Alternative alla stampa 3D in metallo: i procedimenti di fusione a cera persa e fusione in sabbia
Anche se la stragrande maggioranza delle parti nei prodotti con cui interagiamo ogni giorno sono ormai fatte di plastica, molte applicazioni continuano a richiedere la resistenza e la durevolezza del metallo.
La stampa 3D diretta in metallo è stata pubblicizzata come un metodo rapido per creare parti quasi finali in materiali resistenti come il titanio, ma gli alti costi delle attrezzature, la necessità di tecnici specializzati e una scelta di leghe limitata hanno ridotto l’uso di questa tecnologia ad applicazioni molto particolari e di alto valore.
Le stampanti 3D stereolitografiche (SLA) sono spesso considerate principalmente come strumenti per creare parti in plastica, ma la loro elevata precisione e l’ampia gamma di materiali disponibili le rendono idonee alla produzione di parti metalliche a costi ridotti, con una maggiore libertà di design e in meno tempo rispetto ai metodi tradizionali.
Leggi il nostro white paper per scoprire come usare al meglio la velocità e la flessibilità della stampa 3D senza dover affrontare il costo delle stampanti per metalli usando i workflow di fusione del metallo. Continua a leggere per avere una panoramica sui fondamenti della fusione da modelli stampati in 3D, tra cui la fusione diretta a cera persa, la fusione indiretta a cera persa e la fusione in sabbia.
Whitepaper: introduzione alla fusione dei metalli con la stampa 3D
I fondamenti della fusione dei metalli
Per applicazioni in cui le parti richiedono dettagli ben definiti o forme complesse, la fusione rimane un processo di fabbricazione molto efficiente a livello di costi e risultati ed è usata per componenti critici nel settore aerospaziale, automobilistico e medico.
La fusione del metallo risale almeno all’anno 3200 a.C. ed è passata attraverso diversi cicli di evoluzione fino a diventare il processo moderno e affidabile che conosciamo oggi. Attualmente i procedimenti industriali di fusione del metallo sono usati per applicazioni che vanno dagli impianti per le ginocchia fino alle parti per trattori.
Il processo di base per creare parti in metallo fuso presenta dei tratti in comune con altre tecniche:
- Il fabbricante crea un modello che rappresenta la parte sotto forma di elemento rimovibile per creare un'impronta su un materiale come la sabbia o all’interno del materiale dello stampo stesso per poi effettuare la colata.
- In entrambi i casi abbiamo una cavità con la forma del modello in cui viene versato il metallo fuso.
- Il metallo fuso viene fatto raffreddare e lo stampo viene aperto o rotto per recuperare l’oggetto.
- Le parti fuse presentano tracce del processo nei punti in cui fori, aperture o canali dirigono il flusso di gas e metallo fuso durante la fusione. Infine, un operatore della fonderia taglia via il materiale in eccesso e poi lima, gratta, sabbia o lavora a macchina le parti fuse per ottenere la forma e la superficie richieste. In alcuni casi le parti fuse sono trattate ad alte temperature.
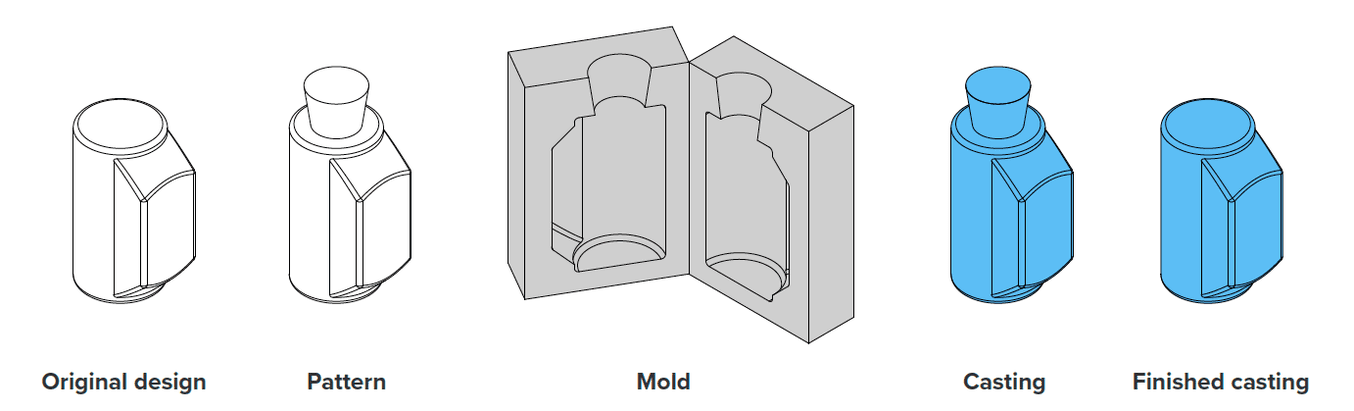
Un’illustrazione delle fasi dal design originale fino alla fusione finale.
In ogni procedimento di fusione devono essere fabbricate due forme di base: un modello e uno stampo. Il modello è praticamente una versione leggermente modificata della parte da produrre.
Il design del modello presenta alcune differenze rispetto alla forma della parte finale:
- Le dimensioni dei modelli vengono ampliate per compensare il restringimento che avviene durante la fusione.
- Spesso i modelli contengono elementi necessari al procedimento di fusione ma che non saranno presenti nella parte finale (ad esempio aperture per permettere il flusso controllato del metallo, sfiati per la liberazione di gas, ecc.).
- Alcuni elementi del modello possono essere di dimensioni maggiori o riempiti per operazioni secondarie usate per produrre elementi a tolleranza molto ristretta (foratura, svuotamento, ecc.).
Normalmente i modelli sono fatti di legno, schiuma, plastica o cera. A volte il design del modello contiene elementi relazionati con il procedimento di fusione, come aperture per permettere il flusso del metallo.
Lo stampo include il negativo del modello insieme a canali di colata, aperture, sfiati, scanalature e altri elementi per controllare il flusso di metallo e gas durante la fusione.
Gli stampi possono essere fatti di diversi materiali (ceramica, grafite, gesso, sabbia) e devono essere in grado di resistere alle alte temperature e le sollecitazioni meccaniche del procedimento di fusione.
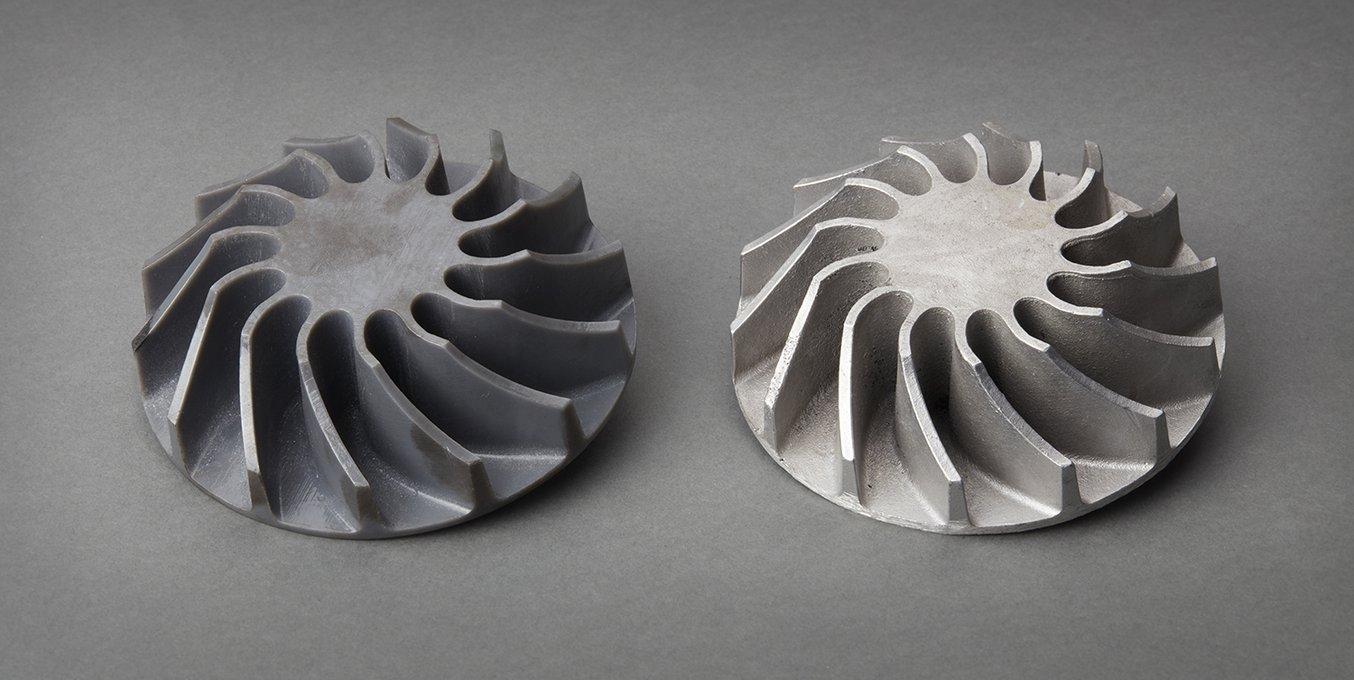
La fabbricazione di parti di metallo con la stampa 3D
Scopri le linee guida di progettazione per creare modelli stampati in 3D, esplora passo a passo il procedimento di fusione diretta a cera persa e le linee guida per la fusione indiretta a cera persa e la fusione in sabbia.
Scarica il whitepaperFusione diretta a cera persa
Il procedimento di fusione diretta a cera persa passa direttamente dalla creazione di un modello a ricoprirlo con materiale di rivestimento. Poiché il metodo di creazione di modelli a iniezione di cera comporta varie fasi, viene considerato indiretto.
La fusione diretta a cera persa è più indicata per piccole produzioni o la sperimentazione iniziale su una nuova parte, poiché ogni parte stampata dovrà essere sottoposta a processi di rifinitura. La fusione diretta a cera persa è una buona scelta anche per parti più grandi o parti con sezioni trasversali più spesse che potrebbero essere difficili da modellare con cera perché tendono a deformarsi o a restringersi.
La fusione diretta a cera persa è utile per la produzione di parti con forme troppo complesse da stampare o parti con ampi sottosquadri e dettagli di superficie sottili dove lo stampaggio è possibile ma richiede un forte investimento in attrezzature.
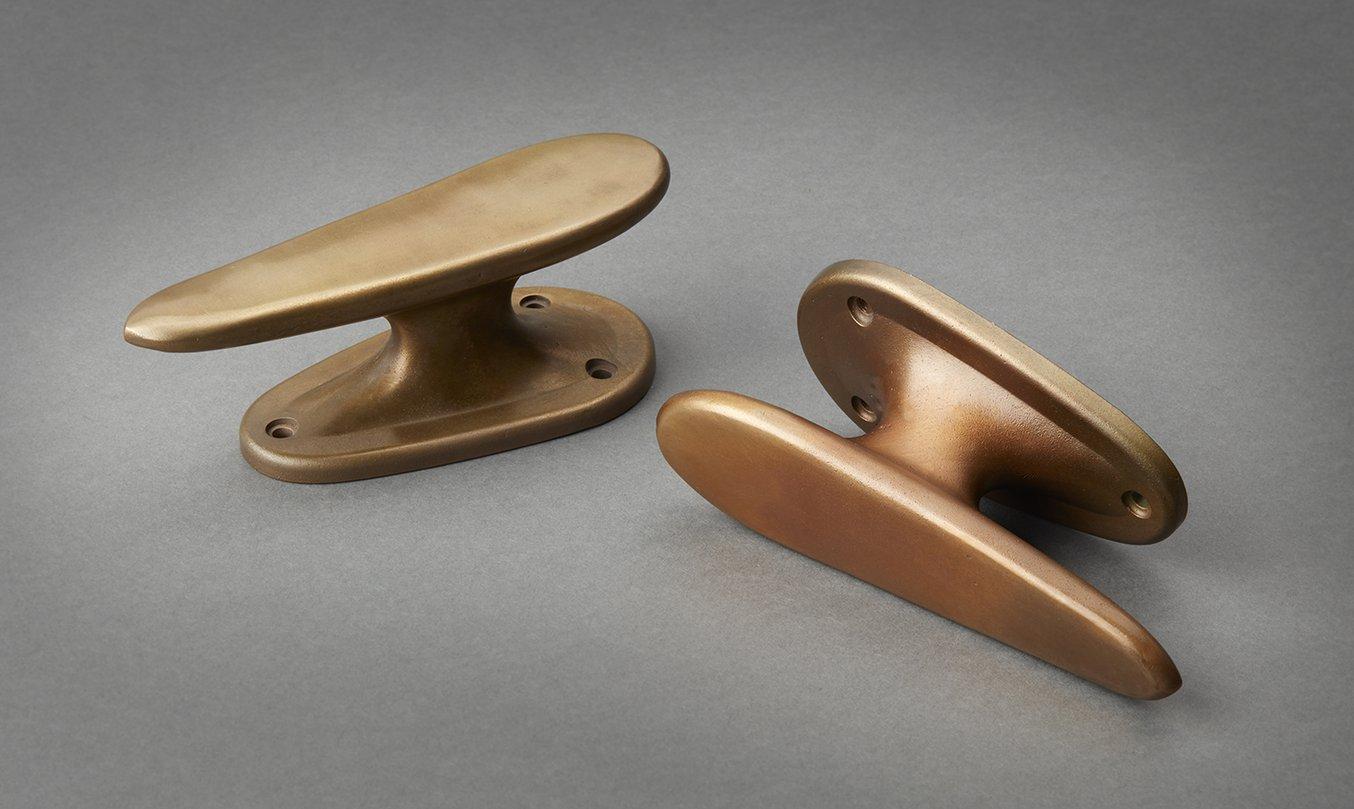
Parti fuse da modelli SLA stampati con la Clear Resin su una stampante 3D di Formlabs.
Tradizionalmente i modelli per la fusione diretta a cera persa venivano intagliati a mano o creati a macchina se dovevano essere prodotte solo poche unità della parte.
Con l’avvento della stampa 3D, gli ingegneri hanno cominciato a sperimentare con la stampa diretta dei modelli, per poter ridurre i tempi di produzione e avere una libertà con le forme che andasse oltre i limiti di fabbricabilità imposti dai processi di stampaggio.
Fusione indiretta a cera persa
Il processo di creazione di modelli da stampi o attrezzature viene chiamato fusione indiretta a cera persa perché, appunto, richiede la creazione di stampi per produrre i modelli oltre agli stampi di fusione finali.
Gli stampi rigidi per la cera normalmente vengono fabbricati attraverso la lavorazione meccanica di alluminio o acciaio. La produzione di questi stampi di metallo costa migliaia di dollari e richiede settimane di lavorazione meccanica e rifiniture prima che possano essere usati, e che le parti possano essere valutate all’interno di un procedimento di fusione. Stampando le attrezzature direttamente, gli ingegneri e i progettisti possono ridurre i tempi che intercorrono tra la progettazione e i primi test da settimane a pochi giorni.
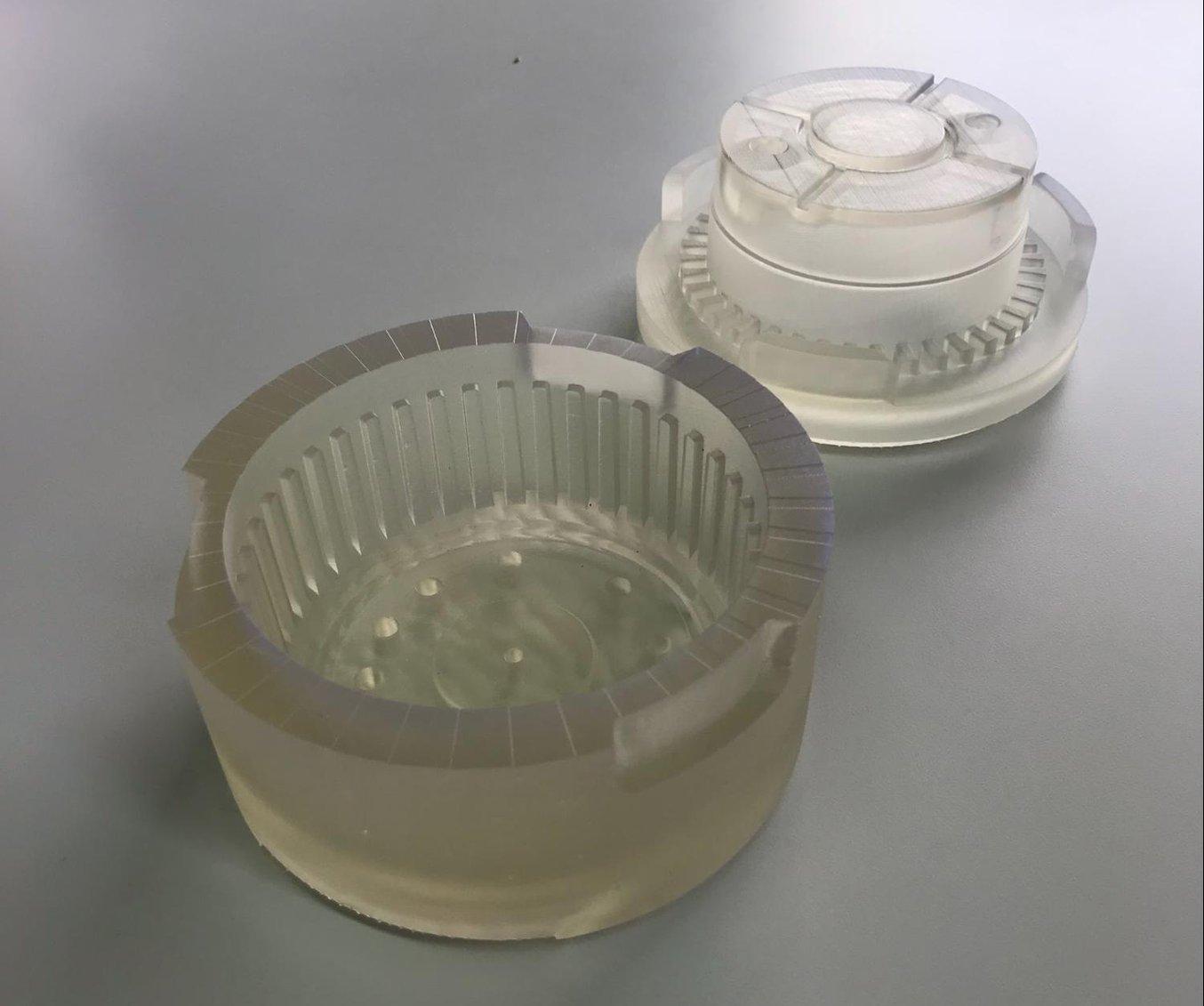
Stampo per iniezione di cera stampato in 3D con la Clear Resin.
Gli stampi per la produzione di modelli in cera possono essere stampati con la High Temp Resin. Per una finitura superficiale ottimale, si consiglia di levigare e lucidare le superfici interne, se si ha bisogno di uno stampo liscio, o sabbiarle per renderle uniformemente opache.
Per assicurarsi che le parti finali siano delle dimensioni corrette, si consiglia di creare uno stampo leggermente più grande per compensare il restringimento. Le percentuali di restringimento della cera durante il procedimento di fusione si possono trovare nelle specifiche del fornitore.
Anche se i pezzi stampati devono seguire specifiche regole di design per lo stampaggio (evitare sottosquadri, lo sformo è utile, ecc.), si possono ottenere modelli più complessi usando dime di assemblaggio per combinare diversi componenti in un’unica struttura.
Fusione in sabbia
Nel procedimento di fusione con sabbia, il personale della fonderia riempie dei contenitori chiamati telai di gettata o staffe con un miscuglio di sabbia e legante, e poi ammassa la sabbia intorno al modello. Il modello viene rimosso creando una cavità in cui viene poi versato il metallo fuso.
Per parti con elementi su una sola faccia è possibile usare uno stampo aperto. Le parti con elementi su diverse superfici richiedono stampi a cavità chiusa con un contenitore superiore e uno inferiore.
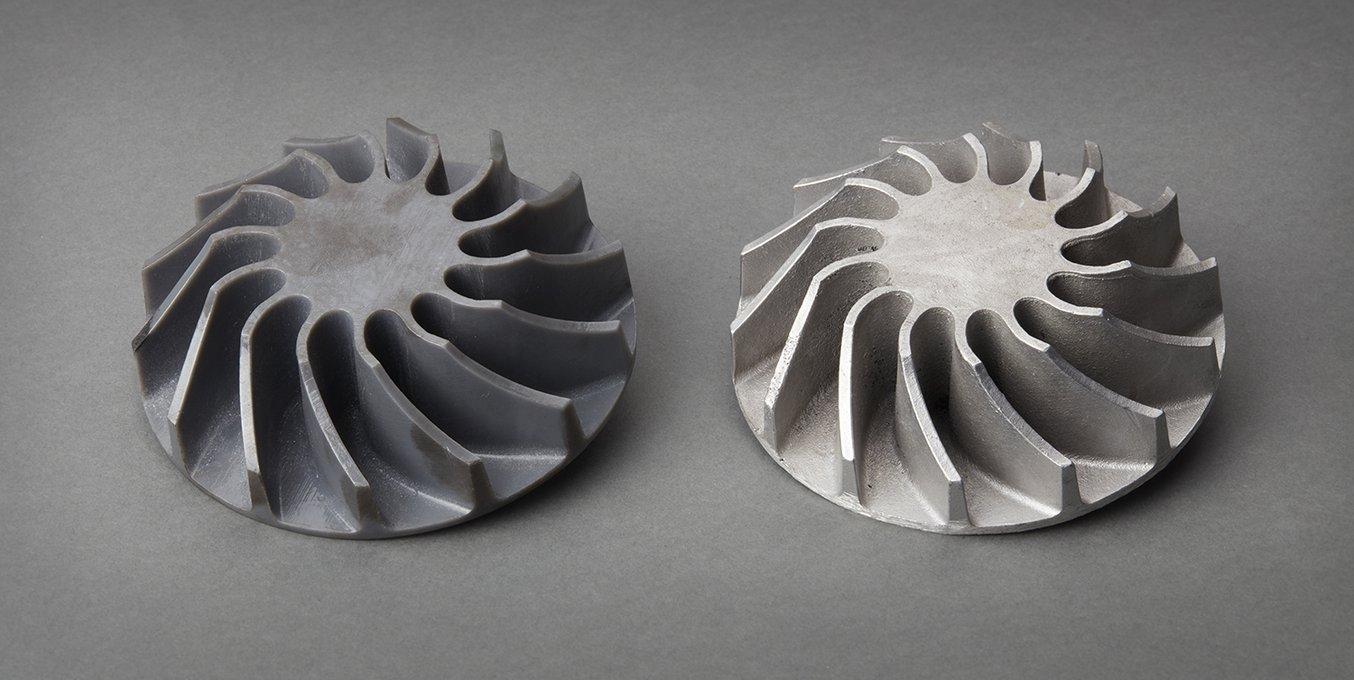
Modello stampato con la Grey Resin e colata finale in alluminio creata con uno stampo a una sola faccia.
Negli stampi chiusi, il metallo passa attraverso un sistema di chiuse prima di raggiungere la cavità della parte. Il sistema di chiuse è studiato appositamente per minimizzare le imperfezioni estetiche dovute a una colata di metallo non ottimale.
Gli stampi di sabbia a cavità chiusa a volte utilizzano dei nuclei sospesi per creare cavità interne nella fusione finale, ad esempio per i gruppi motore o gli alloggiamenti per pompe.
La fabbricazione di parti di metallo con la stampa 3D
Le stampanti SLA desktop forniscono alle fonderie una vasta gamma di soluzioni a basso costo per la produzione dei modelli e delle attrezzature, garantendo la precisione necessaria per i design delle moderne parti fuse.
Aggiungendo la stampa 3D ai tradizionali flussi di lavoro delle fonderie, i fabbricanti possono rispondere più rapidamente alle richieste dei clienti, rimandare gli investimenti in attrezzature e verificare i design in maniera economica. Inoltre, l'uso sempre più esteso dell'ottimizzazione topologica nell'ingegneria e nello sviluppo dei prodotti porta a una maggiore richiesta di forme che possano essere create attraverso la stampa diretta di modelli.
Creazione dei modelli e metodi di fusione a confronto
Parti di piccole dimensioni | Parti di grandi dimensioni | Piccoli dettagli/finiture di superficie lisce su una parte fusa | Libertà con le forme | |
---|---|---|---|---|
Fusione a cera persa: modello stampato direttamente con la Castable Wax Resin | Sì | No | Sì | Alta |
Fusione a cera persa: modello stampato direttamente con la Clear Resin | No | Sì | Sì | Alta |
Fusione a cera persa: modello indiretto (stampo) | Sì | Sì | Sì | Media |
Fusione con sabbia: modello stampato direttamente con qualunque resina dura | Sì | Sì | No | Bassa |
Scopri le linee guida di progettazione per creare modelli stampati in 3D, esplora passo a passo il procedimento di fusione diretta a cera persa, le linee guida per la fusione indiretta a cera persa e la fusione in sabbia e molto altro nel nostro whitepaper.
Whitepaper: La fabbricazione di parti di metallo con la stampa 3D