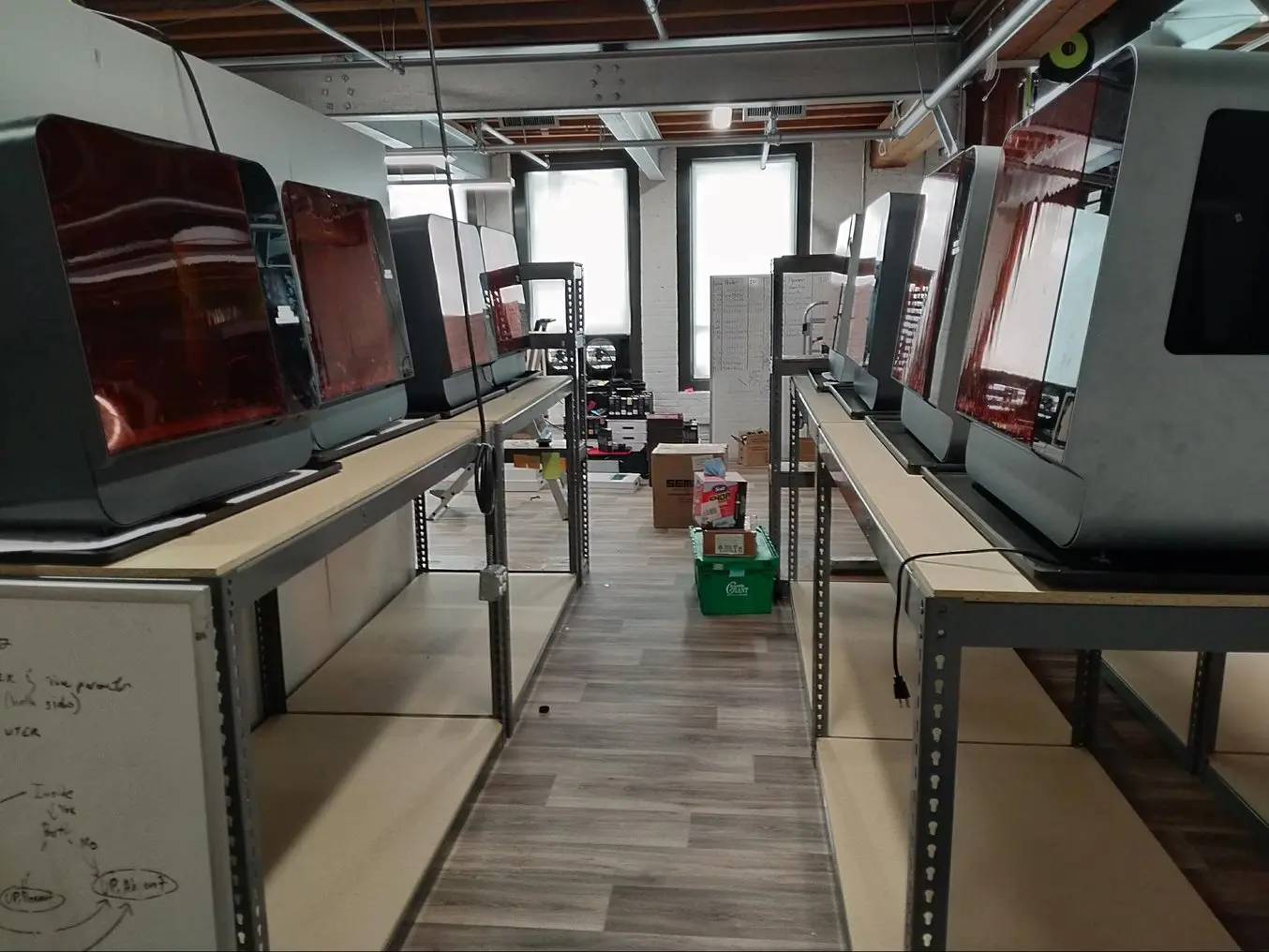
Unités PVT de la Form 3L avant le contrôle qualité au siège de la compagnie. Au stade du PVT, il est encore courant de renvoyer des unités de production du fabricant sous contrat à l'équipe d'ingénierie pour un contrôle de qualité final avant que les produits ne soient prêts à être expédiés aux clients (surtout lorsqu'une pandémie mondiale rend impossible un contrôle de qualité en personne chez le fabricant sous contrat).
Production de masse
L'étape finale de l'évolution de la maturité du produit est la progression vers la production de masse. Elle commence généralement par une quantité minimale de 5000 unités, mais peut aller jusqu'à plusieurs millions d'unités dans le cas de produits de consommation populaires tels que la PlayStation, l'iPad, l'iPhone ou le Rubik's cube.
Dans cette phase, la ligne de production initiale peut être reproduite sur d'autres lignes pour être exploitée en parallèle. Une analyse des défaillances et du rendement sur un petit pourcentage d'unités garantit une qualité constante. Les premiers retours arriveront, et l'analyse EFFA garantira que toutes les unités défaillantes seront renvoyées à l'équipe d'ingénierie. Pour garantir davantage de qualité, les usines et les fournisseurs doivent être supervisés afin d'éviter toute modification imprévue de l'outillage ou des paramètres de processus entraînant des variations de qualité. L'accent est mis sur l'amélioration du rendement, la réduction des coûts et l'expansion si nécessaire. L'équipe de marketing et de vente peut ici se concentrer sur le développement du matériel de marketing, la publicité, ainsi que la prévision des volumes de vente.
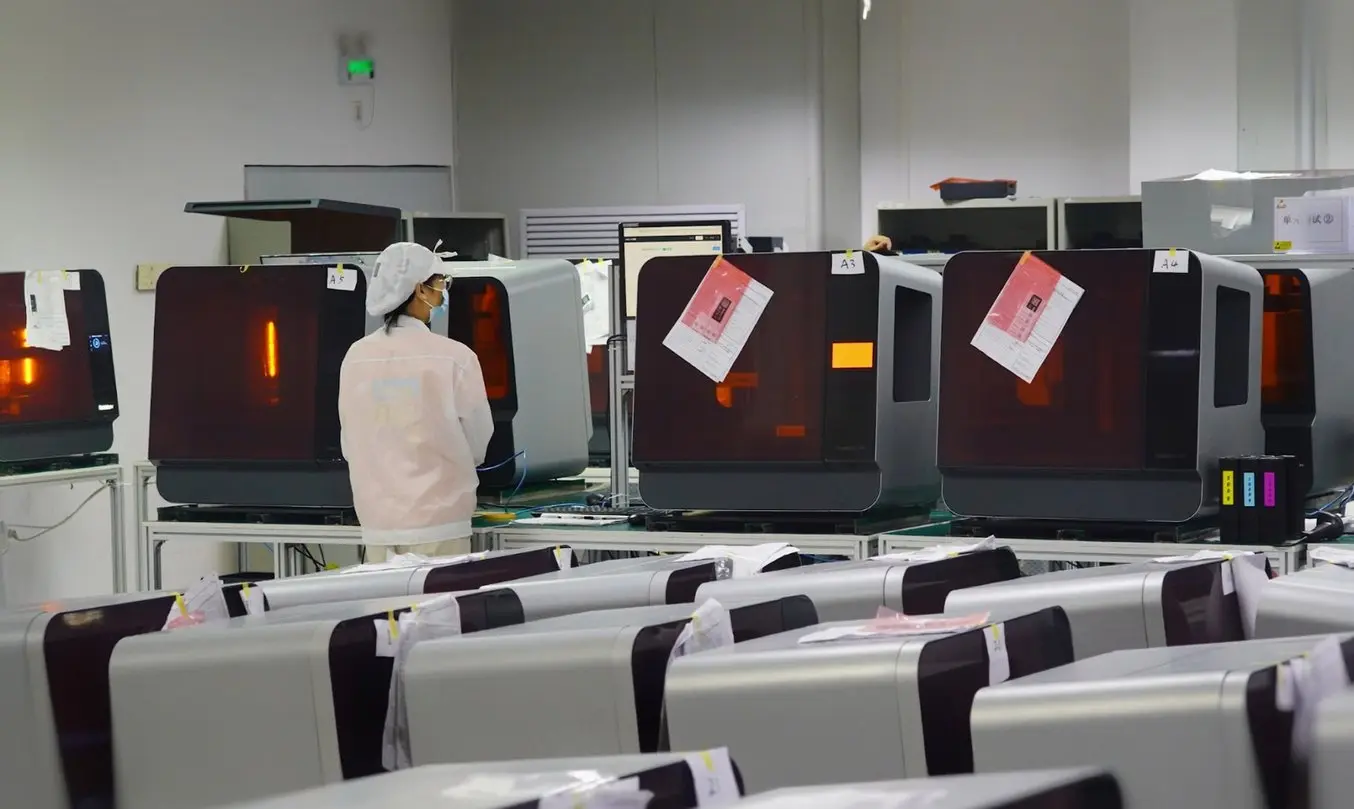
Unités de Form 3L produites en masse après le contrôle AQ/CQ chez le fabricant contractuel.
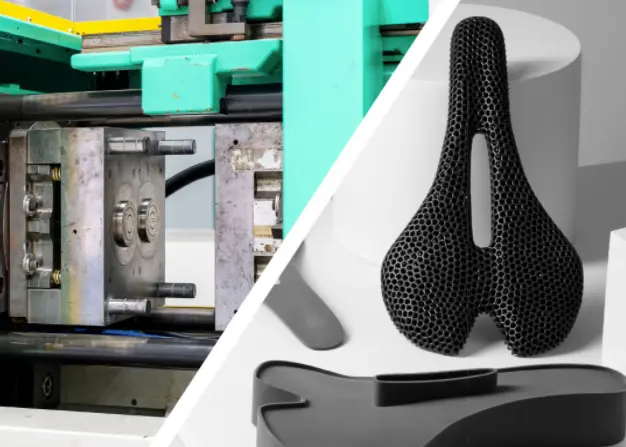
Impression 3D SLS ou moulage par injection : quand remplacer des pièces moulées par l'impression 3D
Ce livre blanc présente la dynamique des coûts pour des cas d'utilisation réels, et vous montre comment utiliser l'impression 3D SLS, le moulage par injection, ou les deux.
Les différentes étapes du processus de développement de nouveaux produits
Phase | NPP | POC | EVT | DVT | PVT | Production de masse |
---|---|---|---|---|---|---|
Maturité | Cas commercial | Prototype alpha | Prototype bêta | Échantillons de pré-production | Produit commercial complet | Produit commercial complet |
Durée | 1 – 3 mois | 3 mois à 3 ans ou plus | 3 – 6 mois | 3 mois | 1 mois | 3 mois ou plus |
Objectif principal | Comprendre l'opportunité du marché, créer une liste des exigences produit (PRD) | Prouver l'intérêt de l'utilisateur | Unité apte à la production | Faisabilité de la mise à l'échelle | Préparation à la production de masse | Assurance qualité |
Quantité | 0 | 5 | <50 | <500 | 500+ | 5000+ |
Ventes | Positionnement | Plan de marketing | Prévisions de ventes | Préparation du lancement | Plan de vente | Publicité |
VOC (voix du client) | Entretiens, groupes de discussion | Tests utilisateurs exploratoires | Tests utilisateurs en laboratoire | Tests utilisateurs in-situ | Analyse du terrain | Retour d'information continu |
Lieu | En interne | En interne + partenaire de conception (facultatif) | En interne + partenaire d'ingénierie (facultatif) | Fabricant sous contrat + validation interne | Fabricant sous contrat | Fabricant sous contrat |
Conclusion
Prendre les mauvaises décisions ou négliger des détails essentiels à un stade trop avancé du développement du produit peut entraîner des coûts élevés et des retards importants. Les entreprises ne peuvent pas non plus se permettre de nuire à leur réputation en envoyant des unités bêta erronées. Une approche du développement par phases basée sur la validation est nécessaire pour toutes les formes de produits, systèmes et services complexes. Cela permet de garantir une trajectoire optimale vers la production de masse tout en limitant les ressources au minimum.
Pour résumer les phases de maturité du produit, l'objectif des phases de POC et de prototypage est de vérifier que le concept du produit est viable, que les gens en ont besoin et qu'il est possible de le développer. Au cours de l'étape EVT, l'équipe de développement vise à établir la confiance dans le bon fonctionnement de la conception. L'étape DVT vérifie que la conception peut être fabriquée en grandes quantités et fait passer au produit de nombreux tests, tandis que l'étape PVT est là pour garantir que la ligne de production peut produire les volumes souhaités. Pendant la production de masse, l'accent est mis sur les ventes, le maintien de la qualité, le traitement des retours, la préparation des futurs changements de conception et la fin de vie.
On ne saurait trop insister sur l'importance d'une liste d'exigences produit (PRD) complète, d'une approche de prototypage bien planifiée et d'une analyse approfondie aux premiers stades du développement du produit, afin d'éviter des changements radicaux en cours de route. Mais la satisfaction que vous ressentirez en ouvrant le premier carton tout juste sorti de la chaîne de montage et en voyant le fruit de mois voire d'années de travail acharné est incomparable.
L'impression 3D est l'un des outils qui peuvent aider vos équipes tout au long du processus de développement des produits. Qu'il s'agisse de prototypes haute-fidélité, d'outillage rapide ou de dispositifs de fixation pour la chaîne de montage, les imprimantes 3D peuvent vous aider à accélérer le processus de développement et à garantir une fabrication réussie.