Stampanti 3D potenti e accessibili per professionisti
Formlabs sta stabilendo il punto di riferimento del settore per la stampa 3D professionale per le aziende di tutto il mondo con stampanti 3D accessibili e affidabili desktop e da banco. Adatta in scala la prototipazione e la produzione con parti ad alta risoluzione a una frazione del costo e dell'ingombro delle stampanti 3D industriali.
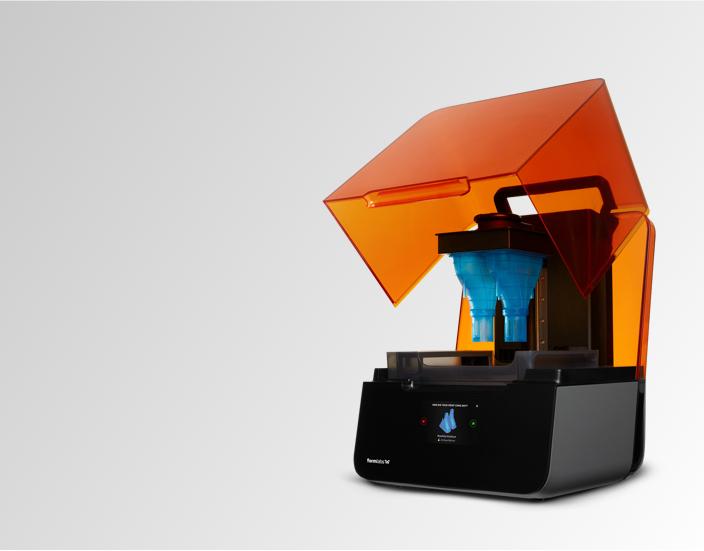
Form 3
La stampante 3D desktop leader del settore, con la potenza della tecnologia Low Force Stereolithography
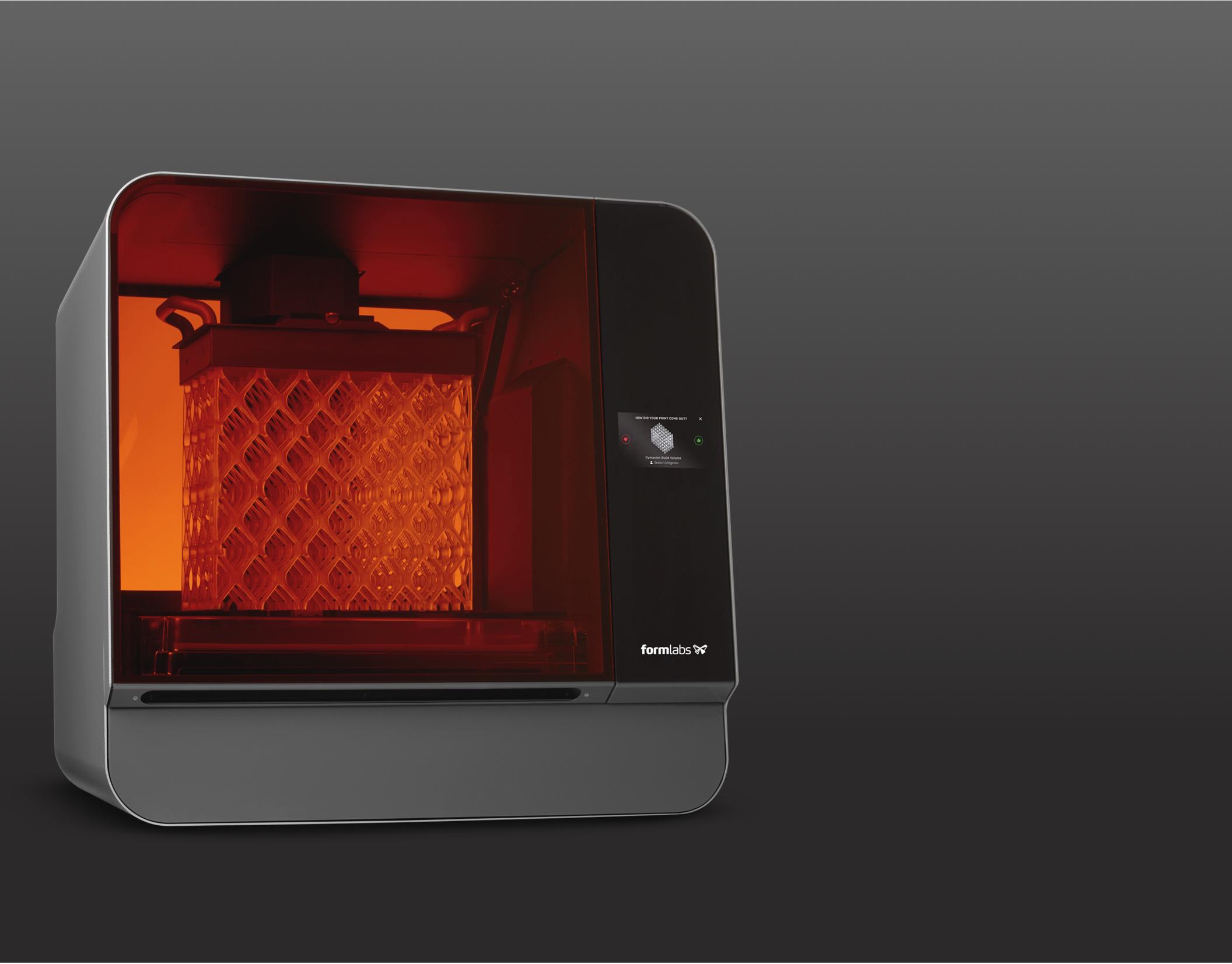
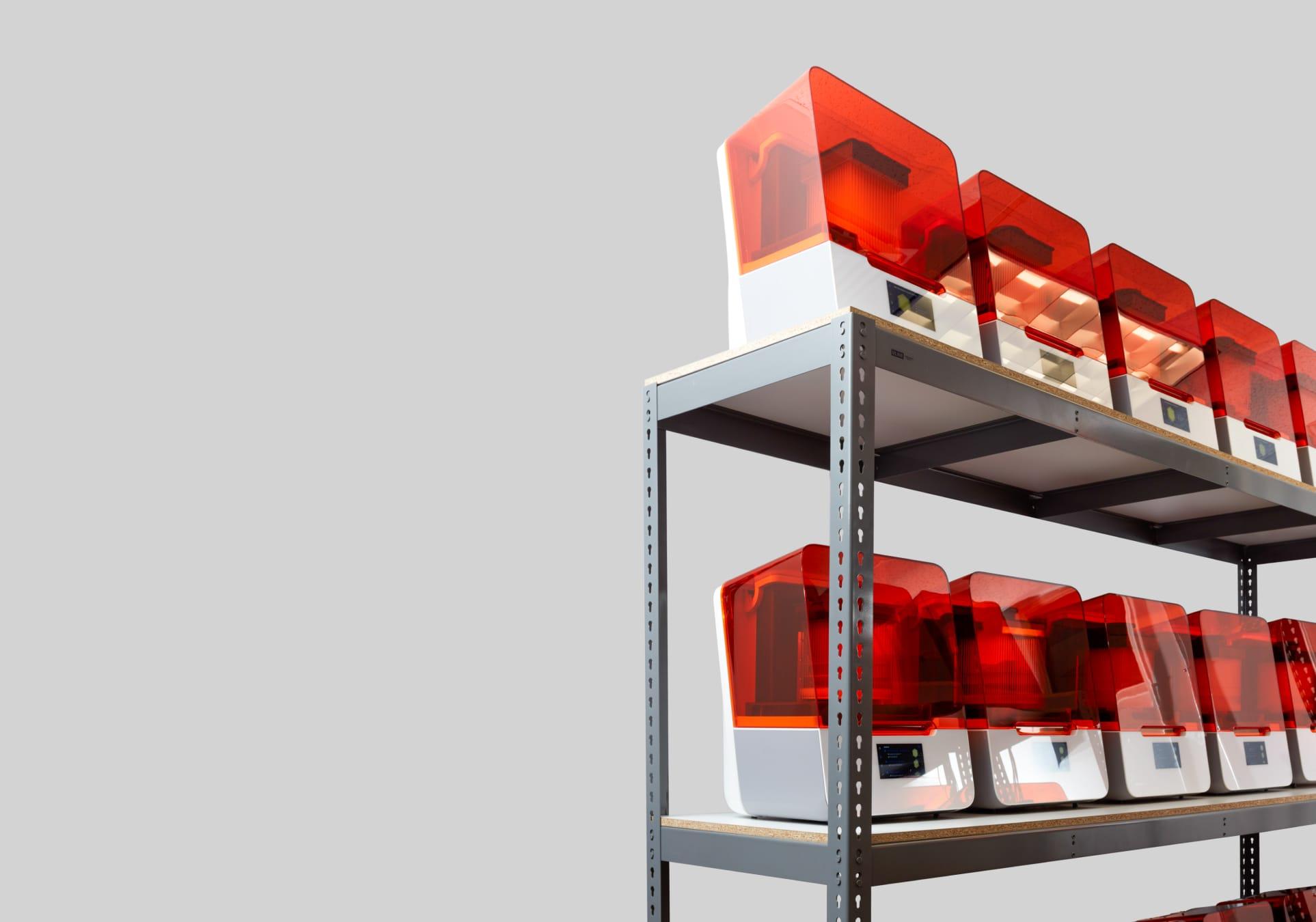
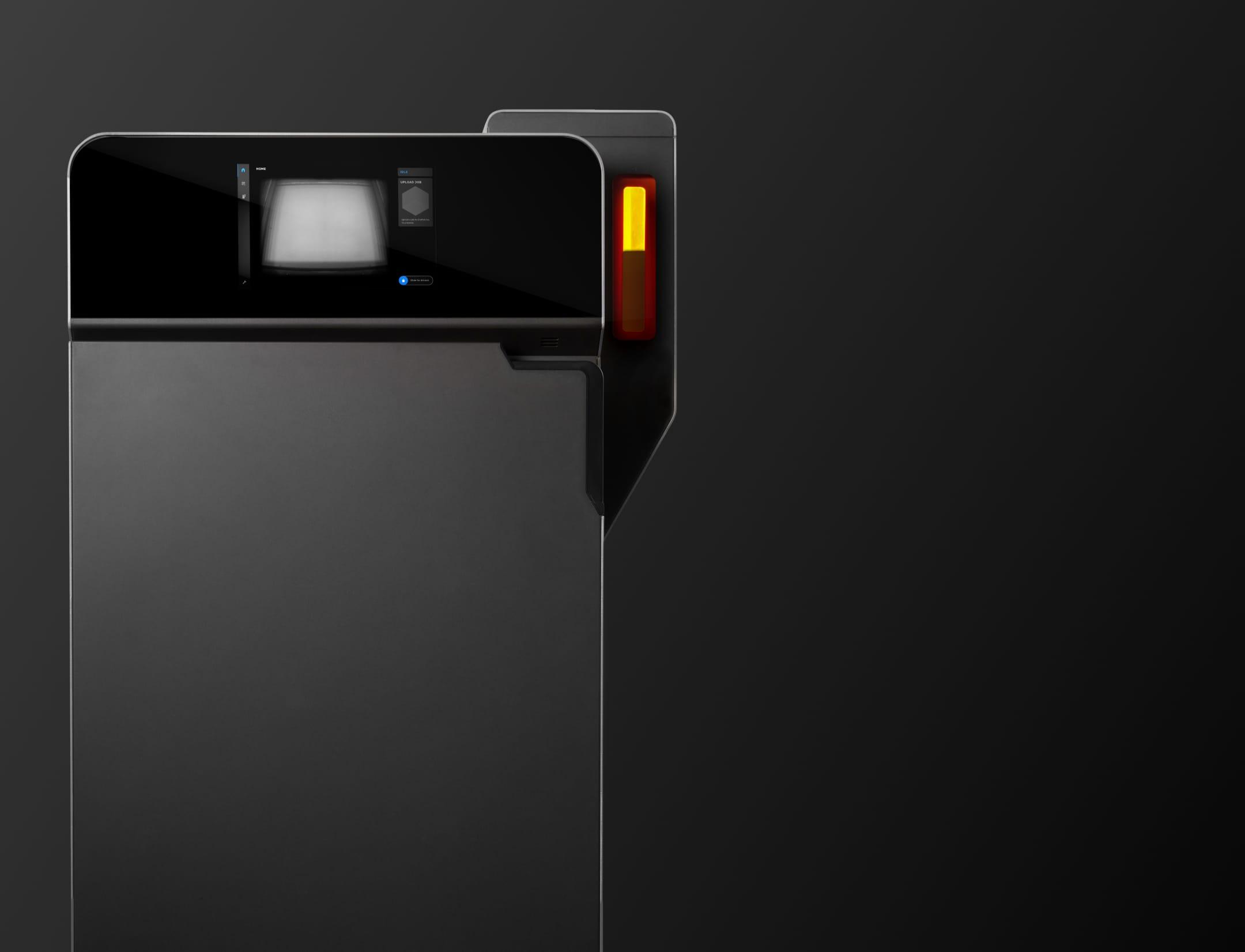
Che cos'è la stampa 3D?
La produzione additiva (ingl. "additive manufacturing", AM), o stampa 3D, consente di creare parti tridimensionali a partire da modelli progettati al computer (CAD) tramite l'aggiunta di più strati di materiale sovrapposti finché non viene completato il pezzo.
Anche se le tecnologie di stampa 3D sono in circolazione fin dagli anni '80, le recenti innovazioni in termini di meccanica, materiali e software hanno reso la stampa 3D accessibile a una vasta gamma di attività, consentendo a sempre più aziende di utilizzare degli strumenti che in precedenza erano alla portata solo di pochi settori tecnologici.
Oggigiorno, le stampanti 3D desktop e da banco professionali a costo ridotto accelerano l'innovazione e supportano le aziende in svariati settori, tra cui ingegneria, produzione, odontoiatria, medicina, istruzione, intrattenimento, gioielleria e audiologia.
Come funziona la stampa 3D?
Tutti i processi di stampa 3D iniziano con un modello CAD, che viene inviato al software per prepararne il design. A seconda della tecnologia, la stampante 3D può produrre la parte strato per strato, solidificando la resina o sinterizzando la polvere. Le parti vengono poi rimosse dalla stampante e sottoposti a post-elaborazione per l'applicazione specifica.
Scopri come passare dalla progettazione alla stampa 3D con la stampante 3D SLA Form 3. Questo video di 5 minuti illustra i concetti di base per l'utilizzo della Form 3, dal software e i materiali alla stampa e la post-elaborazione.
1. Progettazione
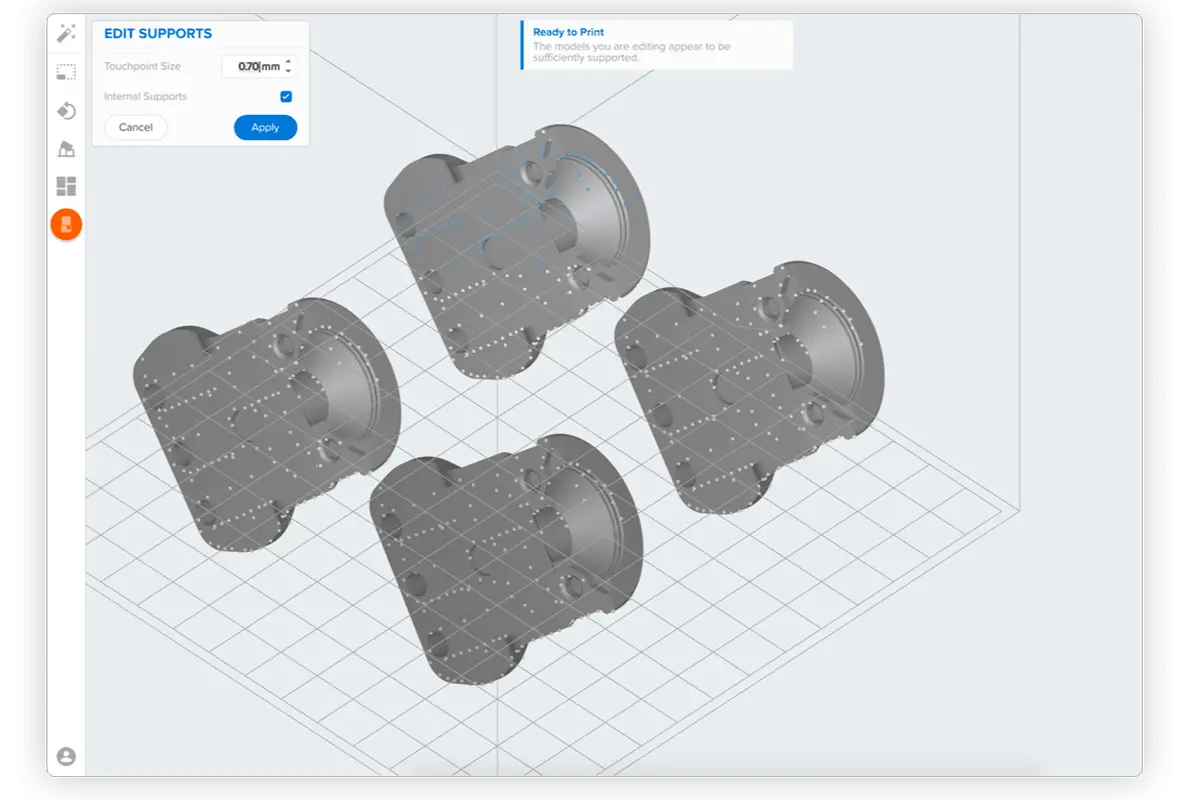
Le stampanti 3D creano le parti da modelli tridimensionali, le rappresentazioni matematiche di qualsiasi superficie tridimensionale realizzata tramite un software CAD o sviluppata a partire da dati di scansione 3D. Il design viene poi esportato come file STL o OBJ compatibile con il software di preparazione della stampa.
Ciascuna stampante SLA include un software per specificare le impostazioni di stampa e suddividere il modello digitale in strati che rappresentano le sezioni trasversali orizzontali del pezzo. Le impostazioni di stampa regolabili includono l'orientamento, le strutture di supporto (se necessarie), lo spessore dello strato e il materiale. Quando l'impostazione è stata completata, il software invia le istruzioni alla stampante via wireless o mediante connessione cavo.
2. Stampa 3D
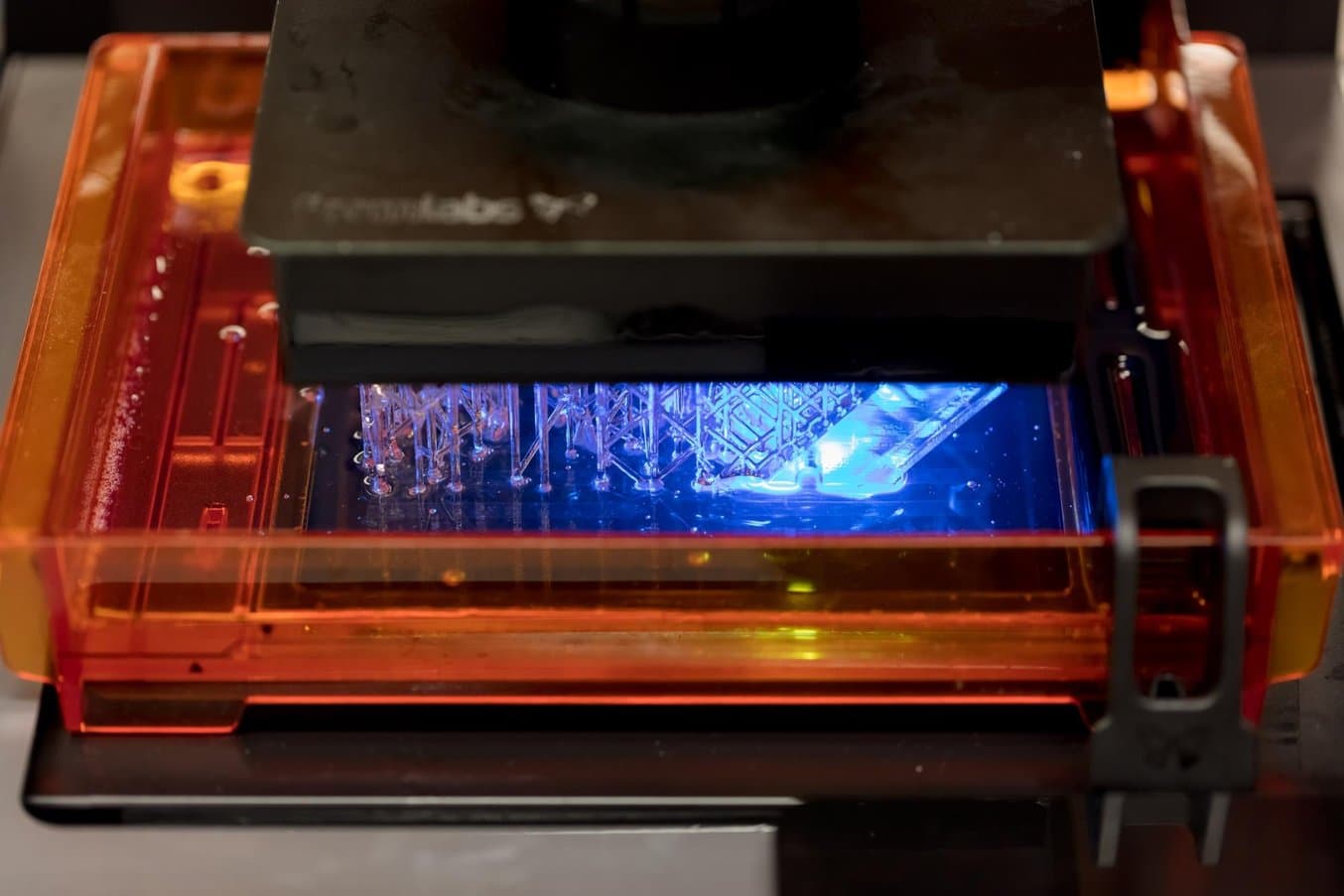
Alcune stampanti 3D utilizzano un laser per polimerizzare la resina liquida in plastica indurita, altre fondono piccole particelle di polvere di polimeri ad alte temperature per creare le parti. La maggioranza delle stampanti 3D può funzionare senza supervisione fino al completamento della stampa, e i sistemi moderni ricaricano automaticamente dalle cartucce il materiale necessario.
Con le stampanti 3D di Formlabs, un Dashboard online consente di gestire in remoto stampanti, materiali e team.
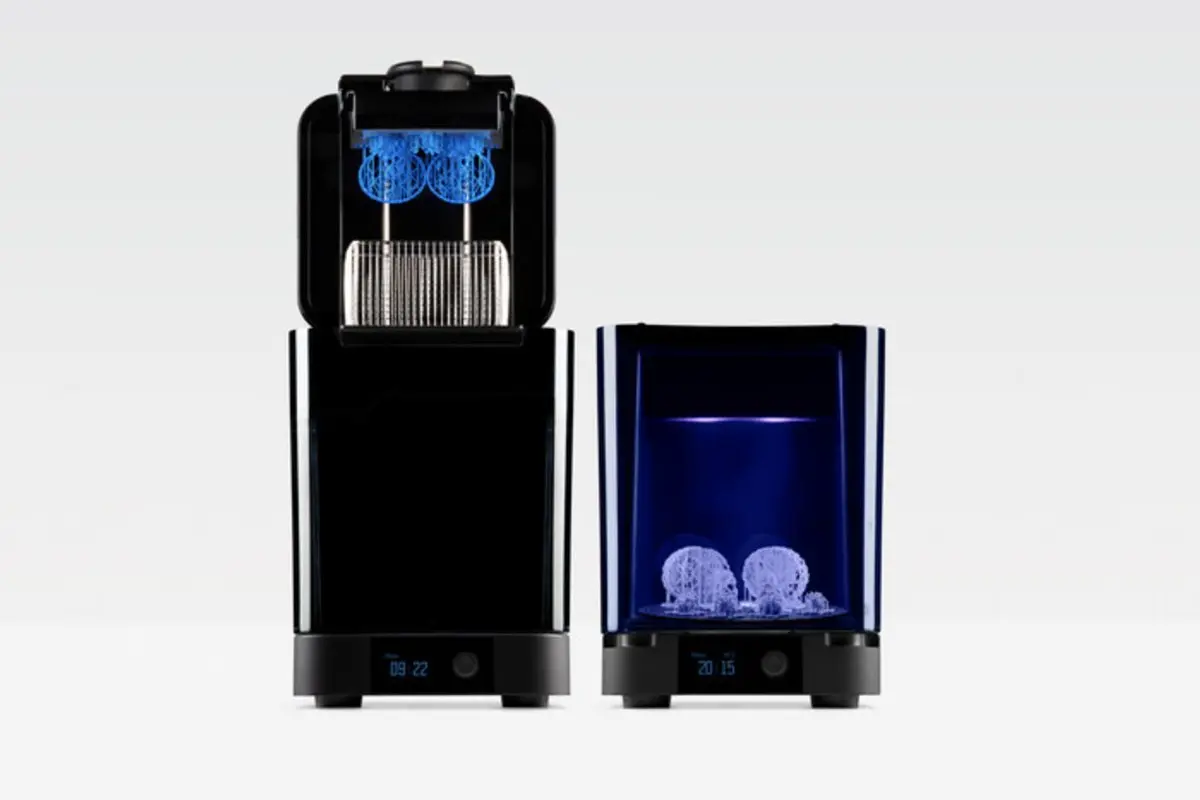
A seconda della tecnologia e del materiale, le parti stampate possono richiedere il risciacquo in alcool isopropilico per rimuovere dalla superficie la resina non polimerizzata, la polimerizzazione post-stampa per stabilizzarne le proprietà meccaniche, del lavoro manuale per rimuovere le strutture di supporto o una pulizia con aria compressa o una granigliatrice per rimuovere la polvere in eccesso. Alcuni di questi processi possono essere automatizzati tramite l'uso di accessori.
Le parti stampate in 3D possono essere utilizzate direttamente o sottoposte a post-elaborazione per applicazioni specifiche, e la finitura richiesta può essere ottenuta mediante lavorazione meccanica, applicazione del primer, verniciatura, fissaggio o giunzione. Spesso, la stampa 3D serve anche come fase intermedia rispetto ai metodi di produzione convenzionali, ad esempio per la realizzazione di stampi positivi nella fusione a cera persa di gioielli e apparecchi dentali, o come stampi per parti personalizzate.
3. Post-elaborazione
Come scegliere una tecnologia di stampa 3D
Non sai quale tecnologia di stampa 3D è più adatta alle tue esigenze? In questa guida confrontiamo le tecnologie di stampa 3D FDM, SLA ed SLS in base alle valutazioni di acquisto più comuni.
Ogni processo di stampa 3D ha vantaggi e limitazioni che lo rendono più o meno adatto a determinate applicazioni. Questo video confronta le caratteristiche funzionali e visive delle stampanti 3D a modellazione a deposizione fusa, stereolitografiche e a sinterizzazione laser selettiva per aiutarti a identificare la soluzione più adatta alle tue esigenze.
Hai bisogno di produrre parti o prototipi personalizzati in modo rapido? Rispetto all’esternalizzazione a fornitori di servizi o all’uso di strumenti tradizionali, come la lavorazione meccanica, l’implementazione di una stampante 3D in-house può farti risparmiare settimane in termini di tempo di realizzazione. In questo video, confrontiamo la velocità dei diversi processi di stampa 3D: modellazione a deposizione fusa, stereolitografia e sinterizzazione laser selettiva.
Il confronto delle diverse stampanti 3D in termini di costo va al di là del prezzo di listino, in quanto è importante considerare il costo delle parti stampate in 3D. Scopri i tre fattori da prendere in considerazione quando si analizzano i costi e come confrontarli per la stampa 3D a modellazione a deposizione fusa, stereolitografica e a sinterizzazione laser selettiva.
I vantaggi della stampa 3D
Dato che i processi di produzione additiva costruiscono oggetti aggiungendo materiale strato per strato, offrono un insieme unico di vantaggi rispetto ai tradizionali processi di produzione sottrattiva e formativa.
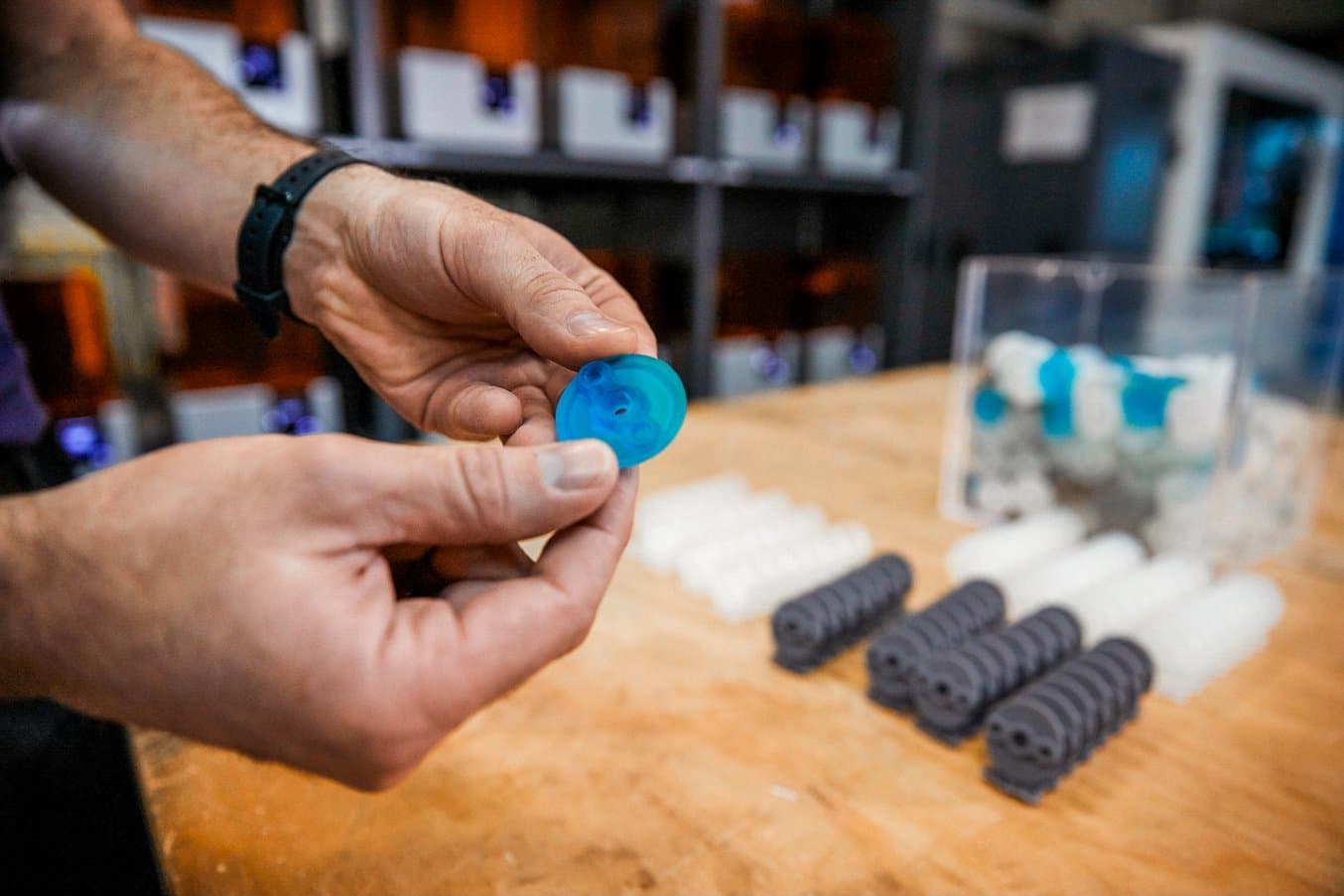
Velocità
Con i processi di fabbricazione tradizionali, possono essere necessarie settimane o mesi per ricevere una parte. La stampa 3D trasforma i modelli CAD in parti fisiche in poche ore, producendo unità e assemblaggi che vanno dai modelli concettuali unici ai prototipi funzionali e perfino le piccole serie di produzione per i test. Questo permette a progettisti e ingegneri di sviluppare idee più velocemente e aiuta le aziende a lanciare i prodotti sul mercato più rapidamente.
Gli ingegneri dell'AMRC si sono rivolti alla stampa 3D per produrre rapidamente 500 tappi per foratura ad alta precisione utilizzati nelle prove di trapanatura svolte per conto di Airbus, riducendo i tempi di realizzazione da diverse settimane a soli tre giorni.
Costo
Con la stampa 3D non sono necessari gli strumenti e le impostazioni costosi associati con lo stampaggio a iniezione o la lavorazione meccanica: la stessa attrezzatura può essere utilizzata per realizzare geometrie diverse in applicazioni che vanno dalla prototipazione alla produzione. A mano a mano che la stampa 3D consente sempre più spesso di produrre parti pronte per l'uso funzionali, può integrare o sostituire i metodi di produzione tradizionali per una gamma crescente di applicazioni a volumi medio-bassi.
Pankl Racing Systems ha sostituito dime e fissaggi lavorati a macchina con parti stampate in 3D, riducendo i costi dell'80-90% e risparmiando quindi 150 000 dollari.
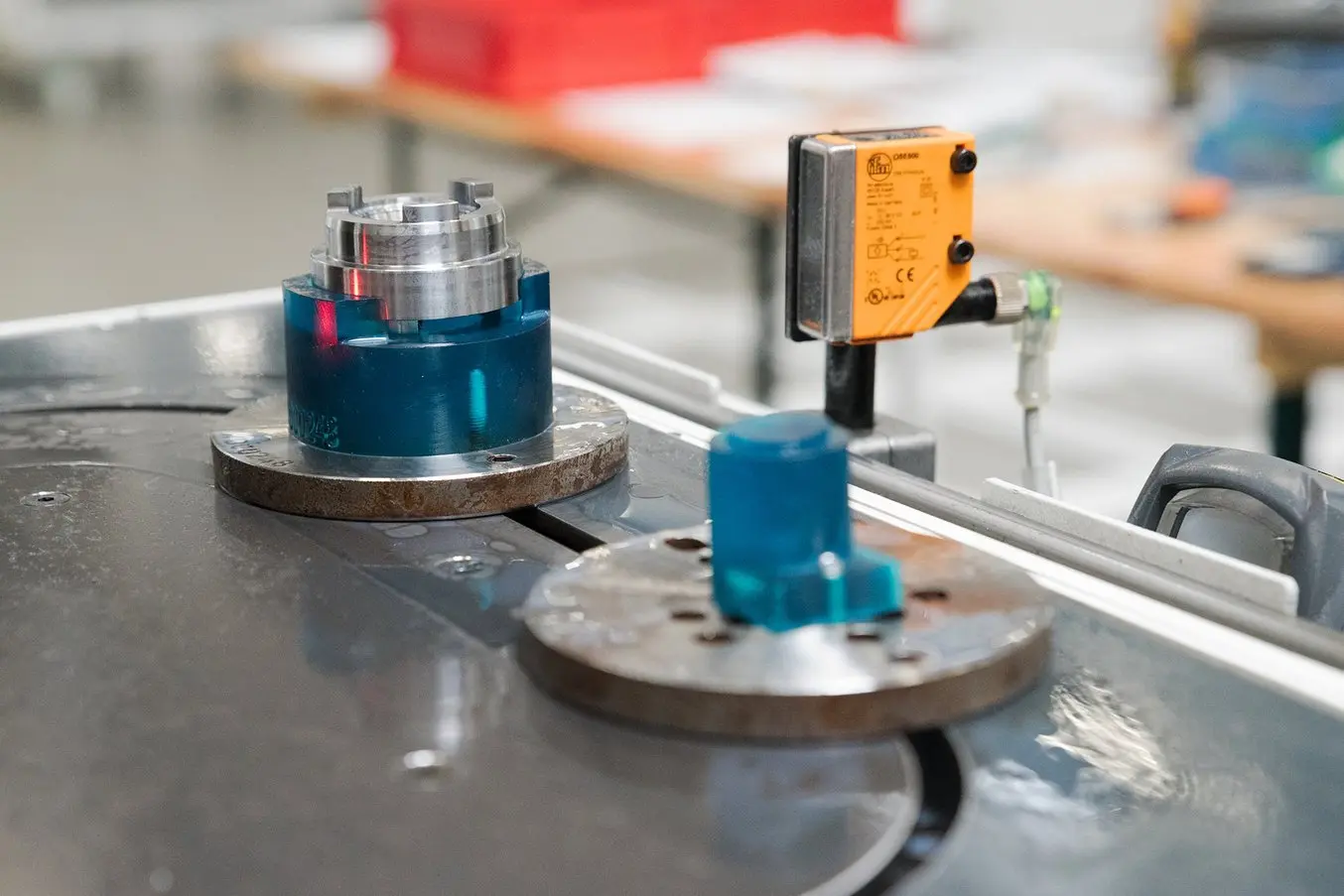
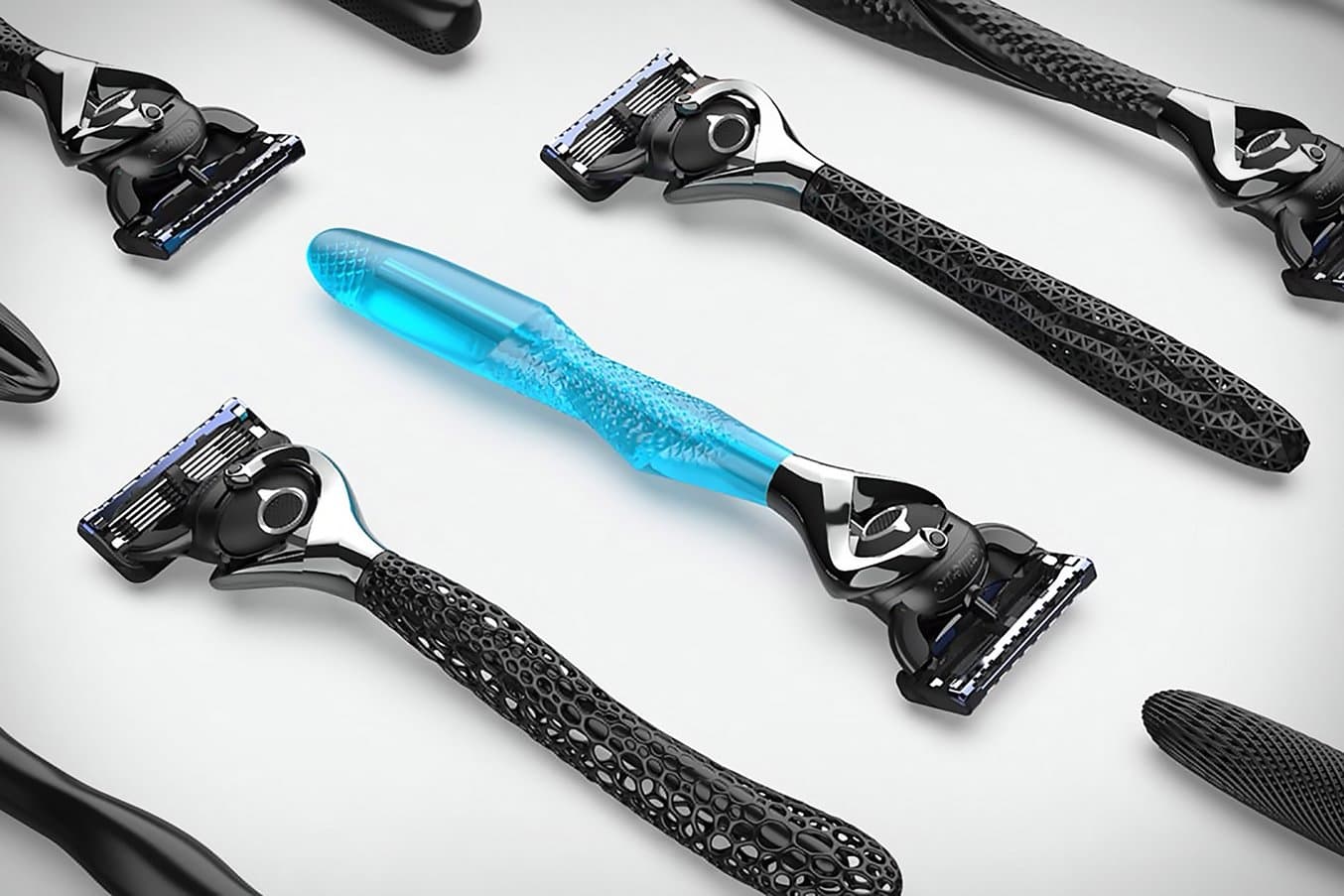
Personalizzazione
Dalle scarpe ai vestiti e le biciclette, siamo circondati da prodotti di dimensioni limitate e uniformi, perché le aziende cercano di standardizzare i prodotti per renderli economici da produrre. Con la stampa 3D basta modificare il design digitale per adattare ogni prodotto in base al cliente, senza costi aggiuntivi a livello di attrezzature. Questa trasformazione ha iniziato a prendere piede in settori in cui la personalizzazione è essenziale, come la medicina e l'odontoiatria ma, dato che la stampa 3D diventa sempre più accessibile, viene utilizzata in un numero crescente di casi per personalizzare in massa i prodotti di consumo.
Razor Maker™ di Gillette dà ai consumatori la possibilità di creare e ordinare manici di rasoio personalizzati stampati in 3D, avendo a disposizione 48 design diversi tra cui scegliere (e in continua crescita), una vasta gamma di colori e l'opzione di aggiungere del testo.
Libertà di design
La stampa 3D consente di creare forme e parti complesse, come sporgenze, microcanali e forme organiche, che sarebbero costose o addirittura impossibili da realizzare con i metodi di produzione tradizionali. Ciò offre l'opportunità di consolidare gli assemblaggi in meno parti singole per diminuire il peso, alleggerire i giunti deboli e ridurre i tempi di montaggio, offrendo nuove possibilità di progettazione e ingegnerizzazione.
Nervous System ha lanciato la prima linea di gioielli in ceramica stampati in 3D, composta da design complessi che sarebbe stato impossibile realizzare con qualsiasi altra tecnica di lavorazione della ceramica.
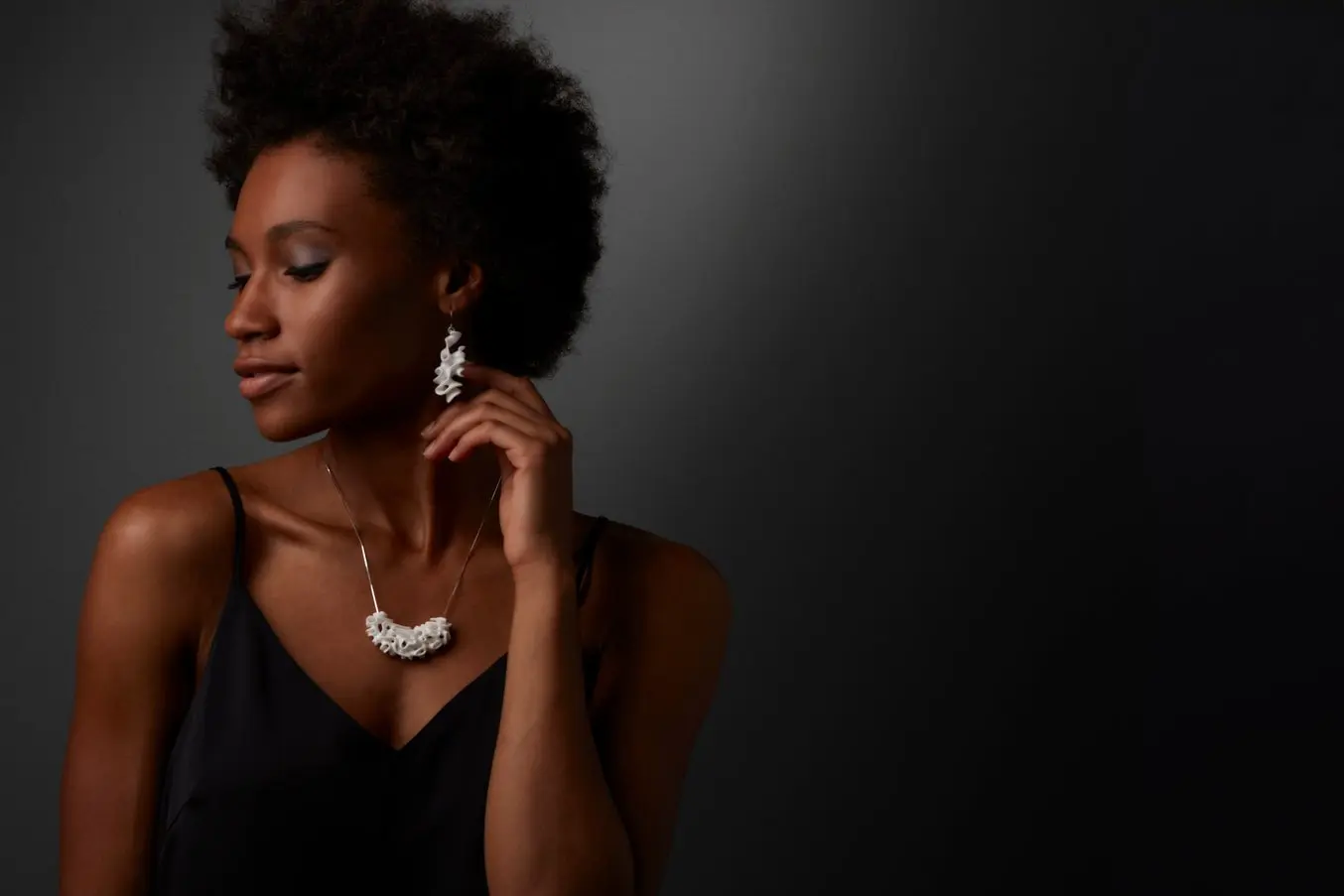
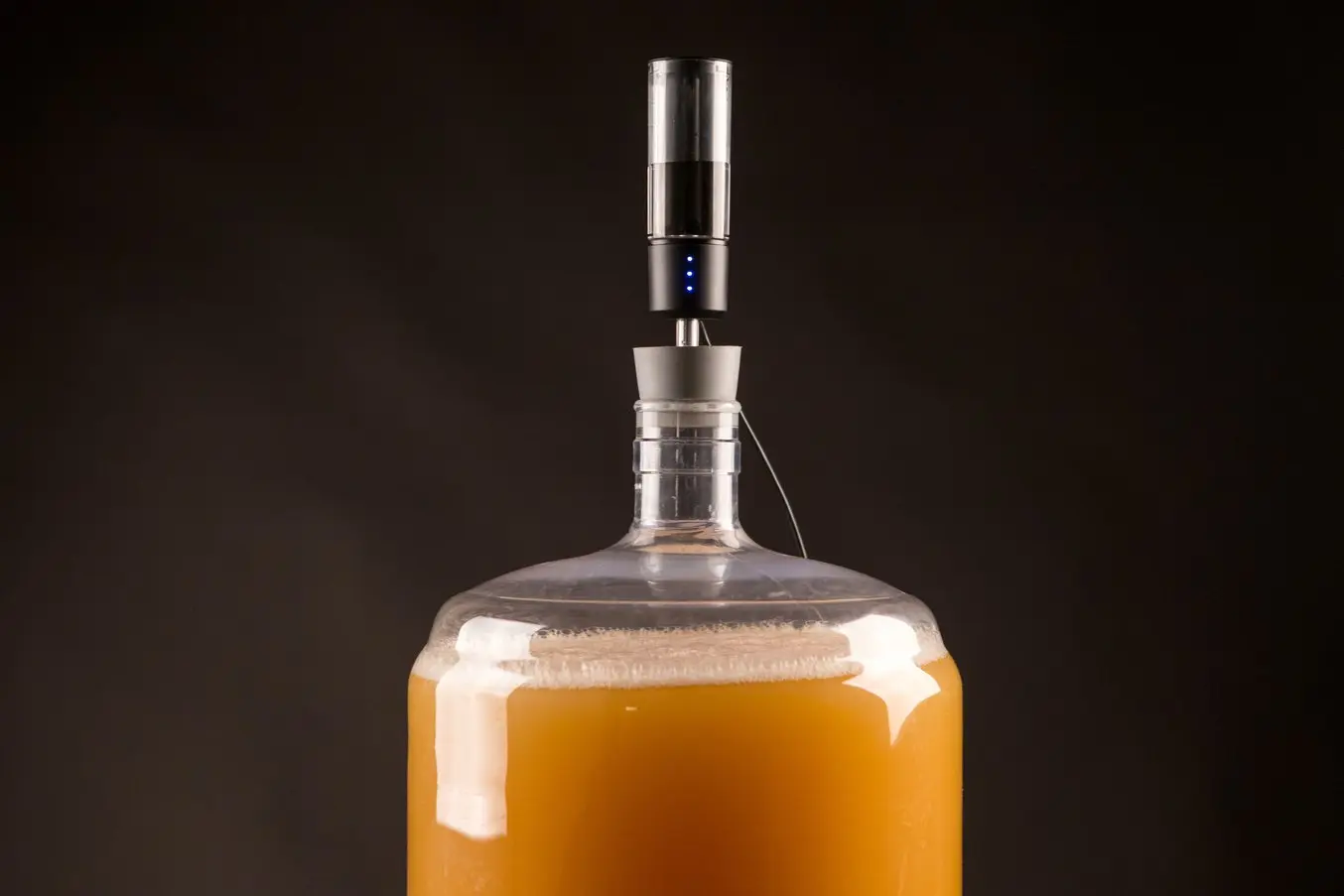
Rischio ridotto
Lo sviluppo del prodotto è un processo iterativo che richiede molteplici cicli di test, valutazione e perfezionamento. Se i difetti di design vengono rilevati durante le prime fasi, si possono evitare costose revisioni e modifiche delle attrezzature durante i passaggi successivi. Grazie alla stampa 3D, gli ingegneri possono eseguire test rigorosi su prototipi che hanno l'aspetto e la funzionalità dei prodotti finali, riducendo perciò il rischio di riscontrare problemi di usabilità e manifattura prima di avviare la produzione.
Gli sviluppatori di Plaato, una camera di compensazione trasparente per la realizzazione di birra artigianale, hanno stampato in 3D 1000 prototipi, così da perfezionare il loro progetto prima di investire in costose attrezzature.
Applicazioni e usi della stampa 3D
La stampa 3D accelera l'innovazione e sostiene le aziende in svariati settori, tra cui ingegneria, produzione, odontoiatria, medicina, istruzione, intrattenimento, gioielleria, audiologia e molto altro.
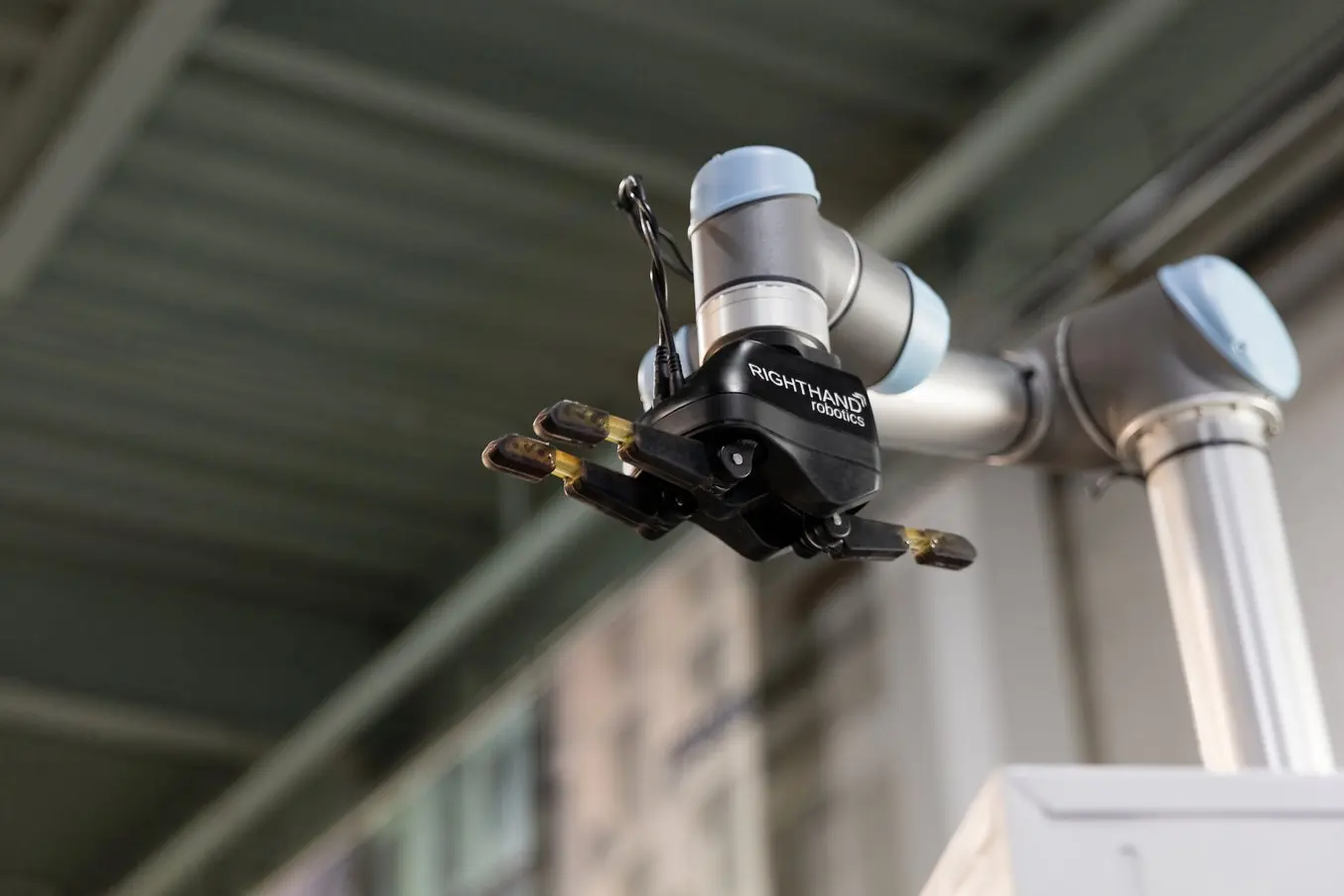
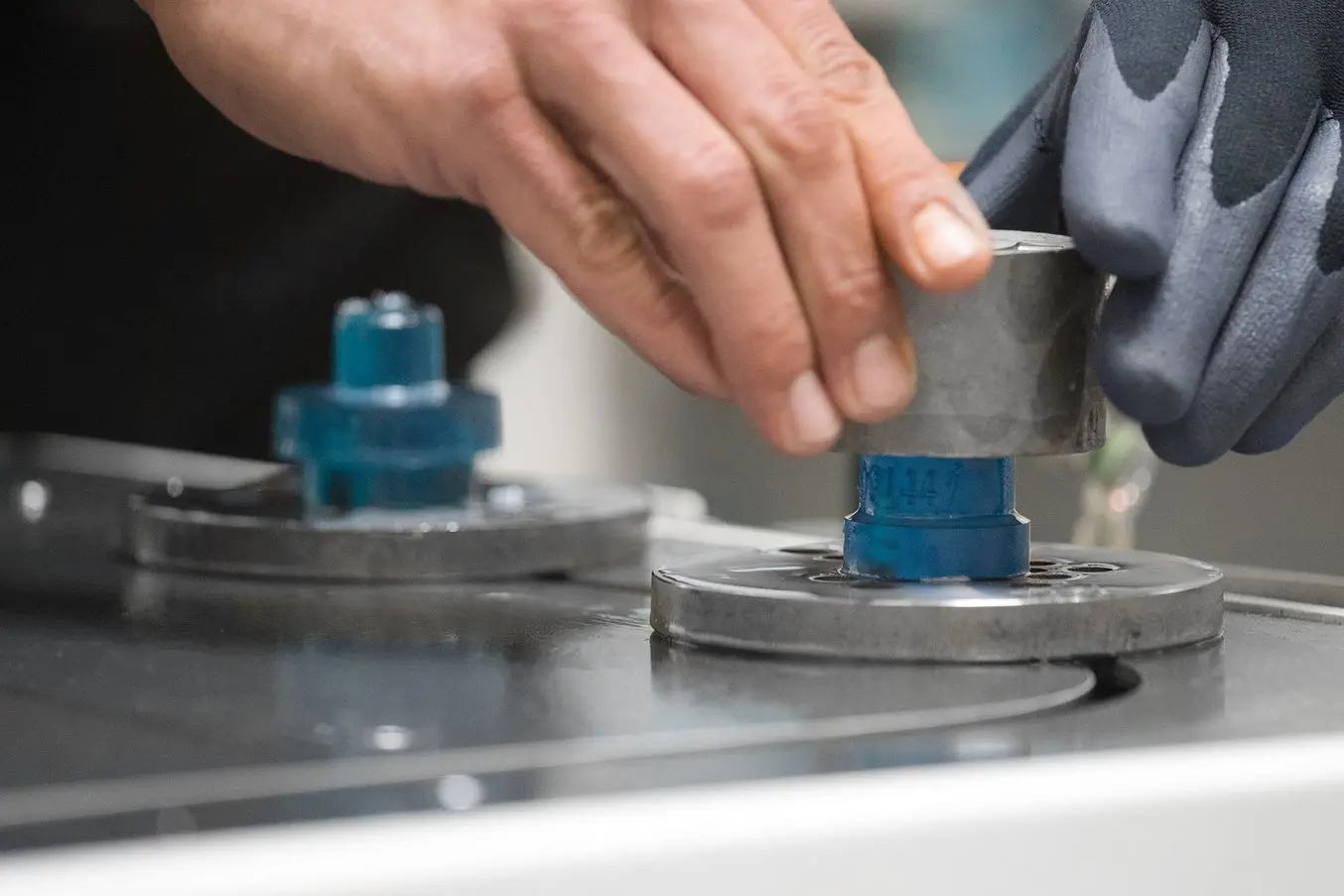
Produzione
I fabbricanti automatizzano i processi di produzione e snelliscono il workflow realizzando prototipi delle attrezzature e stampando direttamente in 3D strumenti, stampi e ausili di produzione su misura a un costo e con tempi di realizzazione inferiori rispetto alla manifattura tradizionale. Ciò consente di ridurre i costi e i difetti di fabbricazione, aumentare la qualità, velocizzare l'assemblaggio e massimizzare l'efficacia della manodopera.
Applicazioni:
- Dime e fissaggi
- Attrezzature
- Stampaggio (stampaggio a iniezione, sovrastampaggio)
- Fusione dei metalli
- Produzione a breve termine
- Produzione di massa su misura
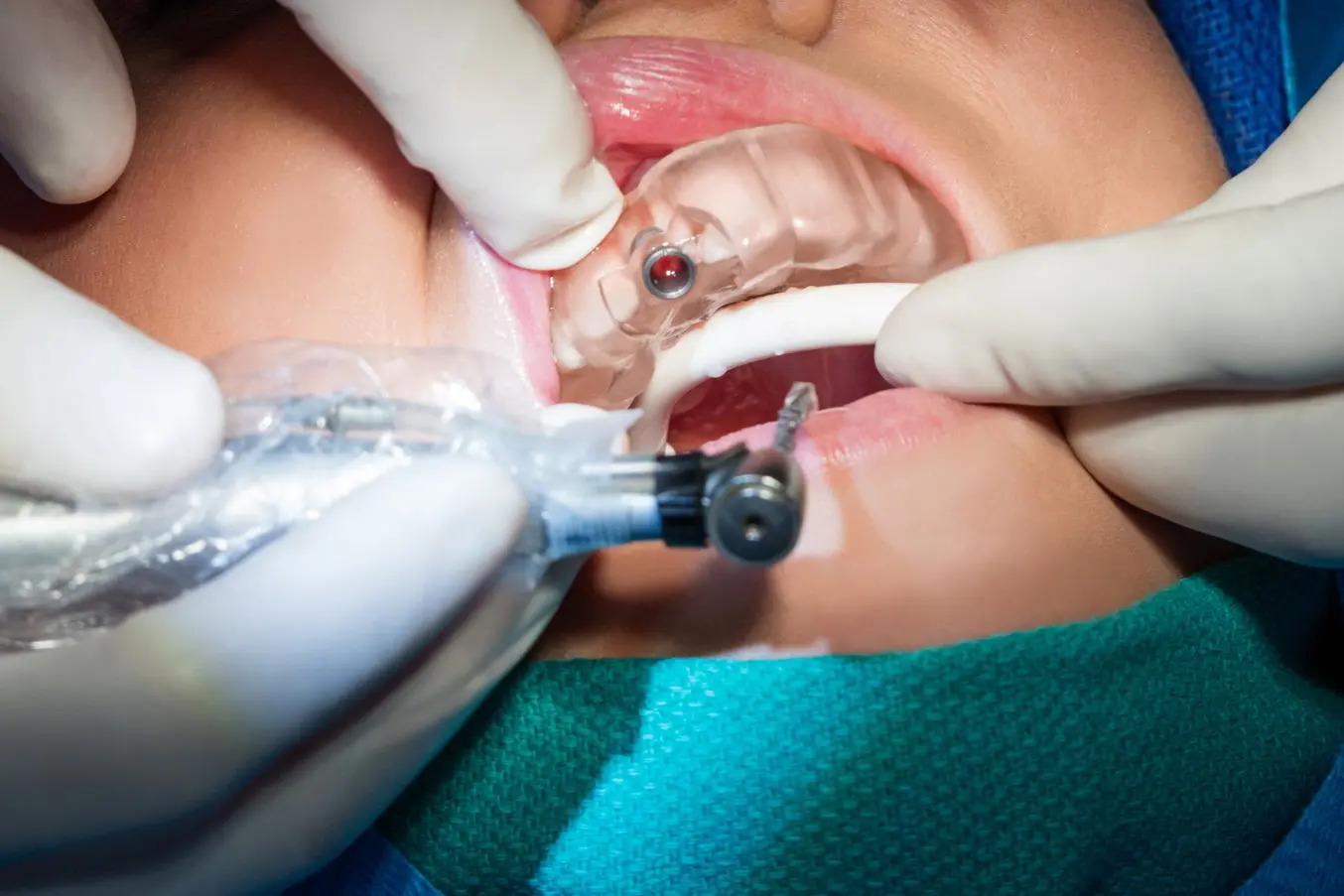
Odontoiatria
L'odontoiatria digitale riduce i rischi di incertezze introdotte da fattori umani, fornendo una maggiore uniformità, accuratezza e precisione in ogni fase del workflow per migliorare l'assistenza al paziente. Le stampanti 3D possono produrre una gamma di prodotti e dispositivi personalizzati di alta qualità a bassi costi unitari, con aggiustaggi migliori e risultati riproducibili.
Applicazioni:
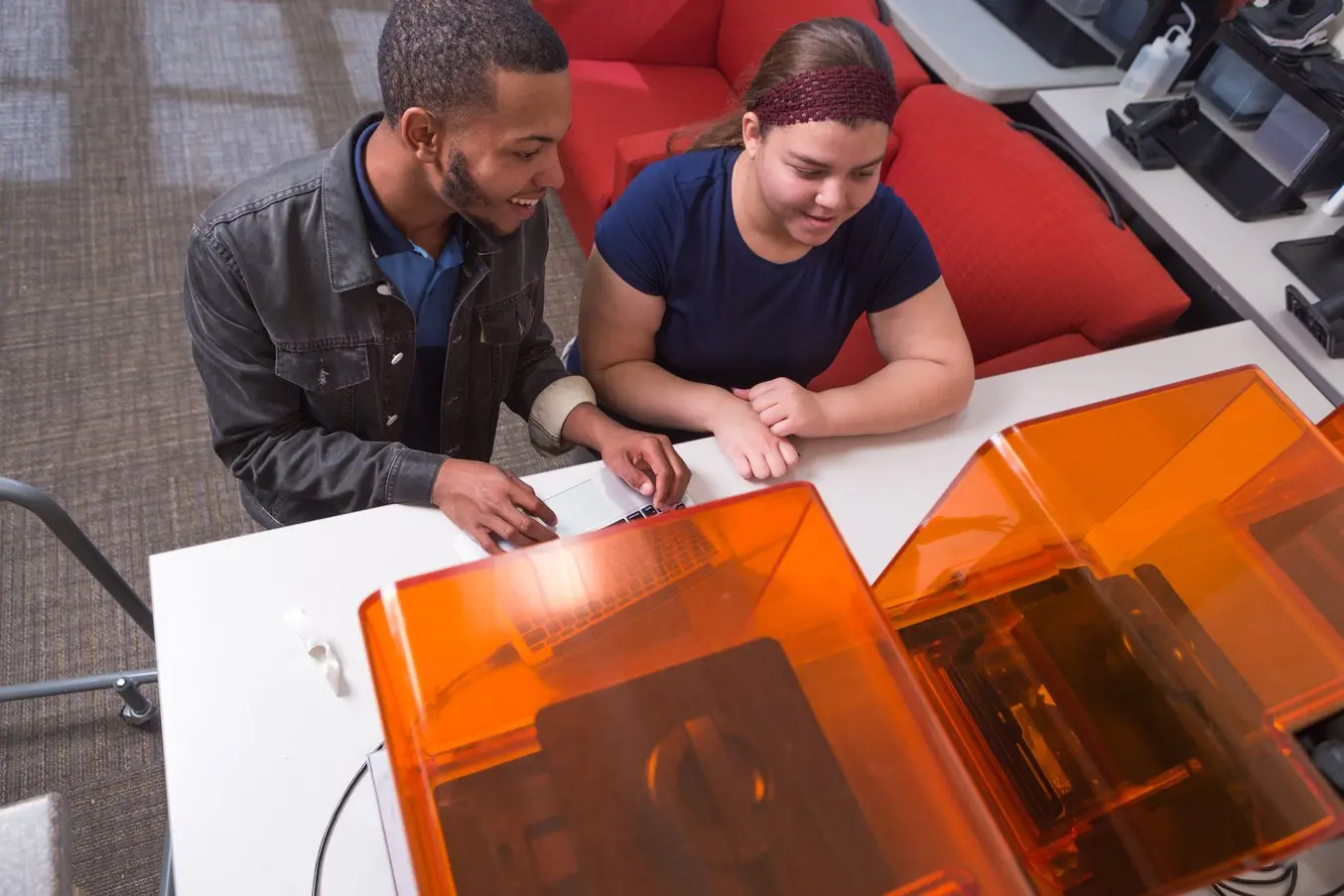
Istruzione
Le stampanti 3D sono strumenti multifunzionali per l'apprendimento approfondito e la ricerca avanzata. Sono in grado di incoraggiare la creatività e avvicinano gli studenti a tecnologie di livello professionale supportando i programmi STEAM nella scienza, ingegneria, arte e design.
Applicazioni:
- Modelli per i programmi STEAM
- Laboratori di fabbricazione e spazi creatori
- Postazioni di ricerca personalizzate
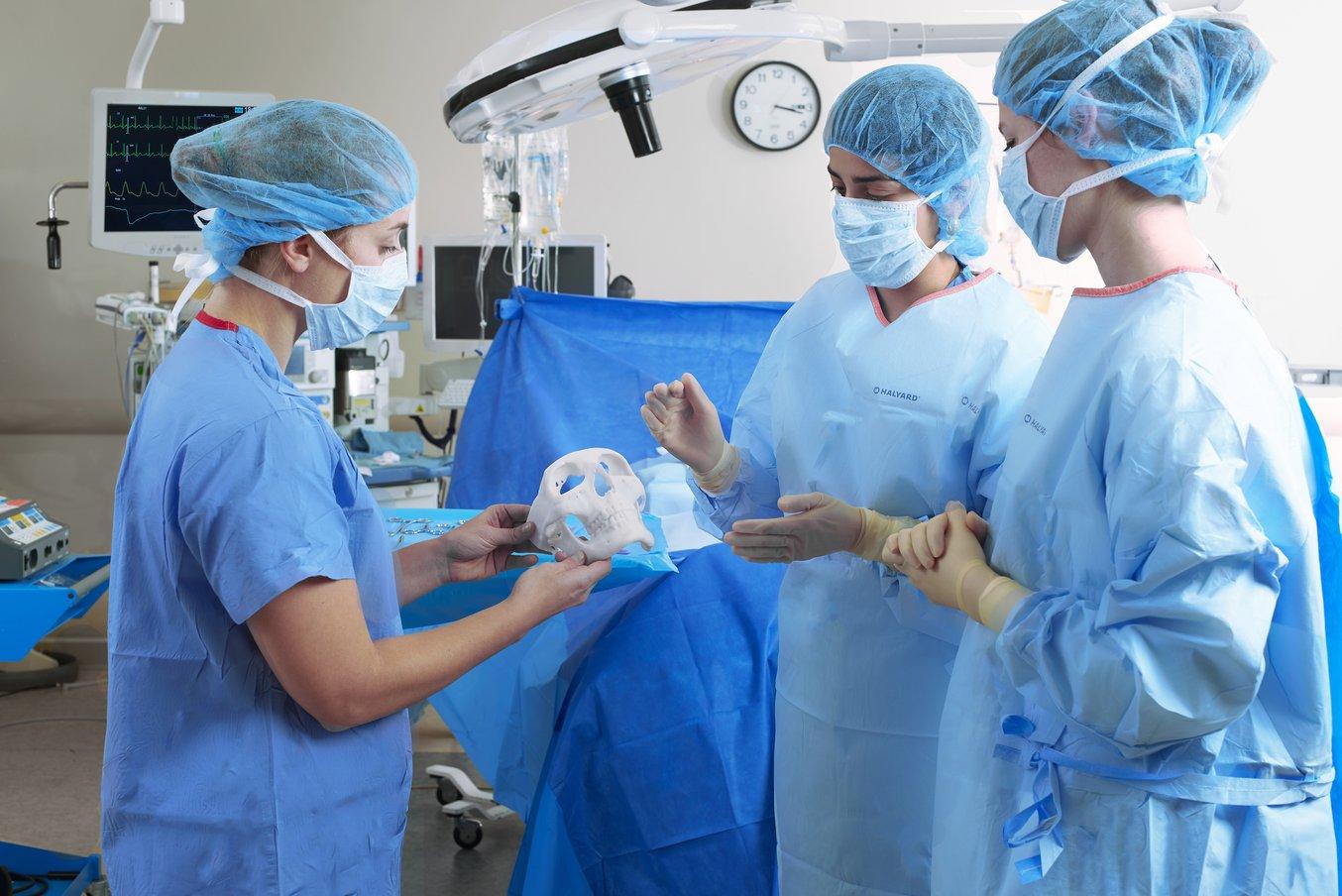
Medicina
La stampa 3D desktop economica e professionale aiuta i medici ad effettuare trattamenti e creare dispositivi su misura per servire in modo migliore l'individuo, aprendo le porte ad applicazioni medicali di alto impatto, allo stesso tempo consentendo alle organizzazioni un significativo risparmio di tempo e costi, dal laboratorio alla sala operatoria.
Applicazioni:
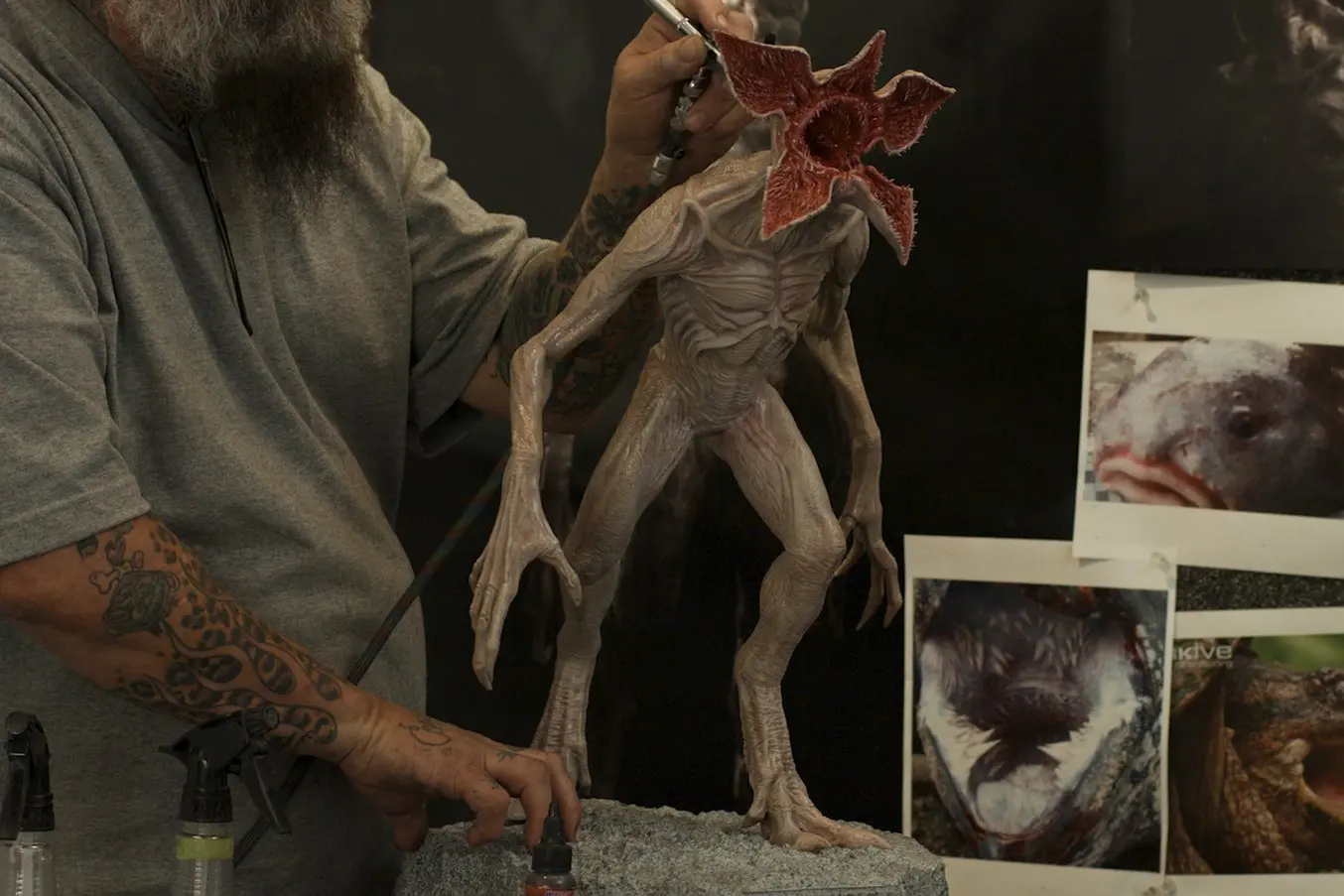
Intrattenimento
I modelli fisici ad alta definizione sono ampiamente usati nella scultura, nel modellismo di personaggi e nella produzione di materiale scenico. Le parti stampate in 3D hanno presenziato in film stop-motion, videogiochi, costumi personalizzati e addirittura in effetti speciali nelle superproduzioni cinematografiche.
Applicazioni:
- Sculture iper-realistiche
- Modelli di personaggi
- Oggetti di scena
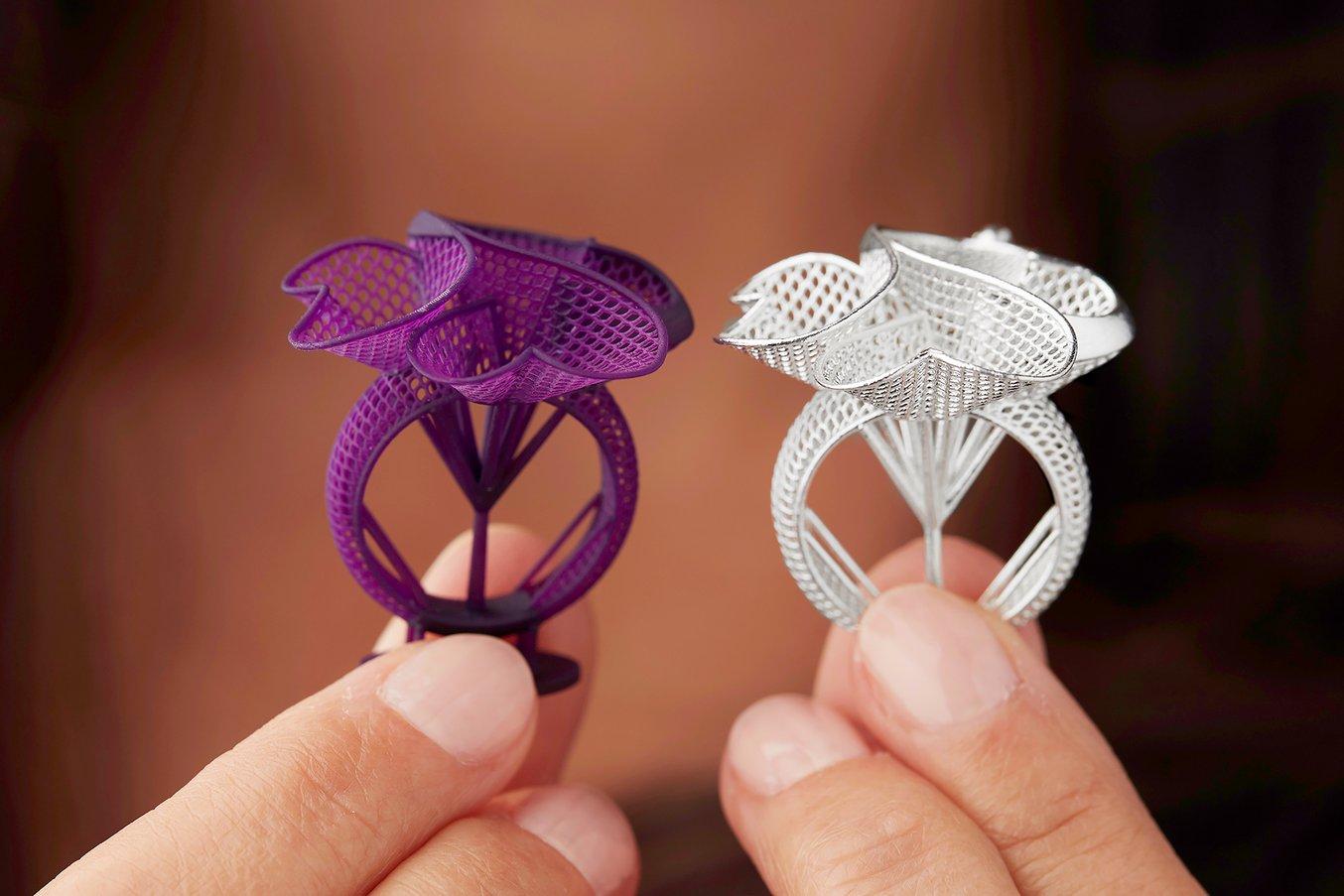
Gioielleria
I gioiellieri professionisti usano i software CAD e la stampa 3D per effettuare prototipazioni rapide di progetti, eseguire adattamenti per clienti e produrre lotti numerosi di pezzi pronti per la fusione. Gli strumenti digitali consentono di ottenere parti uniformi e dettagliate, senza i problemi e l'instabilità che si presentano con l'intaglio in cera.
Applicazioni:
- Fusione a cera persa
- Pezzi di montaggio
- Modelli master per lo stampaggio della gomma
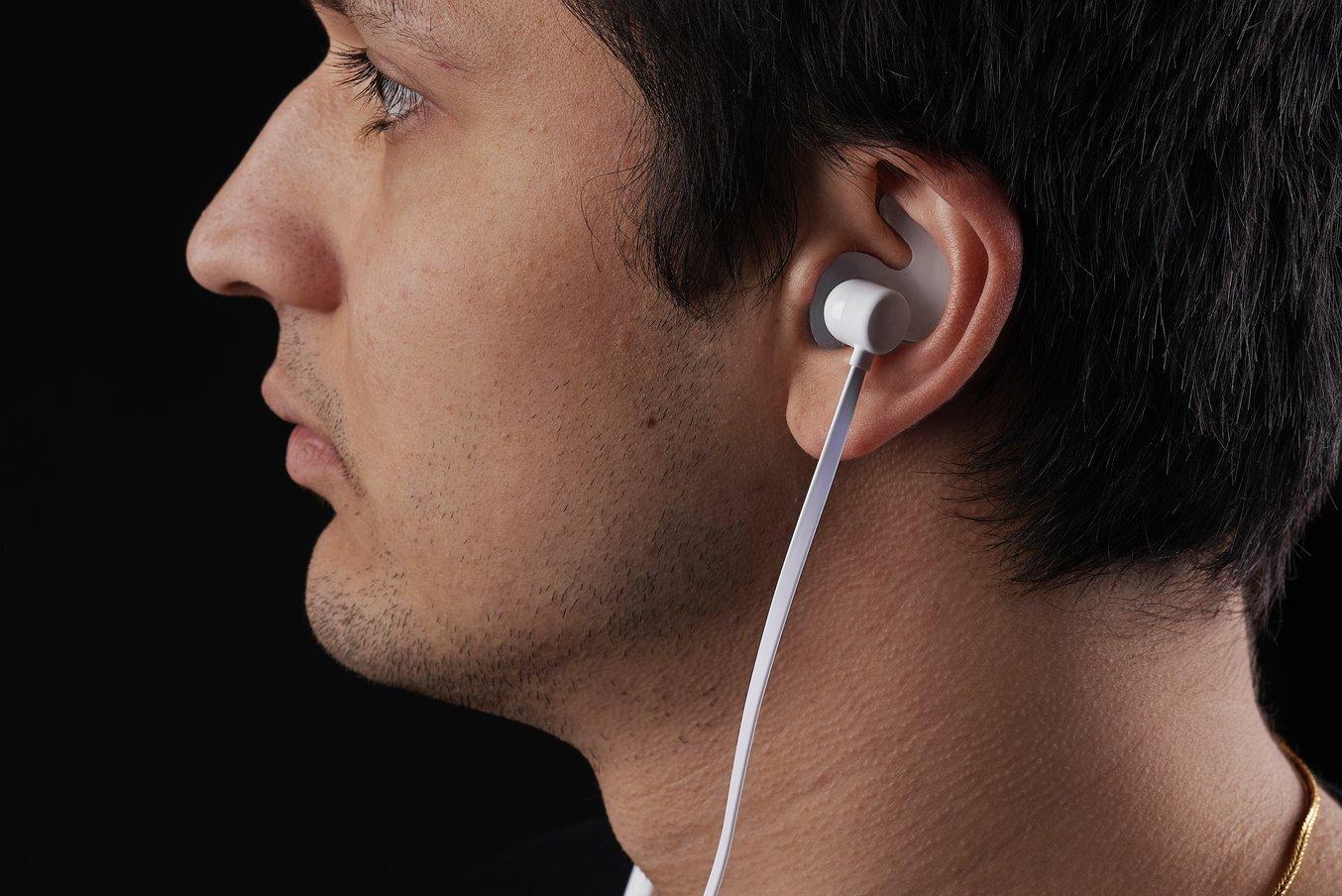
Tipi di stampanti 3D
Formlabs offre due tecnologie professionali di stampa 3D, la stereolitografia e la sinterizzazione laser selettiva, portando questi strumenti di fabbricazione industriale potenti e accessibili nelle mani creative dei professionisti in tutto il mondo.
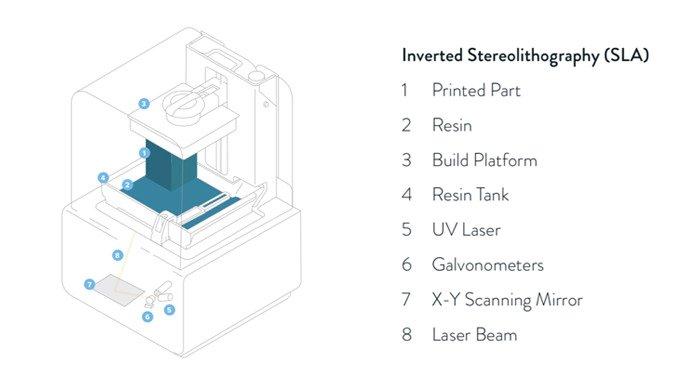
Stereolitografia (SLA)
Come funziona la stereolitografia
La stampa 3D stereolitografica (SLA) utilizza un laser per polimerizzare la resina fotopolimerica liquida in parti isotrope solide.
Con il processo più comune, la stereolitografia invertita, una piattaforma di stampa viene immersa in un serbatoio di resina, lasciando solo un sottile strato di liquido tra la piattaforma e il fondo del serbatoio. I galvanometri dirigono il laser attraverso una finestra trasparente sul fondo del serbatoio resina, tracciando una sezione trasversale del modello 3D e indurendo in maniera selettiva il materiale. La stampa viene realizzata in strati consecutivi, ognuno dei quali ha uno spessore inferiore a cento micron. Le strutture di supporto mantengono le sporgenze ancorate alla piattaforma, se necessario. Quando uno strato è completo, la parte viene staccata dal fondo del serbatoio, lasciando fluire la resina fresca al di sotto, e la piattaforma viene nuovamente abbassata. Questo processo si ripete fino al completamento della stampa.
La stereolitografia è ideale per:
- Prototipazione rapida
- Prototipazione funzionale
- Creazione di modelli concettuali
- Produzione a breve termine
- Applicazioni odontoiatriche
- Prototipazione e fusione a cera persa per gioielleria
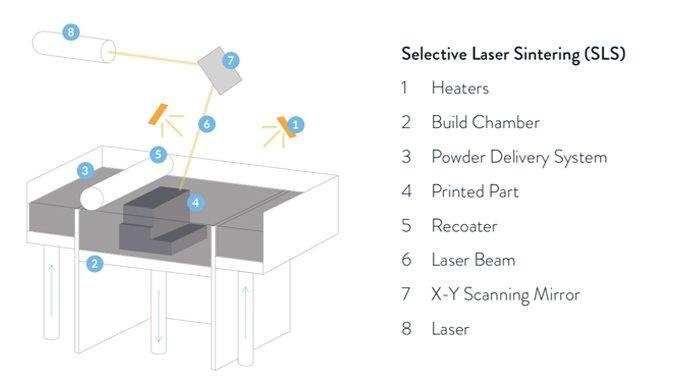
Sinterizzazione laser selettiva (SLS)
Come funziona la sinterizzazione laser selettiva
Le stampanti 3D a sinterizzazione laser selettiva (SLS) utilizzano un laser ad alta potenza per sinterizzare piccole particelle di polvere di polimeri in una struttura solida.
Uno strato sottile di polvere viene disposto sopra una piattaforma all'interno della camera di stampa e la stampante preriscalda la polvere a una temperatura appena inferiore al punto di fusione del materiale grezzo. Il laser scansiona una sezione trasversale del modello 3D, fondendo meccanicamente le particelle per creare una parte solida. La polvere non fusa sostiene la parte durante il processo di stampa ed elimina la necessità di strutture di supporto dedicate. La piattaforma si abbassa di un livello all'interno della camera di stampa, di solito intorno ai 50-200 micron, e uno strumento apposito cosparge un nuovo strato di polvere. Il laser scansiona quindi la sezione trasversale successiva della stampa e questo processo si ripete per ogni strato fino al completamento delle parti.
La sinterizzazione laser selettiva è ideale per:
- Prototipazione funzionale
- Parti per uso finale
- Manifattura personalizzata, ponte o a breve termine
Materiali per la stampa 3D
Il mercato dei materiali per la stampa 3D è ampio e in continua crescita, con stampanti per tutto, dalle materie plastiche ai metalli, e persino per alimenti e tessuti vivi in fase di sviluppo. Formlabs offre la seguente gamma di materiali fotopolimerici per la stampa desktop.
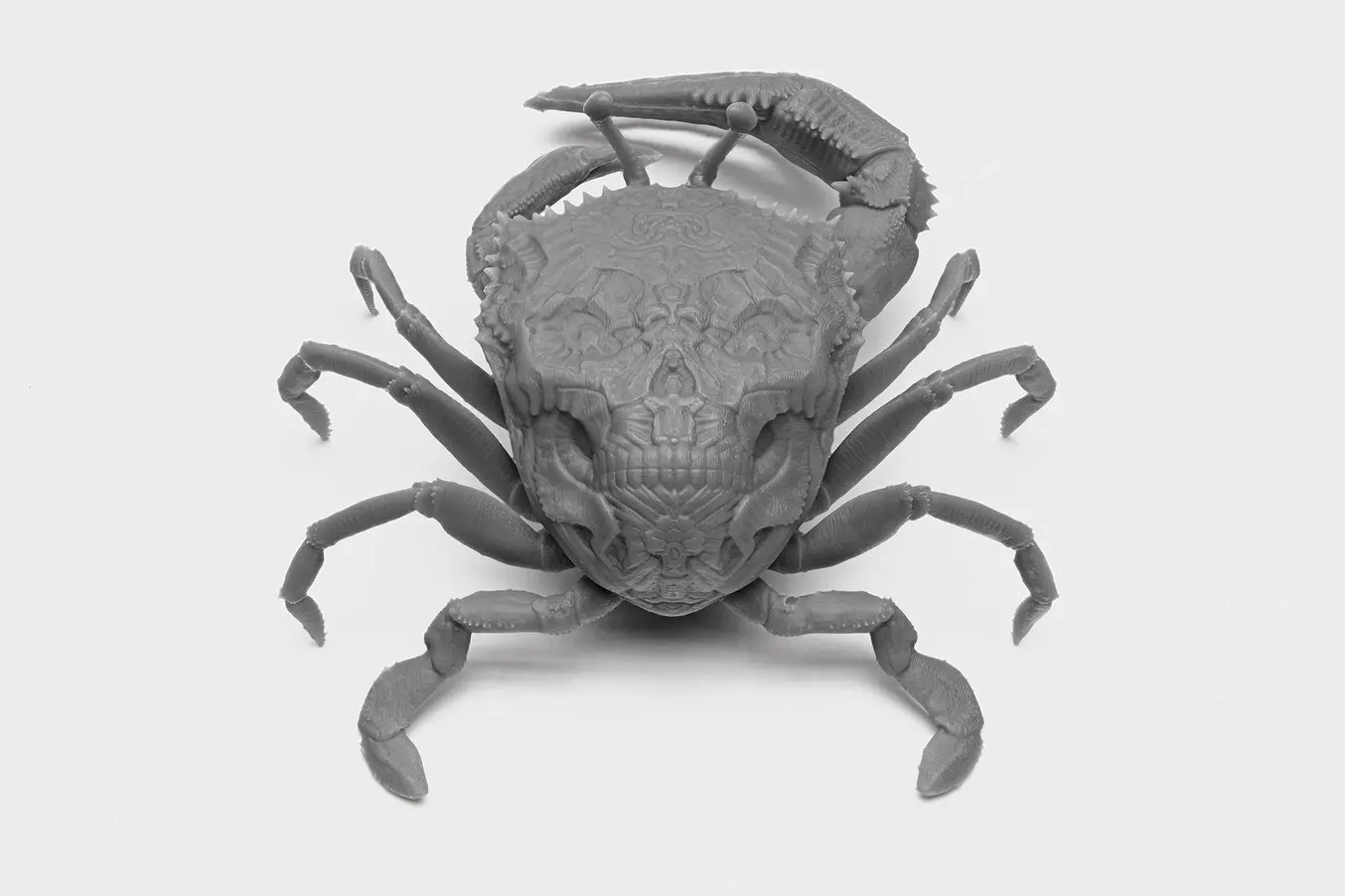
Standard
I materiali di stampa 3D standard offrono alta risoluzione, particolari precisi e una finitura superficiale liscia ideale per la prototipazione rapida, lo sviluppo di prodotti e le applicazioni di modellazione generale.
Questi materiali sono disponibili in Black Resin, White Resin e Grey Resin, con finitura e aspetto opachi, trasparenti per tutte le parti che richiedono traslucidità e come kit di colori per abbinarli a quasi tutti i colori personalizzati.
Ingegneria
I materiali di stampa 3D per l'ingegneria, la produzione e il design di prodotto sono formulati per fornire funzionalità avanzate, resistere a test approfonditi, ottenere buone prestazioni se sottoposti a sollecitazioni e rimanere stabili nel tempo.
I materiali ingegneristici sono ideali per la stampa 3D di modelli concettuali e prototipi resistenti e precisi, per eseguire iterazioni rapide di più design, valutare forma e aderenza e ottimizzare i processi di fabbricazione.
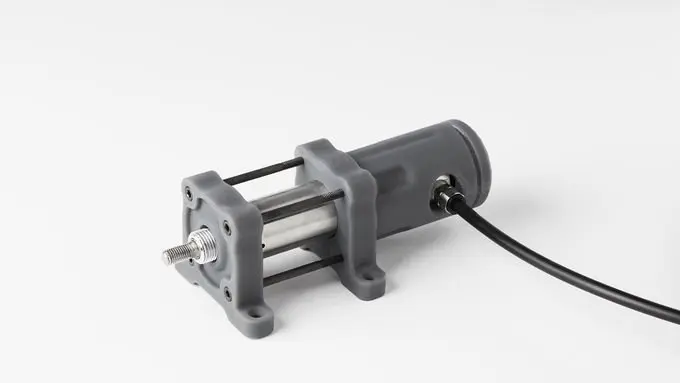
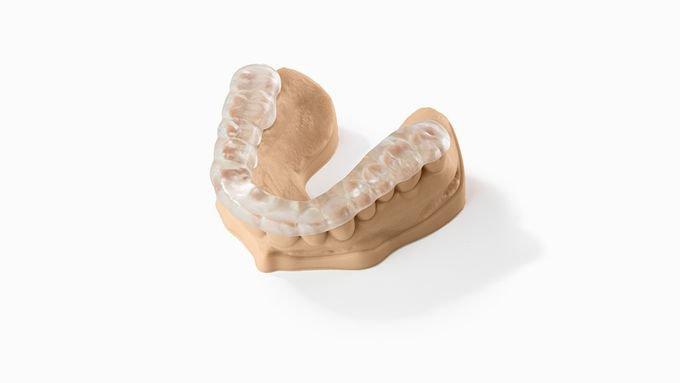
Odontoiatria
Le resine dentali consentono ai laboratori odontotecnici e agli studi dentistici di produrre rapidamente e a costi contenuti una gamma di prodotti odontoiatrici, da modelli dentali a dime chirurgiche biocompatibili, bite dentali e modelli ortodontici per la termoformatura di retainer e allineatori.
Gioielleria
Le resine per gioielleria sono create in modo da consentire di riprodurre dettagli mozzafiato e realizzare gioielli su misura a costi più contenuti. Queste resine sono ideali per la prototipazione e la fusione di gioielli, così come la gomma vulcanizzata e la vulcanizzazione a temperatura ambiente.
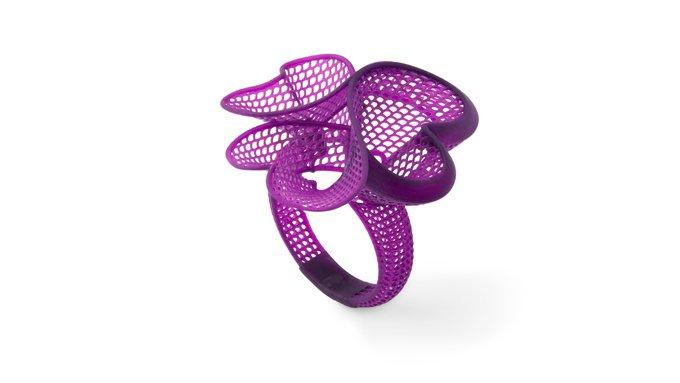
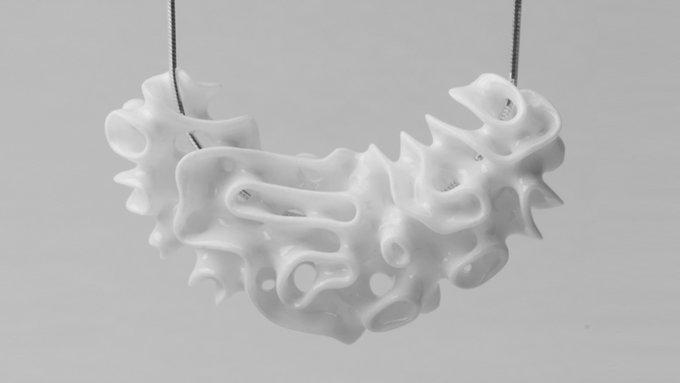
Ceramica
Materiale sperimentale che allarga l'orizzonte di possibilità di creazione con la stampa 3D, la Ceramic Resin è stata sviluppata per la realizzazione di parti con una finitura simile alla pietra e la cottura per creare un pezzo completamente in ceramica. Fabbrica parti in ceramica per la ricerca ingegneristica o per creare oggetti artistici e insoliti pezzi di design.
Costi della stampa 3D e ritorno d'investimento
Negli ultimi anni, le stampanti industriali 3D ad alta risoluzione sono diventate più accessibili, intuitive e affidabili. Di conseguenza, la tecnologia è ora accessibile a un maggior numero di imprese. Leggi la nostra guida approfondita sui costi della stampa 3D, oppure prova il nostro strumento interattivo e scopri se questa tecnologia è adatta per la tua attività dal punto di vista economico.

Nozioni base di stampa 3D e FAQ
È la prima volta che senti parlare di stampa 3D? Esplora le nostre guide per scoprire i termini chiave e le caratteristiche specifiche della stampa 3D e trovare la soluzione più adatta alla tua attività.
Richiedi un campione stampato in 3D
Guarda e tocca con mano la precisione di Formlabs e scopri i nostri materiali per trovare quello più adatto alle tue esigenze.