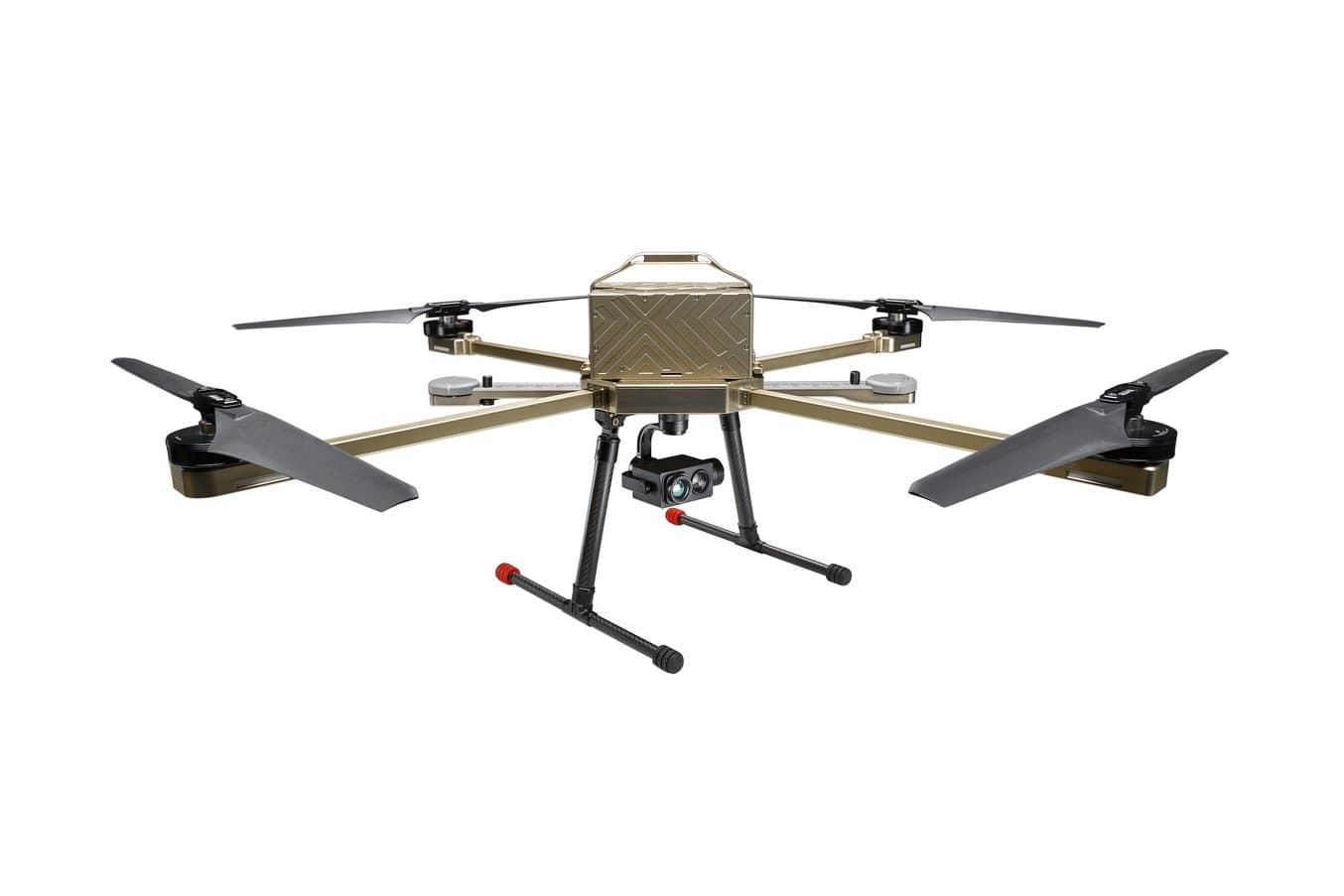
Disastri naturali, invasioni militari, navi che affondano, aerei che si schiantano: questo tipo di immagini cattura facilmente l'attenzione delle persone. Si tratta di fotografie che vengono spesso scattate con strumenti relativamente recenti, chiamati droni o veicoli aerei senza pilota (UAV). Con l'avanzare di questa tecnologia, le aziende produttrici continuano a superare i limiti di distanza, velocità e peso che questi apparecchi possono raggiungere.
Nextech, azienda sudafricana produttrice di droni, utilizza le stampanti 3D a sinterizzazione laser selettiva (SLS) di Formlabs per creare UAV personalizzati ad alte prestazioni per clienti nei settori più disparati. Le caratteristiche delle parti SLS, robuste e pronte per l'utilizzo finale, consentono a Nextech di progettare, prototipare e produrre pezzi con un unico workflow semplificato.
Liam Kroone, tecnico di progettazione meccanica, ci ha parlato dei punti di forza del loro workflow ibrido, spiegandoci come la stampa 3D SLS in-house ha aiutato l'azienda a ritagliarsi un posto in questo settore estremamente competitivo. "Il workflow di stampa 3D ci permette di soddisfare i requisiti specifici della nostra clientela, sviluppare nuovi prodotti e migliorare i design molto più rapidamente", ci racconta Kroone.
In questo articolo, scoprirai come Nextech utilizza la stampa 3D SLS per:
-
Risparmiare milioni di dollari sulla lavorazione meccanica CNC grazie a una sola stampante Fuse 1+ 30W.
-
Creare estremità alari di droni in fibra di carbonio con stampi realizzati in 3D.
-
Unire lavorazione meccanica, fibra di carbonio e stampa 3D SLS per ottenere peso e stabilità ottimali.
Difficoltà tipiche della produzione di droni
I veicoli aerei senza pilota vengono impiegati da decenni, principalmente nelle missioni tattiche e di sorveglianza da parte di organizzazioni militari. In settori come agricoltura, gestione della fauna selvatica o climatologia, l'utilizzo diffuso di questi apparecchi è stato limitato dai costi elevati. Ogni cliente richiede per i propri droni caratteristiche specifiche: resistenza a particolari temperature ambientali e condizioni climatiche, tipologia di telecamera o altro carico utile, distanza tra il punto di alimentazione e carico utile e molto altro. I componenti della maggior parte dei modelli di drone sfruttano parti prodotte in massa, ma i diversi requisiti impongono inevitabilmente un certo livello di personalizzazione.
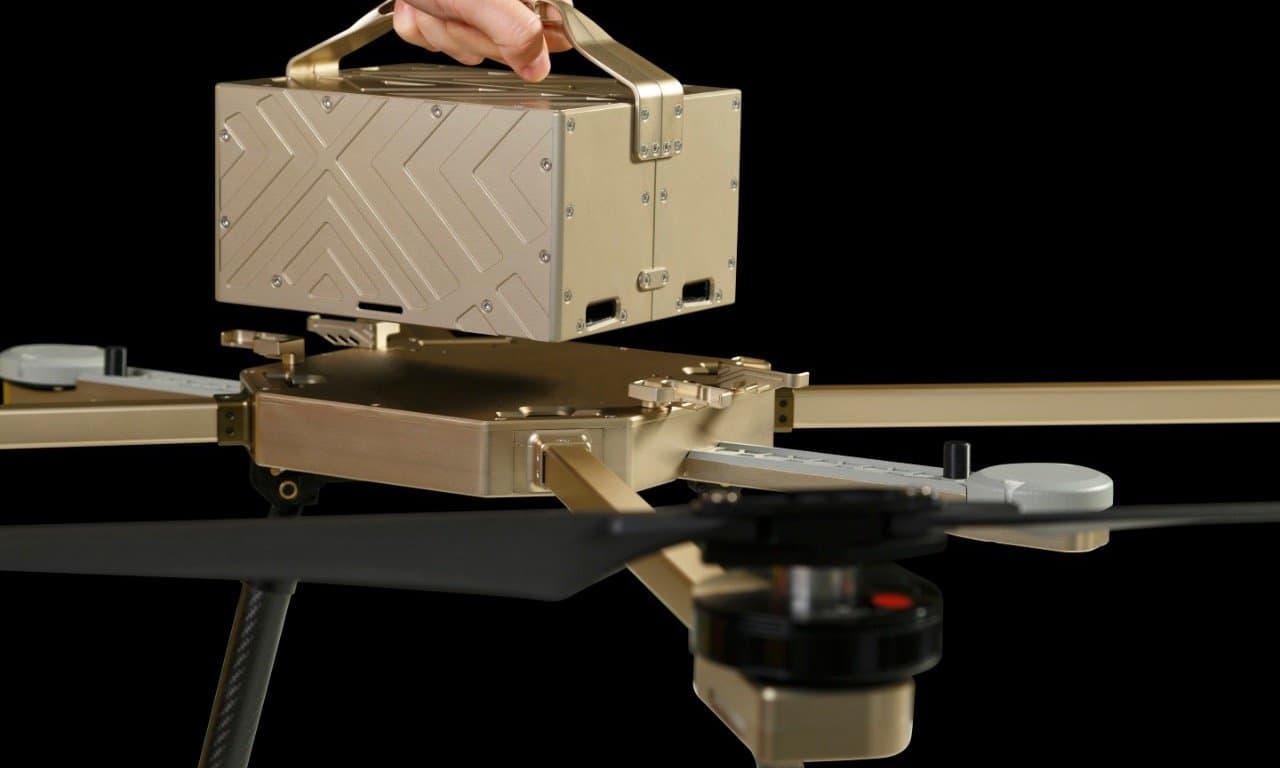
Spesso la parte più pesante di un drone è l'alloggiamento della batteria; per questo motivo, Nextech utilizza la stampa 3D per ottimizzare il peso di altri componenti, in modo che i droni possano raggiungere mete più lontane senza rinunciare alla stabilità o al carico utile.
Personalizzare le parti con le tecniche di produzione tradizionali è difficile: creazione di stampi, lavorazione meccanica, taglio laser o a getto d'acqua sono metodi costosi, in particolare per le complesse geometrie richieste in questo ambito. La stampa 3D ha permesso alle aziende produttrici di droni di creare forme complesse e prodotti personalizzati a prezzi accessibili, ma la difficoltà di trovare la tecnologia e i materiali giusti ne ha limitato l'adozione. Il workflow SLS della Fuse 1+ 30W consente a Nextech di prototipare rapidamente, aumentare la capacità di iterazione sulla base dei feedback della clientela e produrre lotti di componenti personalizzati a prezzi accessibili.
Adozione della stereolitografia in-house
Prima di portare la stampante SLS Fuse 1+ 30W in-house, Nextech esternalizzava la stampa 3D o la lavorazione meccanica dei componenti durante la fase di prototipazione. "L'università locale stampava per noi in 3D lotti di piccoli componenti con grandi apparecchi EOS industriali, ma ci volevano settimane per riceverli", racconta Kroone.
L'adozione della stampante in-house ha velocizzato le tempistiche di sviluppo, consentendo al team di collaborare in modo più stretto con la clientela. "Ogni progetto è unico e occorre prototipare rapidamente parti complesse e ricche di dettagli, con una finitura di alta qualità", afferma Kroone, che aggiunge: "Bisogna ad esempio inserire staffe e poi testare stabilità, peso e sensazione tattile, o ancora incorporare una guarnizione per aumentare l'isolamento e quindi testare l'aderenza e la facilità di utilizzo per assicurarsi che il prodotto finale sia di alta qualità".
Eseguire iterazioni frequenti era impossibile con l'esternalizzazione. L'attesa di giorni o settimane riduceva il tempo disponibile e limitava la quantità di test funzionali. "Avere una stampante in-house ti permette di dare una spinta al volume di produzione e ottimizzare l'utilizzo dei materiali. Possiamo creare parti in plastica senza realizzare stampi a iniezione, che sono molto dispendiosi in termini di tempi e costi", afferma Kroone.
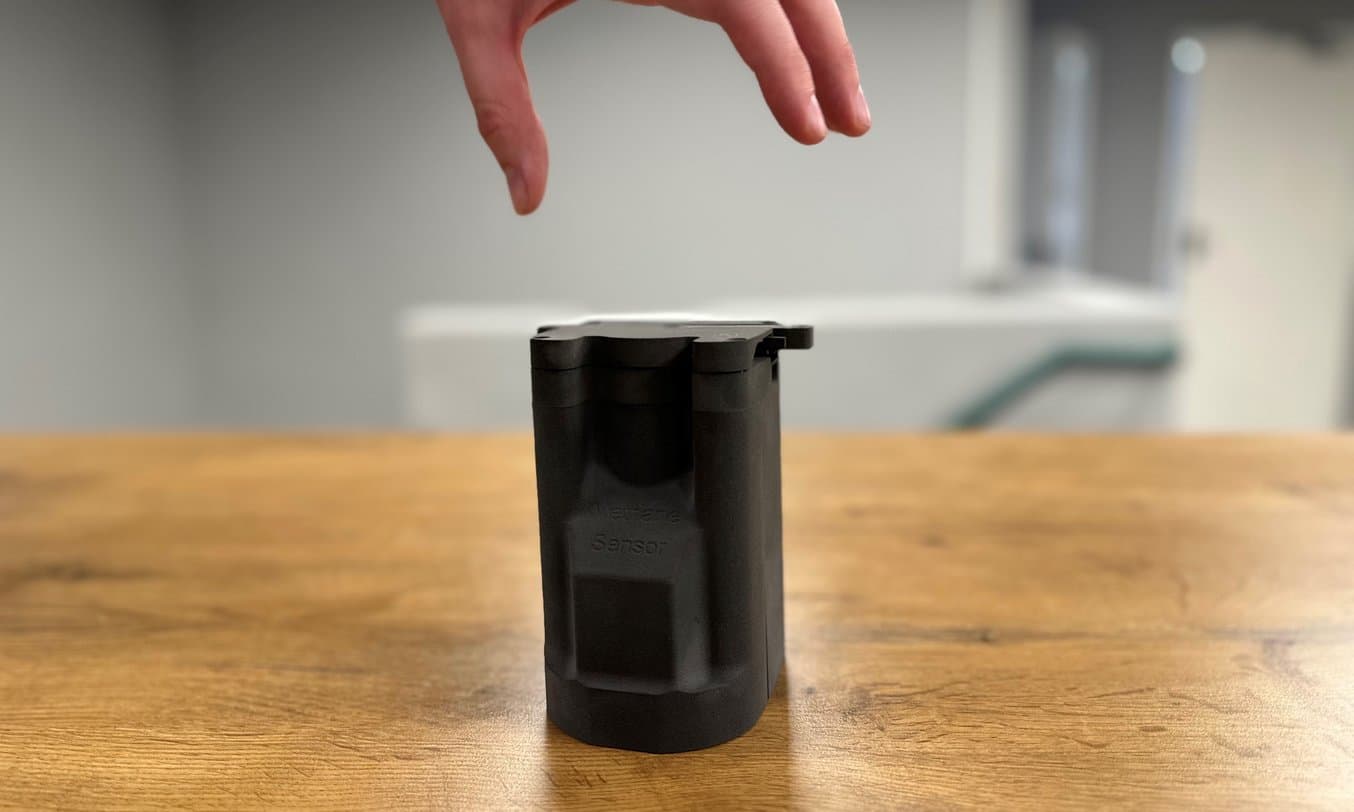
Un sensore di metano su misura realizzato con la stampante 3D SLS Fuse 1+ 30W in Nylon 12 Powder. La stampa in-house ha permesso di ridurre i costi di progettazione e produzione.
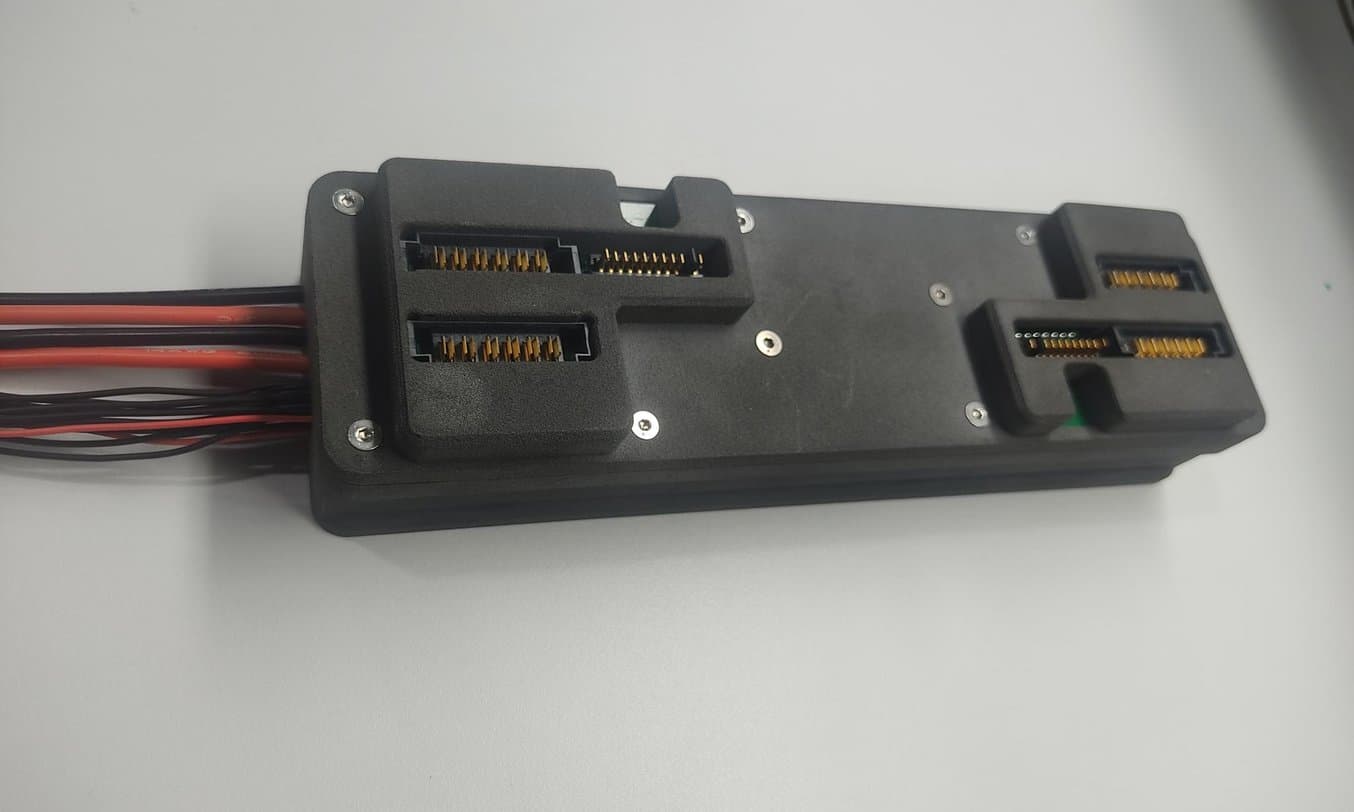
Anche questo caricabatterie personalizzato è stato stampato in Nylon 12 Powder con la Fuse 1+ 30W. Grazie alla produzione in-house, Nextech è diventata più agile e può rispondere più facilmente alle richieste di progetti della clientela.
Parti complesse con tecnologie complementari
Ogni cliente necessita di carichi utili diversi, come varie tipologie di telecamere o sensori per l'ispezione agricola, ambientale o della fauna selvatica. Da ciò deriva la necessità di realizzare staffe personalizzate per fissare questi elementi al telaio dei droni. Le caratteristiche delle staffe variano da progetto a progetto. Ad esempio, può essere necessario posizionare il carico utile lontano dal punto di alimentazione, poiché quest'ultimo potrebbe surriscaldarsi su lunghe distanze, oppure mantenerlo a un'inclinazione particolare. Per progettare e fabbricare le staffe, che devono essere resistenti e durevoli, Nextech utilizza una combinazione di stampa 3D SLS, materiali compositi e lavorazione meccanica. Il suo punto di forza è l'ottimizzazione delle tecnologie affinché si completino a vicenda, piuttosto che sostituirsi l'un l'altra.
"La combinazione della lavorazione meccanica tradizionale con la stampa 3D SLS per me ha posto le basi del modo in cui produrremo qualsiasi articolo in futuro."
Liam Kroone, ingegnere di progettazione meccanica presso Nextech
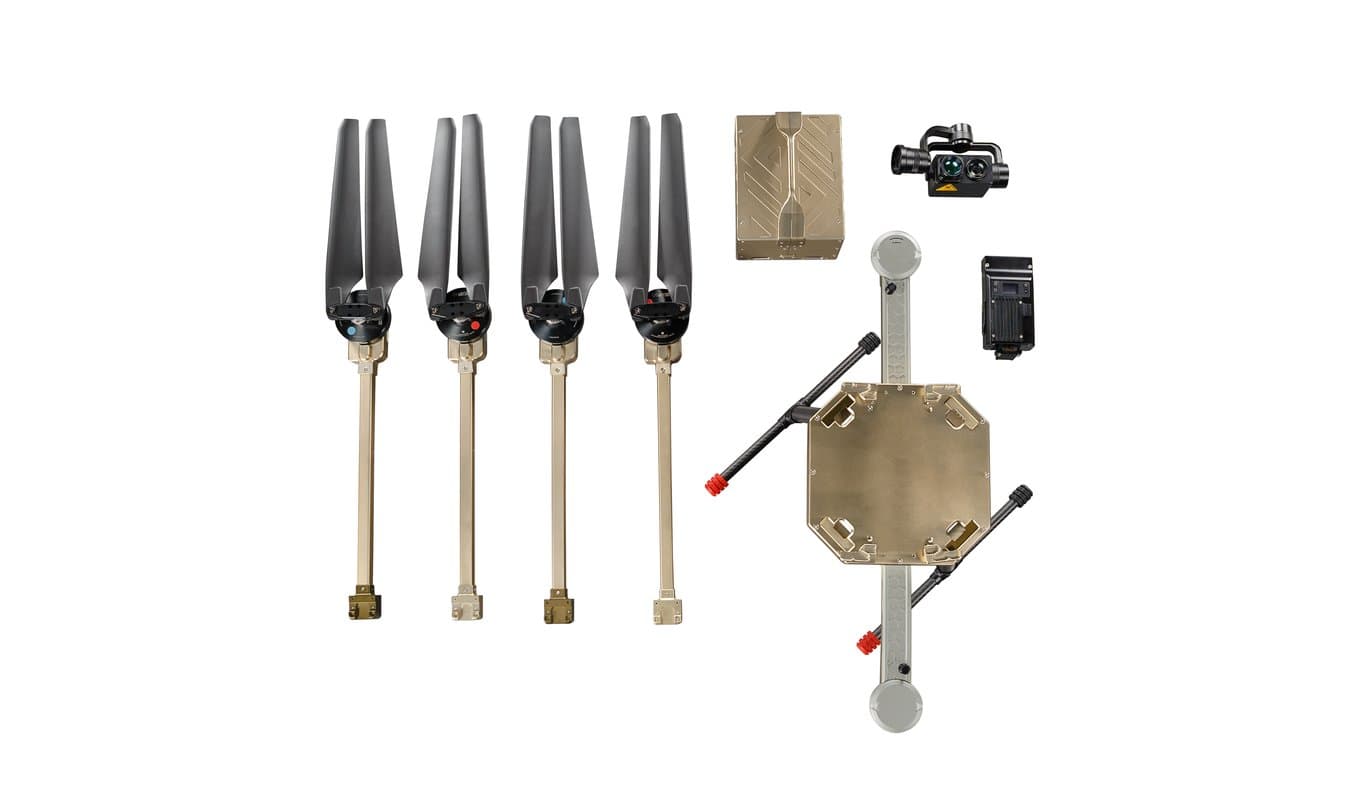
Il modello a quattro eliche Atlas-T sfrutta una combinazione di parti realizzate tramite stampa 3D SLS (pale dell'antenna e coperture di supporto cardanico e sensore di metano), parti in metallo realizzate tramite lavorazione meccanica e parti in fibra di carbonio, per ottimizzare il carico utile e creare geometrie uniche per prestazioni eccellenti.
Misurazione dello scioglimento dei ghiacciai
Il catalogo Nextech include un drone ad ali fisse con apertura alare di 3,2 metri e una distanza massima percorribile di 100 chilometri. Nell'ambito di un progetto in collaborazione con il governo francese, questo drone era utilizzato per osservare e ispezionare le calotte di ghiaccio in scioglimento dell'Artico. L'apparecchio trasportava dispositivi di imaging multispettrale e termico personalizzati per misurare l'influenza dell'oceano sulla velocità di scioglimento. Il team di Nextech ha dovuto progettare staffe e componenti del corpo del drone personalizzati per permettere all'apparecchio di trasportare questa delicata tipologia di carico utile. Il team ha inoltre progettato estremità alari adatte a condizioni estreme.
"Se la massa del drone o le condizioni ambientali cambiano, il profilo delle estremità alari deve fare altrettanto. Durante la prototipazione le variabili possono cambiare. Realizzare le parti tramite la lavorazione meccanica è molto costoso quando non sappiamo ancora esattamente come sarà il prodotto finale", afferma Kroone.
Le estremità alari definitive vengono realizzate in un composito di fibra di carbonio, ma la creazione degli stampi per questi materiali richiede troppo tempo e la lavorazione meccanica è troppo costosa. L'utilizzo della Nylon 12 Powder con la Fuse 1+ 30W permette al team di sperimentare forme complesse che hanno un peso simile a quello delle parti per utilizzo finale in fibra di carbonio.
"Se l'idea è utilizzare l'alluminio o la fibra di carbonio, è difficile ottenere lo stampo giusto già nella fase iniziale del progetto. La Fuse 1+ 30W ci permette di creare forme complesse e realizzare svariate versioni. Se è necessario apportare modifiche, possiamo stampare un nuovo design senza troppe difficoltà", spiega Kroone.
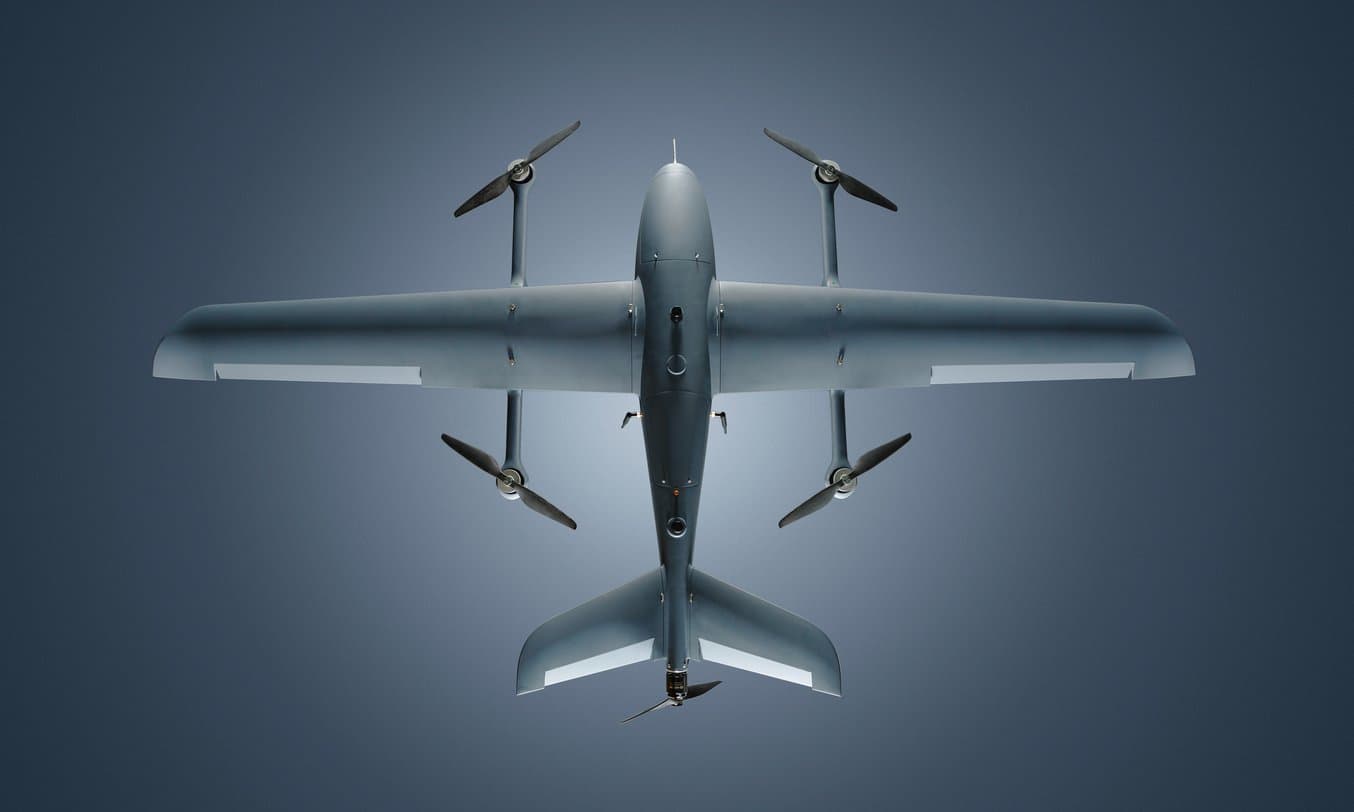
Questo rendering di un drone ad ali fisse di Nextech mostra la portata e la complessità del design.
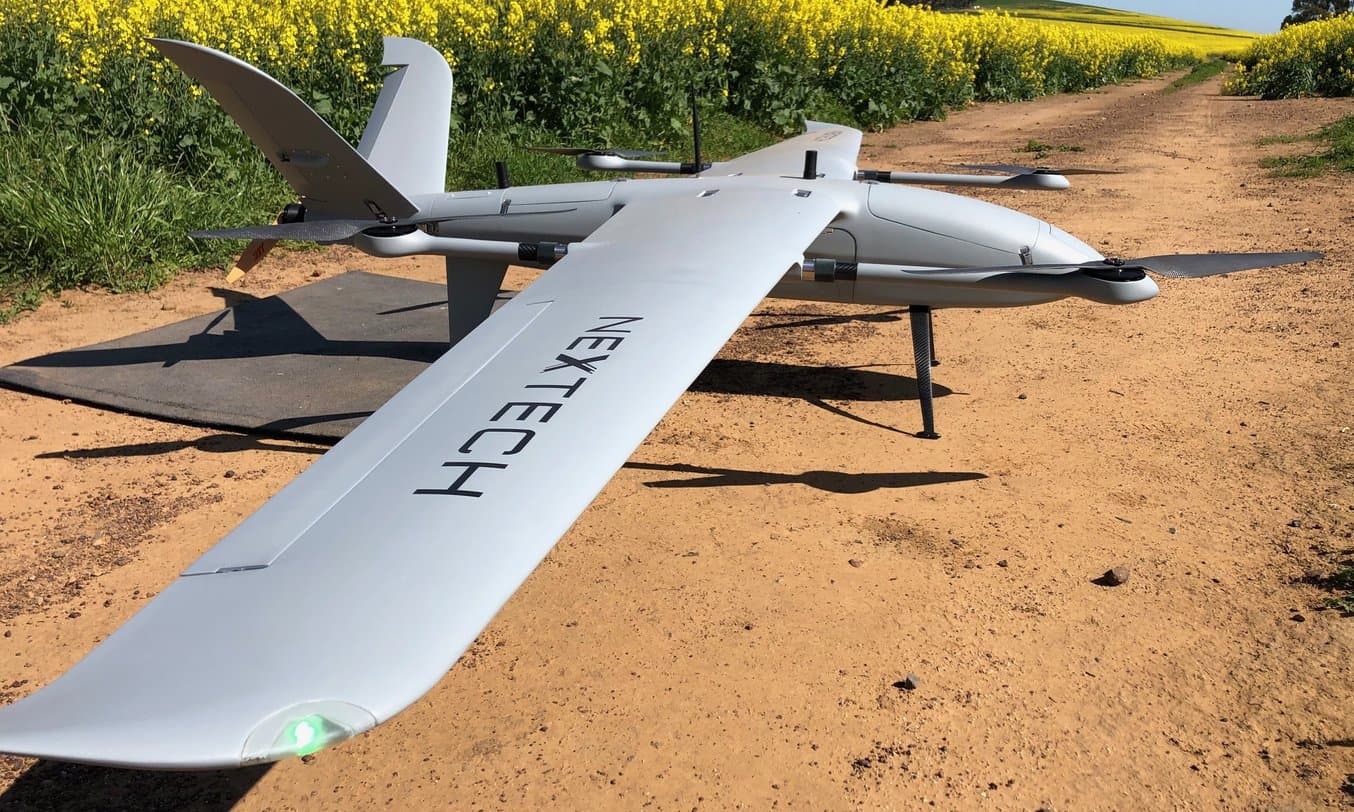
Il team di Nextech si è affidato a un processo di progettazione che sfrutta lo stampaggio in fibra di carbonio con la Fuse 1+ 30W e la Nylon 12 Powder per eseguire rapidamente iterazioni e test funzionali delle estremità alari del drone ad ali fisse.
Produzione di 100 parti per utilizzo finale alla volta
Per la progettazione del drone multirotore Atlas-T, il team ha sperimentato vari design che permettessero di mantenere la tecnologia di trasmissione a determinati angoli e distanze. Il modo in cui il dispositivo viene sorretto ha un impatto sulle sue prestazioni e il corretto posizionamento del GPS e dell'antenna consente di ottenere un raggio di spostamento più ampio e una migliore qualità della trasmissione. La tecnologia di tracciamento dell'antenna a lungo raggio non deve essere ostacolata da materiali conduttivi voluminosi; la personalizzazione dei fissaggi del carico utile e dell'antenna richiede quindi la realizzazione di geometrie complesse e l'esecuzione di numerosi cicli di test iterativi con un materiale non conduttivo.
Kroone ha utilizzato la Fuse 1+ 30W per sviluppare supporti di montaggio della batteria con una funzione di inserimento a scatto. Il design comprendeva componenti sia interni che esterni, stampati in Nylon 12 Powder per il drone di utilizzo finale. A causa delle dimensioni dei componenti interni e dell'elevato volume di produzione, era difficile programmare in modo efficiente le macchine a controllo numerico. "L'inserimento di queste piccole parti all'interno delle macchine a controllo numerico richiederebbe molto tempo, ma con la Fuse 1+ 30W possiamo stamparne cento alla volta", afferma Kroone.
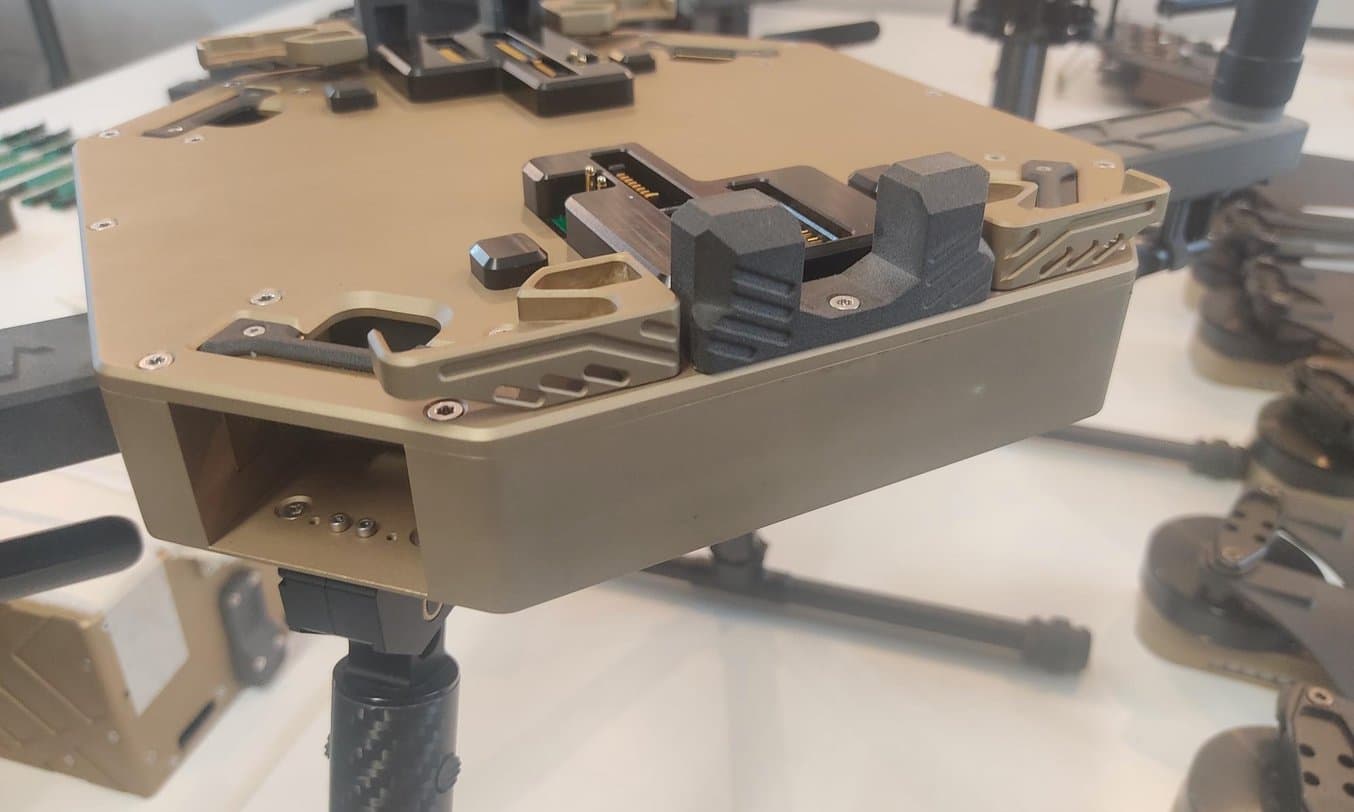
Il supporto di montaggio della batteria per utilizzo finale installato sul drone a quattro eliche Atlas-T viene realizzato con la stampante 3D SLS Fuse 1+ 30W in Nylon 12 Powder.
Risultati all'altezza di apparecchi da milioni di dollari
L'unione della sinterizzazione laser selettiva con il controllo numerico computerizzato apporta una maggiore flessibilità al processo di progettazione e produzione di Nextech, che è ora in grado di produrre parti in lotti e realizzare geometrie complesse con la Fuse 1+ 30W. L'azienda continua inoltre a usare la lavorazione meccanica per le parti in alluminio ad alta resistenza di altri componenti. Nella ricerca del giusto apparecchio SLS, era importante trovarne uno all'altezza delle macchine a controllo numerico già in possesso dell'azienda. Per questo Nextech ha scelto la Fuse 1+ 30W. "È davvero uno strumento tecnologico straordinario. Le macchine a controllo numerico ci sono costate milioni di dollari, mentre [la Fuse 1+ 30W] ci offre la stessa capacità di produzione a un costo di 60 000 $ ad apparecchio", afferma Kroone.
Per ogni nuovo drone di Nextech utilizzato con buoni risultati, la notorietà dell'azienda aumenta, così come la domanda. Nextech conta sulla Fuse 1+ 30W per una produzione uniforme e fluida. "La ripetibilità e l'affidabilità sono fondamentali per garantire la produzione di droni di alta qualità in tempi rapidi. È risaputo che molte stampanti SLS riscontrano errori o non riescono a completare un progetto, mentre la Fuse 1+ 30W è un apparecchio di alta qualità supportato da un'assistenza di livello eccellente", afferma Kroone. L'affidabilità dell'apparecchio stesso, unita all'impegno di Formlabs per fornire assistenza di massima qualità in tutto il mondo, aiutano la produzione ad andare avanti.
Il settore dei droni è estremamente competitivo e vede le aziende contendersi grossi contratti con i governi o nei settori della ricerca e dell'agricoltura. Per non rimanere indietro, le aziende produttrici devono aggiornare costantemente le loro tecnologie e offrire opzioni personalizzabili per ogni progetto. La stampa 3D e l'adozione in-house della sinterizzazione laser selettiva e della lavorazione meccanica CNC sono ciò che consente a Nextech di distinguersi dalla concorrenza.
"Credo che le aziende che producono in lotti ma non hanno un apparecchio del genere saranno in difficoltà in futuro. La mancanza di workflow in-house da implementare quando serve rappresenta un grande svantaggio."
Liam Kroone, ingegnere di progettazione meccanica presso Nextech
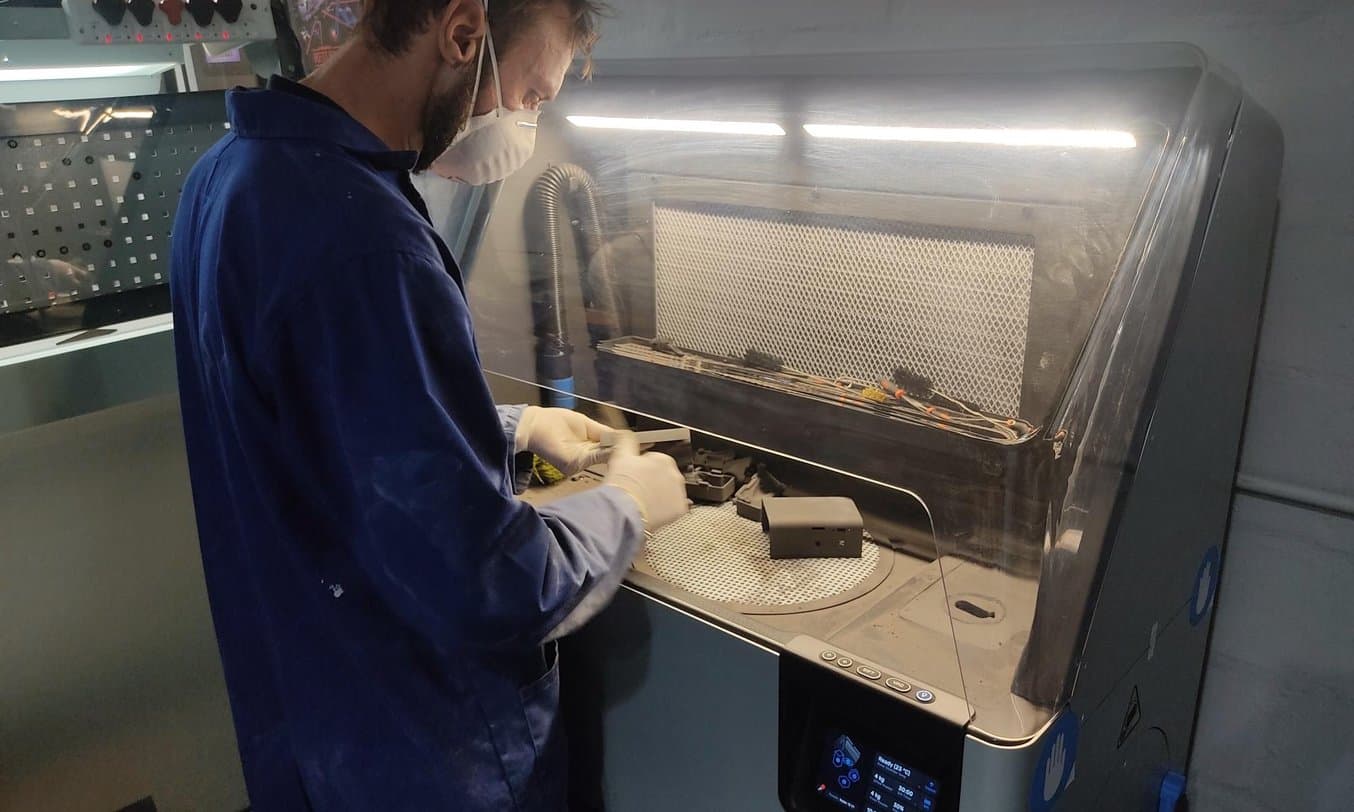
La Fuse Sift consente di implementare un workflow sicuro ed efficiente per la rimozione di polvere dalle parti e il riutilizzo dei materiali.
La combinazione di tecnologie di manifattura tradizionali con workflow avanzati di produzione additiva in-house ha permesso a Nextech di guadagnarsi un posto di rilievo nel settore. L'affidabilità delle stampanti SLS della serie Fuse di Formlabs permette all'azienda di essere agile, rispondere alle richieste dei clienti e ai cambi di fornitore e migliorare costantemente i suoi prodotti.
Un ringraziamento speciale al nostro partner rivenditore sudafricano BuildVolume per i consigli e l'assistenza forniti a Nextech sulle soluzioni di stampa 3D di Formlabs.