Deutsche Bahn è una delle più grandi società ferroviarie del mondo e si occupa della mobilità di oltre 10 milioni di persone al giorno. Provvedere alla manutenzione dell'enorme infrastruttura necessaria per gestire un traffico di queste dimensioni non è un'impresa da poco: la società ha più di 50 stabilimenti in tutta la Germania per la manutenzione della sua flotta di treni passeggeri e merci.
Lo stabilimento più a nord si trova a Neumünster e conta circa 750 dipendenti che si occupano della manutenzione, della riparazione o, a volte, della revisione completa o dell'ammodernamento delle carrozze passeggeri per i treni urbani e interurbani. Quella di Neumünster è però anche una delle sedi con un laboratorio di stampa 3D in loco, una caratteristica che rende le operazioni più efficienti.
"Abbiamo iniziato a utilizzare la stampa 3D nel 2015 e da allora abbiamo prodotto più di 100 000 parti, con un risparmio di milioni di euro."
Susanne Tost, specialista marketing per il progetto di stampa 3D di Deutsche Bahn
In questo articolo Carsten Wolfgramm, ingegnere di produzione ed esperto di produzione additiva presso il dipartimento di manutenzione dei veicoli di Deutsche Bahn, e Susanne Tost, specialista marketing per il progetto di stampa 3D di Deutsche Bahn, raccontano come Deutsche Bah utilizza le soluzioni di stampa 3D di Formlabs per produrre supporti di produzione che semplificano i workflow, riducono i costi e contribuiscono a riportare i treni sui binari più velocemente.
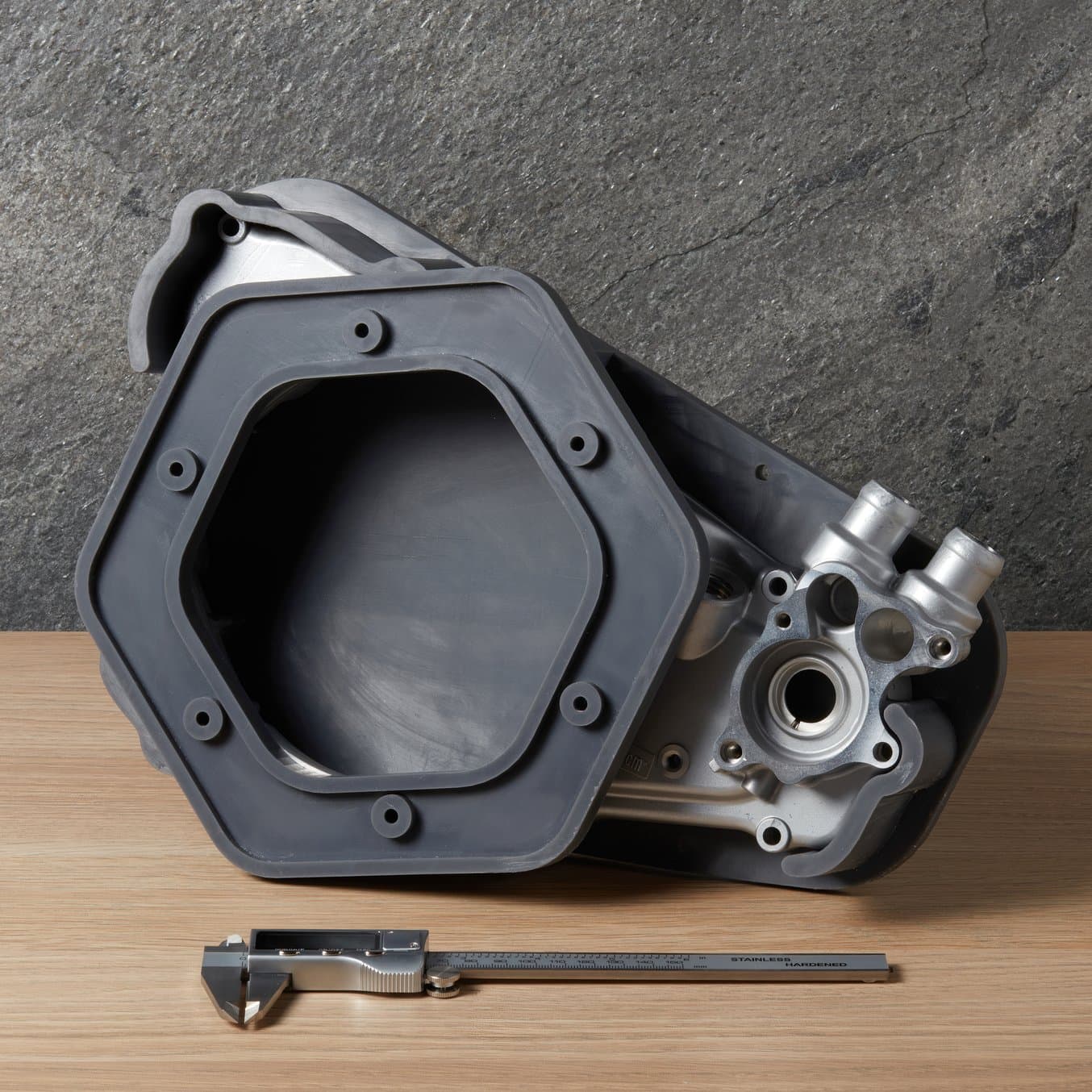
Come stampare in 3D dime, fissaggi e altri supporti di produzione in-house
Questo whitepaper illustra i principi fondamentali alla base della creazione in-house di dime, fissaggi e altri supporti di produzione efficaci.
Produzione di supporti di produzione in loco e su richiesta
Pensato per i viaggi d'affari e gli spostamenti su lunghe distanze, l'Intercity Express (ICE), che raggiunge la velocità di 320 km/h, è il treno passeggeri di punta di Deutsche Bahn.
Le carrozze dei treni ICE 1 di prima generazione, in circolazione da oltre 30 anni, sono in fase di ricondizionamento completo: vengono praticamente distrutte, ricostruite da zero, rinnovate con servizi moderni e riverniciate.
Questo importante progetto di ammodernamento richiede la stretta collaborazione di più stabilimenti e reparti, nonché di varie figure professionali, come pittori, fabbri, elettricisti e altri ancora. Lo stabilimento di Neumünster è uno dei principali centri a livello nazionale.
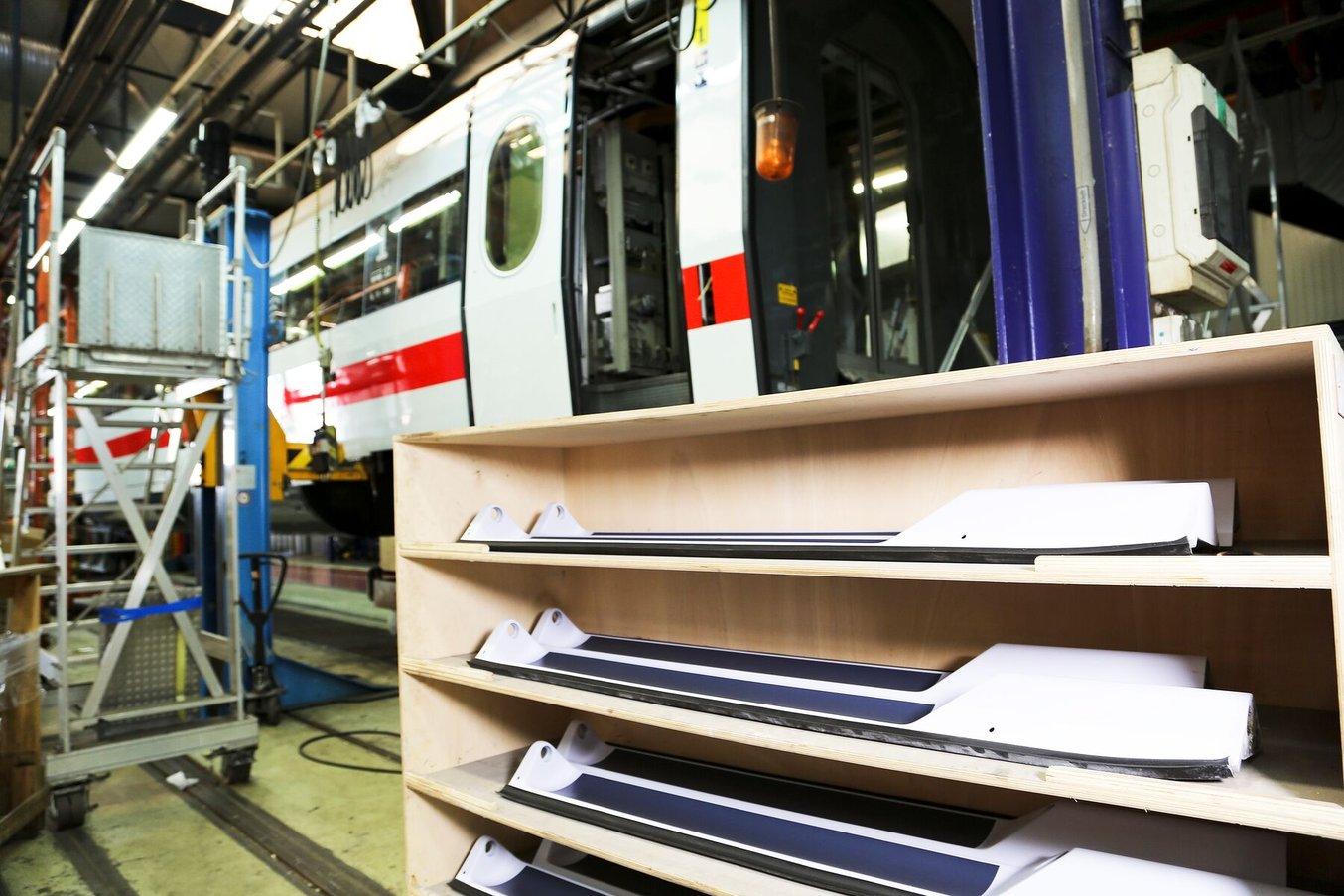
Lo stabilimento per la manutenzione dei veicoli di Deutsche Bahn di Neumünster è uno degli impianti coinvolti nell'importante progetto di ammodernamento delle carrozze dei treni ICE 1.
"I supporti di produzione sono essenziali, perché non si può fare tutto con gli strumenti convenzionali in commercio", ha affermato Wolfgramm.
Il ricondizionamento dei singoli componenti e lo smontaggio e riassemblaggio delle carrozze prevedono molti passaggi che possono essere eseguiti più facilmente, così da risparmiare tempo o garantire qualità e uniformità. Inoltre, se si modernizzano decine di carrozze, i vantaggi di questi strumenti aumentano rapidamente.
"Insieme al personale di questo e altri stabilimenti, stiamo sviluppando numerosi strumenti pratici che aiutano a incollare i pittogrammi, tracciare le linee o contrassegnare i punti da forare senza dover sprecare tempo nel prendere le misure. La tecnologia di stampa 3D può essere utilizzata per produrre modelli di grandi dimensioni che facilitano il lavoro", ha spiegato Wolfgramm.
In passato, i supporti di produzione venivano prodotti nelle falegnamerie segando, levigando e fresando il legno. Quando invece erano necessarie parti in metallo, servivano apparecchi tradizionali per la lavorazione dei metalli, come torni o fresatrici. Queste soluzioni richiedono molto tempo, molta manodopera e costi elevati.
"La produzione additiva offre la straordinaria possibilità di creare rapidamente una forma iniziale e poi di perfezionarla. Dal momento che abbiamo i progetti digitali nel software CAD, possiamo modificarli velocemente se non soddisfano le esigenze o se devono essere cambiati. Se un design deve essere aggiornato, ingrandito o rimpicciolito, la stampa 3D, e in particolare quella con la polvere, è imbattibile."
Carsten Wolfgramm, ingegnere di produzione ed esperto di produzione additiva presso Deutsche Bahn
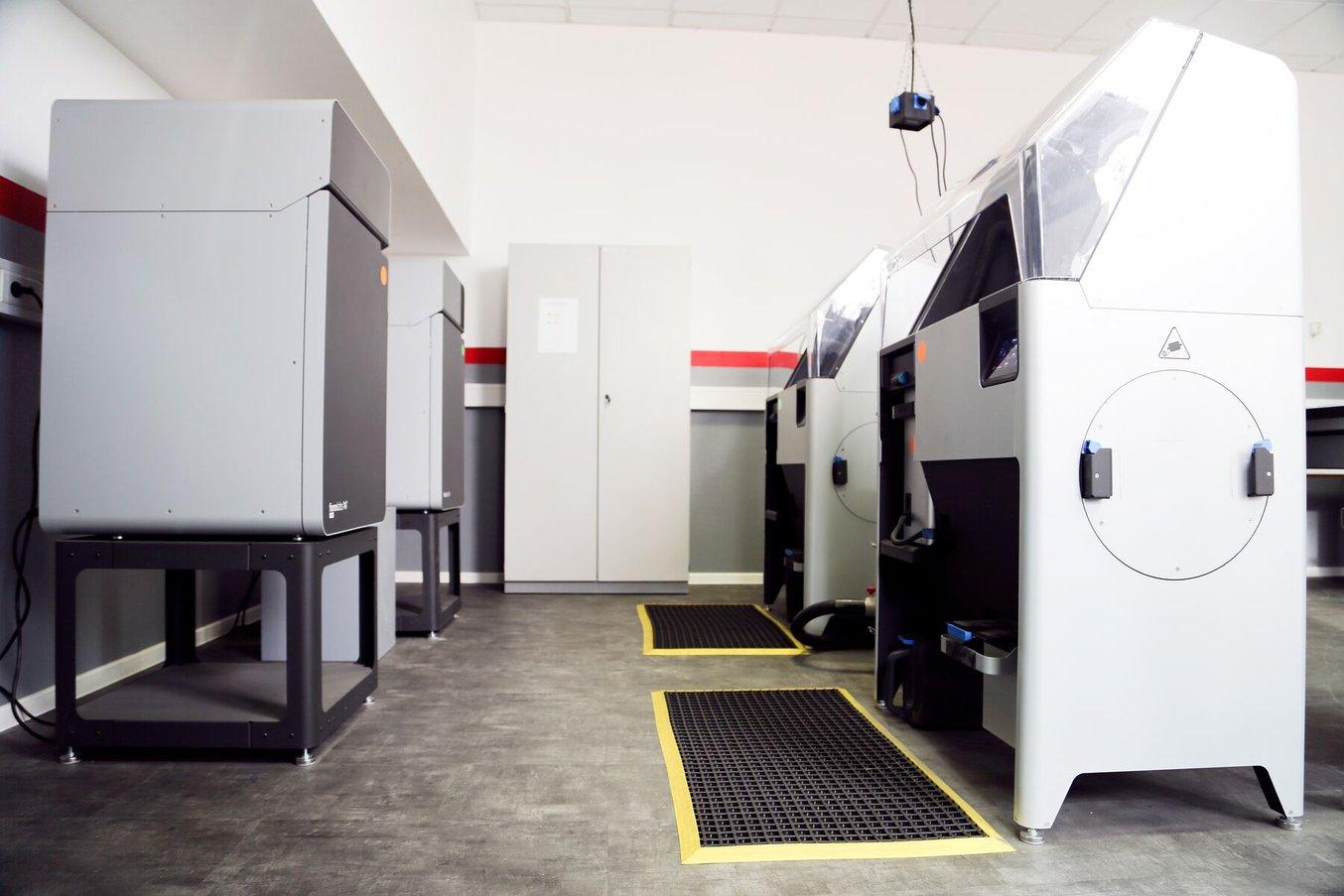
Il laboratorio di stampa 3D di Neumünster conta dieci stampanti 3D, tra cui due stampanti SLS della serie Fuse.
Il team di Deutsche Bahn ha collaborato con il partner Platinum di Formlabs IGO3D sullo sviluppo strategico della produzione additiva e per identificare la soluzione migliore per la propria attività e le proprie applicazioni.
Il laboratorio di stampa 3D di Neumünster conta dieci stampanti 3D che utilizzano un'ampia gamma di tecnologie. Due sono stampanti SLS della serie Fuse, una delle quali utilizza la Nylon 12 Powder, un materiale versatile e resistente, mentre l'altra usa la TPU 90A Powder, che consente di ottenere parti flessibili. Nel laboratorio sono presenti anche due stampanti a resina, la Form 3L di grande formato e una Form 3.
A seconda della richiesta e dei requisiti del componente, Wolfgramm e il suo team non devono far altro che scegliere il processo di stampa e il materiale più adatto.
"Utilizziamo le stampanti Formlabs perché il rapporto prezzo/prestazioni è imbattibile. Sono affidabili e davvero plug-and-play, soprattutto quelle SLS. In questo modo si semplifica molto il lavoro di iterazione continua delle parti. Funzionano 24 ore su 24, sette giorni su sette, tutto l'anno."
Carsten Wolfgramm, ingegnere di produzione ed esperto di produzione additiva presso Deutsche Bahn
La presenza del laboratorio di stampa 3D a Neumünster consente al team di rimanere agile e di rispondere prontamente alle richieste. "Gestire e spedire gli ordini ci consente di non dipendere dalle catene di fornitura né dai lunghi tempi di consegna", ha commentato Wolfgramm.
"Grazie alla stampa 3D in-house, riusciamo a rispondere molto rapidamente alle esigenze quotidiane dello stabilimento. Possiamo creare in anticipo design per diverse applicazioni, produrli direttamente in loco e poi implementarli nello stabilimento. Non esistono altri metodi di produzione che ci consentano di farlo", ha aggiunto Tost.
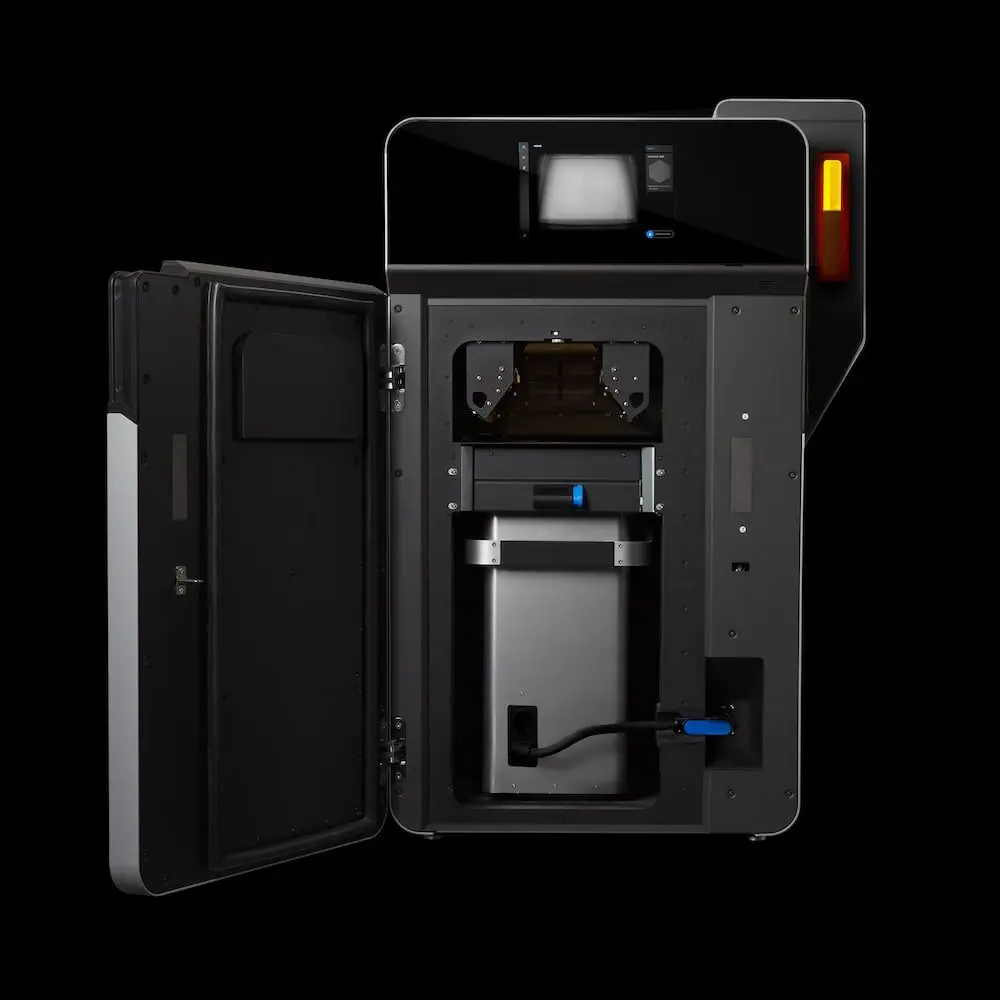
Produzione rapida di parti SLS ad alte prestazioni con la nuova Fuse 1+ 30W
Guarda la nostra dimostrazione di prodotto per un'introduzione alla Fuse 1+ 30W e alla stampa 3D SLS svolta dagli esperti di Formlabs.
Applicazioni della produzione additiva a Neumünster
Strumenti di mascheratura per la verniciatura
Durante il restauro delle carrozze dei treni ICE 1, tutti i componenti in plastica vengono rimossi, levigati, riempiti e riverniciati. Uno di questi componenti è un pannello in plastica scanalato di grandi dimensioni, montato dietro le maniglie delle porte delle carrozze. Tutti i pannelli dovevano essere riverniciati con due colori, in modo che le sezioni scure garantissero una protezione più duratura da sporcizia e tracce di utilizzo.
Verniciare forme curve e schemi complessi richiede generalmente misurazioni minuziose con righelli e calibri pieghevoli, in modo che chi esegue il lavoro possa segnare le posizioni e mascherare correttamente le superfici per ottenere una finitura uniforme.
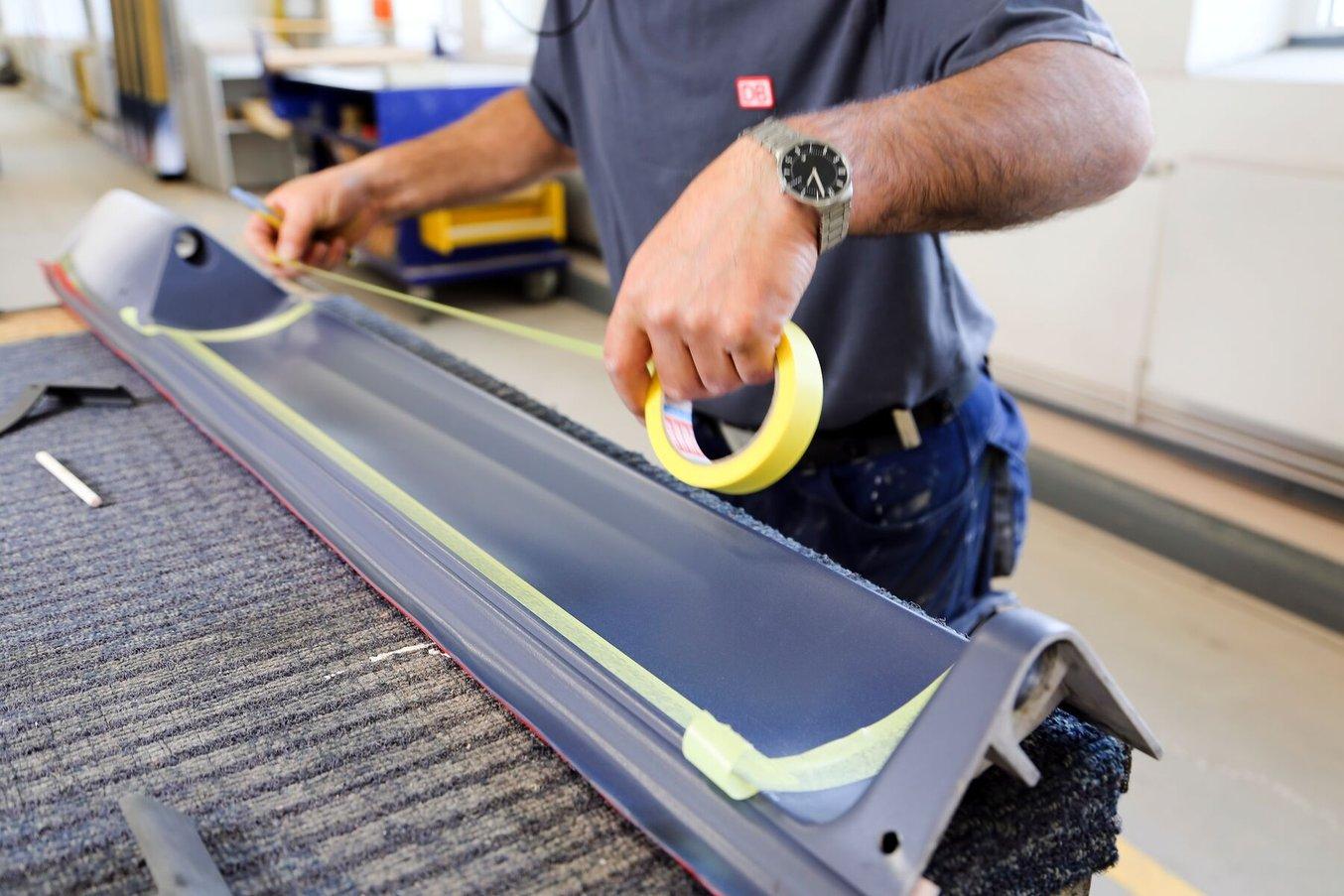
La mascheratura di forme organiche è generalmente un'operazione manuale che richiede molto tempo.
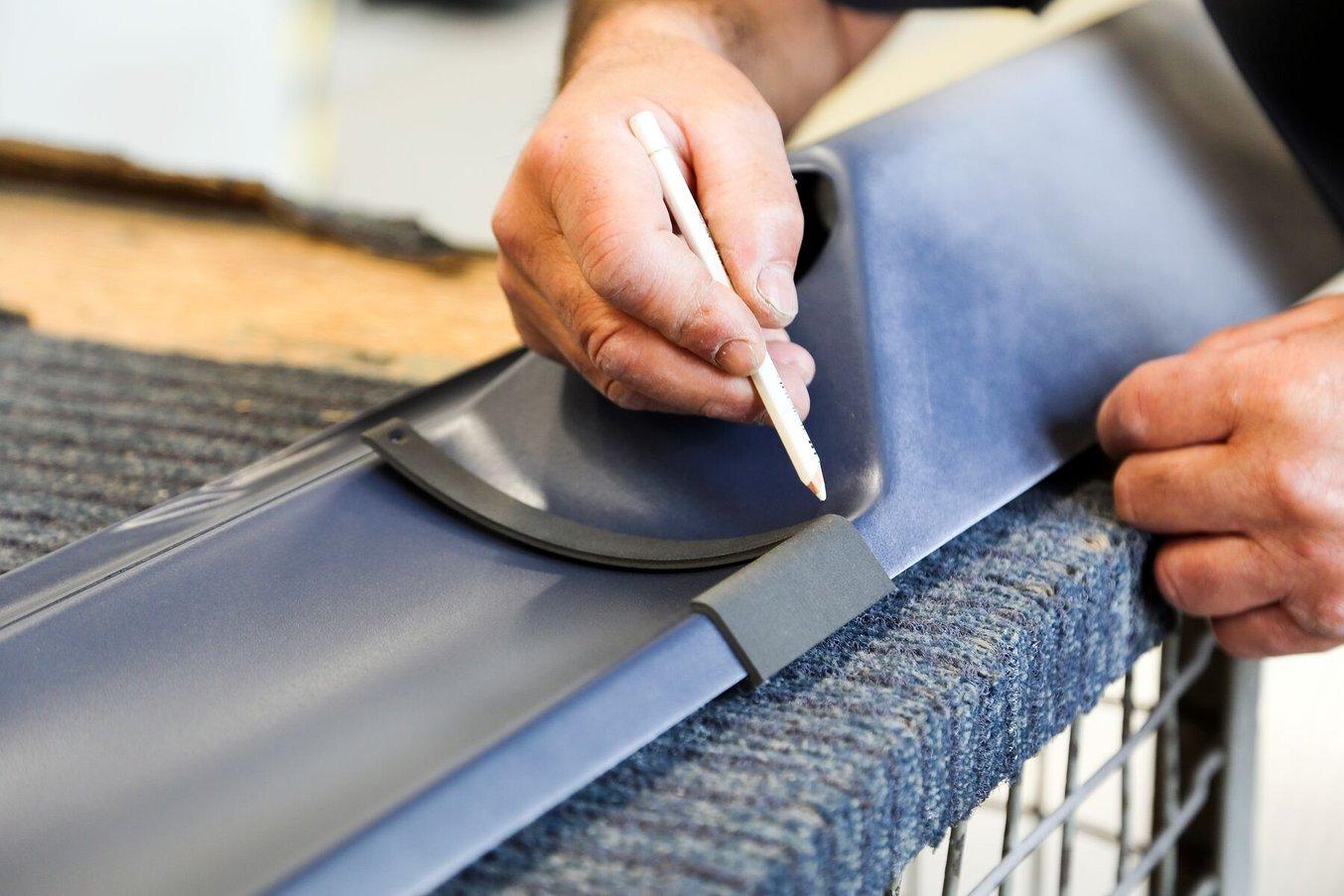
strumenti di mascheratura stampati in 3D possono ridurre drasticamente il tempo necessario per le misurazioni.
"Con la stampa 3D possiamo realizzare facilmente un singolo stencil per poi utilizzarlo in vari modi in altri stabilimenti e laboratori. In alcuni casi è stato possibile completare in soli due minuti un lavoro di verniciatura che in passato avrebbe richiesto 30 minuti", ha spiegato Tost.
A differenza degli strumenti tradizionali, la stampa 3D offre una maggiore libertà di design per creare strumenti complessi che si adattano a determinati progetti. "La produzione additiva, in particolare la tecnologia SLS, consente di realizzare geometrie complesse, come raggi e piccoli rigonfiamenti", ha aggiunto Wolfgramm.
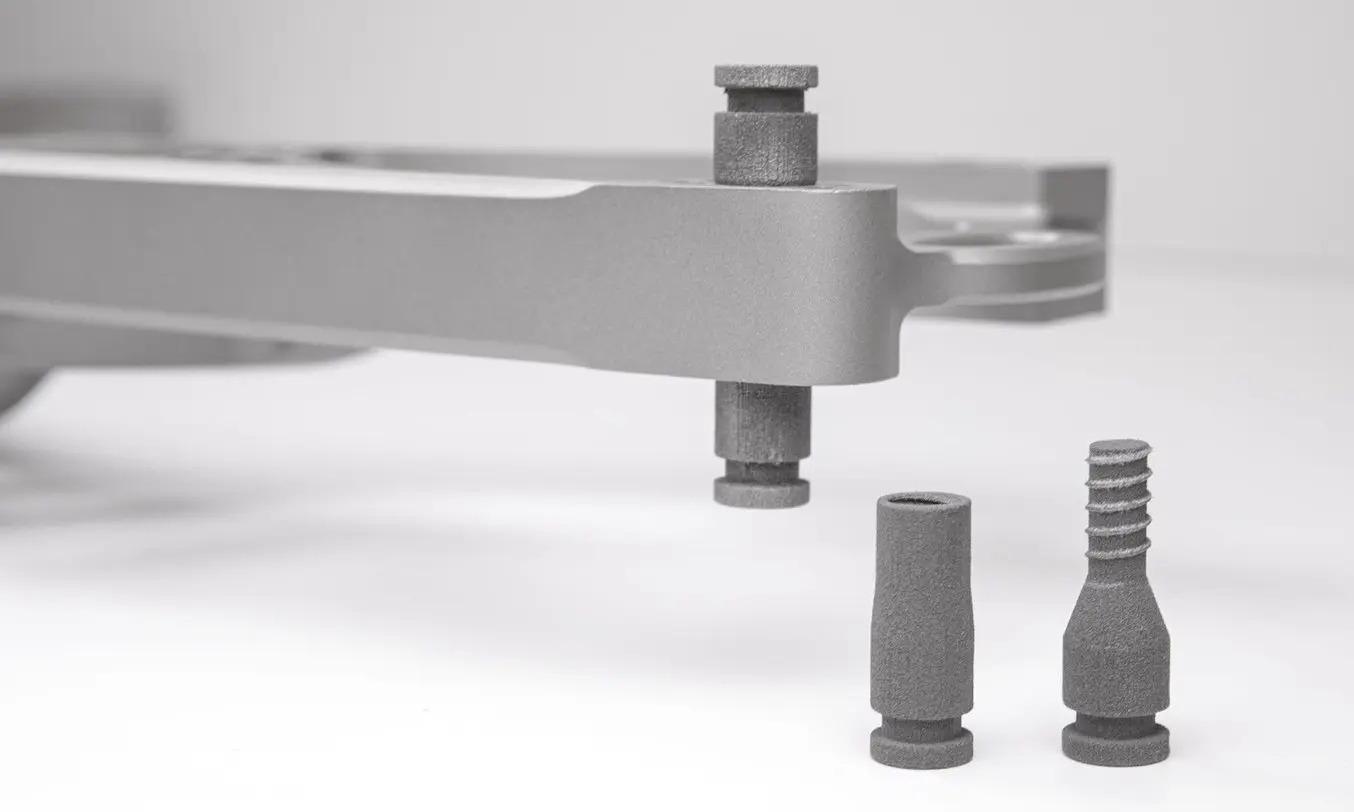
Guida completa agli strumenti di mascheratura stampati in 3D
In questo whitepaper illustriamo come l'utilizzo della stampa 3D per creare strumenti di mascheratura per verniciatura, rivestimento, placcatura o finitura delle parti può ridurre tempi e costi di manodopera e consente di ottenere geometrie e finiture nuove e complesse.
Protezione antigraffio per i portabagagli
Quando le carrozze vengono smontate, i portabagagli vengono rimossi. Dopo il restauro, una volta verniciate e rivestite le pareti, devono essere reinstallati. I portabagagli sono ingombranti e pesanti e vanno montati a filo con la parete, per cui era necessario trovare un materiale flessibile da utilizzare come protezione contro graffi e urti. Un singolo graffio accidentale alle pareti può comportare una rilavorazione dispendiosa in termini di tempo e denaro. Per questo motivo, il team di Deutsche Bahn ha progettato delle protezioni personalizzate e le ha stampate con la Fuse 1+ 30W utilizzando la TPU 90A Powder.
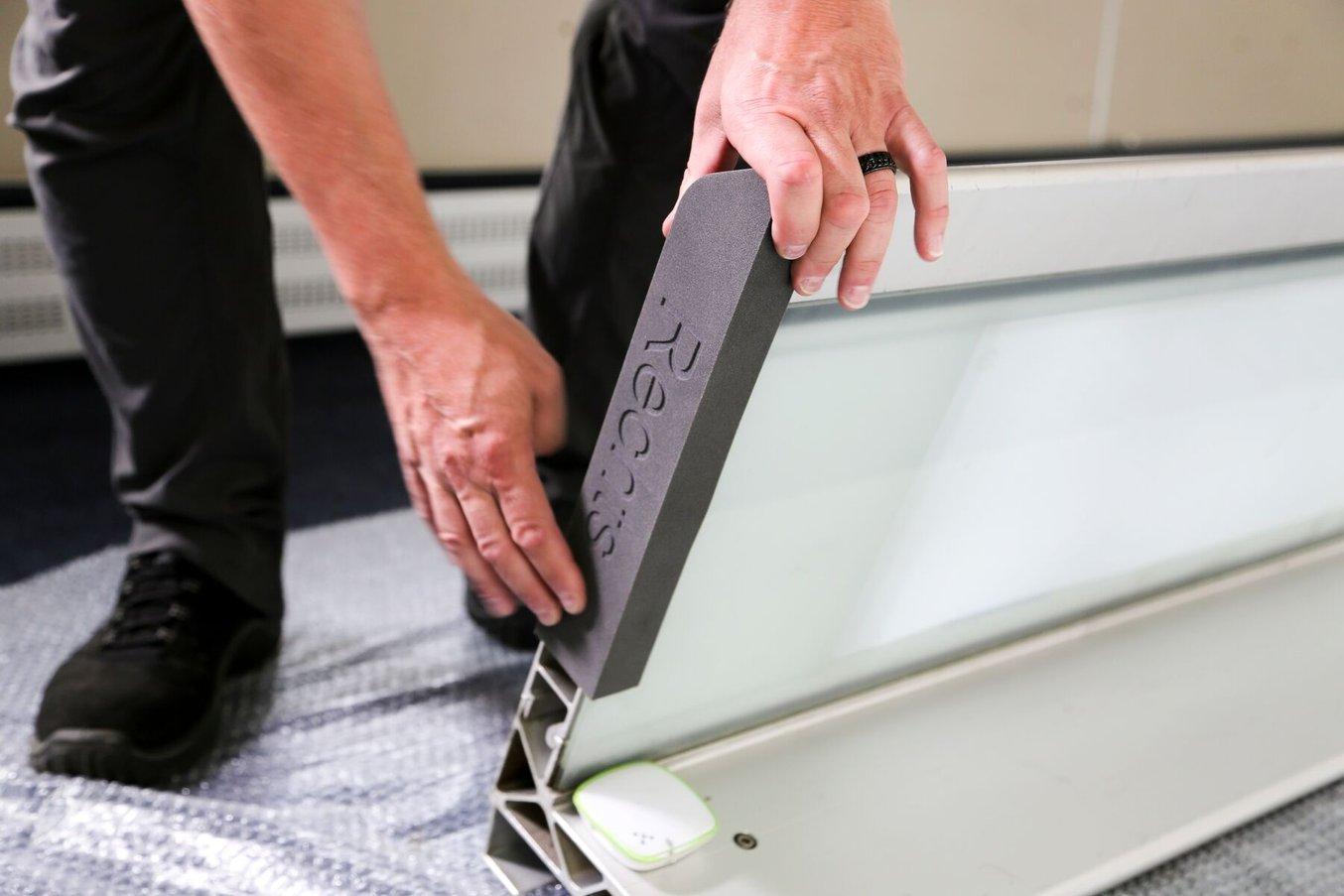
Il team utilizza un materiale flessibile, la TPU 90A Powder, per la protezione contro graffi e urti.
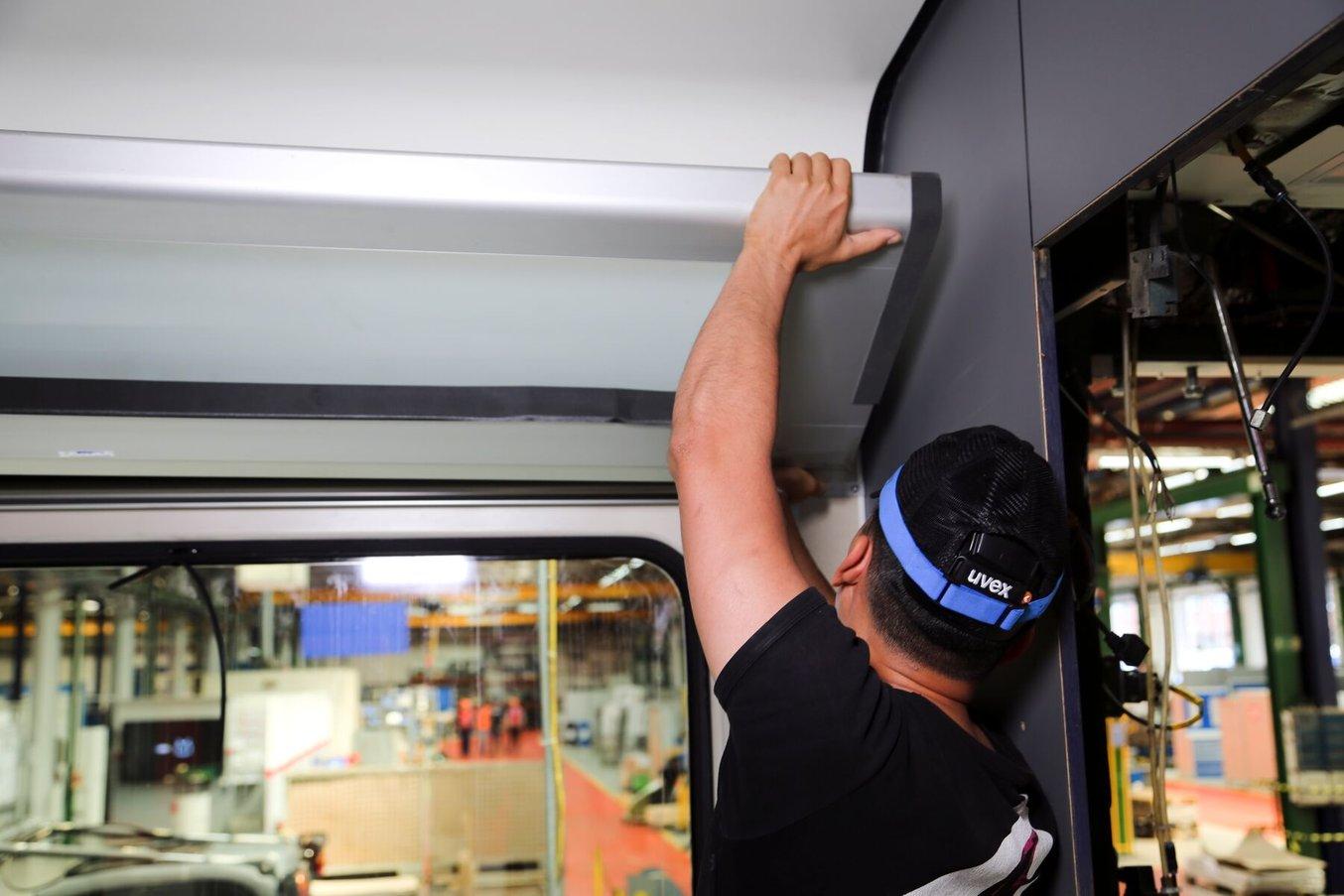
La stampa 3D SLS consente di realizzare una parte sottile che si inserisce tra il portabagagli e la parete.
"Prima di poter contare su questa protezione stampata in 3D, il personale cercava di evitare i graffi usando del pluriball o accorgimenti simili, che non sempre si rivelavano efficaci. Grazie alle parti in TPU, siamo finalmente riusciti a prevenire qualsiasi tipo di danno", ha dichiarato Wolfgramm.
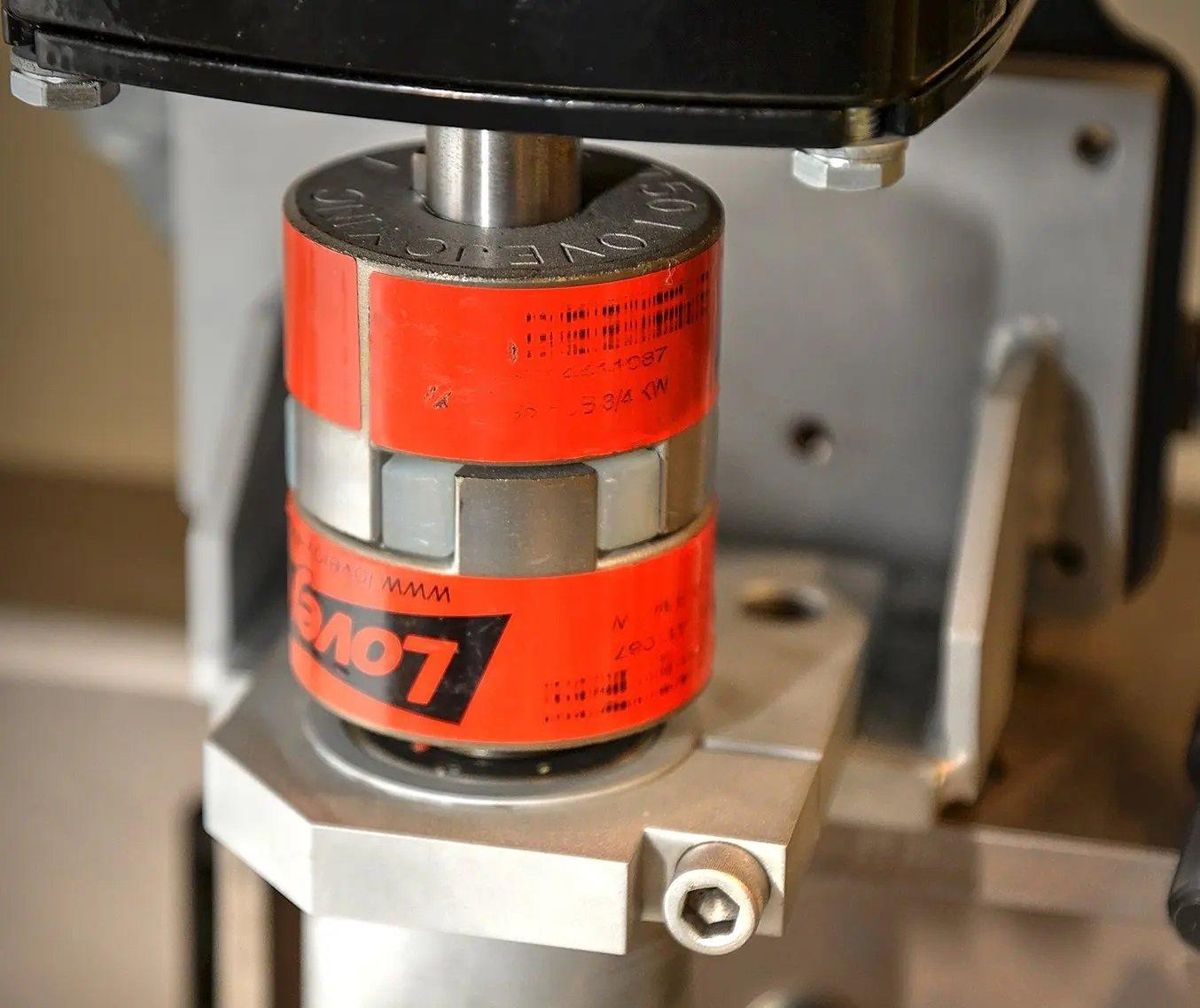
Miglioramento dell'efficienza produttiva con dime e fissaggi stampati in 3D
Guarda questo webinar per scoprire come la stampa 3D in-house permette di creare dime, fissaggi e strumenti personalizzati che consentono di semplificare le operazioni di produzione e ridurre i costi.
Prototipo di coperchio di guida dei cavi
Le carrozze dei treni ICE 1 sono state prodotte più di 30 anni fa, pertanto alcune parti non sono più in produzione. Durante il processo di restauro, il team si è accorto che molti dei coperchi che proteggono e indirizzano i cavi delle prese elettriche montate sotto i sedili si erano rotti a causa delle operazioni di pulizia o erano andati persi. Trattandosi di parti personalizzate, non era facile trovarne di nuove.
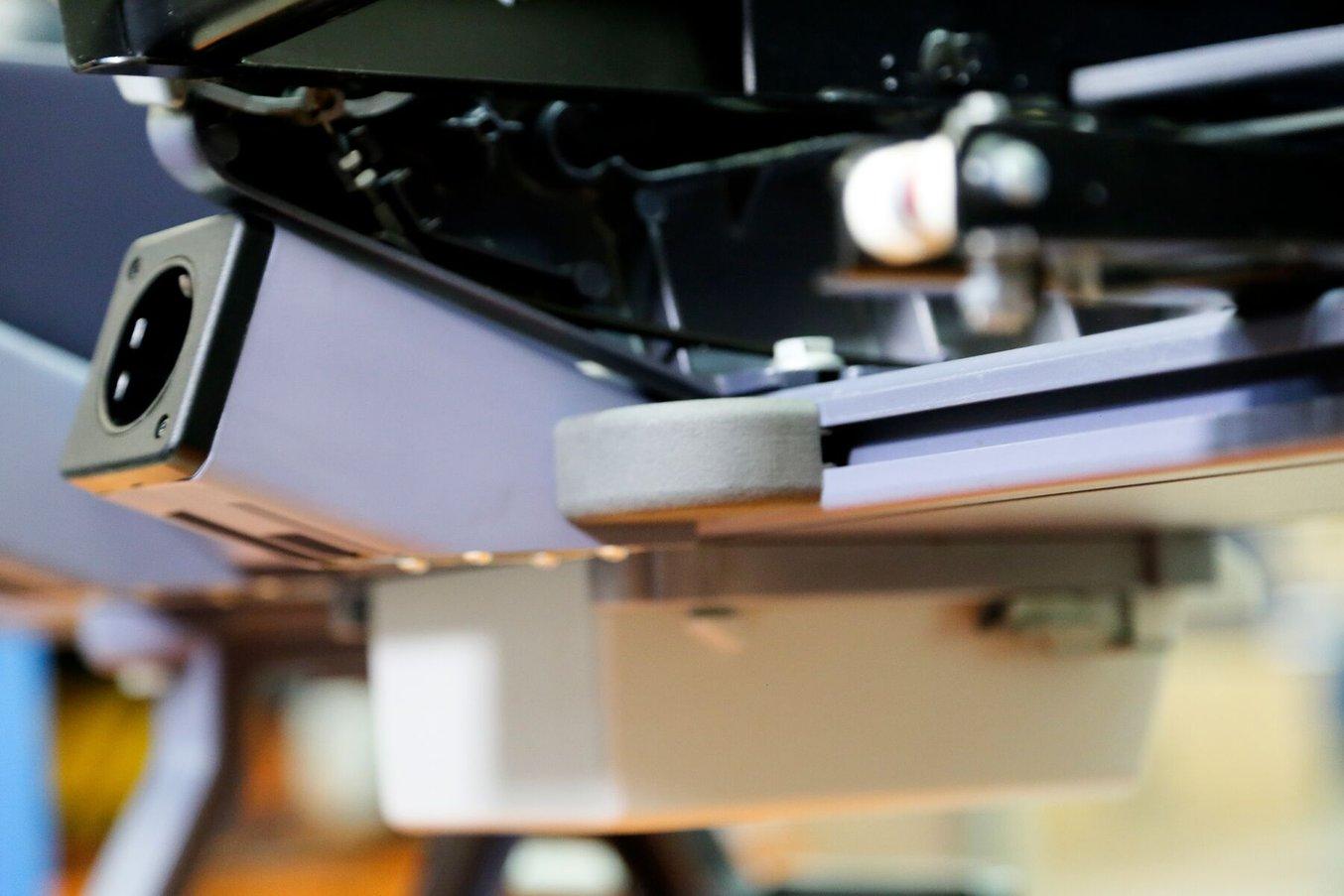
Molti dei coperchi che proteggono e guidano i cavi delle prese elettriche sulle carrozze dei treni ICE 1 sono stati persi.
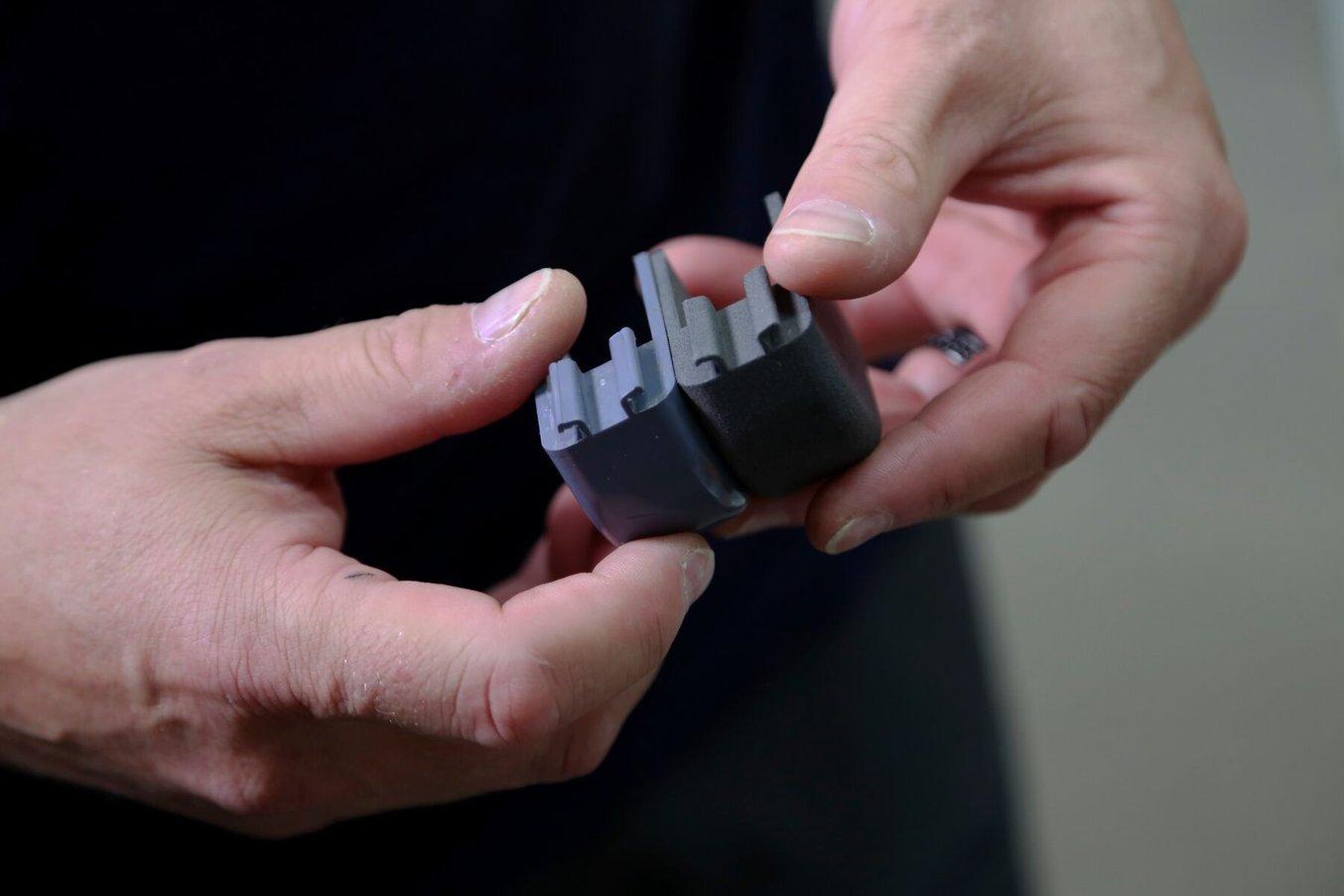
Il team di Deutsche Bahn ha ricreato il design mediante ingegneria inversa e ha utilizzato i prototipi realizzati con la stampa 3D SLS per testarne l'aderenza e farsi un'idea delle dimensioni reali.
"I coperchi sono stati riprogettati dal gruppo Deutsche Bahn e ci è stato chiesto di realizzare i prototipi con la stampa 3D SLS e la Nylon 12 Powder per testarne l'aderenza e avere un'idea delle dimensioni reali. Già la seconda versione era perfetta, si applicava senza difficoltà. Le possibilità offerte dalla stampa SLS sono eccezionali. Considerate aderenza e resistenza del materiale e velocità di realizzazione, vale sicuramente la pena provare questa tecnologia", ha spiegato Wolfgramm.
Supporto per scanner portatile
I supporti di produzione possono essere utilizzati anche per semplificare le attività quotidiane del personale nei vari stabilimenti. Il personale di DB Fernverkehr addetto alla gestione dei materiali utilizza scanner portatili per le operazioni di identificazione e gestione. In passato il team doveva tenere gli scanner in mano e posarli ogni volta che doveva prendere qualcosa o usare entrambe le mani.
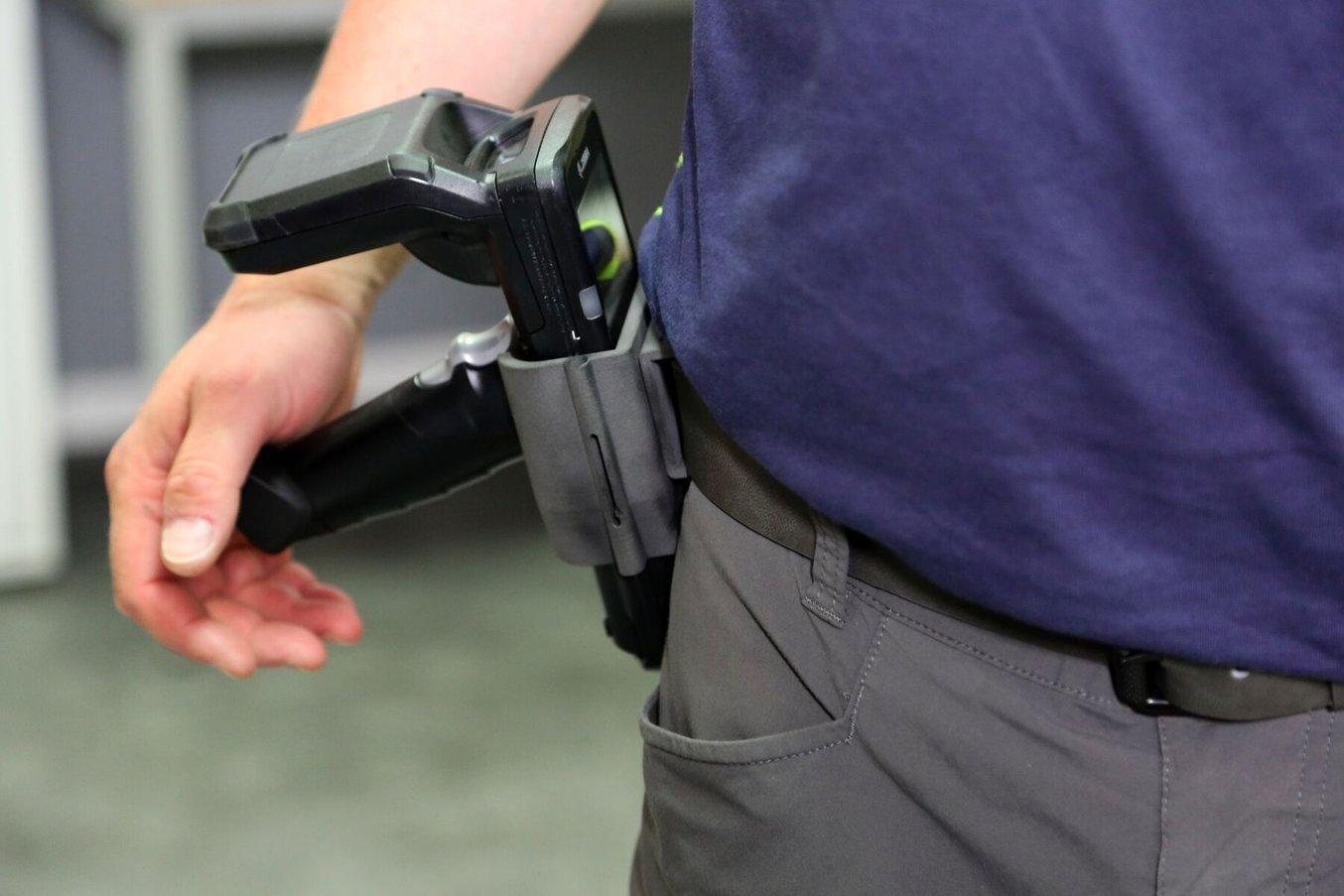
Il personale addetto alla gestione dei materiali aveva bisogno di un supporto per gli scanner portatili, in modo da poterli trasportare senza tenere occupate le mani.
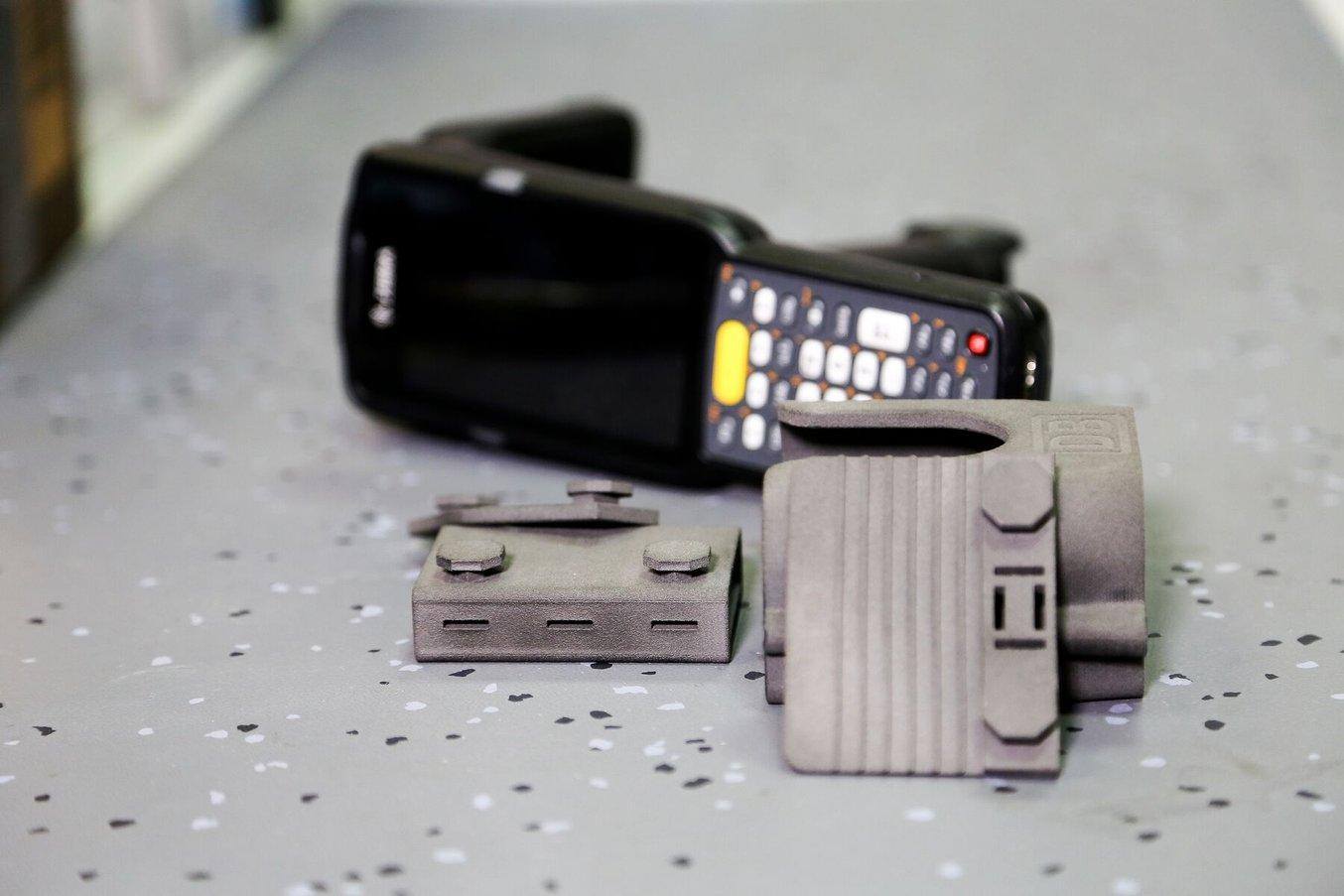
Il team ha creato tre diversi supporti che possono essere fissati a una borsa, una cintura o un pannello per gli utensili.
"Ci hanno chiesto di progettare un supporto per gli scanner portatili, in modo da averli sempre a portata di mano. Abbiamo creato tre diversi supporti che possono essere fissati a una borsa, una cintura o un pannello per gli utensili. La stampa 3D SLS è una tecnologia comoda, perché riproduce fedelmente i modelli e non prevede grandi strutture di supporto da rimuovere, quindi la post-elaborazione è ridotta al minimo: bastano rimozione della polvere e sabbiatura", ha detto Wolfgramm.
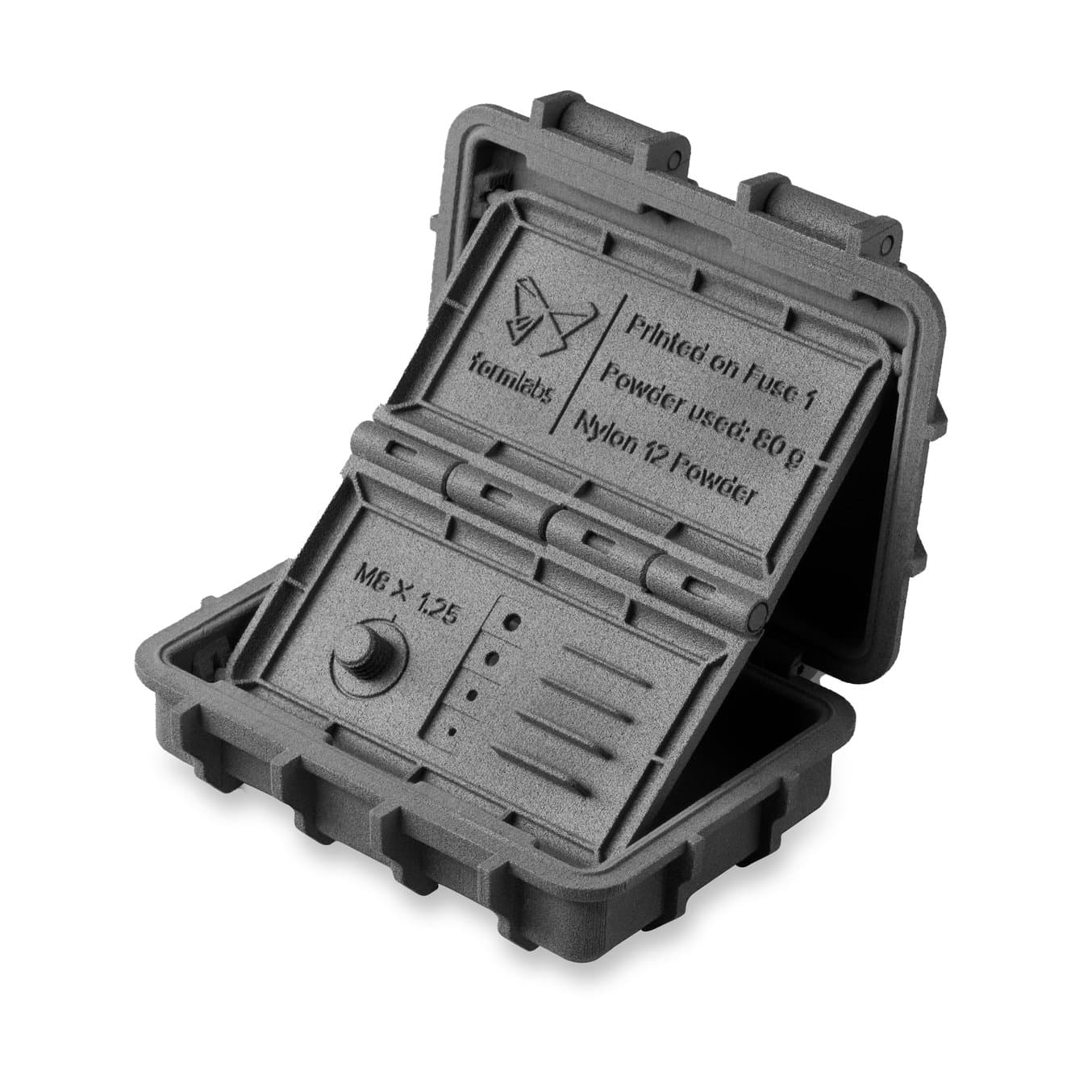
Richiedi un campione gratuito
Guarda e tocca con mano la qualità di Formlabs. Saremo lieti di inviare presso la tua azienda una parte SLS stampata con la Fuse 1+ 30W come campione gratuito.
Sguardo al futuro: digitalizzazione della manutenzione dei veicoli
"La produzione additiva sarà sempre più utilizzata. Consente di realizzare geometrie complesse impossibili da ottenere con apparecchi tradizionali e di produrre e riprodurre strumenti in modo semplice senza costi aggiuntivi elevati. Una volta digitalizzati, lo strumento o la parte possono essere stampati in qualsiasi laboratorio", ha spiegato Wolfgramm.
L'obiettivo finale è naturalmente quello di poter produrre un maggior numero di parti di ricambio per utilizzo finale stampate in 3D per la flotta di treni di Deutsche Bahn. Tuttavia, le norme di sicurezza per i treni sono rigide quanto quelle per gli aerei, se non addirittura di più, e si possono rispettare solo con le stampanti FDM industriali presenti in loco. Deutsche Bahn collabora con Formlabs e altri partner per sviluppare workflow, procedure e materiali che possano essere certificati per soddisfare questi requisiti in futuro.
"Il nostro obiettivo è digitalizzare il 10% di tutte le parti di ricambio entro il 2030. Questo ci permetterà di rifabbricare le parti su richiesta e di consegnarle in tempi molto brevi, ma anche di rispettare l'ambiente e gestire i materiali e le risorse in modo ecologico, rispondendo così anche a molte altre sfide."