Ashley Furniture: da un'idea a 700 parti stampate in 3D direttamente in fabbrica
Poco dopo aver introdotto nell'azienda la prima stampante 3D stereolitografica (SLA), un ingegnere di produzione di Ashley Furniture ebbe un'idea: era possibile sostituire dei perni di allineamento lavorati con parti stampate in 3D pronte all'uso, evitando i lunghi tempi di attesa e le quantità minime d'ordine a cui si era soggetti esternalizzandone la produzione?
La risposta fu "sì" e fece scaturire altre domande.
Oggi, circa due anni dopo e con una stampante in più, ci sono 700 parti stampate in 3D in servizio nello stabilimento di produzione di Ashley Furniture di Arcadia (Wisconsin), accanto a robot industriali e macchine per la fresatura CNC, dall'assemblaggio alla fabbricazione.
I dipendenti dell'azienda continuano a porre domande e a sottoporre idee, e la società continua a crescere.
Guarda il video per scoprire come e perché Ashley Furniture, il maggior produttore di mobili al mondo, integra le nuove tecnologie, dalla stampa 3D alla robotica, nelle sue fabbriche.
La ricetta per una produzione di successo
Ashley Furniture è il maggior produttore di mobili al mondo e, nonostante debba fare i conti con un mercato del lavoro in contrazione, continua a crescere inesorabilmente.
"Realizziamo un 10% in più di attività solo nel nostro stabilimento di Arcadia, con il 15% di manodopera in meno," afferma Vaughn Pieters, Direttore Senior delle Operazioni del comparto mobili da riordino.
Con una filosofia aziendale che incoraggia i dipendenti a partecipare attivamente ai processi di miglioramento continuo, Ashley Furniture applica tecnologie avanzate per integrare la manodopera e massimizzare il valore del personale, attingendo miglioramenti di processi e innovazioni direttamente dai lavoratori.
Scopri di più sulle pratiche dell'azienda e sull'approccio alle nuove tecnologie che hanno alimentato il successo a lungo termine di Ashley Furniture.
"L'automazione ci ha consentito di rimuovere una parte del pesante sforzo fisico che ha stigmatizzato la produzione negli ultimi 50-60 anni. Non abbiamo più operai che svolgono lavoro fisico faticoso per tutto il giorno. Lasciamo che siano le macchine a farlo. Allo stesso tempo lasciamo che il dipendente usi la testa, che cerchi di migliorare il processo," dice Pieters.
"Abbiamo introdotto il nostro primo robot cinque anni fa, e ora, facendo il giro dello stabilimento, si può vedere dove abbiamo aggiunto l'automazione. La stampa 3D ha intrapreso lo stesso percorso di crescita."

Ashley Furniture ha 700 parti 3D in servizio nel suo stabilimento di produzione, dall'assemblaggio alla fabbricazione.
Dalla prototipazione in-house a dime, fissaggi e attrezzatura
Negli ultimi 30 anni Brian Konkel, ingegnere di produzione di Ashley Furniture, ha lavorato nei reparti Progettazione, Ingegneria e Produzione, trovando numerose opportunità per applicare la stampa 3D all'interno di ciascuna area.
Prima di ricorrere alla stampa 3D nello stabilimento di produzione, Ashley Furniture aveva già usato la stampa 3D in-house per la prototipazione. L'azienda aveva precedentemente usato la stampa 3D per decenni, esternalizzando la produzione di qualche parte fin dagli anni '90, e introducendo infine una stampante a filamento (FDM, modellazione a deposizione fusa) quando il volume di ordini iniziò ad aumentare.
L'azienda iniziò a stampare sempre più parti in-house, ma la qualità diventò un problema. Il team passò poi alla stereolitografia laser, acquistando la stampante 3D Form 2 di Formlabs.
Nella stampa 3D stereolitografica (SLA) un laser polimerizza in modo selettivo la resina liquida in parti solide, strato dopo strato, mentre la modellazione a deposizione fusa (FDM) realizza parti fondendo ed estrudendo strati di filamento termoplastico. Scopri di più sulla differenza tra stereolitografia (SLA) e modellazione a deposizione fusa (FDM).
"Ci siamo resi conto che stavamo cercando una qualità di finitura superficiale leggermente superiore e tolleranze più strette. La stampa 3D SLA con la Form 2 ci consentiva di creare oggetti con dettagli quali accoppiamenti a scatto per differenti componenti di fissaggio," dice Konkel.
"Una bella opzione offerta dalla Form 2 è la varietà di materiali disponibili per la stampa. Potevamo iniziare a stampare un componente, e se quel particolare materiale non era esattamente quello che cercavamo, c'erano altre opzioni disponibili."
Le cose hanno cominciato a decollare quando il team ha incorporato nella fabbrica la stampante 3D Form 2. Oltre alla prototipazione, Konkel ha trovato aree per applicare la stampa 3D alla produzione. Il volume di stampa è aumentato talmente in sei mesi che l'azienda ha ordinato una seconda stampante.
"Attualmente utilizziamo entrambe le stampanti Formlabs per un minimo di 40 ore settimanali," dice Konkel.
Adattare in scala parti di produzione stampate in 3D
La stampa di parti era una soluzione rapida e a basso rischio per testare e implementare idee volte a incrementare l'efficienza, dal risparmio di tempo e denaro generato dalla creazione di parti di ricambi in-house fino all'individuazione di soluzioni creative che hanno cambiato radicalmente il modo in cui l'azienda organizza lo stabilimento di produzione.
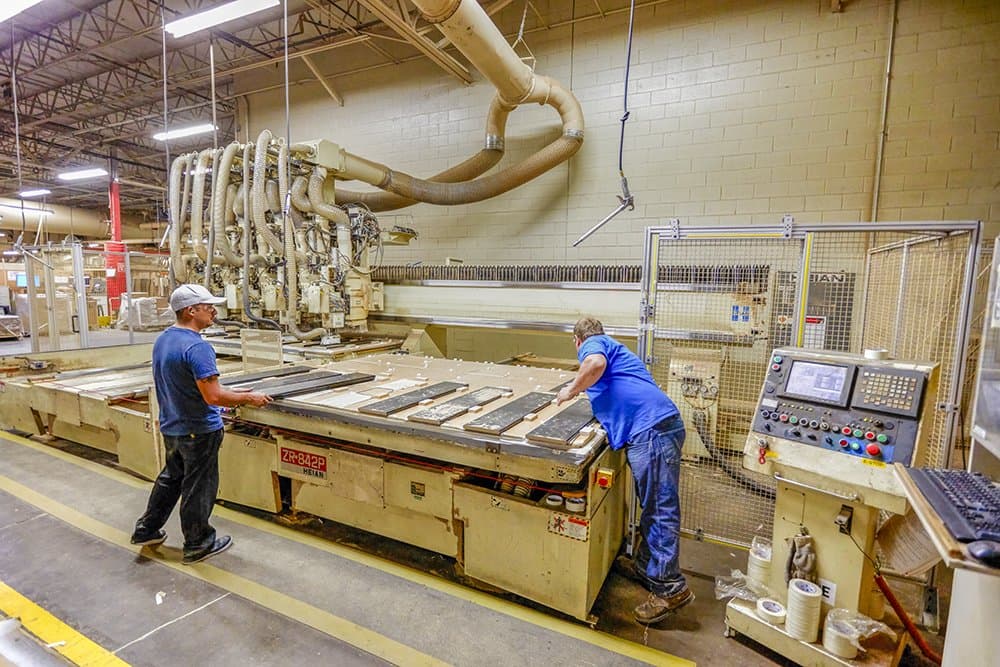
Centinaia di perni di collegamento stampati in Durable Resin sono in servizio sulle fresatrici CNC nella fabbrica di Ashley Furniture di Arcadia.
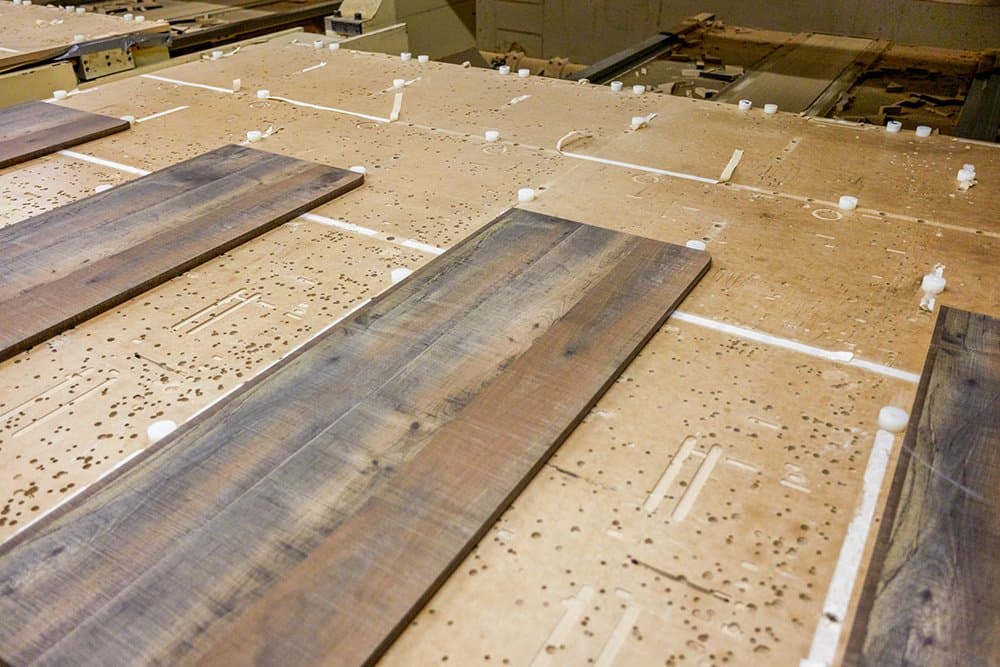
La sola stampa dei perni di allineamento in 3D ha permesso di risparmiare una quantità significativa di tempo e denaro rispetto all'esternalizzazione delle parti in nylon.
"In precedenza ricevevamo i perni da un'officina con un quantitativo d'ordine minimo molto alto, pari a 1200 parti tornite in nylon. Ora siamo in grado di eludere questo passaggio e dimezzare letteralmente il prezzo", afferma Konkel.
Stampare la parte in-house non ha solo consentito di risparmiare risorse rispetto all'esternalizzazione, ma anche di evitare tempi di inattività fra un lavoro e l'altro. Precedentemente, per ciascuna tavola veniva creato un fissaggio speciale. Ora gli operai usano un foglio di installazione che consente di riposizionare rapidamente i perni in un semplice sistema a griglia.
Confronto dei costi: perni di allineamento
Esternalizzazione all'officina | Stampa 3D in-house con la Form 2 | |
---|---|---|
Costo | Quantità minima d'ordine di 1200 pezzi, 10 $ per ciascuna parte. | Nessuna quantità minima, 5,90 $ per parte |
Tempo di consegna | 3-4 settimane | 15 ore e 30 minuti per 16 parti realizzate da due stampanti |
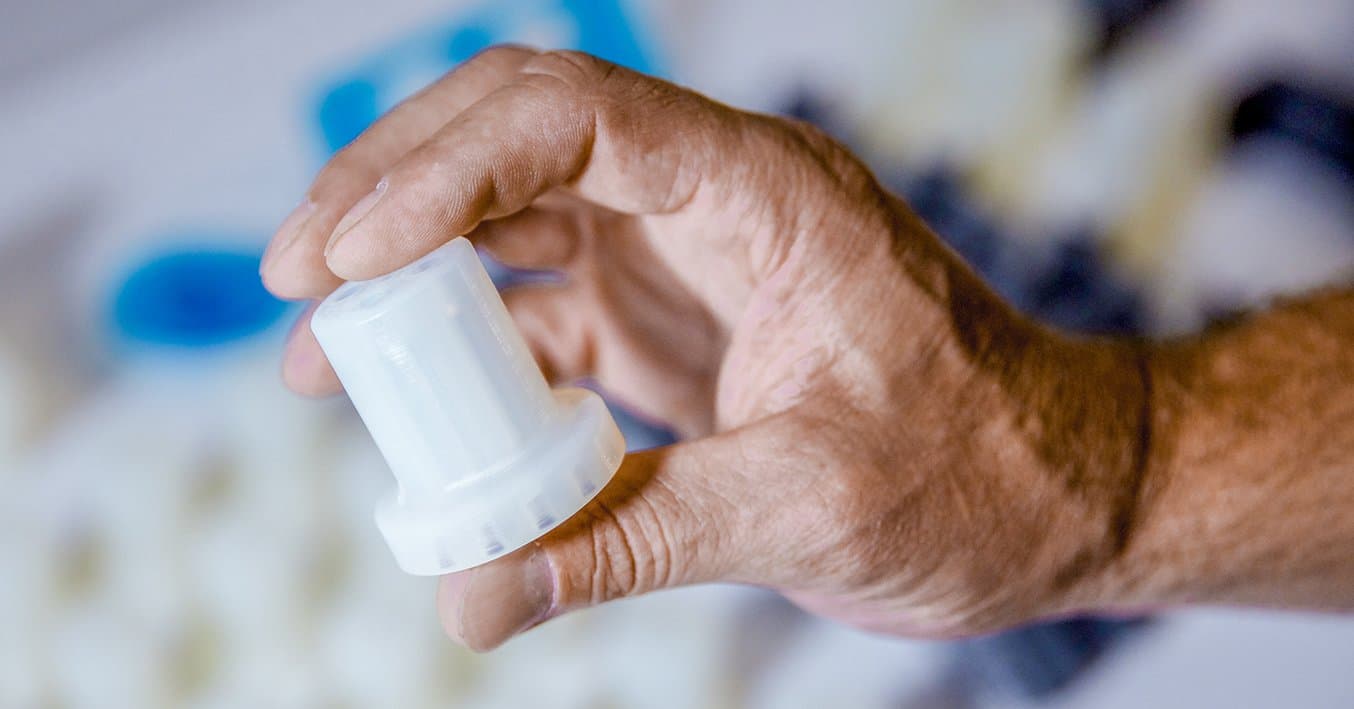
Un sistema universale per gli ancoraggi
Una delle soluzioni più creative dell'azienda è stata la creazione di un sistema universale per gli ancoraggi. Analogamente al sistema a griglia per i perni di allineamento, il team ha creato un sistema universale di fissaggi che si serve di parti stampate in 3D per semplificare gli aggiustamenti durante la conversione dei prodotti, eliminando completamente la necessità di rivolgersi a officine di produzione che realizzerebbero ciascun nuovo fissaggio da zero.
"Le parti stampate in 3D colmano la lacuna fra le diverse configurazioni" dice Konkel.
Il sistema universale di fissaggi di Konkel si serve di parti stampate in 3D per semplificare gli aggiustamenti durante la conversione dei prodotti.
Ora, dopo l'introduzione di un nuovo articolo, l'azienda ha solo bisogno di apportare alcune modifiche alle dimensioni dei modelli solidi preesistenti per progettare e stampare nuove parti e adattare così il sistema. Per il resto, può riutilizzare tutte le configurazioni e le geometrie esistenti. Gli operai di assemblaggio seguono semplici istruzioni per ciascun cambio, facendo scorrere su binari verso l'alto e il basso degli attuatori e riserrandoli nella nuova posizione, sostituendo poi le parti stampate in 3D adatte alla nuova configurazione.
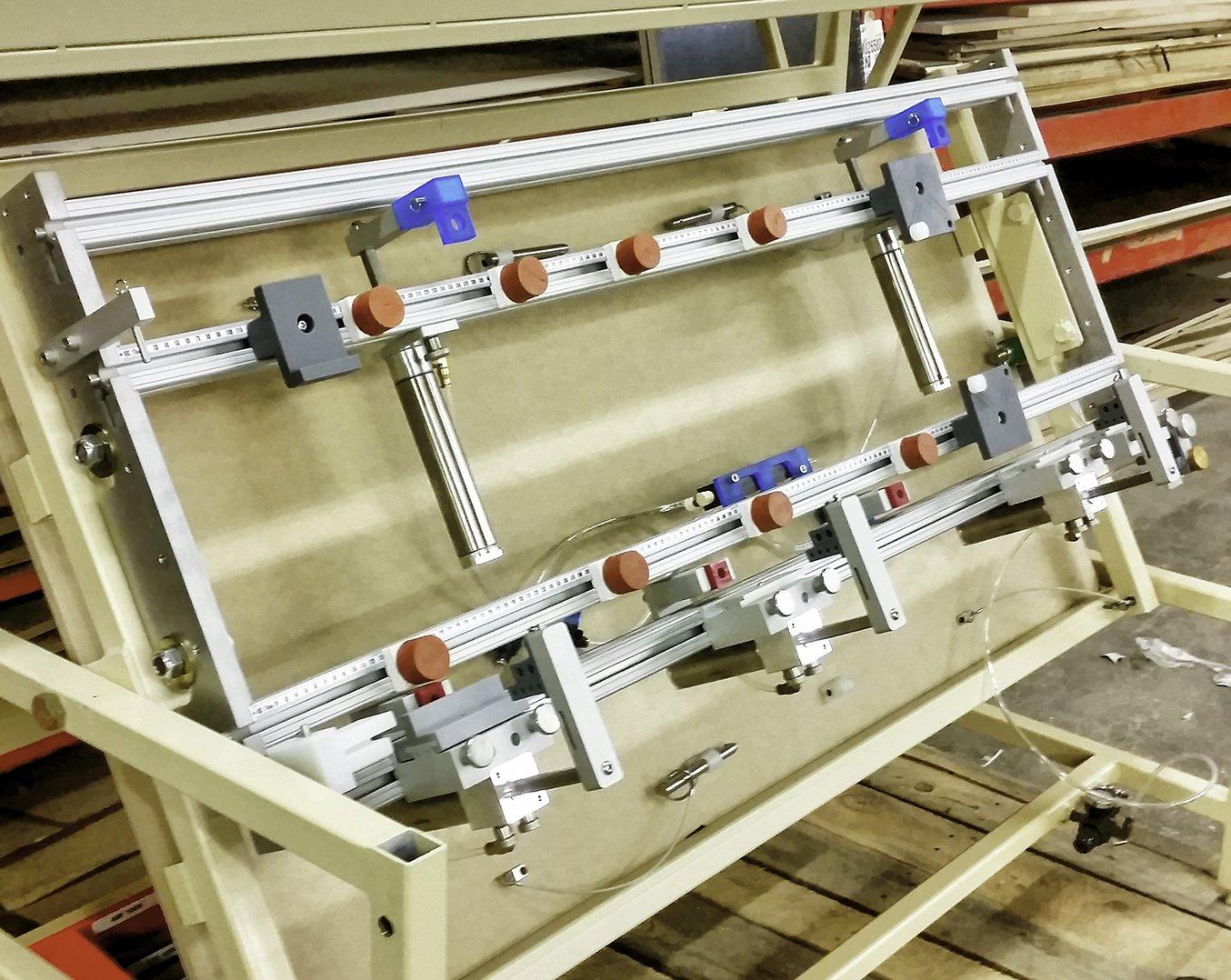
L'ancoraggio universale si serve di parti stampate in 3D intercambiabili da adattare a ciascun nuovo articolo.
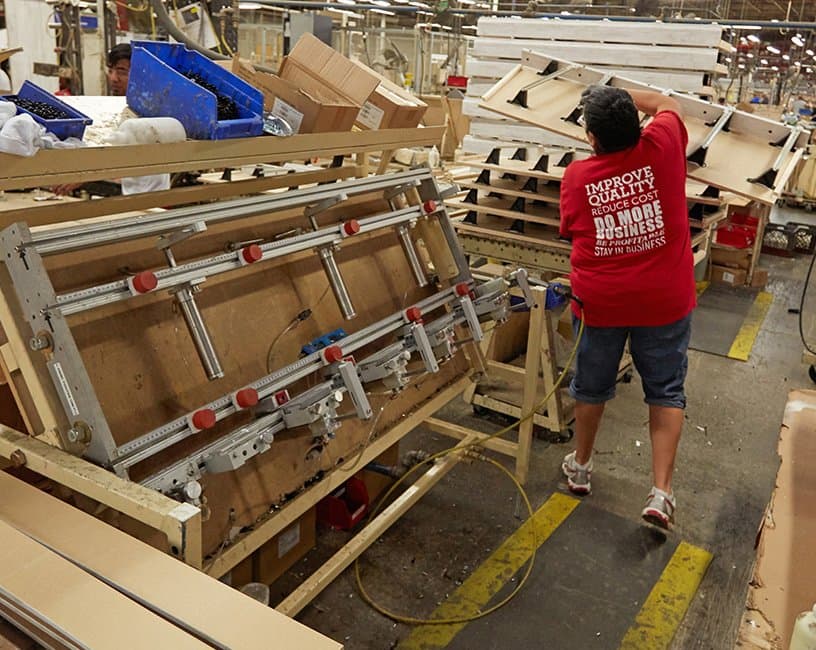
"Con la stampa 3D, sostituire le parti diventa ovviamente facilissimo, ma siamo rimasti sorpresi anche dalla loro longevità: alcune sono durate il triplo rispetto a quanto ci saremmo aspettati. Sono passati quasi nove mesi prima di doverle sostituire," afferma Konkel.
"Ad esempio, alcune parti vengono usate ciclicamente ogni minuto, abbassandosi e bloccando per avvitare un assemblaggio".
Il sistema universale ha ridotto in modo significativo il tempo di configurazione nell'area di assemblaggio, nonché lo spazio richiesto per l'archiviazione dei pezzi originali del fissaggio, che potevano pesare fino a 200 libbre (circa 90 kg).
"Con la stampa 3D, sostituire le parti diventa ovviamente facilissimo, ma siamo rimasti sorpresi anche dalla loro longevità: alcune sono durate il triplo rispetto a quanto ci saremmo aspettati. Sono passati quasi nove mesi prima di doverle sostituire."
Brian Konkel, ingegnere di produzione di Ashley Furniture
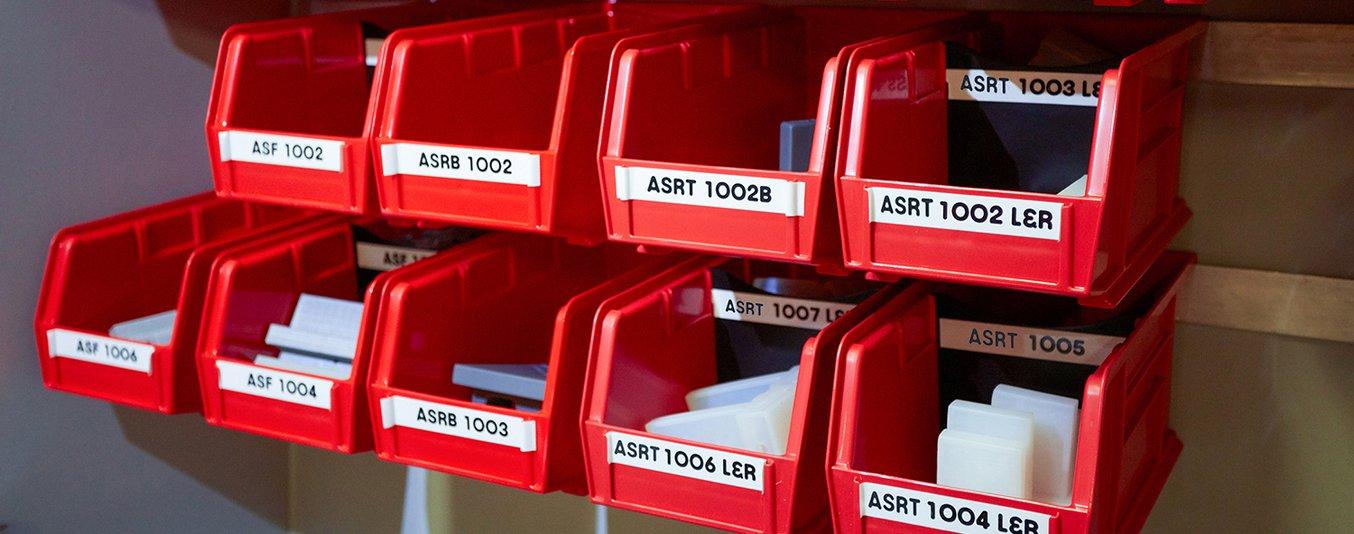
I design delle parti vengono conservati in un inventario digitale. Quando queste sono state stampate, il team usa un semplice sistema di contenitori: ciascuno viene etichettato con il numero della parte e, assieme a una guida di configurazione, consente agli operai di assemblaggio di cambiare facilmente le parti fra un modello e l'altro.
"In precedenza dovevamo fabbricare una dima specifica per una determinata linea di prodotti. Con la stampa 3D delle parti si tratta semplicemente di sostituire le parti per effettuare un adattamento ai diversi articoli. Abbiamo letteralmente sostituito fissaggi che misurano tre piedi per sei (circa 1 x 2 m) con un semplice sistema di contenitori; è un'operazione di configurazione che richiede due minuti," dice Konkel.
"Questo esonera i costruttori di dime dallo svolgimento di compiti ripetitivi e consente loro di lavorare su questioni più urgenti, passando da un lavoro serrato a pezzi più impegnativi."
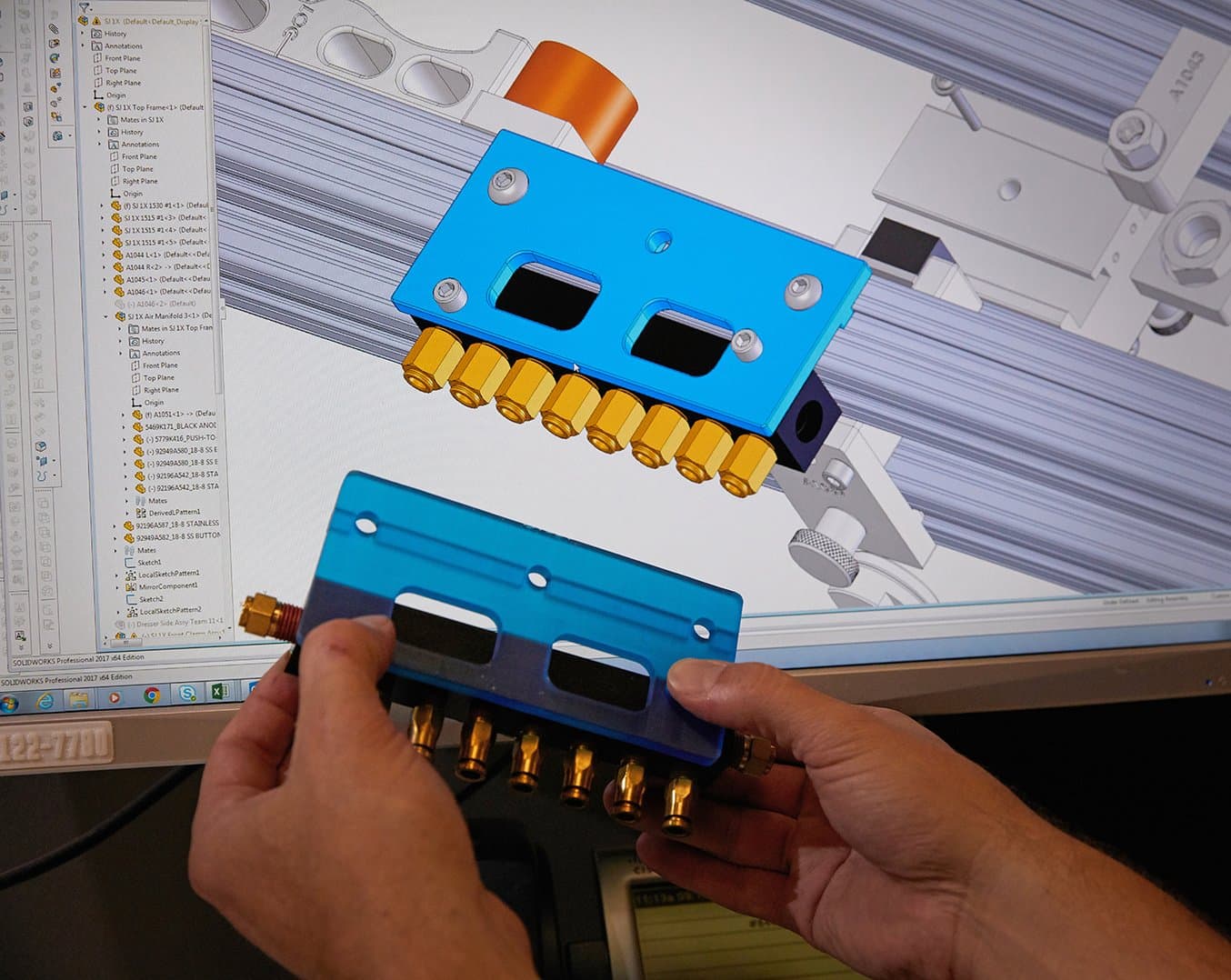
La configurazione universale include un collettore di aspirazione dell'aria stampato in Tough Resin.
"La Tough Resin è un materiale che si è rivelato efficace per le attrezzature di fissaggio, ossia qualsiasi cosa che applichiamo all'estremità di un attuatore. Presenta una resistenza all'impatto eccellente," afferma Konkel.
Personalizzare gli strumenti ed evitare una costosa esternalizzazione con parti di ricambio
La creazione di un pezzo di ricambio è stata una scoperta facile e pratica. Non era possibile acquistare separatamente una guarnizione per un trapano, e l'unica opzione era quella di acquistare il blocco intero, il che risultava molto costoso.
"L'azienda non vendeva solo l'anello, dovevamo acquistare l'intero blocco per 700 $," ricorda Konkel. "Invece abbiamo potuto scansionare la parte in 3D per catturarne la geometria e stampare un pezzo di ricambio al costo di solo 1 $, così da poter continuare a utilizzare il trapano, senza dover comprare l'assemblaggio intero."
Scopri come usare la scansione e la stampa 3D per l’ingegneria inversa.
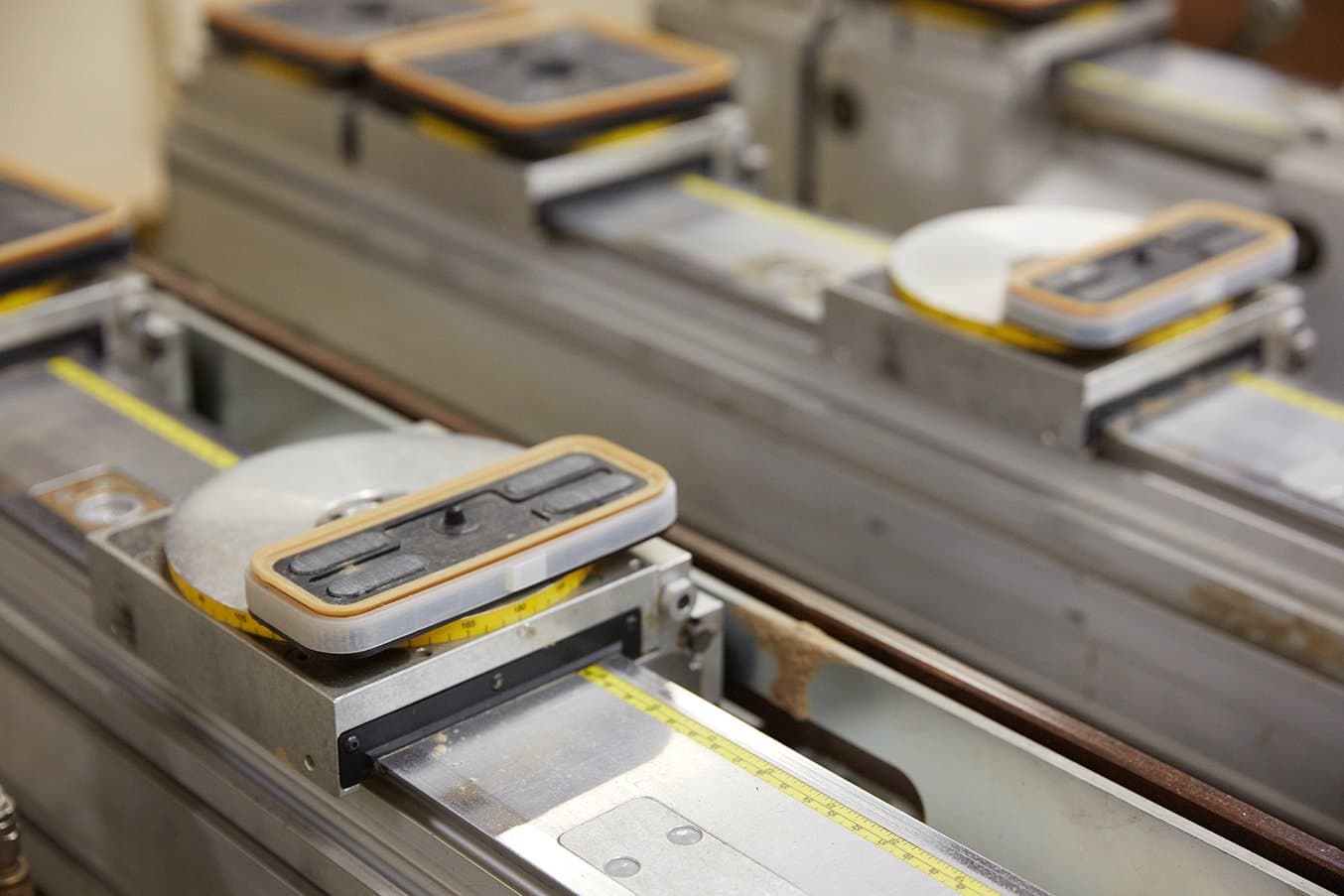
Invece di acquistare un nuovo blocco per 700 $, l'azienda ha stampato in 3D la parte che doveva essere sostituita al costo di un solo dollaro.
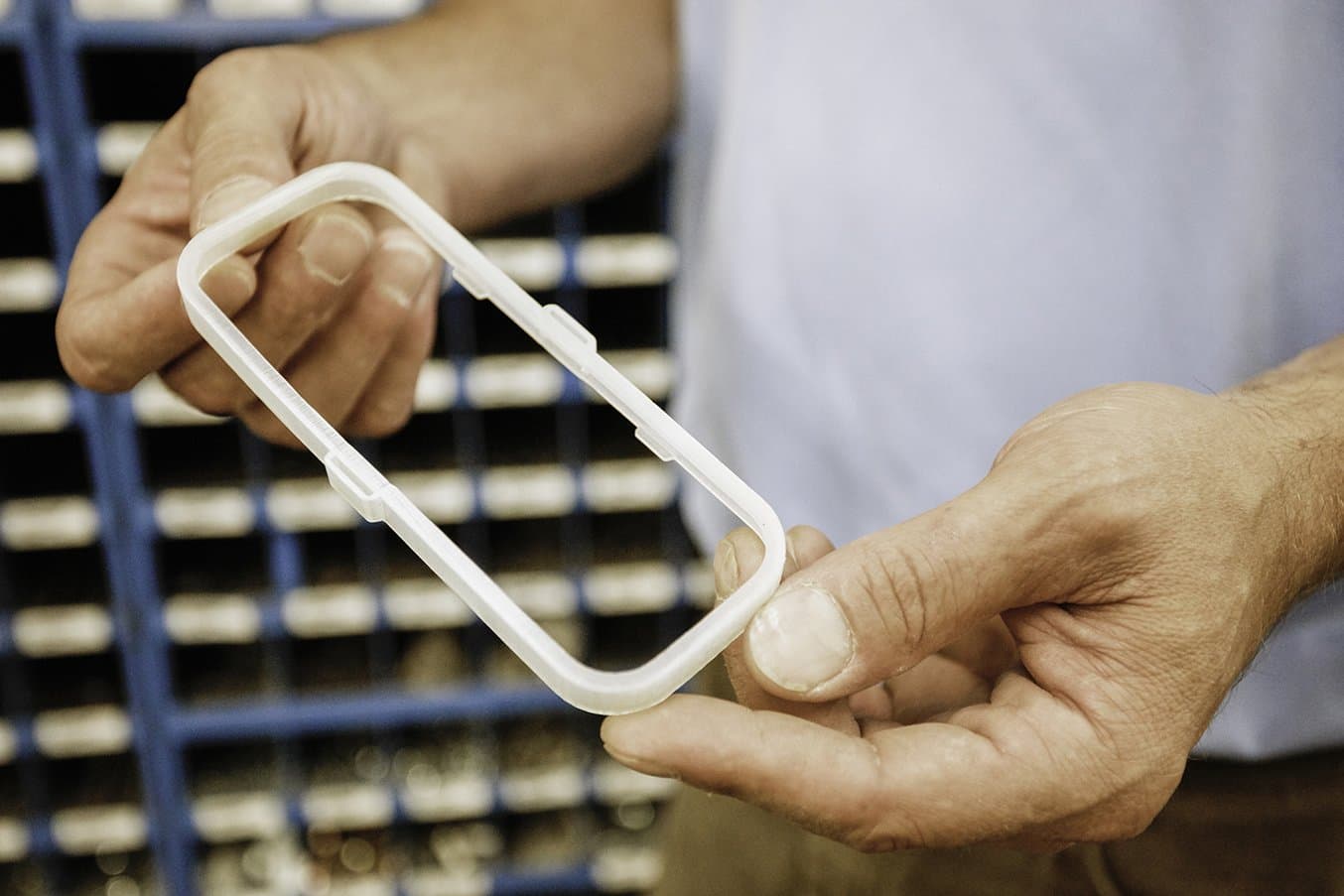
La Form 2, inoltre, ha consentito al team di creare utensili personalizzati, sviluppando ad esempio una guida per pistola sparapunti.
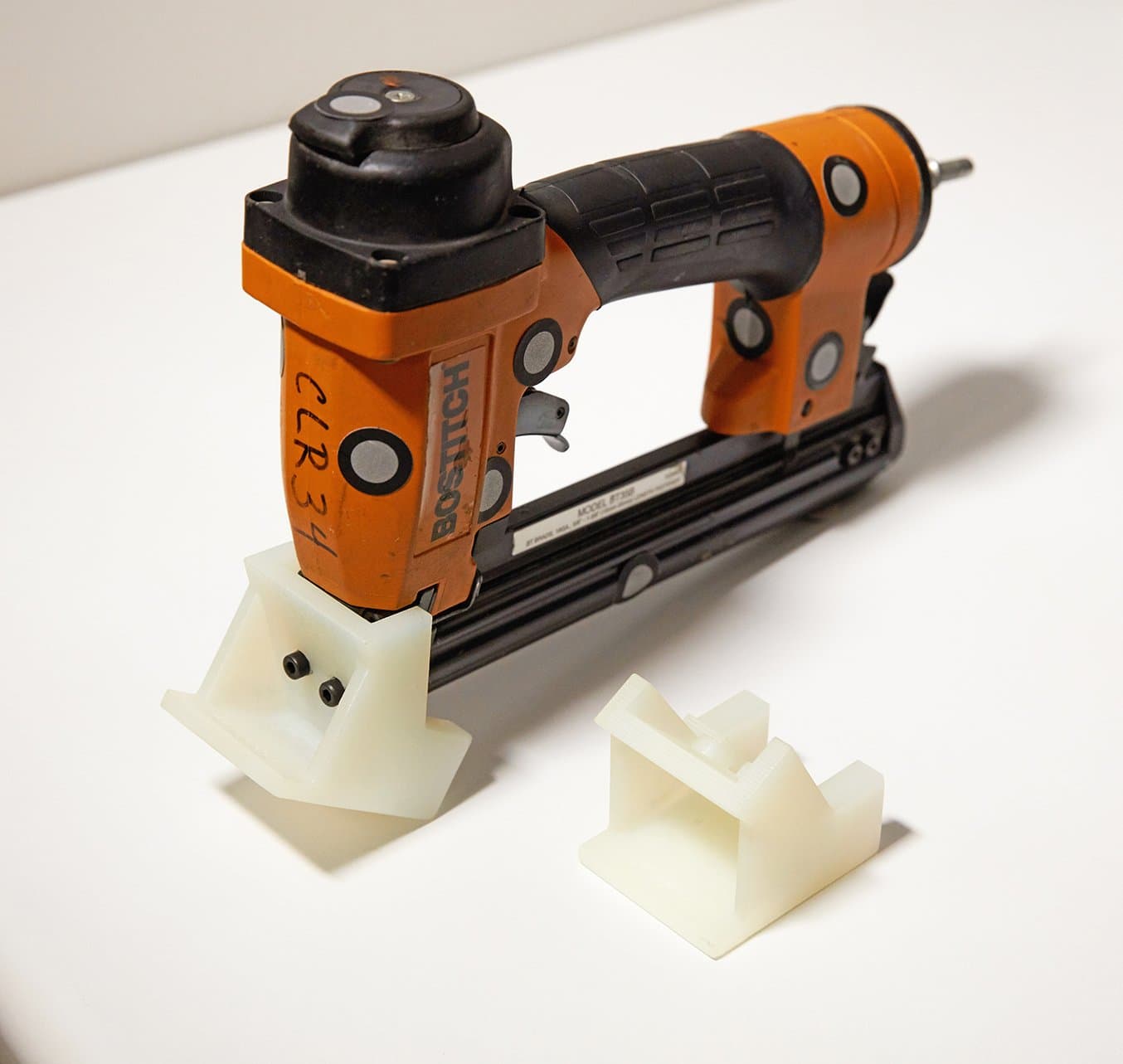
Una guida per pistola sparapunti stampata in 3D con la Durable Resin.
Esplorare la stampa 3D nella produzione
La stampa 3D in-house con la Form 2 ha fornito ulteriori opportunità ai dipendenti di Ashley Furniture di risolvere i problemi in maniera creativa e aumentare la produttività nello stabilimento di produzione. Il team fa funzionare entrambe le stampanti 40 ore a settimana e l'azienda continua ad esplorare nuovi modi di migliorare i processi.
"La Form 2 e l'abilità di stampare parti in 3D ci hanno consentito di allontanarci da alcuni modelli tradizionali di sviluppo di fissaggi e attrezzature," dice Konkel. "Ci consente di adattarci rapidamente a ogni suggerimento o necessità e di creare geometrie che non siamo capaci di produrre o lavorare a macchina altrimenti. Ora siamo in grado di fare cose che erano praticamente impossibili in passato."
Scopri di più su come i produttori e gli ingegneri usano la stampa 3D per migliorare l'efficacia dei processi e cambiare i metodi di produzione.
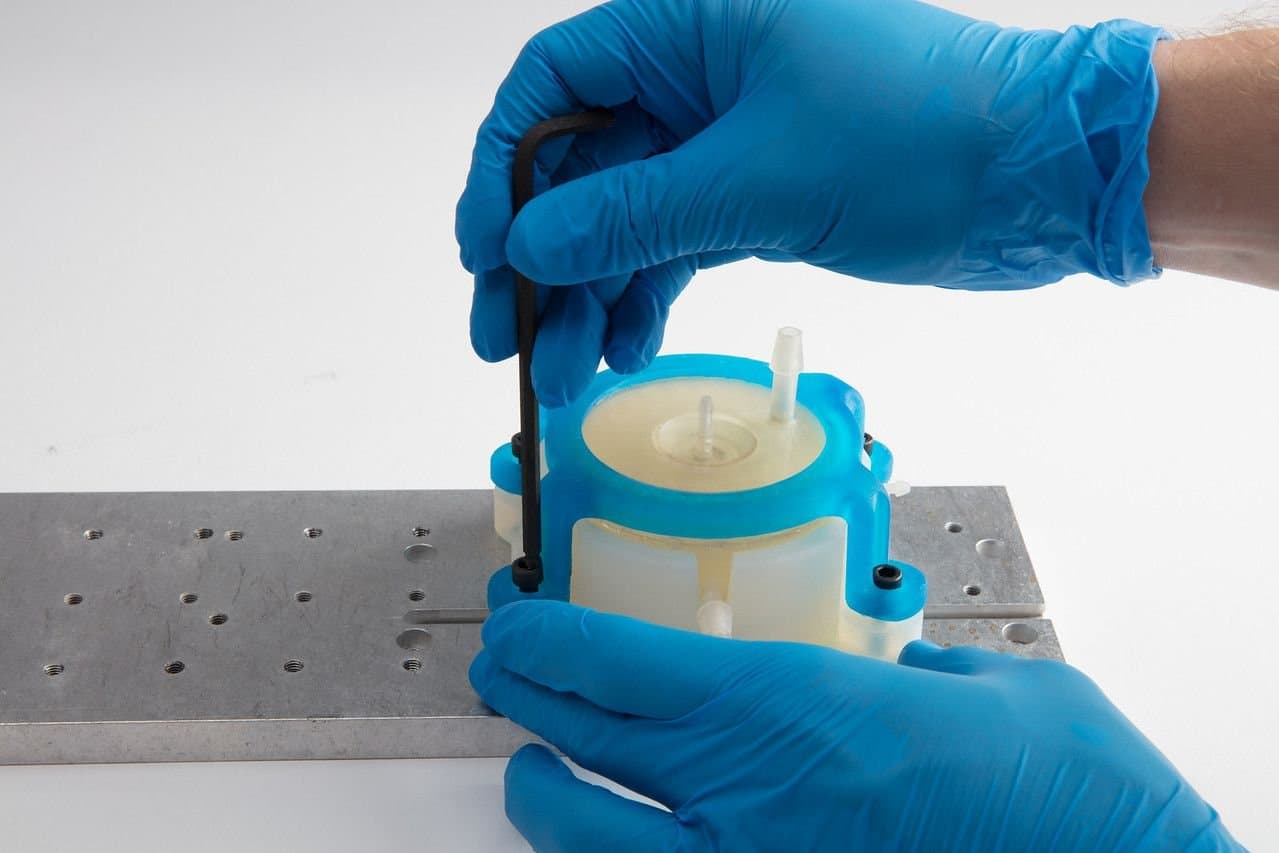
Progettazione di dime e attrezzi destinati alla stampa 3D
Scarica il nostro whitepaper per scoprire come ridurre i costi, i tempi di sviluppo e creare un workflow di produzione più efficiente grazie alla stampa in 3D di dime e fissaggi.
Scarica il whitepaper