Comment Lufthansa Technik utilise des outils imprimés en 3D pour fabriquer des marquages de sorties de secours
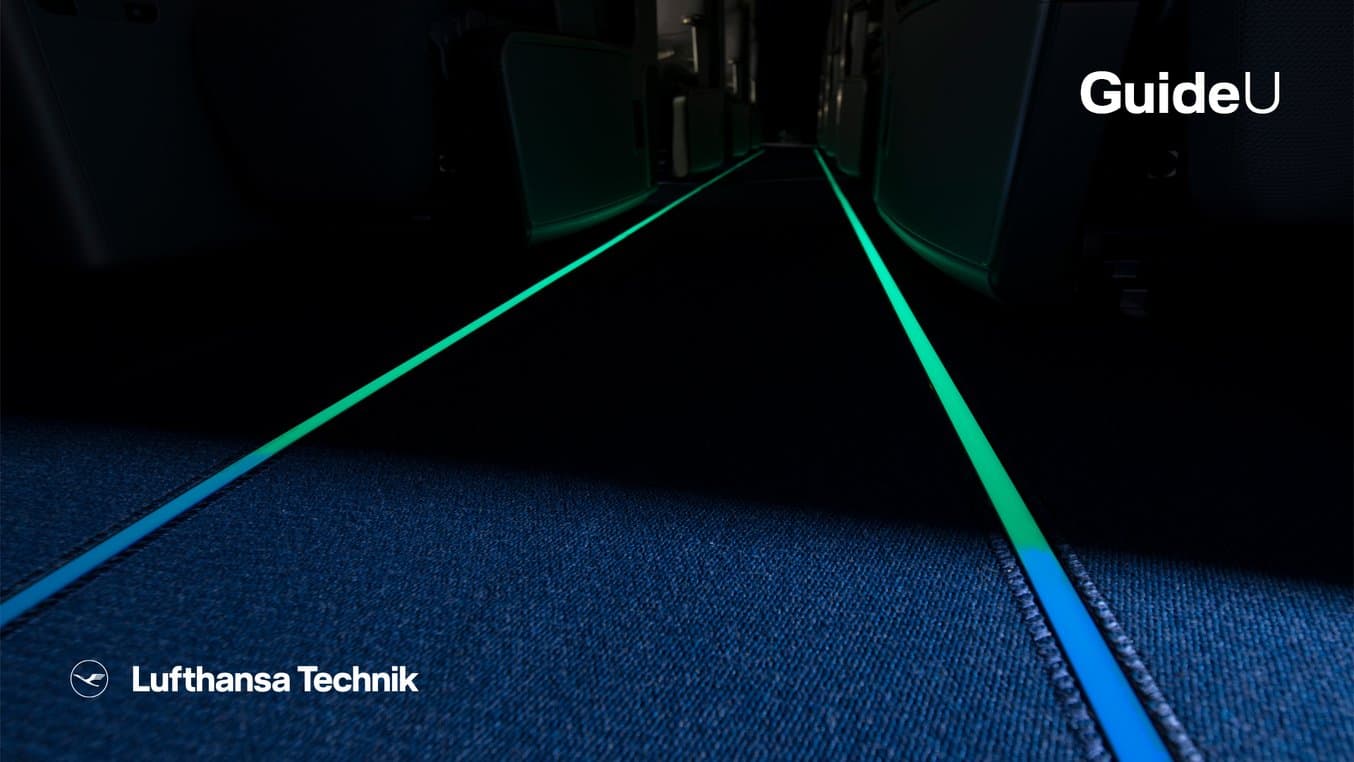
Lufthansa Technik AG, a subsidiary of the Lufthansa Group, not only takes care of maintenance and repairs in the aviation sector, but also sells aviation products and aircraft components to large original equipment manufacturers (OEMs), such as Airbus and Boeing.
One of these product lines is escape-route markings for the interior of aircraft, which are produced in an innovative way with the help of 3D printed manufacturing aids.
In an interview with Ulrich Zarth, project engineer at Lufthansa Technik AG, we talked about how the company uses these 3D printed tools as consumables in production and how 3D printing makes process optimization more flexible.
Marquage de sorties de secours pour Airbus, Boeing & Co.
Lufthansa Technik AG, l'un des plus grands fournisseurs mondiaux de services de maintenance, de réparation et de révision dans le domaine de l'aviation, a déjà largement recours à la fabrication additive. Depuis 2018, une division interdépartementale de l'entreprise est chargée de la recherche et du développement de divers procédés d'impression 3D pour la fabrication de produits aéronautiques, ainsi que d'outils et de dispositifs pour leur production. Les principaux clients de ces composants d'avions sont principalement les grands équipementiers, tels qu'Airbus et Boeing.
L'un des produits imprimés en 3D de Lufthansa Technik est le marquage des sorties de secours Guide U pour l'intérieur des avions. Ces marquages au sol innovants sont photoluminescents : ils sont composés de pigments de couleur auto-éclairants qui sont rechargés par l’éclairage normal de la cabine et brillent dans l’obscurité en cas de coupure d’électricité. Les bandes auto-éclairantes situées le long des rangées de sièges sur le plancher d'un avion indiquent le chemin vers les sorties de secours en cas d'urgence.
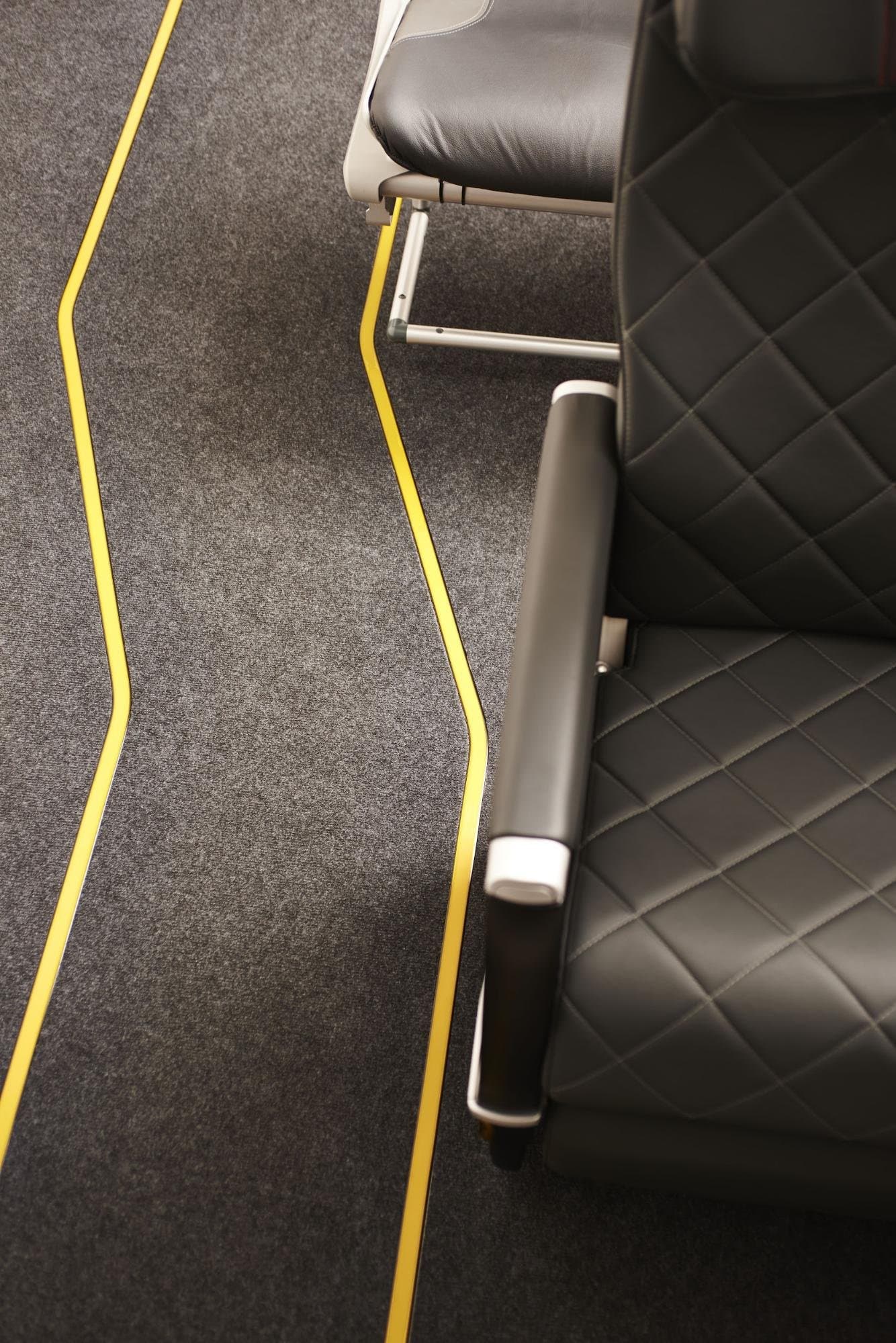
Bandes lumineuses Guide U installées comme marquage des sorties de secours dans un avion.
Ce système breveté est produit en interne depuis novembre 2021 à Hambourg, en Allemagne.
Des buses imprimées en 3D comme consommables en production
Pour produire ces marquages de sorties de secours, l'équipe de Lufthansa Technik a utilisé des aides à la fabrication imprimées en 3D. Après que différentes méthodes ont été testées, l'impression 3D stéréolithographique (SLA) a été choisie pour fabriquer une buse utilisée comme composant d'outillage pour le processus de fabrication.
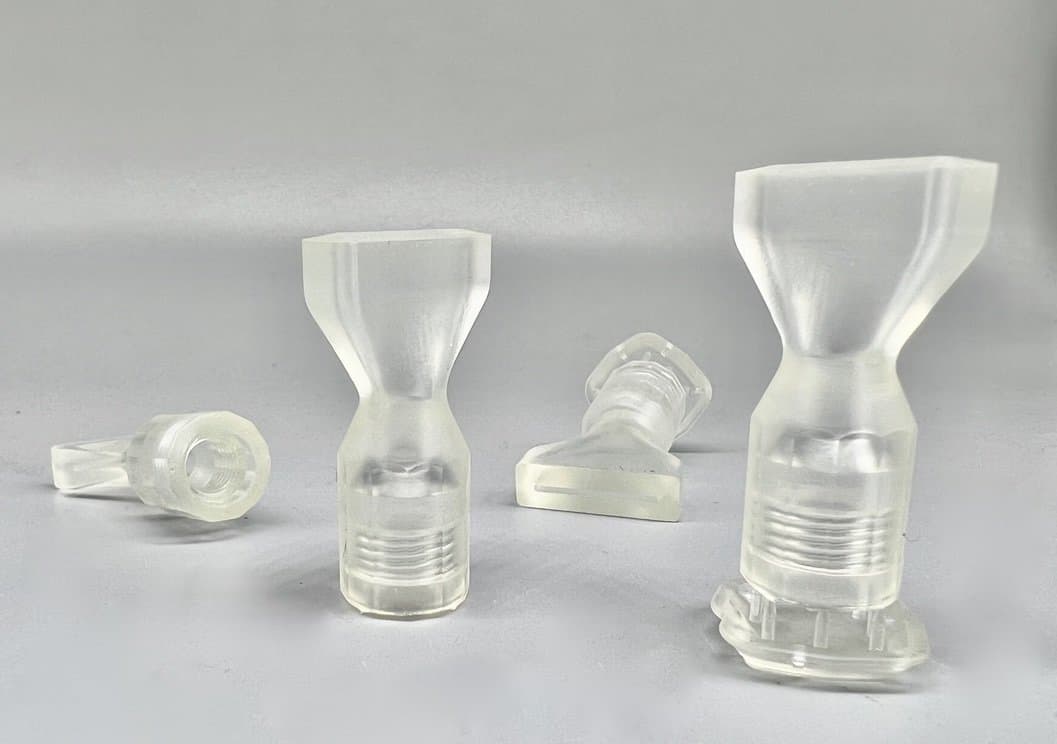
La buse en Clear Resin, avec le filet intégré (à droite, on peut voir les structures de support).
Une exigence particulière était que cette buse soit traitée comme un consommable. La buse imprimée en 3D est une alternative rentable à une aide à la fabrication qui serait autrement produite avec un processus conventionnel comme l'usinage ou le moulage par injection. La buse est fabriquée par impression 3D SLA à l'aide de Clear Resin, qui répond aux exigences de qualité et de précision nécessaires pour l'outil. Cette solution permet à Lufthansa Technik de remplacer quotidiennement la buse et ainsi d’optimiser le processus de production.
« Si vous voulez obtenir rapidement des formes précises, je vous recommande vivement l’impression 3D, surtout si vous travaillez dans le secteur du plastique. »
Ulrich Zarth
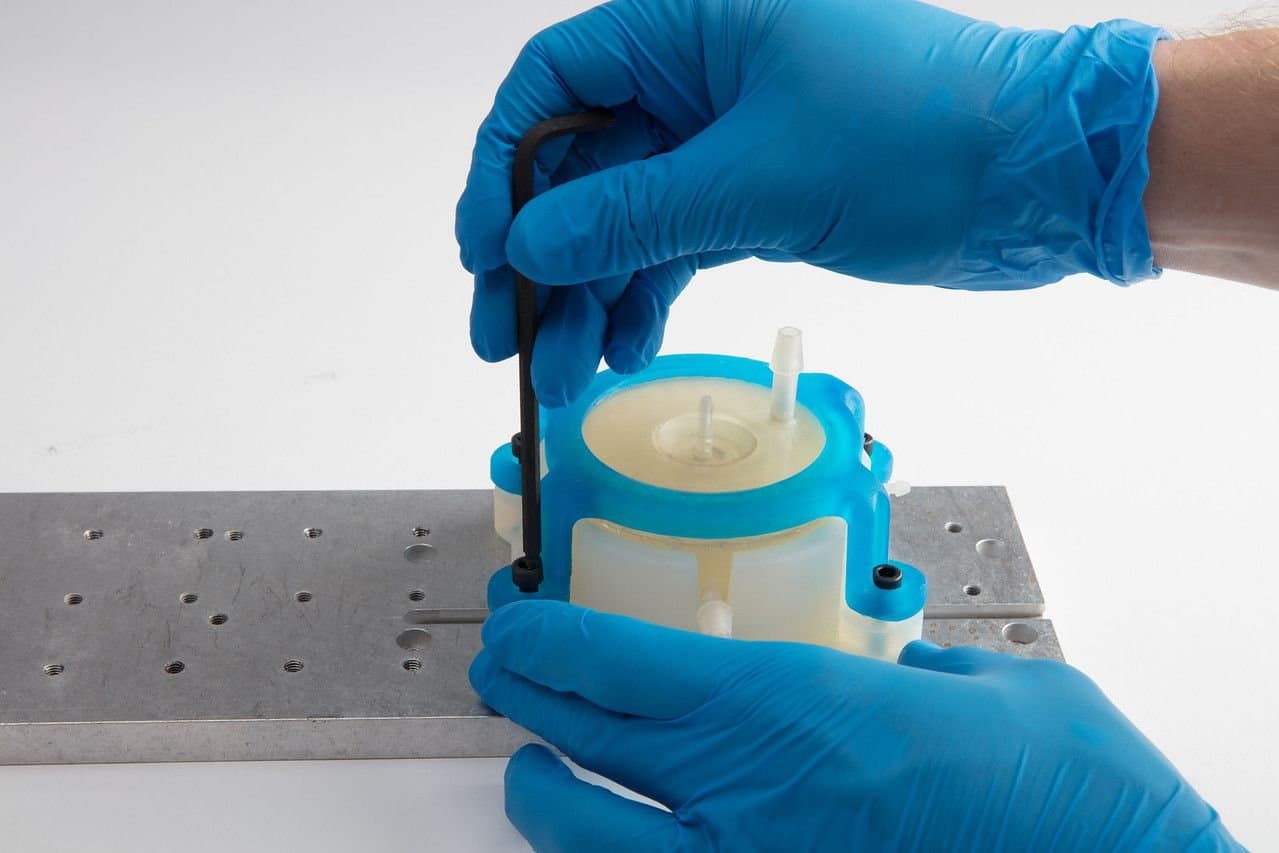
Conception de gabarits et de fixations par impression 3D
Téléchargez notre livre blanc pour en savoir plus sur les meilleures pratiques pour la conception de gabarits et de fixations et sur les applications des gabarits et des fixations dans la fabrication.
Plus de précision et de flexibilité grâce à l'impression 3D SLA
Cet outil de production a été imprimé sur la Form 3L en collaboration avec myprintoo, partenaire de Formlabs. La grande surface de la plateforme de fabrication de la Form 3L a permis d’imprimer 72 buses en une seule fois. En comparaison, la Form 3+, la version plus petite de l'imprimante 3D SLA de Formlabs, serait capable d'imprimer 25 buses en une fois. Le Form 3L a permis de gagner beaucoup de temps dans la production de la pièce sans sacrifier la précision d'impression de la buse.
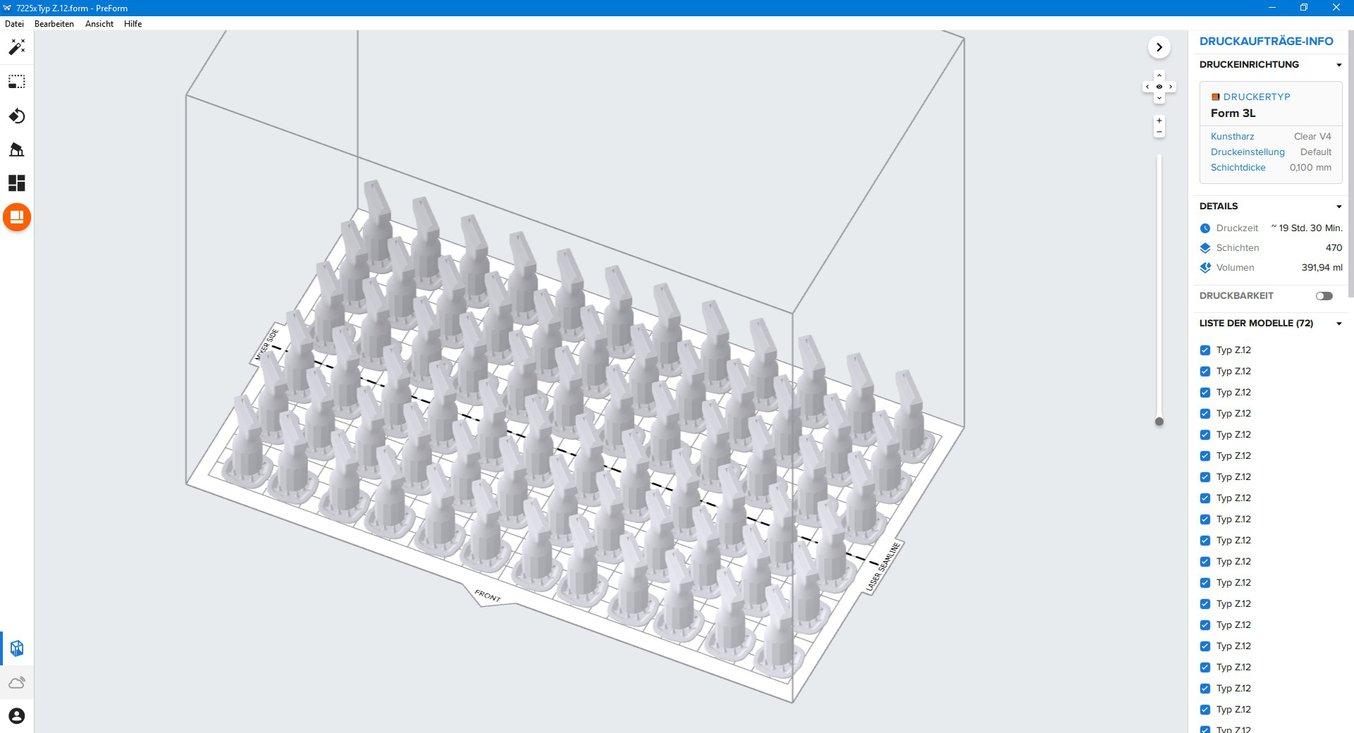
72 buses produites sur la Form 3L avec un temps d'impression de 19,5 heures.
« Nous avons suivi la fabrication de l'outil pendant le processus d'itération afin d'apporter d'éventuels ajustements à l'épaisseur de couche, à l'orientation de l'impression, voire à une partie de la géométrie du composant, et ainsi garantir la fiabilité du processus et la qualité de l'impression », explique Jonathan Wulf de myprintoo.
Après l'impression, les buses peuvent être directement utilisées dans le processus de production des bandes lumineuses Guide U sans aucune autre étape que le post-traitement standard.
Plusieurs matériaux Formlabs ont été testés avant que le choix ne se porte sur Clear Resin. Non seulement cette résine offre la stabilité et la qualité de surface requises, mais elle permet également à Lufthansa Technik de constamment optimiser son processus de production.
En étroite collaboration avec le partenaire de Formlabs myprintoo, Zarth, ingénieur de projet responsable, a itéré cinq versions de la buse. En raison de la rapidité et de la fiabilité du service et de la livraison des pièces imprimées en 3D par myprintoo, le design a pu être légèrement retouché pour optimiser le processus.
« Nous sommes très contents de cette collaboration. Par exemple, nous avons remarqué un après-midi que quelque chose ne fonctionnait pas comme prévu dans le processus. Le soir même, le modèle de la buse était corrigé, et nous avons pu imprimer de nouvelles buses dès le lendemain. »
Ulrich Zarth
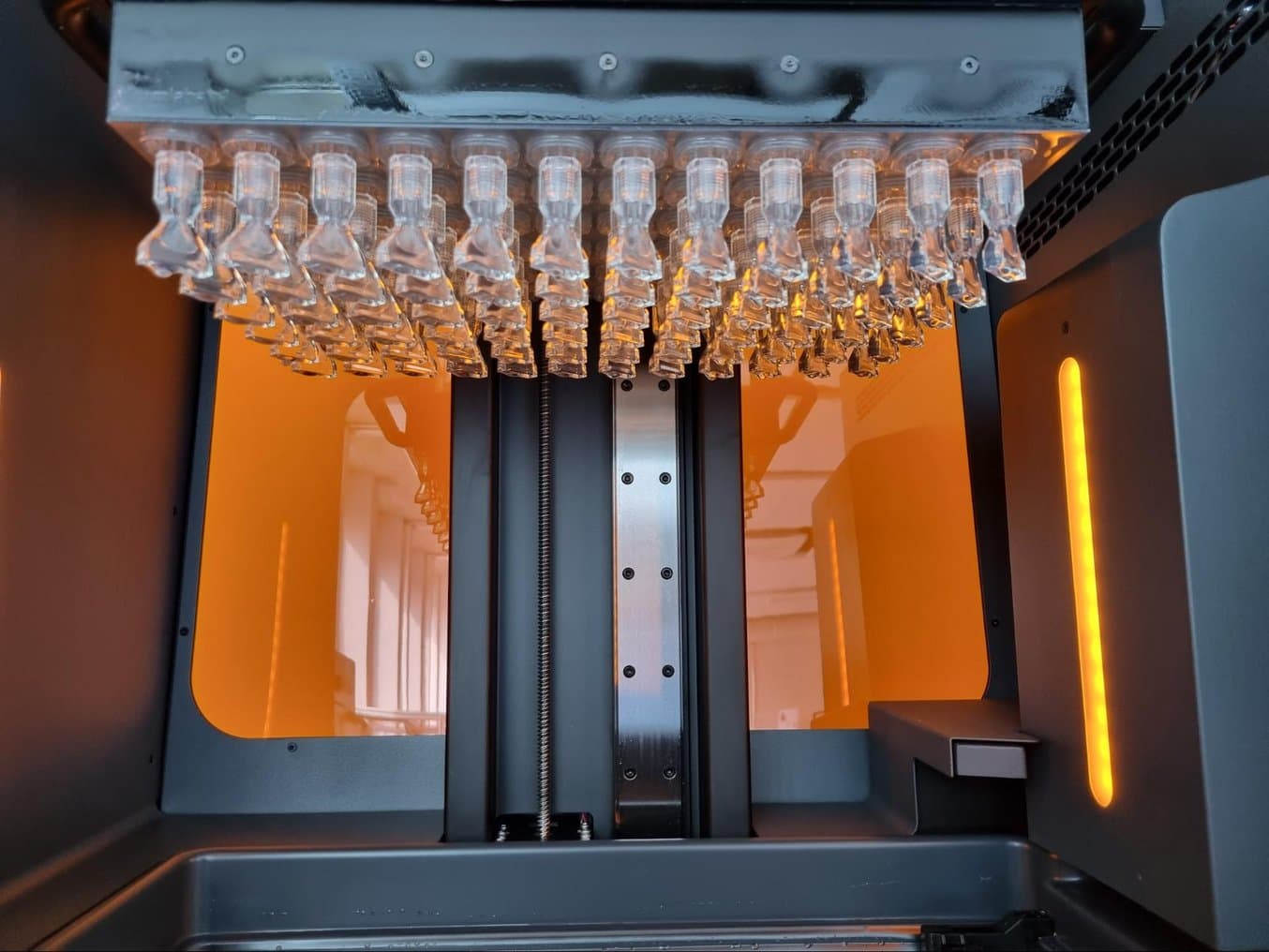
Buses de Lufthansa Technik imprimées sur la Form 3L avec Clear Resin.
Optimisation flexible des processus de production grâce à l'impression 3D
Ulrich Zarth et son équipe ont gagné énormément de temps et d’argent en imprimant en 3D et en interne ce petit composant. Ils ont également évité d’imposer des quantités minimales de commande élevées et sont restés beaucoup plus flexibles dans l’optimisation de leur processus par rapport aux méthodes de fabrication traditionnelles.
« Théoriquement, nous aurions aussi pu mouler nos pièces par injection. Mais nous n’aurions jamais eu autant de flexibilité dans la forme et l’ajustement de la buse. C’est pour moi l’un des grands avantages de l’impression 3D », a expliqué M. Zarth.
En outre, par rapport à l'impression 3D FDM, l'impression 3D SLA s'est avérée être une solution de haute qualité pour cette application.
Les outils de production imprimés en 3D comme alternative aux méthodes traditionnelles
De nombreuses entreprises fabriquent leurs outils en plastique ou en métal en utilisant des techniques traditionnelles telles que le moulage par injection ou l'usinage CNC. Ces techniques exigent de passer par des sous-traitants externes et s'accompagnent donc de longs délais, de coûts excessifs et de quantités minimales élevées.
En fonction de l'application et des exigences, ces processus peuvent être remplacés par des outils imprimés en 3D. La buse utilisée dans la production des marquages de sorties de secours Guide U par Lufthansa Technik illustre bien que l'impression 3D SLA permet une alternative plus économique et plus flexible.
« Contrairement à nous, beaucoup de gens ne sont pas encore au courant des avantages que représente l'utilisation d'outils imprimés en 3D dans la production. »
Ulrich Zarth
Outre les aides à la fabrication, l'impression 3D offre un large choix d'alternatives aux processus traditionnels allant du prototypage rapide à l'outillage rapide.