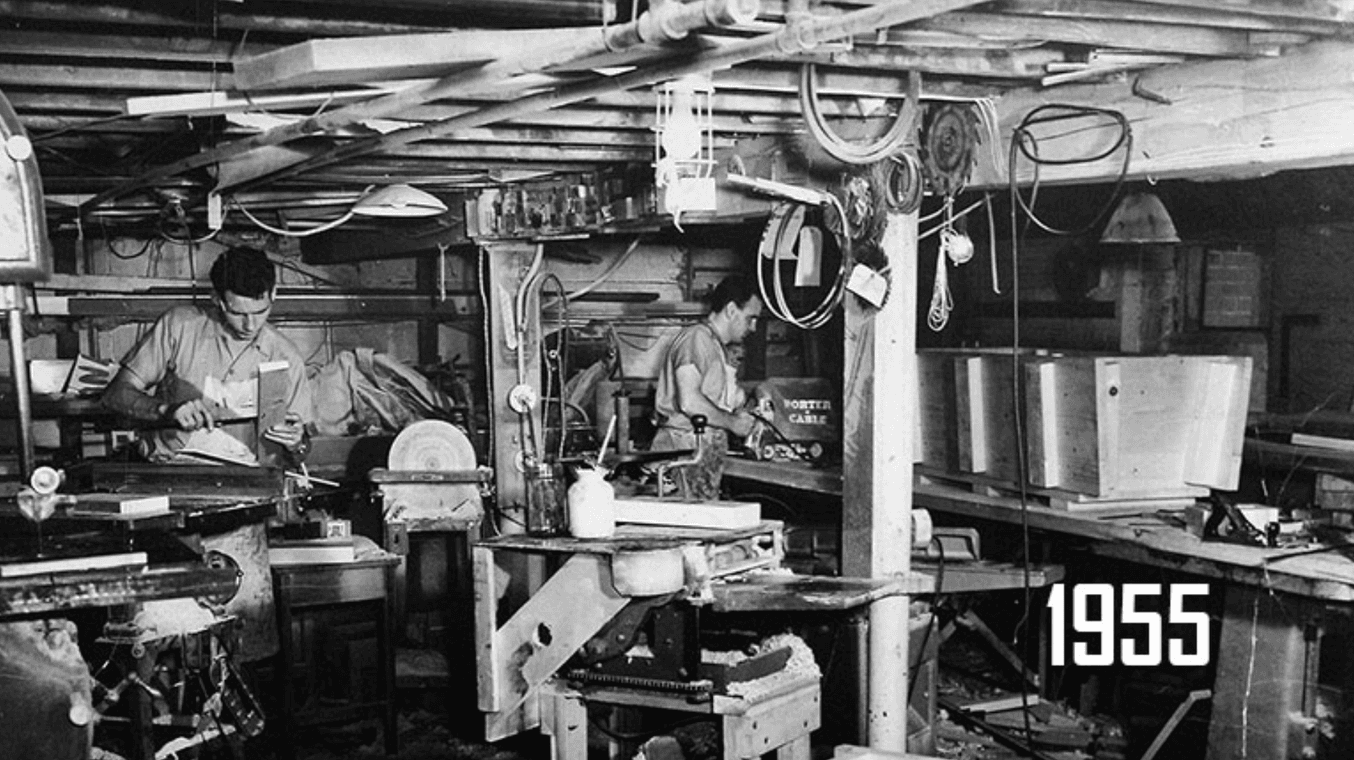
Productive Plastics si occupa di produzione di plastica dal 1955 e realizza tramite termoformatura parti di alta qualità per il settore medico, ferroviario, elettronico, automobilistico e non solo.
Productive Plastics si occupa di produzione di plastica tramite termoformatura a livello industriale. Ogni aspetto di questa azienda è eccezionalmente grande, dagli apparecchi ai clienti fino ai volumi. In qualsiasi momento può trovarsi a dover gestire un ordine di centinaia di scudi protettivi per dispositivi medici di grandi dimensioni per svariate aziende sanitarie della lista Fortune 500, ma anche a dover produrre migliaia di componenti per i braccioli di vagoni ferroviari.
Le parti personalizzate sono sempre diverse, mentre gli apparecchi e la manodopera impiegati presso Productive Plastics sono sempre gli stessi. L'azienda deve ottimizzare e personalizzare ogni processo per adattarlo alle nuove geometrie e tipologie di parti. Per fare ciò, ha creato un ampio catalogo di supporti di produzione con la stampante 3D a sinterizzazione laser selettiva (SLS) Fuse 1.
Lo stabilimento di produzione di plastica di Productive Plastics
La termoformatura è un processo di produzione che sottopone a calore fogli di plastica e li modella in una forma desiderata. La formatura sottovuoto, la formatura a pressione e la formatura meccanica sono alcuni dei metodi più utilizzati tra i tanti disponibili. Productive Plastics gestisce sei celle produttive, che consentono lo svolgimento simultaneo di più progetti. Ogni cella comprende una termoformatrice industriale, una fresatrice CNC, un'area di assemblaggio e un sistema informatico per organizzare e monitorare le operazioni.
Le sei celle funzionano in modo continuo: non appena un ordine viene completato, viene avviato il successivo. Dustin Johnson, ingegnere che si occupa delle attrezzature, seleziona e progetta i supporti di produzione necessari per ogni ordine. Un progetto potrebbe richiedere una guida di foratura per aiutare il personale tecnico a unire con precisione due parti, mentre un altro potrebbe richiedere una parte di ricambio per un apparecchio rotto.
"La Fuse 1 è stata la nostra prima stampante 3D. Prima che la introducessimo nel nostro workflow, dovevamo lavorare il legno per le dime, esternalizzare la produzione di fissaggi personalizzati ad aziende di stampaggio a iniezione oppure fare a meno di un supporto di produzione e stimare il distanziamento", afferma Johnson.
Grazie alla Fuse 1 è stato possibile ridurre i costi, migliorare la produttività ed evitare interruzioni delle attività e ritardi. Johnson ha persino iniziato a progettare alternative per utilizzo finale da stampare in 3D e impiegare negli assemblaggi dei clienti. "Produrre in-house ci permette di controllare molto meglio le tempistiche, poiché è molto più facile stampare una parte che richiederla a clienti o fornitori esterni. E più attività possiamo svolgere in-house, più il sistema è conveniente", afferma Kyle Davidson, direttore commerciale e marketing di Productive Plastics.
Riduzione dei costi con dime e fissaggi in-house
Productive Plastics è specializzata nella termoformatura a livello industriale di componenti per utilizzo finale, per i quali impiega spesso fogli spessi di lega PVC/acrilico come Kydex. Sebbene il costo di un singolo foglio sia relativamente basso, la possibilità di ridurre gli sprechi allineando correttamente la dimensione di morsetti, parti e stampo consente loro, e ai loro clienti, di risparmiare migliaia di dollari.
Ad esempio, per un elemento per gli interni di una carrozza ferroviaria, i parametri dello stampo comportavano una distanza eccessiva dei morsetti dallo stampo stesso. Era necessario mantenere una distanza di ¼ di pollice (circa 6,4 mm) tra lo stampo e il telaio di fissaggio; ciò si poteva ottenere usando un fissaggio specifico oppure scegliendo un foglio di materiale più grande.
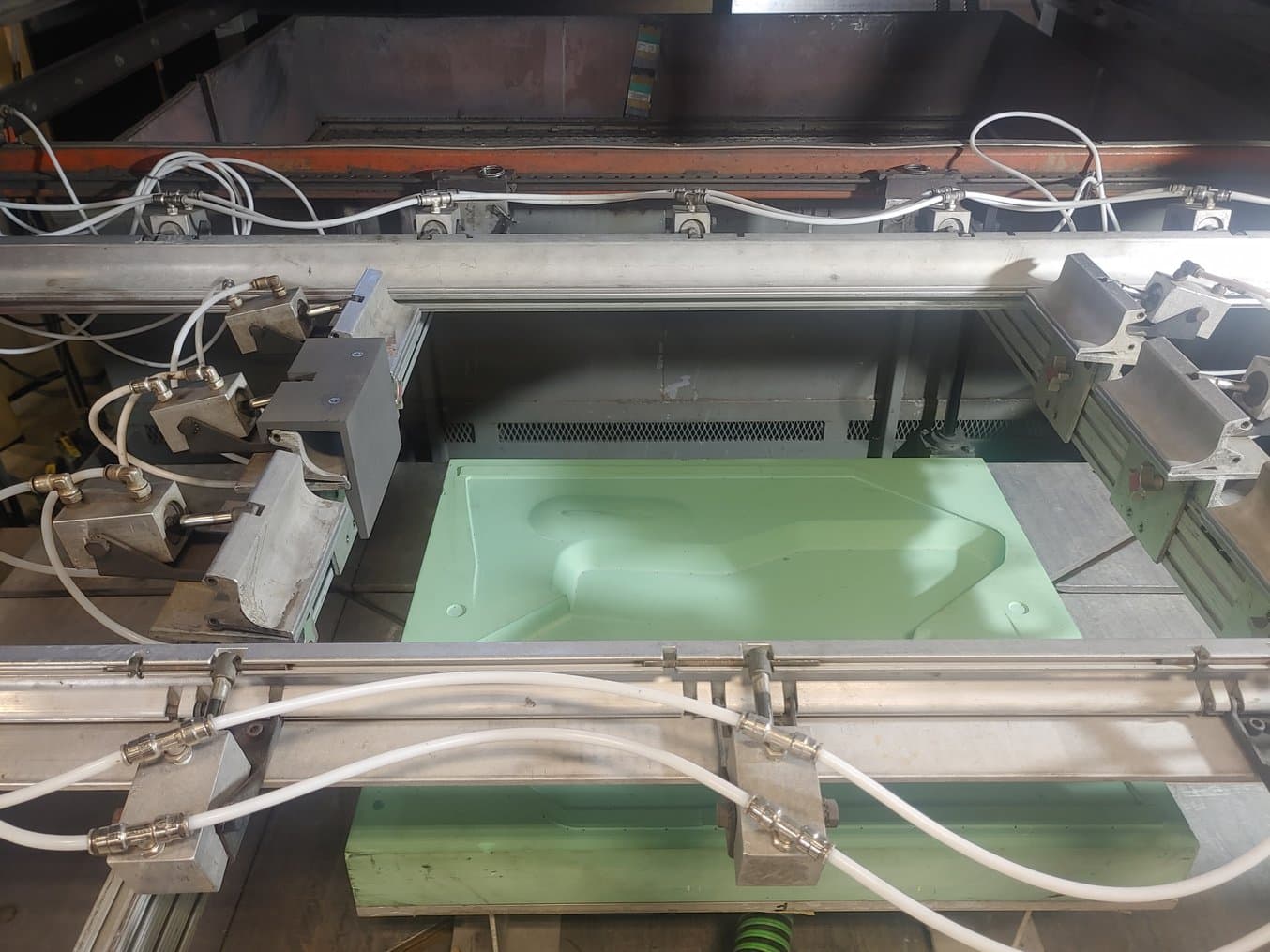
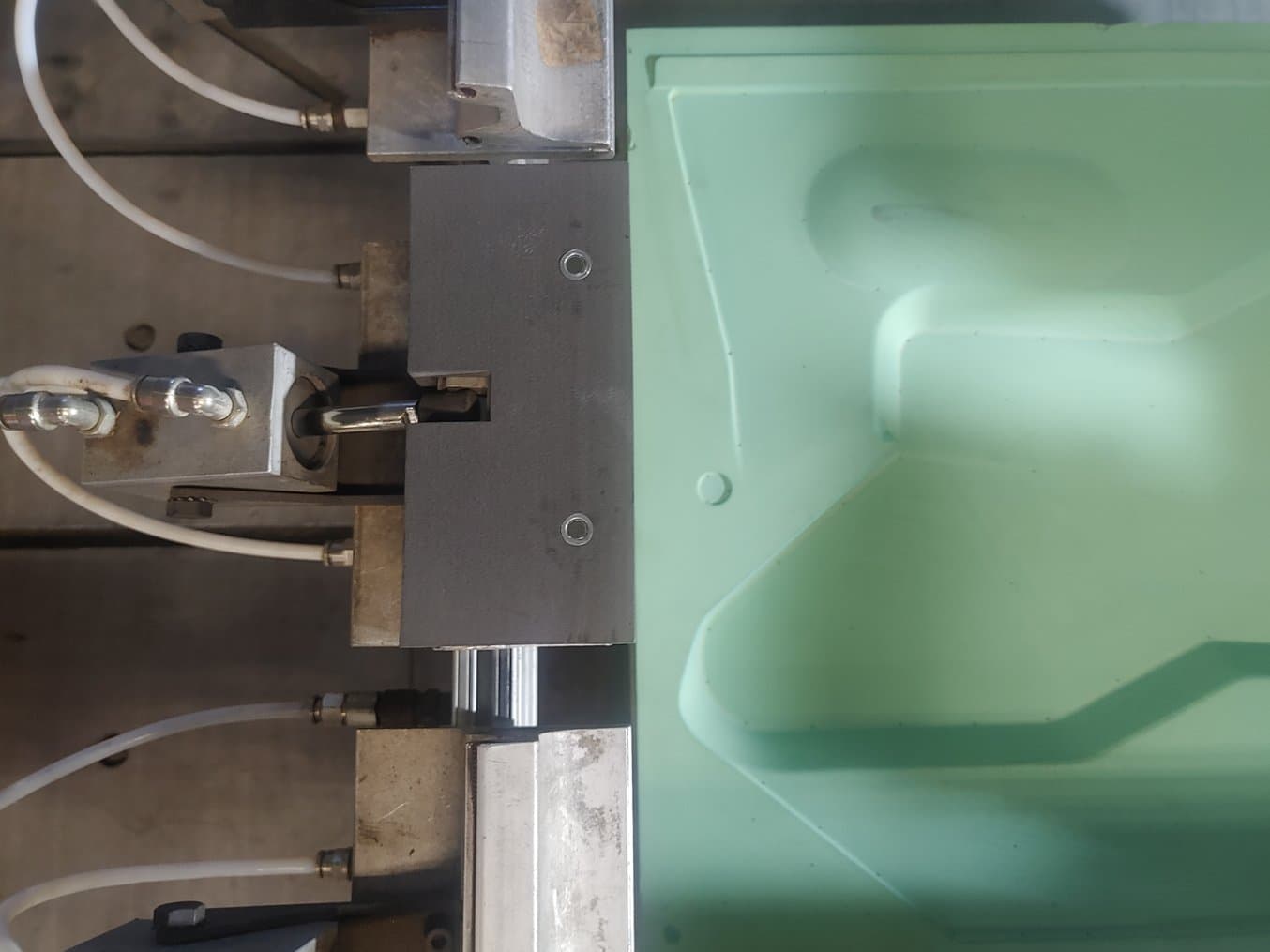
Il morsetto di fissaggio (parte di colore grigio chiaro) assicura il corretto distanziamento tra lo stampo (verde chiaro) e il telaio di fissaggio (struttura metallica).
Un foglio di dimensioni maggiori è anche più pesante, il che comporta un costo per parte più elevato e un incremento degli sprechi. Inoltre, esternalizzare la lavorazione meccanica di morsetti personalizzati ritarda di due/tre settimane il tempo di consegna. La stampa 3D in-house di morsetti di fissaggio ha consentito di usare fogli di dimensioni ottimali, risparmiare denaro e ridurre gli sprechi, evitando al contempo ritardi della produzione.
"Poter utilizzare fogli di dimensioni molto specifiche permette al cliente di risparmiare denaro. L'uso della stampa 3D consente di adattare le larghezze a morsetti personalizzati e di lavorare con margini altamente affidabili. In un solo giorno abbiamo iniziato a stampare e a produrre a pieno ritmo."
Kyle Davidson
Parti di ricambio per garantire l'operatività dello stabilimento
Quando si hanno tanti clienti diversi e numerose scadenze da rispettare, la produzione non si ferma per nessun motivo. Sempre ammesso che l'apparecchio per la formatura sottovuoto non si guasti. Quando il girante della pompa si è rotto, il team prevedeva dalle sei alle otto settimane per la consegna della parte di ricambio. "Un'azienda non può dire di occuparsi di termoformatura se non ha una pompa sottovuoto. Non potevamo permetterci di fermare un'intera cella per sei settimane, quindi era necessaria una soluzione provvisoria", afferma Davidson.
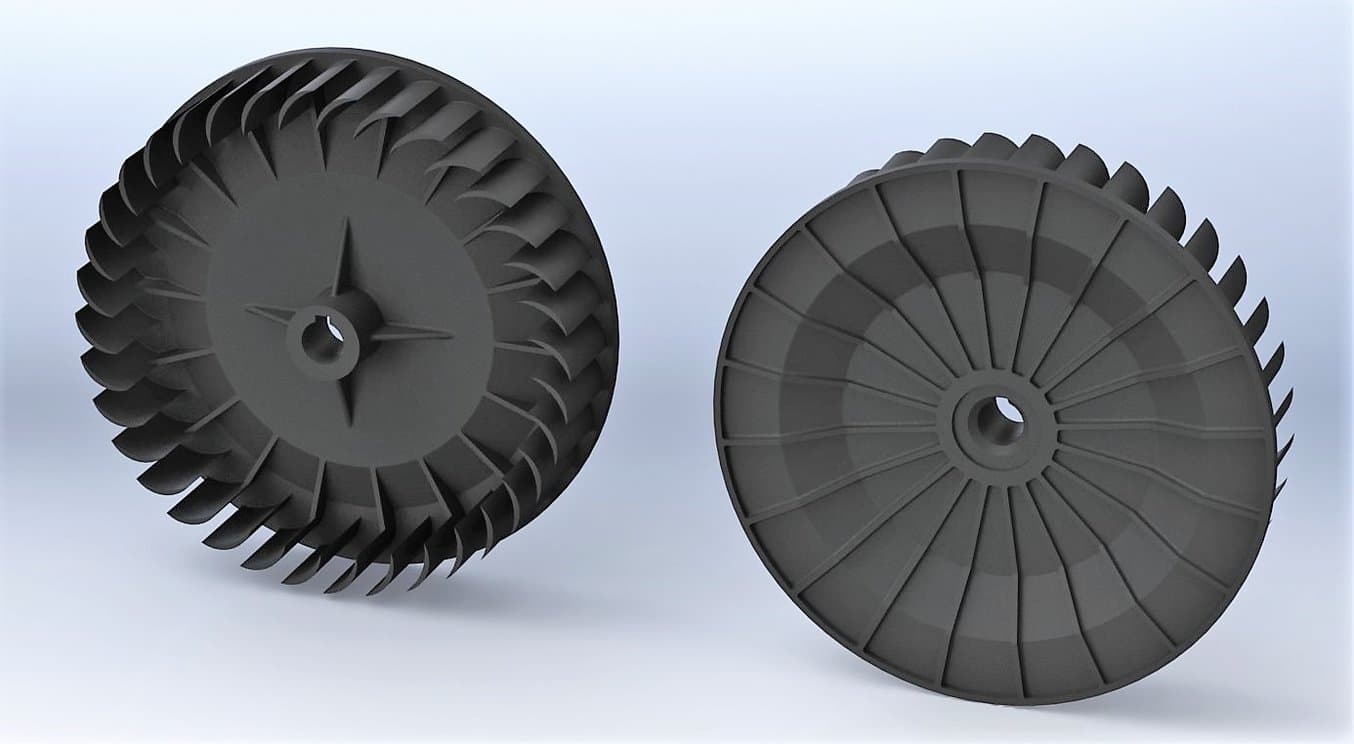
Il file 3D del girante su SolidWorks. Entrambi i lati hanno aree negative e positive e un foro centrale. Ciò non permette di ricorrere a tecnologie che usano strutture di supporto, ad esempio la FDM e la SLA.
Il team ha progettato con SolidWorks due iterazioni sostitutive per il girante, poi le ha stampate durante la notte con la Fuse 1 utilizzando la Nylon 12 Powder. Il girante ha funzionato subito, inserendosi alla perfezione nella pompa sottovuoto e consentendo alla cella di riprendere a lavorare. La natura autoportante della stampa 3D SLS ha permesso di realizzare un design a due lati con un foro centrale. Senza supporti da rimuovere o processi di post-elaborazione, il girante era immediatamente pronto per essere inserito nell'apparecchio originale.
"Attendere una parte di ricambio avrebbe fermato un'intera cella per settimane, causando perdite per circa 30 000 $. È bastata questa singola parte di ricambio provvisoria ad ammortizzare il costo della stampante."
Kyle Davidson
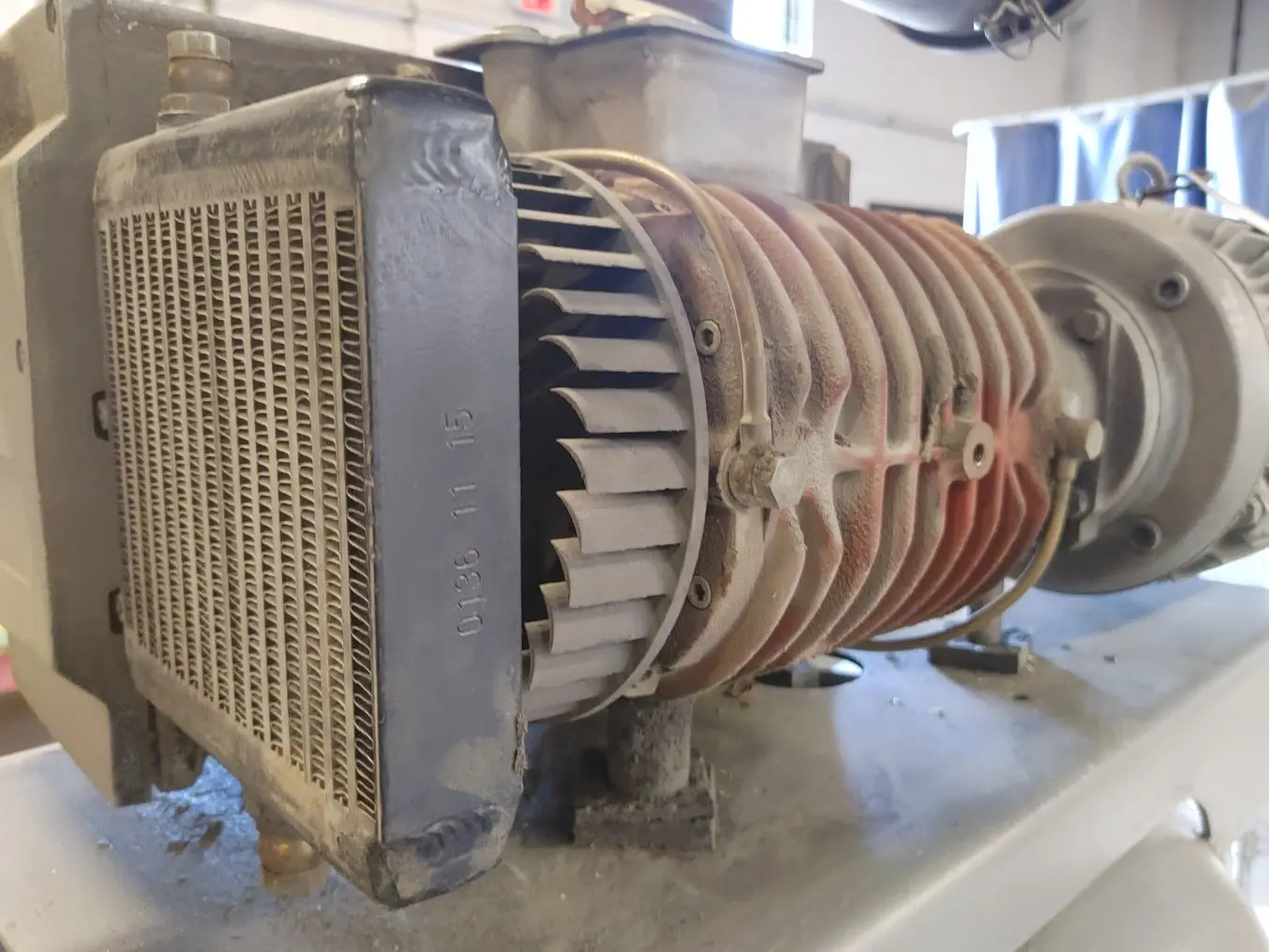
Un primo piano (a destra) e un'immagine ingrandita (a sinistra) del girante stampato in 3D, inserito perfettamente nella pompa sottovuoto della termoformatrice industriale.
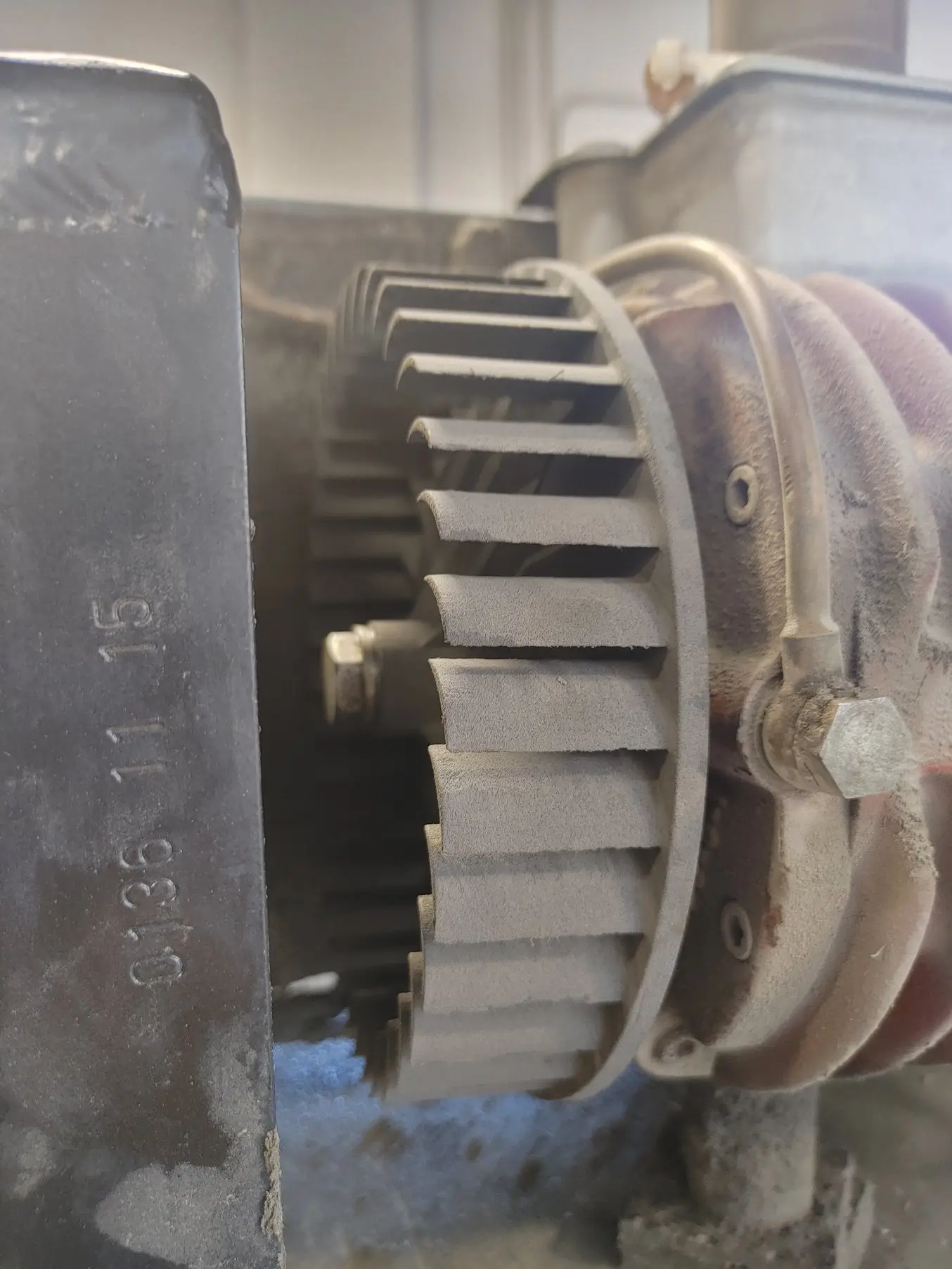
Ogni secondo fa la differenza
Una volta formate, le parti sono spesso soggette a processi secondari, come assemblaggio o finitura. Tali processi secondari richiedono strumenti e manipolazioni speciali, come l'applicazione a mano di un nastro adesivo per la verniciatura. Per questa parte, il personale tecnico applicava del nastro adesivo su una superficie rivestita di rame critica, per poi applicare a mano lo stencil nel punto in cui il rame terminava, in modo che la vernice coprisse il resto della parte. Il taglio veniva eseguito a occhio, per cui erano frequenti errori, graffi sul rame o secondi tentativi. Grazie a una o due guide per stencil stampate in 3D, gli operatori possono eseguire il taglio in modo rapido ed efficiente.
"Anche se si risparmiano solo dieci o 15 secondi per ogni parte, ciò si traduce in un notevole risparmio sui costi per l'intero ciclo di vita del prodotto", afferma Johnson. "Prima la parte era intagliata a mano nel legno, un'operazione laboriosa e dispendiosa in termini di tempo. La parte stampata in 3D costa un paio di dollari ed è facile da applicare con una sola mano".
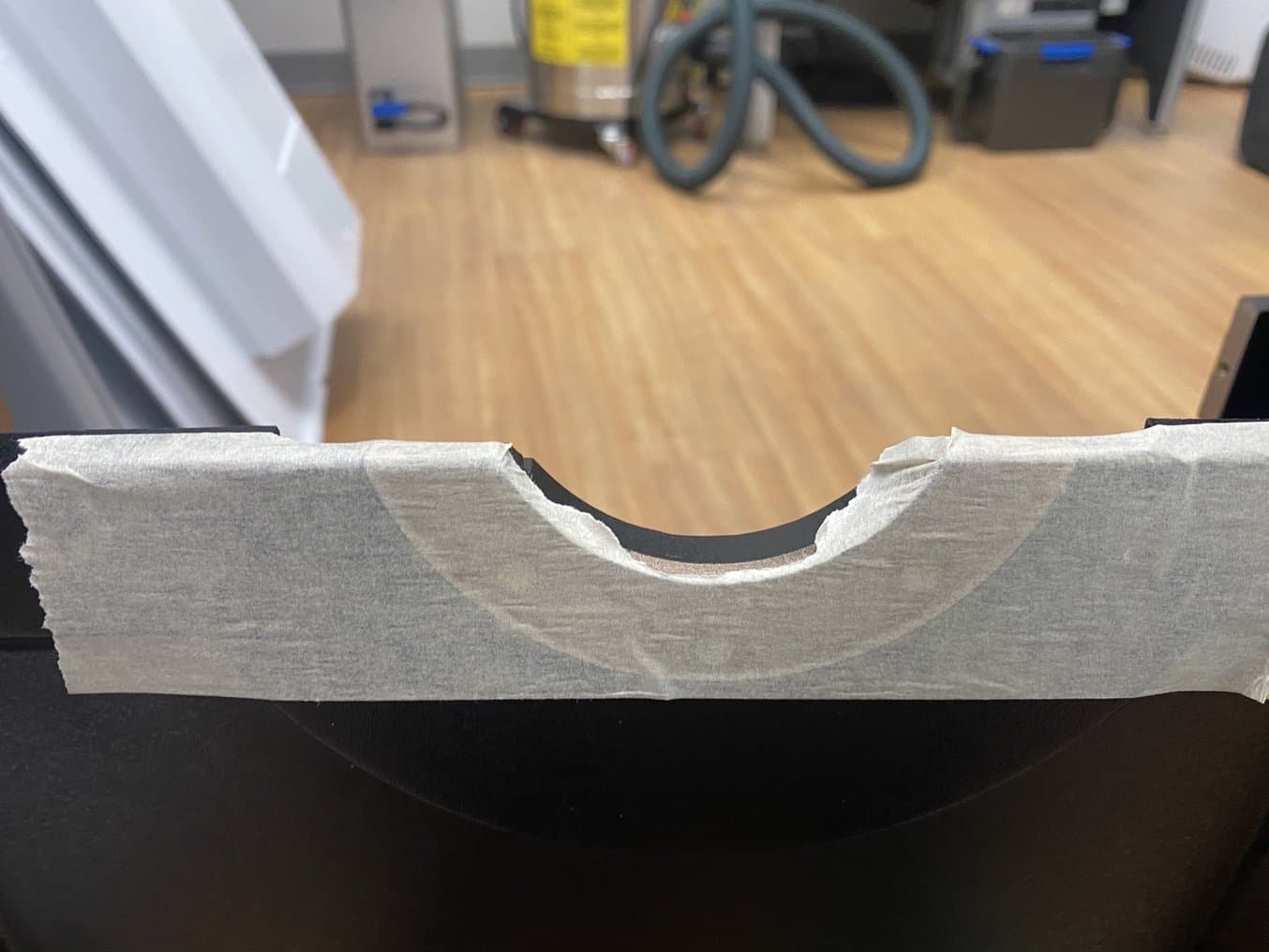
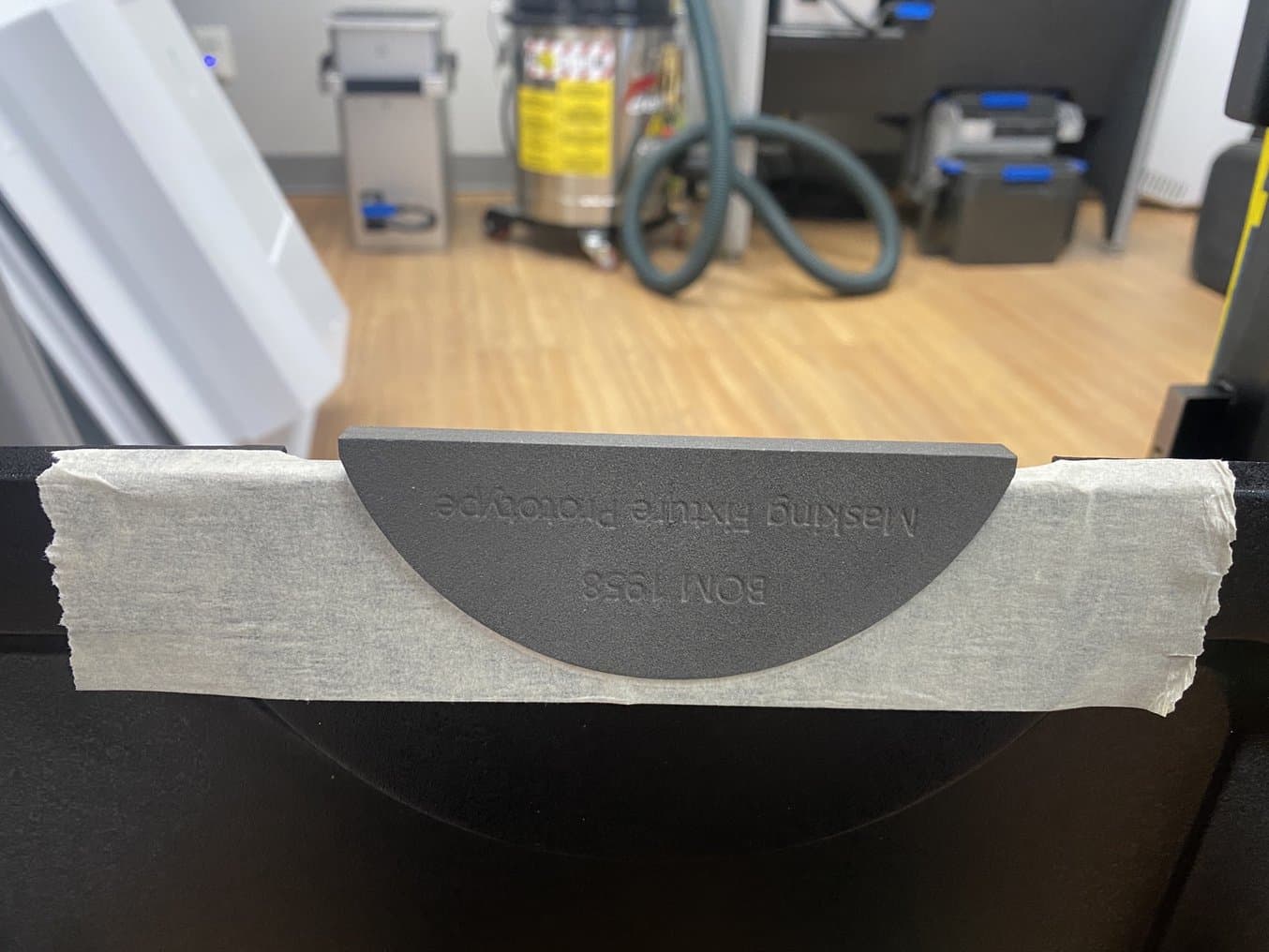
Nel primo passaggio, il nastro adesivo ricopre un'ampia sezione della parte. Nel secondo, la parte stampata in 3D funge da stencil. Il personale tecnico taglierà via il resto del nastro attorno alla parte, assicurando che la porzione rivestita di rame non venga verniciata di nero come il resto della superficie.
Migliore comunicazione con i clienti per evitare sorprese
Durante il processo di design, Productive Plastics collabora con i propri clienti per sviluppare la parte, il processo di termoformatura e il tipo di blocchi che vengono affissi alle parti in un assemblaggio secondario. Questi blocchi, necessari per l'integrità strutturale o per gli attacchi di un assemblaggio funzionale, devono inserirsi perfettamente nel foglio termoformato. Dal momento che vengono prodotti nell'ordine delle centinaia o delle migliaia di unità, un piccolo errore può avere grandi conseguenze in termini di costi.
In precedenza, il team disegnava uno schizzo del blocco con le dimensioni e le tolleranze necessarie; tuttavia, poiché è complicato rappresentare in modo chiaro le superfici angolate in un disegno bidimensionale, spesso i blocchi venivano prodotti con la sagoma o le dimensioni sbagliate. Tali errori venivano alla luce appena prima di un ciclo di termoformatura, e ciò portava al blocco totale dell'intero progetto. Poter produrre in-house con la Fuse 1 consente a ogni cliente di creare set di blocchi che si adattano perfettamente.
"Dato che ne produciamo migliaia e migliaia, se anche un solo blocco ha un diametro leggermente sbagliato, ciò si traduce in uno spreco enorme e nell'impossibilità di finire il progetto. Poter inviare ai clienti un prodotto fisico ci costa solo pochi dollari ed evita di produrre migliaia di parti in modo errato", afferma Johnson.
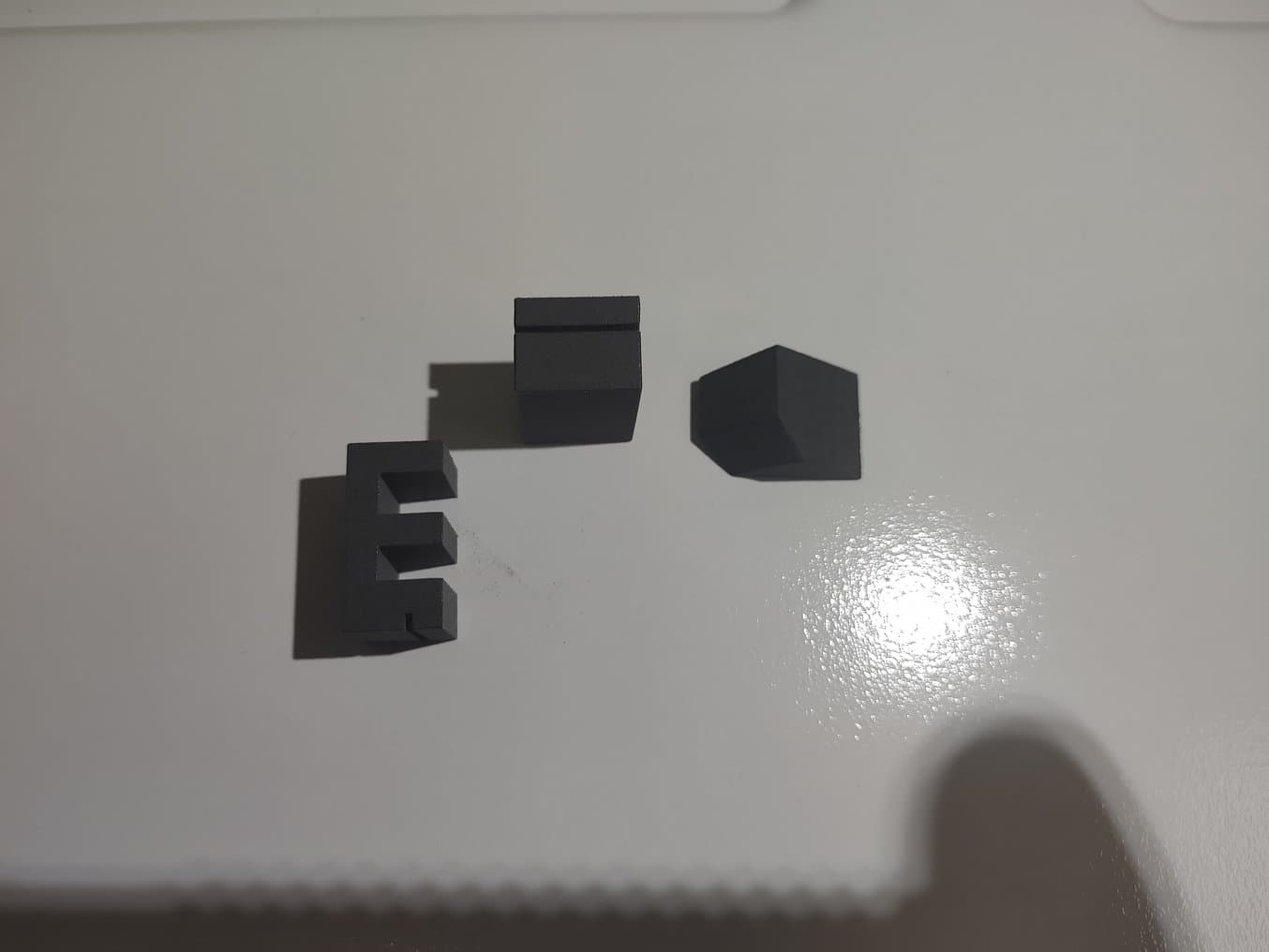
I blocchi personalizzati stampati in 3D sono usati nella fase di assemblaggio, dove una parte termoformata viene assemblata in modo funzionale. Un singolo blocco non realizzato correttamente può comportare un'interruzione improvvisa dell'intero calendario di produzione.
Migliore efficienza di ogni cella
Volume degli ordini, variazioni delle parti e numero di fasi nel processo: presso Productive Plastics c'è sempre qualcosa a cui pensare. Qualsiasi soluzione che renda più fluido il processo di comunicazione tra dipartimenti ha un enorme impatto sull'efficienza del team.
Ciascuna cella produttiva è dotata di un sistema di monitoraggio computerizzato che tiene traccia di ordini, manuali degli apparecchi, catalogo di supporti di produzione e parti. Sebbene il team stesse cercando di passare dai computer ai tablet, non c'era un modo semplice per rendere questo tipo di dispositivo facilmente accessibile e allo stesso tempo portatile. Le resistenti custodie di tipo industriale non si adattavano a nessun attacco standard, per cui spesso venivano lasciate su uno scaffale o su una postazione di lavoro già occupata. Johnson ha smontato un comune supporto per telefono e ha applicato l'ingegneria inversa, progettando una soluzione più grande in grado di agganciarsi alla custodia di tipo industriale del tablet e di fissarsi saldamente a un pannello di legno.
"In questo modo avevamo a disposizione una soluzione portatile, che allo stesso tempo era accessibile ai nostri operatori nel modo più semplice possibile. Non riuscivamo a trovare nulla a meno di 300 $, allora le ho stampate con la Fuse 1 per 30 $ e le abbiamo montate in ogni cella, più un paio extra", dice Johnson.
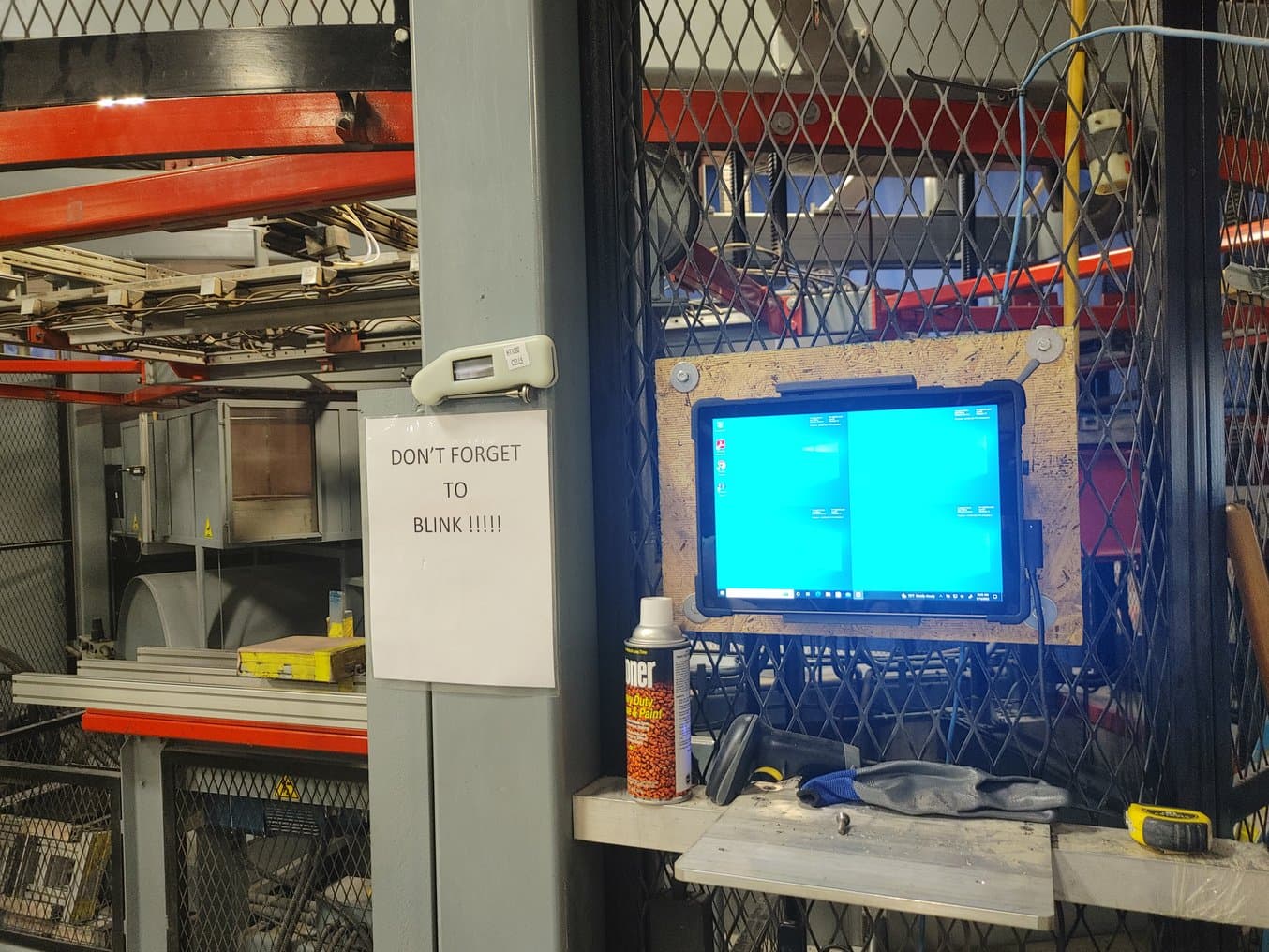
Il supporto per tablet progettato su misura è in grado di agganciarsi al tablet per poterlo utilizzare facilmente sulla parete, ma è anche abbastanza flessibile da consentire all'utente di staccare il tablet dal supporto e portarlo con sé mentre si sposta all'interno della cella.
Massima velocità di produzione
Una volta terminato il processo di termoformatura iniziale, gli operatori eseguono i processi secondari necessari, ad esempio fissaggio dei blocchi alla parte per l'assemblaggio, rifilatura della parte o qualsiasi altra operazione per preparare la consegna al cliente. Productive Plastics si impegna a offrire una tolleranza di 0,003 pollici (0,76 mm) tra blocchi e parte realizzata tramite stampaggio, pertanto era necessario effettuare una misurazione per assicurarsi che ogni blocco fosse perfettamente attaccato.
In passato, il team faceva a meno delle guide e prendeva le misure a occhio oppure utilizzava blocchi di legno incollati tra loro e poi sottoposti a lavorazione meccanica per ottenere le dimensioni giuste. Entrambi i metodi erano laboriosi, rallentavano il processo e generavano errori che dovevano essere corretti. Johnson è riuscito a progettare una dima di posizionamento che indica con precisione il punto in cui fissare i blocchi sul pezzo termoformato, consentendo così al personale di fissarli correttamente in pochi secondi.
"L'uso contemporaneo di più set di dime consente la massima velocità di produzione, e ci ha aiutato a migliorare la precisione di posizionamento dei blocchi e a risparmiare il tempo che prima dedicavamo alla levigatura o alla lavorazione meccanica dei blocchi", afferma Davidson.
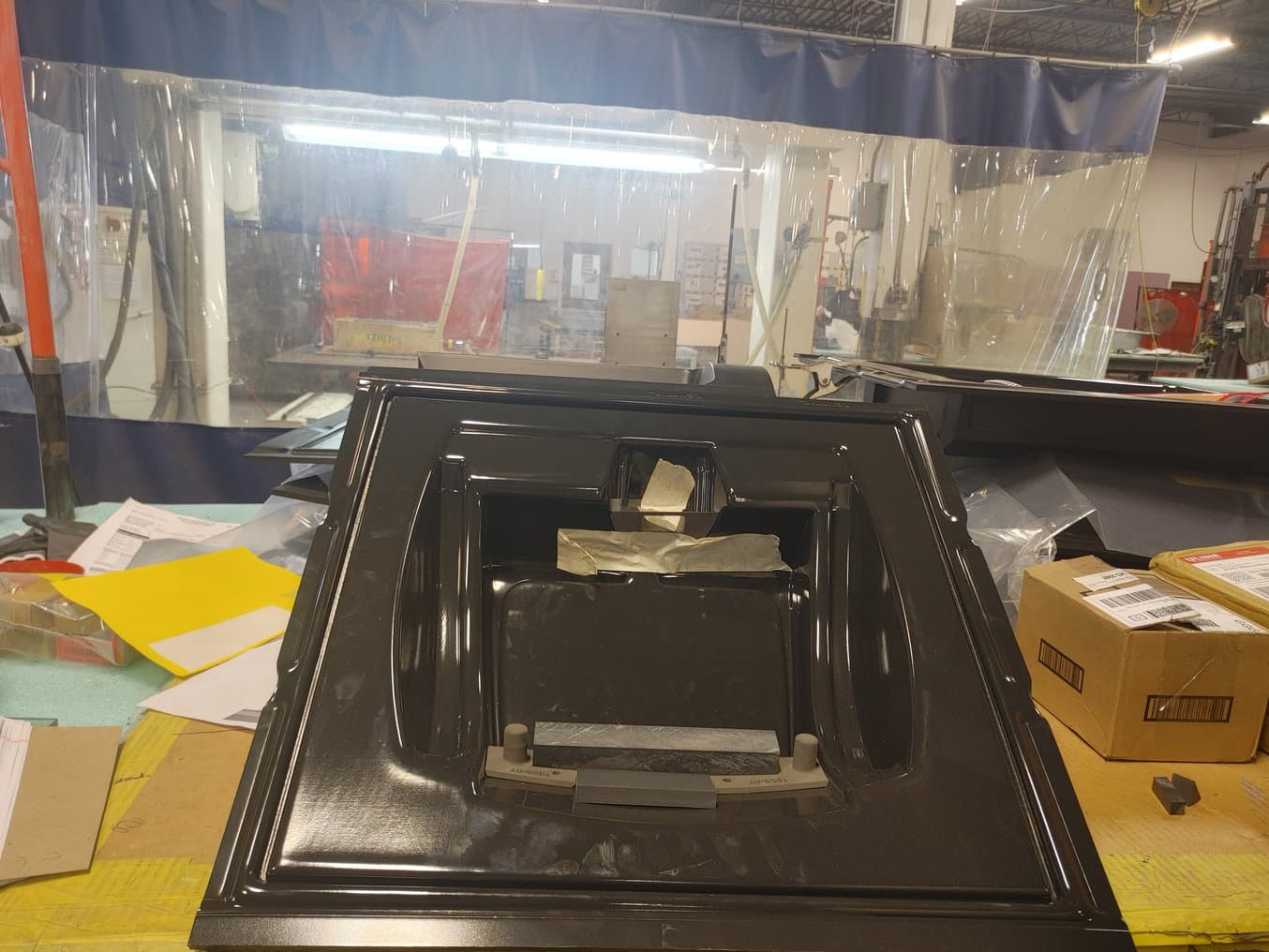
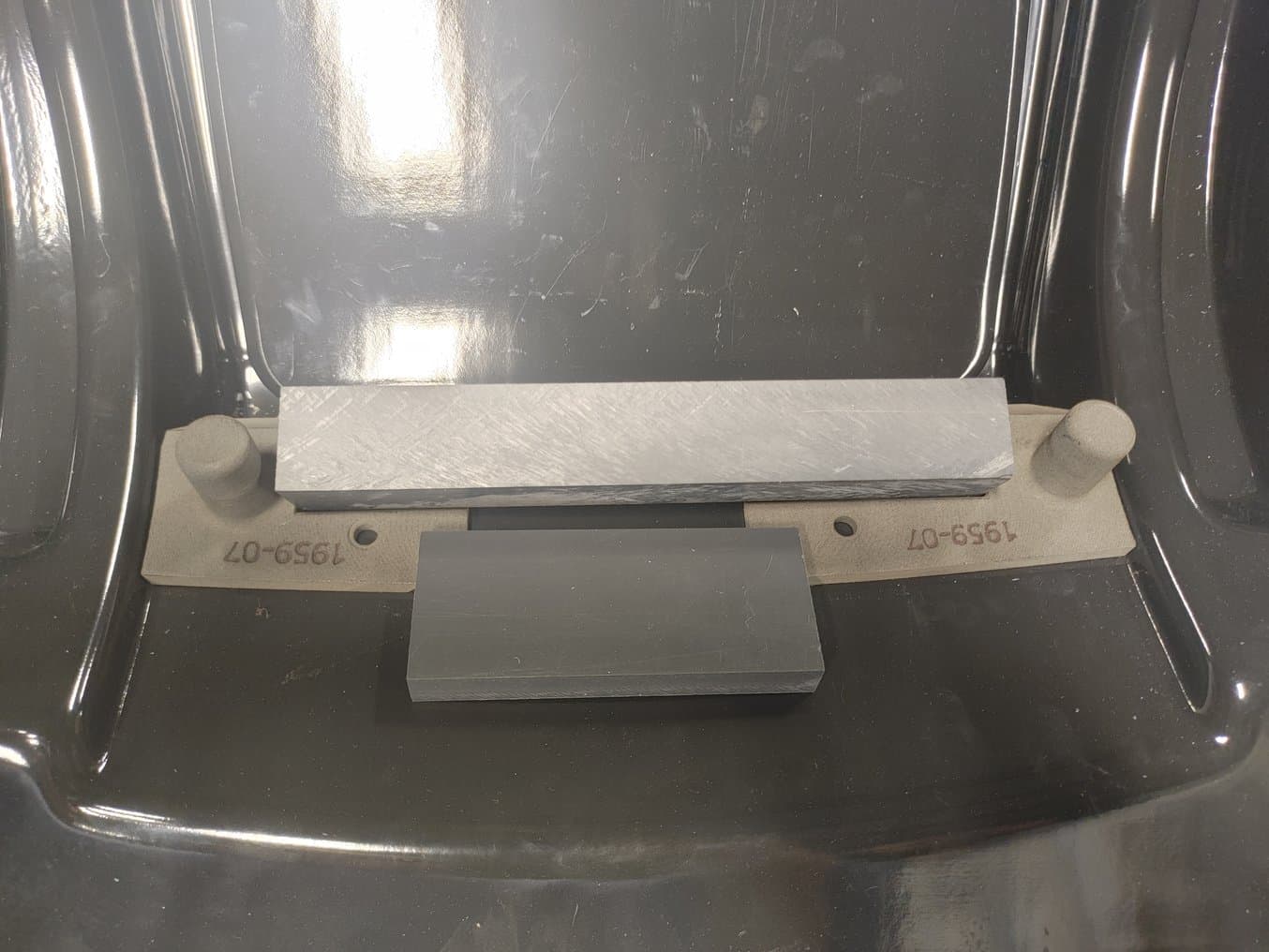
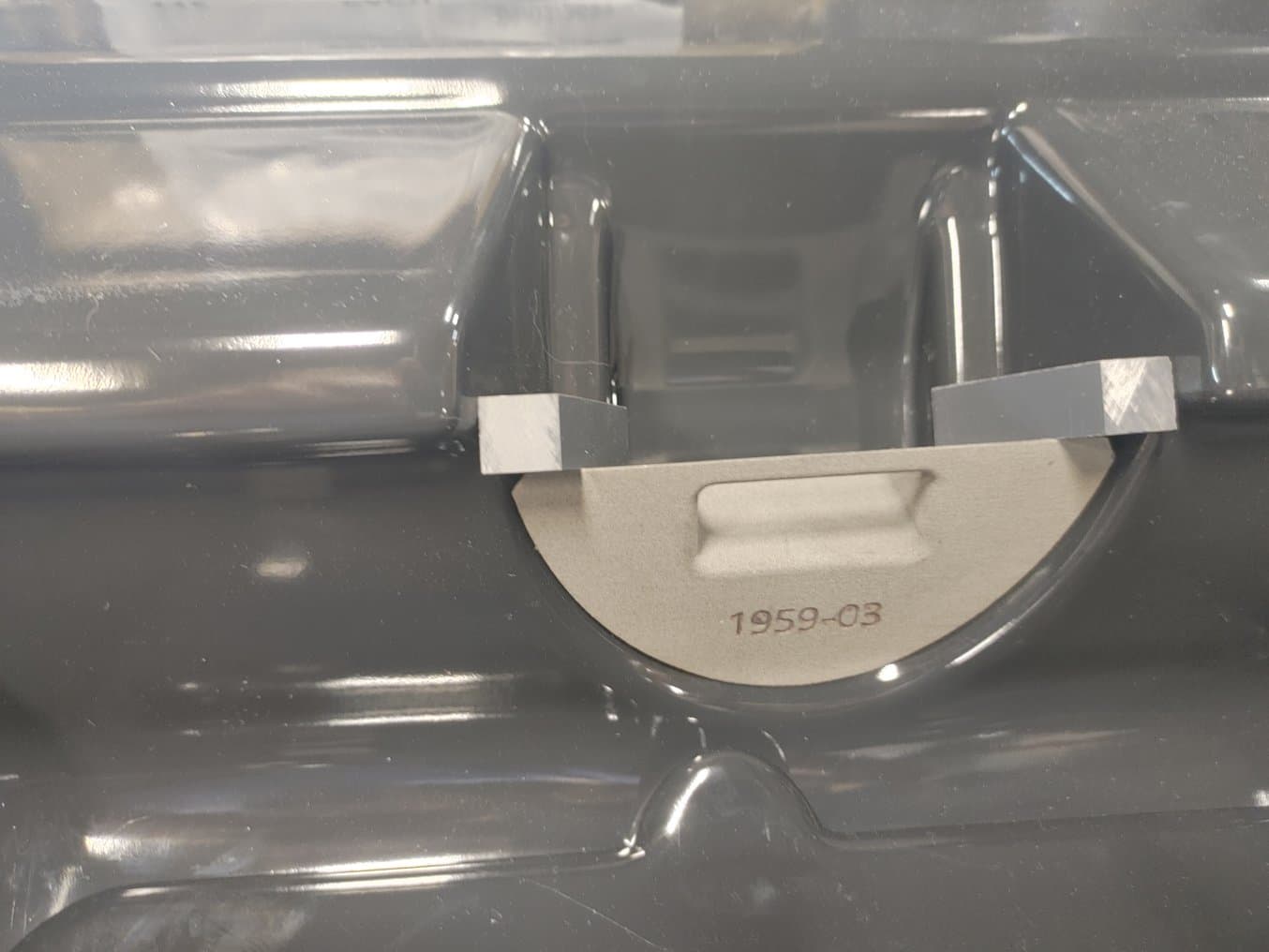
Lo scudo protettivo del dispositivo medico (parte di colore nero ottenuta tramite stampaggio, foto di sinistra) richiede l'attacco di due blocchi (barra color argento lunga e barra color grigio scuro più corta). Le due dime di posizionamento (le parti di colore grigio chiaro con manopole a destra e sinistra) mostrano all'operatore dove fissarle esattamente, consentendo un risparmio di tempo e un corretto posizionamento.
Alternative per utilizzo finale con la Nylon 12 Powder
L'anno scorso Productive Plastics ha sperimentato difficoltà nel reperire un particolare componente a causa dei ritardi nella catena di fornitura. Per questo motivo, Johnson ha deciso di provare a stampare in 3D uno dei componenti di piccole dimensioni che solitamente ricevono da aziende che si occupano di stampaggio a iniezione. Il componente può essere inserito in un apparecchio usato presso le strutture di assistenza sanitaria per coprire le aperture non in uso, come i collegamenti al circuito endovenoso o altri sistemi di erogazione di fluidi. Grazie all'uso della Nylon 12 Powder sulla Fuse 1, Johnson è stato in grado di ricreare perfettamente il componente stampato a iniezione. Sebbene fosse necessaria una specifica approvazione normativa per l'uso in una struttura medica, il team lo ha proposto con successo al cliente come alternativa possibile qualora si verificassero problemi nella catena di fornitura.
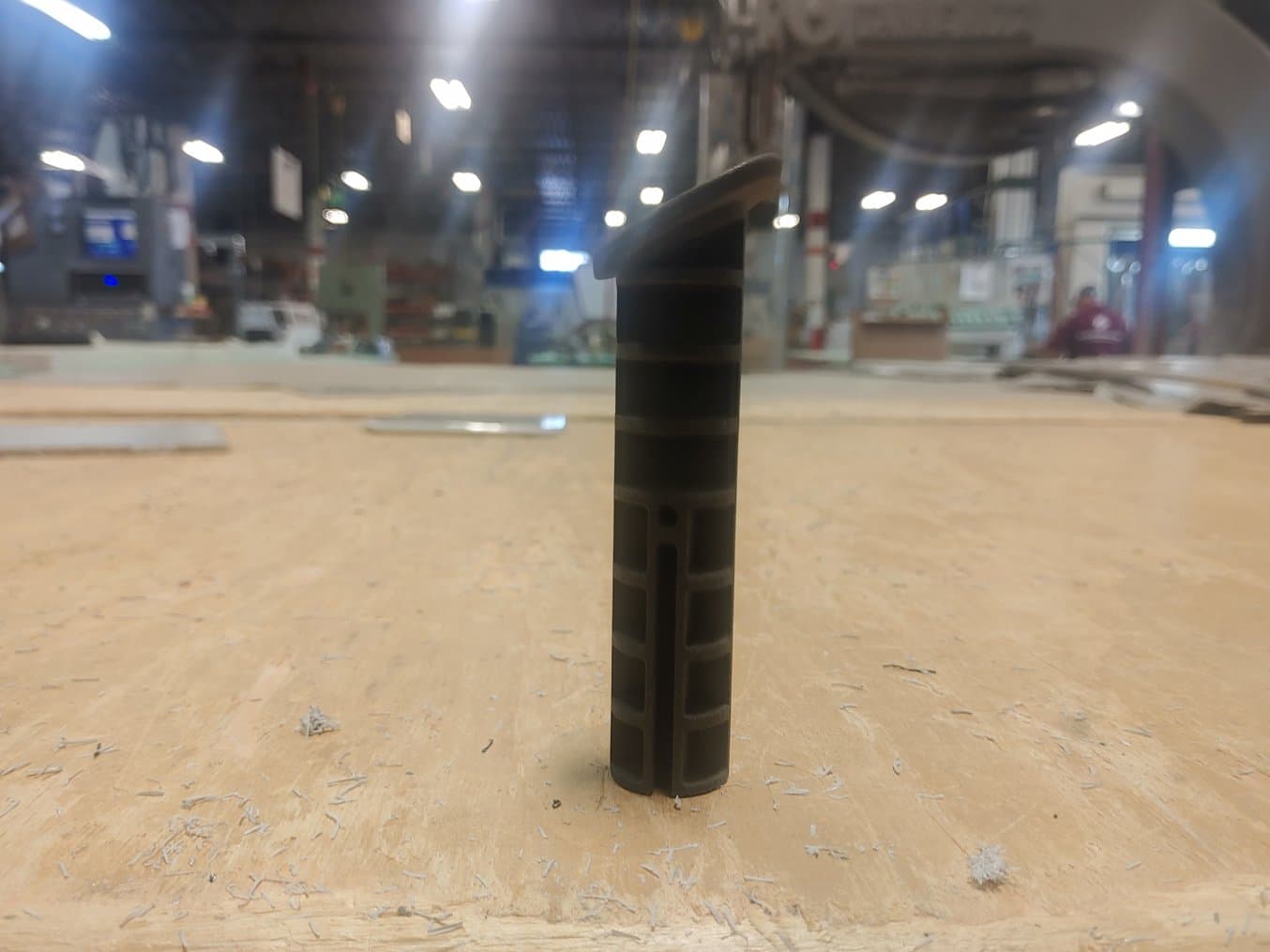
Il tappo stampato sulla Fuse 1 con la Nylon 12 Powder rappresenta un'alternativa prodotta in-house allo stesso componente stampato a iniezione.
Creazione di un catalogo digitale di supporti per il futuro
Quando gli ordini dei clienti vengono realizzati mediante stampaggio nell'ordine delle centinaia e delle migliaia di unità, anche i più piccoli dettagli fanno la differenza. Se il team di assemblaggio può risparmiare 10 secondi per parte usando una dima di posizionamento per attaccare i blocchi, o se un apparecchio può rimanere operativo con una parte di ricambio stampata in 3D, l'intera attività aziendale viene resa più efficiente e costante. L'uso della Fuse 1 e della Nylon 12 Powder consentono a Johnson non solo di superare eventuali difficoltà, ma anche di migliorare preventivamente i processi prima che causino problemi di produzione veri e propri. I vantaggi si riflettono anche sui clienti: la stampa 3D contribuisce a tenere basso il costo per parte ed elevata la soddisfazione complessiva.
"Adesso, quando i dipendenti dello stabilimento mi dicono di aver rotto una parte o mi chiedono se è possibile semplificare una procedura, mi basta stampare una parte per risolvere il problema. La quantità di tempo risparmiata è impressionante", afferma Johnson. Il team ha potuto aumentare la produttività complessiva concentrandosi preventivamente sulle aree dello stabilimento in cui ostacoli o riparazioni possono rallentare il funzionamento. La Fuse 1, la loro prima stampante 3D, ha aperto nuovi orizzonti di produzione.