Des prothèses avancées rendues accessible : comment PSYONIC a développé une main bionique grâce à la fabrication additive
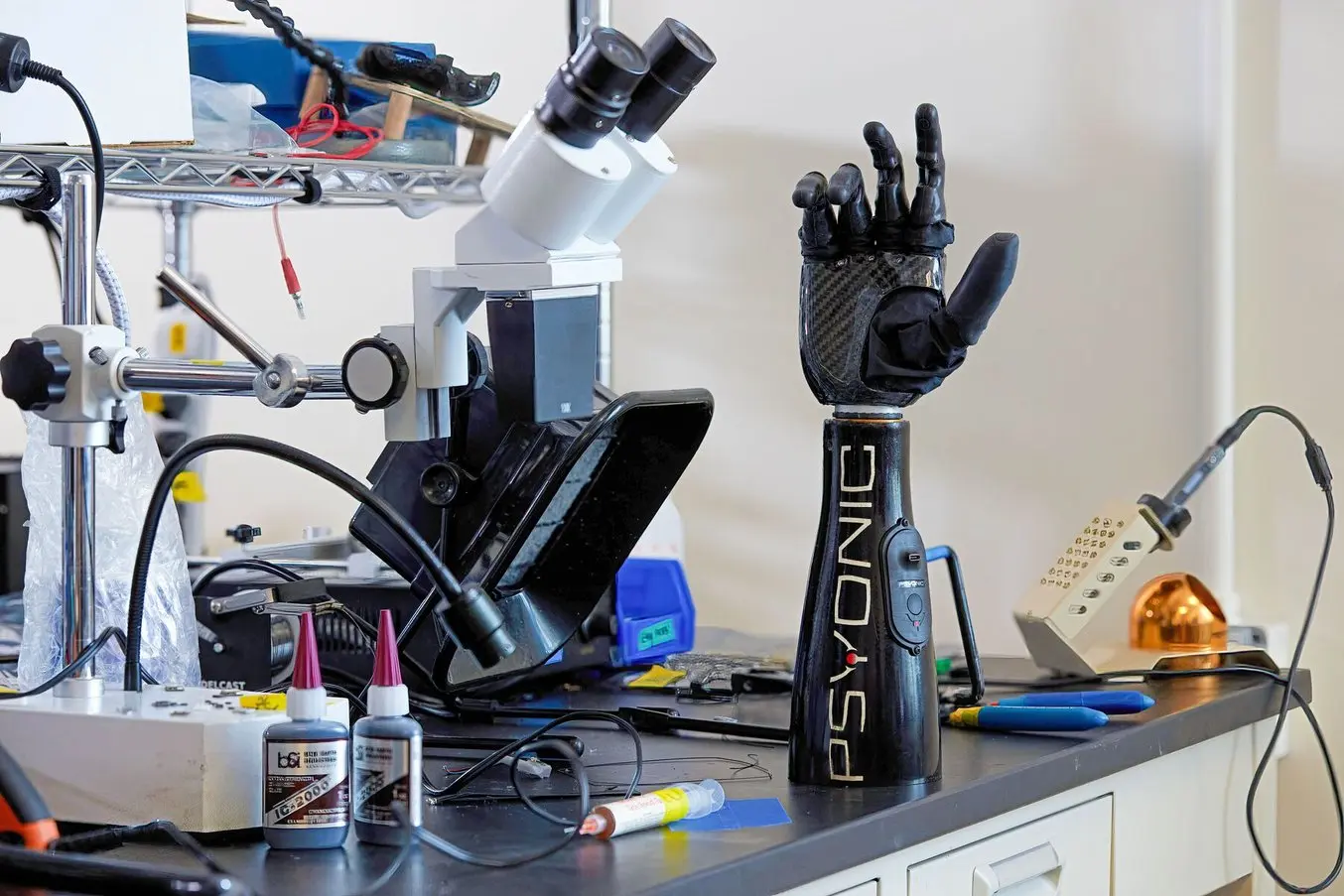
Dans le monde, plus de 50 millions de personnes doivent se faire amputer d'un membre1 en raison de causes traumatiques. Pour les patients se remettant d'une amputation, accepter de porter une prothèse n'est pas toujours facile. La plupart d'entre eux veulent retrouver une vie normale : conduire une voiture, s'entraîner à la salle de sport, faire le ménage dans la maison. Mais la plupart des prothèses traditionnelles sont rudimentaires, coûteuses et fragiles. Aujourd'hui, environ 10 % des patients nécessitant un bras prothétique avancé peuvent se l'offrir.
PSYONIC, créateur de l'Ability Hand, est une entreprise qui tente de révolutionner le marché. Conçue et fabriquée en interne à l'aide de méthodes de fabrication hybrides (notamment l'impression 3D, le moulage par injection, le moulage de silicone et les machines à commande numérique), l'Ability Hand permet aux patients de retrouver leur vie et leur mobilité.
Qu'est-ce que PSYONIC a réussi à accomplir avec les imprimantes 3D SLA de Formlabs ?
- Créer de toutes pièces une prothèse de membre supérieur homologuée par la FDA, couverte par Medicare et révolutionnant le secteur.
- Recueillir les commentaires clients et réaliser rapidement des prototypes en interne pour améliorer la conception et la fonctionnalité de l'Ability Hand.
- Déployer une véritable méthode de production hybride pour vendre l'Ability Hand à un prix abordable.
- Aider les patients à retrouver une vie normale, y compris le sergent Garrett Anderson.
- Baisser les prix et rendre la prothèse accessible à plus de patients (de 10 % à 75 %)
- Utiliser de nouveaux matériaux d'impression 3D durables et résistants aux chocs pour créer des pièces finales de longue durée.
Dans cet article, nous nous entretenons avec le PDG Aadeel Akhtar, PhD, et l'ingénieur mécanicien en chef James Austin pour savoir comment ils ont fabriqué l'Ability Hand, pourquoi ce marché est si mal exploité et comment l'impression 3D a joué un rôle essentiel dans leur stratégie de commercialisation. Nous rencontrerons également le sergent Garrett Anderson, l'un des premiers utilisateurs de l'Ability Hand.
Le besoin d'une meilleure solution pour les membres supérieurs
En 2005, alors qu'il était déployé en Irak, le véhicule du sergent Garrett Anderson a été touché par une bombe au bord de la route. On lui a diagnostiqué par la suite des lésions cérébrales traumatiques légères et une mâchoire cassée. M. Anderson a dû être amputé du bras droit au-dessous du coude. De retour chez lui, une grande partie de sa vie a repris son cours normal, mais il avait toujours certaines difficultés. Il s'est inscrit à l'Illinois State University, a obtenu un diplôme de premier cycle et une maîtrise, et a eu deux enfants.
Les membres artificiels actuellement proposés ne sont pas toujours très avancés : des crochets sont parfois encore utilisés pour certaines fonctionnalités de base. Malgré les progrès rapides réalisés dans d'autres domaines médicaux importants au fil des ans, la fabrication de prothèses restent à la traîne.
M. Anderson a fini par entrer en contact avec un jeune doctorant nommé Aadeel Akhtar. Comme M. Anderson, M. Akhtar n'était pas satisfait de l'état actuel de la fabrication de prothèses. « C'est quelque chose que j'ai voulu faire toute ma vie, depuis l'âge de sept ans. Mes parents sont originaires du Pakistan. Je leur rendais visite quand j'ai rencontré pour la première fois quelqu'un avec une différence de membre. Elle avait mon âge, il lui manquait la jambe droite et elle utilisait une branche d'arbre comme béquille. C'est ce qui m'a donné envie de me lancer dans ce domaine, de fabriquer les dispositifs bioniques les plus avancés au monde, et de les rendre accessibles à tous. »
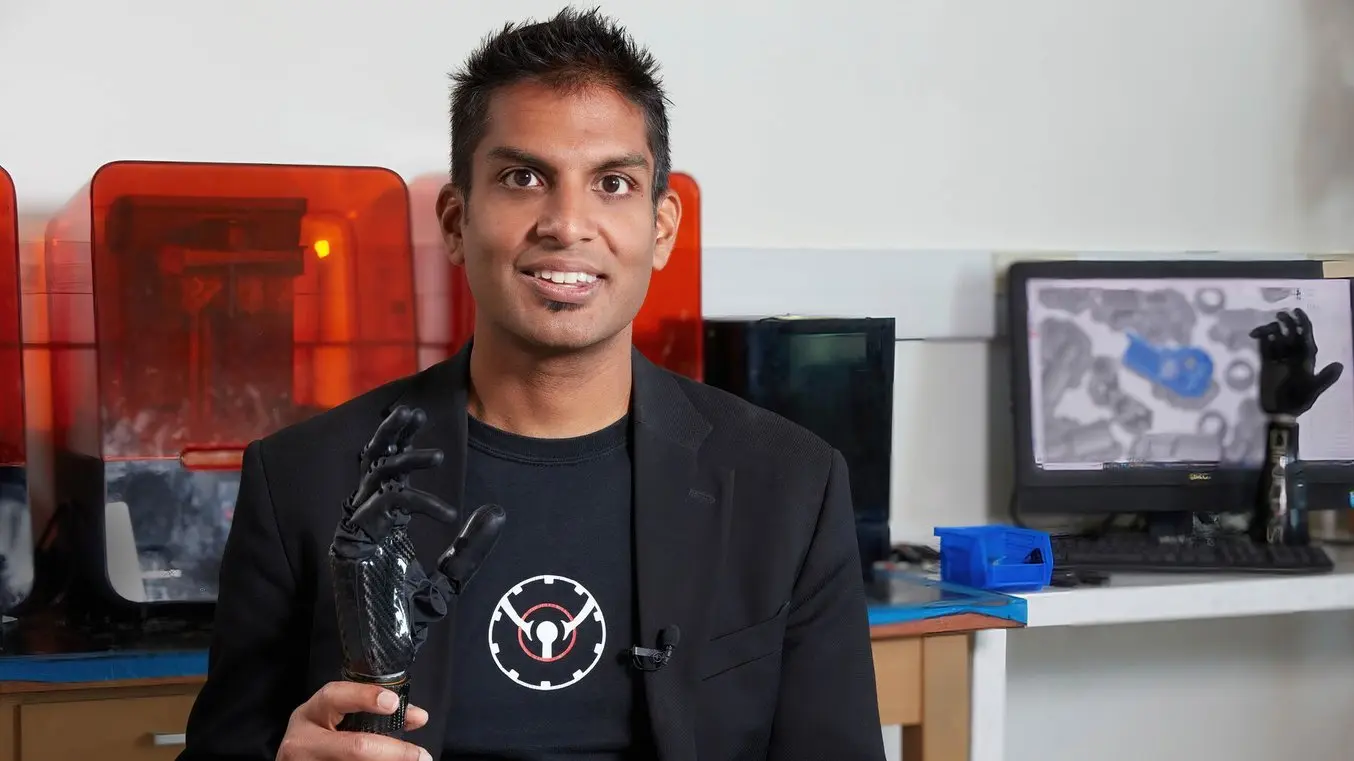
Le PDG Aadeel Akhtar, PhD, tenant la version la plus récente de l'Ability Hand.
Mais la mise sur le marché d'une nouvelle prothèse révolutionnaire n'a pas été une tâche facile. « Au cours des sept dernières années, nous avons testé neuf prototypes différents de l'Ability Hand, qui est maintenant disponible dans tout le pays, enregistrée auprès de la FDA et couverte par Medicare », a déclaré M. Akhtar.
À quoi ressemble la fabrication hybride moderne
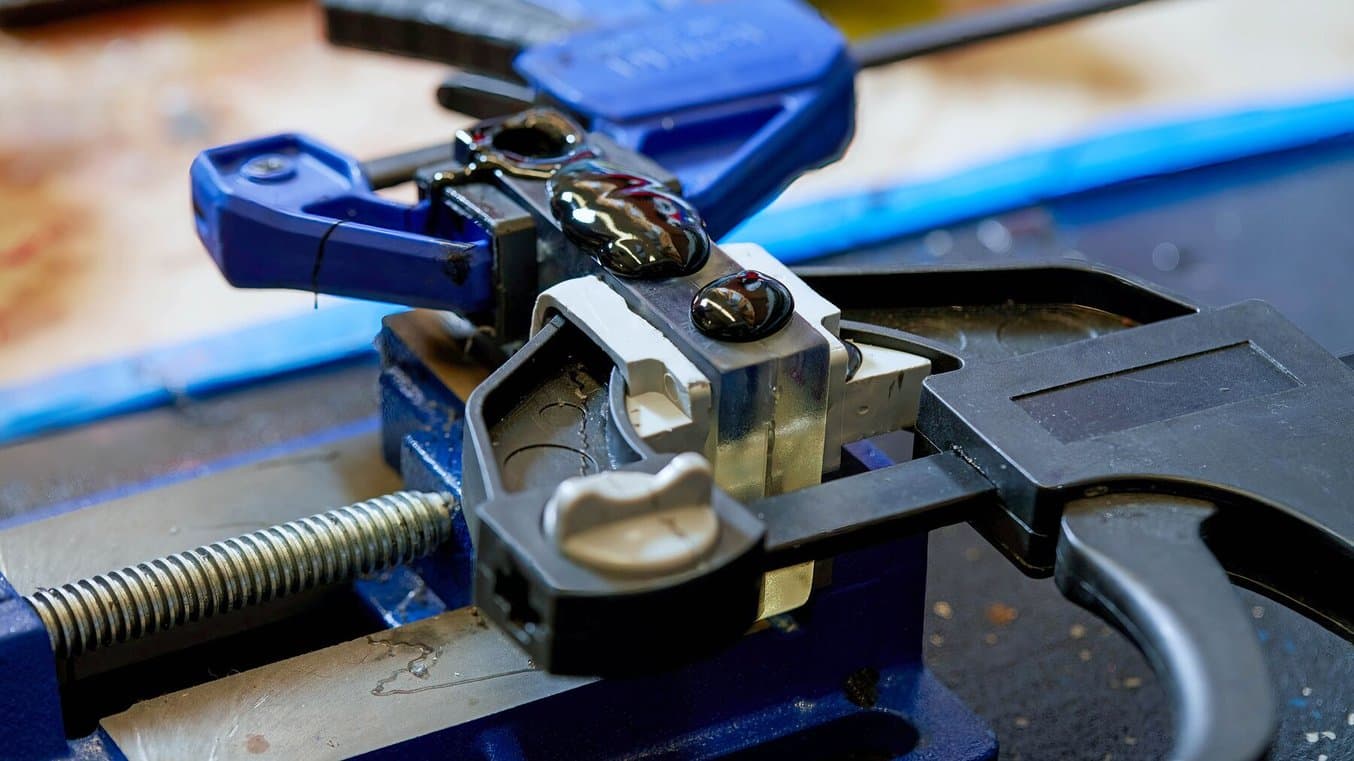
De plus en plus, les petites et grandes entreprises se tournent vers l'impression 3D en interne pour réaliser des prototypes et mettre de nouveaux produits sur le marché. Dans les secteurs où les coûts initiaux de R&D sont élevés, comme par exemple la fabrication de dispositifs médicaux, l'impression 3D est devenue un outil essentiel pour les équipes d'ingénierie.
Une prothèse nouvelle génération doit être fabriquée rapidement pour intégrer les commentaires utilisateurs, résistante et durable pour ne pas se briser au cours des tâches quotidiennes, légère pour ne pas fatiguer l'utilisateur et ne pas lui causer de crampes au bras, et fournir un véritable retour sensoriel. Ce n'est pas une mince affaire !
Qu'est-ce qui a changé dans la fabrication des dispositifs pour permettre à une petite entreprise comme PSYONIC de révolutionner le marché des prothèses traditionnelles ?
- L'impression 3D a été très utilisée en prototypage et en développement de produits pendant des décennies. Aujourd'hui, cette technologie a beaucoup évolué, notamment avec le frittage sélectif par laser (SLS) et la stéréolithographie (SLA), et commence à être largement utilisée dans la fabrication.
- Elle permet d'imprimer des pièces finales de haute qualité, de produire de gros volumes de pièces, et supporte une grande variété de matériaux. Tous ces éléments font de l'impression 3D une technologie adaptée pour la fabrication de nouveaux dispositifs médicaux.
- En plus de la fabrication directe de pièces finales, l'impression 3D offre des avantages indéniables en « production hybride ». Elle joue le rôle d'intermédiaire par rapport aux processus traditionnels, notamment pour la fabrication de moules, d'outillage, de modèles, de fixations et de gabarits d'assemblage. C'est ce qu'on appelle l'outillage rapide et les aides à la fabrication.
M. Austin nous a dit que « le mélange des différentes méthodes de fabrication est extrêmement important pour les startups en général, mais surtout pour PSYONIC. Vu la taille de notre compagnie, nous n'aurions jamais pu concurrencer d'autres entreprises de prothèses si nous avions dû nous en tenir à une fabrication purement traditionnelle. Les coûts d'autres techniques comme l'usinage CNC et le moulage par injection, surtout pour la création de prototypes avec de multiples itérations, auraient été beaucoup trop élevés pour nous. Mais depuis l'avènement des différents types d'impression 3D, nous avons pu réaliser rapidement des prototypes, modifier nos itérations et produire de petites séries de pièces à faible coût. Grâce notamment aux imprimantes 3D de Formlabs, l'impression 3D joue désormais un rôle central dans notre processus de développement. »
Voyons un peu comment PSYONIC utilise l'impression 3D en interne pour fabriquer l'Ability Hand.
Mouler en interne des pièces en fibres de carbone
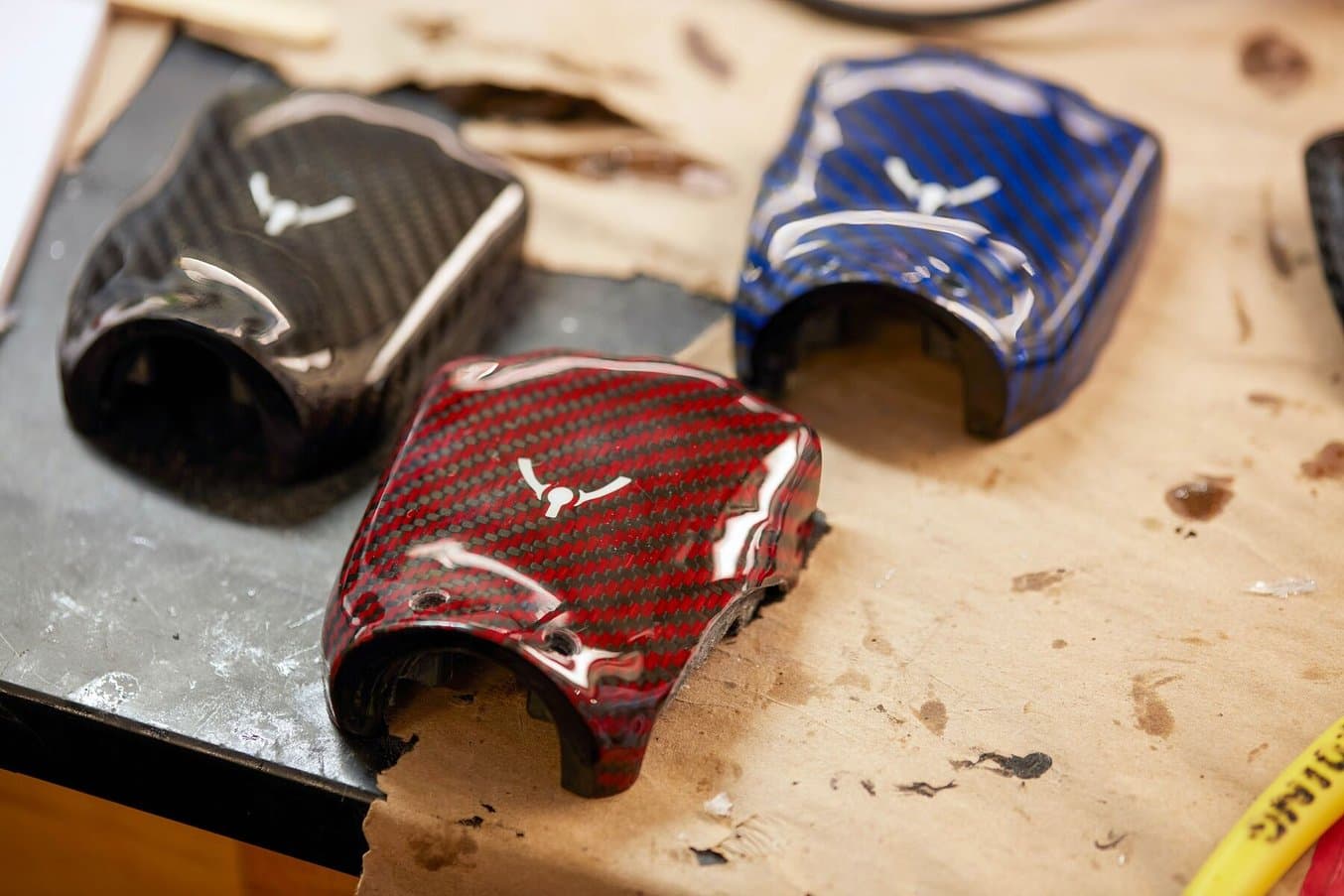
Le moulage en interne de fibre de carbone a permis à PSYONIC d'améliorer le design de l'Ability Hand.
La fibre de carbone est un matériau puissant pour la fabrication, car elle augmente la durabilité et la rigidité globales de l'Ability Hand tout en réduisant son poids. Cependant, les moules traditionnels sont coûteux, ce qui ne permet pas d'itérer et de créer le bon nombre de moules pour la production de petites séries. Mais aujourd'hui, les entreprises n'ont pas à choisir entre la fabrication additive et les machines CNC traditionnelles : elles peuvent simplement faire les deux.
M. Austin nous a expliqué que « dans les premières itérations, l'impression 3D SLA était en fait assez importante. Nous n'avions pas les ressources nécessaires pour produire des moules par usinage, par exemple. À la place, nous avons produit des moules avec High Temp Resin. Ce matériau est fragile mais résistant à la chaleur, ce qui nous a permis de presser les feuilles de fibre de carbone, de leur donner la forme que nous voulions, de les mettre dans un four à haute température pour les durcir, puis de les coller à la main. »
Les moules imprimés en 3D pour fabriquer des pièces en fibre de carbone peuvent réduire les coûts et les délais de production. Les ingénieurs peuvent imprimer directement le moule à bas coût et en quelques heures sans avoir à le sculpter à la main ou à utiliser un équipement CNC. Grâce à High Temp Resin et à Rigid 10K Resin, les entreprises de dispositifs médicaux en pleine croissance comme PSYONIC peuvent réaliser des formes de moules complexes avec des détails fins qui seraient difficiles à fabriquer avec des méthodes traditionnelles.
M. Austin a utilisé High Temp Resin pour créer plusieurs moules, testant ainsi sa conception à moindre coût. Il nous a affirmé que « si la forme ne nous plaisait pas, il suffisait de la modifier dans le logiciel CAO, de la renvoyer à l'imprimante 3D, d'imprimer une autre pièce en High Temp Resin, et nous étions déjà prêts à itérer. Pour la durabilité à long terme, nous avons fini par usiner les moules, mais pour ce premier prototypage et ces tests à court terme, High Temp Resin et les imprimantes Form 3 ont été d'une aide précieuse. » High Temp Resin présente une température de fléchissement sous charge (TFC) de 238 °C à 0,45 MPa et est capable de résister à la chaleur et à la pression d’un autoclave.
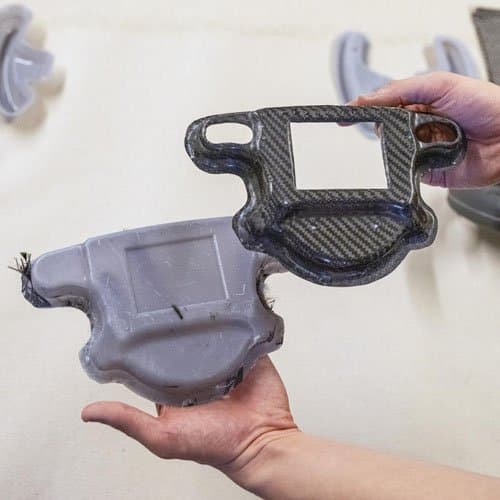
La fabrication de pièces en fibre de carbone avec des moules imprimés en 3D
Téléchargez ce livre blanc pour obtenir des instructions de conception de moules ainsi que des guides étape par étape concernant les méthodes de pré-imprégnation et de laminage manuel pour créer des pièces en fibre de carbone.
Rétro-ingénierie
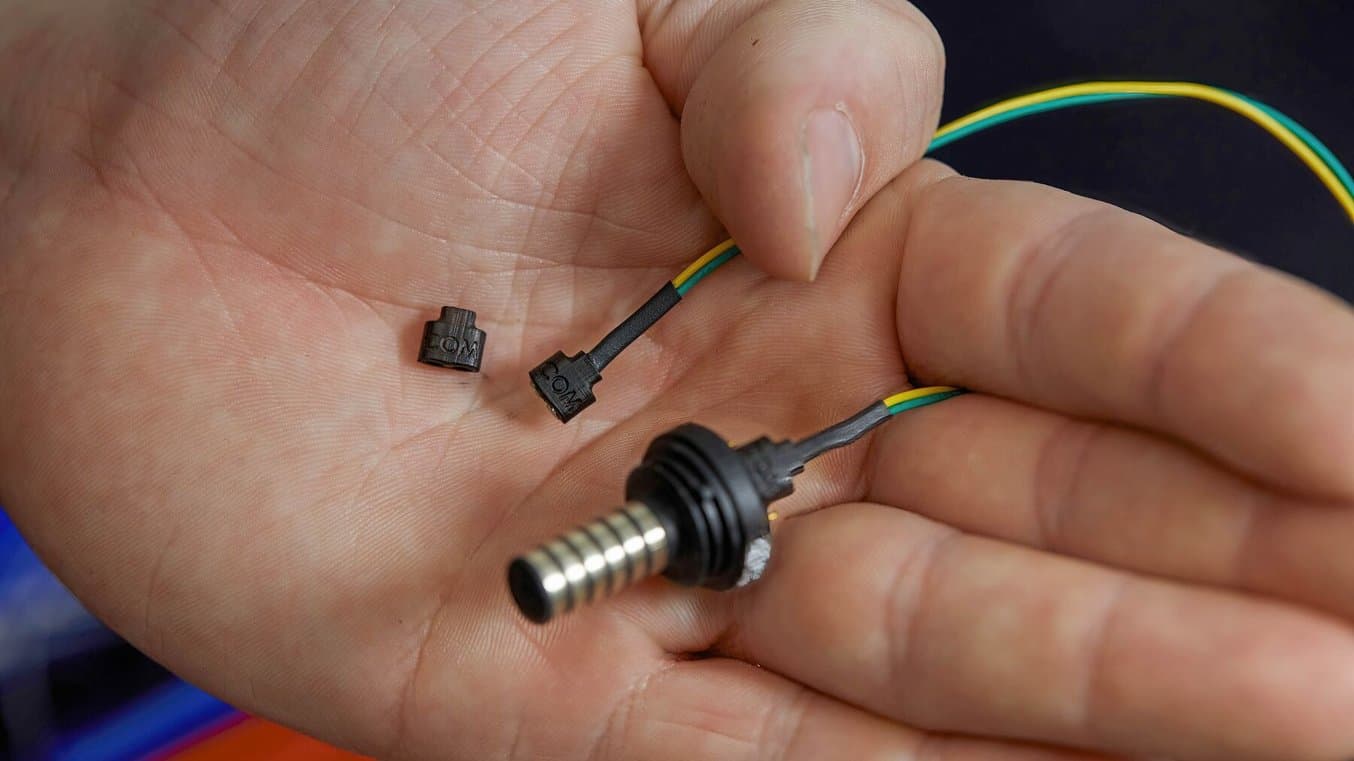
Pour aider à réduire les coûts, PSYONIC a rétroconçu de petits connecteurs.
La rétro-ingénierie est un bon moyen de créer des conceptions numériques à partir d'une pièce physique. Elle peut être un outil précieux pour le prototypage en ingénierie. Une équipe d'ingénieurs qualifiés utilisant une imprimante 3D peut effectuer une rétroconception rapide des pièces, ce qui réduit les retards de production.
Toute personne travaillant dans le domaine médical sait à quel point les pièces propriétaires peuvent être coûteuses, le remplacement d'un petit clip pouvant parfois coûter des centaines de dollars. Pour les petites entreprises telles que PSYONIC, le prix des pièces de rechange peut être prohibitif.
PSYONIC a pris les choses en main, se tournant une fois de plus vers ses imprimantes 3D internes pour accélérer le développement et réduire les coûts. M. Austin nous affirme : « il y a parfois des pièces dont nous avons besoin pour que nos produits soient compatibles avec les produits d'autres entreprises, et il est parfois possible des les acheter, mais, comme beaucoup de choses dans le secteur médicale, elles ont un coût exorbitant. Pour les pièces plus petites, nous avons la capacité d'effectuer assez facilement une rétroconception de la forme, puis de les produire simplement nous-mêmes en interne. »
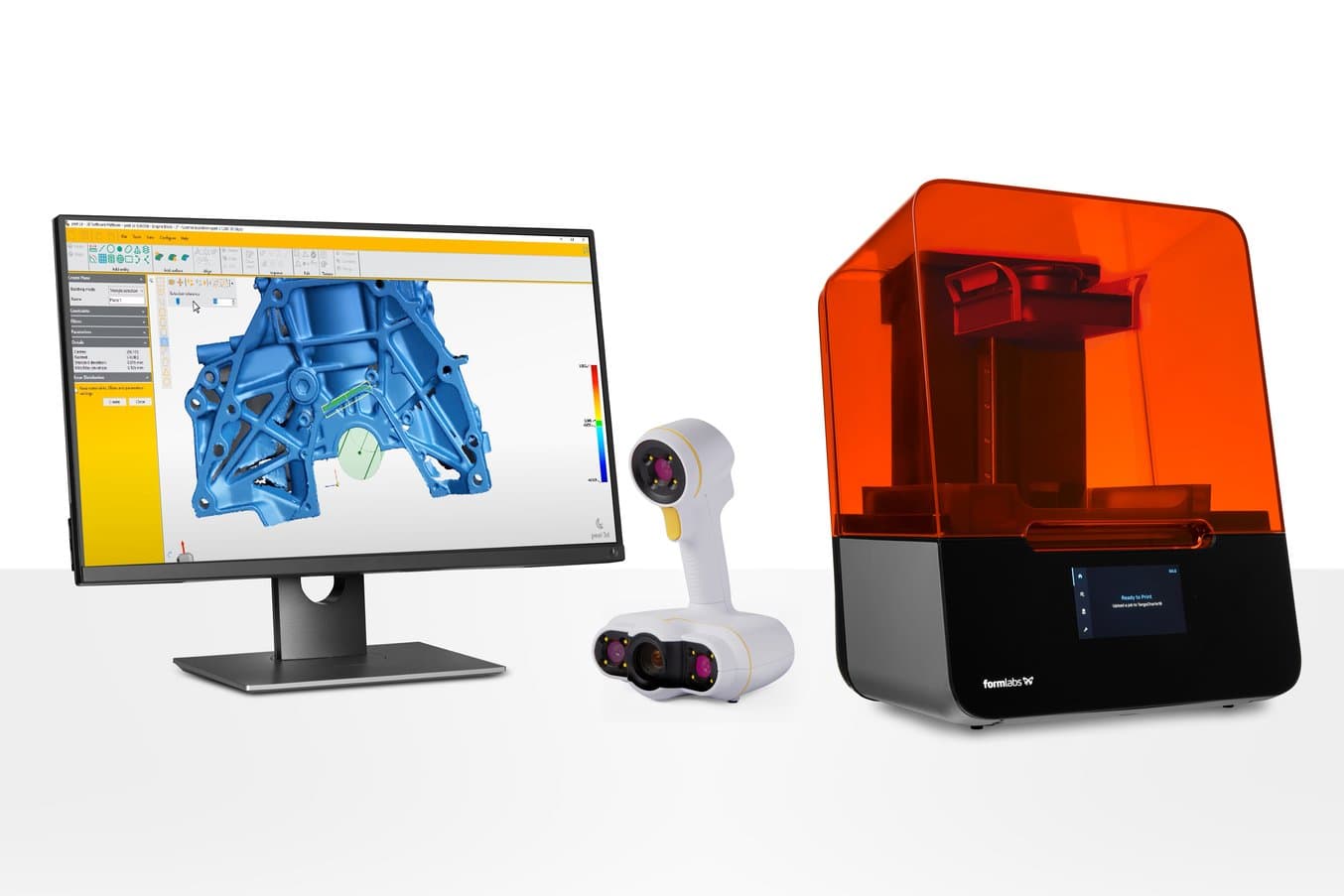
Numérisation et impression 3D pour la rétro-ingénierie et d’autres applications
Téléchargez ce livre blanc pour comprendre comment la numérisation et l'impression 3D fonctionnent en tandem pour la rétro-ingénierie. Le rapport présente un aperçu du marché actuel des scanners 3D.
Outillage rapide pour l'injection et le moulage de silicone
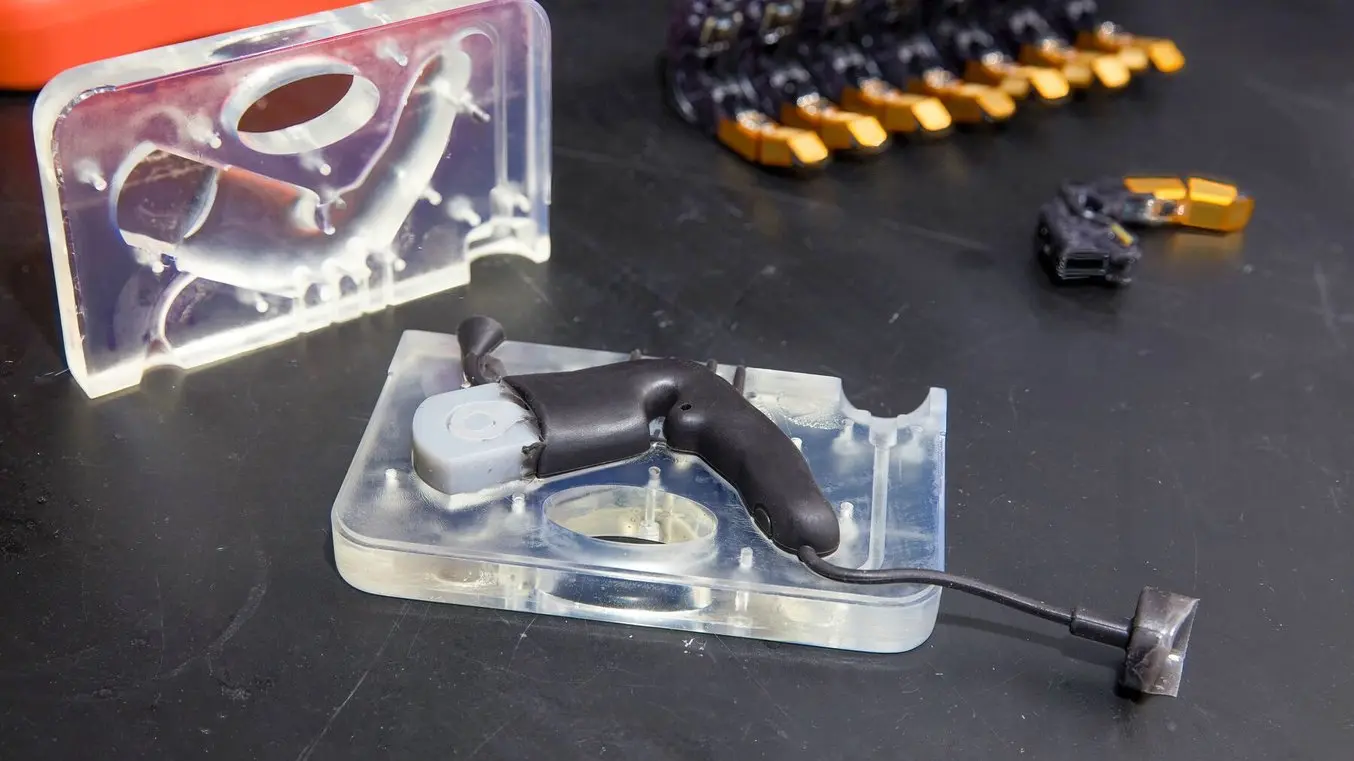
L'introduction du moulage par injection en petites séries dans le processus de développement des dispositifs médicaux peut être une aubaine pour de nombreuses équipes d'ingénieurs. Lorsque vous commencez à développer un nouveau produit, produire de petits lots de pièces finales avec de l'outillage rapide est un moyen efficace et abordable de passer du prototypage à la production de masse sans acheter d'outillages en dur coûteux. L'équipe de PSYONIC a commencé par imprimer en 3D toutes les pièces de l'Ability Hand, y compris les doigts, afin de réduire les coûts. Ils ont rapidement constaté qu'il était nécessaire de mouler des doigts plus robustes, et ont décidé d'utiliser des moules imprimés en 3D au lieu de mouler directement les doigts.
M. Akhtar nous a parlé de cette transition en disant que « l'un de nos plus grands défis a été de savoir comment faire pour que cette main reste peu coûteuse à fabriquer, mais plus durable que tout ce qui existe sur le marché. Quand nous avons commencé à fabriquer ces mains, nous imprimions l'ensemble en 3D, ce qui était très rentable. Mais après avoir discuté avec des centaines de patients et de cliniciens, nous avons remarqué que beaucoup se plaignaient de la fragilité de leur main bionique à 50 000 $. Ils heurtaient accidentellement le coin d'une table et, comme les doigts étaient fabriqués à partir de composants rigides imprimés en 3D, ils se brisaient au niveau des articulations. Les doigts actuels sont flexibles : en cas de choc, ils se plient et reviennent à leur position initiale. C'est ce genre de fonctionnalité que nous voulions intégrer à nos prothèses pour les rendre plus durables. »
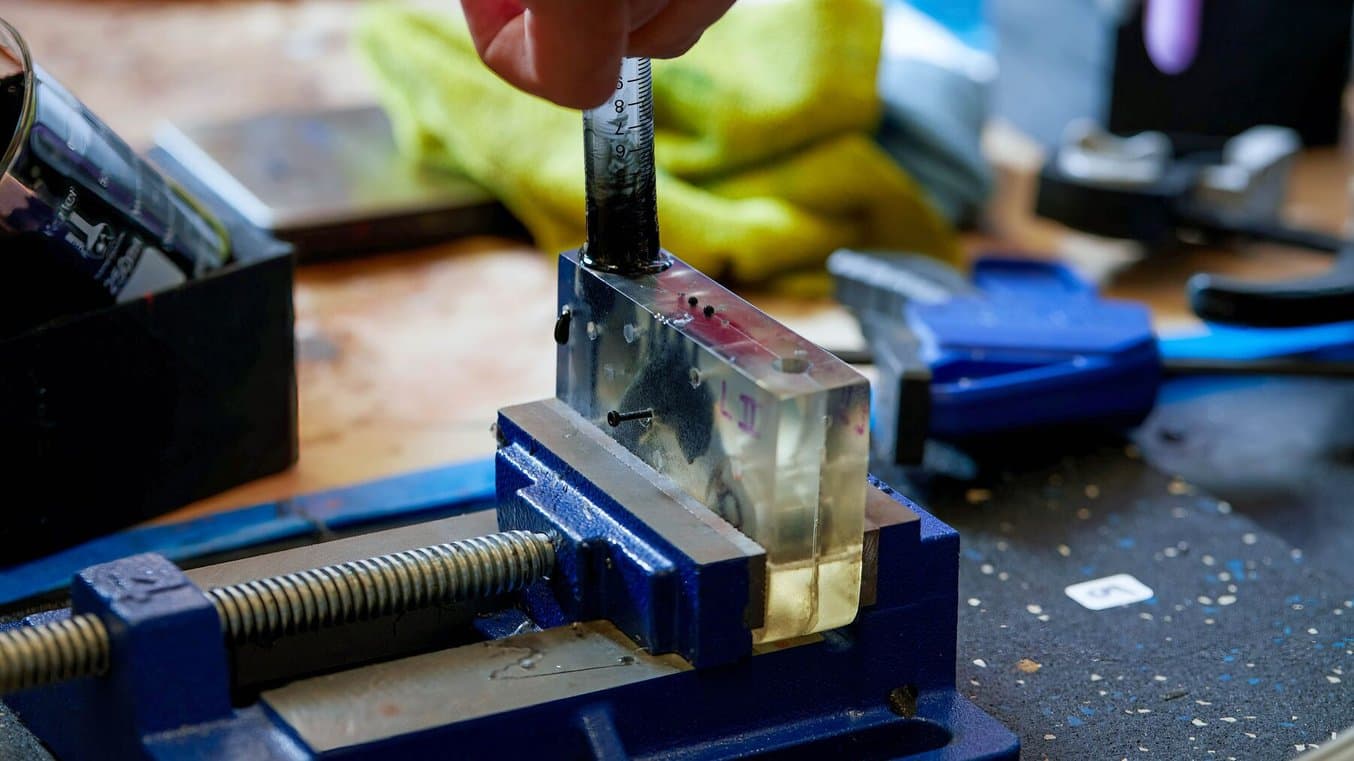
L'équipe a commencé par utiliser des imprimantes 3D de dépôt de fil fondu (FDM) pour créer ses moules. Les imprimantes FDM offrent des impressions rapides et bon marché, mais elles ne sont pas très pratiques en cas d'urgence. Les moules doivent être très lisses et imprimés en haute résolution, ce qui rend la technologie SLA plus adaptée. M. Austin nous a confié : « nous moulions déjà nos doigts auparavant, mais les moules étaient imprimés par FDM. » Ils présentaient un certain nombre de problèmes pour l'injection, principalement parce que leur finition de surface n'était pas bonne. Nous obtenions des stries, qui sont typiques des objets imprimés par FDM, car les pièces sont réalisées couche par couche. Par conséquent, toutes nos pièces moulées se retrouvaient avec d'étranges textures striées sur le dessus. Nous avons ensuite commencé à utiliser Clear Resin, qui permet d'obtenir une finition de surface beaucoup plus lisse en raison de sa résolution plus élevée. Nous produisons nos moules en prenant la forme négative du doigt ou du pouce, en la soustrayant d'un bloc, et en ajoutant des canaux et des entrées pour que le silicone soit injecté dans les deux parties. Une fois ce moule conçu et imprimé sur une imprimante 3D, nous y plaçons un os imprimé en 3D, qui forme l'ossature du doigt.
Nous fixons le moule en Clear Resin autour du doigt, mélangeons le silicone bi-composant, l'injectons à l'aide d'une seringue dans un trou du moule et remplissons le moule avec ce silicone bi-composant qui enveloppe entièrement le doigt. Une fois l'opération terminée, vous obtenez un beau doigt fraîchement moulé. Et nous avons pu utiliser ces moules de nombreuses fois. Nous pouvons les ouvrir et les réutiliser des dizaines de fois. Le seul problème avec les moules en Clear Resin est qu'ils s'usent avec le temps, principalement à cause de la manipulation. Mais même lorsque cela se produit, il suffit de les réimprimer, et dans les 24 heures, nous obtenons un autre moule prêt à être utilisé. »
M. Austin a choisi la résolution la plus élevée sur sa Form 3 (25 microns) pour créer à la fois ses pièces d'utilisation finale et ses moules. M. Austin nous a dit que « nous imprimons à la plus haute résolution possible pour tous nos matériaux. Pour les pièces en Tough 1500 Resin, c'est parce que les tolérances sont très strictes. Elles s'ajustent parfaitement à l'intérieur de la main et autour des composants qu'elles renferment. Toute variation pourrait entraîner un frottement excessif pendant le mouvement ou un désalignement des pièces correspondantes. Elles doivent donc être fabriquées avec la plus grande précision possible afin d'obtenir un ajustement et une fonctionnalité optimaux. Pour les moules, la raison pour laquelle nous les imprimons avec la résolution la plus élevée est que la finition de la surface doit être aussi lisse que possible. Puis nous les lavons très soigneusement avec la Form Wash pour obtenir une surface extrêmement lisse qui va être reproduite dans le silicone que nous y moulons ensuite. »
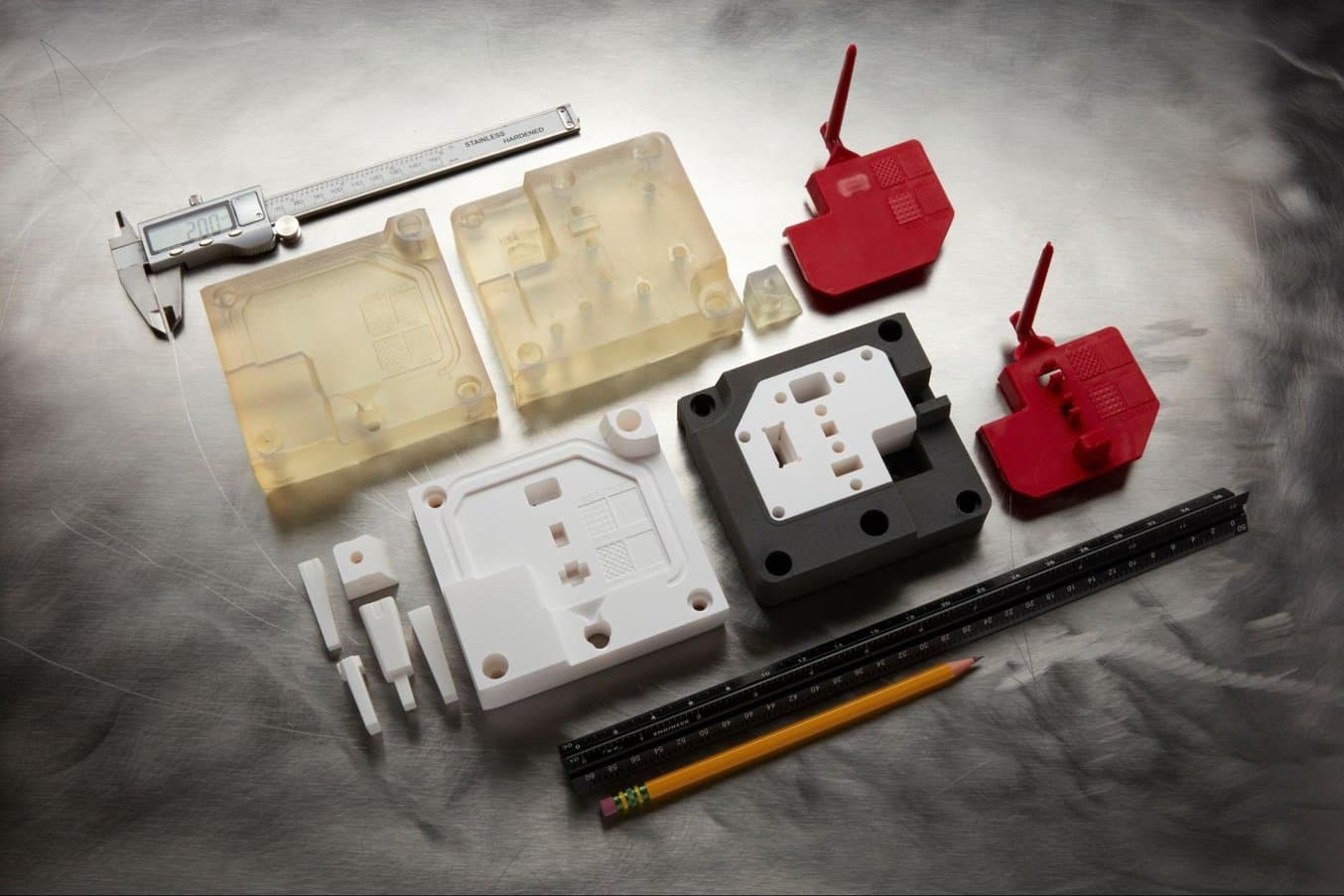
Guide de l'outillage rapide
Dans ce livre blanc, apprenez comment combiner l'outillage rapide imprimé en 3D avec des procédés de fabrication traditionnels tels que le moulage par injection, le formage sous vide ou la fonderie.
Prendre en compte les commentaires clients pour le prototypage rapide
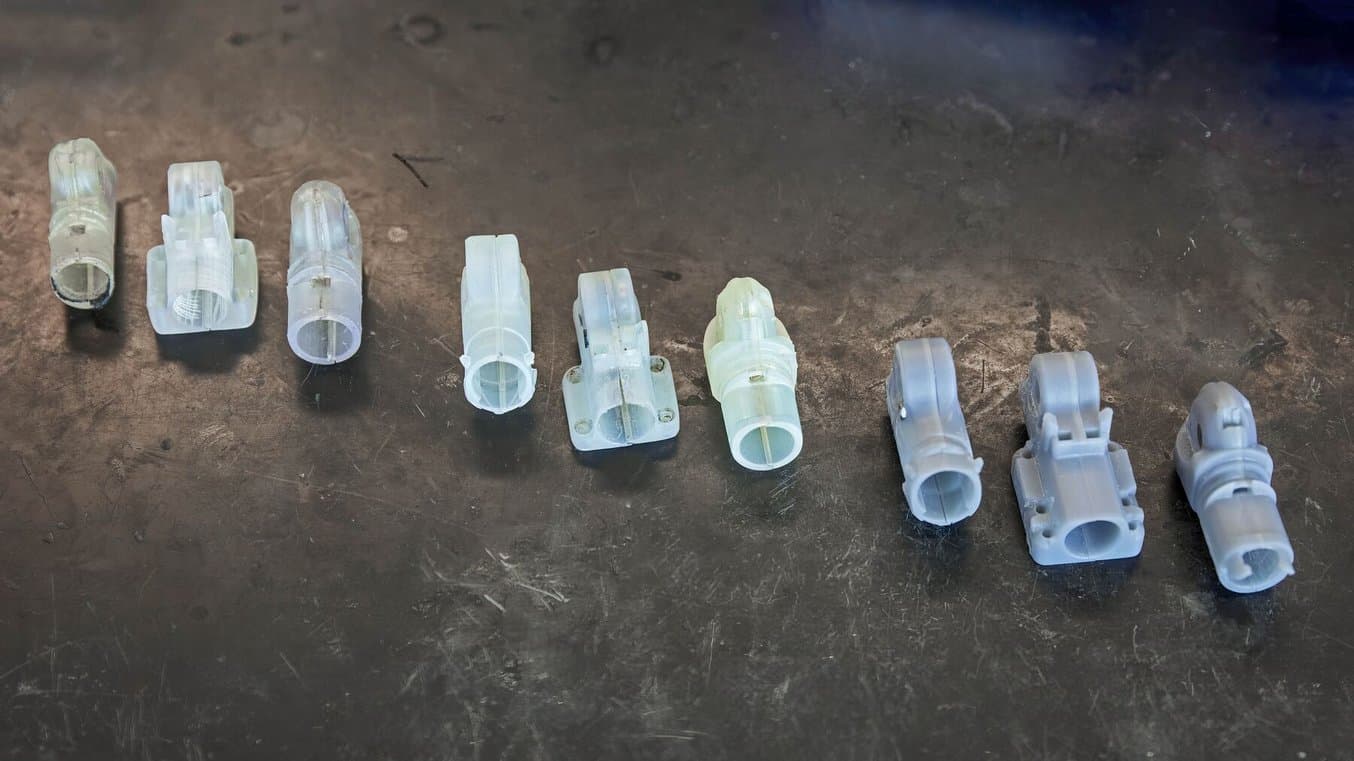
PSYONIC a prototypé un nombre incalculable de pièces au cours des dernières années, en intégrant les commentaires des clients dans la conception de l'Ability Hand.
Pour tout nouveau dispositif, le prototypage rapide joue un rôle essentiel dans le processus de développement. Il est encore plus important pour les dispositifs médicaux, car les patients et les utilisateurs finaux laissent beaucoup de commentaires sur les pièces. Les entreprises de dispositifs médicaux passent souvent par des centaines de prototypes d'une seule pièce avant d'être prêtes pour les essais sur le terrain, et les tests réglementaires et cliniques exigent d'être extrêmement rigoureux. M. Austin a été confronté à ce problème lorsqu'il a testé l'Ability Hand : « nous avons eu plusieurs cas où un patient cassait quelque chose d'une manière à laquelle nous n'avions pas pensé, et il y avait généralement un moyen facile le réparer. J'ai modifié la prothèse, fabriqué un prototype, fait un test et ai obtenu une nouvelle Ability Hand après une semaine ou deux. »
M. Austin nous a dit que « nous essayons d'équilibrer nos méthodes de fabrication pour optimiser ce que nous pouvons en fonction des tâches en cours. Beaucoup de nos prototypes sont d'abord imprimés par FDM ou par SLA, puis, une fois que nous avons décidé d'un design plus ou moins définitif, nous pouvons les fabriquer avec par exemple une machine CNC métal, ce qui est plus coûteux et plus long, mais plus durable à long terme. Certaines pièces peuvent rester en résine SLA : elles fonctionnent très bien telles quelles. Certaines choses sont un peu plus durables une fois qu'elles sont fabriquées en métal. Grâce à toutes ces options, nous pouvons vraiment combiner plusieurs méthodes pour optimiser chaque pièce et nous assurer que nous en avons pour notre argent. Le coût de fabrication est très bas, mais les performances sont très élevées. »
Impression 3D de pièces finales
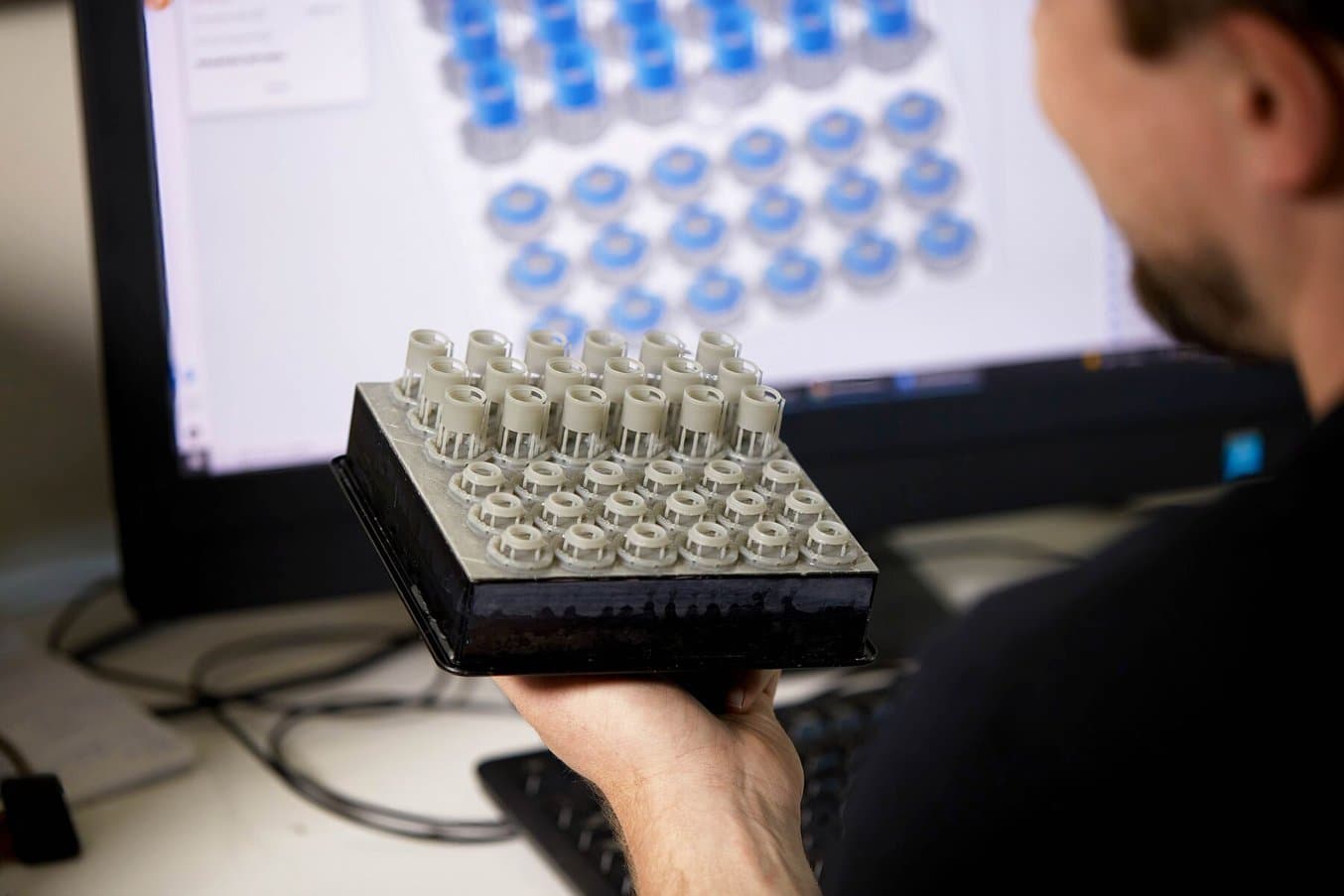
M. Austin tient un lot de pièces d'utilisation finale imprimées avec Tough 1500 Resin.
Grâce aux progrès récents des matériaux d'impression 3D, les pièces qui sortent directement de l'imprimante conviennent souvent aux modèles destinés aux clients, voire aux pièces d'utilisation finale elles-mêmes, ce qui évite d'utiliser un outillage traditionnel coûteux et réduit les délais de développement.
En imprimant avec Tough 1500 Resin, M. Austin a trouvé un matériau parfait pour de nombreuses pièces finales présentes dans l'Ability Hand.
« Nous utilisons beaucoup l'impression SLA pour le prototypage. Mais elle nous sert avant tout à fabriquer des produits finis. C'est particulièrement vrai pour les pièces en Tough 1500 Resin, qui restent supérieures à tout autre objet imprimé en 3D que nous pourrions fabriquer avec cette résolution, et beaucoup plus rentables que les pièces moulées par injection. Pour les quantités que nous produisons et les propriétés que nous recherchons en termes de force, de résolution, de résistance thermique et de résistance aux chocs, Tough 1500 Resin est honnêtement la meilleure chose que nous ayons trouvée, et nous continuons à l'utiliser pour tous nos dispositifs », nous confie Austin.
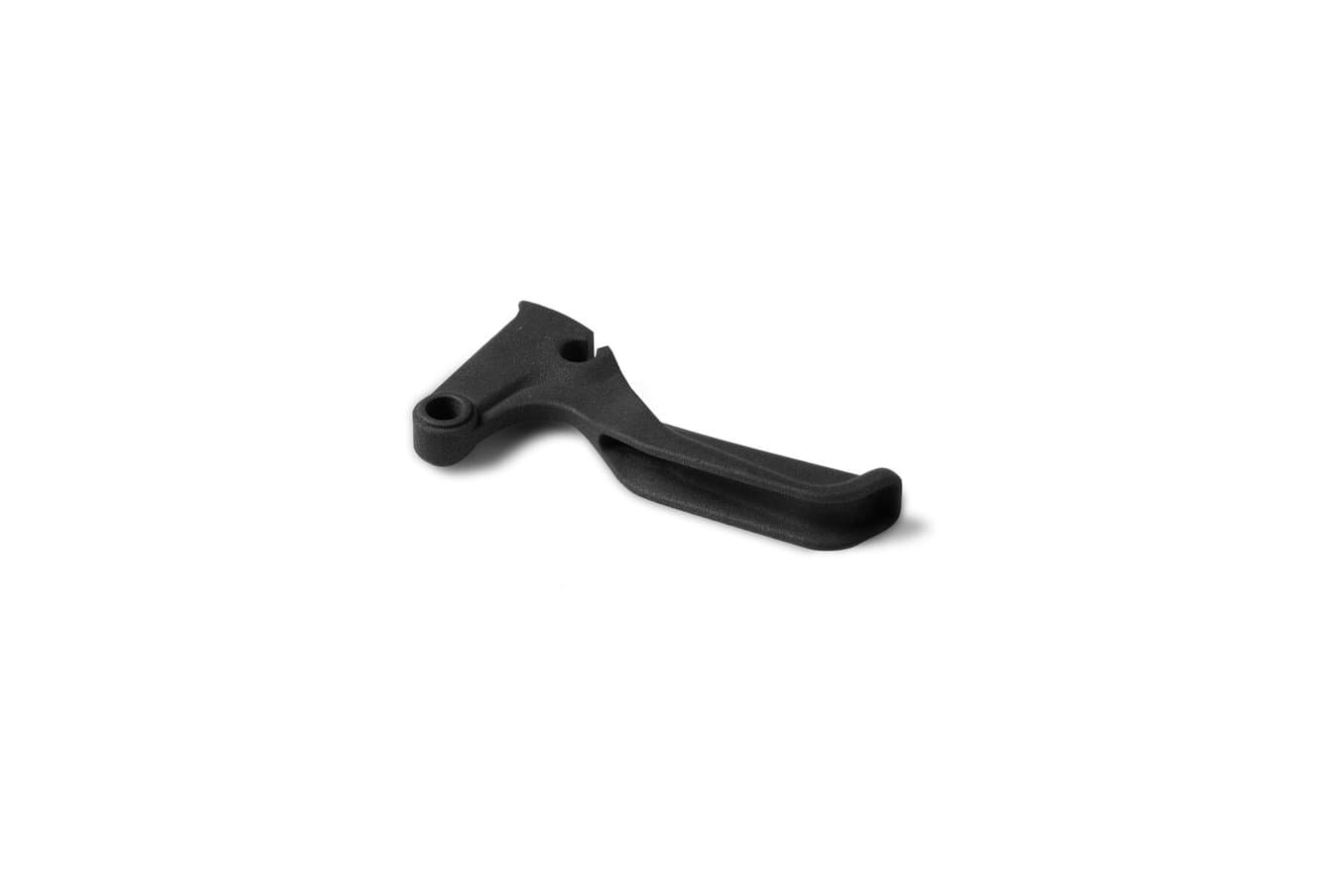
Commandez un échantillon gratuit
Examinez et constatez par vous-même la qualité Formlabs. Nous enverrons un échantillon gratuit à votre bureau.
Des dispositifs qui peuvent survivre à n'importe quoi
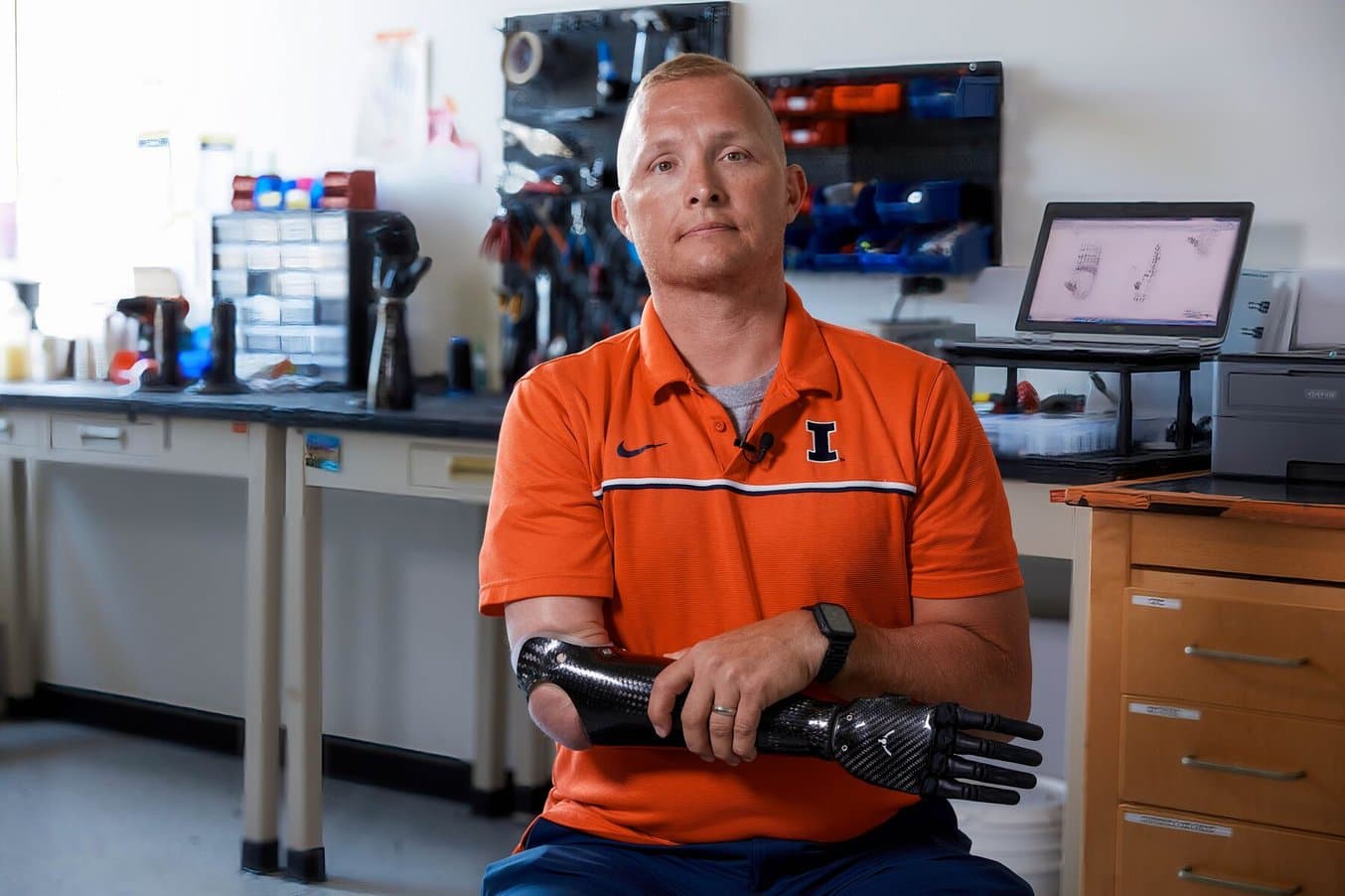
La croissance de PSYONIC en tant qu'entreprise a poussé Akhtar et son équipe à utiliser des techniques de fabrication hybrides modernes et des solutions d'ingénierie innovantes. PSYONIC cherche actuellement à se développer et à proposer son produit aux utilisateurs du monde entier. Pour l'instant, la croissance se concentre sur le marché nord-américain, avec une augmentation de la production de l'Ability Hand à partir de la fin 2022.
« Ce que veulent nos patients, c'est pouvoir réaliser des activités normales de la vie quotidienne. Les dispositifs existants ne permettent souvent pas d'effectuer certaines des tâches les plus simples. Nous sommes allés bien au-delà, grâce aux nombreuses innovations que nous avons apportées à la conception de notre Ability Hand », a déclaré M. Akhtar. M. Anderson a ajouté : « Au début de cette année, c'était la première fois que je pouvais réellement sentir que je touchais la main de ma fille avec cette main prothétique, grâce au retour sensoriel. »