La strada per arrivare alla macchina stampata in 3D: 5 modi in cui la stampa 3D sta cambiando il settore automobilistico
È ancora presto per acquistare un'auto stampata in 3D presso un concessionario, ma questa tecnologia è stata per molti anni una parte fondamentale del processo di sviluppo delle automobili. Di recente, tuttavia, ha cominciato a prendere piede in tutti gli aspetti della produzione.
La stampa 3D può aggiungere un enorme valore alle catene di fornitura, dando accesso a un ampio spettro di applicazioni produttive. La tecnologia sta diventando sempre più praticabile e conveniente, e alcune aziende riescono a introdurre la produzione additiva in house per supportare i processi in fabbrica. Nuovi materiali resilienti offrono opportunità inedite di produrre stampe 3D funzionali e ad alta precisione, in grado di sostituire le parti finali e permettere di personalizzare i componenti e ottenere prestazioni elevate. Ma questo è solo l'inizio.
Scopri i cinque modi in cui la stampa 3D sta alimentando l'innovazione nel settore automobilistico, dal design alla produzione e oltre.
1. Reinventare i processi di prototipazione
La prototipazione è stata storicamente il caso d'uso più comune per la stampa 3D nel settore automobilistico. Grazie alla maggiore velocità di prototipazione consentita dalla stampa 3D, la prototipazione rapida è diventata praticamente sinonimo di stampa 3D, e la tecnologia ha rivoluzionato il processo di sviluppo dei prodotti.
Con la stampa 3D, i progettisti del settore automobilistico possono realizzare rapidamente un prototipo di una parte fisica o di un assemblaggio, da un semplice elemento interno a un cruscotto o persino un modello in scala di un'intera auto. La prototipazione rapida consente alle aziende di trasformare le idee in Proof-of-Concept convincenti, che possono poi essere sviluppati fino a diventare prototipi di alta qualità molto simili al risultato finale e, infine, guidare i prodotti lungo una serie di fasi di validazione che portano alla produzione in serie. Nel settore automobilistico questa convalida rapida è assolutamente fondamentale. “Fermare una linea di produzione automobilistica anche solo per un'ora può avere un costo esorbitante” spiega Andrew Edman, responsabile del design di prodotto, ingegneria e settore della produzione presso Formlabs.
Grazie all'uso in house della stampa 3D stereolitografica (SLA), progettisti e ingegneri di Ringbrothers possono eseguire iterazioni liberamente, in maniera efficace e a un costo contenuto.
Un tempo la prototipazione era un processo lungo e quindi potenzialmente costoso, dato che venivano eseguite più iterazioni di un prodotto. Con la stampa 3D è possibile creare prototipi incredibilmente convincenti e rappresentativi in un solo giorno, e a un costo decisamente inferiore. Le stampanti 3D desktop consentono ai team di ingegneria e design di introdurre la tecnologia all'interno dell'azienda per aumentare i cicli di iterazione e accorciare la distanza tra l'idea e il prodotto finale, rafforzando complessivamente il flusso di lavoro.
2. Creare parti complesse, personalizzate e ad alte prestazioni
La stampa 3D è ideale per la realizzazione di parti personalizzate a costi notevolmente ridotti, dando così ai produttori numerose nuove possibilità di produzione da offrire ai clienti.
Per le aziende più piccole, che pongono la stampa 3D al centro della loro attività, come l'officina di parti personalizzate per auto Ringbrothers, la stampa 3D offre nuove possibilità di migliorare la qualità e liberare la creatività, fornendo uno spazio vitale per sperimentare e perfezionare i progetti personalizzati, senza doversi preoccupare dei costi potenziali e dei processi di produzione normalmente legati alla personalizzazione e che richiederebbero molto tempo.
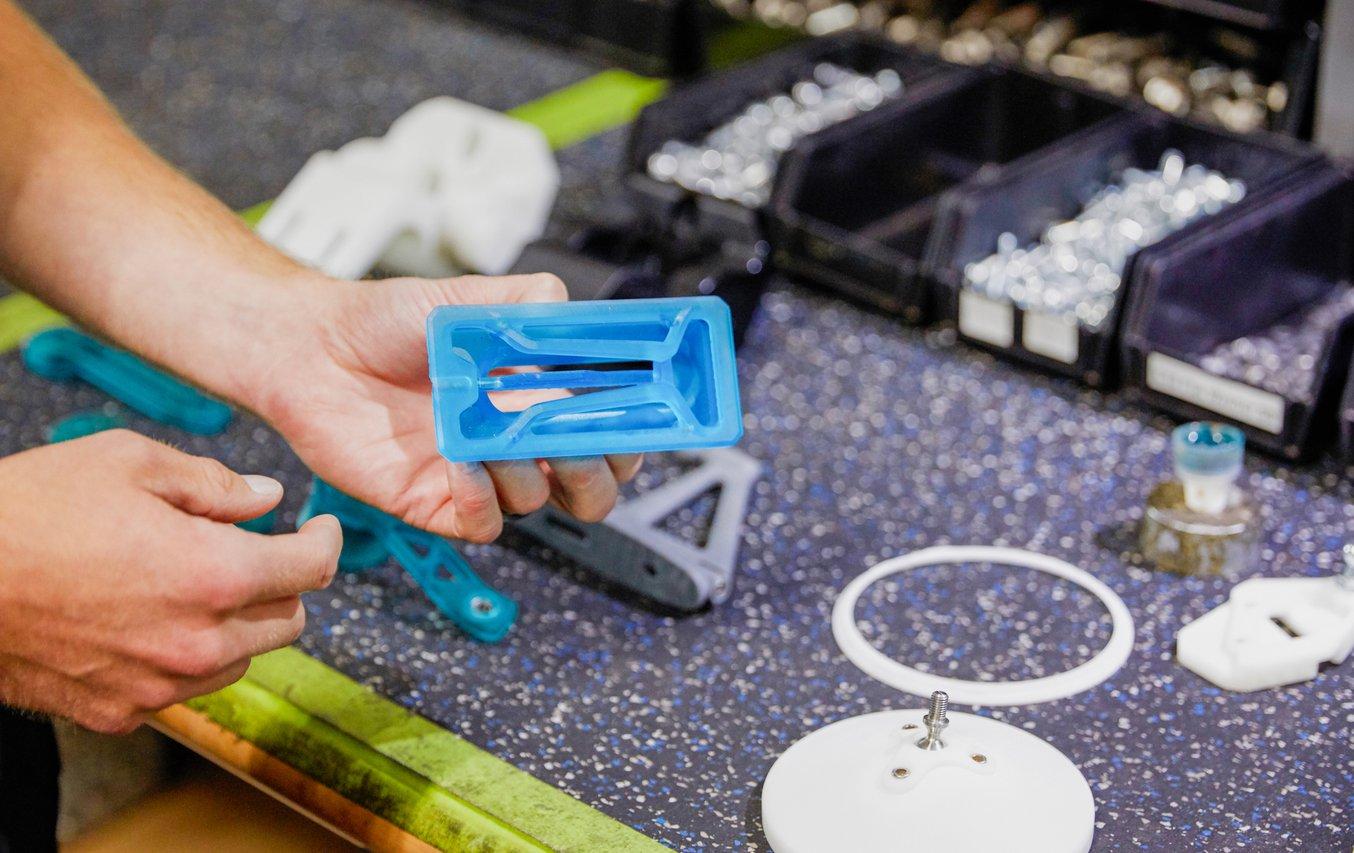
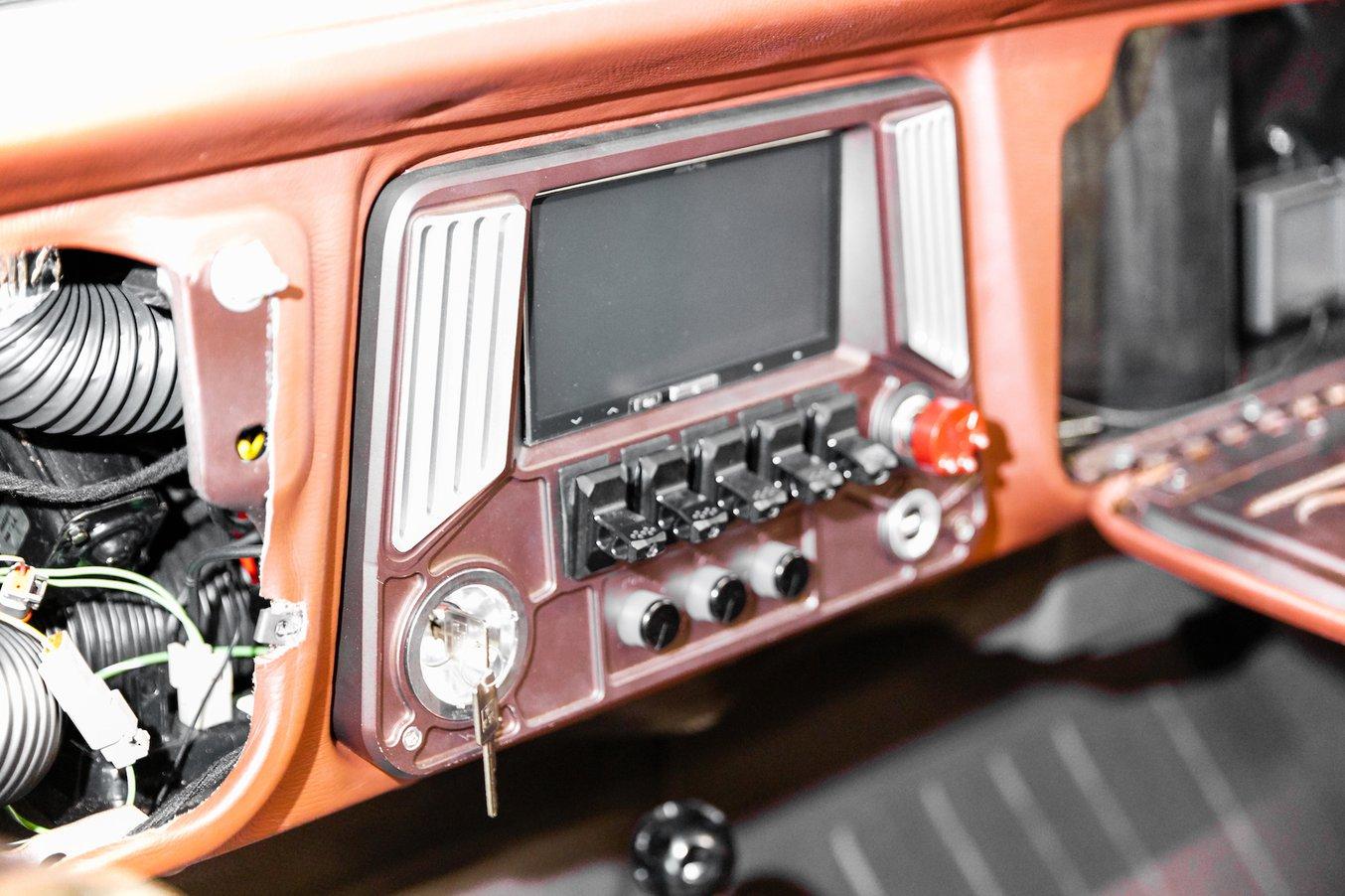
Ringbrothers usa la stampa 3D per creare parti destinate all'uso finale come questa bocchetta di aerazione.
Anche le grandi aziende stanno combinando la tecnologia di stampa 3D con i metodi tradizionali. Volkswagen ha ricreato il suo Microbus del '62, sostituendone il motore a benzina con uno elettrico da 120 cavalli e 230 Nm di coppia. Questo modello chiamato "Type 20" presenta anche una serie di miglioramenti resi possibili dalla stampa 3D, tra cui le ruote in alluminio progettate in maniera generativa. Anche i coprimozzi sono stati stampati in 3D: sembrano in acciaio, ma in realtà sono stati realizzati con una stampante 3D SLA di Formlabs e poi elettroplaccati per assumere l'aspetto di parti metalliche.
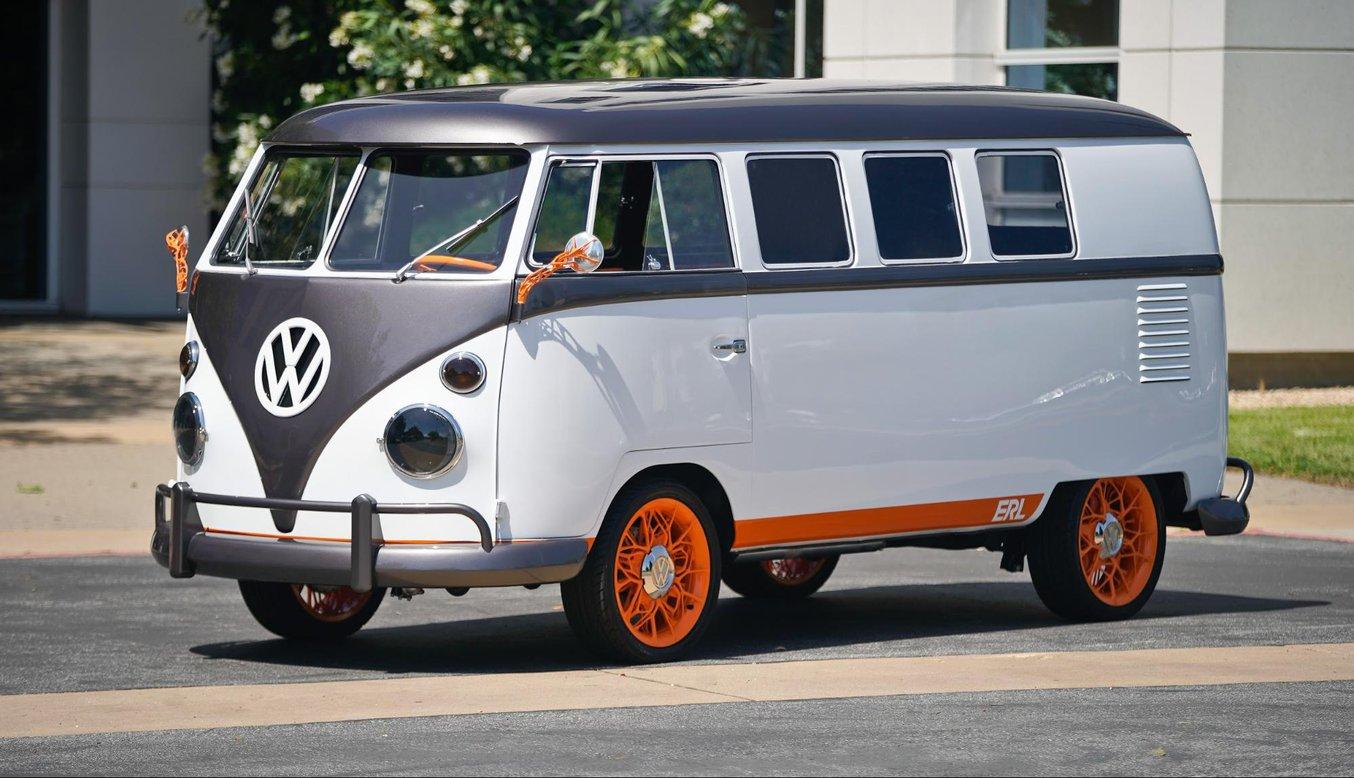
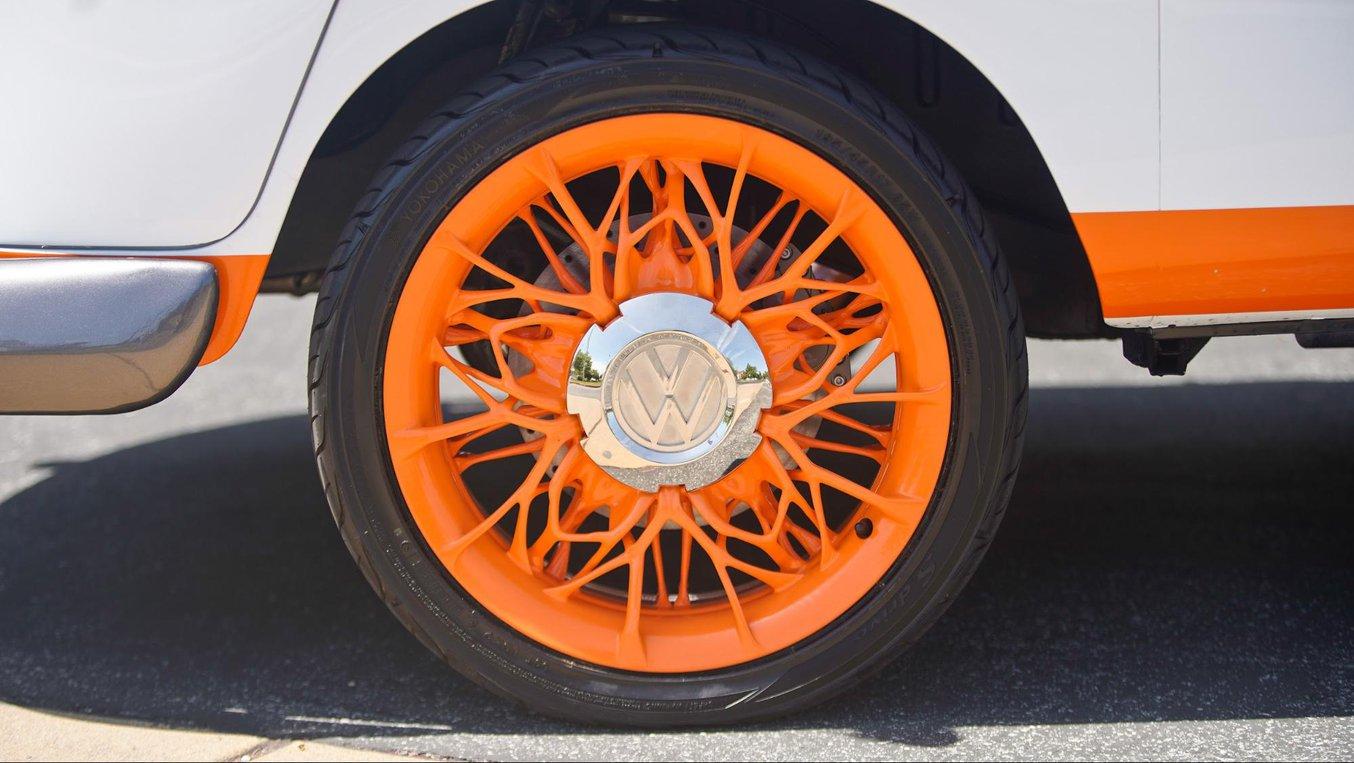
I coprimozzi di questo Microbus Volkswagen sono stati stampati in 3D su una stampante 3D SLA di Formlabs e poi elettroplaccati e lucidati per farli assomigliare a parti in acciaio cromato. (immagini: VW)
La Bentley Speed 6 è un altro esempio. La casa automobilistica di lusso ha utilizzato l'avanzata tecnologia di stampa 3D in metallo per creare parti molto più dettagliate e complesse (griglia, prese d'aria laterali, maniglie delle porte e scarichi) rispetto a quanto disponibile nei suoi modelli di produzione attuali.
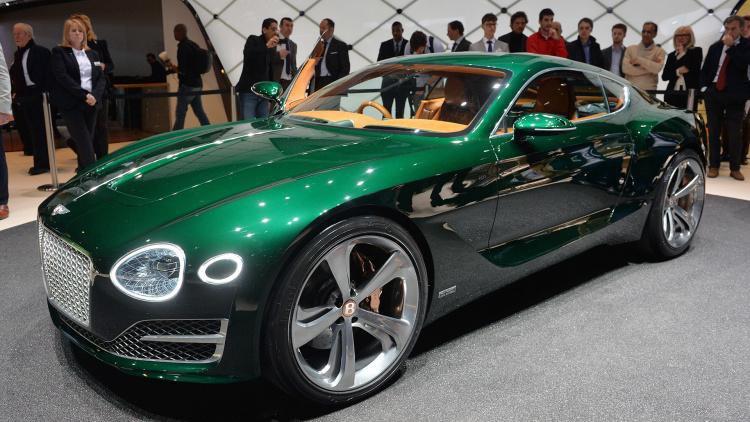
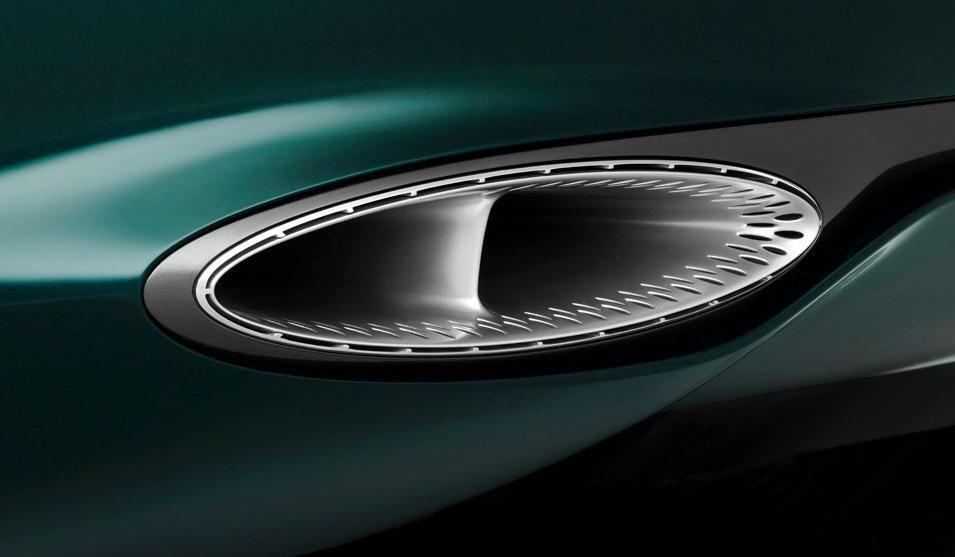
Bentley ha utilizzato la tecnologia di stampa in metallo per creare parti complesse con precisione millimetrica. (fonte: Bentley)
Le applicazioni di stampa 3D, però, non si limitano ai classici e ai modelli concettuali o espositivi. Il software di personalizzazione di Twikit ha permesso alla casa automobilistica britannica MINI di offrire servizi di personalizzazione di massa per le loro auto utilizzando la stampa 3D, dando agli acquirenti il pieno controllo sulla progettazione. I clienti possono personalizzare i componenti interni o esterni del loro veicolo con una gamma di font, modelli e immagini, e rivedere il proprio progetto grazie a visualizzazioni in 3D. La riduzione dei costi consentita dalla stampa 3D, fondamentale affinché un progetto di questo tipo sia commercialmente valido, ha reso questa forma di personalizzazione accessibile al pubblico.
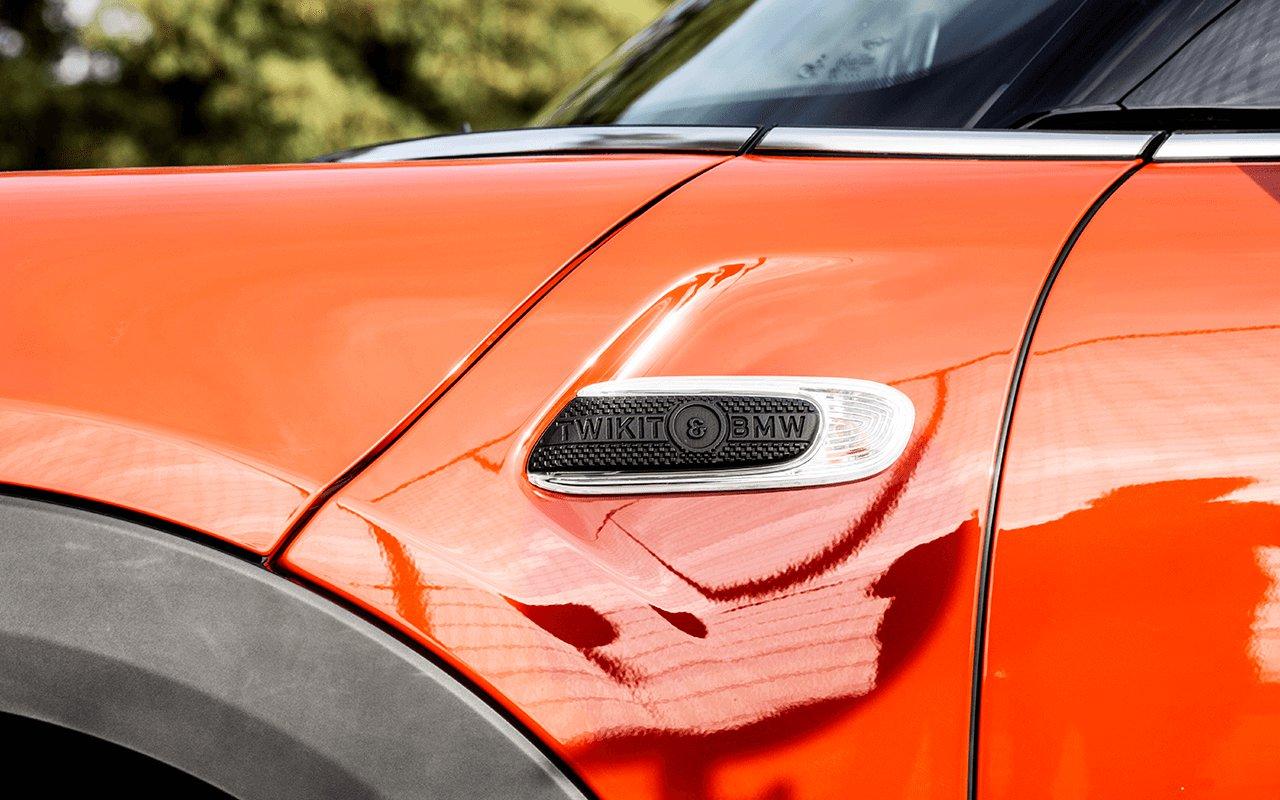
La collaborazione di MINI con Twikit offre ai clienti il pieno controllo sul design, consentendo di personalizzare i componenti interni o esterni del veicolo. (fonte: Twikit)
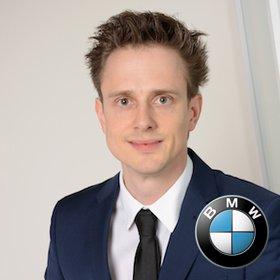
La stampa 3D nella produzione di BMW
In questo filmato, Christian Gröschel, capoprogetto presso BMW, descrive il processo dell'azienda per lo sviluppo e l'implementazione del loro programma additivo.
Guarda il videoLa stampa 3D ha anche permesso la creazione di parti che semplicemente non potevano essere prodotte con altri mezzi. La pinza freno monoblocco a otto pistoni di Bugatti ne è un chiaro esempio. Bugatti predilige il titanio per alcuni componenti, perché offre prestazioni elevate, ma la lavorazione del metallo con metodi convenzionali è costosa e impegnativa. L'utilizzo della stampa 3D non solo ha permesso a Bugatti di produrre la pinza in scala come richiesto, ma ha migliorato ulteriormente il suo potenziale a livello di prestazioni, riducendo di molto il peso del componente e rendendolo notevolmente più rigido e resistente rispetto all'alternativa di produzione convenzionale (alluminio).
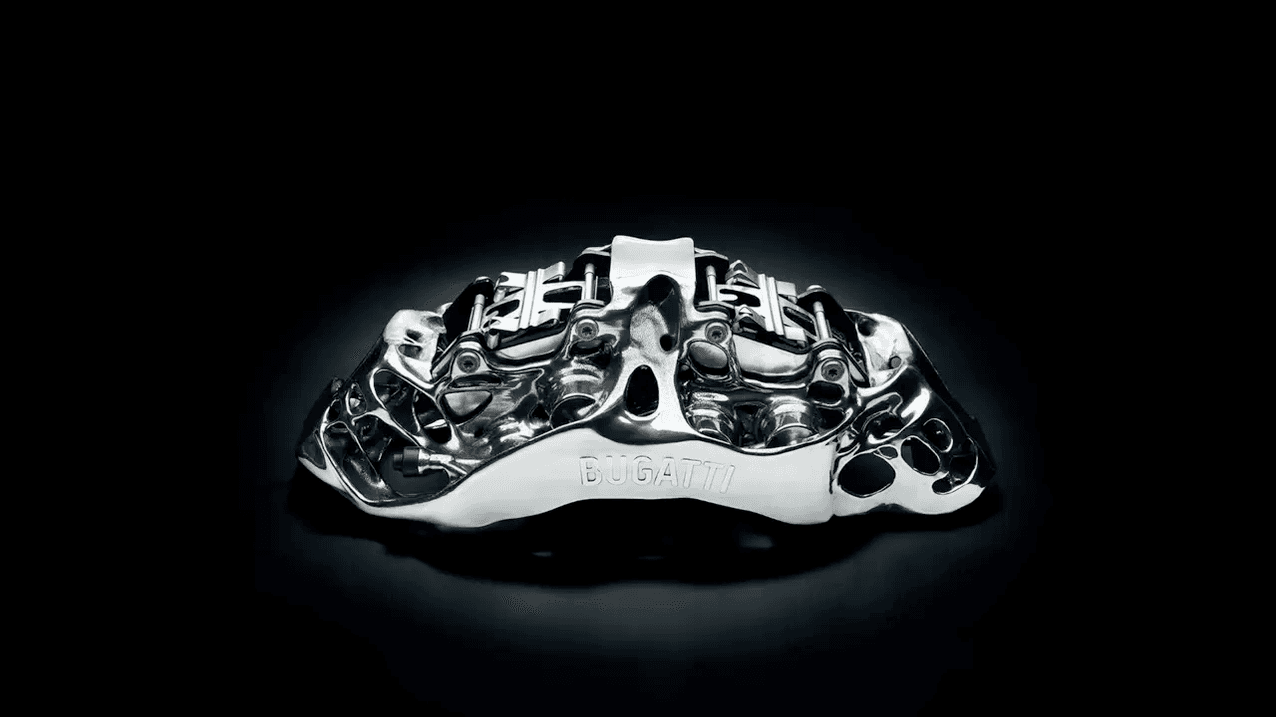
La pinza freno monoblocco a otto pistoni di Bugatti è il più grande componente funzionale al mondo in titanio prodotto mediante stampa 3D. (fonte: Bugatti)
3. Realizzare ausili per attrezzature e produzione
Gli ingegneri utilizzano gli ausili di produzione per semplificare e rendere più affidabili i processi di fabbricazione e assemblaggio, in modo da ridurre i tempi di ciclo e migliorare la sicurezza dei lavoratori. Le fabbriche automobilistiche e i fornitori di componenti utilizzano migliaia di dime e fissaggi personalizzati, ciascuno realizzato su misura e altamente ottimizzato per l'uso finale. Il risultato è la proliferazione di strumenti personalizzati, che aggiungono costi e complessità al processo di fabbricazione.
L'esternalizzazione della produzione di queste parti personalizzate a fornitori di servizi di lavorazione meccanica, che le producono a partire da una billetta di plastica o metallo solida, può ritardare la produzione di settimane, mentre i lunghi tempi di realizzazione rendono difficile l'adattamento ai cambiamenti in fabbrica.
La produzione additiva consente di ridurre i tempi di realizzazione a poche ore e abbassare drasticamente i costi rispetto all'esternalizzazione delle parti a un fornitore esterno. Poiché la complessità non comporta costi aggiuntivi, le parti possono anche essere ottimizzate meglio per il loro uso finale. Inoltre, grazie a nuovi materiali di stampa 3D resilienti, in molti casi i produttori possono sostituire componenti metallici con parti in plastica stampate in 3D o realizzare prototipi e testare gli strumenti prima di fare un investimento.
Di conseguenza, la creazione di ausili di produzione mediante la stampa 3D sta diventando una delle principali applicazioni di questa tecnologia.
Pankl Racing Systems utilizza dime stampate in 3D per fissare le parti al nastro trasportatore durante una serie di fasi di lavorazione meccanica.
Ad esempio, Pankl Racing Systems si affida a una postazione di stampa 3D composta da diverse stampanti 3D SLA di Formlabs per fabbricare i loro strumenti di produzione fondamentali. Nella produzione di parti per gruppi riduttori, ogni parte che l'azienda produce richiede una serie di dime, fissaggi e altre attrezzature personalizzate progettate appositamente per quella parte, mentre passano attraverso molteplici fasi di lavorazione meccanica eseguita utilizzando torni automatici. Grazie alla stampa 3D, gli ingegneri di Pankl sono riusciti a ridurre i tempi di realizzazione per le dime del 90% (da due o tre settimane a meno di un giorno) e hanno diminuito i costi dell'80-90%, consentendo un risparmio di 150 000 $.
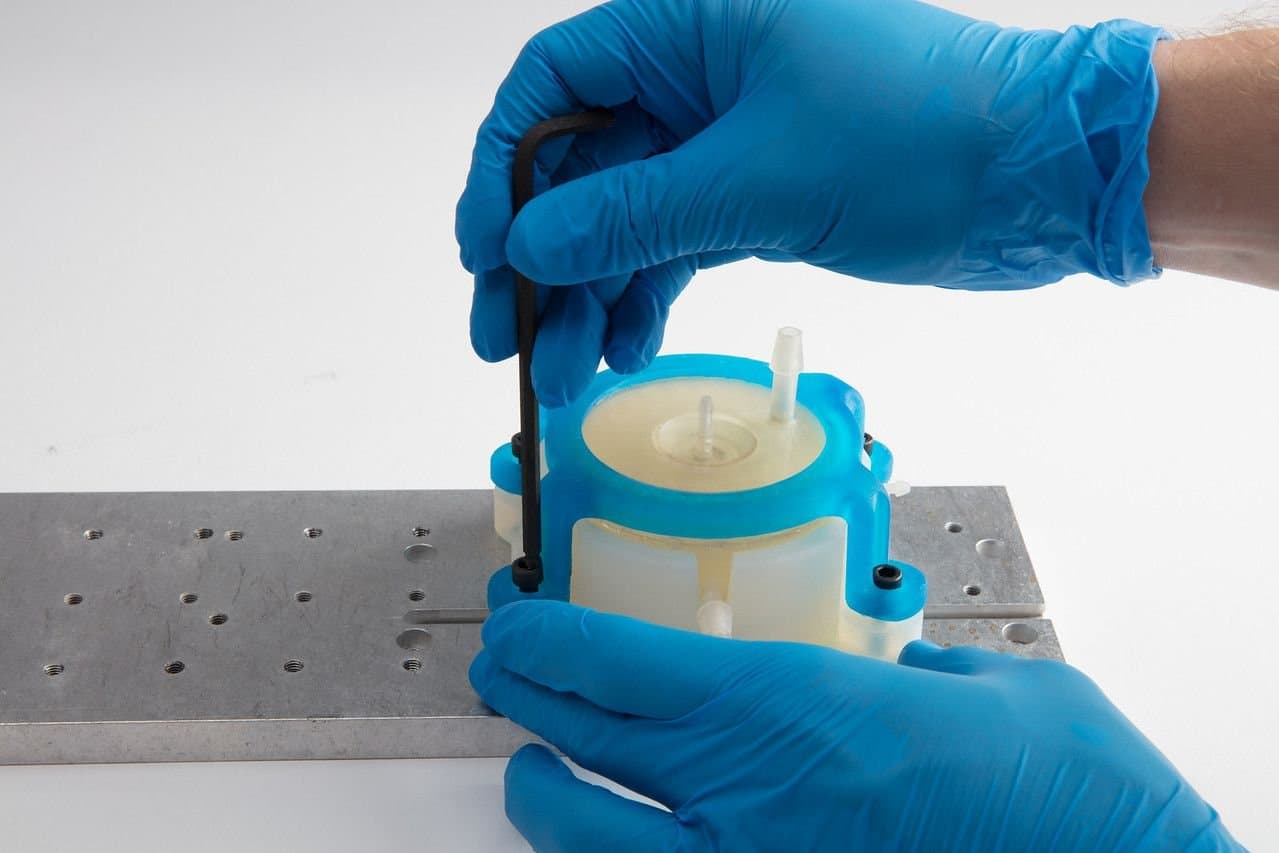
Progettazione di dime e fissaggi destinati alla stampa 3D
Scarica il nostro whitepaper per scoprire come ridurre i costi, i tempi di sviluppo e creare un workflow di produzione più efficiente grazie alla stampa in 3D di dime e fissaggi.
Scarica il whitepaper4. Risolvere il problema delle parti di ricambio
I ricambi hanno rappresentato storicamente una sfida per il settore automobilistico. La loro domanda è sporadica e imprevedibile, rendendo in alcuni casi discutibile il valore finanziario della produzione di componenti di ricambio. Tuttavia, in assenza di parti di ricambio facilmente reperibili, il valore dei prodotti diventa più precario e le riparazioni risultano complicate. Inoltre, la produzione di parti di ricambio in previsione di una domanda futura comporta grandi spese di stoccaggio.
La stampa 3D ha tutte le carte in regola per avere un impatto positivo significativo sul problema delle parti di ricambio nel settore automobilistico. “Credo che [per risolvere il problema delle parti di ricambio grazie alla stampa 3D] siano fondamentali due cose: materiali alternativi con prestazioni equiparabili alle loro controparti tradizionali e un buon rapporto costo-benefici. E stiamo per raggiungere entrambi gli obiettivi” spiega Edman. “Non è tanto una questione se la stampa 3D diventerà il metodo principale di produzione di parti di ricambio, quanto piuttosto di quando avverrà questo cambiamento.”
Grazie all'uso del software CAD, i design di tutte le parti possono essere conservati come copia digitale, rendendo quindi obsoleta la necessità di mantenere un inventario. Con la proliferazione delle stampanti 3D da banco, una parte di ricambio potrebbe essere prodotta in negozio su richiesta del cliente. L'accessibilità della tecnologia incoraggerà i fornitori ad aprire nuovi spazi per fornire con facilità pezzi di ricambio stampati in 3D.
Anche i componenti che non esistono più possono potenzialmente essere realizzati su richiesta tramite processi di ingegneria inversa basati su scansioni digitali di parti esistenti. I design più vecchi potrebbero avere una nuova vita. "C'è chi ha un'auto classica con più di 50 anni. Un giorno forse riusciremo a fornir loro assistenza in maniera più automatica grazie alla stampa 3D" spiega Edman.
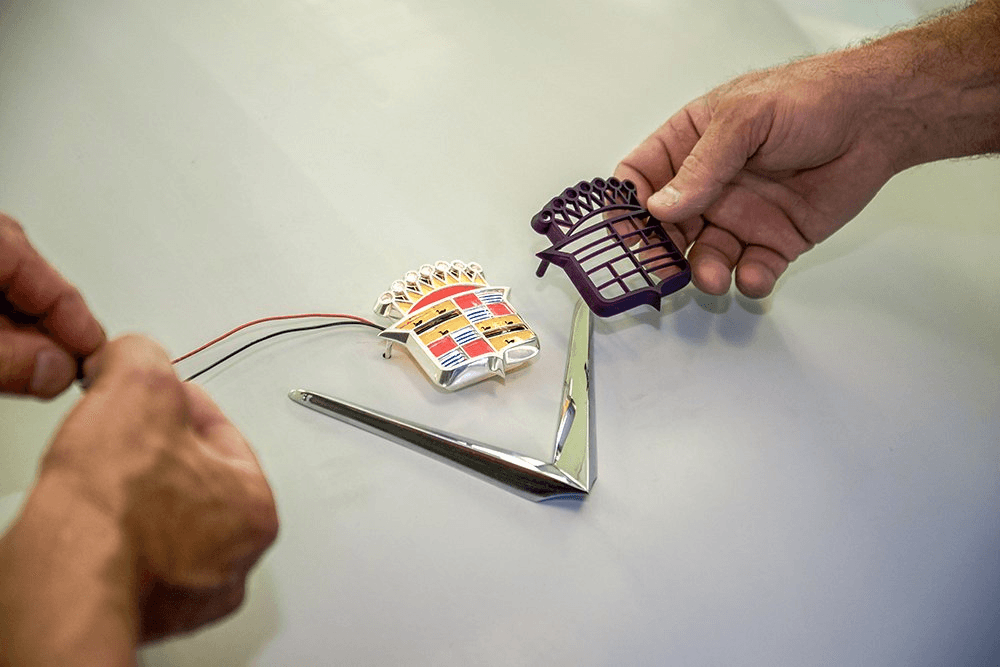
Ringbrother ha riprodotto l'emblema Cadillac per un veicolo d'epoca personalizzato stampandone in 3D la forma e fondendola in metallo.
5. Facilitare la produzione generale di parti
Con la graduale riduzione dei costi di hardware e materiali per la stampa 3D, assisteremo a una progressiva transizione verso la produzione di componenti generici per auto.
Le stampanti 3D possono migliorare l'efficienza nella fase generale di produzione delle parti. Come fa notare Edman, "le tecniche di stampa 3D diventeranno più comuni nei casi in cui è possibile sfruttare i benefici della produzione additiva per unire i componenti tramite piegatura. Potresti avere un assemblaggio composto da 6 o 7 elementi che ora puoi combinare in un'unica parte stampata. Risparmierai così tempo e denaro, anche se la singola parte potrebbe risultare più costosa." Consolidando le parti, i metodi di stampa 3D possono anche contribuire a ridurre il peso e migliorare l'efficienza dei consumi di carburante.
La vasta gamma di materiali offerti dalla stampa 3D sta iniziando a soddisfare i requisiti meccanici dei diversi componenti di un veicolo. Una volta che i metodi additivi avranno raggiunto la parità di costo con i metodi tradizionali (ad es. stampaggio, pressofusione), avrà più senso dal punto di vista produttivo e finanziario incorporare ulteriormente la stampa 3D nella produzione generale delle parti.
+1. Automobili stampate in 3D
Anche se manca ancora molto prima che le auto completamente stampate in 3D possano fare il loro ingresso sul mercato, ci sono alcuni progetti entusiasmanti che mostrano la direzione in cui si sta dirigendo il settore:
Light Cocoon di EDAG: questo concetto realizzato dallo sviluppatore automobilistico indipendente EDAG vanta una struttura portante simile a un ramo stampato in 3D che si ispira alla natura. Nonostante la struttura utilizzi meno materiale di un telaio normale, vengono soddisfatti tutti i requisiti dei componenti strutturalmente rilevanti. Per rendere il telaio resiliente agli elementi, la struttura è rivestita in tessuto.
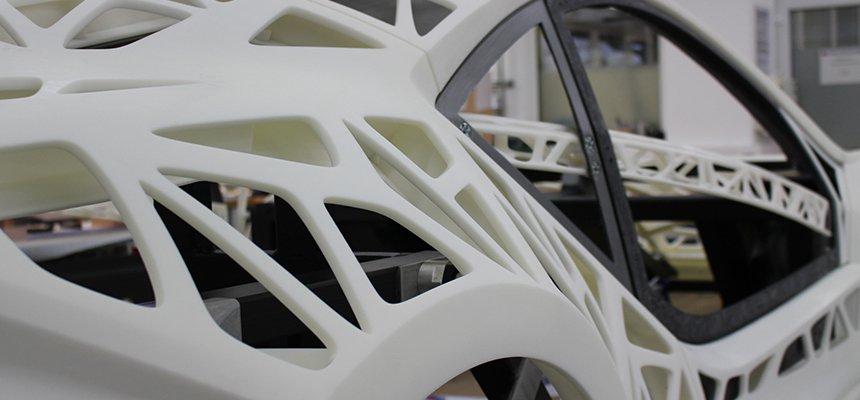
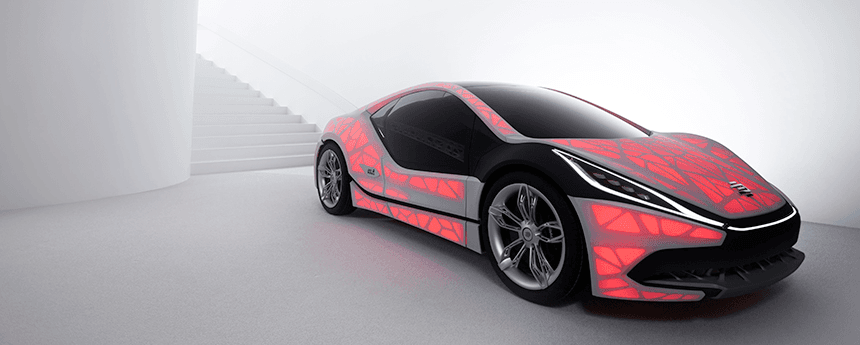
Oltre alla resistenza agli agenti atmosferici, la copertura della Light Cocoon di EDAG offre assoluta libertà di progettazione e personalizzazione. (fonte: EDAG)
The Blade: la "prima superauto stampata in 3D al mondo" è stata progettata per essere prodotta con materiali a basso costo (considerando che si tratta di una "superauto"), come tubi in fibra di carbonio e barre di alluminio, che vengono combinati con parti metalliche stampate in 3D progettate in maniera generativa per ottenere un peso ridotto e prestazioni elevate.
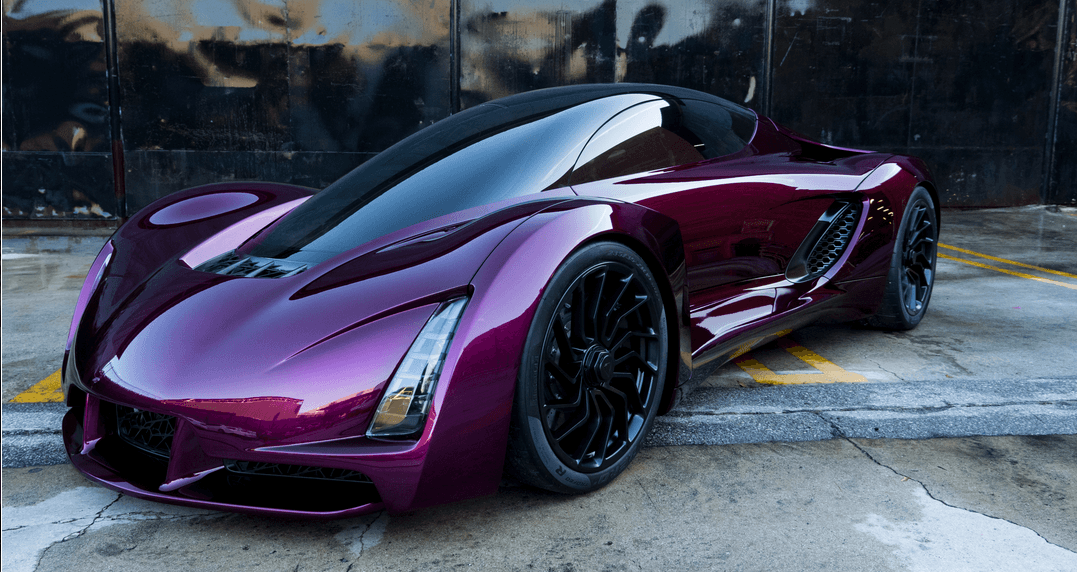
The Blade è la "prima superauto stampata in 3D al mondo". (fonte: Divergent3D)
Strati: la prima auto elettrica al mondo che utilizza ampiamente la stampa 3D durante il processo di produzione, realizzata da Local Motors. L'auto è composta da 50 parti singole: molte meno rispetto ai circa 30 000 pezzi di un veicolo tradizionale. Il suo telaio e la maggior parte degli elementi strutturali sono stati stampati in 3D in meno di 24 ore, e l'azienda punta a raggiungere tempi di realizzazione inferiori alle 10 ore.
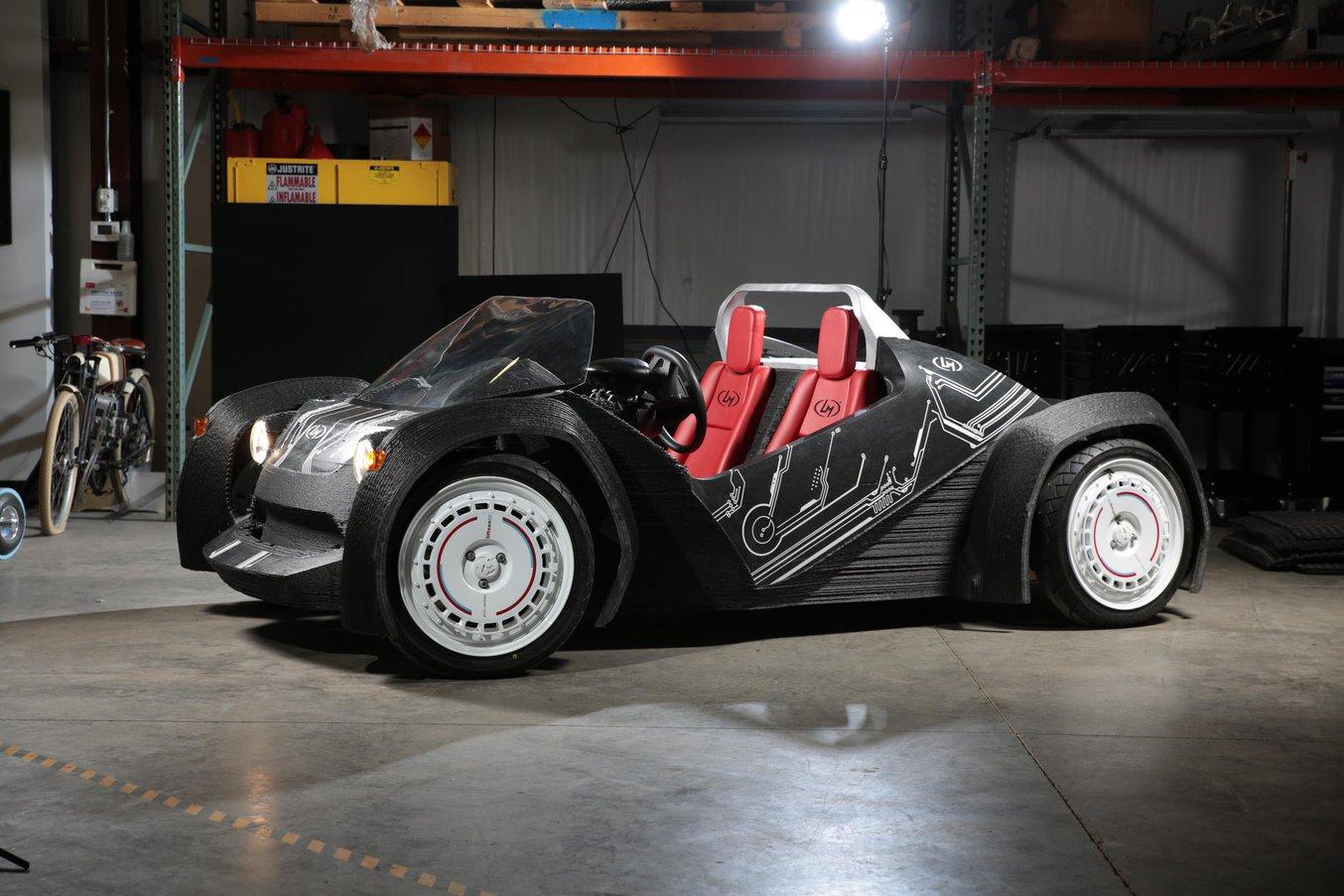
Strati è composta da 50 parti individuali e sono state necessarie meno di 24 ore per stamparla in 3D.
LSEV: sviluppata dall'azienda italiana XEV, la LSEV potrebbe essere la prima auto elettrica stampata in 3D "di massa" quando arriverà sul mercato alla fine di quest'anno. Oltre al telaio, ai sedili e al parabrezza, tutte le parti visibili della LSEV vengono stampate in 3D. Grazie all'ampio uso della stampa 3D, l'azienda è riuscita a ridurre il numero di componenti da 2000 a soli 57, ottenendo un design leggero che pesa solo 450 chili.
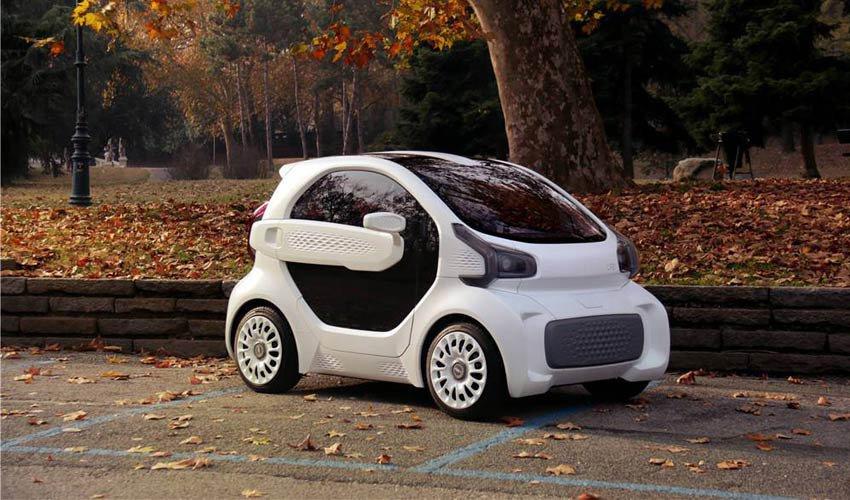
La LSEV è la prima auto elettrica stampata in 3D "di massa" che dovrebbe arrivare sul mercato alla fine di quest'anno.
Anche se questi progetti, e molte altre iniziative di stampa 3D, sono ancora nella fase concettuale, il grado di diffusione della stampa 3D in varie aree del settore automobilistico è incredibile. In alcuni casi, la tecnologia di stampa 3D sta espandendo i confini e allargando l'orizzonte di possibilità di progettazione e produzione. In altri casi, riduce i costi di produzione e consente di risparmiare tempo.
Con la graduale realizzazione del valore aggiunto offerto dalla stampa 3D, il miglioramento della tecnologia e l'aumento di materiali disponibili, l'uso della stampa 3D nel settore continuerà ad aumentare.
Scopri di più sugli ambiti di applicazione della stampa 3D nel settore della produzione