Heidelberger Druckmaschinen AG è la principale azienda produttrice di macchine da stampa offset al mondo, presente in oltre 170 Paesi con quasi 10 000 dipendenti. Produce un'ampia gamma di strumenti e soluzioni di automazione per l'intera catena del valore nel settore della stampa, da alcune delle più grandi e veloci macchine da stampa all'avanguardia a taglierine e piegatrici.
Circa sei anni fa, HEIDELBERG ha inserito nel suo workflow anche la stampa 3D. Inizialmente, ha introdotto questa tecnologia per ottimizzare la prototipazione e lo sviluppo dei prodotti, riducendo i costi e i tempi di produzione. Attualmente l'azienda utilizza le parti stampate in 3D per la produzione in serie, realizzando migliaia di parti all'anno per circa 15 applicazioni diverse.
Continua a leggere per scoprire come le parti realizzate con la stampa 3D a sinterizzazione laser selettiva (SLS) possono essere utilizzate in applicazioni di robotica leggera e persino sostituire le parti in acciaio delle piegatrici.
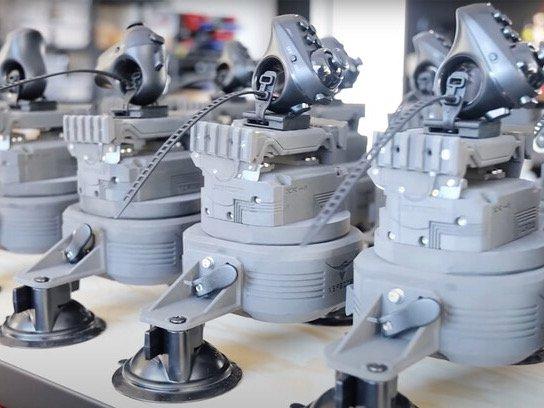
Test di resistenza su parti stampate in 3D per applicazioni per utilizzo finale
In questo whitepaper vengono illustrate le soluzioni di Formlabs in ambito di hardware e materiali per la stampa 3D di parti per utilizzo finale. Saranno inoltre presentati vari casi di studio e risultati di test di resistenza, eseguiti per verificare l'idoneità dei materiali di stampa 3D per applicazioni per utilizzo finale.
Accelerazione dello sviluppo dei prodotti
"HEIDELBERG si affida a noi per i progetti relativi ai nuovi sviluppi, soprattutto per la realizzazione di componenti e assemblaggi impossibili da produrre in maniera tradizionale", ha dichiarato Joachim Krumma.
Dopo aver lavorato per 15 anni presso HEIDELBERG occupandosi dello sviluppo di prodotti e applicazioni, Krumma dirige ora CTS-3 GmbH, una società di consulenza tecnologica nel campo della produzione additiva. CTS-3 GmbH collabora a stretto contatto con il team di ricerca e sviluppo di HEIDELBERG e fornisce supporto nello sviluppo dei prodotti e nel passaggio alla produzione in serie per le nuove applicazioni.
Una parte di questo sviluppo avviene sul campo, per testare e perfezionare direttamente il prodotto di HEIDELBERG con il feedback in tempo reale della clientela finale.
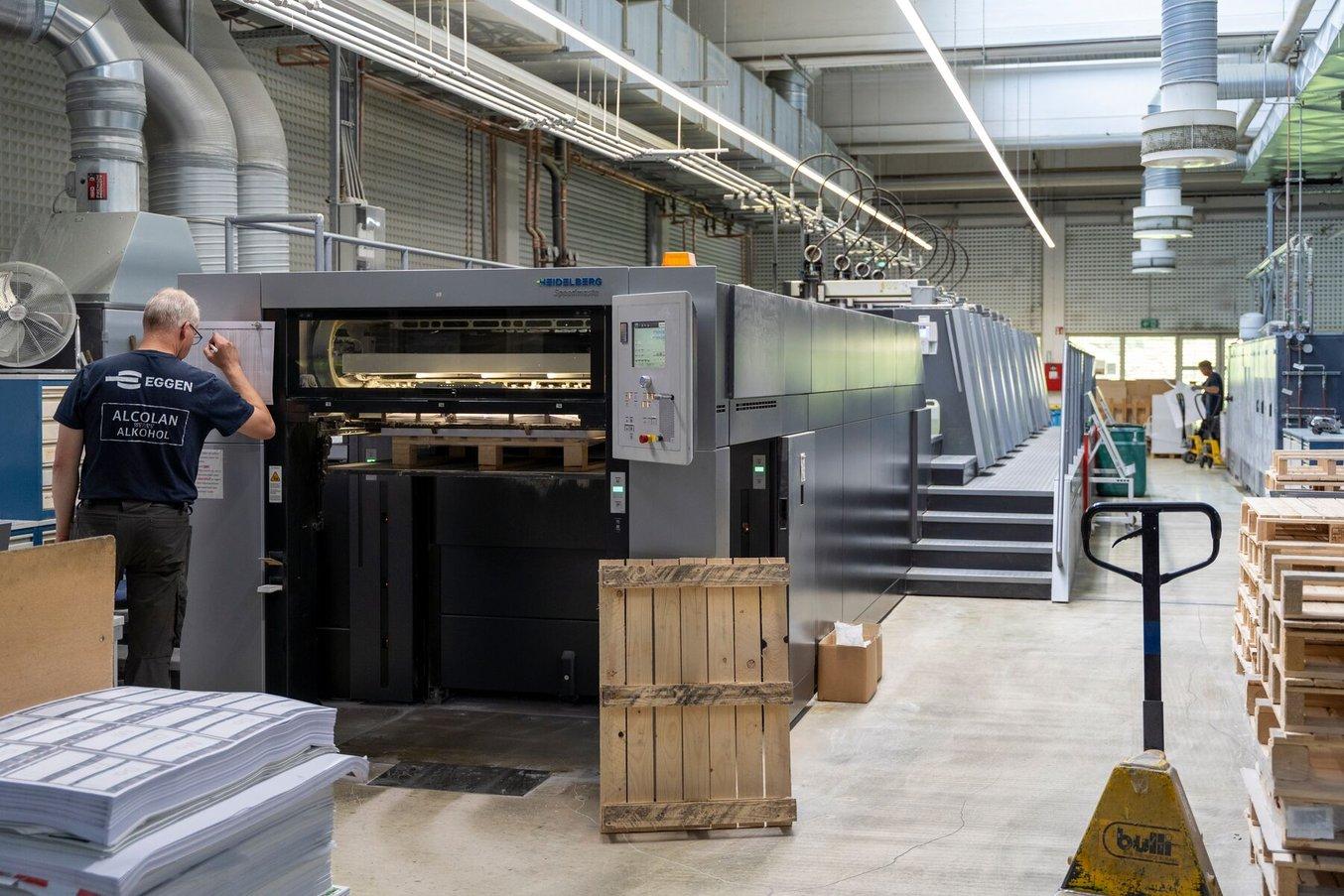
Meinders & Elstermann è una grande azienda di stampa offset con sede a Belm, in Germania.
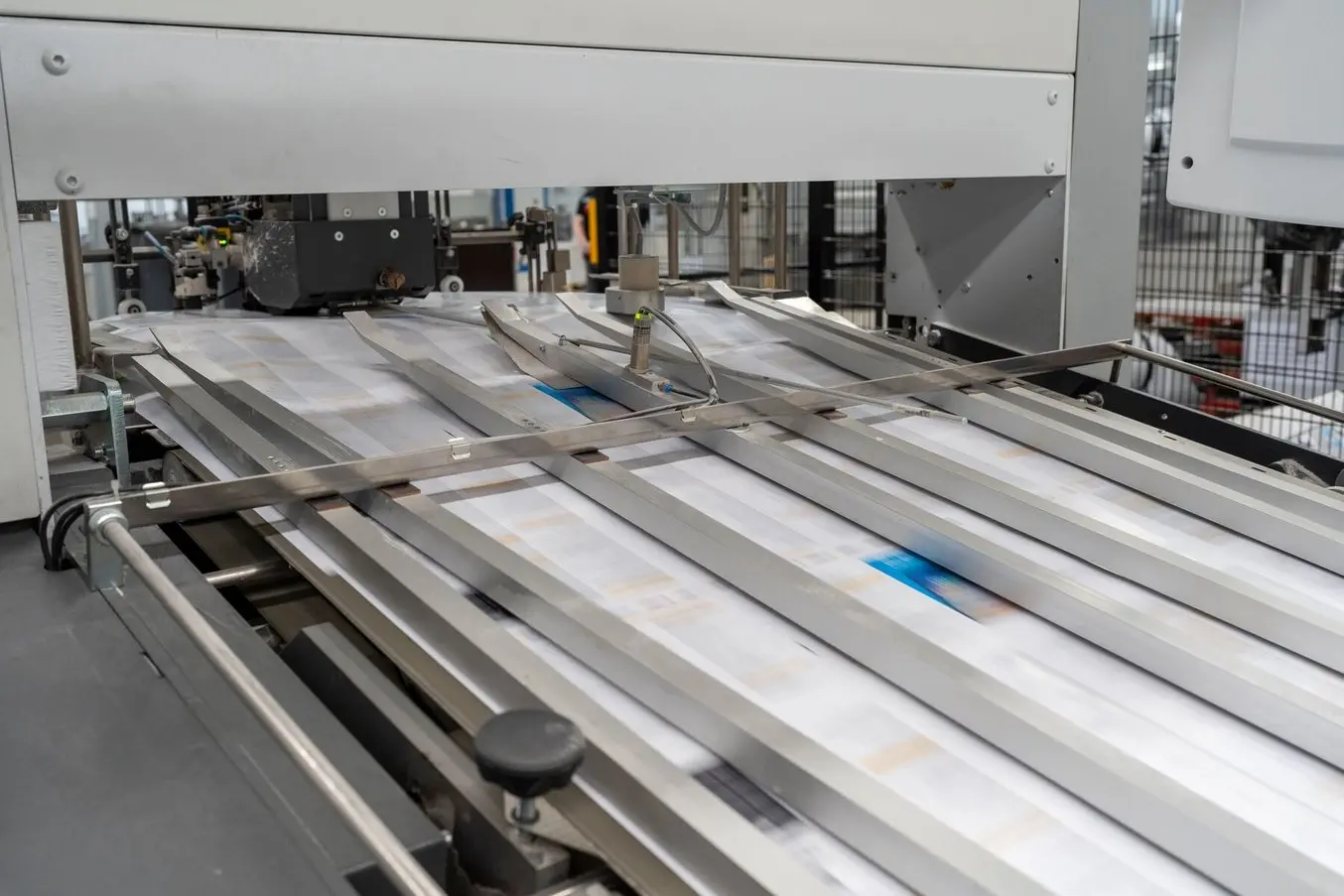
I nuovi prodotti di HEIDELBERG vengono testati e ulteriormente sviluppati presso la loro sede.
"Meinders & Elstermann è una grande azienda di stampa offset con sede a Belm, in Germania. Stampiamo circa 100-120 milioni di fogli di carta all'anno. Abbiamo quattro macchine da stampa HEIDELBERG nella tipografia e sette piegatrici nel reparto di finitura delle stampe. Noi testiamo gli apparecchi che HEIDELBERG vuole lanciare sul mercato, sottoponendoli a un processo di sviluppo continuo presso la nostra struttura", ha affermato Klaus Harig, responsabile del reparto di lavorazione di Meinders & Elstermann GmbH & Co. KG.
Le parti stampate in 3D vengono impiegate per un'ampia gamma di applicazioni: parti leggere per i robot pick-and-place, nuovi componenti per le piegatrici e parti sostitutive per i componenti in acciaio degli apparecchi. Per produrle, il team utilizza una stampante 3D SLS della serie Fuse e la Nylon 12 Powder per le parti rigide o la TPU 90A Powder per quelle flessibili.
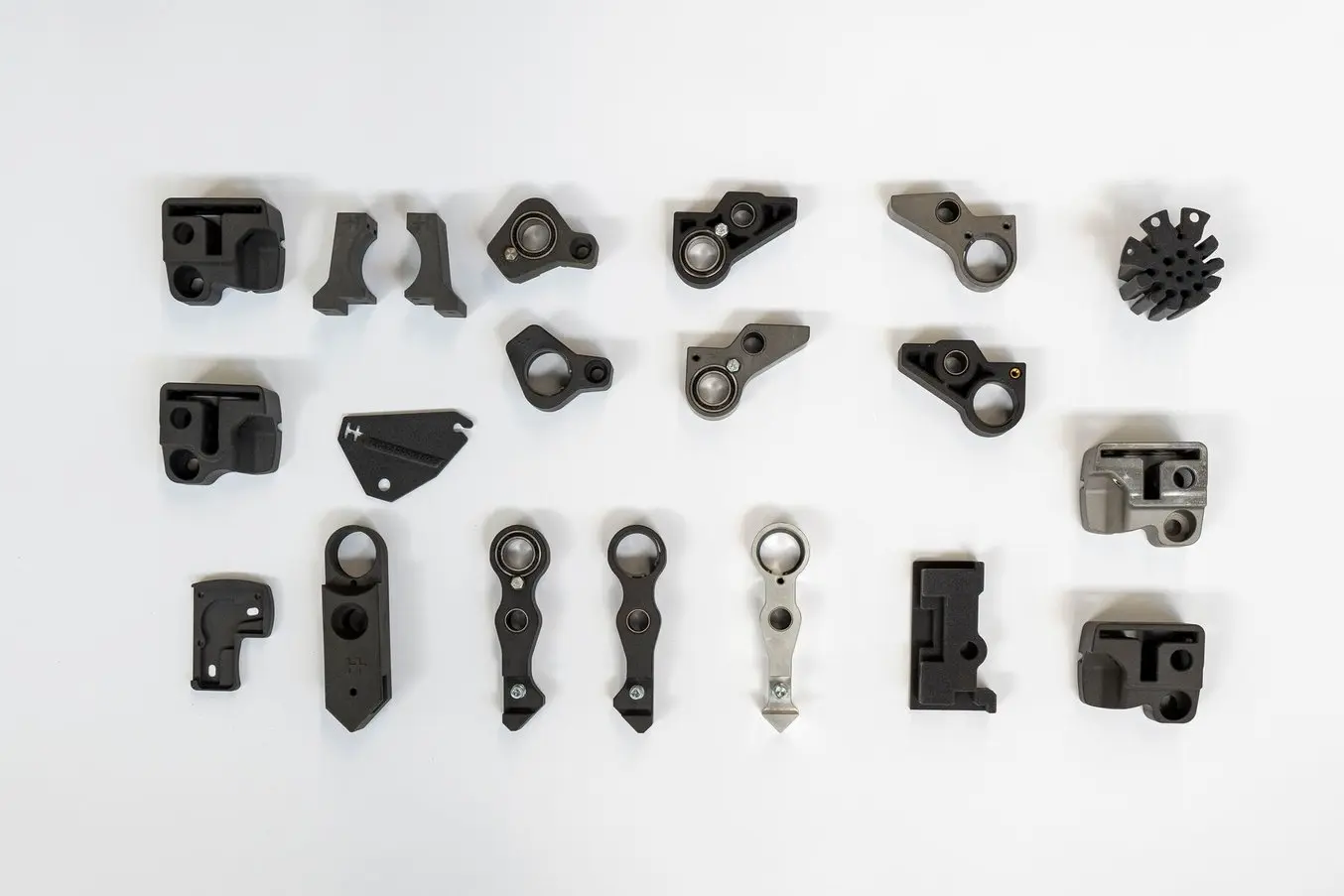
HEIDELBERG utilizza le parti stampate in 3D per un'ampia gamma di applicazioni, tra cui parti leggere per i robot e parti sostitutive per i componenti in acciaio degli apparecchi.
"Un aspetto fondamentale per noi è la velocità della stampa 3D. Abbiamo tempi di risposta rapidi alle richieste della clientela, che cambiano continuamente. Siamo in grado di sviluppare e produrre nuove parti in uno o due giorni, mentre prima in alcuni casi occorrevano diverse settimane. Ecco perché la stampa 3D è perfetta per noi."
Joachim Krumma, dirigente presso CTS-3 GmbH
Oltre a ridurre i tempi di realizzazione, i risparmi sui costi sono enormi, soprattutto nel campo della prototipazione, ma anche nella produzione in serie di parti per utilizzo finale personalizzate con volumi ridotti. "I costi sono spesso 10 o 20 volte inferiori rispetto alla normale produzione di parti", ha dichiarato Krumma.
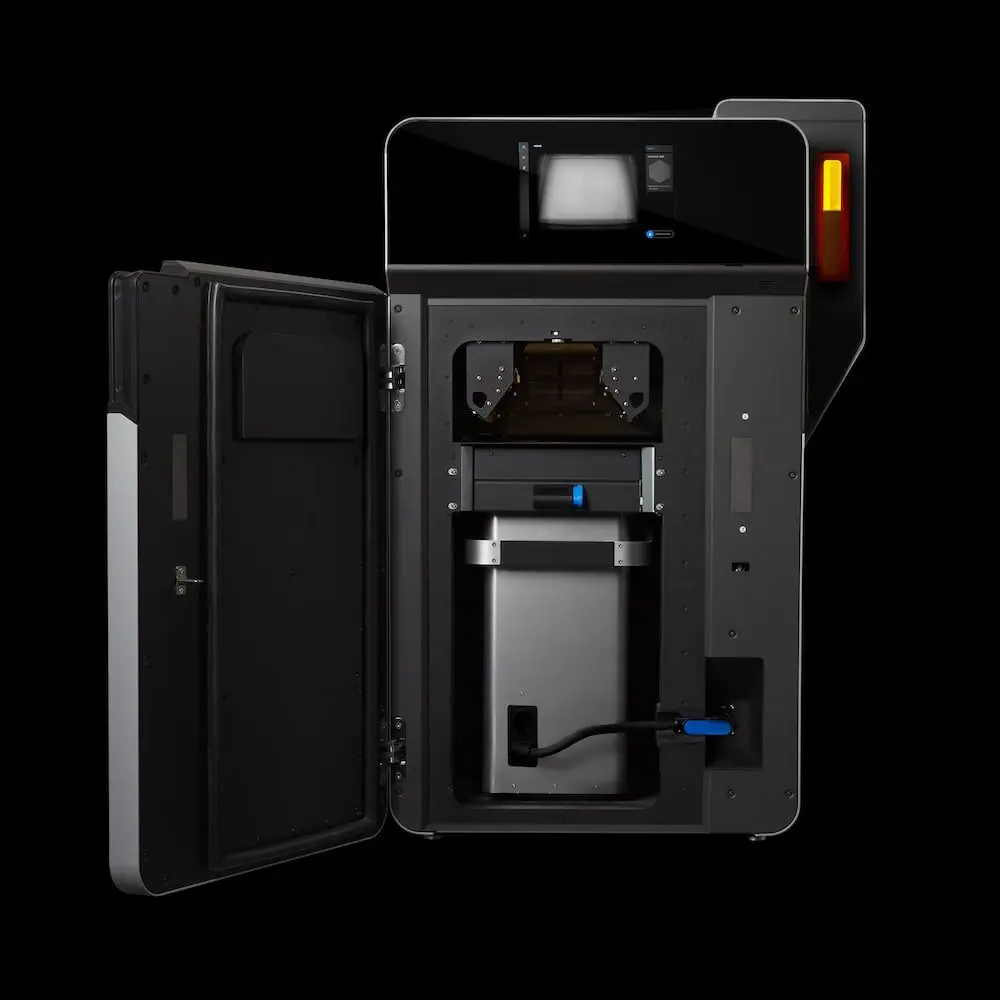
Produzione rapida di parti SLS ad alte prestazioni con la nuova Fuse 1+ 30W
Guarda la nostra dimostrazione di prodotto per un'introduzione alla Fuse 1+ 30W e alla stampa 3D SLS svolta dagli esperti di Formlabs.
Parti leggere per la robotica
L'apparecchio con il maggior numero di componenti stampati in 3D è il P-Stacker, un sistema robotizzato pick-and-place all'avanguardia che preleva i pacchi di fogli piegati dalla piegatrice e li posiziona su un pallet.
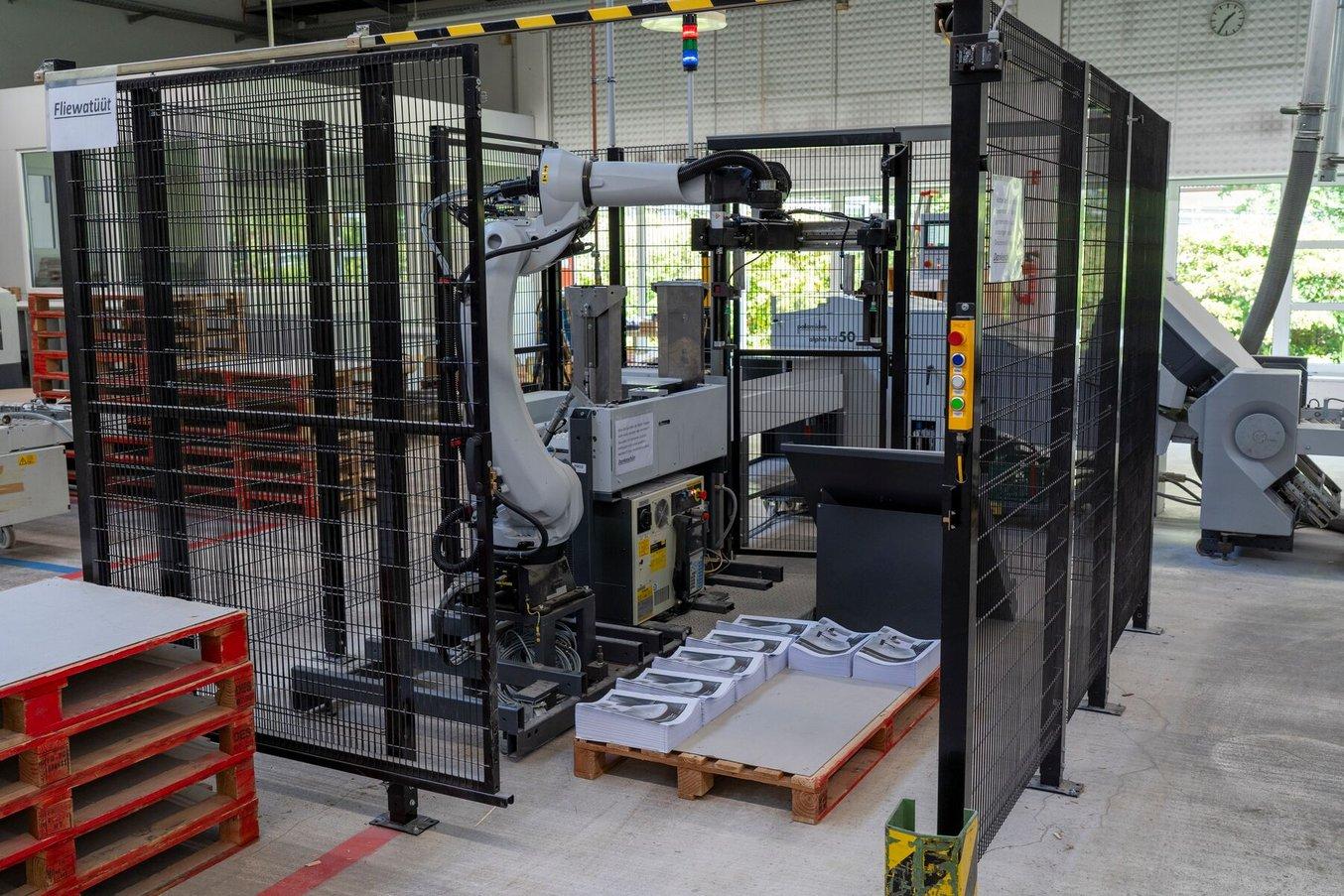
Il P-Stacker si occupa di accatastare i pacchi di fogli dietro la piegatrice, riducendo il carico di lavoro del personale.
"Il robot è in grado di impilare i pallet fino a raggiungere un metro di altezza. A seconda della sua velocità, riesce a disporre fino a 18 000 fogli all'ora. Prima di iniziare a usare il P-Stacker, questo compito era affidato a una sola persona che doveva spostare ogni giorno da quattro a sei tonnellate di pacchi sui pallet", ha spiegato Harig.
Molte delle parti stampate in 3D all'interno di questo robot sono molto complesse e svolgono diverse funzioni contemporaneamente, come i giunti e le staffe universali responsabili del movimento e del fissaggio dell'asse, dell'aspirazione pneumatica, della tecnologia dei sensori e delle proprietà di scorrimento.
"Il peso ha un ruolo essenziale, soprattutto nelle applicazioni di robotica. È direttamente proporzionale alla sollecitazione meccanica a cui sono sottoposte le parti, che incide sulla loro resistenza alla fatica. Il sistema ha una densità di componenti piuttosto elevata, il che significa che abbiamo poco spazio a disposizione per assemblaggi e parti di grandi dimensioni", ha dichiarato Krumma.
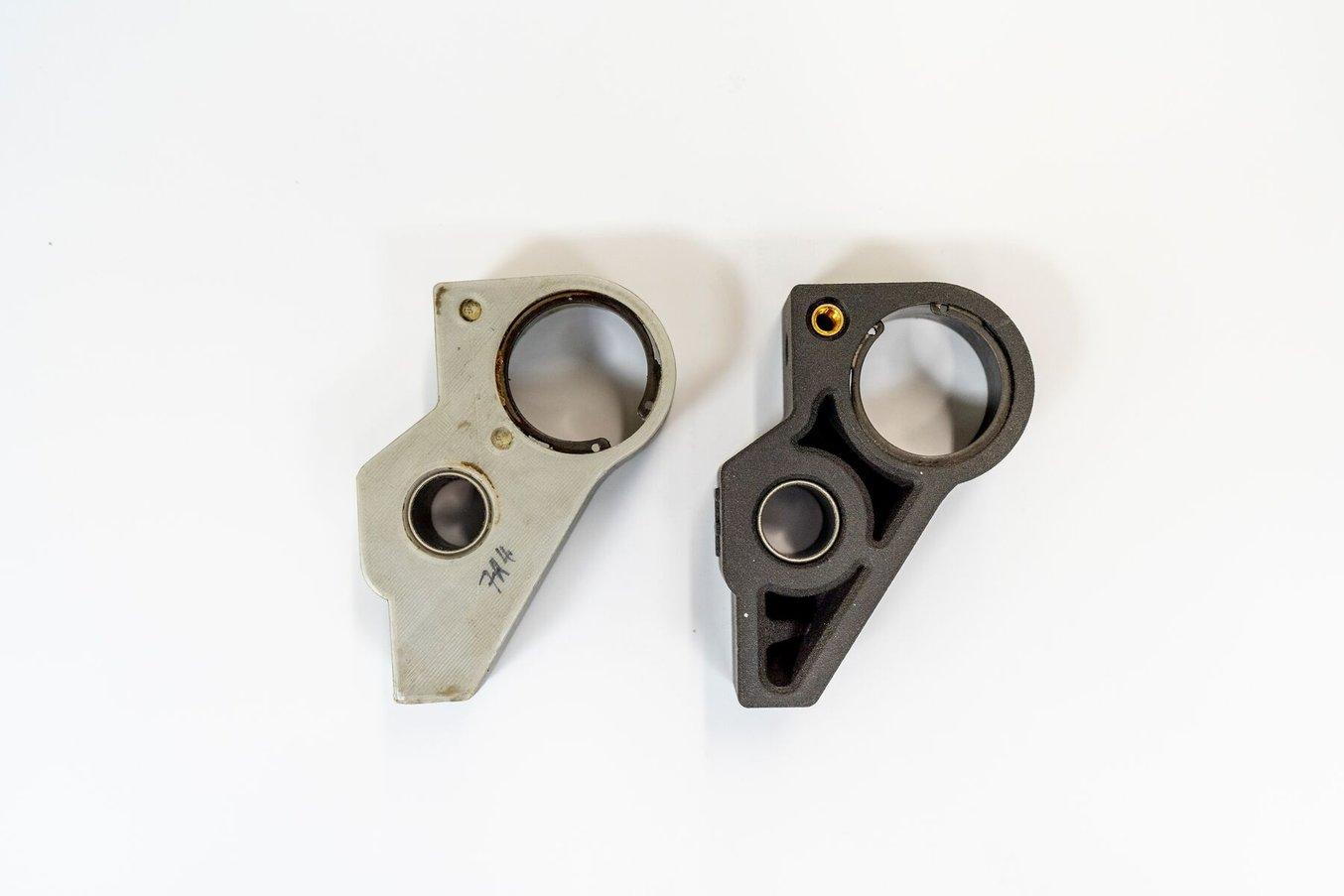
Le parti in plastica stampate in 3D sono più leggere dell'acciaio e i design possono essere ottimizzati ulteriormente a seconda delle sollecitazioni e delle forze a cui vengono sottoposti. Un design più complesso non comporta costi più elevati, a differenza di quanto accade con gli strumenti di produzione tradizionali, come la lavorazione meccanica.
Di conseguenza, spesso si ottengono strutture molto complesse e amorfe, sviluppate appositamente per un'applicazione specifica in base alle sollecitazioni e alle forze a cui sono sottoposte, che possono essere molto elevate a causa dell'utilizzo continuo. Le parti stampate in 3D sono spesso combinate con altri elementi come cuscinetti in metallo o componenti rivestiti in teflon, che hanno proprietà anti-frizione.
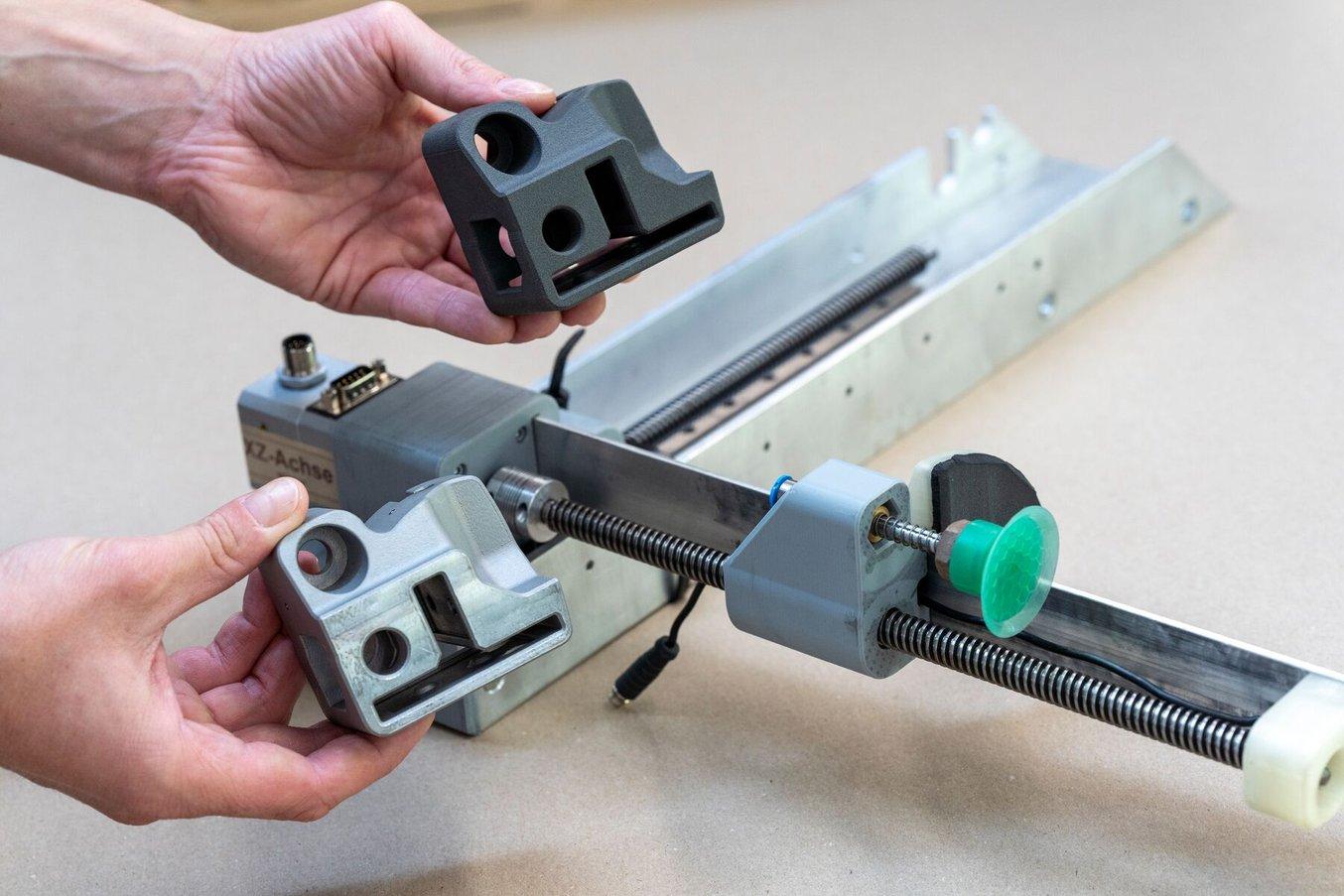
Molte parti stampate in 3D all'interno del robot sono molto complesse e svolgono diverse funzioni. I componenti robusti e resistenti vengono prodotti in Nylon 12 Powder.
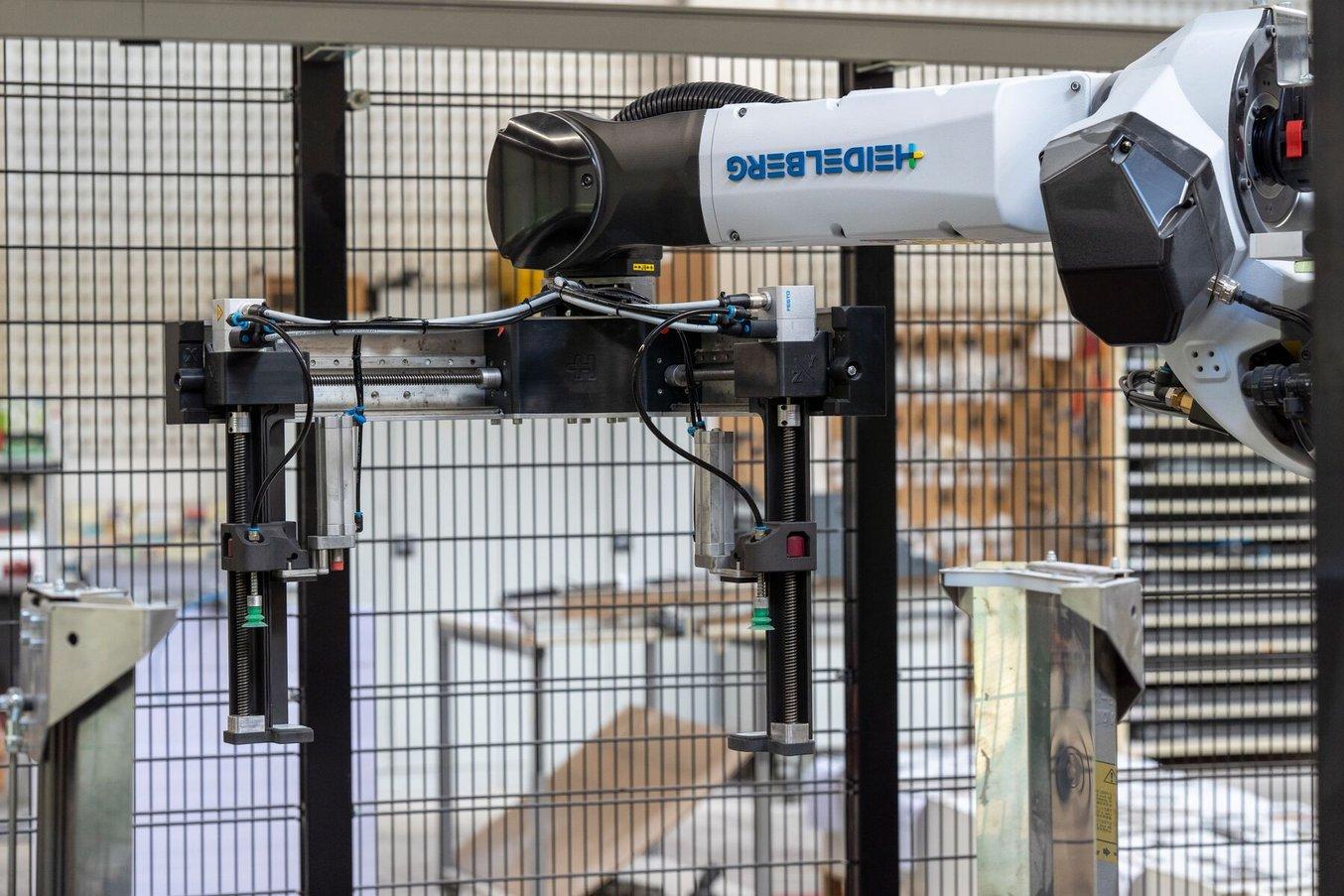
Il peso ha un ruolo essenziale, poiché è direttamente proporzionale alla sollecitazione meccanica a cui sono sottoposte le parti.
Molte di queste forme complesse non sarebbero né convenienti né ottenibili con metodi tradizionali come la lavorazione meccanica, poiché alcune parti contengono diversi assemblaggi e componenti che dovrebbero essere minuziosamente montati, allineati e rilavorati. Inoltre, sarebbero molto più pesanti e la densità dei componenti sarebbe ancora più elevata.
"Se anche fosse possibile produrre diverse parti in maniera tradizionale, l'impegno richiesto sarebbe comunque enorme, diversamente da quanto accade con la stampa 3D. La stampa SLS, grazie alla possibilità di semplificare componenti e assemblaggi, ci permette di riprodurre forme piuttosto complesse poiché riusciamo a sviluppare e stampare geometrie molto amorfe. È perfetta per noi."
Joachim Krumma, dirigente presso CTS-3 GmbH
Alcune parti sono meno complesse, ma richiedono comunque un'elevata precisione o delicatezza. Si tratta di parti flessibili che impediscono la contaminazione, proteggono gli spigoli vivi e i sensori o evitano l'usura.
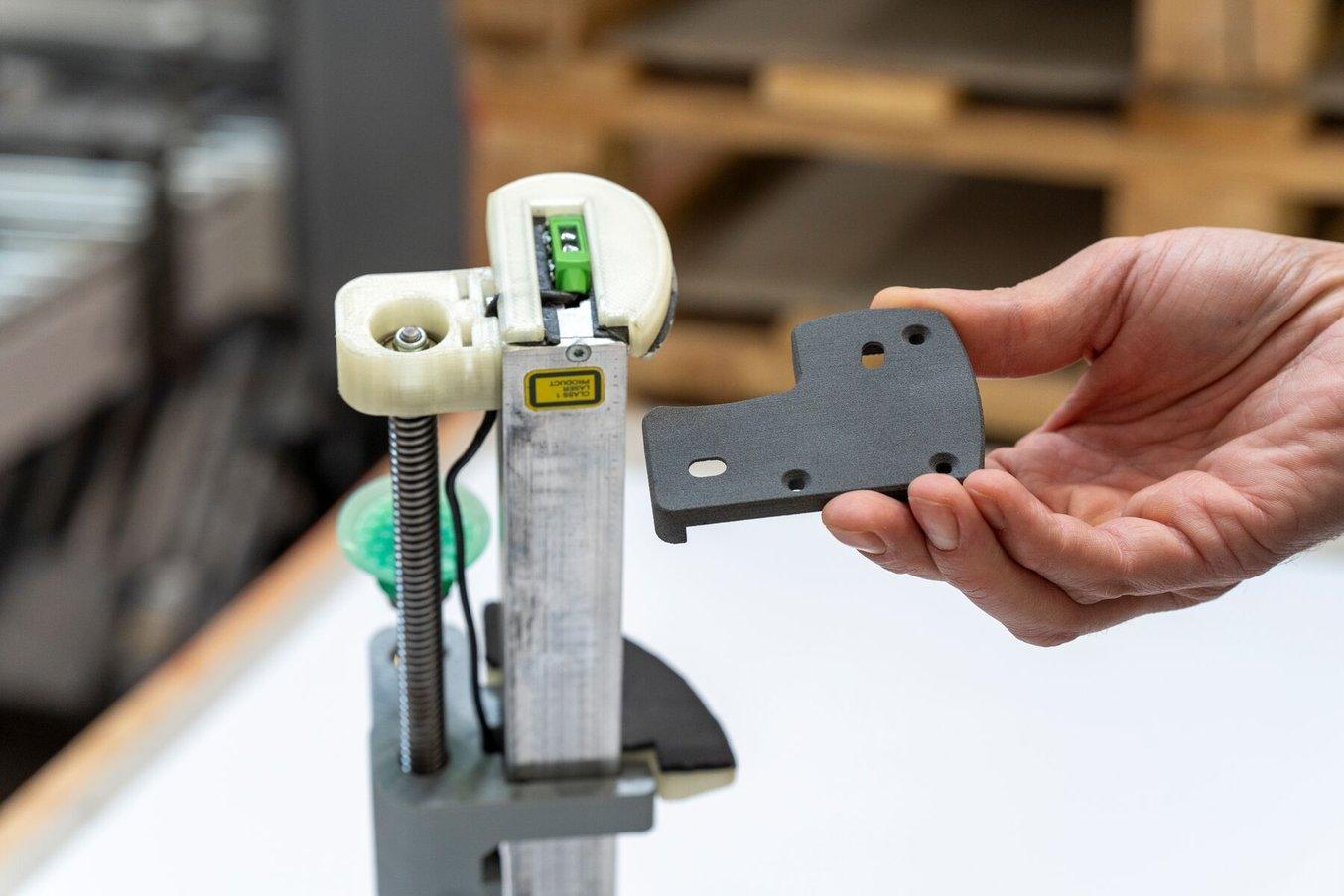
Parte flessibile stampata in TPU 90A Powder che protegge i sensori e altri componenti per organi di presa.
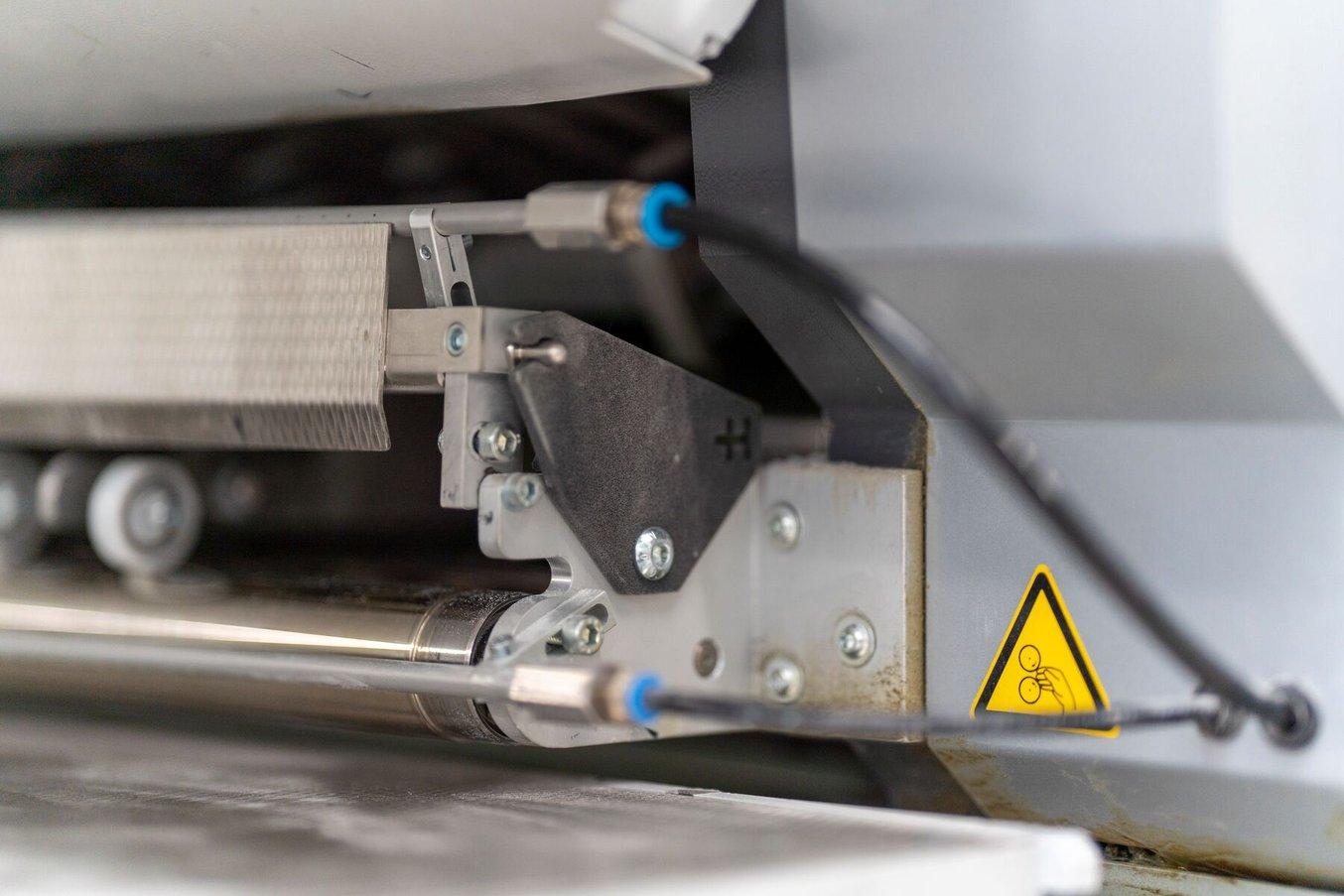
Le parti flessibili sono ideali per i componenti con accoppiamento a scatto. Proteggendo gli spigoli vivi, proteggono anche il personale.
"Nel nostro robot è stata recentemente installata una parte stampata in 3D in grado di prevenire la rottura dei cavi e quindi di aumentarne naturalmente la vita utile. In questo modo riusciamo a evitare giorni di inattività quando i cablaggi devono essere sostituiti", ha dichiarato Harig.
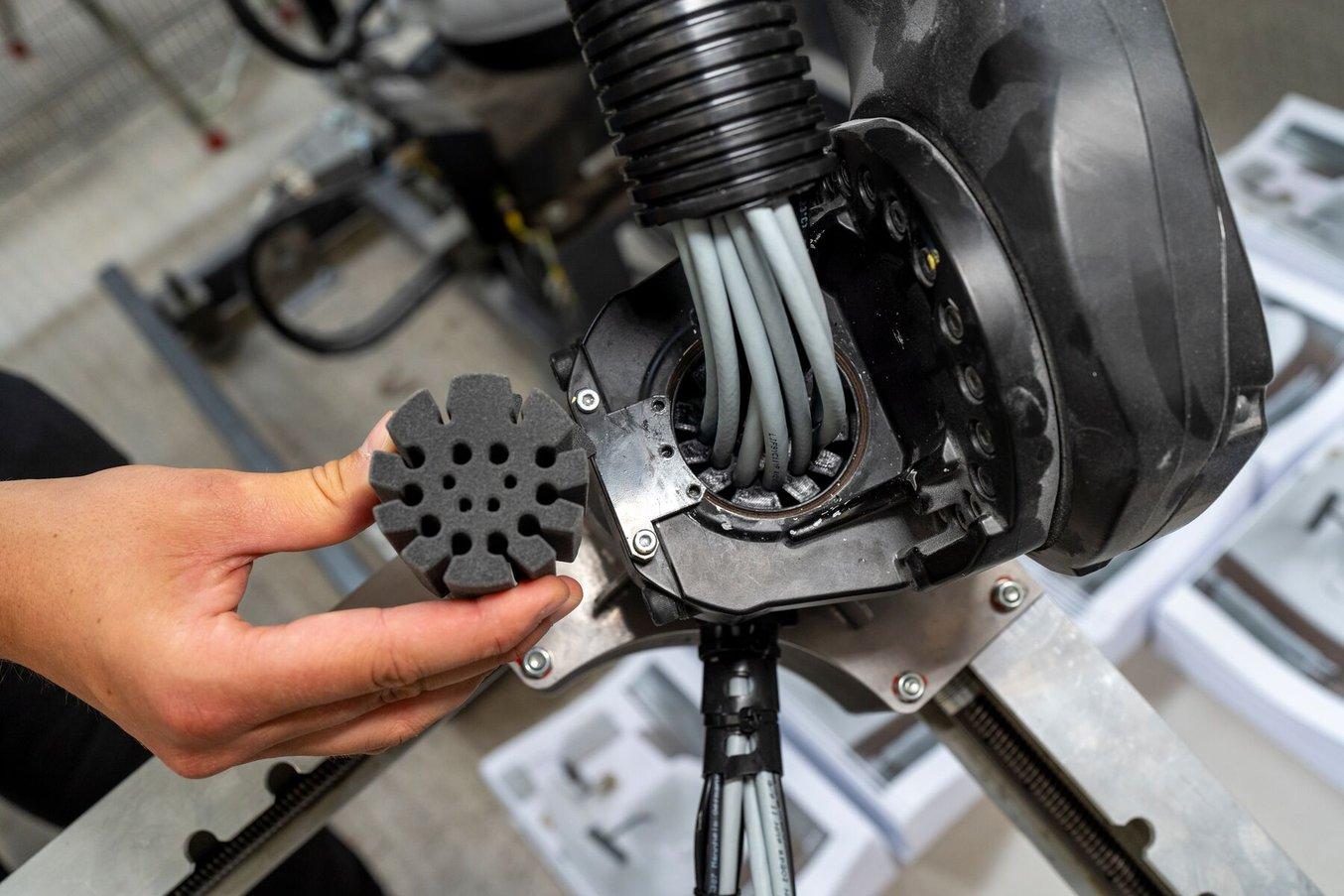
Questa guida flessibile, prodotta con una stampante 3D SLS della serie Fuse, ha un design complesso e offre una soluzione resistente a lungo termine per proteggere i cavi dall'usura.
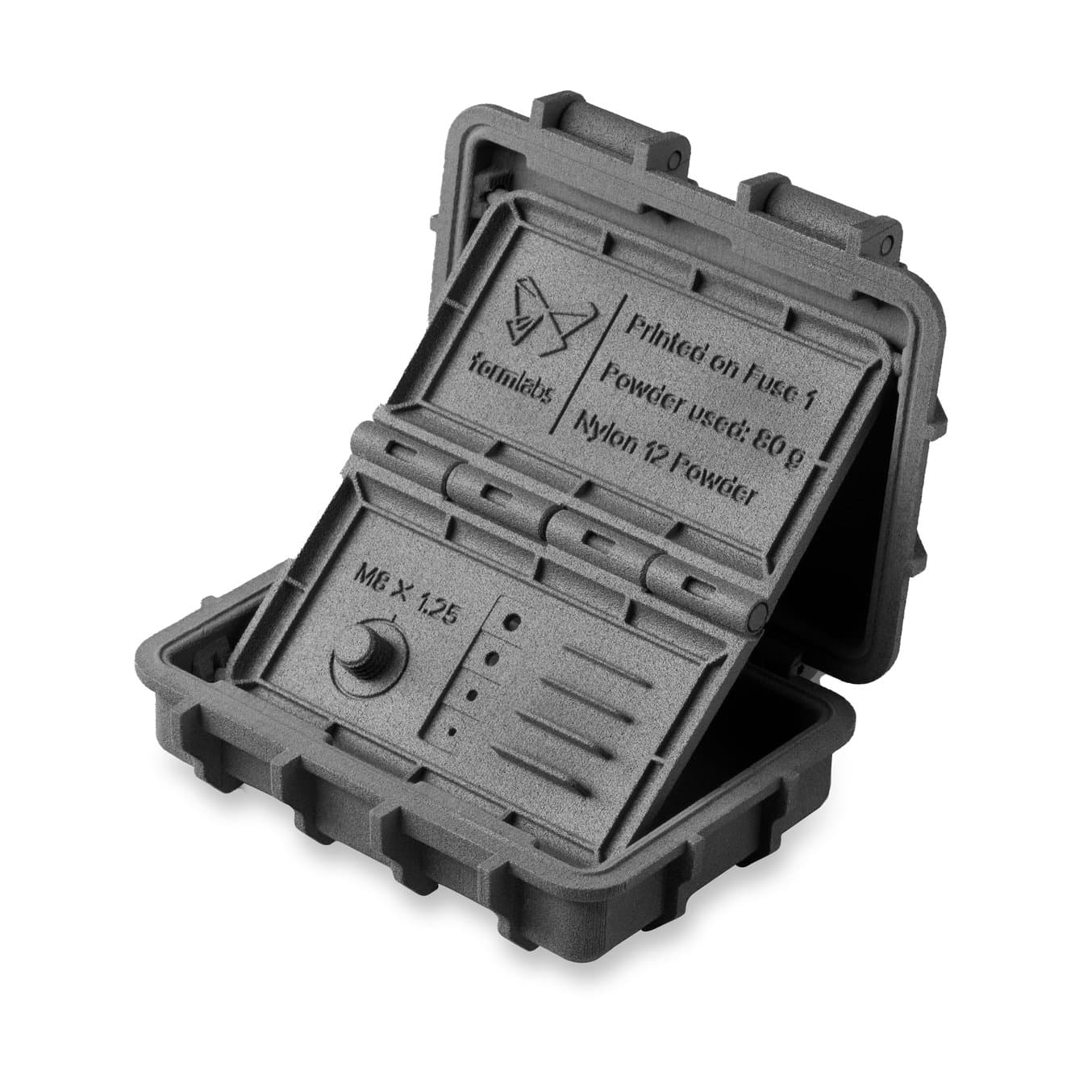
Richiedi un campione gratuito
Guarda e tocca con mano la qualità di Formlabs. Saremo lieti di inviare presso la tua azienda una parte SLS stampata con la Fuse 1+ 30W come campione gratuito.
Parti di ricambio che sostituiscono l'acciaio
Evitare e ridurre i tempi di inattività degli apparecchi è essenziale nel settore della stampa: eventuali ritardi possono tradursi in consegne non effettuate e rendere obsoleto il materiale stampato. L'ampia rete di assistenza di HEIDELBERG è in grado di spedire il 95% delle parti sostitutive a qualsiasi destinazione in tutto il mondo entro 24 ore, ma il team voleva verificare se le parti sostitutive stampate in 3D su richiesta potessero rappresentare una soluzione per le parti fuori produzione.
In una delle vecchie piegatrici di Meinders & Elstermann, Krumma ha installato delle parti stampate in 3D per sostituire una serie di componenti che originariamente erano stati realizzati in acciaio mediante lavorazione meccanica, come i giunti che sostengono i rulli metallici che pesano fino a 13 kg. Le parti si trovano sotto il coperchio dell'apparecchio, sono esposte a un ambiente eccessivamente sporco e grasso e sottoposte a notevoli sollecitazioni meccaniche e fisiche dovute all'uso prolungato, anche durante gli arresti di emergenza, quando l'intero apparecchio si blocca in una frazione di secondo.
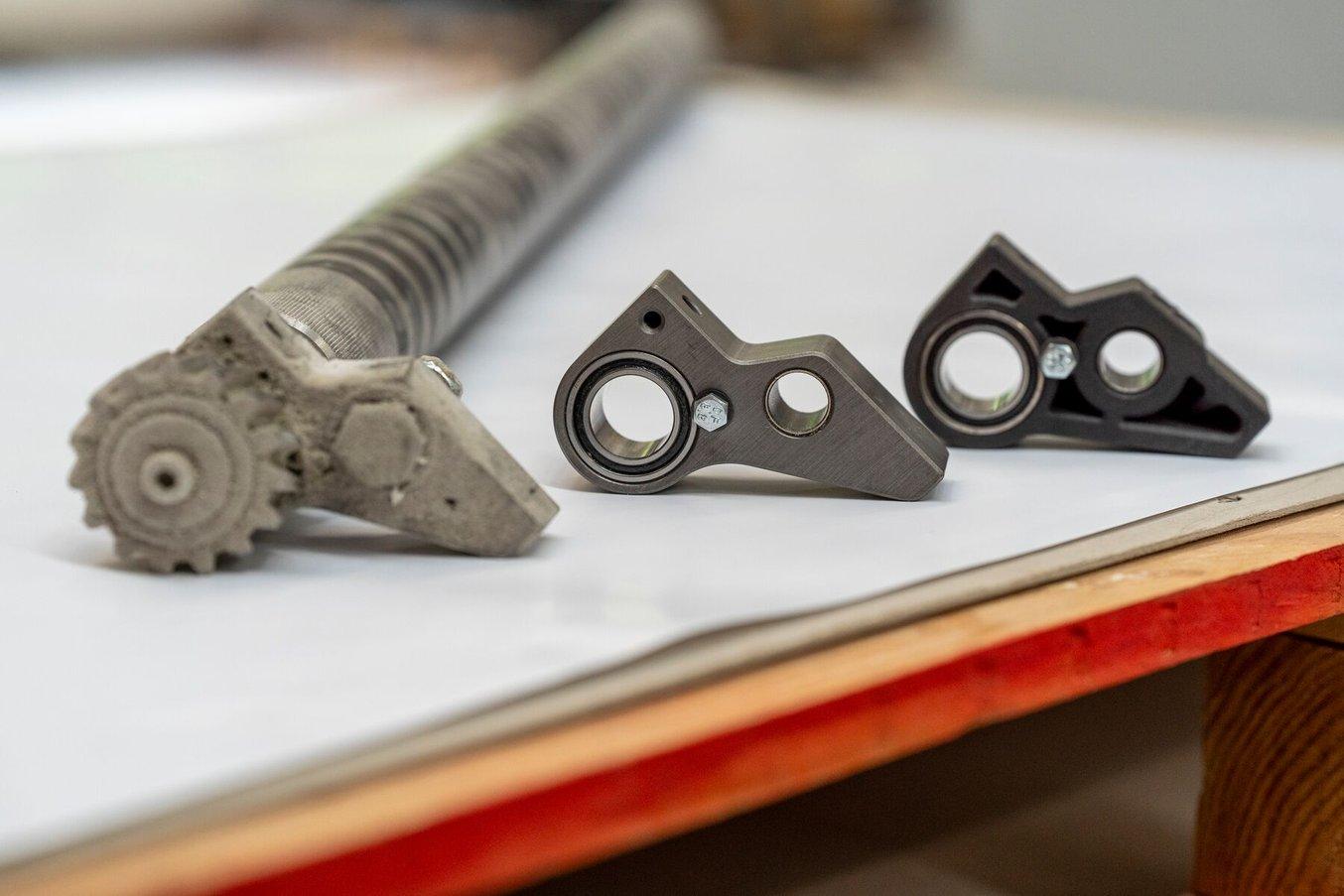
Le parti sostitutive stampate in 3D sono assemblate con cuscinetti e componenti metallici anti-frizione.
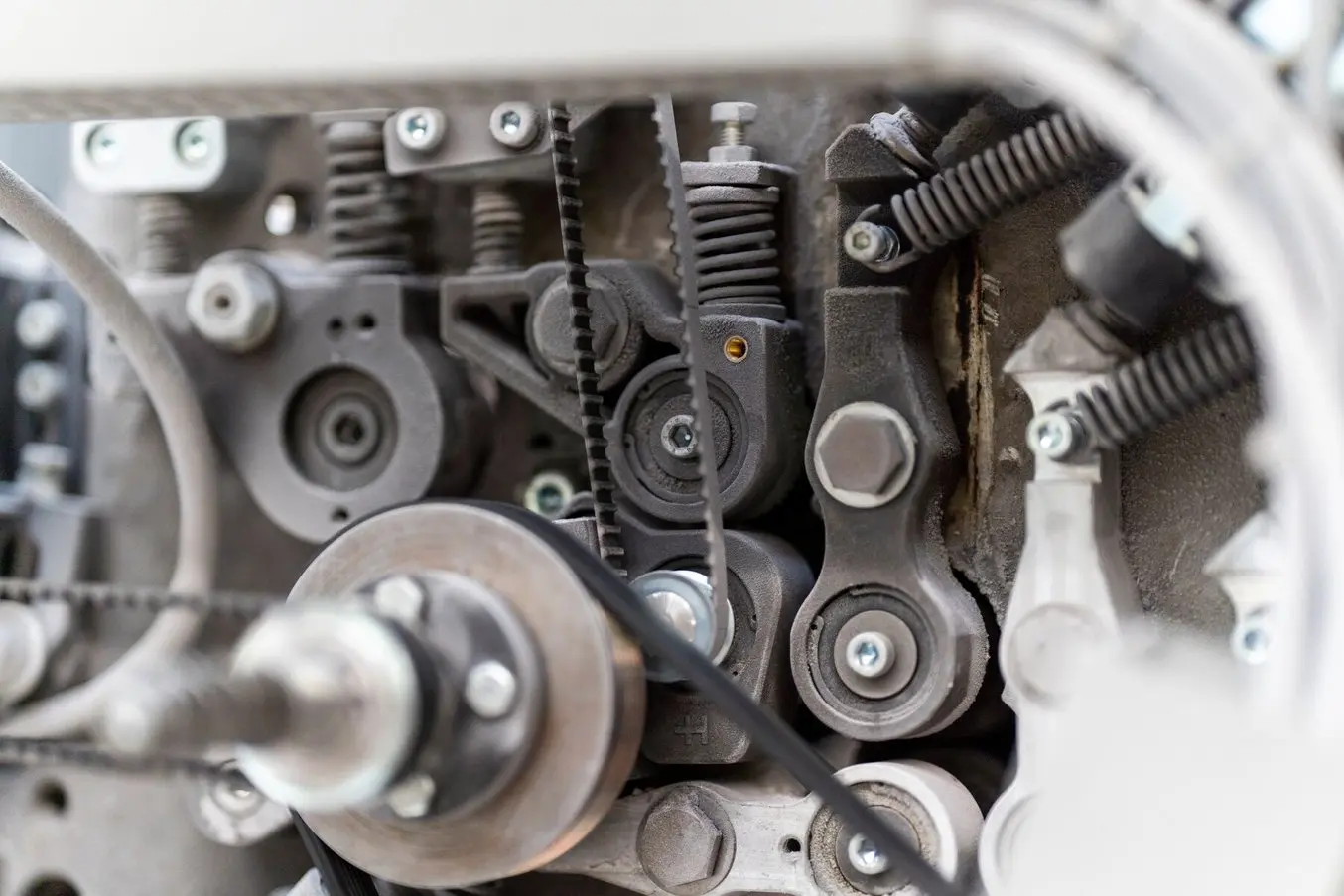
I giunti sostengono i rulli metallici che ruotano ad alta velocità e pesano fino a 13 kg ciascuno.
"Devono resistere a sollecitazioni continue, vale a dire due turni per cinque giorni a settimana con carichi estremamente elevati. Le parti attualmente installate si trovano negli apparecchi da più di due anni e mezzo. Questo non era previsto nella fase iniziale di sviluppo. Tuttavia, le abbiamo tenute sotto costante osservazione ed è apparso subito chiaro che erano in grado di resistere a questo carico continuo."
Joachim Krumma, dirigente presso CTS-3 GmbH
"Devo dire che sono decisamente molto resistenti. Neanch'io ci credevo, ma finora non è stato necessario sostituire nessuna parte nelle nostre piegatrici", ha aggiunto Harig.
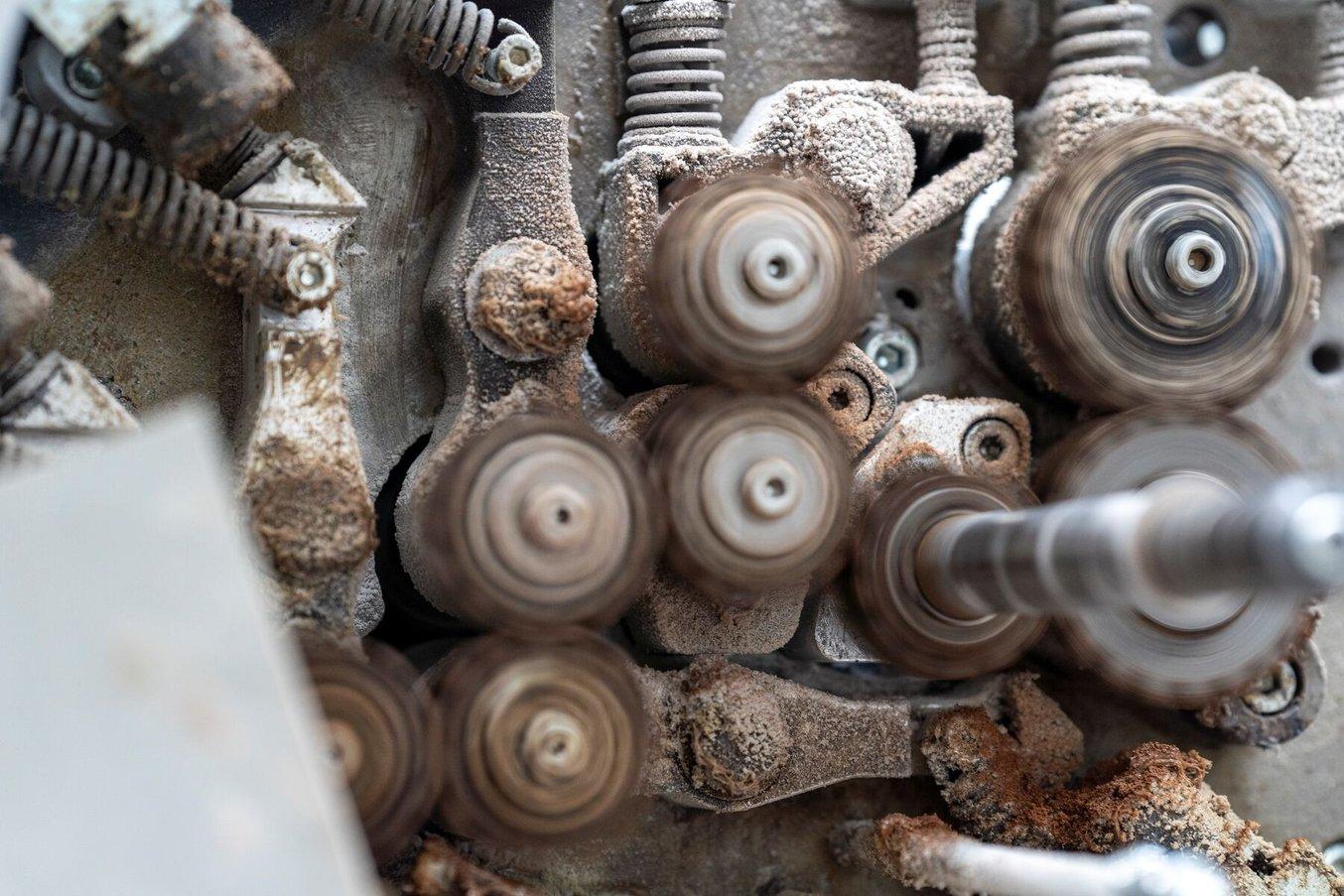
Alcune delle parti sostitutive stampate in 3D sono state installate due anni e mezzo fa in una piegatrice, operativa su due turni per cinque giorni alla settimana, e sono esposte a un ambiente eccessivamente sporco e grasso.
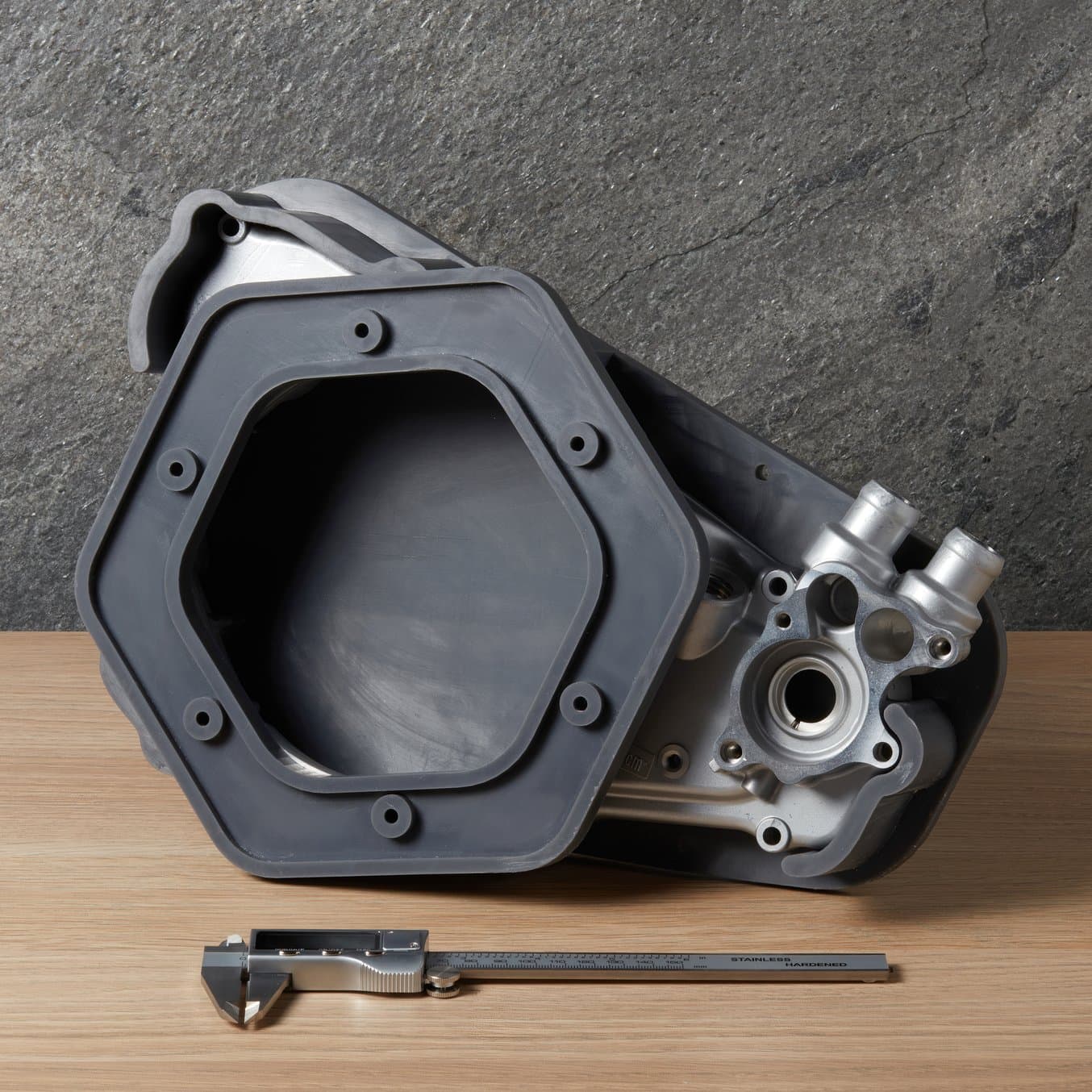
Come stampare in 3D dime, fissaggi e altri supporti di produzione in-house
Questo whitepaper illustra i principi fondamentali alla base della creazione in-house di dime, fissaggi e altri supporti di produzione efficaci.
Un supporto alla stampa per rimanere competitiva
"Buona parte della clientela preferisce i prodotti online a quelli stampati. Di conseguenza, il numero di ordini a cui eravamo abituati si è ridotto. Le tirature sono sempre più limitate e devono essere disponibili più rapidamente. L'unico modo per affrontare questa situazione è utilizzare nuovi apparecchi. In futuro ci saranno meno tipografie e quelle che resteranno dovranno assicurarsi di essere ben preparate ad affrontare le sfide del futuro", ha affermato Harig.
Il ricorso alle stampanti 3D e la collaborazione con aziende come la CTS-3 GmbH di Krumma ha permesso a HEIDELBERG di accelerare lo sviluppo dei prodotti e alla clientela finale di rimanere competitiva in un mercato in rapida evoluzione.
"Se non avessimo avuto a disposizione questa tecnologia, in particolare la stampa 3D SLS con la serie Fuse, i processi di sviluppo si sarebbero notevolmente prolungati. Le stampanti 3D ci permettono di completare passaggi di sviluppo molto impegnativi in pochissimo tempo. Possiamo testare, rifiutare o sviluppare ulteriormente le idee e produrre le parti durante la notte per poi testarle nelle sedi della clientela il giorno successivo. Senza questa tecnologia, il processo di sviluppo sarebbe pressoché simile alla produzione tradizionale."
Joachim Krumma, dirigente presso CTS-3 GmbH
"La stampa 3D compie passi da gigante ogni anno. Chi resta fermo rimane indietro. Il processo di stampa 3D si è rivelato da subito molto vantaggioso rispetto alla produzione tradizionale. Non vediamo l'ora di scoprire cosa ci riserverà il futuro", ha affermato Krumma.